eao 09 Series User manual

www.eao.com
Series 09 – Rugged Keypad.
Operating instructions and safety instructions
Operating instructions

www.eao.com 2
Operating instructions and safety instructions
Project
S09, 1707, 1708 Rugged Keypad
Document Number
1707900701
Document
Description
Operating and safety instructions for the keypads
EAO Automotive GmbH & Co. KG
Richard-Wagner-Straße 3
08209 Auerbach/Vogtl.

www.eao.com 3
Change History
Version
Valid
from
SW-
Version
Change Description Status Author Date
01 initial intial BEC 15.10.2019
02 CAN Open Safety added Update ESF 05.11.2019
04 Correction in Chapter 8.4 Update SCI 15.11.2019
05 CAN communications extended Update GOM 05.02.2020
06 4.05.001
Document number corrected
Chapter 8.2 updated
Chapter 11.2 updated
Review ESF, column for SW-Version in
Change History added
Update SCI 25.02.2020
07
4.05.001 Chapter 11.1.2
- Output current Wakeup Out changed
- circuit diagrams for wakeup added
- example messages J1939 fixed
Update SCI/GOM 03.03.2020
08 4.05.001 - Chapter 0 added Update GOM 06.03.2020
09 6.03.000 - Chapter 7.4 use inside closed vehicles
- Chapter 14 Cleaning updated Update ESF 18.01.2021
10 6.04.000
- Chapter 9.6 (Error handling) added
- Chapter 13 (RCC) added
- RCC application note (proportional-digital)
added
- Structure of lighting objects and
interaction of objects explained
- Differences between SW-Version
4.05.001 and 6.03.000 explained
- Application Note for manually change the
Baudrate, node-ID and stuck button time
added
Update MAR 02.06.2021

www.eao.com 4
Referenced Dokuments
Reference
Version
Author
Date
K-Matrix J1939 20 HEP 04.02.2021
K-Matrix CANopen/CANopen-Safety
20
HEP
04.02.2021
1707 product information 02 EBJ 12.05.2021
CiA CANopen® application layer and general
communication profile „CAN poster“]
CiA 301 “CANopen application and communication
profile”
4.2.0 21.02.2011
CiA 320 “Services and protocols for sleep and wake-up
handling”
1.0.0 14.03.2018
SAE J1939-73: Application Layer - Diagnostics 05.2017
SAE J1939-21: Data Link Layer
03.2016
SAE J1939-81: Network Management 03.2017
Series 09, Rugged CAN Keypads - CE-Certification -
Compliancy of EAO Products - HDI July,15, 2021

www.eao.com 5
Table of contents
1. Safety warnings..................................................................................................12
Intended use ......................................................................................................12
2. Proper environment............................................................................................13
3. General description ............................................................................................13
4. Technical specification .......................................................................................15
5. Scope of delivery................................................................................................16
6. Storage ..............................................................................................................16
7. Mechanical installation/mounting........................................................................17
Installation in a panel by means of retaining clamps (retaining clamp version) ...17
Installation in a panel with self-locking nuts (screw-in version) ...........................18
7.2.1 Mounting sequence............................................................................................18
Installation of the symbol inserts ........................................................................19
Use inside closed vehicles .................................................................................20
8. Electrical installation and interface operation......................................................21
Electrical installation...........................................................................................21
8.1.1 Pinning...............................................................................................................21
Booting and resetting behaviour.........................................................................21
9. SAE J1939 communication protocol...................................................................23
Composition of the CAN Identifier ......................................................................23
Keypad specific values.......................................................................................24
Installation in a network......................................................................................24
Service Data – Proprietary A..............................................................................25
9.4.1 Read Data object Request .................................................................................25
9.4.2 Read data object reply OK .................................................................................26
9.4.3 Read data object reply NOK...............................................................................26
9.4.4 Write data object request ...................................................................................27
9.4.5 Write data object reply OK .................................................................................28
9.4.6 Write data object reply NOK...............................................................................28
Process Data Proprietary A and B......................................................................29
9.5.1 Process Data Proprietary A – Rx configuration messages .................................29
9.5.2 Process Data Proprietary B – Tx process data...................................................29
Diagnostics ........................................................................................................30
9.6.1 Current Module Temperature .............................................................................30
9.6.2 Current voltage...................................................................................................31
9.6.3 Error handling ....................................................................................................31
9.6.3.1 Active diagnostic trouble codes (DM1) ...............................................................31

www.eao.com 6
9.6.3.2 Previously active diagnostic trouble codes (DM2) ..............................................33
9.6.3.3 Diagnostic data clear/reset of previously active DTCs (DM3) .............................35
Save settings to Volatile/Non-Volatile memory ...................................................35
Custom Layer Settings .......................................................................................36
9.8.1 Manually configure the Baudrate........................................................................36
9.8.2 Manually configure the Node-ID .........................................................................37
Basic Functions..................................................................................................37
9.9.1 Button press data ...............................................................................................37
9.9.1.1 Stuck Button Time..............................................................................................37
9.9.1.2 Reconfigure Stuck Button Time..........................................................................37
9.9.2 Symbol Illumination ............................................................................................38
9.9.2.1 Activating Symbol Illumination............................................................................38
9.9.2.2 Choosing the active brightness setting for the symbol LEDs ..............................39
9.9.2.3 Changing the brightness setting for the symbol LEDs ........................................40
9.9.2.4 Changing the temporal patterns for the symbol LEDs (flash modes) ..................40
9.9.2.5 Adjusting the timings in flash modes ..................................................................41
9.9.2.6 Changing the global brightness for the symbol LEDs .........................................41
9.9.3 Halo-Ring Illumination ........................................................................................42
9.9.3.1 Activating Halo lighting .......................................................................................42
9.9.3.2 Choosing the active brightness setting for the halo LEDs...................................43
9.9.3.3 Changing the brightness setting for the Halo LED illumination ...........................44
9.9.3.4 Choosing the temporal patterns for the Halo LED illumination............................45
9.9.3.5 Changing the global brightness for the Halo LED illumination ............................46
9.9.3.6 Choosing the active colour setting for the Halo LED illumination ........................46
9.9.3.7 Changing the colour setting for the Halo LED illumination ..................................47
9.9.3.8 Adjusting the timings in flash modes ..................................................................48
Changes between Software version 04.05.001 and 06.03.000 or newer ............49
10. CANopen communication protocol .....................................................................50
Composition of the CAN Identifier ......................................................................50
Standard communication parameters.................................................................50
Installation in a CAN-network .............................................................................50
SDO communication ..........................................................................................52
PDO communication ..........................................................................................53
10.5.1 PDO communication parameter .........................................................................54
10.5.2 Mapping of PDOs...............................................................................................54
10.5.3 Automatic COB-ID update..................................................................................56
Diagnostics, Error Codes ...................................................................................57

www.eao.com 7
Save settings to Volatile and Non-Volatile memory ............................................58
Custom Layer Settings .......................................................................................59
10.8.1 Manually configure the baud rate .......................................................................59
10.8.2 Manually configure the Node-ID .........................................................................60
Basic functions...................................................................................................60
10.9.1 Pressed Key data...............................................................................................60
10.9.1.1 Stuck Button Time..............................................................................................60
10.9.1.2 Reconfigure Stuck Button Time..........................................................................61
10.9.2 Symbol Illumination ............................................................................................61
10.9.2.1 Activating Symbol Illumination............................................................................61
10.9.2.2 Choosing the active brightness setting for the symbol LED’s..............................62
10.9.2.3 Changing the brightness setting for the symbol LED’s........................................62
10.9.2.4 Changing the temporal patterns for the symbol LED Illumination .......................63
10.9.2.5 Changing the global brightness for the symbol LED Illumination ........................63
10.9.3 Halo-Ring Illumination ........................................................................................63
10.9.3.1 Activating Halo Ring Illumination ........................................................................63
10.9.3.2 Choosing the active brightness setting for the Halo LED’s .................................65
10.9.3.3 Changing the brightness setting for the Halo LED’s ...........................................65
10.9.3.4 Choosing the temporal patterns for the Halo LED’s for flashing modes ..............66
10.9.3.5 Changing the global brightness for the Halo LED’s ............................................66
10.9.3.6 Choosing the active colour setting for the Halo LED’s ........................................67
10.9.3.7 Changing the colour setting for the Halo LED’s ..................................................67
10.9.3.8 Adjusting the timings in flash modes ..................................................................68
Changes between Software version 04.05.001 and 06.03.000 or newer ............69
11. Special functions ................................................................................................70
Sleep/Wakeup, Power Saving ............................................................................70
11.1.1 Sleep/Wakeup over CAN ...................................................................................70
11.1.2 Sleep/Wakeup over 2 wire hardware interface ...................................................70
11.1.3 Sleep/Wakeup summary ....................................................................................72
Structure of lightning objects ..............................................................................72
11.2.1 Depending objects .............................................................................................73
11.2.2 Linking the objects .............................................................................................74
Communication timeout......................................................................................76
12. CANopen-Safety communication protocol ..........................................................76
13. Rotary Cursor controller .....................................................................................76
Communication Objects .....................................................................................77
Working with the RCC ........................................................................................78

www.eao.com 8
14. Operation ...........................................................................................................78
General information............................................................................................78
15. Cleaning.............................................................................................................79
16. Optional accessories..........................................................................................79
17. Liability for quality defects ..................................................................................79
18. Service, repair....................................................................................................80
19. Decommissioning, disposal ................................................................................80
20. Declaration of Conformity...................................................................................80

www.eao.com 9
List of abbreviations and units
CA Controller Application
CAN Controller Area Network
CiA CAN in Automation
CLS Custom Layer Setting
COB Communication Object
CS Command Specific
DLC Data Length Count
DM Diagnostic Message
EDS Electronic Data Sheet
EOL End Of Line
EU European Union
HB High Byte
HMI Human-Machine-Interface
IP International Protection
ISO International Organization for Standardization
kbps Kilo bit per second
LB Low Byte
LED Light emitting diode
LSB Least Significant Bit
mm milli meter
MOT Ministry of Transport
MSB Most Significant Bit
NMT Network Management
NVM Non Volatile Memory
PDO Process Data Object
PDU Payload Data Unit
PGN Parameter Group Number

www.eao.com 10
Prop A Proprietary A
Prop B Proprietary B
RCC Rotary Cursor Controller
RGB Red-Green-Blue
Rx Receive
SAE Society of Automotive Engineers
SDO Service Data Object
SPN Suspect Parameter Number
Tx Transmit

www.eao.com 11
Used symbols
Caution!
Indicates a hazardous situation which, if not avoided, may result in a
minor or moderate injury
Attention
Describes information on installation which, if ignored, can lead to
malfunctions
Note
Indicates a situation which, if not avoided, may result in property
damage
Indicates an executive activity
Indicates an application tip

www.eao.com 12
1. Safety warnings
The safe system handling requires knowledge of the operating instructions.
Caution!
Connect the power supply in accordance with the safety regulations
for electrical equipment.
Risk of injury
Damage to the keypad
Note
Avoid shocks and impacts to the keypad during installation
Damage to or destruction of the keypad
The supply voltage must not exceed the specified limit.
Damage to or destruction of the keypad
Protect the cable and the connector from damages
Damage to or destruction of the keypad
Never kink the cable, do not bend the cable in tight radii. Dynamic
movement of the cable should be avoided as far as possible, as well as
chafing of the cable on system components.
Damage to the cable or connector
Intended use
The modules were developed for applications in vehicles with MOT approval within the EU and
for intelligent control with CAN bus integration. The robust, modular design with a protection
degree of up to IP 67 and the possibility of customer-specific adaptations and the arrangement
of keypad symbols are facts that make the devices the best choice for harsh use in heavy-duty
and special vehicles.
The keypads may only be operated within the parameters specified in the technical data.
The keypads must be used in such a way that no persons are endangered or machines
damaged in the event of failure or malfunction.
Commissioning must be carried out by qualified personnel.

www.eao.com 13
2. Proper environment
See Technical specification.
Note
If possible, avoid abrupt changes in the operating temperature of the
keypad, cable and connector.
Damage to the keypad, cable or connector
Caution!
Do not operate the keypad in:
Potentially explosive atmospheres
Applications where the keypad, cable and connector are completely or
partly submerged for extended periods of time
Situations in which the keypad, cable and connector are subjected to
harsh external shocks and impacts
Do not use for remaining in final customer installations due to
validation not completed
Risk of injury
Damage to the keypad, cable or connector
The design of the keyboard (keys can still be pressed) means that keys are
protected from freezing as long as the keys remain accessible and can be
pressed. This means that the keyboard can also be used in snow and ice.
3. General description
Series 09 Rugged Keypads offer high reliability: The modules are designed for an intelligent
control with CAN bus integration. The robust, modular design with protection degrees of up to
IP6K7 and the possibility of customer-specific adaptations and the arrangement of symbol
inserts predestine the devices for harsh use in heavy-duty and special vehicles. The modules
are as well designed for ECE certification.
High reliability and functional safety are indispensable for the control of safety-relevant
applications in vehicles and machines – whether in construction machinery, construction
vehicles, agricultural machinery or in various types of special and commercial vehicles. Harsh
environmental conditions and low back panel depth require a robust and compact product
design. In addition, the control and signalling devices must be precisely configurable both
mechanically and electronically for the respective application. The high-quality Rugged Keypad
meets these requirements with a cutting-edge system integration.

www.eao.com 14
Typical applications
Special vehicles such as fire engines, road sweepers, cleaning vehicles, dustcarts, snow
clearing vehicles and snow groomers. Heavy-duty vehicles such as construction and
agricultural vehicles
Advantages
Individual 4-segment and RGB Halo Ring Illumination
Intelligent HMIs with CAN bus integration
Robust, ergonomic and innovative design with a protection degree of up to IP6K7
(mounted state front: IP6K7; back: IP20 without plugged connector). Protection degree
for assembled situation in responsibility of customer application.
Interchangeable ISO 7000 symbols or customer-specific symbols
Robust and innovative design
The design of the Rugged Keypads is characterised by a robust and innovative construction.
The control and signalling devices, which are protected up to IP6K7, function reliably at an
operating temperature of – 40 °C to + 85 °C. The low back panel depth and robust clip-in or
screw-in mounting allow a flexible and easy installation, either vertically or horizontally. The
high-quality devices also offer an excellent haptic and, thanks to the bright RGB LED halo and
LED symbol illumination, are clearly visible in daylight and at night. An attractive and
configurable 4-segment halo button illumination is integrated as standard.
The customisable illumination provides the operator with excellent visual feedback and is
combined with a unique, contemporary design.
Durability
The series 09 CAN modules are produced in our automotive competence centre located in
Germany. This allows us to apply our many years of comprehensive experience as an original
equipment manufacturer (OEM) in the automotive industry to the heavy duty and special
vehicles markets. At the same time, this offers EAO customers high quality, durable products
and services. The development and production process is aligned and executed according to
automotive standards, including qualified suppliers. This requirement ensures EAO high
quality products and solutions.
CAN bus integration
Thanks to the CAN bus integration, the devices are integrated intelligently and easily into a
CAN system – as standard with a Deutsch DT series connector. The device controls its function
according to the CAN command.
Designed for E1 applications and CAN bus integration
The robust control units with flexible illumination are ideally suited for use in heavy duty and
special vehicle applications.

www.eao.com 15
4. Technical specification
Validation ongoing and not completed:
Mechanical characteristics
Actuation force: 6,5 N
Overload: 250 N
Service life – Rugged Keypad: up to 1 million cycles of operation
Electrical characteristics
Operating voltage range: 8-32 VDC
Illumination
LED symbol illumination – colour: white LED
LED halo ring illumination – colour: RGB
Symbols
Symbols in accordance with ISO 7000
Customer-specific symbols on request
Connections/interfaces
CAN interface (ISO 11898)
CAN protocols: CANopen (CiA 401), SAE J1939
Baudrate: 250 (default), 500 kb/s (software configurable)
Ambient conditions (validation not yet completed)
Operating temperature: -40 °C … +85 °C
Storage temperature: -40 °C … +85 °C
Protection degree
IP6K7 protection (mounted state front: IP6K7; back: IP20 without plugged connector).
Protection degree for assembled situation in responsibility of customer application.
Attention
The protection degree of up to IP67 to be achieved depends on the front
panel and type of mounting and must be ensured by the customer.

www.eao.com 16
5. Scope of delivery
1 Rugged CAN keypad, with cable and connector (type Deutsch 6 pin)
Mounting material, depending on version
Retaining clamp version: 6 retaining clamps graduated according to mounting panel
thickness for 1mm - 4mm
Screw-in version: 4 nuts each with washers and spacers and 1 sleeve
Attention
For symbol inserts: quantity according to order, separate scope of delivery.
6. Storage
See Technical specification.
Note
If possible, avoid abrupt changes in the storage temperature of the keypad
cable and connector.
Damage to the keypad, cable or connector
Do not expose the open contacts of the unprotected connector to
condensing air humidity.
Damage to the keypad, cable or connector
Check the delivery immediately after unpacking with regard to
completeness and transport damages.
If any damage or incompleteness is found, please contact the supplier
immediately.
Optional accessories can be found in the annex Optional accessories.

www.eao.com 17
7. Mechanical installation/mounting
2 mounting versions are available: Installation in a panel by means of retaining clamps
(retaining clamp version) or screws (screw-in version).
Installation in a panel by means of retaining clamps
(retaining clamp version)
See drawing “1707 product information (drawing no. 1707940001)”.
If the keypad is mounted or dismounted several times, new retaining clamps must be used
each time. This prevents the retaining clamps from settling. To change the retaining clamps,
press the clamp flat on the underside, then you can push out and dismount the retaining clamp.
The marking of the retaining clamp for the respective front panel thickness is imprinted as
number 1 to 4 on the clamp, which is also visible when mounted. The number 1 on the retaining
clamp means that it is suitable for a front panel thickness of 1mm. A mixed use of different
types of retaining clamps in a keypad is not permitted.
The keypad shall be pressed evenly into the panel with the mounted retaining clamps, while
tilting should be avoided. Press evenly on the housing and not on the buttons.
Note
Damage to the buttons
The plug-in connection must be established with a suitable connector. The plug-in connection
can alternatively be established before or after mounting the keypad into the panel.
The keypad is automatically centred to the panel by the 6 retaining clamps, i.e. the exact
positioning of the keypad depends on the accuracy of the installation opening.

www.eao.com 18
Installation in a panel with self-locking nuts (screw-in
version)
See drawing “1707 product information”.
If the keypad is mounted or dismounted several times, new self-locking nuts must be used
each time.
Caution!
Exceeding the maximum permissible torque inevitably leads to the
destruction of the keypad. The keypad is no longer tight nor leak proof in
this case.
Incorrect mounting of the keypad, e.g. incorrect number of rubber washers
or without washers (see 7.2.1 Mounting sequence), may result in damages
to the keypad.
Risk of injury
Damage to the keypad
Electric shock
The
specified overload force refers to the switches, not to the mounting
situation. For Rotary Cursor Controller it is recommended to use the screw-
in variant.
Risk of Unfastening
7.2.1 Mounting sequence
First of all, the rubber washers should be mounted according to the front panel thickness. No
rubber washers are necessary for a front panel thickness of 1 mm. Mount 1 rubber washer per
screw bolt for a front panel thickness of 2 mm, mount 2 rubber washers per screw bolt for a
front panel thickness of 3 mm and mount 3 rubber washers per screw bolt for a front panel
thickness of 4 mm. Since these have a slightly smaller inner diameter, they clamp lightly on
the thread of the bolt to make it more difficult for the washers to fall off. Afterwards, the keypad
has to be installed in the front panel, while the cable incl. connector has to be pushed through
the sleeve. The sleeve can be installed rotated by 180° in each case. Afterwards, the 4 washers
have to be installed over the screw bolts and fixed with the nuts. The correct tightening torque
is defined in the 1707 product information and must be observed. The last step is to connect
the plug connector.
The keypad of the screw-in version must be aligned manually to the panel. There is no
automatic centering, the keypad can be slightly pushed into the mounting panel (depending on
the opening size of the panel).

www.eao.com 19
Caution!
For both versions, make sure that the opening for pressure and humidity
compensation on the underside of the keypad is not closed or covered while
installed.
Damage to the keypad
The cables must not be bent during installation and the transition to the
potting area must not be damaged. The minimum bending radius of R 6 mm
for static bending and R 16 mm for dynamic bending (bending 10 times
max.) must not be undercut. The plug connector needs to be fixed (e.g. by
a DT Deutsch assembly clip) on application side to prevent the connector
plug from free movement!
Damage to the keypad
Installation of the symbol inserts
The symbol inserts can be changed in a panel both in the installed and in the non-installed
state of the keypad.
Each symbol insert can be installed rotated in a 90° grid. When mounting the symbol inserts,
make sure that the position of the symbols has the desired orientation towards the keypad.
The symbol inserts have a mechanical coding to the housing of the keypad. A slight twisting
of the symbol inserts to the keypad is technically possible and does not constitute a defect.
The symbol inserts must be mounted / dismounted under the edge of the housing around the
insert using a tool without sharp edges (similar to mounting a vehicle tyre on a rim). The insert
tool (article number: 09-0A00.0001), which is available as an accessory, is best suited for this.
There should be no visible gap between the housing of the keypad and the symbol insert after
installation, because dirt may penetrate here during operation and negatively influence the
lighting function of the keypad.

www.eao.com 20
Caution!
When mounting and dismounting the symbol inserts, make sure that the
housing is not damaged. The silicone of the housing must not be pierced,
otherwise the protection degree of the keypad is not fulfilled. Similarly, the
coating of the housing must not be damaged, otherwise the chemical
resistance of the keypad is no longer guaranteed.
Damage to the keypad
Loss of tightness of the keypad
It must be always ensured that the symbol inserts are mounted in the correct
position.
Risk of injury
Note
When changing the symbol inserts, make sure that there are no liquids or
impurities between the housing and the symbol insert. These would
negatively affect the illumination of the symbols.
When using the version for snap-in mounting in a mounting panel, you need
retaining clamps.
When using the version for screw-in mounting in a mounting panel, you
need the sleeve, nuts, washers and spacers to bridge the distance between
keypad and sleeve in the thickness of the mounting panel.
Do not forget the spacers during mounting. Only hand-tighten the self-
locking nuts.
Damage to the keypad and/ or sleeve
Note
Only use original mounting material and optional accessories.
Damage to the keypad
Use inside closed vehicles
Due to the product is designed for outdoor applications and not for use in closed vehicle
interior, odor testing according odor testing specifications like VDA270 is in customer’s
responsibility. The test should be performed to customer application needs.
Other manuals for 09 Series
2
Table of contents
Other eao Keypad manuals
Popular Keypad manuals by other brands

Honeywell
Honeywell 6150 - Ademco Fixed - Display Keypad Installation and setup guide
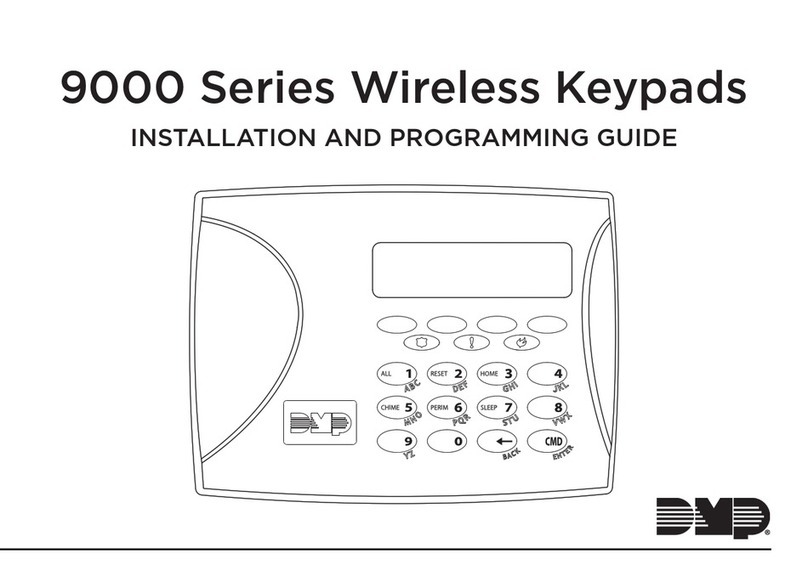
DMP Electronics
DMP Electronics 9000 Series Installation and programming guide
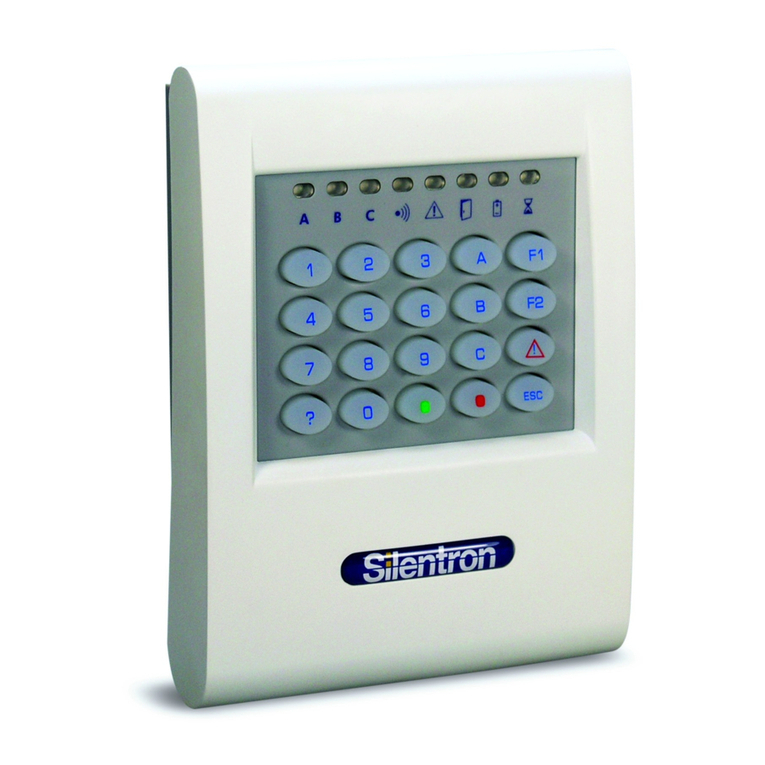
SILENTRON
SILENTRON 5528 HT manual
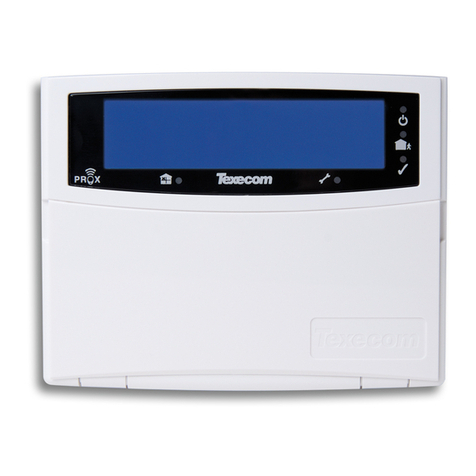
Texecom
Texecom Premier LCDLP installation manual
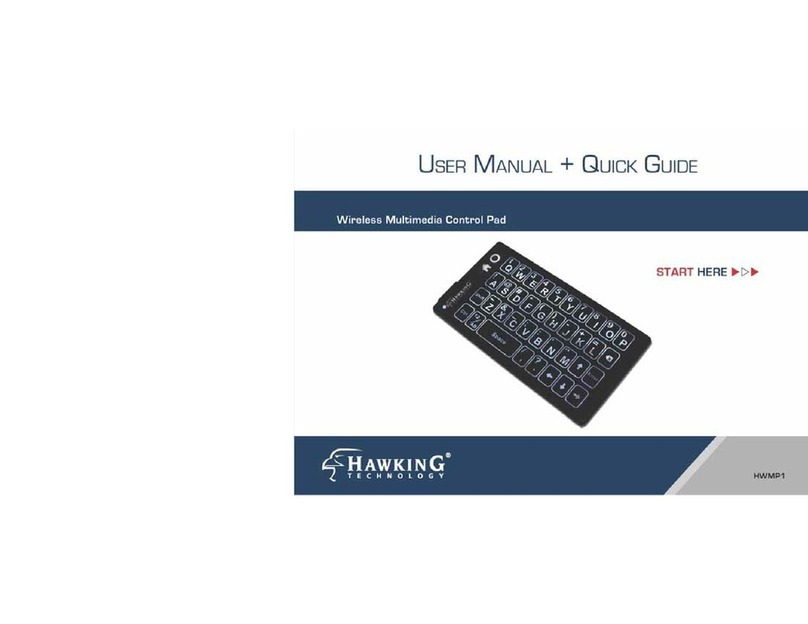
Hawking
Hawking HWPM1 User manual and quick start guide
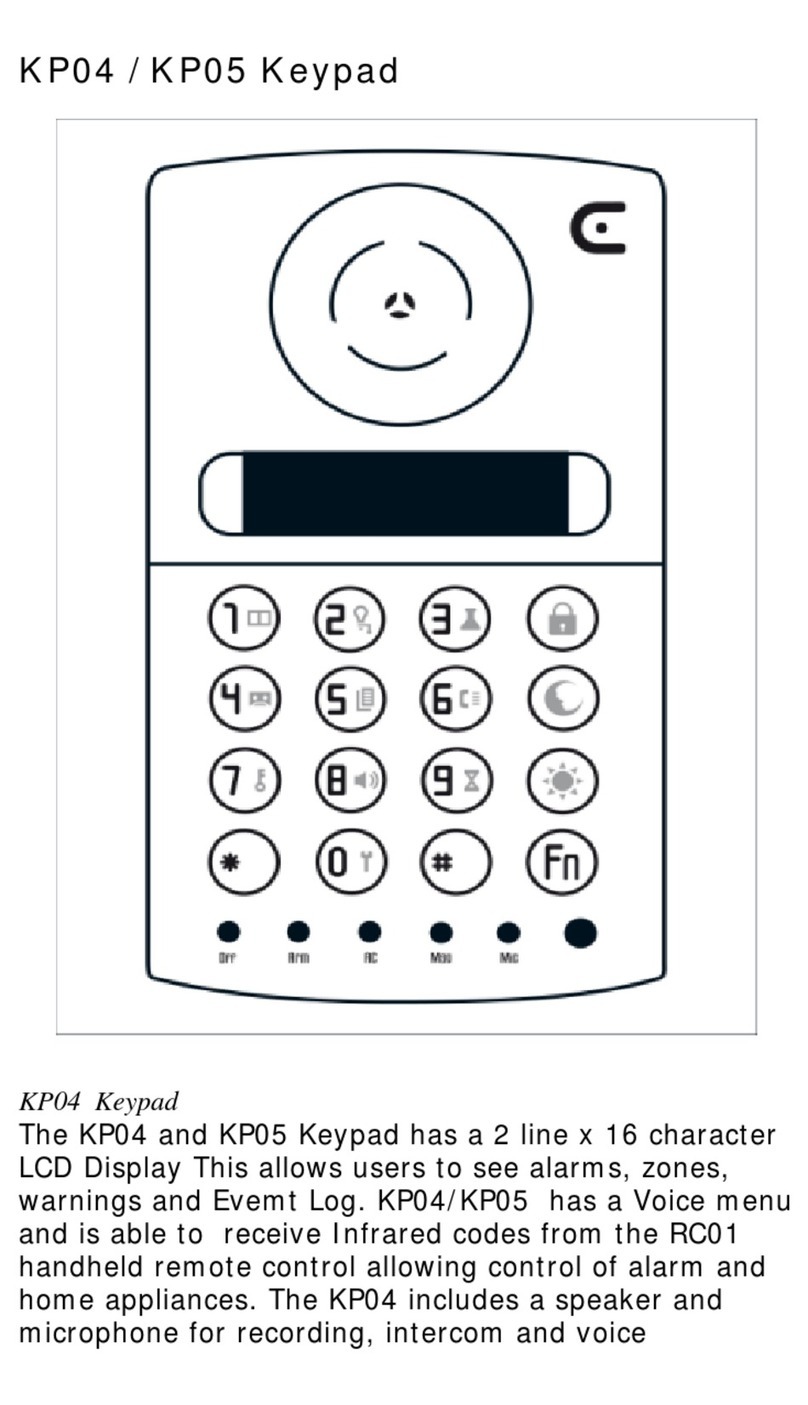
Cytech
Cytech KP04 quick start guide