Colibri SMARTHUB User manual

1SMARTHUB
SMARTHUB Device Monitoring Unit
USER MANUAL

2SMARTHUB
Table of Contents
1. GENERAL
1.1. Compliance and Certification
1.2. Statement of Conformity
1.3. Safety Warnings
1.4. General Overview
1.5. SMARTHUB Ecosystem
1.6. Main Features
1.7. Basic Configuration
1.8. SMARTHUB Case Contents
1.9. Display Tablet
1.10. SMARTHUB APP
1.11. HSM Jet Spindle
2. INSTALLATION
2.1. System Requirements
2.2. Mechanical Installation
2.3. Electrical Installation (wiring)
2.4. Signals Control
2.4.1. Signals Wiring
2.4.2. Signals Time Chart
2.5. LED Panel Indicators
2.6. Validation Test Procedures
2.7. Post Installation
2.8. Operation in Multiple Machines
3. MOBILE APP
3.1. APP Screens
4. MAINTENANCE
5. FAQs
6. WARRANTY

3SMARTHUB
1. GENERAL
1.1. Compliance and Certification
SMARTHUB is environmental and mechanical laboratory tested and certified.
FCC Compliance Statement:
This device has been tested and found to comply with the limits for a Class A digital
device, pursuant to Part 15 of the FCC Rules. These limits are designed to provide
reasonable protection against harmful interference in residential installations. This
equipment generates uses and can radiate radio frequency energy and, if not installed
and used in accordance with the instructions, may cause harmful interference to radio
and television reception.
However, there is no guarantee that interference will not occur in a particular
installation. If this device does cause such interference, which can be verified by
turning the device off and on, the user is encouraged to eliminate the interference by
one or more of the following measures:
•Re-orient or re-locate the receiving antenna.
•Increase the distance between the device and the receiver.
•Connect the device to an outlet on a circuit different from the one that supplies
power to the receiver.
WARNING! Changes or modifications to this unit not expressly approved
by the party responsible for compliance could void the user’s authority
to operate the equipment.
WARNING! Tablet, RF device, lithium battery, electric device 24V
(AC/DC).
This device complies with FCC Rules Part 15: Operation is subject to two conditions:
1. This device may not cause harmful interference, and
2. This device must accept any interference that may be received or that may
cause undesired operation.
To comply with FCC Section 1.310 for human exposure to radio frequency
electromagnetic fields, implement the following instruction: A distance of at least 20
cm between the equipment and all persons should be maintained during operation of
the equipment.
GENERAL

4SMARTHUB
1.2 Statement of Conformity
The SMARTHUB unit and spindle speed sensor are IP67 complaint.
The SMARTHUB device meets the following standards:
European Standards (CE)
•EMC: EN 301489-1/17
•Radio: EN 300328 V 1.8.1
•Safety: EN 61010-1:2010
American Standards (UL)
•EMC: FCC Part 15 B
•Radio: FCC Part 15 C
•Safety: UL 61010-1
Japan / Singapore Standards
•Radio: Law No. 31
•ARIB STD T-66
1.3 Safety Warnings
Read the Manual:
Safety of the operator is a main concern. Avoid accidents by reading the
safety alerts and taking a careful approach to handling the equipment.
The operator can avoid many accidents by observing the following
precautions. Review the safety instructions of the manufacturer and all
organizations responsible for the prevention of accidents.
Ensure the Following:
The work area and area around the CNC machine are free of obstacles.
The work area is properly lit. The equipment is operated only by a
responsible adult trained in its operation. The equipment is not
operated by a person under the influence of drugs or alcohol. The
equipment is not operated by a person with any illness or physical
condition that might reduce reflexes or awareness and increase
exposure to risk. Before beginning operation, install all of the safety
devices prescribed by the manufacturer.
Warning:
Always use safety glasses or protective screens to protect your eyes.
GENERAL

5SMARTHUB
1.4 General Overview
The SMARTHUB is an innovative real time data monitoring, processing, and switching
unit for safe, efficient operating of the HSM Jet Spindle (SPINJET/Typhoon/TR speed
increasers) installed on CNC milling or turning centers.
1.5 SMARTHUB Ecosystem
SMARTHUB receives a wireless 2.4 GHz signal from the Spindle's on-board speed
sensor RPMs and other data (battery, RSSI, hours, etc.), process it and relays it to the
machine PLC. The SMARTHUB communicates directly with the machine PLC via
protected electric wire/cable. SMARTHUB communicates directly with the machine
PLC via protected electric cable.
The SMARTHUB relays data, signals, warnings and alarms to the Tablet Display/APP.
RPM status of the spindle (rotating or stationary), enables or disables the door lock
mechanism as a safety measure. Additional functions include stopping the work cycle
if speed is too low. Extra device monitoring sensors may be added, such as heat,
vibration, strain, pressure, etc.
Data is displayed and managed via the user-friendly Tablet/ Mobile APP. Operators
can view a real time speed graph screen, along with short-term speed history, sensor
battery levels and RF signal strength.
GENERAL

6SMARTHUB
1.6 Main Features
•SMARTHUB monitors up to 4 devices working simultaneously and can store
another 128 devices in stand-by mode.
•SMARTHUB continuously monitors real- time RPMs, battery level, RSSI, speed
alerts, device ID, working hours, and also displays tools installed and machine ID.
•Four colored LEDs indicate operating modes.
•SMARTHUB casing is compact, streamlined, robust, and IP67 sealed.
1.7 Basic Configuration — 5 PLC I/O SIGNALS:
•Low RSSI
•Low Battery
•High / Low Speed Limit Exceeded
•Spindle Speed ≠ 0
•Power ON
1.8 SMARTHUB Case Contents
•One SMARTHUB Unit
•UL Cable (one meter), male Amphenol connector at
the SMARTHUB end, stripped for wiring at the other
end. Longer cable or additional connectors are
available upon request
•User Manual and Installation Guide
1.9 Display Tablet
The Display Tablet is a sealed, IP68 rugged model, featuring a slim, light-weight casing
and convenient holding strap. It comes in a protective carry case, and includes, a
charger, USB cable and manufacturer's instructions booklet.
NOTE: The Display Tablet is ordered and packaged separately.
GENERAL

7SMARTHUB
1.10 SMARTHUB APP
The user-friendly APP has been preinstalled on the Display Tablet.
The software provides:
•Operating status and position of Jet Spindles in the ATC magazine
•Monitor and display of spindle status (running or fully stopped), real-time RPMs,
short-term RPM history screen, spindle transmitter battery levels, signal strength
and spindle working hours
•Up to 4 spindles operating simultaneously
•Warnings and alarms: Low/high RPM limits
•Manual programming:
oAdjustable low/high speed limits
oCutting tool information:
Work station data
Spindle I/D number
Machine identification data
1.11 HSM Jet Spindle
Colibri's coolant-driven HSM Jet Spindle, tradenames
(SPINJET/Typhoon) are packaged and sold separately.
Please refer to the HSM Jet Spindle User Manual for
installation and operating instructions.
GENERAL

8SMARTHUB
2. INSTALLATION
The SMARTHUB unit connects with all common PLC I/O ports and takes up only a
small area for mounting in the CNC machine. It requires minimal mechanical
installation.
.
2.1. System Requirements
•24V (AC/DC) xxx [mA] max power feed line
•5 x I/O port types
•Mounting placement: Stationary position with direct, unobstructed Wi-Fi access
to the machine spindle sensor
•Mounting holes according to mechanical mounting layout schematic
•Display Tablet charging: Standard 220/110 50Hz socket
2.2. Mechanical Installation
•SmartHUB should be mounted inside the machine workpiece processing cabinet.
•The back side of SMARTHUB unit has 4 standard M5 threads to interface with a
mounting bracket (not supplied), or cabinet wall.
•For the maximum RF performance, it is recommended to install the SMARTHUB
on the back wall of the processing cabinet, with logo facing outwards.
•SMARTHUB should be installed in a vertical position with connector facing
downwards.
•Although designed to flush excessive coolant in a 90overtical position, it is
recommended to install at a slight tilt (5-25 degrees) facing downwards, to rush
coolant and chip evacuation when needed.
•SMARTHUB unit includes a 1 meter cable with male connectors at both ends:
Amphenol 12-08PMMS-SF8001.
INSTALLATION

9SMARTHUB
2.3. Electrical Installation (wiring)
Principal Signals Electrical Circuit Diagram
2.4. Signals Control
Sealed (IP certified), the SMARTHUB Unit is powered by a 24VDC from the CNC
machine electric cabinet, providing signals in discrete control mode (connected
to PLC I/O's), or optionally send data packs via RS232 serial communication.
INSTALLATION

10SMARTHUB
2.4.1. Signals Wiring
•POWER ON: System is ON. 1 when system is on 0 when no power feed.
•LOW RSSI: Weak signal strength. Signal is high when RSSI is weak; signal is low
when RSSI OK.
•: Low battery in spindle transmitter. Signal is high when battery level is
low; signal is low when the spindle stops.
•ZERO RPM: Spindle is stopped – may be used to control machine door latch
(safety). 1 when power is on and spindle speed = 0.
•HIGH/LOW RPM: Speed either lower or higher than the preset limit. Signal is high
when high or low limit preset values are exceeded, Signal low when speed returns
to normal.
NOTE: Additional signals available upon customer request.

11SMARTHUB
2.4.2. Signals Time Chart
High/Low RPM limits can be selected by using default values for each spindle
type, or by manually programming the desired
limits.
2.5. LED Panel Indicators
The SMARTHUB has a 4 colored LED panel indicators that signify functionality
modes or possible fault. After powering up, LEDs will turn on for 3 seconds while
performing a self-test procedure.
•GREEN LED stays lit permanently, as long as the device is powered.
•BLUE LED lights up when the Bluetooth module is ON and functioning properly.
•YELLOW LED lights up when SMARTHUB is receiving data from a revolving spindle.
•RED LED will blink if there is an alert or warning status from a revolving spindle.
2.6. Validation Test Procedures
Blue
Green
Yellow
Red
Power up - 3 seconds ON ON ON ON
No Active Spindle ON ON
Active Spindle ON ON ON
Active Spindle with alert/warning ON ON ON BLINK
INSTALLATION
INSTALLATION

12SMARTHUB
2.6.1.Validation Test 1 (using external power supply)
a.Connect the device to the external power supply
•Connect the AC adapter to the electric socket
•Connect the BLACK alligator clip to the device PINK wire (ground)
•Connect the RED alligator clip to the device RED wire (power)
•The unit should power on, with all LED lights flashing for 3 seconds
b.Test default signals (default values)
•Remove all batteries from simulation tags
•Connect the multi-meter (fluke) BLACK line to the PINK wire (ground)
•Do not disconnect the adaptor line
•Turn on the multi-meter and set dial to DC detection
Power-on (GREEN wire)
Default state is
HIGH
Touch GREEN wire with
multi-meter RED point
Reading should show
22.5V ~ 23.9V
Low-RSSI (YELLOW wire)
Default state is
LOW
Touch YELLOW wire
with multi-meter RED
point
Reading should show ~ 0V
Low-battery (WHITE wire)
Default state is
LOW
Touch WHITE wire with
multi-meter RED point
Reading should show ~ 0V
Zero RPM (GREY wire)
Default state is
HIGH
Touch GREY wire with
multi-meter RED point
Reading should show
22.5V ~ 23.9V
High/low RPM (BLUE wire)
Default state is
LOW
Touch BLUE wire with
multi-meter RED point
Reading should show ~ 0V
c.Test live signals (during spindle operation)
•Make sure SmartHUB power is on (BLUE and GREEN lights should be lit)
•Turn on Tablet display
•Tap "Devices" to see the list of connected devices
•Remove all devices by tapping the "X" button
•Insert battery into one simulation tag (note ID on the side)
•Connect the simulation tag to the SmartHUB by tapping "Add Device" on the
application and entering simulation tag ID (1003 / 1004)
•Check the tag is connected by returning to the main screen. If no information is
displayed on the main screen, reboot Tablet and reconnect
•When simulated graphs appear, check the signals to see if the state (High/Low)
changes as follows:

13SMARTHUB
1. Zero RPM (GREY wire) - default state is HIGH - touch the GREY wire with the
multi-meter RED point - reading should show ~ 0V
2. High/low RPM (BLUE wire) - default state is LOW - touch the BLUE wire with the
multi-meter RED point - reading should show 22.5V ~ 23.9V if spindle speed is
out of limits
NOTE: The SmartHUB should be in proper working order if the above tests have been
performed correctly.
2.6.2. Validation Test 2 (using the machine power supply)
•Disconnect the external power supply
•With machine maker employee, connect the PINK wire to the machine ground
•With machine maker employee, connect the RED wire to the machine power
•Perform both DEFAULT and LIVE SIGNAL tests again
2.7. Post Installation Procedures
SMARTHUB is designed to operate automatically in the presence of an RF
transmission signal from a paired device (spindle).
2.8. Operating in Multiple Machines
Multiple SMARTHUB units may be installed (one per machine) in different machines
located in close proximity, however certain limitations may apply. The Tablet APP
recognizes more than one active SMARTHUB and will automatically change the main
page display from the 'single machine view' to the 'multiple machine view'.
3. MOBILE APP
The Application (APP) is a proprietary, closed software program that has been
preinstalled on the Display Tablet. It is specially designed for operation with the
SMARTHUB ecosystem to monitor and display all existing functions. It also allows the
operator to input and alter data such as connections, presets, alerts, updated working
conditions, etc.
3.1. APP Screens
INSTALLATION

14SMARTHUB
To enter information where needed in any screen, tap the field and a keyboard
will pop up.
•Welcome Screen
Upon powering up the Tablet, a welcome
screen is displayed for 5 seconds, until the
application is loaded.
•Add New Device Screen
1. Sensor ID: Tool ID printed on the side of the Sensor (4 characters), mandatory.
2. Tool Position: Tool's position in the tool magazine.
3. Cutting Tool: Description of cutting tool.
4. Device SN:Serial number of the spindle.
5. Model: Spindle model selected from drop down list.
6. Machine: Name of the machine operating the spindle.
7. Speed Limit: This field sets the default speed limits. If the spindle rotates outside
the allowed speed limits an alert will be generated. The 'Automatic Setting' uses
system default limits, while the 'Manual Setting' allows the user to enter custom
speed limits.
8. Low Limit: Custom speed limit low range.
9. High Limit: Custom speed limit high range.
10. Cancel: Cancel adding new device.
MOBILE APP

15SMARTHUB
11. Store Device: Save new device settings to the system.
•Device List Screen
After spindle is stored, the Device List screen will appear, listing all connected
spindles.
1. Spindle Icon: Represents the type of spindle used.
2. Tag ID: Sensor ID, printed on the side of the Tag.
3. Model: Sensor model.
4. Machine: Name of the machine.
5. Tool: Type of tool.
6. Position: Position of the spindle (sensor) in the tool magazine.
7. Work Time: Total spindle work time (hours).
8. RSSI: Signal Strength Indicator. Grey when sensor is not active or transmitting.
9. Edit: Press icon on any line to edit spindle properties.
10. Remove: Tap icon on any line to disconnect the spindle.
11. Add Device: Tap icon to connect another spindle.
•Active Tags Screen
MOBILE APP

16SMARTHUB
1. Add Device: Tap to enter spindle properties and connect a new device.
2. Device List: Tap to view list of devices currently connected.
3. Calculator: Not functional in this version.
4. Resources: Tap to view support documents and help videos.
5. Settings: Tap to view or update system settings.
6. Active Spindle: Tap to display active spindle rotation speed charts.
7. Active Spindle: Displays additional active spindle.
8. Alert: Indication of High/Low RPM.
9. Warning: Indication of Low Battery or Low RSSI.
Note: Tap the Warning/Alert sign to view more detailed status information.

17SMARTHUB
•Graphs Screen
1. Minimized Graph: RPM graph of an active spindle/sensor, tap to enlarge.
2. Minimized Graph: RPM graph of an additional active spindle/sensor.
3. Main Graph: RPM Graph of selected spindle/sensor. Press and drag to zoom.
4. Upper Speed Limit: Dashed line represents the upper speed limit.
5. Lower Speed Limit: Dashed line represents the lower speed limit.
6. Warning / Alert: Icon appears to indicate an active warning or alert.
7. Battery Status: Battery value. Less than 10% activates a warning.
8. Signal Strength: Icon indicates sign strength from all bands filled white (strong
signal) to all bands grey, (weak or no signal).
9. RPM Reading: Most recently measured RPM value from selected spindle.
10. Station: Machine name.
11. Cutting Tool: Cutting tool type.
MOBILE APP

18SMARTHUB
4. MAINTENANCE
The SMARTHUB unit is free from maintenance. It is however recommended to
periodically wipe the face of the unit with a clean cloth, to ensure colored LED
indicators are unobstructed by cutting fluid residue and easily visible.
•Recommended Operating Environment:Temperature Range: 0 - 50° C
•Storage Conditions:The SMARTHUB unit must be stored in conditions meeting the
following requirements.
oSheltered from possible adverse weather conditions
oIdeal storage temperature range: 15 ºC to 27 º C
oHumidity range: 30% to 60% relative humidity (RH)
Warning:
It is strictly prohibited immerse the SMARTHUB in a fluid bath.
MAINTENANCE

19SMARTHUB
5. FAQs
Review the section MOBILE APP for information about display screen alerts and
management. Answers to common questions appear below.
When is the High/Low Speed Warning Signal activated?
This signal will activate when spindle RPMs are either higher or lower than the pre-
set value programmed by user or automatically set by the program when selecting
one of the spindle models preprogrammed into the system.
What do the Speed Signal Indications actually mean?
•
Low pressure (low speed)
•Over pressure (high speed)
•Heavy load on the spindle or incorrect machining conditions, spindle
malfunction (low rpm’s)
What are the High/Low Speed Warning Signal Options?
•
Option 1: Stays as visual warning on screen, until the operator acknowledges
it.
•Option 2: Stop cycle until machine operator checks what is wrong.
Why is the Low Battery Signal warning always lit?
•The "low battery signal" timing is triggered by the battery condition, but goes
back to zero level when spindle stops transmitting (stops)
•If battery was not replaced when spindle operation resumes; (rotational speed
+ spindle data transmission) a "low battery" warning will appear, and remain
on until spindle stops again and so on, or until battery is replaced.
•Therefore the trigger for that signal is the low battery level and the terminator
is "spindle stop"
•The battery life is long, at least ~750 hr.
•It is highly recommended to replace battery when necessary, otherwise no
data will be transmitted and the SmartHUB will no longer "recognize" the
spindle. This can pose safety problems
FAQS

20SMARTHUB
Can the SmartHUB system be used to configure other devices?
The SmartHUB and APP are designed to support auxiliary equipment not usually
monitored by the machine controller, such as lathe live tooling, other auxiliary
spindles (mechanical, pneumatic, electric), etc. This requires a sensor installed on
the target device.
Will the SmartHUB work without the tablet?
The SmartHUB continues monitoring and sending warning alerts to machine PLC,
regardless of the presence of the tablet. The tablet is a must for binding the
spindles to the SmartHUB and viewing the real-time data.
What will happen if two SmartHUB units operate close to one another?
Nothing happens as long as the spindle/device isn’t paired to both of them.
Will the SmartHUB immediately receive the spindle (device) transmissions?
As long as the device is paired with the SmartHUB, it immediately and
automatically starts monitoring.
How many more signals can be added in the future?
More signals may be added as needed; the main limitation in discrete I/O mode
is the cable size and free ports in the PLC.
FAQS
Table of contents
Popular Measuring Instrument manuals by other brands
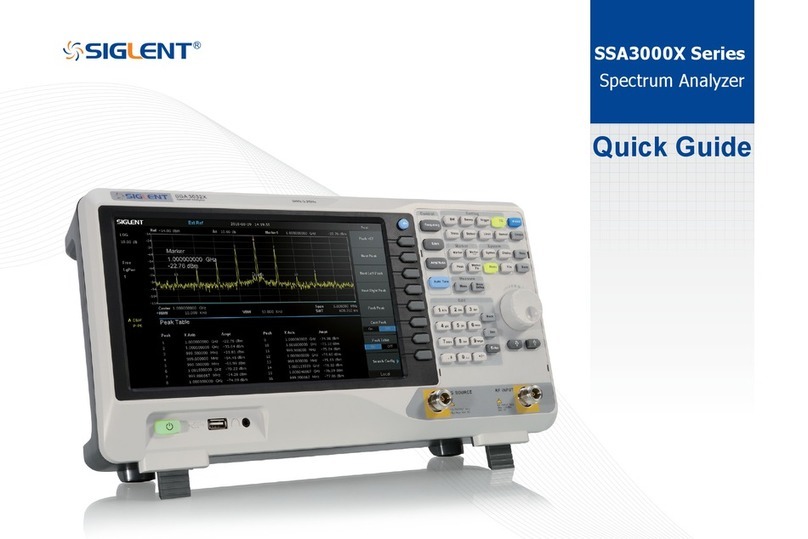
SIGLENT TECHNOLOGIES
SIGLENT TECHNOLOGIES SSA3000X Series quick guide
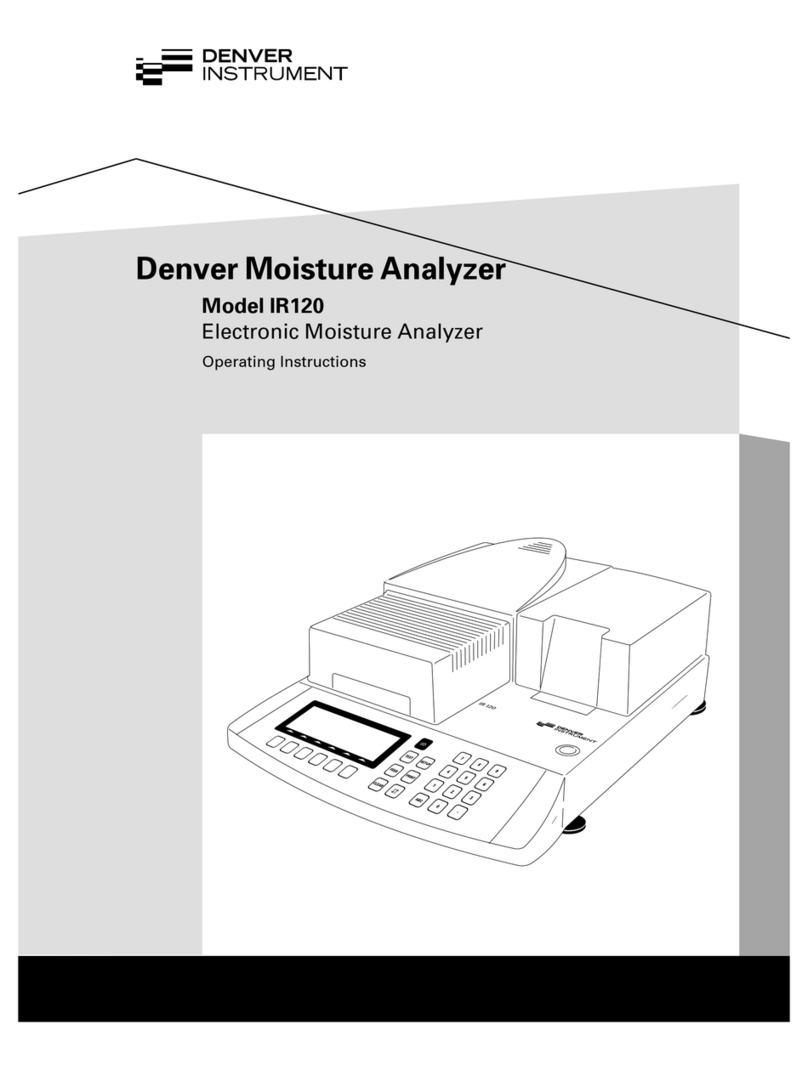
Denver Instrument
Denver Instrument IR120 operating instructions
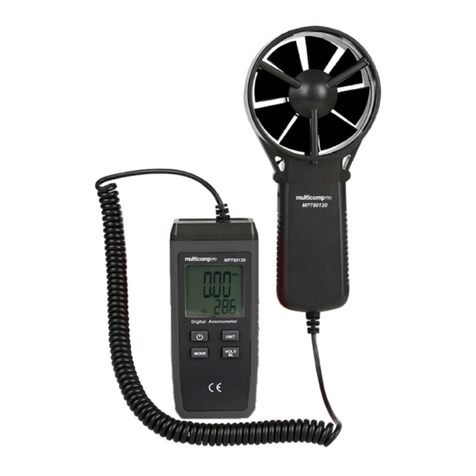
multicomp pro
multicomp pro MP780119 manual
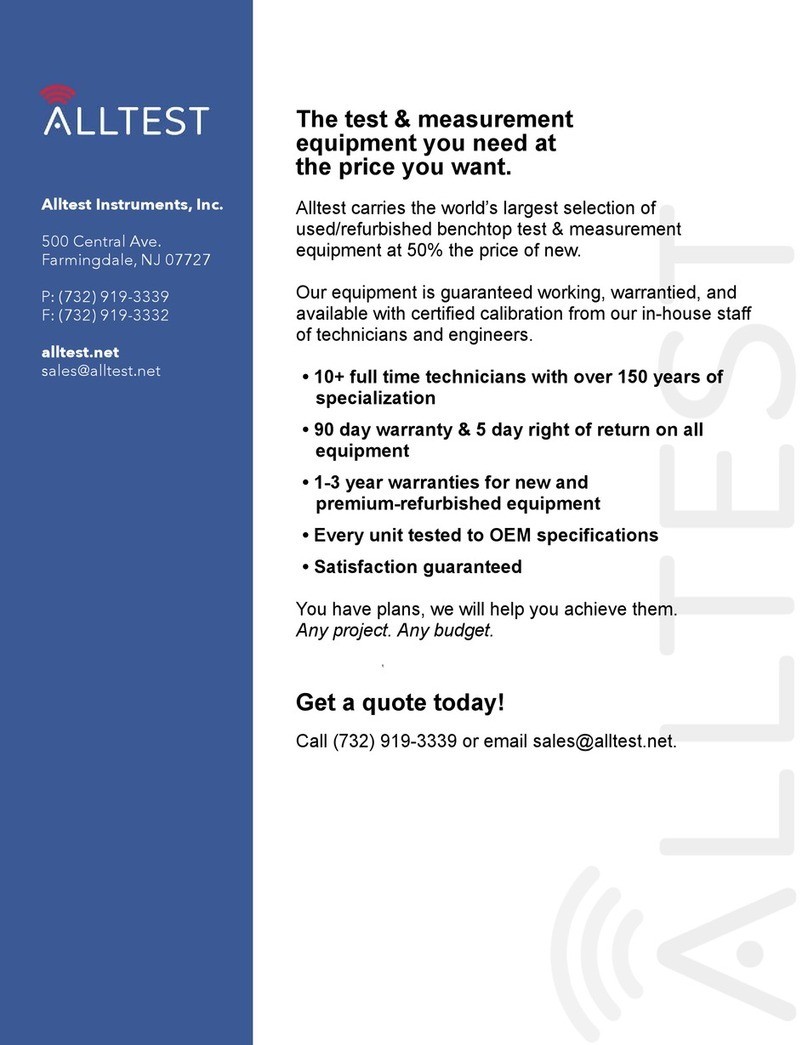
Agilent Technologies
Agilent Technologies 85052A Repair manual
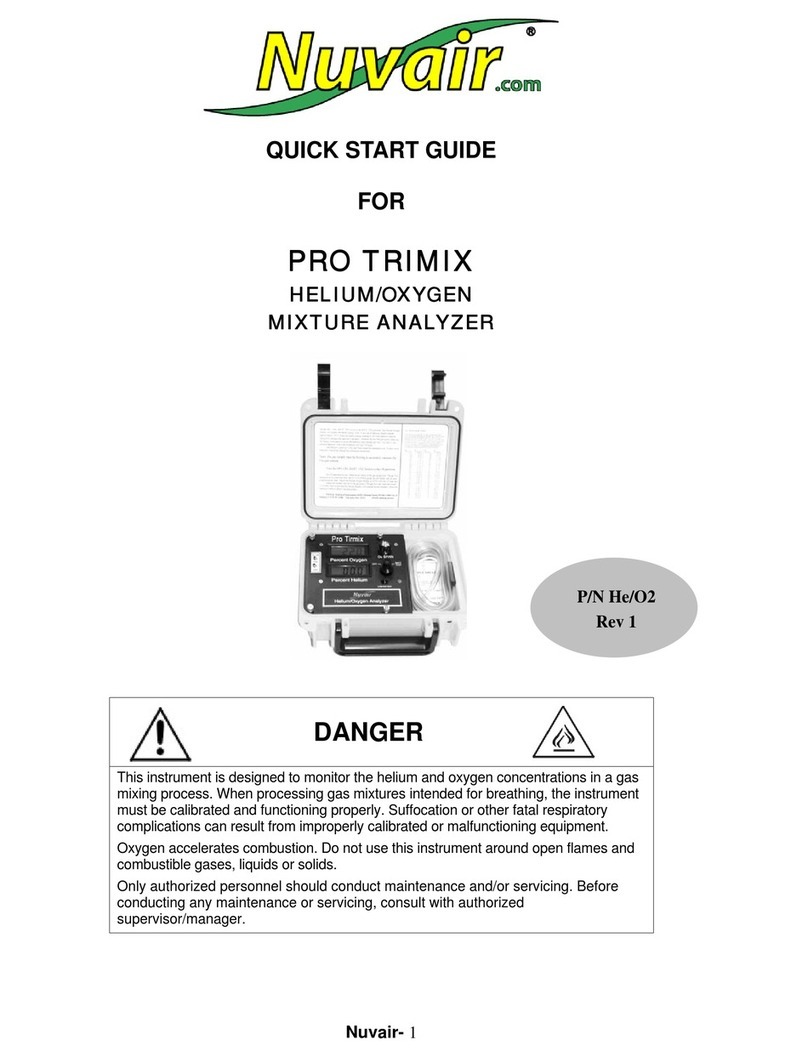
Nuvair
Nuvair PRO TRIMIX quick start guide

DAKOTA ULTRASONICS
DAKOTA ULTRASONICS MMX-6 DL Operation manual