Fagor SPM User manual

version. 0303 - in.-
- SPM - AC SPINDLE MOTOR


i
Títle: AC Spindle Motor: [ SPM Series]
Type of documentation: Description and installation of SPM motors:
Association with spindle modular drives SPD and compact
SCD drives.
Name - model -: SPM motor manual - in.-
Version: 0303 - in -
Electronic document: SPM.pdf
Headsquarters: FAGOR AUTOMATION S.COOP.
Bº San Andrés s/n, Apdo. 144
C.P. 20500 ARRASATE - MONDRAGÓN
www.fagorautomation.com
info@fagorautomation.es
Phone: 34 - 943 - 719200
Service phone : 34 - 943 - 771118
The information described in this manual may be subject to changes due to
technical modifications. FAGOR AUTOMATION S.Coop. reserves the rigth to
change the contents of this manual without prior notice.
All rights reserved. No part of this documentation may be copied, transmitted,
transcribed, stored in a backup device or translated into another language
without Fagor Automation‘s permission.

DECLARATION OF CONFORMITY
ii
Manufacturer: Fagor Automation S.Coop.
Barrio de San Andrés s/n; C.P. 20500, Mondragón - Guipúzcoa - SPAIN.
We hereby declare, under our responsability that the product:
Fagor Servo Drive System
consisting of the following modules and accesories
Power Supplies: XPS-25, XPS-65, PS-25A, PS-25B3, PS-25B4, PS-65A and APS-24
Modular Drives: AXD / SPD 1.08, 1.15, 1.25, 1.35, 2.50, 2.75, 2.85,3.100, 3.150,3.200
Compact Drives: ACD / SCD 1.08, 1.15, 1.25, 2.50, 2.75
Modular positioning Drives: MMC 1.08, 1.15, 1.25, 1.35, 2.50, 2.75, 3.100, 3.150.
Compact positioning Drives: CMC 1.08, 1.15, 1.25, 2.50, 2.75
Accessory Modules: RM-15, ER, CM - 1.60, CHOKES and DDS PROG MODULE
Power Supply Filter: EMK 3040, EMK 3120
Motors: Brushless AC Fagor AXM, FXM and FKM
and Spindle Asynchronous Fagor SPM and FM7
mentioned on this declaration, meet the requirements:
SAFETY:
EN 60204-1: Machine safety. Electrical equipment of the machines.
ELECTROMAGNETIC COMPATIBILITY:
EN 61800-3: EMC directive for servo drive systems.
EN 61000-4-2: Electrostatic discharges.
EN 61000-4-3: [ 26 MHz to 1000 MHz ] - Radiated radio frequency electromagnetic
fields -.
EN 61000-4-4: Burst and fast Transients.
EN 61000-4-5: Power surges.
According to the European Directives 73/23/EEC on Low Voltage [modified by the 93/68/EEC directive] 98/37/CEE
on Machinery Safety and 92/31/CEE on Electromagnetic Compatibility. [EN 61800-3: 1996, Specific Regulation on
Electromagnetic Compatibility for Servo Drive Systems].
In Mondragón, March 1 st, 2003

WARRANTY TERMS
iii
INITIAL WARRANTY:
All products manufactured or marketed by FAGOR carry a 12 - month warranty for the end user.
In order to prevent the possibility of having the time period from the time a product leaves our
warehouse until the end user actually receives it run against this 12 - month warranty, the OEM or
distributor must communicate to FAGOR the destination, identification and installation date of the
machine by filling out the Warranty Form that comes with each product.
The starting date of the warranty for the user will be the one appearing as the installation date of
the machine on the Warranty Form.
This system ensures the 12 . month warranty period for the user.
FAGOR offers a 12 - month period for the OEM or distributor for selling and installing the product. This
means that the warranty starting date may be up to one year after the product has left our warehouse
so long as the warranty control sheet has been sent back to us. This translates into the extension of
warranty period to two years since the product left our warehouse. If this sheet has not been sent to
us, the warranty period ends 15 months from when the product left our warehouse.
FAGOR is committed to repairing or replacing its products from the time when the first such product
was launched up to 8 years after such product has disappeared from the product catalog.
It is entirely up to FAGOR to determine whether a repair is to be considered under warranty.
EXCLUDING CLAUSES:
The repair will take place at our facilities. Therefore, all shipping expenses as well as travelling
expenses incurred by technical personnel are NOT under warranty even when the unit is under
warranty.
This warranty will be applied so long as the equipment has been installed according to the
instructions, it has not been mistreated or damaged by accident or negligence and has been handled
by personnel authorized by FAGOR.
If once the service call or repair has been completed, the cause of the failure is not to be blamed the
FAGOR product, the customer must cover all generated expenses according to current fees.
No other implicit or explicit warranty is covered and FAGOR AUTOMATION shall not be held
responsible, under any circumstances, of the damage which could be originated.
SERVICE CONTRACTS:
Service and Maintenance Contracts are available for the customer within the warranty period as well
as outside of it.

Fagor Automation S.Coop
SPM motor manual
iv
To ensure a long life for the spindle AC motor, read carefully the procedures
described in the CONTENTS section.
This user manual contains detailed documentation about SPM series motors and
their related spindle AC drives.
CONTENTS
NOTES FOR SAVE OPERATION ........................v
1. NOTES ON USE................................................. vi
2. STORAGE...........................................................vii
3. TRANSPORTATION............................................vii
4. INSTALLATION ..................................................viii
5. WIRING............................................................... ix
6. OPERATION ........................................................x
7. MAINTENANCE AND INSPECTION ...................x
GENERAL PRECAUTIONS
• This manual may be modified when necessary because of improvement of the product, modifica-
tion or changes in specifications.
• To order a copy of this manual if your copy has been damaged or lost, contact your FAGOR repre-
sentative.
• FAGOR is not responsible for any modification of the product made by the user since that will void
our guarantee.

Fagor Automation S.Coop
SPM motor manual
v
NOTES FOR SAVE OPERATION
Read these instructions throughly before use of AC SPINDLE MOTOR. In these
instructions, NOTES FOR SAVE OPERATION are classified as and
.
Indicates a potencially hazardous which, if not avoided, may result in death or
serious injury to personnel.
Indicates a potencially hazardous situation which, if not avoided, may result in
minor or moderate injury to personnel and damage to equipment. It may also be
used to alert against unsafe practices.
Even item described in may result in a vital accident in some
situations. In either case, follow these important notes.
The following shows the symbols of [ PROHIBITION ] and [ MANDATORY ]
action.
Specifies prohibited handling.
Specifies actions that must be taken.
After reading these instructions, keep it readily available for these using the
equipment.

Fagor Automation S.Coop
SPM motor manual
vi
1. NOTES ON USE
• Observe the following items to avoid electrical shock or injury.
• Ground the ground terminals of the inverter and the motor (or ground the metal-
lic part such as frame in case of no ground terminal) according to local and/or
national electrical codes.
Failure to observe this warning can result in electrical shock.
• User grounding wires of a size complying with relevant international or local
standards.
• Do not damage the cables or apply excess stress; do not place heavy objects
on the cables or clamp the cables.
Failure to observe this warning can result in electrical shock.
• Use only the specified combinations of the inverter and the motor.
Failure to observe this caution may result in fire or malfunctions.
• Use the shortest cables possible. Separate the power cables from the signal
cables. The noise in the cable may cause the equipment to vibrate or run
improperly.
• Never use at locations exposed to water splashes, corrosive and inflammable
gases, or near combustible substances.
Failure to observe this caution may result in fire or malfunctions.
• Use under the following environmental conditions:
[1] Indoors where no corrosive or explosive gas exists.
[2] Well - ventilated without dust or metallic particles.
[3] Ambient temperature from 0°C to +40°C and free from freezing.
[4] Humidity from 20% to 80% [non - condensing].
[5] Altitude 1000 metres above sea - level.
[6] Easy to check, clean and maintain.
For use at locations where the excessive water or oil splashes exist, use a
cover or other protection. It is recommended to place the terminal box upward.

Fagor Automation S.Coop
SPM motor manual
vii
2. STORAGE
3. TRANSPORTATION
• Do not store the equipment in locations where water splashes are
present or where there is corrosive gases or liquids.
• Store the motor horizontally and guarded against any possible blows.
Make sure that no strange objects get into it through the cooling
system.
• Store the equipment protected from direct sunlight in the specified
range of temperature and humidity: [AC Spindle motor: 0°C to +60°C,
5% and 95% RH ].
• No maintenance is needed on the bearings while the motor is stored.
• The motor shaft should be turned a few revolutions every 2 or 3
months.
• Do not lift the cables or the motor shaft when carrying the equipment.
Ignoring this point may cause personal damage or improper operation
due to damage to the motor.
• Do not load the products excessively.
Failure to observe this caution may result in collapse of cargo and
personal injury.
• Use the motor eyebolts exclusively for lifting and transportation of the
motor. Do not attempt to move when other equipment is attached to
the motor.
• Before lifiting or moving it, make sure that the eyebolts are securely
screwed, the load is well balanced and the cable or chain used to
move the motor is the right one.

Fagor Automation S.Coop
SPM motor manual
viii
4. INSTALLATION
• Do not climb up on the motor or place heavy objects on it.
Failure to observe this caution may result in personal injury.
• Do not block the air inlet and outlet, and do not let foreign materials enter.
Ignoring this point may cause fire and damage to the unit.
• When unpacking, be careful of the nails in the wood frame.
Failure to observe this caution may result in personal injury.
• Cover the rotary parts so as not to touch them.
Failure to observe this warning can result in personal injury..
• The motor shaft extension is coated with anticorrosive paint. Before installation, wipe
off the paint with a cloth soaked in detergent liquid.
• When connecting the motor to a load machine, be careful with centering, belt
tension and pulley parallelism.
• For coupling with the load machine, use a flexible coupling.
• The feedback device [ encoder ] joined to the shaft is a precision unit. Do not apply
too pressure onto its output shaft. Design machines so that the thrust load and
radial load applied to the motor shaft extension during operation should be within the
allowable range described in the manual of each model.
• Never make any additional machining to the motor.

Fagor Automation S.Coop
SPM motor manual
ix
5. WIRING
• The installation must comply with the EMC 89/336/EEC directive.
• The motor is a component to be installed on machines. The machine must comply
with the 89 / 392/ EEC directive on machine safety and it must not be powered until
such directive is complied with.
• Perform wiring securely according to the connection diagrams.
Failure to observe this caution may cause motor runaway and personal injury.
• Verify that the input power is OFF before wiring.
• Use a protection circuit to avoid connecting the main machine while the motor - fan
assembly is not running.
• Perform proper grounding and noise control.
• Make wiring length as short as possible. Separate the power cables from the signal
lines. Do not run power cables and signal lines in the same duct or bundle. Noise on
signal lines may cause vibration or malfunctions
• Use FAGOR - specified cables. To use other cables, check the rated current of your
equipment, and consider operating environment to select correct cables.

Fagor Automation S.Coop
SPM motor manual
x
6. OPERATION
7. MAINTENANCE AND INSPECTION
• Do not operate the equipment with the terminal box cover removed. After wir-
ing, replace the terminal box cover.
Failure to observe this warning may result in electrical shock.
• Perform test run as follows. Secure the motor and disconnect from load
machine system, check operations, then connect the motor to the load
machine.
Failure to observe this caution may result in personal injury.
• If an alarm is issued, correct the cause, verify safety, then reset the alarm
and resume operation. (Check Drive manual).
• If momentary power loss occurs, turn the power supply OFF. The machine
may resume operation suddenly and may result in personal injury.
• Build an external emergency stop circuit that inmediately stops operation and
shuts down power in an emergency.
• Only authorized personnel should be permitted to disassemble or repair the
equipment.
• If it becomes necessary to disassemble the motor, contact your FAGOR rep-
resentative.
• To perform the inspection and maintenance, refer to the instructions in this
manual. The spindle AC motor only needs a simple daily inspection. Adapt
the inspection periods according to the running conditions and work
environment.

1. INTRODUCTION ................................................................................................1
Specifications..................................................................................................................3
Structure..........................................................................................................................4
General characteristics....................................................................................................6
2. ELECTRICAL CHARACTERISTICS ..................................................................7
Definitions .......................................................................................................................9
Operating modes...........................................................................................................11
Influence of the supply voltage......................................................................................13
Technical data and characteristics................................................................................14
Power graphs - turning speed: associated drive....................................................................14
3. MECHANICAL CHARACTERISTICS ..............................................................27
Construction types: Mounting possibilities ....................................................................29
Precautions when installing the motor....................................................................................30
Ball bearings: Useful life and precautions.....................................................................31
Balancing ......................................................................................................................32
Mounting the gear boxes...............................................................................................33
Radial and axial loads...................................................................................................33
Coupling considerations................................................................................................36
Direct coupling. Considerations..............................................................................................36
Belt coupling. Considerations.................................................................................................36
Gear coupling. Considerations...............................................................................................37
Mounting a pulley or a gear to the motor shaft.......................................................................37
Dimensions ...................................................................................................................39
4. INSTALLATION ................................................................................................49
Ventilation .....................................................................................................................51
General considerations ..........................................................................................................51
Fan connection.......................................................................................................................51
Characteristics of the fan........................................................................................................52
Motor connection - drive................................................................................................53
Connection of the SPM motor to the drive .............................................................................53
MPC 4x ... power cable..........................................................................................................54
Mechanical characteristics of the power cable MPC 4x ........................................................55
Selecting the power cable MPC 4x ... ....................................................................................55
Motor feedback - drive connection................................................................................56
Conection of the motor feedback to the drive.........................................................................56
GENERAL INDEX

PinOut of the encoder connector............................................................................................57
Encoder connection. EEC Cable............................................................................................58
Encoder connection. EEC - SP Cable ...................................................................................58
Mechanical characteristics of the cable for the encoder ........................................................60
5. MAINTENANCE ...............................................................................................61
General considerations .................................................................................................63
Checks prior to start-up..........................................................................................................63
Checks after start-up..............................................................................................................63
Maintenance periods.....................................................................................................63
6. SELECTION .....................................................................................................65
Characteristics table......................................................................................................67
Selecting the motor and the spindle drive.....................................................................69
Drive selection........................................................................................................................69
Motor identificaction plate [ label ].................................................................................70
Sales reference.............................................................................................................71

1
1
Fagor Automation S.Coop
SPM motor manual
INTRODUCTION


Fagor Automation S.Coop
SPM motor manual
3
Specifications
Fagor SPM series motors are asynchronous motors also known as induction
motors, with a squirrel - cage rotor, and are specially designed to work on machine -
tool spindles.
Depending on the winding voltage, this SPM series has two models:
•SPM xxx.xx.xxxxx.1 with a 270 Vac winding
•SPM xxx.xx.xxxxx.0 with a 330 Vac winding
Its main features are:
• Wide range of rated power:
Its sturdy design, the use of high precision bearings [special bearings] and
other elements make it possible to offer a power range from 2.2Kw to
37 Kw in S1 with a maximum speed of up to 9000 rpm.
• No maintenance is required.
• Excellent peak, continuous and stall torque.
• High reliability:
The protection level meets the IP54 standard and has a highly reliable
sinusoidal encoder for velocity feedback.
• Cooling system:
All motors come with a cooling fan to be connected to single-phase
220 Vac and a frequency of 50 Hz or 60 Hz.

Fagor Automation S.Coop
SPM motor manual
4
Structure
The structure of the motor is shown below:
fig.1 SPM motor configuration
Nr Name Nr Name
1Extruded motor frame 11 Fan terminal board guard
2Motor terminal board 12 Front side cover
3Seeger 13 Electro - blowing fan
4Encoder support pin 14 Seal
5Fan support 15 Fan terminal board guard
6Fan - Encoder module 16 Bearing
7Rear side cover 17 Drive end side key
8Wound stator 18 Fixing screw
9Motor covers tie rod 19 Fixing nut
10 Encoder connector 20 Rotor unit
table 1 Listing of the elements of the SPM motor

Fagor Automation S.Coop
SPM motor manual
5
fig.2 shows the location of the terminal box to connect the main power and the fan
as well as the location of the motor feedback connector.
fig.2 Layout of the terminal box for power and fan connection. Feedback encoder
connector.
Nr Name
Terminal box for power connection
Feedback encoder connector
Terminal box for fan connection.
Note that the numbers: are not printed on the motor
table 2 Listing of the connections at the SPM motor
1
12
3
1
1
2
3
1
123

Fagor Automation S.Coop
SPM motor manual
6
General characteristics
The F classification of the winding insulation is based on its capability to run at
maximum temperature.
This temperature 155°C [ 311°F ] represents the maximum running temperature for
the winding. In other words, if the motor ran 40 hrs a week in a clean and dry
environment, its life expectancy would be 10 to 20 years before the insulation
deteriorates due to heat to the point that it can no longer withstand the applied
voltage.
Motor type Induction. Squirrel cage
Termal protection Thermistor: klixon N.C. [ 250 V - 2.5 A ]
Tripple sensor
Balancing Degree S - ISO 2373 -
SR degree [ upon request ]
[ with the key mounted on the shaft ]
Mounting IM 2001 B3 / B5
[ optionally V1 / V5 , V3 / V6 ]
Gear box Special flange [ optional ]
Electrical insulation class F [ 155°C - 311°F ]
Protection IP54
Noise Meets IEC 34- 9 standard
Storage temperature Between - 20°C and + 80°C [ - 4°F / 176°F ]
Maximum ambient temperature Between 0°C and + 40°C [ 32°F / 104°F ]
Maximum ambient humidity Between 20% and 80% [ non condensing ]
Recommended maximum installation
altitude 1000 m [ 3281 ft ] over sea - level
Axial fan Standard on all models
Independent power supply
Feedback Sinewave encoder
Meets EC regulation IEC 34 - 1
table 3 General characteristics of SPM motors
Table of contents
Other Fagor Engine manuals
Popular Engine manuals by other brands

Armstrong
Armstrong HE Series Installation and operating instructions
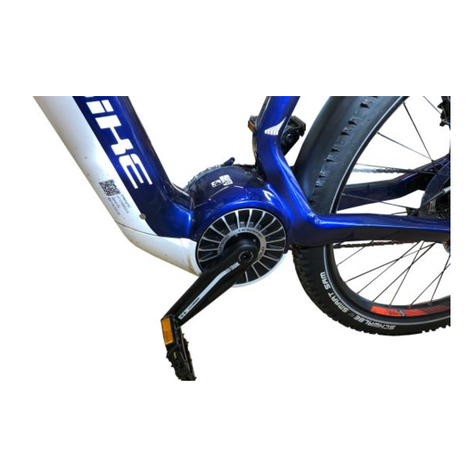
Bikespeed
Bikespeed Real Speed TQ HPR 120S Instructions for the installation and description of the functions
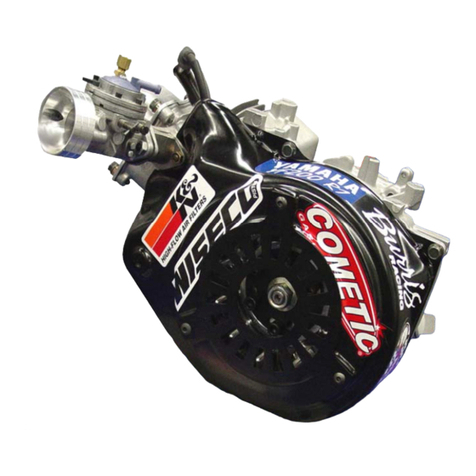
Yamaha
Yamaha YF200 R1 owner's manual
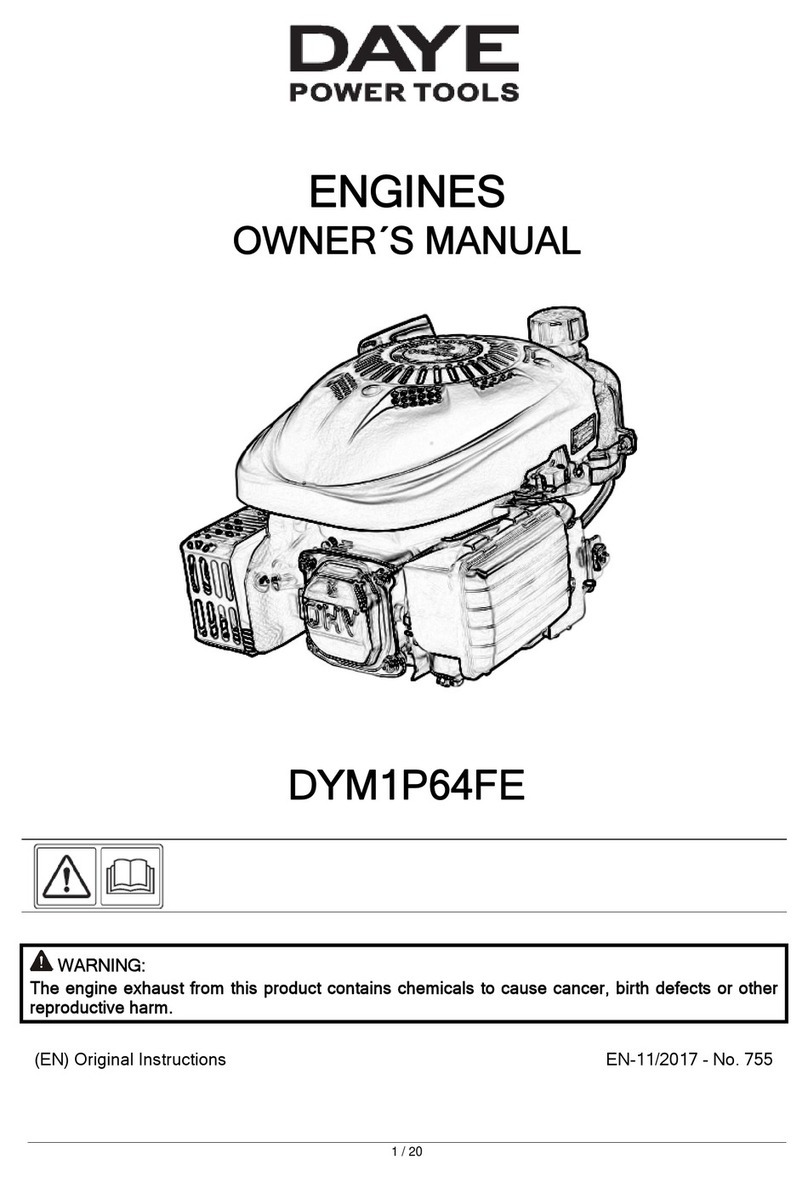
DAYE
DAYE DYM1P64FE owner's manual
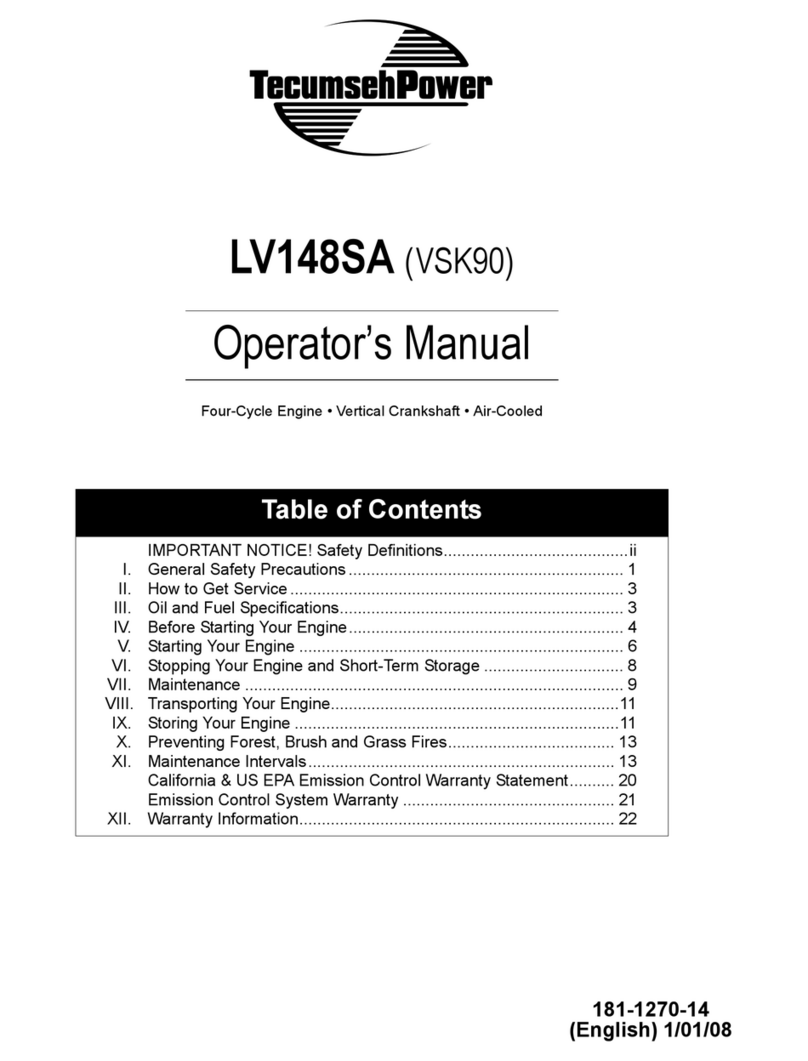
Tecumseh
Tecumseh LV148SA Operator's manual
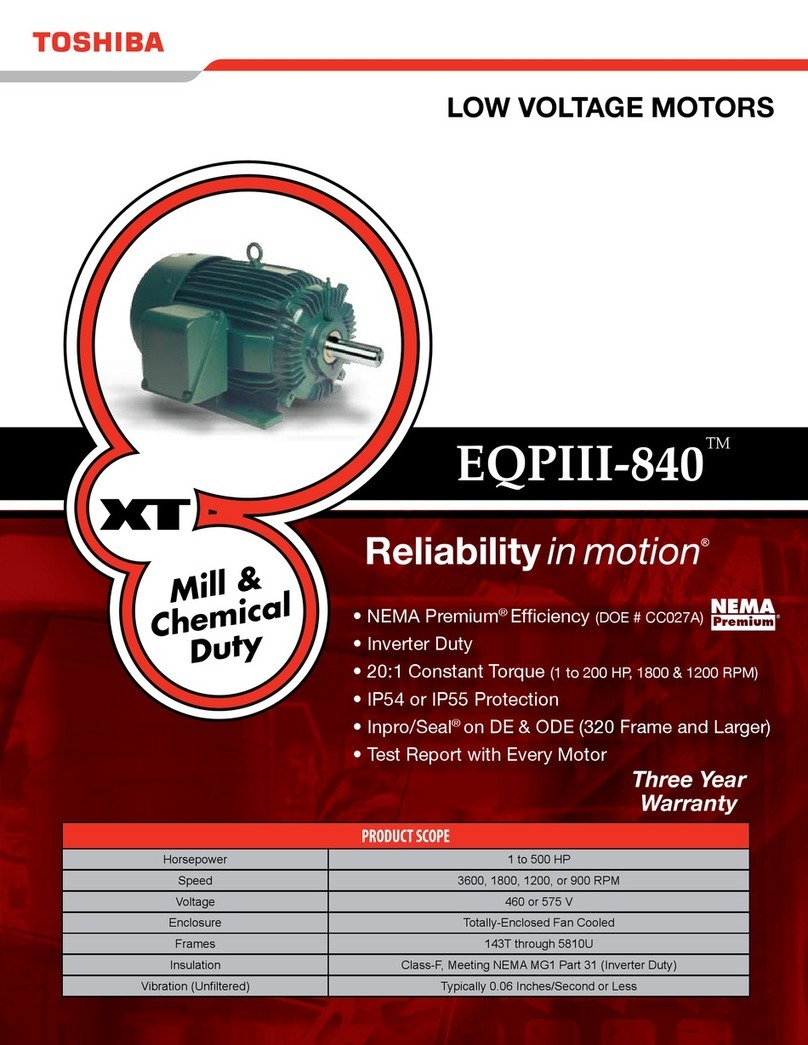
Toshiba
Toshiba EQPIII-840 Product brochure

Volkswagen Marine
Volkswagen Marine SDI Series Additional Operating Manual
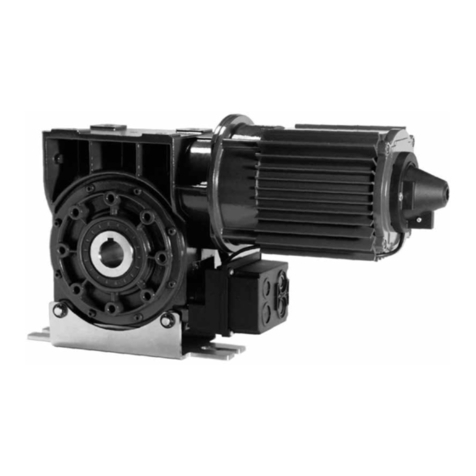
Nice
Nice RDF Series Instructions and information for installation and use
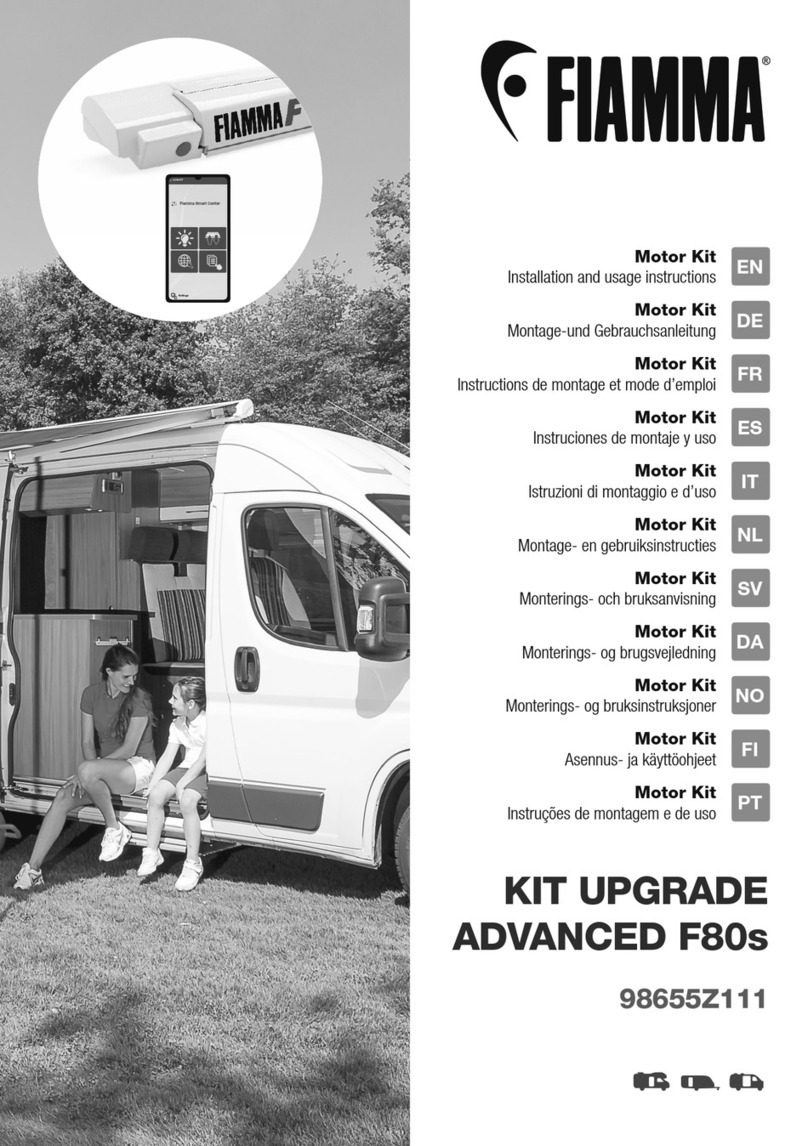
Fiamma
Fiamma 98655Z111 Installation and usage instructions

Hino Motors
Hino Motors W04D Workshop manual
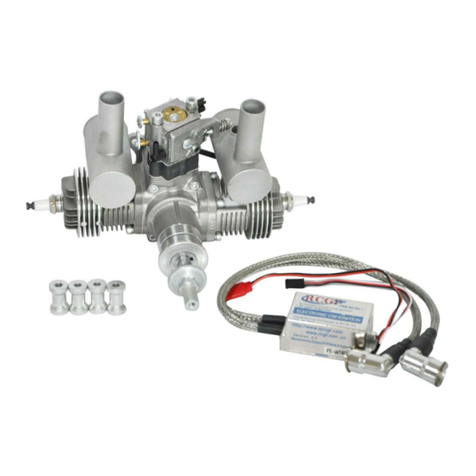
RCGF
RCGF 30CC-Twin Operator's manual
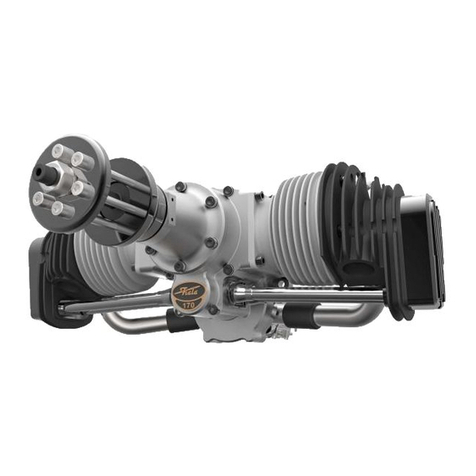
FIALA MOTORS
FIALA MOTORS FM170B2-FS manual