CTD D45AX User manual

INSTRUCTION BULLETIN
& MAINTENANCE MANUAL
FOR CTD MODELS
D45AX & D45FX
CTD MACHINES
2382 E 48th Street
Vernon, CA 90058
(213) 689-4455 FAX (213) 689-1255
e-mail:ctdsaw@ctdsaw.com WWW: http://www.ctdsaw.com
05.2016
CTD MODEL NO:______________________
CTD SERIAL NO:______________________
MANUFACTURE DATE:________________
DISTRIBUTOR PURCHASED THROUGH:
(IF ANY)___________________________________________

INDEX
SUBJECT PAGE NO.
Machine Requirements................................................................................................................ 2
Installation and Set-Up................................................................................................................ 3
Electrical Installation................................................................................................................... 6
Air Pneumatics............................................................................................................................. 7
Safety Instructions....................................................................................................................... 11
How to Operate the Machine....................................................................................................... 12
Preventative Maintenance............................................................................................................ 15
Repair and Service....................................................................................................................... 16
D45FX Special Installation and Set-Up....................................................................................... 17
Spindle & Pivot Shaft Diagrams, Installation and Parts..................................................................... 18, 19
D45AX & D45FX Saw Head Assemblies ...................................................................................... 20, 21
D45AX Base & Air System Exploded View.................................................................................... 22
D45AX/FX Blade Guard Exploded View........................................................................................ 23
D45FX Stand Exploded View......................................................................................................... 24
New Style D45AX Pivot Exploded View......................................................................................... 25
OMD Exploded View...................................................................................................................... 26
Air Stop / Chip Breaker Exploded View........................................................................................... 27
Warranty......................................................................................................................................... 28
Machine Requirements:
MODEL NO: _____________________ SERIAL NO:______________________
Cutting Capacities:
Height Width
7/8”(22mm) 5-3/4”(146mm)
3-1/4” (83mm) 3”(76mm)
14” High Top (355mm) Blade Capacity
Height Width
2”(51mm) 6”(152mm)
3.25”(83mm) 3-1/2” (89mm)
-2-
Electrical Requirements: Based on two motors per machine
Motor Size Required Amperage Breaker Needed
2 H.P., 1 Phase 230 Volt 25 amps 40 amp
2 H.P., 3 Phase 230 Volt 10.8 amps 20 amp
2 H.P., 3 Phase 460 Volt 5.4 amps 15 amp
Pneumatic Requirements:
1 CFM per 10 strokes at 75 PSI (.043 cubic meters at 5.4 kg/cm2)
Dust Collection Requirements: 1200 CFM at 6” outlet
Cutting Tool Requirements: Heavy, rigid plate blades
10” blades: .090 to .100 plate 12” blades: .100 to .110 plate 14” blades: .120 to .130 plate
12” (305mm) Blade Capacity

-3-
Installation and Set Up:
CTD 12”, and 14” Models D45AX Automatic & D45FX Foot Cut Off Saws:
The CTD saw you have purchased is designed to cut wood, aluminum, and plastic, with of course, the proper
blade and conditions. For the material you are cutting, please refer to the cutting instructions for
each material type. The D45AX uses a NEMA 56 Frame 1-1/2 H.P., 3450 RPM, 60 HZ TEFC motor. CTD
uses a speed-up drive so that the blade will run at approximately 9500 SFPM on a 10” blade, and 11,400 SFPM
on a 12” blade. The D45AX and D45FX are exactly the same machine with the exception of the Air Pneumatic
System. All instructions will pertain to both machines unless specifically excluded.
IMPORTANT: Before operating saw, please be sure to read the “SAFETY INSTRUCTIONS TO THE OP-
ERATOR” (on Page No. 11).
Note: The floor stand must be shimmed, leveled and bolted to the floor or framed in to eliminate vibration.
Use holes provided in bottom of floor stand. All machines have been completely assembled at the factory,
then disassembled for shipment.
Space Requirements:
Assembly of Tables to Floor Stand:
1. Assemble leg to table with 3/8-16 bolts and nuts provided. Turn table upside down and attach leg to
table with leg rising vertically. Note: The hole in the table (when mounted properly) should be toward
the front of the table and far away from the blade to attach Fence Support Angle, P/N 15F82
(see Diagram “A”). If you have purchased a Vision Gage Assembly, be careful to protect lined measuring
gage.
2. Attach Table, P/N BF17 to machine floor stand on Angle Bracket, P/N BF05A. Use 3/8-16 bolts and
nuts provided on angle bracket.
Diagram “A”

Blade Installation:
Before setting blades on spindle, always shut off or disconnect air supply. With motor OFF and power
disconnected, remove blade guard by removing wing nuts on top of main blade guard. Also remove bolts located
at the front and sides of the blade guard. Remove main guard completely, by lifting off machine, exposing Arm
Assembly.
1. Remove Spindle Nut, P/N 15B1P36 or 37 and Outer Flange, P/N 150M13X. If necessary, hold blade in
hand with rag or lower blade into a piece of wood. Push down with a 15/16” wrench.
2. Place blade on spindle with tips pointing down. Make sure Slinger (inner flange P/N 150M14X) and blade
surface are clean before putting blade on spindle. This is a critical surface and is ground within.0005
flatness. Any debris or dust will wear this surface. Wipe both surfaces (blade and slinger) with a clean rag.
A. The blade must ALWAYS rotate to the rear of the machine on the underside of the blade
(see Diagram “D” on page No. 8).
Always check rotation before cutting a piece of material.
3. Replace Outer Flange, P/N 150M13X and nut
as before and tighten (refer to Diagram “B”).
Pull up with wrench. Do not over-tighten.
snugging the blade is all that is necessary.
If blades were purchased from CTD, your machine has
been set with your blades. If not, blade diameters may
vary. Check to see if the blades you are using conform
to Diagram “C”. If repositioning is necessary, follow
instructions below.
1. Position the arms so that the centerline of the
spindles are 2” above the table (see Diagram “D”).
A 1-1/2” thick spacer placed between the spindle nut flat and the table will bring the centerline up to 2”. It
is at this position that the two blades are the closest together.
2. Set blades as shown in Diagram “C” about 1/8” apart.
A. Loosen three hold down bolts on pivot bracket and move the entire arm and pivot assembly in or out of
its original position as needed in the keyway (see Diagram “E”).
B. Tighten three hold down bolts after positioning heads.
3. Use this method of setting blades ONLY. If blades are set at table level, they will contact each other on the
upstroke. This can cause severe damage to the blades.
Diagram “B”
Diagram “C”
Diagram “E”
-4-

Attaching Measuring System to Machine: (see specific instructions for the Measuring System purchased)
For: FEX, OMD, RAB, OMD/RAB Combination Gages, or PAS
1. Place long measuring gage on table with measuring tape facing up. Bolt through Front Fence Angle, P/N
15M36R with 3/8-16 bolts provided. Adjust gage so measurement rule is correctly set (see Diagram “G”);
A. With scale or ruler touching the side of the tips of the blade, measure a distance away from the blade.
Be sure the ruler and the tape on the fence gage read the same.
B. Adjust fence, left to right as necessary.
C. Both fences, left and right, must be in perfect alignment. Use a long straight edge for this purpose.
1. Take a two foot steel scale lying flat on table base. Butt edge forward against fences. Touch each
outside corner of scale. If one side pulls away from fence, then long fence is not in alignment with
left fence (see Diagram “F”).
D. Attach fence support angle to fence and table.
2. Place aluminum angle with slide into keyway. (Rabbet
Angle Assembly, P/N 15E85 is comprised of Slide,
P/N 15M80 & Rabbet Angle, P/N 15M85)
A. Move angle forward to front fence and square up.
B. When rabbet angle is square against front fence,
both measurement rules should read the same.
This may be visually deceiving.
Use a 90° square to check.
C. Adjust rabbet angle on slide as necessary by loosening 1/4-20 bolts on rabbet slide.
3. How to use Rabbet Gage:
A. Feed stick length with 45° mitre past right blade.
B. Slide aluminum angle under rabbet of wood moulding to desired dimension.
C. Move outside stop and clamp to that point and lock.
D. Slide rabbet angle back and cut.
-5-
Vision Gage Assembly:
The vision gage has been completely installed on your machine before shipment. It is then disassembled for
shipment.
1. Attach leg to table with 3/8-16 bolts and nuts provided.
2. Attach Table, P/N BF17C to machine floor stand on Angle Bracket, P/N BF05A. Use 3/8-16 bolts and nuts
provided on angle bracket.
3. Butt Vision Gage as close as possible to to the edge of the base casting P/N 15C20. Attach Vision Gage
to machine base with 10-32 screws provided.
A. With a scale or ruler touching the side of the tips of the blade, measure a distance away from the blade.
Be sure ruler and vision gage markings read the same. Adjust left to right as necessary.
4. Put outside Fence Gage, P/N 15BM223 on top of lined Vision Gage so that lines terminate at fence. Attach
outside measuring gage with 3/8-16 bolts provided to Right Front Fence Angle, P/N 15M36R. Adjust gage
so measurement rule is correct. Follow instructions under No. 3A above. Attach Fence Support Angle,
P/N 15F82 with bolt and nuts provided.
Diagram “F”
Diagram “G”

-6-
Vision Gage Diagram
Electrical Installation:
The CTD D45’s use two 2 H.P. single or three phase 3450 RPM, 60 HZ TEFC (totally enclosed fan cooled)
motors on a NEMA 56Z Frame. CTD uses a speed up drive so that the blade will run at approximately 3700 RPM.
Electrical installation should be performed by a qualified and certified electrician. A lock-out or disconnect switch
is located in front of the machine. It is a rotary switch to the left front of the machines. This disconnect switch is
used to shut off power to the machine and should be used whenever the blades are changed or at any time the
machine is serviced and the blades are exposed. A Dual Magnetic Starter, located inside the left side panel of the
machine protects the motor from overheating and will not allow the motor to restart itself after power outages or
undervoltage situations. The START button turns the motors “ON”. The STOP button turns the motor “OFF”.
Note: The STOP button must be pulled out before the START button will activate the motors.
I
f the blade guard is not set in place properly, the motors will not turn on. An interlock switch located below the
blade guard must be contacted before power is supplied to the starter.
Electrical Installation of Power to Starter by a Qualified Electrician:
All wiring from the motors to the starter has been completed and tested at the factory several times. The voltage
has been clearly tagged. DO NOT CONNECT ANY VOLTAGE THAT IS DIFFERENT THAN THE TAGGED
VOLTAGE, AS THIS MAY CAUSE SEVERE DAMAGE AND DANGER.. CONSULT FACTORY IF ANY
CHANGES ARE NEEDED.
Bring incoming power lines to the rear of the machine on left side using hard wire and dust proof connectors.
Attach incoming power lines through Floor Stand to the rotary disconnect switch. Connect to terminals 2 & 4
for single phase motors, and to terminals 2,4 & 6 for three phase motors. Always ground the green wire.
(See wiring diagram on Page 7.)
Single Phase Motor Replacement:
Connect motor leads to T1 and T3 of overload relay for single phase motors. (See wiring diagram for single
phase motors on following page) Green ground wire must be grounded to enclosure. If using type “SO” wire
and plug, use a dust tight connector through Floor Stand and a grounded plug. Be sure to check rotation. If a
change is necessary, open the motor box located on the motor, and switch the #8 and the #5 wires. This reverses
the rotation of a single phase motor. The blade must rotate down and to the rear on the underside of the blade
(see Diagram “D” on Page No. 8).

-7-
Three Phase Motor Replacement:
Connect motor line leads to T1, T2, & T3 of the overload relays. (See wiring diagram for three phase motors.)
Green ground wire must be grounded to enclosure. Be sure to check rotation as polarities may be different.
The blade must rotate down and to the rear on the underside of the blade (see Diagram “D” on Page No. 8). If a
change in rotation is necessary, reverse any two of the incoming power wires. Example: If the blades are running
backwards and incoming wires are connected White L1,Black L2,Red L3, switch the Black wire with the Red so
that Black is connected to L3 and Red is connected to L2. This will change the blades to rotate properly.
Motor Load Amperes Per Motor Circuit Breakers and Fuse Blocks
MOTOR SIZE 110 VOLT220 VOLT 440 VOLT 208/230 VOLT 460 VOLT
2 H.P., 1 Phase 25 amps 12.5 amps N/A QCD2060H -
2 H.P., 3 Phase N/A 5.4 amps 2.7 amps QCR3025H 15 amps Fuses
280 Volt Wiring Diagram
480 Volt Wiring Diagram

-8-
D45AX Air/Pneumatic System
Diagram “D”
Rotation
No. Part No. Description
1 153S71 CTD #3 Air Cylinder
2 153P27 Clevis Mount for Cylinder
3 B3P50 Way Normally Open Valve
4 4BF101 Valve Bracket
5 15M77 Upstop Block for Upstroke
Limit
6 15M26 Clevis Power Feed
7 15MS25A Front Pivot Shaft AX
8 15E30A/F Pivot Tube Assembly with tang
& shaft
9 157P73 Cylinder Bumper
10 B3P71 Way Spring Return Foot Valve
11 15M05 Eccentric Pin
**Upstroke Safety Bolt
Do not adjust! (for safety purposes only)
No. Part No. Description
12 15C002LX Pivot Bracket, Left
15C002RX Pivot Bracket, Right
3 15C001LX Arm Casting, Left
15C001RX Arm Casting, Right
14 15E27 Pull Rod Assembly
15 B3P60 Downstroke Control Valve
16 B3P60 Upstroke Control Valve
17 150B3P20 Downstop Bumper
150B1P20 Threaded Rod Bumper
1E 150E70 Air Cylinder Assembly
2E B3P71 Foot Valve Assembly

-9-
D45AX Air/Pneumatic System: (not for D45FX)
The air pneumatic system on the D45AX is simple to use and understand, and easy to operate. The main
components of the air system are shown below in the Air Circuit Piping Diagram. The system operates by
depressing the Foot Valve, P/N B3P71. This gives a signal to the main 4-Way Control Valve in the Foot Valve
to change the direction—allowing air to pass to the main drive Cylinder, P/N 153S71. This pushes the saw
heads down. The speed of descent is controlled by the Speed Control Valve, P/N B3P60. The saws reverse
when the Foot Valve is released. This signals the 4-way valve to change direction of air flow to the drive
cylinder and the saw heads reverse. See additional headings for operational components. Also refer to
Diagram “D” for parts listing of air components.
Diagram “I“ Air Circuit Piping for Model D45AX
Air Supply—The air supply must be turned off and all electrics disconnected before making adjustment on the
power feed. A working pressure of 75 PSI (5.4kg/cm2) is required. An industrial-type compressor of at least
3 CFM (.085 cubic meters) is recommended. An additional 3 CFM (.085 cubic meters is required for Spray
Mists. A conveniently located valve should be supplied by the user to shut off the air line. Arms should be
Raised or lowered by hand when setting up machine.
FR—An Air Filter/Regulator is installed ahead of the air inlet to the machine. This system helps
prevent foreign matter from entering the system. The FR is comprised of two different components.
1. The Air Filter Bowl is located on the left side and is provided with an automatic drain. This collects and
then releases foreign matter and condensation collected by the air filter.
2. The Pressure Regulator, which is located on top of the air filter, controls the amount of air pressure allowed
into the system. An operating pressure of 75 PSI is required. (This is set at the factory.)

Air Filter/Regulator
Foot Valve:
The Foot Valve, P/N B3P71 actuates the saw heads downward. Once the foot valve is depressed, it must be
held down. The stroke or downward movement of the saw heads can be reversed at any time by releasing on
the foot pedal. Since the Foot Valve rests on the floor, it is important to clean it regularly, as debris from
cutting can make its way into the valve, causing improper function. Do not maintain pressure on the Foot
Pedal, as the saw cannot reverse stroke.
Speed Control of Blades Movement:
The downstroke speed of the blades is controlled by the lower Speed Control Valve, P/N B3P60, No. 15. The
upstroke speed is controlled by the upper Speed Control Valve, P/N B3P60, No. 16. Both are located on the
right side of the floor stand and are connected to the main control 4-Way Valve. (See Diagram “D”) An easy
way to remember is the upstroke is controlled by the upper valve, and the downstroke is controlled by the lower
(down) valve. Up is up, and down is down.
Length of Stroke Adjustment:
The D45AX is unique in that the travel of the air cylinder can be adjusted to stroke only the length needed
to cut a particular moulding. Example: The highest moulding to be cut is 2” high. To adjust the stroke:
1. Shut off air supply and disconnect power.
2. Manually lower saw blades so that they are 1/2” above the work.
3. Adjust Upstop Clamp, No. 5 to contact Accessory Valve, No. 3 (see Diagram “D” on Page No. 8).
A. Loosen Upstop Clamp by using a 5/16 hex wrench on socket cap screw.
B. Move Upstop Block upward on cylinder shaft to contact Accessory Valve, closing the valve.
C. Tighten socket cap screw at this position.
4. The blades will now return to this height.
Adjust the Downstroke Bumper, No. 17 to contact Arm Casting, No. 13 as soon as the blades have cut
through the work.
You now have eliminated wasted motion and time, thereby increasing production. Always provide a safe dis-
tance between the blade and the work. Re-adjust the blade guard whenever the clamp is changed to make sure
the blades are completely covered.
-10-

-11-
Safety Instructions to the Operator:
1. KNOW YOUR CTD SAW. Read this instruction manual carefully. Learn the operation, application, and
limitations, as well as the specific potential hazards peculiar to this machine.
2. Avoid accidental starting. Make sure switch is OFF before plugging in power cord. A Dual Magnetic
Starter is provided to give the operator added protection.
3. Always use a plug equipped with a ground.
4. Always keep blade guard in place. Do not wire-up or chain-up, so that blade is exposed.
5. Be sure all unnecessary tools are removed from machine before turning on power.
6. Use safety goggles. Also use a face or dust mask if operation is dusty.
7. Support work. To maintain control of work at all times, it is necessary that material be level with cutting
surface.
8. Wear proper apparel. Do not wear loose clothing or jewelry. Do not wear a tie or gloves. These items can
get caught in the moving parts of the machine.
9. Do not over-reach. Keep your proper footing and balance at all times.
10. Maintain your machine in top condition. Use proper blades. Clean machine weekly for proper maintenance.
11. Keep work area clean. Cluttered areas, benches and slippery floors invite accidents.
12. Avoid dangerous environments. Keep work area well illuminated.
13. Wear ear protection if exposed to long periods of very noisy shop operations.
14. Keep visitors away. All visitors should be kept a safe distance from work area.
15. Do not force the machine. The saw will do a better job and be safer to operate at the speed for which it was
designed. Forcing the saw can be very hazardous to the operator.
16. Use recommended accessories. Use of other accessories may be hazardous. Use this instruction manual or
consult CTD for the proper accessories available.
17. Do not drown the blade using a steady stream of coolant when cutting non-ferrous materials. Only spray
the work to cool it.
18. Be sure to use the proper blade for the particular material to be cut.
19. Disconnect power cord before adjusting, servicing, and before changing belts, or for installing accessories.
20. Safety is a combination of operator COMMON SENSE and ALERTNESS at all times when the machine is
being used.
21. WARNING!!! DO NOT ALLOW FAMILIARITY (GAINED FROM FREQUENT USE OF YOUR SAW)
TO DULL YOUR AWARENESS!! ALWAYS REMEMBER THAT A CARELESS FRACTION OF A SECOND
IS SUFFICIENT TO INFLICT SEVERE INJURY!!
Trouble Shooting the Pneumatic System for the D45AX Cut-Off Saw:
If there is no control over the power feed stroke;
A. Replace either Upstroke Flow Control Valve, No. 16 or Downstroke Control Valve, No. 15. Another
possible cause are bad seals in the air cylinder. Listen for any air leakage.
B. If machine will not start a cycle, or will not reverse, check the 4-Way Foot Valve, No.10. To do this, depress
the pedal. Listen for the valve to bleed air out of the line, or any air leak. Also, check for any mechanical
binding. Disconnect electricity and air supply from the machine. Manually move saw heads down and back
to check for binding of the saw arms or feed mechanism. If machine is bound up, clear the blockage.
Air Hold Down Clamps for the Material:
Both Horizontal and Vertical Air Clamps are available and can be purchased as an optional accessory. These
clamps pneumatically hold the material in place when the saw blades are cutting the material. If clamps are
not purchased, the operator MUST HAND HOLD THE MATERIAL. The clamps are controlled by a 3-Way
Valve mounted on the bottom of the Power Feed Unit. When the machine is in the rest position, the Upstroke
Clamp, No. 5 contacts the 3-Way Valve, No. 3. As soon as the Power Feed is tripped by the Foot Valve, the 3-
Way Valve is released to actuate the clamps. A manual Shut-Off for the clamps can be provided upon request
from the factory.

-12-
How to operate the D45AX & D45FX:
Before operating the machine, please read the “SAFETY INSTRUCTIONS TO THE OPERATOR”. Other
important information and features need to be learned before operating the machine.
Rotation:
Both blades must rotate to the rear of the machine on the underside of the blades
(see Diagram “D”on Page No. 8.)
Blade Guard:
It is important that the Finger Guards, P/N 20F180 are adjusted to completely cover the blade.
The finger-guards, attached to the main blade guard, should be positioned around the material to give
maximum operator protection.
The main blade guard can be removed by loosening the wing nuts on top of the
guard and setting aside. Also remove bolts located at the front and sides of the
blade guard. The main blade guard will now lift off the machine. After changing
blades, replace blade guard. Be sure to provide clearance between the blade guard
and the top of the blade at the top of the stroke.
This label is attached to the blade guards. NEVER PUT HANDS OR FINGERS
NEAR OR UNDER THE MOVING BLADE!! Use a piece of wood to remove
short pieces from saw.
Cutting: (see Diagram “J”)
A fixed Double Mitre Saw, such as the D45X operates by making two 45° cuts at one time. The machine “V”
notches the piece of material between the two blades. To make the first cut on a stick length;
1. Feed the material to the centerline of the machine so that ONLY the left blade makes a trim cut. Be careful
not to overfeed beyond the centerline of the machine, as the piece can be hit with the right blade, possibly
throwing the unclamped piece into the saw blade causing damage.
2. After making the trim cut, feed the material (now with a 45° mitre cut) to the stop at the desired length.
If using a Rabbet Gage, slide angle under rabbet of moulding and move moulding to desired dimension.
Move outside stop to same position and lock (see Diagram “K”).
3. Continue to feed length to stop as above, and make double mitre cuts until length is used.
4. RULE OF DOUBLE MITRE CUTTING—If the piece to be cut cannot be held on both sides of the blade,
do not cut it!!!
5. Be sure to adjust blades so that the blades reverse as soon as saws have cut through the material. This elimi-
nates the blade hitting the material twice (see Length of Stroke Adjustment on Page No. 10 for instructions).
Minimum cut length on the D45AX and D45FX is 5” on the point to point dimension.Consult factory
for shorter lengths.
Diagram “J” Diagram “K”

-13-
Cutting Speed:
The blade is rotating at approximately 3700 RPM. When moving the blade through the material, the blade must
NEVER be allowed to dwell in the work. If fine finishes are required;
1. Use a sharp blade.
2. Use a constant, even pressure when cutting through material.
Clamping and Work Slippage:
The work must never be allowed to move or vibrate as it is being cut. When the work is positioned against a
stop, it must be clamped either by hand holding or by pneumatic air clamps. Never allow unclamped work
between the blade and the stop, as the blade can grab the material and throw it—thereby causing damage to the
blade, the machine, and possibly harming the operator. CTD offers both Horizontal and Vertical Clamps. The
Horizontal Clamp pushes the material forward against the front fence. Vertical Clamps hold the material down,
against the table base. Both clamps are offered as optional extras and are highly recommended. The clamps
are actuated at the same time as the saw heads by depressing the Foot Valve. Check your material for squareness,
using a 90° square. Material that is out of square will move when it is cut, thereby causing irregular mitres. See
“IRREGULAR MITRES”, Page No. 16. Additional tooling may be needed. Consult factory for information.
Vertical Clamp Assy.45° Horizontal Clamp Assy.
Cutting Wood:
While wood is generally soft and simpler to cut than aluminum, it requires that the material be held in place
as the blades pass through the material. CTD suggests using a Carbide Blade with an Alternate Top Bevel
(ATB) for lighter wood sections and picture frame mouldings. This type of blade gives the finest of finishes.
No ONE blade will cut all material perfectly. High laquers or mica mouldings require a special modified blade
for best results. Consult factory. Never use a wood blade to cut aluminum, as it will chip and fracture the
carbide tips of the blade.
Cutting Plastic:
Plastic can be cut as easily as wood on the D45X models. However, because of its elastic properties, the material
can deflect as the blades pass through. Therefore it is important to clamp the material as close as possible to the
blade and support it by use of fixtures. CTD offers special 45° clamps for this application. Additional tooling may
be required. Special carbide blades are avialable for cutting platics.

Cutting Aluminum:
As with cutting any material, it is important that aluminum be clamped properly. Precision blades are required
for accurate cutting. CTD suggests and uses a Triple Chip Grind on all its non-ferrous Carbide Blades. When
cutting aluminum, or other non-ferrous materials, it is essential that the blades be lubricated with a Spray Mist
System or other blade lubricating system for the finest finish. See SAWBLADE LUBRICATION SYSTEM
below for more details.
Combination Blades:
Any combination blade is basically an aluminum cutting blade. Significant blade life in between sharpenings
will be lost if a blade is used for cutting both aluminum and wood. The amount of production for either wood
or aluminum should be the determining factor in the assessment of the particular blade type to be used. Please
consult factory.
Sawblade Lubrication System:
The Sawblade Lubrication System is used when cutting aluminum or other non-ferrous material . This system
normally uses a Water Soluble Oil mixture of 10 parts water to one part oil. The system operates by syphoning
the lubrication up the line to the spray nozzle. Any air leak will cause inconsistent fluid flow to the spray nozzle.
BE SURE your fluid is free from chips and other debris. A fluid container supplied with the machine contains a
One-Way Check Valve, Part No. B3P96 at the end of the clear fluid line. This check valve helps to hold the
lubrication in the line. However, after a couple of minutes the lubrication or oil will back-flow into the container.
Priming of the system may be necessary if the machine has been standing without use. The system may be shut off
by closing the toggle valve next to the vacuum pump. The fluid must be clean or the vaccum pump will clog.
CTD Bio Lubrication System:
The CTD biodegradable lubrication system operates by pulse spraying a minute amount of biodegrad-
able lubricant directly on to the saw tooth of the blade in time-measured increments. The majority of the
lubricant then dissipates with the heat of the cutting action. Chips coming off the blade are hot and dry, and are
more easily collected (see specific instructions included with system).
-14-

-15-
Cutting Wide Materials:
Wider mouldings can easily be cut on the D45’s because of our unique above-table saw head design. This
design allows for use of the bottom of the blade to cut, as well as the front of the blade. Of course, the blade
must be stopped before the flange (holding the blade on) makes contact with the moulding or material to be cut.
To stop the blade before it reaches the table (refer to Diagram”D” on Page No. 8);
1. Shut off air supply and disconnect power when making any adjustment to the machine.
2. Adjust Downstroke Bumper so that the blades will stop before the flange contacts material.
See “LENGTH OF STROKE ADJUSTMENT” on Page No. 10 for more details.
Cutting Smaller Materials:
When cutting larger production runs of smaller height and width materials, you will want to limit the upstroke
and downstroke of the machine to save time and motion.
1. Shut off air supply and disconnect power.
2. Lower saw heads so that saw blades are 1/2” above the material to be cut, NEVER cut below the height of
main blade guard, so the blades are exposed.
3. Adjust Upstop Clamp, No. 5 to contact Accessory Valve (3-Way Normally Open). This clamp limits the
upstroke of the cylinder on the piston rod. The saw heads will now return to this position every time when
completing a cycle.
4. Always provide a safe distance between the blade and the work to be cut. Re-adjust the finger guards
whenever the upstop clamp is changed. Make sure the blades are completely enclosed. See “LENGTH OF
STROKE ADJUSTMENT” on Page No. 10 for additional details.
Scrap:
The D45’s operate by making two 45° mitres at the same time. A “V” shaped piece is removed and falls into
the scrap chute located on the right hand side of the machine. A scrap box should be supplied to collect the scrap
pieces. To minimize scrap, make sure blades are set close together as shown in Diagram “C“ on Page No. 4. Also
see “BLADE INSTALLATION” on Page No. 4. Generally, you will loose between 3/8” (9mm) to ½” (13mm)
of scrap material.
Preventative Maintenance:
The D45AX and D45FX are relatively easy machines to operate and maintain. Below is a weekly check list of
general maintenance items. The best preventative maintenance advise is to CLEAN THE MACHINE DAILY,
especially around the pivot points on the machine.
Lubrication and Adjustments of Bearings:
NO LUBRICATION OR ADJUSTMENTS ARE REQUIRED. All CTD cut-off saws are assembled using
sealed, prelubricated ball bearings. The spindle and pivot assemblies are constructed using preloaded belleville
springs. These springs eliminate the need for adjustments of bearings and also greatly increase the life of
these bearings. All air cylinders are “lubed for life”.
Sound Levels:
During normal running of the machine without cutting the typical sound range will be between 60-85 db.
Due to the wide variety of blades available, CTD cannot warrant that maximum allowable OSHA sound limits
can be met--particularly during the cutting cycle.

-16-
General Maintenance Check List:
Always disconnect electrical power and air supply.
1. Keep machine clean—especially around pivot bracket and pivot bearings.
2. Blow off and clean;
A. Around air cylinder.
B. Spherical rod ends.
C. Pivot tube attached to the bottom of the air cylinder—especially at the pivot points.
3. Check Air Filter Bowl for water and condensation build up.
4. Remove any scrap pieces and dust build up from inside floor stand cabinet.
5. Check monthly:
A. For excessive belt wear.
B. Make sure motor pulley set screws are tight.
Repair and Service:
Always use CTD factory authorized replacement parts and consult factory before making any repairs or
adjustments which may be unclear.
Irregular Mitres:
Irregular mitre cuts are almost always caused by out-of square material. Check your material with a 90° square
and a straight edge. Material that has a high spot on the bottom, will move or roll forward as it is being cut
(even with pneumatic hold down clamps), thereby causing the blade to cut more on the inside of the moulding
than the outside. Another cause of irregular mitre cuts is too thin a plate thickness on blades. Blade plate
thickness should be .090 to .100 on 10” blades, and .095 to .110 on 12” blades. Blades will find the easiest
avenue to cut through material, and sometimes the blade plate will distort when cutting heavier sections. The
drawing below is an example of a cut when blade plate is too thin for the material being cut.
Fence Alignment and 45° Angle Adjustment of Blades:
All D45’s are present at the factory for perfect 45° double mitre cuts. If any adjustments are necessary;
1. Check alignment of front fences—left to right as shown in Diagram “F” on Page No. 5). Use a two foot
steel scale or quality precision straight edge and lay flat on table base. Butt edge against fence bracket and
long measuring gage. Touch the outside corner of the straight edge. If one side of the straight edge pulls
away from the fence, then the long fence gage is not in alignment with the Left Fence Bracket, P/N
15M36L.
2. Loosen 3/8-16 lock nut on Right Fence Bracket, P/N 15M36R and Fence Support Angle, P/N 15F82.
Clean all surfaces of dirt or dust, and re-assemble as before.
3. Re-align right fence to left fence with your straight edge. Once you are sure both fences are in alignment,
you now have a reference point to check your 45° mitre.
If adjustment ot the 45° mitre settings are necessary, you will need a precision draftsman’s triangle. Check
the 45° mitre by placing the triangle against the left fence and in between the gullets or teeth of a Carbide Blade
Touch the triangle against the steel plate of the blade—not against the tips. If an adjustment is necessary;
A. Loosen the three lock down nuts for the pivot bracket, using 9/16 wrench (see Diagram “E” on Page No. 4).
B. Locate Eccentric Pin, No 11 in Diagram “D”. There is a lock bolt (1/4-20x1” bolt with nut) that locks
the eccentric pin in place (see Diagram “E”). Loosen nut and bolt. Adjust eccentric pin until blade plate
aligns perfectly with precision triangle. Now, tighten the eccentric pin lock bolt and nut.
C. Tighten three lock down bolts for the pivot bracket.

-17-
Pull Rods: (refer to Diagram “D”, No. 14 on Page No. 8)
It is important that both blades finish the cut on the material at the same time. If you are getting tear-out on one
side, then a pull rod adjustment may be necessary. The pull rods are tapped left and right, and operate as a turn-
buckle. By loosening the lock nuts and turning the pull rod, the blade is adjusted up, or down from its original
position. A turn to the right shortens the pull rod length. A turn to the left lengths the pull rod. This adjustment
may be necessary after replacing or resharpening blades. It can also eliminate tear-out on wood mouldings. A
chip breaker can be provided as an optional accessory to support the scrap piece and support the material next to
the blade edge—also helping to eliminate tear-out.
**Do not adjust safety upstroke bolt to contact table (for safety purposes only).
Other Repairs:
See specific areas within the manual for additional information on repairs and maintenance.

-18-
D45X Spindle Assembly & Bearing Installation Instructions:
(refer to sketch on following page.)
It is suggested that replacement spindle assemblies be purchased from CTD before disassembling. Old spindles
can be returned for bearing replacement and slinger refacing for a nominal fee. The D45X spindle assembly
provides for a slip-fit between the outer races of the bearing and the housing or arm casting, and a press-fitbetween
the inner race and the spindle. Great care must be taken with ball bearings or the life of the bearing will be reduced.
Disconnect power and air supply to the machine.To remove the spindle assembly;
A. Remove belts
1. Twist belt inside out by hand while rotating forward over spindle pulley
2. Once belt is inside out, pull belt off while rotating around pulleys.
3. Repeat the same procedure for second belt. (Repeat Step No. 1 & 2.)
An alternative method is to loosen the motor.
B. Remove Spindle Pulley Nut, No. 9 by holding pulley.
C. Remove Pulley, No. 8 and place Pulley Nut, No. 9 back onto spindle to protect threads.
D. With a soft hammer or rubber mallet, gently drive spindle towards blade side. Take care to protect pivot
bearings by holding arm casting on blade side to overcome effects of hammer blows.
E. Remove Pulley Nut, No. 9 once again.
F. Spindle Assembly, consisting of Spindle No. 1, Slinger No.3, and Blade Bearing No. 4 will come out of
housing. Pulley bearing will slip out. If you have purchased a replacement spindle, go to item “L”.
G. If bearing on the blade side must be replaced, an arbor press must be used to disassemble the bearing and
the slinger from the spindle. Great care must be used in disassembling, or the spindle will be scored or
stripped by the slinger. Before pressing apart, scribe a line on the face of the spindle and the slinger so
that they will be reassembled in exactly the same position in relation to each other.
H. Press off slinger and bearing from spindle.
I. Press new bearing on to spindle, making sure spindle is square to the bore.
J. Replace slinger, as above, making sure scored lines match.
K. The face of the slinger must be checked to make sure the face (next to the blade) is running true. Using a
dial indicator, the slinger should have a maximum run-out of .001 total. If it is not in tolerance, it should be
refaced. To reface, partially assemble pulley bearing on spindle. Hold outer races of both bearings gently in
a vise. Use the side of a surface grinder wheel to dress the face of the slinger by rotating spindle in bearings
slowly against the direction of the grinding wheel.
L. Make sure that Belleville Springs, No. 6 are assembled in housing as shown in sketch. To reassemble
spindle assembly, slip blade bearing into housing up to the snap ring.
M. Slide pulley bearing onto the spindle as far as it will go.
N. Slide pulley onto shaft. This will allow you to use Pulley Nut, No. 9 to press bearing on. Tighten Pulley Nut
No. 9, pushing bearing onto spindle.
O. To replace belts, reverse procedure under section “A” above. If motor was moved, the centerline of the
motor shaft and the spindle must be parallel. Both pulleys must be in line or belts will not wear evenly.
This should be checked by placing a straight edge across both pulleys. Tighten motor.
P. Belt tension is of critical importance. To obtain proper tension, press down on top of belts with a
moderate amount of pressure. Belts should deflect approximately 1/4”.
Q. Tighten set screw in both pulleys. To check assembly after tightening belts, apply pressure in the
direction of the blade on the pulley nut. A slight spring pressure should be felt. If spindle does not
spring back, the belts may be too tight.

-19-
No.Description Part No.
1 Spindle, Right hand 150M12RX
Spindle, Left hand 150M12LX
2 Flange 150M13X
3 Slinger 150M14X
4 Inside Bearing 150B2P15
5 Snap Ring (2 required) 2B2P06
6 Belleville Spring (4 required) 2B2P07
7 Outside Bearing 2B2P05
8 Spindle Pulley 30B4P23
9 Pulley Jam Nut, Right 15B1P36R
Pulley Jam Nut, Left 15B1P36L
10 Drive Belt, 3V355 (2) 10”&12” 154P48
Drive Belt 14” H.T. 3VX375(2) 9B4P35
11 Arm Casting, Right 15C001RX
Arm Casting, Left 15C001LX
12 Spindle Nut, Right 15B1P36R
Spindle Nut, Left 15B1P37L
----Spindle Assembly, Left
with ground slinger 150E12LX
----Spindle Assembly, Right
with ground slinger 150E12RX
----Arm Assembly w/ Spindle, Left 150E001LX
----Arm Assembly w/Spindle, Right 150E001RX
----Arm & Pivot Assembly, Left 150E101LX
----Arm & Pivot Assembly, Right 150E101RX
Pivot Shaft Parts, D45X
A. 3BM08 Pivot Shaft
B. 2B2P05 Pivot Bearing (2 required)
C. 3B2P10 Belleville Spring (2 required)
D. 3B2P11 Snap Ring (2 required)
Pivot & Motor Parts
15C002LX or RX Pivot Bracket, Left or Right
15M03 Key Pivot Bracket Blade Guard
15M06 Motor Mount Plate
2B4P24 Motor Pulley
150E50L or R Belt/Blade Guard Assy, Lt or Rt
15B6S03 2 H.P. 1 Phase Motor, 60 Hz
15B6S06 2 H.P. 3 Phase Motor, 60 Hz
15B6S04 2 H.P. 1 Phase Motor, 50 Hz
Floor Stand & Table Parts
15F21A or F Floor Stand, Auto or Foot
15C20 Table Base
15M23A Pivot Tube, D45AX
15M23F Pivot Tube, D45FX
15E30A Pivot Tube Assy, D45AX
15E30F Pivot Tube Assy, D45FX
15M24 Rear Pivot Shaft
15MS25A Front Pivot Shaft, D45AX
15M92 Front Pivot Shaft, D45FX
15M27A Pull Rod, D45AX
15E27A or F Pull Rod Assembly
152P28L or R Spherical Rod Bearing, Lt or Rt
Floor Stand & Table Parts continued
15M36L Front Fence, Left
15M36R Front Fence, Right
152P21 Bronze Bushing Pivot Tube
150M44 Top Cylinder Eye Mount
Air Cylinder & Air Feed Parts
150E70 Air Cylinder Assembly
153P27 Cylinder Clevis Mount
4BF101 Valve Bracket
153S71 CTD No. 3 Air Cylinder
15M77 Cylinder Up-Stop Block
B3P50 3-Way Normally Open Valve
15M26 Rod Clevis
B3P71 Foot Valve Assembly
B3P154 FR Unit with Auto Drain
157P73 Rubber Bumper
15M86 Bumper Ring
B3P60 Upstroke & Downstroke
Flow Control Valve

-20-
D45AX & D45FX SAW HEAD ASSEMBLIES
This manual suits for next models
1
Table of contents
Other CTD Saw manuals
Popular Saw manuals by other brands
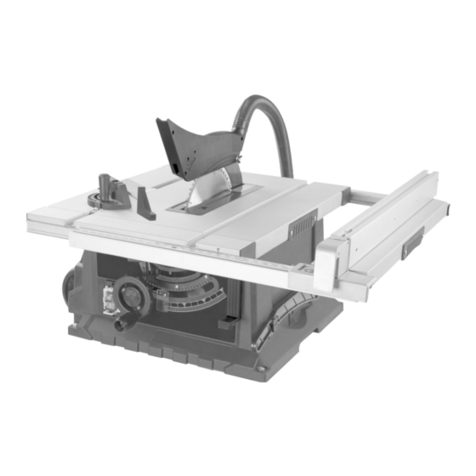
Red Stone
Red Stone 3901314940 Translation from the original instruction manual
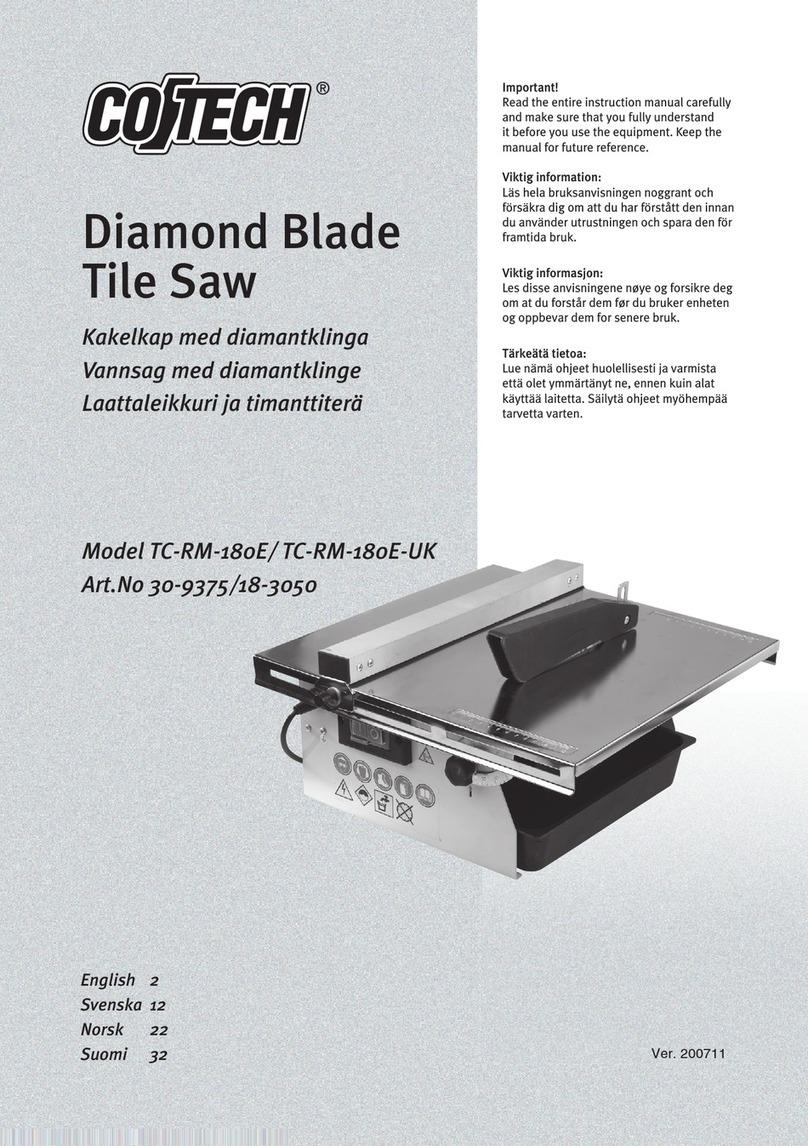
CO/Tech
CO/Tech TC-RM-180E instruction manual

woodmizer
woodmizer LT35 Safety, Setup, Operation & Maintenance Manual

Cosen
Cosen SH-700DM instruction manual
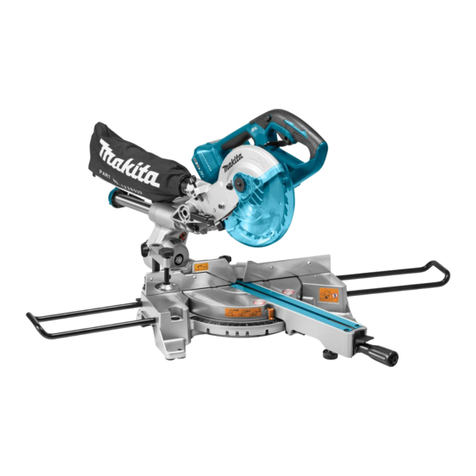
Makita
Makita DLS714 instruction manual
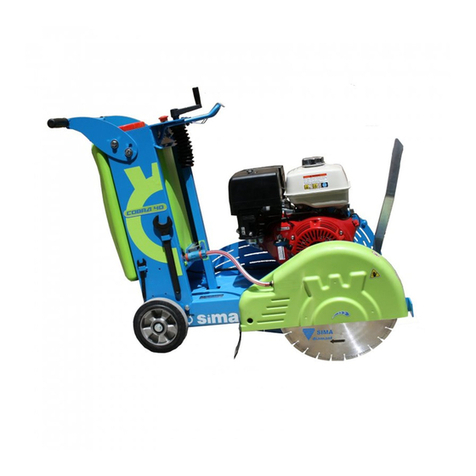
Sima
Sima COBRA-40 Original user guide