Dynapac CP142 Instruction Manual

DYNAPAC
CP142
Box 504, SE-371 23 Karlskrona, Sweden
Phone: +46 455 30 60 00, Fax: +46 455 30 60 30
www.dynapac.com
O142EN1
OPERATION

19
ILF015WO1

Reservation for changes.
Printed in Sweden.
Pneumatic Tire Roller
CP142
Operation
O142EN1, May 2004
Diesel engine:
Cummins 4B4.5 - 99C
These instructions apply from:
CP142 PIN (S/N) *2163BR2000*
The CP142 Pneumatic Tire Roller uses a modular ballast system which consists of bolt
on ballast boxes that provide an accurate and uniform tire load. The roller is designed for
compaction of roads, airfields, dams and similar constructions.
The CP142 compacts asphalt, concrete, base courses and subbase courses efficiently
and at a high rate. Seperate information is available on request concerning accessories
and optional equipment.
The illustrated machine in this manual can be equipped with optional equipment.
KEEP THIS MANUAL FOR
FUTURE REFERENCE

2CP142 O142EN1
CONTENTS
Safety instructions – Personal safety
Special caution – Machine or component damage
The safety manual, which accompanies each
machine, must be studied by each operator of
the roller. Always follow the safety rules and
do not remove the manual from the roller.
This manual contains instructions for operation and use of
the roller. For care and maintenance information, see the
MAINTENANCE, CC142 manual.
Remember that when you start and drive a
cold machine, the hydraulic fluid is cold and
the braking distance will be longer than nor-
mal until the machine reaches normal working
temperature.
WARNING SYMBOLS
SAFETY MANUAL
GENERAL
CALIFORNIA
Proposition 65 Warning
Diesel engine exhaust and some of its
constituents are known to the State of
California to cause cancer, birth defects,
and other reproductive harm.
Page
Safety instructions (Also read the safety manual) .......... 3
Safety when driving ..................................................... 4, 5
Safety decals, location and description ....................... 6, 7
Machine and engine plates .............................................. 8
Instruments and controls ................................................. 9
Instruments and controls, functional description ..... 10, 11
Before starting .......................................................... 12-14
Starting .......................................................................... 15
Operation ................................................................. 16-17
Ground caontact pressure chart (valid for 14 ply) ........ 17
Scrapers positions ........................................................ 18
Braking .......................................................................... 19
Parking .......................................................................... 20
Instructions for Lifting .................................................... 20
Instructions for towing ................................................... 21
Transportation ............................................................... 22
Operating instructions – Summary ................................ 23

3CP142 O142EN1
SAFETY INSTRUCTIONS (Also read the safety manual)
1. The operator must be familiar with the contents of the OPERATION
MANUAL before starting the roller.
2. Make sure that all instructions in the MAINTENANCE MANUAL are
followed.
3. Only trained and/or experienced operators are allowed to drive the
roller. Passengers are not allowed on the roller. Remain seated during
all operation.
4. Never use the roller if it is in need of adjustment or repairs.
5. Board and leave the roller only when it is stationary. Use the grips and
railings that are provided. A ”three-point grip” is recommended
whenever you board or leave the machine—both feet and one hand, or
one foot and both hands in contact with the machine.
6. Always use the Roll Over Protective Structure (ROPS) when the
machine is used on risky ground.
7. Drive slowly in sharp bends.
8. Avoid driving at an angle on slopes; drive straight up or down.
9. When driving close to unsafe edges or holes, make sure that at least 1/4
of the outer tire width is firmly on material that has already been
compacted.
10. Make sure that there are no obstacles in the direction of travel, on the
ground or overhead.
11. Drive extra carefully on uneven ground.
12. Use the safety equipment provided. The seat belt must be worn on
machines fitted with ROPS.
13. Keep the roller clean. Clean dirt and grease from the operator’s platform
without delay. Keep all signs and decals clean and clearly legible.
14. Safety measures before refueling:
– Stop the engine.
– Don’t smoke.
– No naked flame in the vicinity.
– Ground the nozzle of the filling device against the tank to prevent
sparks.
15. Before repairs or service:
– Place chocks against the drums/wheels and against the strike-off
blade.
– Lock the articulation if necessary.
16. Hearing protectors are recommended if the noise level is higher than 85
db(A). The noise level will vary depending on the surface being worked
on by the machine.
17. Make no changes or modifications on the roller that could affect safety.
Changes may only be made following written consent by Dynapac.
18. Do not use the roller until the hydraulic fluid has reached its normal
working temperature. Braking distance can be longer than usual if the
fluid is cold. See starting instructions in the OPERATION MANUAL.

4CP142 O142EN1
SAFETY WHEN DRIVING
Driving near an edge
When driving close to unsafe edges or holes, make
sure that at least 1/4 of the outer tire width is firmly on
material that has already been compacted.
Remember that the machine’s center of
gravity is displaced outwards when stee-
ring to one side. For example, it moves to
the right when steering to the left.
At least
1/4
Fig. 1 Wheel position when driving close
to edge.

5CP142 O142EN1
SAFETY WHEN DRIVING
Slopes
Fig. 2 Driving on slopes.
Max. 20°
or 36%
The ROPS (Roll Over Protective Structure)
is always recommended when driving on
slopes or insecure ground.
Where possible, avoid all driving
across
a
slope. Instead, drive up and down on slop-
ing ground.
The tipping angle is measured on level, hard ground
and a stationary machine without ballast. The steering
angle is zero (machine moving straight forward) and all
tanks full. Remember that loose ground, steering of the
machine, driving speed and increase in height of the
center of gravity (for example, with accessories) may
cause the machine to topple even on a smaller slope
than specified here.

6CP142 O142EN1
SAFETY DECALS, LOCATION AND DESCRIPTION
41114
3, 2
13 671 79
10 5 4
13
1379176 13
12
8
3

7CP142 O142EN1
SAFETY DECALS, LOCATION AND DESCRIPTION
Crush zone, articulation.
Maintain a safe distance
from the crush zone.
Warning for hot surface.
The surface must not be
touched.
Warning for rotating engine
components. Keep your
hands at a safe distance
from the danger zone.
The operator is urgently
requested to read the safety
manual, and the operation
and maintenance instructions
before using the machine.
1.
2.
3.
4.
903424
903459
903423
903422
5.
Lifting
point
Diesel fuel
Tire pressure
9.
8.
588176
14.
6.
Hydraulic
fluid
272372
10.
Battery
disconnecter
12.
904835
7.
11.
Handbooks
903425
Mass Kg
904870
Hoisting plate
Study the chapter about
towing before disengaging
the brakes.
Danger of being crushed.
904895
Securing
point
13.
382751
374765
Min 250kPa/ 35psi
Max 850kPa/ 120psi
791275
Sound Power
level
105

8CP142 O142EN1
MACHINE AND ENGINE PLATES
Machine plate
Fig. 3 Left hand side
1. Machine plate
Fig. 5 Engine
1. Type plate
2. EPA sign (USA)
1
Engine plate
The engine type plate (1) on Cummins engines is
located on the left side of the toothed-belt cover. The
plate shows the type of engine, serial number and
engine data. Please state the serial number of the
engine when ordering spares. See also the engine
manual.
The machine type plate (1) is located on the left side of
the steering column. The plate shows the
manufacturer’s name and address, type of machine,
PIN “Part Identification Number” (serial number), weight
in working order, engine power and year of
manufacture. CE markings and the year of
manufacture may be omitted on machines supplied to
markets outside the EU.
1
IMPORTANT ENGINE INFORMATION
This engine conforms to YYYY U.S. EPA
and California regulations for
heavy duty non-road compression
ignition diesel cycle engines as
applicable.
THIS ENGINE IS CERTIFIED TO OPERATE
ON DIESEL FUEL
XXXXXXX
2
Serial number on frame
Fig. 4 Front frame
1. Serial number
The serial number (1) of the machine is punched on the
front right edge of the forward frame beam. This
number is identical with the PIN (serial number) on the
machine data plate.
1
Cummins Engine Company, Inc
Columbus, Indiana
47202-3005
Warning Injury may result and warranty is voided
if fuel rate, rpm or altitude exceed published
maximumvaluesforthismodelandapplication.
DateofMFG.
Made in Great Britain.
XXXXXXX
CID/L. CPL Engine Serial No.
Family Cust. Spec.
Engine Model
Valve lash Timing-TDCInch Int. Exh.
MM Int. Exh. Fuel rate at rated HPcold
#
Firing Order
RatedHP/KW at RPM
FR
Please state the machine´s PIN when ordering
spares.

9CP142 O142EN1
INSTRUMENTS AND CONTROLS
Fig. 6 Instruments and control panel
12 13
17
15
16
1
2
3
4
56
11
10
9
147 8
18 19 20 21 22
23 24 25 26
27
1. Light switch, working lights
2. Light switch, parking/headlights
3. Light switch, bright headlights
4. Turning lights
5. Hazard flashers
6. Hazard beacon
7. Start/Stop switch
8. Gear selector, low/high
9. Sprinkler switch, Man/Off/Auto
10. Water pump switch
11. Sprinkler timer
12. Fuel gauge
13. Tachometer
14. RPM control
15. Reserve/Parking brake knob
16. Horn
17. Forward/Reverse lever
18. Control light, charging
19. Control light, hydraulic fluid temperature
20. Control light, engine coolant temperature
21. Control light, fuel level
22. Hourmeter
23. Control light, air cleaner
24. Control light, hydraulic filter
25. Control light, engine oil pressure
26. Control light, brakes
27. Handbook compartment
= Option

10 CP142 O142EN1
INSTRUMENTS AND CONTROLS, FUNCTIONAL DESCRIPTION
1 Working lights, switch
(Opition)
2 Parking/headlights, switch
(Opition)
3 Bright headlights, switch
(Opition)
4 Turning lights, switch
(Opition)
5 Warning flashers, switch
(Opition)
6 Hazard beacon, switch
(Opition)
7 Starter switch
8 Gear selector, low/high
9 Sprinkler, switch
10 Water pump switch
(Opition)
11 Sprinklertimer,
switch
12 Fuel gauge
13 Tachometer
14 RPM control
Item in Designation Symbol Function
fig. 6
Turn to the right to switch on the working
lights.
Turn right to switch on the parking lights
and further right to switch on the headlights.
Turn right to switch on the main beam.
In the left position, the dipped beam lights.
Turn left to switch on the left direction
indicator, etc. The flashing indicator is OFF
in the middle position.
Turn right to switch on hazard flashers.
Turn right to activate the hazard beacon.
In position , the electric circuit is broken.
In position , all instruments and electric
controls are powered.
In position , the start motor is activated.
Tortoise = Working speed, low.
Hare = Transport speed, high.
The sprinkler system is on all the time in
MAN mode. The sprinkler system is turned
off in OFF mode. The sprinkler system is on
in AUTO mode when the Forward/Reverse
lever is not in neutral.
Turn right to activate the other water pump, if
any.
The switch has six different timer position to
regulate the amount of water to the wheels.
The left position gives least water. The right
position gives most water.
Indicates level in the fuel tank.
Indicates engine speed in RPM. Multiply the
meter value by 100.
Release/lock with the centre button. Pull out
the control to increase engine speed, push in
to reduce. Turn/screw the handle to finely
adjust the speed. Turn clockwise to increase,
anticlockwise to reduce.
MAN
O
AUTO

11CP142 O142EN1
INSTRUMENTS AND CONTROLS, FUNCTIONAL DESCRIPTION
15 Reserve/Parking brake knob
16 Horn, switch
17 Forward/Reverse lever
18 Warning lamp,
charging
19 Warning lamp,
hydraulic fluid temperature
20 Warning lamp,
engine coolant temperature
21 Warning lamp,
fuel level
22 Hourmeter
23 Warning lamp,
air cleaner
24 Warning lamp,
hydraulic filter
25 Warning lamp,
engine oil pressure
26 Warning lamp,
brakes
27 Handbook compartment
Item in Designation Symbol Function
fig. 6
Press to activate the reserve brake. Press
when the machine is stationary to activate the
parking brake.
Pull out to release both brakes.
Press to sound the horn.
The lever must be in neutral to enable the
engine to start; the engine will not start if the
forward/reverse lever is in any other position.
The forward/reverse lever controls the driving
direction and speed of the roller. Move the
lever forward to drive the roller forward, etc.
The speed of the roller is proportional to the
distance of the lever from the neutral position.
The further from neutral the higher the speed.
The lamp lights when the alternator is not
charging the battery. The lamp goes out when
the alternator is charging the battery.
If the light lights, the hydraulic fluid is too hot.
Do not drive the roller; cool the fluid by
allowing the engine to idle and locate the fault.
If the light lights, the engine is too hot.
Stop the engine immediately and locate the
fault. See also the engine manual.
When the lamp lights, there is only enough
fuel left for a short distance. Refuel as soon
as possible.
Engine running time is indicated in hours.
If the light lights while the engine is running at
full RPM, the air cleaner needs cleaning or
replacing.
If the light lights while the engine is running at
full RPM, the hydraulic filters need changing.
Stop the engine immediately if the warning
lamp lights and identify the cause. See
engine instruction manual.
The lamp lights when the reserve/parking
brake knob (15) is pressed.
Storage space for the roller’s operator and
safety manuals.
P
STOP

12 CP142 O142EN1
BEFORE STARTING
Battery disconnecter
– Switching on
Fig. 8 Engine compartment
1. Battery disconnecter
The battery disconnecter is located in the engine
compartment. Open the engine hood and set the key
(1) to the ON position. All systems of the roller are
connected to the battery.
The engine hood must be unlocked during
operation, so the battery power can be
disconnected quickly if necessary.
Operator’s seat – Setting
Set the operator’s seat in a comfortable position and so
that the controls are easily accessible.
The seat has the following adjustment capabilities:
– Length adjustment (1)
– Backrest slope (2)
– Weight adjustment (3)
Fig. 9 Operator’s seat
1. Length setting
2. Seat-back slope
3. Operator’s weight
Engine compartment cover
Remember to do daily service. See the maintenance
manual.
Ensure that the engine hood support is
securely in position for all work in the
engine compartment.
Fig. 7 Access door
1. Engine oil dipstick
2. Battery disconnecter
3. Engine compartment
1
12
3
3
2
1

13CP142 O142EN1
BEFORE STARTING
Turn the starter switch (7) to position I. All warning
lamps should light for about 5 seconds and the beeper
should sound. Make sure that the warning lamps light.
Check that the warning lamps for charging (18), oil
pressure (25) and parking brake (26) light.
The hourmeter (22) records the number of hours so
long as the engine is running.
Make sure that the reserve/parking brake
knob (15) is pushed in. If the parking brake
is not applied, the roller may start to roll
when starting the engine on sloping gro-
und.
Instruments and lights
– Control
Seat belt
Fig. 10 Instrument panel
7. Starter switch
12. Instrument, fuel level
15. Reserve/Parking brake knob
18. Control light, charging
22. Hourmeter
25. Control light, engine oil pressure
26. Brake lamp
Fig. 11 Operator’s seat
1. Seat belt
If the roller is equipped with a ROPS (Roll Over
Protective Structure), always use the seat belt and wear
a hard hat.
Replace the seat belt if it shows signs of
wear or has been subjected to severe force.
Ensure that the anti-slip on the platform is
in good condition; replace with new anti-
slip if friction is poor.
1
25
18
15
12
7
2226

14 CP142 O142EN1
Fig. 13 Ballastboxar
FÖRE START
The ballast boxes can be added or removed as
necessary. To add bolt-on ballast boxes:
With 8 boxes (option)
1. Begin to fit ballast box (1) at the very rear right hand
and then (2) at the very rear left hand.
Continue in chronological order, see picture 13.
2. Securely fasten the screws.
With 6 boxes (STD):
1. Ignore ballast boxes (1) and(2) in figure 12 and 13,
where the additional foot steps will be mounted.
Start to fit the ballast box (3) and then (4) on
respectively places. Continue in chronological order,
see picture 13.
2. Securely fasten the screws.
The ballast boxes weight is approx. 1,02 ton-
nes (2.250 lbs) each. Use secure handling
equipment to move the boxes.
Bolt-on ballast boxes
Fig. 12 Max. ballast, 8 boxes
1357
7
8642
A
B
531
A - Tapered screw connecting the pairs of boxes.
B - Mounting screw (2 per box)
To remove the bolt-on ballast boxes:
Push the left hand side ballast box in as shown by the
arrow to reduce tension on screw "A".
Remove screw "A".
Hook lifting device to lifting eye of box.
Remove screws "B".
Lift and remove box.
To remove ballast boxes the two front most boxes have
to be removed first to gain access to the second row.
To install ballast boxes the two on the rearmost position
have to be installed first.
When using less than eight ballast boxes, the boxes
must be installed on the front most possible position to
achieve the best weight distribution possible.
Always add/remove two boxes at a time. The
weight must be evenly distributed on the roller.

15CP142 O142EN1
Warm up the engine at idling speed for a few minutes,
longer if the ambient temperature is below +10°C
(50°F).
Check while warming up that the warning lamps for oil
pressure (25) and charging (18) are out. The warning
lamp (26) for the parking brake should still light.
Remember that when you start and drive a
cold machine, the hydraulic fluid is cold
and the braking distance will be longer
than normal until the machine reaches
normal working temperature.
Make sure that ventilation (extraction) is
adequate if the engine is run indoors. Risk
of carbon monoxide poisoning.
STARTING
Starting the engine
Set the forward/reverse lever (17) in neutral. The
engine can only be started with the lever in neutral.
Make sure that the reserve/parking brake
knob (15) is definitely pushed in. If the
parking brake is not applied, the roller may
start to roll when startingthe engine on
sloping ground.
Turn the start switch (7) to the position I. The switch
lights until the required pre-heating is ready. Check the
fuel gauge and make sure that all the warning lamps
light.
Within 10 seconds after finished pre-heating: Turn the
start switch to the starting position and release it
immediately when the engine has started.
Do not run the starter motor too long;
preferably wait a minute or so if the engine
does not start.
Fig. 14 Instrument panel
7. Start switch
12. Fuel gauge
14. RPM control
15. Reserve/Parking brake knob
17. Forward/Reverse lever
7
20
25
13
14
17
18
12
15
26
Fig. 15 Instrument panel
13. Tachometer
18. Control light, charging
20. Warning lamp, engine coolant temp.
25. Warning lamp, engine oil pressure
26. Warning lamp, parking brake

16 CP142 O142EN1
Driving the roller
Fig. 16 Instrument panel
13. Tachometer
14. RPM control
OPERATION
Fig. 17 Instrument panel
8. Gear selector
15. Reserve/Parking brake knob
17. Forward/reverse lever
Fig. 18 Instrument panel
15. Reserve/Parking brake knob
19. Warning lamp,
hydraulic fluid temperature
20. Warning lamp, engine coolant
temp.
13
14
17
8
19 20
15
Under no circumstances may the machine
be operated from the outside. The operator
must remain seated inside the machine
during all operation.
Pull up the rev control (14) until the tachometer (13) (if
any) shows 2200 r/min (for the CE machine, 1800 r/
min). Turn the control knob (14) to adjust. Counter-
clockwise = increase. Clockwise = reduce.
Check that the steering is working by turning the steer-
ing wheel once to the right and once to the left, while the
roller is stationary.
Make sure that the area in front of and
behind the roller is clear.
Turn the gear selector (8) to the desired setting.
Pull up the reserve/parking brake knob and
check that the warning lamp for the parking
brake is out. When starting the roller on a
slope, be prepared that it may begin to roll.
Low mode (working speed) - 10 km/h (6 mph)
High mode (travelling speed) - 19 km/h (12 mph)
The high mode may only be used for trave-
ling driving on a smooth surface.
Carefully move the forward/reverse lever (17) to the
desired direction of travel. Speed increases as the
lever is moved from the neutral position.
Speed must always be regulated with the
forward/reverse lever and not by changing
speed of the engine.
Test the reserve brake by pressing the
reserve/parking brake knob (15) while the
roller is running slowly forward.
Check now and then while driving that the gauges show
normal readings. In the event of abnormal values or if the
beeper sounds, stop the roller and the engine
immediately. Check and remedy any fault, see also the
maintenance manual and the engine manual.
Inspect the tire tread now and then to detect
asphalt compound that has fastened—this is
likely before the tires are sufficiently warm.
Mixing 2-4% cutting fluid in the sprinkler water
for the tires can prevent sticking.

17CP142 O142EN1
Wheel load Tire inflation pressure, kg/cm²
kg 240 350 480 620 720 830
GROUND PRESSURE, kPa
1130 350 400 430 460 510 590
1360 380 430 460 480 530 610
1585 400 450 470 510 560 630
GROUND CAONTACT PRESSURE CHART (valid for 14 ply)
Wheel load Tire inflation pressure, psi
lbs 35 50 70 90 105 120
GROUND PRESSURE, psi
2500 51 58 62 67 74 86
3000 55 62 67 70 77 88
3500 58 65 68 74 81 91
OPERATION
Instrument panel
Fig. 19 Instrument panel
10. Sprinkler switch
11. Sprinkler timer (option)
Drive toward the compaction area. Start spraying water
on the tires before going on hot asphalt.
Turn on the sprinkler pump with switch (10).
When the tires reaches the normal working temperatur,
the sprinkler timer (option) can be used to give an
economic water consumption.
10 11
kPa
psi

18 CP142 O142EN1
Operation
Fig. 20 Operation position
1. Coco mats
2. Lever
SCRAPERS POSITIONS
To set the scrapers and coco mats in operation
position, release the lever (2) and let the coco mats
rest on tires.
The rear wheels have individual levers for each
scraper/mat.
To disengage the coco mats on the front wheels pull
the lever (2) and lock in off position.
The rear wheels have individual levers – lock each
scraper/mat in off position.
Disengaged
Fig. 21 Disengaged position
1. Coco mats
2. Lever
1
1
2
2
Other manuals for CP142
2
Table of contents
Other Dynapac Garbage Disposal manuals
Popular Garbage Disposal manuals by other brands
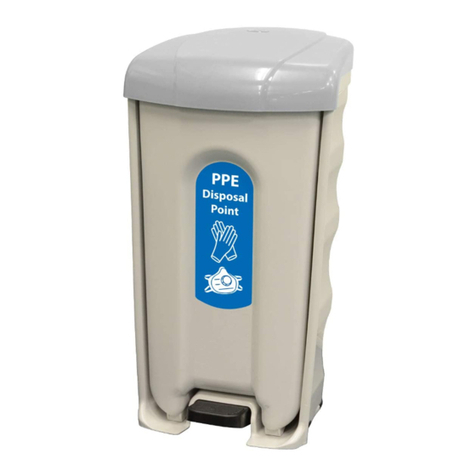
Glasdon
Glasdon NEXUS SHUTTLE BIN Operator Instruction Leaflet
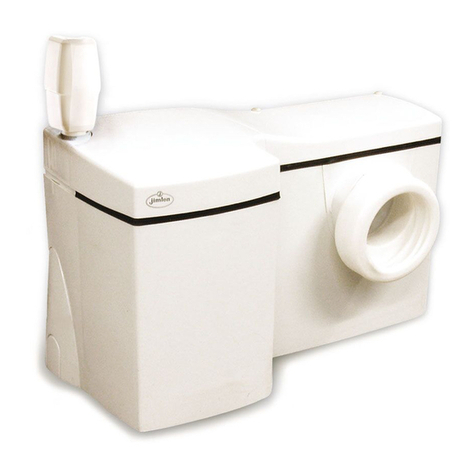
JIMTEN
JIMTEN CICLON L T-604 Maintenance and Instruction Manual

KitchenAid
KitchenAid KWC-200 installation instructions
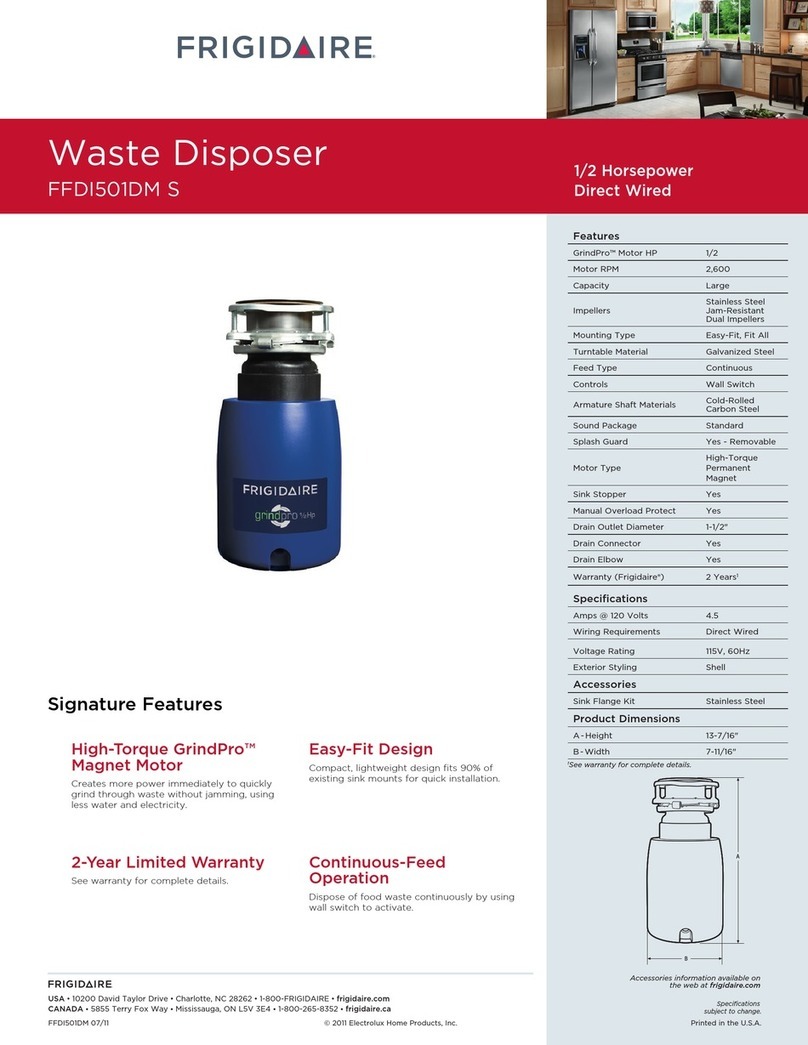
Frigidaire
Frigidaire FFDI501DMS Product specifications

InSinkErator
InSinkErator Evolution Compact Manual reset
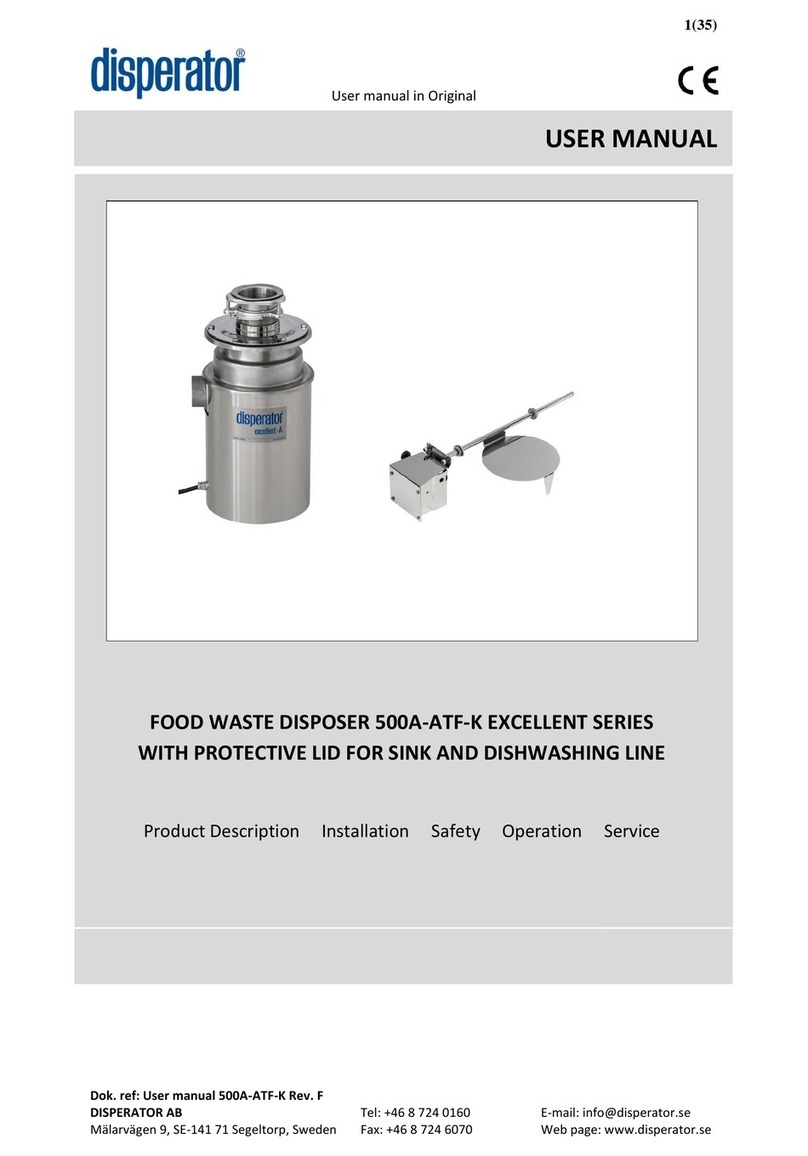
disperator
disperator 500A-ATF-K user manual