Calyenty RBH 125 Reference guide

1
Calyenty
Swimming Pool Heat Pumps
Customer Manual, RBH125 SUPER, RBH185 SUPER
Thank you for choosing a Calyenty Heat pump.
Contents
1. Quick reference: 2.
1.1 Controller screen: 2.
1.2 Circulation/filtration pump timer/clock: .
2. Installation: 4.
2.1 Materials to required to install your Calyenty heat pump, you will need: 4.
2.2 Tools: 4.
2. Where to put the heat pump in the hydraulic system: 5.
2.4 Multiple heat pump installations: 6.
2.5 Installation Procedure: 7.
2.6 Connecting to the electricity supply: 9.
. Initial Startup: 11
4. Usage: 12.
4.1 Control panel: 12.
4.2 Start up procedure: 12.
5. Backwashing the pool/sand filter: 1 .
6. Maintenance and Troubleshooting: 1 .
6.1 Maintenance: 1 .
6.2 Troubleshooting: 14.
7. Error codes and what to do: 15.
8. Defrosting: 17.
9. Model Data: 18.
10. Exterior Features: 19.
11. Interior Features: 20.
12. General Information: 21.
12.1 Features: 22.
12.2 Notes 21.
12. Energy Saving Tips: 22.
1 . Mounting the Temperature sensor: 2 .
14. Warranty: 25.

2
Warranty information.
Please note your warranty may be invalidated if you do not properly maintain the water
in your pool and all ancillary pool equipment, see the full warranty at the base of this
document. Also your warranty will be invalidated if the heat pump is not installed
following the procedures in THIS manual exactly.
Calyenty continue to explore constant improvements in our products and consequently
can be modified without notice; the present pictures in this note or the characteristics
which are described are not contractual.
This manual includes the information about specifications, installation, debugging,
operation and maintenance. Please read this manual carefully before you install, start,
repair or service the unit. Professional technicians must carry out the installation of the
unit. The manufacturer shall not be held legally responsible for any damage of the unit
or physical injury or death caused by improper installation, debugging, operation,
maintenance or disregarding the manual.
1.Qui k Referen e
1.1 Controller s reen
Under normal operating conditions your LED screen should appear as below
(temperatures may vary.)
This controller has various timer functions that you will not need. You can set the date
and time, apart from this, all you need to set is your desired temperature with the arrow
buttons.

3
1.2 Cir ulation/filtration pump timer/ lo k
Setting the Time Clock (Guidelines only):
Time clock above illustrates auto mode with 12 daytime hours (between 9.00am and
9.00pm), n.b if the top slider switch is in the I position the filter pump will run
continuously, and in O will be off. There are many types and makes of timer; however
they all have this basic functionality. It is far better if you have or get fitted a timer with
a memory so that the settings do not shift after power interruptions.
It is recommended that for optimum filtration of an 8m x 4m or 10m x 5m pool with a
0.75 - 1.2 kW circulation/filter pump, the pump runs for 6 - 8 hours a day during the day,
i.e. from 10.00am until 6.00pm. This coincides with the optimum time settings for the
running of the heat pump too. As the ambient air temperature drops into the colder
months you may find that you need to increase the time that the circulation/filter pump
runs up to twelve hours to maintain the pool water temperature that you require.
Please note that in colder climates you may find that it becomes uneconomical to
maintain a high pool water temperature during the colder months, or that the
temperature loss is greater than the temperature gain provided by the heat pump. In
such cases you may decide that it is prudent to cease using your heater. Remember
during months where the outside ambient temperature drops to zero you must use the
by-pass and drain down your heat pump.

4
2. Installation.
Materials. To Install your Calyenty heat pump, you will need:
• x 50mm ball valves for the bye-pass.
• 2 x 50 mm pressure 90°elbow fittings.
• 2 x 50 mm pressure T fittings.
• Adequate 50mm pressure tubing (rigid or flexible).
• uPVC solvent and cement.
• Adequate 2.5mm x core flexible electrical cable.
You may find that you need some more pressure fittings or 45°elbows depending on
where you position the heat pump in relation to your existing installation.
2.2 Tools:
Tape measure, hacksaw, Philips screwdriver, Drill + m8 masonry bit, strap wrench.
Do not over tighten any water fittings; hand tight should be sufficient to ensure a good
watertight seal.

5
2.3 Where to put the heat pump in the hydrauli system:
The unit is generally installed outdoors (for indoor installation, please consult Calyenty).
Install the unit downstream of all pumps and filters and upstream of all chlorinators,
ozonizers and chemical pumps.
2.4 Multiple heat pump installations:

6
Where more than one heat pump is to be installed it is essential that they are connected
to the water system in parallel, see diagram below:
2.5 Installation Pro edure:

7
1. This unit should be installed by a competent person.
2. All electrical work should be carried out by a qualified electrician / lampista.
. Check packaging for obvious signs of damage, before installation begins. Report
any damage to Calyenty before installation if you have concerns.
4. Please read the Installation & Operation Manuals carefully before you install or
operate the unit.
5. The company will not be responsible should someone be injured in the event of
the proper installation procedures have not having been adhered to.
6. Choose a suitable location for your heat pump. Remember this must satisfy your
aesthetic requirements, should be close to the filter pump, be on flat ground
(unless positioned on a custom bracket), be in a sunny position if possible and
comply with the space requirements as illustrated:
The unit needs continuous fresh air while running. Please leave enough space around
the unit for unobstructed air absorption and discharging. Don't keep the unit in an
enclosed area, or the discharged cold air will circulate in the unit again and
consequently lower the heating efficiency.
7. Lift the heat pump into place onto the base.

8
8. The water is fed through the heat pump using the circulation/filter pump. You
will need to identify the return pipe from the filter to the pool (this is often
marked RETURN). You will now need to cut into this return plumbing / pipe work
of the pool system. Before you make this cut, make sure that if there are shut off
valves/taps in this pipe-work, and that they are in the closed position. USEFUL
TIP: If there are not any taps, it is possible to do this work without draining the
pool by inserting wine bottle corks into the return jets. IMPORTANT – Make sure
that the connection from the filter goes to the pipe connector on the heat pump
marked WATER INLET. Connect the pipe connector on the heat pump marked
WATER OUTLET to the return pipe that continues to the pool jets. See diagram
on page below to ensure that the pipe work is connected correctly as shown.
When making uPVC connections, it is very important that the surfaces of both
the pipe and the fitting are clean and dry. It is also very important to thoroughly
wipe the surfaces with the solvent cleaner, as this starts the chemical reaction to
ensure a good bond when the adhesive is applied. Make sure that the adhesive
covers 100% of both surfaces that are to come in contact with each other.
9. Connect the supplied control panel to the snap connecters to complete the
installation. The control panel must be mounted in a convenient dry place,
preferably inside, under a terrace roof is OK provided the controller is out of
direct sunlight.
10. We recommend that the heat pump is fitted within 8 meters (25 feet) of the
existing circulation pump for maximum performance. This is not critical but could
slightly reduce the efficiency of the unit if positioned further than this distance.
11. If the water in the heat pump is allowed to freeze it will damage the unit. It is
essential for the guarantee to remain valid to drain the heat pump during
months where the outside ambient air temperature can drop to 0°C. Simply
close the ball valve / shutoffs and open the bye-pass. Drain the unit by removing
the lower most water connector.
12. Please make sure that minimum water flow speed is m³/h.
1 . While the unit is running, water in the air may condense on the fins of the
evaporator. If the air humidity is very high, the condensation water within an
hour can be several gallons.

9
2.6 Conne ting to the ele tri ity supply:
IMPORTANT: Power supply to the filter pump, and the heat pump, and the switching on
and off of both devices must be the same and simultaneous. Using the electrical entry
marked “Power Supply” connect the heat pump to the dead side of the filter pump
timer clock electricity supply. Please ensure this is carried out be a qualified Electrician
or Lampista. It is important to give the heat pump power supply its own RCD circuit
breaker. N.B. Please check that when the power to the filter pump is cut or times out
from the timer, the power to the heat pump is also cut and the back lit LCD controller
switches off.
Make sure no power is supplied to the unit while connecting.
Always comply with the national and local electrical codes and standards.
In case any emergency occurs, the unit must be equipped with a breaker, which is
located within sight and accessible from the unit.
The unit must be well earthed.
Several screws fix the electrical component front panel cover to the cabinet. Unscrew
and remove the front panel to connect the power cable to the terminal marked POWER.
You can ignore the terminal marked PUMP. Also plug in the control panel cable. When
the connections have been made, replace this front panel very carefully. Make sure that
it is fixed firmly by the screws. It is vital that the PCB/terminal cover is replaced properly,
make sure that the edges of the cover are underneath the corresponding edges of the
heat pump body and the water tight seal is snug between the surfaces.
Mains connection
It is recommended that a qualified technician connects your heat pump to the mains.
2.5mm cable must be present in the pool house connected to a 25amp circuit breaker in
the house main fuse box provided that the run is no more than 25m. Any greater
distance you must run a new cable of at least 4.0mm.

10

11
3. Initial Startup
IMPORTANT: Make sure the by-pass is open and allowing sufficient flow of water to and
through the heat pump before switching power on
Notice: the unit will not heat the pool when the water circulation pump is not working.
The back lit controller screen will be blank.
3.1 Starting Steps:
Check whether the connectors, wires and cables of the unit, water pump, chlorinator,
ozonizer, chemical pumps and control panel are correctly coupled or connected.
Turn on the water pump and filter. Check for water leakage and verify the water flow.
Turn on the power of the unit. Then press the button ON/OFF on the control panel. All
Calyenty heat pumps have a variable start delay which can be from just a few seconds to
several minutes. This feature reduces load on your power supply which irrespective of
the electrical consuming device is always significantly more on start up. This feature
cuts down on power overload, ensuring the circulation pump and heat pump, or
multiple heat pumps never start at the same time.
After the unit runs for a few minutes, check whether the air discharged from the fan is
cooler than the ambient air as it should be.
Turn the water pump off while the unit is running. The unit should stop working
automatically. Turn on the unit again, set the temperature on the control panel and
keep the whole pool system running. The unit will stop running automatically as the
pool water reaches the set temperature. When the temperature drops to 1degree lower
than the set temperature, the unit will restart automatically.

12
4. Using your heat pump:
1. On/off Button
Press On/Off button to switch on/off the unit.
2. Set Button
This is where you can change various parameters. On commissioning, press this
button for five seconds to enter parameter change mode, after five seconds you
will see parameter P0 – make sure this is set at 0 (if different you can change the
value with the up/down button). Press the set button once more to P1 and
make sure this value is set at 0.
3. Timer Button
To set the lo k
Press Timer Button for five seconds to enter clock set mode.
Press timer button once to set HOUR by pressing up/down arrow n.b it is a 24
hour clock.
Press timer button again to set MINUTES.
There is a timer built into this ontroller that is now obsolete
It is very important that the timer is set as follows:
Press timer button once quickly to enter timer mode.
Use the arrow buttons to set “on” time to 1 .00 hours.
Use the arrow buttons to set the “off” time also to 1 .00 hours.
4. Up Button
Press Up Button to set temperatures or time upwards.
5. Down Button
Press Down Button to set temperatures or time downwards.
6. Temp Button
Press Temp Button to check Evaporator Coil Temperature and Ambient Air
Temperature.
7. Mode Button
Press Mode button to select the activation or inactivation of backup electricity
heating function (where fitted ).

13
5. Ba kwashing the pool/sand filter:
While the filter pump is running and the heat pump is switched on switch the heat
pump off by pressing the on/off button on the heat pump control panel. Switch the
filter pump off, close all taps to and from the pool so that you can remove and clean the
filter basket of leaves and any large debris. Replace the filter basket and replace the
cover and seal, re-open the taps that are normally open from the pool under normal
filtration conditions (skimmers and drain/fondo) and leave closed any return taps to the
pool and set the multi port selector valve to the position marked backwash. Check that
if there is a tap on the drain that this is open during backwashing. Switch the filter pump
on and leave running for approximately two minutes or until the water in the sight glass
is running clean. Switch the filter pump off and move the multi-port selector to the
position marked rinse. Switch the filter pump back on and rinse for a suitable period,
usually around a minute. Switch off the filter pump and re-open the taps back to the
pool return. Change the multi-port selector back to its normal filter position. Switch the
filter pump back on so that the pool is filtering normally. Check that the flow into the
pool via the return jets is its usual strength. Switch the heat pump back on with the red
on off button on the heat pump control panel.
6. Maintenan e and Troubleshooting
6.1 Maintenan e
General maintenan e:
The unit should be maintained by qualified technicians on a regular basis. Ask Calyenty
or your local dealer about our maintenance contract options.
A professional technician should clean the unit periodically. It is NOT recommended to
use a sprinkler to flush the unit.
The unit is designed to withstand normal rainfall. A flow of water into the inside of the
unit may damage the components (place unit away from garden sprinklers & watering
systems). If the unit is located under the eaves, ensure water does not flow directly onto
the unit.
• Clean the drain hose.
• Ensure a proper water flow:
• Keep the filter clean. The filter may get dirty along with use. A dirty filter can
reduce the water flow.

14
• Keep the pump clean.
• Check the valves often
6.2 Troubleshooting
The unit would not run.
Is the screen of control panel lit? If not, ensure the electrical wires and cables are
correctly connected and the power is on.
If the screen displays E5, check the water flow. Whether the water pump is running
normally or the filter is jammed?
The unit will stop running automatically when the pool water reaches the set
temperature.
The unit is running but not heating.
Is the air discharged from the fan cooler than the ambient temperature? If not, ask a
professional technician to check the refrigerant system.
Be sure the space around the unit is broad enough. There should not be obstruction of
air.
Environment problem
Under certain external conditions the heat exchanges between the refrigerant and the
water on one hand and between the fluid and the air on the other hand are insufficient;
the consequence is that the refrigerating circuit runs up in pressure and the compressor
consumes more electricity.
The temperature sensors compressor outlet and the magnetic circuit breaker on the
compressor power supply protect the compressor from these extreme conditions.
The condition causing this situation is as follows:
In heating mode:
- Insufficient water flow:
close the by-pass valve for increasing the refrigerant exchange water
In cooling mode:
- Too important water flow: open the by pass valve for decreasing the water flow and so
the exchange water refrigerant
- Insufficient air flow: be sure that the real net of condenser is not blocked.

15
Note: these error codes are likely to occur if temperature of swimming pool water is
high and the ambient air is hot.
7. Error codes and what to do:
Troubleshooting
Guide
Problem
Possible
Reason
Solution
1) The water pump is too small. The insufficient
water
flow results in gas discharge temperature
protection.
Change to bigger water
pump
2) The water pump is installed in the wrong direction
or he three phase water pump is running in the
opposite
direction.
Put the water pump in the right
direction
and put the phase wires of the water
pump in the right
sequence.
3) ir exists in the water
pump.
Discharge the
air
4) The water filter on the inlet water pipe is
blocked.
Clean the filter or replace
it
5) The pipe diameter is too small or there is
a
bottleneck
restriction.
Change to pipe to the correct
size
6) The gas discharge thermo switch is
damaged.
Replace
it
7) The gas discharge thermo switch has a
poor
contact to the
mainboard.
Improve the
contact
8) The mainboard is
damaged.
Replace
it
Error code E5
(Single
compressor
system);Error
code
E7,E9 (
Dual
compressor
system)
9) Insufficient refrigerant in the
system.
Check where the leakage is and
fill
refrigerant
1) The water pump is not running, hence the
water
flow switch circuit is not
closed.
Replace it if
damaged
2) There is no water in the pipe, hence the water
flow
circuit is not
closed.
Check if there is water in the water
tank
3) The blade in the water flow switch seizes
up.
Replace the switch or the
wire
4) The wires of water flow switch has a poor contact
to the
mainboard.
Improve the
contact
Error code
E4
( Single
compressor
system); Error code
E6 ( dual
compressor
system)
5) Mains power cord is incorrectly connected to
terminals 1 and 2, resulting in a damaged
mainboard.
Replace the
mainboard
1) Defrost cut-in temperature is set
incorrectly.
S
e
t
the
de
f
r
ost
cut
-
i
n
tempera
t
u
r
e
a
s
factory default "-2℃" ( For
single
compressor system the evaporator
coil
temperature is observable from
the
p
a
nel)
2) The evaporator coil temperature sensor is placed
in the wrong
position.
Place the sensor on the second
lowest
row of coil on the
evaporator
3) The Ohm value of the evaporator coil
temperature
sensor changes abnormally; the sensor is
damaged.
Replace the
sensor
Ice builds up on
the
evaporator but
the
system
cannot
defrost it
properly.
4) The defrost check valve or the defrost capillary
is
blocked.
Replace check valve or
capillary
1) The heat pump is
undersized.
Size the correct
model
2) Water tank is poorly
insulated.
Insulate the water tank
properly
3) Water pipes are poorly
insulated.
Insulate the water pipe
properly
Water
temperature
rises too
slowly
4) Mains water supply is
unreasonable.
Redesign the mains water
supply

16
5)
Th
e
sp
ace
b
e
tw
e
e
n
i
n
l
et
w
a
t
er
p
i
p
e
an
d
o
u
t
l
e
t
water pipe is too narrow, resulting in
water
sho
r
tcirc
u
it.
The space between inlet and outlet
wate
r
pipes should be no less than
1m
6) The heat pump is installed in a place where
the
ventilation is not
good.
Improve the
ventilation
7) Insufficient refrigerant inside the
system.
Check where the leakage is and
fill
refrigerant
1) The phase sequence board in the electrical
box
activates fault-phase or lack-phase
protection
Check if there is a lack-phase and
put
the phase wire in the right
position
Single
compressor
System: water
pump
and fan motor
is
running, but
the
compressor does
not
start; Dual
comp
ressor
system:
Fan motor
is
running,
but
the
compressor
and
water
pump do
not
start.
2) Phase sequence board is
damaged
Replace the phase sequence
board
1) No power
input
Plug in the power
cord
2) Power voltage is not
correct
Start the heat pump under the
right
voltage
3) Power voltage drops when the unit is started.
The
unit draws a huge
current.
Low power capacity in the
network;
Wires in wrong (too small)
diameter
are
used.
4) Fault-phase or lack-phase problem with the
mains
power
supply.
Put the phase wires in the right
position
5) Poor contact problem with the wiring in
the
system.
Improve the
contact
6) The heat pump is in clock timer shutdown
state.
Check the clock timer settings. Reset
or
cancel
it.
7) The system is in
protection.
Check what kind of protection it is
and
remedy
it.
Heat pump does
not
start
properly
8) Damaged mainboard or damaged
temperature
sensor.
Replace the mainboard or
sensor

17
8 Defrost Control
Defrost Cut-in Conditions: only when the following two onditions are satisfied:
1.Compressor continuous running time ≥ Defrost Cut-in Time (P2)
2. Evaporator Coil Temperature ≤ Defrost Cut-in Temperature (P )
When the unit enters defrosting mode, the 4-way reversing valve will de-
energize, directing the hot gas to the evaporator coil. The fan motor will
stop but the compressor and pump will continue working.
Defrost Cut-out Conditions: when either of the following onditions are
satisfied:
a. Evaporator Coil Temperature ≥ Defrost Cut-out Temperature (P5)
b. Defrosting time ≥ Defrost Cut-out Time (P4)
When the unit reverts to heating from defrosting mode, the 4-way
reversing valve will energize and the fan motor will begin to work.
For ed Defrost:
When the unit is in standby state, hold Arrow Down button for five seconds
will lead to forced defrost function.
After any Defrosting the unit will exit defrost state.

18
9. Model Data:

19
10. Exterior Features.

20
11. Interior Features.
Other manuals for RBH 125
1
This manual suits for next models
1
Table of contents
Other Calyenty Heat Pump manuals
Popular Heat Pump manuals by other brands
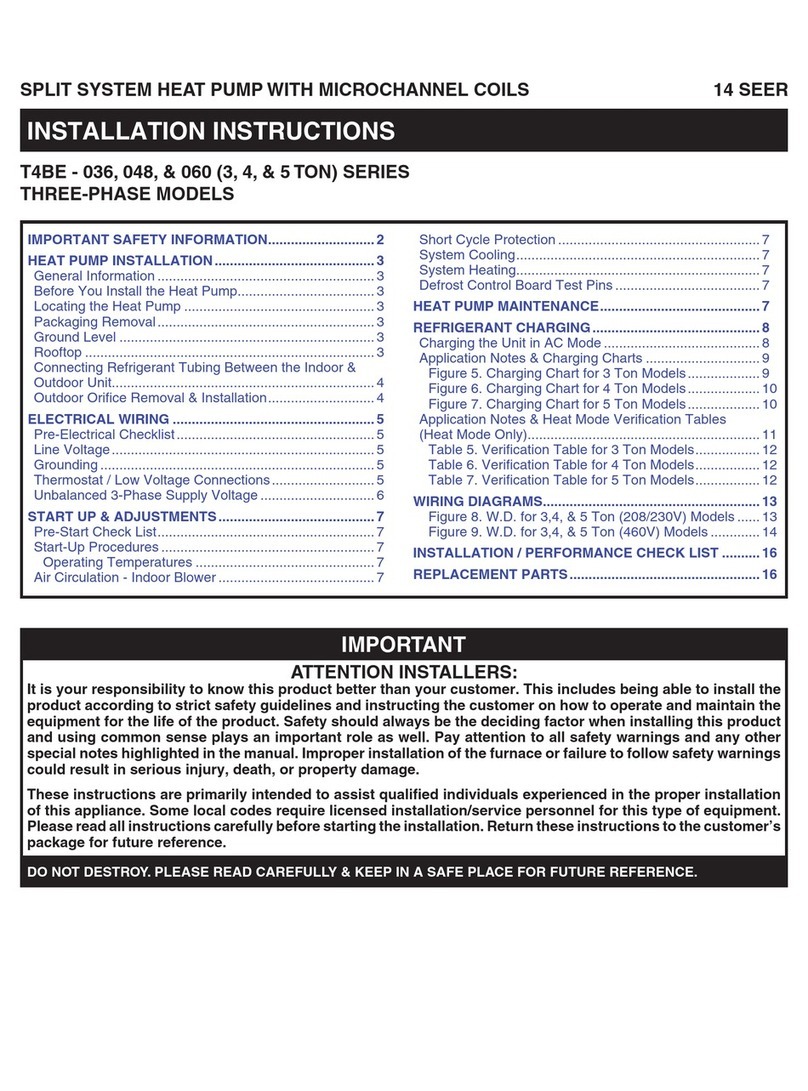
Nortek
Nortek T4BE 036 Series installation instructions
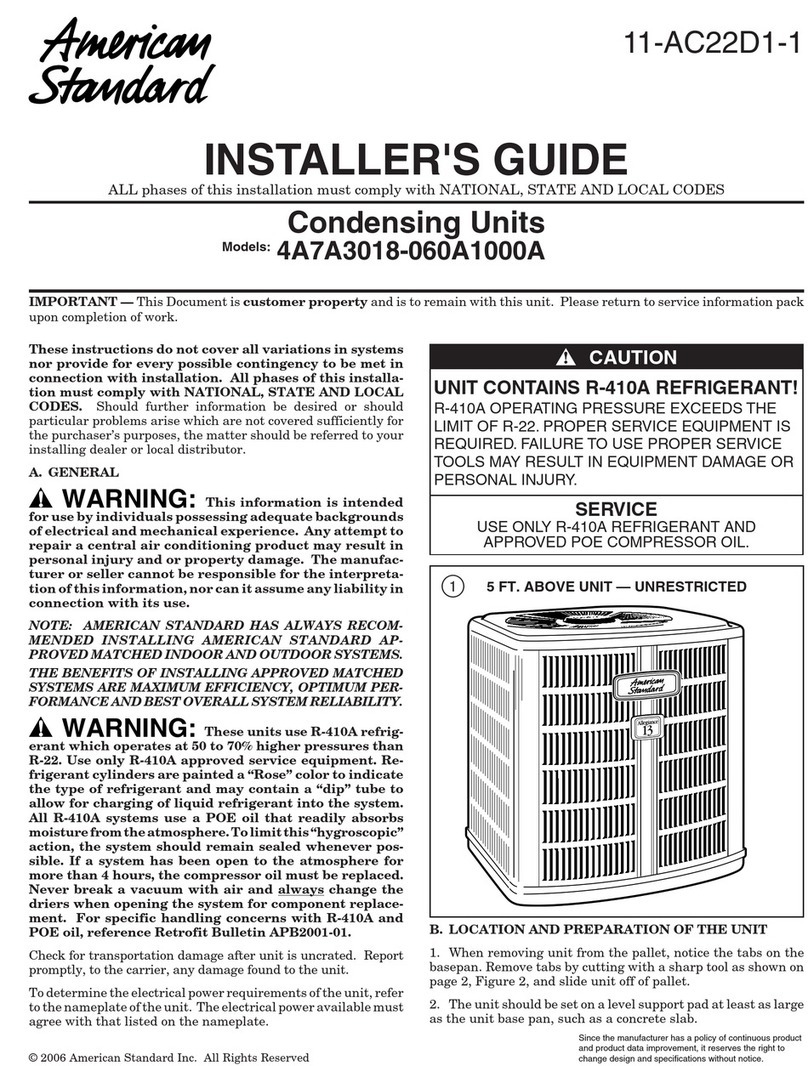
American Standard
American Standard 4A7A3018-060A1000A Installer's guide

LG
LG ARWN038GA2 Service manual

Ingersoll-Rand
Ingersoll-Rand 4WCC4024A1000A Installer's guide

PoolFact Industries
PoolFact Industries Perfectemp owner's manual

Orca
Orca WSW COMPOSITE Installation and user manual