Carrier 19XR04027401 Assembly instructions

Manufacturer reserves the right to discontinue, or change at any time, specifications or designs without notice and without incurring obligations.
Catalog No. 04-531900050-01 Printed in U.S.A. Form 19XR-CLT-16SI Pg 1 5-17 Replaces: 19XR-6SI
Installation, Operating, and
Maintenance Instructions
SAFETY CONSIDERATIONS
Positive pressure storage systems are designed to pro-
vide safe and reliable service when operated within
design specifications. When operating this equipment,
use good judgment and safety precautions to avoid dam-
age to equipment and property or injury to personnel.
Installation, start-up, and servicing of this equipment
can be hazardous due to system pressures, electrical
components, and equipment location (roofs, elevated
structures, etc.). Only trained, qualified installers and
service technicians should install, start up, and service
this equipment.
Be sure you understand and follow the procedures and
safety precautions contained in this guide.
DANGER
Failure to follow these procedures will result in severe per-
sonal injury or death.
DO NOT VENT refrigerant relief valves within a building.
Outlet from rupture disc or relief valve must be vented out-
doors in accordance with the latest edition of ASHRAE 15
(American Society of Heating, Refrigerating, and Air-
Conditioning Engineers). The accumulation of refrigerant
in an enclosed space can displace oxygen and cause
asphyxiation.
PROVIDE adequate ventilation in accordance with
ASHRAE 15, especially for enclosed and low overhead
spaces. Inhalation of high concentrations of vapor is harm-
ful and may cause heart irregularities, unconsciousness, or
death. Misuse can be fatal. Vapor is heavier than air and
reduces the amount of oxygen available for breathing.
Product causes eye and skin irritation. Decomposition
products are hazardous.
DO NOT USE OXYGEN to purge lines or to pressurize a
machine for any purpose. Oxygen gas reacts violently with
oil, grease, and other common substances.
NEVER EXCEED specified test pressures, VERIFY the
allowable test pressure by checking the instruction litera-
ture and the design pressures on the equipment nameplate.
DO NOT USE air for leak testing. Use only tracer gases
and dry nitrogen.
DO NOT VALVE OFF any safety device.
BE SURE that all pressure relief devices are properly
installed and functioning before operating any machine.
WARNING
Failure to follow these procedures may result in personal
injury or death.
DO NOT USE TORCH to remove any component. System
contains oil and refrigerant under pressure.
To remove a component, wear protective gloves and gog-
gles and proceed as follows:
a. Shut off electrical power to unit.
b. Recover refrigerant to relieve all pressure from sys-
tem using both high-pressure and low-pressure ports.
c. Traces of vapor should be displaced with nitrogen
and the work area should be well ventilated. Refrig-
erant in contact with an open flame produces toxic
gases.
d. Cut component connection tubing with tubing cutter,
and remove component from unit. Use a pan to catch
any oil that may come out of the lines and as a gage
for how much oil to add to the system.
e. Carefully unsweat remaining tubing stubs when nec-
essary. Oil can ignite when exposed to torch flame.
DO NOT USE eyebolts or eyebolt holes to rig machine
sections or the entire assembly.
DO NOT work on high-voltage equipment unless you are a
qualified electrician.
DO NOT WORK ON electrical components, including
control panels, switches, starters, or oil heater until you are
sure ALL POWER IS OFF and no residual voltage can
leak from capacitors or solid-state components.
LOCK OPEN AND TAG electrical circuits during servic-
ing. IF WORK IS INTERRUPTED, confirm that all cir-
cuits are de-energized before resuming work.
AVOID SPILLING liquid refrigerant on skin or getting it
into the eyes. USE SAFETY GOGGLES. Wash any spills
from the skin with soap and water. If any enters the eyes,
IMMEDIATELY FLUSH EYES with water and consult a
physician.
NEVER APPLY an open flame or live steam to a refriger-
ant cylinder. Dangerous overpressure can result. When
necessary to heat refrigerant, use only warm (110 F [43 C])
water.
DO NOT REUSE disposable (nonreturnable) cylinders or
attempt to refill them. It is DANGEROUS AND ILLE-
GAL. When cylinder is emptied, evacuate remaining gas
pressure, loosen the collar and unscrew and discard the
valve stem. DO NOT INCINERATE.
(Warnings continued on next page.)
19XR
Positive Pressure Storage System
50/60 Hz

2
CONTENTS
Page
SAFETY CONSIDERATIONS . . . . . . . . . . . . . . . . . . . . 1,2
INTRODUCTION . . . . . . . . . . . . . . . . . . . . . . . . . . . . . . . . 2,3
INSTALLATION. . . . . . . . . . . . . . . . . . . . . . . . . . . . . . . . 3-10
Step 1 — Complete Pre-Installation Checks . . . . . . 3
• IDENTIFY UNIT
• INSPECT SHIPMENT
Step 2 — Mount the Pumpout Unit . . . . . . . . . . . . . . . 3
• MOUNTING ON THE CHILLER
• FLOOR MOUNTING
Step 3 — Rig the Storage Tank . . . . . . . . . . . . . . . . . . . 4
Step 4 — Make Piping Connections . . . . . . . . . . . . . . 6
• INSTALL VENT PIPING TO RELIEF DEVICES
Step 5 — Make Electrical Connections . . . . . . . . . . . 6
CONTROLS AND COMPONENTS . . . . . . . . . . . . . . . . 11
Pumpout Unit . . . . . . . . . . . . . . . . . . . . . . . . . . . . . . . . . . . 11
• CONTROLS
• SAFETY CONTROL SETTINGS
•COMPRESSOR
• CONDENSER
•OILSEPARATOR
• SUCTION AND DISCHARGE VALVES
Storage Tank . . . . . . . . . . . . . . . . . . . . . . . . . . . . . . . . . . . . 11
•DRAINVALVE
• DUAL RELIEF VALVES
• PRESSURE GAGE
• LEVEL GAGE
OPERATION. . . . . . . . . . . . . . . . . . . . . . . . . . . . . . . . . . 11-17
Overview . . . . . . . . . . . . . . . . . . . . . . . . . . . . . . . . . . . . . . . . 11
• REFRIGERANT TRANSFER
• TRANSFERRING LIQUID REFRIGERANT FROM
THE CHILLER COOLER TO THE CHILLER
CONDENSER OR PUMPOUT STORAGE TANK
• TRANSFERRING LIQUID REFRIGERANT FROM
THE CHILLER CONDENSER OR PUMPOUT
STORAGE TANK TO THE CHILLER COOLER
• DISTILLING THE REFRIGERANT
Pumpout and Refrigerant Transfer
Procedures. . . . . . . . . . . . . . . . . . . . . . . . . . . . . . . . . . . . . . 11
• PREPARATION
• OPERATING THE PUMPOUT UNIT
MAINTENANCE. . . . . . . . . . . . . . . . . . . . . . . . . . . . . . . . . . 17
Pumpout Compressor Oil Charge . . . . . . . . . . . . . . . 17
Storage Tank . . . . . . . . . . . . . . . . . . . . . . . . . . . . . . . . . . . . 17
Ordering Replacement Parts . . . . . . . . . . . . . . . . . . . . 17
TROUBLESHOOTING . . . . . . . . . . . . . . . . . . . . . . . . 17,18
INTRODUCTION
The 19XR Positive Pressure Storage (PPS) system has been
designed to help owners and operators of positive pressure
chillers store HFC-134a refrigerant during service and repair
work. The 19XR system conserves this refrigerant and pre-
vents the release of excessive amounts of refrigerant into the
WARNING
CHECK THE REFRIGERANT TYPE before transferring
refrigerant to the machine. The introduction of the wrong
refrigerant can cause damage or malfunction to this
machine.
Operation of this equipment with refrigerants other than
those cited herein should comply with ASHRAE 15 (latest
edition). Contact Carrier for further information on use of
this machine with other refrigerants.
ENSURE that refrigerant is only pumped to or stored in
tanks that are ASME (American Society of Mechanical
Engineers) certified for the pressures appropriate to the
refrigerant being handled.
DO NOT ATTEMPT TO REMOVE fittings, covers, etc.,
while machine is under pressure or while machine is run-
ning. Be sure pressure is at 0 psig (0 kPa) before breaking
any refrigerant connection.
CAREFULLY INSPECT all relief devices, rupture discs,
and other relief devices AT LEAST ONCE A YEAR. If
machine operates in a corrosive atmosphere, inspect the
devices at more frequent intervals.
DO NOT ATTEMPT TO REPAIR OR RECONDITION
any relief device when corrosion or build-up of foreign
material (rust, dirt, scale, etc.) is found within the valve
body or mechanism. Replace the device.
DO NOT install relief devices in series or backwards.
USE CARE when working near or in line with a com-
pressed spring. Sudden release of the spring can cause it
and objects in its path to act as projectiles.
CAUTION
Failure to follow these procedures may result in personal
injury or damage to equipment.
EQUIPMENT should be operated by certified personnel
only.
DO NOT STEP on refrigerant lines. Broken lines can whip
about and cause personal injury and damage to the
machine.
DO NOT climb over a machine. Use platform, catwalk, or
staging. Follow safe practices when using ladders.
USE MECHANICAL EQUIPMENT (crane, hoist, etc.) to
lift or move inspection covers or other heavy components.
Even if components are light, use such equipment when
there is a risk of slipping or losing your balance.
BE AWARE that certain automatic start arrangements
CAN ENGAGE THE STARTER. Open the disconnect
ahead of the starter in addition to shutting off the machine
or pump.
USE only repair or replacement parts that meet the code
requirements of the original equipment.
DOUBLE-CHECK that coupling nut wrenches, dial indi-
cators, or other items have been removed before rotating
any shafts.
DO NOT LOOSEN a packing gland nut before checking
that the nut has a positive thread engagement.
PERIODICALLY INSPECT all valves, fittings, and piping
for corrosion, rust, leaks, or damage.
DO NOT MIX REFRIGERANT from chillers that use dif-
ferent compressor oils. Compressor damage can result.
(Cautions continued in next column.)
CAUTION
DO NOT re-use compressor oil or any oil that has been
exposed to the atmosphere. Dispose of oil per local codes
and regulations.
DO NOT leave refrigerant system open to air any longer
than the actual time required to service the equipment. Seal
circuits being serviced and charge with dry nitrogen to pre-
vent oil contamination when timely repairs cannot be
completed.

3
atmosphere. The proper use of this equipment minimizes the
loss of HFCs.
The 19XR PPS system shown in Fig. 1 consists of a pump-
out unit mounted on a storage tank. The pumpout unit is
offered as a free-standing unit that can be used with chillers
that have an existing storage tank or with chillers that have iso-
lation valves that permit built-in refrigerant storage.
The 19XR PPS systems are factory tested and certified to
the American Society of Mechanical Engineers (ASME) pres-
sure vessel code. The tanks are constructed of certified steel
and are pressure rated at 185 psig (1276 kPa). The PPS storage
tank is equipped with dual relief valves for proper venting per
ASHRAE 15 (American Society of Heating, Refrigerating, and
Air-Conditioning Engineers) guidelines. An automatic level
switch is prewired to the control circuit to ensure proper stor-
age levels.
The 19XR pumpout unit is a complete, hermetic, compact
unit that consists of:
• a hermetic reciprocating compressor with a direct-drive
motor.
• a water-cooled refrigerant condenser.
• an oil separator.
• suction and discharge valves to control refrigerant flow.
• prewired safety and control devices.
INSTALLATION
Step 1 — Complete Pre-Installation Checks
IDENTIFY UNIT — Identify the assembly number (see
Table 1) printed on the pumpout unit and storage tank name-
plates. Check this information against the job requirements.
Figure 1 shows the PPS system and its major components.
Refer to Tables 2 and 3 for physical data.
INSPECT SHIPMENT — Inspect unit for damage before
removing unit from shipping conveyance. If unit appears dam-
aged, it should be inspected by a shipping inspector before
removal. File a claim with the shipping company if shipment is
damaged or incomplete. The manufacturer is not responsible
for damage incurred during transit.
Check all components. Notify the supplier immediately if
any item is missing. To prevent loss or damage, leave all parts
in their original package until they are needed.
Step 2 — Mount the Pumpout Unit — The
pumpout unit, if purchased separately, may be mounted
directly on the chiller or it may be floor mounted.
MOUNTING ON THE CHILLER — See instructions pro-
vided with the chiller for mounting the pumpout unit. A typical
chiller mount is shown in Fig. 2.
FLOOR MOUNTING — Select a ventilated and accessible
area, free of traffic or other hazards. Remove and discard the
4 angle supports at the base of the pumpout unit and bolt the
unit to the floor through the holes at the base of the pumpout
unit. Special isolation is unnecessary. Contact surface and
dimensions for the pumpout unit are given in Fig. 3.
Table 1 — Positive Pressure System Assembly Numbers (R-134a)
LEGEND NOTES:
1. All storage vessels are 185 psig (1276 kPa) designs per the ASME (Ameri-
can Society of Mechanical Engineers) Boiler Pressure Vessel Code, Sec-
tion VIII Division 1.
2. All units above are shipped with a 15 psig (103 kPa) nitrogen charge.
3. Nominal horsepower for all pumpout units is 3.0.
PUMPOUT
SYSTEM
ARRANGEMENT
NUMBER
PUMPOUT UNIT
ASSEMBLY NUMBER COMPRESSOR MOTOR
(V-PH-Hz) MAXIMUM
RLA LRA STORAGE TANK
19XR04027401 19XR04035801 208/230-3-50/60 15.8 105.0 28 cu ft (0.8 cu m)
19XR04027402 19XR04035802 460-3-60 7.8 52.0 28 cu ft (0.8 cu m)
19XR04027403 19XR04035803 400-3-50 7.8 52.0 28 cu ft (0.8 cu m)
19XR04027501 19XR04035801 208/230-3-50/60 15.8 105.0 52 cu ft (1.5 cu m)
19XR04027502 19XR04035802 460-3-60 7.8 52.0 52 cu ft (1.5 cu m)
19XR04027503 19XR04035803 400-3-50 7.8 52.0 52 cu ft (1.5 cu m)
19XR04026801 19XR04035801 208/230-3-50/60 15.8 105.0 Free-standing
19XR04026802 19XR04035802 460-3-60 7.8 52.0 Free-standing
19XR04026803 19XR04035803 400-3-50 7.8 52.0 Free-standing
19XR14017801 19XR04035801 208/230-3-50/60 15.8 105.0 Unit-mounted, frame 1
19XR14017802 19XR04035802 460-3-60 7.8 52.0 Unit-mounted, frame 1
19XR14017803 19XR04035803 400-3-50 7.8 52.0 Unit-mounted, frame 1
19XR34017801 19XR04035801 208/230-3-50/60 15.8 105.0 Unit-mounted, frame 2 or 3
19XR34017802 19XR04035802 460-3-60 7.8 52.0 Unit-mounted, frame 2 or 3
19XR34017803 19XR04035803 400-3-50 7.8 52.0 Unit-mounted, frame 2 or 3
19XR44017801 19XR04035801 208/230-3-50/60 15.8 105.0 Unit-mounted, frame 4
19XR44017802 19XR04035802 460-3-60 7.8 52.0 Unit-mounted, frame 4
19XR44017803 19XR04035803 400-3-50 7.8 52.0 Unit-mounted, frame 4
19XR54017801 19XR04035801 208/230-3-50/60 15.8 105.0 Unit-mounted, frame 5
19XR54017802 19XR04035803 460-3-60 7.8 52.0 Unit-mounted, frame 5
19XR54017803 19XR04035803 400-3-50 7.8 52.0 Unit-mounted, frame 5
19XR64017801 19XR04035801 208/230-3-50/60 15.8 105.0 Unit-mounted, frame 6
19XR64017802 19XR04035802 460-3-60 7.8 52.0 Unit-mounted, frame 6
19XR64017803 19XR04035803 400-3-50 7.8 52.0 Unit-mounted, frame 6
19XR74017801 19XR04035801 208/230-3-50/60 15.8 105.0 Unit-mounted, frame 7
19XR74017802 19XR04035802 460-3-60 7.8 52.0 Unit-mounted, frame 7
19XR74017803 19XR04035803 400-3-50 7.8 52.0 Unit-mounted, frame 7
19XR84017801 19XR04035801 208/230-3-50/60 15.8 105.0 Unit-mounted, frame 8
19XR84017802 19XR04035802 460-3-60 7.8 52.0 Unit-mounted, frame 8
19XR84017803 19XR04035803 400-3-50 7.8 52.0 Unit-mounted, frame 8
LRA — Locked Rotor Amps
RLA — Rated Load Amps

4
Step 3 — Rig the Storage Tank — The complete
19XR system can be rigged as a single assembly. See the rig-
ging instructions on the label attached to the assembly. Also
refer to the rigging guide (Fig. 4), physical data in Tables 2 and
3, and contact surface and dimensions for the complete sys-
tem in Fig. 5. Lift the assembly only from the 4 points indicated
in the rigging guide. Each rigging cable must be capable of
supporting the entire weight of the assembly.
WARNING
Lifting the assembly from points other than those speci-
fied may result in serious damage to the assembly and
personal injury. Rigging equipment and procedures must
be adequate for assembly. See Tables 2 and 3 for weights.
(These weights are broken down into pumpout unit and
storage tank weights. For the complete assembly weight,
add all components together.)
Fig.1 — 19XR Positive Pressure Storage System
CONTACTOR TERMINAL
STRIP FUSES
TRANSFORMER
SWITCH
19XR PUMPOUT UNIT 19XR CONTROL BOX (INTERIOR)
a19-2444
FRAME
ASSEMBLY
CONTROL
PANEL
VALVE 2
VALVE 4
VALVE 5
VALVE 3
ENTERING
WATER
LEAVING
WATER CONDENSER
OIL
SEPARATOR
OIL
HEATER
COMPRESSOR
a19-2444 a19-1569ef
COMPRESSOR
CONTROL
BOX
VALVE
ASSEMBLY
CONDENSER
OIL
SEPARATOR
Fig. 2 — 19XR Pumpout Unit: Typical Chiller Mount
a19-1570ef

5
NOTE: Dimensions in inches (millimeters).
Fig. 3 — Pumpout Unit Contact Surfaces and Dimensions
(438)
(250)
(337)
(241)
(73)
(116)
(25)
(247)
(333)
(584)
(108)
WATER CONNECTIONS
3/4" FNPT
VAPOR CONNECTIONS
1/2" MALE FLARE
CONDENSER
OIL SIGHTGLASS
COMPRESSOR
VACUUM SWITCH
OIL SEPARATORHIGH-PRESSURE SWITCH
CONTROL PANEL
ELECTRICAL
CONNECTION
LOCATION
23.00
13.12
9.74
1.00
2.88
4.58
9.50
13.25
9.48
19.00
4.25
7.94
(202)
10.50
(267)
(2X) 1.82
(33)
8.21
(209)
11.59
(294)
18.13
(461)
3.25
(83)
24.75
(629)
28.45
(723)
MOUNTING HOLES
ELECTRICAL CONNECTION OPTION LIST
TRADE SIZE
(in.) QTY LOCATION
1/21TOP
3/41BOTTOM
11 MIDDLE
11/41 MIDDLE
a19-2445
Fig. 4 — Rigging Guide
NOTES:
1. Each chain must be capable of supporting the entire weight of the machine.
2. Minimum chain length:
28 ft3(0.79 m3) tank — 10-0(3098 mm)
52 ft3(1.47 m3) tank — 15-6(4724 mm)
STORAGE
TANK
SIZE
CENTER OF
GRAVITY
DIMENSIONS
(APPROX.)
ft-in. (mm)
OVERALL DIMENSIONS
(APPROX.)
ft-in. (mm)
EMPTY
WEIGHT
lb (kg)
ABCDE
28 CU FT
(0.8 CU M) 4-91/8
(1451) 1-77/8
(505) 10-5
(3175) 2-43/4
(730) 4-41/4
(1327) 2,385
(1082)
52 CU FT
(1.5 CU M) 6-115/8
(2124) 1-83/4
(527) 14-111/4
(4553) 2-81/2
(826) 4-81/4
(1429) 3,415
(1549)
a19-1572ef

6
Table 2 — Physical Data — 19XR Pumpout Unit
*The pumpout unit weight includes the compressor/condenser, con-
trol box, and the oil separator.
NOTES:
1. The motor is hermetic with thermal protection.
2. The control box is mounted and wired with an ON/OFF/AUTO.
switch according to NEMA 1 (National Electrical Manufacturing
Association).
3. The starter contactor is located in the control box. The over-
loads on the motor are wired and the internal disconnect switch
is supplied by the customer.
Table 3 — 19XR Storage Tank Rated Dry Weight and Refrigerant Capacity
LEGEND
*The above dry weight includes the pumpout unit weight of 164 lb
(75 kg).
Step 4 — Make Piping Connections — Figure 5
represents typical pumpout unit/chiller piping connections.
Standard connections for 1/2-in. OD copper tubing are provid-
ed. Install the field-supplied FPT tee with pipe plug in the pip-
ing as shown in Fig. 5. This tee is used for refrigerant charging.
NOTE: If any field piping runs exceed 50 ft in length, use
7/8-in. OD copper tubing to minimize pressure drop.
Pumpout unit water piping connections are shown in Fig. 5.
Both connections are 3/4-in. NPT (female). A shutoff valve
should be installed in the water line. Provide a means for blow-
ing water from the condenser coil at winter shutdown to
prevent freeze-up damage. Refer to the Job Data for water
piping particulars.
INSTALL VENT PIPING TO RELIEF DEVICES — The
pumpout storage tank is factory-equipped with relief devices.
Refer to Fig. 6 and Table 4 for size and location of the relief
devices. Vent the relief devices to the outdoors in accordance
with ANSI/ASHRAE 15 Safety Code (latest edition) for
Mechanical Refrigeration and all other applicable codes.
Pumpout unit relief devices are set to relieve at 235 psig
(1620 kPa). Storage tank relief devices are set to relieve at
185 psig (1276 kPa).
1. If relief devices are manifolded, the cross-sectional area
of the relief pipe must at least equal the sum of the areas
required for individual relief pipes.
2. Provide a pipe plug near outlet side of each relief device
for leak testing. Provide pipe fittings that allow vent pip-
ing to be disconnected periodically for inspection of valve
mechanism.
3. Piping to relief devices must not apply stress to the
device. Adequately support piping. A length of flexible
tubing or piping near the device is essential on spring-
isolated machines.
4. Cover the outdoor vent with a rain cap and place a con-
densation drain at the low point in the vent piping to pre-
vent water build-up on the atmospheric side of the relief
device.
Step 5 — Make Electrical Connections — See
nameplate on compressor of pumpout unit and Table 1 for
motor electrical data. Wire unit according to the diagram inside
the control box.
Figure 7 is the wiring schematic for a complete system that
includes the 19XR storage tank and the pumpout unit. Figure 8
is the wiring schematic for the pumpout unit. Use this schemat-
ic for installations that do not include an auxiliary pumpout
storage tank.
NOTE: Use copper conductors only.
ENGLISH SI
Pumpout Unit Weight* lb (kg) 164 (75)
Pumpout Condenser Water Flow Rate gpm (L/s) 7-9 (.45-.58)
Pumpout Condenser Water Pressure Drop psig (kPa) 0.3 (2.0)
Maximum Entering Condenser Water Temperature F (C) 85 (29)
Maximum Leaving Condenser Water Temperature F (C) 100 (37)
Relief Valve psig (kPa) 235 (1620)
Condenser Pressure Rating
Refrigerant Side psig (kPa) 450 (3102)
Waterside psig (kPa) 450 (3102)
SIZE
cu ft (cu m) TANK OD
in. (mm) DRY WEIGHT*
lb (kg)
MAXIMUM REFRIGERANT CAPACITY LB (KG)
ASHRAE/ANSI 15 UL 1963
R-134a R-134a
28 (0.8) 24.00 (610) 2334 (1059) 1860 (844) 1716 (778)
52 (1.5) 27.25 (692) 3414 (1549) 3563 (1616) 3286 (1491)
ANSI — American National Standards Institute
ASHRAE — American Society of Heating, Refrigeration,
and Air-Conditioning Engineers
UL — Underwriters’ Laboratories
DANGER
Refrigerant discharged into confined spaces can displace
oxygen and cause asphyxiation.

7
0’- 3 1/2"
[89mm]
2’- 9 7/8"
[860mm]
2’- 5"
[737mm] 0’- 9 7/8"
[249mm]
4’- 9 1/2"
[1451mm]
6’- 4 3/16"
[1935mm]
1" NPT
LIQUID CONN. 0’- 9"
[229mm]
TYPICAL
3’- 1 1/4"
[946mm]
3’- 4 5/8"
[1032mm]
3’- 4 7/8"
[1038mm]
2’- 9 9/16"
[852mm]
VAPOR
3/4" NPT
PUMPOUT CONDENSER
WATER INLET CONN.
1/2" MALE FLARE
VAPOR CONN.
3/4" NPT
PUMPOUT CONDENSER
WATER OUTLET CONN.
ELECTRICAL SERVICE
ACCESS SPACE
20 3/4" X 8 3/4" X 4 1/2"
(BOTH SIDES)
28 CU.FT. [.79 CU. METER]
STORGE TANK WITH PUMPOUT UNIT
10’- 5 "
[3175mm]
NOTES:
1. Denotes center of gravity.
2. Dimensions in [ ] are in millimeters.
3. The weights and center of gravity values given are for an empty
storage tank.
4. For additional information on the pumpout unit, see certified
drawings.
5. Conduit knockout is located on the side of the control box.
6. Storage tank weight: 2334 lb (1059 kg).
TOP VIEW
FRONT VIEW
1’-0 3/4"
[324mm]
3/8" MALE FLARE
RELIEF VALVE CONN.
1/2" DIA. K.O.
ELECTRICAL CONN.
(PUMPOUT POWER)
(FAR SIDE)
3’- 11 3/8"
[1203mm]
3’- 9"
[1143mm]
0’- 3 1/4"
[83mm]
0’- 10"
[254mm]
1’- 7 7/8"
[505mm]
4’- 4 1/4"
[1327mm]
0’- 2 3/4"
[70mm]
0’- 7 15/16"
[202mm]
(FARSIDE)
28 CU FT [0.8 CU METER] STORAGE TANK WITH PUMPOUT UNIT
LEFT SIDE VIEW
2'- 5 3/4"
[756mm]
LEVEL GAGE
0' - 5 1/2"
[140mm]
PRESSURE GAGE
3/8" MALE FLARE
RELIEF VALVE CONN.
1/2" DIA. K.O.
ELECTRICAL CONN.
(PUMPOUT POWER)
2' - 0 3/8"
[619mm] 1' - 7 "
[483mm]
5' - 0 1/4 "
[1530mm]
9' - 10 "
[2997mm]
0' - 5 7/8 "
[149mm]
(2) 1-1/4" NPT RELIEF
VALVE OUTLET (SEE FIELD
INSTALLATION NOTES)
2' - 4 3/4 "
[730mm]
0' - 9 "
[229mm]
TYPICAL
1' - 2 3/8 "
[365mm]
a19-2442
a19-1585
a19-1584
Fig. 5 — Storage Tank with Pumpout Unit

8
2'-6"
[762mm] 3/8" MALE FLARE
RELIEF VALVE CONN.
1/2" DIA. K.O.
ELECTRICAL CONN.
(PUMPOUT POWER)
0'-9"
[229 mm]
TYPICAL
2'-8 1/2"
[826 mm]
1'-4 1/4"
[413 mm]
14'-4 1/2"
[4381mm]
0'-5 7/8"
[149mm]
(2) 1-1/4" NPT RELIEF
VALVE OUTLET (SEE FIELD
INSTALLATION NOTES)
5'-0 1/2"
[1537mm]
1'-7"
[483mm]
2'-0 5/8"
[625mm]
PRESSURE GAGE
0'-5 1/2"
[140mm]
LEVEL GAGE
0’ - 3 3/8"
[86mm]
2’ - 10 1/8"
[867mm]
2’ - 5 1/4"
[742mm]
6’ - 11 5/8"
[2124mm]
0’ - 9 7/8"
[249mm]
7’ - 2 1/4"
[2191mm] 14’ - 11 1/4"
[4553mm]
1" NPT
LIQUID CONN.
52 CU. FT. [1.47 CU. METER]
STORAGE TANK WITH PUMPOUT UNIT
3’ - 8 3/4"
[1137mm]
3’ - 1 7/16"
[951mm]
0’ - 9 "
[229mm]
TYPICAL
3’ - 8 1/2 "
[1130mm]
3’ - 4 1/2"
[1029mm]
ELECTRICAL SERVICE
ACCESS SPACE
20 3/4" X 8 3/4" X 4 1/2"
(BOTH SIDES)
3/4" NPT
PUMPOUT CONDENSER
WATER OUTLET CONN.
1/2" MALE FLARE
VAPOR CONN.
3/4" NPT
PUMPOUT CONDENSER
WATER INLET CONN.
VAPOR
1’ - 0 3/4"
[324mm]
3/8" MALE FLARE
RELIEF VALVE CONN.
1/2" DIA. K.O.
ELECTRICAL CONN.
(PUMPOUT POWER)
(FAR SIDE)
0’ - 0 15/16"
[202mm]
(FARSIDE)
0’ - 2 3/4"
[70mm]
4’ - 3 1/4"
[1302mm]
4’ - 1"
[1225mm]
0’ - 3 1/4"
[83mm]
0’ - 10"
[254mm]
1’ - 8 3/4"
[527mm]
4’ - 8 1/4"
[1429mm]
Fig. 5 — Storage Tank with Pumpout Unit (cont)
NOTES:
1. Denotes center of gravity.
2. Dimensions in [ ] are in millimeters.
3. The weights and center of gravity values given are for an empty
storage tank.
4. For additional information on the pumpout unit, see certified
drawings.
5. Conduit knockout is located on the side of the control box.
6. Storage tank weight: 3414 lb (1549 kg).
FRONT VIEW
TOP VIEW
LEFT SIDE VIEW
52 CU FT [1.5 CU METER] STORAGE TANK WITH PUMPOUT UNIT
a19-2443
a19-1583
a19-1582

9
Table 4 — Relief Devices
STORAGE
TANK SIZE
cu ft (cu m)
RELIEF VALVE
OUTLET SIZE QUANTITY REQUIRED “C” FACTOR
lb air
min kg air
min
28 (0.8) 11/4in. NPT
Female Connector 2 34.5 15.6
52 (1.5) 11/4in. NPT
Female Connector 2 52.3 23.7
SERVICE VALVES
PUMPOUT
COMPRESSOR
PRESSURE RELIEF
VALVE
OIL
SEPARATOR
PUMPOUT
CONDENSER
WATER
CONNECTIONS
23
45
TO TOP OF
STORAGE TANK
STORAGE TANK
VAPOR VALVE
FROM BOTTOM
OF STORAGE TANK
STORAGE TANK
LIQUID REFRIGERANT VALVE
TEE FOR
REFRIGERANT
CHARGING
TO TOP OF
CHILLER
CONDENSER
SEE NOTE
# 1
TO TOP OF
CHILLER
COOLER
SEE NOTES
# 1 AND 2
CHECK
VALVE
SERVICE VALVES
PUMPOUT
COMPRESSOR
PRESSURE RELIEF
VALVE
OIL
SEPARATOR
PUMPOUT
CONDENSER
WATER
CONNECTIONS
23
45
TO TOP OF
STORAGE TANK
STORAGE TANK
VAPOR VALVE
FROM BOTTOM
OF STORAGE TANK
STORAGE TANK
LIQUID REFRIGERANT VALVE
TEE FOR
REFRIGERANT
CHARGING
TO BOTTOM OF
COOLER AND
CHILLER
CONDENSER
SEE NOTE
# 1
TO TOP OF
CHILLER
COOLER
OR CONDENSER
SEE NOTES
# 1 AND 2
TO ADDITIONAL
CHILLERS
CHECK
VALVE
CHILLERS WITHOUT ISOLATION VALVES CHILLERS WITH ISOLATION VALVES
(WITH OR WITHOUT PUMPOUT STORAGE TANKS)
GENERAL PIPING CONNECTION SIZES
NOTES:
1. The field-supplied tubing is to be 1/2-in. OD tubing (min.) and
must be arranged and supported to avoid stresses on the equip-
ment, transmission of vibrations, and interference with routine
access during the reading, adjusting, and servicing of the equip-
ment. If the distance from the chiller to the pumpout unit is over
50 ft, then 7/8-in. OD tubing (min.) must be used. Provisions
should be made for adjustment in each plane of the tubing and
for both periodic and major servicing of the equipment. Special
care must be taken so that the safety head does not experience
tubing strain. Vent the safety head per ASHRAE 15 (American
Society of Heating, Refrigerating, and Air-Conditioning Engi-
neers), latest revision.
2. The tubing and valve from the storage tank to the pumpout com-
pressor is factory supplied when the unit is factory mounted.
CONNECTION SIZE (in.)
Refrigerant Transfer Connections 1/2Flare (male)
Condenser Water Cooling Connectors 3/4NPT (female)
Safety Relief Head Pumpdown 3/8Flare (male)
LEGEND
Factory-Supplied Tubing
Field-Supplied Tubing
Field-Supplied Tubing (Multiple Chillers)
Service Valve (Factory Supplied)
Service Valve (Field Supplied)
Fig. 6 — Typical Pumpout Unit/Chiller Connection Schematic
a19-1575ef a19-1576ef

10
Fig. 7 — 19XR Pumpout System Wiring Schematic
a19-2447
LOW PRESSURE CONTROL
NC OPEN < 7 psia (-15.7 in. HG)
CLOSE > 9 psia (-11.6 in. HG)
HIGH PRESSURE
SAFETY
NC OPEN > 185psig
CONTROL POWER
TRANSFORMER
XFMR-1
69 VA
PUMP OUT
COMPRESSOR
CRANKCASE HEATER
240-600v
27-40 WATT
COPELAND PN 081-0031-03
WHT
RED
ORN
HIGH LEVEL
GAGE ALARM
(NC-OPEN AT
90% STORAGE
TANK LEVEL)
WHT
X2
C
5
4
X2
X2
1
X1
FU3
0.5A
H1 H4
FU1
FU2
0.25A
0.25A
GND
2
23
SS-1
OFF
AUTO ON
2
L2
L1 8
7
HTR-1
MTR-1
2 OL
2 OL
2 OL
C
C
C
LEVEL GAGE
ALARM SWITCH
NO
NC
LEGEND
C—Contactor
FU — Fuse
GND — Ground
HTR — Heater
MTR — Motor
NC — Normally Closed
OL — Overload
SS — Selector Switch
Fig. 8 — Pumpout Unit Wiring Schematic
a19-2448
LOW PRESSURE CONTROL
NC OPEN < 7 psia {-15.7 in. HG}
CLOSE > 9 psia {-11.6 in. HG}
HIGH PRESSURE
SAFETY
NC OPEN > 185psig
CONTROL POWER
TRANSFORMER
XFMR-1
69 VA
PUMP OUT
COMPRESSOR
CRANKCASE HEATER
240-600v
27-40 WATT
X2
C
5
4
X2
X2
1
X1
FU3
0.5A
H1 H4
FU1
FU2
0.25A
0.25A
GND
2
23
SS-1
OFF
AUTO ON
2
L2
L1 8
7
HTR-1
MTR-1
2 OL
2 OL
2 OL
C
C
C
LEGEND
C—Contactor
FU — Fuse
GND — Ground
HTR — Heater
MTR — Motor
NC — Normally Closed
OL — Overload
SS — Selector Switch

11
CONTROLS AND COMPONENTS
Figure 1 shows the major components of the PPS system.
Pumpout Unit — The pumpout unit consists of a
hermetic reciprocating compressor, a water cooled refrigerant
condenser, an oil separator, and prewired safety and control
devices. The pumpout unit comes equipped with a 4-way
transfer valve manifold to interconnect both liquid and vapor
transfer and to pressurize the chiller during transfer of refriger-
ant from chiller to storage tank.
CONTROLS — The pumpout unit has the following controls:
manual/off/automatic selector switch, transformer, .25 amp
fuses for the primary side of the transformer, 5 amp fuse for the
secondary side of the transformer, contactor, terminal strip,
high pressure cutout switch and low pressure switch.
SAFETY CONTROL SETTINGS — The pumpout unit high-
pressure switch (Fig. 3) is set to open at the settings listed in
Table 5. The switch setting is checked by operating the pumpout
condenser and slowly throttling the pumpout condenser water.
When the selector switch is in the Automatic position, the
pumpout will cycle on a low pressure/vacuum switch. This
switch will shut down the pumpout compressor when suction
pressure reaches 7 ± 1.5 psia or 15 ± 3 in. Hg vacuum
(51.7 kPa absolute). When the selector switch is in the On
position, the pumpout compressor will continue to run until
refrigerant vapor flow is so low that the compressor motor
overheats. At this time the compressor motor overload will
shut off the compressor. This is NOT recommended.
Table 5 — High Pressure Switch Settings
COMPRESSOR — The hermetic compressor assembly
comes equipped with internal thermal protection on the motor
and a self-regulating crankcase heater.
CONDENSER — The water-cooled condenser is a brazed
plate heat exchanger. During transfer, it condenses refrigerant
vapor to liquid.
OIL SEPARATOR — The pumpout unit includes an in-line
oil separator to remove oil that becomes mixed with refrigerant
and returns the oil to the compressor.
SUCTION AND DISCHARGE VALVES — The pumpout
unit comes with a 4-way transfer valve manifold to intercon-
nect both liquid and vapor transfer and to pressurize the chiller
during transfer of refrigerant from chiller to storage tank or
from one chiller vessel to another.
Storage Tank — The storage tank is rated for positive
pressure refrigerants under ASME Section VIII pressure vessel
codes with a minimum of 185 psig (1276 kPa) rating. The tank
components include:
DRAIN VALVE — Located at its lowest point of drain with a
minimum of 1 in. NPT.
DUAL RELIEF VALVES — Two relief valves and a 3-way
shut-off valve.
PRESSURE GAGE — A 30 in. Hg vacuum -0-400 psig
(101-0-2760 kPa) compound pressure gage.
LEVEL GAGE — Liquid level gage (magnetically coupled
dial type) with electronic shut-off at 90% liquid capacity.
OPERATION
Overview — Transferring refrigerant from one vessel to
another is accomplished by using either gravity or pressure
differential. A difference in elevation between 2 vessels results
in a gravity flow of liquid; a difference in pressure forces the
liquid from one vessel to the other. The latter method requires
lowering the pressure in one vessel. If there is liquid in that
vessel, its temperature must be lowered, and the pressure in the
other vessel must be simultaneously increased.
Under most circumstances, creating the pressure differential
is not a difficult process. Some applications, such as ice
storage, outdoor installations, or installations with high tem-
perature differentials between the storage tank and the chiller
may require additional consideration. In some instances, it may
be necessary to add auxiliary heat to one of the vessels or to in-
sulate the storage tank at job sites where high ambient tempera-
ture or sun load make it difficult to reduce the temperature and
pressure in the tank. Outdoor installations must have a roof or
cover over the storage tank to ensure that the pressure in the
tank does not exceed the chiller relief pressure setting.
REFRIGERANT TRANSFER — When refrigerant is being
evacuated from the chiller cooler or condenser vessels, any
liquid refrigerant left in a vessel will flash off, lowering the
temperature in that vessel enough to freeze the fluid (usually
water) flowing through the cooler or condenser tubes. This
event, called tube freeze-up, can cause extensive damage to the
chiller; therefore, all liquid refrigerant must be removed from a
vessel before evacuation of refrigerant vapor is started. If all
the liquid cannot be removed, then the cooler water and con-
denser water pumps must be operated throughout the process
of evacuating refrigerant vapor to keep fluid moving through
the cooler and condenser tubes.
TRANSFERRING LIQUID REFRIGERANT FROM THE
CHILLER COOLER TO THE CHILLER CONDENSER
OR PUMPOUT STORAGE TANK — Chiller and pumpout
unit valves are set to permit the pumpout compressor to
discharge refrigerant vapor into the cooler vessel, lowering
pressure in the condenser vessel/storage tank. The pressure
differential forces liquid from the cooler vessel into the con-
denser vessel/storage tank. After all the liquid is transferred, the
refrigerant vapor remaining in the cooler vessel can be drawn
off by reducing pressure in the chiller and discharging the
vapor through the pumpout unit condenser into the condenser
vessel/storage tank.
NOTE: The pumpout selector switch can be placed in On
or Automatic mode. In Automatic mode, the compressor will
shut off automatically once the suction pressure drops to 7 psia
or 15 in. Hg vacuum (51.7 kPa absolute). In On mode, the unit
will continue to pumpout regardless of the suction (vacuum)
pressure.
TRANSFERRING LIQUID REFRIGERANT FROM THE
CHILLER CONDENSER OR PUMPOUT STORAGE
TANK TO THE CHILLER COOLER — Chiller and pump-
out unit valves are set to increase pressure in the chiller
condenser vessel/storage tank and to reduce pressure in the
cooler vessel. Pressure in the cooler vessel is lowered to corre-
spond to a saturated refrigerant liquid temperature 2° F (1.1° C)
above the freezing temperature of the liquid circulating through
the chiller cooler/condenser tubes (34 F [1.1 C] for water). The
valves are set so that the pressure in the cooler vessel is lower
than that of the condenser vessel/storage tank, forcing the liq-
uid into the cooler vessel.
NOTE: The pumpout selector switch can be placed in On or
Automatic mode. In Automatic mode, the compressor will shut
off automatically once the suction pressure drops to 7 psia or
15 in. Hg vacuum (51.7 kPa absolute). In On mode, the unit
will continue to pumpout regardless of the suction (vacuum)
pressure.
REFRIGERANT HIGH-PRESSURE SWITCH
CUTOUT CUT-IN
R-134a 185 ± 10 psig
(1276 ± 69 kPa) 140 ± 10 psig
(965 ± 69 kPa)
WARNING
During transfer of refrigerant into and out of the pumpout
storage tank, carefully monitor the storage tank level gage.
Do not fill the tank more than 90% of capacity to allow for
refrigerant expansion. Overfilling may result in damage to
the tank and personal injury. For maximum refrigerant
capacity, refer to Table 3.

12
NOTE: During this operation, maintain water circulation
through the chiller cooler and condenser vessels to prevent
tube freeze-up.
DISTILLING THE REFRIGERANT — Refrigerant vapor is
transferred from the chiller cooler vessel or pumpout storage
tank through the pumpout condenser, condensed to a liquid,
and pumped to the chiller condenser vessel. During this opera-
tion, water circulation must be maintained in the pump-out
condenser. Refrigerant impurities left in the chiller cooler ves-
sel or storage tank are then drained off. This operation can take
from 4 to 14 hours, depending on the type and amount of re-
frigerant being distilled.
The Pumpout and Refrigerant Transfer Procedures section
gives step-by-step instructions on performing these operations.
Pumpout and Refrigerant Transfer
Procedures
PREPARATION — The 19XR chiller may come equipped
with an optional pumpout storage tank, pumpout system, or
pumpout compressor. The refrigerant can be pumped for ser-
vice work to either the chiller compressor vessel or chiller con-
denser vessel by using the optional pumpout system. If a
pumpout storage tank is supplied, the refrigerant can be iso-
lated in the storage tank. The following procedures describe
how to transfer refrigerant from vessel to vessel and perform
chiller evacuation.
OPERATING THE OPTIONAL PUMPOUT UNIT (Fig. 9)
— Oil should be visible in the pumpout unit compressor sight
glass under all operating conditions and during shutdown. If oil
is low, add oil as described under Maintenance section, page
17. The pumpout unit control wiring schematic is detailed in
Fig. 8.
To Read Refrigerant Pressures (during pumpout or leak test-
ing):
1. The ICVC display on the chiller control panel is suitable
for determining refrigerant-side pressures and low (soft)
vacuum. To assure the desired range and accuracy when
measuring evacuation and dehydration, use a quality
vacuum indicator or manometer. This can be placed on
the Schrader connections on each vessel by removing the
pressure transducer.
2. To determine pumpout storage tank pressure, a 30 in. Hg
vacuum -0-400 psi (-101-0-2769 kPa) gage is attached to
the storage tank.
3. Refer to Fig. 10 and 11 for valve locations and numbers.
Positive Pressure Chillers With Storage Tanks — In the
Valve/Condition tables that accompany these instructions, the
letter “C” indicates a closed valve. Figures 9 and 10 show the
locations of the valves.
CAUTION
The power to the pumpout compressor oil heater must be
on whenever any valve connecting the pumpout compres-
sor to the chiller or storage tank is open. Leaving the heater
off will result in oil dilution by refrigerant and can lead to
compressor failure.
If the compressor is found with the heater off and a
valve open the heater must be on for at least 4 hours to
drive the refrigerant from the oil. When heating the oil the
compressor suction must be open to a vessel to give the re-
frigerant a means to leave the compressor.
CAUTION
Always run the chiller cooler and condenser water pumps
and always charge or transfer refrigerant as a gas when the
chiller pressure is less than 35 psig (241 kPa). Below these
pressures, liquid refrigerant flashes into gas, resulting in
extremely low temperatures in the cooler/condenser tubes
and possibly causing tube freeze-up.
DANGER
During transfer of refrigerant into and out of the optional
storage tank, carefully monitor the storage tank level gage.
Do not fill the tank more than 90% of capacity to allow for
refrigerant expansion. Overfilling may result in damage to
the tank or the release of refrigerant which will result in
personal injury or death.
CAUTION
Do not mix refrigerants from chillers that use different
compressor oils. Compressor damage can result. The
pumpout oil separator comes pre-charged with 13 oz of
ISO viscosity 220 POE (Polyol Ester) oil. The pumpout
compressor is approved for use with ISO viscosity 220
POE oil or ISO viscosity 68 POE oil. The pumpout com-
pressor is also factory precharged with oil.
CAUTION
Transfer, addition, or removal of refrigerant in spring-
isolated chillers may place severe stress on external piping
if springs have not been blocked in both up and down
directions.
CAUTION
Always run chiller cooler and condenser water pumps and
always charge or transfer refrigerant as a gas when chiller
vessel pressure is less than 35 psig (241 kPa). Below these
pressures, liquid refrigerant flashes into gas, resulting in
extremely low temperatures in the cooler/condenser tubes
and possibly causing tube freeze-up.
CAUTION
The power to the pumpout compressor oil heater must be
on whenever any valve connecting the pumpout compres-
sor to the chiller or storage tank is open. Leaving the heater
off will result in oil dilution by refrigerant and can lead to
compressor failure.
If the compressor is found with the heater off and a valve
open the heater must be on for at least 4 hours to drive the
refrigerant from the oil. When heating the oil the compres-
sor suction must be open to a vessel to give the refrigerant
a means to leave the compressor.

13
Transfer Refrigerant from Storage Tank Vessel to Chiller
1. Equalize refrigerant pressure.
a. Turn on chiller water pumps, establishing water
flow (assumes vacuum condition in chiller sys-
tem).
b. Close pumpout and storage tank valves 2, 4, 5, 7,
8, 10 (if present open isolation valve 11 and other
isolation valves between cooler and condenser).
Open storage tank valve 6; open chiller valves 1A
and 1B.
c. Gradually open valve 5 to slowly increase chiller
pressure to 35 psig (241 kPa) to reduce the poten-
tial of tube freeze up.
d. Open valve 5 fully after the chiller pressure
reaches 35 psig (241 kPa) or greater. Let chiller
pressure reach 40 psig (276 kPa), then chiller water
pumps can be turned off. Fully close valve 5.
e. Open valve 8 and 10 to let higher pressure in the
recovery tank push liquid refrigerant into the con-
denser float chamber and heat exchangers until the
refrigerant pressure equalizes between the recov-
ery tank and chiller.
2. Push liquid to chiller, them remove remaining vapor from
storage tank:
a. To prepare for liquid, push open valve 4.
b. Ensure pumpout condenser water is off, then turn
on the pumpout compressor in manual mode to
push liquid to chiller. Monitor the storage tank
level until tank is empty of liquid refrigerant.
c. Close charging valves 8 and 10.
d. Turn off the pumpout compressor.
e. To prepare for removal of remaining refrigerant
vapor in storage tank, close pumpout valves 3 and
4 and open valves 2 and 5.
f. Turn on pumpout condenser water.
g. Run pumpout unit in auto until the vacuum switch
is satisfied. This occurs approximately at 15 in Hg
vacuum (48 kPa absolute or 7 psia), removing the
residual refrigerant vapor from the recovery tank
and condensing to a liquid in the chiller.
h. Close valves 1A, 1B, 2, 5, 6.
i. Turn off pumpout condenser water.
Transfer Refrigerant from Chiller to Storage Tank Vessel
1. Equalize refrigerant pressure.
a. Dehydrate the refrigerant storage vessel, and con-
nected hoses/piping so there are no non-condens-
ables mixed with the refrigerant.
b. Locate valves as identified below:
c. Slowly open valve 5 until the refrigerant pressure
reaches 35 psig (241 kPa) in the storage
Fig. 9 — Pumpout Unit
OIL FILL 1/4-IN. FLARE VALVE
a19-2446
FRAME
ASSEMBLY
CONTROL
PANEL
VALVE 2
VALVE 4
VALVE 5
VALVE 3
ENTERING
WATER
LEAVING
WATER CONDENSER
OIL
SEPARATOR
OIL
HEATER
COMPRESSOR
a19-
2444
WARNING
During transfer of refrigerant into and out of the 19XR
storage tank, carefully monitor the storage tank level gage.
Do not fill the tank more than 90% of capacity to allow for
refrigerant expansion. Overfilling may result in damage to
the tank and personal injury.
VALVE 1A1B23456781011
CONDITION C C C C C C
VALVE 1A1B23456781011
CONDITION C C C C C C
VALVE 1A1B23456781011
CONDITION C C C C
VALVE 1A1B23456781011
CONDITION C C C
VALVE 1A1B23456781011
CONDITION C C C C C
VALVE 1A1B23456781011
CONDITIONCCCCCCCCCC
VALVE 1A1B23456781011
CONDITION C C C C C C

14
tank, followed by valves 7 and 10 to allow liquid
refrigerant to drain by gravity.
2. Push remaining liquid, followed by refrigerant vapor re-
moval from chiller.
a. To prepare for liquid push, turn off the pumpout
condenser water. Place valves in the following
positions:
b. Run the pumpout compressor in manual until all
liquid is pushed out of the chiller (approximately
45 minutes). Close valves 2, 5, 7, and 10, then stop
compressor.
c. Turn on pumpout condenser water.
d. Open valves 3 and 4, and place valves in the fol-
lowing positions:
e. Run the pumpout compressor until the chiller pres-
sure reaches 35 psig (241 kPa), followed by turn-
ing off the pumpout compressor. Warm chiller
condenser water will boil off any entrapped liquid
refrigerant, and chiller pressure will rise.
f. When chiller pressure rises to 40 psig (276 kPa),
turn on the pumpout compressor until the pressure
reaches 35 psig (241 kPa) again; then turn off the
pumpout compressor. Repeat this process until the
chiller pressure no longer rises.
g. Start the chiller water pumps (condenser and
cooler), establishing water flow. At this point, turn
on the pumpout compressor in auto until the vac-
uum switch is satisfied. This occurs at approxi-
mately 15 in Hg vacuum (48 kPa absolute or
7psia).
h. Close valves.
i. Turn off the pumpout condenser water.
Chillers With Isolation Valves — In the Valve/Condition ta-
bles that accompany these instructions, the letter “C” indicates
a closed valve.
The valves referred to in the following instructions are
shown in Fig. 9 and 11. The cooler/condenser vessels can be
used for refrigerant isolation for certain service conditions
when the isolation valve package is specified.
Transfer Refrigerant from Cooler to Condenser
a. Turn off chiller water pumps and pumpout con-
denser water supply (if applicable). It is assumed
that the starting point is as shown in the following
table and that pressures in both vessels are above
35 psig (241 kPa).
b. Keeping valves 7 and 8 closed, install charging
hose from liquid line charging valve 7 to valve 8
on the condenser float chamber. Evacuate or purge
hose of non-condensables. Note that this creates a
flow path between cooler and condenser that
bypasses the linear float, reducing the potential for
damage during refrigerant transfer.
c. Open valves 1A, 1B, 2, 5, and 8.
d. Turn on pumpout compressor, generating a refrig-
erant pressure differential of 10 to 20 psi (69 to
138 kPa) to push liquid out of the chiller cooler
vessel.
e. Slowly open valve 7 to allow liquid transfer. Rapid
opening of valve 7 can result in float valve dam-
age.
f. When all liquid has been pushed into the chiller
condenser vessel, close valve 8.
g. Turn off the pumpout compressor.
h. Close pumpout valves 2 and 5 while opening valve
3 and 4 to prepare for removal of remaining refrig-
erant vapor in cooler vessel.
i. Turn on pumpout condenser water.
j. Turn on pumpout compressor. Turn on the chiller
water pump to establish water flow when the
cooler refrigerant pressure is 35 psig (241 kPa).
The water pumps have to be in operation when-
ever the refrigerant pressure is equal to or less
than 35 psig (241 kPa) to reduce the potential of
tube damage.
k. Run the pumpout compressor until the cooler pres-
sure reaches 35 psig (241 kPa), then turn off the
pumpout compressor. Warm chiller cooler water
will boil off any entrapped liquid refrigerant, and
chiller pressure will rise. Repeat this process until
the chiller pressure no longer rises.
l. Run pumpout unit in auto until the vacuum switch
is satisfied; this occurs at approximately 15 in. Hg
vacuum (48 kPa absolute or 7 psia). Close valve
1A.
m. Monitor that cooler pressure does not rise (if it
does, then repeat previous step).
n. With service valve 1A closed, shut down pumpout
compressor (if still running).
o. Close remaining valves.
p. Remove charging hose between 7 and 8 (evacuate
prior to removal).
q. Turn off pumpout condenser water.
r. Turn off chiller water pumps, and lockout chiller
compressor.
Transfer Refrigerant from Condenser to Cooler
a. Turn off chiller water pumps and pumpout con-
denser water supply (if applicable). It is assumed
that the starting point is as shown in the following
VALVE 1A1B23456781011
CONDITION C C C
VALVE 1A1B23456781011
CONDITION C C C
VALVE 1A1B23456781011
CONDITION C C C C C C C
VALVE 1A1B23456781011
CONDITION C C C C C
VALVE 1A1B23456781011
CONDITIONCCCCCCCCCC
VALVE 1A1B23457811
CONDITION CCCCCCCCC
VALVE 1A1B23457811
CONDITION C C C C
VALVE 1A1B23457811
CONDITION C C C C
VALVE 1A1B23457811
CONDITION C C C C
VALVE 1A1B23457811
CONDITION C C C C C
VALVE 1A1B23457811
CONDITION CCCCCCCCC

15
table and that pressures in both vessels are above
35 psig (241 kPa).
b. Set valves as shown below to allow the refrigerant
to equalize:
c. Turn on pumpout compressor, and develop a 10 to
20 psi (69 to 138 kPa) refrigerant differential pres-
sure between the vessels.
d. Partially open valve 11 while maintaining a refrig-
erant pressure differential to push liquid refrigerant
out of the chiller condenser to the cooler.
e. When all liquid is out of the chiller condenser,
close valve 11 and any other isolation valves on the
chiller.
f. Turn off the pumpout compressor.
g. Close pumpout valves 3 and 4 while opening valve
2 and 5 to prepare for removal of remaining refrig-
erant vapor in condenser vessel.
h. Turn on pumpout condenser water.
i. Turn on pumpout compressor.
j. Turn on the chiller water pumps, establishing water
flow when the condenser refrigerant pressure is 35
psig (241 kPa). The water pumps have to be in
operation whenever the refrigerant pressure is
equal to or less than 35 psig (241 kPa) to reduce
the potential of tube damage.
k. Run the pumpout compressor until the condenser
refrigerant pressure reaches 35 psig (241 kPa) then
turn off the pumpout compressor. Warm condenser
water will boil off any entrapped liquid refrigerant,
and chiller pressure will rise. Repeat this process
until the chiller pressure no longer rises.
l. Run pumpout unit in auto until the vacuum switch
is satisfied; this occurs at approximately 15 in. Hg
vacuum (48 kPa absolute or 7 psia). Close
valve 1B.
m. Monitor that condenser pressure does not rise (if it
does, then repeat previous step).
n. With service valve 1B closed, shut down pumpout
compressor (if still running).
o. Close remaining valves.
p. Turn off pumpout condenser water.
q. Turn off chiller water pumps, and lock out chiller
compressor.
Return Chiller to Normal Operating Conditions
1. Vapor Pressure Equalization:
a. Ensure that the chiller vessel that was exposed to
ambient has been evacuated. Final vacuum prior to
charging with refrigerant should in all cases be
29.9 in. Hg (500 microns, 0.07 kPa [abs]) or less.
b. Turn on chiller water pumps.
c. Open valves 1A, 1B, and 2.
d. Slowly open valve 4, gradually increasing pressure
in the evacuated vessel to 35 psig (241 kPa).
e. Leak test to ensure chiller vessel integrity.
f. Open valve 4 fully for cooler and condenser pres-
sure equalization (vapor equalization).
g. Close valves 1A, 1B, 2, and 4.
2. Liquid equalization:
a. If refrigerant is stored in cooler, install a charging
hose between valves 7 and 8, and open both the
valves and any other isolation valves (except valve
11) for liquid to drain into the condenser while
bypassing the linear float valve. If refrigerant is
stored in the condenser, keep valve 11 and any
other isolation valves open for liquid drain.
b. If valves 7 and 8 were used to bypass the linear
float valve, once the liquid transfer is complete,
close these valves, and slowly open valve 11.
c. Turn off chiller water pumps.
Distilling the Refrigerant
1. Transfer the refrigerant from the chiller to the pumpout
storage tank as described in the Transfer Refrigerant from
Chiller to Storage Tank Vessel section.
2. Equalize the refrigerant pressure.
a. Turn on chiller water pumps and monitor chiller
pressures.
b. Close pumpout and storage tank valves 2, 4, 5, and
10, and close chiller charging valve 7; open chiller
isolation valve 11 and any other chiller isolation
valves, if present.
c. Open pumpout and storage tank valves 3 and 6;
open chiller valves 1a and 1b.
d. Gradually crack open valve 5 to increase chiller
pressure to 35 psig (241 kPa). Slowly feed refriger-
ant to prevent freeze-up.
e. Open valve 5 fully after the chiller pressure rises
above the freezing point of the refrigerant. Let the
storage tank and chiller pressure equalize.
3. Transfer remaining refrigerant.
a. Close valve 3.
b. Open valve 2.
c. Turn on pumpout condenser water.
VALVE 1A1B23457811
CONDITION CCCCCCCCC
VALVE 1A1B23457811
CONDITION C C C C C
VALVE 1A1B23457811
CONDITION C C C C C
VALVE 1A1B23457811
CONDITION C C C C C C
VALVE 1A1B23457811
CONDITION CCCCCCCCC
VALVE 1A1B23457811
CONDITION C C C C C C
VALVE 1A1B23457811
CONDITION C C C C C
VALVE 1A1B23457811
CONDITION CCCCCCCCC
VALVE 1A1B23457811
CONDITION
(CHARGE IN
COOLER) CCCCCC C
CONDITION
(CHARGE IN
CONDENSER) CCCCCCCC
VALVE 1A1B2345671011
CONDITION C C C C C
VALVE 1A1B2345671011
CONDITION C C C C

16
d. Run the pumpout compressor until the storage tank
pressure reaches 5 psig (34 kPa), 18 in. Hg vacuum
(41 kPa absolute) in Manual or Automatic mode.
e. Turn off the pumpout compressor.
f. Close valves 1a, 1b, 2, 5, and 6.Turn off pumpout
condenser water.
4. Drain the contaminants from the bottom of the storage
tank into a container. Dispose of contaminants safely.
VALVE 1A1B2345671011
CONDITION CCCCCCCCC
a19-2434
6
10
7
1a
11
8
1b
5
3
4
2
PUMPOUT
COMPRESSOR
RELIEF
VALVE
PUMPOUT
CONDENSER
CHECK
VALVE
CONDENSER
COOLER
STORAGE VESSEL
OIL
SEPARATOR
Fig. 10 — Typical Optional Pumpout System Piping Schematic with Storage Tank
NOTES:
1. Maintain at least 2 feet (610 mm) clearance around storage tank for service and operation work.
2. Valve 8 is only applicable for products with linear float valves.

17
MAINTENANCE
Periodic maintenance is necessary to keep all components
functioning as designed. A maintenance log is recommended
to ensure a proper maintenance schedule is followed.
Pumpout Compressor Oil Charge — Use oil con-
forming to Carrier specifications for centrifugal or screw com-
pressor use. Oil requirements are listed in Table 6.
Monitor and adjust compressor oil level as often as
necessary. When replacing lost oil, add the same type of oil that
is used in the chiller being pumped out.
Table 6 — Pumpout Compressor Requirements
The pumpout oil separator comes pre-charged with 13 oz of
ISO viscosity 220 POE (Polyol Ester) oil. The pumpout com-
pressor is approved for use with ISO viscosity 220 POE oil or
ISO viscosity 68 POE oil. The pumpout compressor is also fac-
tory precharged with POE oil.
Oil should be visible in the pumpout compressor sight glass
both during operation and at shutdown. Always check the oil
level before operating the pumpout compressor.
Oil can be added to the 1/4-in. SAE flare access valve port
running from the top of the oil separator to the compressor
while the compressor is running. Be careful not to overfill.
NOTE: Compressor access valve has a self-sealing fitting
which will require a hose connection with a depressor to open.
To change or remove oil, the compressor will have to be re-
moved from the assembly. Compressor can be disconnected
from connected tubing by the quick connect fittings at suction
and discharge and oil recovery line.
Prior to removal, close service valves 2, 3, 4, and 5, and run
the pumpout compressor in AUTOMATIC until the vacuum
switch is satisfied and the compressor shuts off.
Move pumpout selector switch to OFF, and turn off all power
to unit prior to removing compressor unit from pumpout as-
sembly frame and connecting tubing.
Service valves 2, 3, 4, and 5 remain closed while compres-
sor is removed. Put compressor back in place. Use the torque
values listed in Table 7 for reassembly:
Table 7 — Torque Values for Reassembly
Be sure to use backup wrench and pull a deep vacuum in the
serviced pumpout tubing prior to any refrigerant exposure. At
this point, confirm that the oil level is satisfactory and put the
pumpout back in service.
Storage Tank — To prevent moisture and contaminants
from entering the storage tank, maintain positive pressure in
the tank when not transferring refrigerant. Leak test the storage
tank periodically.
Ordering Replacement Parts — The following in-
formation must accompany an order for Carrier-specified parts:
• machine model number and serial number
• name, quantity, and part number of the part required
• delivery address and method of shipment
TROUBLESHOOTING
Information on troubleshooting for the PPS system is in-
cluded in Table 8.
a19-2435
7
1a
11
8
1b
5
3
4
2
PUMPOUT
COMPRESSOR
OIL
SEPARATOR
RELIEF
V
ALVE
PUMPOUT
CONDENSER
CHECK
VALVE
CONDENSER
COOLER
Fig. 11 — Typical Optional Pumpout System Piping Schematic without Storage Tank
NOTE: Valve 8 is only applicable for products with linear float valves.
REFRIGERANT ISO
VISCOSITY CARRIER
SPECIFICATION NO.
R-134a 68 PP47-31
220 PP47-32
PARAMETER VALUES
ft-lb Nm
Suction 80 to 100 109 to 136
Discharge 50 to 60 68 to 81
O-ring Face Seal 7 to 9 10 to 12

18
Table 8 — Troubleshooting
SYMPTOM PROBABLE CAUSE REMEDY
Compressor Does Not
Run Main power line open Replace fuse or reset circuit breaker.
Loose terminal connection Check connections.
Improperly wired controls Check wiring and rewire.
Low line voltage Check line voltage; determine location of voltage drop.
Compressor motor defective Check motor winding for open or short. Replace compressor if
necessary.
Seized compressor Replace compressor.
High level gage alarm Check refrigerant level and remove excess.
Compressor Cycles On
High-Pressure Control High-pressure control erratic in action Check capillary tube for pinches. Set control as required.
Discharge valve partially closed. Open valve.
Air in system Purge system.
Condenser scaled. Clean condenser.
Condenser water pump or fans not
operating. Start pump or fans.
Unit Operates Too Long Isolation valves partially open Close valves.
System Noises Piping vibrations Support piping as required. Check for loose pipe connectors.
Insufficient compressor oil Add oil.
Compressor Loses Oil Leak in system Locate and repair leak.
Plugged or stuck compressor oil return
check valve Repair or replace valve.
Liquid refrigerant carries oil out of
compressor Check to ensure only refrigerant vapor enters compressor suc-
tion line. Add oil as necessary.
Motor shutdown on internal thermal protec-
tion high temperature cutout. High temperature cutout should reset within 120 minutes.


Manufacturer reserves the right to discontinue, or change at any time, specifications or designs without notice and without incurring obligations.
Catalog No. 04-531900050-01 Printed in U.S.A. Form 19XR-CLT-16SI Pg 20 5-17 Replaces: 19XR-6SI
© Carrier Corporation 2017
This manual suits for next models
33
Table of contents
Other Carrier Storage manuals
Popular Storage manuals by other brands
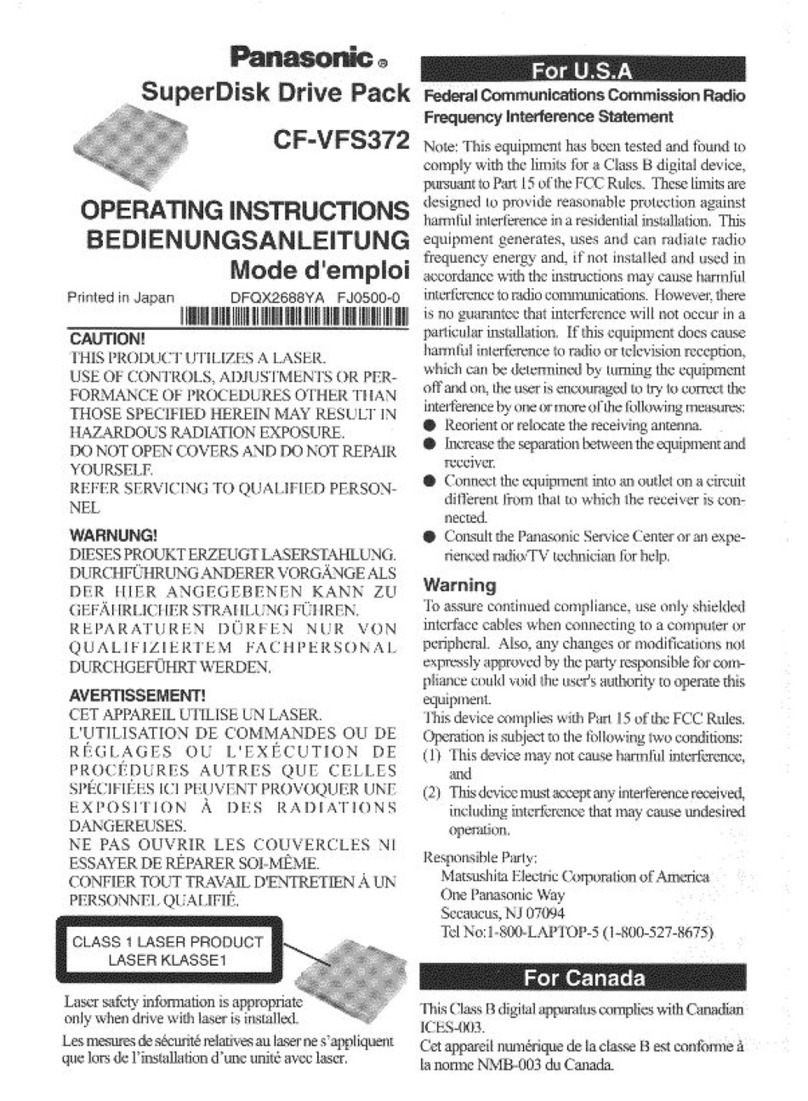
Panasonic
Panasonic CF-VFS372 operating instructions
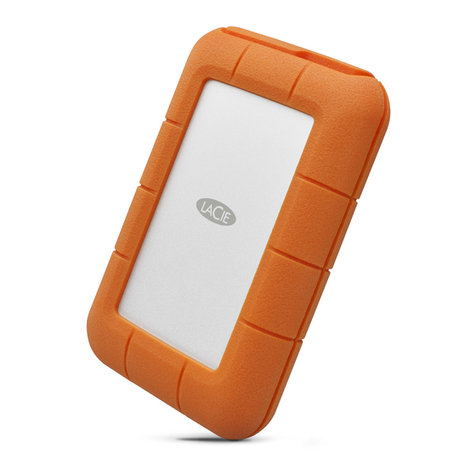
LaCie
LaCie Rugged USB 3.0 Thunderbolt™ Series user manual
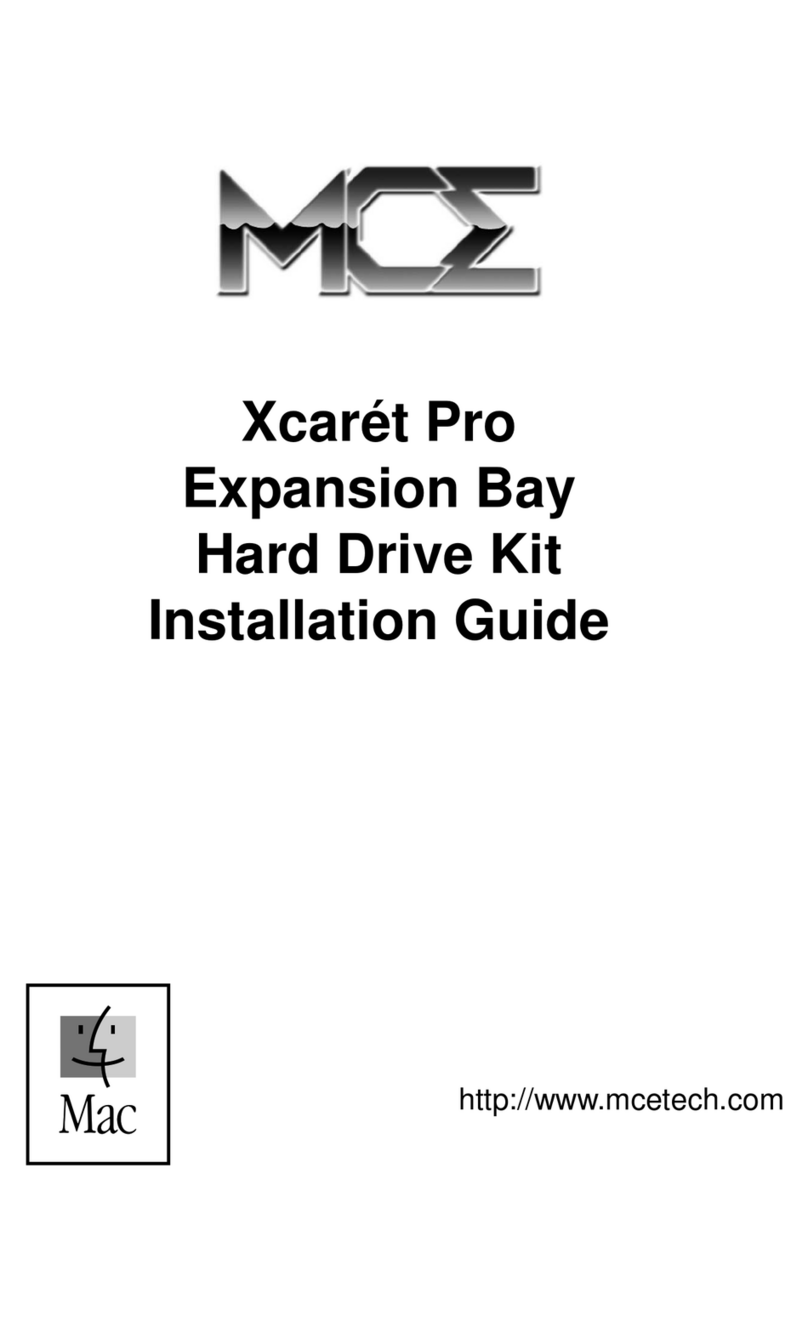
MCE Technologies
MCE Technologies Xcaret Pro installation guide
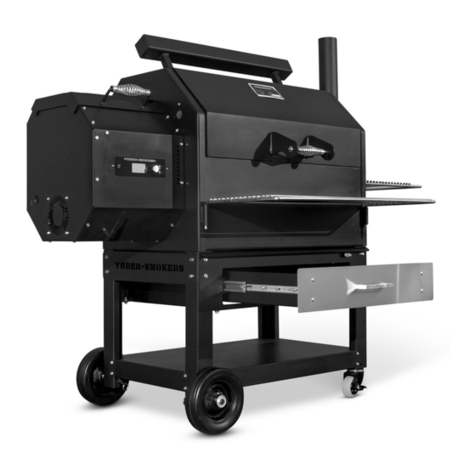
Yoder Smokers
Yoder Smokers YS 480 Assembly and installation
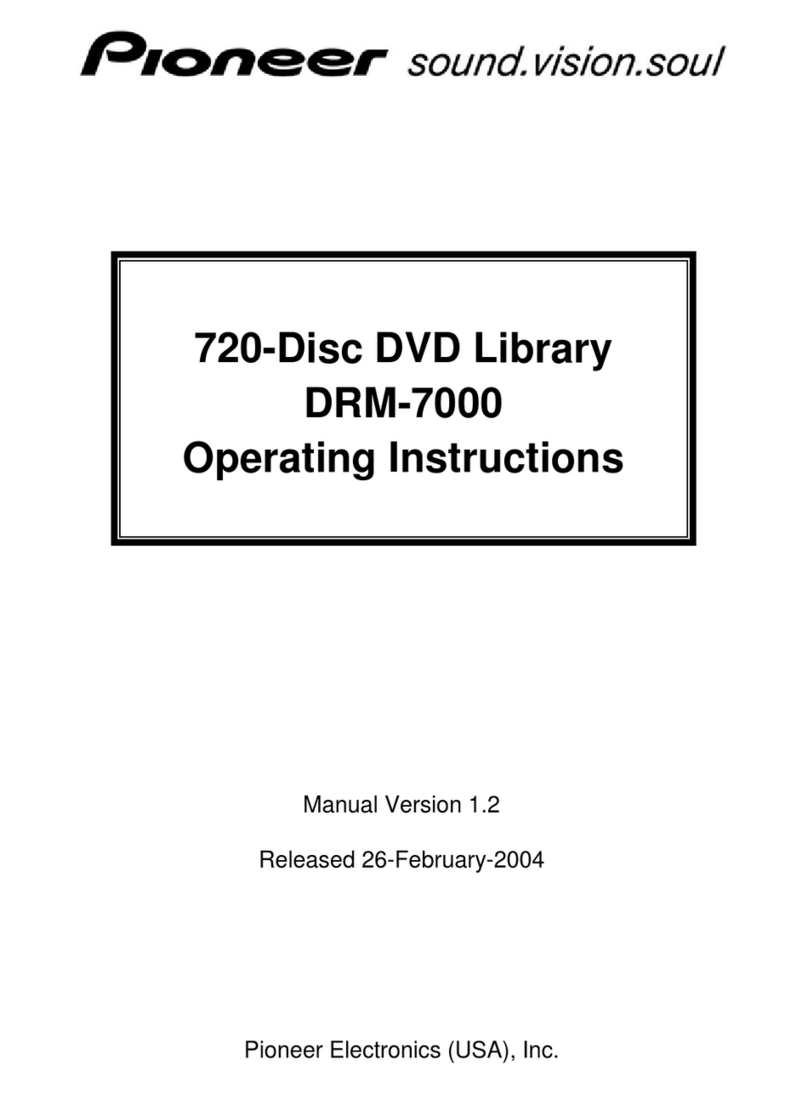
Pioneer
Pioneer DRM-7000 operating instructions
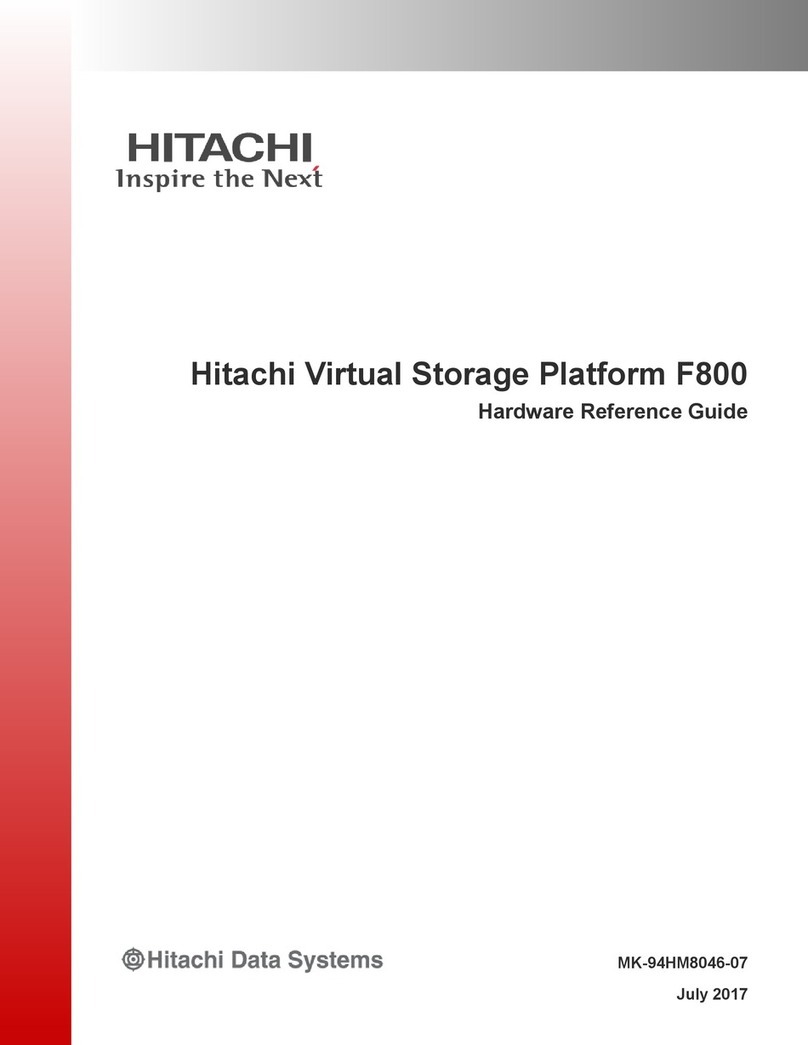
Hitachi
Hitachi Virtual Storage Platform F800 Hardware reference guide