Edgetech HP125 Series User manual

HP125 SERIES
2
QUICK STARTUP GUIDE
Safety
Electrical and compressed Gas Hazards
The HP125 delivered to you has been tested for safety, calibrated and approved as
shipped from the factory. Note the following precautions:
CAUTION
Do not modify the unit. Improper modification can damage the product
or lead to malfunction.
CAUTION
The transmitter body does not have user serviceable parts inside, and is
not designed to be opened. Opening the transmitter will void the
warranty.
ESD Protection
Electrostatic Discharge (ESD) can cause immediate or latent damage to
electronic circuits. Edgetech Instruments products are adequately protected
against ESD for their intended use. It is possible to damage the product, however,
by delivering electrostatic discharges when touching, removing, or inserting any
objects inside the equipment housing.
1. To make sure you are not delivering high static voltages yourself when handling the
replaceable sensor tip PCB
2. Handle ESD sensitive components on a properly grounded and protected ESD workbench.
3. When an ESD workbench is not available, ground yourself to the equipment chassis with a
wrist strap and a resistive connection cord.
4If you are unable to take either of the above precautions, touch a conductive part of the
equipment chassis with your other hand before touching ESD sensitive components.
Always hold component boards by the edges and avoid touching the component contacts.
When the Probe is first introduced into the process it will need a period of time for the materials to dry
down before the sensor reads Dew Point and RH correctly.
During installation process the probe will have been exposed to ambient conditions. The stainless steel
filter and the tip PCB will have absorbed some moisture.
Once installed in the process any entrained moisture will be drawn off by the process gas and the unit
will quickly reach equilibrium.
The initial RH and Dew Point values displayed when first installed may be misleading

HP125 SERIES
3
WHEN USING PROBE with CABLE.
Before mounting the probe into any system ensure the system is safe to work on.
Depressurized and verify that all power to connections are isolated in the Off position.
Installation should be carried out by trained technicians and following local safety protocols
1. Select Probe insertion position, insure safe clearance around the probe to avoid damage
2. Check all pipe fittings and pipe boss dry assembly for fit up
(Probe is standard with ½” NPT fitting option ¾”NPT )
3. Insert pipe fittings using suitable sealing tape or sealing compound
Mount the Probe in position to measure the desired gas.
4. Ensure the Probe is inserted to an adequate depth to obtain a good flow of the sample gas
around the tip sensor. Insertion depth; Max 6”(15cm) Min 2.4” (6cm) compression fitting
must avoid the connection to the tip cover
5. Tighten the swage fitting till it grips the probe in place but at this stage do not apply force.
6. Re check the probe position and measurement depth are correct, fully tighten all pipe
fittings.
7. To correctly tighten a Swagelok fitting,
8. Ensure there is adequate cable length from the probe cable to make connection to customer
system (3ft or 6ft length are supplied) cable can be cut to fit.
9. Check Probe Pin connector correctly mates with cable connector
Connect Probe wiring as shown below:
ITEM
CABLE colour
24VdcPower Supply –Pos.
RED
24VdcPower Supply –Neg.
BLACK
0-10V Temperature.
YELLOW
0-10V RH
WHITE
0-10V Dew Point
BLUE
0-10V psig or mbar
ORANGE
RS232 Serial Input –TX
GREEN
RS232 -Com
BROWN
DC power supply. Specifications are: 24VDC ± 10%, 1A maximum.
Notes:
Connect only the Outputs desired. See drawing in the HT125 Manual for further
connection details.
Do not apply DC Power until all wiring is completed and checked.

HP125 SERIES
4
QUICK STARTUP GUIDE
WHEN USING PROBE with INTERFACE CONTROL & DISPLAY MODULE
1. Mount the Probe as detailed in page 1 section 1 through 6.
2. Connect cable from Probe to Electronics Unit
(if applicable). Unit is prewired to the DCM if ordered as an option from factory
3. Customers connections can be made as detailed in table below
Other values can be defined with order or
Alarm relays can be programed on site via RS232
TERMINAL TB1
ITEM
1,2
ALARM Relay 2
3,4
ALARM Relay 1
5
CHASSIS GROUND
6
ANALOG OUTPUT 2
7
ANALOG OUTPUT 1
8
ANALOG OUTPUT RET.
9
FOR FACTORY USE
10
FOR FACTORY USE
11
RS232 RETURN
12
DC POWER IN (+)
13
DC POWER IN (-)
14
RS232 TX
15
RS232 RX
DC power supply. Specifications are: 24VDC ± 10%, 1A maximum.
See Attached TB1 Pin Connector Guide. Note Pin Nine is used as terminal location
guide
Connect only the Outputs desired. See the HT125 Manual for details.
Double check that the 24V power supply is correctly connected terminals 12 & 13
Do not apply DC Power until all wiring is completed.

HP125 SERIES
5
TABLE OF CONTENTS Page
1.0 Quick Startup 2
List of Illustrations 5
List of Tables 5
2.0 Edgetech Commitment to Quality 7
3.0 Introduction 8
3.1 General Description 8
3.2 Specifications Summary 9
3.3 Model Descriptions 9
3.4 Available Options 10
4.0 Installation 12
4.1 Mounting the Probe 12
4.2 Probe Electrical Wiring 14
4.3 Probe with CAM option 15
4.4 Mounting DCM case 16
4.4.1 Wiring Probe to DCM 16
4.4.2 Wiring Inputs / Outputs 17
4.5 Selection of Analog output ranges 18
5.0 Basic Block Diagram 19
5.1 Probe Assembly 19
5.2 Electronics Module 20
5.3 Complete System 20
6.0 Operation 21
6.1 Initial Bench Testing 21
6.2 Normal Operation 21
6.3 Factory Default Conditions 21
6.4 RS-232 Serial Port 22
6.5 Serial Port Setup 22
6.6 Set up with PC & USB only 23
6.7 Changing DCM program 24
6.7.1 Programming the Alarm Relays 25
6.7.2 Calibrating the Analog Outputs 26
7.0 Maintenance 27
7.1 Sensor Circuit Board 27
7.1.1 Removing the Sensor Board 27
7.1.2 Sensor Reassembly 28

HP125 SERIES
6
8.0 Specifications 29
9.0 Appendix 31
9.1 Warranty Information 32
9.2 Mounting Dimensions 33
9.2.1 Wall Mount 33
9.2.2 Duct Mount 34
LIST OF ILLUSTRATIONS Page
3-1 Some HP125 Configurations 9
3-3 Unit alarm versions 10
4-1 HP125 with Swagelok fitting 13
4-3 CAM installation details 15
4-4 Electronics Unit Wiring 16
4-5 DCM terminal strip connections 17
4-6 DCM Analog DIP switches 18
5-1 Probe Block Diagram 19
5-2 System Block Diagram 21
7-1 Sensor Exploded View 28
LIST OF TABLES Page
3-1 Standard Configurations 10
3-2 Measurement Ranges 12
4-1 Probe Wiring 14
4-2 HP125 Wiring Colors 14
4-3 DCM Serial Port Wiring 16
4-4 DCM Analog Output Wiring 18
4-5 DCM Analog output Dip Switch 18
6-1 Serial cable wiring 23

HP125 SERIES
7
2.0 EDGETECH’S INSTRUMENTS COMMITMENT TO
QUALITY
Thank you for purchasing one of our products. At Edgetech Instruments, it is
our policy to provide cost-effective products and support services that meet or
exceed your requirements, to deliver them on time, and to continuously look
for ways to improve both.
We all take great pride in the products which we manufacture 100% in the
USA.
We want you to be entirely satisfied with your instrument. The information
contained in this manual will get you started. It tells you what you need to get
your equipment up and running, and introduces its many features.
We always enjoy hearing from the people who use our products. Your
experience with our products is an invaluable source of information that we
can use to continuously improve what we manufacture. We encourage you to
contact or visit us to discuss any issues whatsoever that relate to our products
or your application.
The Employees of Edgetech Instruments Inc.

HP125 SERIES
8
3.0 INTRODUCTION
3.1 GENERAL DESCRIPTION
The Edgetech Instruments HP125 Series is a family of multi-function probes that offers a variety of
measurement parameters with high accuracy. A single sensor can provide up to 4 measurement
parameters. Dew point, Relative Humidity (%RH), Temperature and Pressure (psia or mbar). Electrical
analog and digital outputs are provided
The HP 125 probes are designed for ease of installation and operation. Field-replaceable sensor
modules have standardized outputs for interchangeability. Replacement tip sensors come with
calibration certification and automatically integrate with the main sensor. The power requirement is a
common unregulated DC power supply. User-available electrical outputs include linear analog voltage
(or optional current).
Mounting options include Wall Mount, Remote Mount, and Duct Mount configurations. A remote or
local Display Unit (Type DIS) is available, with a two-line LCD display, two alarm relays, and two
analog outputs.
The analog outputs can be configured by dip switch for either 4-20mA, 0- 10V and 0-5V operation.
Figure 3-1 Some of the Available HP125 Configurations
a. Stand-alone Probe
b. Remote Mount with Display Option
c. Wall Mount

HP125 SERIES
9
3.2 SPECIFICATIONS SUMMARY
(See Specifications, Chapter 8, for additional information)
3.2.1 STAND-ALONE PROBE
Analog Outputs: Up to four 0 –10 Vdc
Digital Output: RS-232 serial output. Reporting function every 10s, space delimited
Power Supply: 24 Vdc +10%, unregulated, 1A max.
Accuracy
Relative Humidity +1.8% @ 23°C (0 TO 90% RH)
Temperature +0.5°C
Pressure +1 mbar @ 25°C (600 to 1200 mbar) / ±5mbar (-40°C to +125°C)
Dew Point + 1°C for –10°C to 95°C DP and + 2°C for –40°C to –10°C
Mounting: Cable Length 3 feet (1M) std or 6ft (2M) option
Fitting: 1/2 inch NPT stainless steel
Dimensions: Length: 9.5 inches
Diameter:1/2 inch
Materials: Housing: 316 Stainless Steel
Filter: Sintered SS 100µm (removable)
3.2.2 PROBE WITH ELECTRONICS UNIT
Analog Outputs: Dip switch selectable 4 –20mA, 0 –10V and 0 –5V. x2
Digital Output: RS-232C, bi-directional
Alarm Relays: Form A (SPST, NO) x2
Power Supply: 24Vdc +10% unregulated, 1A max.
RH Accuracy: +1.8% @ 23°C (0 TO 90% RH
Temp. Accuracy: +0.5°C
Electronics Housing Protection:
IP66 (NEMA 4X) Dust tight and moisture resistant

HP125 SERIES
10
Table 3-1 HP125 Series, Standard Available Configurations
MODEL NO.
SENSOR ONLY
SENSOR PLUS
ELECTRONICS MODULE –
WITH DISPLAY
HP125
X
X
HPP125
X
X
HPB125
X
X
3.3 HP125 MODEL DESCRIPTIONS
HP125 –RH / Temperature / Calculated Dew Point.
HPP125- Pressure / RH / Temperature / Calculated Dew Point.
HPB125 - Barometric Pressure / RH / Temperature / Calculated Dew Point
3.4 AVAILABLE OPTIONS
Probe
-2M- Optional Sensor connection cable length 6ft (2M).
-3/4NPT–An optional pipe fitting to adapt the ½ in probe to fit replace old HT probe series.
Display and electronic control module
-DIS- Remote electronics module with two-line LCD digital display, two configurable analog outputs,
Bi directional RS-232C, and two programmable alarm relays.
-VAC- Universal Power supply input 110/220V 50/60Hz output 24Vdc.
-F- Two FORM C fail safe relays. Power Off = Alarm Mode (enclosure length increases by 2”).
-85- Integrated dual 85dbA audible and simulated visible strobe LED Alarm with disable switch.
-100- Individual 100dbA audible alarm with mute switch and separate simulated visible strobe LED.
Dew Point -10C
Pressure: 120 PSIG
Mute Switch
100dB Audible Alarm
Dew Point -10C
Pressure: 120 PSIG
Flashing Light and 85 dB
audible Alarm
Alarm Disable
Flashing Light
-85 -100
HP125-DCM
Display Control Module HP125-DCM
Display Control Module

HP125 SERIES
11
Sampling Options
-SM- Surface Wall mount, the sensor is mounted between two polypropylene blocks with integral
surface wall
mount.
-UN-Same as wall mount only the sensor holding blocks can be fitted into a Uni-strut fitting
-FSS- 300psi Stainless Steel pipe flange mount with gasket, with integral threaded sensor boss.
-FPVC- 150psi PVC pipe flange mount with gasket, with integral threaded sensor boss
-CAM- Compressed air sample module allows a measured sample of gas to pass across the probe and
bleed to atmosphere. Includes Isolation valve for service access and metered sample flow.
SURFACE WALL
MOUNT
RH 49.0%
T 23.7C DP 12.4C
HP125-DCM
Display Control Module
RH 49.0%
T 23.7C DP 12.4C
HP125-DCM
Display Control Module
FLANGE MOUNT
FOR DUCTS,
ISOLATION CHAMBER,
PROCESS WALL PENETRATION
RH 49.0%
T 23.7C DP 12.4C
HP125-DCM
Display Control Module
Open
Valve
Sample Flow past
Probe Sensors
CAM MOUNT
Includes Isolation Valve
and Fixed Orifice
UNI-STRUT MOUNT
For Wall Mount,
Skid Mount,
OEM Mount
(does not include strut)
-HP125 Tip –Field-replaceable sensor module for RH/Temperature/Dew Point. Interchangeability
accurate to published specification.
-HPP125 Tip –Field-replaceable sensor module for RH/Temperature/Pressure. Interchangeability
accurate to published specification.
-HPB125 Tip –Field-replaceable sensor module for RH/Temperature/Barometric Pressure.
Interchangeability accurate to published specification.

HP125 SERIES
12
Table 3-2 HP125 Series Sensor Measurement Ranges
MODEL NO.
OUTPUT 1
OUTPUT 2
OUTPUT 3
OUTPUT 4
HP125
DEW POINT
AIR TEMP.
PERCENT RH
DEFAULT RANGE
-40 to +95ºC
-40 to +125ºC
0 TO 99.9%
MAX. LIMITS
-60 to +95ºC
-40 to +125ºC
0 TO 99.9%
HPP125
DEW POINT
AIR TEMP.
PERCENT RH
PRESSURE
DEFAULT RANGE
-40 to +95ºC
-40 to +125ºC
0 TO 99.9%
0 to 400psia
MAX. LIMITS
-60 to +95ºC
-40 to +125ºC
0 TO 99.9%
0 to 400psia
HPB125
DEW POINT
AIR TEMP.
PERCENT RH
BAR. PRESSURE
DEFAULT RANGE
-40C TO +95°C
-20 to +125ºC
0 to 99.9%
600 to 1200 mbar
MAX. LIMITS
-60C TO +95°C
-20 to + 125ºC
0 to 99.9%
600 to 1200 mbar
4.0 INSTALLATION
4.1 MOUNTING THE PROBE
The HP125 Probe includes a stainless steel Swagelok mounting sleeve commonly used in pipe
connections. It is supplied with a tapered male 1/2-inch NPT pipe thread or optional ¾-inch NPT male
fitting. The Swagelok fitting should be removed from the probe and carefully split into its two
component parts. The male NPT part should be mounted in a gas-tight manner to the pipe or to a flat
surface of a duct or chamber wall containing the gas to be measured.
To install the mount and Probe:
1. Separate the two parts of the Swagelok mounting sleeve.
2. Screw the front portion of the mounting sleeve (the tapered NPT fitting) into a pre-mounted
threaded mating fitting. Teflon™ tape may be used for a good seal. Do not over-tighten. The
¾-NPT adaptor will allow the new HP125 range to be fitted in place of the previous HT/HB
sensors from Edgetech.
3. The ½-inch female part of the pipe mount along with the SS flare feral is mounted on the probe body.
Ensure that the flare feral is installed with the flat side on the top and the tapered side facing down
towards the sensor end of the probe
4. Insert the Probe into the rear portion, and screw this part of the mount into the
previously mounted front portion, so that the Probe is gripped snugly. Do not over-tighten at this stage.
As much of the Probe as possible should protrude inside the area to be measured, to avoid possible
laminar flow errors. Designed to allow the user to set the depth of penetration from 2.4” (6cm) to 6”
inch (15cm) depending on application needs.

HP125 SERIES
13
5. Once the probe is correctly positioned install the connection cable to check length and ease of access to
the cable connections at both ends. Remove the connection cable to avoid twisting. Now firstly tighten
the pipe bases section and then with the probe in the selected insertion depth tighten the Swagelok
fitting. Caution do not over tighten.
6. How to install Swagelok fittings. Insert the HP125 probe to your selected insertion depth, tighten by
hand until the nut is finger tight. Further tighten the nut until the probe will not turn by hand and cannot
be moved axially in the fitting.
Mark the nut at the at the 6-0-clock position
While holding the fitting body steady, tighten the nut one and one quarter turns till the nut is in
the 9-0-clock position.
Swagelok fittings may be disassembled and reassembled many times.
Always depressurize the system before disassembling a Swagelok tube fitting
Prior to disassembly mark the nut positions this will ensure you return the fitting to the same
positions. At this point tighten the nut up slightly.
Fig 4.1 Shows HP125 with ¾” NPT to ½” Swagelok fitting
NPT section of fitting
Swagelok ½” female
fitting

HP125 SERIES
14
4.2 Wiring probe only See Wiring Table 4-1and Figure 4-2 below.
ITEM
CABLE colour
24VdcPower Supply –Pos.
RED
24VdcPower Supply –Neg.
BLACK
0-10V Temperature.
YELLOW
0-10V RH
WHITE
0-10V Dew Point
BLUE
0-10V psig or mbar
ORANGE
RS232 Serial Input –TX
GREEN
RS232 -Com
BROWN
DC power supply. Specifications are: 24VDC ± 10%, 1A maximum.
Table 4-1 HP125 Probe Wiring Table
1. Connect Power Supply wiring as shown. The Positive voltage output of the supply is
connected to the RED wire. The Negative output of the supply is connected to the
BLACK wire.
2. Connect the Analog Output wiring as shown. Up to four 0 to 10 Vdc outputs are
available. Connect Outputs 1, 2, 3 and 4 as required, observing the color codes.
3. Connect the RS-232 Serial Output if desired. Only 2 wires are required if the output is
needed for transmitting information only
Table 4-2 HP125 Probe Wiring Table

HP125 SERIES
15
4.3 Installation HP125 Probe with CAM option
CAM
Dew Point -10C
Pressure: 120 PSIG
Bleeder
Port
Connection
to Compressed Air Header ¾” NPT
BLEED
PROBE
CAM
Ball
Valve
Closed Ball
Valve
Open
TEE
Reducer Bushing
BLEEDER
VALVE
BALL
VALVE
1. Close ball valve on the CAM. Close the Bleeder valve (clockwise).
2. Install the HP125 Probe onto the CAM top port. The CAM is supplied with a Reducer Bushing
to accommodate the installation of the Probe when equipped with a ½ inch NPT male threaded
compression fitting. If the HP125 is equipped with a ¾ inch NPT fitting, then remove the
reducing bushing and thread the probe directly into the TEE fitting. Be certain to apply thread
tape to male threads of the probe compression fitting before installation to ensure a seal.
3. The probe slides through the compression fitting. Adjust height of the probe with the CAM
TEE so that the probe sensing tip is approximately in the center of the TEE (gas will flow past
the tip and then out of the bleeder valve).
4. Ensure the Compressed Gas Source pressure is OFF (de-pressurized). Connect the CAM at the
bottom port of the ball valve. Ensure all fittings are tightened. CAUTION the CAM is
designed to operate with compressed gas. Always take the proper safety precautions when
working with pressurized gases!
5. Re-pressurize Compressed Air System. Slowly open the Ball Valve to pressurize the CAM and
probe. Check for leaks.
6. Slowly adjust the CAM bleeder valve to allow a small flow of gas out. This flow should be
very small- just noticeable. You can check flow with a flowmeter. Ideal flow is approximately
1-3 LPM.

HP125 SERIES
16
4.4 MOUNTING THE DCM MODULE
Instruments with the plastic wall mount housing are mounted to a flat surface as follows:
For dimensional details of case see Appendix 9.2 page 34
1. Remove the front cover. Using a flat screwdriver, carefully unscrew the four slotted plastic
screws.
2. Mounting screws (not provided) are inserted in the same holes as the cover screws. They
must have a head diameter that is small enough to fit inside the clearance holes, but large
enough to press against the collar located at the bottom of the holes. No. 8 pan head or
round head screws are recommended.
3. Reinstall the front cover. Do not over-tighten the cover mounting
screws.
MOUNTING CONSIDERATIONS
1. If the Digital Display has been provided, is it easily visible?
2. Is the location convenient for routing electrical wiring?
3. Is the module within 6 feet (1.8 meters) of the Sensor location
4.4.1 PROBE WITH DCM Option ELECTRONICS MODULE
See Tables 4-2, 4-3, and Figure 4-1, 4.2 below.
If the HP125 is ordered with the display DCM option then it will come with the HP125 sensor and
power cable already completely prewire.
If installing the Display module when ordered as separate option
Carefully tap out the desired knockouts, and mount the cable glands.
We recommend that you route the Probe Cable through a bushing on the left. Route all
other wiring through the bushing on the right.
Run the cable from the Probe to the display unit. Only the probe RS232 and power cables are used
to connect the probe to the display module. As Table 4.2. A right angle jack plug is used for the
RS232 connection to PCB see Fig 4.2
Table 4.3 Fig 4.2
ITEM
CABLE colour
24VdcPower Supply –Pos.
RED
24VdcPower Supply –Neg.
BLACK
RS232 Serial Input –TX
GREEN
RS232 –Com
BROWN

HP125 SERIES
17
4.4.2 INPUT/OUTPUT WIRING
Wire the Analog Outputs as required. See 4.4 below for information on output selection.
Connect the RS-232 Serial Output if desired. Only 2 wires are required if the output is needed
for transmitting information only. A third wire is added for bi-directional communications with
the serial port
1. Wire the External customer connections as shown in Table 4-3.
2. Wire the two 4 to 20 mA Analog Outputs and Alarm Relays as shown in Table 4-2 if desired.
3. Connect to the RS-232C Serial Port at J6 if desired.
Figure 4-5 DCMTerminal Strip Wiring
DC PWR IN (+)
RS232 RTN
ANALOG OUT RTN
ANALOG OUT 1
ANALOG OUT 2
RS232 RX
RS232 TX
DC PWR IN (-)
ALARM 1
ALARM 2
CHASSIS GND

HP125 SERIES
18
TERMINAL
ITEM
1,2
ALARM 2
3,4
ALARM 1
5
CHASSIS GROUND
6
ANALOG OUTPUT 2
7
ANALOG OUTPUT 1
8
ANALOG OUTPUT RET.
9
FOR FACTORY USE
10
FOR FACTORY USE
11
RS232 RETURN
12
DC POWER IN (+)
13
DC POWER IN (-)
14
RS232 TX
15
RS232 RX
Table 4.4
Connect the Alarm relays as needed. Used as upper or lower setpoint Alarm Relays.
See Section 5.4.4 for further information.
4.5 SELECTION OF ANALOG OUTPUTS
Two small electrical switches allow the selection of analog output scaling. These switches are located
in the top left corner of the circuit board as shown in Figure 4-2 below. You can select the outputs to
be either 4 to 20 mA, o to 5VDC, or 0 to 10VDC. To modify the output scaling, proceed as follows:
1. Be sure that DC Power is not applied to the unit.
2. Remove the outer cover.
3. Using a small screwdriver, set the switches as shown in Table 4-2.
4. Replace the cover.
5. Reapply DC power.
OUTPUTS
SWITCH 1
SWITCH 2
4 to 20 mA
DOWN
----
0 to 5VDC
UP
UP
0 to 10VDC
UP
DOWN
Table 4-5. Analog Output Switch Settings
Figure 4-2 Output Selector Switches
SWITCH 1
SWITCH 2

HP125 SERIES
19
BASIC BLOCK DIAGRAM THEORY OF OPERATION
5.1 PROBE ASSEMBLY
See Figure 5-1, the Probe Assy. Basic Block Diagram.
The Probe Assembly is a stand-alone, completely self-contained measuring system. All
units include the RH and Temperature Sensors, and some optional probes include a
Pressure Sensor as well. The field-replaceable tip Sensor Circuit Board has standardized
output levels for all four measured parameters. Therefore, boards may be quickly
replaced while in operation without the need for recalibration, maintaining full system
accuracy. The Microprocessor performs the system control, parameter calculation, and
serial digital communications. Digital-to-Analog (D-A) conversion provides four 0 to
10 Vdc linear Analog Outputs corresponding to the measured and/or calculated
parameters.
The serial digital RS-232 interface is allowing to user to only receive and record
measured information,
Figure 5-1 Basic Block Diagram, Probe Assy
RH
SENSOR
TEMP.
SENSOR
PRESSURE
SENSOR
NORMALIZATION - CALIBRATION
STAGE
MICROPROCESSOR
D-A
D-A
SENSOR BOARD PLUG-IN ASSY.
SENSOR BOARD PLUG-IN CONNECTOR
0 - 10 VDC
RH OUT
0 - 10 VDC
TEMP. OUT
D-A
0 - 10 VDC
PRESSURE OUT
RS-232
(TX)
RS-232
(RX)
SERIAL PORT
DP/FP OUT

HP125 SERIES
20
5.2 HP125 ELECTRONICS MODULE (Type DCM)
Although the Probe may be used as a stand-alone measuring device, it also may be connected to the
type DCM remote display unit, for additional capability. The complete HP125 system consists of the
Probe, the interconnecting 3 foot (1meter) cable, and the electronics module. Outputs of the unit
include a Serial Port, two Alarm Relays and two configurable analog outputs. A two-line LCD Digital
Display is also included that can display all the operating parameters.
5.3 THE COMPLETE HP125 SYSTEM
Figure 5-2 is a basic block diagram of the complete Humidity, Temperature, DewPoint and optional
Pressure measuring system. The remote Probe is connected, via the attached cable, to the electronics
module. The system is completely controlled by the microprocessor in this module. Upto four sets of
analog voltage outputs from the Probe are routed through the Analog Scaling and Selection stage. The
scaling of these output signals may be programmed by the user to any desired range by using the RS-
232 Serial Port. The bi-directional RS-232 is brought out to a connector in the electronics module. The
user can also program the two Alarm Relay set points via this digital interface. The built-in LCD
Digital Display, which provides information on all measured parameters, is also controlled by the
microprocessor. In addition, the microprocessor is used to calculate other parameters than those
directly measured by the sensors in the Probe. These may be shown on the Digital Display, and they
are also available on both the analog and digital (RS-232) outputs. The Alarm Relays may also be set
for these calculated values. Figure 5-2 System Basic Block Diagram
RH
SENSOR
TEMP.
SENSOR
PRESSURE
SENSOR
(OPTION)
SERIAL
PORT
(TX) (RX)
ANALOG
OUTPUTS
(0 - 10V X3)
3 FT. SENSOR CABLE
HP 125 PROBE ASSY.
MICROPROCESSOR
ANALOG
SCALING
AND
SELECTION
DIGITAL
DISPLAY
ALARM
RELAY
#1
ALARM
RELAY
#2
ELECTRICAL CONNECTORS
ALARM
1
ALARM
2
RS-232
(TX) (RX)
1 2
USER INTERFACE
ANALOG OUTPUTS
This manual suits for next models
1
Table of contents
Other Edgetech Measuring Instrument manuals
Popular Measuring Instrument manuals by other brands
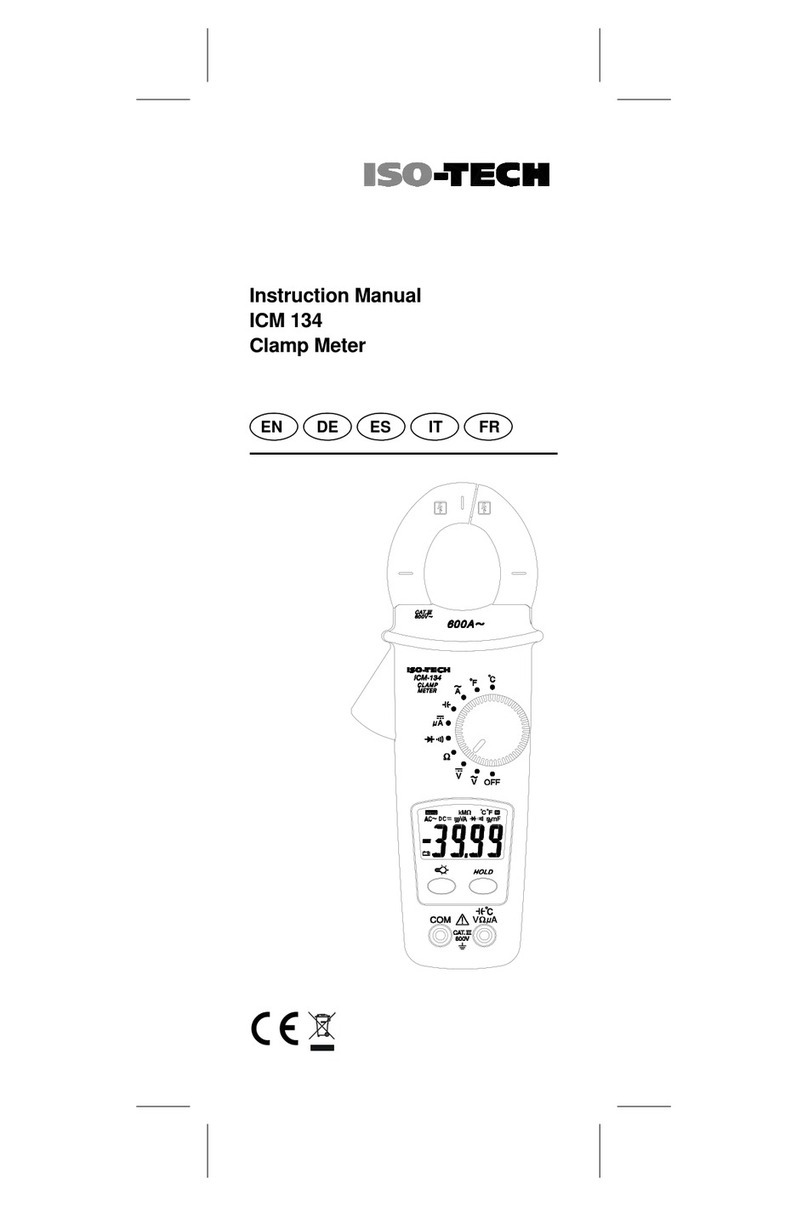
Isotech
Isotech ICM 134 instruction manual
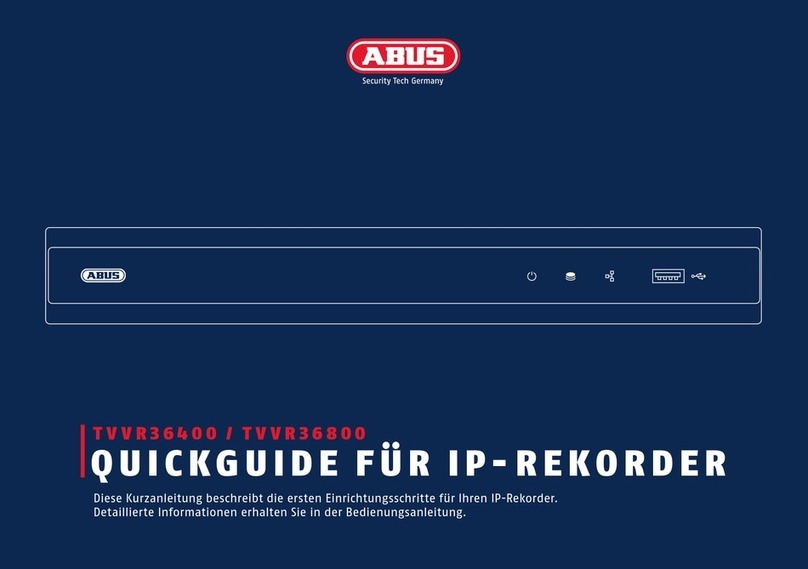
Abus
Abus TVVR36400 quick start guide

SureShot
SureShot PINLOC 6000iPSM user manual

Kyoritsu Electrical Instruments Works, Ltd.
Kyoritsu Electrical Instruments Works, Ltd. KEW 8343 instruction manual

red lion
red lion PAXLR manual
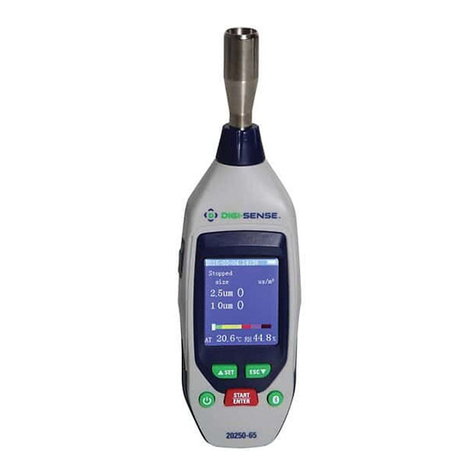
Digi-Sense
Digi-Sense 20250-65 user manual