CTD DMC70A User manual

INSTRUCTION BULLETININSTRUCTION BULLETIN
INSTRUCTION BULLETININSTRUCTION BULLETIN
INSTRUCTION BULLETIN
& MAINTENANCE MANUAL& MAINTENANCE MANUAL
& MAINTENANCE MANUAL& MAINTENANCE MANUAL
& MAINTENANCE MANUAL
FOR CTD MODELFOR CTD MODEL
FOR CTD MODELFOR CTD MODEL
FOR CTD MODEL
DMC70 “MITRE MAX”DMC70 “MITRE MAX”
DMC70 “MITRE MAX”DMC70 “MITRE MAX”
DMC70 “MITRE MAX”
06.01.08
CTD MACHINESCTD MACHINES
CTD MACHINESCTD MACHINES
CTD MACHINES
2300 East 12300 East 1
2300 East 12300 East 1
2300 East 11th S1th S
1th S1th S
1th Streettreet
treettreet
treet
LosLos
LosLos
Los Angeles, CAAngeles, CA
Angeles, CAAngeles, CA
Angeles, CA 90021-281790021-2817
90021-281790021-2817
90021-2817
(213) 689-4455 F(213) 689-4455 F
(213) 689-4455 F(213) 689-4455 F
(213) 689-4455 FAX (213) 689-1255AX (213) 689-1255
AX (213) 689-1255AX (213) 689-1255
AX (213) 689-1255
e-mail:ctdsaw@ctdsawctdsaw@ctdsaw
ctdsaw@ctdsawctdsaw@ctdsaw
ctdsaw@ctdsaw.com.com
.com.com
.com WWW: http://wwwhttp://www
http://wwwhttp://www
http://www.ctdsaw.ctdsaw
.ctdsaw.ctdsaw
.ctdsaw.com.com
.com.com
.com
CTDMODELNO:______________________CTDMODELNO:______________________
CTDMODELNO:______________________CTDMODELNO:______________________
CTDMODELNO:______________________
CTDSERIALNO:______________________CTDSERIALNO:______________________
CTDSERIALNO:______________________CTDSERIALNO:______________________
CTDSERIALNO:______________________
MANUFACTURE DATE:________________MANUFACTURE DATE:________________
MANUFACTURE DATE:________________MANUFACTURE DATE:________________
MANUFACTURE DATE:________________
DISTRIBUTOR PURCHASED THROUGH:DISTRIBUTOR PURCHASED THROUGH:
DISTRIBUTOR PURCHASED THROUGH:DISTRIBUTOR PURCHASED THROUGH:
DISTRIBUTOR PURCHASED THROUGH:
((
((
(
IFANYIFANY
IFANYIFANY
IFANY
)___________________________________________)___________________________________________
)___________________________________________)___________________________________________
)___________________________________________

INDEXINDEX
INDEXINDEX
INDEX
SUBJECT PAGE NO.
Machine Requirements................................................................................................................ 2
Installation and Set-Up................................................................................................................ 3
Electrical Installation...................................................................................................................... 5-6
Air Pneumatics.............................................................................................................................. 7-8
Safety Instructions......................................................................................................................... 10
How to Operate the Machine........................................................................................................ 11
Preventative Maintenance.............................................................................................................. 14
Repair and Service........................................................................................................................ 15
Spindle Diagrams.......................................................................................................................... 15-16
Spindle & Motor Mount Exploded View........................................................................................ 17
Top Plate Exploded View............................................................................................................... 18-20
Gage & Table Exploded View......................................................................................................... 21
Floor Stand Exploded View............................................................................................................ 22-23
Parts List...................................................................................................................................... 24
Machine Requirements:Machine Requirements:
Machine Requirements:Machine Requirements:
Machine Requirements:
MODEL NO: _____________________ SERIAL NO:______________________
Cutting CapacitiesCutting Capacities
Cutting CapacitiesCutting Capacities
Cutting Capacities:
13”13”
13”13”
13” (330mm) Blade Capacity
Height Width
4”(102mm) 8”(203mm)
-2-
Electrical Requirements:Electrical Requirements:
Electrical Requirements:Electrical Requirements:
Electrical Requirements: Based on two motors per machine
Pneumatic Requirements:Pneumatic Requirements:
Pneumatic Requirements:Pneumatic Requirements:
Pneumatic Requirements:
1 CFM per 10 strokes at 75 PSI (.043 cubic meters at 5.4 kg/cm2)
Dust Collection Requirements:Dust Collection Requirements:
Dust Collection Requirements:Dust Collection Requirements:
Dust Collection Requirements:
1200 CFM at two 4” outlets
CuttingCutting
CuttingCutting
Cutting TT
TT
Tool Requirements:ool Requirements:
ool Requirements:ool Requirements:
ool Requirements:
Heavy, rigid plate blades 13” blades: .120 to .130 plate
Motor Size RequiredAmperage Breaker Needed
1-1/2 H.P.,1 Phase 230 Volt 20 amps 30 amp
1-1/2 H.P., 3 Phase 230 Volt 9.2 amps 15 amp
1-1/2 H.P., 3 Phase 460 Volt 4.6 amps 15 amp
2 H.P., 3 Phase 208 Volt 5.7 amps 20 amp
2 H.P., 1 Phase 230 Volt 25 amps 40 amp
2 H.P., 3 Phase 230 Volt 10.8 amps 20 amp
2 H.P., 3 Phase 460 Volt 5.4 amps 15 amp

-3-
Installation and Set UpInstallation and Set Up
Installation and Set UpInstallation and Set Up
Installation and Set Up::
::
:
CTD 13”(330mm) Models DMC70A Automatic & DMC70M Manual Double Mitre Cross-Cut Saws:
The CTD saw you have purchased is designed to cut wood, aluminum, and plastic, with of course, the proper
blade and conditions. For the material you are cutting, please refer to the cutting instructions for
each material type. The DMC70 uses a NEMA 56 Frame 1-1/2 H.P., 3450 RPM, 60 HZ TEFC motor. CTD uses a
speed-up drive so that the blade will run at approximately 12,000 SFPM on a 13” (330mm) blade. The DMC70A and
the DMC70M are exactly the same machine with the exception of the Air Pneumatic
System. All instructions will pertain to
both
machines unless specifically excluded.
IMPORIMPOR
IMPORIMPOR
IMPORTT
TT
TANTANT
ANTANT
ANT
::
::
: Before operating saw, please be sure to read the “SAFETY INSTRUCTIONS TO THE
OPERATOR” (on Page No. 10).
NoteNote
NoteNote
Note::
::
:
The floor stand must be leveled to the floor to eliminate vibration. Adjustable leveling feet are provided.
Adjust leveling feet as necessary by loosening lock nut. All machines have been completely assembled at the factory,
then disassembled for shipment.
Space Requirements:Space Requirements:
Space Requirements:Space Requirements:
Space Requirements:
Assembly of Tables to Floor Stand:Assembly of Tables to Floor Stand:
Assembly of Tables to Floor Stand:Assembly of Tables to Floor Stand:
Assembly of Tables to Floor Stand:
1. Assemble leg to table with 3/8-16 bolts and nuts provided. Turn table upside down and attach leg to
table with leg rising vertically.
Note
: The hole in the table (when mounted properly) should be toward
the front of the table and far away from the blade to attach Fence Support Bar, P/N 20M82
(see Diagram “A”). If you have purchased a Vision Gage Assembly, be careful to protect lined measuring
gage.
2. Attach Table, P/N BF17 to machine floor stand on Angle Bracket, P/N BF05A. Use 3/8-16 bolts and
nuts provided on angle bracket.
Diagram “A”

Blade InstallationBlade Installation
Blade InstallationBlade Installation
Blade Installation:
Before setting blades on spindle, always shut off or disconnect air supply. With motor OFFOFF
OFFOFF
OFF and power
disconnected, loosen front blade guard bolts. The main blade guard will hinge up and open, exposing blade and spindle.
Loosening the bolts automatically shuts down machine, due to an interlock switch located on hinged blade guard.
1. Remove Spindle Nut, P/N 9B1P36 or 37 and Outer Flange, P/N 8M02. If necessary, hold blade in
hand with a rag. Push down with a 1-7/16” wrench provided.
2. Place blade on spindle with tips pointing down. Make sure Slinger (inner flange P/N 8M03) and blade
surface are cleanclean
cleanclean
clean before putting blade on spindle. This is a critical surface and is ground within .0005
flatness. Any debris or dust will wear this surface. Wipe both surfaces (blade and slinger) with a clean rag.
A. The blade must ALWAYSALWAYS
ALWAYSALWAYS
ALWAYS rotate to the rear of the machine on the underside of the blade
(see Diagram “D” on page No. 4).
Always check rotation before cutting a piece of material.Always check rotation before cutting a piece of material.
Always check rotation before cutting a piece of material.Always check rotation before cutting a piece of material.
Always check rotation before cutting a piece of material.
3. Replace Outer Flange, P/N 8M03 and nut
as before and tighten (refer to Diagram “B”).
Pull up with wrench. Do not over-tighten;
snugging the blade is all that is necessary.
Diagram “B”
-4-
VV
VV
Vision Gageision Gage
ision Gageision Gage
ision Gage Assembly:Assembly:
Assembly:Assembly:
Assembly:
The vision gage has been completely installed on your machine before shipment. It is then disassembled for
shipment.
1. Attach leg to table with 3/8-16 bolts and nuts provided.
2. Attach Table, P/N BF17D to machine floor stand on Angle Bracket, P/N BF05A. Use 3/8-16 bolts and nuts
provided on angle bracket.
3. Butt Vision Gage and table as close as possible to the edge of the base plate P/N 70M01.
A. With a scale or ruler touching the side of the tips of the blade, measure a distance away from the blade. Be sure ruler
and vision gage markings read the same. Adjust Left to Right as necessary.
4. Put outside Fence Gage, P/N 70M223-6’on top of lined Vision Gage so that lines terminate at fence. Attach
outside measuring gage with 3/8-16 bolts provided to Right Front Fence Angle, P/N 70M35R. Adjust gage
so measurement rule is correct. Follow instructions under No. 3A above. Attach Fence Support Bar,
P/N 20M82 with bolt and nuts provided to the table front. See Diagram “A” on page 3.
Attaching Measuring System to Machine:Attaching Measuring System to Machine:
Attaching Measuring System to Machine:Attaching Measuring System to Machine:
Attaching Measuring System to Machine:
Diagram “F”
Diagram “D”
Front
Rear

-5-
Electrical InstallationElectrical Installation
Electrical InstallationElectrical Installation
Electrical Installation::
::
:
The CTD DMC70’s use two 1-1/2 H.P. single or three phase 3450 RPM, 60 HZ TEFC (totally enclosed fan cooled)
motors on a NEMA 56Z Frame. CTD uses a speed up drive so that the blade will run at approximately 3700 RPM.
Electrical installation should be performed by a qualified and certified electrician. A lock-out or disconnect switch
is located in front of the machine. It is a rotary switch to the left front of the machines. This disconnect switch is
used to shut off power to the machine and should be used whenever the blades are changed or at any time the
machine is serviced and the blades are exposed. A Dual Magnetic Starter, located inside the left side panel of the
machine protects the motor from overheating and will not allow the motor to restart itself after power outages or
undervoltage situations. The START button turns the motors “ON”. The STOP button turns the motors “OFF”.
Note: The STOP button must be pulled out before the START button will activate the motors.
Electrical Installation of Power to Starter by a Qualified Electrician:Electrical Installation of Power to Starter by a Qualified Electrician:
Electrical Installation of Power to Starter by a Qualified Electrician:Electrical Installation of Power to Starter by a Qualified Electrician:
Electrical Installation of Power to Starter by a Qualified Electrician:
All wiring from the motors to the starter has been completed and tested at the factory several times. The voltage
has been clearly tagged.
DO NOT CONNECT ANY VOLTAGE THAT IS DIFFERENT THAN THE TAGGED
VOLTAGE, AS THIS MAY CAUSE SEVERE DAMAGE AND DANGER.. CONSULT FACTORY IF ANY
CHANGES ARE NEEDED.
Bring incoming power lines to the left side using hard wire and dust proof connectors.
Attach incoming power lines through Floor Stand to the rotary disconnect switch. Connect to terminals 2 & 4
for single phase motors, and to terminals 2, 4 & 6 for three phase motors. Always ground the green wire.
(See wiring diagram on Page 6.)
Single Phase Motor Replacement:Single Phase Motor Replacement:
Single Phase Motor Replacement:Single Phase Motor Replacement:
Single Phase Motor Replacement:
Connect motor leads to T1 and T3 of overload relay for single phase motors. (See wiring diagram for single
phase motors on following page) Green ground wire must be grounded to enclosure. If using type “SO” wire
and plug, use a dust tight connector through Floor Stand and a grounded plug.
Be sure to check
rotation. If a
change is necessary, open the motor box located on the motor, and switch the #8 and the #5 wires. This reverses
the rotation of a single phase motor. The blade must rotate down and to the rear on the underside of the blade
(see Diagram “D” on Page No. 4).
Vision Gage Diagram
The hinged front blade guard must be tightened down in place properlyThe hinged front blade guard must be tightened down in place properly
The hinged front blade guard must be tightened down in place properlyThe hinged front blade guard must be tightened down in place properly
The hinged front blade guard must be tightened down in place properly..
..
. An interlock switch, located on theAn interlock switch, located on the
An interlock switch, located on theAn interlock switch, located on the
An interlock switch, located on the
blade guard must be contacted or the motors will not start.blade guard must be contacted or the motors will not start.
blade guard must be contacted or the motors will not start.blade guard must be contacted or the motors will not start.
blade guard must be contacted or the motors will not start.

-6-
Three Phase Motor Replacement:Three Phase Motor Replacement:
Three Phase Motor Replacement:Three Phase Motor Replacement:
Three Phase Motor Replacement:
Connect motor line leads to T1, T2, & T3 of the overload relays. (See wiring diagram for three phase motors.)
Green ground wire must be grounded to enclosure.
Be sure to check rotation
as polarities may be different.
The blade must rotate down and to the rear on the underside of the blade (see Diagram “D” on Page No. 4). If a
change in rotation is necessary, reverse any two of the incoming power wires.
Example:
If the blades are running
backwards and incoming wires are connected White L1,Black L2,Red L3, switch the Black wire with the Red so
that Black is connected to L3 and Red is connected to L2. This will change the blades to rotate properly.
Motor Load Amperes Per MotorMotor Load Amperes Per Motor
Motor Load Amperes Per MotorMotor Load Amperes Per Motor
Motor Load Amperes Per Motor
MOTOR SIZE 110 VOLT220 VOLT440 VOLT
1-1/2 H.P., 1 Phase 20 amps 10 amps N/A
1-1/2 H.P., 3 Phase N/A 4.6 amps 2.3 amps
2 H.P., 1 Phase 25 amps 12.5 amps N/A
2 H.P., 3 Phase N/A 5.4 amps 2.7 amps
Single Phase Wiring DiagramSingle Phase Wiring Diagram
Single Phase Wiring DiagramSingle Phase Wiring Diagram
Single Phase Wiring Diagram
Three Phase Wiring DiagramThree Phase Wiring Diagram
Three Phase Wiring DiagramThree Phase Wiring Diagram
Three Phase Wiring Diagram

-7-
DMC70DMC70
DMC70DMC70
DMC70 Air/PneumaticAir/Pneumatic
Air/PneumaticAir/Pneumatic
Air/Pneumatic WW
WW
Wiring Diagramiring Diagram
iring Diagramiring Diagram
iring Diagram

-8-
DMC70DMC70
DMC70DMC70
DMC70 Air/Pneumatic SystemAir/Pneumatic System
Air/Pneumatic SystemAir/Pneumatic System
Air/Pneumatic System::
::
:
The air pneumatic system on the DMC70 is simple to use and understand, and easy to operate. The main
components of the air system are shown below in the Air Circuit Piping Diagram. The system operates by
depressing the foot switch to actuate clamps. Pushing the foot switch again releases clamps. Once the clamps are clamped,
the operator depresses the two-hand control buttons simultaneously, P/N 70B5P79. This gives a signal to the main 4-Way
Control Valves for the left saw to change direction—allowing air to pass to the main drive Cylinder on the left, P/N
70B3P75. This pushes the saw forward to a limit switch. The speed of the stroke is controlled by the Speed Control
Valve, P/N70B3P60. The left saw reverses and returns to the rest position, then the right saw moves forward to the limit
switch and then reverses and returns to the rest position. The vertical clamps then release. If the two-hand control buttons
are released anytime during the cycle, then the cycle is terminated and the saws will return to the rear or rest position. The
cycle will have to be restarted by clamping and then pushing the two-hand buttons simultaneously.
Diagram “I“Air Circuit Piping for Model DMC70A
Air SupplyAir Supply
Air SupplyAir Supply
Air Supply—The air supply must be turned off and all electrics disconnected before making adjustment on the
power feed. A working pressure of 75 PSI (5.4kg/cm2) is required. An industrial-type compressor of at least
3 CFM (.085 cubic meters) is recommended. An additional 3 CFM (.085 cubic meters is required for Sawblade
Lubrication System. Aconveniently located valve is supplied by the user to shut off the air line. Saws should beSaws should be
Saws should beSaws should be
Saws should be
movedmoved
movedmoved
moved
by handby hand
by handby hand
by hand
when setting up machine.when setting up machine.
when setting up machine.when setting up machine.
when setting up machine.
FRFR
FRFR
FR—An Air Filter/Regulator is installed ahead of the air inlet to the machine. This system helps prevent foreign matter
from entering the system. The FR is comprised of two different components.
1. The
Air Filter Bowl is located on the left side and is provided with an automatic drain. This collects and
then releases foreign matter and condensation collected by the air filter.
2. The Pressure Regulator, which is located on top of the air filter, controls the amount of air pressure allowed
into the system. An operating pressure of 75 PSI is required. (This is set at the factory.)

Air Filter/RegulatorAir Filter/Regulator
Air Filter/RegulatorAir Filter/Regulator
Air Filter/Regulator
TT
TT
Two Hand Control and Selector Switch:wo Hand Control and Selector Switch:
wo Hand Control and Selector Switch:wo Hand Control and Selector Switch:
wo Hand Control and Selector Switch:
The saw movement is controlled by depressing the two-hand anti-tie down control buttons. Once the clamps are
actuated via the foot switch, the two-hand buttons are depressed. The buttons must be held down throughout the saw
cutting cycle. The stroke of the saw heads can be reversed at any time by releasing the two-hand buttons. The selec-
tor switch can be used to operate only the left saw, only the right saw, or both. The selector switch “left” will only allow
the two-hand buttons to operate the left saw. The selector switch “right” will only allow the two-hand buttons to
operate the right saw. Selector switch “both” allows the two-hand control to operate the left saw and then the right
saw, to complete a cycle.
Speed Control of Blades Movement:Speed Control of Blades Movement:
Speed Control of Blades Movement:Speed Control of Blades Movement:
Speed Control of Blades Movement:
The forward speed of the left blade is controlled by the left Speed Control Valve, P/N 70 B3P60. The forward
speed of the right blade is controlled by the right Speed Control Valve, P/N 70B3P60. Both are located in the two-
hand button enclosure, located in the front of the machine. An easy way to remember is the
left
valve controls the
left
saw, and the
right
valve controls the
right saw.
-9-
Air Hold Down Clamps for the Material:Air Hold Down Clamps for the Material:
Air Hold Down Clamps for the Material:Air Hold Down Clamps for the Material:
Air Hold Down Clamps for the Material:
Horizontal manual clamps are supplied standard on the hand operated DMC70M and two VerticalAir Clamps are
supplied standard on the pneumatic version, the DMC70A. These clamps help hold the material in place when the saw
blades are cutting the material. If clamps are not used, the operator
MUST HAND HOLD THE MATERIAL
. For the
hand operated DMC70M, the horizontal clamp pad or shoe needs to be adjusted so that it sits about 1/8” away from
the inside or rabbet of the material. When pulling the saw forward, the clamp will move forward to contact material and
push it towrds the front fences. The vertical clamps, on the DMC70A are controlled by two 4-Way Valves located in
the control panel on the lower right front side of the machine. The clamps are actuated by a foot switch when the two-
hand control buttons are depressed. A manual shut-off switch for the vertical air clamps is provided.

-10-
Safety Instructions to the Operator:Safety Instructions to the Operator:
Safety Instructions to the Operator:Safety Instructions to the Operator:
Safety Instructions to the Operator:
1.
KNOW YOUR CTD SAW
. Read this instruction manual carefully. Learn the operation, application, and
limitations, as well as the specific potential hazards peculiar to this machine.
2. Avoid accidental starting. Make sure switch is OFFOFF
OFFOFF
OFF before plugging in power cord. A Dual Magnetic
Starter is provided to give the operator added protection.
3. Always use a plug equipped with a ground.
4. Always keep blade guard in place. Do not wire-up or chain-up, so that blade is exposed.
5. Be sure all unnecessary tools are removed from machine before turning on power.
6. Use safety goggles. Also use a face or dust mask if operation is dusty.
7. Support work. To maintain control of work at all times, it is necessary that material be level with cutting
surface.
8. Wear proper apparel. Do not wear loose clothing or jewelry. Do not wear a tie or gloves. These items can
get caught in the moving parts of the machine.
9. Do not over-reach. Keep your proper footing and balance at all times.
10. Maintain your machine in top condition. Use proper blades. Clean machine weekly for proper maintenance.
11. Keep work area clean. Cluttered areas, benches and slippery floors invite accidents.
12. Avoid dangerous environments. Keep work area well illuminated.
13. Wear ear protection if exposed to long periods of very noisy shop operations.
14. Keep visitors away. All visitors should be kept a safe distance from work area.
15. Do not force the machine. The saw will do a better job and be safer to operate at the speed for which it was
designed. Forcing the saw can be very hazardous to the operator.
16. Use recommended accessories. Use of other accessories may be hazardous. Use this instruction manual or
consult CTD for the proper accessories available.
17. Do not drown the blade using a steady stream of coolant when cutting non-ferrous materials. Only spray
the work to cool it.
18. Be sure to use the proper blade for the particular material to be cut.
19. Disconnect power cord before adjusting, servicing, and before changing belts, or for installing accessories.
20. Safety is a combination of operator
COMMON SENSE
and
ALERTNESS
at all times when the machine is
being used.
21.
WARNING!!!WARNING!!!
WARNING!!!WARNING!!!
WARNING!!! DO NOT ALLOW FAMILIARITY (GAINED FROM FREQUENT USE OF YOUR SAW)
TO DULL YOUR AWARENESS!! ALWAYS REMEMBER THAT A CARELESS FRACTION OF A SECOND
IS SUFFICIENT TO INFLICT SEVERE INJURY!!
TT
TT
Trouble Shooting the Pneumatic System for the DMC70 Cross-Cut Sawrouble Shooting the Pneumatic System for the DMC70 Cross-Cut Saw
rouble Shooting the Pneumatic System for the DMC70 Cross-Cut Sawrouble Shooting the Pneumatic System for the DMC70 Cross-Cut Saw
rouble Shooting the Pneumatic System for the DMC70 Cross-Cut Saw:
If there is no control over the speed of the cylinder stroke:
A. Replace either Left or Right Flow Control Valve (see exploded view on page 22, item #23). Another possible
cause are bad seals in the air cylinder. Listen for any air leakage.
B. If machine cycle will not start, or will not reverse, check the two-hand control buttons. Also, check for any
mechanical binding. Disconnect electricity and air supply from the machine. Manually move saws forward and back to
check for binding of the saw or feed mechanism. If machine is bound up, clear the blockage.
Remember, there is an
Interlock switch located under the hinged blade guard. The blade guard must be solidly in place and the bolts
tightened for the machine to operate.

-11-
How to operate the DMC70A or DMC70M:How to operate the DMC70A or DMC70M:
How to operate the DMC70A or DMC70M:How to operate the DMC70A or DMC70M:
How to operate the DMC70A or DMC70M:
Before operating the machine, please read the “SAFETY INSTRUCTIONS TO THE OPERATOR”. Other
important information and features need to be learned before operating the machine.
Rotation:Rotation:
Rotation:Rotation:
Rotation:
Both blades must rotate to the rear of the machine on the underside of the blades
(see Diagram “D”on Page No. 4.)
Blade Guard:Blade Guard:
Blade Guard:Blade Guard:
Blade Guard:
It is important that the Finger Guards, P/N 20F180 are adjusted to completely cover the blade.It is important that the Finger Guards, P/N 20F180 are adjusted to completely cover the blade.
It is important that the Finger Guards, P/N 20F180 are adjusted to completely cover the blade.It is important that the Finger Guards, P/N 20F180 are adjusted to completely cover the blade.
It is important that the Finger Guards, P/N 20F180 are adjusted to completely cover the blade.
The fingerThe finger
The fingerThe finger
The finger-guards, attached to the hinged main blade guard, should be positioned around the material to give-guards, attached to the hinged main blade guard, should be positioned around the material to give
-guards, attached to the hinged main blade guard, should be positioned around the material to give-guards, attached to the hinged main blade guard, should be positioned around the material to give
-guards, attached to the hinged main blade guard, should be positioned around the material to give
maximum operator protection.maximum operator protection.
maximum operator protection.maximum operator protection.
maximum operator protection.
The main blade guard can be hinged up by loosening the lock bolts on front of the
guard. An interlock switch locks out the power to the saws until the hinged guard is back
in place and the bolts are tightened completely. Disconnect the air supply and move the
blades forward manually exposing the blades Follow the instructions on page 4, Blade
installation, for changing the blades. After changing blades, replace blade guard and
tighten guard lock down bolts .
Be sure to provide clearance between the blade guard
and the top of the blade at the top of the stroke.
This label is attached to the blade
guards.
NEVER PUTNEVER PUT
NEVER PUTNEVER PUT
NEVER PUT HANDS OR FINGERS NEAR OR UNDERHANDS OR FINGERS NEAR OR UNDER
HANDS OR FINGERS NEAR OR UNDERHANDS OR FINGERS NEAR OR UNDER
HANDS OR FINGERS NEAR OR UNDER THE MOVTHE MOV
THE MOVTHE MOV
THE MOV--
--
-
ING BLADE!!ING BLADE!!
ING BLADE!!ING BLADE!!
ING BLADE!!
Use a piece of wood to remove short pieces from saw.
Cutting:Cutting:
Cutting:Cutting:
Cutting: (see Diagram “J” and “K”)
A fixed Double Mitre Saw, such as the DMC70 operates by making two 45°cuts at one time. The machine “V”
notches the piece of material between the two blades. To make the first cut on a stick length;
1. Feed the material to the centerline of the machine so that
ONLYONLY
ONLYONLY
ONLY
the
left
blade
makes a trim cut. Be careful
not to overfeed beyond the centerline of the machine, as the piece can be hit with the right blade, possibly
throwing the unclamped piece into the saw blade, causing damage.
2. After making the trim cut, feed the material (now with a 45°mitre cut) to the stop at the desired length.
When using the Vision Gage, slide the moulding to the desired inside dimension, sighting down the line to the inside
of the rabbet of the moulding.
Move outside stop to same position and lock (see Diagram “K”).
3. Continue to feed length to stop as above, and make double mitre cuts until length is used.
4.
RULE OF DOUBLE MITRE CUTTINGRULE OF DOUBLE MITRE CUTTING
RULE OF DOUBLE MITRE CUTTINGRULE OF DOUBLE MITRE CUTTING
RULE OF DOUBLE MITRE CUTTING
—If the piece to be cut cannot be held on both sidesboth sides
both sidesboth sides
both sides of the blade,
do not cut it!!!do not cut it!!!
do not cut it!!!do not cut it!!!
do not cut it!!!
Minimum cut length on the DMC70A and DMC70M is 5 1/2” on the point to point dimensionMinimum cut length on the DMC70A and DMC70M is 5 1/2” on the point to point dimension
Minimum cut length on the DMC70A and DMC70M is 5 1/2” on the point to point dimensionMinimum cut length on the DMC70A and DMC70M is 5 1/2” on the point to point dimension
Minimum cut length on the DMC70A and DMC70M is 5 1/2” on the point to point dimension. ConsultConsult
ConsultConsult
Consult
factory for shorter lengths.factory for shorter lengths.
factory for shorter lengths.factory for shorter lengths.
factory for shorter lengths.
Diagram “J” Diagram “K”

-12-
Cutting Speed:Cutting Speed:
Cutting Speed:Cutting Speed:
Cutting Speed:
The blade is rotating at approximately 3700 RPM. When moving the blade through the material, the blade must
NEVERNEVER
NEVERNEVER
NEVER
be allowed to dwell in the work. If fine finishes are required;
1. Use a sharp blade.
2. Use a
constant, even pressureconstant, even pressure
constant, even pressureconstant, even pressure
constant, even pressure
when cutting through material.
Clamping and Work Slippage:Clamping and Work Slippage:
Clamping and Work Slippage:Clamping and Work Slippage:
Clamping and Work Slippage:
The work must never be allowed to move or vibrate as it is being cut. When the work is positioned against a
stop, it must be clamped either by the manual horizontal clamp or by vertical pneumatic air clamps. Never allow unclamped
work between the blade and the stop, as the blade can grab the material and throw it—thereby causing damage to the
blade, the machine, and possibly harming the operator. Vertical Clamps hold the material down, against the table base.
Vertical clamps are offered as standard equipment on the DMC70A air operated machine. Manual horizontal clamps are
standard on the DMC70M manually hand operated machine. Check your material for squareness, using a 90°square.
Material that is out of square will move when it is cut, thereby causing irregular mitres. See “IRREGULAR MITRES”,
Page No. 15. Additional tooling may be needed. Consult factory for information.
Vertical Clamp Assy.Manual 45° Horizontal ClampAssy.
CuttingCutting
CuttingCutting
Cutting WW
WW
Wood:ood:
ood:ood:
ood:
While wood is generally soft and simpler to cut than aluminum, it requires that the material be held in place
as the blades pass through the material. CTD suggests using a Carbide Blade with an Alternate Top Bevel
(ATB) for lighter wood sections and picture frame mouldings. This type of blade gives the finest of finishes.
No
ONE
blade will cut all material perfectly. High lacquers or mica mouldings may require a special modified blade
for best results. Consult factory.
Never use a woodwood
woodwood
wood blade to cut aluminum,aluminum,
aluminum,aluminum,
aluminum,
as it will chip and fracture the
carbide tips of the blade.
Cutting Plastic:Cutting Plastic:
Cutting Plastic:Cutting Plastic:
Cutting Plastic:
Plastic can be cut as easily as wood on the DMC70 models. However, because of its elastic properties, the material can
deflect as the blades pass through. Therefore, it is important to clamp the material as close as possible to the blade and
support it by use of fixtures. Additional tooling may be required. Special carbide blades are available for cutting plastics.

CuttingCutting
CuttingCutting
Cutting Aluminum:Aluminum:
Aluminum:Aluminum:
Aluminum:
As with cutting any material, it is important that aluminum be clamped properly. Precision blades are required
for accurate cutting. CTD suggests and uses a Triple Chip Grind on all its nonferrous Carbide Blades. When
cutting aluminum, or other nonferrous materials, it is essential that the blades be lubricated with a Saw Blade Lubrication
System or other blade lubricating system for the finest finish. See SAWBLADE LUBRICATION SYSTEM
below for more details.
Combination Blades:Combination Blades:
Combination Blades:Combination Blades:
Combination Blades:
Any combination blade is basically an aluminum cutting blade. Significant blade life in between sharpenings
will be lost if a blade is used for cutting both aluminum and wood. The amount of production for either wood
or aluminum should be the determining factor in the assessment of the particular blade type to be used. Please
consult factory.
Sawblade Lubrication System:Sawblade Lubrication System:
Sawblade Lubrication System:Sawblade Lubrication System:
Sawblade Lubrication System:
The Sawblade Lubrication System is used when cutting aluminum or other nonferrous material . This system normally
uses a Water Soluble Oil mixture of
10 parts water to one part oil.
The system operates by siphoning the lubrication up
the line to the spray nozzle. Any air leak will cause inconsistent fluid flow to the spray nozzle.
BEBE
BEBE
BE SURE
your fluid is free
from chips and other debris. A fluid container supplied with the machine contains a One-Way Check Valve, Part No.
B3P96 at the end of the clear fluid line. This check valve helps to hold the lubrication in the line. However, after a couple
of minutes the lubrication or oil will back-flow into the container. Priming of the system may be necessary if the machine has
been standing without use. The system may be shut off by closing the toggle valve next to the vacuum pump. The fluid
must be clean or the vacuum pump will clog.
CTD Bio Lubrication System:CTD Bio Lubrication System:
CTD Bio Lubrication System:CTD Bio Lubrication System:
CTD Bio Lubrication System:
The CTD biodegradable lubrication system operates by pulse spraying a minute amount of biodegradable lubri-
cant directly on to the saw tooth of the blade in time-measured increments. The majority of the lubricant then
dissipates with the heat of the cutting action. Chips coming off the blade are hot and dry, and are more easily collected
(see specific instructions included with system).
-13-

-14-
Cutting Wide Materials:Cutting Wide Materials:
Cutting Wide Materials:Cutting Wide Materials:
Cutting Wide Materials:
Wider mouldings can easily be cut on the DMC70’s because of our unique below table saw head design. This design
allows for use of the top of the blade to cut, as well as the front of the blade. One blade completes the cut before the
second blade begins its cut. The blades cross-over an intersecting point to create a virtually scrap free cut.
Scrap:Scrap:
Scrap:Scrap:
Scrap:
The DMC70’s operate by making two 45°mitres one right after the other. A “V” shaped piece is removed and falls into
the scrap drawer and bin located on the bottom front of the machine. Empty the scrap bin regularly. The blades cross-over
an intersecting point that virtually eliminates the scrap. Only the kerf of the two blades is lost in the cutting action.
Preventative Maintenance:Preventative Maintenance:
Preventative Maintenance:Preventative Maintenance:
Preventative Maintenance:
The DMC70’s are relatively easy machines to operate and maintain. Below is a weekly check list of
general maintenance items. The best preventative maintenance advice is to
CLEAN THE MACHINE DAILY,
especially around the pivot points or moving parts of the machine.
Lubrication andLubrication and
Lubrication andLubrication and
Lubrication and Adjustments of BearingsAdjustments of Bearings
Adjustments of BearingsAdjustments of Bearings
Adjustments of Bearings::
::
:
INSPECTINSPECT
INSPECTINSPECT
INSPECT
AND LUBRICAAND LUBRICA
AND LUBRICAAND LUBRICA
AND LUBRICATE BEARING BLOCKS ONCETE BEARING BLOCKS ONCE
TE BEARING BLOCKS ONCETE BEARING BLOCKS ONCE
TE BEARING BLOCKS ONCE AA
AA
AMONTHMONTH
MONTHMONTH
MONTH..
..
.
Bearing blocks and linear tracks
(see picture below) must be inspected and lubricated regularly in order to keep fine particules of dust out of the ball
bearings. Spindles are assembled using sealed, prelubricated ball bearings. It is not necessary to lubricate the spindle
bearings. They also use preloaded belleville springs. These springs eliminate the need for adjustments of bearings and
also greatly increase the life of these bearings. All air cylinders are “lube for life”.
Sound Levels:Sound Levels:
Sound Levels:Sound Levels:
Sound Levels:
During normal running of the machine without cutting the typical sound range will be between 60-85 db.
Due to the wide variety of blades available, CTD cannot warrant that maximum allowable OSHA sound limits
can be met--particularly during the cutting cycle.
Grease here
General Maintenance Check List:General Maintenance Check List:
General Maintenance Check List:General Maintenance Check List:
General Maintenance Check List:
Always disconnect electrical power and air supply.
1. Keep machine clean—especially around the bearing
track.
2. Blow off and clean:
A. Around air cylinder.
3. Check Air Filter Bowl for water and condensation
build up.
4. Remove any scrap pieces and dust build up from inside
floor stand cabinet.
5. Check monthly:
A. Lubricate bearing blocks as detailed on page 15.Lubricate bearing blocks as detailed on page 15.
Lubricate bearing blocks as detailed on page 15.Lubricate bearing blocks as detailed on page 15.
Lubricate bearing blocks as detailed on page 15.
B. Make sure motor pulley set screws are tight.
C. For excessive belt wear.

-15-
Repair and Service:Repair and Service:
Repair and Service:Repair and Service:
Repair and Service:
Always use CTD factory authorized replacement parts and consult factory before making any repairs or
adjustments which may be unclear.
Irregular Mitres:Irregular Mitres:
Irregular Mitres:Irregular Mitres:
Irregular Mitres:
Irregular mitre cuts are almost always caused by out-of square material. Check your
material with a 90°square and a straight edge. Material that has a high spot on the
bottom, will move or roll forward as it is being cut (even with pneumatic hold down
clamps), thereby causing the blade to cut more on the inside of the moulding than the
outside. Another cause of irregular mitre cuts is too thin a plate thickness on blades.
Blade plate thickness should be .120 to .130 on 13” blades. Blades will find the
easiest avenue to cut through material, and sometimes the blade plate will distort when
cutting heavier sections. The drawing below is an example of a cut when blade plate is
too thin for the material being cut.
Fence Alignment and 45Fence Alignment and 45
Fence Alignment and 45Fence Alignment and 45
Fence Alignment and 45°Angle Adjustment of Blades:Angle Adjustment of Blades:
Angle Adjustment of Blades:Angle Adjustment of Blades:
Angle Adjustment of Blades:
All DMC70’s are present at the factory for perfect 45°double mitre cuts. If any adjustments are necessary:
1. Check alignment of front fences—left to right as shown in Diagram “F” on Page No. 4). Use a two foot
steel scale or quality precision straight edge and lay flat on table base. Butt edge against fence bracket and
long measuring gage. Touch the outside corner of the straight edge. If one side of the straight edge pulls
away from the fence, then the long fence gage is not in alignment with the Left Fence Bracket, P/N
70M35L.
2. Loosen 3/8-16 lock nut on Right Fence Bracket, P/N 70M35R and Fence Support Bar, P/N 20M26.
Clean all surfaces of dirt or dust, and re-assemble as before.
3. Re-align right fence to left fence with your straight edge. Once you are sure both fences are in alignment,
you now have a reference point to check your 45°mitre.
For Model DMC70: (see spindle drawing on page 16)
A. Hinge up Guard Cover, P/N 70F03E by loosening two front guard bolts.
B. Push saw forward to remove spindle housing P/N 9A05 from slide.
1. Remove hex cap screws with wrench and detach Spindle Housing, P/N 9A05 from slide P/N 70A04.
2. Using a vise with aluminum jaws, hold slinger and loosen jam nut No. 9, but leave jam nut on spindle.
3. Loosen set screws in pulley.
DMC70 SpindleDMC70 Spindle
DMC70 SpindleDMC70 Spindle
DMC70 Spindle Assembly and Bearing Installation Instructions:Assembly and Bearing Installation Instructions:
Assembly and Bearing Installation Instructions:Assembly and Bearing Installation Instructions:
Assembly and Bearing Installation Instructions:
Grease Requirements and Grease Gun:Grease Requirements and Grease Gun:
Grease Requirements and Grease Gun:Grease Requirements and Grease Gun:
Grease Requirements and Grease Gun:
Use a Pistol Grip Grease Gun P/N 70B7P55P/N 70B7P55
P/N 70B7P55P/N 70B7P55
P/N 70B7P55 to grease both block bearings
on the machine (see picture on Page 14). Squeeze handle four times to dispense grease.
Grease tube is P/N 70B7P56P/N 70B7P56
P/N 70B7P56P/N 70B7P56
P/N 70B7P56 with the following specification of KP 2 K-20 which is
suitable for harsh dry environments. Remember to lubricate monthlyRemember to lubricate monthly
Remember to lubricate monthlyRemember to lubricate monthly
Remember to lubricate monthly..
..
.

-16-
1. 90M01L DMC70 Spindle, Left
90M01R DMC70 Spindle, Right
2. 8M03 DMC70 Flange
3. 8M02 DMC70 Slinger
4. 9B2P04X Double Row Bearing
5. 9B2P06 Snap Ring
6. 2B4P28 Spindle Pulley 2.6”, .787 bore
7. 2BM23 Pulley Key
8. 9B2P05 Belleville Springs (4 required)
9. 151P16L Jam Nut, Left
151P16R Jam Nut, Right
10. 9B2P03 Bearing, Jam Nut side
11. 70B4P25 3VX450 DMC70 Drive Belt Banded
(2 required)
12. 9A05 Spindle Housing
13. 9B1P44L Spindle Nut, Left
9B1P44R Spindle Nut, Right
DMC70 SpindleDMC70 Spindle
DMC70 SpindleDMC70 Spindle
DMC70 Spindle Assembly PartsAssembly Parts
Assembly PartsAssembly Parts
Assembly Parts
4. With jam nut on end of spindle thread (to protect threads), gently tap jam nut
toward slinger
side
using a lead or
rubber mallet. The spindle assembly will begin to move out of the spindle housing. Remove jam nut when assembly is
almost out. Spindle assembly consisting of Spindle No. 1, Slinger No. 3 and Bearing No. 4 will come out of housing.
Pulley No. 6 will slide out of housing when spindle assembly is removed. Bearing on jam nut side will slide out of
housing.
5. Replace bearings or belts as necessary.
6. Bearing on blade side is a press fit on spindle. If bearing on the blade side must be replaced, a puller must be used
to disassemble the bearing from the spindle.
7. Press new bearing No. 4 on to spindle, making sure spindle is square to the bore.
8. To re-install spindle in spindle housing, take Spindle
No. 1 (with Slinger No. 3 and Bearing No. 4), and slowly insert into housing.
9. Position Pulley No. 6 in center of housing. Place Key No. 7 in broached keyway in spindle. Position belts around
pulley, through housing. Push spindle through pulley, and through opposite wall of spindle housing.
10. From jam nut side of housing, place Belleville Springs No. 8 into housing. Be careful they are inserted correctly as
shown in diagram.
11. Now, push bearing No. 10 into housing and on spindle, being careful that bearing goes into housing square.
12. Replace jam nut No. 9 on spindle threads. Holding slinger No. 3 in vise, slowly tighten jam nut. This will cause
bearing to slowly push into housing. Tighten thoroughly until bearing bottoms out on shoulder of spindle.
13. Tighten set screws in pulley.
14. The face of Slinger No. 3 must be checked with a dial indicator to make sure it is running true. If it is not, it should
be refaced. To reface, use the side of a surface grinding wheel. Dress the face of the slinger by rotating spindle in
bearings slowly against the direction of the grinding wheel.
15. Replace housing on spindle Slide (P/N 70A04) with four hex cap screws.
16. Place belts around motor pulley and tighten.

-17-
Right Side Shown,
Left Opposite

-18-
DMC70 Top Plate Assembly
Top View

-19-
DMC70 Top Plate Assembly
Bottom View

-20-
DMC70 Plates Assembly
Parts List
This manual suits for next models
1
Table of contents
Other CTD Saw manuals
Popular Saw manuals by other brands
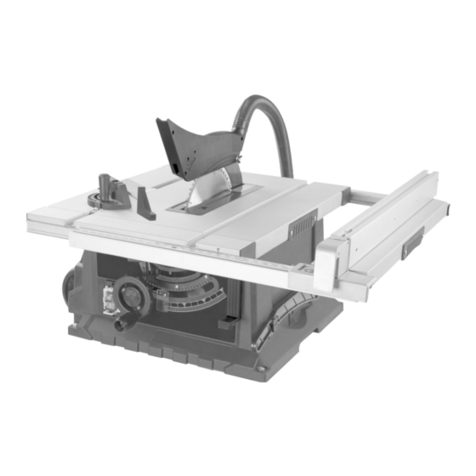
Red Stone
Red Stone 3901314940 Translation from the original instruction manual
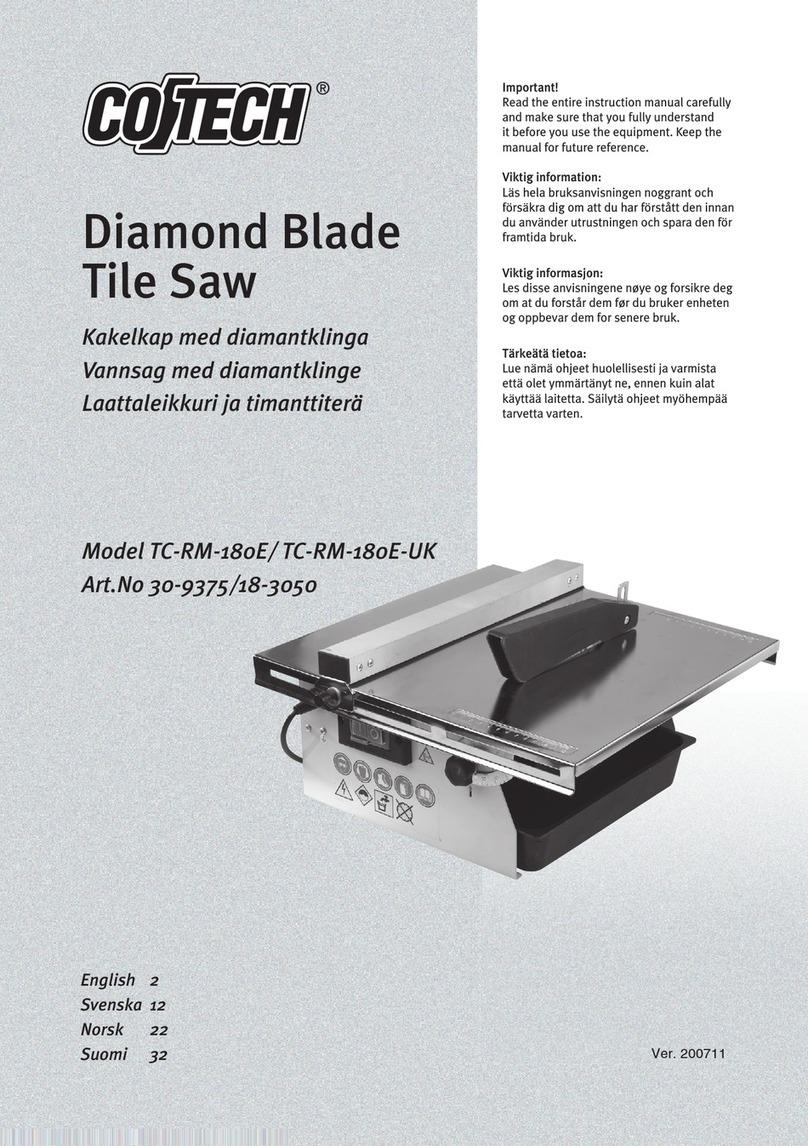
CO/Tech
CO/Tech TC-RM-180E instruction manual

woodmizer
woodmizer LT35 Safety, Setup, Operation & Maintenance Manual

Cosen
Cosen SH-700DM instruction manual
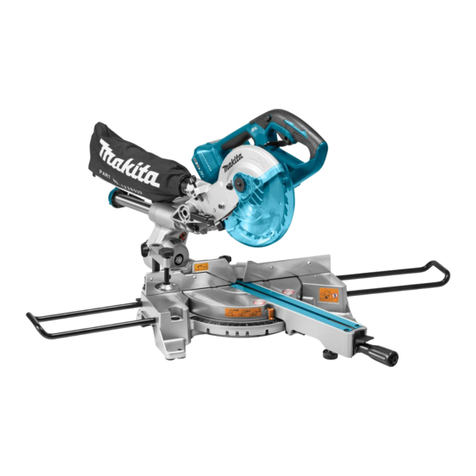
Makita
Makita DLS714 instruction manual
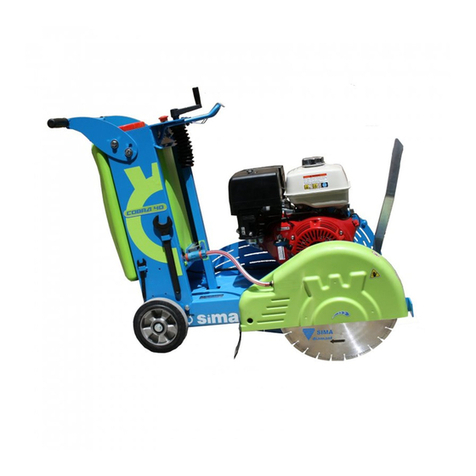
Sima
Sima COBRA-40 Original user guide