ddtop UTK User manual

1/ 11
WWW.DDTOP.COM
UTK
DISPLACER LEVEL SWITCH
Operation Manual
UTK-DT-JS-1012-2018(A)

2/ 11
WWW.DDTOP.COM
Preface
Thank you for choosing the products of Dandong Top Electronics Instrument (Group)Co.,Ltd.
This operation manual provides you with important information on installation, connection and
commissioning as well as on maintenance, troubleshooting and storage. Please read it carefully
before installation and commissioning and keep it as part of the product near the meter for easy
reading.
This manual can be downloaded by entering the version number at www.ddtop.com .
如未遵照本说明书进行操作,则本仪表所提供的防护可能会被破坏。
If the instructions are not followed, the protection provided by the meter may be destroyed.
Trademark, Copyright and Restriction Instructions
Dandong Top Electronics Instrument (Group) Co.,Ltd.®, Dandong Top Pump Co., Ltd.®, DDTOP®
are registered trademarks of the company.
The performance specifications of the meter are effective as of the date of publication and are
subject to change without notice. Dandong Top Electronics Instrument (Group)Co.,Ltd. reserves the
right to modify the products described in this manual at any time without prior notice.
Quality Assurance
Dandong Top Electronics Instrument (Group) Co.,Ltd. guarantees that all glass plate level gauge
have no defects in materials and manufacturing processes within one year from the date of delivery.
During the warranty period, if the product returns with quality problems and the claim is
determined by the manufacturer to be within the scope of warranty, Dandong Top Electronics
Instrument (Group) Co.,Ltd. is responsible for repair or replacement of the buyer (or owner) free of
charge.
Dandong Top Electronics Instrument (Group) Co.,Ltd. is not responsible for the costs caused by
improper use of equipment, labor claims, direct or subsequent damage and installation and use of
equipment. In addition to the special written warranty certificate for certain products of Dandong
Top Electronics Instrument (Group) Co.,Ltd., Dandong Top Electronics Instrument (Group) Co.,Ltd.
does not provide any express or implied warranty.
Quality
Dandong Top Electronics Instrument (Group) Co.,Ltd. has passed the ISO9001 quality system
certification. The whole process of product production is strictly in accordance with the scope of the
quality system, providing the strongest guarantee for product and service quality.

3/ 11
WWW.DDTOP.COM
Content
1. Safety Tips ................................................................................................................................................4
1.1 Explosion may result in death or serious injury.................................................................................4
1.2 Process leaks can cause serious injury or death................................................................................4
1.3 Failure to follow safe installation guidelines may result in death or serious injury................ 4
2. Product Manual .......................................................................................................................................4
2.1 Main Structure of Product ........................................................................................................................4
2.2 Operating Principle .....................................................................................................................................5
2.3 Packaging.......................................................................................................................................................7
2.4 Transporting..................................................................................................................................................7
2.5 Storage............................................................................................................................................................ 7
3. Technical Characteristics .........................................................................................................................7
3.1 Main Performance.......................................................................................................................................7
3.2 Main Parameters..........................................................................................................................................7
4 Dimensional Outline Drawing-Figure 2..................................................................................................7
5 Unpacking and Inspection .......................................................................................................................8
5.1 Unpacking Inspection Notice...................................................................................................................8
Figure 4 Sample Nameplate .......................................................................................................................8
6 Installation.................................................................................................................................................8
6.1 Installation Tool............................................................................................................................................8
6.2 Installation Technical Requirements...................................................................................................... 9
6.3 Installation Procedure ................................................................................................................................9
7.Debugging ................................................................................................................................................9
7.1 Preparation for Commissioning ...........................................................................................................9
7.2 Electrical Wiring............................................................................................................................................9
7.3 Debugging Operation Process..............................................................................................................10
8. Precautions.............................................................................................................................................10
9 Fault Analysis and Elimination...............................................................................................................11
10 Disassembly ..........................................................................................................................................11
10.1 Warnings....................................................................................................................................................11
10.2 Waste Removal ........................................................................................................................................11
11 Product Certifications...........................................................................................................................11

4/ 11
WWW.DDTOP.COM
1. Safety Tips
It is expressly prohibited to modify or change products for safety reasons,repair or replacement
only allows the use of accessories specified by the manufacturer.
1.1 Explosion may result in death or serious injury.
When installing equipment in an explosive atmosphere, be sure to follow applicable local, national,
international standards, codes, and procedures. Be sure to install the equipment in intrinsically safe
or non-flammable site operating procedures.
1.2 Process leaks can cause serious injury or death.
Care should be taken to lift the transmitter. If the process seal is damaged, the medium may leak at
the joint.
1.3 Failure to follow safe installation guidelines may result in death or serious injury.
The operations described in this manual are performed by professionally trained and qualified
professionals or end-user specialized professionals to complete.
2. Product Manual
2.1 Main Structure of Product
igure 1-1 Ball float type
Figure 1-1 Displacer type
1
2
3
4
5
6
7
8
9
Figure 1-1 Figure 1-1

5/ 11
WWW.DDTOP.COM
1
11
12
3
4
5
6
7
8
9
10
Figure 1-2
1. Displacer chamber
2. Float, Buoyancy Measurement Element
3. Housing with 360° rotation
4. Magnetic switch assembly, micro switch and reed switch optional
5. Isolation sleeve
6. Magnetic rod, including magnetic steel
7. Fasteners, including bolt and nut washers
8. Head flange
9. Seal
10. Spring assembly
11. Displacer
12. Wire rope
2.2 Operating Principle
2.21 Classification of Displacer Level Switch
The Displacer Level Switch is divided into ball float type and displacer type based on the different
sensor elements. The ball float type is used in the working condition where the pressure is no more
than 6.3 MPa. The displacer type is usually used in the working condition that the operating
pressure is high or the top mounted alarm setting value is large. Refer to Figure 2 and Figure 3 for
the operating principle.

6/ 11
WWW.DDTOP.COM
Figure 2-1 Ball Float Type Operating Principle Figure 2-2 Displacer Type Operating Principle
2.2.2 Float Type Operating Principle
With the float ball as the induction element, the float ball is rigidly connected with the magnetic rod.
When the level rises, the ball float drives the magnetic rod upward into the magnetic field area of
the magnetic switch assembly. Through magnetic induction or magnetic coupling, the switch
contacts are switched on or off. When the level is lowered, the float ball moves downward and
drives the magnetic rod away from the magnetic field of the magnetic switch assembly. Then the
magnetic controlling switch returns to its original state, or the offset magnetic steel returns to a new
equilibrium position under the action of gravity and makes switch contact on or off to realize the
level that can be controlled and given an alarm.
2.1.3 Displacer Type Operating Principle
With the displacer as the sensing element, the displacer hangs on a spring through the suspension
rod. When the level is raised, the liquid contacts with the displacer and the displacer creates a
buoyancy. With the buoyancy, the pulling force on spring is smaller, and the spring shrinks, driving
the magnetic rod upward into the magnetic field area of the magnetic switch assembly. By magnetic
induction or through magnetic co-operation, magnetically controlled switch or bias magnetic steel
drives the switch contacts are switched on or off. When the level is lowered, the floating force is
reduced, and the spring is subjected to a larger pull force. The spring drives the magnetic rod out of
the magnetic field of the magnetic switch assembly. The magnetically controlled switch restores the
original state or bias magnetic steel, under the self-weight, back to the new equilibrium position,
making the switch contacts switched on or off for the control or alarm of the level.

7/ 11
WWW.DDTOP.COM
2.3 Packaging
Please take your packaging waste to a special recycling facility.
2.4 Transporting
Please use quality lifting equipment and lifting straps, and pay attention to safety.
2.5 Storage
Storage temperature -20℃~40℃; Storage humidity≤40%.
3. Technical Characteristics
3.1 Main Performance
3.1.1 Has passed the national explosion-proof certification, certification mark.
Intrinsically safe: Ex ia CT1-T5/T6,
Explosion isolation: Ex dⅡCT1-T5/T6.
3.1.2 Product Standard: Q/AMM 004 Displacer Level Controller
3.2 Main Parameters
3.2.1 Supply Voltage:AC220V DC24V
3.2.2 Output Signal: Relay Contact SPDT or DPDT
4 Dimensional Outline Drawing-Figure 2.
If special dimensions are required when ordering, the actual dimensions shall prevail.
Figure 3-1 UTK-100A Figure 5 UTK-100B Figure 3-3 UTK-100C

8/ 11
WWW.DDTOP.COM
Figure 7 UTK-100D Figure 3-5 UTK-300 Figure 3-6 UTK-400
5 Unpacking and Inspection
5.1 Unpacking Inspection Notice
5.1.1 Check whether the nameplate of the product (Figure 4) is consistent with the information in
the supply list.
5.1.2 Check the quantity and material of each part against the packing list.
5.1.3 Check the appearance of the instrument for defects, damage and other abnormal conditions.
Figure 4 Sample Nameplate
6 Installation
6.1 Installation Tool
6.1.1 Wrenches, flange gaskets and flange bolts for process connections
6.1.2 Gradienter

9/ 11
WWW.DDTOP.COM
6.2 Installation Technical Requirements
6.2.1 When installing the chamber, the flange axis of the chamber side must be perpendicular to the
horizontal plane, and the verticality is within 3 °. 6.2.2 Ensure that the level of the equipment lead
pipe is within 3 °.
6.2.2 Ensure that there are no ferromagnetic particles in the medium that could be attracted to the
controller magnetic rod and affect switching performance.
6.2.4 The fluctuation frequency of the measured medium's level cannot be too large, and the
fluctuation range can’t exceed its permissible action limit.
6.3 Installation Procedure
6.3.1 Place the gasket on the flange sealing surface of the container.
6.3.2 Align the switch flange with the container flange, install flange bolts and nuts, and ensure that
the flange gasket is installed correctly.
7.Debugging
7.1 Preparation for Commissioning
7.1.1 Debugging tools: Multimeter
7.2 Electrical Wiring
7.2.1 Wiring Cable Preparation:The wiring cable shall be outer diameter Ф10mm five-core rubber
sleeve soft wire or rubber cable, one of which is inner ground wire. The other four cores are for a
pair of normally open and normally closed contact lines (using two of them), or for two pairs of
normally open and normally closed contacts wirings.
7.2.2Wiring Procedure
1. Remove the enclosure cover.
2. Wiring according to the wiring diagram, please note that the high-alarm and low-alarm switch
action is reversed, be sure to follow the wiring diagram (see Figure 5) to connect to the correct
terminal. For SPDT form, high report connect a pair of normally open point - common terminal (see
Figure 5-1), low report connect a pair of normally closed point - common terminal.
(See Figure 5-2), for DTDP form, the high report is connected to two pairs of normally open
points-public end (see Figure 5-3), and the low report is connected to two pairs of normally closed
points-public end (see Figure 5-4).

10 / 11
WWW.DDTOP.COM
Figure5-1 Figure5-2 Figure5-3 Figure5-4
3. All terminals shall be in good contact with each other, and the nut of outgoing wire shall be
properly pressed to prevent the lead from loosening.
4. Make sure that excess lines do not interfere with the movement of the switch cover or switch
mechanism.
7.3 Debugging Operation Process
1. The instrument should not be subjected to strong vibration and impact, especially on the float
level switch should not be strongly tension pressure, so as to avoid damage to the spring.
2.The instrument may not participate in impactful process tests such as air sweeps performed
before the device is put into production.
3.During commissioning, if water is used as the medium (not actually measured medium), the
following two situations will occur: ρmedium <ρwater and ρmedium>ρwater. If ρmedium <
ρwater, it can be debugged with water. If ρmedium>ρwater, it can't be debugged with water. It
can only be debugged with actual measuring medium.
4. For ρmedium <ρwater When calibrating with water, the alarm position will be lower than the
alarm position required by the actual measurement medium. The difference will be different due to
different working conditions and cannot be calculated by formula.
8. Precautions
8.1 The design density should be the same with the design density. If the density changes, please
contact the manufacturer to confirm whether it can continue to be used.
8.2 During the installing and uninstalling process, the torque tube should be protected as much as
possible to prevent damage.
8.3 The displacer level controller is not suitable for high vibration working condition.
8.4 Medium with viscosity higher than 500mPa/s is not suitable for use with the displacer level
controller.
8.5 Medium with ferromagnetic particles are not suitable for use with displacer level controller.
8.6 After wiring, tighten the power supply cover to prevent the instrument from getting wet.

11 / 11
WWW.DDTOP.COM
9 Fault Analysis and Elimination
Problem
Cause
Remedy
Level to the specified position, the switch is
not activated.
1. The ball is too heavy to float.
2. The float ball or displacer is dented,
leaky and filled with media.
3. Magnetic rod is caused by
ferromagnetic particles or obstacles in the
medium. Movement is blocked
4. Malfunction of magnetic switch
assembly.
5. Spring is damage.
6. Rod connecting float or displacer is
broken.
1. Confirm the density and contact the
manufacturer to replace the float ball
2. Replace the float or displacer
3. Remove the instrument and clean the float
and magnetic rod
4. Replace switch components.
5. Replace the spring.
6. Replace the rod
There is deviation between actual alarm
position and specification.
1. Process condition is not consistent
with design condition. (The actual density or
alarm setting value is inconsistent with the
design value);
2. On-site heat tracing caused the
changes in medium density;
1. Determine the process parameters again, and
contact the manufacturer to replace the relevant
parts
2. Adjust the heat tracing temperature to prevent
changes in the density of the medium;
10 Disassembly
10.1 Warnings
10.1.1 Before dismantling, be aware of hazardous process conditions such as pressure in the vessel,
high temperature, corrosive or toxic media.
10.1.2 Refer to the installation procedures in 6.3 and the instructions in section 7.2 Electrical wiring,
and dismantle the completed components in reverse order of operation.
10.2 Waste Removal
Waste disposal should be carried out in accordance with the current guidelines in each region.
11 Product Certifications
This manual suits for next models
6
Table of contents
Other ddtop Switch manuals
Popular Switch manuals by other brands

Honeywell
Honeywell PLS750C user guide
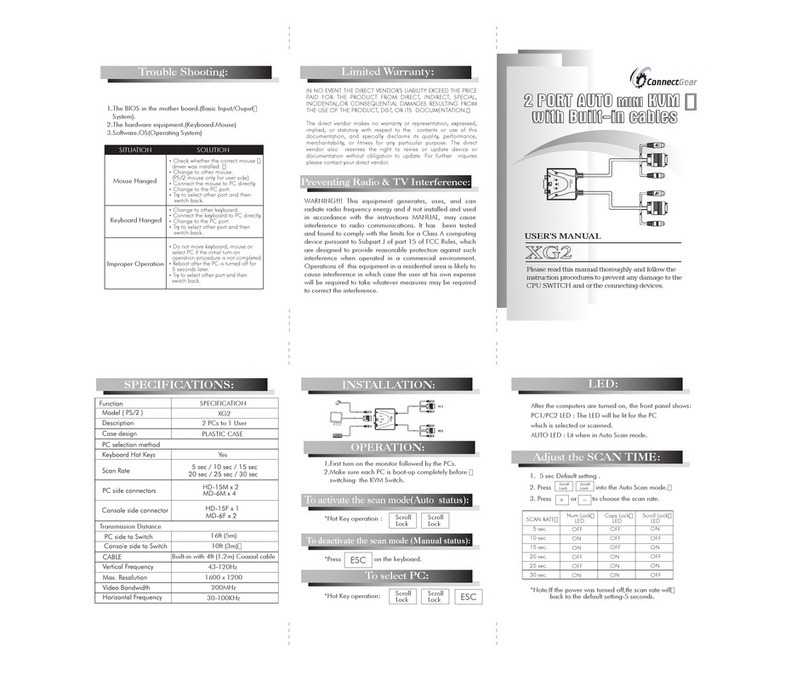
ConnectGear
ConnectGear XG2 user manual

Sinotimer
Sinotimer TM-610 quick start guide
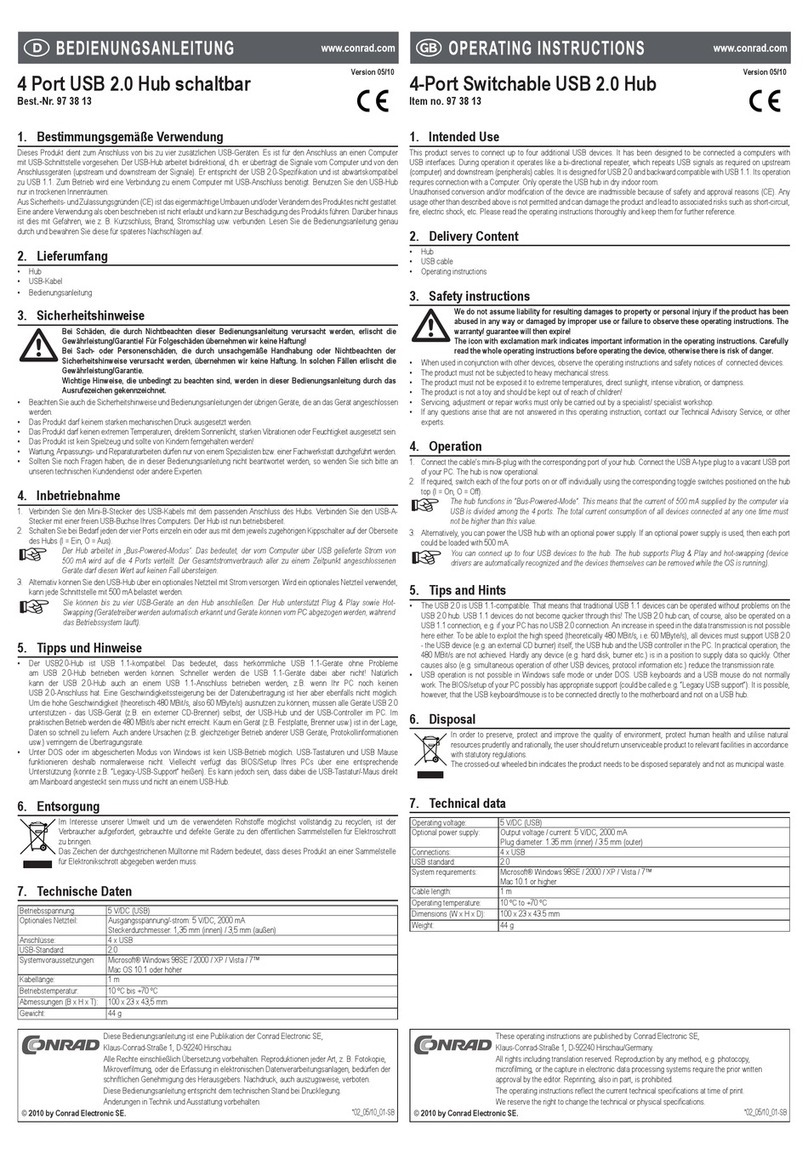
Conrad
Conrad 97 38 13 operating instructions

Extreme Networks
Extreme Networks Summit X670-G2 Series Installation note
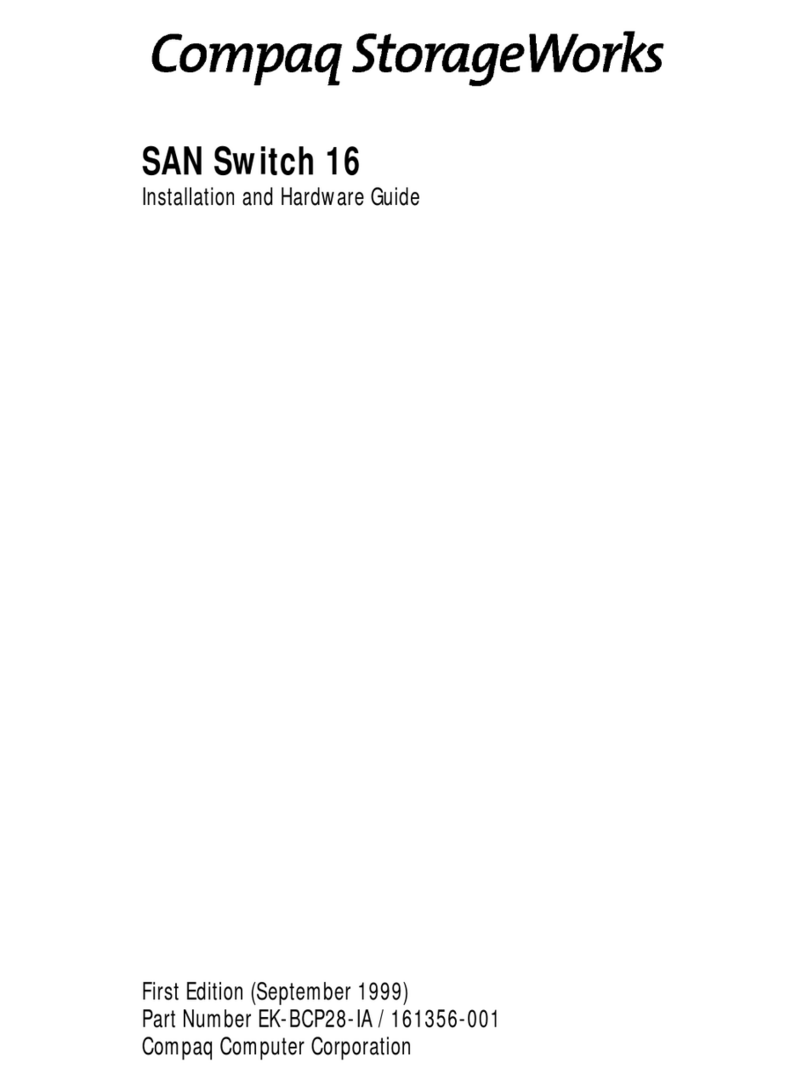
Compaq Storageworks
Compaq Storageworks SAN Switch 16 Installation and hardware guide