Cosa 9610 User manual

INSTALLATION, OPERATION AND MAINTENANCE MANUAL – COSA 9610™
2 | Page
INSTALLATION,
OPERATION
AND
MAINTENANCE
MANUAL
COSA 9610™
Version:
1.4.6
Revision date: Nov 9th, 2021
CAL.01.
D
.9826

INSTALLATION, OPERATION AND MAINTENANCE MANUAL – COSA
9610™
3 | Page
COSA Xentaur CORPORATION
New York Texas Corporate Headquarters,
Manufacturing Offices: Sales & Service Offices:
84G Horseblock Rd. 4140 World Houston Parkway
Yaphank, NY 11980 Suite 180
Tel: 631-345-3434 Houston, TX 77032
Tel: 713-947-9591
Fax: 713-947-7549
E-mail: service@cosaxentaur.com
http://www.cosaxentaur.com
Copyright ©
2021
All rights reserve
d.
The contents of this publication are presented for informational purposes only. While every effort has
been
made to ensure this document error-free, it should not be construed as warranties or
guarantees,
expressed or implied, regarding the product or services described herein or its use or
applicability.
COSA Xentaur Corporation reserves the right to revise or to improve the design or specifications of
the
COSA 9610™ at any time and without
notice.

INSTALLATION, OPERATION AND MAINTENANCE MANUAL – COSA
9610™
4 | Page
Table of Contents
1. INTRODUCTION....................................................................................................................................... 7
1.1. INTRODUCTION ................................................................................................................................ 7
1.1.1. Purpose of the analyzer ................................................................................................................. 7
1.2. THE COSA 9610™ ANALYZER .............................................................................................................. 7
1.2.1. Oven with oxygen sensor ............................................................................................................... 8
1.2.2. The sample system (SCS).............................................................................................................. 8
1.3. CALIBRATION PROCEDURE ............................................................................................................... 9
1.4. EXTENDED (DUAL) RANGE OPTION .............................................................................................. 11
1.4.1. Operation.................................................................................................................................... 11
1.5. SPECIFICATIONS COSA 9610™ WOBBE INDEX ANALYZER ...................................................... 11
1.5.1. Analyzer performance ............................................................................................................... 11
1.5.2. Utilities ........................................................................................................................................ 12
1.5.3. Installation.................................................................................................................................. 12
1.5.4. Connection ................................................................................................................................. 13
1.6 X-Purge Option..................................................................................................................................... 13
1.6.1. Purpose............................................................................................................................................ 13
1.6.2. Operation of X-purge and component kits................................................................................. 14
1.6.2.1 Operation ...................................................................................................................................... 15
1.6.2.2. Electronic Power Control Unit – EPCU ..................................................................................... 15
1.6.2.3. User-Interface Controller – UIC................................................................................................ 15
1.6.2.4. Pneumatic Manifold with I.S. Solenoid.................................................................................... 16
1.6.2.5. Purge Timing ............................................................................................................................... 17
1.6.2.6. Fixed Purge Time........................................................................................................................ 17
1.6.2.7. Dynamic Purge Time .................................................................................................................. 17
1.6.2.8. Purging Modes............................................................................................................................. 18
1.6.2.9. Inputs ........................................................................................................................................... 18
1.6.2.10. Outputs ...................................................................................................................................... 19
1.6.2.11. EPV-6000 I.S. Relief Vent........................................................................................................ 19
1.7 Z-Purge Option........................................................................................................................................ 20
1.7.1 Purpose............................................................................................................................................. 20

INSTALLATION, OPERATION AND MAINTENANCE MANUAL – COSA
9610™
5 | Page
1.7.2. Operation......................................................................................................................................... 21
1.8 Flow alarm ............................................................................................................................................... 21
1.9 System maintenance.............................................................................................................................. 23
2. INSTALLATION....................................................................................................................................... 24
2.1. GENERAL................................................................................................................................................. 24
2.2. STORAGE ................................................................................................................................................ 24
2.3. PLACEMENT............................................................................................................................................ 24
2.3.1. General ............................................................................................................................................ 24
2.3.2. COSA 9610™ in general purpose execution ............................................................................. 25
2.4. MECHANICAL CONNECTIONS.............................................................................................................. 25
2.4.1. General........................................................................................................................................ 25
2.4.2. Sample supply............................................................................................................................ 27
2.4.3. Calibration gasses...................................................................................................................... 27
2.4.4. Instrument Air Input ................................................................................................................. 27
2.5. ELECTRICAL CONNECTIONS ....................................................................................................... 27
2.5.1. Analyzer electronics (ATEX application). .................................................................................... 27
2.5.2. Analyzer electronics (NEC US application). ................................................................................ 28
3. IN OPERATION....................................................................................................................................... 28
3.1. START-UP SAMPLE CONDITIONING SYSTEM.............................................................................. 28
3.1.1. Inspection, visual and external connections .............................................................................. 28
3.1.2. Air orifice selection......................................................................................................................... 29
3.1.3. Opening of shut-off valves ........................................................................................................... 29
3.1.4. Setting of gas pressure reducer................................................................................................... 29
3.1.5. Adjusting flow with flow meters .................................................................................................. 29
3.1.6. Adjusting booster relays................................................................................................................ 30
3.2. START-UP OF THE CONTROL UNIT............................................................................................ 31
3.2.1. Description.................................................................................................................................. 31
3.2.2. Programming the measurement parameters......................................................................... 31
3.2.3. Main screen.................................................................................................................................... 32
3.3. PROGRAMMING MENUS ...................................................................................................................... 36
3.3.1. Calibration Menu........................................................................................................................ 36
3.3.2. Operation Menu........................................................................................................................ 36

INSTALLATION, OPERATION AND MAINTENANCE MANUAL – COSA
9610™
6 | Page
3.3.3. Measurement Menu................................................................................................................... 37
3.3.4. Output Menu .............................................................................................................................. 38
3.3.5. Communications Menu.............................................................................................................. 40
3.3.6. System Menu.............................................................................................................................. 41
3.3.7. Reset Alarms Menu.................................................................................................................... 43
3.4. TEMPERATURE CONTROLLED OVEN.................................................................................................. 43
3.4.1. Furnace temperature control unit................................................................................................ 43
3.4.2. Adjustment procedure temperature regulator......................................................................... 44
4. PREVENTIVE MAINTENANCE............................................................................................................ 45
4.1. WEEKLY, MONTHLY, THREE (3) MONTH MAINTENANCE............................................................... 45
4.1.1. Filters.............................................................................................................................................. 45
4.2. ANNUAL MAINTENANCE....................................................................................................................... 45
4.3. TROUBLESHOOTING......................................................................................................................... 46
4.4. REPLACEMENT OF RESIDUAL OXYGEN SENSOR AND CELL HOUSING....................................... 47
5. MODBUS REGISTER LIST
....................................................................................................................... 53
5.1. COIL REGISTERS .................................................................................................................................. 53
5.2. DISCRETE INPUT REGISTERS............................................................................................................ 54
5.3. INPUT REGISTERS................................................................................................................................ 55
5.4. VARIABLE LIST...................................................................................................................................... 68
6. INSTALLATION DRAWING
.................................................................................................................... 69
7. ORDERING OF SPARE PARTS................................................................................................................ 70
7.1 COSA 9610 Standard Temperature Spare Parts List as of 5-2021 ............................................... 70
7.2 COSA 9610 Mid Temperature Spare Parts List as of 5-2021 ......................................................... 72
8. CERTIFICATION
........................................................................................................................................ 75

INSTALLATION, OPERATION AND MAINTENANCE MANUAL – COSA
9610™
7 | Page
1. INTRODUCTION
1.1. INTRODUCTION
1.1.1. Purpose of the analyzer
The continuous COSA 9610™ analyzer determines online the Wobbe-index of a gas. The
COSA 9610™ can be used both, as feed forward and feedback analyzer for gases mixing
or as a feed forward analyzer for burning control. In order to achieve an optimal
performance of the analyzer system it is necessary to read this manual thoroughly before
installation and start-up.
For the combustion of gas, air is required. When supplying the right quantity of air, the
gas will completely burn. This is the so-called stoichiometric air requirement of the gas.
Because of this, the Wobbe-index can also be seen as a value for the need of air in gas.
By burning the gas with a small excess of air, the flue gas will contain the remaining
oxygen from the air, which has not taken part in the combustion. When the Wobbe-
index of a gas changes, the stoichiometric air requirement, and the percentage of the
remaining oxygen in the flue gas will change simultaneously. By measuring the
concentration of oxygen in the flue gas, after calibrating the instrument with two gasses
with known Wobbe-index, the Wobbe index can be calculated.
1.2. THE COSA 9610™ ANALYZER
The COSA 9610™ features fast response time and high accuracy. These features make it
unique over conventional Wobbe index analyzers. The oxygen concentration in the air is
considered as constant, namely 20.95%. Functionally we can divide the analyzer-unit in 3
major parts:
•
Sample System
•
Electronics compartment
•
Oven compartment
Optionally the COSA 9610™ can be built in an explosion proof execution. In explosion
proof execution, the analyzer is protected with a purge system.
WARNING - Potential Electrostatic Charging Hazard.
Due to the materials construction of the viewing port, there is a potential to build up an
electrostatic charge across the surface. Suitable precautions should be taken to reduce
this risk.

INSTALLATION, OPERATION AND MAINTENANCE MANUAL – COSA
9610™
8 | Page
1.2.1. Oven with oxygen sensor
The gas/air mixture is burnt catalytically in an oven, which is kept at 812ºC with a heating
spiral. The temperature is maintained with temperature control using a K-type
thermocouple. The oxygen sensor in the oven is a zirconium oxide cell. This is mounted
such, that one side is in contact with the outside air and the other side with the flue
gasses. At high temperatures, (600ºC) O2-ions in the ZrO2 grating become mobile through
vacancies therein. By fixing porous Pt-electrodes at both sides of the ZrO2, O2, gas
molecules can, through diffusion by and uptake of two electrons from the Pt electrode,
enter the ZrO2 as O2-ion, move to the other electrodes, and be converted in gaseous O2
again by release of the two electrons.
1.2.2. The sample system (SCS)
In the sample conditioning system (SCS), gas and air are mixed in a constant proportion,
such that a small excess of air is present (± 2.5% oxygen) in the flue gas. The gas and air
pressure are equalized by a dome-loaded pressure reducer (or booster relay), where the
gas pressure governs the air pressure.
The booster relay has a temperature reducing effect; the gas/air mixing proportion can
therefore vary as consequence of variations in viscosity. Therefore, the temperature of the
gas and the air are equalized in a heat exchanger. The gas and air temperature are still at
surrounding temperatures, however, as long as gas and air fluctuate to the same extent
this hardly influences the mixing proportion. In case of large surrounding temperature
fluctuations, the calibration sequence has to be performed more often. Hereafter gas and
air are mixed in the mixing chamber. The mixing chamber is equipped with orifices in the
inlet nozzles. The gas and airflow are determined by a critical expansion over the orifices.
The turbulence created provides a homogeneous mixture.
The diameter ratio of the orifices, together with the ratio between gas and air pressure,
determine the mixing proportion.

INSTALLATION, OPERATION AND MAINTENANCE MANUAL – COSA
9610™
9 | Page
After the mixing chamber, the mixture flow is divided into an excess flow to vent and a
flow to oven. The flow to the burning oven will be approximately 30-50 Nl/hr (500 - 800
Ncc/min). The vented stream is approximately 500 Nl/hr (8000 Ncc/min) with a maximum
1000 Nl/hr (16,000 Ncc/min).
1.3. CALIBRATION PROCEDURE
The analyzer can be calibrated in three different ways:
•
Single point calibration
Only one calibration gas is used. The value of the gas is chosen middle of the
measuring range. This is only used to correct any offset error to the measurements.
•
Two-point calibration
Two calibration gases are used. The low calibration gas is set at ± 20% of the
measuring range. The high calibration gas is set at ± 80% of the measuring range.
The advantage over a single point calibration is the increased accuracy over the entire
span.
•
Three-point calibration
This method uses three calibration gases and is mandatory for a dual range analyzer.
The medium range calibration gas must be in the middle of the measuring range.
All three calibration methods can be performed both manually and automatically:
•
Manually
The operator navigates the procedure via on-screen menu to open the correct gas
valves to the analyzer. The operator controls the timing.
•
Automatically

INSTALLATION, OPERATION AND MAINTENANCE MANUAL – COSA
9610™
10 | Page
The analyzer itself controls the timing of the valves
switching.
When the measured
values stay within the specified tolerances, the newly calculated calibration.
parameters will be accepted. Otherwise, the analyzer will keep the old value and
generates a CAL ERROR on the display and switch the system fault contact and
calibration fault contact.
The automatic calibration can be started as followed:
•
Programmable time schedule (Timed calibration)
•
Initiated manually via on-screen menu (Semi-automatic calibration)
•
External host activates the calibration request contact (Remote calibration)
The one-point calibration/validation procedure will be executed as followed:
1. Analyzer activates calibration/validation contact.
2. The procedure pauses for the specified “Calibration Start Delay” time for the
external host to prepare for calibration/validation.
3. Process gas is switched off and the calibration gas is switch on.
4. The analyzer waits for the readings to stabilize up to the “Switch Time”.
5. Calibration gas is switched off and the process gas is switched on.
6. Analyzer deactivates calibration/validation contact.
The two-point calibration/validation procedure will be executed as followed:
1. Analyzer activates calibration/validation contact.
2. The procedure pauses for the specified “Calibration Start Delay” time for the
external host to prepare for calibration/validation.
3. Process gas is switched off and the low calibration gas is switch on.
4. The analyzer waits for the readings to stabilize up to the “Switch Time”.
5. Low calibration gas is switched off and the high calibration gas is switched on.
6. The analyzer waits for the readings to stabilize up to the “Switch Time”.
7. High calibration gas is switched off and the process gas is switched on.
8. Analyzer deactivates calibration/validation contact.
The three-point calibration/validation procedure will be executed as followed:
1. Analyzer activates calibration/validation contact.
2. The procedure pauses for the specified “Calibration Start Delay” time for the
external host to prepare for calibration/validation.
3. Process gas is switched off and the low calibration gas is switch on.
4. The analyzer waits for the readings to stabilize up to the “Switch Time”.
5. Low calibration gas is switched off and the medium calibration gas is switched on.
6. The analyzer waits for the readings to stabilize up to the “Switch Time”.
7. The analyzer switched the gas stream to the high range mixing chamber.
8. The analyzer waits for the readings to stabilize up to the “Switch Time”.

INSTALLATION, OPERATION AND MAINTENANCE MANUAL – COSA
9610™
11 | Page
9. Medium calibration gas is switched off and the high calibration gas is switched on.
10.
The analyzer waits for the readings to stabilize up to the “Switch Time”.
11.
High calibration gas is switched off and the process gas is switched on.
12.
Analyzer deactivates calibration/validation contact.
Between each step of the calibration process a switch time is programmed enabling the
analyzer to stabilize. After the switch time the new value is used in the calibration
algorithm. The calibration gas switch time is user programmable. By default, it is set at
120 seconds. Depending on the distance to the calibration gases it may be necessary to
change to a longer or shorter delay.
1.4. EXTENDED (DUAL) RANGE OPTION
1.4.1.Operation
When the measuring range of the analyzer is larger than 1150BTU/SCF, an
extended range option is available which covers a Wobbe index of 2730.BTU/SCF.
This is accomplished by adding a second gas-mixing orifice and selection valves to
make changeover possible.
The dilution ratios of each mixing orifice are chosen such that the measuring ranges
overlap.
Via the software it is possible to create a 4/20mA current loop signal that covers the
whole range. It is necessary to establish a switch over point that must be calibrated.
For this reason, the calibration system is expanded with an extra solenoid valve.
1.5. SPECIFICATIONS COSA 9610™ WOBBE INDEX ANALYZER
1.5.1.Analyzer performance

INSTALLATION, OPERATION AND MAINTENANCE MANUAL – COSA
9610™
12 | Page
Make
Cosa Xentaur Corporation
Service
Natural gas, fuel-gas, biogas, etc.
Ranges
Wobbe index 0-2730 BTU/scf (0-102 MJ/Nm3),
span 0-1150 BTU/scf (43 MJ/Nm3) (selectable)
CARI 0-20, span 0-10
Accuracy
± 0.4% of measuring value natural gas
Repeatability
±0.7 BTU/scf (±0.03 MJ/Nm3)
Drift
< 0.4 BTU/scf (< 0.01 MJ/Nm3)/ 24 hours
Response time
T90<5 seconds†
T90 >10 second with Density Cell
Output
2 isolated 4-20 mA outputs, 4 outputs total optional
Span and service selectable
Display & Optional Digital Output/ RS485, TCP/IP
8 User-programmable contact relays
Safety
General area
† Wobbe w/o density cell or with streaming S.G. option
1.5.2.Utilities
Power supply
110 VAC, 50/60 Hz or 230 VAC/50 Hz
Power consumption
1260 VA to 3000 VA maximum based on options
Instrument air
20 SCFH (566 SLPH) (base analyzer) at 42psig
40 SCFH (1,133 SLPH) (z-purge) at 80psig
444 SCFH (12,579 SLPH) (purge and vortex system) at 80psig
Sample
2 SCFH (0.94 SLPM) at 28psig
1.5.3.Installation
Mounting
Freestanding Frame.
Dimensions
40.8 x 40.8 x 16.3 inches (1000 x 1000 x 400 mm)
Weight
Up to 450 lbs (204 kg). Shipping weight 750 lbs (340 kg)
Ambient temperature
50 to 104º F (10 to 40 °C)
Extended range to -40 to 140°F (-40 to 60°C) With Heater and
Vortex Cooler options in electronics cabinet
Allow ambient temperature variation: ±45ºF (7 °C) per 24 hours
Sunshade or three-sided shelter recommended were possible
Humidity
0-90%

INSTALLATION, OPERATION AND MAINTENANCE MANUAL – COSA
9610™
13 | Page
1.5.4.Connection
CONNECTION
SERVICE
SIZE
DESCRIPTION
MAT'
NOTE
N1 PROCESS GAS 1/8" OD
COMPRESSION
FITTING
SS-316
N2
CALIBRATION GAS
LOW
1/8" OD
COMPRESSION
FITTING
SS-316
N3 CALIBRATION GAS MID 1/8" OD
COMPRESSION
FITTING
SS-316
IF
APPLICABLE
N4 CALIBRATION GAS HI 1/8" OD
COMPRESSION
FITTING
SS-316
N5 INSTRUMENT AIR 1/2" OD
COMPRESSION
FITTING
SS-316
N7 ATMOSPHERIC VENT
(GAS BYPASS) 1/4" OD COMPRESSION
FITTING SS-316
N8 ATMOSPHERIC VENT
(VENT FROM OVEN)) 1/4" OD COMPRESSION
FITTING SS-316
1.6 X-Purge Option
1.6.1. Purpose
The COSA 9610™ Calorimeter is protected by a Pepperl & Fuchs X-purge unit. The purge
Type X and Ex px purge pressurization system protects general-purpose equipment mounted
in a standard enclosure so that it can be located and operated in a hazardous area. The
hazardous area classification can be Class I and/or Class II, Division 1/Zone 1 and/or Zone

INSTALLATION, OPERATION AND MAINTENANCE MANUAL – COSA
9610™
14 | Page
21. The X-purge operates by controlling and monitoring compressed instrument air through
the protected enclosure(s) to remove and prevent the accumulation of flammable gas,
vapors, or dust.
The X-Purge system features these main parts:
•
Electronic processor (EPCU) housed in an explosion/flameproof enclosure
•
I.S. electrical/pneumatic manifold assembly
•
Input/output connections and controls for operation
•
I.S. user interface for programming and monitoring the system
•
316L stainless steel type 4X IP66 enclosure for EPCU and connections
•
Pressure relief vent with flow and pressure monitoring at the exhaust
The user interface allows programming of up to 4 switch inputs, temperature modules,
enclosure power contacts, 2 auxiliary outputs, and various operational functions. Also, the
user interface screen allows monitoring and easy setup of configurable variables. With the
user interface menus, configuration of the standard information for setup and operation of a
system such as purge time, flow rates, pressures, and enclosure size are easily
programmable. Additional features allow Class I and Class II operation, inputs for system
bypass, enclosure power on/off, temperature overload and activation of Rapid Exchange
flow for cooling or auxiliary relay for separate cooling source, delay power shutdown, and
much more. The two auxiliary contact outputs can be configured to activate on most of the
input switches or any of the configured alarm states for pressure, flows, and temperature.
The power for the solenoid valve on the manifold unit, inputs, and EPV-6000 vent are
provided by the EPCU through the internal, galvanically isolated intrinsic barrier. No
additional intrinsic safety barriers are required for annunciation.
The X-Purge provides a complete system for purging and pressurizing enclosures for
hazardous location operation.
The X-Purge system can be set up for Class I/ Division 1 (Zone 1), Class II/Division 1 (Zone
21), or both Class I & Class II/Division 1(Zone 1 & Zone 21) applications in accordance with
the NEC-NFPA 70, NFPA496, ISA 12.4, IEC61241-4, and EN60079-2. This system also
complies with IEC61508, SIL 2 level of integrity with SIL 3 option available.
1.6.2. Operation of X-purge and component kits

INSTALLATION, OPERATION AND MAINTENANCE MANUAL – COSA
9610™
15 | Page
1.6.2.1 Operation
The X-Purge consists of the control unit and user interface mounted in a 316L stainless steel
Type 4X (IP66) enclosure with the pneumatic solenoid valve mounted on the unit. A
proportional valve can be ordered in place of the solenoid valve for continuous control of
flow and pressure to the enclosure.
The EPV-X-Purge relief vent is separate and is mounted to the enclosure. The components
of the X-Purge control unit are listed below:
•
EPCU mounted in an explosion/flameproof enclosure
•
I.S. user-interface with display and cable
•
I.S. termination board (does not come with ‘CK’ kit version)
•
Manifold with I.S. solenoid valve (does not come with ‘CK’ kit version)
•
Flush mount type 4X IP66 fitting for protective gas supply to enclosure with tube attached
•
Type 4X cable glands for I.S. wiring to I.S. inputs, vents, and temperature modules
•
316L stainless steel pipe nipples for power wires
•
316L stainless steel type 4X enclosure for the X-Purge controller
The components of the EPV-6000 vent:
•
EPV-6000 vent with spark arrestor screen
•
1½” sealing nut with gasket for attachment of vent to customer’s enclosure
•
One 5 meter, quick disconnect cable; blue (denoting I.S.), for connection to I.S.
termination board inside X-Purge control unit
The X-Purge control unit and vent are mounted to the calorimeter enclosure. Bottom, right
side mounting can be completed with only one control unit and vent. One unit is used for
enclosure sizes up to 450 ft3 (12.7 m3).
1.6.2.2. Electronic Power Control Unit – EPCU
The EPCU houses the redundant microprocessors, enclosure power contacts, (2) auxiliary
contacts, power supply module, galvanically isolated barriers for the inputs, vent(s), and
temperature modules; all stackable and easy to remove and install into the explosion proof
enclosure that houses them.
The power supply module is available in 24 VDC or 100-240 VAC units. The enclosure power
contacts are forced-guided safety relays. The auxiliary contacts can be user configured for
different functions depending on user requirements.
1.6.2.3. User-Interface Controller – UIC

INSTALLATION, OPERATION AND MAINTENANCE MANUAL – COSA
9610™
16 | Page
The X-Purge is user programmable for many of the configurable options available. This is
done with the intrinsically safe user-interface on the face of the unit, which can also be
remote mounted. The user-interface is a 2 x 20 LCD that is programmed through a set of
buttons on the menu driven unit. All configuration and options are programmed through
this unit. There are also (5) LEDs for easy visual indication of operation:
•
Safe Pressure – This turns on (blue) when safe pressure is achieved inside the
enclosure.
•
Enclosure power – This is (red) when the enclosure power is off, and (green) when
enclosure power is on. The enclosure power can be on only after a successful purge
and a safe pressure is achieved. Bypass option allows power to remain on if safe
pressure is lost.
•
Rapid Exchange® – The Rapid Exchange or purging flow rate turns on (blue) when the
flow rate is measuring proper flow.
•
System Bypass – This turns on (yellow) when the system bypass is active. This should
be used only when the area around the enclosure is known to be safe.
•
Alarm Fault – The (red) LED blinks when any alarm input is detected and is solid when
there is an internal system fault.
1.6.2.4. Pneumatic Manifold with I.S. Solenoid
•
Manifold with I.S. solenoid valve: The manifold system is mounted on the 6000 control
unit providing a needle valve to set enclosure pressure and an I.S. solenoid valve that is
used for purging (Rapid Exchange). Power for the I.S. solenoid valve is provided by the
EPCU and is galvanically isolated. Regulated instrument-grade air is required.
• Proportional valve option: The I.S. proportional valve is separated on the 6000 control unit
and provides continuous flow and pressure to the enclosure for purging (Rapid Exchange)
and pressurization. Power for the I.S. solenoid valve is provided by the EPCU and is
galvanically isolated. No needle valve is required. Pressures can be controlled from a user
set-point.
Certifications allow the X-Purge to be used on enclosures in a gas hazardous atmosphere.
Gas atmospheres require the purging of the enclosure. Dust atmospheres require the
physical removal of all the dust that collects inside. Both gas and dust atmospheres require
the following:
1) removing the dust,
2) sealing the enclosure, and then
3) purging the enclosure.

INSTALLATION, OPERATION AND MAINTENANCE MANUAL – COSA
9610™
17 | Page
After these sequences, the pressure within the enclosure is above the minimum level. The
equipment within the enclosure can be energized.
1.6.2.5. Purge Timing
When using the X-Purge in a gas or gas and dust location, the time for purging an enclosure
can be based either on a known purge rate and time (fixed purge time), or based on the
flow rate being measured from the vent (dynamic purge time). Both methods base the time
on the flow measurement at the vent, and complete the process in steps. The EPCU will take
the readings from the vent and use the appropriate reading (listed below) as the useable
flow rate. For example, if the flow rate measurement from the EPV-6000 vent is 7 SCFM, the
EPCU will use 5 SCFM as the flow rate for evaluation. The flow rate measurement steps and
corresponding enclosure pressures are as follows:
•
5 SCFM @ 1.3” w.c. , (141 l/min @ 33 mm w.c.)
•
12 SCFM @ 2.5” w.c., (340 l/min @ 64 mm w.c.)
•
20 SCFM @ 3.1” w.c., (565 l/min @ 77 mm w.c.)
•
30 SCFM @ 3.4” w.c., (850 l/min @ 86 mm w.c.)
The COSA 9610™ uses the first setting of 5 SCFM @ 1.3” w.c. to establish the purge within
the enclosures. This volume exchange and purge timing is factory set to 8mins, but can be
re-configured to a different value if required by the Area Authority having jurisdiction at the
installation site.
1.6.2.6. Fixed Purge Time
If the purge time must be held to a specific time, then this time is based on the known
enclosure volume, number of volume exchanges, and flow rate through the vent. If the flow
rate is below the required minimum, then the purging cycle will reset and will not start until
the flow rate is above the selected rate. This set up does not allow purge flow to go below
the value required and will not recalculate the time for purging if it goes above the required
purge rate.
1.6.2.7. Dynamic Purge Time
Dynamic purge time allows the purge time to be updated to the purge flow through the
vent. This method is not dependent on a constant flow from the protective gas source. It
bases the purge time on the measured flow and not a set flow. This is very useful when the
protective gas supply pressure varies throughout the purging cycle or when it may vary from

INSTALLATION, OPERATION AND MAINTENANCE MANUAL – COSA
9610™
18 | Page
one installation to another.
The following parameters must be entered for the dynamic purge time:
• Enclosure volume
• Number of exchanges
The purge time will be based on the measurement of the vent and evaluation of this
measurement from the EPCU. This allows recalculation of the time based on this
measurement. During the dynamic purge time, the user-interface will display the purge time
in a percentage starting with 0% and ending with 100% (purge time complete).
1.6.2.8. Purging Modes
Purging start-up can be set up in 4 different modes, which are explained below:
• STD – Standard mode requires the operator to engage the manifold solenoid valve
manually when purging and manually disengage when a successful purging is
complete.
• SA – Semiautomatic mode requires the operator to engage the manifold solenoid
valve manually when purging. The EPCU will automatically disengage when a
successful purging is complete.
• FA – Fully-automatic mode will automatically engage the manifold solenoid valve
when safe pressure is detected and will automatically disengage when a successful
purging is complete.
• PV –The proportional mode will continuously control the flow rate during and after
purging. This allows maximum efficiency of the protective gas supply. This is very
useful for areas where there is a limited amount of the protective gas supply
available.
1.6.2.9. Inputs
There are (4) intrinsic safety inputs for activation of various outputs and actions by the
EPCU. These inputs accept only a dry contact for activation and are supplied by the EPCU’s
galvanically isolated barrier. The assignments of the inputs for various actions are achieved
through the user-interface controller. Only one function can operate an input. These inputs
can bypass the system for live maintenance on the enclosure.

INSTALLATION, OPERATION AND MAINTENANCE MANUAL – COSA
9610™
19 | Page
The intrinsic safety inputs activate the auxiliary relays, energize the Rapid Exchange valve,
de-energize the enclosure contacts, and shut the system down, in addition to many more
actions and outputs.
1.6.2.10. Outputs
There are (2) normally open dry contacts for the enclosure power that can be energized
only after a successful purging and a minimum enclosure pressure is maintained. Loss of
pressure will cause the contacts to de-energize unless the shutdown timer is active, or
bypass mode is implemented.
Also available are the Auxiliary 1 and Auxiliary 2, SPDT dry contact outputs. The auxiliary
outputs can be user configured using the user-interface controller and are controlled by
various inputs or various conditions such as low pressure, loss of pressure, bypass
implemented, Rapid Exchange valve on, enclosure above maximum pressure setting, and
many more. Both enclosure contacts and auxiliary contacts are forced-guided safety relays
for functional safety.
1.6.2.11. EPV-6000 I.S. Relief Vent
The EPV-6000 vent exhausts excess pressure from the enclosure if the pressure within the
enclosure is above 1.0” w.c. and measures flow and pressure during operation. The X-Purge
vent has a pressure transducer and thermal flow sensor that is connected to the 6000 EPCU
and is intrinsically safe through the galvanic isolation barrier within the EPCU. Because
measurement of the flow is always at the exhaust of the pressurized enclosure, the vent is
located on the enclosure(s) such that it is venting to the atmosphere. The vent is connected
to the I.S. termination board using theV1 connector and cable that comes with the vent. The
EPV-6000 vent can be mounted vertically or horizontally and is not gravity dependent. For
corrosive environments, the EPV-6000 has an optional stainless-steel cap so that the body of
the vent is mounted in the enclosure with just the stainless steel cap exposed to the outside
environment.
The I.S. termination board is mounted inside the Type 4X (IP66) stainless steel enclosure
and does not require any lead seals to the EPCU enclosure. Wiring from the EPCU to this I.S.
termination board is provided. The power connection for enclosure power, auxiliary outputs
and power to the EPCU is completed within the explosion proof enclosure that houses the
EPCU. A stainless steel ¾” conduit extends to the outside of the Type 4X, IP66 stainless
steel enclosure for easy connection of the lead seals. Lead seals or Ex de cable glands are
not provided. Any certified lead seal or Ex de cable glands can be used. No special seals are
required. See X-purge manual for electrical connections.

INSTALLATION, OPERATION AND MAINTENANCE MANUAL – COSA
9610™
20 | Page
1.7 Z-Purge Option
1.7.1 Purpose
The COSA 9610™ Calorimeter is protected by a Pepperl & Fuchs’ Bebco EPS system type Z
rapid exchange purging system, model 1002. It allows the use of general purpose or
nonrated non-rated electrical or electronic devices, with exception to devices that produce
excessive heat, utilize combustible gas, or expose arcing contacts to the hazardous
atmosphere, in NEMA (National Electrical Manufacturers Association) 4 or 12 enclosures in
the place of explosion proof NEMA 7 enclosures. Other purposes include heat, moisture and
dust contamination prevention.
The purge Type Z pressurization system protects general-purpose equipment mounted in a
standard enclosure so that it can be located and operated in a hazardous area. The
hazardous area classification can be Class I, Division 2, Group B, C, D. The Z-purge operates
by controlling and monitoring compressed instrument air through the protected enclosure(s)
to remove and prevent the accumulation of flammable gas, vapors, or dust.
The Z-Purge system features these main parts:
•
Enclosure pressure gauge
•
Enclosure pressure control valve
•
Rapid exchange control valve

INSTALLATION, OPERATION AND MAINTENANCE MANUAL – COSA
9610™
21 | Page
•
Rapid exchange pressure gauge
•
Venturi orifice
•
Regulator
•
EXP pressure loss alarm switch
1.7.2. Operation
With the inert gas supply connected, enclosure power deenergized and alarm system
energized (if utilized).
1. Carefully read start-up instruction nameplate on system.
2. Check operation of the enclosure protection vent (model EPV-2), opening it manually
several times.
3. Seal protected enclosure.
4. Open enclosure pressure control valve, by turning CCW, to set enclosure pressure
gauge at “safe” pressure, the pressure loss alarm switch should then activate to silence
the alarm system (if utilized).
5. Ensure the protection system enclosure pressure gauge maintains a “safe” pressure
for one (1) minute.
6. Open Rapid Exchange control valve fully by turning 90° CCW and quickly ensure the
enclosure protection vent opens. Note: The enclosure pressure gauge should move
quickly off scale to the right, this is normal for all Rapid Exchange purging systems.
7. Standby for the exchange time as specified on the start-up instruction nameplate (five
minutes minimum), then close the Rapid Exchange control valve fully.
8. Wait for the enclosure pressure gauge to return to a "safe" pressure and energize the
protected enclosure power via the local disconnect switch.
9. Ensure the enclosure pressure indicator maintains a “safe” pressure before leaving
system unattended.
1.8 Flow alarm
The flow alarm is an ABB Automation Series 10A6100 PurgemasterTM meter. It is a low capacity, glass
Other manuals for 9610
2
Table of contents
Other Cosa Measuring Instrument manuals
Popular Measuring Instrument manuals by other brands
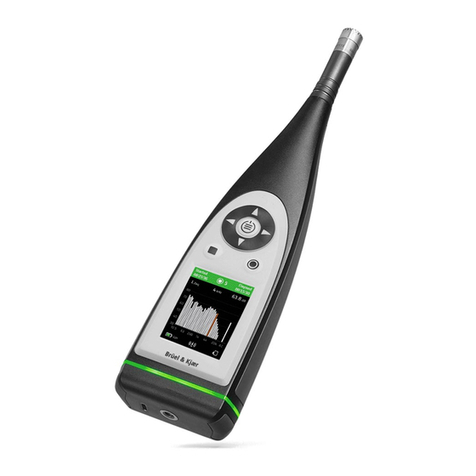
BRUEL & KJAER
BRUEL & KJAER 2245 instruction manual

Doran Scales
Doran Scales APS2200 Series Technical manual
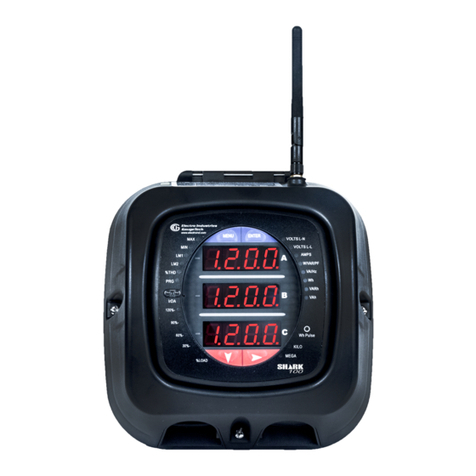
Electro Industries/GaugeTech
Electro Industries/GaugeTech Shark 100 Installation and operation manual
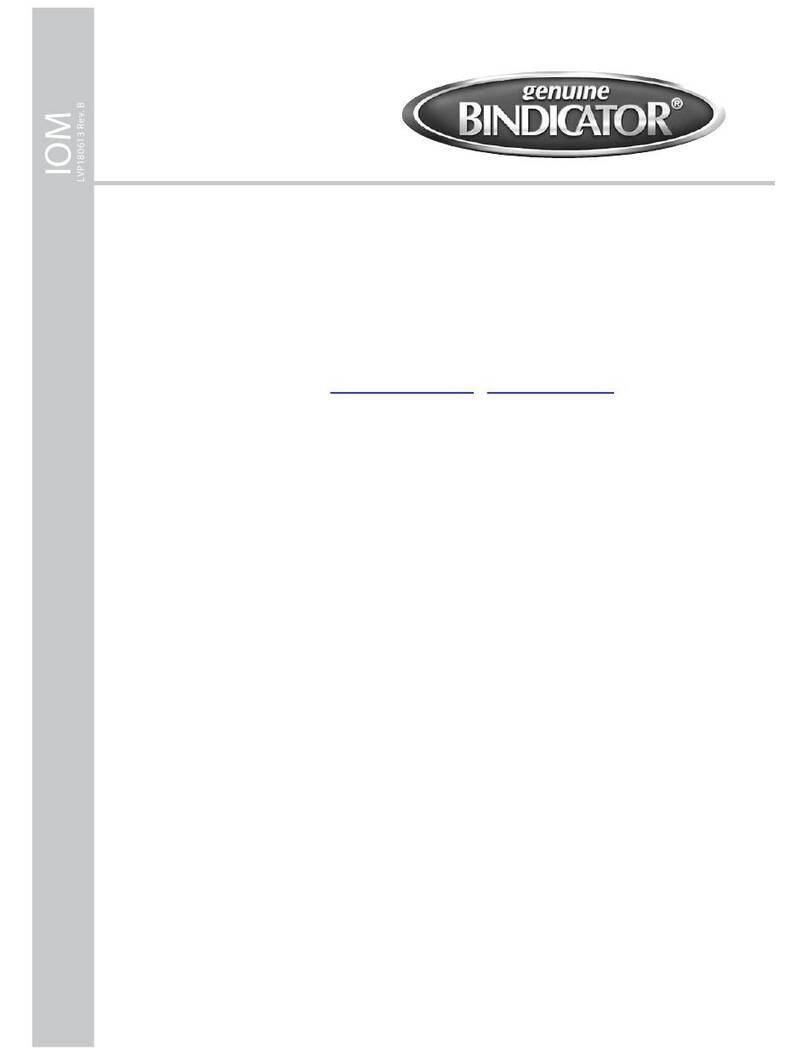
Bindicator
Bindicator Pulse Point II Series Installation & operation manual
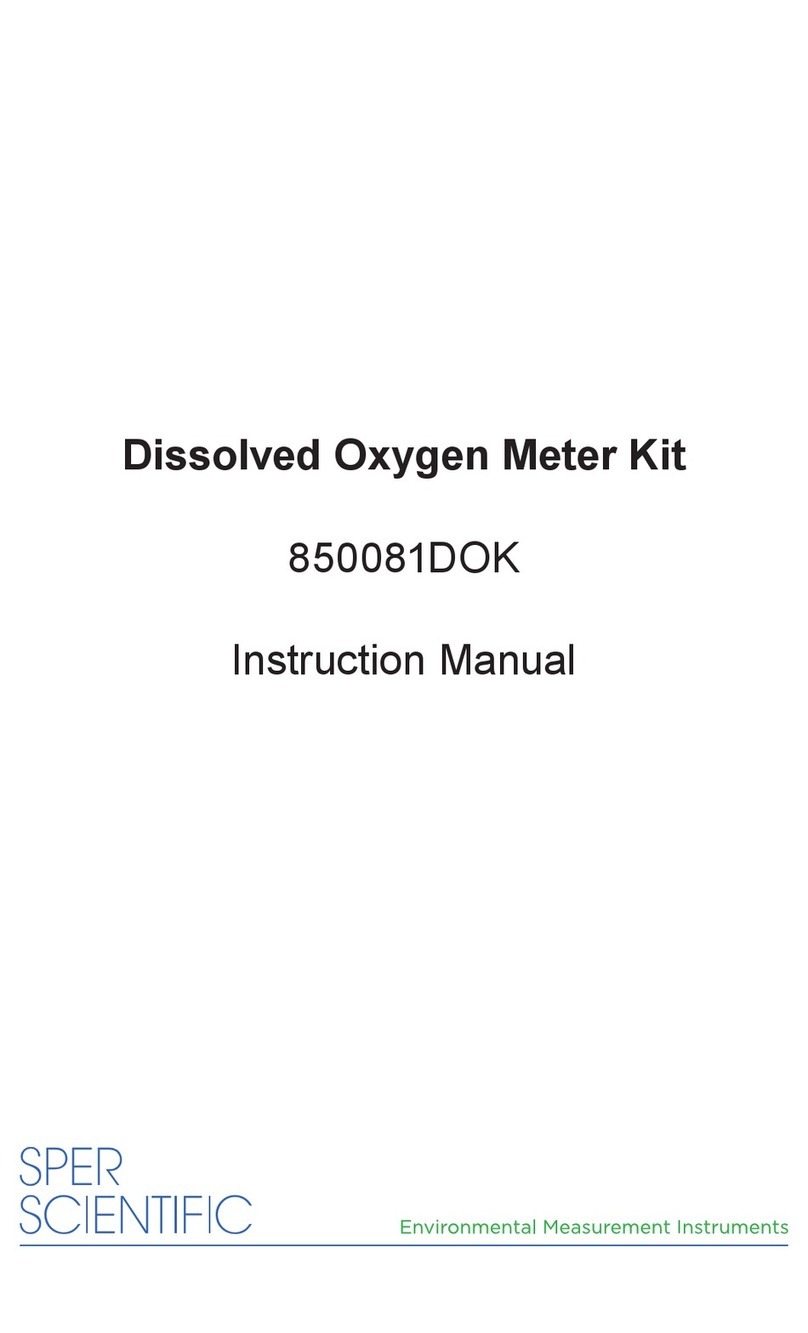
Sper scientific
Sper scientific 850081DOK instruction manual
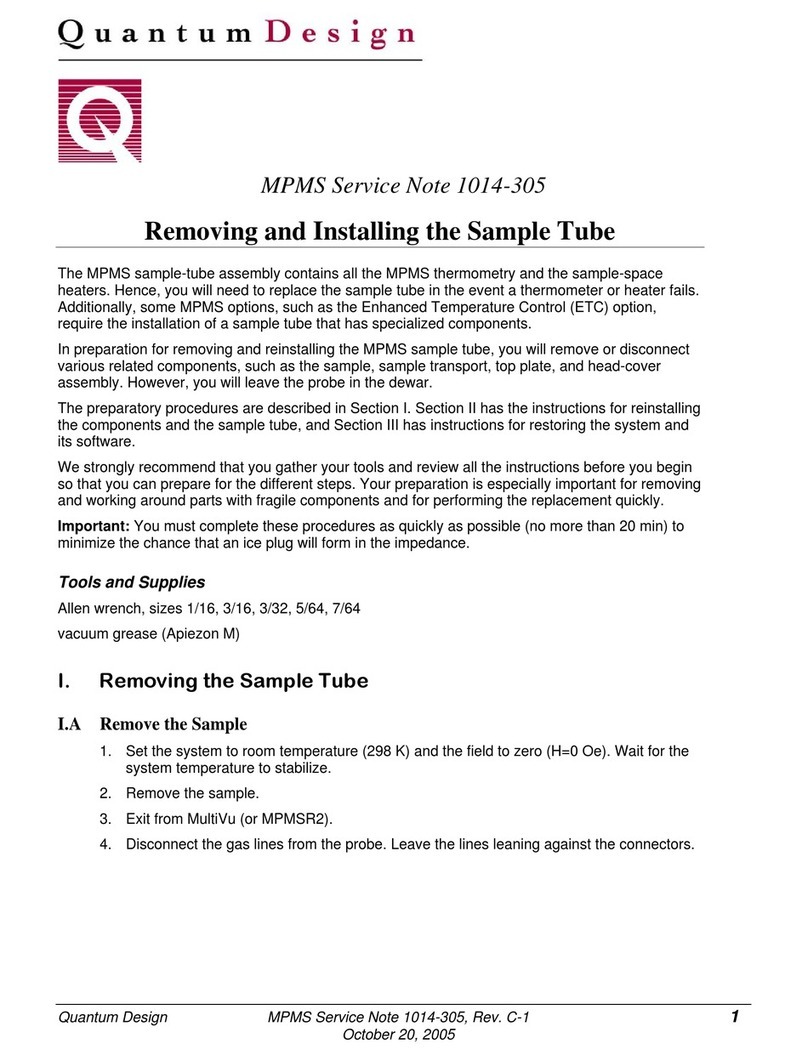
Quantum Design
Quantum Design MPMS Service note