DB Industries SALALIFT 8101000 Operator's manual

© Copyright 2003 DB Industries, Inc.
User Instruction Manual
Salalift® and Salalift® IIWinches
8101000and8102001Series
This manual is intended to meet industry
standards, including OSHA 1910.146 and
ANSI Z117.1, and should be used as part
of an employee training program as
required by OSHA.
WARNING:Thisproductis tobe usedaspartof acompletesystem.The
usermustfollow themanufacturer'sinstructions foreachcomponent ofthe
completesystem.Theseinstructionsmustbe providedto theuserof this
equipment.Manufacturer'sinstructionsmust befollowedforproper useand
maintenanceof thisproduct.Alterationsormisuse ofthis product,orfailure
tofollow instructionsmayresult inserious injuryordeath.
IMPORTANT:Ifyouhave questionson theuse,care,application, or
suitabilityfor useof thissafety equipment,contact DBI/SALA.
IMPORTANT:Beforeusingthisequipment recordtheproduct identification
informationfrom the IDlabel on thewinch inthe inspection and
maintenancelog insection 9.0of thismanual.
The8101000,8101002,8101004,and 8101006 Salalift
Series ManuallyOperatedWinchesareclassified byUnder-
writers Laboratories, Inc. as to the 350 lbs. load capacity
only.
actoolsupply.com
actoolsupply.com
actoolsupply.com

actoolsupply.com
actoolsupply.com
DBI SALA 8304000 Sealed SRL Salalift Tripod Confined Space Entry Kit
DBI SALA 8304010 Sealed SRL Salalift II Confined Space Kit
DBI SALA 8304011 Sealed SRL Salalift II Confined Space Kit
DBI SALA 8300020 Confined Space Entry Salalift II Winch Tripod 60 Ft
DBI SALA 8300030 Confined Space Entry Salalift II 60Ft Winch 7' Tripod

3
Figure 1 - 8101000 Series Parts Identification
actoolsupply.com
actoolsupply.com

44
Figure 2 - 8102001 Series Parts Identification
actoolsupply.com
actoolsupply.com

5
DESCRIPTIONS
SALALIFT®Winches:
8101000: 60feet of1/4inch galvanizedwirerope, carryingbag.
8101002: 60 feet of 1/4 inch stainless steel wire rope, carrying bag.
8101004: 120feet of 1/4inch galvanizedwirerope, carryingbag.
8101006: 120 feet of 1/4 inch stainless steel wire rope, carrying bag.
8101101: 140feet of 1/4inch galvanizedwirerope, carryingbag.
8101103: 140 feet of 1/4 inch stainless steel wire rope, carrying bag.
SALALIFT®IIWinches:
8102001: 60feet of1/4inch galvanizedwirerope, carryingbag.
8102003: 60 feet of 1/4 inch stainless steel wire rope, carrying bag.
8102009: 90feet of 3/16inch galvanizedwirerope, carryingbag.
8102011: 90 ft. of 3/16 inch stainless steel wire rope, carrying bag.
8102005: 120feet of 3/16inch galvanized wirerope, carrying bag.
8102007: 120 feet of 3/16 inch stainless steel wire rope, carrying bag.
IMPORTANT: Forspecial (custom)versionsofthis product,followthe
instructionsherein.See supplementalinstructions,ifincluded,foradditional
instructionsoncustomequipment.
1.0 APPLICATIONS
1.1 PURPOSE: DBI/SALA Salalift winches are to be used for work
positioning(8101000series only), personnelriding,materialhandling,
climbing protection, or rescue and evacuation.These winch models are
to be used with a DBI/SALA tripod, davit arm, or other support
structure, and may be used in situations where personnel or materials
needto be raisedor lowered 60-140feet.
1.2 WINCH APPLICATIONTYPES:
A. WORK POSITIONING:The Salalift winch(8101000seriesonly)is
used to suspend the worker in a work position, acting as the primary
means of support.Applications include suspending a worker in a
work seat or harness. A back-up personal fall arrest system must be
attachedto the suspendedemployee.
NOTE: OSHA requiresthatmanualor poweredwinches beindependently
evaluatedandclassified foruseasa singlepointsuspension system.See
OSHAregulation 29CFR1926.451, and29CFR1910.28.
B. PERSONNEL RIDING: The Salalift or Salalift II winch is used to raise
or lower a worker to a work level. At the work level the worker is no
longersupportedbythe winch.It is recommended that the workerbe
connectedto aback-up arrestsystemwhilebeing raisedor lowered.
actoolsupply.com
actoolsupply.com

6
C. RESCUE AND EVACUATION:The Salalift or Salalift II winch is used
toraiseor loweran endangeredor injured worker, orrescue
personnel.Applicationsinclude permit andnon-permitconfined
space entry work.
D. CLIMBING PROTECTION:The Salalift or Salalift II winch is used to
protecta workerascending ordescending afixed ladderor similar
structure. It is recommended that this use of the winch be restricted
to structures where other means of climbing protection; such as
permanently installed ladder safety systems or personal fall arrest
systems are infeasible. For this application, the following conditions
must be met:
1. Ladder or steps are in good condition and allows for a straight,
continuousclimb.
2. The worker climbing the ladder is wearing a full body harness and
the winch line is connected to the dorsal (back) D-ring of the
harness.
3. Thewinch operatoris trainedandcompetent inthe operationof
thewinch.
4. No slack line is allowed to develop when the worker moves up or
down the ladder.
5. DBI/SALA recommends, for the 8101000 series winches only,
thatan energy absorbinglanyardbe connectedbetweenthe
harnessdorsal D-ringandthe winchline.
1.3 LIMITATIONS:Thefollowingapplicationlimitations mustbe considered
before using this product.Failure to observe product limitations could
result in serious injury or death.
A. INSTALLATION:The winchmustbe installed inaccordance withthe
requirements stated in section 3.0 of this manual.
B. CAPACITY:Themaximumworkingload forthis product is350 lbs.
(160kg).
C. PERSONAL FALL ARREST SYSTEMS: Personal fallarrest
systems used with the Salalift or Salalift II winch must meet
applicablestate and federalregulations and therequirementsstated
in section 3.3.
D. PHYSICAL AND ENVIRONMENTAL HAZARDS:Useofthis
equipmentin areaswith physical orenvironmental hazardsmay
actoolsupply.com
actoolsupply.com

7
require that additional precautions be taken to reduce the possibility
of damage to this equipment or injury to the user.Hazards may
include, but are not limited to; high heat (welding or metal cutting),
acid or caustic chemicals, corrosive environments such as
exposure to seawater, high voltage power lines, explosive or toxic
gases, moving machinery or sharp edges. Contact DBI/SALA if you
have questions about the application of this equipment in areas
wherephysicalor environmentalhazardsare present.
E. TRAINING:This equipment is to be installed and used by persons
who have been trained in its correct application and use.
1.4 Refer to national standards, including; ANSI Z117.1, local, state, and
OSHArequirements(26CFR 1910.146),formore information onthe
application of this and associated equipment.
2.0 SYSTEM REQUIREMENTS
2.1 COMPATIBILITY OF COMPONENTS:DBI/SALAequipment is
designedfor usewithDBI/SALA approvedcomponents and
subsystems only.Substitutions or replacements made with non-
approved components or subsystems may jeopardize compatibility of
equipment and may effect the safety and reliability of the complete
system.
2.2 COMPATIBILITY OF CONNECTORS: Connectorsare considered tobe
compatiblewith connectingelementswhen theyhave beendesignedto
work together in such a way that their sizes and shapes do not cause
their gate mechanisms to inadvertently open regardless of how they
become oriented. Contact DBI/SALA if you have any questions about
compatibility.
Connectors( hooks,carabiners, and D-rings)must becapable of
supporting at least 5,000 lbs.(22kN).Connectors must be compatible
withthe anchorageor other systemcomponents. Donot use equipment
thatis notcompatible.Non-compatible connectorsmay unintentionally
disengage.See Figure3. Connectorsmust be compatiblein size,
shape,and strength.Self lockingsnap hooksand carabinersare
requiredby ANSIZ359.1and OSHA.
2.3 Making Connections: Onlyuseself-locking snaphooksand carabiners
with this equipment. Only use connectors that are suitable to each
application. Ensure all connections are compatible in size, shape and
strength. Do not use equipment that is not compatible. Ensure all
connectors are fully closed and locked.
actoolsupply.com
actoolsupply.com

8
DBI/SALAconnectors (snaphooks and carabiners)are designedtobe
used only as specified in each product’s user’s instructions.See Figure
4for inappropriate connections.DBI/SALA snap hooksand carabiners
shouldnot beconnected:
A. To a D-ring to which another connector is attached.
B. In a manner that would result in a load on the gate.
NOTE: Largethroat openingsnaphooksshouldnot beconnectedto
standardsize D-ringsor similarobjectswhichwillresult ina loadon thegate
ifthe hookorD-ring twistsorrotates. Largethroat snaphooksare designed
foruseon fixedstructuralelements suchasrebar orcrossmembers thatare
notshaped inaway thatcan capturethe gateof the hook.
C. Ina falseengagement, where featuresthat protrudefrom thesnap
hook or carabiner catch on the anchor and without visual
confirmation seems to be fully engaged to the anchor point.
D. Toeachother.
E. Directly to webbing or rope lanyard or tie-back (unless the
manufacturer’s instructions for boththe lanyardandconnector
specifically allows such a connection).
Figure 3 - Unintentional Disengagement (Roll-out)
If the connecting element that a snap hook (shown) or carabiner attaches to is
undersized or irregular in shape, a situation could occur where the connecting
element applies a force to the gate of the snap hook or carabiner. This force may
cause the gate (of either a self-locking or a non-locking snap hook) to open,
allowing the snap hook or carabiner to disengage from the connecting point.
1. Force is applied to
the snap hook. 2. The gate presses against
the connecting ring. 3.The gate opens
allowing the snap
hook to slip off.
Small ring or other
non-compatibly
shapedelement
actoolsupply.com
actoolsupply.com

9
F. To any object which is shaped or dimensioned such that the snap
hook or carabiner will not close and lock, or that roll-out could occur.
2.4 SUPPORT STRUCTURE STRENGTH: Thesupport structuretowhich
the winch is installed must meet minimum strength requirements stated
in section 3.4
3.0 OPERATION AND USE
WARNING: Donot alterorintentionallymisuse thisequipment.Consult
DBI/SALAwhen usingthisequipment incombination withcomponentsor
subsystemsotherthanthose describedinthismanual.Some subsystem
and componentcombinationsmayinterferewith theoperationof this
equipment.Usecautionwhen usingthisequipmentaroundmoving
machinery,electricalhazards,chemical hazards,andsharpedges.
WARNING:Consult your doctorif thereisreason todoubtyourfitness to
safelyabsorb theshock fromafall arrest.Age andfitnessseriouslyaffecta
worker'sability towithstandfalls. Pregnantwomen orminorsmust notuse a
DBI/SALAwinch,unless forunavoidableemergencyusesituations.
3.1 BEFORE EACH USE:Before each use of this equipment carefully
inspect it to ensure it is in good working condition. Check for worn or
damaged parts.Ensure all parts are present and secure.Check
operation of winch;ensure that it will lift, lower, and hold the load under
normaloperation. Check winchand entire systemfor damage and
corrosion.See section 5.0 for further inspection details.Do not use if
inspectionreveals anunsafe condition.
Figure 4 - Inappropriate Connections
actoolsupply.com
actoolsupply.com

10
3.2 PLANNING: Plan your system and how it will function before starting
your work. Consider all factors that affect your safety during use. Some
important points to consider when planning your system are:
A. HAZARD EVALUATION:Evaluatejob sitehazardspriortostarting
work.Consult applicableOSHAand industrystandardsfor
guidelinesand regulatoryrequirementson issuessuch as confined
space entry, personal fall arrest systems (PFAS), and single point
adjustablesuspended scaffolds.
B. WORK SITE GEOMETRY:Theinstallation anduse ofthe support
structure (tripod, davit arm and base) must be consistent with the
geometricrequirements stated inthe associated manufacturer's
instruction manuals.When suspendingworking linesfrom the
support structure, check for obstructions or sharp edges in the work
path.Avoid working where the user may swing and hit an object, or
where lines may cross or tangle with that of another worker.
C. SECONDARYORBACK-UP FALLARREST SYSTEM:When using
the Salalift winch (8101000 series) as a support for work positioning,
a secondary or back-up fall arrest system is required. See OSHA 29
CFR1910.28 and1926.451.TheDBI/SALAtripodanddavitarmhas
provisions for connection of a secondary or back-up PFAS.See
sections 3.3 and 3.5 (A).
D. RESCUE: A means of dealing with an accident or emergency must
be planned in advance.Response time can play an important role in
the survival of an injured worker.Users of this equipment must be
trainedinemergencyprocedures.
3.3 REQUIREMENTS FOR PERSONAL FALL ARREST SYSTEMS:PFAS
used with the Salalift or Salalift II winch and support structure must
meetapplicableOSHArequirements.
• The PFAS should be rigged to minimize any potential free fall and
never allow a free fall greater than 6 feet. It is recommended that the
PFAS used with this equipment include a full body harness as the
body support component. PFAS's that incorporate full body
harnesses must maintain fall arrest forces below 1,800 lbs. and arrest
the fall within 42 inches. Body belts, unless incorporated into a full
body harness, are not recommended for use with this equipment. A
typical PFAS includes a full body harness, connecting subsystem or
component(self retracting lifelineorlifeline andropegrab), and the
necessary connectors to couple the system together.
•Anchorages selected for PFAS must sustain static loads, applied in
the directions permitted by the PFAS, of at least; (A) 3,600 lbs.
actoolsupply.com
actoolsupply.com

11
(16kN) when certification exists (see ANSI Z359.1 for certification
definition), or (B) 5,000 lbs. (22kN) in the absence of certification.
When more than one PFAS is attached to an anchorage, the
anchorage strengths set forth in (A) and (B) must be multiplied by the
numberof PFASattached tothe anchorage.Per OSHA1926.500 and
1910.66: Anchorages used for attachment of a PFAS shall be
independentofanyanchoragebeingusedtosupportorsuspend
platforms, and must support at least 5,000 lbs. (22kN) per user
attached, or be designed, installed, and used as part of a complete
PFAS which maintains a safety factor of at least two, and is
supervisedby aqualifiedperson.
WARNING: Readand followmanufacturer'sinstructions for thepersonalfall
arrestequipment selectedfor usewiththe winchandsupportstructure.
IMPORTANT: Body beltsare notallowedfor freefallsituations.Bodybelts
increasethe riskof injuryduring fallarrest incomparisontoafull body
harness.Limitedsuspension timeandthe potentialforimproperlywearing a
bodybelt may resultinadded dangerto theuser’shealth.
3.4 INSTALLATION OFWINCHTO SUPPORT STRUCTURE:
A. MOUNTINGBRACKET:Thesewinchesincorporatea“quick-mount”
style bracket for attachment to the support structure. DBI/SALA
tripods, davit arms, and other support structures supplied by
DBI/SALA, include a bracket that mates with the winch quick-mount
bracket. All DBI/SALA winches include the quick-mount bracket.
Whenusing the 8102001series winchwiththe 8004176WallMount
Bracket, a mounting adapter kit is required. Contact DBI/SALA for
moreinformation.
B. LOAD REQUIREMENTS: Figure 5illustratesmountingthe winch to
thesupport structure and theload requirements.Themounting
bracket must support the loads shown in Figure 5.
C. GEOMETRIC REQUIREMENTS: Refer tothesupport structure
manufacturer'sinstructions for geometricrequirements.Installations
of the winch to support structures other than those provided by
DBI/SALA must meet the geometric requirements shown in
Figure 5.Position the support structure so the load and the lifeline of
thewinch canbe directedover thework areawhen installed.For
personnel use, do not position the support structure where the
worker will have to swing under the support structure to reach the
workarea.Avoid positioningthesupport structurewherethe working
linemay abradeagainstsharp edges.
actoolsupply.com
actoolsupply.com

12
IMPORTANT:Positionthe winchandsupportstructurein alocationwhich
allowsthe operatortosafely usethe winch.
D. QUICK-MOUNT INSTALLATION: SeeFigure 6.Mountthe winch
using the quick-mount bracket as follows:
Step 1. Pull out the locking detent pin by depressing the button on end
of the pin. Lift the winch into place and position the slot in the
bracket over the fixed pin on the support structure bracket.
Step 2. Push the top of winch in toward the support structure while the
bottom rotates on the fixed pin. Align the holes and push the
detent pin through until it stops. Ensure the pin locks in place.
Figure 5 - Load/Geometric Requirements
actoolsupply.com
actoolsupply.com

13
Step 3. Slowly pull out the winch line.Route the line over the support
structure pulley system.See the support structure
manufacturer'sinstructions fordetails.
E. WELDED INSTALLATIONS:If welding the mounting bracket to a
support structure it is recommended that the welding be done by a
certified welder.Portions of the mounting bracket that have been
exposeddue to weldingshouldbe paintedorotherwise protected
fromcorrosion.
Figure 6 - Quick-Mount Installation
3.5 OPERATIONOFWINCH:
A. CONNECTINGWINCH LINETO LOAD: SeeFigure7.For
applications that do not require a secondary PFAS, the winch line
shouldbe connectedtothe worker'sharness back D-ring.For
applications requiring a secondary PFAS, the winch line should be
connected to aY-type lanyard and this lanyard should be attached to
theworker'sharnessshoulder D-rings.Thesecondarylifelineshould
beconnected totheworker's harnessback D-ring. Formaterial
handling applications, connect the winch line to the load using a tie-
offadapter or otheranchoring device.
B. SALALIFTWINCH (8101000 Series):Attach thewinchto the
support structure as described in section 3.4 (D).Install the winch
crank handle onto the high or low speed shaft by aligning the handle
with the shaft and pushing firmly inward until the handle snaps in
place.To release the handle from the shaft, depress the handle
release and pull the handle off the shaft. Pull the ratchet lever
downward and feed the line off the drum by rotating the crank handle
in the“lower”direction.Route the line over the support structure
pulley system.
actoolsupply.com
actoolsupply.com

14
TO RAISE A LOAD:Rotate thewinchcrankhandle clockwise when
using the low speed shaft and counterclockwise when using the high
speed shaft.For worker safety, the crank handle incorporates an
overload clutch which limits the winch lifting force on the high speed
shaft to approximately 250 lbs. and 500 lbs. on the low speed shaft,
thus reducing the possibility of injury should a worker become
entangledduring retrieval.Do not exceedthe ratedcapacity of 350
lbs.
TO LOWER A LOAD: Rotatethewinch crank handle inthe“raise”
direction until the ratchet brake lever can be pulled down, then rotate
thecrankhandle inthe“lower”direction.Whena loadis suspended
from the winch, use caution when the ratchet brake lever is pulled
down since the load will be transferred to the winch crank handle.To
prevent loss of control of the load, do not blockor restrict the ratchet
lever from engaging the teeth on the drum, except by normal manual
operation.If theoperatorfatigues, orfor any reasondesires to“hold”
the load, allow the ratchet brake to engage and support the load.
The Salalift® I winch is designed and typically used for manual
operation.Certainsituations where thespeed ofthe rescue, coupled
with fatigue experienced by operator during long lifts, may
necessitatethe needfora powereddrive operation. ContactDBI/
SALAfor moreinformation.
C. SALALIFT IIWINCH (8102001 Series):Attachthe winch tothe
support structure as described in section 3.4 (D).Install winch crank
handle onto the input shaft by aligning the hub of the crank handle
with the square drive marked "winch shaft" and pushing firmly
inwarduntil handlesnaps inplace (thegrip onthe handleshould
Figure 7 - Connection
actoolsupply.com
actoolsupply.com

15
face outward).To release the crank handle from the shaft, pull the
handle off the shaft.
Feed the line off the winch drum by rotating the
crankhandle in theloweringdirection (counterclockwise).Apply
slight tension to the line while feeding it off the drum.Free-wheel
mode may also be used, see section 3.5 (C). Route the line over the
support structure pulley system.
TO RAISE A LOAD:Rotate the winch crank handle in the raise
direction (clockwise).To hold or momentarily suspend the load, stop
cranking.The automatic clutch/brake will hold the load if handle is
released.The winchincorporatesan overload clutchlimiting the
lifting force to approximately 700 lbs., reducing the chance of injury
ifa workerbecomesentangled duringretrieval. Do notexceed the
rated capacity of 350 lbs.
TO LOWER A LOAD:Rotate thewinch crankhandle inthe lower
direction(counterclockwise).When lowering linewithouta load,
maintain slight tension on the line to aid payout.
FREE-WHEEL MODE: Removethecrankhandlefromtheraise/lower
input shaft. Reverse the crank handle and install it onto the square
drive marked "freewheel shaft" by aligning the handle hub with the
shaft.See Figure 8.Toengage free-wheelmode,rotatethe crank
handle counterclockwise until it stops and hold.The line can now be
freely pulled off of the winch drum.To avoid build-up of slack line on
the drum, pull the line off the drum smoothly, remove slack on the
drum by releasing the crank handle and pulling on the line. If the line
pays out too rapidly, an over speed brake will activate and lock,
stopping the line. If this happens, return to the winch mode and
rotate the crank handle clockwise two turns to unlock the over
speedbrake. Do notengage free-wheel modewith load onthe lifting
line,removeload on thelinebefore engaging free-wheelmode.
When using the Salalift II for climbing protection applications, free-
wheel mode is not recommended.The operator must be attentive to
slack line; paying out and reeling in line as needed.
D. IMPACT INDICATOR AND CABLE RESERVE:TheSalalift IIwinch
is supplied with a connecting swiveling hook that incorporates a load
indicator.This indicator functions if the winch is severely impact
loaded or if the lifting capacity is exceeded by a preset amount. See
section 5.0 for inspection of load indicator.The Salalift II
incorporatesa reserve cableretention feature onthe cable drum.
With the drum near empty (single layer of cable remaining), the
shear pin is visible.See Figure 10.The reserve cable ensures that
theshock absorbingfeatureis availablethroughoutthe working
range of the winch. If the winch is shock loaded at the reserve point
actoolsupply.com
actoolsupply.com

16
of cable payout, the shear pin will shear, allowing the shock
absorber to function normally.If the shear pin has been sheared, the
unit must be returned for inspection and repair.See section 5.0 for
inspection details.
IMPORTANT: Donot usewinch for liftingor loweringof morethan one
person,exceptfor emergencysituations.In thiscase,if usingthe8101000
series, thelowspeedshaft mustbe usedto preventhandle slippage.The
maximumlifting forceisapproximately 500lbs.
WARNING:If thecrankingtensioneasesduring lowering,theperson or
materialbeinglowered hasreacheda worklevelorobstruction. Donot
continuecrankingwithout communicatingwiththepersonor checkingthe
materialbeinglowered. Alwayskeepthe cabletensionfirm.Slack cable
couldcause afree fall.
WARNING: A minimum of four wraps of line must remain on the drum at all
timeson the8101000 series.One completelayer ofline mustremainonthe
8102001series. Donot attempttoreverse windthe lineonto thedrum. Line
mustwind ontothe drumby turningthe crankhandle inthe "raise"direction
only.Checkperiodicallytosee thatthe lineis windingevenlyon thedrum.
Usegloveswhenhandling line.
4.0 TRAINING
4.1 It is the responsibility of the user to assure they are familiar with these
instructions,and are trained in thecorrect careand useof thisequipment.
Figure 8 - Free-Wheel Mode
actoolsupply.com
actoolsupply.com

17
User must also be aware of the operating characteristics, application
limits, and the consequences of improper use of this equipment.
IMPORTANT:Trainingmustbeconducted withoutexposingthetraineetoa
fallhazard.Trainingshouldberepeated onaperiodicbasis.
5.0 INSPECTION
5.1 FREQUENCY:
•Before Each Use: Visually inspect per steps listed in sections 5.2
and5.3.
•Monthly: A formal inspection of the winch should be done by a
competent person other than the user. See sections 5.2 and 5.3 for
guidelines. Record results in the inspection and maintenance log in
section 9.0.
•Annual: It is recommended that the winch be serviced by a factory
authorizedservicecenteror themanufacturer.Extremeworking
conditions may require increasing the frequency of inspections.
Annual servicing shall include, but not be limited to, an intensive
inspectionand cleaningofall internaland external components.
Failure to provide proper service may shorten product life and could
endangerperformance.
•After An Impact: Inspect entire winch according to section 5.2.
WARNING: If thewinch hasbeen subjectedto impactforces, itmustbe
immediatelyremovedfrom serviceandinspected. Ifthewinchfailsto pass
theinspection, donot use.Theequipmentmustbesenttoanauthorized
servicecenterforrepair.
IMPORTANT: Extremeworkingconditions(harshenvironment,prolonged
use,etc.)may requireincreasingthefrequency ofinspections.
5.2 GENERAL INSPECTION STEPS FOR ALLWINCH MODELS:
Step 1. Inspect all screws, bolts and nuts. Ensure they are securely
attached and tight. Check to see if any bolts, nuts or other
parts are missing, or have been substituted or altered in any
way.Inspect covers, housings, guards, etc. Ensure they are
free of cracks, dents, or other damage.
Step 2. Crank handle must lock positively onto the shaft and be free of
cracks, bends, or other damage.
actoolsupply.com
actoolsupply.com

18
Step 3. Connecting hook must not be damaged, broken, distorted, or
have any sharp edges, burrs, cracks, worn parts, or corrosion.
Ensure the connecting hook works properly.Hook gate must
move freely and lock upon closing.Hook must swivel freely.
Step 4. Wire Rope: Inspect entire length of wire rope assembly starting
at the hook. Always wear protective gloves when inspecting
wirerope.
A. Inspect for broken wires by passing the wire rope through gloved
hands, flexing it every few inches to expose breaks. Broken wires
can be removed by bending the wire back and forth parallel to the
rope length. Do not attempt to pull wires out of rope. Inspect for
kinks, cuts, crushed burned areas, or other damage.Wire rope with
serious damage must be removed from service.
B. The wire rope assembly must be replaced by an authorized service
center if there are six or more randomly distributed broken wires in
one lay, or three or more broken wires in one strand in one lay.Note:
A “lay” of wire rope is the length of wire rope that it takes for a
strand(the largergroups of wires)to completeonerevolution or
twist along the rope.
C. The wire rope assembly must be replaced by an authorized service
center if there are any broken wires within one inch of the metal
compression sleeves at either end of the assembly.Note:To inspect
wirerope areanearcompression sleevesonhook end,remove
counterweight(8101000series) or sliderubberhookbumper up on
wirerope(8102001series).
D. Inspect entire length of wire rope for signs of corrosion. Severely
corrodedwirerope mustbereplaced.
Synthetic Rope: Inspect for the following if the winch uses synthetic rope:
A. Inspect for concentrated wear, frayed strands, broken yarns, cuts,
and abrasions.The line must be free of knots, excessive soiling,
heavypaint buildup,and ruststaining throughoutits length.
B. The line must be free of chemical or heat damage, indicated by
brown,discolored,or brittleareas.
C. The line must be free of ultraviolet damage, indicated by discoloration
and the presence of splinters and slivers on the rope surface.
D. All of the above factors are known to reduce rope strength. As a rule
of thumb, rope strength is reduced proportional to the cross
actoolsupply.com
actoolsupply.com

19
sectionalareaof the ropedamaged.Damagedor questionable rope
shouldbe replaced byanauthorized servicecenter.
Step 5. Inspect all identification and warning labels, ensuring that they
arelegibleand securelyattached.See Figure 1(8101000
series),Figure 2(8102001 series) andsection 8.0.
Step 6. Inspect each system component (support structure, back-up
fall arrest system, body support, connectors, etc.) according to
manufacturer'sinstructions.
Step 7. See additional inspection steps for the winch in sections 5.3,
5.4, and 5.5.
5.3 INSPECTION OF SALALIFTWINCH (8101000 SERIES): Thefollowing
steps are additional inspection procedures to those in section 5.2 that
mustbe performedon the 8101000series winch.SeeFigure 1.
Step 1. Check operation of the winch in high and low speed positions; it
must crank up and down freely.Stiff or rough operation may
indicateaworngear or bearing.
Step 2. Inspect the ratchet brake.With the brake engaged, the drum
should be prevented from paying off cable.The spring must be
in place and undamaged.The ratchet brake lever must fully
engage the teeth on the drum, the drum teeth must be in good
condition.
Step 3. Inspect for oil in the gearbox by removing plug on top and tilting
unit so oil can be seen through hole. Inspect for oil leaks.
Step 4. Check operation of the handle over speed brake as follows:
A. Over level ground set up support structure and winch as it will be
used.
B. By raising or lowering the winch cable, position the lifting hook to
approximatelychestheight.
C. Removethe winchcrank handle andhave someonehold the ratchet
brake lever in its disengaged position, such as when lowering a
load.
D. Pull down sharply on the lifting hook to engage the over speed
brake.
actoolsupply.com
actoolsupply.com

20
E. If the brake fails to engage or noticeable brake slippage occurs,
remove from service and return to an authorized service center for
repair.
Step 5. Check operation of the drum over speed brake as follows, see
Figure9:
A. To test the drum over speed brake, remove the handle over speed
brake assembly.Using a snap ring pliers, remove the ring that
retains the handle over speed brake assembly on the low speed
shaft.Remove the brake assembly, taking care not to damage the
pawl springs on the back side of the brake. Note: If damage exists
on the shaft such as a nick or corrosion, repair the damaged area
using a file or emery cloth before removing the brake assembly.
B. With the handle over speed brake removed, on level ground, set up
the support structure and winch as it will be used.To test the drum
overspeedbrake,removethecrankhandleanddisengagetheratchet
brake,then pull downsharply on thewinchcable toengagebrake.
C. If the brake fails to engage or slippage of more than one inch occurs
(a small amount of brake slippage is normal), remove the winch
Figure 9 - Inspecting level wind 8101000
actoolsupply.com
actoolsupply.com
This manual suits for next models
11
Table of contents
Popular Other manuals by other brands
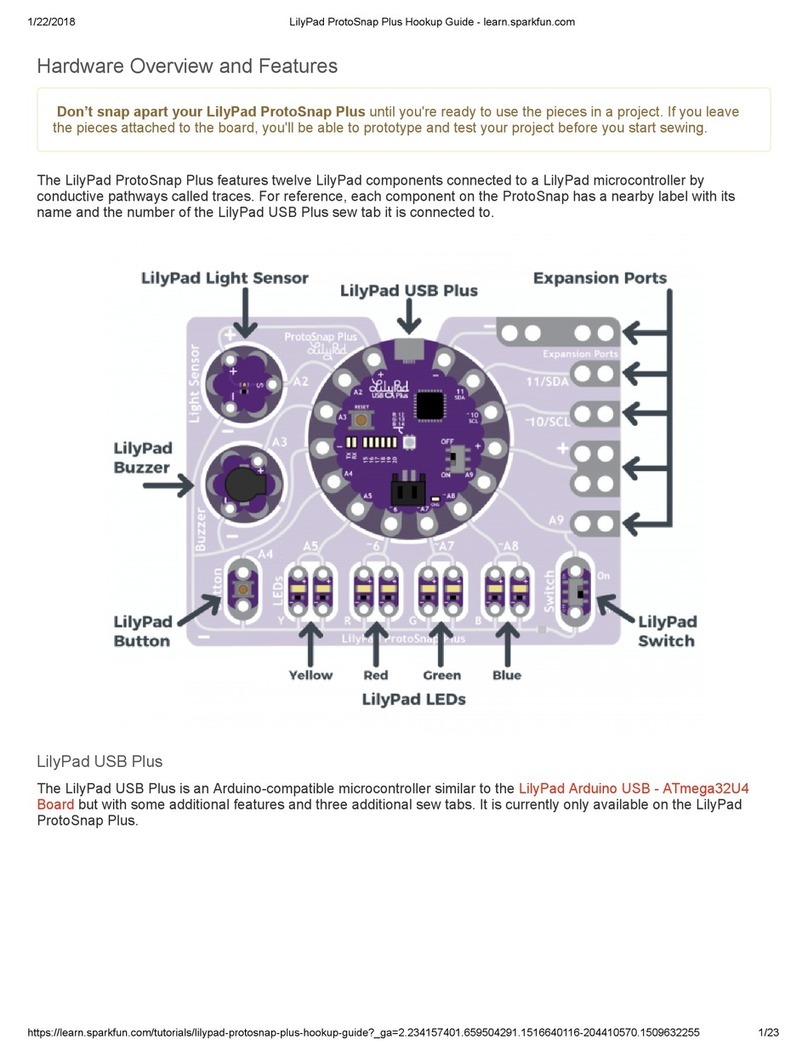
Sparkfun Electronics
Sparkfun Electronics LilyPad ProtoSnap Plus HOOK-UP GUIDE

Numatics
Numatics Modulair 105 Installation and maintenance instruction
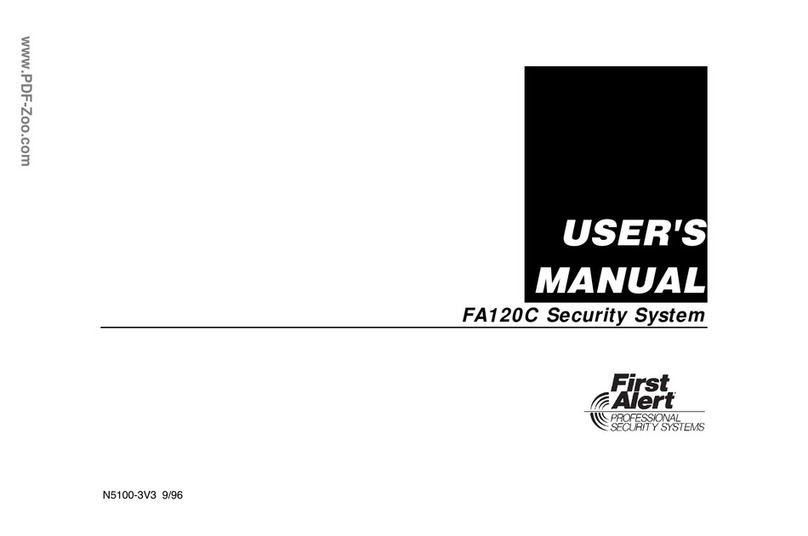
First Alert
First Alert FA120C user manual
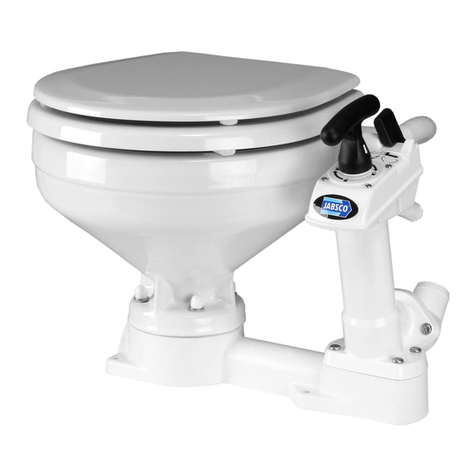
JABSCO
JABSCO Twist n Lock manual
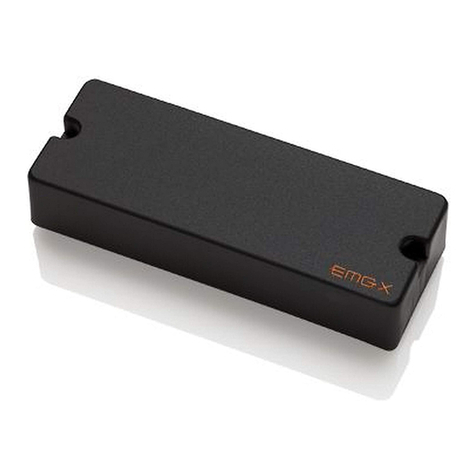
EMG
EMG 45-TW-X Installation information
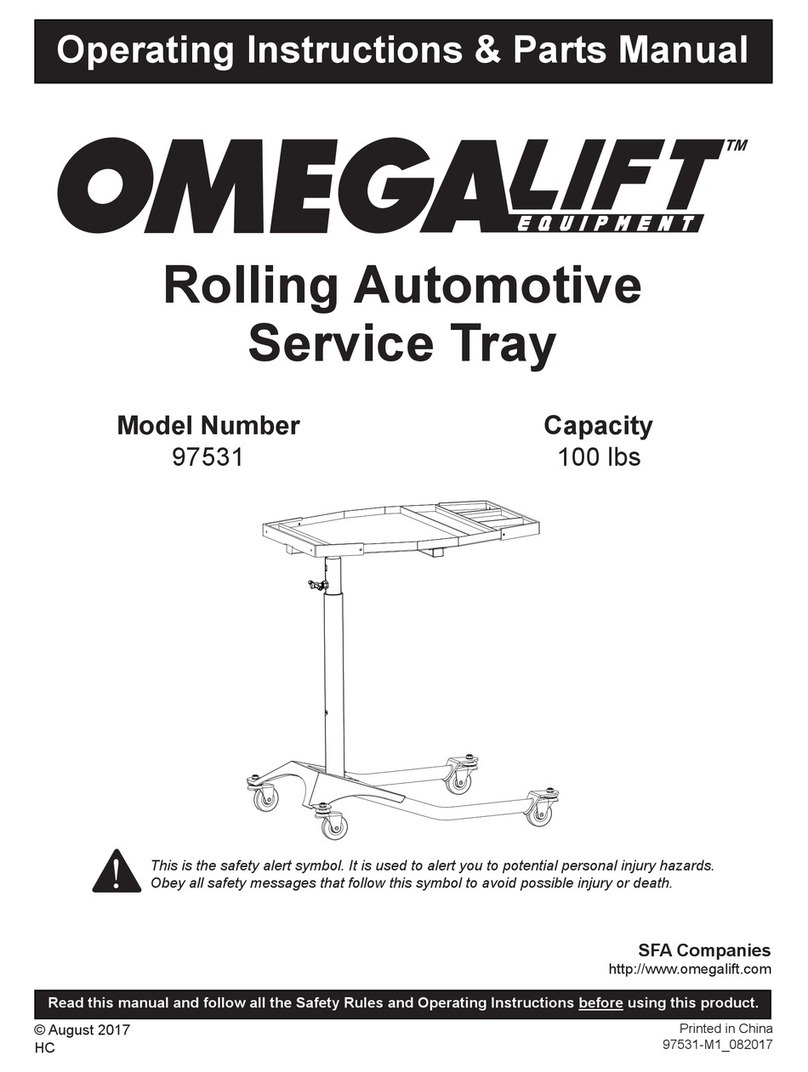
SFA
SFA OmegaLift 97531 operating instructions