Cannon Tools NEILSEN CT2594 Assembly instructions

50 TON HYDRAULIC SHOP PRESS CT2594
Instruction & Assembly
CANNON TOOLS LTD
Add: 20 station road, Rowley Regis, west midlands,B65 0JU.U.K.
SAVE THESE INSTRUCTIONS FOR FUTURE REFERENCE


1
EC DECLARATION OF CONFORMITY
We CANNON TOOLS LTD
20 Station road, Rowley Regis, West Midlands,B65 0JU.U.K.
Declare that the following machine complies with the appropriate basic safety and
health requirements of the EC Directive based on its design and type, as brought
into circulation by us.
In case of alteration of the machine, not agreed upon by us, this declaration will
lose its validity.
Product description: 50 TON HYDRAULIC SHOP PRESS
Model: CT2594
Applicable EC Directives:
EC Machinery Directive 2006/42/EC
Harmonized standards
EN ISO 12100:2010, EN ISO 16092-3:2018
20 Station Road, Rowley Regis, West Midlands, B65 0JU.U.K.
Mr. Gurcharan Tony Singh Sanghera
Managing Director
CANNON TOOLS LTD
2021-12-8

2
1. SPECIFICATION
Model: CT2594
Capacity: 50Tons
Working range: 0-1000mm
Ram stroke: 185mm
Air pressure: 110 -120PSI
Air inlet: 1/4" NPT
2. IMPORTANT SAFETY INFORMATION
You will need this manual for the safety warnings and precautions, assembly,
operating, inspection, maintenance, and cleaning procedures. Keep your invoice
with this manual. Write the invoice number on the inside of the front cover. Keep
this manual and invoice in a safe and dry place for future reference.
GENERAL SAFETY WARNINGS
1. Keep work area clean and dry. Cluttered, dark or wet work areas invite injuries.
2. Keep children and bystanders away from work area. Do not allow children or
untrained individuals to handle this product.
3. Store idle equipment. When not in use, tools and equipment should be stored
in a dry location to inhibit rust. Always lock up tools and equipment and keep out
of reach of children.
4. Do not use a power tool while tired or under the influence of drugs, alcohol,
or medication. A moment of inattention while operating power tools may result in
serious personal injury. Read warning labels on prescriptions to determine if your
judgment or reflexes are impaired while taking drugs. If there is any doubt, do not
use this product.
5. Dress with safety in mind. Wear ANSI approved safety impact eyeglasses and
heavy-duty work gloves when using this product. Non-skid footwear or safety
Shoes should be used when working with this product. Do not wear loose clothing
or jewelry as they can become caught in moving parts. Wear a protective hair
Covering to prevent long hair from becoming caught in moving parts.
6. Do not overreach. Keep proper footing and balance at all times. Proper footing
and balance enable better control in unexpected situations.
7. Stay alert. Watch what you are doing at all times. Use common sense. Do not
use this product when you are tired or distracted from the job at hand.
8. Check for misalignment or binding of moving parts, breakage of parts, and any
other condition that may affect the tool’s operation. If damaged, have the tool
serviced before using. Many accidents are caused by poorly maintained tools.
9. Maintain this product with care. Keep this tool clean and dry for better and safer
performance.
10. Maintenance: For your safety, service and maintenance should be performed

3
regularly by a qualified technician.
11. Do not force the tool. Use the correct tool for your application. The correct tool
will do the job better and safer at the rate for which it is designed. Do not force the
tool and do not use the tool for a purpose for which it is not intended.
SPECIFIC PRODUCT WARNINGS
1. Use the correct tool for the job. This tool was designed for a specific function.
Do not modify or alter this tool or use it for an unintended purpose.
2. The maximum load is 50 tons. Do not exceed this rated capacity. Never apply
excessive force to a workpiece and always use the pressure gauge to accurately
determine the applied load.
3. Inspect the press before each use. Do not use if any component is bent,
broken, cracked, leaking or showing other damage. Do not use the press after a
shock load until a qualified technician has examined the press.
4. Check to ensure that all bolts and nuts are tight.
5. Only use this shop press on a surface that is stable, level and not slippery. The
surface must be capable of sustaining the weight of the shop press and the load.
6. Ensure that the workpiece is center-loaded and secure. An unbalanced load
may slip off the heel blocks or bed frame.
7. Keep hands and feet away from the bed area at all times.
8. Do not use the shop press to compress a spring or any other item that could
disengage and cause a potential hazard. Never stand directly in front of a loaded
press and never leave a loaded press unattended.
9. Do not allow an untrained person to operate the press.
10. Do not use brake fluid or other improper fluid in place of hydraulic oil. Avoid
mixing different types of oil when adding hydraulic oil. Only good quality hydraulic
jack oil can be used.
11. Do not expose the press to rain, snow or inclement weather.
12. Bolt the press to the floor if it is to be used on bulky or unstable items.
HYDRAULIC SAFETY DANGER!
Seek immediate medical attention if hydraulic fluid under pressure penetrates
your skin. See Injection Injury precautions for instructions before using a
pressurized hydraulic system.
1. Do not touch or handle hydraulic hoses or components while under pressure.
Hydraulic fluid escaping under pressure has sufficient force to penetrate your
clothing and skin. A pinpoint hole may inject hydraulic fluid into your body. Seek
immediate medical attention if this occurs .
2. Never exceed the hydraulic system’s load capacity .
3. Do not adjust the hydraulic system’s relief setting. The settings are pre-set by
the factory.
4. Hydraulic oil under pressure is hot and can cause a burn injury if touched,

4
sprayed or spilled. Allow the hydraulic system to cool before conducting
maintenance.
5. Hydraulic components require regular inspection. Release all pressure from
the system before you inspect it. Replace damaged hydraulic parts with identical
manufacturer's components.
6. Do not attempt makeshift repairs to a hydraulic system. Such repairs can fail
suddenly and create a hazardous condition.
7. A damaged or disconnected hydraulic hose under pressure may whip around
and inflict personal injury or damage the work area. Secure the hose to a fixed or
permanent structure with clamps or cable ties.
8. Hydraulic fluid has a combustible flash point of 200°F (93°C). Do not expose
the fluid to an ignition source.
9. Change your clothing immediately if sprayed with hydraulic fluid. Store clothing
or rags contaminated with hydraulic fluid in an approved metal safety can with a
spring-closing lid and venting designed to contain a fire.
10. Only use hydraulic fluid in the pump. Do not substitute or mix brake fluid, or
any other fluid, with the hydraulic fluid. This can result in a pump failure and injure
the user or bystander. It may also damage the pump.
AIR TOOL PRECAUTIONS
1. Extended exposure to air tool noise may cause hearing loss. Ear protection
gear can reduce or eliminate the noise level.
2. Inspect the tool's air hose for cracks, fraying or other faults before each use.
Discontinue use if the air hose is damaged or hissing is heard from the air hose or
connectors, while operating the tool. Replace the defective component/air hose.
3. Do not allow people, mobile equipment or vehicles to pass over the
unprotected air hose. Position the air hose away from high traffic areas, in a
reinforced conduit or place planks on both sides of the air hose to create a
protective trench.
4. Prevent damage to the air hose by observing the following:
a. Keep the air hose behind the tool and out of the tool's work path.
b. Keep the air hose away from heat, oil, sharp edges or moving parts.
c. Do not wrap the air hose around the tool as sharp edges may pierce or crack
the air hose. Coil the air hose when storing.
5. A damaged or disconnected air hose under pressure may whip around and
inflict personal injury or damage the work area. Secure the compressor's air hose
to a fixed or permanent structure with clamps or cable ties.
6. Install an in-line shutoff valve or regulator to allow immediate control over the
air supply in an emergency, even if a hose is ruptured.
7. Check the manufacturer’s maximum pressure rating for air tools and
accessories. Compressor outlet pressure must be regulated so as to never
exceed the maximum pressure rating of the tool.

5
3. TECHNICAL DESCRIPTION
4. UNPACKING AND CHECKING
WARNING! Do not operate the tool if any part is missing. Replace the missing
part before operating. Failure to do so could result in a malfunction and personal
injury.
Remove the parts and accessories from the packaging and inspect for damage.
Make sure that all items in the parts list are included.

6
5. ASSEMBLY
Secure the right and left Base Supports to the bottoms of the frame, using Screws,
Spring Washers , and Nuts for each Base Support. Attach Seek help to set
upright.
Connect each of the four support bars to the post and base section with bolts , flat
washers , lock washers and nuts .
6. OPERATION
Before the first use, check for proper hydraulic oil level in the system. Then
thoroughly test the hydraulic ram for proper operation prior to its actual use.
1. Pour a teaspoon of good quality, air tool lubricant into the air supply inlet of the
foot pedal. Connect to the air supply and operate for 3 seconds to evenly
distribute lubricant.
2. Purge air from the hydraulic system. See Bleeding the Hydraulic System in the
Maintenance section.
OPERATING THE SHOP PRESS
WARNING! Ensure that you read, understand and apply the safety instructions
and warnings before use.
1. Place the heel blocks on the adjust beam , then insert a workpiece on the heel
blocks.
2. Lift or lower the bed frame with the hand winch until it is in position. Insert a
support pin into the left and right posts beneath the bed frame. Lower the bed
frame so it rests on the pins. Secure the pins with retaining rings.
3. Close the release valve by turning it until it is firmly closed.
4. Connect the air inlet to the air compressor. Set the compressor’s air pressure
regulator at no more than 120 psi. Turn on the air compressor to permit air to flow
to the pump assembly. Continue pressing until the serrated saddle nears the
workpiece, then turn off the compressor.When an air source is unavailable, pump
the handle until the serrated saddle nears the workpiece.
5. Align the workpiece and ram to ensure center-loading.
6. Turn on the compressor (or pump the handle) to apply load to the workpiece.
7. When the work is done, turn off the compressor (or stop pumping the handle).
Slowly and carefully remove load from the workpiece by turning the release valve
counterclockwise in small increments.
8. Once the ram has fully retracted, remove the workpiece from the bed frame.
9. Disconnect the air inlet fitting from the air source when finished for the day.

7
7. MAINTENANCE
Maintain the tool with care. A tool in good condition is efficient, easier to control
and will have fewer problems. Inspect the tool components periodically. Repair or
replace damaged or worn components. Only use identical replacement parts
when servicing. Keep the tool handles clean, dry and free from oil/grease at all
times.
1. Periodically, lightly oil all moving parts including the pump piston and hydraulic
ram.
2. Check hydraulic connections and hoses before each use. Do not use if cut,
damaged, leaking or otherwise damaged connections and/or hoses are noted.
8. EXPLODED VIEW

8
PARTS LIST
Part No.
Description
Qty
Part No.
Description
Qty
1
Bolt
6
21
Arbor plate
2
2
Cross beam
1
22
Pressure beam
1
3
Damping nut M16
4
23
Jack
1
4
Spring washer M22
8
24
Bole
4
5
Washer M22
8
25
Washer M16
8
6
Damping nut M22
8
26
Gear
1
7
Pole
2
27
Gear seat
1
8
Pin
2
28
Damping nut M10
10
9
Tighter the screws
4
29
Bole
2
10
Washer M12
38
30
Steel wire
1
11
Bolt
12
31
Collet
2
12
Leg
2
32
Steel shaft
4
13
Damping nut M12
6
33
Steel wheel
4
14
Connect board
2
34
Washer M18
4
15
Bolt
7
35
Block loop
4
16
Washer M10
10
17
Bolt
6
18
Pump
1
19
Handle
1
20
Adjust beam
1


CANNON TOOLS LTD
20 Station road, Rowley Regis, West Midlands,B65 0JU.U.K.
Made in China
Table of contents
Popular Power Tools manuals by other brands
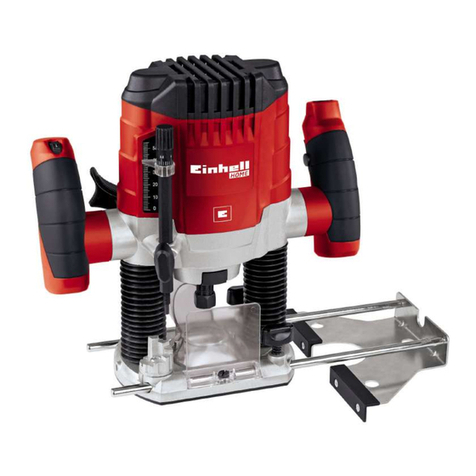
EINHELL
EINHELL TC-RO 1155 E Original operating instructions
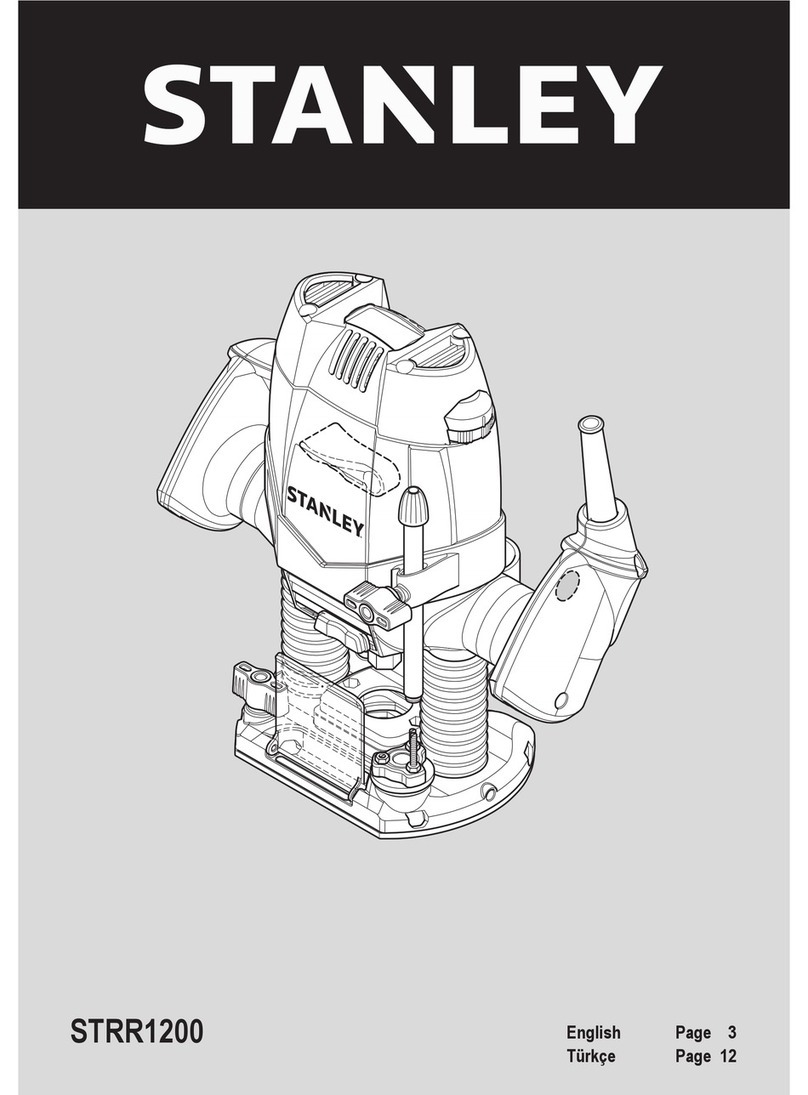
Stanley
Stanley STRR1200 Original instructions
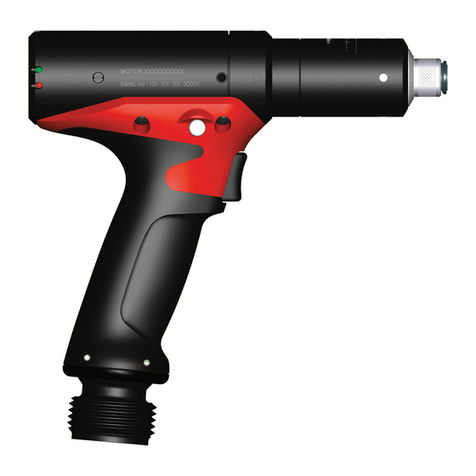
Desoutter
Desoutter ECPL Series user manual
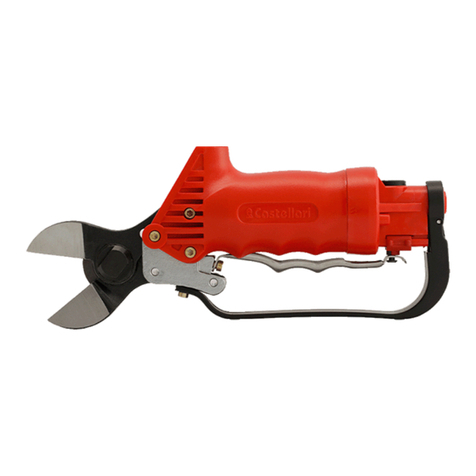
Castellari
Castellari SISTEM Use and maintenance manual
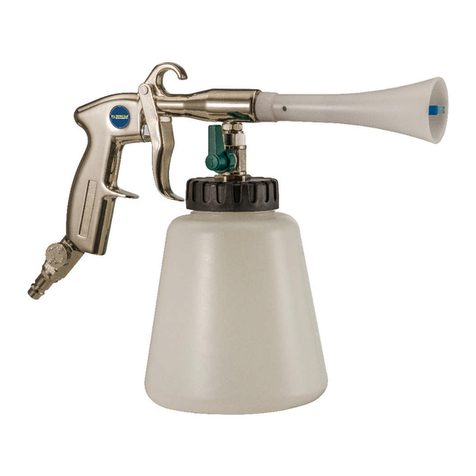
Schulz
Schulz Tornador STP 01 instruction manual

Chicago Electric
Chicago Electric 67632 Set up and operating instructions