BERNINI DESIGN BE32 User manual

BE32 NET USER MANUAL VersionA17C 09/10/11 1
1.0 GENERAL DESCRIPTION
BE32 is a control system for STANDBY GEN-SET features 22 powerful programmable
parameters (section 10.00 and 11.02 ). Input from the GEN-SET provides visual indication for
the following:
LOW FUEL LEVEL , OVERLOAD, ALARM 1 and2 , LOW OIL PRESSURE, HIGH
TEMPERATURE (two channels), FUEL ALARM, EXTERNAL EMERGENCY STOP, ENGINE
RUNNING and REMOTE TEST.
The following parameters are measured and sampled as analogue inputs:
MAINS VOLTAGE (3-PHASE), GENERATOR VOLTAGE (3-PHASE), BATTERY VOLTAGE,
GENERATOR CURRENT (3-PHASE), GENERATOR and MAINS FREQUENCY.
These outputs are relay controlled : START, STOP SOLENOID, ALARM OUTPUT, FUEL
SOLENOID, MAINS CONTACTOR and GENERATOR CONTACTOR , GLOW PREHEAT and
'IDLE SPEED' .
For the remote transmission of alarms, and for special functions, eight static outputs are
available: ‘OIL’ , ‘TEMP’., ‘FUEL’ , ‘STARTING FAILURE’, ‘OVERLOAD FIRST LEVEL’,
‘ENGINE RUNNING’,’ BATTERY FAILURE’ and ‘GENERATOR VOLTAGE’.
The BE32-NET version includes RS232C interface and SENDERS interface for oil pressure
and engine temperature .
1.1 FRONT PANEL SELECTIONS
The control key switch, on the front panel, has 3 positions 'AUTO'-'RESET'-'MAN'. The key
position 'RESET' or 'MAN' of the key switch is repeated on the JB9 output connector.
1.10 ‘AUTO’ OPERATING MODE
The timers referring to GEN-SET automation are expressed on the ch. '0' and '1' (see page 7).
These timers are activated when the voltage parameters on ch. 'D' and 'E' reach the
programmed thresholds. The GEN-SET starts in 'AUTO' for the following : MAINS voltage or
frequency failure, periodic 'START' (ch 'A' and 'B'), REMOTE TEST (input JM-10) and/or
‘REMOTE START’(input JF7). All starting characteristics are specified on ch.'5'-'6'-'7'-'D'-'E'-'G'
and 'F''.
'C' is the trip level of overload protection for the GEN-SET. The first level 'c' warns to
disconnect the 'NON VITAL' loads by using JB-4 output. The GEN-SET will stop after full
MAINS restoration (or remote control restoration) or when an alarm is detected. The MAINS and
GENERATOR contactor are controlled automatically by means of the timers and thresholds .
The contactor will be enabled only if the electrical parameters VOLTAGE/FREQUENCY are
within the programmed value (ch.'D'-'E'-'H'-'h'-'L' ). If the sequences of the phase are not the
same for the mains and for the generator an alarm -r- will appear on the display. In this
condition the contactor remains disabled.
1.11 ‘MANUAL’ OPERATING MODE
This allows the 'off-load' starting of the GEN-SET by means of the 'START' and 'STOP' push-
buttons. The load is not tranferred to the generator. To enable the GENERATOR contactor in
‘MAN’ the user must provide external wiring by using JB3 terminal (‘GENERATOR VOLTAGE’
output).
NOTE:' ch'. means 'channel of the automation parameter'. Example: ch. 'C' is the 'C' parameter
on the automation table (see page 7).

BE32 NET USER MANUAL VersionA17C 09/10/11 2
1.12 ‘RESET’ OPERATING MODE
With the key switch in this position it is possible to clear fault alarms and to program the
parameters ( section 5.0).
1,13 START - STOP
These are the push-buttons for the manual control of the engine (enabled only in 'MAN').
In 'AUTO' the activation of the 'STOP' push button will perform ,if the engine is running, an
emergency stop cycle. The message 'E04' will appear on the display, and the user must clear
this alarm in order to start the engine.
2.0 BE32 DISPLAY FEATURES
The BE32 features a high performance 3 digit display. With the ‘UP’/’DOWN’ push-buttons it is
possible to select the following measurements:
2.01 Data: the automation parameters are displayed in the program mode (see page 6). On the
left one digit is displayed for the appropriate channel and on the right, two digits for the
significant value. If the BE32 is not in the 'program mode' the display will show the 'HOUR
COUNT'. The resolution is 1 hour. When the count is over 999 a right decimal point will appear
as indication multiplied by 10 (resolution 10 hours).To clear the counter press together STOP
and ACK for 10 “ when the key switch is in ‘MAN’ position.
2.02 Aac: value of the generator current in the range 000 to 800A. The current transformer
ratio is defined in channel 'L' (page 6b). The reading is selected single/three-phase. The BE32-
NET reading range is up to 8000Aac.
2.03 Vac: voltage of the MAINS or of the GEN-SET. The measurement range is 0 Vac to 500
Vac. If the FUEL SOLENOID is opened the display will show the GEN-SET voltage. If the FUEL
SOLENOID is closed the display will show the MAINS voltage.
2.04 HZ: frequency of the mains/generator. The resolution is 0.1 HZ. The range is 00.0 to 99.9
Hz . The display shows automatically mains (if ‘FUEL SOLENOID’ is disabled) or generator (if
‘FUEL SOLENOID’ is energised).
2.05 Vdc: battery voltage measurement. The range is 00.0 Vdc to 32.4 Vdc. This measurement
is displayed by pressing simultaneously the UP and DOWN push-buttons.
BE32-NET OPTION: see section 11.01 for further information.
3.0 LED INDICATIONS
The front facia has alarms indication by means of red LEDs:
OIL PRESSURE ALARM. This alarm monitors the pressure
inputs wired on terminal JF-9(engine shutdown),JM-7(warning).
The delay from the engine starting point is programmed on CH.
‘
2
’
(normally closed contact)
TEMPERATURE ALARM . This alarm monitors the inputs JF-
3(shutdown),JM-6(warning) . The engine will stop after the
cooling down time. The selection, normally closed or open, is
made by programming a code in ch. ‘I’ (see page 7).

BE32 NET USER MANUAL VersionA17C 09/10/11 3
This alarm energize if, after a complete engine start cycle, the voltage of the generator does not
reach the threshold defined on ch. ‘E’ (150 seconds’ delay). The engine stops and this two
LEDs will light in flashing mode.
This alarm has 3 sources: one is external and two are internal. The external source is the
terminal JF-4 (energized to ground). The first internal source is the threshold ‘C’ of the
CURRENT measurement (see page 7): one of the three current measurements must be greater
than the threshold ‘C’ for 6 seconds at least. The second source is the generator voltage that
falls below the voltage threshold ‘E’ for 6 seconds.
The engine will stop after the cooling down time (channel ‘8’).
These are auxiliary (normally open) STOP inputs.
There is a 10 seconds’ delay from engine crank
disconnection .ALARM1: JF-1 terminal.
ALARM 2: JF-8 terminal .
Fail to start alarm: the automatic starting cyle has failed (see
parameters ‘5’-‘6’-‘7’ on page 7).
Yellow LEDs indicating the status of the
stop solenoid/glow/fuel relay outputs.
‘FUEL THANK’ has yellow LED only for
optical warning (JF-5). ‘NO FUEL IN
THE TANK’ alarm stops the engine (JF-
2). ‘BATTERY VOLTAGE ALARM’ warns
for a Low Voltage condition.

BE32 NET USER MANUAL VersionA17C 09/10/11 4
The signal source for OVER SPEED monitoring is the frequency measurement of the generator
voltage ‘VL1’ to ‘VL2’. The threshold is defined on ch. ‘H’ and the trip has a 4 seconds’ delay.
The cooling down time is nort provided.
BELT BREAK ALARM
This protection features engine stop if a belt break occurs. To enable this protection, select the
code on parameter ‘I’ (page 9). The protection has a 10” delay and the condition of alarm is the
loss of voltage on terminal W.L./D+( inputs JM3-4). The alarm will show a ‘r.c.’ message on
display.
These are the push buttons to start and stop the set. The green LEDs ‘RUN’ indicate the status
of the engine: ‘RUNNING’(LEDs on) or ‘NOT RUNNING’ (LEDs off).These LEDs will light if a
voltage greater than 130Vac is detected on generator or a voltage is detected on W.L. (JM3-4).
The START push button is enabled only by the KEY SWITCH in MAN position. The STOP push
button is always enabled. The action on the STOP push button in AUTO mode will energise a
REMOTE STOP cycle (see below).
REMOTE STOP alarm monitors the JF-10 input. If
grounded, a STOP cycle will be initiated.This alarm,also
refers to the STOP push button action in ‘AUTO’ mode.
REMOTE COMPUTER has yellow LED indicating the
communication to external computer by means of RS232C
serial interface.
SLAVE (red LED) and MASTER (green LED) are not used.
ALARM / RESET (ACK.) push button has some functions:
acknowledges the alarms and ,used together with the STOP
push button, enables the PROGRAMMING mode (see
PROGRAMMING on page 6)

BE32 NET USER MANUAL VersionA17C 09/10/11 5
‘GENERATOR VOLTAGE’ is a green LED inicating the presence of GENERATOR voltage.
This Led will light if the voltage of the generator is greater than the threshold on ch. ‘E’.
‘GENERATOR CONTACTOR’. The green LED ‘ON’ will light if the generator contactor output
relay is energised (JE1-2-3 terminals).
‘MAINS CONTACTOR’. The green LED ‘ON’ will light if the mains contactor output relay is NOT
energised (JD4-5-6). To drive an external contactor the user must wire the normally closed
contacts(JD5-6). In this way, a failure to the BE32 system will keep the mains contactor closed.
‘MAINS’ is a green LED indicating the presence of mains voltage. This led will light if the
voltage and frequency parameters meet the programmed thresholds (see page 7).
4.0 GENERAL CHARACTERISTICS
SUPPLY:..........7V d.c. to 32V d.c., 40 to 150 mA , transient voltage protection and
reverse polarity protection are included.
CURRENT TRANSFORMER:.......... 5 Aac. continuously / 10Aac for 30”,
two wire connection, one side grounded
ratio up 8000Aac (BE32-NET) .
VAC INPUTS RATINGS:.......continuously 600Vac max. line to line (generator and mains).
VAC MAXIMUM 2 MINUTES :................... 2000V ac line to line .
VAC MAXIMUM OVER VOLTAGE............ 5000V (8/20 microseconds).
STATIC OUTPUTS:..........12V-24V/150 mA, short circuit protected .
ENGINE RELAY CONTROLS:.......... 8A/12 Vdc to 24V dc (external fuse is recommended).
CONTACTOR RELAY CONTROLS...8A/250V resistive,3A/250Vac inductive
external protection fuses are recommended.
DIGITAL INPUTS:...........contact grounded polarity, 10mA /closed circuit current,
V battery voltage / open circuit, overvoltage protection:250V/10Ms,
Hardware and Software filtering for safe operation.
ANALOG INPUT (SENDERS)....resistance range 10 OHM to 500 OHM, overvoltage protection,
shielding is recommended over 4M length
DYNAMO/CHARGE ALTERNATOR (W.L.):.......... 2,5W 12Vdc or 24Vdc.
W.L./D+ SENSITIVITY..............4Vac/dc to 20Vac/dc , rear cover trimmer calibration.
DIMENSION and WEIGHT:.......... see page 14.
OPERATING TEMPERATURE:.......... –25°C to 70°C (R.H. 95%).
DISPLAY ACCURACY :..........+/- 2%, +/- 1 LSD(least significant digit).
MEASUREMENTS RESOLUTION........8 bit (255 point of measure)
PRECISION............user adjustable by calibration program down to 0 (OPTION –NET)
TIMING PRECISION...................+/- 0.1% over all operating conditions
FREQUENCY MEASUREMENT THRESHOLD:.......150Vac (line to line), resolution 0.1Hz
BE32 USER MANUAL (VERSION A17C)
SERIAL INTERFACE (OPTION-PLUS)..........standard RS232C

BE32 NET USER MANUAL VersionA17C 09/10/11 6
DATA RETENTION..................eeprom 100 year guaranteed on –40°C to +85°C
CONTROL SYSTEM....................8 bit/6MHz microprocessor with full hardware watch-dog
DESIGN :.......... meet EN50081/1/2,50082/1/2,60801-2,61003-1,60546-1.
EXTERNAL OVER VOLTAGE PROTECTION DEVICES , ON MAINS INPUTS, ARE
RECOMMENDED (2KV ac) TO AVOID FAILURE DURING HIGH ENERGY LIGHTENING.
5.0 PROGRAMMING INSTRUCTIONS
The table on page 7 lists the adjustable parameters. Of the three digits displayed the left is
the address parameter and the right digits are the significant value.
The 'PROGRAM MODE 'is enabled by pressing for 5 seconds at least the ‘STOP’ and ‘ACK’
push-buttons simultaneously (with the key-switch in the RESET position). In the program mode
the led 'DATA' will light. By pressing 'UP' or 'DOWN' it is possible to select the address of
automation parameters. By pressing the 'UP' ( or 'DOWN') and 'STOP' push-buttons together it
is possible to increase (or decrease) the selected parameter.
The BE32 unit is factory pre-programmed with DEFAULT parameters.
The defaults are always available by pressing simultaneously the cursors 'UP' and 'DOWN' for
two seconds at least (only in 'PROGRAM MODE ').
The data are pushed in a non volatile memory at the first transition of the KEY in ‘MAN’ or
‘AUTO’. It is recommended to check the data changing by the following : a) - put the set in
‘MAN’, b) - disconnect V battery for 30 seconds, c) - supply the BE32, d) – select ‘PROGRAM
MODE’ and check the modified data. If an error occurs, try a new programming cycle.
6.0 MAINS SIMULATED
When the JC-10 input is grounded BE32 simulates the presence of the mains.
The internal microcomputer will display an '-on' message to indicate the 'MAINS PRESENCE'.
This connection is used in applications where MAINS is not available and the user needs a
remote starting by means of an external switch, a level switch, a timer or others.
7.0 MAINS HIGH VOLTAGE
In addition to the MAINS failure due to Under Voltage (parameter 'D') or Frequency (parameters
'h'/’H’) there is a MAINS failure for HIGH voltage. The threshold is fixed to 495 Vac. The display
will show a message 'E02'. The failure will disappear as the voltage will come in the window
between 'D' and 495V.
8.0 UNDER FREQUENCY PROTECTION
The under speed protection is programmable at address 'h'. The source of the signal is the
frequency measurement of the ALTERNATOR voltage. If the frequency does not reach the
programmed threshold the BE32 will not enable the contactor of the generator. If BE32 detects
a frequency failure (with the contactor already enabled and the load transferred to the GEN-
SET) an alarm situation is generated: the alternator contactor is opened and the engine is
stopped after a cooling down timing. The display will show
'EO1' that means UNDER FREQUENCY.
9.0 MAINS AND GENERATOR CONTACTOR AUTOMATION
The coil of MAINS contactor is enabled if all three Voltage phases are between 'D' and
495Vac. The frequency must be within 'h' and 'H' values. This stability must persist for time '1'
timer (mains restore). The MAINS contactor is opened if a failure (V or Hz) is detected for 2
seconds at least. The GEN-SET will start after MAINS FAILURE TIME (channel '0') and will stop
after time '1' and '8' timers. The GENERATOR contactor is enabled in the same way but only in
'AUTO'. It will also be opened if any internal or external alarm is detected. The contactor are
enabled only if the mains and generator have the same phase sequence (ccw).
If the phase rotation is different a message -r- will appear on the display. A safe time delay of 2
seconds is inserted between GENERATOR and MAINS contactor actions.

BE32 NET USER MANUAL VersionA17C 09/10/11 7
10.00 PARAMETERS LIST
ADDRESS DESCRIPTION RANGE FACTORY DEFAULT
0 Mains fault delay 1'-9',05"to 59" 5 seconds
1 Mains restore 1'-9',05"to59" 5 seconds
2 Oil pressure fault delay 0"-99" 10 seconds
3 Energised to stop
solenoid time
10"-99" 15 seconds
4 Horn enable 00"-99" 60 seconds
5 Cranking up time 00"-99" 5 seconds
6 Attempts number 1-99 3 attempts
7 Time between Attempts
pulses
1"-99" 5 seconds
8 Cooling down time 1'-9',0"-59" 30 seconds
9 V alternator time 1'-9',0"-59" 5 seconds
A Periodic start 1-99 days 00 days
B Periodic run time 1'-99' 00 minutes
C
Gen set Overload
(TRIP)
000A-999A
000A(inhibited)
c Gen set Overload
(WARNING)
000A-999A 000A(inhibited)
D Mains failure 100V-500V 330V
E Generator failure 100V-500V 330V
F Glow time 0"-99" 0 seconds
G Idle Speed 0"-99" 99 (nominal speed)
H Over Frequency 00-99(4 seconds delay) 57Hz
h
Under Frequency
00-99(6 seconds delay)
47Hz
I
Belt break/code
CODE (page 9)
00
L VOLT/AMP. Range CODE (page 9) 01
NOTE: the values of the ‘DEFAULT’ are subjected to changes without notice. We recommend
to check these values before putting the BE32 control system in use.

BE32 NET USER MANUAL VersionA17C 09/10/11 8
11.00 BE32 –NET OPTION
This option features interface to analogue senders, multilink communication to up 10 BE32 units
and an extended C.T.s ratio up 8000Aac.
11.01 SENDER INTERFACE and DISPLAY
The system features VDO sender interface as follows.
Oil pressure sensor JM-7 Temperature sensor JM-6 (‘0’ code)
0 kg/cm2 10 OHM 40°C 287,4 OHM
2Kg/cm2 42 OHM 70°C 95,2 OHM
4Kg/cm2 82 OHM 115°C 25,8 OHM
6Kg/cm2 119 OHM 128°C 18,7 OHM
8Kg/cm2 152 OHM .... ....
10Kg/cm2 180 OHM .... ....
.... .... .... ....
The pressure has, on display, a range 00.0 KG/cm2 to 25,6 KG/cm2. To display the value press
the ‘UP’ cursor until the ‘DATA’ LED lights :a message ‘H’ will appear (hours count). Next action
on ‘UP’ will display a message ‘dc’ (battery voltage). Further pressure on ‘UP’ will show a
message ‘t’ (temperature in a range 000°C to 255°C). Finally, a last action on ‘UP’ will show the
message ‘P’ (pressure measure ). By pressing again the ‘UP’ push button the selection
‘FREQUENCY’ is made on display. The BE32 over the serial number 1200 have ,on the back
cover, the holes for close calibration by means trimmer (see page 13 and 14). The Release
A17C features the selection of different temperature senders. The programming is made on
parameter ‘L’. The ‘0’ code,on left side, will enable the above temperature sender (default). A ‘1’
code will select the following realtionship: 66°=180
ohm,100°=62ohm,130°=72ohm,150°=18,6ohm.
The code ‘2’ will enable the following
relationship:100°=151ohm,150°=40ohm,180°=21ohm,200°=14,3ohm.
11.02 ALARM / PARAMETER PROGRAMMING
Option –NET features additional programming parameters. To access these locations enter the
programming mode (page 6). The added parameters are : ‘n’ (current transformer ratio), ‘P’
(pressure threshold), ‘T’ (temperature threshold) and ‘SL’ (slave number).
11.03 CURRENT TRANSFORMER RATIO
‘n’ : extends the ratio to of CTs. Permitted value are :00 to 99 (means up 990Aac) and 10. to
80. (means 1000 Aac to 8000Aac). A decimal point means multiplied by 100.
EXAMPLES: 33 is 330Aac, 48 is 480Aac, 48. is 4800Aac, 70.is 7000Aac.
Be careful in programming ‘c’ and ‘C’: a decimal point will mean multiplied by one hundred.
11-04 PRESSURE ALARM
‘P’ : has a range 0.0 to 9.9 Kg/cm2. The alarm warns the user by means of the OIL PRESSURE
LED on front panel and by exciting the output alarm relay JC-2 and output alarm JB7. The alarm
does not stop the engine (only warning action). To disable the alarm put 0.0 on parameter ‘P’.

BE32 NET USER MANUAL VersionA17C 09/10/11 9
11.05 TEMPERATURE ALARM
‘t’ :has a range up to 250°C. To program the temperature alarm : a)-enter in the programming
mode, b)-by means of the ‘UP’ cursors select the message ‘t’, c)-press together ‘STOP’ and
‘UP’ or ‘DOWN’ push buttons in order to program the threshold. The alarm drives the ‘ALARM 1’
led (on front facia) and JC-2/JB-8 ALARM outputs. Not any stop action on the engine is made
(only warning action). To disable the protection put a full scale value 250 on parameter ’t’.
11.06 SLAVE PROGRAMMING
In a multidrop application where a certain number of BE32 are connected in a same link the
user must put a SLAVE number on each BE32. In this way the external computer is able to
access to the BE32 data without communication errors. Be32-NET includes a communication
program running on P.C..This software operates in a point to point communication system. The
user must program the same slave number on the BE32 side and on P.C. side (For multidrop
software contact the Factory). To program the slave : a)-enter programming mode, b) by means
of the ‘UP’/’DOWN’ cursors select ‘SL’, c) – put a number in the field 0-9 , d) PUT THE SAME
NUMBER ON THE COMPUTER SIDE (see instruction included in the DEMO.TXT file).
11.07 ADDITIONAL ALARM OUTPUTS
The option –NET has additional output alarm information:
JC-5 OVER FREQUENCY
JC-9 OVER/UNDER VOLTAGE
Be careful in using these low power static outputs (max 20mA at V battery voltage), these
outputs are intended to drive low power load (PLC input).
11.08 NEW FEATURES OF THE RELASE ‘A17C’
A) Alarm3 (JF7) is the remote test input. The BE32 will transfer the load to the generator (JM10
is a remote test without load transfer).
B) JB2 : is the alarm repetition of Battery failure
C) JB6 : is the alarm repetition for ‘low level fuel’ and ‘fuel end’
D) Channel L: additional sender models (see 11.00).
11.09 MEASUREMENTS CALIBRATION.
This section are reserved to a product with serial number over 1200.
To adjust the electrical measurements it is available, to the user, the digital correction.
INSTRUCTION:
A) Disconnect the Vdc supply and put the key switch in RESET.
B) Apply the Vdc supply and ,at the same time, press the ‘STOP’ push button for 2 seconds at
least.
C) Connect the electrical parameter to be calibrate (Mains Voltage, Generator Voltage/Current)
D) By means of ‘UP’ or ‘DOWN’ push buttons select one of the following parameters (a code
number ‘0’ to ‘5‘will appear on the display)
0 : MAINS VOLTAGE (common for all 3-phase).
1 : GENERATOR VOLTAGE (common for all 3-phase).
2 : GENERATOR CURRENT L1.
3 : GENERATOR CURRENT L2.
4 : GENERATOR CURRENT L3.
5 : BATTERY VOLTAGE.
By pushing the ‘STOP’ push button the actual measure will appear. To adjust the reading: push
together ‘STOP’ and ‘UP’ ( or ‘DOWN’) until the desired reading is reached.
To save in the memory this new ratio of reading push together ‘STOP’ and ‘ACK’: the display
will ‘flash’ once to confirm the ‘memory write cycle’ operation.
TO COMPLETE THE CALIBRATION: UNPLUG THE SUPPLY AND PUT THE SYSTEM IN
‘MANUAL’ OR ‘AUTO’ OPERATING MODE AND CHECK THE ACCURACY OFTHE NEW
MEASUREMENTS .

BE32 NET USER MANUAL VersionA17C 09/10/11 10

BE32 NET USER MANUAL VersionA17C 09/10/11 11

BE32 NET USER MANUAL VersionA17C 09/10/11 12

BE32 NET USER MANUAL VersionA17C 09/10/11 13
Seconds or minutes of mains
failure to initiate automatic
GEN-SET start.
MAINS FAILURE TIME
0"/59",1'/9'
( 5 seconds )
MAINS RESTORE
0"/59",1'/9'
( 5 seconds )
Seconds or minutes of mains in
stable conditions to initiate
automatic stop of GEN-SET.
OIL DELAY TIME
0" / 99"
( 10 seconds )
Time to mask the low oil pressure
input alarm (JF-9) from engine start.
STOP TIME
10" / 99"
( 15" )
Time of STOP solenoid enabling
relay output JC-4.
ALARM OUTPUT
0" / 99"
( 60 SECONDS )
The code '99' disables the timer :the alarm
output is cleared only by the ACK. push-button.
Other values will perform automatic alarm
output clearing.
ENGINE STARTING PULSE
0" / 99"
( 5 seconds )
Seconds of START solenoid excitement.
This timer is reset if the engine starts
before the programmed timeout.
Start attempt
1 / 99
( 5 attempts )
Numbers of automatic attempts
during automatic start cycle.
ATTEMPTS INTERVAL
0" / 99"
( 5 seconds )
COOLING TIME
0"/99", 1'/9'
( 30 seconds )
Engine cooling time after mains
restoration. During this time the
engine will run off-load.
GENERATOR TIME
0"/99",1'/9'
( 5 seconds )
Time of stable generator voltage to
enable generator contactor output
relay (JE1-2-3)
PERIODIC AUTO-TEST
0 / 99 Days
( 00, disabled )
Days between automatic periodic
starting cycle. 00 is a code to
disable the periodic test. The set
must be placed in 'AUTO'.
PERIODIC RUN-TIME
0' / 99 '
OVERLOAD FIRST LEVEL
00(0) / 99(9) A
(000 Amperes)
(00 minutes)
Time of engine running during periodic
automatic test. The set must be in 'AUTO'
to enable this function.
When the GEN-SET current is greater than
this value, the output JB-4 is enabled.
To avoid false trigger a delay of 3 second
is inserted.
Interval between starting pulse
attempts

BE32 NET USER MANUAL VersionA17C 09/10/11 14
'C' is the set point of the
overload level.The protection
has a 6 seconds' delay. The
value is up 99A for C.T. 50/5
and 100/5. The value is X 10
(by ten) for othter C.T. ratio
GEN-SET OVERLOAD
000A-990A
(000)
MAINS FAILURE
100V-500V
( 340V )
GENERATOR FAILURE
100V-500V
( 340V )
Mains voltage threshold. The hysteresis
is -5V/+15V.Example 'd'=380: below 375
there is a MAINS failure, above 395 there
is a MAINS restore.
Generator voltage threshold. The hysteresis
is -5V/+15V.Example 'd'=380: below 375
there is a MAINS failure, above 395 there
is a MAINS restore.
This is the preheat time. As default
no preheat time is included (00").
This output relay is wired on JC-1.
Speed control
00" / 99"
( 99 )
This function features the control
of the nominal speed.Example :'G'=20.
After 20" from the 'engine start' the JC-3
output will energize. This positive output is
used to drive the speed regulator to the
nominal speed.
DISPLAY CONTROL
CURRENT TRANF. RATIO
00 - 99
(00 as default code)
DO NOT PUT CODES OUTSIDE THIS
PERMITTED TABLE: ABNORMAL
SITUATION MAY BE EXPECTED.
FOR ADDITIONAL RATIOs SEE
SECTION 11.03.
This is the set point of the
Over Speed protection. The
delay is 4 seconds.
This is the set point of the
Under Speed protection. The
delay is 4 seconds. This source
of alarm drive the display message
'E01'. The protection is enabled only
if the load is trasferred to the GEN-SET.
The following table is permitted:
00 : JF3/6 N.O. / Belt break inhibited
01 : JF3/6 N.O. / Belt break enabled
10 : JF3/6 N.C./ Belt break inhibited
11 : JF3/6 N.C./ Belt break enabled
GLOW PLUG
Enable Time
00"/99" (00")
JC-3 not energized : engine runs at idle speed
JC-3 energized : engine runs at nominal speed.
The value 99 is not a time but a disable code:
the output JC-3 not used.
OVER SPEED
00Hz / 99Hz
( 57 )
UNDER SPEED
00Hz / 99Hz
( 47 )
BELT BREAK ENABLE
TEMPERATURE SWITCH
00-99 Code
(00- default)
JF3 is the temperature alarm inputs.
N.O. means NORMALLY OPEN
contact with no tempertature alarm.
N.C. means Normally Closed
in normal condition ( no alarm)
In scan mode the display
w
ill show all values. The
right decimal point will
flash when the display
change the phase . Each
value will persists 2 ".
0=typ 0
1=typ1
2=typ2
(page15)
Table of contents
Other BERNINI DESIGN Controllers manuals
Popular Controllers manuals by other brands
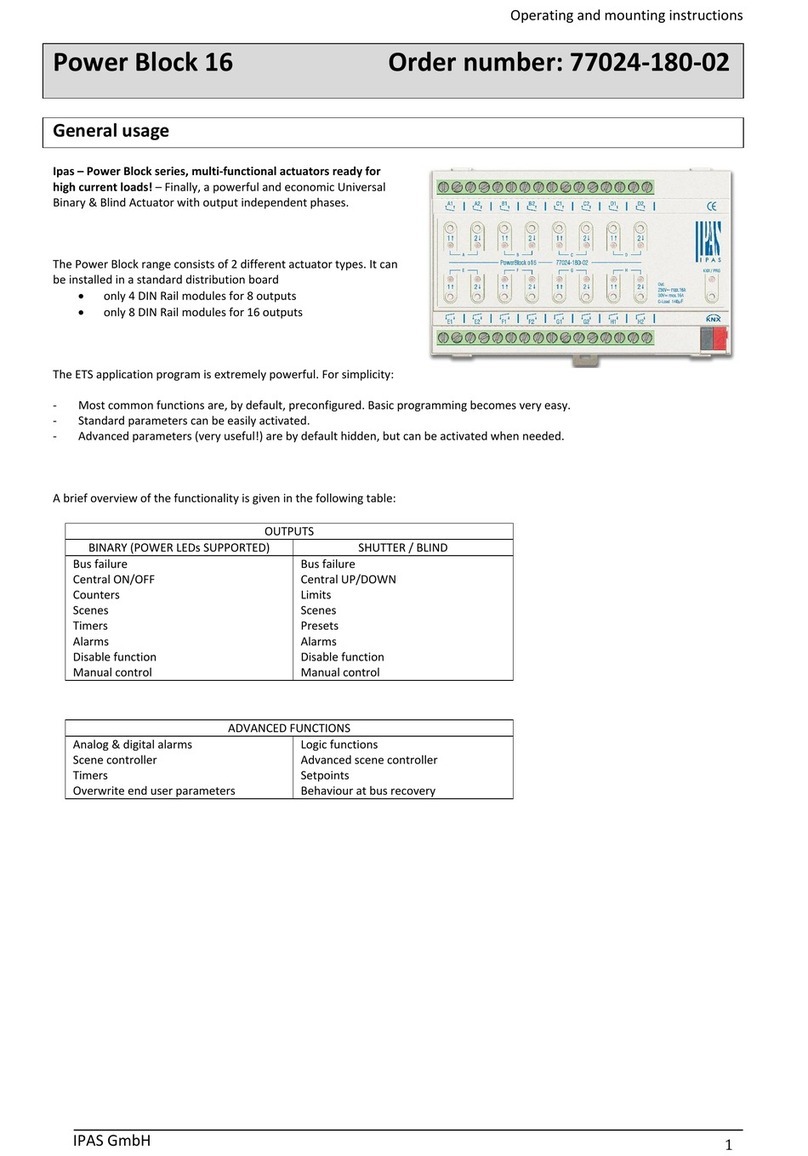
IPAS
IPAS Power Block Series Operating and mounting instructions
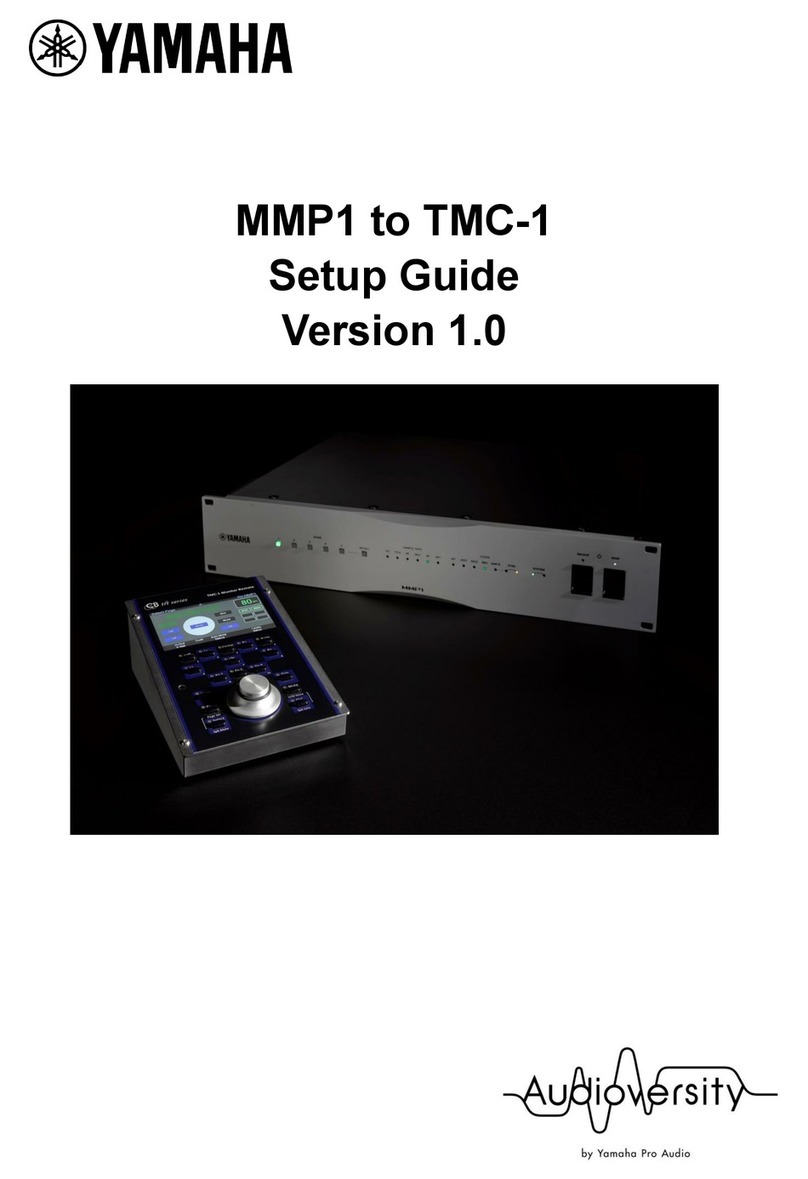
CB ELECTRONICS
CB ELECTRONICS TMC-1 Setup guide
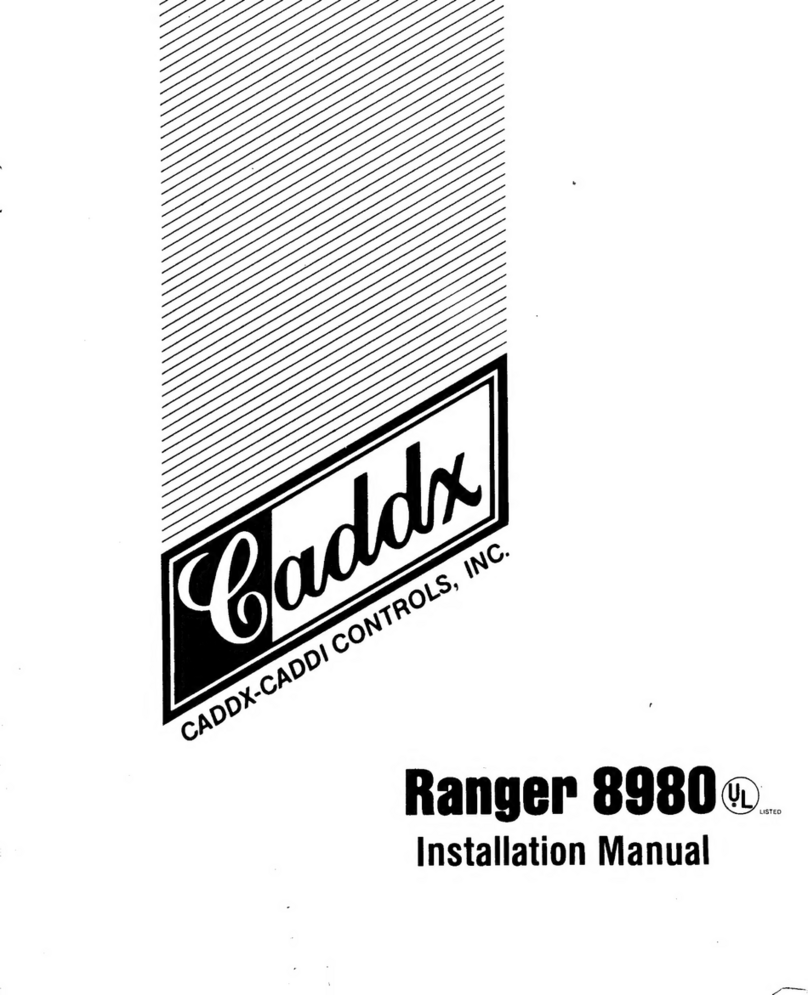
Caddx-Caddi Controls
Caddx-Caddi Controls Ranger 8980 installation manual
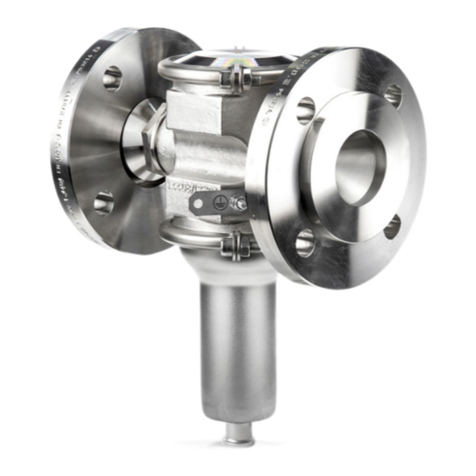
Mankenberg
Mankenberg UV 5.5 ATEX H2 operating manual
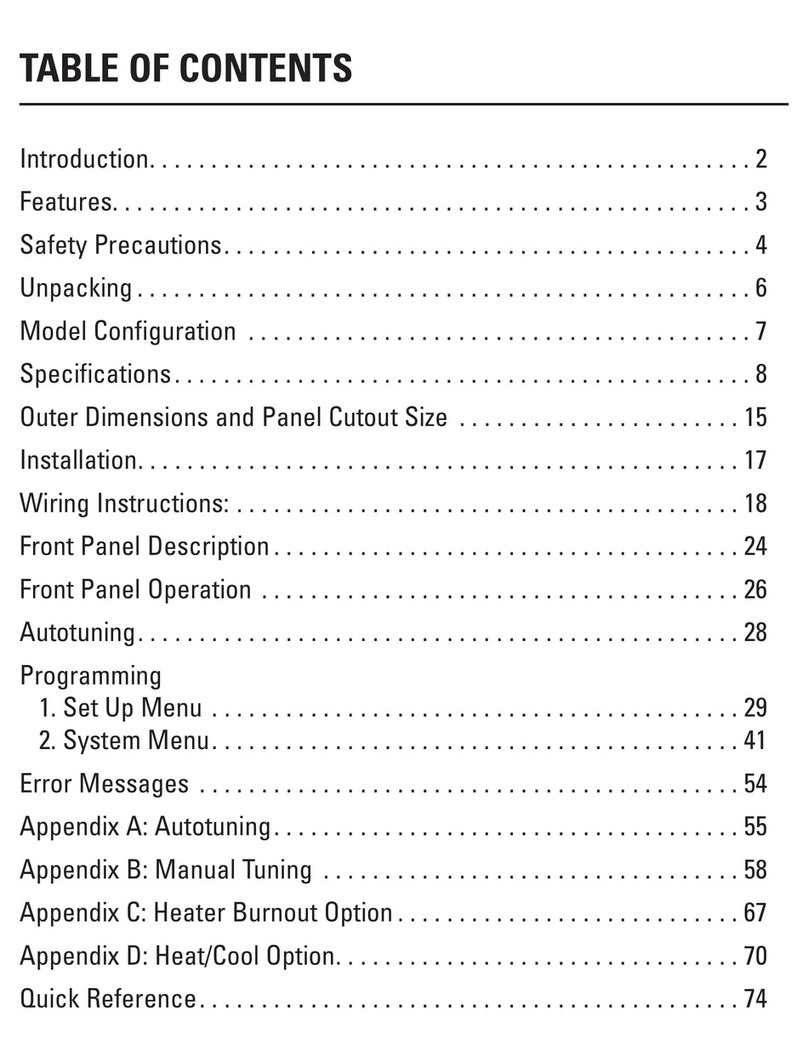
Omega
Omega CN4420 Series manual
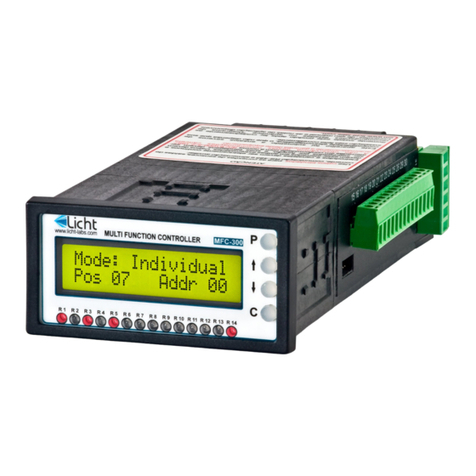
Licht
Licht MFC-300/P Technical manual