CAMERA LINK Q-2A340 User manual

Operating and user manual
QUARTZ SERIES
CAMERA LINK MODELS

OPERATING AND USER MANUAL QUARTZ SERIES
2

OPERATING AND USER MANUAL QUARTZ SERIES
3
About Adimec
Adimec is the leading supplier of high-performance digital camera modules and camera-lens
assemblies for use in three market segments: machine vision, medical imaging, and applications for
government purposes such as traffic and defense systems. In developing our products as a partner
to major OEMs around the world, we utilize the synergy between these segments to shine in terms of
image quality, speed, dynamic range and reliability.
Adimec is the only company in the market that weds the specific needs of its highly demanding
customers to its technological inventiveness, generating vision solutions of exceptional quality. These
industry-leading customer specials are the models for our standard products.
Thanks to this unique approach, Adimec’s solutions add crucial competitive value to our customers’
high-end systems and their applications, as they yield brilliant results to the users of those systems.
The Netherlands-based holding company has business offices in Europe, the United States, Japan,
and Singapore. For more detailed information about Adimec and our products you can visit our
website www.adimec.com or you can contact your local dealer or the business offices in your region:
Adimec Advanced Image Systems B.V.•
PO Box 7909
5605 SH Eindhoven
The Netherlands
Phone: +31 (40) 2353 920
Fax: +31 (40) 2353 905
E-mail: [email protected]
Adimec Japan•
2-10-3-103, Narimasu, Itabashi-Ku
175-0094 Tokyo, Japan
Phone: +81 (3) 5968 8377
Fax: +81 (3) 5968 8388
E-mail: [email protected]
Adimec Electronic Imaging Inc.•
PO Box 80529
Stoneham, MA 02180,
USA
Phone: +1 (781) 279 0770
Fax: +1 (781) 279 0571
E-mail: [email protected]
Adimec Asia/Pacific•
190 Middle Road, #17-06 Fortune Centre
Singapore 188979
Phone: +65 6334 1236
Fax: +65 6334 1436
E-mail: [email protected]

OPERATING AND USER MANUAL QUARTZ series
4
Contents
1. GENERAL INTRODUCTION 7
1.1 Product Highlights 7
1.2 About this manual 7
1.3 Standards 7
2. PRECAUTIONS 9
2.1 Safety precautions 9
2.2 Handling 9
3. INSTALLATION HARDWARE 13
3.1 Electrical interface - CoaXPress 13
3.2 Electrical interface - strobe and trigger 13
3.3 LED indicators 15
3.4 Quick start 15
4. FUNCTIONAL DESCRIPTION 17
4.1 Block diagram 17
5. CONTROL OF THE CAMERA 19
5.1 Introduction CoaXPress and GenICam 19
5.2 Structure of camera control 20
6. CAMERA IDENTIFICATION AND CONTROL 23
6.1 Interface settings (ICategory: BootstrapCoaXPress) 23
6.2 ICategory: DeviceControl 24
6.3 ICategory: ImageFormatControl 25
6.4 Image acquisition (Icategory: AcquisitionControl) 28
6.5 Flashstrobe Commands (Icategory: CounterAndTimerControl) 35
6.6 Gain and black level (Icategory: AnalogControl) 36
6.7 Output remap (Icategory: LUTControl) 36
6.8 User set (ICategory: UserSetControl) 37
6.9 Built In Test (ICategory: Adimec) 37
6.10 Defect pixel correction (ICategory: DefectPixel) 38
6.11 Flat Field calibrations and corrections (ICategory: Calibration) 39
6.12 Buffer commands (Icategory: BurstMode) 45
6.13 High Dynamic Range mode (ICaterogy: Multislope) 46

OPERATING AND USER MANUAL QUARTZ SERIES
6

OPERATING AND USER MANUAL QUARTZ SERIES
7
General introduction1.
The Quartz CMOS cameras described in this manual provide a range of resolutions at the highest
possible speed. All have in common a global shutter operation, CCD like image quality and reliability.
Unlike competitors who are offering general purpose cameras, our products are developed with the
specific needs of OEMs and their applications in mind.
Product Highlights1.1
The Quartz cameras offer the following features:
High quality images on account of sophisticated internal processing•
Full a-synchronous image capture•
Lowest noise attainable to global shutter CMOS sensor•
Programmable interface speed•
Programmable region of interest•
Full Camera Link interface•
Q-2A340 Q-4A150 Q-4A180 Q-12A65
Max resolution 2048 x 1088 2048 x 2048 2048 x 2048 4096 x 3072
Max sustained speed
at full resolution
340 fps
(2000 x 1088
CL 10 tap)
156 fps
(2048 x 2048
CL 8 tap)
180 fps
(2000 x 2048
CL 10 tap)
65 fps
(4080 x 3072
CL 10 tap)
Max burst speed at
full resolution
340 fps
(2000 x 1088
CL 10 tap)
180 fps
(2000 x 2048
CL 10 tap)
180 fps
(2000 x 2048
CL 10 tap)
75 fps
(4080 x 3072
CL 10 tap)
About this manual1.2
This manual provides the necessary information for setting up, operating and troubleshooting the
camera.
We strongly recommend reading this manual before you unpack or operate the camera.
The manual is applicable to the following Quartz models, color as well as monochrome, with Camera
Link interface:
Q-2A340•
Q-4A150•
Q-4A180•
Q-12A65•
Unless stated differently, all information in this manual is applicable to all camera versions.
In this manual we use the following standard symbols in the left margin to draw your attention:
Command syntax
Return message
NOTE Practical tip or note
Standards1.3
Camera Link – Specification of Camera Link Interface Standard for Digital Cameras and Frame
Grabbers – Version 2.0 - Februari 2012.

OPERATING AND USER MANUAL QUARTZ SERIES
8
Liability1.4
Adimec puts in a lot of effort in preparing this manual. Please inform your Adimec Business Office of
any inaccuracies or omissions. Adimec Advanced Image Systems B.V. cannot be held responsible
for any technical or typographical errors and reserves the right to make changes to the product and
manuals without prior notice. Adimec Advanced Image Systems B.V. makes no warranty of any kind
with regard to the material contained within this document, including, but not limited to, the implied
warranties of merchantability and fitness for a particular purpose. Adimec Advanced Image Systems
B.V. shall not be liable or responsible for incidental or consequential damages in connection with the
furnishing, performance or use of this material.
Layout, composing and editorial staff: Adimec Advanced Image Systems B.V.
Illustrations: Adimec Advanced Image Systems B.V.
All rights reserved. No part of this document may be reproduced, stored in a database or retrieval
system, or published in any other form or way, electronically, mechanically, by print, photo print,
microfilm or any other means without prior written permission from the publisher.
All correspondence regarding copyrights, translations:
Adimec Advanced Image Systems B.V.
PO Box 7909 Luchthavenweg 91
5605 SH Eindhoven 5657 EA Eindhoven
The Netherlands The Netherlands
Tel: +31 (40) 2353920
Fax: +31 (40) 2353905
URL: www.adimec.com
Publication number: 186880 Manual Quartz CL Ver. 1.0.
© Copyright 2013 Adimec Advanced Image Systems B.V. Eindhoven, The Netherlands.

OPERATING AND USER MANUAL QUARTZ SERIES
9
Precautions2.
NOTE:It is advised to include the text of this chapter in the assembly documents of the system in
which the camera is used.
A CMOS sensor camera is a sensitive device. Please read the following precautions carefully before
you continue unpacking or operating the camera.
Safety precautions2.1
General2.1.1.
It is advised to unpack and handle the camera in a clean, ESD protected working area.
It is advised to read the whole manual before using the camera.
Safety symbols2.1.2.
The following safety symbols are applicable to and indicated on the camera.
Symbol for “Conformiteé European”
The exclamation mark within an equilateral triangle is intended to alert the user to the
presence of important operating and maintenance (servicing) instructions in the
literature accompanying the instrument.
Handling2.2
General2.2.1.
In order to prevent damage to the camera and to keep the CMOS sensor clean, please take the
following precautions.
Always keep the sensor cap in place, as long as no lens is attached.•
Remove the lens cap just before the lens is screwed on the camera. It is advised to perform this•
operation in a clean room or clean bench.
Never touch the CMOS sensor surface. The cover glass is easily damaged and the CMOS sensor•
can be damaged by ESD (electrostatic discharge).
Cleaning of the CMOS sensor2.2.2.
Cleaning of a CMOS sensor is a rather difficult task. Depending on the aperture of the lens used, any
dust particles with a size of 10µ and larger can show up in your image.
All cameras are checked for cleanliness in our factory before shipment. Proper handling instructions
during system assembly can prevent the CMOS sensor from getting contaminated.
Should cleaning of the CMOS sensor be necessary follow the instruction below.
NOTE: that damage of the CMOS sensor due to scratches on the cover glass or electrostatic
discharge (ESD) is not covered by warranty!
The correct working environment for cleaning is essential in order to ease cleaning and to prevent
damage of the CMOS sensor.

OPERATING AND USER MANUAL QUARTZ SERIES
10
Precautions:
Take precautions to prevent ESD that can damage the CMOS sensor.•
Cleaning of the CMOS sensor, and assembly of the lens is preferably performed in a clean•
room or clean bench.
Never try to clean the CMOS sensor at a relative humidity lower than 30 %. A relative humidity of•
40 % or higher is preferred in order to minimize the chance of damage due to ESD.
It is advisable to use an ionizer, in order to minimize the built-up of ESD.•
Be sure to clean the lensmount of the lens before assembly.•
Use non-fluffing Q-tips and Alcohol (or Hexane) for cleaning. De-ionized water may be necessary•
to remove ionic contaminants like salts.
Any Q-tip should be used only once - you will otherwise move dirt from one place to another.•
Never dry rub the window. This may cause static charges or scratches that can destroy the CMOS•
sensor.
Cleaning instructions:
First try to remove the contamination by using clean, dry air. (Use an ultra-filtered, non-residue1.
dust remover spray). Avoid blowing air into the screw thread of the lensmount, because this may
cause contamination on the CMOS sensor due to loose particles and traces of oil or grease.
If this step does not result in an acceptable result, continue with step 2.
Remove the lensmount by unscrewing the 4 crosshead screws2.
that hold the lensmount (see figure 2.1).
Crosshead screws that hold the lensmount (front view of the camera).Figure 2.1:
Clean the inner screw thread of the lensmount using Alcohol or Hexane and a Q-tip.3.
Clean the CMOS sensor cover glass using Alcohol or Hexane and a Q-tip.4.
Gently and carefully rub the window always in the same direction, e.g. top to down.
Install the lensmount back on the camera front.5.
Maximum tightening force may not exceed 0.3 Nm.
Install a lens, power up the camera, set the lens at a small aperture (F16) and point6.
the lens at a bright source. Adjust gain and integration time if necessary.
Check the image on the monitor for dark spots and stripes caused by contamination7.
on the CMOS sensor cover glass. (Note that the image on the monitor should not
saturate due to over exposure - if necessary close the iris even further).
If the CMOS sensor is not clean, repeat steps 4 - 7 using a new Q-tip. After three unsuccessful8.
tries, it is advised to wait a few minutes before a new attempt is made to clean the CMOS sensor.
(The waiting time allows the electric charge that has been built up during cleaning to neutralize).

OPERATING AND USER MANUAL QUARTZ SERIES
11
Cleaning of the camera2.2.3.
The camera shall NEVER be immersed in water or any other fluid. For cleaning, only use a light moist
tissue.
Maintenance2.2.4.
No specific maintenance other than cleaning is applicable.
Repair and modification2.2.5.
Repair, modification and replacement of parts shall be done only by Adimec to maintain compliance
with the directive 89/336/EEC electromagnetic compatibility and directive 72/23/EEC low voltage
directive and the international standards.
Peripheral equipment2.2.6.
For safety, use an external SELV qualified power supply. Maximum current 1 A.
For safety, peripheral equipment must either be double isolated or SELV qualified.
Mounting / Mechanical2.2.7.
Connectors
Take care during handling of the camera. The Camera Link connector and the power connector should
not be damaged.
The maximum tightening torque for the Camera Link connector may not exceed 0.26 Nm.
Prevent the entry of foreign objects or dirt into the connectors, as this will result in unreliable operation
or damage.
Mounting screws
Take notice of the maximum length of the screws that may be used for mounting of the camera. Using
screws too long can cause damage to the camera. Maximum screw length: 5 mm.

OPERATING AND USER MANUAL QUARTZ SERIES
12

OPERATING AND USER MANUAL QUARTZ SERIES
13
Installation3.
In this chapter all three electrical interfaces as well as the mechanical and optical interface are
described. If a lens and all interfaces are available, it is possible to refer to the quick start paragraph at
the end of this chapter. The other paragraphs describe the interfaces in detail.
Electrical interface - power3.1
Chassis part
Hirose type HR10A-7R-6PB(74)•
Camera male power connectorFigure 3.1:
PIN FUNCTION
1,2 10.2 to 13.8 Vdc
3,4 Not Connected
5,6 GND
Power pin configuration.Table 3.1:
Q-2A340 Q-4A150 Q-4A180 Q-12A65
<8 W <8 W <8 W < 8 W
Power consumption @ 12 Volt.Table 3.2:
NOTE:The supply is reverse voltage protected. When applying power to the camera with the wrong
polarity it will not operate, but will not be damaged.
Mating cable connector
Hirose type HR10A-7P-6S(74)•
Electrical interface - strobe and trigger3.2
An input for external triggering of the camera is available at the I/O connector.
Also a trigger output signal from the camera to control an external flash light is available at this
connector. The input and output are fully programmable. For reference see paragraph 7.5.
The input and output are galvanic isolated from the internal camera electronics by means of an
optocoupler.
4
5
2
3
6
1

OPERATING AND USER MANUAL QUARTZ SERIES
14
Chassis part
Hirose type HR10A-7R-4SB(74)•
Camera female I/O connectorFigure 3.2:
PIN NO. SIGNAL NAME DIRECTION LEVEL AT THE PIN
1Trigger in Input 10..20 mA Anode of optocoupler(*)
2Flash strobe out Output Open collector of optocoupler
3Trigger return Input Isolated gnd Cathode of optocoupler
4Flash strobe return Output Isolated gnd Emitter of optocoupler
(*)serial resistors 470 Ωinside camera, see figure 3.3.
Pinning I/O connectorTable 3.3:
Mating cable connector
Hirose type HR10A-7P-4P(74)•
NOTE:The delay from non-conductive to conductive state of the phototransistor is less than 1.5 µs.
The delay from conductive to non-conductive state of the phototransistor is less than 10 µs.
The recommended termination circuitry is drawn in Figure 3.3.
A current of 2.5 mA is recommended for the Flash output. For the trigger input, a current of 10 mA is
recommended. These current recommendations translate to the recommended resistor values in table
3.4.
VEXT [V] R1 EXT[Ω]R2 EXT[Ω]
3.3 1000 Do not apply
5.0 2000 0
12 4700 470
Recommended series resistor for trigger inputTable 3.4:
4
2
3
1

OPERATING AND USER MANUAL QUARTZ SERIES
15
Recommended terminations of strobe output and trigger input.Figure 3.3:
Electrical interface - Video and Data.3.3
The Camera Link interface is designed to connect the camera to a frame grabber in order to transfer
video to the grabber as well as control data from the grabber to the camera. The maximum cable
length is 10 meter, for a 85MHz interface however 5 meter is recommended.
For a description of the Camera Link interface please refer to the Camera Link specification.
NOTE:PoCL (Power over Camera Link) is not supported. When connecting the camera to a PoCL-
compliant frame grabber, the PoCL-function must be disabled.
NOTE:Two Camera Link cables are required to connect the camera to the grabber. For stable
transmission make sure both cables are equivalent, (i.e. of the same length and preferably the same
brand and type number).
Interface connectors: 3M MDR 26-pins.
Standard Camera Link cables can be ordered at Adimec.
The Camera Link ports assignment is described in chapter 11.
Camera Application

OPERATING AND USER MANUAL QUARTZ SERIES
16
Quick start3.4
Mount a lens on the camera and adjust the iris for F5.6.•
Connect the Camera Link cables to the camera and frame grabber.•
Boot up the PC and start the frame grabber application.•
Connect the power cable to the camera and power up the camera with 12 Vdc.•
Configure the framegrabber to 10 bit pixel depth resolution, 2 taps interleaved and 85 MHz•
pixelclock.
Factory default settings of the Quartz camera series.
Q-2A340 Q-4A150 Q-4A180 Q-12A65
Operation Mode Continuous
Frame Rate 2-taps 25 fps 13 fps
Output Resolution 10 bit
Factory default interface settingsTable 3.5:

OPERATING AND USER MANUAL QUARTZ SERIES
17
Functional description4.
This chapter contains a functional description of the Quartz cameras. It describes the main functions
and features of the camera using a simplified block diagram.
Block diagram4.1
The diagram below shows the main functional blocks of the Quartz cameras.
Block diagram of the cameraFigure 4.1:
The CMOS image sensor is equipped with one analog to digital converter per pixel column.
A programmable Region Of Interest (ROI block) is available. The camera will only output video
information from a rectangular subframe, programmed through the ROI command. This reduces the
amount of data and can increase the frame rate.
The defect pixel correction function can be enabled and disabled on demand.
For functional testing of the camera and frame grabber chain, a test pattern generator is available. The
test pattern generator can also be enabled and disabled on demand.
Flat field correction allows for correction of shading. This can be calibrated in the field.
Digital Gain is applied within the basic processing block. An output look-up table is available; this
table allows real-time conversion of the video levels from the processing chain according to a user
programmable curve (e.g. Gamma-function).
The camera is able to average a number of images before they are output over the interface. This
reduces the temporal noise significantly.
Horizontal binning and vertical binning digitally averages a number of pixels into a single pixel. The
used method is suitable to increase sensitivity.
Flat field
Correction
Basic
Processing
Image tagging
Test pattern
Defect pixel
Correction
Exposure
Modes
ROI
Frame
Averaging
Binning
Image flip
Format
conversion
Image Capture
Image Processing
Image Output
Camera Link
Interface
Frame
Buffering

OPERATING AND USER MANUAL QUARTZ SERIES
18
The output image can be mirrored horizontally and vertically.
All images pass through a real-time dual ported frame memory, referred to as image FIFO. This FIFO
(first-in-first-out memory) allows for temporary buffering of the images if acquisition of frames is done
faster than the Camera Link interface allows. Data will be readout immediately after it is written if
buffering is not necessary, leading to minimal delay between acquisition and camera output.
Image tagging allows for identification of each frame at the output. The camera has a built-in
framecounter. A digital representation of this framecounter can be made visible as either overlaying the
actual video data or added as an extra video line tag.
The video data is mapped to the Camera Link ports. The output resolution can be set to 8 bit or 10 bit
by user command. The output format can be set by user command.
The camera is equipped with a flash strobe output signal on the I/O connector. The active state of the
flash strobe output can be inverted to adapt to the application requirements. The flash strobe output
can be operated in two different modes, which are set through a user command.
The automatic mode: The flash strobe will become active after the sensor is reset and a•
configurable delay time is expired. The strobe will deactivate when the acquisition is completed.
The programmed mode; Both delay time after a sensor reset as well as the duration of the active•
state can be programmed.
The delay time between the sensor reset operation in the active state of the flash strobe, as well
as the duration of the flash strobe if the camera is in programmed strobe timing mode, can be user
programmed.

OPERATING AND USER MANUAL QUARTZ SERIES
19
Control of the camera5.
Introduction5.1
The Quartz cameras are fully software controlled via the Camera Link serial channel using a simple
ASCII based protocol.
It is possible to save settings as ‘power-up default settings’ in the camera.
A command line control application is available to interactively control the camera settings.
Please contact your local Business Office to obtain a copy of the latest release.
Although this is an easy way of changing camera settings, it is also possible to communicate with the
camera using self deployed software. Please refer to chapter 5.2 for the communication protocol.
Use chapters 6 to 10 as a detailed reference of the control commands.
Communication protocol5.2
The camera is controlled by a host system connected to the Camera Link interface using the serial
communication link of the Camera Link. Commands and resulting data are transferred between the
host system and the camera by means of a communication protocol. The host system is the master
in the communication link. All actions are initiated by the host system.The camera only replies to a
message received from the host system.
Data link settings5.2.1.
The data link settings that shall be used for communication with the camera are:
Baud rate 57600 baud
stop bit 1
data bit 8
parity none
handshaking none
Data flow characters5.2.2.
The communication protocol uses data flow control characters to identify a message and for
acknowledgement.
The following data flow characters are defined:
CHAR DEC DESCRIPTION
NUL 0NUL character, is ignored
STX64 start of message identifier
ETX13 end of message identifier
ACK 6positive acknowledgement
NAK 21 negative acknowledgement
Message Format5.2.3.
Command and data are packed in a message. A message starts with the STX character followed
by the message content. The message ends with an ETX character. The characters allowed in the
message content range from decimal 32 to 255.
Format: STX<message content> ETX

OPERATING AND USER MANUAL QUARTZ SERIES
20
Message acknowledgement5.2.4.
After receiving a message, the camera responds with an acknowledgement character. This can be an
ACK character (positive acknowledgement) or a NAK character (negative acknowledgement).
The ACK response is given when the received message was understood (the content of the message
is not considered).
The NAK response is given when the received message was not understood, which may be the case
when invalid characters are received as message content, or the message overruns the camera
receiver buffer capacity.
Reply messages5.2.5.
When a message is sent to the camera that requires data to be transmitted back to the host system,
this data is packed in a message and is sent to the host system after the positive acknowledgement
(ACK) character. When the camera responds with a NAK character no data is send back to the host
system.
Communication timing5.2.6.
The time between the successive characters making up a message is not limited. The camera
however, when transmitting a message to the host system, has a time interval between successive
characters of less than the time required for a single character to be transmitted.
Host system requirements5.2.7.
After transmitting a message to the camera, the host system must wait for the camera to reply with an
ACK or NAK character. To prevent lock-up, the wait time for the response must be limited by a time-
out period. After not receiving an ACK or NAK character after the time-out period has elapsed, the
host system must consider the transmitted message as not being received.
The time-out time to be used for the camera should be at least 200 ms.
Under normal conditions, a NAK or no response from the camera results from damage of the
transmitted characters due to noise or communication link hardware problems. In such case, the
host system should transmit the message again. The number of repeated transmissions after a NAK
response or no response must be limited by a retry count to prevent lock-up.
If the camera is still responding with a NAK character after the maximum number of retries of
the transmitted message have been sent, the communications channel should be considered
malfunctioning or too noisy.
When the maximum number of retries of the transmitted message has been reached and the camera is
still not responding, the communication channel should be considered disconnected or the camera not
being powered or malfunctioning.
Camera Link interface standard5.3
Introduction5.3.1.
Without getting into detail on the Camera Link standard, this section discusses the mechanics of the
serial communication channel.
Available Camera Link serial software enhancements in the form of Dynamic Link Library files will
greatly simplify the setup of a communication channel.
Both camera manufacturers and frame grabber vendors have issued these DLL files which will provide
standard C, API and native Visual Basic support, so that applications written in C or Visual Basic can
communicate serially with Camera Link cameras.

OPERATING AND USER MANUAL QUARTZ SERIES
21
Overview5.3.2.
The user application calls into the generic clserial.dll, which dynamically loads the.dll file(s) specific to
the frame grabber(s) referred to by the application. It then routes all calls to that .dll file. The following
diagram illustrates this sequence:
Mechanics of communication per Camera link serial channelFigure 5.1:
Features Provided by clserial.dll
Simultaneous, multi-port (including cross vendor) support•
Support for binary or text based data transfers•
Common API across vendors•
Common error codes across vendors•
Common error text across vendors•
Strict, well defined behavior of all functions in specification•
Openness to vendor specific error codes and text•
Ability to enumerate ports on sytem•
Inquireable/adjustable baud rate for ports•
Win 32 support (open source for port to other platforms)•
C/C++ support through import library•
VisualBasic support through type library•
Backwards compatibility with recommended specification of October 2000•
Standard default communication settings for serial port•
Supplied by framegrabber
manufacturer
Supplied by camera
manufacturer
User
application
clserial.dll
clser
xxx
.dll
clser
yyy
.dll
clser
zzz.
dll
Camera CL
control lines
xxx,yyy,zzz are unique identifiers, assigned to AIA member companies.
This manual suits for next models
3
Table of contents
Other CAMERA LINK Security Camera manuals
Popular Security Camera manuals by other brands
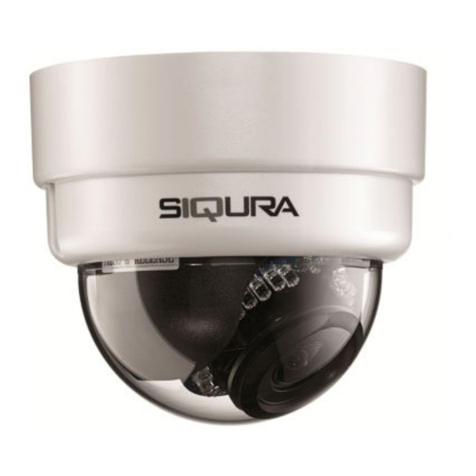
Siqura
Siqura IFD820V1IR installation manual

NEXHO
NEXHO CE Fitting and operating instructions
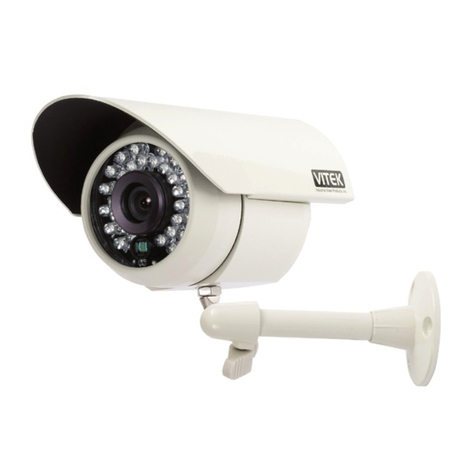
Vitek
Vitek VTC-IRLED30 user guide
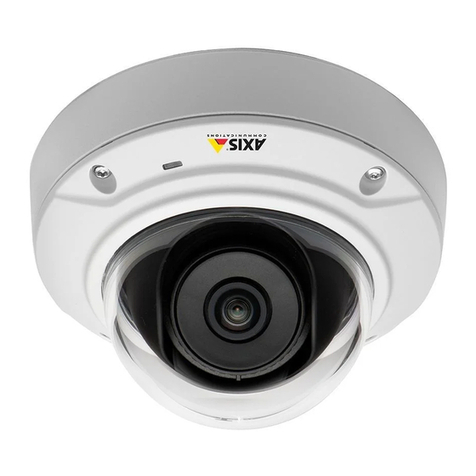
Axis
Axis M3006-V user manual
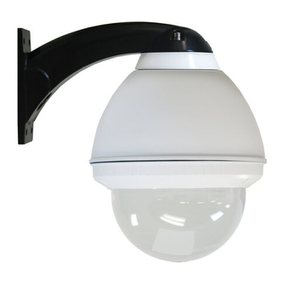
Moog Videolarm
Moog Videolarm SView FDP7C12N-9 Installation and operation instructions
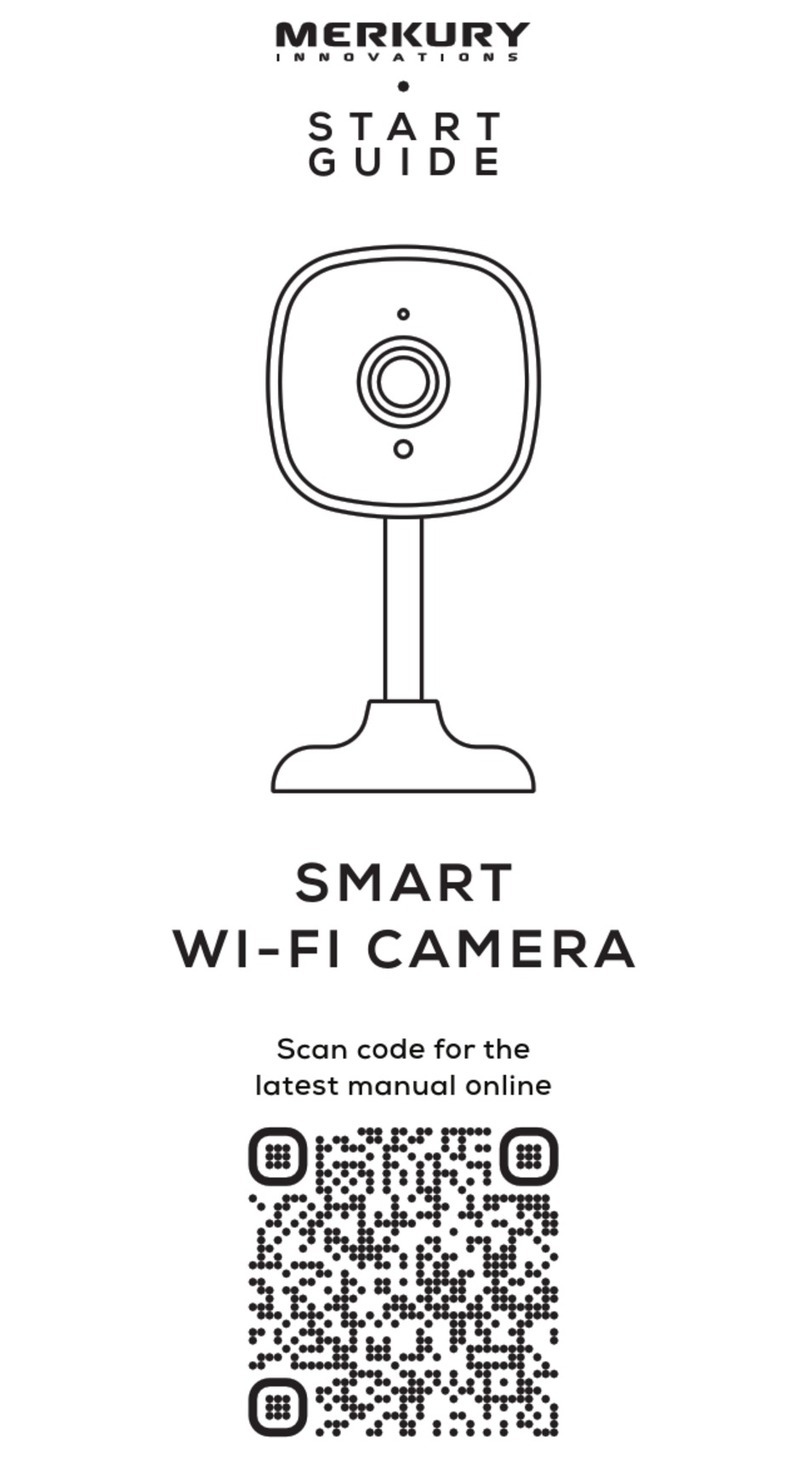
Merkury Innovations
Merkury Innovations SMART WI-FI CAMERA Start guide