CustomCrimp BE Series User manual

1Page
BE SERIES ELECTRONIC TEST BENCH
OPERATORS MANUAL

2Page
BE 3000 ELECTRONIC MANUAL (Rev 8/5/2010)
SAFETY PRECAUTIONS
READ INSTRUCTIONS AND IDENTIFY ALL COMPONENT PARTS
BEFORE OPERATING BENCH
TEST BENCH PRODUCES EXTREMELY HIGH PRESSURE. USE
CAUTION WHEN OPERATING
KEEP HANDS AWAY FROM PINCH POINTS
CONSULT HOSE AND FITTING MANUFACTURER’S SPECIFICA-
TIONS FOR CORRECT TESTING PROCEDURE
ALWAYS WEAR EYE PROTECTION
BE SeriesTest Bench models available:
BE1500 Series: 1500 bar (21,500psi)
BE2500 Series: 2500 bar (37,500psi)
BE3500 Series: 3500 bar (50,000psi)
Operation is similar for all models with the exception of the maximum pressure.
For Parts and Service, Contact:
Custom Machining Services, Inc.
Valparaiso, In 46383
(219) 462-6128

3Page
TEST BENCH PARTS IDENTIFICATION
EMERGENCY STOP
WATER PRESSURE
GAGE
LIGHT SWITCH
PAPER TAPE RECORD
OUTPUT
AIR PRESSURE GAGE
SYSTEM PRESSURE
REGULATOR
WATER DRAIN
VALVE
AIR INLET (80 PSI MIN)
HIGH PRESSURE
MANIFOLD
CONTROL PANEL
WATER INLET
110V ELECTRICAL
CONNECTION
PRINTER CONNECTION
LIGHT CONNECTION
ELECTRICAL INTER-
LOCK SWITCH
110V POWER IN
AIR INLET FILTER
AND LUBRICATOR

4Page
TEST BENCH CONNECTION/OPERATION
TEST BENCH CONNECTIONS
Connect a water supply hose to the water inlet connection which is located at the rear of the control
cabinet.
Connect a water drain hose to the water drain connection located at the rear of the test bench. Run the
drain line to an appropriate drainage area.
Connect an air supply (80 psi Min) to the air inlet/filter, and make certain that the lubricator is filled with
oil. This must be checked periodically to assure proper operation of the pump.
Note: for optimum performance an air supply of 28 SCFM is recommended.
Plug the electrical cord into a standard 110VAC outlet.
TEST BENCH OPERATION
Prior to operating bench, make sure that pressure regulator knob is
adjusted all the way out (counterclockwise).
Follow the screen prompts to input test parameters.
Raise the tank lid and connect hose to be tested to the high
pressure manifold.
Note: The manifold port threads are a special high-pressure coned
configuration that only accepts the proper mating fittings. (Adapters
are available to connect various thread sizes to the manifold.)
Secure the supplied plugs in unused manifold ports.
It is recommended that a high pressure bleed valve be installed on
the free end of the hose for purging air out of the lines.
Open the bleed valve and fill the hose with water.
Close the bleed valve when the hose is filled with water.
Place supplied rubber safety mat over hose.
Lower tank lid and make sure latch engages to ensure it is fully
closed.
Adjust the air pressure regulator such that the maximum test pressure can be achieved. If the air
pressure is set to a higher pressure than required to achieve the hose test pressure there is a danger that
the pump may overshoot the test pressure.
Follow screen prompts to set up and start actual tests.
When the test cycle is complete, disconnect the hose and drain the remaining water from the hos

5Page
TEST PROCEDURE
After the system initializes and
loads, the “Begin Test” screen
will appear.
Press New Test to initiate a test
or Repeat Test to repeat the
previous test.
Press the pressure button to
bring up the pressure adjust-
ment keypad screen.
Enter the max test pressure.
Keypads will pop up for set-
tings not indicated by arrows as
shown on the next screen.
Set the time for the hose to be
held at test pressure. Enter the minimum pressure
allowed during the test cycle.
Enter the number of times that
the test is to be run. Enter the delay time between
test cycles. Review test parameters prior to
running test.
If test parameters and test
setup is correct, start test. Test progress is shown. Test results are shown and the
print option is available.

6Page
DATA LOG OPTION
From the main screen, select
Options. Select More from the Options
menu. Select Data Log from the
second Options screen.
Following instructions on the
screen, Install Flash Drive. Press Start Transfer once the
unit is ready. (Screen will flash
briefly)
Select Remove USB once
transfer completes. Exit and
remove Flash Drive from control
panel.
Log files will be saved on USB drive. Using a computer, locate the
EA_LogCopy folder to view data. A separate file will be saved and
labeled for each day. Information is most compatible with a program
like Microsoft Excel. Test results will be stored and formatted as
shown above.

7Page
INFORMATIONAL TEST SCREENS
There are informational, adjustment and warning screens programmed into the software. While most are self
explanatory, a brief description is given below.
If the test does not complete
satisfactorily, the Hose Failed
screen will appear.
This screen details the cause of
the failed test. Test cycle was unable to finish
due to pressure leaks.
Emergency stop is depressed. Test bench lid is not properly
closed and latched. From the Main Menu Options
screen, default parameters can
be set.
Access to the memory table and
adjustments to the print tape
can be found here.

8Page
Warranty
CustomCrimp “No-Nonsense” Warranty Statement
All CustomCrimp Products are warranted to be free of defects in workmanship and
materials for one year from the date of installation. This warranty ends when the product
becomes unusable for reasons other than defects in workmanship or material.
Any CustomCrimp Product proven to be defective in workmanship or material will be
repaired or replaced at no charge. To obtain benefits of this warranty, first, contact
Warranty Repair Department at Custom Machining Services at (219) 462-6128 and then
deliver via prepaid transportation the complete hydraulic product to:
ATTN: WARRANTY REPAIR DEPT.
Custom Machining Services, Inc.
326 North Co. Rd 400 East
Valparaiso IN 46383
If any product or part manufactured by CustomCrimp is found to be defective by
CustomCrimp, at its option, CustomCrimp will either repair or replace the defective part
or product and return via ground transportation, freight prepaid. Custom Crimp will not
cover any incoming or outgoing freight charges for machines sold outside The
United States.
This warranty does not cover any product or part which is worn out, abused, altered,
used for a purpose other than for which it was intended, or used in a manner which was
inconsistent with any instructions regarding its use.
Electric motors are separately warranted by their manufacturer under the conditions stated
in their separate warranty.
This manual suits for next models
3
Table of contents
Popular Tools Storage manuals by other brands
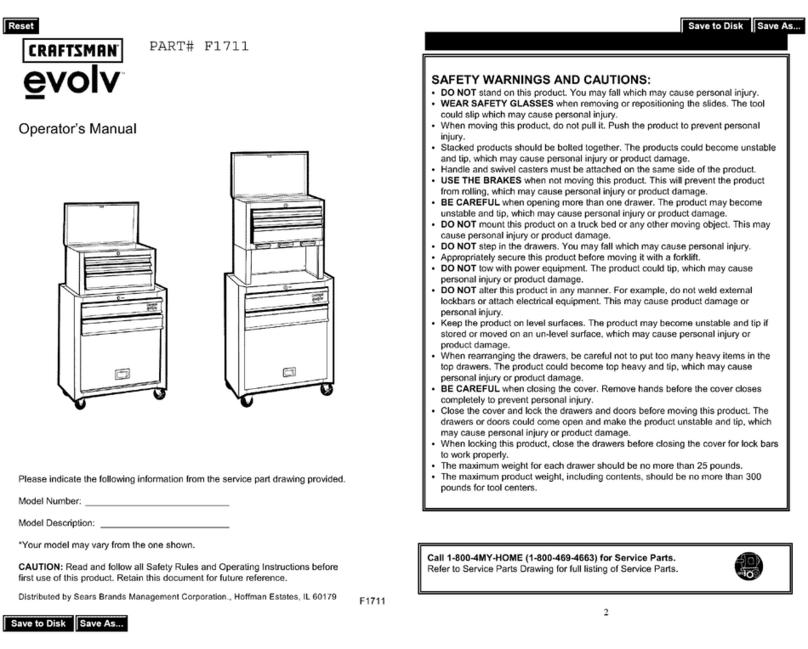
Craftsman
Craftsman evolv F1711 Operator's manual
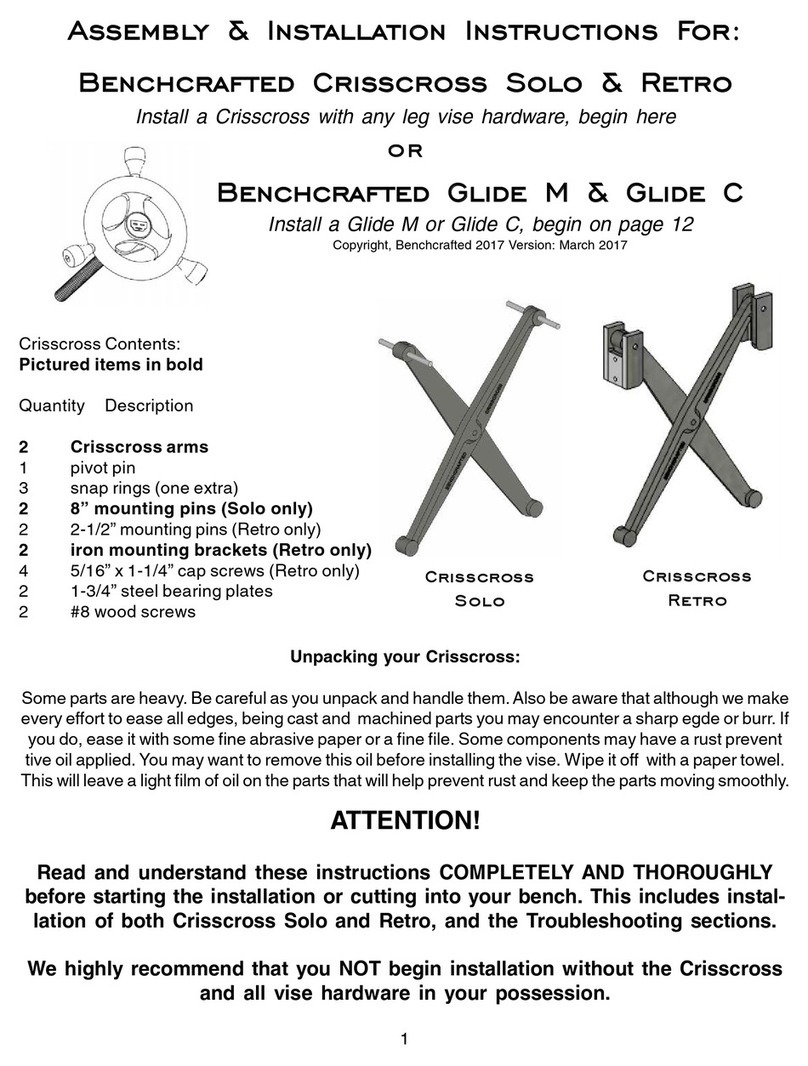
Benchcrafted
Benchcrafted Crisscross Retro Assembly and installation instructions

Seville Classics
Seville Classics UltraHD 20191 Assembly instructions
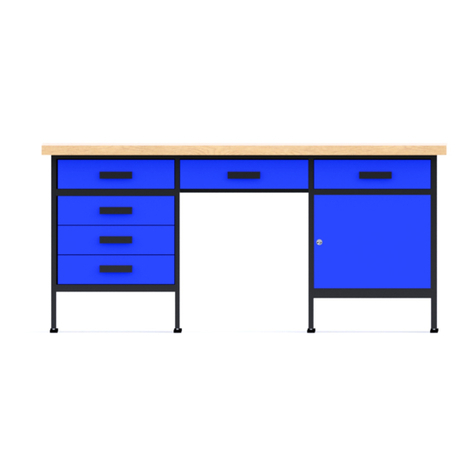
kupper
kupper 12570 Assembly instructions
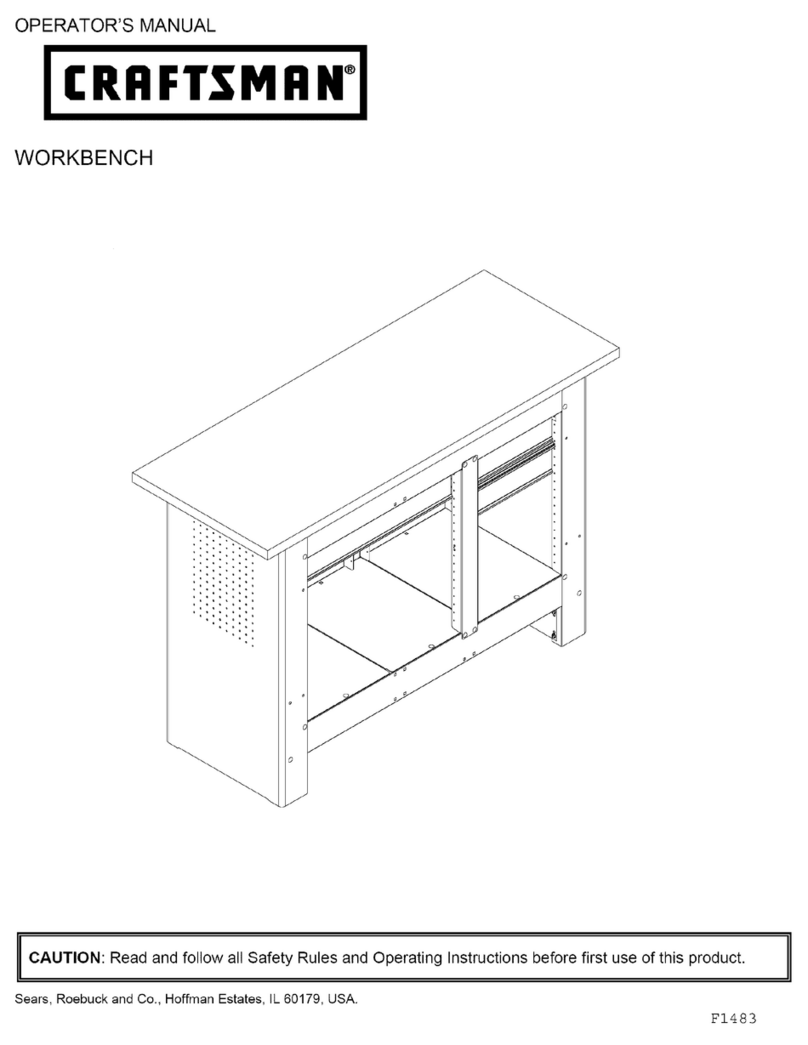
Craftsman
Craftsman Workbench Operator's manual
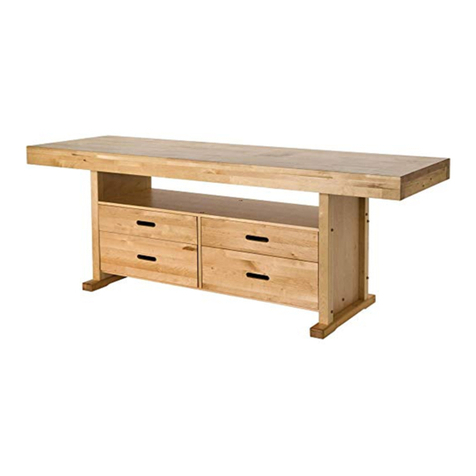
Grizzly
Grizzly T25091 instructions