DINA SAFEONE DN3PD2 User manual

Safety switchgear to monitor the speed
of three-phase and single-phase motors without sensor
Manual
SAFEONE
DN3PD2

DINA Elektronik GmbH
Esslinger Straße 84
72649 Wolfschlugen
Deutschland
Phone +49 7022 9517 0
Mail [email protected]
Web www.dina.de
© Copyright by DINA Elektronik GmbH 2023
All parts of this documentation are protected by copyright.
Any use beyond that permitted under copyright law is not permitted without express written consent from the publish-
er. This applies in particular to the reproduction, distribution and translation of this documentation or parts thereof, as
well as the storage and processing of this content using electronic data processing systems.
The information contained in this documentation corresponds to the technical state of the product at the time these
operating instructions were published.
This manual is valid for:
Description ID-No.
DN3PD2 34PD01
34PD02
34PD03
Legal information
Handbook: Hardware
Target group: Electricians, electrical designers
Editor: DINA Elektronik GmbH
File name: DN3PD2-Handbuch-e-20220927.docx
Language: ENG
Publication as at: 12. January 2023

Inhaltsverzeichnis
SAFEONE DN3PD2 Manual I
Content
1Structure of the document......................................................................................... 1
1.1 Conventions..................................................................................................................1
1.1.1 Emphasizing information.............................................................................. 1
1.1.2 Emphasizing paragraphs using typography..................................................1
1.1.3 Emphasizing words using typography ..........................................................1
1.2 Your opinion is important to us!.....................................................................................2
2Safety........................................................................................................................... 3
2.1 Warnings......................................................................................................................3
2.1.1 Function of warnings .................................................................................... 3
2.1.2 Design of warnings.......................................................................................3
2.1.3 Hazard symbols............................................................................................4
2.2 Qualification of personnel .............................................................................................4
2.2.1 Electrician.....................................................................................................4
2.2.2 Electrical designers...................................................................................... 4
2.3 Intended use and improper use .................................................................................... 5
2.3.1 Certification data .......................................................................................... 5
4Product description.................................................................................................. 10
4.1 Function description....................................................................................................10
4.1.1 Speed monitoring.......................................................................................10
4.2 Acknowledge function................................................................................................. 11
4.3 Start-up monitoring.....................................................................................................11
4.4 Switch-off delay.......................................................................................................... 13
4.5 Switch-on delay..........................................................................................................13
4.6 Advanced settings ...................................................................................................... 14
4.7 Minimum switch-off time .............................................................................................14
4.8 Password....................................................................................................................15
4.9 Validation....................................................................................................................15
4.10 Display........................................................................................................................ 15
4.11 Diagnosis....................................................................................................................15
4.12 Signal outputs.............................................................................................................15
4.13 USB interface .............................................................................................................16
4.14 Connections................................................................................................................16

Inhaltsverzeichnis
SAFEONE DN3PD2 Manual II
4.15 Block diagram.............................................................................................................17
5Applications.............................................................................................................. 18
5.1 Motor with frequency converter................................................................................... 18
5.2 Motor with star-delta circuit......................................................................................... 18
5.3 Single-phase motor.....................................................................................................18
5.4 Synchronous motor..................................................................................................... 19
6Diagnostics and switching status displays ............................................................ 20
6.1 LED indicators............................................................................................................ 20
6.2 Error messages..........................................................................................................21
7Configuration............................................................................................................ 22
7.1 System requirements..................................................................................................23
7.2 Installation of the Configurations-Software..................................................................23
7.3 Connection to the PC..................................................................................................23
7.4 User interface.............................................................................................................24
7.5 Parameterization ........................................................................................................ 25
7.6 Machine data..............................................................................................................26
7.8 Create a project.......................................................................................................... 26
7.9 Edit and Change password......................................................................................... 26
7.10 Diagnose....................................................................................................................27
7.11 Validation....................................................................................................................29
8Example of application............................................................................................. 31
9Order information..................................................................................................... 32
10 Technical data........................................................................................................... 32
10.1 Supply ........................................................................................................................32
10.2 Digital inputs...............................................................................................................32
10.3 Measuring inputs ........................................................................................................ 32
10.4 Signal outputs.............................................................................................................33
10.5 Contact outputs .......................................................................................................... 33
10.6 General data...............................................................................................................33
10.7 Connection data ......................................................................................................... 34
10.8 Environmental conditions............................................................................................ 34
10.9 Dimensions................................................................................................................. 35
10.10 Safety technical data .................................................................................................. 35

Inhaltsverzeichnis
SAFEONE DN3PD2 Manual III
10.11 Safety-related parameters in accordance with DIN EN ISO 13849-1:2016-06 ............35
10.12 Contact life ................................................................................................................. 35
11 Installation and removal........................................................................................... 37
11.1 Installing a module......................................................................................................37
11.1.1 Overview....................................................................................................37
11.2 Removing a module.................................................................................................... 37

1 Structure of the document
SAFEONE DN3PD2 Manual 1
1 Structure of the document
1.1 Conventions
Information of particular important is emphasized in this documentation through the use of sym-
bols, typography or formulations.
1.1.1 Emphasizing information
The following symbols indicate important information:
Degree of hazard (e.g. WARNING): Triangular symbols indicate the degree of hazard
in warnings.
Type of hazard (e.g. electrical shock –dangerous voltage): Triangular symbols indi-
cate the type of hazard in warnings.
Information: Additional clarification.
Tip: Additional information to help optimize the workflow.
1.1.2 Emphasizing paragraphs using typography
The following typography is used to emphasize paragraphs with special functions:
►
Indicates an instruction.
◄
Indicates an expected reaction.
▼
Indicates an unexpected reaction.
∎
Indicates an item in a list.
1.1.3 Emphasizing words using typography
The following typography is used to emphasize words with special functions:
(1)
Represents a numbered item in a figure.
→
Indicates a cross-reference to another page, figure or document.

1 Structure of the document
SAFEONE DN3PD2 Manual 2
1.2 Your opinion is important to us!
We do all we can to provide complete, accurate documentation for the product. If you have any
suggestions for improvement or advice for us, please share your thoughts with us. Send us your
comments by e-mail to the following address.

2 Safety
SAFEONE DN3PD2 Manual 3
2 Safety
2.1 Warnings
2.1.1 Function of warnings
Warnings warn users about hazards when handling the product. The hazards are classified,
specified, described and supplemented with information about how to avoid them.
If there is a warning before a list of instructions, the hazard is present throughout the en-
tire activity.
If there is a warning immediately before an instruction, the hazard is present during the
next step.
2.1.2 Design of warnings
All warnings are indicated by a signal word and a warning symbol. The different combinations of
the signal word and warning symbol indicate the degree of danger.
DANGER
For an immediate hazard that will result in severe injuries or death.
WARNING
For an immediate hazard that could result in severe injuries or death.
CAUTION
For a potentially hazardous situation that could result in injuries.
CAUTION
For a potentially harmful situation in which the product or an item near it could be
damaged.
CAUTION
For a hazard that could cause environmental damage.

2 Safety
SAFEONE DN3PD2 Manual 4
2.1.3 Hazard symbols
Note
The warning symbol may be present alongside another hazard symbol that repre-
sents the type of hazard, in order to attract the reader's attention.
Hazard symbols are indicated by a triangular symbol in the context of warnings. The following
hazard symbols are used in this documentation:
Electric shock –dangerous voltage!
2.2 Qualification of personnel
DINA Elektronik GmbH distinguishes between specialist staff with different qualifications when
it comes to carrying out work on the product. The minimum required qualifications are specified
for each task and are defined as follows:
2.2.1 Electrician
Specialist who installs, maintains and repairs the electrical system in the product. A specialist is
a person whose specialist training means that they have the knowledge and experience, includ-
ing knowledge of relevant regulations, necessary to assess the work assigned to them and the
potential hazards.
Note
When evaluating a person's specialist training, multiple years of work in the rele-
vant field may also be taken into account.
→ DIN VDE 1000-10 Requirements for persons working in a field of electrical engi-
neering.
2.2.2 Electrical designers
Specialists who design the electrical system and the product. A specialist is a person whose
specialist training means that they have the knowledge and experience, including knowledge of
relevant regulations, necessary to assess the work assigned to them and the potential hazards.
Note
When evaluating a person's specialist training, multiple years of work in the rele-
vant field may also be taken into account.
→ DIN VDE 1000-10 Requirements for persons working in a field of electrical engi-
neering.

2 Safety
SAFEONE DN3PD2 Manual 5
2.3 Intended use and improper use
The product has exclusively been developed for use for the purpose described here. The speci-
fications set out in these operating instructions must be strictly complied with.
DN3PD2 is a safety switchgear to monitor the speed of three-phase and single-phase
motors without sensor.
The safety module is intended for use on machines and plants to prevent hazards from
arising.
Any other form of use is regarded as improper use.
If the product is
not used as intended,
improperly maintained or
incorrectly operated,
the manufacturer will not assume any liability for any damage that results. In this case, the risk
shall be borne exclusively by the user.
2.3.1 Certification data
The product is certified as safety equipment in accordance with:
DIN EN ISO 13849-1:2015
Category 4, PLe
EC type examination certificate
Notified body:
TÜV Rheinland Industrie Service GmbH
Am Grauen Stein
51105 Köln
Germany
NB 0035
EMC Directive
Certified by:
ELMAC GmbH Bondorf
CNL, USL
File E227037
QA system certified as per DIN EN ISO
9001:2015
Certified by:
DQS GmbH, 60433 Frankfurt am Main,
Germany
Note

2 Safety
SAFEONE DN3PD2 Manual 6
You can download the certificates from our website:
→ https://www.dina.de/downloads
2.4 Documentation
Operating instructions contain instructions on how to use a product safely, correctly and cost-
effectively. Follow the instructions in these operating instructions in order to prevent hazards,
avoid repair costs and standstill, and improve the reliability and service life of the product. You
must read the operating instructions and ensure that you understand them.
►Before working with the product, read the documentation
SAFEONE DN3PD2 Hardware manual
You can find them at www.dina.de/downloads.
►Always ensure that the operating instructions are available where the prod-
uct is in use.
2.5 Safety regulations
The safety regulations listed below must always be complied with. In the event that these safety
regulations are not complied with or the device is used improperly, DINA Elektronik GmbH
accepts no liability for any resulting injury or damage.
The product must only be installed and commissioned by a skilled electrician or a
trained, instructed person, who is familiar with these operating instructions and the appli-
cable specifications regarding occupational health and safety and accident prevention.
WARNING
Danger to persons and materials! In the event that specifications are not com-
plied with, this can result in death, severe injuries or significant material damage.
Observe VDE, EN and local regulations, in particular with regard to protective
measures.
If the emergency stop is used, either the integrated restart prevention function must be
used or the machine must be prevented from restarting automatically using a superordi-
nate control system.
When installing the device, the required distances as per DIN EN 50274, VDE 0660514
must be taken into account.
►During transport, storage and operation, comply with the conditions set out in EN 60068-
2-1, 2-2.
►Assemble the device in a control cabinet with at least IP54 degree of protection. Other-
wise, dust and moisture can impair the functions. The device must be installed in a con-
trol cabinet.

2 Safety
SAFEONE DN3PD2 Manual 7
►Ensure that the output contacts have sufficient protective circuitry for capacitive and in-
ductive loads.
►Follow the specifications in the general technical data.
Note
More detailed information can be found in the → Technical data section.
WARNING
Electric shock –dangerous voltage! During operation, switching devices conduct
dangerous voltages.
Never remove protective covers from electrical switching devices during operation.
►Replace the device the first time a fault occurs.
►Dispose of the device in accordance with nationally applicable environmen-
tal regulations.
2.5.1 Retrofitting and conversion
Unauthorized conversion voids any warranty. This can cause hazards that can lead to
severe or even fatal injury.
2.5.2 Basic safety regulations
The safety regulations listed below must always be complied with. In the event that these safety
regulations are not complied with or the device is used improperly, DINA Elektronik GmbH
accepts no liability for any resulting injury or damage.
The product described here has been developed to perform safety-related functions as
part of an entire system.
The entire system is made up of sensors, analysis units, reporting units and safe switch-
off concepts.
It is the responsibility of the manufacturer of a system or machine to validate the correct
overall function.
The manufacturer of the system is obligated to check and document the efficacy of the
implemented safety concept within the entire system. This documentation must be pro-
duced again every time the safety concept or safety parameters are modified.
The manufacturer's specifications for the system or machine with regard to maintenance
intervals must be complied with.
DINA Elektronik GmbH is not able to make any guarantees regarding the properties of
an overall system not designed by the company.

2 Safety
SAFEONE DN3PD2 Manual 8
DINA Elektronik GmbH accepts no liability for any recommendations given or implied in
the following description.
No new guarantee, warranty or liability claims that go beyond DINA Elektronik GmbH's
general delivery conditions can be derived from the following description.
To prevent EMC disturbances, the physical environmental and operating conditions
where the product is installed must correspond to the EMC section of DIN EN 602041.
If contact outputs are used, the safety function must be requested at least once per
month for Performance Level (e) and once per year for Performance Level (d).
2.6 Working on live parts
WARNING
Electric shock –dangerous voltage! Touching live components can cause se-
vere or even fatal injury, depending on circumstances, as a result of an electric
shock.
►Never assume that a circuit is dead.
►Always check circuits as a safety precaution! Components being worked on
may only be live if this is absolutely necessary and stipulated.
►Accident prevention regulations (e.g. VBG4 and VDE 105) must be ob-
served during all work.
►Only use suitable, intact tools and measuring equipment.

2 Safety
SAFEONE DN3PD2 Manual 9
3 EC declaration of conformity

4 Product description
SAFEONE DN3PD2 Manual 10
4 Product description
The SAFEONE DN3PD2 is a safety switchgear for sensorless speed monitoring of electric
drives.
The readiness for operation and the switching status of the contact outputs are displayed
via LEDs.
The device has a standard USB connection. The configuration software GO:BEYOND
enables a simple parameterization and online monitoring.
The device is intended for mounting on a 35mm standard rail.
4.1 Function description
The two-channel evaluation unit of the safety switchgear module measures the frequen-
cy of the effective rotating field of the motor at the measuring terminals U, V, W.
After applying the operating voltage (24 V DC) to terminals A1 and A2, the safety relay
will operate a self-test. The safety relay is in safe condition for the duration of the self-
test. The LED OK lights up red.
The device is ready for operation, when the LED OK lights up green.
If the parameterized switching threshold frequencies are exceeded or undershot (fmin
and fmax), or an internal or external fault exists, the enabling current paths 13/14, 23/24
open immediately. The device is in safe switching state.
4.1.1 Speed monitoring
The parameters fmax (maximum frequency) and fmin (minimum frequency) define the speed
limits of the motor. The limit frequencies fmax and fmin are calculated from the speed n and the
number of pole pairs:
f [Hz]= (n [U/min] / 60) x number of pole pairs
Example: 5000 rev /min x 3 (number of pole pairs) / 60 = 250Hz
Asynchronous motors have a load-dependent slip between the motor speed and the rotating
field frequency. This must be observed by the configuration of the switching threshold (fmin and
fmax).
CAUTION
Note that the method of frequency measurement does not recognize a mechani-
cally blocked motor or an overloaded motor!
The following monitoring functions are possible:
Monitoring only at maximum speed
Monitoring of a speed range with startup monitoring

4 Product description
SAFEONE DN3PD2 Manual 11
Monitoring of a speed range without startup monitoring
fmin: minimum frequency
If fmin is undershot, the output contacts (13-14 / 23-24) switch off.
They switch on again after the acknowledgment via the acknowledgment input Q.
Depending on the acknowledgment mode, the switch-on-conditions differ. Please note the
chapter "Startup monitoring". If fmin = 0 there is no monitoring to a minimum speed. The output
contacts remain closed at standstill.
fmax: maximum frequency
If fmax is exceeded, the output contacts (13-14 / 23-24) switch off.
They switch on again after the acknowledgment via the acknowledgment input Q, if fmax (minus
hysteresis) is undershot.
CAUTION
Note that a coasting motor is detected either as a standstill (if fmin = 0, no switch-off)
or underrun (if fmin> 0, switch-off).
4.2 Acknowledge function
The acknowledgment function allows the module to be reset to operational readiness after a
shutdown due to under- or overspeed. The reset takes place via the input Q at the module, if
none of the mentioned states is pre-sent.
Automatic or manual acknowledgment is possible. With automatic acknowledgment, the Q input
must always be connected to 24V DC.
A manual acknowledgment takes place after a falling signal edge at the input Q (tQ ≥ 200ms
and ≤ 10s).
4.3 Start-up monitoring
The startup monitoring time tAis a time limit within which the actual speed must be greater than
fmin. If the minimum speed is not reached during this time, the enable current path opens
again.
The start-up monitoring time is parameterized (0s to 60s). It is not retriggerable, it cannot be
restarted while it is running.
The start-up monitoring time starts
In case of manual acknowledgment: with the falling edge of the acknowledge signal
In case of automatic acknowledgment: if the actual speed is> 1Hz
In the acknowledgment mode without startup monitoring (0s), the outputs only switch on within
the permitted range.

4 Product description
SAFEONE DN3PD2 Manual 12
4.3.1 Functional diagram with start-up monitoring
Automatic acknowledgement
(fmin must be at least 1,1Hz !)
Manual acknowledgement
Hysteresis
t
f
Q-aut om.
fmax
13/14, 23/24
1Hz
0,5 Hz
fmin
Hysteresis
tA>tmin <tmin
tA
1 2 3 54 6 7 8
Hysteresis
t
f
Q-manual
fmax
13/14, 23/24
fmin
Hysteresis
tAtAtA
1 2 3 54 6 7 8
tQ
1
Start-up monitoring time starts if f>1Hz
1
Start-up monitoring time starts with the falling
edge of the acknowledgement signal.
2
Start-up monitoring time is expired. Enabling
current path remains closed because f>fmin.
2
Start-up monitoring time is expired. Enabling
current path remains closed because f>fmin.
3
Enabling current path opens because f<fmin
3
Enabling current path opens because f<fmin.
4
Enabling current path closes, if f<0,5Hz.
4
Start-up monitoring time starts with the falling
edge of the acknowledgement signal.
5
Start-up monitoring time starts if f>1Hz.
5
Start-up monitoring time is expired. Enabling
current path opens because f < fmin1.
6
Start-up monitoring time is expired. Enabling
current path opens because f < fmin.
6
Start-up monitoring time starts again.
7
The setpoint speed was reached outside of
the minimum switch-off time. Enabling cur-
rent path closes.
7
Start-up monitoring time is expired. Enabling
current path remains closed.
8
The setpoint speed was reached within the
minimum switch-off time. Enabling current
path closes after 0.5s.
8
Enabling current path closes because
fmin < f < fmax
4.3.2 Functional diagram without start-up monitoring
Hysteresis
t
Q-man tQ
tQ
tQ
f
Q-aut o
fmax
fmin
Hysteresis
13/14, 23/24
13/14, 23/24

4 Product description
SAFEONE DN3PD2 Manual 13
4.4 Switch-off delay
Optionally, you can set a switch-off delay tV from 0s to 2s for the enable current path. The
switch-off delay time starts if a speed limit is reached. During this time, the enable contacts re-
main closed and the "SPEED" LED flashes. When the switch-off delay time is expired, the ena-
ble current path opens.
If the speed reaches the target range during the switch-off delay time, the contacts remain
closed and the switch-off delay time is reset.
CAUTION
Note that changing the switch-off delay affects the reaction time of the safety function!
Note
The switch-off delay time is not started when the shutdown occurs due to an internal
or external fault.
4.5 Switch-on delay
Optionally, you can set a switch-on delay tE from 0s to 10s for the enable current path. The
switch-on delay time starts, if the frequency is in range and the acknowledgement is done. Dur-
ing this time, the enable contacts remain open and the "SPEED" LED flashes.
When the switch-on delay time is expired, the enable current path closes.
If you have also selected the "Start-up monitoring" function, the outputs only switch on after the
switch-on delay time has expired. Only then is the start-up monitoring active.
Hysteresis
t
Q-man
f
Q-aut o
fmax
fmin
Hysteresis
13/14, 23/24
13/14, 23/24
tVtEtVtEtE
tEtVtEtVtE
tE= switch-on delay tV= switch-off delay

4 Product description
SAFEONE DN3PD2 Manual 14
4.6 Advanced settings
Application dependent disturbances (e.g., vibrations or frequency overshoots) can adversely
affect the measurement process. This can lead to unintentional shutdowns. To ensure availabil-
ity in the case of faulty applications, you can adjust the parameters
Number of measuring cycles
Measurement sensitivity
Number of measuring cycles
In the settings “measuring accuracy” you set the number of measuring cycles to detect the
movement. The parameter determines with how many measurements the measured value is
formed before it is switched off.
This multiple measurement has no influence on the switch-on behavior. Switching on takes
place after one measuring cycle.
Default setting: 3 measuring cycles at frequencies > 30Hz
Maximum number of measuring cycles: 4
CAUTION
The set factor is multiplied by the measuring time of the system and influences the
reaction time of the safety relay.
Few measuring cycles = short reaction time due to fast measuring value formation, but more
prone to external disturbances
One measuring cycle = fastest reaction time
Many measuring cycles = long system reaction time but robust measurement
You can change the number of measuring cycles in the configuration software. You also define
from which frequency this number should be valid.
Below this frequency, a single measurement is always used.
Sensitivity
Change these parameters only after consultation with the DINA Elektronik GmbH service.
4.7 Minimum switch-off time
The minimum switch-off time tmin is the time that the enable current path is at least open after
triggering before it switches on again. It is 0.5s.

4 Product description
SAFEONE DN3PD2 Manual 15
4.8 Password
The transfer of the parameters and the validation function can be password protected. The
password can contain a maximum of 8 characters.
4.9 Validation
To validate the safety function, a validation tool is available in the configuration software.
With this function, the limit values fmax and fmin are reduced or increased by 10%, 20% or
30%, thereby forcing a switch-off.
The validation requires the entry of the device password.
Note
The validation displays the actual frequency, not the actual speed.
The relation actual frequency to speed (taking into account the number of poles and
the gear factor) may have to be additionally validated.
4.10 Display
The safety switchgear indicates its operational readiness and the status of the enabling current
path by the two-color LEDs "OK" and "SPEED".
4.11 Diagnosis
In conjunction with the configuration software, diagnostics offers the following functions:
Reading out values from the safety switchgear during operation
Reading out data which are relevant for switch-off
4.12 Signal outputs
You can use the signal outputs O1 and O2 to control e.c. a non-safety PLC or signal units.
The message outputs have the following properties:
digital
potential-bound
short circuit and overload protection
not safety-related
The output O1 indicates the state of the enabling current path.
The output O2 indicates the operational readiness. This switches off in case of an error.
Table of contents
Other DINA Relay manuals
Popular Relay manuals by other brands
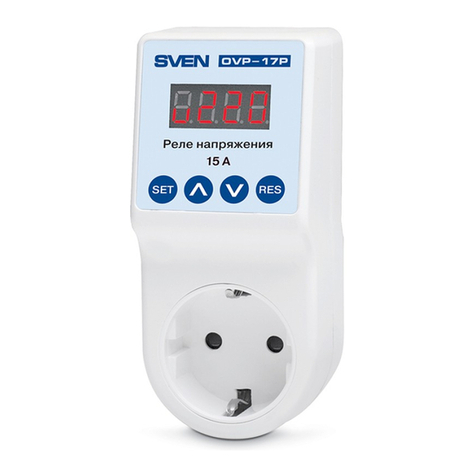
Sven
Sven OVP-17P user manual
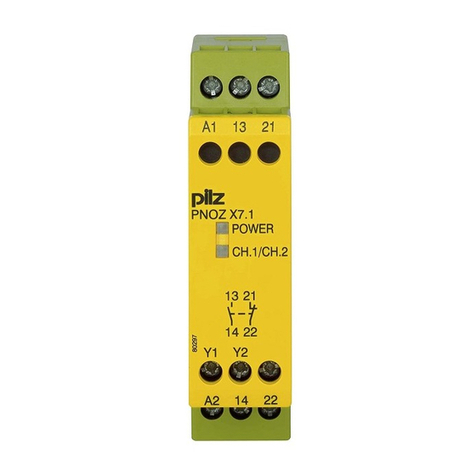
Pilz
Pilz PNOZ X7.1 operating instructions
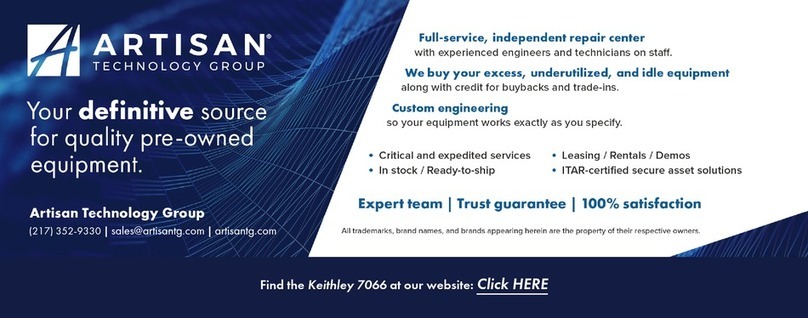
Keithley
Keithley 7066 instruction manual
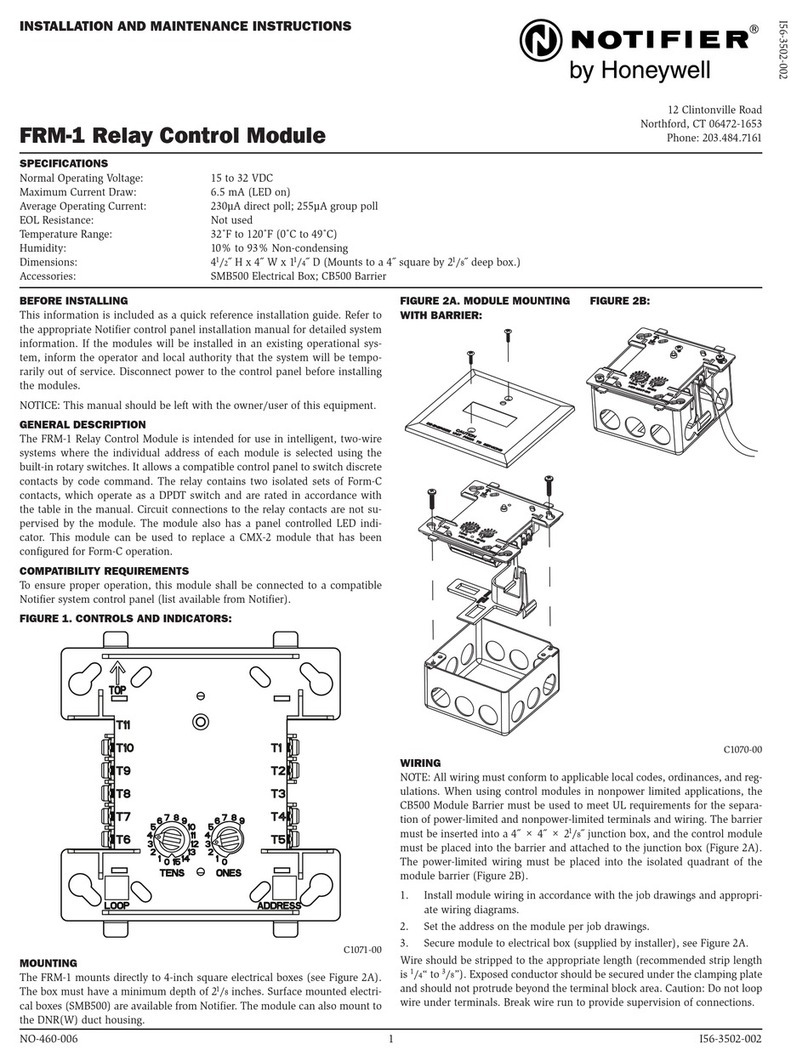
Honeywell
Honeywell NOTIFIER FRM-1 Installation and maintenance instructions

Siemens
Siemens SIRIUS 3TX7680-1A Original operating instructions
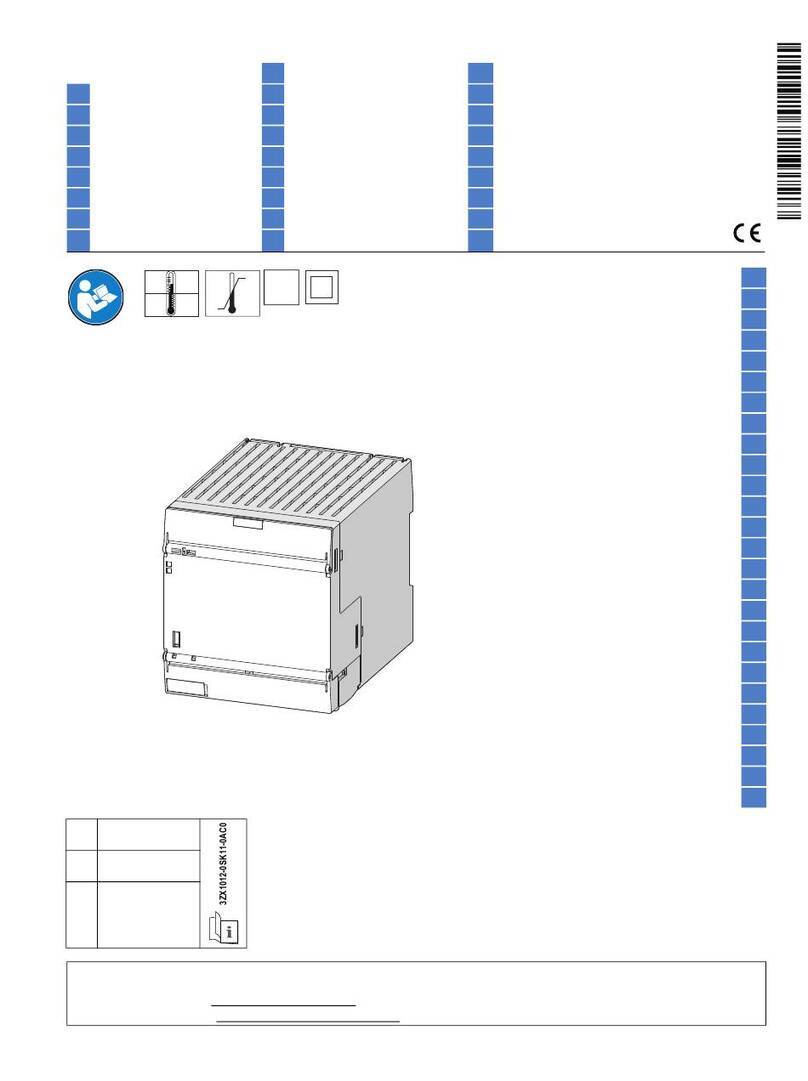
Siemens
Siemens SIRIUS 3SK1213-A 0 Series Original operating instructions