BRASS Akron 6035 CAN Instruction manual

123069
STYLE 6035 CAN JOYSTICK
INSTALLATION, OPERATION & MAINTENANCE MANUAL
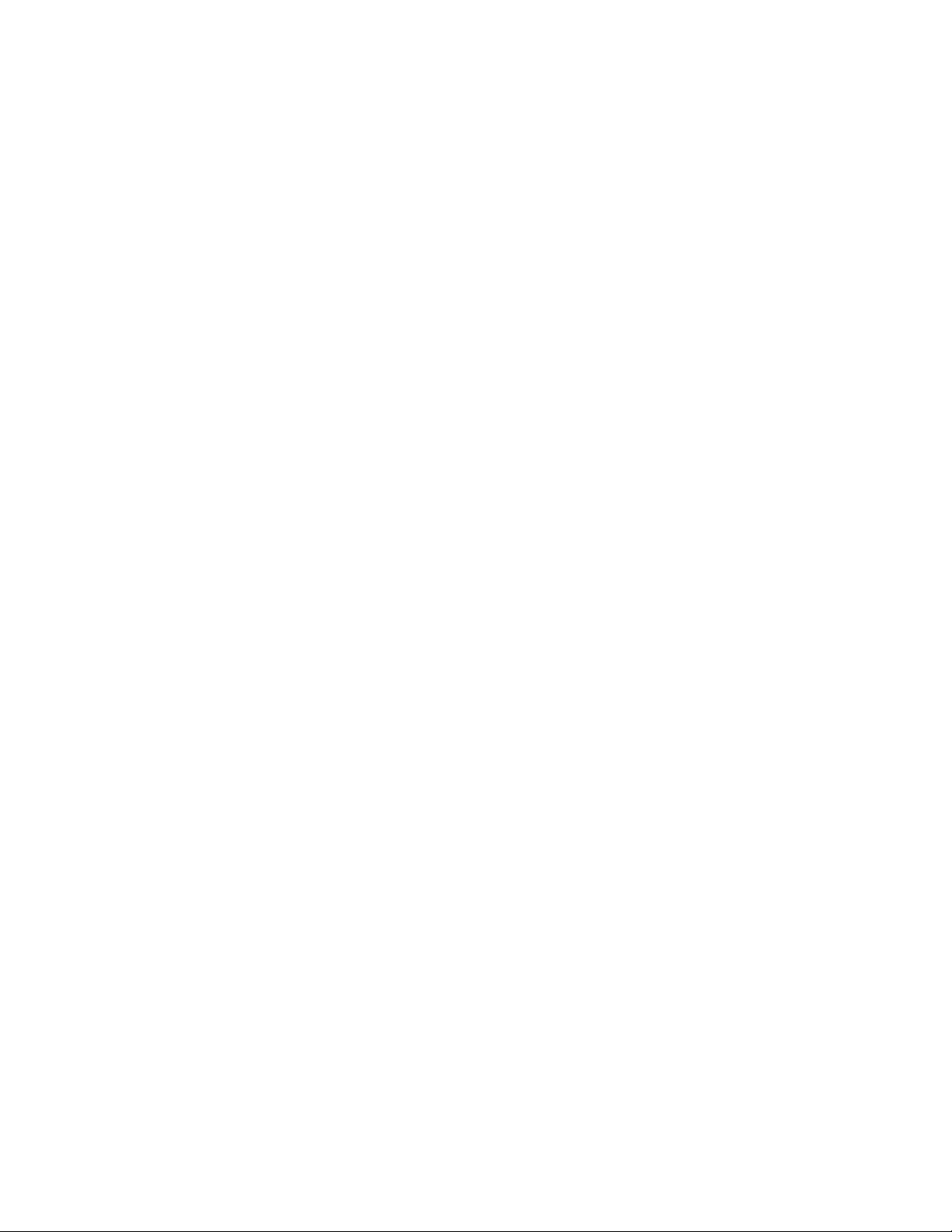
2
TABLE OF CONTENTS
SAFETY SUMMARY
····································································································································································2
PRODUCT SPECIFICATIONS························································································································································3
6035 CAN JOYSTICK·······················································································································································································3
INSTALLATION INSTRUCTIONS··················································································································································4
TOOLS & MATERIALS REQUIRED ·································································································································································4
MECHANICAL INSTALLATION······································································································································································4
ELECTRICAL INSTALLATION··········································································································································································7
OPERATING INSTRUCTIONS······················································································································································10
NORMAL OPERATION···················································································································································································10
SETUP AND CALIBRATION············································································································································································11
Zeroing and Spanning the Joystick····························································································································································11
Changing the Priority Level···············································································································································································11
MAINTENANCE INSTRUCTIONS·················································································································································12
TROUBLESHOOTING··································································································································································13
DIAGNOSTIC LEDs·························································································································································································13
AKROVIEW SOFTWARE·····················································································································································································································13
REVISION HISTORY····································································································································································14
LIST OF ILLUSTRATIONS
Figure 1 – Surface Mounting Hole Layout··························································································································································5
Figure 2 – Flush Mount Hole Layout··································································································································································6
Figure 3 – Adapter Plate Hole Layout································································································································································6
Figure 4 – Connector Label
················································································································································································7
Figure 5 – Typical Electrical Connections··························································································································································8
Figure 6 – Typical J1939 Wiring···········································································································································································9

SAFETY SUMMARY
SIGNAL WORD DEFINITION
Per the ANSI Z535.4 standard, the following signal words and definitions are used to indicate hazardous situations:
DANGER indicates an imminently hazardous situation that, if not avoided, will result in death or serious injury.
WARNING indicates a potentially hazardous situation that, if not avoided, could result in death or serious injury.
CAUTION indicates a potentially hazardous situation that, if not avoided, may result in minor or moderate injury.
It is also used to alert against unsafe practices.
GENERAL SAFETY PRECAUTIONS
The following are general safety precautions that are not related to any specific procedures and therefore do not appear
elsewhere in this publication. These are recommended precautions that personnel must understand and apply during
many phases of operation and maintenance.
For fire fighting use only by trained fire fighters.
Do not use the Joystick when the override cranks are being used or are in position for use.
Although the enclosure for the Joystick is water-resistant, it is important to keep water out of the enclosure.
Prolonged exposure to water will cause damage. When the cover of the enclosure is removed, make sure
the seal under the cover is intact and free of dirt and debris.
This product must be wired in adherence with the SAE J1939/11 specification. Failure to do so may result in
sporadic operation or non-operation.
While this device is designed to reside on a standard J1939 CAN network, it is recommended that Akron Brass
CAN products operate on their own CAN network isolated from the other CAN networks on the vehicle.
3

PRODUCT SPECIFICATIONS
6035 CAN JOYSTICK
• Power-8to33voltsDC,<.25amperes
• OperatingTemperature--40°C.to+85°C.
• StorageTemperature--50°C.to+85°C.
• Communications–J1939/11CANNetwork
• ProportionalControl
INSTALLATION INSTRUCTIONS
TOOLS & MATERIALS REQUIRED
• MediumPhillipsscrewdriver•Smallatscrewdriver
• MetricAllenWrenchSet
• DeutschCrimpingTool
• DeutschDTM06-4S-CE13orequivalentandassociatedcrimpterminals
• OptionalAkronBrass721579pre-wiredconnector/harness
MECHANICAL INSTALLATION
The6035CANJoystickcomeswithamountingkitthatallowseithersurfaceorushmounting.The60350023Joystickisanexception,
withonlyaushmountoption.
For a surface mount application, carefully remove the lid of the Joystick by loosening the four screws on each corner of the lid. Drop
one each of the M2.5 X 20 mm cap screws head first into the four holes in the main enclosure body directly under the four small holes
inthelid.Replaceandreattachthelid.UsingtheappropriateAllenwrench,attachtheushmountbezeltotheJoystick.SeeFigure1
for recommended panel cutout.
Foraushmountapplication,threemethodsmaybeutilized.Whenaccesstothebackofthemountingsurfaceis
available, use four M6 screws from behind to directly mount the Joystick to the surface. See Figure 2 for recommend-
ed hole layout.
Asecondushmountmethodutilizestheincludedadapterplate.UsetheincludedM6atheadscrewstoattachtheadapterplate
to the bottom of the Joystick. Next, utilizing four screws of the customer’s choosing, attach the Joystick to the mounting surface. See
Figure 3 for recommended hole layout.
AthirdushmountmethodisachievedbyinsertingfourscrewsthroughthetopofthelidallthewaythroughtheCANJoystickto
threaded holes located underneath in the mounting surface. This method does not apply to the 60350023.
Although the enclosure for the Joystick is water-resistant, it is important to keep water out of the enclosure.
Prolonged exposure to water will cause damage. When the cover of the enclosure is removed, make sure
the seal under the cover is intact and free of dirt and debris.
5

6
Figure 1
Surface Mounting Hole Layout
5.125
5.125
R.563
.290
Ø
.260
TYP(4)
.190
11-23/32
6.451
5.138
1/4
8-5/32
5-1/8
5-1/8
.192
Ø
THRU
.186
TYP(4)
OPTIONAL BOTTOM MOUNTING OPTIONAL FLUSH MOUNTING
RECCOMENDED OPENING
FOR FLUSH MOUNTING
(TO SCALE)
03

Figure 3
Flush Mount Hole Layout
3.230
4.170
Figure 2
Adapter Plate Hole Layout
5.125
5.125
R.563
.290
Ø
.260
TYP(4)
.190
11-23/32
6.451
5.138
1/4
8-5/32
5-1/8
5-1/8
.192
Ø
THRU
.186
TYP(4)
OPTIONAL BOTTOM MOUNTING OPTIONAL FLUSH MOUNTING
RECCOMENDED OPENING
FOR FLUSH MOUNTING
(TO SCALE)
03
7

8
Figure 4
ELECTRICAL INSTALLATION
This product must be wired in adherence with the SAE J1939/11 specification. Failure to do so may result in
sporadic operation or non-operation.
While this device is designed to reside on a standard J1939 CAN network, it is recommended that Akron Brass
CAN products operate on their own CAN network isolated from the other CAN networks on the vehicle.
The following is intended to provide the basic instructions for installation and operation of the 6035 CAN Joystick. Refer to Figure 4,
Figure 5, and Figure 6 for additional information. Wiring must be in compliance with SAE J1939 for proper operation.
Step 1 Connect Battery Positive to Pin #1 (use of Akron Brass Harness stub part number 721579 is recommended)
Step 2 Connect Battery Negative to Pin #2
Step 3 Connect CAN HI to Pin #3 (Akron Brass Harness stub part number 721579 already has this pin properly connected to a J1939
CAN network stub connector)
Step 4 Connect CAN LO to Pin #4 (Akron Brass Harness stub part number 721579 already has this pin properly connected to a J1939
CAN network stub connector)
Step 5 Add a terminating resistor if this device is at the end of the network.
Switch 1
Switch 2
Switch 3
Connector Laber

Figure 5
+V BAT
-V BAT
CAN_H
CAN_L
VMUX_B
VMUX_A
DIGITAL_IN1
DIGITAL_IN2
DIGITAL_IN3
DIGITAL_IN4
DIGITAL_OUT1
DIGITAL_OUT2
6037 CAN-BUS WIRELESS INTERFACE
TO VEHICLE BATTERY (+) (+12V OR +24V)
(OR)
CENTER OFF TOGGLE SW.
TO VEHICLE BATTERY
12AWG.
12AWG.
20AWG.
20AWG.
16AWG.
16AWG.
16AWG.
16AWG.
16AWG.
16AWG.
16AWG.
(PIN GAUGE)
OTHER CAN DEVICES SUCH AS
6036 DIRECTION INDICATOR
TO VEHICLE BATTERY
(OR)
16AWG.
TO VEHICLE BATTERY (+)
TO VEHICLE BATTERY (+)
TO VEHICLE BATTERY (+)
TO VEHICLE BATTERY (+)
NOTES:
CUSTOMER WIRING USES
DEUTSCH #DT06-4S
1) J1939 CAN REQUIRES 120 OHM
TERMINATING RESISTORS AT EACH
END OF NETWORK.
2) SEE DRAWING D-44723
FOR ADDITIONAL INFORMATION
ON "CAN" WIRING.
CAN-L
CAN-H
UNIVERSAL II
TYPICAL SWITCH
CUSTOMER WIRING USES DEUTSCH #DTM06-12SA-E007
1
2
3
4
5
6
7
8
9
10
11
12
J1
2
3
4
5
6
7
8
9
10
11
12
RELAY COIL PILOT LIGHT
NOTE #1 NOTE #1
1
2
3
4
CAN LO
CAN HI
VEHICLE BATT. (-)
VEHICLE BATT. (+)
6035
CAN JOYSTICK
RELAY COIL
PILOT LIGHT
24
23
1
Typical Electrical Connections
9

10
Figure 6
Typical J1939 Wiring
NETWORK LENTGH (TERMINATOR TO TERMINATOR) NOT TO EXCEED 40 METERS
CAN JOYSTICK (6035)
CUSTOMER WIRING USES
DEUTSCH DT06-4S PLUG
DIRECTION INDICATOR (6036)
CUSTOMER WIRING USES
DEUTSCH DT06-4S PLUG
UNIVERSAL II (6032) (CONNECTOR J1)
CUSTOMER WIRING USES
DEUTSCH HDP26-24-29SE
VEHICLE CAN HI
VEHICLE CAN LO
COMMON
SHIELD DRAIN WIRE MAY BE OPTIONALLY
CONNECTED HERE.
IF SO, MUST NOT BE CONNECTED
ELSEWHERE TO
COMMON OR BATTERY NEGATIVE (-)
(SEE J1939/11 SECTION 5.2.4)
12
12
12
D
B
D
B
F
E
G
E
D
B
C
A
G
G
G
TO BATTERY
POSITIVE (+)
MUST NOT EXCEED 1 METER LENTGH
MUST NOT EXCEED 1 METER LENTGH
SUGGESTED PARTS LIST
PLEASE REFER TO SAE J1939/11
**INSTEAD OF TERMINATING RESISTOR,
MAY CONTINUE ON TO REMAINING
VEHICLE CAN NETWORK**
- KEY CODE
- KEY CODE
- KEY CODE
- KEY CODE
- KEY CODE
- KEY CODE
- KEY CODE
TO BATTERY
POSITIVE (+)
E
G
E
F
MUST NOT EXCEED 1 METER LENTGH
- KEY CODE
- KEY CODE C
ITEM MANUFACTURER DESCRIPTION A-B PART NUMBER
ADeutsch IPD HDP26-24-29SE PLUG 707581
BDeutsch IPD DT06-3S-EP11 PLUG w/ W3S-P012 WEDGE LOCK 742204 / 784201
CDeutsch IPD DT06-3S-P006 TERMINATING RESISTOR ASSEMBLY 742205
DDeutsch IPD DT04-3P-P007 "Y" RECEPTACLE 758306
EDeutsch IPD DT06-3S-EP11 PLUG w/ W3S-1939-P012 WEDGE LOCK 742204 / 784200
FDeutsch IPD DT06-4S w/ W4S WEDGE LOCK 707427 / 785025
GChamplain Wire
Raychem
Northwire
Judd Wire
SAEJ1939/1802SHBLK or
2018E0309 or
FJ1939182-005 or
M0702001
GREEN
YELLOW
A
B
C
A
B
C
120 ohm
GREEN
YELLOW
A
B
C
A
B
C
GREEN
B
C
A
B
CA
B
C
A
B
C
A
B
C
A
B
C
120 ohm
1
2
3
4
GREEN
YELLOW
GREEN
YELLOW
23
24
25
23
24
25
12 13
1
2
3
4
A
B
C
A
B
C
A
B
C
A
B
C
A
B
C
A
B
C
A
B
C
A
B
C
YELLOW
A

OPERATING INSTRUCTIONS
NORMAL OPERATION
The 6035 CAN Joystick is Plug and Play, and comes ready to use. Once installed, the CAN Joystick can be used in conjunction with a
Universal II or StreamMaster II control box to operate the monitor/turret.
NOTE: The 6035 CAN Joystick is designed to be as benign as possible on a typical J1939 network. It performs standard address
claiming. It issues standard J1939 Joystick messages. The CAN Joystick’s default mode is Joystick 3. It is possible to change
this in the field by using the setup mode. It is possible to have multiple Universal II’s and CAN Joysticks on the same
network.ContactAkronBrasscustomersupportforcustomsoftwareifthisisarequirement.
For fire fighting use only by trained fire fighters.
Do not use the Joystick when the override cranks are being used or are in position for use.
The 6035 family of CAN Joysticks have various groups of functions. The paragraphs below detail those functions. Refer to the 6032
Universal II manual or StreamMaster II manual for additional information.
STOW / DEPLOY
The Stow/Deploy switch is used to move the monitor/turret in and out of its stow position for transit. (Refer to the Universal II manu-
al or StreamMaster II manual for teaching the Stow/Deploy positions) Pushing and holding the Stow/Deploy toggle switch forward for
atleasttwosecondswillinitiateadeploysequenceplacingthemonitor/turretinpositionfornormaloperation.Pullingandholding
theStow/Deploytoggleswitchbackwardforatleasttwosecondswillinitiateastowsequenceplacingthemonitor/turretinposition
for transit.
OSCILLATION
The Oscillation (Start/Set)/(Pause/Resume) switch is used to teach and control a horizontal oscillation pattern. Pushing the
Oscillation toggle switch forward, the monitor/turret rotation will be driven toward the right until either: the switch is released, a
soft-limit is encountered, or a hard-limit is encountered. That point will be assigned the rightmost travel point in the auto-oscillate
profile. The monitor/turret will again automatically reverse direction and move to the left until the “Set/Start” switch is pushed and
released, a soft-limit is encountered, or a hard-limit is encountered. That point will be assigned the leftmost travel point in the
auto-oscillate profile. The monitor/turret will then automatically oscillate back and forth between those two points until either: the
Oscillation switch is pulled backward to the “Pause/Resume” position, a Left or Right command is received from a switch or joystick
input, or some other disabling function is encountered. Pulling the Oscillation switch backward to the “Pause/Resume” position will
only pause oscillation, and pulling the Oscillation switch backward to the “Pause/Resume” position switch a second time will cause
oscillation to be resumed using the taught positions. Use of a Left or Right command will cancel oscillation and the profile will be
cleared. The monitor can be moved up and down during oscillation without cancelling the oscillation function.
FLOW HIGH / LOW
TheFlowHigh/Lowswitchisusedtocontrolowonadualgallonagemonitor/turret.Pushingtheswitchforwardtothe“High”
positionwillplacethemonitor/turretinhighowmode.PullingtheFlowswitchbackwardtothe“Low”positionwillplacethe
monitor/turretinthelowowmode.
DRY CHEM
The Dry Chem switch is used to control an associated auxiliary output such as is available on the Universal II controller or CAN I-O
module. See the Universal II controller manual for additional information.
Joystick Operation
The joystick is proportional in the X and Y axis. Pushing the joystick forward will lower the monitor/turret nozzle. The farther forward
the joystick is pushed, the faster will be the motion. Pulling the joystick back will raise the monitor/turret nozzle. Moving the joystick
to the right will rotate the monitor/turret to the right. Moving the joystick to the left will rotate the monitor/turret to the left.
11

12
Discharge Control
The “trigger” switch is used to open and close the water/foam discharge valve. (This assumes the discharge valve has been wired to
theappropriateoutputontheUniversalII)Squeezingthetriggerswitchwillopenthevalve,andreleasingthetriggerswitchwillclose
the valve. The valve may be placed in a continuously open condition by “double-clicking” the trigger switch. The next activation of the
trigger switch will return it to normal momentary operation.
Stream Pattern Control
On top of the joystick is a thumb switch used to control the pattern sleeve of the nozzle. Moving the thumb switch to the right
will move the pattern sleeve towards the straight stream position. Moving the thumb switch to the left will move the pattern sleeve
towards the fog position. In both cases, the pattern sleeve will stop when the thumb switch returns to center position, or the pattern
sleeve reaches the full extent of its travel. This permits a continuously adjustable discharge pattern.
For the 6035 ARFF Joystick, pattern control is accomplished using the two yellow buttons. The left button will move the nozzle toward
the fog pattern and the one on the right will move the nozzle toward the stream pattern when pressed.
SETUP AND CALIBRATION
Changes to the behavior of the joystick can be achieved by entering the setup mode. This can be done in the field with a small
magnet. Three small dots located on the connector label (see Figure 4) identify the location of Hall Eect switches inside the joystick.
Zeroing and Spanning the Joystick
PlaceamagnetovertheSwitch1dotforapproximatelyonesecond(seeFigure4).AllthreeLEDswillbeginashingtheprioritylevel
(thedefaultwillbethreeashes).MomentarilyplacethemagnetoverSwitch3.TheGreenLEDwillbeginashingbyitselfsignaling
the joystick has entered calibration mode. Allow the joystick to return to the centered position (at rest). Momentarily place the mag-
netoverSwitch3.TheYellowLEDwillbeginashingbyitselfsignalingthejoystickhasbeenzeroed.Movethejoysticktoanyoneof
itsfourcorners(maximumXandYdeection).Whileholdingthejoystickatitsmaximum,momentarilyplaceamagnetoverSwitch3.
Atthispoint,allthreeLEDswillbeginashingtheprioritylevelsignalingthejoystickhasbeenspanned.
Either cycling power or momentarily placing a magnet over Switch 2 will reset the joystick and return it to normal operation.
Changing the Priority Level
The SAE J1939/71 specification has made provisions for up to six joysticks residing on the same CAN bus (Joystick1 through Joystick6).
Akron Brass has chosen to interpret this assignment as the priority level. Joystick1 has the highest priority, and Joystick6 has the lowest
priority. A device at Joystick3 issuing “go right” messages would override a device at Joystick5 issuing “go left” messages. Akron Brass
has set the default for the 6041 CAN Switch Box at Joystick1, the 6035 CAN Joystick at Joystick3, and the 6037 CAN Wireless Interface
atJoystick5.Customersmayrequireadierentpriorityscheme.Thefollowingstepsalloweldchangingofprioritylevel.
PlaceamagnetovertheSwitch1dotforapproximatelyonesecond(seeFigure4).AllthreeLEDswillbeginashingthecurrentpriority
level(thedefaultwillbethreeashes).MomentarilyplacingamagnetoverSwitch1againwillincreasetheJoysticknumber(decrease
the priority) by one. Continue with momentarily placing a magnet over Switch 1 until the desired priority level has been reached.
When Joystick6 has been reached, another Switch 1 activation will wrap around to Joystick1. When the desired priority level has been
reached, momentarily place a magnet over Switch 2 to save the setting and the Joystick will reset and return to normal operation.
NOTE: There cannot be two devices with the same priority level. If two devices are assigned the same priority level, only one will
remain active on the network. The remaining device will become inactive and claim CAN node address 254 as defined and
specified by SAE J1939.

WARRANTY AND DISCLAIMER: We warrant Akron Brass products for a period of five (5) years after purchase against defects in materials or workmanship. Akron Brass will repair or replace product
which fails to satisfy this warranty. Repair or replacement shall be at the discretion of Akron Brass. Products must be promptly returned to Akron Brass for warranty service.
We will not be responsible for: wear and tear; any improper installation, use, maintenance or storage; negligence of the owner or user; repair or modification after delivery; damage; failure to follow
our instructions or recommendations; or anything else beyond our control. WE MAKE NO WARRANTIES, EXPRESS OR IMPLIED, OTHER THAN THOSE INCLUDED IN THIS WARRANTY STATEMENT,
AND WE DISCLAIM ANY IMPLIED WARRANTY OF MERCHANTABILITY OR FITNESS FOR ANY PARTICULAR PURPOSE. Further, we will not be responsible for any consequential, incidental or
indirect damages (including, but not limited to, any loss of profits) from any cause whatsoever. No person has authority to change this warranty.
PHONE: 330.264.5678 or 800.228.1161 I FAX: 330.264.2944 or 800.531.7335 I akronbrass.com
ISO 9001 REGISTERED COMPANY
© Akron Brass Company. 2012 All rights reserved. No portion of this can be reproduced without the express written consent of Akron Brass Company.
REVISED: 5/16
MAINTENANCE INSTRUCTIONS
The 6035 CAN Joystick has no user serviceable parts. If the device fails to operate properly, please contact an Akron Brass customer
service representative.
TROUBLESHOOTING
DIAGNOSTIC LEDs
The CAN Joystick has three LEDs located near the connector labeled Ready, Receive, and Transmit. Their colors are Green, Yellow,
and Red respectively. Under normal operation, the Green Ready LED indicates the unit is powered and that the unit’s microprocessor
is running. The Yellow LED will blink on and o when there are CAN messages sent by other devices on the network that pertain to
the Joystick. The Red LED will light when the joystick is sending CAN messages that contain non-centered joystick positions or other
switchoperations.Whenthejoystickreturnstoaquiescentstate,theRedLEDwillturno.
Make sure that no two CAN operator devices (Joystick, Wireless, or Switch Box) have identical priority settings, otherwise one of
them will become inactive.
AKROVIEW SOFTWARE
As with all of the Akron Brass CAN product family, the 6035 CAN Joystick supports the Akroview Software. The software provides
additional diagnostics as well as software updating and other capabilities. Contact Akron Brass for additional information on how
you can obtain a copy of Akroview software.
Table of contents