CTB BKSC GNX Series User manual

DATA NO.: ZL-18-1118-IBCN
The information may be changed while the product is being improved without further notice.
ADD: #9 Yunxi 6 Ave Development Zone Miyun Dist
Beijing China
Tel: +86 10-69076533
Fax: +86 10-69076577
24 Hours Free Hotline: 400-888-9055
CTB TECHNOLOGY
Distributor
CTB Co.,Ltd

DATA NO.: ZL-18-1118-IBCN
CTB Co., Ltd.
GH DRIVER
Operating manual
AC servo driver
Model: BKSC - □ □ □ □ GHX
Class 400V, 1.5 ~ 315KW (2.5 ~ 460KVA)
Please send the manual to final user, and keep it properly.
CTB TECHNOLOGY

GH DRIVER
Thank you for purchasing GH series servo driver produced by Beijing CTB Servo Co., Ltd. The GH series
AC servo driver is a high-quality, multi-functional and low-noise AC servo driver that was researched,
developed and manufactured by Beijing CTB Servo Co., Ltd. The driver is servo driver for AC induction
motor (IM) and AC permanent magnet synchronous motor (PM). It can control the position, speed,
acceleration and output torque of various AC servo motor appropriately.
In command to achieve control functions of various machine tools, GH series AC servo driver is
equipped with dual 32-bit CPU and abundant control function module. It can be conveniently
connected with various domestic and foreign CNC systems through standard control interfaces to
allow full play for function of CNC system. The characteristics of torque, acceleration and deceleration,
precision and efficiency of machine tool which is equipped with GH series AC servo driver are
remarkable, and accurate stop, C-axis, rigid tapping, electronic shift, multi-axis synchronization and
other functions can be realized easily.
As the first choice of driving product of various machine tool power shaft, GH series AC servo driver can
be widely used for drive of product such as CNC milling machine, vertical machining center, horizontal
machining center, CNC boring machine, CNC lathe, vertical lathe, heavy horizontal lathe and gantry
machine tool.
For proper application, please read the manual carefully before using the GH series AC servo driver.
Abnormal operation, fault or reduction of service life, and even personal injury accident may be caused
by inappropriate use. Therefore, the manual shall be read repeatedly before use, and operate in
strict accordance with the instructions. The manual is attachment with the equipment. Please keep it
properly after using for future repair and maintenance of the driver.
Preface
01

GH DRIVER
The following symbols are used for safety-related content in the manual. Sentences marked by the safety symbols
describe important content, and must be abided. If the requirements in the safety-related content are not abided,
application of the product may lead to abnormal product operation, damage to the product, even danger and
personal injury.
Use the symbol where danger, even personal injury or death when wrong about the
described content.
Use the symbol where danger, even mild or moderate personal injury and equipment
damage when wrong about the described content.
Prohibited matters (matters that cannot do).
Certain matters do not belong to “danger”, and “caution”, but they are required to be
abided by user. They are marked in the relevant sections.
Safety -related symbol description
Caution
Danger
02
Forbid
Important

GH DRIVER
Safety precautions
◆Installation
◆Wiring
◆Unpacking inspection
03
●For risk of injury, please do not install damaged or part missing driver.
●For risk of fire, please install the equipment on nonflammable metal plate without
combustible materials around.
●Please be sure to tighten the mounting screws of the driver. Falling and damage of the
driver or personal injury may be caused by mounting screws loosing.
●Please do not install the equipment in environment with flammable gas where an
explosion is caused easily.
●For risk of electric shock and fire, please make sure that the input power supply is in
the OFF state before wiring.
●For risk of electric shock, the operation on main circuit terminal of the controller shall
be conducted after the power is cut off for five minutes, and the power charge
indicator CHARGE in the controller completely extinguished.
●For risk of electric shock and fire, the wiring shall be carried by professional electrical
engineering personnel.
●For risk of electric shock and fire, the ground terminal must be grounded reliably.
(earth resistance shall be lower than 4Ω)
●It’s prohibited to directly connect terminals of P / PB and N, or connect the zero line or
the earth wire to the N terminal. Otherwise, the rectifier bridge will be shorted and the
main loop will be burned.
●It’s prohibited to connect the high-voltage line to control terminal of the driver.
Otherwise, the control board will be burned.
●For risk of injury, please set emergency stop and locking circuit at the outside of the
controller (user is responsible for the wiring) .
●There is a risk of electric shock and short circuit.
Caution
Caution
Danger

GH DRIVER
◆Wiring
◆Trial run
04
●For risk of injury and fire, please ensure that the voltage of the main circuit AC input
power and the rated voltage of the driver are consistent.
●Please do not conduct withstand voltage and insulation test to the controller arbitrarily.
Otherwise, the semiconductor and other components in the controller may be damaged.
●For risk of fire, please connect braking resistor and braking unit according to the wiring
diagram.
●Please do not connect the AC input power cord to the output U, V, W terminals.
Otherwise, damage to inside of the controller may be caused.
●For risk of fire and malfunction of the controller, please tighten the terminals of main
loop and control circuit with appropriate torque.
●Please do not connect the phase shifting electrolytic capacitor and LC / RC noise filter
to the output circuit. Otherwise, damage to inside of the controller may be caused.
●Please do not connect the electromagnetic switch and electromagnetic contactor to
the output circuit to connect or disconnect the load. During loaded operation of the
controller, the surge current will cause protection circuit action of the controller.
●For risk of electric shock and short circuit, please do not touch the terminals of the main
circuit directly after power-on.
●Please confirm the input and output signals to guarantee safe operation. Malfunction of
the system will cause casualties and damage to the work piece and nearby equipment.
●For risk of injury, alarm reset only can be done after ensuring that the operating signal
is cut off. Alarm reset with operating signal will lead to suddenly re-start.
●For risk of driver burning, the inside of long term stored driver shall be checked for
water and condensation.
●For risk of electric shock and burning the equipment, it’s prohibited to touch the
terminals of the driver with hand during operating.
●For risk of scalding, the running servo driver and motor may have a high temperature
rise, please do not touch.
●For risk of scalding and electric shock as the braking resistor has a high temperature
rise for discharging, please do not touch.
●For risk of damage to the equipment and accident, please do not change the settings
of the drive arbitrarily.
Caution
Caution
Danger

GH DRIVER
05
◆Maintenance and inspection
●For risk of electric shock, please do not directly touch terminals of the controller. Some
of them have high voltage and very dangerous.
●For risk of electric shock, please do install the housing before power-on; and must
disconnect the power firstly before removing the housing.
●For risk of electric shock and fire, please confirm that the power source is in the OFF
state or not before wiring.
●Inspection and maintenance only can be carried out after cut off the main circuit input
power and confirm that the power charge indicator CHARGE completely extinguished.
There is a risk of electric shock as residual power in electrolytic capacitor.
●Please make designated professional electrical engineering personnel to conduct
inspection and maintenance. Before work, please take off metal object (watch, rings
etc.), and use tools with insulation protection during operation. Otherwise, it may cause
electric shock.
●For risk of explosion and fire, used battery, circuit printing plate must not be throw into
fire. Otherwise, it may cause explosion.
●CMOS IC integrated circuit is installed on main control panel. Full attention shall be
paid during operating. The electrostatic induction due to direct touching of finger on
the main control panel may cause damage to the main control panel.
●For risk of electric shock, please do not conduct wiring and removing terminal when
the equipment is energized.
●For risk of damage to the equipment, the appropriate parameter settings must be
carried out before running after control panel replacing.
Caution
Danger

GH DRIVER
06
Table of contents
Preface ...................................................................................................................................................................................... 1
Safety -related symbol description ................................................................................................................................. 2
Safety precautions ................................................................................................................................................................ 3
Chapter 1 - Installation ..........................................................................................…………………………………………..…………………………. 1-1
Introduction to GH DRIVER ............................................................................…..………………………….…..……………………… 1-2
Unpacking inspection .............................................................................................……………………………………....………..… 1-3
Standard specifications and performance parameters ...................................................................................... 1-4
Driver nameplate description ……………………………..................................................................………………………..………… 1-5
External dimensions and installation dimensions ………………………….........................................................………… 1-5
Confirmation and requirements of the installation space ……………………..............................................…..……… 1-8
Notes on motor and load …………………………………......................................................................................………..………… 1-8
Notes on the driver …………………………………………………......................................................................................…..………… 1-9
Notes on scrapping ……………………….....................................................................................…………………………..………… 1-10
Chapter 2 – wiring ………………………………………………………………............................................................................................……...………. 2-1
Selection and connection of peripheral devices ……………….……..............................................………………...……… 2-2
Wiring of the main circuit terminals ………………………………………...........................................................…………………… 2-3
Control circuit wiring ……………..…………………………………......................................................................……………………… 2-11
Connection of the encoder interface …………………………………………………........................................................……… 2-20
Connection of serial communication port …………………………….........................................................………………… 2-23
Chapter 3 - Manipulator application ………………………………........................................................................…………..……………. 3-1
Digital tube display 0.4 ~ 18.5kw driver:
Configuration and key functions of the manipulator …………………….............................................…………………… 3-2
The operating state of the driver …………………………………………………………........................................................………… 3-3
Operative mode of the manipulator …………………………………………..........................................................………………… 3-4
Use method of the manipulator ………………………………..…………..............................................................…………………… 3-4
Modify the parameters with the manipulator ……………………………....................................................…………………… 3-5
Monitor operating state with the manipulator ……………….................................................….……………………………… 3-5
Digital tube display 22 ~ 315kw driver:
Configuration and key functions of the manipulator …………………….............................................…………………… 3-6
The operating state of the driver …………………………………………………………........................................................………… 3-8
Operative mode of the manipulator …………………………………………..........................................................………………… 3-8
Use method of the manipulator ………………………………..…………..............................................................…………………… 3-9
Modify the parameters with the manipulator ……………………………....................................................…………………… 3-9
Monitor operating state with the manipulator ……………….................................................….…………………………… 3-10
Chapter 4 - Test run ……………………………………………………………................................................................................................…..……… 4-1
Basic procedure of test run ………………………………………..………….................................................................………………… 4-2
Confirmation of connection of the main circuit ……………………………..................................................………………… 4-2
Motor and driver parameters confirmation ……………………………….....................................................…………………… 4-3
Loaded test run ……………………………………………………...........................................................................…………………………… 4-3

GH DRIVER
07
Chapter 5 - Parameter list …………………………………………………......................................................................................………………… 5-1
Running monitoring parameter U1 ……………………………………….......................................................……….………………. 5-2
Running monitoring parameterU2 …………………………………………………….........................................................…………. 5-2
Malfunction state record parameter U3 ………………………………..................................................……………….…………… 5-4
Basic parameter A1 …………………………………………………….…..............................................................................….………….. 5-5
User self-defined parameter A2 ……………………………………………........................................................……………..………… 5-7
User self-defined parameter A3 ………………………………….………………........................................................…….….……… 5-10
Bn bus parameters group ………………………………….………………………….............................................................………….. 5-14
User parameters Cn ……………………………......…………………….........................................................................……….………. 5-18
Motor driving parameter Dn …………………………………………………..................................................................….…………. 5-22
Encoder parameter En …………………………………………………........................................................................…………………. 5-26
Fn function parameters ………………………………………………………............................................................................………. 5-30
Hn interface parameter set …………………………………………………….....................................................................…………. 5-35
Pn protection parameter set ……………………..................................…....................................................……………………. 5-41
Sn system parameter set .............................................................................................................................................. 5-45
Chapter 6 – Setting parameters by function ………...………….......................................................................…..……………… 6-1
Analog speed control ……………………………............................................................................………………..…………………….. 6-2
Pulse speed control ………………………………….....................................................................…………...……………………………… 6-4
Analog rigid tapping …………………………………………….…………….....................................................................………………… 6-5
Pulse rigid tapping /pulse position ………………….……………...........................................................................………….… 6-6
Accurate stop …………………………………………………….................................................................................………………………… 6-8
Swing ……………………………………………………………….………..........................................................................................…………… 6-9
Operation panel operation ……………………………………...................................................................................….………… 6-10
Modbus communication settlement …………………………….…......................................................................…………… 6-11
Star–Delta switch ……………………………………..................….....................................................................…………………….…. 6-11
S curve ………………………………………………….......................................................................................……………………………….. 6-13
Field bus application ..................................................................................................................................................... 6-14
DA1, DA2 analog output function ............................................................................................................................. 6-15
Chapter 7 – PLC functions introduction ………………………………......................................................................………………….. 7-1
List of fault alarm and remedies ………………………………..................................................................................……..…….. 7-2
Common fault analysis ………………….……………………………...................................................................................………….. 7-6
Alarm reset method ……….…...........................................................................................……………………………………....….. 7-10
Chapter 8 - MechatrolinkII usage ……………………………………………….......................................................................................... 8-1
Prompt …………………………………………….............................................................................................................…………………… 8-2
Routine maintenance ………………………………………………………………...................................................................…………….. 8-3
Regular maintenance ………………………………………………………………...................................................................…………….. 8-3
Wearing parts of the driver ……………………………………………………...................................................................……….…….. 8-4
Driver storage ………………………………………………………………...................................................................…...............………….. 8-4
Drive warranty ……………………………………………………………….................................................................................…………….. 8-4

GH DRIVER
GH DRIVER
1
Installation
The chapter describes matters to be confirmed and installation requirements for the user
after getting the GH DRIVER.
Introduction to GH DRIVER ..............................................................…… 1-2
Unpacking inspection ..........................................................................… 1-3
Standard specifications and performance parameters .............. 1-4
Driver nameplate description …………………………….............................… 1-5
External dimensions and installation dimensions ………….………… 1-5
Confirmation and requirements of the installation space ...…… 1-8
Notes on motor and load …………………………………................................… 1-8
Notes on the driver …………………………………………………...........................… 1-9
Notes on scrapping ………………………...................................................… 1-10
1-1

GH DRIVER
GH DRIVER is a type of driver that specifically designed for machine tool. Precise control of position, speed, acceleration and output
torque of AC induction servo motor and AC inverter motor is allowed through the driver. It can be used for control of motor of
machining center, CNC milling machine, CNC drilling machine, CNC lathe, CNC grinder, and feed motor of large gantry equipment
and vertical lathe. To achieve the best operation effect, please complete wiring with CNC system by the “CTB servo application
manual “, and carry out installation and commissioning in accordance to the manual.
1-2
BKSC
15
1
6
B
7
2D
10
9
E
8
O
2
4
3
7P5
4
GH
Code Item Description Illustrated model meaning
1 Manufacturer code BKSC: code for driver product of the manufacturer Manufactured by CTB CO., LTD.
2 Voltage level
2: level 200V
4: level 400V
6: level 600V
level 400V
3 Power code See power code list for detail 7.5kW
4 Product series GS: GS series driver
GH: GH series driver GH series driver
5 Encoder model
0: no encoder interface
1: Incremental encoder
2: Rotary encoder
3: Sine-cosine encoder
4: Absolute value encoder
5: Smart card
Incremental encoder
6 Product model None: standard
B: general type General type
7 Encoder agreement
None: standard design 1: SSI protocol
2: Renishaw encoder (BISS)
3: SYNTEC encoder
4. Tamogawa 8401 (23rd absolute value)
5: Tamogawa 8501 (17-bit absolute value)
7: Tamogawa N7 encoder
8: Tamogawa N8/N9 encoder
9: Nikon encoder
Renishaw encoder (BISS)
Note: item 7 holds when item 5
equals 4
8 Egress Identifier None: domestic products
O: Export products (English letter O)
Non-standard requirements to main
board of driver
Model description (taking 7.5kW as example)
Table 1-1 Detailed description of motor model designation
Introduction to GH DRIVER

GH DRIVER
Unpacking inspection
Table 1-3 Confirm items
Driver model Rated capacity
(KVA)
Rated input current
(A)
Rated output current
(A)
Adapt motor power
(KW) Built-in brake unit
BKSC-41P5GHX 2.5 4 3 1.5 有
BKSC-42P2GHX 3 6 5 2.2 有
BKSC-43P7GHX 5.5 9 8 3.7 有
BKSC-45P5GHX 8.5 14.2 13 5.5 有
BKSC-47P5GHX 11 18 17 7.5 有
BKSC-4011GHX 17 26 25 11 有
BKSC-4015GHX 21 35 32 15 有
BKSC-4018GHX 24 38.5 37 18.5 有
BKSC-4022GHX 30 46.5 45 22 有
BKSC-4030GHX 40 62 60 30 有
BKSC-4037GHX 50 76 75 37 有
BKSC-4045GHX 60 92 90 45 有
BKSC-4055GHX 72 113 110 55 有
BKSC-4075GHX 100 157 152 75 有
BKSC-4090GHX 116 190 185 90 有
BKSC-4110GHX 138 236 230 110 有
BKSC-4132GHX 167 288 280 132 有
BKSC-4160GHX 200 345 336 160 有
BKSC-4200GHX 250 420 370 200 选配
BKSC-4250GHX 300 530 460 250 选配
BKSC-4315GHX 360 680 570 315 选配
Confirm item Confirm method
Confirm that the materials listed on the packing list are
complete.
Check the materials in the packing against the packing list
stuck to the external packing.
Are they in line with the ordered merchandise? Please confirm the label at the side of the driver.
Is there any damage? Check the overall appearance for damage during
transportation.
●GH DRIVER SERIES APPLIES FOR 21 TYPES WITH A MOTOR CAPACITY OF 1.5KW TO 315KW.
PLEASE SEE TABLE 1-2 FOR DETAIL
1-3
Table 1-2 GH DRIVER model (rated voltage: 400v)
Please confirm the following items when you get the product. Please contact directly with the dealer or manufacturer that purchased
from for any adverse situation. Please see Table 1-3 for detail.
Code Item Description Illustrated model meaning
9 Special label
None: standard products
E: Ethercat bus
M: Mecholink bus
J: electro-hydraulic servo
C: CANopen bus
PN: Profinet bus
PB: Profobus
PL: powerlink bus
M2: Mecholink Ⅱbus
M3: Mecholink Ⅲbus
Ethercat bus
10 Battery options None: standard products
D: Equipped with batteries Equipped with batteries

GH DRIVER
Standard specifications and performance parameters
Please see Table 1-4 for standard specifications and performance parameters of 3-phase Class 400V driver
Table 1-4 Standard specifications and performance parameters of GH DRIVER
Model BKSC-XXXXGHX
41P5 42P2 43P4 45P5 47P5 4011 4015 4018 4022 4030 4037 4045 4055 4075 4090 4110 4132 4160 4200 4250 4315
Adapt motor power KW
1.5 2.2 3.7 5.5 7.5 11 15 18.5 22 30 37 45 55 75 90 110 132 160 200 250 315
Capacity KVA 2.5 3 5.5 8.5 11 17 21 24 30 40 50 60 72 100 116 138 167 200 250 300 360
Current A 3 5 8 13 17 25 32 37 45 60 75 90 110 152 185 230 280 336 370 460 570
Maximum output
voltage V 3-phase 380/400/415/440V corresponding input voltage
Maximum output
speed rpm 4-pole motor 24000rpm: 50/60Hz
Rated voltage and
frequency 3-phase 380/400/415/440V: 50/60Hz±5%
Allowed voltage
pulsation +10%, -15%
Allowed frequency
pulsation ±5%
Control mode Sine wave PWM modulation, entirely closed-loop vector control
Torque feather 200% rated torque output below the fundamental frequency. Accuracy: ±5%
Range of speed
regulation 1:24000
Speed control
accuracy ±0.1%
Frequency set
resolution Digital quantity: : 0.01Hz; Analog: Unipolar, maximum output frequency is /4092; bipolar, maximum output frequency is / 2046
Position control
accuracy ±1 PULSE
Acceleration and
deceleration time 0~3000s
Brake mode dynamic braking. 125%rated torque: built-in braking unit (external braking resistor)
Overload capacity 200% rated current 30s
Digital quantity
input 12-channel isolation photo-coupler input; input mode: PNP, NPN optional
Digital quantity
output 6-channel isolation photo-coupler output; 24V, 10mA
Analog input 2-channel; -10V~+10V 1 channel, 0~10V 1-channel
Analog output 2-channel; -10V~+10V
Relay output 1 channel: a group of N.O/N.C contact: AC250V/DC30V, 1A
Fault output relay 1 channel: a group of N.O/N.C contact: AC250V/DC30V, 1A
Encoder input
interface
Two: Motor encoders: receive incremental encoder, rotary transformer, sine and cosine encoder, absolute encoder
External encoders: receive incremental encoder
PULSE input
interface One: direction PULSE , orthotropic PULSE optional
Encoder output
interface One: maximum output frequency is 300KHz: cable driven output mode: RS422 standard
Bus interface RS485, CAN, MechtroLink, PowerLink, Ethercat
Speed control Range: 0~24000rpm; turning: positive and negative; speed order: analog, PULSE frequency, multi - stage speed control,
communication
Position control Automatic return to zero, reciprocating positioning, multi-point positioning
Torque control Coiling control, swing control, torque limiting
Other functions External encoder positioning, synchronous drive, hydraulic servo, PID control
river/motor over-
current With independent driver, motor overcurrent detection function
Driver/motor
overload With independent driver, motor overload detection function
Motor overheating Built-in motor thermal protection interface
Low voltage/
Overvoltage The busbar voltage of main circuit: higher than 800V, overvoltage alarm output; lower than 400V,undervoltage alarm output
Service site Free of dust, corrosive gas and inflammable gas
Temperature -10~45℃
Humidity Lower than 95%RH (no condensation)
Vibration vibration frequency≤20Hz: 9.8m/s2;20Hz≤vibration frequency≤50Hz: 2m/s2;
1-4
Output Power
Control function Protection function
Control characteristics Input and output interface Service
environment

GH DRIVER
AC DRIVER
MODEL:BKSC-4011GH5 NO.CZ00285911
CP:CP1000A5 V:10481/10470
POWER:11kW
INPUT:3PH 380~440V 26A 50/60Hz
OUTPUT:17KVA 26A 0~400Hz 0~400V
CTB CO.,LTD Made in china
Dimension
Model A B W H D Connecting terminal screw Installation screw Weight (kg)
BKSC-41P5GHX
45.5 276 91 290 200 Wire nail width
3mm M6 3BKSC-42P2GHX
BKSC-43P7GHX
1. 1.5-3.7kw driver
Driver nameplate description
Table 1-5 Dimensions (mm) and weight (kg) of GH DRIVER (1.5-3.7kw) driver
External dimensions and installation dimensions
Nameplate which indicates model and rated values of the driver is affixed to the lower right of housing of the driver. The
content of the nameplate is shown in Figure 1-1.
Note: the two-dimension code includes manufacturing number of the driver; customer name of the driver (take BEIJING CTB SERVO
CO., LTD. as an example); contract number; driver model; main board model; software number; non-standard (take standard as an
example) and other description.
Figure 1-1 AC Servo driver nameplate
Figure 1-2
B
H
A
W
D
Please see diagram 1-2 for external dimensions and installation dimensions
Driver model
Main board model
Rated power
Input specific ations
Output specific ations
Software number
Manufacturing number
1-5

GH DRIVER
1-6
Table 1-6 Dimensions (mm) and weight (kg) of GH DRIVER (5.5-11kw) driver
Figure 1-3
2、5.5~11kw driver
Please see diagram 1-3 for external dimensions and installation dimensions
H
B
W
D
A
H
B
A
W
D
3、15~45kw driver
Please see diagram 1-4 for external dimensions and installation dimensions.
Table 1-7 Dimensions (mm) and weight (kg) of GH DRIVER (15-45kw) driver
Figure 1-4
Dimension
Model A B W H D Connecting terminal screw Installation screw Weight (kg)
BKSC-45P5GHX
80 276 132 290 200 Wire nail width
5mm M6 5BKSC-47P5GHX
BKSC-4011GHX
Dimension
Model A B W H D Connecting terminal screw Installation screw Weight (kg)
BKSC-4015GHX 140 380 194 400 230 M6 M6 14
BKSC-4018GHX
BKSC-4022GHX 236 376 282 390 270 M6 M8 20
BKSC-4030GHX
BKSC-4037GHX 300 376 380 390 270 M8 M8 26
BKSC-4045GHX

GH DRIVER
1-7
Figure 1-5
Figure 1-6
4、55~160kw driver
Please see diagram 1-5 for external dimensions and installation dimensions
4、200~315kw driver
Please see diagram 1-6 for external dimensions and installation dimensions
Table 1-8 Dimensions (mm) and weight (kg) of GH DRIVER (55-160kw) driver
B
H
A
W
D
E E
H
D
W
Table 1-9 Dimensions (mm) and weight (kg) of GH DRIVER (200-315kw) driver
Dimension
Model A B W H D E Connecting terminal
screw Installation screw Weight (kg)
BKSC-4055GHX 392 376 472 390 270 196 M10 M8 33
BKSC-4075GHX
BKSC-4090GHX
360 690 464 720 320 180 M10 M10 90
BKSC-4110GHX
BKSC-4132GHX
BKSC-4160GHX
Dimension
Model A B W H D Connecting terminal screw Installation screw Weight (kg)
BKSC-4200GHX
- - 800 1800 600 - - 230BKSC-4250GHX
BKSC-4315GHX

GH DRIVER
Confirmation and requirements of the installation space
Installation environment
The following items shall be noted when selecting the installation environment:
1. Ambient temperature: operate in -10℃~ 45℃; if the ambient temperature is higher than 45℃, the equipment shall be used
with 30% derating for each 5℃temperature rise.
★Note: If the ambient temperature is higher than 45℃, the ventilation shall be strengthened, and use by the specified derating.
2. The humidity of the installation site shall lower than 95%, and free of condensing;
3. Do not install the equipment in place with dust or metal powder;
4. The equipment shall be installed at place without corrosive, explosive gas;
5. The equipment shall be installed at place that meets the requirements of vibration. The vibration frequency ≤ 20Hz: 9.8m/s2;
20Hz ≤ vibration frequency ≤ 50Hz: 2m/s2;
6. The equipment shall be installed at place away from direct sunlight.
Installation direction and space
● Installation spacing and distance requirements of single driver are shown in Figure 1-7.
● Generally, abreast installation mode is adopted when multiple drivers are installed in the control cabinet, and air inlet, outlet
and dedicated cooling fan shall be equipped; if up and down installation mode is adopted, stream guidance clapboard shall be
added between drivers to guarantee good cooling effect as shown in Figure 1-8.
Figure 1-7 Single controller installation Figure 1-8 Multiple controllers installation
Notes on motor and load
Compared with frequency conversion operation
GH DRIVER is full closed-loop vector servo driver. It adjusts output voltage and current automatically according to the load change.
It’s more energy-efficient than inverter with higher speed control accuracy and wider speed regulation range. As the controlled
motor and driver are closed loop, the control of position, speed and torque can be achieved conveniently.
Constant torque operation
When motor works in constant torque area, the output torque of the motor is required by the mechanical operation instead of the
rated torque of the motor. However, the maximum continuous output torque of the motor must not exceed the rated torque.
1-8
120mm Above
120mm Above
50mm Above
Control cabinet
air inlet
Air outlet and cooling fan
Driver Driver
50mm Above
Fan exhaust

GH DRIVER
1-9
High-speed operation in constant power area
For high-speed operation in constant power area, the increased vibration and noise shall be considered, and the service speed
range of motor bearing and mechanical devices must be confirmed, and consulted in advance. It’s strictly prohibited to make the
machine operate above the rated speed.
Lubrication of the mechanical device
For reduction box and gear head motor and other mechanical device that requires lubrication, damage may be caused due to
deterioration of lubricating effect in long-term low-speed operation. It must be consulted in advance.
Negative torque load
Negative torque load occurs frequently for load such as lifting. The driver will generate over-current and overvoltage alarm and
trip. Equipping of brake components or mechanical safety devices shall be considered.
Reciprocating load
Please pay attention to unstable phenomenon in output current when the driver is driving piston reciprocating load. The
phenomenon is more prominent in long-term low-frequency operation. The capacity of driver shall be increased.
Mechanical resonance point of the load device
The driver may encounter the mechanical resonance point of the load device in certain output frequency range. It can be avoided
by setting jump frequency.
Notes on the driver
Applications not in rated voltage
The servo driver shall not be used in voltage that not in the working voltage range. Please conduct voltage transformation with
appropriate step-up or step-down unit as required.
Note on the drive 3 phase input into 2-phase input
The device shall not be changed into 2-phase input, otherwise, default phase protection will occur.
Capacitor or pressure-sensitive device to improve power factor
As shown in Figure 1-9, the output of the driver is PULSE wave, drive failure tripping or damage to the device will be caused due to
capacitor or pressure-sensitive device for lightning to improve power factor installed at the output side. They must be removed.
Figure 1-9 Capacitor is prohibited at the output end of controller

GH DRIVER
Lightning attack protection
lightning over-current device is equipped in the driver for self-protection to induction stroke
Altitude and derating operation
For areas with altitude over 1000 m, derating operation is necessary due to deterioration of cooling effect of the drive caused by
thin air. The relationship curve of rated current of driver and altitude is shown in Figure 1-10.
Figure 1-10 Derating curve of rated current of driver and altitude
Notes on scrapping:
Explosion of electrolytic capacitor: the electrolytic capacitors on main circuit and printed panel may explode when
incinerated.
Plastic incineration waste gas: toxic gases will be generated in incineration of front panel and other plastic parts.
Processing method: please process the waste as industrial waste.
★Description: The contents of the manual are subject to change due to product upgrade or optimize. The new
version shall prevail.
Output current
Altitude (m)
1-10

GH DRIVER
GH DRIVER
2
Wiring
The chapter describes the wiring specifications of power supply terminals and control circuit
terminals, and install wiring specifications of control board jumpers and expansion interface
board.
2-1
Selection and connection of peripheral devices ……………….……… 2-2
Wiring of the main circuit terminals ………………………………………...…… 2-3
Control circuit wiring ……………..…………………………………....................… 2-11
Connection of the encoder interface ………………………………………… 2-20
Connection of serial communication port …………………………….… 2-23
This manual suits for next models
21
Table of contents
Popular Servo Drive manuals by other brands

Leadshine
Leadshine ES2-DA808 user manual
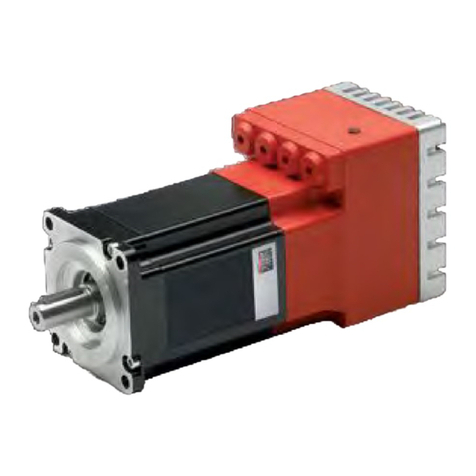
Motor Power Company
Motor Power Company DUET_FL 48/10 user manual

Siemens
Siemens SINAMIC S120 Equipment manual
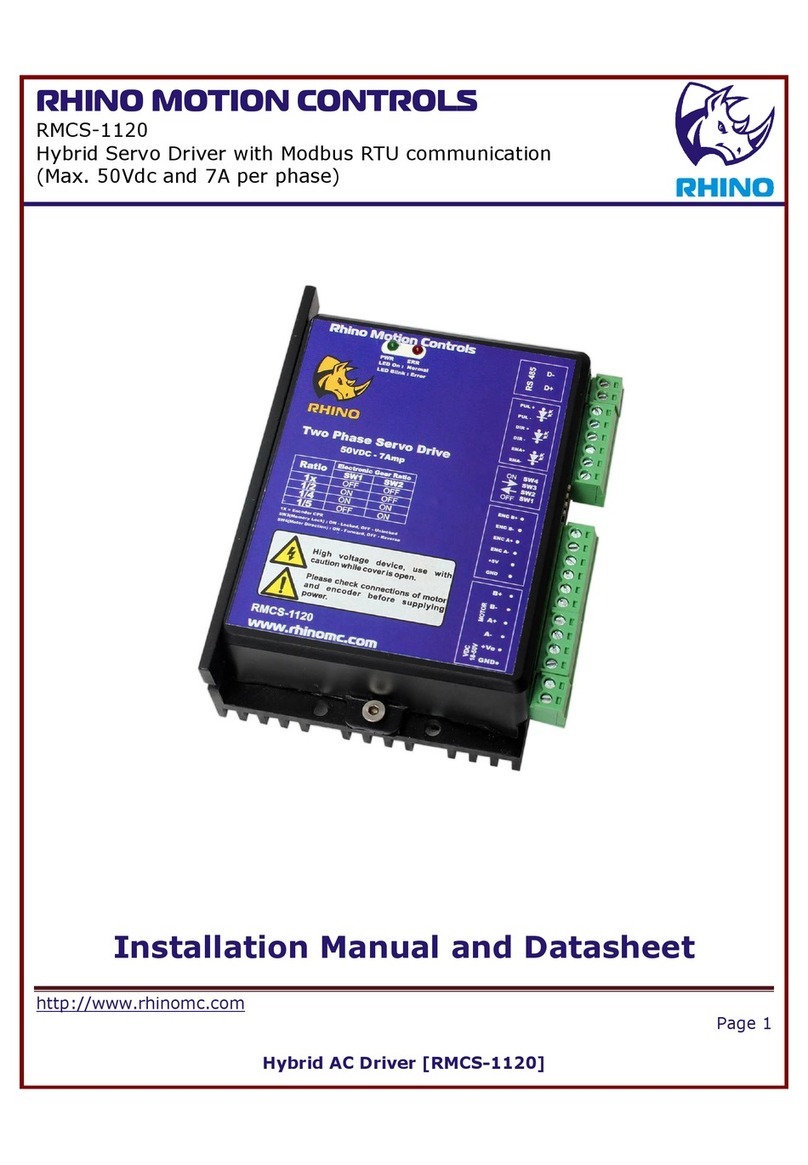
RHINO MOTION CONTROLS
RHINO MOTION CONTROLS RMCS-1120 Installation Manual and Datasheet
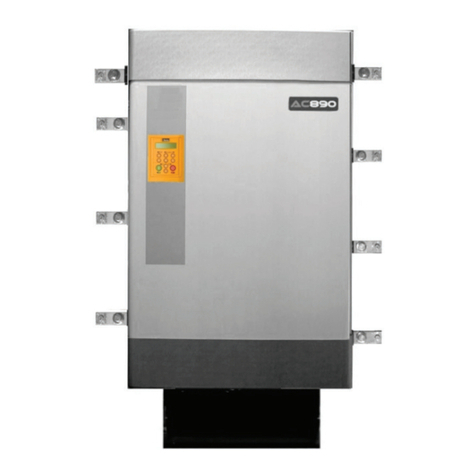
Parker
Parker ac890 product manual
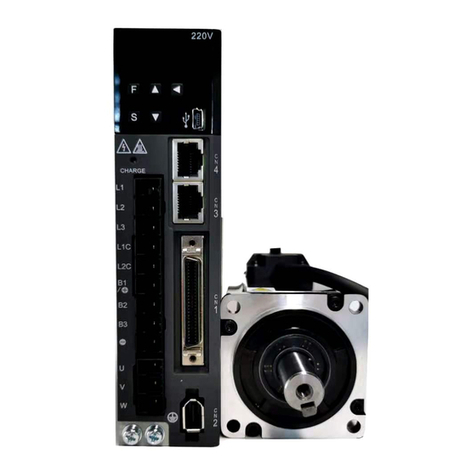
HNC Electric
HNC Electric HSD7-E Series user manual
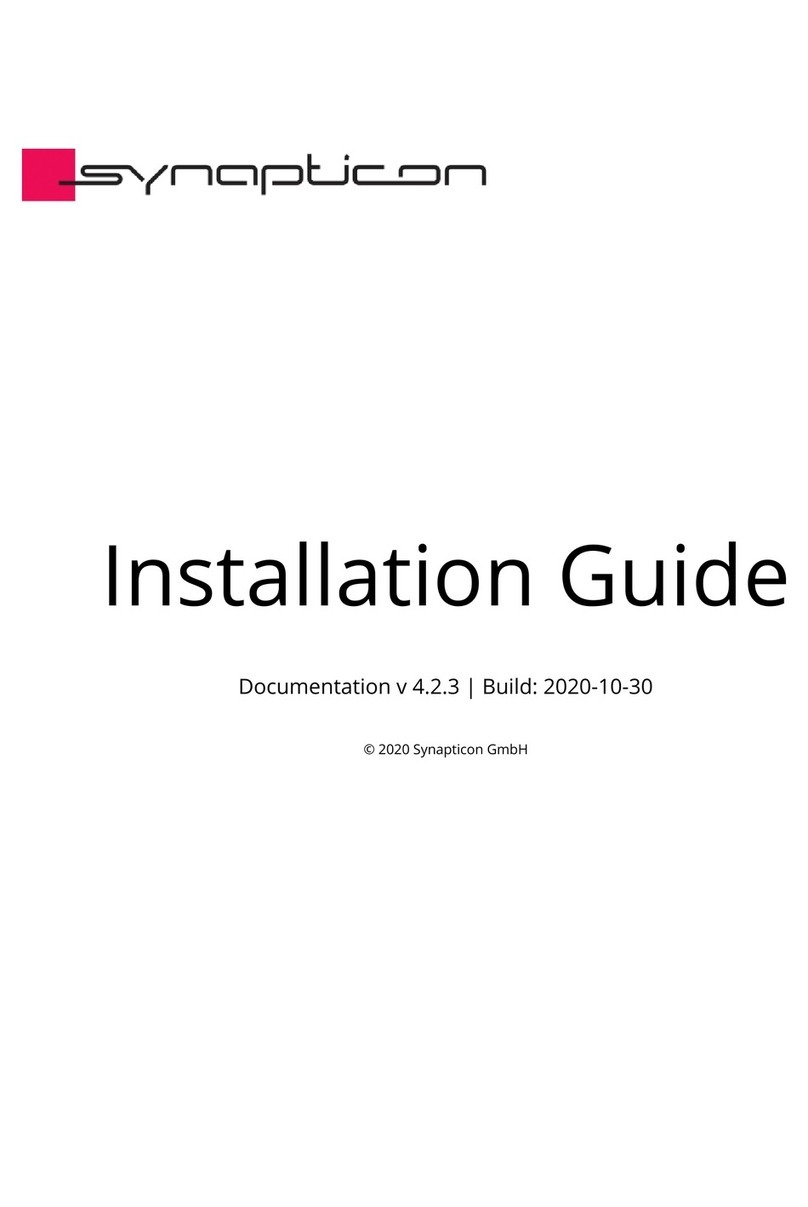
SYNAPTICON
SYNAPTICON SOMANET Circulo Series installation guide

Siemens
Siemens SINAMICS V90 operating instructions
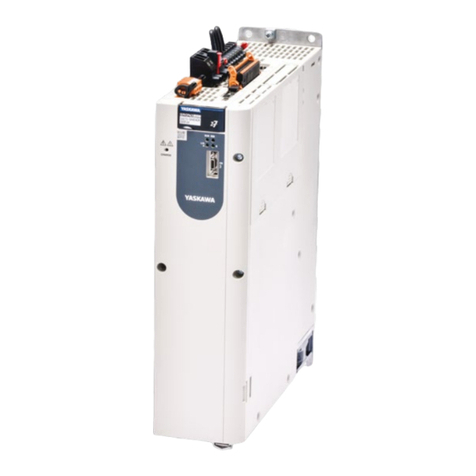
YASKAWA
YASKAWA SGD7S-1R9D product manual
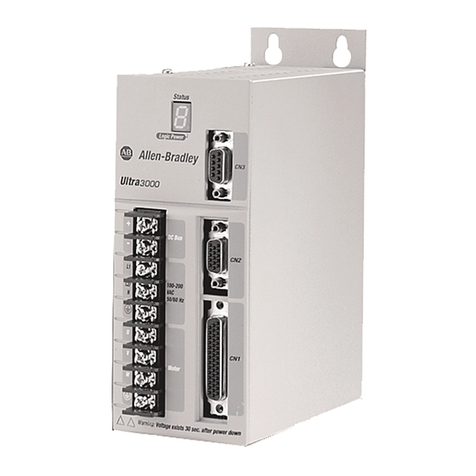
Allen-Bradley
Allen-Bradley 2098-DSD-010 installation manual

SEW-Eurodrive
SEW-Eurodrive CMP Series Addendum to the operating instructions
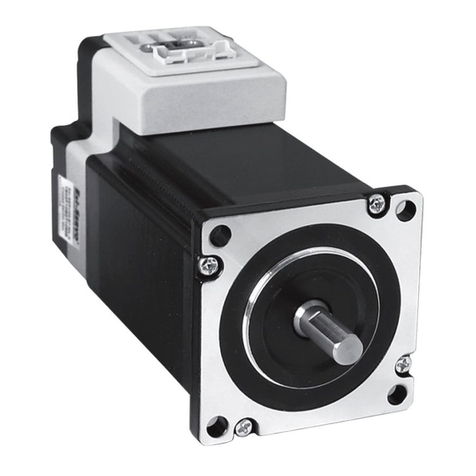
Fastech
Fastech Ezi-Servo II BT manual