Cutler-Hammer Digitrip 3000 Programming manual

I.B. 17555
Effective 03/97
Cutler-Hammer
Instructions for Installation, Operation and Maintenance
of the Cutler-Hammer Digitrip 3000 Protective Relay

I.B. 17555 Page iii
Effective 03/97
TABLE OF CONTENTS
PAGE
SECTION 1 INTRODUCTION . . . . . . . . . . . . . . . . . . . . . . . . . . . . . . . . . . . . . . . . . . . . . . . . . . . . . . . . . . . . . . . . . 1
1-1 Preliminary Comments and Safety Precautions..................................................................................................1
1-1.1 Warranty and Liability Information..........................................................................................................1
1-1.2 Safety Precautions.................................................................................................................................1
1-2 General Information.............................................................................................................................................1
1-3 Functions/Features/Options................................................................................................................................2
1-4 Standards............................................................................................................................................................5
SECTION 2 FUNCTIONAL DESCRIPTION . . . . . . . . . . . . . . . . . . . . . . . . . . . . . . . . . . . . . . . . . . . . . . . . . . . . . . 6
2-1 Protection, Testing and Communication Capabilities..........................................................................................6
2-1.1 RMS Sensing .........................................................................................................................................6
2-1.2 Pickup Setting ........................................................................................................................................6
2-1.3 Time Setting ...........................................................................................................................................6
2-1.4 Protection Curve Settings.......................................................................................................................6
2-1.5 Integral Testing.....................................................................................................................................10
2-1.6 Communications...................................................................................................................................10
2-2 Protective Relay Hardware................................................................................................................................11
2-2.1 Front Operations Panel........................................................................................................................11
2-2.2 Rear Access Panel...............................................................................................................................14
2-2.3 External Hardware................................................................................................................................16
2-3 UL Testing and Specification Summary............................................................................................................16
SECTION 3 OPERATION . . . . . . . . . . . . . . . . . . . . . . . . . . . . . . . . . . . . . . . . . . . . . . . . . . . . . . . . . . . . . . . . . . . 18
3-1 Introduction........................................................................................................................................................18
3-2 Power-Up and Self Testing ...............................................................................................................................18
3-3 Panel Operations...............................................................................................................................................18
3-3.1 Characteristic Curve.............................................................................................................................18
3-3.2 Program Mode......................................................................................................................................24
3-3.3 Programming Overview........................................................................................................................26
3-3.4 Test Mode ............................................................................................................................................27
3-4 Communications Function.................................................................................................................................27
SECTION 4 APPLICATION CONSIDERATIONS . . . . . . . . . . . . . . . . . . . . . . . . . . . . . . . . . . . . . . . . . . . . . . . . . 31
4-1 Zone Interlocking Capabilities...........................................................................................................................31
SECTION 5 INSTALLATION, STARTUP AND TESTING . . . . . . . . . . . . . . . . . . . . . . . . . . . . . . . . . . . . . . . . . . . 34
5-1 Introduction........................................................................................................................................................34
5-2 Panel Preparation..............................................................................................................................................34
5-2.1 Cutout...................................................................................................................................................34
5-2.2 Mounting...............................................................................................................................................34

I.B. 17555
Page iv
Effective 03/97
PAGE
5-3 Replacing Digitrip MV with Digitrip 3000...........................................................................................................34
5-4 Wiring................................................................................................................................................................35
5-5 Initial Startup .....................................................................................................................................................35
5-5.1 Before Power Application.....................................................................................................................35
5-5.2 Initial Power Application.......................................................................................................................36
5-6 Miscellaneous Testing.......................................................................................................................................36
SECTION 6 MAINTENANCE AND STORAGE . . . . . . . . . . . . . . . . . . . . . . . . . . . . . . . . . . . . . . . . . . . . . . . . . . . 37
6-1 General .............................................................................................................................................................37
6-1.1 Storage.................................................................................................................................................37
6-2 Troubleshooting Guide (Table 6-1) ...................................................................................................................37
6-3 Replacement.....................................................................................................................................................37
SECTION 7 TIME CURRENT CURVES . . . . . . . . . . . . . . . . . . . . . . . . . . . . . . . . . . . . . . . . . . . . . . . . . . . . . . . . . 40
7-1 Digitrip 3000 Inverse Time Overcurrent Curves................................................................................................40
7-2 Digitrip 3000 Curve Equations...........................................................................................................................60

I.B. 17555 Page v
Effective 03/97
FIGURES
Figure Title Page
1-1 Digitrip 3000 Protective Relay (Front View)...............................................................................................1
1-2 Digitrip 3000 Protective Relay (Rear and Side Views) ..............................................................................2
1-3 A Digitrip 3000 Protective Relay Installed on a Metal Assembly Panel with a DP-4000 ...........................3
1-4 Digitrip 3000 Protective Relay with DIP Switches Shown in Upper Left (Rear View)................................3
1-5 Digitrip 3000 Curve Shape Possibilities.....................................................................................................4
1-6 Installed Jumpers in Place on Terminal Block TB-1 Disabling the
Zone Interlocking Feature..........................................................................................................................5
2-1 Typical Communications Wiring Diagram................................................................................................12
3-1 Digitrip 3000 Typical Wiring Diagram ......................................................................................................19
3-2 Digitrip 3000 Time-Current Characteristic Curves...................................................................................20
3-3 Sample Electronic Curves .......................................................................................................................21
3-4 Typical Inverse Time Overcurrent Pickup Horizontal Movement.............................................................21
3-5 Typical Time Multiplier Adjustment (I2T Response).................................................................................22
3-6 Short Delay Setting Adjustment...............................................................................................................22
3-7 Short Delay Time Adjustment..................................................................................................................22
3-8 Typical is Curve with I2T Slope................................................................................................................23
3-9 Instantaneous Setting Adjustment...........................................................................................................23
3-10 Programming Sequence Preview............................................................................................................26
3-11 Local Programming Sequence Flow Chart..............................................................................................28
4-1 Connection Diagram for Typical Phase Zone Selective Interlocking.......................................................32
4-2 Connection Diagram for Typical Ground Zone Selective Interlocking.....................................................33
5-1 Cutout Dimensions (Inches) ....................................................................................................................34
5-2 Digitrip 3000 Protective Relay Dimensions (Inches)................................................................................35
7-1 Inverse Time Overcurrent Phase, I4T Curves (SC-5390-92B) ................................................................41
7-2 Inverse Time Overcurrent Phase, I2T Curves (SC-5391-92B) ................................................................42
7-3 Inverse Time Overcurrent Phase, IT Curves (SC-5392-92B)..................................................................43
7-4 Inverse Time Overcurrent Phase, Flat Curves (SC-5393-92B)...............................................................44
7-5 Short Delay Phase Curves (SC-5394-92B).............................................................................................45
7-6 Inverse Time Overcurrent/Short Delay Curves (SC-5395-92B)...............................................................46
7-7 Instantaneous Curves (SC-5396-92B).....................................................................................................47
7-8 Inverse Time Overcurrent Ground, I4T Curves (SC-5399-92B)...............................................................48
7-9 Inverse Time Overcurrent Ground, I2T Curves (SC-5400-92B)...............................................................49
7-10 Inverse Time Overcurrent Ground, IT Curves (SC-5401-92B)................................................................50
7-11 Inverse Time Overcurrent Ground, Flat Curves (SC-5402-92B) .............................................................51
7-12 Short Delay Ground Curves (SC-5403-92B) ...........................................................................................52
7-13 ANSI Moderately Inverse Curves (SC-6685-96)......................................................................................53
7-14 ANSI Very Inverse Curves (SC-6686-96)................................................................................................54
7-15 ANSI Extremely Inverse Curves (SC-6687-96) .......................................................................................55
7-16 IEC-A Moderately Inverse Curves (SC-6688-96) ....................................................................................56
7-17 IEC-B Very Inverse Curves (SC-6689-96)...............................................................................................57
7-18 IEC-C Extremely Inverse Curves (SC-6690-96)......................................................................................58
7-19 IEC-D Flat Curves (SC-6691-96).............................................................................................................59

I.B. 17555
Page vi
Effective 03/97
TABLES
Table Title Page
2.1 Curve Selection .........................................................................................................................................6
2.2 Characteristic for Phase Element..............................................................................................................7
2.3 Characteristic for Ground Element ............................................................................................................8
2.4 Miscellaneous Settings..............................................................................................................................9
2.5 Factory Set Defaults................................................................................................................................10
3.1 Digitrip 3000 Curve Shapes.....................................................................................................................18
3.2 Digitrip 3000 Display Messages ..............................................................................................................30
5.1 Digitrip 3000 Dip Switch Settings.............................................................................................................36
6.1 Troubleshooting Guide ............................................................................................................................38

I.B. 17555 Page 1
Effective 03/97
SECTION 1: INTRODUCTION
1-1 PRELIMINARY COMMENTS AND SAFETY PRE-
CAUTIONS
This technical document is intended to cover most
aspects associated with the installation, application,
operation and maintenance of the Cutler-Hammer
Digitrip 3000 Protective Relay. This document is provid-
ed as a guide for authorized and qualified personnel
only in the selection and application of the Digitrip 3000
Protective Relay. Please refer to the specific WARNING
and CAUTION in Section 1-1.2 before proceeding. If fur-
ther information is required by the purchaser regarding a
particular installation, application or maintenance activi-
ty, a Cutler-Hammer representative should be contact-
ed.
1-1.1 WARRANTY AND LIABILITY INFORMATION
NO WARRANTIES, EXPRESSED OR IMPLIED,
INCLUDING WARRANTIES OF FITNESS FOR A PAR-
TICULAR PURPOSE OF MERCHANTABILITY, OR
WARRANTIES ARISING FROM COURSE OF DEAL-
ING OR USAGE OF TRADE, ARE MADE REGARDING
THE INFORMATION, RECOMMENDATIONS AND
DESCRIPTIONS CONTAINED HEREIN. In no event will
Cutler-Hammer be responsible to the purchaser or user
in contract, in tort (including negligence), strict liability or
otherwise for any special, indirect, incidental or conse-
quential damage or loss whatsoever, including but not
limited to damage or loss of use of equipment, plant or
power system, cost of capital, loss of power, additional
expenses in the use of existing power facilities, or
claims against the purchaser or user by its customers
resulting from the use of the information and descrip-
tions contained herein.
1-1.2 SAFETY PRECAUTIONS
All safety codes, safety standards and/or regulations
must be strictly observed in the installation, operation
and maintenance of this device.
THE WARNINGS AND CAUTIONS INCLUDED AS
PART OF THE PROCEDURAL STEPS IN THIS DOCU-
MENT ARE FOR PERSONNEL SAFETY AND PRO-
TECTION OF EQUIPMENT FROM DAMAGE. AN
EXAMPLE OF A TYPICAL WARNING LABEL HEAD-
ING IS SHOWN ABOVE TO FAMILIARIZE PERSON-
NEL WITH THE STYLE OF PRESENTATION. THIS
WILL HELP TO INSURE THAT PERSONNEL ARE
ALERT TO WARNINGS, WHICH MAY APPEAR
THROUGHOUT THE DOCUMENT. IN ADDITION,
CAUTIONS ARE ALL UPPER CASE AND BOLDFACE.
COMPLETELY READ AND UNDERSTAND THE
MATERIAL PRESENTED IN THIS DOCUMENT
BEFORE ATTEMPTING INSTALLATION, OPERATION
OR APPLICATION OF THE EQUIPMENT. IN ADDI-
TION, ONLY QUALIFIED PERSONS SHOULD BE
PERMITTED TO PERFORM ANY WORK ASSOCIAT-
ED WITH THE EQUIPMENT. ANY WIRING INSTRUC-
TIONS PRESENTED IN THIS DOCUMENT MUST BE
FOLLOWED PRECISELY. FAILURE TO DO SO
COULD CAUSE PERMANENT EQUIPMENT DAMAGE.
1-2 GENERAL INFORMATION
The Digitrip 3000 Protective Relay is a panel mounted
multi-function, microprocessor based overcurrent relay,
designed for both ANSI and IEC applications (Figures 1-
1and 1-2). It is a self-contained device which operates
!
CAUTION
!
WARNING
Figure 1-1 Digitrip 3000 Protective Relay (Front View)

I.B. 17555
Page 2
Effective 03/97
from either AC or DC control power, and provides true
RMS sensing of each phase and ground current. Only
one relay is required per three-phase circuit. Current
monitoring and operator selectable protective functions
are integral to each device.
THE LOSS OF CONTROL VOLTAGE WILL CAUSE
THE DIGITRIP 3000 TO BE INOPERATIVE. IF AC
CONTROL VOLTAGE IS USED, AN APPROPRIATE
RELIABLE POWER SOURCE/SCHEME SHOULD BE
SELECTED (POSSIBLY A UPS SYSTEM) TO SUPPLY
POWER TO THE RELAY.
The Digitrip 3000 Protective Relay provides protection
for most types of medium voltage electrical power distri-
bution systems. It was designed for use with Cutler-
Hammer Type VCP-W vacuum circuit breakers, as well
as other manufacturers’ medium and high voltage circuit
breakers (Figure 1-3). Digitrip 3000 Protective Relays
are compatible for use with all circuit breakers utilizing a
shunt trip coil. Thermal curves, plus ANSI and IEC
inverse time overcurrent curves provide close coordina-
tion with both downstream and upstream protective
devices. One Digitrip 3000 Protective Relay replaces
the normal complement of three or four conventional
electro-mechanical overcurrent relays, an ammeter, a
demand ammeter, an ammeter switch, and, in some sit-
uations, a lockout relay switch (device 86). All Digitrip
3000 Protective Relays include a built-in INCOM com-
munication capability compatible with the Cutler-
Hammer IMPACC system.
1-3 FUNCTIONS/FEATURES/OPTIONS
The primary function of the Digitrip 3000 Protective
Relay is overcurrent protection. This is achieved by ana-
lyzing the secondary current signals received from the
switch-gear current transformers. When predetermined
current levels and time delay settings are exceeded, the
closing of trip contact(s) is used to initiate breaker trip-
ping.
The Digitrip 3000 Protective Relay operates from the
secondary output of standard switchgear current trans-
formers rated at In= 5 amperes. It is operator configured
Figure 1-2 Digitrip 3000 Protective Relay (Rear and Side Views)
!
CAUTION

I.B. 17555 Page 3
Effective 03/97
Figure 1-3 A Digitrip 3000 Protective Relay (right)
Installed on a Metal Assembly Panel with a DP-4000 (left) Figure 1-4 Digitrip 3000 Protective Relay with DIP
Switches Shown in Upper Left (Rear View)
to fit specific distribution system requirements. The cur-
rent transformer ratio information is programmed into
Digitrip 3000 by setting pushbuttons located on the face-
plate of the relay. The phase and ground CT ratios can
be independently programmed over a range of 5:5 to
5000:5. Refer to Table 2.4 for all available CT ratio set-
tings.
Protective functions are also configured by using the
pushbuttons on the faceplate of the relay. These protec-
tive functions can be programmed with the circuit break-
er in the open or closed position. DIP Switch S2, located
on the rear of the relay, is used to control closed breaker
setting ability (Figure 1-4). Refer to paragraph 2-2.2 and
Table 5.1 for additional information. Inverse time over-
current protection for the phase element cannot be dis-
abled. This insures that all phase protection cannot be
disabled. The relay also automatically exits the program
mode, if there is no programming activity for 2-1/2 min-
utes. Programming and test mode security is provided by
a sealable, hinged access cover on the front of the relay.
Direct reading displays indicate the value currently being
considered, while multi-colored LEDs indicate opera-
tional conditions and specific functions (Figure 1-1).
In addition to performing a continuous self-testing of
internal circuitry as a part of normal operation, all
Digitrip 3000 Protective Relays include a front accessi-
ble, integral field testing capability. In the integral test
mode, a test current simulates an overload or short cir-
cuit condition, to check that all tripping features are
functioning properly. The test function is user selectable
to trip or not trip the breaker. Refer to Paragraph 2-1.5
for additional information.
The Digitrip 3000 Protective Relay provides five protec-
tive functions for both phase and ground protection. The
ground element is capable of a residual, an external
source ground or a zero sequence connection. If ground
protection is not desired, the ground element does not
have to be connected.
The five protective settings are:
• Inverse Time Overcurrent Pickup
• Inverse Time Overcurrent Time Multiplier
• Short Delay Pickup
• Short Delay Time
• Instantaneous Pickup
Each of the protective functions are independently pro-
grammed for various combinations to fit specific system
requirements. For protective functions not required, the
relay will allow all of the protective functions on ground

I.B. 17555
Page 4
Effective 03/97
and all but the inverse time overcurrent function on
phase to be disabled. When the Digitrip 3000 is not set
for an instantaneous trip function, a true making current
release (discriminator) is available. If not desired, the
discriminator can be disabled.
Digitrip 3000 Protective Relays provide greater selective
coordination potential by providing 11 different curve
shapes (Figure 1-5).
• Thermal Curves (4 shapes
)
- It
- I2t
- I4t
- Flat
• ANSI Curves (3 shapes per ANSI C37.112)
- Moderately Inverse
- Very Inverse
- Extremely Inverse
• IEC Curves (4 shapes per IEC 255-3)
- IEC-A (Moderately Inverse)
- IEC-B (Very Inverse)
- IEC-C (Extremely Inverse)
- IEC-D (Definite Time)
The ground element of Digitrip 3000 can have a curve
shape independent of the phase element, providing for
a more versatile ground protection.
With this vast selection of Curve Shapes, Digitrip 3000
provides protection capable of coordinating with most
any existing electro-mechanical overcurrent relay or
power fuse.
A pictorial representation of characteristic curve shapes
is provided on the face of the relay for reference purpos-
es (Figure 1-1).
All Digitrip 3000 Protective Relays have zone selective
interlocking capabilities for phase and ground fault pro-
tection. Zone selective interlocking is a means by which
two or more coordinated trip devices can communicate
to alter their pre-set tripping modes to provide a faster
response for certain upstream fault conditions. The relay
is shipped with the zone selective interlocking feature
disabled by the use of the two jumpers on the rear
mounted terminal strip TB1(Figure 1-6).
Digitrip 3000 Protective Relays operating parameters
and troubleshooting information are displayed on the
front of the relay, via the two display windows. This is
considered “ON DEVICE” information. In addition, all
relay information can be transmitted to a remote location
via the built-in INCOM communication system. This type
of information is referred to as “COMMUNICATED
INFORMATION.” In addition to being able to provide a
circuit breaker “OPEN” or “CLOSED” status to the
remote location, the Digitrip 3000 displays and remotely
transmits parameters, such as:
Figure 1-5 Digitrip 3000 Curve Shape Possibilities
TIME
CURRENT
I4t
I2t
It
FLAT
(Curve Shape)
(Short Delay)
(Instantaneous)
TIME
CURRENT
(Curve Shape)
(Short Delay)
(Instantaneous)
XTRM
VERY
MOD
TIME
CURRENT
IEC-C IEC-B
IEC-A
(Curve Shape)
(Short Delay)
(Instantaneous)
IEC-D
Thermal Curves ANSI Curves➀IEC Curves➁
➀
ANSI Curve shapes defined by ANSI C37.112.
➁
IEC Curve shapes defined by IEC 255-3.

I.B. 17555 Page 5
Effective 03/97
• Individual phase currents
• Ground current
• Maximum current for each phase and ground since
last reset (Amp. Demand)
• Magnitude and phase of current causing trip
• Cause of trip
• Current transformer ratio
• Existing setpoint settings
The remote communications capability is made possible
by the Cutler-Hammer Integrated Communications
(INCOM) Chip and Protocol compatible with the
IMPACC Monitor and Control System. The protocol per-
mits a remote master computer to perform:
(1) Interrogation of relay data
(2) Execution of circuit breaker
“Close” and“Trip” commands
(3) “Reset” of the relay after a trip
(4) Downloading of settings
Reliable two-way communications can be provided over
a twisted pair communications network. The Digitrip
3000 Protective Relay is supplied with a built-in commu-
nications capability compatible with the Cutler-Hammer
IMPACC system.
1-4 STANDARDS
Digitrip 3000 Protective Relays are “Component
Recognized” by the Underwriters Laboratory, Inc.®
under UL File E154862. Refer to Section 2-3 UL Testing
and Specification Summary for more information.
Figure 1-6 Installed Jumpers in Place on Terminal
Block TB-1 Disabling the Zone Interlocking Feature

I.B. 17555
Page 6
Effective 03/97
SECTION 2: FUNCTIONAL DESCRIPTION
2-1 PROTECTION, TESTING AND COMMUNICATION
CAPABILITIES
2-1.1 RMS SENSING
Digitrip 3000 Protective Relays provide true RMS sens-
ing for proper correlation with the thermal characteristics
of conductors and equipment. The root mean square
(rms) value is determined by a microprocessor calcula-
tion of discrete sampled points of the current waveform.
This root mean square value is used for the protection
response and metering displays of the relay.
2-1.2 PICKUP SETTING
A Digitrip 3000 Protective Relay pickup setting is a dis-
crete, preselected value of current used to initiate a trip-
ping action. The Digitrip 3000 has several current based
tripping functions:
• Phase inverse time overcurrent tripping - Thermal,
ANSI, and IEC Curves.
• Ground inverse time overcurrent tripping - Thermal,
ANSI, and IEC Curves. Ground selection is indepen-
dent of phase selection.
• Phase and ground short delay tripping.
• Phase and ground instantaneous tripping.
As shown in Figure 3-2, the ANSI and IEC “Curve
Shapes” are in terms of multiples of Ipu (Pickup
Current of the CT Primary), whereas “short delay”
and “instantaneous” are in terms of multiples of In
(5A secondary of CT primary current). The thermal
curve is represented in terms of multiples of Infor its
curve shape, short delay, and instantaneous set-
tings. This must be considered in the coordination
study and in the programming of the Digitrip 3000
Protective Relay.
Example: Thermal Curves, Short Delay and
Instantaneous settings using I
n
CT Rating = In= 1200A.
Pickup Setting = 1.5
Pickup (amps) = (1200)(1.5)
= 1800A.
Example: ANSI and IEC curves using I
pu
CT Rating = 1200A.
Ipu = Pickup Current = 1800A.
CT Ratio = 1200:5
(Entered as “1200”)
Actual secondary current at pickup =
7.5A. = (1800/1200) x 5
2-1.3 TIME SETTING
A Digitrip 3000 Protective Relay time setting is a prese-
lected time delay initiated when a pickup point on the
long or short curve is exceeded. If the current value
drops below the pickup value, the timing function resets.
No memory is provided. If the current value does not
drop below pickup, the amount of delay before tripping
occurs is a function of the current magnitude and the
time setting. The delay can be determined from the
appropriate time-current curves.
2-1.4 PROTECTION CURVE SETTINGS
Curve Selection: Extensive flexibility on inverse time
overcurrent (phase and ground) curve shaping is possi-
ble with eleven available curve types. The selection and
associated result is determined by the type of curve
shape that best fits the coordination requirements
(Figure 1-5, Table 2.1). Different curve shape settings
Table 2.1 Curve Selection
Curve Type Selection Result
Thermal It Moderately Inverse
I2t Inverse
I4t Extremely Inverse
FLAT Definite or Fixed Time
ANSI MOD Moderately Inverse
VERY Very Inverse
XTRM Extremely Inverse
IEC IEC-A Moderately Inverse
IEC-B Very Inverse
IEC-C Extremely Inverse
IEC-D Definite Time
NOTICE

I.B. 17555 Page 7
Effective 03/97
Table 2.2 Characteristic for Phase Element
CURVE SHAPE IT, I2T, I4T, FLAT, MOD, VERY, XTRM,
IECA, IECB, IECC, IECD
INVERSE TIME OVERCURRENT 0.20, 0.25, 0.30, 0.35, 0.40, 0.45, 0.50, + 5%
PICKUP 0.55, 0.60, 0.65, 0.70, 0.75, 0.80, 0.85,
0.90, 0.95, 1.00, 1.10, 1.20, 1.30, 1.40,
1.50, 1.60, 1.70, 1.80, 1.90, 2.00, 2.10,
2.20
INVERSE TIME OVERCURRENT
Curve = IT, I
2
T, I
4
T:
TIME MULTIPLIER 0.20, 0.25, 0.30, 0.35, 0.40, 0.45, 0.50, +10%➀ ➁ IT SC-5392-92B
0.55, 0.60, 0.65, 0.70, 0.75, 0.80, 0.85, I2T SC-5391-92B
0.90, 0.95, 1.00, 1.25, 1.50, 1.75, 2.00, I4T SC-5390-92B
2.25, 2.50, 2.75, 3.00, 3.50, 4.00, 4.50,
5.00, 5.50, 6.00, 6.50, 7.00, 7.50, 8.00,
8.50, 9.00, 10.0, 12.5, 15.0, 17.5, 20.0,
22.5, 25.0, 27.5, 30.0, 35.0, 40.0
Curve = FLAT:
0.20, 0.25, 0.30, 0.35, 0.40, 0.45, 0.50, + 0.05 SEC FLAT
0.55, 0.60, 0.65, 0.70, 0.75, 0.80, 0.85, SC 5393-92B
0.90, 0.95, 1.00, 1.25, 1.50, 1.75, 2.00
Curve = ANSI MOD, VERY, XTRM:
+10%➀ ➂ MOD SC-6685-96
0.1, 0.2, 0.3, 0.4, 0.5, 0.6, 0.7, 0.8, 0.9, VERY SC-6686-96
1.0, 1.1, 1.2, 1.3, 1.4, 1.5, 1.6, 1.7, 1.8, XTRM SC-6687-96
1.9, 2.0, 2.1, 2.2, 2.3, 2.4, 2.5, 2.6, 2.7,
2.8, 2.9, 3.0, 3.1, 3.2, 3.3, 3.4, 3.5, 3.6,
3.7, 3.8, 3.9, 4.0, 4.1, 4.2, 4.3, 4.4, 4.5,
4.6, 4.7, 4.8, 4.9, 5.0
Curve = IECA, IECB, IECC, IECD:
+10%➀ ➂ ➃ IECA SC-6688-96
0.05, 0.10, 0.15, 0.20, 0.25, 0.30, 0.35, IECB SC-6689-96
0.40, 0.45, 0.50, 0.55, 0.60, 0.65, 0.70, IECC SC-6690-96
0.75, 0.80, 0.85, 0.90, 0.95, 1.00 IECD SC-6691-96
SHORT DELAY PICKUP 1.00, 1.25, 1.50, 1.75, 2.00, 2.25, 2.50, + 10% SC-5394-92B
2.75, 3.00, 3.50, 4.00, 4.50, 5.00, 5.50,
6.00, 6.50, 7.00, 7.50, 8.00, 8.50, 9.00,
9.50, 10.0, 11.0, NONE
SHORT DELAY TIME 0.05, 0.10, 0.15, 0.20, 0.25, 0.30, 0.35, + 0.05 SEC SC-5394-92B
(In Seconds) 0.40, 0.45, 0.50, 0.55, 0.60, 0.65, 0.70,
0.75, 0.80, 0.85, 0.90, 0.95, 1.00, 1.25,
1.50
INSTANTANEOUS PICKUP 1.00, 1.25, 1.50, 1.75, 2.00, 2.25, 2.50, + 10% SC-5396-92B
2.75, 3.00, 3.50, 4.00, 4.50, 5.00, 5.50,
6.00, 6.50, 7.00, 7.50, 8.00, 8.50, 9.00,
9.50, 10.0, 12.5, 15.0, 17.5, 20.0, 22.5,
25.0, NONE
DISCRIMINATOR D ON Fixed At 11 x In+ 10%
(If Phase INST set to NONE) D OFF
NOTES: ➀ Curves go to constant operating time above 30 x In.
➁ Tolerance: ± 10% or 0.09 seconds, whichever is larger. Minimum operating trip time is 0.05 seconds.
➂ Tolerance: ± 10% or 0.09 seconds, whichever is larger (>1.5 x Ipu). Minimum trip time is 2 power line cycles.
➃ For IECD, the Time Multiplier Tolerance is ±0.05 seconds.
TYPE SETTING AVAILABLE SETTINGS TOLERANCE CURVE #

I.B. 17555
Page 8
Effective 03/97
CURVE SHAPE IT, I2T, I4T, FLAT, MOD, VERY, XTRM,
IECA, IECB, IECC, IECD
INVERSE TIME OVERCURRENT 0.100, 0.125, 0.150, 0.175, 0.200, 0.225, + 5%
PICKUP 0.250, 0.275, 0.300, 0.350, 0.400, 0.450,
0.500, 0.550, 0.600, 0.650, 0.700, 0.750,
0.800, 0.850, 0.900, 0.950, 1.00, 1.25,
1.50, 1.75, 2.00, NONE
INVERSE TIME OVERCURRENT
Curve = IT, I
2
T, I
4
T:
TIME MULTIPLIER 0.20, 0.25, 0.30, 0.35, 0.40, 0.45, 0.50, 0.55, +10%➀ ➁ ➄ IT SC-5401-92B
0.60, 0.65, 0.70, 0.75, 0.80, 0.85, 0.90, 0.95, I2T SC-5400-92B
Ground Time Multiplier setting options 1.00, 1.25, 1.50, 1.75, 2.00, 2.25, 2.50, 2.75, I4T SC-5399-92B
depend upon Ground Curve setting 3.00, 3.50, 4.00, 4.50, 5.00, 5.50, 6.00, 6.50,
selection. 7.00, 7.50, 8.00, 8.50, 9.00, 10.0, 12.5, 15.0,
17.5, 20.0, 22.5, 25.0, 27.5, 30.0, 35.0, 40.0
Curve = FLAT:
0.20, 0.25, 0.30, 0.35, 0.40, 0.45,0.50, + 0.05 SEC FLAT
0.55, 0.60, 0.65, 0.70, 0.75, 0.80, 0.85, SC-5402-92B
0.90, 0.95, 1.00, 1.25, 1.50, 1.75, 2.00
Curve = ANSI MOD, VERY, XTRM:
+10%➀➂➄ MOD SC-6685-96
0.1, 0.2, 0.3, 0.4, 0.5, 0.6, 0.7, 0.8, 0.9, 1.0, VERY SC-6686-96
1.1, 1.2, 1.3, 1.4, 1.5, 1.6, 1.7, 1.8, 1.9, 2.0, XTRM SC-6687-96
2.1, 2.2, 2.3, 2.4, 2.5, 2.6, 2.7, 2.8, 2.9, 3.0,
3.1, 3.2, 3.3, 3.4, 3.5, 3.6, 3.7, 3.8, 3.9, 4.0,
4.1, 4.2, 4.3, 4.4, 4.5, 4.6, 4.7, 4.8, 4.9, 5.0
Curve = IECA, IECB, IECC, IECD:
+10%➀ ➂ ➃ ➄ IECA SC-6688-96
0.05, 0.10, 0.15, 0.20, 0.25, 0.30, 0.35, IECB SC-6689-96
0.40, 0.45, 0.50, 0.55, 0.60, 0.65, 0.70, IECC SC-6690-96
0.75, 0.80, 0.85, 0.90, 0.95, 1.00 IECD SC-6691-96
SHORT DELAY PICKUP 0.100, 0.125, 0.150, 0.175, 0.200, 0.225, + 10% SC-5403-92B
0.250, 0.275, 0.300, 0.350, 0.400, 0.450,
0.500, 0.550, 0.600, 0.650, 0.700, 0.750,
0.800, 0.850, 0.900, 0.950, 1.00, 1.25,
1.50, 1.75, 2.00, 2.25, 2.50, 2.75, 3.00,
3.50, 4.00, 4.50, 5.00, 5.50, 6.00, 6.50,
7.00, 7.50, 8.00, 8.50, 9.00, 9.50, 10.0,
11.0, NONE
SHORT DELAY TIME 0.05, 0.10, 0.15, 0.20, 0.25, 0.30, 0.35, + 0.05 SEC SC-5403-92B
(In Seconds) 0.40, 0.45, 0.50, 0.55, 0.60, 0.65, 0.70,
0.75, 0.80, 0.85, 0.90, 0.95, 1.00, 1.25,
1.50
INSTANTANEOUS PICKUP 0.50, 0.55, 0.60, 0.65, 0.70, 0.75, 0.80, + 10% SC-5396-92B
0.85,0.90, 0.95, 1.00, 1.25, 1.50, 1.75,
2.00, 2.25, 2.50, 2.75, 3.00, 3.50, 4.00,
4.50, 5.00, 5.50, 6.00, 6.50, 7.00, 8.00,
8.50, 9.00, 9.50, 10.0, 11.0, NONE
Table 2.3 Characteristic for Ground Element
TYPE SETTING AVAILABLE SETTINGS TOLERANCE CURVE #
NOTES: ➀ Curves go to constant operating time above 30 x In.
➁ Tolerance: ± 10% or 0.09 seconds, whichever is larger. Minimum operating trip time is 0.05 seconds.
➂ Tolerance: ± 10% or 0.09 seconds, whichever is larger (>1.5 x Ipu). Minimum trip time is 2 power line cycles.
➃ For IECD, the Time Multiplier Tolerance is ±0.05 seconds.
➄ For Ground Pickup ≤0.2pu: trip time tolerance is ±15%.

I.B. 17555 Page 9
Effective 03/97
can be applied to phase and ground to maximize coordi-
nation flexibility. The curves are discussed in more
detail in paragraph 3-3.1.
Phase Inverse Time Overcurrent Pickup: The avail-
able pickup settings, shown in Table 2.2, range from
0.20 to 2.2 times (In).
Phase Inverse Time Overcurrent Time Multiplier:
The available time settings, shown in Table 2.2, depend
on the curve shape selected. For the thermal curves,
the settings represent relay operating times at a current
value equal to 3 times (In). For ANSI and IEC curves,
the settings represent the relay’s time multiplier for the
current value equal to I/Ipu.
Phase Short Delay Pickup: The available pickup set-
tings, shown in Table 2.2, range from 1 to 11 times (In)
or NONE. If NONE is selected, the short delay protec-
tive function is disabled.
Phase Short Delay Time: The available time settings,
shown in Table 2.2, range from 0.05 to 1.5 seconds at
currents equal to or above the short delay pickup setting
selected. If NONE was selected for the Phase Short
Delay Pickup Setting, the relay will bypass requesting
the time setting.
Phase Instantaneous: The available pickup settings,
shown in Table 2.2, range from 1 to 25 times (In) or
NONE. If NONE is selected, the instantaneous protec-
tive function is disabled and a choice of whether to turn
the discriminator option on (DON) or off (DOFF) is
offered. The discriminator is a true making current
release. When the circuit breaker closes, the discrimina-
tor function, if selected to be on, is functional in an
instantaneous trip mode for 10 cycles after the breaker
closes. The breaker will trip instantaneously via the dis-
criminator, if the fault current is above 11 times (In).
After the 10 cycle period has passed, the discriminator
will no longer be functional. It becomes functional again
only when the breaker opens and then is reclosed.
Ground Fault: After the phase instantaneous setting is
established, the ground curve shape, the ground inverse
time overcurrent pickup, ground inverse time overcur-
rent time, ground short delay pickup, ground short delay
time and ground instantaneous settings are selected.
The available settings are shown in Table 2.3. Note that
the ground curve settings are independent of the phase
curve and are programmed separately.
Programming the ground settings is done in the same
manner as the phase settings, except there is no dis-
criminator option for ground instantaneous, and there is
a NONE selection for the inverse time overcurrent pick-
up setting.
High Load: The available high load time-out settings
are shown in Table 2.4. At a current 85% or above the
HIGHLOAD TIME 0 Sec, 5 Sec, 10 Sec, 30 Sec, 1 min, 2 min, 5 min,
(pickup fixed @ 0.85 X Phase
Time Overcurrent Setting)
FREQUENCY 50 Hz, 60 Hz
PHASE CT RATIO 5, 10, 25, 50, 75, 100, 150, 200, 250, 300, 400, 500, 600, 630,
800, 1000, 1200, 1250, 1500, 1600, 2000, 2400, 2500, 3000,
3200, 4000, 5000
GROUND CT RATIO 5, 10, 25, 50, 75, 100, 150, 200, 250, 300, 400, 500, 600, 630,
800, 1000, 1200, 1250, 1500, 1600, 2000, 2400, 2500, 3000,
3200, 4000, 5000
TEST Phase ...........................................................................P1, P2, P3, P4, P5, P6, P7, P8, P9, P10, P12, P14, P16
P18, P20, P22, P25
Phase Trip....................................................................P3T, P10T, P25T
Ground..........................................................................G.1, G.2, G.3, G.4, G.5, G.6, G.7, G.8, G.9, G1, G2, G3, G4
G5, G6, G8, G10
Ground Trip ..................................................................G1T, G3T, G10T
TYPE SETTING AVAILABLE SETTINGS
Table 2.4 Miscellaneous Settings

I.B. 17555
Page 10
Effective 03/97
inverse time overcurrent phase setting value, the high
load function will begin timing to the time setting select-
ed and the High Load LED will blink. If the current drops
below the 85% value, the high load timer will reset, and
only start again when the 85% value is again reached.
When the high load timer times out, the “High Load”
LED on the front of the relay lights continuously and an
alarm signal is sent over the communication network.
System Frequency Selection: Either 60Hz or 50Hz
may be selected (Table 2.4).
Phase and Ground CT Ratio Selection: The available
CT ratio’s, shown in Table 2.4, range from 5:5 to
5000:5.
Defaults: In the unlikely event of missing or invalid set-
tings, the Operational LED will blink Red instead of
Green and the relay will display “PRGM” in the Settings
Display window. This means that the program of set-
tings should be re-entered and saved.
2-1.5 INTEGRAL TESTING
Digitrip 3000 Protective Relays have a front accessible,
integral field testing capability. This feature introduces a
selected level of internal test current to simulate an over-
load or short circuit. It checks proper functioning of the
relay and verifies that curve settings have been set-up
correctly. The integral test function provides selectable
“Trip” and “No Trip” test settings for both phase and
ground testing. Refer to Table 2.4 for available test set-
tings. The “P” used in Table 2.4 refers to a phase current
test setting, while the “G” refers to a ground current test
setting. “T” in the table means that the test will initiate a
breaker trip. All settings are in per unit current values
times the In value, which is the selected CT rating.
THE TEST MODE SHOULD NOT BE USED TO TRIP
LIVE CURRENT CARRYING CIRCUITS. IF A LIVE
CURRENT OF GREATER THAN 0.1 TIMES THE (In)
VALUE IS FLOWING IN EITHER A PHASE OR
GROUND CIRCUIT, THE TEST MODE IS AUTOMATI-
CALLY EXITED, ACCOMPANIED BY AN ERROR
MESSAGE IN THE SETTINGS/TEST TIME/ TRIP
CAUSE WINDOW.
2-1.6 COMMUNICATIONS
An important function of the Digitrip 3000 Protective
Relay is communications and control via the Cutler-
!
CAUTION
DIP SWITCH SETTINGS
Type Default Setting
S1: ON (Digitrip 3000 IMPACC Buffers)
S2: OFF (Program with Breaker Open Only)
S3: OFF (Standard Relay Configuration -
OC/Instantaneous)
S4: ON (Enable Remote Open/Close)
S5: OFF (Reserved)
S6: OFF (Reserved)
S7: OFF (Reserved)
S8: OFF (Disable Download Setpoints)
S9: OFF (Manual Reset)
S10: OFF (Reserved)
PHASE SETTINGS
Type Default Setting
Curve Shape: It
LDPU: 1.0
LDT: 5 sec.
SDPU: 1.5
SDT: 1.0 sec.
INST: 1.75
GROUND SETTINGS
Type Default Setting
Curve Shape: It
LDPU: 0.5
LDT: 5 sec.
SDPU: 0.75
SDT: 1.0 sec.
INST: 1.0
MISCELLANEOUS SETTINGS
Type Default Setting
DISC: OFF
HILD: 10 sec.
FREQ: 60 Hz
PCT: 500
GCT: 500
Table 2.5 Factory Set Defaults

I.B. 17555 Page 11
Effective 03/97
Hammer Integrated Communications (INCOM) Protocol.
It allows the combining of electrical distribution and con-
trol products with personal computers into a comprehen-
sive communications and control network.
The Digitrip 3000’s communications chip permits the
interrogation of relay data, remote tripping and closing
of breaker, the Reset of the relay after a trip, and down-
loading of set points from a remote master computer.
Communications is accomplished from the relay to the
master computer via a 115.2 KHz. frequency carrier sig-
nal over a shielded twisted pair of conductors. The
receiving terminal is a remote mounted master comput-
er (IBM compatible). Refer to Figure 2-1 for a typical
communications wiring diagram.
Ground shielding should be provided at one place
only, with the computer end being the recommend-
ed location.
2-2 PROTECTIVE RELAY HARDWARE
2-2.1 FRONT OPERATIONS PANEL
The operations panel, which is normally accessible from
the outside of the switchgear panel door, provides a
means to program, monitor and test the unit (Figure
1-1). For the purpose of familiarization, the panel is
divided into three sub-sections:
1. Pushbuttons
2. LEDs
3. Display Windows
Pushbuttons: The front operations panel supports
eleven membrane pushbuttons. Pushbuttons are color
coded (red, white, blue, yellow) by their function to be
operational friendly. For example, blue pushbuttons are
associated with actual program functions, yellow push-
buttons with integral testing functions, and white push-
buttons are common to both operations or are indepen-
dent. White pushbuttons accomplish their function when
depressed. They can be held down and not released to
accelerate their function. Blue and Yellow pushbuttons
accomplish their function after having been pressed and
released.
Reset Pushbutton (Red)
The Reset pushbutton is used to reset any of the follow-
ing: the trip relays (overcurrent and instantaneous), the
trip alarm relay, the trip LEDs, and the ampere demand
current. Reset applies to both normal operations and
integral testing. If the unit is in the auto-reset mode, as
set by DIP switch #9 on the back of the unit, the trip
relays and the trip alarm relay will automatically reset
when the circuit breaker is opened after a trip.
Program Mode Pushbutton (Blue)
The Program Mode pushbutton, which is accessed by
opening the sealable, hinged access cover, is used to
enter and exit the program mode. When this pushbutton
is pressed and released, the program LED flashes and
setpoints can be altered. DIP Switch S2 establishes
when the Program Mode can be entered. With S2 set to
“off,” the Program Mode can only be entered when the
breaker is open. With S2 set to “on,” the Program Mode
can be entered with the breaker open or closed. Any
selections made in the program mode are only saved
when the Save Settings pushbutton, which is described
later, is depressed. When programming is concluded,
the Program Mode pushbutton should be pressed to exit
the program mode. Note that if the Save Settings push-
button is not depressed prior to exiting the program
mode, the previous settings will be retained. The pro-
gram mode is also exited if the Reset pushbutton is
pressed or if there is no programming activity for
approximately 2-1/2 minutes.
Note: Each Digitrip 3000 is shipped from the factory
with nominal protection settings. The relay
should be programmed by the user before being
put into service, as these nominal values may
not give optimum system protection or coordina-
tion. Remove tag from security door to access
the “Program Mode” pushbutton.
Test Mode Pushbutton (Yellow)
Also located behind the sealable hinged access cover is
the Test Mode pushbutton. This pushbutton is used to
enter and exit the test mode. When the pushbutton is
pressed and released, the word TEST will appear in the
Settings/Test Time/Trip Cause display window. If there
is more than 0.1 times (In) current flowing in either the
phase or the ground circuit, the Test Mode cannot be
initiated and the error message “ERR” will appear in the
display window. The test mode will also automatically be
exited if there is no activity for 2-1/2 minutes.
Select Test Pushbutton (Yellow)
The Select Test pushbutton is used, after the test mode
has been entered, to select the type of test. There are
phase and ground tests to trip or not trip the breaker.
(See Section 3-3.4).
Test Pushbutton (Yellow)
The selected test operation is initiated by pressing and
releasing the Test pushbutton.
NOTICE

I.B. 17555
Page 12
Effective 03/97
Figure 2-1 Typical Communications Wiring Diagram
➀FOR NETWORK INTERCONNECTION CABLE, SEE CABLE SPECIFICATIONS ON FIG. 3-1.
➁REFER TO CIRCUIT BREAKER WIRING DIAGRAMS FOR ACTUAL CONNECTIONS.
➂CARBON COMPOSITION RESISTOR MUST BE INSTALLED ON THE MOST REMOTE DEVICE AS SHOWN:
- 150 OHM, 1/2 WATT FOR 1200 BAUD RATE COMMUNICATIONS.
- 100 OHM, 1/2 WATT FOR 9600 BAUD RATE COMMUNICATIONS.
➃A CUTLER-HAMMER CONI (COMPUTER OPERATED NETWORK INTERFACE) OR CONI-3 CARD MUST BE INSERTED
INTO THE COMPUTER ISA BUS.
➄CUSTOMER TO SUPPLY A COMPUTER AND MODULAR TELEPHONE CONNECTOR TYPE RJ11 AND WIRE PER VIEW A
➅GROUND SHIELDING AT ONE PLACE ONLY (COMPUTER END RECOMMENDED).
➆WHERE DEVICES ARE DAISY CHAINED, TIE SHIELDING TOGETHER FOR END-TO-END CONTINUITY. SOME PROD-
UCTS WILL PROVIDE AN EXTRA TERMINAL FOR A TIE POINT FOR THE CABLE SHIELD LEADS.
➇CIRCUIT BREAKER TRUCK OPERATED CELL TOC SWITCH (SHOWN FOR CIRCUIT BREAKER IN “CONNECTED”
POSITION) IS OPTIONAL TO AUTOMATICALLY DISCONNECT RELAY FROM THE COMMUNICATION NETWORK WHEN
CIRCUIT BREAKER IS IN THE “TEST” POSITION.
➈ON LAST DEVICE IN NETWORK, TIE BACK SHIELD AND TAPE.
➉WHEN TOC SWITCH IS USED, DOWNLOADING OF PROTECTION SETTINGS FROM THE COMPUTER WILL NOT BE
POSSIBLE WITH BREAKER IN THE “TEST” POSITION.
0 3 1
1
2
TB2
INCOM
Digitrip 3000
0
1
With Digitrip
RMS 800
DSII Circuit
Breaker
0 4 7
IQ DP-4000
with PONI 0
IBM (or IBM Compatible
Computer)
A3 A2 A1
RES
0
2
With Digitrip
RMS 800
SPB Circuit
Breaker
0
P3
3
10
81
52 TOC
A
7
8
52 TOC
A
8
52 TOC
A
7
22
7
6
4
See
View "A"
1
2
3
4
View "A"
Note: Address Viewed on "SETTINGS"
Display Window
9

I.B. 17555 Page 13
Effective 03/97
Select Settings Pushbutton (Blue)
In the program mode of operation, the Select Settings
pushbutton is used to step to the next setpoint by press-
ing and releasing the pushbutton. This pushbutton steps
forward. To step back, the Select Settings pushbutton
can be pressed and held, while pressing and releasing
the Lower pushbutton.
Raise/Lower Pushbutton (White)
The Raise and Lower pushbuttons are used during the
program and test modes to increase or decrease the
value of the displayed setpoint. The Lower pushbutton
also serves a dual function in conjunction with the
Select Settings pushbutton, as described under Select
Settings Pushbutton.
Save Settings Pushbutton (Blue)
While in the program mode, selected setpoints can be
saved by depressing and releasing the Save Settings
pushbutton. Settings can be saved individually or one
time as a group. If the Save Settings pushbutton is not
used, the previous setpoints will remain when the pro-
gram mode is exited.
View Settings Pushbutton (Blue)
The View Settings pushbutton is functional only when
the unit is in the normal operating mode, not the pro-
gram or test modes. It functions to display the unit’s set-
points, including the phase and ground current trans-
former ratio selected via programming.
Select Pushbutton (White)
The Select pushbutton is used to step between any of
the eight current values that are displayed in the RMS
Amperes window. The eight currents are IA, IB, IC, IG,
IA ampere demand, IB ampere demand, IC ampere
demand, and IG ampere demand. Stepping with this
pushbutton is in the sequence just given. The currents
displayed are the present RMS values; the ampere
demand currents are the averaged RMS values sensed
over a 5 minute period of time. The demand value is the
largest 5 minute average measured since the amp
demand was last reset.
LEDs: LEDs are used to indicate a number of func-
tions, operations and/or warnings. Many of the LEDs
used provide different indication messages. The specific
message is determined by the color and a constant on
or blinking operation. Several of the LEDs are bi-colored
and can be lit green or red.
Operational LED
The Operational LED at the top of the relay should be
green and blink on for approximately one second and
then off for one second. This indicates that the relay is
functioning properly in its normal operation mode. If this
LED is blinking red, it indicates the relay may need
reprogramming. If this LED is lit in any color shade other
than a definite green or red, or if it is not blinking at all,
an internal problem has been detected requiring
replacement of the relay.
High Load LED
The High Load LED will blink green when high load set-
tings are being selected in the program mode. In the
operational or test modes, the High Load LED will blink
red when a load current of 85% or above the inverse
time overcurrent phase pick-up setting is reached. If the
load current remains at 85% or above the inverse time
overcurrent phase pickup setting for the time interval
setting, the LED will change to steady red at the end of
the time interval. Whenever the load current drops
below the 85% level, the timer will reset and the LED
will turn off.
Communication Trip LED
This LED, will be continuous red when the breaker has
been tripped by the master computer via INCOM. The
LED will turn off when the Reset pushbutton is pressed
or the circuit breaker is reclosed.
Curve Shape LED
This LED will blink green when the slope setpoint is dis-
played in the Settings/Test Time/Trip Cause window
while in the program mode. When the curve shape set-
point is being viewed in the unit’s normal operating
mode, this LED will be a continuous green.
Time Overcurrent Setting LED
This LED is bi-colored. While in the program mode, the
LED will blink green when the inverse time overcurrent
pickup setpoint is displayed in the Settings/Test
Time/Trip Cause window. It will be a continuous green
when the inverse time overcurrent pickup setpoint is
being viewed in the unit’s normal operating mode. The
LED will blink red whenever the load current exceeds the
inverse time overcurrent pickup setpoint. If the relay trips
on inverse time overcurrent, the LED will be continuous
red.
Inverse Time Overcurrent Time LED
This LED will blink green when the LED time overcur-
rent time setpoint is displayed in the Settings/Test
Time/Trip Cause window while in the program mode.
When the time multiplier is being viewed in the unit’s
normal operating mode, the LED is continuous green.
Short Delay Setting LED
This LED is bi-colored and operates like the time over-
current setting LED.

I.B. 17555
Page 14
Effective 03/97
Short Delay Time LED
The short delay time LED, when lit is green, and oper-
ates like the inverse time overcurrent time LED.
Instantaneous LED
This LED is bi-colored and operates like the inverse
time overcurrent setting LED.
Phase LED
The phase LED is bi-colored. The LED will blink green
when the phase inverse time overcurrent setting, inverse
time multiplier, short delay setting, short delay time, and
instantaneous setpoints are displayed in the Settings/Test
Time/Trip Cause window while in the program mode.
When these setpoints are viewed in the normal operating
mode, this LED will be continuous green.
The LED will blink red, along with the time overcurrent
setting LED whenever the phase load current exceeds
the inverse time overcurrent pickup setpoint.
The LED will be continuous red, whenever a trip is initi-
ated by the phase inverse time overcurrent, short delay,
or instantaneous protective functions.
Ground LED
The ground LED is also bi-colored (green/red). The
ground LED operates exactly like the phase LED for all
ground associated functions.
Amp Demand LED
This LED will be continuous green when an ampere
demand current is being viewed in the RMS Amperes
window.
I
A
, I
B
, I
C
, I
G
LEDs
The specific phase or ground current LEDs will be con-
tinuous green when that phase or ground current is
being displayed in the RMS Amperes window. When the
Amp Demand LED is also lit, the displayed current is the
Ampere Demand Current.
Program LED
This LED is continuous green when the relay is in the
program mode.
Test LED
This LED is continuous green when the relay is in the
test mode.
Display Windows: Two windows are used to display all
of the relay’s data, setpoints and messages. One win-
dow is located in the upper portion of the relay’s face-
plate and is labeled RMS Amperes. A second window is
located in the lower portion of the faceplate adjacent to
the program and test LEDs. It is labeled Settings/Test
Time/Trip Cause.
RMS Amperes Window
This window has a five digit numeric display. It is used
to show:
1. Present phase or ground currents
2. Largest phase or ground demand currents since last
reset
3. Fault current (displayed after a trip until a reset action
is initiated)
4. Phase and ground current transformer CT setting
(when “View Settings” pushbutton is used with the
relay in the normal operating mode)
Settings/Test Time/Trip Cause Window
This window is a four character Trip Cause Window
alphanumeric display used to show the value of the set-
points, the test time, or the cause of trip.
2-2.2 REAR ACCESS PANEL
THE BACK OF DIGITRIP 3000, WHEN ENERGIZED,
OFFERS EXPOSURE TO LIVE PARTS WHERE THE
HAZARD OF A FATAL ELECTRIC SHOCK IS PRE-
SENT. ALWAYS DISCONNECT SOURCE AND CON-
TROL POWER SUPPLY BEFORE TOUCHING ANY-
THING ON THE REAR OF THE DIGITRIP 3000. FAIL-
URE TO DO SO COULD RESULT IN INJURY OR
DEATH.
The rear access panel of Digitrip 3000 is normally accessi-
ble from the rear of an open panel door (Figure 1-2). All
wiring connections to the Digitrip 3000 Protective Relay
are made at the chassis’ rear. For the sake of uniform
identification, the frame of reference when discussing the
rear access panel is facing the back of the relay. The DIP
switches, for example, are located on the upper left of the
rear panel (Figure 1-4). Become familiar with the functions
and connections involved, especially the following:
DIP Switches: A set of ten DIP switches are located in
the upper left portion of the rear panel. Refer to Table
5.1 for DIP switch positions. Their basic functions are as
follows:
1. Switch S1 is used to select whether the IMPACC
buffers are set for the Digitrip 3000 configuration or
the Digitrip MV configuration. (Refer to Section 5 for
configuring the Digitrip 3000 as a replacement for a
Digitrip MV.)
!
WARNING

I.B. 17555 Page 15
Effective 03/97
2. Switch S2 is used to enable/disable the ability to pro-
gram the setpoints when the breaker is in the open or
closed position.
CARE MUST BE TAKEN WHEN PROGRAMMING
THE DIGITRIP 3000 WHILE THE BREAKER IS
CLOSED AND CURRENT IS FLOWING. AN INCOR-
RECT SETTING CONFIGURATION COULD CAUSE
THE RELAY TO TRIP THE BREAKER WHEN SET-
TINGS ARE SAVED.
3. Switch S3 is used to configure the trip contacts as
shown below:
Trip Contacts Dip Sw. OFF Pos. Dip Sw. ON Pos.
TB 12 & 13 Phase & Ground Trip Inst. Ground Trip Inst./OC
TB 14 & 15 Phase & Ground Trip OC/ Phase Trip Inst./OC/
Communications Communications
4. Switch S4 is used to enable/disable the ability to
open or close the breaker remotely from the commu-
nications interface (host computer).
5. Switch S8 is used to enable/disable the ability to
download setpoints from the communication interface
(host computer).
6. Switch S9 is used to select whether the relay should
be self-reset or manually reset (lock out function).
For additional details refer to the following para-
graphs entitled “Manual Reset” and “Auto Reset.”
7. Switches S5, S6, S7 and S10 are reserved.
Manual Reset: (DIP Switch S9 OFF) In this mode the
Trip Instantaneous contact (TB2 12 and 13), Trip
Overcurrent contact (TB2 14 and 15) and the Trip Alarm
contact (TB2 6, 7 and 8) change state after a protection
trip operation. The contacts stay in that state until the
“Reset” Pushbutton is depressed. In addition, the front
panel will hold the cause of trip in the “Trip Cause” win-
dow and the fault current magnitude in the “RMS
Ampere” window until the “Reset” pushbutton is
depressed. A RESET COMMAND can be sent to the
Digitrip 3000 by a master computer to remotely reset the
Digitrip 3000.
Auto Reset: (DIP Switch S9 ON) In this mode the Trip
Instantaneous contacts (TB2 12 and 13) or Trip
Overcurrent contacts (TB2 14 and 15) are momentarily
closed after a protection trip operation. The contacts will
remain closed until the breaker’s 52b auxiliary switch
contact closes. The Trip Alarm Relay, however, remains
energized until the “Reset” Pushbutton is depressed or
a RESET COMMAND is received from a communication
system master. In this mode after a trip is initiated and
the breaker has opened, the display will BLINK the
cause of the trip in the “Trip Cause” window and the
“RMS Ampere” window will show the fault current mag-
nitude. Both displays clear when the circuit breaker is
reclosed.
Communicating LED: A red LED just above terminal
block (TB2) is used when the relay is communicating. If
the relay is the type designed to accept field installation
of a communication module at a later date, this LED is
not functional at any time.
Terminal Block One (TB1): TB1 is located on the left
side of the rear panel, and is numbered 1 through 15,
with 1, 2, 3, 7 and 8 not used.
Terminals 5 and 6 are provided for the AC or DC input
control power connections and Terminal 4 is the con-
nection for equipment ground.
Terminal 9 and 10 provide for connection to a required
dry 52b contact and to a 52 TOC contact from the circuit
breaker.
When the relay has input control power, Terminals 9
and 10 will have this potential on them.
Terminals 11 and 12 are used for ground zone interlock-
ing, inverse time overcurrent protection and short delay
protection. The zone interlocking function is a low level
DC signal used to coordinate with “downstream” and “up-
stream” breakers that see or do not see the fault. If the
function is not used but a inverse time overcurrent or
short delay time is desired, the two terminals should stay
jumpered as they were when shipped from the factory.
Terminals 13 and 14 are used for phase zone interlock-
ing, inverse time overcurrent protection and short delay
protection.
Terminal 15 is the zone signal common. Zone common
should never be connected to earth ground.
Refer to Figure 4-1 for a typical phase zone interlock-
ing/wiring scheme.
Note: Digitrip 3000 Protective Relays are shipped with
a phase zone interlocking jumper (across termi-
nals TB1-13 and 14) and a ground zone inter-
locking jumper (across terminals TB1-11 and
!
CAUTION
NOTICE
Table of contents
Popular Other manuals by other brands
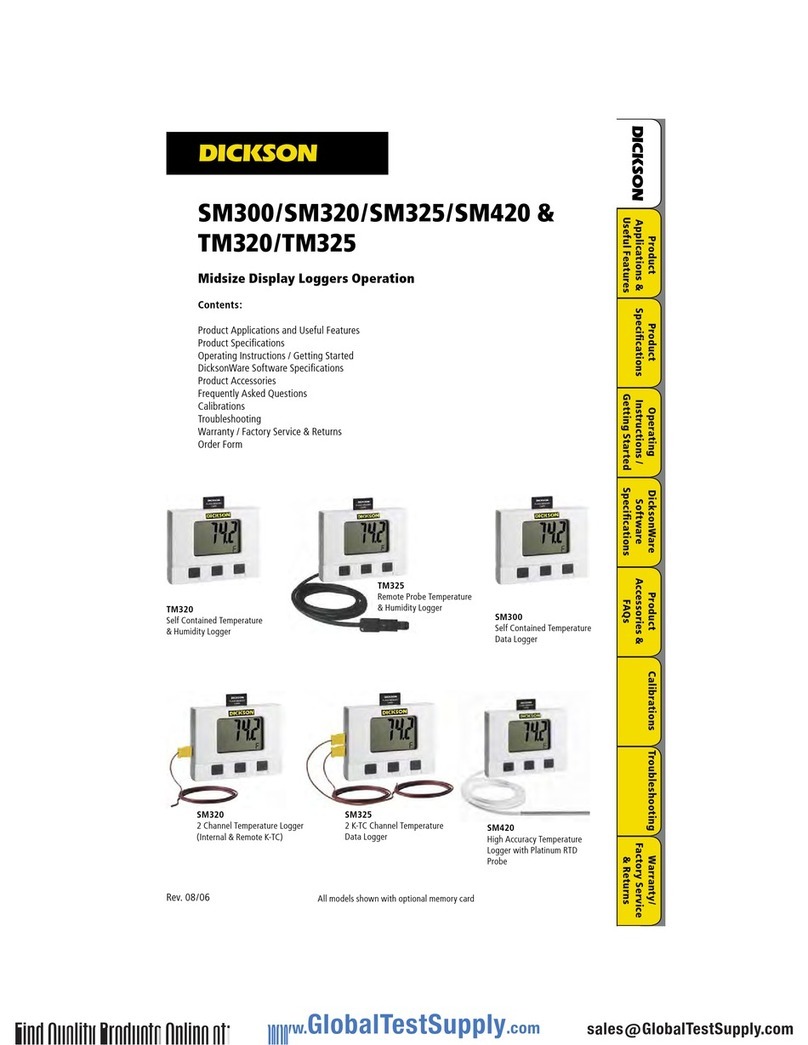
Dickson
Dickson SM300 operating instructions
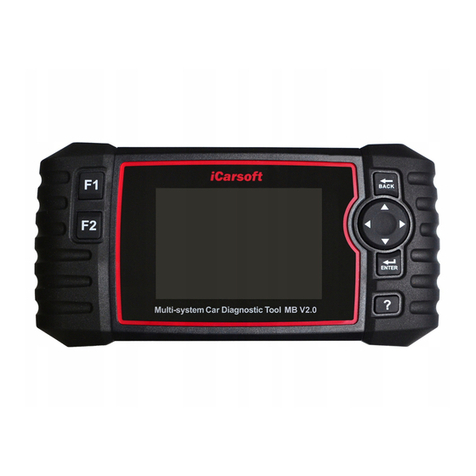
iCarsoft
iCarsoft MB V2.0 user manual

Wilo
Wilo Control SC-Fire Jockey Installation and operating instructions
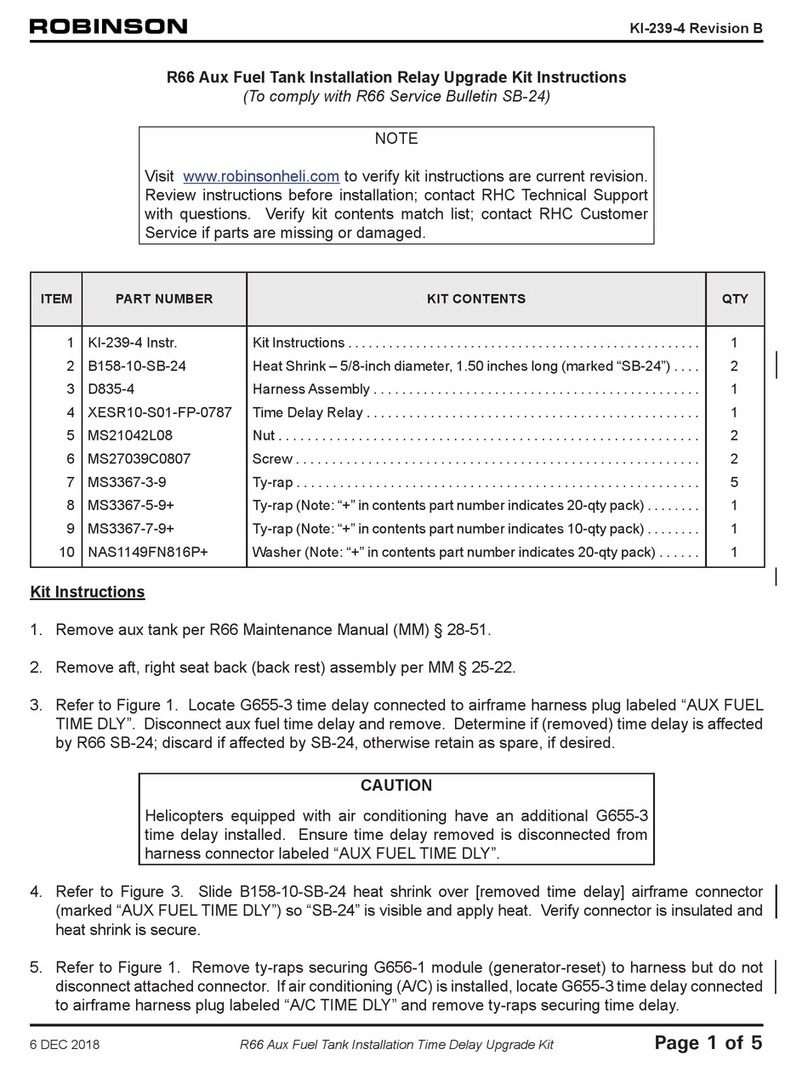
Robinson
Robinson R-66 Series Lithium-Ion installation instructions

MadgeTech
MadgeTech UltraShock-5 Product user guide

Motorvac
Motorvac 500-1125B user manual