EG&G ORTEC 476 User manual

n
f
7
■
\
.
fi
iKiBu.
i.:^^
Modei
47o
Mult'pl^^xer/Routar
instruction
Manual

Model
476
Multiplexer/Router
Instruction
Manual
Printed
in
U.S.A.
3080
02C
0379

STANDARD
WARRANTY
FOR
EG&G
ORTEC
INSTRUMENTS
EG&G
ORTEC
warrants
that
the
items
will
be
delivered
free
from
defects
in
material
or
workmanship.
EG&G
ORTEC
makes
no
other
warranties,
express
or
implied,
and
specifically
NO
WARRANTY
OF
MERCHANTABILITY
OR
FITNESS
FOR
A
PARTICULAR
PURPOSE.
EG&G
ORTEC's
exclusive
liability
is
limited
to
repairing
or
replacing
at
EG&G
ORTEC's
option,
items
found
by
EG&G
ORTEC
to
be
defective
in
workmanship
or
materials
within
one
year
from
the
date
of
delivery.
EG&G
ORTEC's
liability
on
any
claim
of
any
kind,
including
negligence,
loss
or
damages
arising
out
of,
connected
with,
or
from
the
performance
or
breach
thereof,
or
from
the
manufacture,
sale,
delivery,
resale,
repair,
or
use
of
any
item
or
services
covered
by
this
agree
ment
or
purchase
order,
shall
in
no
case
exceed
the
price
allocable
to
the
item
or
service
furnished
or
any
part
thereof
that
gives
rise
to
the
claim.
In
the
event
EG&G
ORTEC
fails
to
manufacture
or
deliver
items
called
for
in
this
agreement
or
purchase
order,
EG&G
ORTEC's
exclusive
liability
and
buyer's
exclusive
remedy
shall
be
release
of
the
buyer
from
the
obligation
to
pay
the
purchase
price.
In
no
event
shall
EG&G
ORTEC
be
liable
for
special
or
consequential
damages.
QUALITY
CONTROL
Before
being
approved
for
shipment,
each
EG&G
ORTEC
instrument
must
pass
a
stringent
set
of
quality
control
tests
designed
to
expose
any
flaws
in
materials
or
workmanship.
Permanent
records
of
these
tests
are
maintained
for
use
in
warranty
repair
and
as
a
source
of
statistical
information
for
design
improvements.
REPAIR
SERVICE
If
it
becomes
necessary
to
return
this
instrument
for
repair,
it
is
essential
that
Customer
Services
be
contacted
in
advance
of
its
return
so
that
a
Return
Authorization
Number
can
be
assigned
to
the
unit.
Also,
EG&G
ORTEC
must
be
informed,
either
in
writing
or
by
telephone
[(615)
482-4411],
of
the
nature
of
the
fault
of
the
instrument
being
returned
and
of
the
model,
serial,
and
revision
("Rev"
on
rear
panel)
numbers.
Failure
to
do
so
may
cause
unnecessary
delays
in
getting
the
unit
repaired.
The
EG&G
ORTEC
standard
procedure
requires
that
instruments
returned
for
repair
pass
the
same
quality
control
tests
that
are
used
for
new-production
instruments.
Instruments
that
are
returned
should
be
packed
so
that
they
will
withstand
normal
transit
handling
and
must
be
shipped
PREPAID
via
Air
Parcel
Post
or
United
Parcel
Service
to
the
nearest
EG&G
ORTEC
repair
center.
The
address
label
and
the
package
should
include
the
Return
Authorization
Number
assigned.
Instruments
being
returned
that
are
damaged
in
transit
due
to
inadequate
packing
will
be
repaired
at
the
sender's
expense,
and
it
will
be
the
sender's
responsibility
to
make
claim
with
the
shipper.
Instruments
not
in
warranty
will
be
repaired
at
the
standard
charge
unless
they
have
been
grossly
misused
or
mishandled,
in
which
case
the
user
will
be
notified
prior
to
the
repair
being
done.
A
quotation
will
be
sent
with
the
notification.
DAMAGE
IN
TRANSIT
Shipments
should
be
examined
immediately
upon
receipt
for
evidence
of
external
or
concealed
damage.
The
carrier
making
delivery
should
be
notified
immediately
of
any
such
damage,
since
the
carrier
is
normally
liable
for
damage
in
shipment.
Packing
materials,
waybills,
and
other
such
documentation
should
be
preserved
in
order
to
establish
claims.
After
such
notification
to
the
carrier,
please
notify
EG&G
ORTEC
of
the
circumstances
so
that
assistance
can
be
provided
in
making
damage
claims
and
in
providing
replacement
equipment
if
necessary.

Ill
CONTENTS
Page
WARRANTY
ii
PHOTOGRAPHS
iv
1.
DESCRIPTION
1
1.1.
Purpose
•
1
1.2.
Description
1
1.3.
Related
Equipment
1
2.
SPECIFICATIONS
1
2.1.
Performance
1
2.2.
Controls
2
2.3.
Internal
Jumpers
2
2.4.
Inputs
2
2.5.
Outputs
2
2.6.
Data
Bus
Connector
2
2.7.
Electrical
and
Mechanical
2
3.
INSTALLATION
3
3.1.
General
3
3.2.
Connection
to
Power
.
3
3.3.
Input
Interconnections
3
3.4.
Analyzer
Interconnections
3
3.5.
Internal
Jumper
Selections
3
3.6.
Internal
Time
Constant
Selections
4
4.
OPERATION
4
4.1.
Threshold
Adjustment
4
4.2.
Fine
Gain
Adjustments
4
4.3.
Operating
Procedures
4
5.
CIRCUIT
DESCRIPTION
4
5.1.
General
4
5.2.
Linear
Circuit
5
5.3.
Logic
Gates
5
5.4.
Routing
Generator
5
5.5.
Routing
Outputs
and
Handshake
Signals
5
5.6.
Internal
Power
Distribution
6
6.
FACTORY
SERVICE
6
APPENDIX
7
Schematic
476-0201-SI

nultiKexer
'•%
0
m
LINEAU
CUT
CCNTRCL

EG&G
ORTEC
MODEL
476
MULTIPLEXER/ROUTER
1.
DESCRIPTION
1.1.
PURPOSE
The
EG&G
ORTEC
476
Multiplexer/Router
is
a
modular
nuclear
instrument
that
will
interface
a
quantity
of
detec
tor-preamplifier-amplifier
circuits
into
a
single
data
accumulation
system
and
provide
for
simultaneous
stor
age
of
their
separate
spectra.
Each
of
the
detector-pre
amplifier-amplifier
circuits
is
connected
to
the
analyzer
through
one
of
the
multiple
channels
in
the
476.
The
476
then
provides
the
multiplexed
analog
signals
for
all
chan
nels,
together
with
logic
levels,
to
indicate
the
unique
channel
through
which
each
analog
signal
was
processed.
If
the
data
acquisition
system
is
set
to
respond
to
the
logic
signals
as
intended,
its
total
memory
is
subdivided
so
that
a
unique
spectrum
can
then
be
accumulated
for
the
sig
nals
from
each
of
the
detector-preamplifier-amplifier
channels.
There
are
three
basic
versions
of
the
EG&G
ORTEC
476
Multiplexer/Router.
The
476-04
includes
four
input
chan
nels:
the
476-08
includes
eight
channels:
and
the
476-16
includes
16
channels.
This
manual
will
discuss,
primarily,
the
476-16
version.
The
principles
of
operation
and
the
logic
are
similar
for
each
of
the
other
two
versions.
1.2.
PHYSICAL
DESCRIPTION
The
476
is
built
in
a
double-width
NIM
module
that
must
be
installed
in
a
standard
bin
and
power
supply
for
opera
tion.
All
of
the
input
signal
connections
are
included
on
the
front
panel,
together
with
individual
fine
gain
controls
for
each
channel
and
other
operator
controls.
The
multi
plexed
analog
output
and
the
binary-coded,
logic
channel
identification
output
are
on
the
rear
panel.
A
common
threshold
control
is
included
on
the
front
panel.
This
permits
the
operator
to
adjust
an
input
ampli
tude
threshold
for
all
channels:
it
is
normally
set
just
above
system
noise.
A
toggle
switch
permits
the
operator
to
select
any
single
channel,
together
with
the
rotary
selector
switch
at
the
upper
right,
so
that
its
gain
can
be
adjusted
conveniently.
The
toggle
switch
is
normally
set
at
the
Multiplex
position,
and
the
rotary
switch
is
ineffec
tive
since
all
channels
are
active.
1.3.
RELATED
EQUIPMENT
The
design
of
the
476
Multiplexer/Router
is
compatible
with
the
EG&G
ORTEC
7000
Series
Data
Acquisition
and
Analysis
Systems
(DAAS),
and
can
be
easily
customized
for
operation
with
other
multichannel
analyzer
systems
such
as
the
EG&G
ORTEC
6240B.
Internal
jumper
selec
tions
permit
the
subgroup
selections
to
affect
any
two,
three,
or
four
adjacent
address
bits
from
2®
through
2".
This
allows
subgroup
routing
to
be
used
for
a
wide
variety
of
total
memory
capacities,
which
are
available
in
these
analyzers.
Mode
selection
signals
and
timing
logic
signals
are
also
included
in
the
interconnections.
To
permit
very
large
systems
to
be
developed,
there
is
a
provision
for
jumper
selection
to
activate
a
particular
476
where
there
can
be
as
many
as
four
of
these
units
in
the
system.
This
provision
could
conceivably
permit
a
system
to
be
organized
with
as
many
as
48
separate
detector-
preamplifier-amplifier
input
channels
and
with
unique
storage
of
the
spectrum
from
each
channel.
2.
SPECIFICATIONS
2.1.
PERFORMANCE
MULTIPLEXING
CAPACITY
One
to
16
linear
(analog)
channels
in
the
476-16:8
channels
in
the
476-8:4
channels
in
the
476-4.
EXPANSION
CAPABILITY
Provisions
to
expand
to
three
multiplexing
modules.
ANALYZER
MODE
IDENTIFICATION
Jumper
selec
tions
to
identify
any
one
of
three
possible
analyzer
modes.
TIME
CONSTANT
Each
channel
includes
switching
to
match
the
time
constant
of
the
amplifier
from
which
the
signals
are
furnished:
1-,
2-,
3-,
or
6-^8
shaping
can
be
matched.
ISOLATION
Typically
65
dB
from
any
off-channel.
OPERATING
TEMPERATURE
0
to
50°
0
(273
-
323K).
DC
LEVEL
SHIFT
<0.1
mV/°G.
INTEGRAL
NONLINEARITY
<0.1%.
NOMINAL
GAIN
=
unity.
GAIN
STABILITY
50
ppm/°G.
GATING
Internal
logic
gates
an
analog
signal
through
the
476
for
the
identified
channel
only:
automatically
locks
out
response
in
all
other
channels.
Also
accepts
external
ADG
Busy
signal
to
inhibit
switching
of
analog
signals
until
the
ADG
has
finished
processing
the
signal.

2.2.
CONTROLS
CHANNEL
SELECT
Front
panel
rotary
switch
selects
any
single
channel
continuously
for
calibration
or
testing
purposes.
16-position
switch
in
the
476-16;
8
positions
in
the
476-8;
4
positions
in
the
476-4.
SINGLE
CHANNEL/NORMAL
MULTIPLEX
Front
panel
toggle
switch
allows
either
the
Channel
Select
switch
or
internal
logic
to
control
the
linear
gate
channel
selections.
THRESHOLD
Front
panel
discriminator
threshold
con
trol
common
to
all
channels;
10-turn
Helipot;
range
0
to
100
mV.
FINE
GAIN
Front
panel
20-turn
control
for
each
chan
nel,
used
to
trim
the
unity
gain
adjustment;
range
~±0.34%.
TIME
CONSTANT
A
4-section
miniature
slide
switch,
mounted
on
the
printed
circuit,
permits
selection
of
1,
2,
3,
or
6
ius
to
match
the
related
amplifier
shaping
time
con
stant;
one
switch
assembly
for
each
channel.
2.3.
INTERNAL
JUMPERS
7010/6240B
Jumper
selects
either
polarity
of
strobe
signal
from
related
analyzer.
476
SELECT
Jumper
selects
which
of
four
possible
476
modules
is
active;
must
match
the
ADC
to
which
the
476
is
connected.
ROUTING
BITS
Jumpers
select
the
high
order
bits
for
routing
according
to
memory
capacity
and
number
of
subgroups;
select
4
adjacent
bits
for
16
subgroups,
3
bits
for
8
subgroups,
or
2
bits
for
4
subgroups;
available
bit
identities
are
from
FED8
through
FED15.
MODE
SELECTIONS
Jumper
selects
which
of
three
modes
is
identified
to
the
analyzer
from
the
476;
BM1
identifies
a
PHA
type
request
normally
not
used.
2.4.
INPUTS
LINEAR
INPUTS
One
BNC
connector
per
channel
on
the
front
panel
accepts
0-
to
10-V
positive
pulses
from
an
amplifier,
shaped
with
1-,
2-,
3-,
or
6-ais
time
constant
or
stretched
>2
^lS.
Z,„
~100n,
dc-coupled.
ADC
BUSY
Rear
panel
BNC
connector
accepts
an
ADC
Busy
signal
from
the
analyzer
to
hold
a
routing
signal
until
storage
is
complete.
CONTROL
Rear
panel
20-pin
connector
carries
ex
ternal
control
signals
for
logic
gates;
signals
are
listed
in
Table
2.1.
A
low
logic
level
on
the
corresponding
FEC
line
+1
disables
that
input.
(FEC0
inhibits
channel
1,
etc.)
2.5.
OUTPUTS
LINEAR
OUT
Rear
panel
BNC
provides
the
analog
out
put
to
be
used
as
an
ADC
input
in
the
related
analyzer.
GATE
OUT
Rear
panel
BNC
provides
a
logic
pulse
to
be
used
as
a
gate
input
to
the
ADC.
Nominally
+4
V
from
discriminator
crossing
of
a
valid
pulse
until
ADC
Busy
returns
to
false.
Table
2.1.
Front
End
Control
Bus.
Pin
Signal
Pin
Signal
1
Gnd
11
Gnd
2
FEC0
12
FEC8
3
FEC1
13
FEC9
4
FEC2
14
FEC10
5
FEC3
15
FEC
11
6
FEC4
16
FEC12
7
FEC5
17
FEC13
8
FEC6
18
FEC14
9
FEC7
19
FEC15
10
Gnd
20
Gnd
2.6.
DATA
BUS
CONNECTOR
DATA
BUS
Rear
panel
50-pin
connector
provides
both
data
and
handshake
signals
between
the
476
and
the
re
lated
analyzer;
pin
assignments
are
listed
in
Table
2.2.
2.7.
ELECTRICAL
AND
MECHANICAL
POWER
REQUIREMENTS
+12
V,
220
mA;
-12
V,
45
mA;
+24
V,
160
mA;
-24
V,
40
mA.
DIMENSIONS
NIM-standard
double-width
module
(2.70
by
8.714
in.front
panel)
per
TID-20893
(Rev).
Table
2.2.
Front
End
Data
Bus.
Pin
Signal
Pin
Signal
1
FED0
26
BM01
2
FED1
27
BM02
3
FED2
28
GND
4
FED3
29
FERDY
5
FED4
30
GND
6
FED5
31
COMP
7
FED6
32
GND
8
FED7
33
STROBE
9
FED8
34
GND
10
FED9
35
ENAB
11
FED10
36
GND
12
FED11
37
SEL0
13
FED12
38
GND
14
FED13
39
SEL1
15
FED14
40
GND
16
FED15
41
SEL2
17
FED16
42
GND
18
FED17
43
SEL3
19
FED18
44
GND
20
FED19
45
ADC
READY
21
FED20
46
GND
22
FED21
47
TX
COMP
23
FED22
48
GND
24
FED23
49
ADCSTROBE
25
BMO0
50
GND

3.
INSTALLATION
3.1.
GENERAL
The
476
Multiplexer/Router
is
used
in
conjunction
with
a
NIM-standard
bin
and
power
supply,
such
as
the
EG&G
ORTEG
401/402
Series.
The
bin
and
power
supply
is
designed
for
rack
mounting:
therefore
if
any
other
in
struments
which
generate
heat
are
mounted
in
the
same
rack,
it
is
important
that
sufficient
circulating
air
pre
vents
any
localized
heating
of
the
solid-state
circuitry
used
in
the
476.
Precautions
should
be
taken
to
ensure
that
the
476
is
not
subjected
to
temperatures
in
excess
of
120°F
(50°
0).
3.2.
CONNECTION
TO
POWER
The
476
contains
no
power
supply
and
must
obtain
its
dc
operating
power
from
the
NIM
bin
and
power
supply
in
which
it
is
inserted
for
operation.
Always
turn
off
power
for
the
bin
power
supply
before
inserting
or
removing
any
modules.
The
EG&G
ORTEC
modules
are
designed
so
that
it
is
not
possible
to
overload
the
bin
power
supply
with
a
full
complement
of
modules
in
the
bin.
Since,
how
ever,
this
may
not
be
true
when
the
bin
contains
modules
other
than
those
of
EG&G
ORTEC
design,
power
supply
voltages
should
be
checked
after
modules
have
been
in
serted.
The
EG&G
ORTEG
401/402
Series
Bins
and
Power
Supplies
are
designed
with
test
points
on
the
power
supply
control
panel
so
that
these
dc
voltage
levels
may
be
monitored
easily.
3.3.
INPUT
INTERCONNECTIONS
The
inputs
that
are
furnished
from
shaping
and/or
biased
amplifiers
are
located
on
the
front
panel
of
the
476.
They
are
numbered
from
1
through
16
and
are
to
be
used
arbi
trarily
except
that
each
will
generate
a
routing
signal
according
to
its
sequential
significance.
For
example,
the
inputs
that
are
furnished
through
connectors
1
through
8
will
provide
a
false
signal
through
the
most
significant
bit
(of
4
bits)
to
select
a
memory
segment
within
the
first
half
of
the
available
memory.
Those
inputs
through
connec
tors
9
through
16
will
provide
a
true
signal
through
this
same
line
to
select
the
upper
half
of
the
available
memory.
Thus,
if
only
two
of
the
available
16
inputs
were
to
be
used,
and
the
memory
were
subdivided
into
halves,
the
input
connections
should
be
furnished
to
connectors
8
and
16
of
the
476.
This
basic
logic
can
be
extrapolated
for
other
configurations.
To
use
4
inputs
and
operate
the
memory
with
division
into
quadrants,
use
input
connectors
4,8,12,
and
16
on
the
476.
When
used
with
a
7000
Series
Analyzer,
this
is
software-controlied
and
does
not
apply.
The
ADG
Busy
input
on
the
rear
panel
can
accept
this
signal
from
the
related
ADG
to
aid
in
the
timing
of
the
internal
gating
logic
of
the
476.
This
connection
is
recom
mended.
3.4.
ANALYZER
INTERCONNECTIONS
The
Linear
Out
connector
on
the
476
rear
panel
is
the
source
of
analog
signals
to
be
used
for
the
ADG
input.
Use
93fi
cable
to
connect
the
476
Linear
Out
connector
to
the
ADG
Linear
Input.
Use
of
the
Gontrol
connector
on
the
476
rear
panel
is
op
tional.
If
it
is
used,
the
analyzer
can
provide
a
ground
level
through
any
of
its
16
control
lines
to
inhibit
transfer
of
signals
through
the
associated
476
channel(s).
A
cable,
terminated
with
20-pin
connectors,
is
furnished
to
permit
this
interconnection
between
the
476
and
the
7000
Series
DAAS.
The
50-pin
Data
Bus
connector
on
the
rear
panel
must
be
connected
to
the
analyzer
because
it
contains
the
hand
shake
and
control
signals
that
are
used
between
the
in
struments
as
well
as
the
routing
signals
that
are
generated
in
the
476.
A
cable,
terminated
with
50-pin
connectors,
is
furnished
for
this
interconnection.
The
use
of
the
routing
signals
is
optional,
since
the
476
can
be
used
to
accept
inputs
from
several
detectors
that
are
to
be
analyzed
in
a
single
spectrum;
this
effectively
increases
the
detection
efficiency
according
to
the
geometric
positioning
of
the
several
detectors.
However,
the
routing
signals
are
gener
ated
and
furnished
to
the
analyzer,
whether
they
are
used
or
not.
3.5.
INTERNAL
JUMPER
SELECTIONS
Provisions
are
included
on
the
printed
circuit
board
in
side
the
476
for
selections
of
various
operating
param
eters,
and
these
must
be
examined
and
revised
as
re
quired
by
the
specific
application.
One
jumper
selects
either
of
two
alternate
settings;
one
is
marked
7010
and
the
other
is
marked
6240B.
The
pur
pose
is
to
select
which
of
two
complementary
Strobe
signal
polarities
will
be
accepted
to
enable
routing
selec
tions.
The
high-true
signals
are
furnished
from
the
EG&G
ORTEG
7000
Series
DAAS,
while
the
low-true
signals
are
provided
from
the
EG&G
ORTEG
6240B
Multichannel
Analyzer.
The
resulting
polarity
of
the
ADG
STROBE
output
and
the
mode
output
selections
is
correct
for
the
7000
Series
applications;
these
signals
are
not
used
in
the
6240B
applications,
so
their
inverted
polarity
does
not
make
any
difference.
There
is
a
block
that
accommodates
4
jumpers,
associ
ated
with
the
input
lines
marked
SEL0
through
SEL3.
No
jumper
is
required
if
the
476
output
is
furnished
to
an
analyzer
with
a
single
ADG.
If
it
is
used
in
a
multiple-ADG
configuration,
the
ADG
that
is
used
in
conjunction
with
the
476
must
be
identified
(SEL0,
SEL1,
SEL2,
or
SEL3),
and
a
jumper
must
be
instailed
in
the
476
to
match
the
ADG
identity.
A
third
jumper
block
includes
three
alternate
jumper
locations.
When
the
476
is
shipped
from
the
factory,
a
jumper
is
installed
to
the
BM01
output
selection,
and
this
is
used
in
a
7000
Series
DAAS
to
identify
each
data
trans-
fer
as
a
PHA
type
request.
The
alternate
settings,
BMO0
and
BM02,
are
reserved
for
possible
future
operations
that
may
be
selected
in
the
7000
Series
DAAS.

The
largest
jumper
block
permits
the
four
available
rout
ing
output
bits
to
be
connected
across
to
any
four
adja-
cent
address
bits
within
the
limits
of
FEDS
through
FED
15.
When
the
unit
is
shipped
from
the
factory,
these
jumpers
are
set
to
select
FED12
through
FED15;
software
in
the
DAAS
may
be
used
to
translate
these
selections
to
the
four
most
significant
bits
in
whatever
memory
size
is
included.
If
desired,
the
four
jumpers
can
be
moved
to
any
four
adjacent
output
lines
within
the
range
that
is
identified.
3.6.
INTERNAL
TIME
CONSTANT
SELECTIONS
Each
channel
in
the
476
has
an
input
circuit
that
includes
a
group
of
four
time
constant
selection
switches.
These
are
miniature
slide
switches
mounted
across
the
bottom
of
the
printed
circuit.
The
switch
assembly
toward
the
rear
panel
is
associated
with
channel
0
(the
Linear
Input
1
connector),
and
the
assembly
toward
the
front
panel
is
used
for
the
highest
numbered
channel.
The
four
switches
in
each
assembly
are
numbered
(1,
2,
3,
and
4).
Only
one
of
these
four
switches
is
to
be
set
at
the
On
position.
Use
the
switch
that
is
appropriate
for
the
shaping
time
of
the
input
pulses.
Use
switch
1
if
the
input
is
shaped
with
a
l-^s
time
constant
or
if
it
is
stretched
for
at
least
2
/js.
Use
switch
2
if
the
input
has
2-fiS
shaping.
Use
switch
3
for
3
nS.
Use
switch
4
for
6-ns
shaping.
Note
that
the
shaping
time
constant
selection
for
each
channel
is
completely
independent
from
all
other
chan
nels.
4.
OPERATION
4.1.
THRESHOLD
ADJUSTMENT
The
Threshold
control
at
the
upper
left
on
the
front
panel
is
used
to
set
the
discrimination
level
just
above
the
sys
tem
noise,
and
this
is
common
to
all
input
channels.
The
range
for
this
control
is
0
to
100
mV,
which
should
be
adequate
for
any
normal
application.
4.2.
FINE
GAIN
ADJUSTMENTS
Each
channel
in
the
476
includes
a
Fine
Gain
screwdriver
control
on
the
front
panel.
This
control
is
used,
when
required,
to
equalize
small
differences
in
the
linear
gain
between
channels.
The
range
of
each
control
is
limited
to
±0.34%.
Larger
gain
changes
should
be
controlled
at
the
input
amplifier
in
the
system;
this
is
for
trim
purposes
only.
The
intended
gain
factor
for
each
signal
that
passes
through
the
linear
portion
of
the
476
is
unity.
The
effective
gain
through
each
channel
can
be
measured
by
setting
the
front
panel
toggle
switch
at
Channel
Select
and
then
turning
the
Channel
Selector
switch
to
each
channel
that
is
to
be
examined.
A
dynamic
check,
using
a
radioactive
source
to
affect
each
related
detector,
is
recommended.
When
the
testing
has
been
accomplished,
return
the
toggle
switch
to
Normal
Multiplex
(the
Channel
Selector
is
ineffective
for
this
toggle
switch
setting).
4.3.
OPERATING
PROCEDURES
After
the
476
has
been
installed
according
to
the
informa
tion
in
Section
3,
and
its
threshold
and
gain
adjustments
have
been
made,
no
further
operating
controls
are
re
quired.
Each
input
pulse
from
any
of
its
sources
will
trigger
a
logic
response
that
will
generate
a
routing
output
identification;
the
response
to
one
input
will
also
inhibit
any
input
pulse
through
an
alternate
channel
until
the
first
pulse
has
been
transferred
to
the
ADC.
The
Busy
indicator
on
the
476
front
panel
provides
a
visual
indi
cation
that
input
signal
amplitudes
are
exceeding
the
threshold;
it
can
be
used
as
an
aid
when
adjusting
the
Threshold
control.
The
internally
generated
routing
signal
is
also
used
to
gate
the
linear
signal
through
to
the
Linear
Out
connector
on
the
rear
panel.
5.
CIRCUIT
DESCRIPTION
5.1.
GENERAL
The
schematic
for
the
EG&G
ORTEC
476
Multiplexer/
Router
is
476-0201-S1,
included
at
the
back
of
this
manual.
All
the
circuits
are
included
on
the
single
printed
circuit
board
and
on
the
front
and
rear
panels.
The
follow
ing
parts
are
included
in
the
circuits:
1.
Sixteen
Linear
Input
circuits.
Each
input
signal
is
furnished
through
a
Fine
Gain
adjustment
and
into
an
analog
multiplexer.
The
logic
circuit
selects
one
of
the
16
inputs
according
to
a
4-line
binary
code
(the
internally
generated
routing
signal).
2.
Each
input
signal
is
also
furnished
into
a
logical
gate
that
identifies
the
channel
into
which
the
signal
is
re
ceived
and
permits
gating
for
that
signal
together
with
lockout
of
any
subsequent
input
signal(s)
until
the
first
has
been
transferred.

3.
A
routing
signal
generator,
using
16
input
lines
and
a
4-bit
binary
decoder;
also
accommodates
any
single
channel
selection.
4.
Routing
signal
output
circuit
and
analyzer
handshake
signals.
5.2.
LINEAR
CIRCUIT
Input
1
can
be
used
as
the
typical
circuit.
The
signal
passes
through
ONI
and
Fine
Gain
adjustment
R185
and
is
applied
to
one
of
the
16
inputs
of
101,
pin
19.
When
all
four
levels
at
pins
14
through
17
are
high,
the
input
at
pin
19
is
switched
through
to
pin
28.
The
linear
signal
then
passes
through
A2
and
A1
to
provide
the
Linear
Out
sig
nal
through
CN17.
Each
alternate
input
circuit
is
identical
to
the
Input
1
cir
cuit.
The
selection
between
the
16
inputs
to
101
is
a
func
tion
of
the
binary-coded
levels
at
its
pins
14
through
17,
and
this
combination
is
generated
by
the
routing
signal
generator.
5.3.
LOGIC
GATES
Each
of
the
16
inputs
is
also
connected
to
a
gated
dis
criminator.
Input
1
can
again
be
used
as
the
typical
circuit.
The
input
signal
from
ONI
is
furnished
through
01
to
buffer-shaper
105-8
(the
section
of
105
that
includes
pin
8
as
the
output).
The
shaped
output
from
105-8
is
fur
nished
into
discriminator
109-2,
where
it
is
compared
to
the
level
furnished
from
Threshold
control
R20;
when
109-2
triggers,
this
sets
flip-flop
1026-13.
1017-8
provides
a
low
level
to
pin
10
of
1016
to
indicate
that
an
input
has
been
acknowledged
through
channel
0
(the
Input
1
in
ternal
circuit).
Integrated
circuit
1016
encodes
the
signal
from
its
pin
10
for
its
3-line
binary
output
and
switches
the
level
at
its
pin
15
to
high.
1015-8
switches
to
low
to
latch
the
binary
code
from
1016
through
1013,
where
it
will
remain
until
the
next
input
signal
initiates
a
new
sequence.
The
low
at
1015-8
also
triggers
two
monostables;
1039-7
turns
on
the
front
panel
Busy
indicator,
and
1039-9
generates
an
in
hibit
to
all
gates
through
1040-3
and
IO40-6;
no
new
input
pulse
can
initiate
a
response
until
the
gate
signal
has
been
released.
The
gate
signal
from
1039-9
is
gated
through
1040-3
together
with
the
level
furnished
through
the
ADO
Busy
input
circuit,
ONI8,
and
the
response
through
all
channels
can
thus
be
inhibited
until
the
ADO
Busy
returns
to
a
low
level
after
the
signal
has
been
processed.
If
the
circuits
through
the
rear
panel
control
connectorare
used,
the
FEO0
line
(Front
End
Oontrol
for
channel
0)
can
be
used
to
aid
in
determining
the
exact
reset
time
for
flip-flop
1026-13,
or
it
can
be
held
as
a
low
input
to
inhibit
any
response
through
channel
0
as
a
function
of
the
soft
ware
in
the
analyzer.
An
input
through
channel
1
to
7
(0N2
through
0N8)
will
generate
a
logic
response
through
its
unique
circuit
to
trigger
its
flip-flop
within
the
group
from
1026-9
through
1024-7,
and
the
result
will
be
encoded
in
1016
for
the
rout
ing
identity
to
1013,
and
the
gating
will
be
provided
in
the
same
manner
as
described
above.
An
input
to
channel
8
(0N9)
will
generate
a
response
through
1022-13
that
is
furnished
to
1011.
When
this
occurs,
1011
generates
the
encoded
output
through
its
pins
6,
7,
and
9
and
also
switches
its
pins
14
and
15
to
high.
The
high
at
1011-14
causes
latch
1013
to
look
at
the
inputs
from
1011
instead
of
those
from
1016.
The
high
at
1011-15
carries
through
1016
and
initiates
the
responses
for
1015-8.
An
input
through
channel
9
through
15
(ON10
through
0N16)
will
generate
a
logic
response
through
its
unique
circuit
and
trigger
its
flip-flop
within
the
group
from
1022-9
through
IO20-4,
and
the
result
will
be
en
coded
in
1011
for
the
routing
identity
and
control
to
1013
in
the
same
manner
as
described
for
a
signal
through
channel
8.
5.4.
ROUTING
GENERATOR
A
low-true
binary
code
for
channels
0
through
15
is
pro
vided
at
pins
15,14,13,
and
12,
respectively,
of
1013.
This
information
is
obtained
as
described
in
Section
5.3above.
The
channel
code
is
furnished
as
one
of
the
two
input
groups
to
multiplexer
1014.
If
1014-1
is
high,
this
input
is
transferred
directly
to
the
4-line
output
of
1014
and
used
as
the
routing
code.
The
alternate
input
to
1014
comes
from
1023
and
is
ac
cepted
when
1014-1
is
low.
1023
encodes
the
selection
of
switch
317,
in
which
settings
1
through
16
of
817
corre
spond
respectively
to
channels
0
through
15
as
decoded
by
10
23.
Switch
S18
determines
whether
1014-1
is
at
a
high
or
low
level.
When
it
is
set
at
Normal
Multiplex,
1014-1
is
high
and
the
output
is
the
channel
code
from
1013.
When
switch
SI8
is
set
at
Single
Obannel
Select,
1014-1
is
low
and
the
output
is
the
channel
code
from
1023.
The
4-llne
output
from
1014
is
furnished
through
inverters
to
control
the
selection
by
101
(see
Section
5.2).
It
is
also
furnished
to
four
OR
gates,
1018-3,
-6,
-11,
and
-8,
for
transfer
as
routing
output
signals.
The
common
control
line
to
these
four
gates
must
be
held
low
to
permit
the
transfer
of
the
routing
code.
5.5.
ROUTING
OUTPUTS
AND
HANDSHAKE
SIGNALS
A
strobe
signal
must
be
furnished
from
the
associated
ADO
to
complete
the
transfer
of
the
routing
output
in
formation.
This
will
be
furnished
from
the
ADO
in
re
sponse
to
the
Linear
Out
analog
signal
that
has
been
furnished
through
0N17
(see
Section
5.2).
Ifasystem
has
more
than
one
ADO,
the
correct
SEL
line
must
also
have
been
pulled
to
a
high
level
and
this
information
trans
ferred
through
an
internal
jumper
to
pin
9
of
1027-8.
If
the
7010/6240B
jumper
has
been
set
at
6240B,
the
input
strobe
from
the
analyzer
is
a
low
level
and
will
enable
the
transfer
through
the
OR
gates
in
1018.
The
combination
of
FED
lines
that
carry
the
coded
routing
signal
is
deter-

mined
by
the
jumpers
(see
Section
3.5).
No
other
transfer
signals
are
used
in
the
6240B,
so
the
remaining
signals
are
of
no
consequence.
If
the
7010/6240B
jumper
has
been
set
at
7010,
the
input
strobe
from
the
analyzer
must
be
a
high
level
signal.
IC27-8
must
have
been
enabled
as
described
above,
and
its
output
switches
to
low
when
the
strobe
is
furnished.
The
low
at
IC27-8
enables
the
OR
gates
in
1018
to
transfer
the
coded
routing
signal.
It
also
provides
the
BM1
output
(if
the
jumper
is
set
as
shown
in
schematic
476-0201-SI)
to
identify
this
as
a
PHA
request
to
the
analyzer.
These
signals
are
used
only
when
an
EG&G
ORTEC
800
ADC
is
connected
to
a
7000
Series
analyzer
in
parallel
with
the
476.
When
the
800
ADC
generates
an
ADC
READY,
it
passes
through
the
476
to
generate
a
FERDY
signal
to
the
7000
to
indicate
that
the
800
ADC
has
data
ready
to
trans
fer
to
the
7000.
The
7000
then
generates
a
strobe
signal
to
gate
the
routing
information
onto
the
FED
lines:
it
is
also
inverted
and
passed
to
the
800
ADC
as
an
ADC
STRCBE
to
place
the
address
information
in
the
ADC
onto
the
low-order
FED
lines.
A
CCMP
signal
from
the
7000
indi
cates
that
the
address
transfer
is
finished
and
this
signal
is
inverted
and
passed
to
the
800
ADC
as
a
TXCCMPLETE
signal.
5.6.
INTERNAL
POWER
DISTRIBUTION
The
circuits
of
the
476
require
operating
do
power
levels
at
±12
V
and
±24
V,
furnished
directly
from
the
bin
power
supply,
and
at
+5
V.
The
+5
V
level
is
derived
from
the
+12
V
input
through
regulator
IC41.
6.
FACTORY
SERVICE
This
instrument
can
be
returned
to
the
EG&G
CRTEC
factory
forserviceand
repair
at
a
nominal
cost.
The
EG&G
CRTEC
standard
procedure
for
repair
ensures
that
the
same
quality
control
and
checkout
procedures
that
are
used
for
a
new
instrument
will
be
used
for
the
repaired
unit.
Always
contact
Customer
Services
at
EG&G
CRTEC,
(615)
482-4411,
before
sending
in
an
instrument
for
repair
to
obtain
shipping
instructions
and
so
that
the
required
Return
Authorization
Number
can
be
assigned
to
the
unit.
This
number
should
be
written
on
the
address
label
and
on
the
package.

APPENDIX
REPLACEABLE
PARTS
ORDERING
INFORMATION
The
Replaceable
Parts
List
shown
below
contains
Infor
mation
needed
for
ordering
spare
and/or
replacement
parts.
Each
listing
indicates
the
reference
designator
number,
the
part
number,
a
description
of
the
component,
and
the
part
manufacturer
and
manufacturer's
part
number.
All
inquiries
concerning
spare
and/or
replacement
parts
and
all
orders
for
same
should
include
the
model
serial,
and
revision
("Rev"
on
rear
panel)
numbers
of
the
instru
ments
involved
and
should
be
addressed
to
EG&G
ORTEC
Customer
Services
at
100
Midland
Road,
Oak
Ridge,
Tennessee
37830.
The
Manager
of
Customer
Ser
vices
can
be
reached
by
telephone
at
(615)
482-4411.
The
minimum
order
for
spare
and/or
replacement
parts
is
$50.00.
ORDERING
INFORMATION
FOR
PARTS
NOT
LISTED
In
order
to
facilitate
the
ordering
of
a
part
not
listed
below,
the
following
information
should
be
submitted
to
Cus
tomer
Services;
1.
the
instrument
model
number,
2.
the
instrument
serial
number,
3.
revision
("Rev"
on
rear
panel)
number,
4.
a
description
of
the
part,
5.
information
as
to
the
function
and
location
of
the
part.
The
solid-state-device
(diodes,
transistors,
and
integrated
circuits)
types
installed
in
your
instrument
may
differ
from
those
shown
in
the
schematic
diagram
and
parts
list.
In
such
cases,
necessary
replacements
can
be
made
with
either
the
type
shown
or
the
type
actually
installed
in
the
instrument.
Replaceable
Parts
List
EG&G
ORTEC
item
No.
All
Models
476-8
&
476-16
476-16
Only
Capacitors
3
pF
10%
471520
072
10
pF
5%
Mica
500
V
417010
071
39
pF
5%
Mica
468750
079
47
pF
5%
Mica
468420
05,
6,
13,
15
019,
25,27,
30
032,
36,
41, 43, 46,
53,
55,
58
220
pF
2%
Mica
500
V
417080
075,
81
■
500
pF
20%
Mica
500
V
408930
01,
4,
12,
14
017,
24,
26,
29
031,
35,
40, 42, 45,
52,54,
57
1000
pF
Disc
436370
059
10000
pF
Disc
436380
02,
3,
8,
10, 11,
16,
018,
20,
21, 22, 23,
28
033,
34,
37,38,
39,
44,47,
60, 62,
67,
70, 77,
84,
48,
49,
50, 51,
56
88,89,
90,
91,
92,
93,
94,
95.
96,
97
10
mF
10%
35
V
409440
07,
61,
63,65,66,
68,
69,
74,
78,
82,
85,86,
87
15
mF
10%
16
V
409490
064,
76
33
mF
10%
16
V
409520
080,
83
Indicator
LED
Indicator,
mounted
637980
D1
Integrated
Circuits
HA1-4625-5
450710
105
104
102,
3
HA1-4905-5
450700
109
108
106,
7
HD1-0165-5
450730
1023
HI1-506-5
450720
101
LM340T
5
V
Regulator
440440
1041
SN7400N
440730
1040
SN7417N
654600
1019,
28,
37,
38

8
Replaceable
Parts
List
(cont'd.)
EG&G
ORTEC
Item
No.
All
Models
476-8
&
476-16
476-16
Only
74LS00
495310
IC27
74LS04
604480
IC32,
33,
36
IC29
74LS08
604650
IC35
IC34
IC30,
31
74LS10
495290
IC17,
25
iCIO,
12,
21
74LS32
495280
IC18
74LS148
656030
IC11,
16
74LS157
495160
IC14
74LS279
449190
IC26
IC24
IC20,
22
74LS298
655990
IC13
74L10
663630
IC15
9602PC
637520
IC39
Inductors
2.2
Hybrid
Operational
Amplifiers
HOA0101
HOA0201
Transistors
FD1735
MPS6531
Resistor
Assemblies
Seven
each
5.1
K
Resistors
ion
5%
1/4W
cc
611770
LI,
2.
3
51
n
5%
1/4W
CC
lOOn
5%
3W
WW
igen
i%
i/sw
mf
t2
200n
20T
Trim
pot
200n
20T
Pot
330n
5%
1/4W
CC
422n
1%
1/8W
MF
T2
51
on
5%
1/4W
CC
51
in
1%
1/8W
MF
T2
562n
1%
1/8W
MF
T2
909n
1%
1/8W
MF
T2
IK
1%
1/8W
MF
T2
IK
5%
1/4W
CC
IK
10T
Pot
1.1K
1%
1/8W
MF
T2
1.21K
1%
1/8W
MF
T2
1.96K
1%
1/8W
MF
T2
2.37K
1%
1/8W
MF
T2
3.48K
1%
1/8W
MF
72
679310
A1
679300
A2
480180
Q2
436550
Q1,3
658480
RA2,
3,
4
402020
R8,
10.
21, 24,
226,
231,
232,
234,
236,
244, 245,
249,250,
251
402710
R1,
11,
27,
35,
186,
188, 190,
192
406940
R223
468330
R241
435630
R239,
242
435820
R20
402160
R183
467630
R248
402200
R22,
26,
43,
45
467490
R6,
16,
32,
40
468120
R246
468030
R237,
240
467420
R238
402260
R218,
222,
224
437550
R185,
187, 189,
191
468000
R235,
243
467560
R2,
7,
12,
18,
28,
34,36,
42
617100
R247
617110
R3,
13,
29,
37
621100
R4,
14,
30,
38
R54,
57,
66.
69
R48,
58,
72,
80,
194,
196,198,
200
R67,
70,
88,
90
R53,
63,
77,
85
R193,
195, 197,
199
R49,
56,
59,
65,
73,
79,
81,
87
R50,
60,
74,
82
R51,
61,
75,
83
RA1
R99,
102, 111, 114, 143,
146,155,
158
R93,
103, 117, 125, 137,
147,
161,169,
202,204,
206,208,210,212,
214,
216
R112,
115, 133, 135, 156,
159, 177,
179
R98,
108, 122, 130,
142,
152,
166,
174
R201,
203, 205, 207,
209,
211,
213,
215
R94,
101, 104,
110,
118,
124, 126,
132,
138,
145,
148, 154,
162,
168, 170,
176
R95,
105,
119, 127,
139,
149,163,
171
R96,
106,
120, 128, 140,
150,
164,
172

Replaceable
Parts
List
(cont'd.)
EG&G
ORTEC
Item
No.
All
Models
476-8
&
476-16
476-16
Only
4.64K
1%
1/8W
MF
T2
468020
R9,
17.
33,
41
R55,
64,
78,
86
R100,
109,
123, 131, 144,
153, 167,
175
5.1K
5%
1/4W
CC
402390
R47,
184,
217,
R92
220,
221,
228
6.81
K
1%
1/8W
MF
T2
467680
R19
7.5K
1%
1/8W
MF
T2
468230
R5,
15,
31,
39
R52,
62,
76,
84
R97,
107, 121,
129, 141,
151, 165,
173
10K
5%
1/4W
CC
402450
R219
15K
5%
1/4W
CC
402480
R181
51K
5%
1/4W
CC
402800
R182
75K
1%
1/8W
MFT2
451710
R233
100K
5%
1/4W
CC
402570
R23,
25,
44,
46
R68,
71,
89,
91
R113,
116, 134, 136,
157,
160, 178,
180
147K
1%
1/8W
MF
T2
617070
R225,
227
Table of contents
Popular Multiplexer manuals by other brands
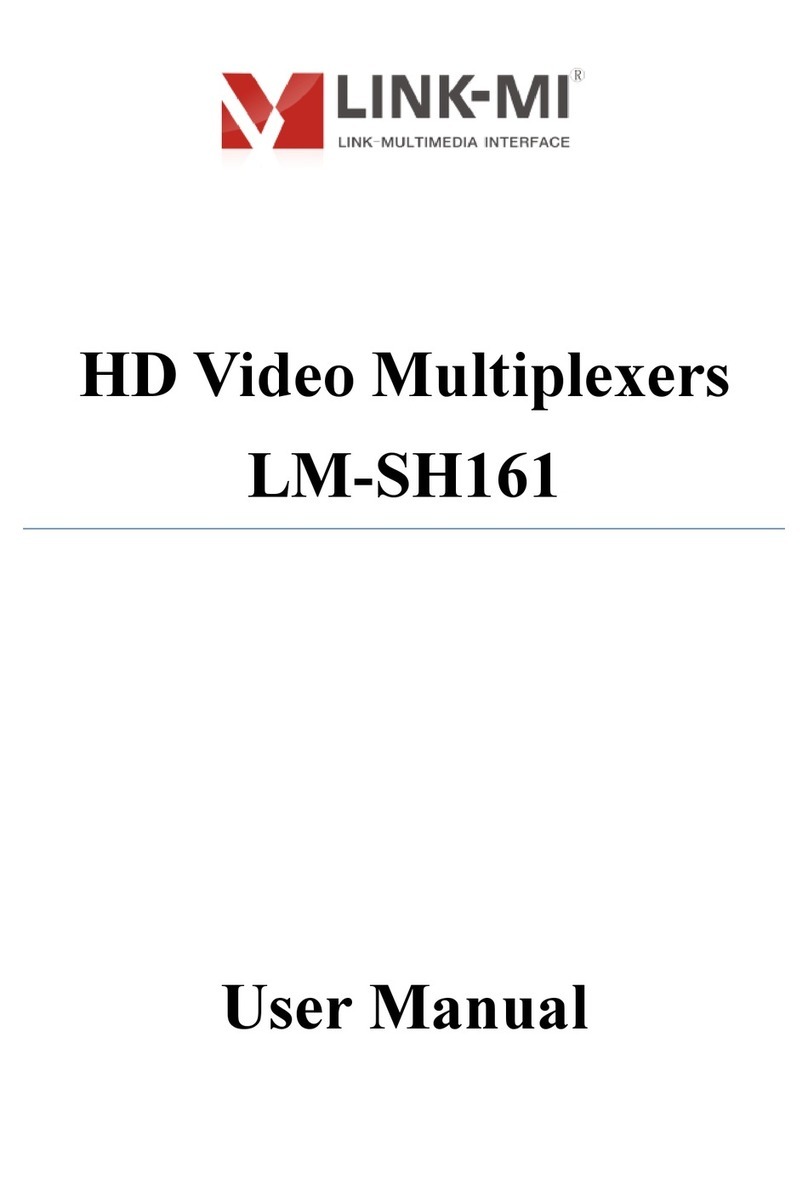
LINK-MI
LINK-MI LM-SH161 user manual
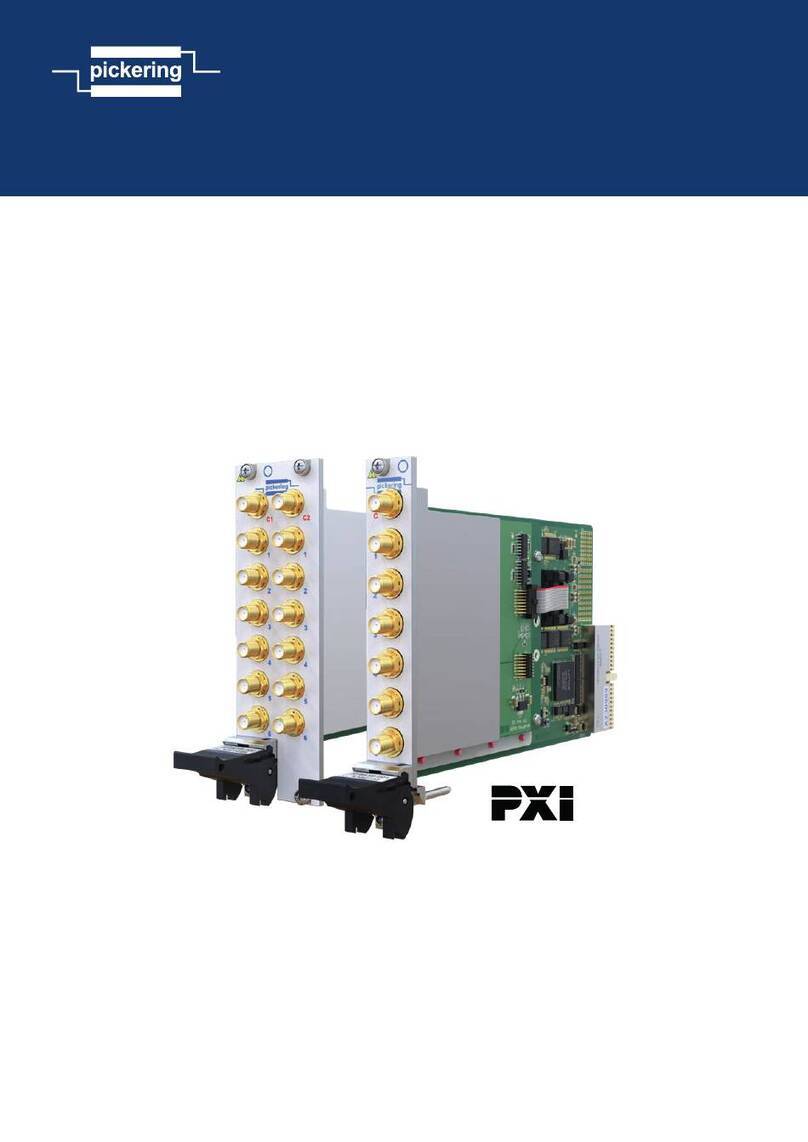
Pickering
Pickering 40-881B-001 user manual

Comnet
Comnet FTA2C1M1 Installation and operation manual
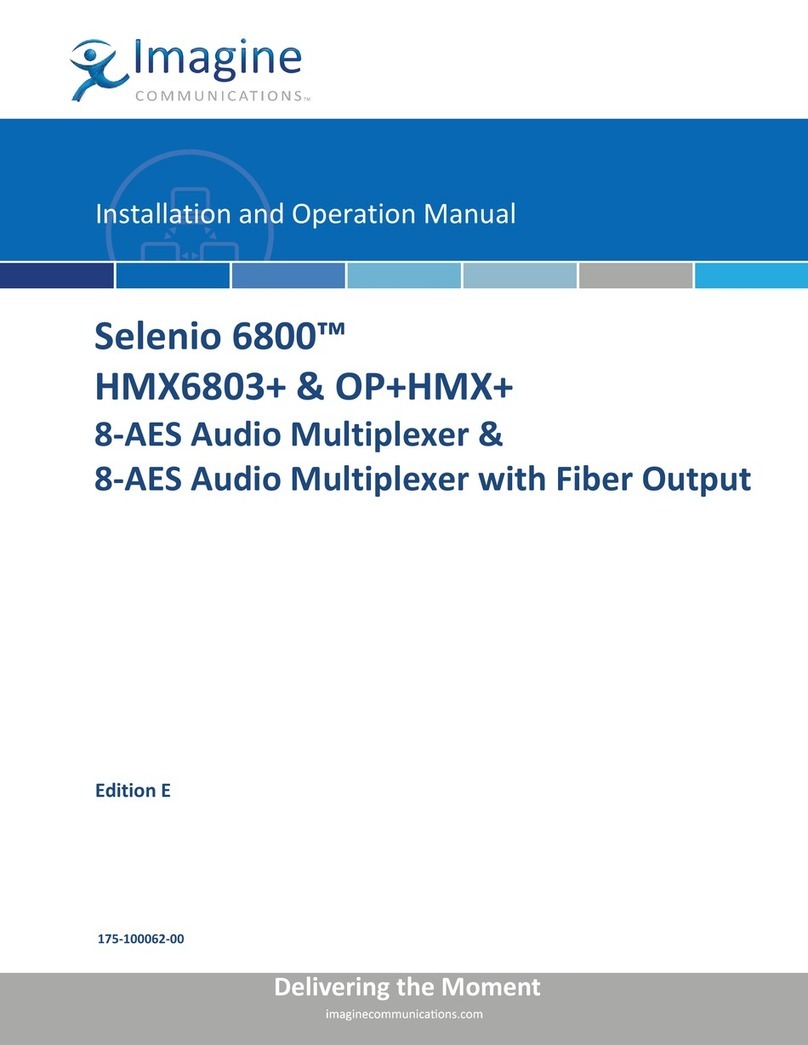
Imagine communications
Imagine communications HMX6803 Plus Installation and operation manual
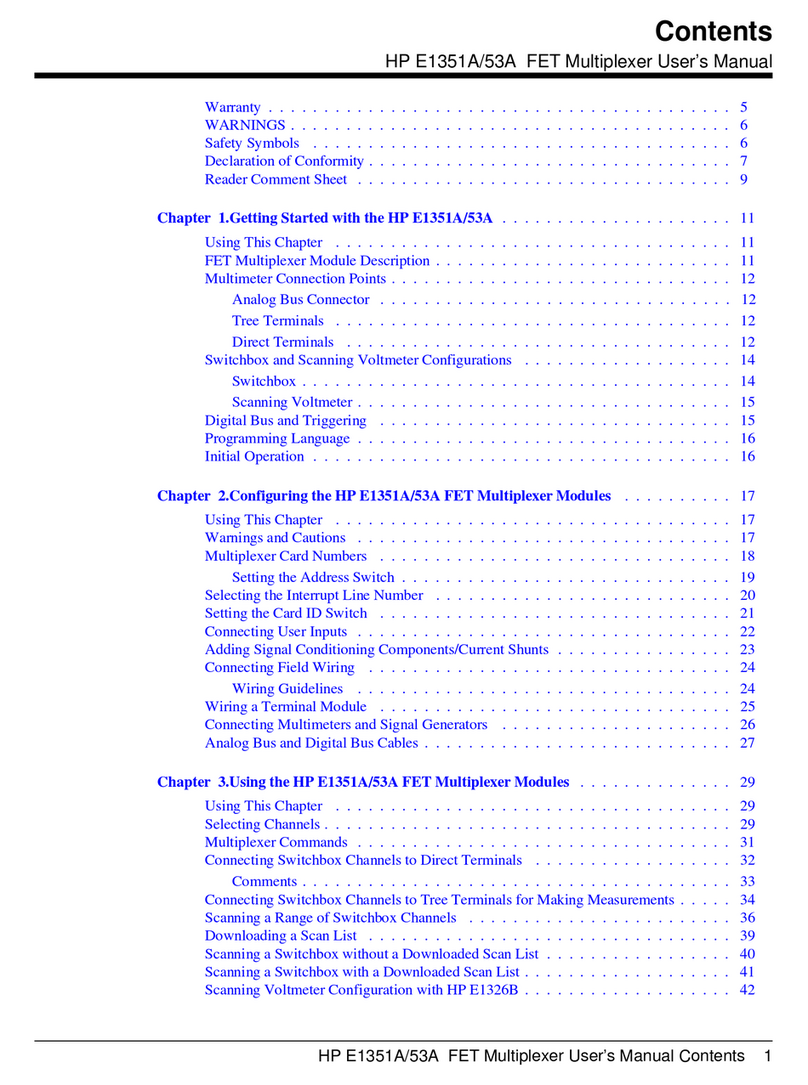
HP
HP E1351A user manual
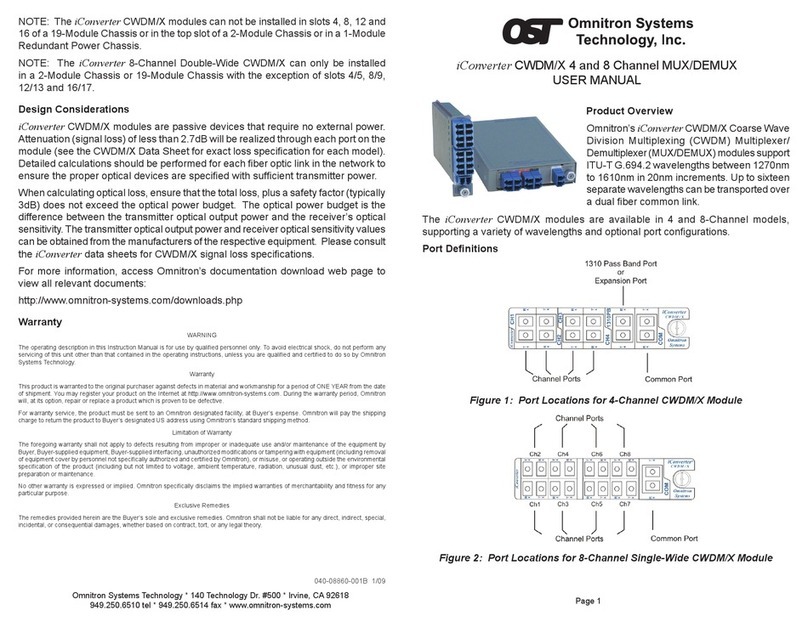
Omnitron Systems Technology
Omnitron Systems Technology iConverter CWDM/X user manual