DynaQuip JE Series User manual

JE Series Product Guide
MODELS: JE2S, JE3S, JE5S, JE7S, JE15S, JE30S
MULTI-VOLTAGE ON-OFF SMART ELECTRIC ACTUATORS
PLEASE READ THESE INSTRUCTIONS CAREFULLY BEFORE INSTALLING
OR CONNECTING POWER TO THE ACTUATOR. THE ACTUATOR MUST
BE INSTALLED, OPERATED AND REPAIRED BY QUALIFIED PERSONNEL
COMPLYING WITH ALL APPLICABLE CODES, STANDARDS AND SAFETY
REGULATIONS. DAMAGE CAUSED BY NONCOMPLIANCE TO THESE
INSTRUCTIONS IS NOT COVERED BY OUR WARRANTY.
INTRODUCTION
This document provides installation, operation and maintenance instructions
for DynaQuip JE Series electric on/o smart actuators. These actuators are
typically used to operate quarter-turn valves. Every actuator has been fully
tested prior to shipment to ensure trouble-free operation.
STORAGE
Actuators should be stored in a clean, dry environment at all times. Do not
install the actuator outdoors or in humid environments without immediately
supplying power to activate the internal heater. The thermostatically
controlled heater will help prevent possible damage caused by
condensation build up inside the actuator.
MOUNTING
The actuator can be mounted in
any orientation. Valves can be
direct mounted to the actuator
using a standard ISO5211
international mounting pad.
ANTI-CONDENSATION HEATER
The electric actuator has an internal thermostatically controlled anti-
condensation heater. The 4-watt heater is automatically activated when power
is supplied to the actuator. It is strongly recommended that power remain ‘ON’
at all times to protect the actuator from damaging eects of condensation. The
heater does not require a separate power supply or additional wiring.
ENCLOSURE RATING
Actuator is rated IP67 weatherproof. The housing is anti-corrosion polyamide.
Do not use these actuators in explosion-proof or hazardous applications.
TEMPERATURE RATING
Operating temperature range of the actuator is -4˚ to 158˚F (-20˚ to 70˚C).
DUTY CYCLE AND MOTOR PROTECTION
JE Series actuators have built-in electronic over-torque protection against
valve jams. These actuators are rated 75% duty cycle.
LED POWER ON AND DIAGNOSTIC LIGHT
The external LED status light provides visual communication between the
actuator and the user. The following chart will show the basic LED functions.
LED Status Actuator Operational Status
Closed: Solid Red
Open: Solid Green Power On
From Open to Closed: Red/Orange
From Closed to Open: Green/Orange Actuator Moving
From Open to Closed: Flashing Red
From Closed to Open: Flashing Green
Over-torque condition or possible problem
with motor/control board or operational
BSR system working
Intermittent Orange Actuator in MANUAL mode (after 90
seconds) or battery needs charging
MANUAL OVERRIDE
DynaQuip JE Series electric actuators have a de-clutchable manual override
for use during setup or loss of power situations. To operate the manual
override, first move the manual override selector located on the side of the
actuator to the ‘MAN’ position. Next, rotate the manual override knob on the
actuator to the desired position, anywhere between 0 (closed) and 90 (open)
degrees. These markings are located on top of the red cover. When finished,
make sure the yellow pointer is within the 0 to 90 working quadrant. Then
move the manual override selector lever back to the ‘AUTO’ position. You can
now resume operation by deactivating power, which resets the actuator.
Do NOT operate the manual override without
first selecting ‘MAN’. Failure to do so may
cause gear damage.
VISUAL VALVE POSITION INDICATOR
Actuators are supplied with a visual valve position indicator. The dome-style
indicator is black with a large yellow pointer. It is located on the top of the
red cover. There are 0 and 90˚ marks molded into the red cover to indicate
the valve position. ‘0’ indicates closed, and ‘90’ indicates an open position.
The yellow pointer should rotate within the 90˚ quadrant.
MAINTENANCE
There are no field serviceable parts inside the actuator (except battery for
models with BSR operation) and no parts that require regular maintenance.
The gear drive is pre-lubricated for life. Actuator should be cycled at least
once per month. The housing may be cleaned with warm soapy water (no
solvents). DO NOT PRESSURE WASH.
ISO5211
Valve
Mounting
Pad
Manual Override
Selector Lever
MAN: Manual Mode
AUTO: Automatic Mode
Visual Position Indicator
(shown in open position)
Manual Override Knob
LED Power On and
Diagnostic Light

ELECTRICAL WIRING
Actuators are multi-voltage capable with automatic voltage sensing. Actuator
circuit should be isolated from other actuators and equipment with its own
independent, fuse protected system. All connections are made using the
supplied DIN plug connectors. The larger connectors accept 8 to 10.5 mm
diameter round cable. The smaller connectors accept 5 to 6mm diameter
round cable.
DIN PLUG CONNECTORS
Disassemble DIN connector as shown in diagram below. Wires are connected
to screw terminals marked 1, 2, 3 and ground. To access screw terminal block
(2), remove the retainer screw (4) and use a small screwdriver to pry terminal
block from housing (3). To ensure water-tightness, use correct cable diameter,
ensure connector gasket (1) is installed, and tighten retainer screw (4) securely.
Failure to do so could allow water ingress and cause major damage to the
actuator.
OPERATION: ON/OFF ACTUATORS
Standard on/o actuator requires power to open and power to close.
Actuator stays in the last known position upon loss of power. On receipt of
a continuous voltage signal, the motor runs and a flat gear system rotates
the actuator output (valve) 90 degrees. The motor is automatically stopped
in each position by internal limit switches. On receipt of a reversing
continuous signal, the motor turns in the opposite direction, reversing the
actuator position.
OPERATION: ON/OFF ACTUATOR WITH BSR OPTION
Wiring is the same as standard on/o version for actuators with BSR (Battery
Spring Return) option. The actuator requires power to open and power to
close. Actuator will move to failsafe position via battery power with loss
of external power. Actuator returns to pre-failure position upon power
resumption. Maintaining power in either the open or closed position will
trickle charge the internal battery and maintain a full charge.
WIRING MAIN POWER CONNECTION
Power is connected to the actuator via the large grey DIN plug connector.
Wires are connected to screw terminals located inside the connector. User/
installer to supply a three-way switch, control relay, PLC or other suitable
switching device to control the actuator position.
Power supplied to PIN 1 and PIN 2: CLOSED POSITION
Power supplied to PIN 1 and PIN 3: OPEN POSITION
Ground: Connect the flat pin on DIN connector to ground.
NOTES: The Neutral (AC voltages) or Negative (DC voltages) must be
connected to PIN 1. Power should be maintained, either in the open or
closed position to activate the internal heater. This heater will help prevent
condensation build-up inside the actuator. ACTUATOR SHOULD HAVE
ITS OWN FUSED AND ISOLATED CIRCUIT. Do not connect actuators in
parallel.
WIRING POSITION
CONFIRMATION LIMIT SWITCHES
Two auxiliary dry contact limit switches
are provided to confirm the actuator
(valve) open and closed position. Use
of these switches is optional. Switch
rating 3A@125/250VAC, 30VDC
resistive load. Do not connect a
ground to this connector.
PIN 1: Common
PIN 2: Signal to confirm
CLOSED POSITION
PIN 3: Signal to confirm
OPEN POSITION
Wire Identification for Optional Pre-Wired DIN Cables
PIN 1 - Brown PIN 3 - Black
PIN 2 - Blue GROUND - Green/Yellow
Before
connecting
power, confirm
correct voltage is
being supplied.
Do not over
tighten screw
(4), correct
torque 3.5lb/in.
JE2S - 7S Series JE15 - 30SSeries
PowerPower Position
Confirmation
Position
Confirmation
Earth
Ground
Customer
Supplied
Switch
Open Closed
Power
VAC or VDC
LS2
CLOSED
Signal
LS1
OPEN
Signal
1
2
3
5
4
21
3
21
3
JE Series Product Guide
PN 194522.001 Rev. B
This manual suits for next models
6
Other DynaQuip Controllers manuals
Popular Controllers manuals by other brands
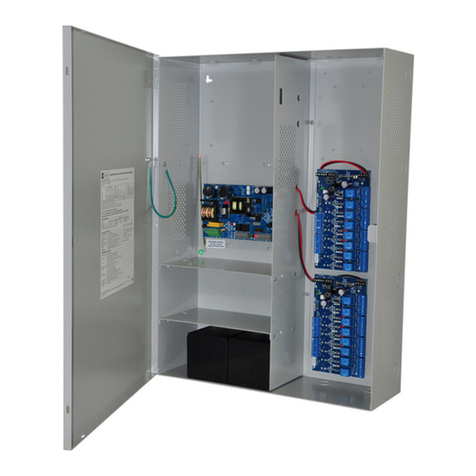
Altronix
Altronix Maximal3FD installation guide
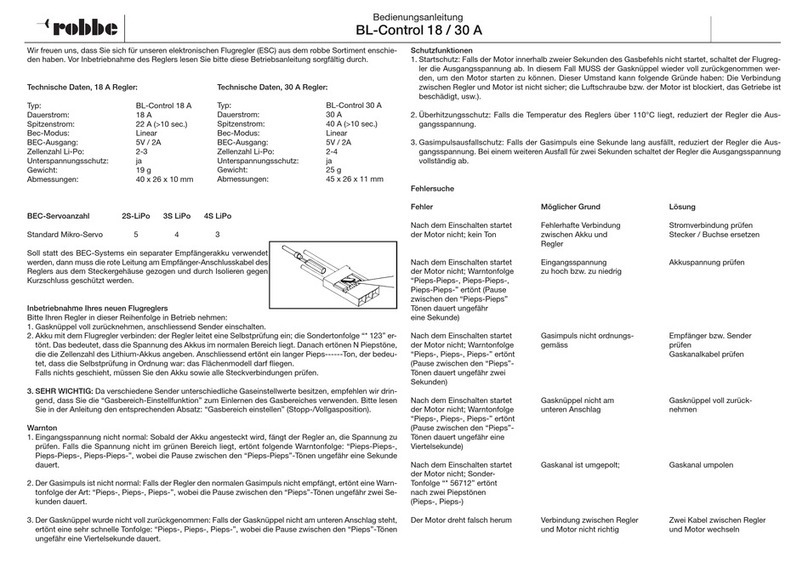
ROBBE
ROBBE BL-Control 18 A operating instructions
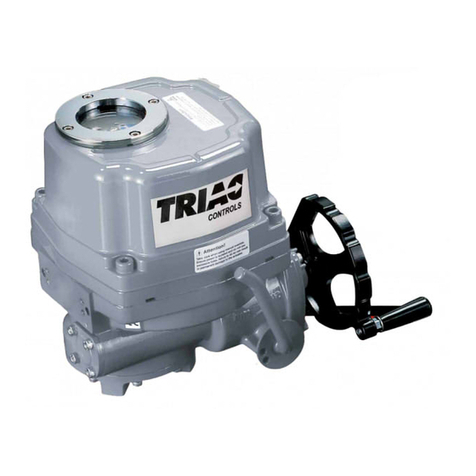
A-T Controls
A-T Controls Triad Controls WE Series Installation and operation manual
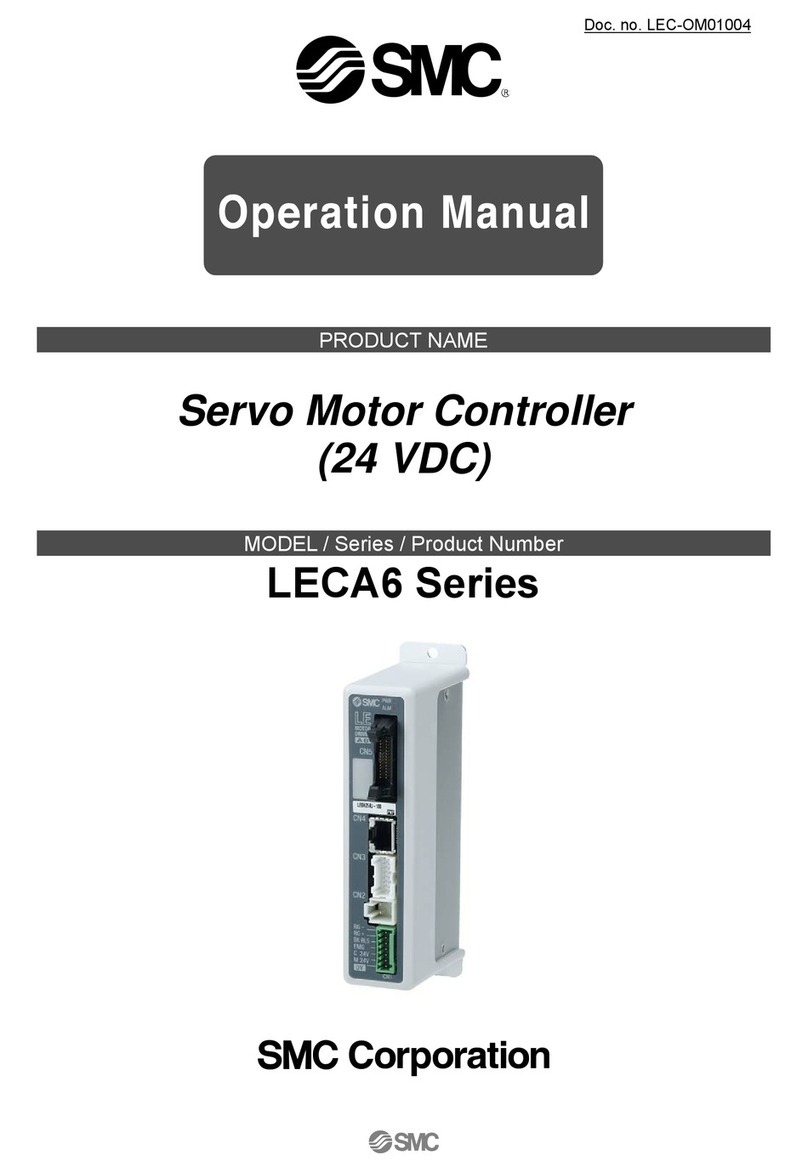
SMC Corporation
SMC Corporation LECA6 Series Operation manual

Elan
Elan RS232 installation manual
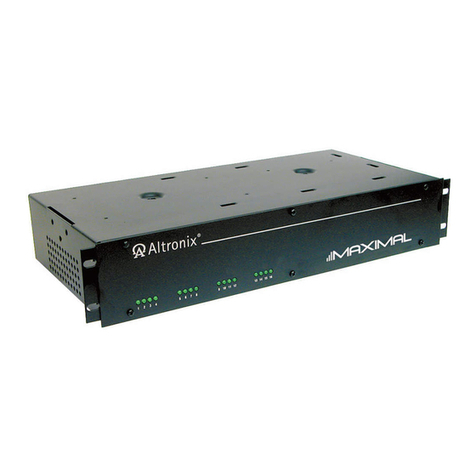
Altronix
Altronix Maximal1RHD installation guide