SCHUNK STM 48V User instructions

05 V01-A/STM-48V/en/2011-04-01/CW Document last updated: 2011-04-01
Electrical Rotary Module
SCHUNK Torque Motor
Type STM 48V
Assembly and Operating Manual

205/STM-48V/en/2011-04-01/CW

Table of contents
05/STM-48V/en/2011-04-01/CW 3
Translation of the original manual
Dear Customer,
Congratulations on choosing a SCHUNK product. By choosing SCHUNK, you have opted for
the highest precision, top quality and best service.
You are going to increase the process reliability of your production and achieve best
machining results –to the customer’s complete satisfaction.
SCHUNK products are inspiring.
Our detailed assembly and operation manual will support you.
Do you have further questions? You may contact us at any time –even after purchase. You
can reach us directly at the mentioned addresses in the last chapter of these instructions.
Kindest Regards,
Your SCHUNK GmbH & Co. KG
Precision Workholding Systems
Bahnhofstr. 106 –134
D-74348 Lauffen/Neckar
Tel. +49-7133-103-2503
Fax +49-7133-103-2189
[email protected]k.com
www.de.schunk.com

Table of contents
405/STM-48V/en/2011-04-01/CW
Table of contents
1 About this manual.................................................................................................8
1.1 Purpose/validity..........................................................................................8
1.2 Target groups.............................................................................................8
1.3 Applicable documents................................................................................8
1.4 Symbols in this manual ..............................................................................9
1.5 Terms used in this manual.........................................................................9
2 Basic safety notes ..............................................................................................10
2.1 Intended use ............................................................................................10
2.2 Environmental and operating conditions ..................................................10
2.3 Controlled production...............................................................................11
2.3.1 Protective equipment...................................................................11
2.3.2 Special standards........................................................................11
2.3.3 Constructional changes, attachments, or modifications...............11
2.3.4 After-sales service.......................................................................12
2.4 Obligations of the manufacturer/operator.................................................12
2.4.1 Choice of personnel and personnel qualifications .......................12
2.4.2 Organizational measures.............................................................12
2.4.3 Disposal.......................................................................................12
2.5 Personnel qualification.............................................................................13
2.5.1 Safety-conscious working............................................................13
2.5.2 Safety measures during transport................................................13
2.5.3 Safety measures during operation...............................................13
2.5.4 Behaviour in the event of faults or emergencies..........................13
2.6 Notes on particular risks...........................................................................14
3 Warranty..............................................................................................................16
4 Scope of delivery................................................................................................16
5 Description of the module..................................................................................17
5.1 STM torque motor....................................................................................17
5.1.1 Design and description of the STM..............................................17
5.1.2 Mechanical interfaces..................................................................18
5.1.3 Electrical interface.......................................................................18

About this manual
05/STM-48V/en/2011-04-01/CW 5
5.1.4 Type key and nameplate.............................................................19
6 Technical Data ....................................................................................................20
6.1 Technical Data des STM..........................................................................20
6.1.1 Technical Data STM135..............................................................20
6.1.2 Technical Data STM170..............................................................21
6.1.3 Technical Data STM210..............................................................23
6.2 Requirements for the power and sensor cables.......................................24
6.3 Brake........................................................................................................25
6.3.1 Technical data for brake valve MV15 ..........................................25
6.3.2 Connection to MCS-12................................................................26
6.3.3 Holding brake moment ................................................................26
7 Assembly.............................................................................................................27
7.1 Mechanical connection.............................................................................27
7.2 Electrical connection ................................................................................30
8 Start-up................................................................................................................32
9 Accessories.........................................................................................................34
9.1 Connection and commissioning of the STM with the SCHUNK
controller MCS-12....................................................................................34
9.1.1 Scope of delivery of the MCS-12 controller .................................34
9.1.2 Technical Data of the MCS-12 controller.....................................34
9.1.3 Design and description of the MCS-12 controller ........................35
9.2 Electrical connection of the module to the MCS-12 controller..................38
9.2.1 Procedure and requirements.......................................................38
9.2.2 Connecting the STM to the MCS12 controller .............................38
9.2.3 Assignment of the terminal strips of the MCS-12 controller.........39
9.2.4 Communication interfaces...........................................................40
10 Start up with PC..................................................................................................42
10.1 SCHUNK MCS-12 controller....................................................................42
10.1.1 Functional principle......................................................................42
10.2 System integration ...................................................................................43
10.2.1 System structure..........................................................................43
10.2.2 Configuration with MCDemo........................................................44
10.2.3 Commissioning of the digital inputs.............................................48

Table of contents
605/STM-48V/en/2011-04-01/CW
10.2.4 Commissioning of the digital outputs...........................................48
10.3 Control parameters ..................................................................................49
10.3.1 STM135.......................................................................................49
10.3.2 STM170.......................................................................................52
10.3.3 STM210.......................................................................................56
11 SCHUNK Motion protocol ..................................................................................59
11.1 Description...............................................................................................59
11.1.1 Most important commands ..........................................................60
12 Replacing the module.........................................................................................64
13 Troubleshooting..................................................................................................65
13.1 SCHUNK Torque Motor STM...................................................................65
13.1.1 STM is not turning .......................................................................65
13.1.2 STM overspeed...........................................................................66
13.1.3 STM oscillates.............................................................................66
13.1.4 Bearing noise...............................................................................66
13.1.5 Error message for the winding temperature ................................67
13.2 MCS-12 controller....................................................................................67
13.2.1 Software error messages ............................................................67
13.2.2 Electrical signals are not transmitted...........................................68
13.2.3 No LED lights up..........................................................................68
13.2.4 „POW“ LED (green) does not light up..........................................68
13.2.5 „RDY“ LED (green) on the controller is not flashing.....................68
13.2.6 „ERR“ LED (red) on the controller is flashing or permanently
on ................................................................................................68
14 Maintenance and care ........................................................................................69
14.1 Maintenance and lubrication intervals......................................................69
14.2 Module Servicing......................................................................................69
14.3 Dismantling the module............................................................................70
15 Transport, storage and disposal .......................................................................71
15.1 Transport..................................................................................................71
15.2 Packaging ................................................................................................71
15.3 Storage.....................................................................................................72
15.4 Disposal ...................................................................................................72

About this manual
05/STM-48V/en/2011-04-01/CW 7
16 Drawing................................................................................................................73
16.1 STM-135 ..................................................................................................73
16.2 STM 170...................................................................................................74
16.3 STM-210 ..................................................................................................75
17 Translation of original EC declaration of incorporation..................................76
18 Contact ................................................................................................................78

About this manual
805/STM-48V/en/2011-04-01/CW
1 About this manual
1.1 Purpose/validity
This manual is part of the module and describes the safe and
proper use during all phases of operation.
This manual is valid only for the module specified on the front
page.
1.2 Target groups
Target group
Task
Manufacturer, operator
Keep this manual available for the personnel at all times.
Require personnel to read and observe this manual and the
applicable documents, especially the safety notes and warnings.
Skilled personnel, fitter
Read, observe and follow this manual and the applicable
documents, especially the safety notes and warnings.
Table 1
1.3 Applicable documents
You can find the following documents on our homepage:
Document
Purpose
Catalog
Technical data or application parameters of the module and informa-
tion on accessories. The last version is always valid.
Software manual for
MotionControl
(only for using the
MCS-12 controller)
Includes more detailed information about the firmware for the MCS-12
controller, which is required for controlling/configuring the STM torque
motor.
General terms of business
Including notes on the warranty.
Table 2

About this manual
05/STM-48V/en/2011-04-01/CW 9
1.4 Symbols in this manual
To give you quick access to information, the following symbols
will be used in this guide:
Symbol
Designation
DANGER
Dangers for persons.
Nonobservance causes death or serious injuries.
WARNING
Dangers for persons.
Nonobservance can cause death or serious injuries.
NOTICE
Information on avoiding material damage, for explanation or to optimize the work
processes.
Prerequisite for a handling instruction.
Handling instruction, also measures in a warning or note.
1.
2.
3. ...
Step-by-step handling instruction.
Observe the order.
Component/spare part represented in a graphic.
Part/detail shown in a graphic which is part of a spare part or which must be pro-
vided by the customer.
(10), (/10/)
Reference in the text or in a handling instruction to a part that is represented in a
graphic.
Table 3
1.5 Terms used in this manual
Term
Meaning
Controller
Frequency converter, controller, AC converter, servo converter, control system
Table 4

Basic safety notes
10 05/STM-48V/en/2011-04-01/CW
2 Basic safety notes
2.1 Intended use
The STM was designed to rotate loads, workpieces and objects.
The STM may only be operated in combination with a controller.
The module is intended for installation in a machine. The re-
quirements of the applicable guidelines must be observed and
complied with.
The module may be used only in the context of its defined appli-
cation parameters.
Any other use or use exceeding that specified is an infringement
of use for intended purpose. The manufacturer bears no liability
for damage resulting from such use.
To use this module as intended, it is also essential to comply with
the manufacturer's specifications regarding commissioning, as-
sembly, operation and ambient conditions.
2.2 Environmental and operating conditions
The module may be used only in the context of its defined
application parameters (see chapter 5, page 17 and catalog).
Make sure that the module's range of application is outside
the explosive area.
Make sure that the environment is clean and the ambient
temperature corresponds to the specifications per the catalog.
Make sure that the environment is free from splash water and
vapors as well as from abrasion or processing dust. Excepted
are modules that are designed specially for contaminated
environments.

Basic safety notes
05/STM-48V/en/2011-04-01/CW 11
2.3 Controlled production
The module represents the state of the art and the recognized
safety rules at the time of delivery. However, it can present risks
if, for example:
•The module is not used in accordance with its intended
purpose.
•The module is not installed or maintained properly.
•The EC Machinery Directive, the VDE directives, the safety
and accident-prevention regulations valid at the usage site, or
the safety and installation notes are not observed.
2.3.1 Protective equipment
When the module is in use, protective equipment must be used to
catch flying parts or to switch the drive into a safe mode should
the module or part of the module fail.
The protective equipment must comply with the requirements of
the EC Machinery Directive and IEC/EN 60204-1.
The STM's housing must be grounded via the controller.
2.3.2 Special standards
The following harmonized standards were adhered to:
•Industrial scientific and medical (ISM) radio-frequency
equipment - Electromagnetic disturbance characteristics -
Limits and methods of measurement (IEC/CISPR 11:2003 +
A1:2004, modified + A2:2006); German version
EN 55011:2007 + A2:2007 class A (this is equivalent to EN
61000-6-4:2004)
•Electromagnetic compatibility (EMC) - Part 6-2: Generic
standards - Immunity for industrial environments (IEC 61000-
6-2:2005); German version EN 61000-6-2:2005
2.3.3 Constructional changes, attachments, or modifications
Additional drill holes, threads, or attachments that are not offered
as accessories by SCHUNK may be attached only with permis-
sion of SCHUNK.
Non-authorized modifications results in the exclusion from prod-
uct liability.

Basic safety notes
12 05/STM-48V/en/2011-04-01/CW
2.3.4 After-sales service
SCHUNK's after-sales service is available for technical informa-
tion and questions concerning SCHUNK products.
Call the contact. (see chapter 18, page 78)
State the ID of the module. (see chapter 6.1, page 20)
2.4 Obligations of the manufacturer/operator
2.4.1 Choice of personnel and personnel qualifications
Work on the module may be carried out by authorized personnel
only. The legal minimum age must be observed.
The assembly, commissioning and repair of the module may be
performed only by trained specialist personnel who have been
instructed how to perform the said work activities.
The manufacturer/operator must ensure that the personnel are
adequately and appropriately trained to perform work on the
module assigned to them.
2.4.2 Organizational measures
Make sure that at least one copy of this manual is kept in the
direct vicinity of the machine/system where the module is
installed, and that it is accessible for the relevant persons.
Ensure that personnel have read and understood this manual,
especially chapter 2 "Basic safety notes".
Provide instructions about and observe the safety and
accident-prevention regulations that apply at the site of use.
Provide instructions about and observe the environmental
protection regulations that apply at the site of use.
Provide protective equipment.
Check the personnel’s conduct regarding the awareness of
safety and hazards from time to time.
2.4.3 Disposal
Send components of the module for recycling or properly
dispose of them according to the local regulations.

Basic safety notes
05/STM-48V/en/2011-04-01/CW 13
2.5 Personnel qualification
2.5.1 Safety-conscious working
Avoid any manner of working that may interfere with the
function and operational safety of the module.
Observe the safety and accident-prevention regulations valid
at the usage site.
Wear protective equipment.
2.5.2 Safety measures during transport
When transporting and handling very heavy modules, take the
corresponding safety precautions.
Make sure the cables have strain relief.
2.5.3 Safety measures during operation
Only operate the module when all protective equipment has
been fitted and is in full working order.
Check the module at least once per shift for externally visible
damage and faults.
Report any changes including changes in operational
behaviour to the responsible place/persons immediately. If
necessary immediately shut down and lock out the
machine/system.
2.5.4 Behaviour in the event of faults or emergencies
If faults on the module occur which could impair safety or if the
operational performance indicates the occurrence of a fault:
Shut down the machine/system immediately, lock it and report
the fault to the responsible place/persons.
Faults may be eliminated by trained and authorized personnel
only.
Only restart the machine/system when the cause of the fault
has been eliminated.

Basic safety notes
14 05/STM-48V/en/2011-04-01/CW
2.6 Notes on particular risks
Risk of injury from objects falling and being ejected!
Provide protective equipment to prevent objects from falling or
being ejected, such as processed workpieces, tools, chips,
fragments, rejects.
Adapt the operating conditions, e.g. reduce the cycle time.
Risk of injury when the machine/system moves
unexpectedly!
Do not move parts by hand when the energy supply is
connected.
Do not reach into the open mechanism or the movement area
of the module.
Remove the energy supplies before installation, modification,
maintenance, or adjustment work.
Perform maintenance, modifications, and additions outside
the danger zone.
For all work, secure the module against accidental operation.
Risk of injury due to moving parts if these are controlled
incorrectly!
Possible causes for control errors:
•Incorrect cabling or wiring
•Removal of safety devices
•Software errors
•Sensor and signal transmitter errors
•Entry of incorrect parameters prior to start-up
•Defective module

Basic safety notes
05/STM-48V/en/2011-04-01/CW 15
Risk of burns due to contact with hot surfaces!
During operation, the surface temperature of the STM may ex-
ceed +85°C (+185°F).
Allow the module to cool down to at least +40°C (+104°F)
before working on the module.
Measure the surface temperature before touching the module.
Wear protective gloves, if necessary.
Risk of electric shock due to contact with live parts!
Before conducting work on the machine and the auxiliary
equipment, disconnect them from the power supply and make
sure they cannot be accidentally switched back on again.
Wait until the frequency converter is discharged.

Warranty
16 05/STM-48V/en/2011-04-01/CW
3 Warranty
The warranty is valid for 24 months from the delivery date to the
production facility under the following conditions:
•Observation of the maintenance intervals (see chapter 14.1,
page 69)
•Observation of the ambient conditions and operating
conditions (see chapter 2.2, page 10)
Also observe our general terms of business.
The warranty does not cover the following:
•Damage occurring as a result of incorrect operation.
•Claims under warranty are excluded when repair or
intervention is carried out by persons not authorized to do so.
•If accessories are used which are not designed for the
module.
4 Scope of delivery
The scope of delivery includes:
•Electrical Rotary Module Type STM in the version ordered
•An exemplar of the Assembly and Operating Manual incl.
Translation of original EC declaration of incorporation
The following accessories are required for the module:
•Connection cable in the version ordered:
–length 5m, 10m, 15m or 20m
The following accessories are available for the module:
•MCS-12 Controller
Order accessories separately.
For additional accessories, see catalog or www.schunk.com.

Description of the module
05/STM-48V/en/2011-04-01/CW 17
5 Description of the module
5.1 STM torque motor
5.1.1 Design and description of the STM
1 Basic carrier (fixed)
2 Rotor (moving)
3 Bearing flange
4 Sealing flange
5 Plug connection
6 Plug (sensor cable)
7 Plug (power cable)
Figure 1 Components
The STM is a completely mounted, permanently excited synchro-
nous motor in a cylindrical housing with a center bore.
The STM has an integrated measuring system. A temperature
sensor is integrated in the motor winding.
The STM belongs to the category of torque motors. The
typical characteristics of a torque motor are its high torque, low
speeds and a strong rigidity.
The STM is used typically for rotating and pivoting of large
masses. The center bore can be used as a media feed-through.
The STM must be operated using a controller. The following op-
erating modes can be set:
•Torque-controlled
•Speed-controlled
•Position-controlled
Overview
Torque motor
Area of application
Operating modes

Description of the module
18 05/STM-48V/en/2011-04-01/CW
5.1.2 Mechanical interfaces
The STM is mounted on a single Franke bearing. This bearing is
lubricated via one-time grease lubrication. Under normal operat-
ing conditions lubrication for 20.000 operating hours is sufficient.
The mechanical interfaces are shown on the drawing in chap-
ter 16 page 73.
5.1.3 Electrical interface
Figure 2 STM schematic diagram
An incremental encoder (TTL signals) is installed as position
feedback unit.
Maintenance-free
lubrication
U
V
W
Winding
Encoder
system
tem
8
P
E
2
Temperature sensor KTY84
STM plug connection
STM
STM basic carrier
UVW + PE
Encoder + Temp.
Controller
Encoder
Encoder
values
Supply
voltage

Description of the module
05/STM-48V/en/2011-04-01/CW 19
5.1.4 Type key and nameplate
Order designation
STMxxx -xxx -S-x - xx
Type
STM210 = d 210 mm
STM170 = d 170 mm
STM135 = d 135 mm
voltage
048 = 48 V rated motor voltage
cable version
S = with plug connection for power component and en-
coder cable
brake
N = without brake
B = with brake
IP protection class
40 = IP40 protection class
The nameplate is attached to one of the broad sides of the mod-
ule.
Designation
Specification
manufacturer
SCHUNK GmbH & Co. KG
type / model - protection class
STM210-48-S-N-40
ID
03068xx
rated torque (MN)
10 Nm
voltage (UN)
48 V
current (IN)
7 A
Table 5 Data on the nameplate (example STM210)

Technical Data
20 05/STM-48V/en/2011-04-01/CW
6 Technical Data
6.1 Technical Data des STM
Further technical data can be found in our catalog. The most re-
cent version applies.
6.1.1 Technical Data STM135
Note
All the technical data shown in the chart refer to the indicated
heat conducting surface.
Type
STM135 48V
ID
03068xx
Heat conducting surface [mm²]
57686
Mechanical operating data
deadweight [kg]
2,7
dimension (Ø x L) [mm]
135x 63
center bore (Ø) [mm]
15
ambient temperature [°C (°F)]
Min.
+5 (+41)
Max.
+55 (+131)
mass moment of inertia of rotating parts [kg m²]
0,001431
max. mass moment of inertia [kg m²]
0,05
rotation range [°]
>360 (turning endlessly)
positioning accuracy *1[°]
0,02
*1Distribution of the end positions of 100 successive motions. When approaching from the same direction.
measuring system
Incremental
IP rating
40
permissible operating mode
S1 - continuous operation*2
*2Applies only if the preconditions in chapter 7.1, page 27 are fulfilled. Otherwise, S6 - continuous mode with intermittent load is
the permitted operating mode.
Electrical connection - required cable cross-sections and number of wire strands
power [mm²]
3 x 1
grounding [mm²]
1 x 1
shaft encoder [mm²]
8 x 0,25
temperature sensor [mm²]
2 x 0,25
specifications for the integrated motor
motor type
synchronous
switching
star
Table of contents
Other SCHUNK Engine manuals

SCHUNK
SCHUNK ERS170 User instructions
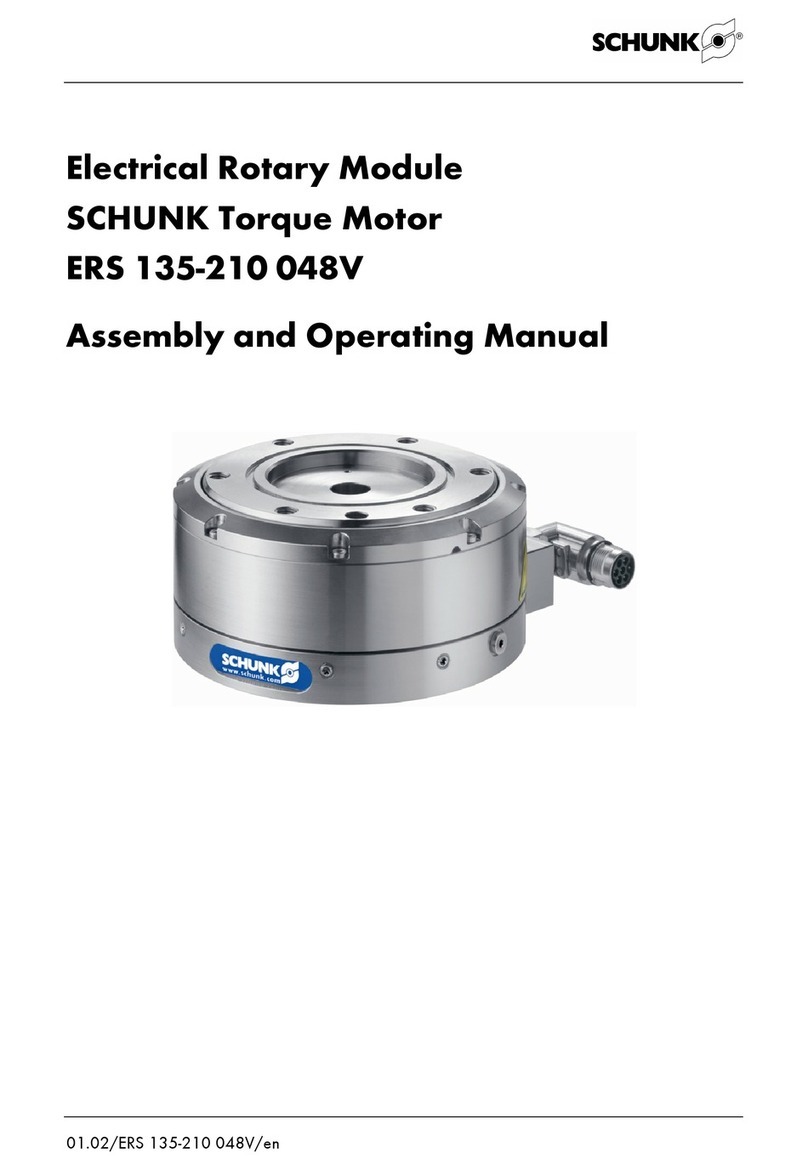
SCHUNK
SCHUNK ERS 135 048V User instructions
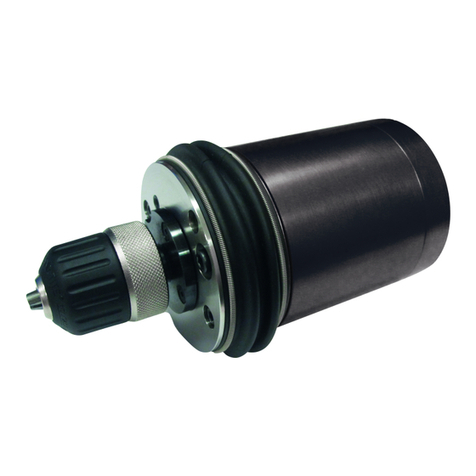
SCHUNK
SCHUNK MFT User instructions

SCHUNK
SCHUNK TENDO Turn DSE User instructions
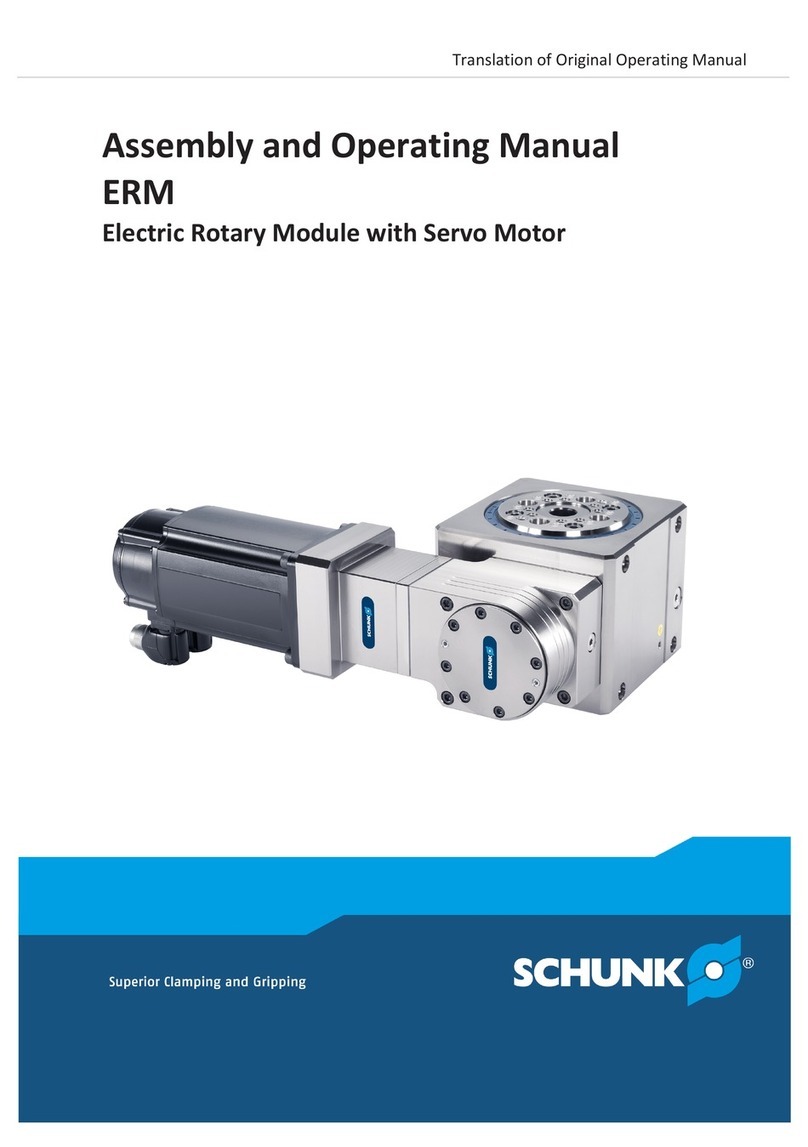
SCHUNK
SCHUNK ERM Series User instructions
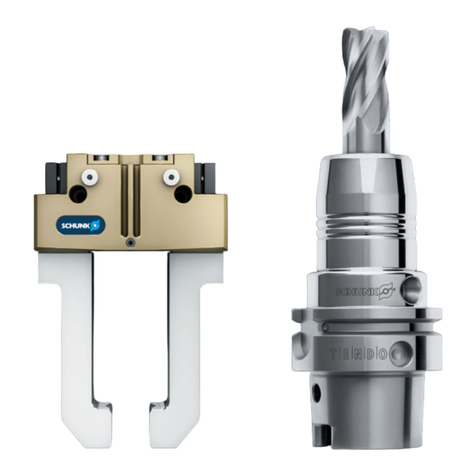
SCHUNK
SCHUNK LDM Series User instructions
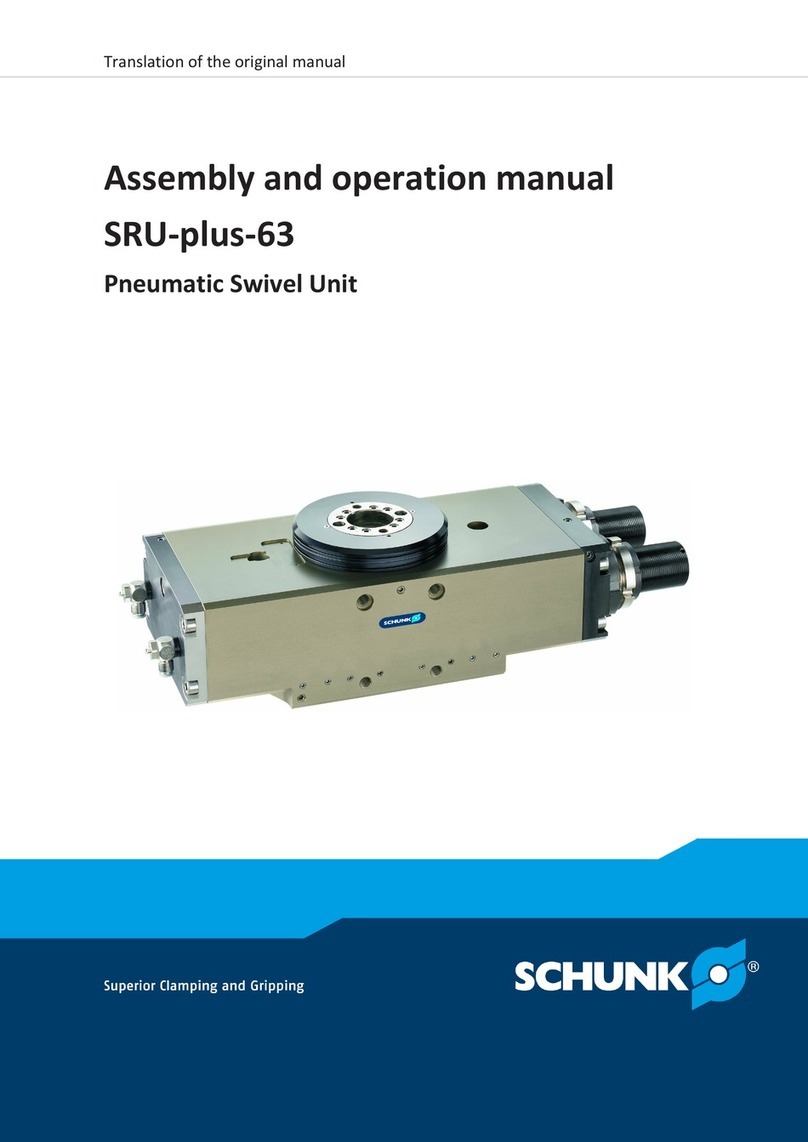
SCHUNK
SCHUNK SRU-plus-63 Installation and operating instructions
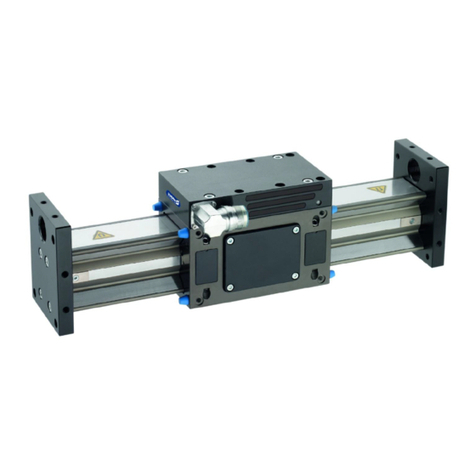
SCHUNK
SCHUNK LDN Series User instructions
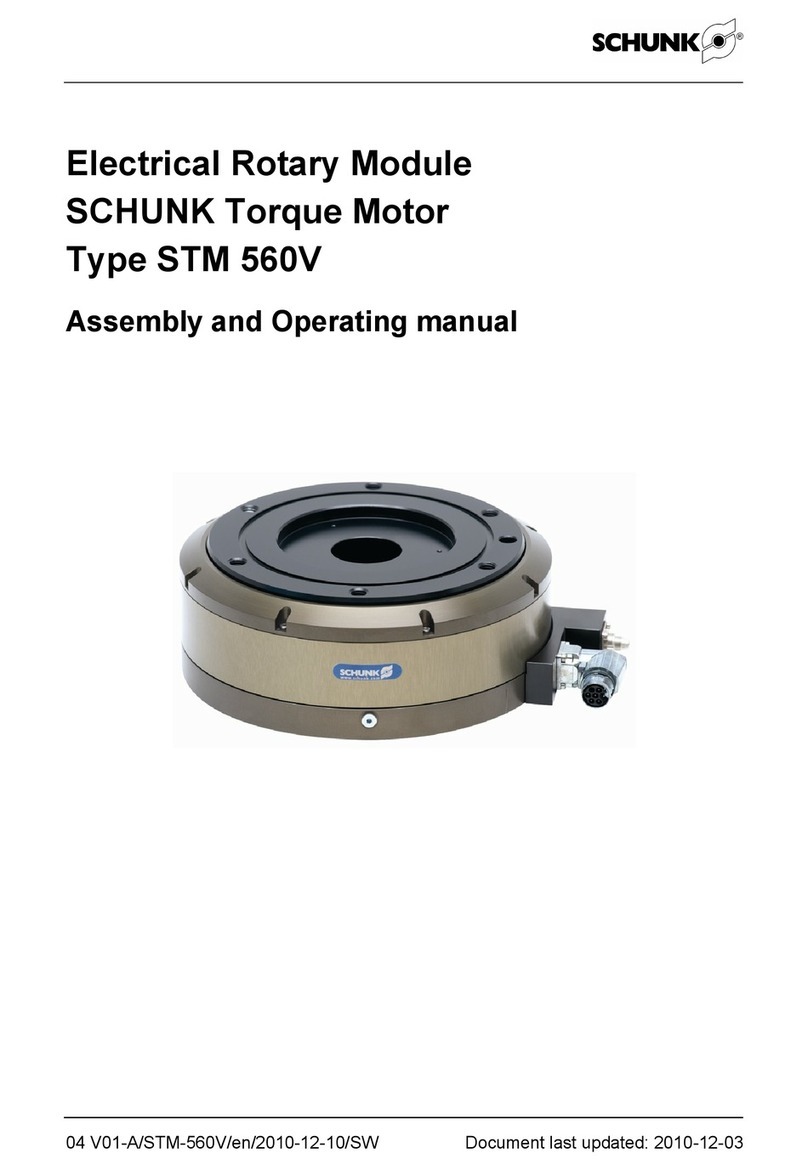
SCHUNK
SCHUNK STM 560V Series User instructions
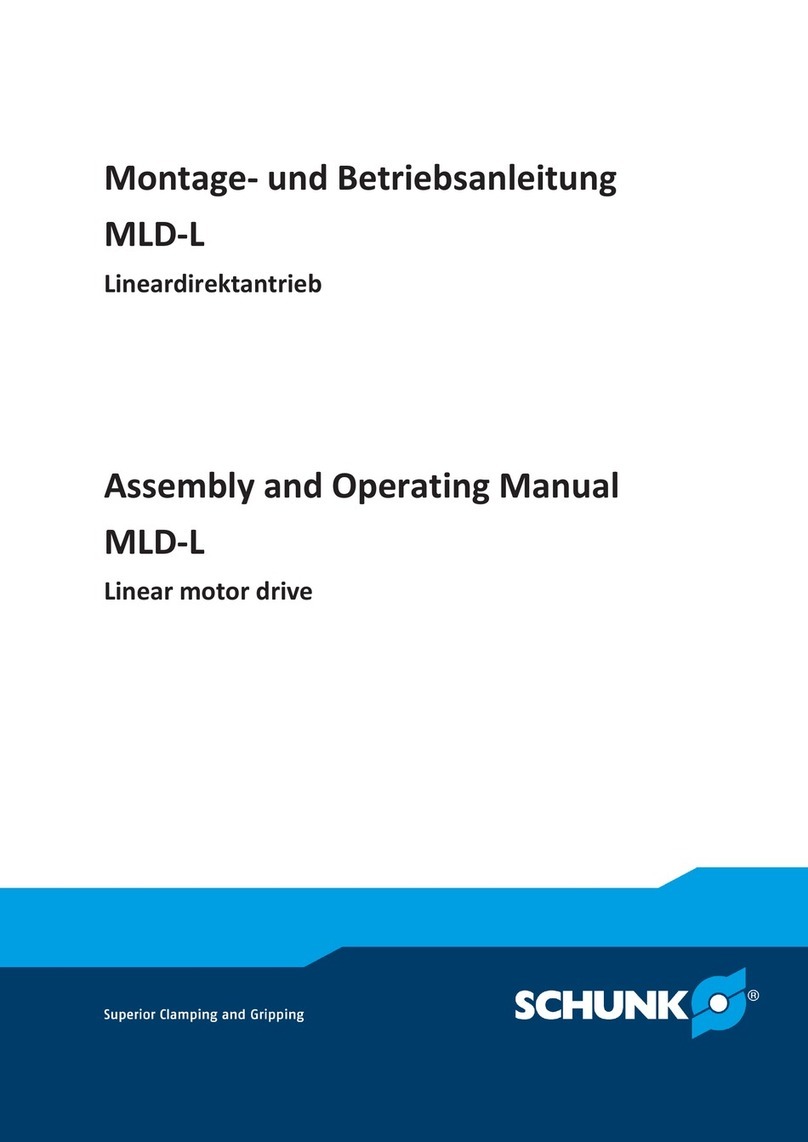
SCHUNK
SCHUNK MLD-L User instructions