dunphy TD User manual

1 of 165
_________________________________________________________________________________________
DUAL FUEL BURNERS
TD/TAD4
GENERAL INFORMATION
AND
OPERATING MANUAL

Operating Instructions For TD/TAD4 Dual Fuel Burner
June 13 2 of 165 TD/TAD4 Manual Rev 4
Revision Table
Rev No.
Description
Date
By
1
2
3
4
Emergency stop information added - section 5.9
Exploded drawings revised –section 11
6.6.13
R.S

Operating Instructions For TD/TAD4 Dual Fuel Burner
June 13 3 of 165 TD/TAD4 Manual Rev 4
`TD/TAD` SERIES DUAL FUEL BURNERS
GENERAL INFORMATION AND OPERATING MANUAL
IMPORTANT
Throughout this publication Dunphy Combustion Limited are referred to as `The Company`.
The manual, which is supplied with every burner, should be read prior to the installation of the unit.
While giving information on the site work involved and on the burner commissioning procedure,
the content cannot include all of the data which may be necessary to achieve the design output of a
burner to a particular appliance because of the wide variety of heating and process plant for which
the burner is suitable precludes this.
The Company strongly advises that the commissioning of the burners is carried out by Dunphy
trained engineers and points out that it may be impossible to impart all the necessary information to
enable others to do so.
Under all circumstances the provisions of The Health and Safety at Work Act 1974 are the most
important consideration and if any doubts exist concerning the safe operation of the burner, The
Company should be contacted for advice. This provision also applies to the legislation of countries
to which the burners may be exported.
Where equipment, not of The Company`s supply, is used in conjunction with the burners, reference
should be made to specific instructions or regulations governing the installation and use of such
equipment.
The Company gratefully acknowledges the permission of component suppliers and others to
reproduce data sheets and technical information in this manual.
For reliable and efficient operation of the burner, it is essential that regular maintenance is carried
out in accordance with the instructions contained in the text of this manual. The fact that a burner
may be under warranty does not absolve the user from the responsibility for this and inadequate
maintenance may lead to claims, made under guarantees of materials or performance being denied
IF IN DOUBT - ASK!
Information contained in this manual is given without any responsibility on the part of the company
for the consequences of the actions of persons making use of such information.
Equipment is supplied strictly under the terms of The Company’s current `Conditions of Supply`
which are printed on the reverse of order acknowledgements and delivery notes.
Copies are available on request.

Operating Instructions For TD/TAD4 Dual Fuel Burner
June 13 4 of 165 TD/TAD4 Manual Rev 4
Contents
1General Information ......................................................................................................................................7
1.1 General ............................................................................................................................................................7
1.2 Working parameters ...................................................................................................................................7
1.3 Fuels .................................................................................................................................................................7
1.3.1 Fuel Tanks ..............................................................................................................................................8
1.3.2 Filtration ..................................................................................................................................................8
1.3.3 Ring Main Pumps..................................................................................................................................8
1.3.4 Pipe Runs ................................................................................................................................................8
1.3.5 Burner Connection...............................................................................................................................8
1.3.6 Burner Filtration ...................................................................................................................................8
1.3.7 Pressure Regulation ............................................................................................................................8
1.3.8 Oil Line Connections ...........................................................................................................................9
1.4 Burner construction ....................................................................................................................................9
1.5 Burner details and power curve ...........................................................................................................12
1.6 General arrangement details.................................................................................................................13
1.6.1 High low/modulating burners on gas, high low on oil .........................................................13
1.6.2 Electronic modulation burners (M RT) .......................................................................................14
1.6.3 TD10-415 Multi –Fuel Low Nox Burner General Arrangement........................................16
1.6.4 TD420 Multi –Fuel Low Nox Burner General Arrangement...............................................17
1.6.5 TAD420 Multi –Fuel Low Nox Burner General Arrangement............................................18
2Installation........................................................................................................................................................19
2.1 Burner Mounting.........................................................................................................................................19
2.2 Gas Valve mounting..................................................................................................................................20
2.2.1 Burner fitted with Unibloc...............................................................................................................20
2.2.2 Burner fitted with Siemens VGD40 gas valve.........................................................................22
2.3 Fuel oil installations ..................................................................................................................................23
2.3.1 Pump Connections.............................................................................................................................23
2.4 Pump Priming ..............................................................................................................................................23
2.5 Gas installation ...........................................................................................................................................24
2.6 Electrical connections ...............................................................................................................................24
2.7 Inverter Connection ..................................................................................................................................24
2.8 Ventilation requirements.........................................................................................................................24
3Combustion Head Settings.......................................................................................................................26
3.1 High / Low Burners ...................................................................................................................................27
3.2 Modulating Burners ...................................................................................................................................28
3.3 Modulating TD410 Burners Fitted With Low NOx Multi-Pipe Gas Head.................................29
3.1 Modulating TD415-420 Burners Fitted With Low NOx Multi-Pipe Gas Head .......................31
3.2 Modulating TD410 Burners Fitted With Low NOx Multi-Pipe Gas Head & Multi-Oil ..........33
3.1 Modulating TD415-420 Burners Fitted With Low NOx Multi-Pipe Gas Head & Multi-Oil.35
3.2 Modulating Burners Fitted With Bio - Gas Head ............................................................................37
3.3 Nozzle Adjustment ....................................................................................................................................38
3.3.1 Gas Head...............................................................................................................................................38
3.3.2 Multipipe Gas Nozzle adjustment ................................................................................................38
4Adjustments and Operating Principles .............................................................................................39
4.1 High/Low burners (HL) ............................................................................................................................39
4.1.1 High / Low Gas ...................................................................................................................................39
4.1.2 High / Low Oil......................................................................................................................................40
4.2 Pneumatic Modulating burners (M and M-sc) on Gas, High / Low on Oil.............................42
4.3 Electronic Modulation burners (M RT)................................................................................................42
4.3.1 Oil Operating System Modulating Burners ART 114 and ART 1400 Nozzles...............43
4.3.2 ART114 Burner Gun ..........................................................................................................................44
4.3.3 ART 1400 Burner Gun ......................................................................................................................44
4.3.4 Oil Operating System Modulating Burners ART 106 Nozzle ..............................................46
4.3.5 Oil Operating System Modulating Burners Multi-Oil Nozzles ............................................48
4.3.6 Oil Operating System High/Low Burners Multi-Oil Nozzles................................................49
4.3.7 Oil Operating System Air / Steam Atomising..........................................................................50
4.3.8 Fuel Pumps and Motors ...................................................................................................................51
5Operation & User Interface .....................................................................................................................52
5.1 The Display / Keypad ...............................................................................................................................52
5.2 Start -up Sequence ...................................................................................................................................53

Operating Instructions For TD/TAD4 Dual Fuel Burner
June 13 5 of 165 TD/TAD4 Manual Rev 4
5.3 Modulation ....................................................................................................................................................55
5.4 Normal mode...............................................................................................................................................55
5.5 Local mode ...................................................................................................................................................55
5.6 Non-volatile lockout ..................................................................................................................................55
5.7 Ratiotronic 6000 Inverter interface additional information .......................................................56
5.8 Post Purge Operation................................................................................................................................56
5.9 Emergency Stop .........................................................................................................................................57
6Component Setup Parameters ...............................................................................................................58
6.1 Ratiotronic 6000.........................................................................................................................................58
6.2 Danfoss VLT FC 102..................................................................................................................................64
6.2.1 RWF 40.000A97 Default Burner Settings .................................................................................66
7Commissioning................................................................................................................................................67
7.1 Basic settings ..............................................................................................................................................67
7.2 Start Gas Heat Input ................................................................................................................................68
7.3 Pre-commissioning ....................................................................................................................................69
7.4 Commissioning –High Low and Pneumatic Modulation burners - Firing on Gas ..............70
7.4.1 Dry run...................................................................................................................................................70
7.4.2 Check for leaks through the automatic gas valve. ...............................................................70
7.4.3 Check rotation of burner fan motor ............................................................................................70
7.4.4 Check for correct control sequence. ...........................................................................................70
7.4.5 Firing the burner ................................................................................................................................71
7.4.6 Combustion values and results.....................................................................................................71
7.4.7 Adjustment of Gas Proving Pressure Switch ...........................................................................72
7.5 Oil Firing........................................................................................................................................................72
7.5.1 Setting the Firing Rate, High / Low Oil Burners.....................................................................72
7.6 Electronic Modulating Burners ..............................................................................................................75
7.6.1 Gas Butterfly Valve ...........................................................................................................................75
7.6.2 Oil Metering Valve .............................................................................................................................75
7.6.3 Adjustment of air pressure proving switch ..............................................................................75
7.6.4 Ratiotronic programming ................................................................................................................76
7.6.5 Setting the servo motors ................................................................................................................76
7.6.6 Burner Commissioning.....................................................................................................................76
7.6.7 Combustion values and results.....................................................................................................76
8Burner Maintenance Schedule ...............................................................................................................77
8.1 Opening the Burner...................................................................................................................................77
8.2 Minor Maintenance ....................................................................................................................................78
8.3 Major Maintenance ....................................................................................................................................78
8.4 Dismantling and Re-assembly of Burners ........................................................................................79
9Faults and fault finding ..............................................................................................................................81
9.1 Ratiotronic 6000/6006.............................................................................................................................81
10 Useful Information .......................................................................................................................................82
11 Exploded Diagram & Spare Parts List................................................................................................85
11.1 Modulating Oil Modulating Gas Setup ................................................................................................85
11.2 Modulating Oil Modulating Gas with DH2 Pump (TD420 Only) ................................................90
11.3 High Low Oil High Low Gas Setup (TD410 Only)...........................................................................94
11.3 Modulating Gas High Low Oil Setup (TD410 Only) .......................................................................99
11.4 Multi-Oil Multi-Gas Exploded Diagram.............................................................................................104
11.5 TD410 Low NOx Combustion Head Assembly...............................................................................109
11.6 TD415-420 Low NOx Combustion Head Assembly .....................................................................109
11.7TD410 Combustion Head Assembly..................................................................................................110
11.8 TD415-420 Combustion Head Assembly ........................................................................................110
11.9 DN65 Unibloc.............................................................................................................................................111
11.10 DN80 Unibloc.........................................................................................................................................111
11.11 DN100 Unibloc ......................................................................................................................................111
11.12 VGD40.65 Assembly for Pneumatic Modulating and High Low Burners .........................112
11.13 VGD40.80 Assembly for Pneumatic Modulating and High Low Burners .........................112
11.14 VGD40.100 Assembly for Pneumatic Modulating and High Low Burners .......................113
11.15 VGD40.65 Assembly for Electronic Modulating Burners .......................................................113
11.16 VGD40.80 Assembly for Electronic Modulating Burners .......................................................114
11.17 VGD40.100 Assembly for Electronic Modulating Burners.....................................................114
12 Component Information ..........................................................................................................................115
12.1 LFL1.333 Burner Control Box ..............................................................................................................115

Operating Instructions For TD/TAD4 Dual Fuel Burner
June 13 6 of 165 TD/TAD4 Manual Rev 4
12.2 RWF 40 Burner temperature controller ...........................................................................................123
12.3 Unibloc .........................................................................................................................................................128
12.3.1 Unibloc General Arrangements ...................................................................................................128
12.3.2 65mm Ratiotronic Unibloc exploded diagram and parts list. ..........................................130
12.3.3 65mm Ratiotronic Unibloc with pilot exploded diagrams and parts list......................131
12.3.4 80mm Ratiotronic Unibloc exploded diagrams and parts list .........................................133
12.3.5 80mm Ratiotronic Unibloc with pilot exploded diagrams and parts list......................134
12.3.6 100mm Ratiotronic Unibloc exploded diagrams and parts list.......................................136
12.3.7 100mm Ratiotronic Unibloc with pilot exploded diagrams and parts list ...................137
12.4 Butterfly Gas Valve .................................................................................................................................139
12.4.1 General Arrangement.....................................................................................................................139
12.4.2 Exploded Diagram ...........................................................................................................................140
12.5 Siemens VGD20 and VGD40 Gas Valve Blocks ............................................................................141
12.5.1 Siemens SKP actuators..................................................................................................................145
12.6 VPS 504 Valve Proving System ..........................................................................................................151
12.7 Variotronic VT Oil Metering Valve......................................................................................................154
12.7.1 General Description.........................................................................................................................154
12.7.2 Construction.......................................................................................................................................154
12.7.3 Valve Maintenance ..........................................................................................................................154
12.7.4 Changing Seals .................................................................................................................................154
12.7.5 Adjustment of the valve................................................................................................................155
12.7.6 Installation of the valve.................................................................................................................155
12.7.7 Valve Drive .........................................................................................................................................155
12.7.8 Exploded Diagram ...........................................................................................................................156
12.8 DH Series Pump .......................................................................................................................................157
12.8.1 Pressure Regulation ........................................................................................................................158
12.8.2 Technical Data Summary..............................................................................................................159
12.8.3 Installation Operation Maintenance ..........................................................................................160
12.8.4 Fault Finding ......................................................................................................................................161
12.8.5 Oil Flow Diagrams............................................................................................................................162

Operating Instructions For TD/TAD4 Dual Fuel Burner
June 13 7 of 165 TD/TAD4 Manual Rev 4
During commissioning, all adjustments to the burner must be made in accordance with the boiler
manufacturer's instructions and these must include checking of flue gas temperature, average water
temperature and CO2 or CO concentration.
1 General Information
1.1 General
Burners must be checked at the time of delivery and any deficiencies or damage immediately
reported to the carrier or supplier. The company will make good any defects or replace missing
items strictly in accordance with their current conditions of supply.
The company has a policy of continuous development and therefore reserve the right to make
changes, without notice, in burner or other specifications.
Burners carrying the same model number may have major differences in their detailed
specification, such as draught tube lengths to suit the dimensions of a particular appliance, which
makes it impossible to give, in a single publication, precise information on the whole range of
applications. Data is readily available from the company and can be supplied on application.
Please give the burner serial number when requesting information.
All TD series burners are manufactured and tested to European Standards BS EN676: 2003 &
A2:2008 Automatic forced draught burners for gaseous fuels, Definitions, requirements, testing,
marking and EN 267 Forced draught oil burners –Definitions, requirements, testing, marking
If a burner is to be fitted to an existing boiler, maximum combustion efficiency can only be
achieved if all heat transfer surfaces are cleaned prior to the installation. Generally `TD` series
burners are not suitable for use in areas of high humidity or in explosive atmospheres, but special
units suitable for use in adverse situations can be manufactured to a customer's specific
requirements. Details of special units are available, on request, from the Dunphy sales department.
1.2 Working parameters
Temperature
0 to +50°C
Relative Humidity
60 - 90% non-condensing
Atmospheric Air Pressure –will generally be in the range of 950 to 1100mbar, but this will change
with altitude, if there are any queries please consult the Dunphy technical department.
1.3 Fuels
'TD / TAD' Series of burner must only be used with the fuels specified on the burner data plate and
in the case of gas, the pressure must not, under any circumstances, drop below the stated
minimum operating level.
The burner is also optimised for use with 35 sec diesel oil.
B100 Bio-diesel must not be used on a standard burner. When using B100, it must be specified at
time of order. Special pumps, valves and seals are used when burning B100.
It is essential that appliance and burner combinations are correctly matched.
If any doubt exists about the suitability of a particular combination the installer
must check with the manufacturers.

Operating Instructions For TD/TAD4 Dual Fuel Burner
June 13 8 of 165 TD/TAD4 Manual Rev 4
1.3.1 Fuel Tanks
Fuel storage tanks must be positioned to maintain a positive head to burners or ring main pumps,
regardless of the oil level in the tank.
Vertical and horizontal storage tanks should be mounted on concrete plinths in accordance with
local, national or any environmental standards that may apply.
The fuel lines and fuel filtration system must be sized to prevent any possibility of vacuum
occurring in the pump suction ports.
If a positive head of oil is not maintained, there is a possibility that cavitations will occur within the
fuel pump.
As a general guide, the fuel storage tanks must be mounted at least one meter above the ring main
fuel pumps which should be sited as close as possible to the tank discharge.
1.3.2 Filtration
Duplex fuel filtration is recommended to the ring main pumps, this will allow for maintenance
without shutdown of the ring main system, during normal operation of the plant.
1.3.3 Ring Main Pumps
The ring main pumps should be sized to give 100 to 150% over the burner pumps fuel
requirements.
Pumps must be fitted with an internal relief valve set at a maximum of 3 bar for pump protection.
Manual isolation valves should be fitted to the pump inlet and outlet pipework to allow for
maintenance. It is recommended that the valves have electric switch packs fitted to them so that
they can be interlocked with oil operation.
It is always preferable to use duplex pumping where practical, particularly on multi-burner
installations.
1.3.4 Pipe Runs
Pipework should be run in a manner that allows it to be self venting and, in sections that require
venting, a suitable vent or de-gassing section should be fitted.
Where overhead ring mains are to be installed particular care and attention should be taken that the
system can be adequately vented. Welded construction is preferable to screwed connections.
1.3.5 Burner Connection
Burner connections should be provided in the ring main pipework adjacent to the boiler and close
enough to allow the burner to be opened without the need to disconnect the flexible oil lines.
Note: - Manual isolation valves should not be fitted on the return lines.
1.3.6 Burner Filtration
Burner filtration will depend on the size of burners in question and the quality/grade of the fuel oil
to be used, but good quality fuel filters, preferably of the self-clean type are recommended.
1.3.7 Pressure Regulation
The Pressure regulating valve of the ring main must be of the low, or zero, hysteresis type and
capable of maintaining a stable ring main pressure through the minimum and maximum flow
conditions of the supply system irrespective of any change in flow volume or viscosity.
A number of suppliers manufacture valves suitable for this purpose and further details are available
from the Dunphy technical department.

Operating Instructions For TD/TAD4 Dual Fuel Burner
June 13 9 of 165 TD/TAD4 Manual Rev 4
1.3.8 Oil Line Connections
It is essential that the final connections between the main oil supply lines and the burner fuel pump
are made with flexible oil lines that are long enough to allow the burner to be swung open on its
hinges without having to be disconnected. Care should be taken to ensure that the flexible oil lines
do not become `kinked` as this will cause damage to the flexible and result in leakage.
1.4 Burner construction
Each ‘T’ series burner is constructed from 5 separate castings described as follows:
Hinge
In common with all other body castings, the mounting casting is manufactured from aluminium
grade LM6 with the front face drilled to the dimensions given in section 1.5 of this manual suitable
for mounting studs. The rear face has two external lugs which form part of the burner hinge and is
drilled to accept the studs that are used to lock the burner closed.
Note: The fuel pipework enters this casting and it is essential that all joints and connections on the
combustion head are checked for security before the burner is hinged to the closed position. See the
maintenance section for details.
This casting houses the burner draught tube and combustion head along with the appropriate
ignition cables and flame detection equipment.
Fan case assembly
This consists of two aluminium castings with machined faces, bolted together and enclosing
the fan (which is sized to suit the particular burner model according to output and combustion
chamber resistance).
Integral with and inside the front half of the fan cases are the compressor blades; on the outside,
external lugs are attached with pins and thrust bearings to the burner mounting casting to form the
hinges.
The rear half is tapped to take the burner lifting eye and pads are used for the attachment of the
components on various models of the burner. The rear face is machined to match the air shutter
assembly, which is attached to it.
A differential air pressure switch, piped across the air inlet and pressure outlet of the combustion air
fan is mounted on the front section. Its function is to prevent the burner from firing if a supply of
combustion air is not available or to lock out the burner if the air supply is interrupted during
normal running.
Air shutter
Combustion air is introduced through two concentric castings, one rotating about the other on a
PTFE bearing surface, regulating the combustion air supply through characterised slots to
accurately maintain the fuel air ratio. Close machining tolerances ensure almost zero leakage when
the damper is fully closed. The characterisation of the slots also ensures very high control of the air
supply at the important low fire end –typically 30 degrees of movement accounts for only 10% of
air throughput thus ensuring very high turndown capability.
The operation of the air shutter is activated by a reversible, mains voltage, synchronous motor (on
high/low burners) or a 240 (or 24V) motor with potentiometer control for fully modulating units.
Adjustable rigid linkage is used and the limits of travel are set by micro switches. Final adjustments
are made during commissioning.
On burners fitted with electronic modulation systems the air shutter and the fuel valves will all be
manufactured with individual drive motors controlled by the modulation system.

Operating Instructions For TD/TAD4 Dual Fuel Burner
June 13 10 of 165 TD/TAD4 Manual Rev 4
Figure 1
Figure 2
On burners which have air inlet silencers as standard a 0-10 scale is fitted to indicate the opening of
the air shutter (not the firing rate) and nylon support bearings ensure that the travel is as smooth as
possible.
Burner Motor
The burner (fan) motor is a continuously rated 2-pole unit with class 'F' insulation, sized according
to the application. The motor is mounted the inside of the inner shutter thus allowing 100% heat
recovery from the motor into the combustion air offering efficiency ratings greater than EFF1. This
also ensures inherently quiet operation from the burner.
Combustion Air Fan
Mounted directly onto the motor shaft and positioned within the fan case assembly, the fan supplies
combustion air via the compressor vanes and mounting casting to the combustion head.
Due to the 'T' burner requirement for extremely low vibration and noise levels the fans are
manufactured and balanced to the very highest standards (ISO 1940-2003).
All fans are colour coded according to size.
Combustion Head
The air for combustion passes from the burner fan at a pressure related to the resistance of the
boiler, down the draught tube to the combustion head. The latter is an assembly of components
which cause the gas to be discharged into the air flow in such a way that optimum mixing takes
place.
Many types of combustion head are available depending on appliance geometry, gas type, available
gas pressure, NOx level requirement etc…
Note: On any burner, an almost infinite combination of combustion head components may be used
to achieve optimum efficiency and a flame shape to suit a very wide range of heat-raising
appliances.
Burner Control Cabinet
Standard burners are supplied with a dust resistant damp-proof cabinet mounted on the side of the
burner. In many cases all the burner controls are fitted within the burner control cabinet (figure 1).
In more complicated installations, this cabinet would house a terminal strip (figure 2) which would
then interface to a control desk via flying leads.

Operating Instructions For TD/TAD4 Dual Fuel Burner
June 13 11 of 165 TD/TAD4 Manual Rev 4
Figure 3
Figure 4
Control desks are available in ‘wardrobe’ type style (figure 3) or ‘desk’ type style (figure 4). These
can vary in complexity and are able to house a whole host of burner/boiler controllers, water levels
controls, inverters, plc etc...
Air Inlet Silencer
Because of their design characteristics, 'T' series burners operate at very low noise levels, however,
further reduction of these levels can be made by fitting air inlet silencers which are designed to
cover the air shutter castings. The standard foam lined silencer typically offers sound levels in the
region of 80dBA. An optional ‘Snorkel’ type silencer is available which will reduce sound levels to
below 75dBA. Silencers can also be tailored to suit ducted air supplies, filters or additional acoustic
attenuation. For extremely sensitive installations, 'Acoustic Shrouds' which cover the entire burner
can be individually designed to suit most applications. Quotations are available on request.
Typical Acoustic Shroud Burner fitted with 'Snorkel' Silencer

12 of 165
1.5 Burner details and power curve
*1 –Based on Nat. Gas C.V 10.4 kW/m3
*2 - Fitted with a Ratiotronic 6000 System
BURNER
Firing Rate kW
GAS
VOLUME
(m3/HR)*1
FIRING MODE OPTIONS
Fan
Motor
KW
Pump
Motor
kW
Voltage
Hz
Ph
Running
Current
Starting
Current
TYPE
MIN
MAX
MIN
MAX
Mod
Gas
High /
Low Oil
High /
Low
Electronic
Modulation
*2
TD410Z
600
4500
58
433
7.5
2.2
380-420
50
3
23 Amp
48 Amp
TD415Z
800
5300
77
510
11.0
2.2
380-420
50
3
32 Amp
64 Amp
TD420Y
1250
6200
120
596
15.0
2.2
380-420
50
3
39 Amp
88 Amp

13 of 165
1.6 General arrangement details
1.6.1 High low/modulating burners on gas, high low on oil
High Low and Pneumatic Modulation burners both use air/gas
ratio valves (details can be found in the component section of this
manual). They have built-in governors thus not requiring an
external governor for gas pressures up to 350mbar.
In this configuration the gas valve requires two signals from the
burner - the air pressure of the burner and furnace resistance of the
boiler. The furnace resistance is monitored with a stainless steel
piece of pipe which is projected into the furnace along the side of
the burner head. This will require an additional hole or notch in the
boiler mounting plate to accommodate –see mounting detail.
TD410 - 415 Burners with VGD40 Gas Valve

Operating Instructions For TD/TAD4 Dual Fuel Burner
June 13 14 of 165 TD/TAD4 Manual Rev 4
1.6.2 Electronic modulation burners (M RT)
Electronic modulation burners are fitted with on/off gas valves and
electronically controlled butterfly valves for the gas regulation. The
gas valve is generally a Unibloc (see component section for details)
however other valves can also be used depending on site details or
customer preference. An additional electronically controlled oil
metering valve is fitted for oil regulation –see principle of
operation section for more details.
TD410 - 415 Burners with Unibloc Gas Valve

Operating Instructions For TD/TAD4 Dual Fuel Burner
June 13 15 of 165 TD/TAD4 Manual Rev 4
TD420 Burners with Unibloc Gas Valve

Operating Instructions For TD/TAD4 Dual Fuel Burner
June 13 16 of 165 TD/TAD4 Manual Rev 4
1.6.3 TD10-415 Multi –Fuel Low Nox Burner General Arrangement

Operating Instructions For TD/TAD4 Dual Fuel Burner
June 13 17 of 165 TD/TAD4 Manual Rev 4
1.6.4 TD420 Multi –Fuel Low Nox Burner General Arrangement

Operating Instructions For TD/TAD4 Dual Fuel Burner
June 13 18 of 165 TD/TAD4 Manual Rev 4
1.6.5 TAD420 Multi –Fuel Low Nox Burner General Arrangement

Operating Instructions For TD/TAD4 Dual Fuel Burner
June 13 19 of 165 TD/TAD4 Manual Rev 4
2Installation
2.1 Burner Mounting
Care must be taken when mounting the burner not to damage the mounting gasket. The furnace
pipe (where fitted) is generally positioned at 12 o’clock on the mounting flange and care must be
taken not to damage it during the mounting process.
Note: - Ensure that the burner mounting gasket is correctly fitted when fixing the burner to
the appliance. This gasket creates a gas-tight seal between the boiler and burner and also
insulates the burner mounting casting.
It is important to check that the burner draught tube projection into the combustion chamber
conforms to the appliance manufacturers instructions.
Non standard draught tube projections are available on request; - please consult the Dunphy sales
dept.
In general, for reverse flame boilers the draught tube projection into the combustion chamber
should be between 50 and 100mm. For other boilers the burner draught tube should finish flush or
slightly proud of any boiler refractory or insulation. Low NOx heads should be projected into the
furnace by at least 100 - 150mm.
If there is any doubt about the correct projection into the combustion chamber, the appliance
manufacturer must be consulted.

Operating Instructions For TD/TAD4 Dual Fuel Burner
June 13 20 of 165 TD/TAD4 Manual Rev 4
2.2 Gas Valve mounting
2.2.1 Burner fitted with Unibloc
The Unibloc gas valve is
a heavy item and will
require two persons to lift
it into position and secure
in place using bolts
provided.
The Unibloc is shipped
pre - connected. Please
consult electrical wiring
diagram for electrical
connections.
Governor shown is
supplied with every
burner using a Unibloc
gas valve and should be
installed according to
guidelines illustrated
below and approximately
10 pipe diameters
upstream of the gas valve.
Pipe work and isolating valve are supplied by others.
Important:
The installer must install a 90° turn type isolation ball valve next to or in close proximity to
the burner and capable of rapid operation.
The manual valve must be capable of operating at a pressure equal to 1.5 times the maximum
supply pressure and where possible must be orientated in such a way that when the valve closes the
handle must fall from the vertical to the horizontal. The valve must have mechanical end stops to
prevent the ball valve from going below the 0° point or above the 90° point.
The gas supply pipework
must be adequately
supported to prevent undue
stress on the burner casing or
the gas train components.
Gas supplies greater than
500mbar must be governed
down to a suitable gas
pressure below 500mbar
using a CE approved high
pressure gas governor. The
gas governor or should be
fitted as per manufactures
instructions, copies available
on request.
Typical Gas train installation
is shown on the right
This manual suits for next models
1
Table of contents
Popular Burner manuals by other brands
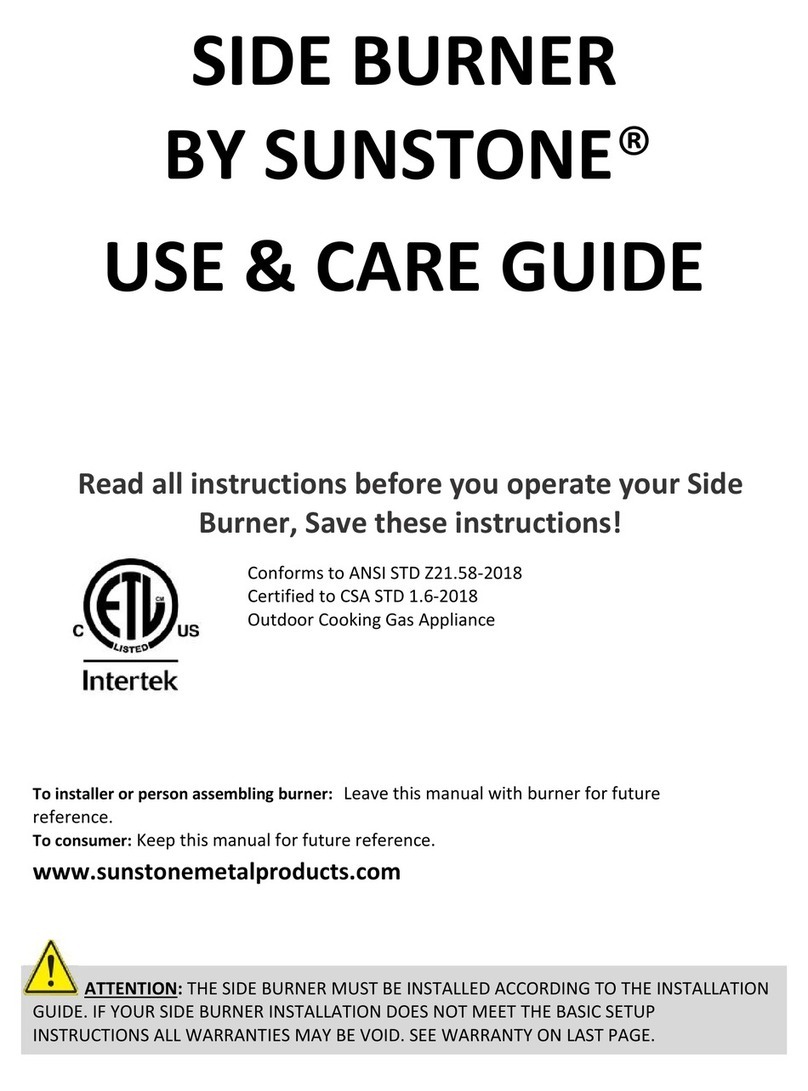
SUNSTONE
SUNSTONE 1SSB Use & care guide
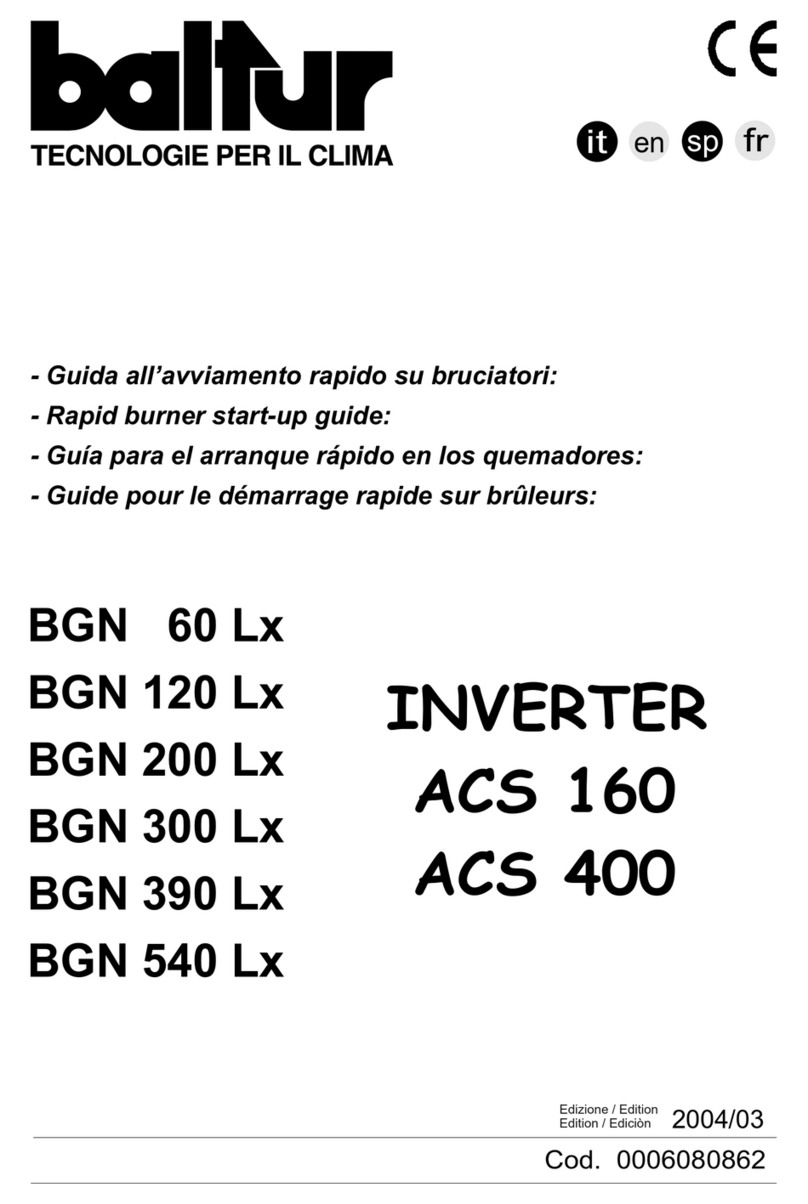
baltur
baltur BGN 60 LX Startup guide
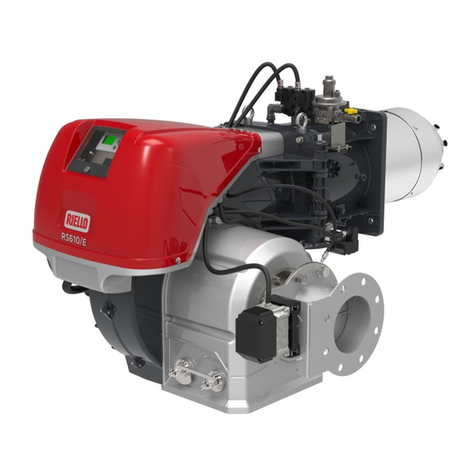
Riello
Riello RS 810/E FGR Installation, use and maintenance instructions
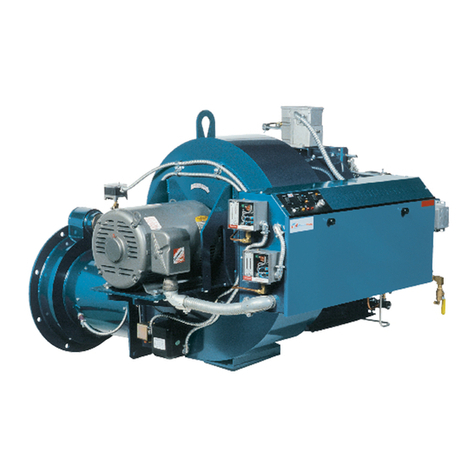
Power Flame
Power Flame Ultra CMax Installation and operation manual
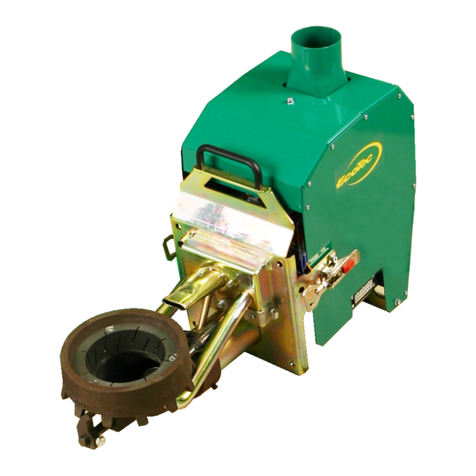
Ecotec
Ecotec BioLine 20 instruction manual
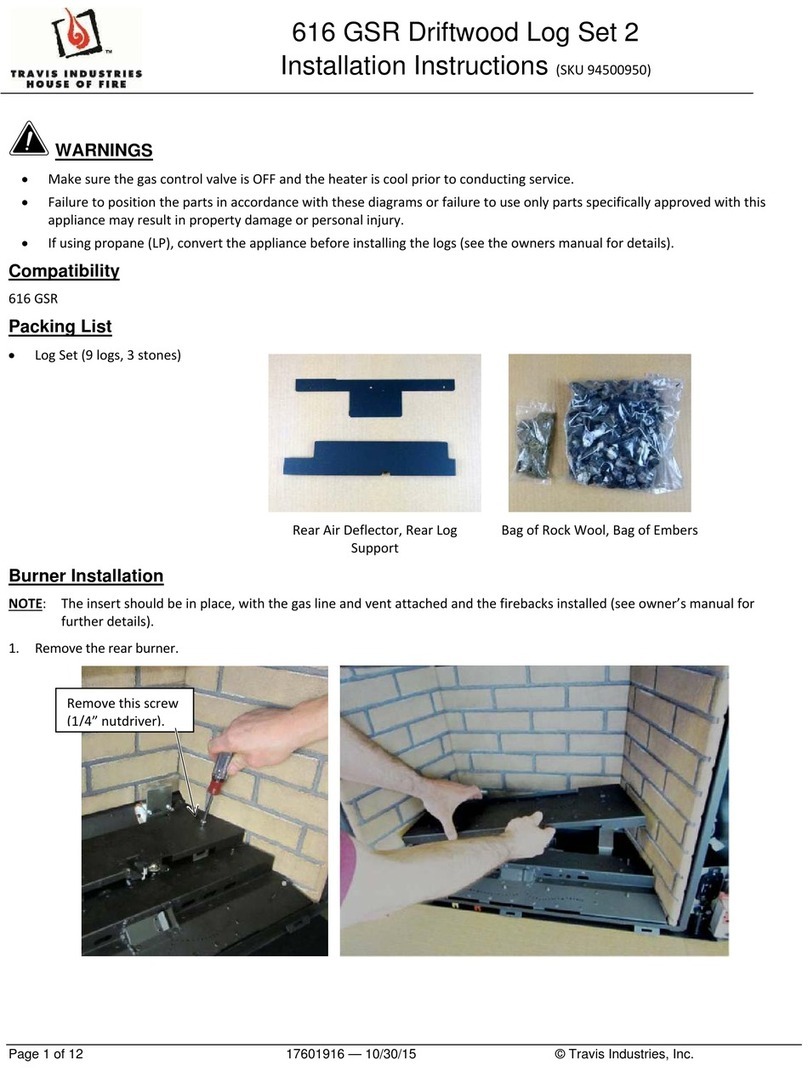
Travis Industries
Travis Industries 616 GSR Driftwood Log Set 2 installation instructions