Control Techniques FM-1 User manual

Reference Manual
P/N 400506-01
Revision: A4
Date: October 1, 2001
© Control Techniques Drives, Inc. 1999, 2001
FM-1 Speed Module


Information furnished by Control Techniques Drives Inc. (Control Techniques) is believed to be
accurate and reliable. However, no responsibility is assumed by Control Techniques for its use.
Control Techniques reserves the right to change the design or operation of the equipment described
herein and any associated motion products without notice. Control Techniques also assumes no
responsibility for any errors that may appear in this document. Information in this document is subject
to change without notice.
P/N 400506-01
Revision: A4
Date: October 1, 2001
© Control Techniques, Drives, Inc. 1999, 2001
FM-1
Speed Module
Reference Manual

ii
© Control Techniques Drives, Inc. 2000, 2001
Part Number: 400506-01
Revision: A4
Date: October 2001
Printed in United States of America
Printed in United States of America
Information in this document is subject to change without notice. No part of this document may be
reproduced or transmitted in any form or by any means, electronic or mechanical, for any purpose,
without the express written permission of Control Techniques.
The following are trademarks of Control Techniques and may not be reproduced in any fashion
without written approval of Control Techniques: EMERSON Motion Control,
EMERSON Motion Control PowerTools, AXIMA, “Motion Made Easy.”
Control Techniques is a division of EMERSON Co.
Control Techniques, Inc. is not affiliated with Microsoft Corporation, owner of the Microsoft,
Windows, and Windows NT trademarks.
This document has been prepared to conform to the current released version of the product. Because
of our extensive development efforts and our desire to further improve and enhance the product,
inconsistencies may exist between the product and documentation in some instances. Call your
customer support representative if you encounter an inconsistency.

iii
Customer Support
Control Techniques
12005 Technology Drive
Eden Prairie, Minnesota 55344-3620
U.S.A.
Telephone: (952) 995-8000 or (800) 893-2321
It is Control Techniques’ goal to ensure your greatest possible satisfaction with the operation
of our products. We are dedicated to providing fast, friendly, and accurate assistance. That is
why we offer you so many ways to get the support you need. Whether it’s by phone, fax or
modem, you can access Control Techniques support information 24 hours a day, seven days
a week. Our wide range of services include:
FAX (952) 995-8099
You can FAX questions and comments to Control Techniques. Just send a FAX to the number
listed above.
Website and Email www.emersonct.com
Website: www.emersonct.com
Email: [email protected]
If you have Internet capabilities, you also have access to technical support using our website.
The website includes technical notes, frequently asked questions, release notes and other
technical documentation. This direct technical support connection lets you request assistance
and exchange software files electronically.
Technical Support (952) 995-8033 or (800) 893-2321
Email: service@emersonct.com
Control Techniques’ “Motion Made Easy” products are backed by a team of professionals
who will service your installation. Our technical support center in Eden Prairie, Minnesota is
ready to help you solve those occasional problems over the telephone. Our technical support
center is available 24 hours a day for emergency service to help speed any problem solving.
Also, all hardware replacement parts, if needed, are available through our customer service
organization.
When you call, please be at your computer, with your documentation easily available, and be
prepared to provide the following information:
• Product version number, found by choosing About from the Help menu
• The type of controller or product you are using

iv
• Exact wording of any messages that appear on your screen
• What you were doing when the problem occurred
• How you tried to solve the problem
Need on-site help? Control Techniques provides service, in most cases, the next day. Just call
Control Techniques’ technical support center when on-site service or maintenance is
required.
Training Services (952) 995-8000 or (800) 893-2321
Email: [email protected]
Control Techniques maintains a highly trained staff of instructors to familiarize customers
with Control Techniques’ “Motion Made Easy” products and their applications. A number of
courses are offered, many of which can be taught in your plant upon request.
Application Engineering (952) 995-8000 or (800) 893-2321
Email: applengr@emersonct.com
An experienced staff of factory application engineers provides complete customer support for
tough or complex applications. Our engineers offer you a broad base of experience and
knowledge of electronic motion control applications.
Customer Service (Sales) (952) 995-8000 or (800) 893-2321
Email: customer.service@emersonct.com
Authorized Control Techniques distributors may place orders directly with our Customer
Service department. Contact the Customer Service department at this number for the
distributor nearest you.
Document Conventions
Manual conventions have been established to help you learn to use this manual quickly and
easily. As much as possible, these conventions correspond to those found in other Microsoft®
Windows® compatible software documentation.
Menu names and options are printed in bold type: the File menu.
Dialog box names begin with uppercase letters: the Axis Limits dialog box.
Dialog box field names are in quotes: “Field Name.”
Button names are in italic: OK button.
Source code is printed in Courier font: Case ERMS.

v
In addition, you will find the following typographic conventions throughout this manual.
“Warning” indicates a potentially hazardous situation that, if not avoided, could result in
death or serious injury.
“Caution” indicates a potentially hazardous situation that, if not avoided, may result in
minor or moderate injury.
“Caution” used without the safety alert symbol indicates a potentially hazardous situation
that, if not avoided, may result in property damage.
Note
For the purpose of this manual and product, “Note” indicates essential information about
the product or the respective part of the manual.
E Series Only
E
N
For the purpose of this manual and product, the “EN” symbol indicates information about
the E Series drive specifically.
Throughout this manual, the word “drive” refers to an E Series drive
This Represents
bold Characters that you must type exactly as they appear. For example, if you are directed to type
a:setup, you should type all the bold characters exactly as they are printed.
italic Placeholders for information you must provide. For example, if you are directed to type
filename, you should type the actual name for a file instead of the word shown in italic type.
ALL CAPITALS Directory names, file names, key names, and acronyms.
SMALL CAPS Non-printable ASCII control characters.
KEY1+KEY2
example: (Alt+F)
A plus sign (+) between key names means to press and hold down the first key while you press
the second key.
KEY1,KEY2
example: (Alt,F) A comma (,) between key names means to press and release the keys one after the other.

vi
Safety Instructions
General Warning
Failure to follow safe installation guidelines can cause death or serious injury. The voltages
used in the product can cause severe electric shock and/or burns and could be lethal. Extreme
care is necessary at all times when working with or adjacent to the product. The installation
must comply with all relevant safety legislation in the country of use.
Qualified Person
For the purpose of this manual and product, a “qualified person” is one who is familiar with
the installation, construction and operation of the equipment and the hazards involved. In
addition, this individual has the following qualifications:
• Is trained and authorized to energize, de-energize, clear and ground and tag circuits and
equipment in accordance with established safety practices.
• Is trained in the proper care and use of protective equipment in accordance with
established safety practices.
• Is trained in rendering first aid.
Reference Materials
The following related reference and installation manuals may be useful with your particuliar
system.
•Function Module Installation Manual (P/N 400506-03)
•Epsilon and E Series Drives Reference Manual (P/N 400501-01)
•PowerTools Software User’s Guide (P/N 400503-01)
•Epsilon and E Series Drive Parameters Reference Manual (P/N 400504-01)

vii
Underwriters Laboratories Recognition
The E Series drives are marked with the “UL Recognized” label after passing a rigorous set
of design and testing criteria developed by UL (UL508C). This label indicates that the UL
certifies this product to be safe when installed according to the installation guidelines and
used within the product specifications.
The “conditions of acceptability” required by UL are:
• The drive ambient temperature must be 40° C (104° F) or less.
• This product is suitable for use on a circuit capable of delivering not more than 5000 RMS
symmetrical amperes, 240 volts maximum.
The “UL Recognized” designation is different than a “UL Listed” designation. The “UL
Listed” designation is generally applicable to stand alone products where the “UL
Recognized” designation is used for components that are part of a system. E Series drives are
usually considered components of a larger control system where the “UL Recognized”
designating is very common and well accepted.
CE Declaration of Conformity
The E Series drives are marked with the “Conformite Europeenne Mark” (CE mark) after
passing a rigorous set of design and testing criteria. This label indicates that this product
meets safety and noise immunity and emmisions (EMC) standards when installed according
to the installation guidelines and used within the product specifications.
FM-1 Speed Module Reference Manual

viii
FM-1 Speed Module Reference Manual
Declaration of Conformity
Manufacturer’s Name: Control Techniques Drives, Inc.
Manufacturer’s Address:
12005 Technology Drive
Eden Prairie, MN 55344
USA
Declares That The Following Products:
Products Description: E Series Digital Servo Drive
Model Number: EN-204, EN-208, EN-214
System Options:
This declaration covers the above products with the
ALP-130 Backup Logic Power Supply and ECI-44 Screw Terminal
Interface.
Designed and manufactured in accordance with the following European harmonized
national and international standards.
Electomagnetic Compatibility:
EN 55011/1991 Class A Group 1, CISPR 11/1990 Class A Group 1
EN 50082-2/1995:
IEC 1000-4-2/1995; EN 61000-4-2, 4kV CD
IEC 1000-4-3/1995; EN 61000-4-3, ENV 50140/1993, 80% AM, 10V/
m @ 3 m
IEC 1000-4-4/1995; EN 61000-4-4, 2 kV ALL LINES
IEC 1000-4-8/1993; EN 61000-4-8, 30 A/m
ENV 50141/1993, 80% AM, 10V, .15-80 MHz
ENV 50204/1995, Pulse, 900 MHz, 50% DTY, 200 Hz
Supplementary Information
The products herewith comply with the requirements of the Low Voltage Directive (LVD) 73/23/EEC
and EMC Directive 89/336/EEC
This electronic drive product is intended to be used with an appropriate motor, electrical protection components and other equipment to form a
complete end product or system. It must only be installed by a professional assembler who is familiar with requirements for safety and
electromagnetic compatibility (“EMC”). The assembler is responsible for ensuring that the end product or system complies with all the
relevant laws in the country where it is to be used. Refer to the product manual for installation guidelines.
December 2, 1997
Bradley Schwartz/ VP Engineering Date
European Contact:
Sobetra Automation
Langeveldpark Lot 10
P. Dasterleusstraat 2
1600 St. Pieters leeuw, Belguim

ix
Safety Considerations
Safety Precautions
This product is intended for professional incorporation into a complete system. If you install
the product incorrectly, it may present a safety hazard. The product and system may use high
voltages and currents, carries a high level of stored electrical energy, or is used to control
mechanical equipment which can cause injury.
You should give close attention to the electrical installation and system design to avoid
hazards either in normal operation or in the event of equipment malfunction. System design,
installation, commissioning and maintenance must be carried out by personnel who have the
necessary training and experience. Read and follow this safety information and the instruction
manual carefully.
Enclosure
This product is intended to be mounted in an enclosure which prevents access except by
trained and authorized personnel, and which prevents the ingress of contamination. This
product is designed for use in an environment classified as pollution degree 2 in accordance
with IEC664-1. This means that only dry, non-conducting contamination is acceptable.
Setup, Commissioning and Maintenance
It is essential that you give careful consideration to changes to drive settings. Depending on
the application, a change could have an impact on safety. You must take appropriate
precautions against inadvertent changes or tampering. Restoring default parameters in certain
applications may cause unpredictable or hazardous operation.
Safety of Machinery
Within the European Union all machinery in which this product is used must comply with
Directive 89/392/EEC, Safety of Machinery.
The product has been designed and tested to a high standard, and failures are very unlikely.
However the level of integrity offered by the product’s control function – for example stop/
start, forward/reverse and maximum speed – is not sufficient for use in safety-critical
applications without additional independent channels of protection. All applications where
malfunction could cause injury or loss of life must be subject to a risk assessment, and further
protection provided where needed.
Note
General warning
Failure to follow safe installation guidelines can cause death or serious injury. The
voltages used in this unit can cause severe electric shock and/or burns, and could be lethal.
Extreme care is necessary at all times when working with or adjacent to this equipment.
FM-1 Speed Module Reference Manual

x
FM-1 Speed Module Reference Manual
The installation must comply with all relevant safety legislation in the country of use.
AC supply isolation device
The AC supply must be removed from the drive using an approved isolation device or
disconnect before any servicing work is performed, other than adjustments to the settings
or parameters specified in the manual. The drive contains capacitors which remain
charged to a potentially lethal voltage after the supply has been removed. Allow at least
30 seconds after removing the supply before carrying out any work which may involve
contact with electrical connections to the drive.
Products connected by plug and socket
A special hazard may exist where the drive is incorporated into a product which is
connected to the AC supply by a plug and socket. When unplugged, the pins of the plug
may be connected to the drive input, which is only separated from the charge stored in the
capacitor by semiconductor devices. To avoid any possibility of electric shock from the
pins, if they are accessible, a means must be provided for automatically isolating the plug
from the drive (e.g., a latching contactor).
Grounding (Earthing, equipotential bonding)
The drive must be grounded by a conductor sufficient to carry the prospective fault current
in the event of a fault. The ground connections shown in the manual must be followed.
Fuses
Fuses or over-current protection must be provided at the input in accordance with the
instructions in the manual.
Isolation of control circuits
The installer must ensure that the external control circuits are isolated from human contact
by at least one layer of insulation rated for use at the applied AC supply voltage.

xi
Reference Materials. . . . . . . . . . . . . . . . . . . . . . . . . . . . . . . . . . . . . . . . . . . . . . . . . . . . . . . . . . . vi
Safety Considerations ix
Safety Precautions . . . . . . . . . . . . . . . . . . . . . . . . . . . . . . . . . . . . . . . . . . . . . . . . . . . . . . . . . . . . ix
Introduction 1
Overview . . . . . . . . . . . . . . . . . . . . . . . . . . . . . . . . . . . . . . . . . . . . . . . . . . . . . . . . . . . . . . . . . . . . 1
Features . . . . . . . . . . . . . . . . . . . . . . . . . . . . . . . . . . . . . . . . . . . . . . . . . . . . . . . . . . . . . . . . . . . . . 2
Quick Start 5
Installing the FM-1 . . . . . . . . . . . . . . . . . . . . . . . . . . . . . . . . . . . . . . . . . . . . . . . . . . . . . . . . . . . . 5
Installing the PowerTools-FM Software . . . . . . . . . . . . . . . . . . . . . . . . . . . . . . . . . . . . . . . . . . . . 8
Setting Up the FM-1 . . . . . . . . . . . . . . . . . . . . . . . . . . . . . . . . . . . . . . . . . . . . . . . . . . . . . . . . . . . 9
Operational Overview 29
User Interface. . . . . . . . . . . . . . . . . . . . . . . . . . . . . . . . . . . . . . . . . . . . . . . . . . . . . . . . . . . . . . . . 29
How Motion Works . . . . . . . . . . . . . . . . . . . . . . . . . . . . . . . . . . . . . . . . . . . . . . . . . . . . . . . . . . . 29
Functional Overview . . . . . . . . . . . . . . . . . . . . . . . . . . . . . . . . . . . . . . . . . . . . . . . . . . . . . . . . . . 30
Pulse Mode . . . . . . . . . . . . . . . . . . . . . . . . . . . . . . . . . . . . . . . . . . . . . . . . . . . . . . . . . . . . . . . . . 30
Encoder Output Scaling. . . . . . . . . . . . . . . . . . . . . . . . . . . . . . . . . . . . . . . . . . . . . . . . . . . . . . . . 35
Velocity Mode . . . . . . . . . . . . . . . . . . . . . . . . . . . . . . . . . . . . . . . . . . . . . . . . . . . . . . . . . . . . . . . 36
Summation Mode. . . . . . . . . . . . . . . . . . . . . . . . . . . . . . . . . . . . . . . . . . . . . . . . . . . . . . . . . . . . . 38
Torque Mode . . . . . . . . . . . . . . . . . . . . . . . . . . . . . . . . . . . . . . . . . . . . . . . . . . . . . . . . . . . . . . . . 43
Drive Operation Modifiers . . . . . . . . . . . . . . . . . . . . . . . . . . . . . . . . . . . . . . . . . . . . . . . . . . . . . 45
Current Foldback . . . . . . . . . . . . . . . . . . . . . . . . . . . . . . . . . . . . . . . . . . . . . . . . . . . . . . . . . . . . . 50
Shunt Operation. . . . . . . . . . . . . . . . . . . . . . . . . . . . . . . . . . . . . . . . . . . . . . . . . . . . . . . . . . . . . . 52
Brake Operation and Wiring . . . . . . . . . . . . . . . . . . . . . . . . . . . . . . . . . . . . . . . . . . . . . . . . . . . . 54
Analog Input . . . . . . . . . . . . . . . . . . . . . . . . . . . . . . . . . . . . . . . . . . . . . . . . . . . . . . . . . . . . . . . . 55
Analog Outputs . . . . . . . . . . . . . . . . . . . . . . . . . . . . . . . . . . . . . . . . . . . . . . . . . . . . . . . . . . . . . . 57
Digital Inputs and Outputs. . . . . . . . . . . . . . . . . . . . . . . . . . . . . . . . . . . . . . . . . . . . . . . . . . . . . . 58
Setting Up Parameters 65
Setup Tab. . . . . . . . . . . . . . . . . . . . . . . . . . . . . . . . . . . . . . . . . . . . . . . . . . . . . . . . . . . . . . . . . . . 65
Inputs Tab . . . . . . . . . . . . . . . . . . . . . . . . . . . . . . . . . . . . . . . . . . . . . . . . . . . . . . . . . . . . . . . . . . 69
Outputs Tab . . . . . . . . . . . . . . . . . . . . . . . . . . . . . . . . . . . . . . . . . . . . . . . . . . . . . . . . . . . . . . . . . 71
Pulse Setup Tab . . . . . . . . . . . . . . . . . . . . . . . . . . . . . . . . . . . . . . . . . . . . . . . . . . . . . . . . . . . . . . 73
Table of Contents
FM-1 Speed Module Reference Manual

FM-1 Speed Module Reference Manual
xii
Position Tab. . . . . . . . . . . . . . . . . . . . . . . . . . . . . . . . . . . . . . . . . . . . . . . . . . . . . . . . . . . . . . . . . 75
Velocity Tab . . . . . . . . . . . . . . . . . . . . . . . . . . . . . . . . . . . . . . . . . . . . . . . . . . . . . . . . . . . . . . . . 77
Torque Tab . . . . . . . . . . . . . . . . . . . . . . . . . . . . . . . . . . . . . . . . . . . . . . . . . . . . . . . . . . . . . . . . . 80
Tuning Tab . . . . . . . . . . . . . . . . . . . . . . . . . . . . . . . . . . . . . . . . . . . . . . . . . . . . . . . . . . . . . . . . . 82
Analog Tab . . . . . . . . . . . . . . . . . . . . . . . . . . . . . . . . . . . . . . . . . . . . . . . . . . . . . . . . . . . . . . . . . 84
I/O Status Tab . . . . . . . . . . . . . . . . . . . . . . . . . . . . . . . . . . . . . . . . . . . . . . . . . . . . . . . . . . . . . . . 87
Status Tab . . . . . . . . . . . . . . . . . . . . . . . . . . . . . . . . . . . . . . . . . . . . . . . . . . . . . . . . . . . . . . . . . . 91
History Tab . . . . . . . . . . . . . . . . . . . . . . . . . . . . . . . . . . . . . . . . . . . . . . . . . . . . . . . . . . . . . . . . . 95
Advanced Tab . . . . . . . . . . . . . . . . . . . . . . . . . . . . . . . . . . . . . . . . . . . . . . . . . . . . . . . . . . . . . . . 96
Tuning Procedures 97
Overview . . . . . . . . . . . . . . . . . . . . . . . . . . . . . . . . . . . . . . . . . . . . . . . . . . . . . . . . . . . . . . . . . . . 97
PID vs. State-Space. . . . . . . . . . . . . . . . . . . . . . . . . . . . . . . . . . . . . . . . . . . . . . . . . . . . . . . . . . . 97
Tuning Procedure . . . . . . . . . . . . . . . . . . . . . . . . . . . . . . . . . . . . . . . . . . . . . . . . . . . . . . . . . . . . 98
Tuning Parameters. . . . . . . . . . . . . . . . . . . . . . . . . . . . . . . . . . . . . . . . . . . . . . . . . . . . . . . . . . . 100
Determining Tuning Parameter Values. . . . . . . . . . . . . . . . . . . . . . . . . . . . . . . . . . . . . . . . . . . 104
Diagnostics and Troubleshooting 109
Diagnostic Display . . . . . . . . . . . . . . . . . . . . . . . . . . . . . . . . . . . . . . . . . . . . . . . . . . . . . . . . . . 109
Fault Codes . . . . . . . . . . . . . . . . . . . . . . . . . . . . . . . . . . . . . . . . . . . . . . . . . . . . . . . . . . . . . . . . 110
Diagnostic Analog Output Test Points . . . . . . . . . . . . . . . . . . . . . . . . . . . . . . . . . . . . . . . . . . . 114
Drive Faults . . . . . . . . . . . . . . . . . . . . . . . . . . . . . . . . . . . . . . . . . . . . . . . . . . . . . . . . . . . . . . . . 116
Watch Window . . . . . . . . . . . . . . . . . . . . . . . . . . . . . . . . . . . . . . . . . . . . . . . . . . . . . . . . . . . . . 117
View Motor Parameters . . . . . . . . . . . . . . . . . . . . . . . . . . . . . . . . . . . . . . . . . . . . . . . . . . . . . . 119
Error Messages . . . . . . . . . . . . . . . . . . . . . . . . . . . . . . . . . . . . . . . . . . . . . . . . . . . . . . . . . . . . . 119
Installation 121
Typical Installation . . . . . . . . . . . . . . . . . . . . . . . . . . . . . . . . . . . . . . . . . . . . . . . . . . . . . . . . . . 121
Overview of Cables. . . . . . . . . . . . . . . . . . . . . . . . . . . . . . . . . . . . . . . . . . . . . . . . . . . . . . . . . . 122
Attaching and Detaching the FM-1. . . . . . . . . . . . . . . . . . . . . . . . . . . . . . . . . . . . . . . . . . . . . . 122
Basic Installation Notes. . . . . . . . . . . . . . . . . . . . . . . . . . . . . . . . . . . . . . . . . . . . . . . . . . . . . . . 124
Electrical Installation. . . . . . . . . . . . . . . . . . . . . . . . . . . . . . . . . . . . . . . . . . . . . . . . . . . . . . . . . 125
Serial Communications . . . . . . . . . . . . . . . . . . . . . . . . . . . . . . . . . . . . . . . . . . . . . . . . . . . . . . . 137
Specifications 139
Electrical Specifications . . . . . . . . . . . . . . . . . . . . . . . . . . . . . . . . . . . . . . . . . . . . . . . . . . . . . . 139
Dimensions and Clearances . . . . . . . . . . . . . . . . . . . . . . . . . . . . . . . . . . . . . . . . . . . . . . . . . . . 140
Cables . . . . . . . . . . . . . . . . . . . . . . . . . . . . . . . . . . . . . . . . . . . . . . . . . . . . . . . . . . . . . . . . . . . . 142
Vendor Contacts . . . . . . . . . . . . . . . . . . . . . . . . . . . . . . . . . . . . . . . . . . . . . . . . . . . . . . . . . . . . 144

xiii
Glossary 145
Index 151

FM-1 Speed Module Reference Manual
xiv

1
Introduction
Overview
The FM-1 is a compact and rugged module that attaches to the front of the E Series drive. It
provides eight digital input lines and four digital output lines in addition to the four input and
three output lines available on the E Series drive. The FM-1 is setup using PowerTools-FM
software. PowerTools-FM is an easy-to-use Microsoft® Windows®-based setup and
diagnostics tool.
With the FM-1 installed, the base drive functions normally, with some additional features,
including eight more inputs and four more outputs. The additional major features include;
eight digital Torque presets, two additional Summation modes, plus an Alternate Operating
mode function.
Figure 1: E Series Drive with Function Module FM-1
Velocity Presets
The FM-1 offers eight Velocity Presets which operate the same as E Series drives. These
velocity presets are numbered 0 through 7 and are selectable with I/O. Each preset velocity
has a ramp associated with it, which is used whether the drive has to accelerate or decelerate
to achieve the selected speed.
FM-1 Speed Module Reference Manual

2
FM-1 Speed Module Reference Manual
Digital Torque Preset Mode
A digital torque submode selection has been added to the Torque mode. This offers eight
torque presets which are selectable with I/O or Modbus, and is in addition to the analog
command torque mode available in the base drive.
Summation Modes
Summation mode in the FM-1 has three summation mode choices:
• Analog Velocity + Preset Velocity
• Pulse mode + Analog Velocity
• Pulse mode + Preset Velocity
The Pulse Summation modes are advantageous in applications that require pulse following
plus the ability to adjust the phase relationship to the master by adding or subtracting velocity
to the ratioed master pulse rate. The Analog + Preset Velocity mode operates the same as it
does in the base drive.
Alternate Operating Mode
The FM-1 permits two different operating modes to be set up. It normally runs according to
the Operating Mode but can be switched to the Alternate Operating Mode by activating an
input function. This provides the user with the flexibility to use a drive with the FM-1 in
applications that previously required a complex controller.
Features
• Three Summation modes; Pulse + Analog Velocity, Pulse + Preset Velocity and Preset
Velocity + Analog Velocity
• Eight Velocity Presets
• Eight Torque Presets
• Eight optically isolated input lines
• Four optically isolated output lines
• Easy to attach and detach
• Easy-to-use Windows-based software
• Extensive fault sensing and diagnostics, including storage and time stamping of the last
10 faults
• No tuning needed for no-load to 10:1 inertia mismatch
• High performance tuning based on inertia, friction and response
• Removable I/O connectors for easy installation

3
Introduction
• Scalable Encoder Output
• Travel Limit functions
Figure 2: FM-1 Speed Module Features
Locking Latch
Aligning Tabs
100-Pin Connector
Front Back
Inputs
Outputs
10-30 VDC
1
2
3
4
5
6
7
8
1
2
3
4
+
-
Speed Module
Inputs
Outputs
10-30 VDC
MODEL
FM-1
PART
960503-01
REV
EB/09
SER
9820B025

4
FM-1 Speed Module Reference Manual
Table of contents
Popular Switch manuals by other brands
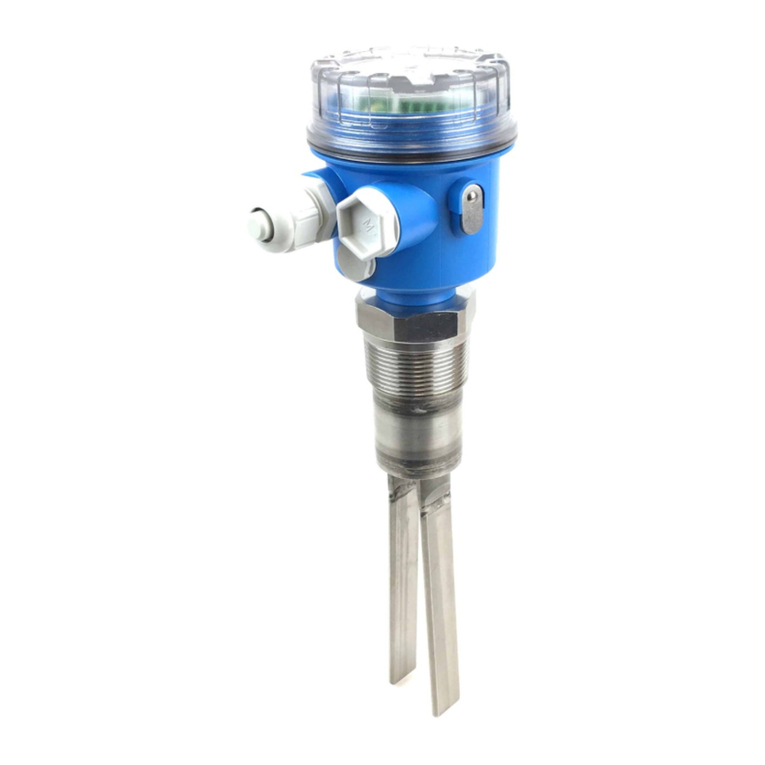
Endress+Hauser
Endress+Hauser Soliphant M FTM50 technical information
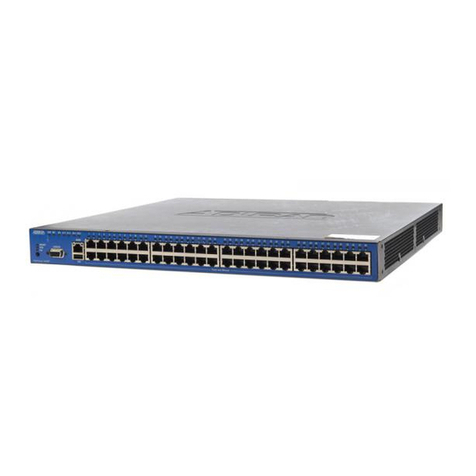
ADTRAN
ADTRAN NetVanta 1638 Hardware installation guide
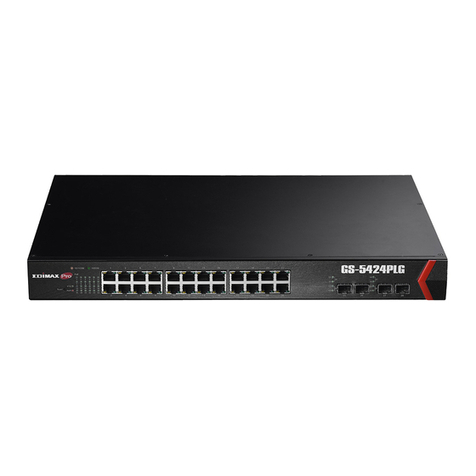
Edimax
Edimax GS-5424PLG How to set up

Encore
Encore ENKVM-USB Specifications

Briggs & Stratton
Briggs & Stratton 71057 installation manual
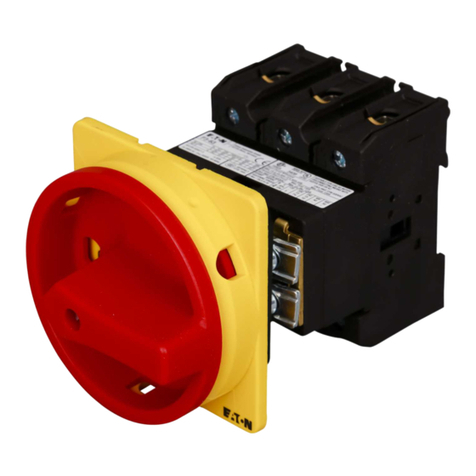
Moeller
Moeller P3 Series installation instructions