Elgar SmartWave SW5250A User manual

SmartWave™
Switching
Amplifier
Operation Manual
This manual covers models:
SW5250A
SW3500A
SW1750A
ELGAR ELECTRONICS CORPORATION
9250 Brown Deer Road
San Diego, CA 92121-2294
1-800-733-5427
Tel: (858) 450-0085
Fax: (858) 458-0267
www.elgar.com
©2002 by Elgar Electronics Corporation
This document contains information proprietary to Elgar Electronics Corporation. The information contained herein is
not to be duplicated or transferred in any manner without prior written permission from Elgar Electronics Corporation.
Jul
y
19, 2002 Document No. M162001-01 Rev F

.

ELGAR ONE–YEAR WARRANTY
Elgar Electronics Corporation (hereinafter referred to as Elgar) warrants its products to be free from defects
in material and workmanship. This product warranty is effective for one year from the date of shipment to
the original purchaser. Liability of Elgar under this warranty shall exist provided that:
• the Buyer exposes the product to normal use and service and provides normal maintenance on the
product;
• Elgar is promptly notified of defects by the Buyer and that notification occurs within the warranty period;
• the Buyer receives a Return Material Authorization (RMA) number from Elgar’s Customer
Service Department prior to the return of the product to Elgar for repair, phone 800-73-ELGAR
(800-733-5427), ext. 2295;
• the Buyer returns the defective product in the original, or equivalent, shipping container;
• if, upon examination of such product by Elgar it is disclosed that, in fact, a defect in materials and/or
workmanship does exist, that the defect in the product was not caused by improper conditions, misuse, or
negligence; and,
• that Elgar markings and nameplates have not been altered or removed and the equipment has not been
repaired or modified by anyone other than Elgar authorized personnel.
This warranty is exclusive and in lieu of all other warranties, expressed or implied, including, but not limited
to, implied warranties of merchantability and fitness of the product to a particular purpose. Elgar, its agents,
or representatives, shall in no circumstance be liable for any direct, indirect, special, penal, or consequential
loss or damage of any nature resulting from the malfunction of the product. Remedies under this warranty
are expressly limited to repair or replacement of the product.
CONDITIONS OF WARRANTY
• To return a defective product, contact an Elgar representative or the Elgar factory for an RMA number.
Unauthorized returns will not be accepted and will be returned at the shipper’s expense.
• For Elgar products found to be defective within thirty days of receipt by the original purchaser, Elgar will
absorb all ground freight charges for the repair. Products found defective within the warranty period, but
beyond the initial thirty-day period, should be returned prepaid to Elgar for repair.
• Normal warranty service is performed by Elgar during the weekday hours of 7:30 am to 4:30 pm Pacific
time. Warranty repair work requested to be accomplished outside of normal working hours will be subject
to Elgar non-warranty service rates.
• Warranty field service is available on an emergency basis. Travel expenses (travel time, per diem expense,
and related air fare) are the responsibility of the Buyer. A Buyer purchase order is required by Elgar prior to
scheduling.
• A product found, upon inspection by Elgar, to be in specification is subject to an inspection fee and
applicable freight charges.
• Equipment purchased in the United States carries only a United States warranty for which repair must be
accomplished at the Elgar factory.
i

Committed to Quality...Striving for Excellence
ii

This page intentionally left blank.
iii

SAFETY NOTICE
Before applying power to the system, verify that the SW Series unit is configured properly for the user’s
particular application.
WARNING!
Hazardous voltages in excess of 280 VRMS, 600V peak may be present when
covers are removed. Qualified personnel must use extreme caution when
servicing this equipment. Circuit boards, test points, and output voltages
may be floating above (below) chassis ground.
Installation and service must be performed by qualified personnel who are aware of dealing with attendant
hazards. This includes such simple tasks as fuse verification.
Ensure that the AC power line ground is connected properly to the SW Series unit input connector
or chassis. Similarly, other power ground lines including those to application and maintenance
equipment must be grounded properly for both personnel and equipment safety.
Always ensure that facility AC input power is de-energized prior to connecting or disconnecting the
input/output power cables.
During normal operation, the operator does not have access to hazardous voltages within the
chassis. However, depending on the user’s application configuration, HIGH VOLTAGES
HAZARDOUS TO HUMAN SAFETY may be generated normally on the output terminals.
Ensure that the output power lines are labeled properly as to the safety hazards and that any
inadvertent contact with hazardous voltages is eliminated. To guard against risk of electrical shock during
open cover checks, do not touch any portion of the electrical circuits. Even when the power is off, capacitors
can retain an electrical charge. Use safety glasses during open cover checks to avoid personal injury by any
sudden failure of a component.
Due to filtering, the unit has high leakage current to the chassis. Therefore, it is essential to operate this unit
with a safety ground.
Some circuits are live even with the front panel switch turned off. Service, fuse verification, and
connection of wiring to the chassis must be accomplished at least five minutes after power has been
removed via external means; all circuits and/or terminals to be touched must be safety grounded to
the chassis.
After the unit has been operating for some time, the metal near the rear of the unit may be hot enough to
cause injury. Let the unit cool before handling.
Qualified service personnel need to be aware that some heat sinks are not at ground, but at high potential.
CAUTION!
380V 3-phase input power systems (4–wire) must have a neutral connection.
The neutral must not be switched. Apply neutral before phase voltage or
serious damage to the equipment may result.
iv

For safe operation, it is required that output power neutral be connected to chassis ground. The SW system
is shipped with a ground wire between power neutral and chassis ground.
These operating instructions form an integral part of the equipment and must be available to the operating
personnel at all times. All the safety instructions and advice notes are to be followed.
Neither Elgar, San Diego, California, USA, nor any of the subsidiary sales organizations can accept any
responsibility for personal, material or consequential injury, loss or damage that results from improper use of
the equipment and accessories.
SAFETY SYMBOLS
CAUTION
Risk of Electrical Shock CAUTION
Refer to Accompan
y
in
g
Documents
Off (Supply)
Standby (Supply)
On (Supply)
Protective Conductor Terminal
Fuse
Direct Current (DC)
Alternating
Three–Phase
Earth (Ground) Terminal
Chassis Ground
Current (AC)
Alternating Current
v


CONTENTS
SECTION 1 GENERAL DESCRIPTION
1.1 Introduction.................................................................................................... 1-1
1.2 Input Specifications ....................................................................................... 1-3
1.3 Output Specifications: Normal Operation Mode............................................. 1-3
1.4 Waveform Specifications............................................................................... 1-5
1.5 Measurements (Optional).............................................................................. 1-5
1.5.1 Parameters Measured....................................................................... 1-5
1.5.2 Measurement Capabilities and Accuracies ....................................... 1-6
1.6 Protection and Safety .................................................................................... 1-9
1.7 Agency Requirements ................................................................................... 1-9
1.8 Physical Specifications (All Models) ............................................................ 1-10
1.9 Environmental Data..................................................................................... 1-10
1.10 Other Standard Features............................................................................. 1-10
1.11 Options........................................................................................................ 1-12
1.12 Glossary of Technical Terms....................................................................... 1-13
1.12.1 RMS Servo...................................................................................... 1-13
1.12.2 Servo Boost..................................................................................... 1-13
1.12.3 X-Load............................................................................................. 1-14
SECTION 2 INSTALLATION
2.1 Introduction.................................................................................................... 2-1
2.2 Unpacking...................................................................................................... 2-1
Operation Manual v

Contents SW 5250A•SW 3500A•SW 1750A
2.3 Pre-installation Inspection..............................................................................2-2
2.4 Installation......................................................................................................2-2
2.5 Air Intake and Exhaust...................................................................................2-2
2.6 Installation/Dimensional Drawing ...................................................................2-3
2.7 Input/Output Connectors................................................................................2-6
2.7.1 BNC Connectors................................................................................2-7
2.7.2 EXT IN (External Input)......................................................................2-7
2.7.3 DFI (Direct Fault Indicator) ................................................................2-8
2.7.4 IEEE 488.2.........................................................................................2-9
2.7.5 Slave Connector................................................................................2-9
2.7.6 Grounding........................................................................................2-10
2.8 Input Power Requirements...........................................................................2-10
2.8.1 187 to 264 VRMS L–L 3-Phase Operation (3-Wire USA) ................2-12
2.8.2 342 to 457 VRMS L–L 3-Phase Operation (4-Wire INTL)................2-12
2.8.3 Single-Phase Input Connections......................................................2-12
2.9 Output Connections to the Load...................................................................2-13
2.9.1 SW 5250A Output Connections.......................................................2-13
2.9.2 SW 3500A and SW 1750A Output Connections..............................2-15
2.9.3 Wiring of Unit...................................................................................2-15
2.10 Wire Gauge Selection ..................................................................................2-15
SECTION 3 OPERATION
3.1 Introduction ....................................................................................................3-1
3.2 Front Panel Controls ......................................................................................3-1
3.3 Menus ............................................................................................................3-3
3.3.1 MAIN MENU......................................................................................3-4
3.3.2 PROGRAM Menu..............................................................................3-5
3.3.3 MEASURE Menu...............................................................................3-8
3.3.4 WAVEFORM Menu............................................................................3-9
3.3.5 SEQUENCE Menu...........................................................................3-15
3.3.6 INSTR (Instrument) Menu................................................................3-23
3.3.7 SYSTEM Menu................................................................................3-24
vi Operation Manual

SW 5250A•SW 3500A•SW 1750A Contents
3.4 Front Panel Programming Conventions....................................................... 3-33
3.5 Front Panel Programming Exercises........................................................... 3-34
3.5.1 Current Inrush Example .................................................................. 3-34
3.5.2 Voltage Spike Example................................................................... 3-38
3.5.3 Voltage Dropout Example ............................................................... 3-42
3.6 SCPI Specification....................................................................................... 3-45
SECTION 4 STANDARD WAVEFORMS
LIST OF TABLES
Table 2–1 Recommended Mounting Slide.................................................................. 2-3
Table 2–2 SW Input/Output Connectors (see Figure 2–3).......................................... 2-6
Table 2–3 EXT IN Connector Pinout........................................................................... 2-7
Table 2–4 DFI Connector Pinout................................................................................. 2-8
Table 2–5 IEEE 488.2 Connector Pinout .................................................................... 2-9
Table 2–6 Slave Connector Pinout ............................................................................. 2-9
Table 2–7 Input Currents for 3-Phase Input Power................................................... 2-11
Table 2–8 Single-Phase Input Configurations........................................................... 2-11
Table 2–9 Recommended Wire Gauge Selection Guide........................................... 2-16
Table 3–1 Sequence Execute Menu.......................................................................... 3-22
Table 3–2 SELF-TEST Results Definitions............................................................... 3-25
Table 3–3 System External Menu............................................................................. 3-28
Table 3–4 Fault Register Bit Definitions.................................................................... 3-29
Table 3–5 Fault Description and Action (FR1).......................................................... 3-30
Table 3–6 Fault Description and Action (FR2).......................................................... 3-31
Table 3–7 Fault Description and Action (FR3).......................................................... 3-31
Operation Manual vii

Contents SW 5250A•SW 3500A•SW 1750A
LIST OF FIGURES
Figure 1–1 Elgar Model SW 5250A AC Power Source (Rack Mount Version) ...........1-1
Figure 2–1 Mounting Dimensions, SmartWave Front View .........................................2-3
Figure 2–2 Mounting Dimensions, SmartWave Top and Side Views...........................2-4
Figure 2–3 SmartWave Rear Panel.............................................................................2-5
Figure 2–4 Parallel Connections................................................................................2-14
Figure 2–5 Sense Lead Connections for 3-Phase Output .........................................2-14
Figure 3–1 Front Panel Controls (SW 5250A).............................................................3-1
viii Operation Manual

SECTION 1
1.1
GENERAL DESCRIPTION
Introduction
The Elgar SmartWaveTM Models SW 5250A, SW 3500A, and SW 1750A use trans-
formerless, direct coupled amplifiers and a true arbitrary waveform generator based
controller. This technology allows you to create, edit and generate complex waveforms
with high DC content for critical ATE and power line disturbance simulation testing.
The SmartWave can create complex waveforms with high DC content for simulating real
world power irregularities, including phase controlled sub-cycle or multi-cycle dropouts,
spikes, sags, surges, frequency excursions, plus frequency and voltage ramps
(sweeps). The unit can also generate clipped waveforms, harmonic distortion, high
current inrush, and other complex waveshapes.
Figure 1–1 Elgar Model SW 5250A AC Power Source (Rack Mount Version)
Operation Manual 1-1

General Description SW 5250A•SW 3500A•SW 1750A
1-2 Operation Manual
The SmartWave model numbers are identified below:
SW5250 A–1–3–2–XXX
Power Options:
5250
3500
1750
Chassis Description:
A = Standard High Impedance
AE = Standard IEC Low Impedance
M, ME, S, SE = N/A
Power Conditioning Options:
1 = Rectifier USA
2 = Rectifier International
3 = PFC USA
4 = PFC International
5, 6 = N/A
Controller Options:
1 = Manual
2 = GPIB
3 = Arbitrary GPIB
Test and Measurement Options:
1 = No T&M
2 = Standard T&M
Non-Standard Options:
Blank = None
Programming is accomplished at the front panel or with a personal computer (PC) using
optional software. A GPIB card in the computer is also required.
A library of 50 factory-supplied waveshapes is provided in Flash Memory. Non-volatile
memory storage is available for an additional 50 user-created waveshapes.
Waveshapes from the libraries can be assigned amplitude and frequency parameters
and be stored as setups in non-volatile memory for immediate user recall. In addition,
you can create up to 1000 timed segments and link them together to form sequences
(transient programs).
The backlit graphics LCD display allows quick confirmation of waveforms when created
or edited from the front panel. Front panel BNCs provide waveform reference outputs
for oscilloscope viewing. The front panel also includes a keypad, a rotary knob, and
Help screens.

SW 5250A•SW 3500A•SW 1750A General Description
Operation Manual 1-3
The SmartWave sources are true DC as well as AC power supplies. Up to 312 VRMS
are available in AC or AC+DC modes. Multi-phase models can be switched to single or
three-phased operation via the front panel or the GPIB.
A wide frequency range of DC or 40 Hz to 5 kHz is available for a broad array of
applications. Utilizing the latest in AC switch mode technology, the SmartWave has
less than -60 dB of noise and ripple with total harmonic distortion (THD) of <0.5% to 500
Hz. A crest factor of 4.0 provides high peak-to-RMS current capability. An optional
power factor correction (PFC) of .99 is also available.
1.2
1.3
Input Specifications
Input Power Ranges: Factory configured 187 to 264 VRMS, 3φL-L (3 wire),
or 342 to 457 VRMS, 3φL-L (4 wire). A chassis ground is also required for safety.
Input Power Factor: .6 with USA rectifier; .35 with INTL rectifier;
.99 with input PFC option.
Input Frequency Range: 47 to 63 Hz (47 to 440 Hz for PFC input only)
Efficiency: 70%, minimum, at full load.
Ride Through: 3 msec, minimum; 10 msec, minimum, with PFC option.
Input Current: Maximum currents are provided in Table 2–7 and Table 2–8.
Initial Turn-on Current Surge: Limited to less than peak value listed in
Table 2–7 and Table 2–8.
Output Specifications: Normal Operation Mode
Calibration Interval:1 year.
Power Factor of Load: 0 lagging to 0 leading.
AC or DC Output Voltage: 0 to 156 VRMS L-N range 0; 0 to 312 VRMS L-N range 1.
Output Current Per Phase: 13A at 135V in 156V range; 6.5A at 270V in 312V range
(1750 VA maximum).
Crest Factor: 4.0 (peak output current to RMS output current).
Output Frequency: DC, or 40 Hz to 5 kHz.
Output Power: 1750 VA, maximum, per phase.

General Description SW 5250A•SW 3500A•SW 1750A
1-4 Operation Manual
Total Harmonic Distortion (Full Linear Load or No Load): 0.25% maximum, 40 to
100 Hz; 0.5% maximum to 500 Hz; and 1% maximum to 1 kHz plus 1%/kHz to 5 kHz.
AC Noise Level: >60 dB RMS below full output (sine wave, 40 to 500 Hz).
Amplitude Stability With Remote Sense: ±0.1% of full scale over 24 hours at
constant line, load and temperature.
Load Regulation: ±0.025% of full scale voltage for a full resistive load to no load;
above 1 kHz, add ±0.015%/kHz.
Line Regulation (DC, or 40 Hz to 5 kHz): ±0.025% of full scale for a ±10% input line
change.
Voltage Accuracy: ±0.1% of range. Above 1 kHz, add 0.2%/kHz. Add ±0.1% of full
scale for "AC PLUS DC" mode. Valid for 5 to 156 VRMS and 10 to 312 VRMS at 25°C
(77°F), sense leads connected. Temperature coefficient less than 50 ppm/°C.
Voltage Resolution: 0.05% of full scale.
Frequency Resolution: 0.01 Hz: 40 to 99.99 Hz
0.05 Hz: 100 to 999.9 Hz
0.5 Hz: 1000 to 5000 Hz
Frequency Accuracy: ±0.01% at 25°C ±0.001%/°C.
Phase Accuracy, Phase-to-Phase Balanced Linear Resistive Load:
±1°, 40 Hz to 1 kHz, plus ±1°/kHz above 1 kHz.
Phase Angle Resolution: 0.1°.
Remote Output Voltage Sense: 5 VRMS total lead drop, maximum.
Output Impedance: 5250 parallel mode, 312V range - meets requirements of
IEC-1000-3-2, Annex A, Supply Source. Valid for equipment classes A, B, C, and D.

SW 5250A•SW 3500A•SW 1750A General Description
Operation Manual 1-5
1.4
1.5
1.5.1
Waveform Specifications
Waveshape Libraries:50 factory-supplied in flash memory; storage available for up to
50 user created in non-volatile RAM.
User Created Setups:A total of 100 steady-state waveforms, consisting of parameters
such as waveshapes from the libraries plus amplitude, frequency, phase angle and
current limit.
Sequencing/Transient Programs:1000 user-created segments stored in non-volatile
RAM up to 100 segments per sequence. Segments include wave-shape, amplitude,
frequency, phase angle, time (from 1 msec to 7 days), and number of cycles.
MIL-STD-704 Transients: Factory-supplied sequencing program.
Measurements (Optional)
Parameters Measured
• 1- to 3-Phase to Neutral RMS Output Voltages
• 1- to 3-Phase to Phase Voltages are Calculated
• 1- to 3-Phase RMS Output Currents
• 1- to 3-Phase Peak Current
• Output Frequency
• 1- to 3-Phase Power
• 1- to 3-Phase VA
• Power Factor of Load Calculated from 1 or 3 Phases
• Output Phase B and C Relative to Phase A

General Description SW 5250A•SW 3500A•SW 1750A
1-6 Operation Manual
1.5.2 Measurement Capabilities and Accuracies
1.5.2.1 Measurement Capability
4½ Digit Analog to Digital Measurement System
Temperature Range for Specified Accuracy:25°C ±5°C.
Operating Temperature Range:0°C to 45°C (32°F to 113°F).
1.5.2.2 Phase to Neutral RMS Voltage Measurement
Valid for phases A, B and C (use phase A for Parallel Mode).
Range:0V to 350.0V, plus sign bit for DC mode.
Accuracy:±0.3% of range, DC or 47 Hz to 1 kHz;
±0.5% of range, 40 to 47 Hz and for 1 kHz to 5 kHz.
Temperature Coefficient: ±200 ppm/°C outside specified range.
1.5.2.3 Phase to Phase RMS Voltage Calculation
Calculated from Phase to Neutral voltages and phases.
Range: 0V to 700V.
Accuracy and Temperature Coefficient: Same as for the Phase to Neutral voltage
(see paragraph 1.5.2.2 above).
1.5.2.4 RMS Current Measurement
Valid for phases A, B, and C (use phase A for Parallel Mode).
Range 1:0A to 7.5A, plus sign bit for DC mode; 3-phase mode, 312V range.
Range 2:0A to 15A, plus sign bit for DC mode; 3-phase mode, 156V range.
Range 3:0A to 22.5A, plus sign bit for DC mode; parallel mode, 312V range.
Range 4:0A to 45A, plus sign bit for DC mode; parallel mode, 156V range.
Accuracy:±1.0% of range, DC or 40 Hz to 500 Hz; add ±1.5%/kHz above 500 Hz.
Accuracies are specified for a maximum crest factor of 4.0.
Temperature Coefficient:±300 ppm/°C outside specified range.

SW 5250A•SW 3500A•SW 1750A General Description
Operation Manual 1-7
1.5.2.5 Peak Current Measurement
Valid for phases A, B, and C (use phase A for Parallel Mode).
Range 1:0A to 28A; 3-phase mode, 312V range.
Range 2:0A to 56A; 3-phase mode, 156V range.
Range 3:0A to 84A; parallel mode, 312V range.
Range 4:0A to 168A; parallel mode, 156V range.
Accuracy:±5% of range, 40 to 500 Hz; add ±1%/kHz, 500 to 5 kHz.
Temperature Coefficient:±300 ppm/°C outside specified range.
1.5.2.6 Power Measurement
Valid for phases A, B, and C. Up to 3 phase total power and parallel mode
(use phase A for parallel mode).
Range 1:0 kW to 1.8 kW; 3-phase mode.
Range 2:0 kW to 5.6 kW; parallel mode and total 3-phase power.
Accuracy:±2.5% of range, DC or 40 to 500 Hz for crest factors <2.0.
Add ±1% for crest factors up to 4.0. Add ±1%/kHz above 500 Hz.
Temperature Coefficient: ±500 ppm/°C outside specified range.
1.5.2.7 VA Measurement
Valid for phases A, B, and C. Up to 3 phase total VA and parallel mode
(use phase A for parallel mode).
Range 1: 0 kW to 1.8 kVA; 3-phase mode.
Range 2: 0 kW to 5.6 kVA; parallel mode and total 3-phase power.
Accuracy: ±2.5% of range, DC or 40 to 500 Hz for crest factors <2.0.
Add ±1% for crest factors up to 4.0. Add ±1%/kHz above 500 Hz.
Temperature Coefficient: ±500 ppm/°C outside specified range.

General Description SW 5250A•SW 3500A•SW 1750A
1-8 Operation Manual
1.5.2.8 Power Factor Calculation
Valid for phases A, B, C, and TOTAL (use phase A for Parallel Mode).
The Power Factor is calculated from the Power and VA measurements. Phase powers
are measured then the total power is calculated; phase VAs are measured then the total
VA is calculated. Power is divided by VA; the result is the Power Factor.
Range: 0 to 1.00.
Accuracy: ±5% of range at full power, DC or 40 to 500 Hz for crest factors <2.0.
Add ±2% for crest factors up to 4.0. Add ±1%/kHz above 500 Hz.
Temperature Coefficient: ±500 ppm/°C outside specified range.
1.5.2.9 Frequency Measurement
Frequencies are calculated based on output zero crossing time measurements. To
minimize errors due to switching noise, a 1 µs filter is used to filter the output signal
before the zero comparator.
Resolution: Frequency is displayed to 5 figures maximum; the leading zeros are
blanked. Displayed resolution is 0.01 Hz.
Accuracy: ±0.5% of reading, at 10% to full output voltage, 0°C to 45°C
(32°F to 113°F).
1.5.2.10 Phase Measurement
Valid for phases A, B, and C relative to each other.
The phase of measured signals are calculated from timing measurements. The
reference is the negative to positive zero crossing of the internal reference (sync pulse)
signal. End of timing is the negative to positive crossing of the signals being measured
with respect to the internal reference. These timing measurements are used to calculate
the phase lead between the two phases being measured.
Resolution: ±1° (for outputs above 20 VRMS).
Accuracy: ±2°, 40 to 500 Hz; add ±2°/kHz above 500 Hz.
For sine wave, balanced resistive load, 10% to 100% of voltage measurement range.
All accuracies are specified for 0°C to 45°C (32°F to 113°F).
This manual suits for next models
2
Table of contents
Other Elgar Amplifier manuals
Popular Amplifier manuals by other brands
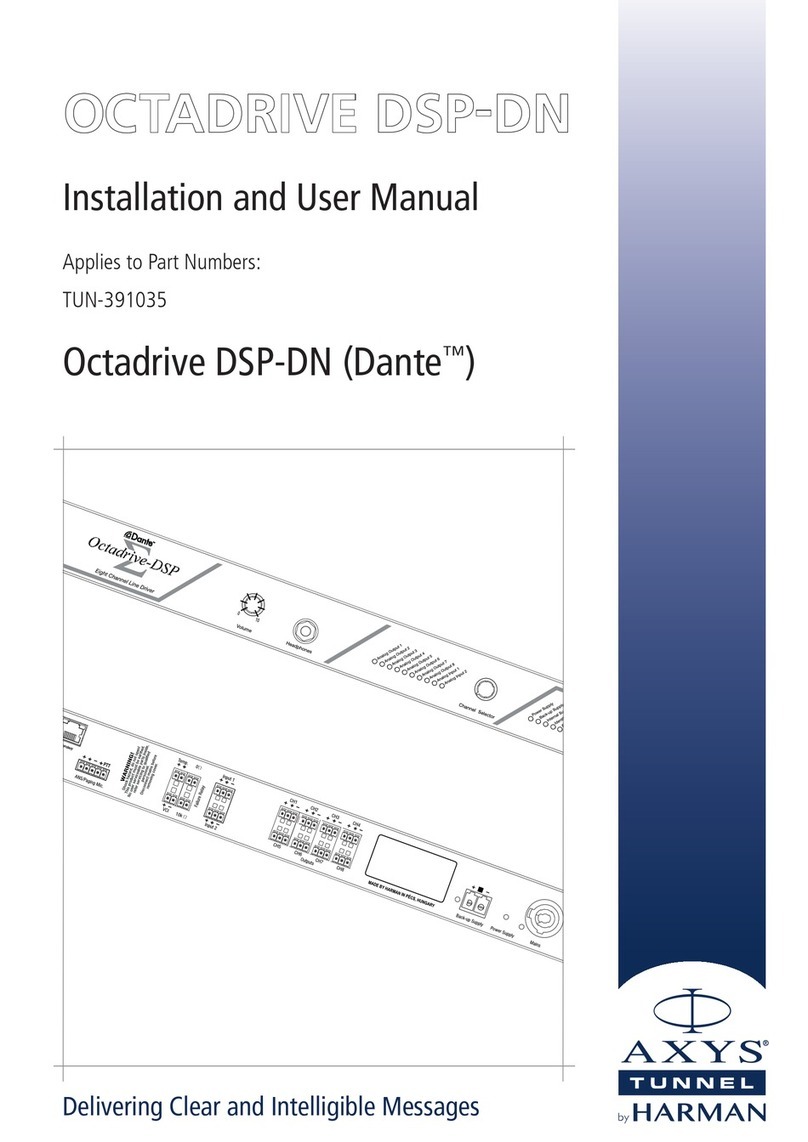
Harman
Harman AXYS Dante OCTADRIVE DSP-DN Installation and user manual
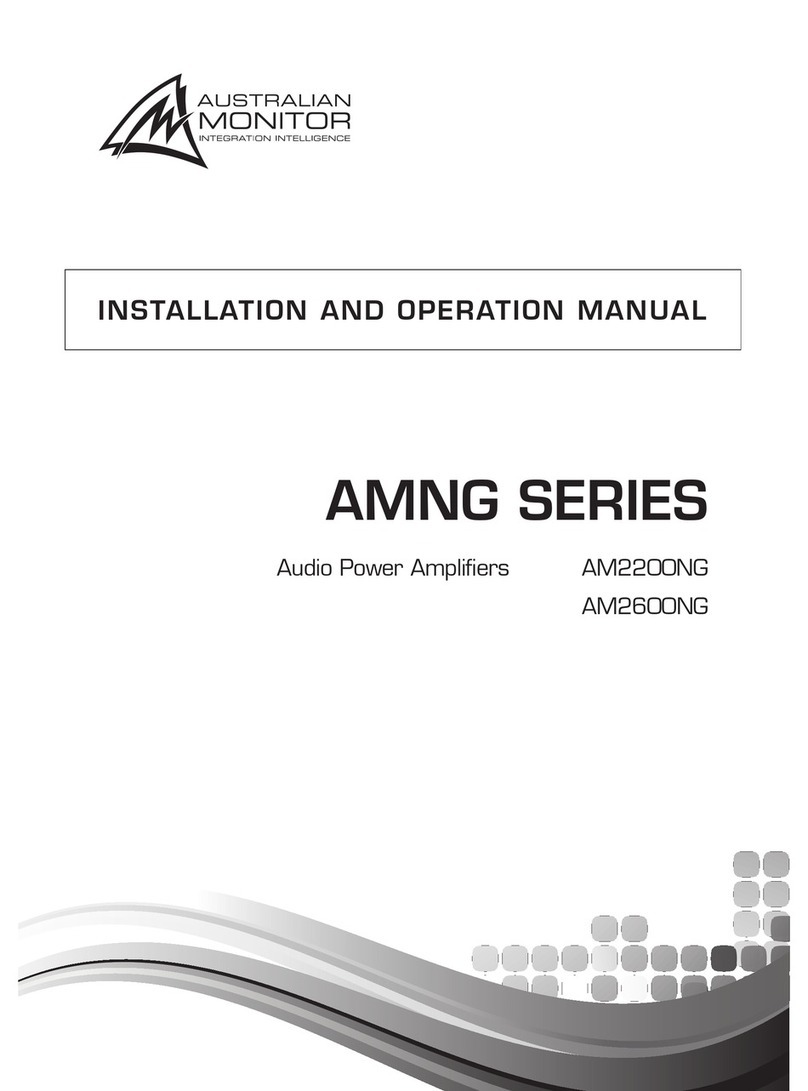
AUSTRALIAN MONITOR
AUSTRALIAN MONITOR AM2200NG Installation and operation manual

Ponovo
Ponovo PAV15000 user manual
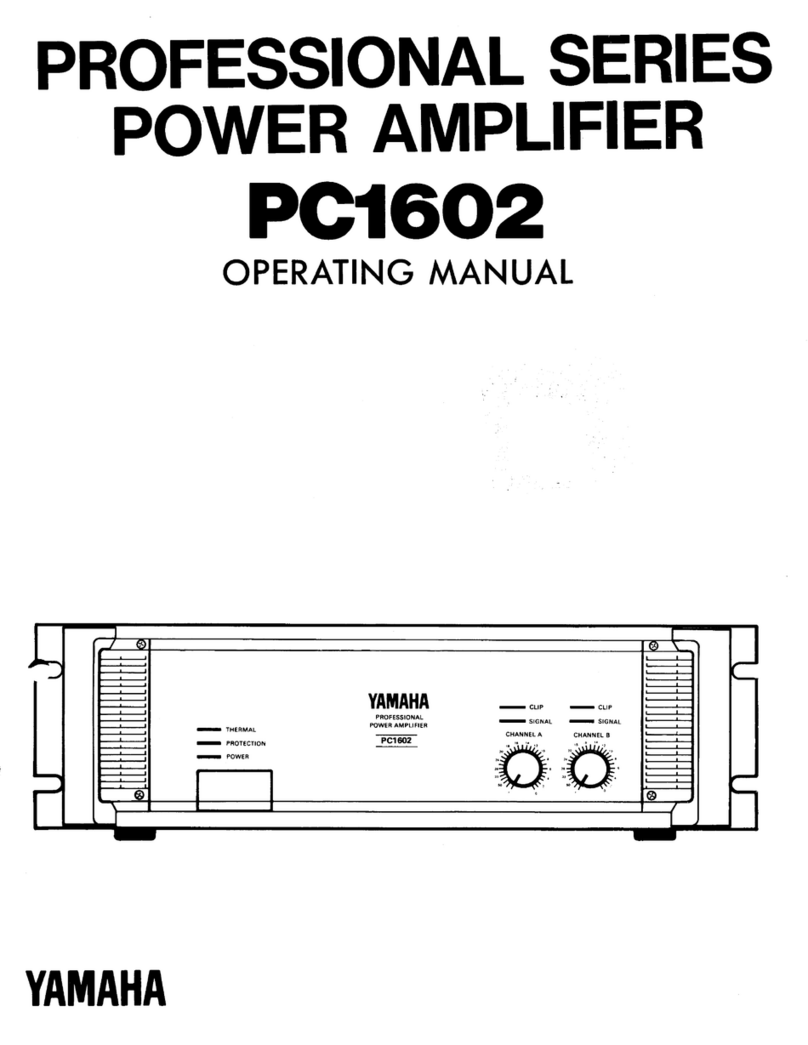
Yamaha
Yamaha PC1602 operating manual

Panasonic
Panasonic Ramsa WX-RP900 operating instructions
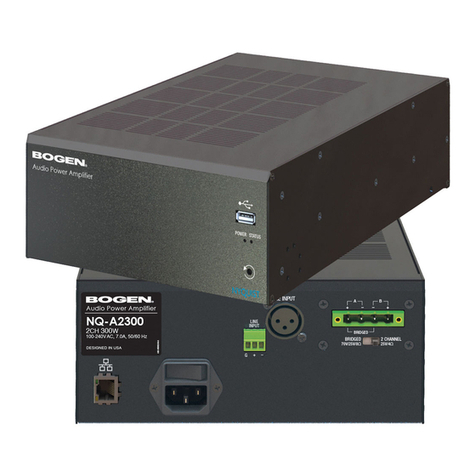
Bogen
Bogen NYQUIST NQ-A2300 Installation and use