EPI 7000 User manual

ELDRIDGE PRODUCTS, INC. Fax 831/648-7780
2700 Garden Road, Building A Telephone 831/648-7777
Monterey, California 93940 Toll Free 800/321-3569
Internet www.epiflow.com
GAS MASS FLOW MEASUREMENT & CONTROL INSTRUMENTATION
“We work as hard as our meters”
INSTRUCTION MANUAL
SERIES 7000, 7100, 7200
THERMAL MASS FLOW SWITCH
Doc. No. 80200401 Rev. C-ACR


Table of Contents
1.0 INTRODUCTION AND INSTALLATION...............................................................................................................................1
INTRODUCTION.............................................................................................................................................................................1
UNPACKINGYOUR INSTRUMENT............................................................................................................................................1
GETTINGACQUAINTED ..............................................................................................................................................................1
INSTALLATIONAND MOUNTINGINSTRUCTION ................................................................................................................1
SERIES7000 POWER REQUIREMENTS .....................................................................................................................................2
SIGNALINTERFACE......................................................................................................................................................................2
2.0 APPLICATION INFORMATION ..............................................................................................................................................3
INLINEFLOW SWITCH APPLICATION .....................................................................................................................................3
INSERTIONFLOW SWITCH APPLICATION.............................................................................................................................3
BALLVALVE RETRACTOROPERATION.................................................................................................................................4
3.0 THEORY AND OPERATION.....................................................................................................................................................5
SENSORTHEORY AND OPERATION.........................................................................................................................................5
FLOW SWITCH OPERATION........................................................................................................................................................5
4.0 CALIBRATION..............................................................................................................................................................................6
FACTORY CALIBRATION............................................................................................................................................................6
FIELD CALIBRATION....................................................................................................................................................................6
5.0 GENERAL INFORMATION.......................................................................................................................................................7
GENERALSPECIFICATIONS .......................................................................................................................................................7
SPECIFICATIONNOTICE..............................................................................................................................................................7
LIMITEDWARRANTY...................................................................................................................................................................7
LIMITEDACCEPTANCE ...............................................................................................................................................................8
SERVICEWORK..............................................................................................................................................................................8
STORAGE .........................................................................................................................................................................................8
6.0 APPENDIX (GUIDELINES AND PRODUCT DRAWINGS)................................................................................................9
PROBELOCATION TABLE........................................................................................................................................................ 10


80200401 Rev. C - ACR Page 1
1.0 INTRODUCTION AND INSTALLATION
INTRODUCTION
The EPI Series 7000 Thermal Mass Flow & Mass Velocity Switches are the net result from over a decade of flow
metering and design experience within the industry. Series 7000 products directly measure the gas molecular
rate of flow, correcting for temperature changes and being insensitive to pressure changes.
UNPACKING YOUR INSTRUMENT
Your Series 7000 thermal mass flow switch is a precision piece of electronic flow instrumentation. Although our
flow switches are rugged, they should be inspected upon delivery to assure that no damage has taken place
during transit. If upon inspection it is found that damage has occurred, notify the carrier immediately, and place
a claim for damaged goods. The shipping container or crate should be handled with care and carefully opened, to
avoid possible damage to the contents. After the container is opened the contents should be carefully removed
and the individual pieces checked against the packing list. Should a discrepancy present itself, contact the EPI
shipping department immediately. The last area of verification, will be to check that the equipment matches
your purchase order specifications. If it is found that a mismatch has taken place, contact the EPI sales
department to resolve any discrepancies.
GETTING ACQUAINTED
We thank you for specifying our Series 7000 thermal mass flow switches. As you know, thermal mass flow
switching devices have been around for many years and are known for their reliability, ease of use and, most
importantly, their direct adjustability.
Your Series 7000 product consists of two major components, the flow sensor and signal board. The sensor is the
heart of the system. It consists of a flow sensing element and temperature sensing element. Other components
are, bridge amplifier, relays and circuit board, transmitter enclosure and probe support piece or flow section.
These individual pieces are integrated into one package. The transmitter is powered by a user supplied DC
power source or by optional AC power.
INSTALLATION AND MOUNTING INSTRUCTION
Proper installation of the flow switch assembly is of great importance. It is important to install the flow switch at
a position where the gas is dry or above the dew point temperature. Installations which allow large droplets of
water to condense out and come in contact with the sensing element must be avoided.
Temperature limitations of the flow switch are listed in the specification section of this manual and show
acceptable limits for the gas temperature along with the environmental temperature limits which the
transmitter electronics may be subjected.
Avoid installations which are immediately downstream of bends, abrupt area increases or decreases, fans,
louvers, or other equipment installed in the line, etc.. These situations can cause non-uniform flow profiles and
swirl which can cause signal errors and false trip points. It is desirable to have as much straight run as possible
to achieve a uniform non-swirling flow profile within the flow conduit. Rule of thumb states that one should
provide a minimum of 10 diameters of straight run upstream and 5 diameters downstream. Although this is not
always possible, it is desirable. In the event of less straight run availability, the available length should be
divided into thirds with two thirds upstream and one third downstream. If installation is other than that stated
above, allow a wider error band when setting the relay trip threshold.

80200401 Rev. C - ACR Page 2
Plumbing in the Series 7000 flow switch is accomplished by one of the following two methods. For Inline style
flow switches, various end configurations are available and will determine the exact process of installation. The
installation will consist generally of plumbing the flow switch in series with the flow conduit by threading,
flanging, welding or (fitting in place with the use of tube fittings on sizes to one inch). The standard end
configuration is MNPT (male national pipe thread), threaded ends. Other end styles are optional.
Insertion style flow switches require the flow switch assembly be inserted through and perpendicular to the flow
conduit. The flow switch assembly is held in place by use of the proper size pipe nipple & coupling or bored
through tube fitting. The tube fitting is provided by the user or purchased as an option from Eldridge Products,
Inc. Installing the tube fitting consists of preparing the flow conduit to accept the fitting by first drilling a
clearance hole for the transmitter probe assembly, welding it in place, or threading it into the proper size 1/2
pipe coupling which has been welded to the flow conduit. Insertion style flow switches have a maximum pressure
stated in the "General Specifications" section of this manual. Caution should be exercised if considering applying
higher pressures, as each size is rated such that the maximum force applied to the transmitter is approximately
25 pounds to reduce the possibility of personal injury when servicing the flow switch. AT HIGHER PRESSURES
A HOLDING DEVICE MAY BE REQUIRED TO PREVENT THE FLOW SWITCH FROM BEING A
PROJECTILE WHEN REMOVING OR REPLACING THE FLOW SWITCH ASSEMBLY UNDER PRESSURE.
SERIES 7000 POWER REQUIREMENTS
Power requirements for the Series 7000 flow switches are 24 Volts DC, 5 Watts standard and 115 VAC 50/60 Hz
optional. For optional AC power a 6 foot power cord is provided and may be removed for permanently installed
conduit wiring. If conduit is used, it should be suitable for the application, electrically conductive and connected
within the enclosure to earth ground. Our recommendation on wire size is 18 Ga. stranded for all AC wiring.
Flow switch power requirements are met with the power provided by the user connection.
SIGNAL INTERFACE
Provided by the flow switch are 5 Amp @ 30 Volts DC or 120 Volts AC relay contact outputs. The contact outputs
are wired in the normally open position. If the normally closed configuration is desired, wiring may be altered
with onboard jumper connections. Our standard operation requires that the relay be energized under a fault
condition. Under "Fail Safe" operation the relay is energized closed under normal conditions and de-energized
under power failure or flow fault conditions.

80200401 Rev. C - ACR Page 3
2.0 APPLICATION INFORMATION
INLINE FLOW SWITCH APPLICATION
Inline refers to a method of installation for which the flow switch has been designed. This design allows the
process gas to flow through the flow switch assembly and across the heated sensor rather than the probe and
heated sensor being inserted into an existing flow section, pipe, duct, etc.. Inline mounting styles are available
through EPI in sizes from 1/8" pipe through 4" pipe and are provided with threaded NPT ends standard.
Optional end mounting styles may be specified, such as tube ends, tube end fittings, butt weld ends, flanged end
configurations etc. if required. Pipe sizes in excess of 4" require the Insertion mounting style discussed later.
Inline flow switches have the sensing element mounted in place within the flow section. The sensor should not
be removed as the accuracy of the flow signal will be affected. Should it become necessary to remove the sensing
element, the element should be replaced in the same alignment as it was originally positioned. The sensor is
somewhat resistant to dirt and particulate build up (and works well with mild build up). It may become
necessary to clean the sensor from time to time if mounted in extremely dirty environments.
Cleaning the sensor consists of shutting off the flow switch power supply, removing the sensor wires from the
printed wiring board (Note: damage will occur to the sensor if the power supply is not disabled first), removing
the conduit head assembly, backing off the tube fitting nut while holding the sensor in place and carefully
extracting the sensor assembly from the flow section.
The actual cleaning process consists of using a detergent or appropriate cleaning agent (which will not attack the
probe assembly materials of construction) suitable for removing the buildup present on the sensor. A soft brush
should be used to gently clean the sensor surface (Do not press very hard or clean too aggressively, as damage
may occur). After the residue removal is complete, the sensor may be rinsed in water or cleaning alcohol. Make
sure to dry the assembly immediately following the cleaning process. Reassembly consists of reversing the steps
listed above.
INSERTION FLOW SWITCH APPLICATION
Insertion refers to a method of installation process which the flow switch is designed. This design allows the flow
switch assembly to be inserted into the process gas flow section, duct or stack. Consequently, allowing the
process gas to flow across the sensor assembly, rather than the process gas flowing through a flow switch
assembly flow section as in the Inline style flow switch. The Insertion style flow switch probe assemblies may be
inserted into any suitable flow section, pipe, duct, etc.. Insertion styles are available through EPI in sizes from
3/8" tube through 1" tube and require a pipe connection or user supplied bored through tube fitting to mount
them in place. Tube fittings are optionally available from the factory.
Optional ball valve retractor assemblies may be specified to allow removal of the probe assembly and shutting off
process gas leaks at that location during maintenance intervals. Sizes are available in 3/8" through 1" to match
up with the sensor sizes.
Insertion style flow probes were designed to allow the sensing element to be mounted in place within a flow
section, conduit, duct, etc.. The sensor may be removed if calibration or cleaning become necessary. The sensor is
somewhat resistant to dirt and particulate build up and works well with mild build up. However, it may become
necessary to clean the sensor from time to time if mounted in extremely dirty environments.
Cleaning the sensor consists of shutting off the flow switch power supply and carefully removing the flow switch
assembly from the flow section, conduit, duct, etc., and cleaning the sensor.

80200401 Rev. C - ACR Page 4
The actual cleaning process consists of using a detergent or appropriate cleaning agent (which will not attack the
sensor assembly materials of construction) suitable for removing the buildup present on the sensor. A soft brush
should be used to gently clean the sensor surface (Do not press very hard or clean too aggressively, as damage
may occur). After the residue removal is complete, the sensor may be rinsed in water or cleaning alcohol. Be sure
to dry the assembly immediately following the cleaning process. Reassembly consists of reversing the steps noted
above.
BALL VALVE RETRACTOR OPERATION
Optional ball valve assemblies are available through EPI and allow removal of the Insertion style flow switch
assemblies for service, calibration, cleaning, etc., while providing a means by which the process gas may be
sealed off at that location, after probe assembly removal.
Installation requires fitting the flow section to which the Insertion probe assembly will be inserted with a
threaded half coupling of the proper size to accommodate the ball valve retractor supplied. In some instances,
this requires direct threading together (or with a reducing bushing) of the retractor assembly. In other cases, it
requires welding the half coupling in place and drilling a clearance hole through for the probe assembly. If the
flow section is under pressure, a hot tap drill rig may be required to get the job done.

80200401 Rev. C - ACR Page 5
3.0 THEORYAND OPERATION
SENSOR THEORY AND OPERATION
Series 7000 products utilize a rugged, cleanable, thermal mass flow sensor. These units consist of a sensor
assembly which is constructed of two RTD (Resistance Temperature Detectors) sensing elements. Materials of
construction are reference grade platinum, ceramic and glass (optional stainless steel sheath over the assembly
for corrosion or abrasion resistance). Two platinum resistance sensors are built up upon the ceramic substrate
with a thin glass coating over the assembly. The sensor assembly is large, rugged, insensitive to dirt buildup and
easily cleaned.
Operation is as follows: The temperature sensor constantly measures the ambient temperature of the gas and
maintains a reference resistance on one side of a Wheatstone bridge. The second sensor is forced through self
heating to a constant temperature above that of the gas stream and is controlled by the temperature sensor and
our forced null Wheatstone bridge amplifier. Our bridge is set up with precise resistance values to maintain the
overheat temperature and compensate for the temperature effects through our temperature compensation
techniques. As a result our sensor assembly is temperature compensated. Since thermal mass flow sensors are
relatively insensitive to pressure changes, pressure compensation is not required.
FLOW SWITCH OPERATION
Since the temperature changes are corrected for and pressure effects are virtually nonexistent, the heated sensor
becomes a mass flow sensor. Gas mass flow across the heated sensor is measured by the thermal heat transfer
(loss) of the sensor. As the gas velocity increases, more heat is transferred from the sensor to the gas stream. Gas
molecules absorb heat while passing the heated sensor surface and thus more power is required of the sensor's
drive circuit to maintain a constant sensor overheat temperature. This heat transfer is directly proportional to
the mass velocity of the gas (density x velocity). The power demand of flow sensor causes our bridge voltage to
change which we use as our nonlinear mass flow or mass velocity flow switch signal. This signal is compared to
on board, trip point reference signals and upon low or high flow, the appropriate output relay is tripped. The
sensor, bridge amplifier, enclosure, probe and flow conduit all form an integral flow switch assembly. Power is
supplied to the flow switch by the user.

80200401 Rev. C - ACR Page 6
4.0 CALIBRATION
FACTORY CALIBRATION
Factory calibration is a two step process. Our first step is to perform a temperature calibration of each flow
sensor. Once this calibration process has been performed, it need not be done again. Secondly, we may perform
an optional factory flow calibration of the flow switch. Our optional factory calibration provides the user with a
10 point look up table of circuit voltage vs. flow and trip point adjustment if known and desired. Although all
flow curves are similar, they are different enough to require individual calibrations be run for each flow switch to
yield the best accuracy.
Flow calibration is a process of comparing or verifying the meter under test against a meter of better accuracy
used as a calibration standard. EPI' flow calibrations are traceable to NIST through traceability of the
instrumentation and equipment used.
FIELD CALIBRATION
Field calibration may be performed on the flow switch by adjusting the threshold trip points to the desired level
while flowing gas at the acceptable rate. Set points may be High/High, Low/Low, High/Low, or Low/High based
on jumper position left & right (JL & LR), see table drawing 60400501. Relay contact K1 trip point is adjusted
with P1 (clockwise up on P1 & P2) and relay contact K2 trip point is adjusted with P2. The contact trip state is
determined by jumper JL & JR per the table in drawing 60400501. The trip point may be monitored with an
Ohm meter placed across the contact while adjusting the potentiometers or by a visual LED indication on board.
Under normal operation P1 is used for the low flow (may also be high) trip point adjustment of relay K1, while
P2 will adjust the high flow (may also be low) trip point of K2. Under “Fail Safe” operation JL & JR change
position. The relay under normal operation is at rest within the normally open contact in the open position,
however under “Fail Safe” operation the relay is energized and the normally open contact is in the closed
position. Our “Fail Safe” connection will give a contact output signal under power failure or flow fault conditions.
Our relay board also has individual time delay adjustments for each relay, P3 for K1 & P4 for K2. Factory set for
one second, P3 & P4 are turned fully counter clockwise. Full clockwise (25 turns) gives 30 second trip point time
delay with a one second reset.

80200401 Rev. C - ACR Page 7
5.0 GENERAL INFORMATION
GENERAL SPECIFICATIONS
Signal output Relay contact, high & low,
5 Amp @ 30 VDC or 120 VAC
Trip point accuracy +/- 1.0% of Set Point
Repeatability +/- 0.5% of Range
Sensor response time (Metal) 1 second
Signal response time Set to 1 second
Turn down ratio 100:1 minimum
Electronics temperature range 0-50°C (32-122°F)
Gas temperature range 0-200°C (32-392°F)
Gas temperature effect .01% /°C for gas
Pressure rating maximum:
Inline flow switches 500 PSI >500 special
Insertion O.D. .500 125 PSI >125 special
.750 55 PSI > 55 special
1.000 30 PSI > 30 special
Power requirements User supplied 24 VDC, @ 250mA Max.
120 VAC 50/60 Hz (optional)
Flow switch enclosure NEMA 4, Class 1, Div 1 Groups B, C and D
Wetted materials 316SS, ceramic, glass, epoxy
NIST traceable calibration Optional for Gas
Calibration Standard (Gas) 70 °F & 29.92" Hg
(Air = .075 lb./cubic foot)
SPECIFICATION NOTICE
Specifications contained herein are subject to change without notice. EPI cannot guarantee the applicability or
suitability of our products in all situations since it is impossible to anticipate or control every condition under
which our products and specifications may be used.
LIMITED WARRANTY
Eldridge Products, Inc. (EPI) warrants its products to be free from defects in materials and workmanship for one
year from the date of factory shipment. If there is a defect, the purchaser must notify EPI of the defect within the
warranty period. Upon receipt of the defective product, EPI will either repair or replace the defective product at
its sole option and at no cost to the purchaser. EPI MAKES NO OTHER WARRANTY, EXPRESS OR IMPLIED,
AS TO THE PRODUCTS. EPI MAKES NO WARRANTY THAT THE GOODS SOLD TO ANY PURCHASER

80200401 Rev. C - ACR Page 8
ARE FIT FOR ANY PARTICULAR PURPOSE. FURTHERMORE, EPI MAKES NO WARRANTY OF
MERCHANTABILITY WITH RESPECT TO ANY PRODUCTS SOLD TO ANY PURCHASERS. There are no
other warranties that extend beyond the description on any brochure or price quote.
LIMITED ACCEPTANCE
Acceptance of any offer is limited to its terms. Acceptances or confirmations that state additional or differing
terms from this price quote shall be operative as acceptances, but all additional or differing terms shall be
deemed material alterations within the meaning of Commercial Code Section 2207(2)(b), and notice of objection
to them pursuant to Commercial Code Section 2207(2)(c) is hereby given. The laws of the State of California
govern this contract and venue is Monterey County. Risk of loss passes F.O.B. EPI factory. Payment due in full
in US Dollars within credit terms granted from factory shipment. Additional fees shall include interest on
unpaid balances that are outstanding for more than granted credit terms, plus all collection costs and attorneys’
fees incurred in collecting any outstanding balance. Any and all additional or differing terms do not become part
of the contract between EPI and any purchaser.
The terms of any offer are expressly limited to the terms detailed in any product brochure or price quote. Any
modification to any of the terms of this offer must be in writing and must be signed by an officer of EPI.
SERVICE WORK
In the event that service work is required or calibration and recertification is required, call the factory and a
return authorization number (RA) will be issued for each job. All units sent in for service work shall include a
RA, work instructions and be shipped prepaid. On receipt of your flow instrumentation, we will inspect the
equipment and give a price quotation for service work to be performed, if not already given.
STORAGE
Equipment and instrumentation shall be stored in an environmentally controlled storage shelter or warehouse
when not in use. All openings shall be sealed off to prevent foreign materials from entering the instrumentation.

80200401 Rev. C - ACR Page 9
6.0 APPENDIX (Guidelines and Product Drawings)
The following pages include installation guidelines and technical/informational drawings related to the Series
7000 Family of thermal mass flow switches. Not all drawings will refer to your specific switch. Please be
especially careful when referencing the wiring diagrams.
INSERTION PROBE PLACEMENT
AND
EFFECTS OF REYNOLDS NUMBER IN CLOSED CONDUITS
Reynolds Number (RD) defines whether laminar flow (viscous effects) or turbulent flow (dynamic effects) are
causing the flow profile within the flow conduit. Laminar flow has a RD of <2000 with a parabolic flow profile,
while turbulent flow has a RD of >4000 with a more uniform (squared up) face velocity. The RD's between 2000
and 4000 are in the transition region allowing a change in profile from laminar to a turbulent face velocity
profile. Turbulent flow profile is not the same as turbulence or swirl within the flow conduit. Changing Reynolds
Numbers are caused by changing flow rates within the flow conduit.
Laminar flow may have a center velocity as high as twice the mean velocity. When an insertion style probe is
placed within the flow conduit, it must be placed at a point of average flow to obtain an accurate flow reading.
Determining a flow profile consists of traversing the flow conduit from wall to wall or as a minimum, performing
a half traverse if the flow profile is known to be symmetrical, with the insertion flow meter to determine the
insertion depth of average flow. After the position of average flow is known, the probe may be permanently
installed by locking in place with a compression fitting such as provided with our ball valve retractor assembly
or through the proper length pipe nipple and coupling provided by the user. There will be two positions of
average flow, one located on each side of center. The suggested placement is past center at the point of average
flow, if the probe length allows.
A well developed flow profile has at least 10 pipe diameters upstream and will typically have a pipe center
velocity of 20% above the average velocity. Conversely, the average velocity is approximately .243R from the
walls. To minimize or eliminate the effects of probe blockage error, the probe location should be toward the near
side, rather than the far side of the pipe.
Although the best method to locate the exact point of average velocity for your specific set of circumstances is to
profile or traverse your duct, the following guidelines serve as a good approximation.
Step 1A: Be sure that sensor orientation is correct. The upstream marking that is scribed on the probe must
be located correctly. (i.e.: It faces upstream)
Step 1B: Place the tip of the sensor protective window next to your pipe/duct entry fitting, touching the outer
pipe wall. Mark the probe shaft at a point even with the outer edge of the mounting hardware.
Step 2: Put a second mark on the probe, the distance indicated in the table below, from the first mark, which
agrees with your application.
Step 3: Insert the probe into the pipe/duct through your fitting until you reach this second mark. Lock the
probe into position, assuring that the flow direction is still properly aligned.

80200401 Rev. C - ACR Page 10
PROBE LOCATION TABLE
PIPE SIZE SCHEDULE 10S SCHEDULE 40S SCHEDULE 80S
2"
2 ½”
3”
3 ½”
4”
5”
6”
8”
10”
12”
1.121"
1.190”
1.266”
1.327”
1.388”
1.527”
1.656”
1.910”
2.181”
2.435”
1.153"
1.253”
1.339”
1.407”
1.476”
1.621”
1.767”
2.042”
2.332”
2.583”
1.204"
1.308”
1.402”
1.477”
1.552”
1.710”
1.882”
2.176”
2.435”
2.678”
Please note that the guidelines above take into account the location of the active part of the sensing element.
Our design of the sensor protective window is such, that the active part of the flow sensor is always .75" from the
end of the protective sensor "window".

80200401 Rev. C - ACR Page 11
F G T G

80200401 Rev. C - ACR Page 12
F G T G

80200401 Rev. C - ACR Page 13

80200401 Rev. C - ACR Page 14

80200401 Rev. C - ACR Page 15

80200401 Rev. C - ACR Page 16
This manual suits for next models
2
Table of contents
Popular Switch manuals by other brands
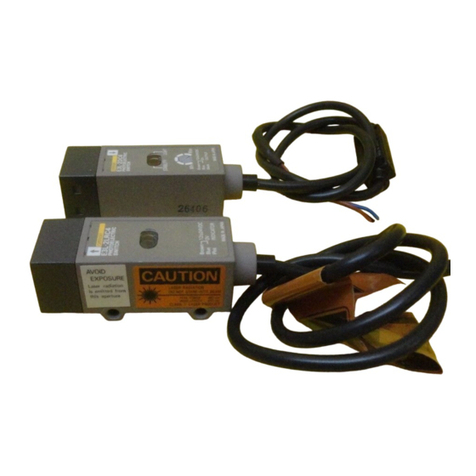
Omron
Omron E3L-2RC4 instruction sheet
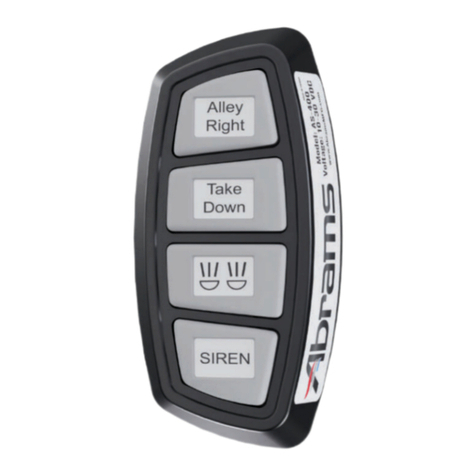
Abrams
Abrams ASTRO 400 Installation and configuration manual
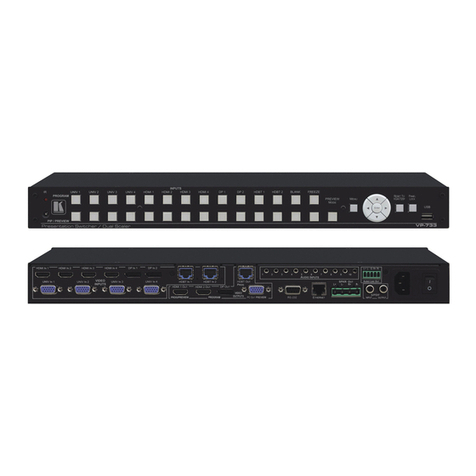
Kramer
Kramer VP-733 user manual

Huawei
Huawei Enterprise S2700 Series Configuration guide
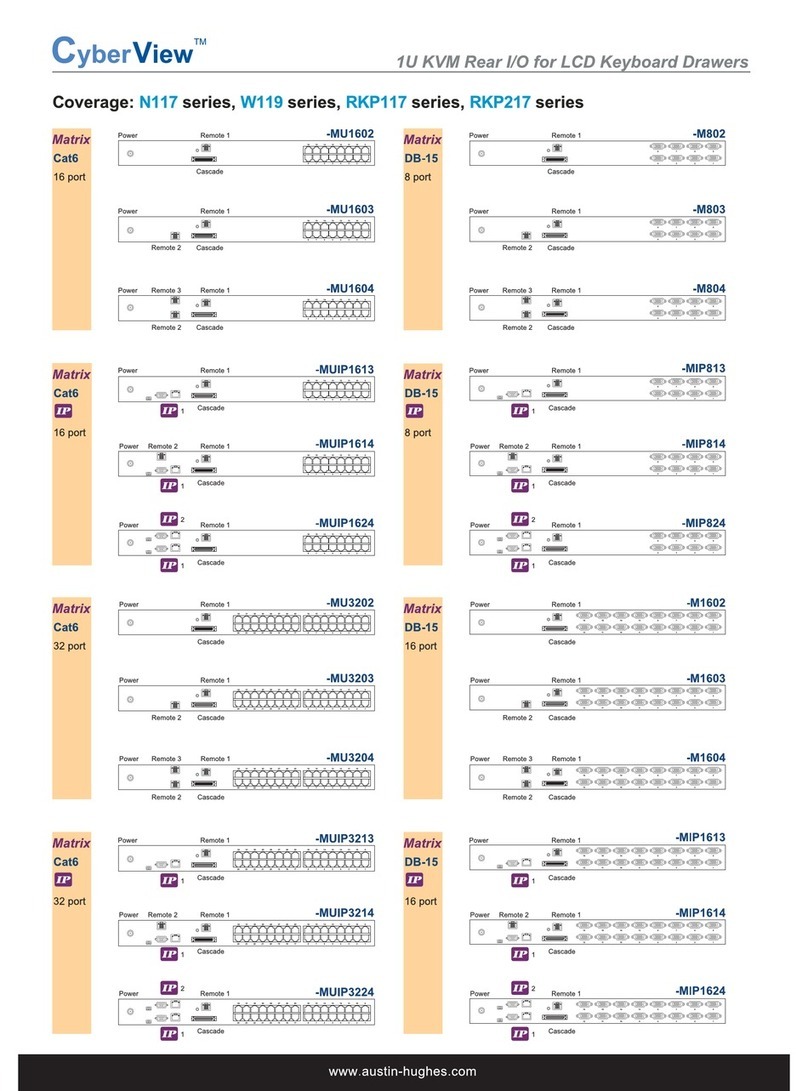
Austin Hughes Electronics
Austin Hughes Electronics CyberView N117 series Catalog
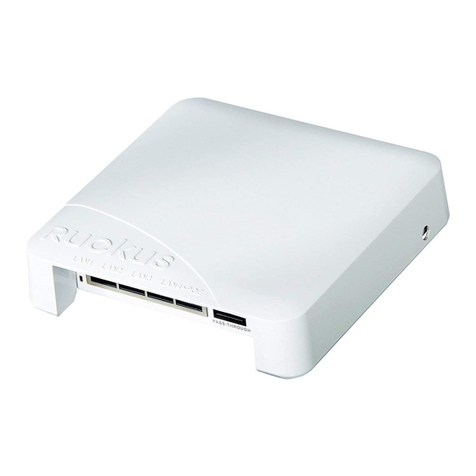
Ruckus Wireless
Ruckus Wireless ZoneFlex 7055 Quick setup guide