DR 22-Ton Quick start guide

Read and understand this manual and all instructions before operating the DR Horizontal/Vertical Log Splitter.
Original Language
DR®
HORIZONTAL/VERTICAL LOG SPLITTER
SAFETY & OPERATING INSTRUCTIONS
Models: 22-Ton
28-Ton
34-Ton
Serial No.
Order No.
DR Power Equipment
Toll-free phone: 1-800-DR-OWNER (376-9637)
Fax: 1-802-877-1213
Website: www.DRpower.com

2DR® HORIZONTAL/VERTICAL LOG SPLITTER
This indicates a hazardous situation, which, if not avoided, could result in death or serious injury.
Table of Contents
Chapter 1: General Safety Rules............................................................................................................................................................ 3
Chapter 2: Assembly and Setting Up The DR HORIZONTAL/VERTICAL LOG SPLITTER................................................................. 7
Chapter 3: Operating The DR HORIZONTAL/VERTICAL LOG SPLITTER ......................................................................................... 18
Chapter 4: Maintaining the DR HORIZONTAL/VERTICAL LOG SPLITTER ....................................................................................... 24
Chapter 5: Troubleshooting .................................................................................................................................................................. 28
Chapter 6: Parts Lists and Schematic Diagrams.................................................................................................................................. 31
Conventions used in this manual
Serial Number and Order Number
A Serial Number is used to identify your machine and is located on the Serial
Number Label on your machine (Figure 1). An Order Number is used to check
and maintain your order history and is located on your packing slip. For your
convenience and ready reference, enter the Serial Number and Order Number in
the space provided on the front cover of this manual.
Additional Information and Potential Changes
DR Power Equipment reserves the right to discontinue, change, and improve its products at any time without notice or obligation
to the purchaser. The descriptions and specifications contained in this manual were in effect at printing. Equipment described
within this manual may be optional. Some illustrations may not be applicable to your machine.
Figure 1
Serial
Number
Label
This information is important in the proper use of your machine. Failure to follow this instruction could result in damage to
your machine or property.
This indicates a hazardous situation, which, if not avoided, could result in minor or moderate injury.
This indicates a hazardous situation, which, if not followed, will result in death or serious injury.

CONTACT US AT w w w .D Rpow e r.com 3
Read this Safety & Operating Instructions manual before you use the DR HORIZONTAL/VERTICAL LOG SPLITTER. Become
familiar with the operation and service recommendations to ensure the best performance from your machine. If you have any
questions or need assistance, please contact us at www.DRpower.com or call toll-free 1-800-DR-OWNER (376-9637) and one of
our Technical Support Representatives will be happy to help you.
California Proposition 65:
Engine exhaust and some of its constituents are known to the state of California to cause cancer, birth defects, and other
reproductive harm.
This product contains or emits chemicals known to the state of California to cause cancer, birth defects, and other
reproductive harm.
Chapter 1: General Safety Rules
Labels
Your DR HORIZONTAL/VERTICAL LOG SPLITTER carries prominent labels as reminders for its proper and safe use. Shown
below are copies of all the Safety and Information labels that appear on the equipment. Take a moment to study them and make a
note of their location on your LOG SPLITTER as you set up and before you operate the unit. Replace damaged or missing safety
and information labels immediately.
California Proposition 65
#33368
#33457

4DR® HORIZONTAL/VERTICAL LOG SPLITTER
Operating this Log Splitter safely is necessary to prevent or minimize the risk of death or serious injury. Unsafe operation can
create a number of hazards for you. Always take the following precautions when operating this Log Splitter:
Always wear protective goggles or safety glasses with side shields while using the Log Splitter to protect your eyes from
possible thrown debris.
Avoid wearing loose clothing or jewelry, which can catch on moving parts.
We recommend wearing gloves while using the Log Splitter. Be sure your gloves fit properly and do not have loose cuffs or
drawstrings.
Wear shoes with non-slip treads when using your Log Splitter. If you have safety shoes, we recommend wearing them. Do
not use the machine while barefoot or wearing open toed sandals.
Wear long pants while operating the Log Splitter.
Use ear protectors or ear plugs rated for at least 20 dba to protect your hearing.
Protecting Yourself and Those Around You
Safety for Children and Pets
Hydraulic Safety
Tragic accidents can occur if the operator is not alert to the presence of children and pets. Children are often attracted to the
machine and the splitting activity.
Never
assume that children will remain where you last saw them. Always follow these
precautions:
Keep children and pets at least 50 feet from the working area and ensure they are under the watchful care of a responsible
adult.
Be alert and turn the machine off if children or pets enter the work area.
Never allow children to operate the Log Splitter.
High fluid pressures are developed in hydraulic machines. Pressurized hydraulic fluid escaping through a pin hole opening can
puncture skin and cause severe blood poisoning. Therefore, the following Instructions should be heeded at all times.
Do not operate the unit with frayed, kinked, cracked or damaged hoses, fittings, or tubing. Stop the engine, wait 5 minutes
and relieve hydraulic system pressure by cycling the valve control lever from forward to reverse several times and returning to
neutral while engine is not running before changing or adjusting fittings, hoses, tubing, or other system components.
Do not change any Log Splitter relief valve settings. They are set at the factory for best Splitter performance and safety.
Do not check for leaks with your hand. Leaks can be located by passing cardboard or wood over the suspected area: Look for
discoloration. If injured by escaping fluid, see a doctor at once. Serious infection or reaction can develop if proper medical
treatment is not administered immediately.
Always wear safety glasses to protect your eyes from hydraulic fluid.
NEVER remove the cap from the hydraulic tank or reservoir while the log splitter is running. The tank could contain hot oil
under pressure which could result in serious injury.
This machine was built to be operated according to the safe operation practices in this manual. As with any type of power
equipment, carelessness or error on the part of the operator can result in serious injury. This machine is capable of
amputating hands and feet and throwing debris. Failure to observe the following safety instructions could result in serious
injury or death.
Many accidents occur when more than one person operates the machine. No helper is allowed to assist with splitter controls
or handling the logs.

CONTACT US AT w w w .D Rpow e r.com 5
Gasoline is a highly flammable liquid. Gasoline also gives off flammable vapor that can be easily ignited and cause a fire or
explosion. Never overlook the hazards of gasoline. Always follow these precautions:
Never run the engine in an enclosed area or without proper ventilation as the exhaust from the engine contains carbon
monoxide, which is an odorless, tasteless, and deadly poisonous gas.
Store all fuel and oil in containers specifically designed and approved for this purpose and keep away from heat and open
flame, and out of the reach of children.
Replace rubber fuel lines and grommets when worn or damaged and after 5 years of use.
Fill the gasoline tank outdoors with the engine off and allow the engine to cool completely. Don't handle gasoline if you or
anyone nearby is smoking, or if you're near anything that could cause it to ignite or explode. Reinstall the fuel tank cap and
fuel container cap securely and Never remove gas cap while the engine is hot or running.
If you spill gasoline, do not attempt to start the engine. Move the machine away from the area of the spill and avoid creating
any source of ignition until the gas vapors have dissipated. Wipe up any spilled fuel to prevent a fire hazard and properly
dispose of the waste.
Allow the engine to cool completely before storing in any enclosure. Never store a machine that has gas in the tank, or a fuel
container, near an open flame or spark such as a water heater, space heater, clothes dryer or furnace.
Never make adjustments or repairs with the engine running. Shut down the engine, disconnect the spark plug wire, keeping it
away from the spark plug to prevent accidental starting, wait 5 minutes before making adjustments, repairs or refueling.
Never tamper with the engine’s governor setting. The governor controls the maximum safe operation speed and protects the
engine. Over-speeding the engine is dangerous and will cause damage to the engine and to the other moving parts of the
machine. If required, see your authorized dealer for engine governor adjustments.
Keep combustible substances away from the engine when it is hot.
Never cover the machine while the muffler is still hot.
Do not operate the engine with the air cleaner or the carburetor air intake cover removed. Removal of such parts could create
a fire hazard. Do not use flammable solutions to clean the air filter.
The muffler and engine become very hot and can cause a severe burn; do not touch.
Safety with Gasoline - Powered Machines
Towing
ALWAYS check before towing to make certain your Splitter is correctly and securely attached to the towing vehicle. Be sure
that the ball hitch you are using is the proper size for the hitch coupler on the machine. Be sure the safety chains are properly
hooked to the vehicle leaving enough slack for turning.
Always use a Class I, 2” ball with this log splitter and replace the ball or coupler if damaged.
Always confirm coupler tightness each time before towing and after towing 50 miles.
ALWAYS use accessory lights and devices when transporting on a road or highway to warn operators of other vehicles. Check
your local government regulations for DOT information.
ALWAYS allow for added length of the Splitter when turning, parking, crossing intersections, and in all driving situations.
ALWAYS be careful when backing up. You could jackknife your Splitter if care is not taken.
NEVER exceed 45 mph. when towing your Splitter. Obey all state and local regulations when towing on state and local roads
and highways. Adjust your speed for terrain and conditions, as needed. Be extra cautious when towing over rough terrain,
especially over a railroad crossing.
NEVER allow anyone to sit or ride on your Splitter.
NEVER carry any cargo or wood on your Splitter.
Do travel slowly over rough terrain, on hillsides, and around curves to prevent tipping.
Do not tow the Splitter near the edge of a ditch or excavation.
ALWAYS turn the fuel shut off valve on the engine to the “OFF” position before towing the log splitter. Failure to do so may
result in flooding the engine.

6DR® HORIZONTAL/VERTICAL LOG SPLITTER
General Safety
A Note to All Users
Under California law, and the laws of some other states, you are not permitted to operate an internal combustion engine using
hydrocarbon fuels without an engine spark arrester. This also applies to operation on US Forest Lands. All DR
HORIZONTAL/VERTICAL LOG SPLITTERS shipped to California, New Mexico and Washington State are provided with spark
arresters. Failure of the owner or operator to maintain this equipment in compliance with state regulations is a misdemeanor
under California law and may be in violation of other state and/or federal regulations. Contact your State Park Association or the
appropriate state organization for specific information in your area. If the engine is equipped with a spark arrestor, clean and
inspect it regularly according to manufacturer’s instructions. Replace if damaged.
No list of warnings and cautions can be all-inclusive. If situations occur that are not covered by this manual, the operator must
apply common sense and operate this DR HORIZONTAL/VERTICAL LOG SPLITTER in a safe manner. Contact us at
www.DRpower.com or call 1-800-DR-OWNER (376-9637) for assistance.
This is a high-powered machine, with moving parts operating with high energy. You must operate the machine safely. Unsafe
operation can create a number of hazards for you, as well as anyone else in the nearby area. Always take the following precautions
when using this machine:
Keep in mind that the operator or user is responsible for accidents or hazards occurring to other people, their property, and
themselves.
Your Log Splitter is a powerful tool, not a plaything. Exercise extreme caution at all times. The machine is designed to split
logs. Do not use it for any other purpose.
Know how to stop the Log Splitter quickly; see “stopping the engine” in chapter 3.
Never operate your unit on a slippery, wet, muddy, or icy surface. Exercise caution to avoid slipping or falling.
See manufacturer’s instructions for proper operation and installation of accessories. Only use accessories approved by DR
Power Equipment.
Never use the machine without ensuring that all guards and shields are in place.
Never, under any conditions, remove, bend, cut, fit, weld, or otherwise alter standard parts on the Log Splitter. This includes
all shields and guards. Modifications to your machine could cause personal injuries and property damage and will void your
warranty.
Allow only one person to operate the Log Splitter at any time. The adult who loads and stabilizes the log must be the person
who operates the control handle.
If the machine should start making an unusual noise or vibration, shut down the engine, disconnect the spark plug wire,
keeping it away from the spark plug to prevent accidental starting, wait 5 minutes for machine to cool down, then inspect for
damage. Vibration is generally a warning of trouble. Check for damaged parts and clean, repair and replace as necessary.
Never tamper with safety devices. Check their proper operation regularly.
Before performing any maintenance or inspection procedure on the Log Splitter shut down the engine, disconnect the spark
plug wire keeping it away from the spark plug to prevent accidental starting, wait 5 minutes for machine to cool down.
Never allow people who are unfamiliar with these instructions to use the Log Splitter. Allow only responsible individuals who
are familiar with these rules of safe operation to use your machine.
Never overload or attempt to split logs beyond the recommendations listed in this manual. Personal injury or damage to the
machine could result.
While using the Log Splitter, don't hurry or take things for granted. When in doubt about the equipment or your
surroundings, stop the machine and take the time to look things over.
Never operate the machine when under the influence of alcohol, drugs, or medication.
Use the machine only in daylight.
Stay alert for hidden hazards or traffic.
Keep all nuts and bolts tight and keep the equipment in good operating condition.
Never leave this machine unattended with the engine running.

CONTACT US AT w w w .D Rpow e r.com 7
Horizontal
Beam Lock
J
ack Stan
d
Hitch
Receiver
Control Handle
Splitting Wedge
Log Dislodger
Cylinder
End Plate
Log Tray
Vertical
Beam Lock
Hydraulic Oil
Reservoir
Road Tow
Wheels
Hydraulic Oil
Fill/Check
Hydraulic
Pump
Chapter 2: Assembly and Setting Up The DR HORIZONTAL/VERTICAL LOG SPLITTER
It may be helpful to familiarize yourself with the controls and features of your DR HORIZONTAL/VERTICAL LOG SPLITTER as
shown in Figure 2 before beginning these procedures. If you have any questions at all, please feel free to contact us at
www.DRpower.com.
DR HORIZONTAL/VERTICAL LOG SPLITTER Controls and Features
Figure 2
Fuel Shut-off
Valve
Choke
Control
Leve
r
Throttle Control
Lever
Recoil Starter
Handle

8DR® HORIZONTAL/VERTICAL LOG SPLITTER
Specifications
Model 22 Ton 28 Ton 34 Ton
Engine See engine manual See engine manual See engine manual
Pump Two-Stage, 10gpm Two-Stage, 10 gpm Two-Stage, 15 gpm
Cylinder (Bore x Stroke) 4 in. x 24 in. 4.5 in. x 24 in. 5 in. x 24 in.
Maximum Splitting Force 22 Tons* 28 Tons* 34 Tons*
Hydraulic Pressure 3400 psi* 3450 psi* 3500 psi*
Maximum Log Length 25 in. 25 in. 25 in.
Wedge Height 8 in. 8 in. 8 in.
Cycle Time Forward 8 Seconds* 8 Seconds* 7 Seconds*
Reverse 5 Seconds* 5 Seconds* 4 Seconds*
Wheels 16 x 4.8 x 8 in. 16 x 4.8 x 8 in. 16 x 4.8 x 8 in.
Hydraulic Capacity Approx. 4 Gallons Approx. 4 Gallons Approx. 5 Gallons
Height (Horizontal / Vertical Position) 41.5 / 71 in. 41.5 / 71 in. 41.5 / 71 in.
Length (Horizontal / Vertical Position) 87 / 84 in. 87 / 84 in. 87 / 84 in.
Width 41 in. 41 in. 41 in.
Net Weight 474 lbs 512 lbs 549 lbs
*Tonnage and cycle times may vary dependent upon mechanical and environmental conditions.

CONTACT US AT w w w .D Rpow e r.com 9
Due to the weight / size of the log splitter, it’s recommended that two or more adults be present to assist with assembling.
Assembly
Tools and Supplies Needed:
Two 13mm Wrenches
Two 14mm Wrenches
16mm Wrench
17mm Wrench
18mm Wrench
19mm Wrench
27mm Wrench
1/2" Wrench
Adjustable Wrench
Needle Nose Pliers
3mm Allen Wrench
Flat Head Screwdriver
Soft Faced Hammer
Thread Locking Compound
Installing the Fenders
Parts Supplied in Hardware Kit #1 (Figure 3):
Item # Part # Description Qty
1 .............33703 ..............Bolt, Hex, M8 X 25 ................................ 8
2 .............30247 ..............Washer, Flat, M8 ................................... 16
3 .............30246 ..............Nut, Nylon Lock, M8............................. 8
4 .............33689 ..............Support, Fender .................................... 2
Compare the contents of the Hardware Kit #1 with the “Parts Supplied” list
above. If you have any questions please contact us at www.DRpower.com or call
1-800-DR-OWNER (376-9637) for assistance.
Note: When installing the Bolts, Washers, and Locknuts, install the Washers so that
one Washer is against the head of the Bolt, and the other Washer is against
the Locknut.
1. Loosely secure the top of the Fender to the Fender Support with a M8 x 25
Bolt, two Flat Washers, and a Locknut (Figure 4).
2. Loosely secure the Fender with the Fender Support to the Reservoir Assembly
as shown using three M8 x 25 Bolts, six Flat Washers, and three Locknuts.
3. Use two 13mm Wrenches to tighten the Hardware.
4. Repeat these steps for the other Fender
Installing the Wheels
Parts Supplied in Hardware Kit #2 (Figure 5):
Item # Part # Description Qty
1 .............33714 ..............Hub Cap ................................................ 2
2 .............25310 ..............Nut, Castle, 1-14.................................... 2
3 .............33755 ..............Pin, Cotter.............................................. 2
Compare the contents of the Hardware Kit #2 with the “Parts Supplied” list
above. If you have any questions please contact us at www.DRpower.com or
call 1-800-DR-OWNER (376-9637) for assistance.
Figure 5
1
2 3
Figure 3
1
2
3
4
Figure 4
Reservoir
A
ssembly
Fende
r
M8 Bolts, Flat
Washers and
Locknut
s
Fender
Support

10 DR® HORIZONTAL/VERTICAL LOG SPLITTER
1. Remove the plastic shipping caps from the Wheels. Make sure the bearing
remains seated when removing the cap. If the bearing comes out with the
cap, reinsert it into the hub.
2. Block the reservoir assembly up off the ground and position a wheel onto the
axle (valve stem facing out) (Figure 6).
3. Screw the Castle Nut onto the Axle and tighten it with an Adjustable Wrench
to seat the Bearing.
4. Back the Castle Nut off and then snug it up to the Bearing lightly.
5. Insert a Cotter Pin through the slots of the Castle Nut and into the hole in
the Axle.
6. Bend the ends of the cotter pin with Needle Nose Pliers so they are tight
against the Castle Nut.
7. Tap the Dust Cap onto the wheel using a Soft Faced Hammer (Figure 7).
8. Repeat these steps for the other Wheel.
Installing the Tow Bar
Parts Supplied in Hardware Kit #3 (Figure 8):
Item # Part # Description Qty
1 ............. 33712 .............. Horizontal Beam Lock .......................... 1
2 ............. 33705 .............. Bolt, Hex, M10 X 80 .............................. 4
3 ............. 30250 .............. Washer, Flat, M10 ................................. 8
4 ............. 30249 .............. Nut, Nylon Lock, M10........................... 4
Compare the contents of the Hardware Kit #3 with the “Parts Supplied” list
above. If you have any questions please contact us at www.DRpower.com or call
1-800-DR-OWNER (376-9637) for assistance.
Note: When installing the Bolts, Washers, and Locknuts, install the Washers so that
one Washer is against the head of the Bolt, and the other Washer is against the
Locknut.
1. Remove the Pin and Hitch Clip that locks the Jack Stand in place (Figure 9).
Rotate the Jack Stand down and secure it with the Pin and Hitch Clip.
2. Secure the Rear of the Tow Bar to the Reservoir Assembly using two M10 x
80 Bolts, four Flat Washers, and two Locknuts. Tighten the Hardware using a
16mm Wrench for the Bolt and a 17mm Wrench for the Locknut.
Note: In the next step, the Horizontal Beam Lock must be installed with the handle
on the RIGHT SIDE as shown in Figure 9. The slot in the beam bracket will only
latch properly to the handle if it is installed as shown.
3. Install the Horizontal Beam Lock onto the Tow Bar as shown using two M10
x 80 Bolts, four Flat Washers, and two Locknuts. Tighten the Hardware using
a 16mm Wrench for the Bolt and a 17mm Wrench for the Locknut.
1 2
3
4
Figure 8
Dust Cap
Figure 7
Figure 6
Castle
Nut
Cotter Pin
A
xle
Valve
Stem
Figure 9
Horizontal
Beam Lock
Handle
this
Side
Bolts, Flat
Washers and
Locknuts
Reservoir
A
ssembly
Bolts, Flat
Washers and
Locknuts
J
ack Stan
d
Pin and
Hitch
Clip

CONTACT US AT w w w .D Rpow e r.com 11
Installing the Pump Assembly
Parts Supplied in Hardware Kit #4 (Figure 10):
Item # Part # Description Qty
1 .............33739 ..............Two Stage Pump Assembly (22 and 28 Ton) ....... 1
33740 ..............Two Stage Pump Assembly (34 Ton) ................... 1
2 .............13286 ..............Bolt, Hex, 5/16-24 ................................................. 4
3 .............30247 ..............Washer, Lock, M8.................................................. 4
4 .............11243 ..............Washer, Flat, M8 ................................................... 4
5 .............35476 ..............O-Ring, 11mm X 2mm.......................................... 2
Compare the contents of the Hardware Kit #4 with the “Parts Supplied” list
above. If you have any questions please contact us at www.DRpower.com or call
1-800-DR-OWNER (376-9637) for assistance.
Note: The O-Rings (Item 5) in Hardware Kit #4 are to be used in the “Installing the
Hydraulic Hoses” section in this Chapter. Set the O-Rings aside in a secure
place until you reach this step.
1. Remove the Engine from its box and place it on a level service.
2. Slowly pull on the engine starter cord to position the key slot at the top of the
shaft (Figure 11).
3. Using a soft face hammer, gently tap the Key (located in the Engine Box) into
the Key Slot on the Engine Shaft.
4. The Coupling may have separated during shipping. Ensure that the two
Coupling Halves are together with the Nylon Insert in the center (Figure 12).
5. Position the Pump Assembly, with the opening facing up, onto the Engine
Shaft so that the key slides into the Coupling (Figure 13). Push the Pump
Assembly onto the shaft until the Pump Mount is flush with the Engine.
Temporarily install a 5/16-24 Bolt to hold the Pump against the Engine.
6. Use a 3mm Allen Wrench to remove one of the Set Screws on the Coupling.
Apply thread lock to the Set Screw and reinstall it. Tighten the Set Screw to
secure the Coupling. Repeat this step for the other Set Screw.
Note: If the Threaded Fitting on the Pump is already on top as shown in Figure 14,
skip step 7 and continue to step 8.
7. Remove the Bolt installed in Step 5. Rotate the Pump Assembly so that the
Threaded Fitting is on the top of the Pump (Figure 14).
8. Secure the Pump Assembly using four 5/16-24 Bolts, M8 Lock Washers,
and M8 Flat Washers. Tighten the Hardware using a 1/2” Wrench.
9. Remove the plastic Shipping Cap From the bottom of the Pump.
Bolts, Lock
Washers, and
Flat Washers
Figure 14
Shipping
Cap
Threaded
Fitting
Figure 13
Coupling
Pump
A
ssembly
Set Screws
Engine
Sha
f
t
Pump Mount
Nylon
Insert
Bolt
Coupling
Nylon
Insert
Figure 12
Figure 11
Key
1
2
3
4
Figure 10
5

12 DR® HORIZONTAL/VERTICAL LOG SPLITTER
Installing the Engine
Parts Supplied in Hardware Kit #5 (Figure 15):
Item # Part # Description Qty
1 ............. 33702 .............. Bolt, Hex, M8 X 40 (22 and 28 Ton)...........4
36110 .............. Bolt, Hex, M10 X 40 (34 Ton).....................4
2 ............. 30247 .............. Washer, Flat, M8 (22 and 28 Ton)..............8
30250 ..............Washer, Flat, M10 (34 Ton)........................8
3 ............. 30246 .............. Nut, Nylon Lock, M8 (22 and 28 Ton) .......4
30249 ..............Nut, Nylon Lock, M10 (34 Ton) .................4
4 ............. 37768 .............. Isolator, Vibration (22 and 28 Ton)............4
37691 ..............Isolator, Vibration (34 Ton) ........................4
Compare the contents of the Hardware Kit #5 with the “Parts Supplied” list
above. If you have any questions please contact us at www.DRpower.com or call
1-800-DR-OWNER (376-9637) for assistance.
Note: When installing the Bolts, Washers, and Locknuts, install the Washers so that
one Washer is against the head of the Bolt, and the other Washer is against the
Locknut.
1. Position the Engine with Pump Assembly onto the Engine Mount as Shown
(Figure 16). Insert a Vibration Isolator between the Engine and Mount at the
four mounting hole locations.
Note: The Kohler engines use M8 hardware and the Briggs and Stratton engines use
M10. The Kohler engines mount to the smaller 4-hole pattern. The Briggs and
Stratton engines mount to the larger 4-hole pattern.
2. Secure the engine with four bolts, eight flat washers, and four Locknuts
(Figure 17). For the 22 Ton and 28 Ton models, tighten the hardware using
two 13mm Wrenches. For the 34 Ton models, tighten the hardware using a
16mm Wrench on the Bolt and a 17mm Wrench on the Locknut.
Reservoir
A
ssembly
Engine
Engine
Mount
Figure 16
Four Places
Bolts, Flat
Washers, and
Locknuts (2 on
other side)
Figure 17
1
2
3
Figure 15
4

CONTACT US AT w w w .D Rpow e r.com 13
Take extra care when raising and lowering the beam as it is very heavy.
Having a second person assist with raising or lowering the beam is
recommended to prevent injury. Be sure to keep hands away from any
p
ossible
p
inch
p
oints.
Installing the Beam Assembly
1. Get help from another person to stand the beam upright on a flat level
surface (Figure 18). Have the helper support the beam as you perform the
following steps.
2. Remove the Pin and Hitch Clip from the Beam Support Bracket. Position the
Reservoir Assembly so that the Beam Support Bracket is in between the Tabs
on the Beam Assembly (Figure 19).
3. Slide the Pin through the aligned holes and secure with the Hitch Clip. You
may need to have a helper lift up on the Tow Bar for the Holes to align.
4. Leave the beam in the upright position for the next steps.
Installing the Hydraulic Hoses
Note: There are three hydraulic hoses listed below, each of them has one end fixed
on the fitting by the manufacturer, the other end needs to be attached. The
Hoses are labeled on the ends for easy installation.
1. Oil Suction Hose, labeled as ①, comes from the bottom of the Oil Reservoir
(Figure 20). Loosen the Hose Clamp on the open end of this hose using a
flat head Screwdriver and connect the hose to the fitting on the bottom of
the Pump. Tighten the hose clamp.
2. Pump/Valve Connecting Hose, labeled as ②, comes from the bottom of the
valve on the Beam Assembly (Figure 21). Apply some Hydraulic Fluid to the
O-Ring (11mm X 2mm) from Hardware Kit #4 and place the O-Ring into the
groove of the fitting on top of the Pump (Figure 22). Screw the open end of
this hose onto the fitting on top of the pump using a 27mm Wrench (or
adjustable wrench) (Figure 20).
3. Oil Return Hose labeled as ③, comes from the front of the valve on the
Beam Assembly (Figure 21). Apply some Hydraulic Fluid to the O-Ring
(11mm X 2mm) from Hardware Kit #4 and place the O-Ring into the groove
at the end of Threaded Fitting on the Oil Reservoir (Figure 22). Screw the
open end of this hose onto the Oil Reservoir using a 27mm Wrench (or
adjustable wrench) to tighten the hose (Figure 20).
Note: Check all hydraulic hoses at both ends for tightness. Tighten as needed.
Figure 22
O-Ring
O-Ring
Threaded
Fitting
Pump
Oil
Reservoir
Pin and
Hitch Clip
Figure 19
Beam
A
ssembl
y
Reservoir
A
ssembl
y
Pin and
Hitch Clip
Figure 18
Beam
A
ssembl
y
Beam Support
Bracket
Reservoir
A
ssembl
y
Tabs
Figure 20
Oil Suction
Hose ①
Hose
Clamp
Oil Return
Hose ③
Pump/Valve
Connecting
Hose ②
Pump
Oil
Reservoi
r
Figure 21
Oil Suction
Hose ①
Oil Return
Hose ③
Pump/Valve
Connecting
Hose ②

14 DR® HORIZONTAL/VERTICAL LOG SPLITTER
Take extra care when raising and lowering the beam as it is very heavy.
Having a second person assist with raising or lowering the beam is
recommended to prevent injury. Be sure to keep hands away from any
p
ossible
p
inch
p
oints.
Installing the Log Trays
Parts Supplied in Hardware Kit #6 (Figure 23):
Item # Part # Description Qty
1 ............. 33707 .............. Bolt, Hex, M12 X 45 ...................................4
2 ............. 30252.............. Washer, Flat, M12 .......................................8
3 ............. 30253 .............. Nut, Nylon Lock, M12.................................4
4 ............. 33708 .............. Bolt, Hex, M10 X 30 ....................................4
5 ............. 30250.............. Washer, Flat, M10 .......................................8
6 ............. 30249 .............. Nut, Nylon Lock, M10.................................4
Compare the contents of the Hardware Kit #6 with the “Parts Supplied” list
above. If you have any questions please contact us at www.DRpower.com or
call 1-800-DR-OWNER (376-9637) for assistance.
Note: When installing the Bolts, Washers, and Locknuts, install the Washers so that
one Washer is against the head of the Bolt, and the other Washer is against the
Locknut.
1. Tighten the Hardware of the loosely assembled Log Trays using a 16mm
Wrench on the Bolts and a 17mm Wrench on the Locknuts (Figure 24).
2. Get help from another person to lower the beam to the horizontal position.
Refer to the “Beam Operating Positions” Section in Chapter 3 for detailed
information on raising and lowering the Beam.
3. Position a Log Tray onto the Beam as shown and loosely secure the End
Plate with two M10 x 30 Bolts, four M10 Flat Washers, and two M10
Locknuts (Figure 25). Repeat this step for the second Log Tray.
4. Loosely secure the bottom supports to the beam with four M12 x 45 Bolts,
eight M12 Flat Washers, and four M12 Locknuts (Figure 26).
5. Tighten the M12 Hardware using an 18mm Wrench on the Bolt and a 19mm
Wrench on the Locknut.
6. Tighten the M10 Hardware using a 16mm Wrench on the Bolt and a 17mm
Wrench on the Locknut.
Figure 25
Log Trays
M10 Bolts,
Flat Washers,
and Locknuts
Figure 24
Hardware
1
2
3
4
5
6
Figure 23
Figure 26
M12 Bolts, Flat
Washers, and
Locknut
s

CONTACT US AT w w w .D Rpow e r.com 15
Assembling the Control Handle
Note: The control handle is shipped hanging from the valve on the handle link
1. Remove the Pin and Hitch Clip from the Control Valve (Figure 27).
2. Rotate the Control Handle up into the operating position and secure with the
Pin and Hitch Clip.
SET UP
Adding Gas and Oil
Engine Oil See Engine Manual for specific Engine capacities and
specifications
Fuel Unleaded gasoline
NOTE: Use only the recommended high detergent engine oil. Other types of oil
could cause problems operating your machine. Please refer to your Engine
Owner’s Manual for detailed oil information.
Supplies Needed:
Clean Rag
Engine Oil
1. Position the machine so the Engine is level. Remove the Oil Fill/Dipstick
and clean the end of it with a rag (Figure 28).
2. Machines are shipped with no oil. Initially add 16 oz. of the oil
recommended by the Engine Manufacturer. Wait one minute for the oil to
settle.
3. Replace the Dipstick and screw it all the way in to ensure an accurate reading
and then remove it to check the oil level. The Oil is at the proper level when it
reaches the Full mark on the Dipstick (Figure 29). Clean the Dipstick with the
clean rag after checking.
4. Continue adding a few ounces of oil at a time, rechecking the Dipstick until
the oil reaches the Full mark. Be careful not to overfill.
5. Replace the Dipstick and screw all the way down when full.
6. Remove the Gas Fill Cap and fill the Gas Tank with fresh, unleaded gas (with
a minimum of 85 Octane) to approximately 1" to 1-1/2" below the top of the
fill neck to allow for fuel expansion (Figure 28). Be careful not to overfill.
Install the Gas Fill Cap before starting the engine. See your Engine Owner’s
Manual for more detailed information.
Note: To refill the gas tank, turn the engine OFF and let the engine cool at least five
minutes before removing the gas fill cap.
Figure 28
Oil Fill/
Dipstick
Gas Fill
Figure 29
Full
Lo
w
Dipstick
Figure 27
Control Handle
Pin and
Hitch Clip
The Engine must be level to get an accurate reading when adjusting the
amount of oil. If the machine is not level, the oil level reading will not be
accurate and may cause engine damage.

16 DR® HORIZONTAL/VERTICAL LOG SPLITTER
Adding Hydraulic Fluid
Supplies Needed:
Paper Towels
Hydraulic Fluid (see Figure 30)
Note: Use the following instructions only when adding Fluid for the first time. Refer to the “Checking the Hydraulic Fluid Level” section
in Chapter 4 for information on maintaining the Hydraulic Fluid level.
Note: The Hydraulic Oil should be selected based on the outside temperature range
the Log Splitter will be used in. Refer to the chart provided to select the appropriate
Hydraulic Oil (Figure 30).
1. Remove the Reservoir Dipstick, which is located next to the engine on top of
the reservoir tank (Figure 31).
2. Slowly fill the Reservoir tank with the recommended Hydraulic Fluid until the
fluid reaches the Initial Fill Line on the Dipstick (Figure 32). Be Careful not to
overfill.
3. Replace the Dipstick in the Reservoir.
4. Make sure the Engine is in the “OFF” position (refer to Figure 37) and
disconnect the spark plug wire from the spark plug. Prime the pump by
pulling the recoil starter handle (refer to Figure 36) as far as it will go.
Repeat approximately 10 times.
5. Reconnect the spark plug wire and start the engine, following instructions in
Chapter 3.
6. Use the control handle to engage the wedge to the farthest extended
position. Then retract the wedge.
Note: Do not refill the tank to the Initial Fill Line. The fluid level has dropped since
the cylinder was cycled. Refilling to this line will overflow the tank. The proper level
for operation is when the fluid is about 1/4" above the bottom of the Dipstick.
7. Stop the Engine and recheck the fluid level. Add fluid as needed so that the
fluid Level is about 1/4" above the bottom of the dipstick (Figure 32).
Note: Failure to refill the tank to the Operating Level will void the splitter’s
warranty. Do not overfill. The proper level for operation is when the fluid is about
1/4" above the bottom of the Dipstick.
8. Restart the engine and extend and retract the wedge 12 complete cycles to
remove any trapped air in the system (the system is “self- bleeding”).
9. Stop the Engine and refill the tank as needed so the fluid is about 1/4"
above the bottom of the dipstick.
Figure 31
Reservoir
Dipstick
Figure 32
Initial Fill Line
1/4"
Operating Level Reservoir Dipstick
ISO 22
ISO 32
ISO 46
ISO 68
0°
(-18°)
10°
(-12°)
20°
(-7°)
30°
(-1°)
40°
(4°)
50°
(10°)
60°
(16°)
70°
(21°)
80°
(27°)
90°
(32°)
TEMPERATURE FAHRENHEIT (CELSIUS)
HYDRAULIC OIL ISO RECOMMENDATIONS
Figure 30
You must add hydraulic fluid before using the splitter. This machine is shipped without hydraulic fluid in the hydraulic
tank. When performing the following procedures, fill the hydraulic tank slowly, checking the level frequently to avoid
overfilling.
To get an accurate reading when checking the hydraulic fluid level:
- The machine should be on a level surface.
- The dipstick should be pushed in fully to ensure an accurate fluid level reading.
After the initial fill, much of the fluid will be drawn into the cylinder and hoses. Make certain the fluid is at the Operating
Level (Figure 32) to prevent damage to the hydraulic pump. DO NOT OVERFILL.

CONTACT US AT w w w .D Rpow e r.com 17
Lubricating the Beam
Supplies Needed:
Fluid Film
1. Lubricate the Beam area (where the splitting wedge will slide) with Fluid Film
(Figure 33). Do not use Grease.
Check the Tire Pressure
Tools Needed:
Tire Pressure Gauge
Air Compressor
1. Remove the Valve Stem Protective Cap and check the tire pressure with a Tire
Pressure Gauge (Figure 34).
2. Check what the manufacturers recommended pressure is that is stamped on
the side of the Tire.
3. If the pressure is too low, add air through the Valve Stem with an air hose.
4. Replace the Valve Stem Protective Cap when finished.
Figure 33
Beam
Do not over inflate the tires. Inflate to the manufacturers recommended
pressure found on the tires. Valve Stem
Protective Cap
Figure 34

18 DR® HORIZONTAL/VERTICAL LOG SPLITTER
Chapter 3: Operating The DR HORIZONTAL/VERTICAL LOG SPLITTER
It may be helpful to better familiarize yourself with the features of your Log Splitter by reviewing Figure 2 in Chapter 2 before
beginning the steps outlined in this chapter.
Starting the Engine
Note: See the Engine Manual for more detailed and specific information on
operating the Engine.
1. Position your Log Splitter on flat, dry ground and chock the Wheels to
prevent the Splitter from moving during use.
2. Make sure the fuel shut-off valve is in the “ON” position (Figure 36).
3. Move the choke control lever to the CHOKE position to the left (should
only be needed if the engine is cold).
4. Move the throttle control lever to the FAST position.
5. Turn the Ignition Switch to the “On” position (Figure 37). Grasp the recoil
starter handle and slowly pull until you feel resistance (Figure 36). Let the
cord retract a little bit then pull the cord rapidly to start the engine. One or
two pulls usually starts the engine.
6. Move the choke control lever (if used for cold engine) slowly back to the
OPEN position (to the right) when the engine is running well (Figure 36).
Note: If the Log Splitter has not been running (cold engine), warm up the engine by
running the engine at half throttle for 3 to 4 minutes before splitting, then advance
the engine throttle control to maximum speed.
Stopping the Engine
1. Move the Throttle Lever to Idle position (Figure 36).
1. Turn the Ignition Switch to the “Off” position (Figure 37).
Fuel Shut-off
Valve
Figure 36
Choke
Control
Leve
r
Throttle Control
Lever
Recoil Starter
Handle
Ignition
Switch
Figure 35
Operating
Zone
Operator
Zone
Horizontal
Position
(Top View)
Vertical
Position
Read and understand all instructions, safety precautions, and/or
warnings listed in “Chapter 1 General Safety Rules” before operating this
DR HORIZONTAL/VERTICAL LOG SPLITTER. If any doubt or question
arises about the correct or safe method of performing anything found in
this manual, please contact our Customer Service Representatives at our
toll free number: 1-800-DR-OWNER (376-9637).
When operating the Log Splitter, make sure you are standing in the safe
operating area (OPERATOR ZONE) as shown in Figure 35. You must stay
in the safe operating area at all times when the wedge is in motion
(whether extending or retracting). Never place any part of your body into
a position that causes an unsafe operating condition.
Figure 37
Ignition
Switch
On
Of
f
Ignition
Switch
Of
f
On
22 and 28 Ton 34 Ton

CONTACT US AT w w w .D Rpow e r.com 19
Hands on
Sides of
Wood
Figure 41
Handling Wood
Note: All logs should be no longer than 24". Use the following photos for the correct
and incorrect methods of splitting logs. Never split a log using an incorrect or
unsafe method.
Note: The Following Warnings and Instructions apply when Splitting Wood in both
the Horizontal and Vertical Positions.
Figure 40
Figure 39
Figure 38
Do not place your hands on the ends of the log when loading the Log
Splitter. This is a very UNSAFE method and could result in injury to your
hands (Figure 38).
Do not reach or step across the beam while the Log Splitter is running.
This is a very UNSAFE method which could cause personal injury or even
death.
Never attempt to split wood across the grain. The Log Splitter was not
designed for cross-grain splitting. Doing so could damage the Log
Splitter and may cause personal injury (Figure 39).
Make sure both ends of the log you are splitting are cut as square as
possible. This will prevent the log from sliding out of position while under
pressure (Figure 40).
When loading a log, always place your hands on the side of the log, not
on the ends, and never use your foot to help stabilize a log (Figure 41).
Failure to do so, may result in crushed or amputated fingers, toes, hand,
or foot.
When stabilizing log with left hand, remove your hand when the wedge
just contacts the log or serious injury may occur.
NEVER place hands or feet between the log and splitting wedge during
forward or reverse stroke as this could result in serious injury or death.
NEVER attempt to load the log splitter when the ram or wedge is in
motion.
Always keep fingers away from any cracks that open in the log while
splitting. They can quickly close and pinch or amputate your fingers.
Never attempt to remove partially split wood from the wedge with your
hands. Fully retract the wedge to dislodge wood with log dislodger.

20 DR® HORIZONTAL/VERTICAL LOG SPLITTER
Splitting Wood
The control handle has three positions:
FORWARD — Move the control handle forward to the FORWARD position to
move wedge toward the log to split (Figure 42).
Note: The control handle will return to the NEUTRAL position as soon as the handle
is released (from the FORWARD position only).
NEUTRAL — Release the control handle or move the lever to the NEUTRAL
position to stop the wedge movement (Figure 43).
REVERSE — Move the control handle back to the REVERSE position to return the
wedge toward the cylinder (Figure 44). The control handle returns to the
NEUTRAL position automatically when fully retracted.
Do not hold the handle in the REVERSE position when fully retracted.
Note: To stop the wedge before it is fully retracted when in the REVERSE position, the
handle must MANUALLY be put in the NEUTRAL position.
1. Start the engine as instructed in the “Starting the Engine” section in this
chapter.
2. Place the log on the Log Splitter. Grasp the log on the sides near the middle of
the log (Figure 45). Center the log, side-to-side, on the beam, making sure that
one end is against the end plate.
3. Using only your hand, push the Control Lever Forward. If the log moves before
it is contacted by the Wedge, release the Handle and reposition the log.
4. Hold the Control Lever, moving the Wedge towards the Log until the log is
split or the cylinder rod stops at its maximum travel position. Stop the Log
Splitter (forward movement), at any point in the splitting process, if you feel
an unsafe splitting condition is occurring. As the log is being split, DO NOT
reach forward and attempt to catch the split wood — let it fall.
5. Once the Wedge reaches its full forward travel, move the Control Lever to the
Reverse Position and the Wedge will return to the retracted position.
Never operate the Log Splitter unless the hydraulic fluid tank is at the proper
level.
Figure 44
Control
Handle
Figure 43
Control
Handle
Figure 42
Control
Handle
If the control handle on your log splitter is not functioning properly, STOP
USE IMMEDIATELY and contact an authorized service dealer.
Do not attempt to service, repair or replace control valve. Contact an
authorized service dealer.
Do not attempt to adjust or modify the control valve or the hydraulic
system from its original settings or manufacturer in any way.
Hands on
Sides of
Log
Figure 45
End Plate
This manual suits for next models
2
Table of contents
Other DR Log Splitter manuals
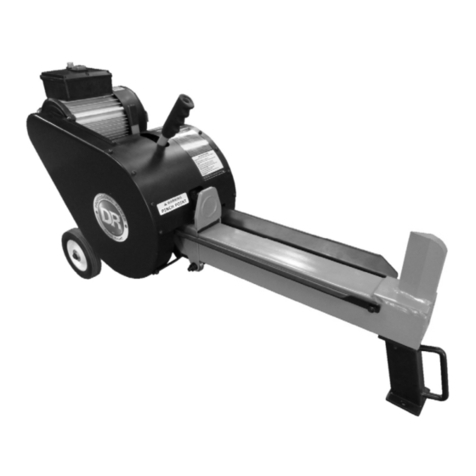
DR
DR K10 RAPIDFIRE User manual

DR
DR PREMIER RAPIDFIRE Quick start guide
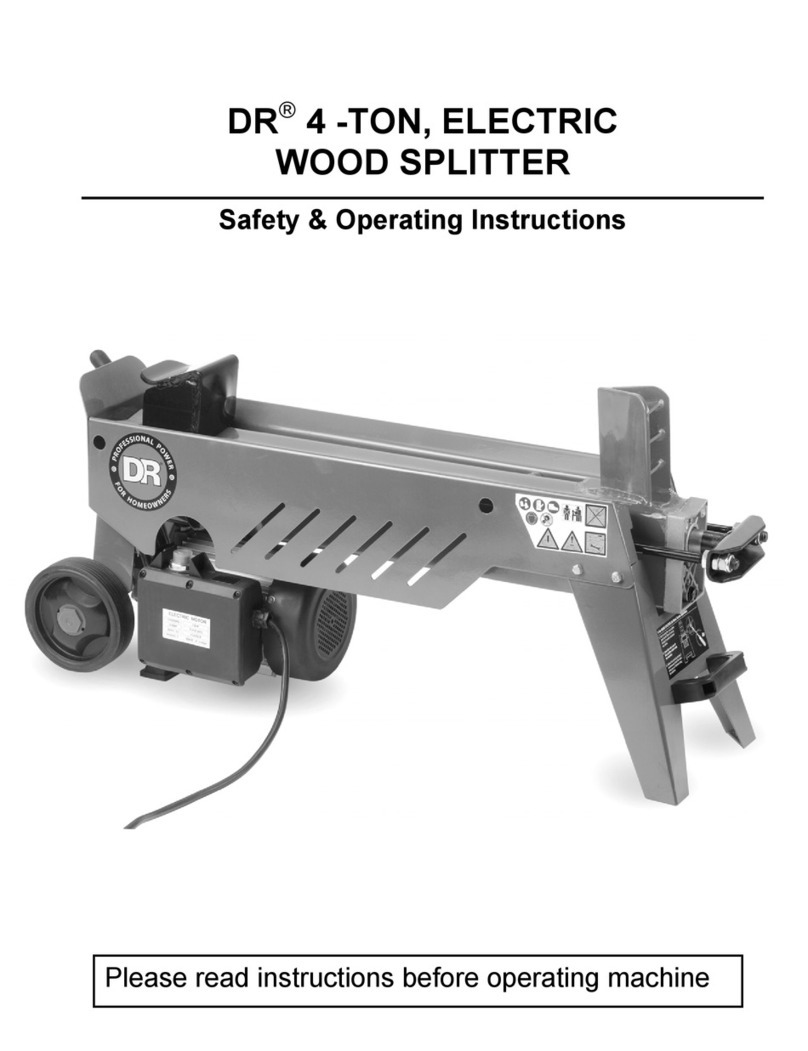
DR
DR DR 4 -TON Quick start guide
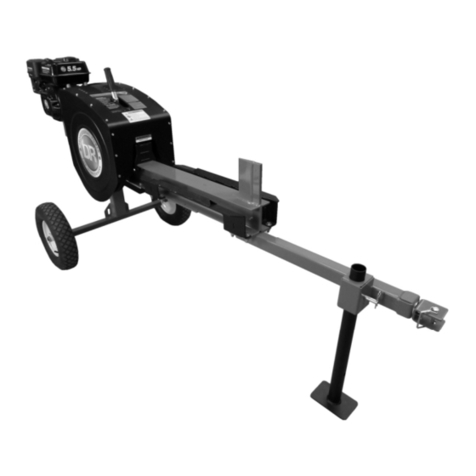
DR
DR RAPIDFIRE Quick start guide
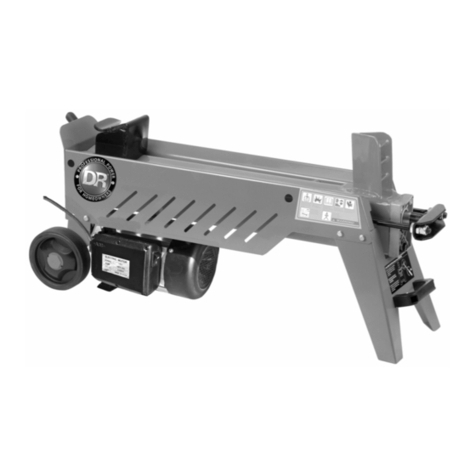
DR
DR ELECTRIC WOOD SPLITTER Quick start guide
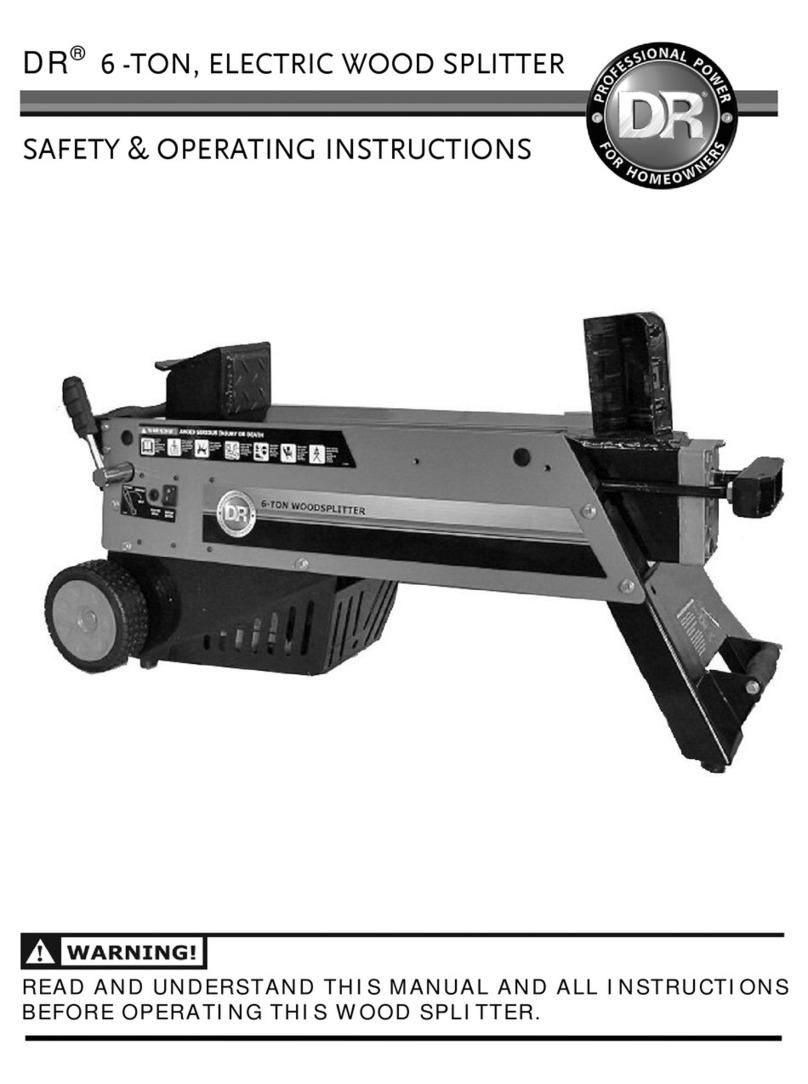
DR
DR 6-TON ELECTRIC WOOD SPLITTER Quick start guide
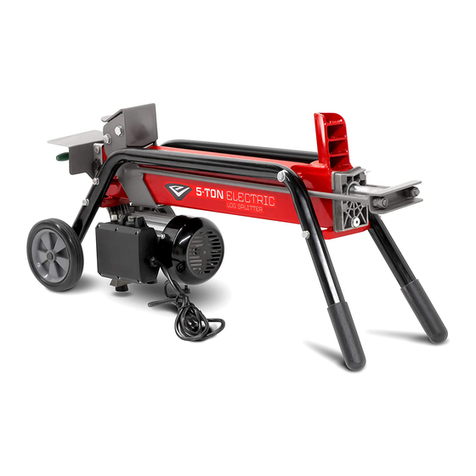
DR
DR PILOT 5TE Quick start guide

DR
DR DUAL-ACTION ELECTRIC Quick start guide