Dynabrade 95524 User manual

Parts Page Reorder No. PD93•08
Effective March, 1993
95524 Motor Tune-Up Kit
01206 Bearing
02651 Bearing
50659
Lock Ring Seal
56047
Rotor Key
*95721
Retaining Ring
56052
Balancer Bearing
56053 Bearing Seal
01020 “O” Ring
01022 Valve Spring
01024 “O” Ring
95523 “O” Ring
95625 Pin
*On previous models, prior to March 1989, please use the
supplied 95629 Screw in place of 95721 Retaining Ring.
On models with Serial Number 89750 and greater,
95721 Retaining Ring not required.
Also included - (1) 95621 Loctite®
Note: Shaded areas represent standard models only.
Loctite is a registered trademark of the Loctite Corp.
95630 Snap Ring
See reverse side for Assembly/Disassembly Instructions.
Refer to appropriate parts page for additional parts
identification. Parts included in kit are identified by part number.
56079 MufflerAssembly
(Non-Vac Only)
50645 Pin
IMPORTANT:
The regular maintenance of any air tool will contribute to greater efficiency of tool and will prolong tool life. This kit contains replacement parts which are
most susceptible to wear. An air tool may wear differently according to the application and operator. It is, therefore, recommended that while the tool is
disassembled, all other parts not included in this kit be examined for excessive wear and be replaced as required.
NOTICE: Manufacturer’s warranty is void if tool is disassembled before warranty expires.
57114
Blade (5) (5/pkg.)
95626
Retaining Ring

Assembly/Disassembly Instructions for Lightweight Dynorbital®Random Orbital Sander
Please refer to parts page for additional parts identification.
A complete repair kit, part number 56077, is available which includes special tools for correct disassembly/assembly of tool.
To Disassemble
1. Invert machine and secure in vise, using 57092 Collar (supplied in 56077 Repair Kit) or padded jaws.
2. Remove sanding pad with 50679 Open-End Wrench (supplied with sander).
3. Remove shroud or optional overskirt. Insert 56058 Lock Ring Tool (supplied with 56077 Repair Kit) into corresponding tabs of lock ring and unscrew.
Motor may now be lifted out for service.
4. Remove 95626 Retaining Ring. Upper motor may now be disassembled.
5. 56039 Rear Bearing Plate with bearing is a “slip” fit on older machines and a “press” fit on newer machines. Remove the
rear plate assembly by securing the 56050 Cylinder in a standard 2 inch bearing separator or use a standard bearing puller
gripped on the cylinder inlet and exhaust area. Push the 56042/44 or 54623 Motor Shaft Balancer through the bearing.
6. Remove 56037 Front Plate and 02651 Front Motor Bearing, using a small (#2) arbor press. Support the edges of the front plate while
pressing on the small end of the 56042/44 or 54623 Shaft Balancer. The 56037 Front Plate should separate from 02651 Front Motor Bearing.
a.) If during step 6, the 56037 Front Plate and 02651 Front Motor Bearing remain together, push 56081 Bearing Chuck (supplied with 56077 Repair Kit)
with ridged side forward into bearing side of assembly until it locks.
b.)Push 95890 Taper Pin (supplied with 56077 Repair Kit) with narrow side forward into front plate side of assembly. Press bearing out using a
small (#2) arbor press.
7. Remove 01206 Bearing from 56039 Rear Plate by using a bearing press tool.
8. Disassemble the balancer assembly as follows:
a.) Remove95630SnapRing. Screw the threaded portion ofthe56056BearingPuller (supplied with 56077 RepairKit)intothe 57069 Balancer
Shaft. Note: Heat the outside of the motor shaft balancer to approximately 200°F and pull the assembly out using the slider weight.
b.)Press off 56052 Bearing and remove loose parts.
9. If during step 8, the 56052 Bearing remains in the motor shaft balancer it can be removed by heating the shaft balancer again and using either an
inside bearing puller or a blind hole bearing puller.
To Reassemble
Important: Be certain parts are clean and in good repair before reassembling.
1. Assemble the balancer assembly as follows:
a.)Install 95630 Snap Ring onto 57069 Balancer Shaft. Install 95628 Shield with convex face toward hex of balancer shaft.
b.)Install 56053 Seal. Note: Be certain seal is pressed completely over the shaft step.
c.) Applyaslight amount#290Loctite®(or equivalent) toinsidediameter of 56052Bearingand the outsidediameterofthe 57069BalancerShaft.
d.)Press fit 56052 Bearing with seal side toward hex of balancer shaft up to shaft step, using 56059 Bearing Press Tool (supplied with 56077
Repair Kit).
2. Place 56042/44 or 54623 Shaft Balancer in a soft jaw vise with large end up.
3. Apply a slight amount #271 Loctite® (or equivalent) in several places around the outside diameter of the 56052 Bearing and slide into the 6042/44 or
54623 Shaft until 56052 Bearing is firmly seated at bottom. Squeeze 95630 Snap Ring into groove to complete the assembly. Remove from vise.
4. Press 02651 Bearing onto 56042/44 or 54623 Shaft down to shoulder using 56059 Bearing Press Tool.
5. Place 56046 Lock Ring (with 50659 Lock Ring Seal in it) onto shaft with lock ring seal facing small end of shaft.
6. Press 56037 Front Bearing Plate onto 02651 Bearing and check for smooth rotation.
7. Place 56047 Rotor Key, Rotor, and Blades onto shaft. Note: Be certain rotor “floats” easily on the shaft. Because the design of this motor uses a
“floating rotor”, there is no need to set or adjust gap between the rotor and end plates.
8. Place 56050 Cylinder over rotor. The “short” line-up pin goes toward the 56037 Front Plate.
9. Place 56039 Rear Bearing Plate (with 01206 Rear Bearing pressed into place) over shaft and “long” end of line-up pin and press fit in place.
Note: Older machines do not require press fitting.
10. Install95626Retaining Ringconcave side toward motor. Note: Becertainretaining ring iscompletelypressed down intoitsgroove on theshaft.
11. Secure motor housing in vise, using 57092 Collar or padded jaws. Slide motor assembly into secured housing.
Note: Be certain line-up pin enters pin hole in the bottom of the housing.
12. Tighten 56046 Lock Ring with 56058 Lock Ring Tool to 28 N m (250 lb.-in). Attach shroud and weight-mated sanding pad.
Tool assembly is complete. Please allow 30 minutes for adhesives to cure before operating tool.
Note: Motor should operate at between 9,500 and 10,000 RPM at 6.2 bar (90 PSI). RPM should be checked with a reed tachometer. Before
operating, we recommend that 2-3 drops of pneumatic tool oil be placed directly into the air inlet with throttle lever depressed.
DYNABRADE®
DYNABRADE, INC., 8989 Sheridan Drive •Clarence, NY 14031-1490 •Phone: (716) 631-0100 •Fax: 716-631-2073 •International Fax: 716-631-2524
DYNABRADE EUROPE s.a.r.l., ZoneArtisanale •L-5485 Wormeldange—Haut, Luxembourg •Telephone: 352 76 84 94 •Fax: 352 76 84 95
©DYNABRADE, INC., 1995 PRINTED IN USA
Other Dynabrade Engine manuals
Popular Engine manuals by other brands

Fiate Aviation
Fiate Aviation MZ202 Instruction and maintenance manual
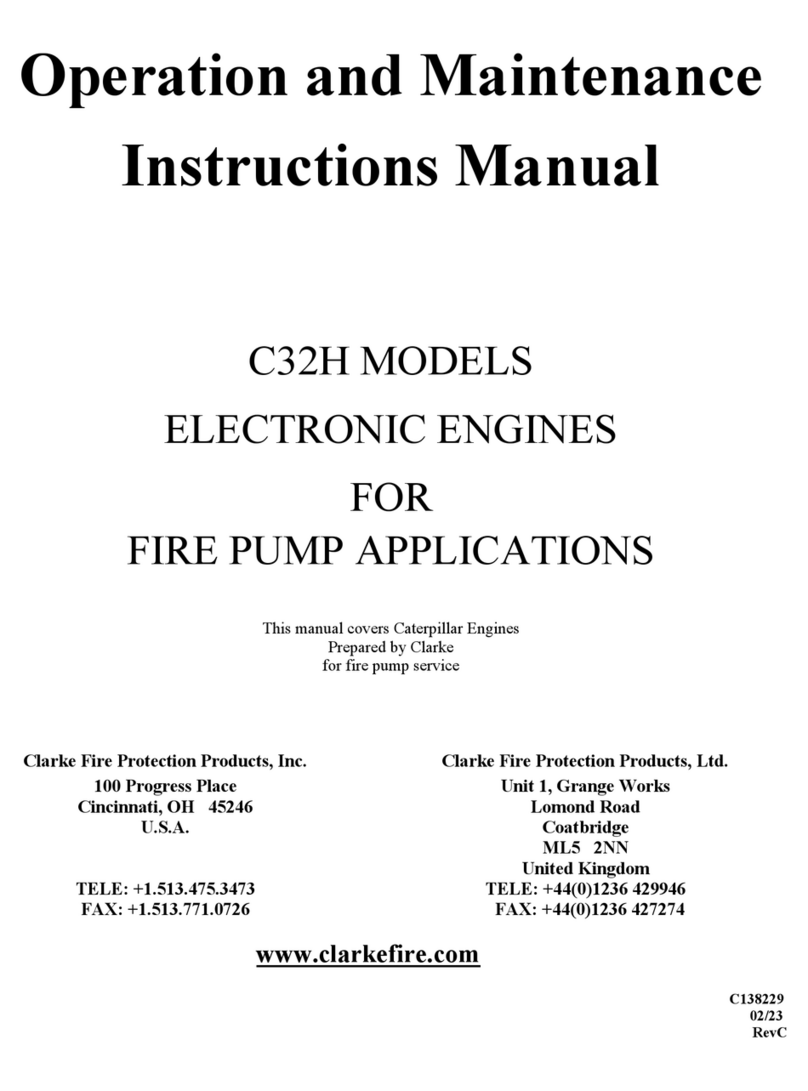
Clarke
Clarke C32H Operation and maintenance instruction manual
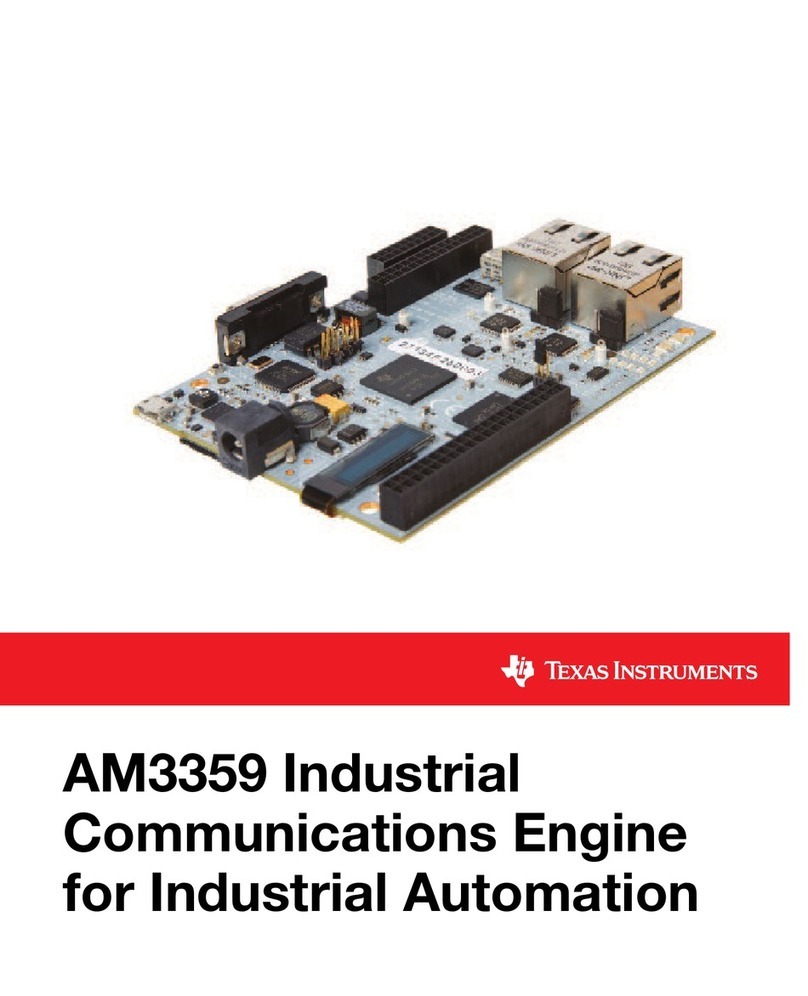
Texas Instruments
Texas Instruments Sitara AM3359 quick start guide

Kohler
Kohler K9J Service manual

Lenze
Lenze g500-B Project planning manual
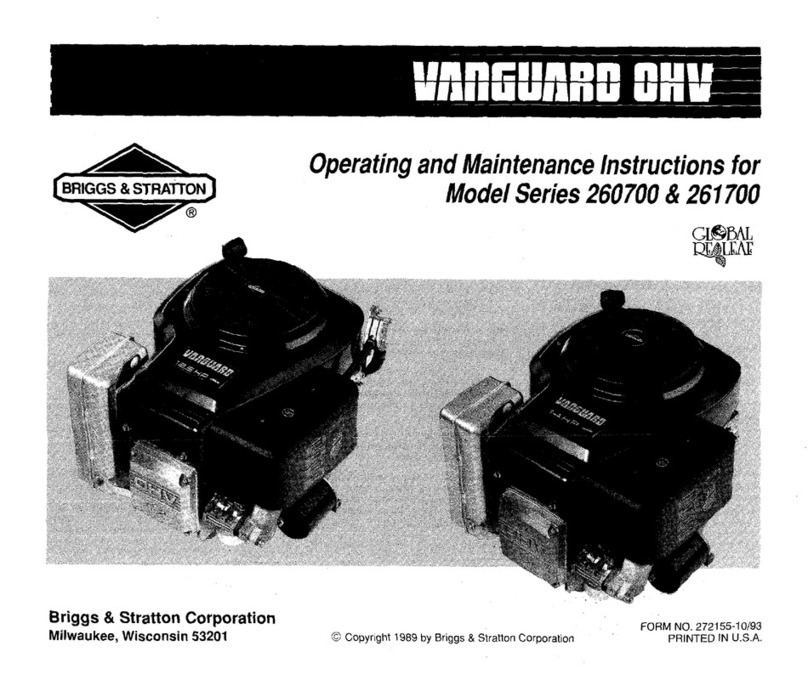
Briggs & Stratton
Briggs & Stratton 260700 Operating and maintenance instructions