Fastech Ezi-STEP-BT-42 Series User manual

www.fastech.co.kr

www.fastech.co.kr
Operating Manual

2
Fastech Co.,Ltd.
1. Precautions 3
2. Main Characteristics 5/6
3. Model Naming 6
4. Specitications 7
4.1 Driver Specitications 7
4.2 Motor Specitications 8
4.2.1 Ezi-STEP-BT-42 Series 8
4.2.2 Ezi-STEP-BT-56 Series 9/10
5. Motor Torque Characteristics 11
6. Installation and Cabling 12
6.1 Notes on Installation12
6.2 Connection Diagram 13
7. Setting and Operating14
7.1 Status monitor LED 14
7.1.1 Status LED Function and Condition14
7.1.2 Protection functions and LED blinking times 15
7.2 Setting Up Parameters 15
7.2.1 Resolution 16
7.2.2 Stop Current16
7.2.3 Pulse Mode 16
7.2.4 Rotation Direction 16
7.2.5 Polarity Run Signal 17
7.2.6 Polarity Alarm Signal 17
7.2.7 Polarity Alarm Reset Signal 17
8. Connectors18
9. External Wiring Diagram 19
10. Control Signal Input/Output Description 20
10.1 Input signal20
10.2 Output signal 21
Table of Contents

3
●Thank you for purchasing Ezi-STEP. Ezi-STEP is an all-in-one Unit. For high-speed and high-
precision drive of a stepping motor, Ezi-STEP is an unique driver that adopts a new control
scheme owing to an on-board high-performance 32bit digital signal processor.
●This manual describes handling, maintenance, repair, diagnosis and troubleshooting of Ezi-
STEP.
●Before operating Ezi-STEP, thoroughly read this manual.
※Before operating ※
◆◆Put the Safety First.
☞☞Before installing, operating and repairing the Ezi-STEP, thoroughly read the manual
and fully understand the contents.
Before operating the Ezi-STEP, understand the mechanical characteristics of the Ezi-
STEP and related safety information and precautions.
☞☞After reading the manual, keep the manual near the Ezi-STEP so that any user can
read the manual whenever needed.
☞☞This manual divides safety precautions into
『『Warning』』
and
『『Attention』』
.
Contents of this manual are subject to change without prior notice for functional
improvement, change of specifications or user's better understanding.
Thoroughly read the manual provided with the purchased Ezi-STEP.
☞☞When the manual is damaged or lost, contact agent or Fastech at the address on
the last page of the manual.
Fastech is not responsible for a product breakdown due to user's dismantling the
product, and such a breakdown is not covered by the warranty.
◆◆General Precautions
1. Precautions
If the user does not properly handle the product, the user may seriously
or slightly injured and damages may occur only in the machine.
Warning
If the user does not properly handle the product, a dangerous situation
(such as an electric shock) may occur resulting in deaths or serious
injuries.
Attention
Although precaution is only a Warning, a serious result could be caused depending on
the situation. Follow safety precautions.

4
Fastech Co.,Ltd.
☞Do not install a damaged Ezi-STEP or a Ezi-STEP with a missing
part.
Otherwise, the user may get injured.
◆◆Check the Status of the Ezi-STEP.
☞Carefully move the Ezi-STEP.
Dropping the product on the user’s foot may cause aninjury.
☞Use non-flammable materials such as metal in the place where
the Ezi-STEP is to be installed.
Otherwise, a fire may occur.
☞When installing several Ezi-STEP in a sealed place, install a
cooling pan to keep the ambient temperature of the Ezi-STEP 55
℃℃or lower.
Otherwise, a fire or other kinds of accidents may occur due to
overheating.
◆◆Install.
☞Before connecting cables, check if input power is off.
Otherwise, an electric shock or a fire may occur.
☞All parameters of the Ezi-STEP were accordingly set in the
factory. To change these parameters, read the manual carefully
first.
Otherwise, the machine may get damaged.
☞The case of the Ezi-STEP is insulated from the ground of the
internal circuit by the condenser. Ground the Ezi-STEP.
Otherwise, an electric shock or a fire may occur.
◆◆Connect Cables.
Warning
Warning
Warning
☞Stop supplying power to the main circuit and wait for a while
before checking or repairing the Ezi-STEP.
Electricity remaining in the capacitor may cause danger.
☞Do not change cabling while power is being supplied.
Otherwise, the user may get injured or the step drive may get
damaged.
☞Do not reconstruct the Ezi-STEP.
Otherwise, an electric shock may occur or the user may get injured.
◆◆Check and Repair.
Attention

5
High Precision microstep function and Filtering (Patent pending)
The high-performance DSP resolves the basic resolution of 1.8。up to maximum 0.0072。(1/250 steps).
Contrary to a conventional driver, Ezi-STEP adjusts PWM control signal in every 25 usec, which makes
it possible to more precise current control and realizes a high-precision microstep operation.
Vibration suppression and High-speed operation (Patent pending)
Ideally the applied currents to a stepping motor are a precise sinusoidal waves. But in practice the
magnetic flux nonlinearity of the motor, the lowering of current due to the increase of back emf at high-
speed and the lowering of the phase voltage are the sources of motor vibration.
For these practice Ezi-STEP detects these nonlinearity with DSP and adjusts the phase of the current
according to the pole position of the motor, drastically suppressing vibration. As reducing the vibration of
the motor, it is possible to operate in high-speed regime.
EZi-STEP can detect the loss-of-synchronization of a
stepping motor without the addition of an external
sensor. By monitoring the voltage, the current, and
the back-emf signal, the on-borad DSP estimates the
current position of a rotor and enables to detect the
loss-of-synchronization (so far seemingly impossible
task in a conventional stepping motor drive), in turn
realizing operation in high-speed region without
worrying about loss-of-synchronization*.
* effective only over 300 rpm
Torque
300 (rpm)
Step-Out Detection(patent pending)
1
Microstep and Filtering(patent pending)
2
Software Damping(patent pending)
3
Software Damping OFF
Software
Damping
Software Damping ON
* This is real measured speed that using 100000[pulse/rev]encoder.
Detecting area of
loss-of-synchronization
2. Main Characteristics

6
Fastech Co.,Ltd.
Besides alarming loss-of-synchronization, there are various warning signals depending on the alarm
issued. Also, Ezi-STEP provides an easy interface to communicate with an upper controller by issuing
RUN/STOP signal.
(The type of alarm issued can be identified by LED indicator)
Driver Output Signal Monitoring
4
Depending on the speed of a stepping motor, Ezi-STEP automatically increases the supply voltage and
prevents the torque lowering due to the low effective operating voltage on a motor from the back emf
voltage, in turn enabling a high-speed operation. Also, the software damping algorithm minimizes the
vibration and prevents the loss-of-synchronization at high-speed.
Improve of High-Speed Driving
5
3. Model Naming
EzStep - BT - 42 - S
Length (S : Short , M : Middle, L : Long, XL : eXtra Long)
Size (42 : 42mm, 56 : 56mm)
Motor+Driver Unit type
Driver Series Type
■Part Numbering

7
4. Specifications
4.1 Driver Specifications
Type
Drive Method
Input Voltage
Operate
Operate
Reserve
Reserve
Condition
Function
I/O
Temp.
Humidity
Vib. Resist.
Resolution(P/R)
May. Freq.
LED Display
STOP Current
Pulse Input Method
Rotational Dir.
Speed/Position
Commamd
Input Signals
Output Signals
Alarm Function
EzStep-BT-42-S/M/L
Bipolar PWM drive with 32bit DSP
24 VDC ±10%
0 ~ +50℃
-20 ~ +70 ℃
35~85% RH (Non condensing)
10~90% RH (Non condensing)
0.5G
500, 1000, 1600, 2000, 3200, 3600, 4000, 5000, 6400, 8000,
10000, 20000, 25000,36000, 40000, 50000 (Set by RS232C
Communication)
*Default : 10000
500 KHz (Duty 50%)
Step-Out, Over-Current, Over-Heat, Over-Voltage
Power Status(Green), Alarm Status(Red)
10% ~ 100% (Set by RS-232C Communication)
Be setted to set value of STOP current after 0.5 second after motor
stop.
*Default : 50%
1 Pulse / 2 Pulse (Set by RS-232C Communication)
1 Pulse: Pulse / Direction, 2 Pulse: CW / CCW
*Default : 2 pulse
CW / CCW (Set by RS232C Communication)*Default : CW
Used when changing the direction of motor rotate.
*Default : CW
Pulse train input (Photocoupler Input)
Photocoupler Input : Motor Free, Alarm Reset
Photocoupler Output : Alarm, Run/Stop
EzStep-BT-56-S/M/L/XL

8
Fastech Co.,Ltd.
EzStep-BT-42-LEzStep-BT-42-MEzStep-BT-42-S
Driver Type
EzStep - BT - 42 - S
EzStep - BT - 42 - M
EzStep - BT - 42 - L
No. of
phase
2
Excitation
method
Micro Step
(Max. 50,000 P/ R)
Rated
Torque(A/ph)
1.5
1.5
1.5
Max. Holding Torque
mNm (kgfcm)
270(2.8)
400(4.1)
490(5.0)
Rotor Inertia
gcm2
38
54
76
Power
Supply(DC)
24V, 2.0A
24V, 2.0A
24V, 2.0A
Shaft Size
(mm)
5.0
5.0
5.0
4.2.1 Ezi-STEP-BT-42 Series
4.2 Motor Specifications
Unit : mm

9
EzStep-BT-56-MEzStep-BT-56-S
Driver Type
EzStep - BT - 56 - S
EzStep - BT - 56 - M
No. of
phase
2
Excitation
method
Micro Step
(Max. 50,000 P/ R)
Rated
Torque(A/ph)
3.0
3.0
Max. Holding Torque
mNm (kgfcm)
810(8.3)
1300(13.3)
Rotor Inertia
gcm2
189
250
Power
Supply(DC)
24V, 4.0A
24V, 4.0A
Shaft Size
(mm)
6.35
6.35
4.2.2 Ezi-STEP-BT-56 Series
Unit : mm

10
Fastech Co.,Ltd.
EzStep-BT-56-L EzStep-BT-56-XL
Driver Type
EzStep - BT - 56 - L
EzStep - BT - 56 - XL
No. of
phase
2
Excitation
method
Micro Step
(Max. 50,000 P/ R)
Rated
Torque(A/ph)
3.0
3.0
Max. Holding Torque
mNm (kgfcm)
2490(25.4)
3540(36.1)
Rotor Inertia
gcm2
493
737
Power
Supply(DC)
24V, 4.0A
24V, 4.0A
Shaft Size
(mm)
6.35
6.35
4.2.2 Ezi-STEP-BT-56 Series
Unit : mm

11
5. Motor Torque Characteristics
EzStep - BT - 42 - S
EzStep - BT - 42 - M
EzStep - BT - 42 - L
EzStep - BT - 56 - S
EzStep - BT - 56 - M
EzStep - BT - 56 - L
EzStep - BT - 56 - XL

12
Fastech Co.,Ltd.
6. Installation and Cabling
6.1 Notes on Installation
1) Ezi-STEP has been designed for indoor uses.
2) The ambient temperature of the room should be 0℃~50℃.
3) If the temperature of the case is higher than 50℃, radiate heat of the outside to cool down the
case.
4) Do not install Ezi-STEP under direct rays, near magnetic or radioactive objects.

13
6.2 Connection Diagram
Power Ezi-STEP
CN1
CN2
CN3
Controller
PC
Input voltage
(24VDC±10%)
Input voltage GND
FG
CW+(Pulse+)
CW-(Pulse-)
CCW+(Dir+)
CCW-(Dir-)
Alarm
Run/Stop
24VDC GND
24VDC
※Alarm Reset
/ Motor Free
Twisted Pair
Shield Cable
※Alarm Reset signal line is also used for Motor FREE signal.
(For details, please refer to the section for Control Input/Output signal)
FG
1
1
2
2
3
3
4
1
2
3
5
9
6
7
8
10
TX
TX
RX
RX
GND
RS-232

14
Fastech Co.,Ltd.
7.1 Status monitor LED
7.1.1 Status LED Function and Condition
7. Setting and Operating
Status Color Function Blinking Condition
Power Green Power input indication Lights when power is ON
Alarm Red Alarm indication
Blinking when protection function is activated
(Identifiable which protection mode is
activated by counting the blinking times)
LED
CN3
CN1
CN2

15
7.1.2 Protection functions and LED blinking times
7.2 Setting Up Parameters
Alarm LED blinking (ex: Speed error)
RS-232C serial communication port of a computer is used to set up various parameters of the
motor driver. The set-up program is supplied with the product on a companion CD. It is
recommended to make a copy of the program in any folder on your computer. Then please
execute the program, named “EzStep Setup.exe”, from the folder.
Please select an appropriate Prot No. and press
icon. Then it will display the various
parameter values previously stored in the driver.
: Display the parameter values stored in the
driver
: Store the parameter values
displayed on the screen into the
driver
Blinking Times Protection Conditions
1
2
3
5
9
Overcurrent
Overspeed
Overheat
Lowpower
Out of Synchronization
1
0.5s
2 3 123
Excessive current flowed into a motor
Motor speed exceeded 3000 RPM
Abnormally, motor did not followed pulsed inputs
Internal temperature of a motor driver exceeded 55℃
Power source voltage is below 20 volts
2.0s

16
Fastech Co.,Ltd.
7.2.1 Resolution
Resolution means the number of pulses per one rotation of a motor.
Select a desired resolution by pressing in icon on EzStep Setup
screen. The possible resolution values are 500, 1000, 1600, 2000, 3200, 3600, 4000, 5000,
6400, 8000, 10000, 20000, 25000, 36000, 40000, 50000.
7.2.2 Stop Current
Stop Current means the motor current value automatically set in 0.5 sec after motor stops. This
is to prevent the overheat of a motor when the motor is under long time idling. Select a desired
Stop Current by pressing in icon on EzStep Setup screen.
The unit of the selection values is a percentage.
7.2.3 Pulse Mode
As the pulsed inputs, a user can choose One-pulse-mode (Pulse/Dir) or two-pulse-
mode(CW/CCW). Select a desired pulse mode by pressing in
icon on EzStep Setup screen.
7.2.4 Rotation Direction
The direction of the motor rotation can be selected either in CW(clockwise) or in CCW(Counter
Clockwise). Select a desired rotation direction by pressing in
icon on EzStep Setup screen.
Press button to store the value selected into the driver.
* The default factory setting is 10,000 [Pulses/Revolution].
Press button to store the value selected into the driver.
* The default factory setting is 50%.
Press button to store the value selected into the driver.
* The default factory setting is two pulse input mode (CW/CCW).
Press button to store the value selected into the driver.
* The default factory setting is CW(clockwise).

17
7.2.7 Polarity Alarm Reset Signal
Input Methol of Motor Free / Alarm reset can be selected. Select a desired method by pressing
in icon on EzStep Setup screen.
Press button to store the value selected into the driver.
* The default factory setting is Normal.
[CAUTION] : When you selet ‘lnverse’ : It can be ‘Motor Free’ status when powen is provided to
EzStep during Signal Connector(CN2)is not connected. The power led(green)is
blinking to show the status of ‘Motor Free’.
Press button to store the value selected into the driver.
* The default factory setting is Normal.
7.2.5 Polarity Run Signal
Run/Stop output method can be selected that indicate the motor running status.Select a desired
method by pressing in icon on EzStep Setup screen.
7.2.6 Polarity Alarm Signal
Alarm signal output method can be selected when error happens. Select a desired method by
pressing in icon on EzStep Setup screen.
Press button to store the value selected into the driver.
* The default factory setting is Normal.

18
Fastech Co.,Ltd.
Power Connector(CN1)
3
1
4
2
Number
1
2
3
4
Function
Power Input: 24 VDC ±10%
Power Input Ground
Frame Ground
NC
Signal Connector(CN2)
Number
1
2
3
4
5
6
7
8
9
10
Function
CW+(PULSE+)
91
10 2
CW-(PULSE-)
CCW+(DIR+)
CCW-(DIR-)
ALARM
+24(VDC) GND
+24(VDC)
ALARM RESET
RUN / STOP
Frame Ground
Input/Output
Input
Input
Input
Input
Output
Input
Input
Input
Output
8. Connectors
RS232C Connector(CN3)
Number
1
2
3
Function
Tx
123
Rx
GND

19
9. External Wiring Diagram
Motion Controller
Power
Control Unit
DC Power Supply
PC
Network Motion Controller PLC
Type
※ For enlanging the length, have to use the extensicn cable.
Power Cable Control Cable
30Cm 30Cm
20m2m
Standard Length
Maximum Length
This manual suits for next models
8
Table of contents
Other Fastech Engine manuals
Popular Engine manuals by other brands

Rotax
Rotax 125 MAX DD2 Repair manual

Dongfeng Chaoyang Diesel engine Co
Dongfeng Chaoyang Diesel engine Co CYQD 32 Series CYQD32 Service manual

Rotek
Rotek YSD490Q Operation & maintenance manual
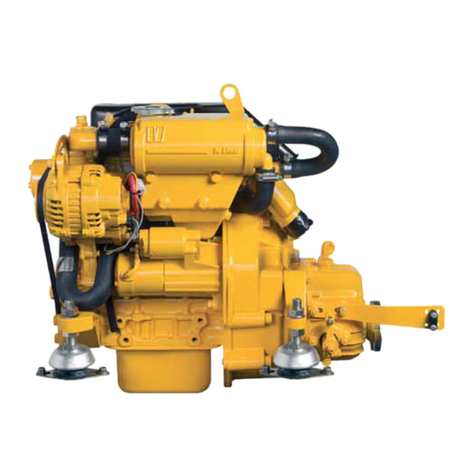
Vetus
Vetus M2.02 Operation manual
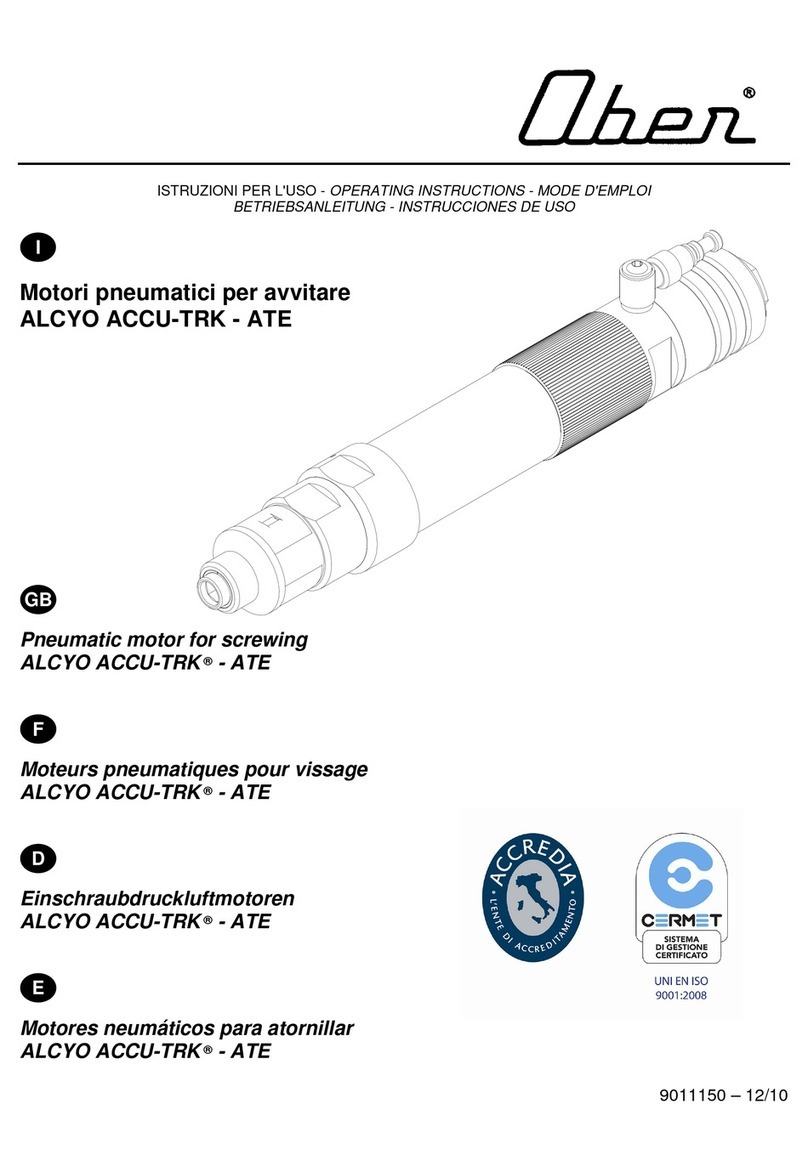
Oben
Oben ALCYO ACCU-TRK-AT operating instructions
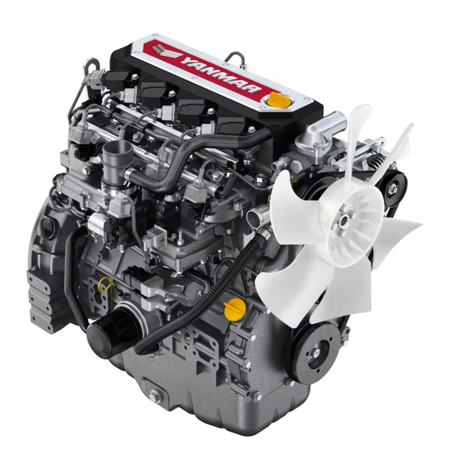
Yanmar
Yanmar L-A series Service manual
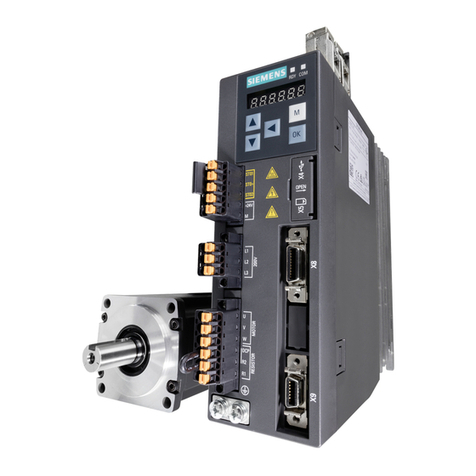
Siemens
Siemens SIMOTICS S-1FL6 installation guide
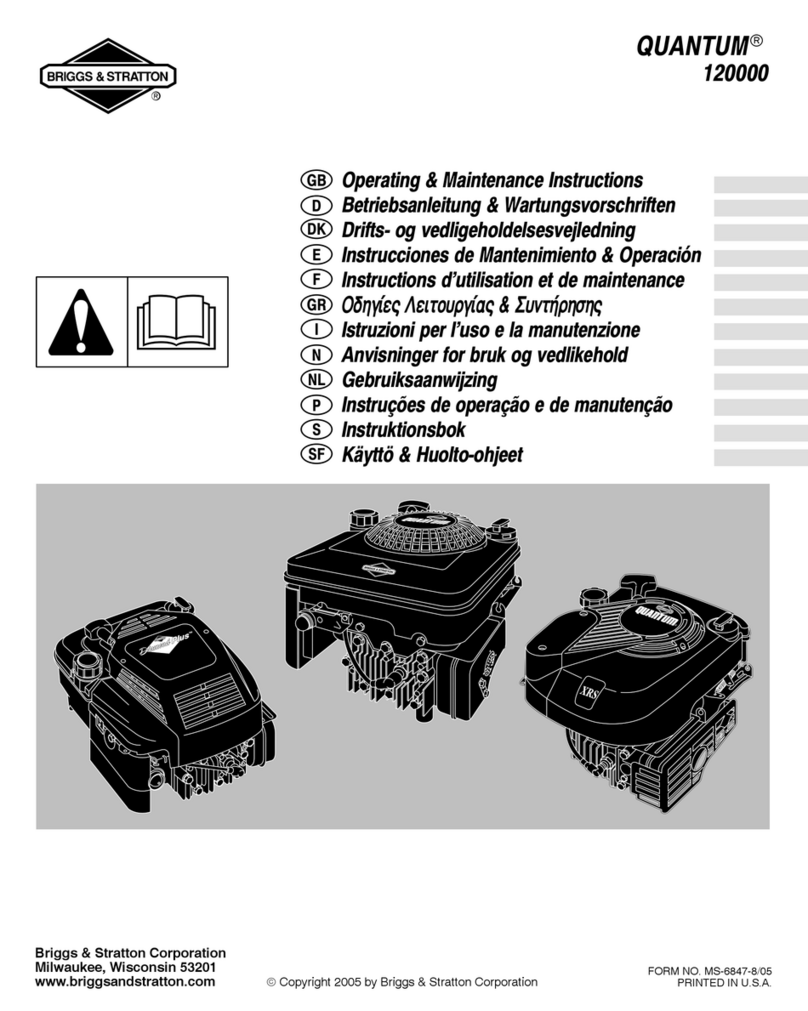
Briggs & Stratton
Briggs & Stratton 120000 Operating and maintenance instructions
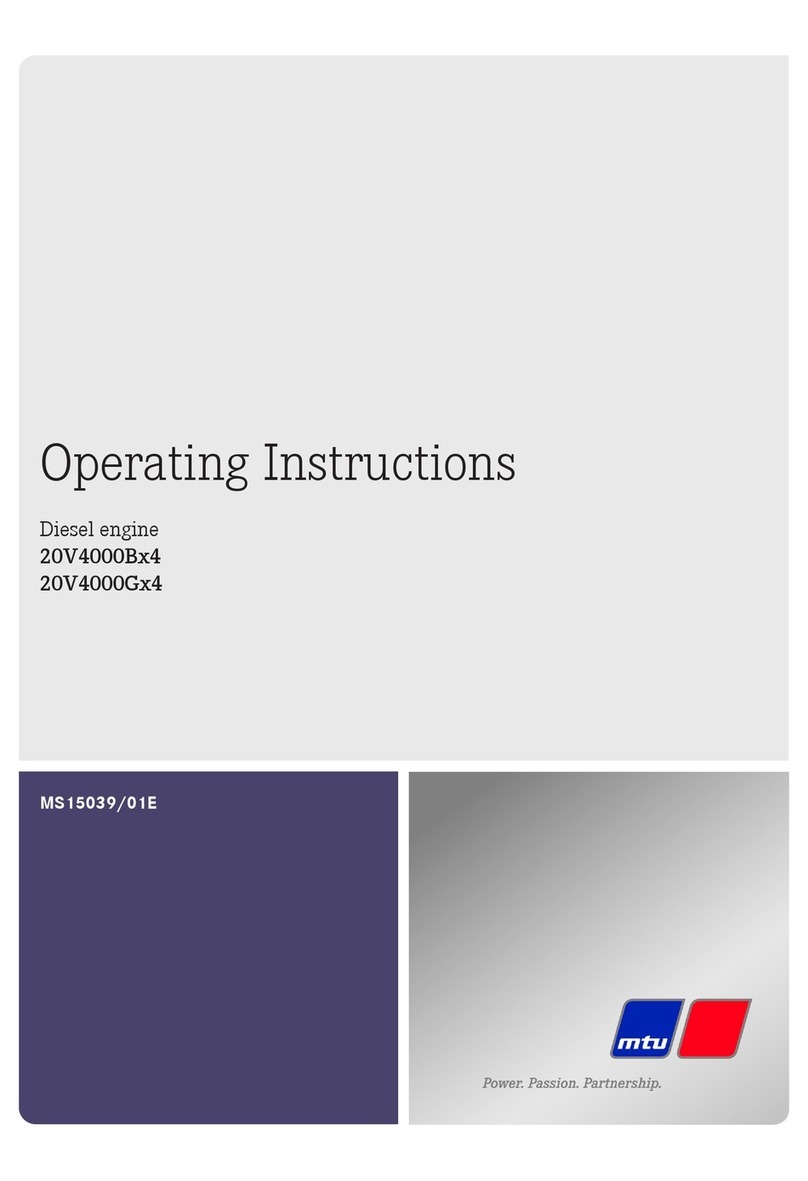
MTU
MTU 20V4000Bx4 operating instructions
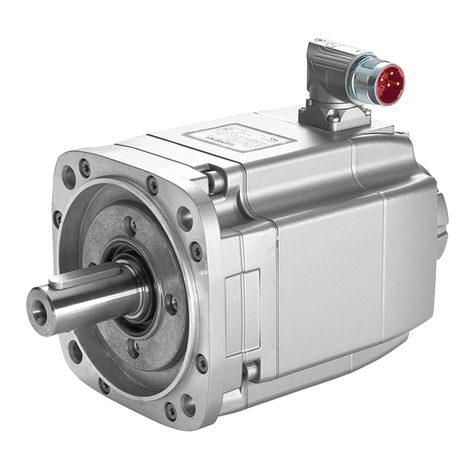
Siemens
Siemens SIMOTICS S-1FK7 DYA Generation 2 operating instructions
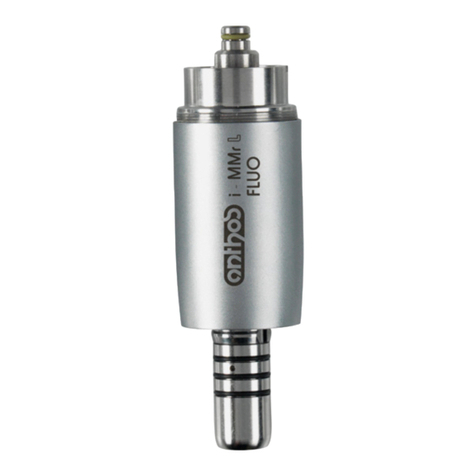
CEFLA
CEFLA I-MMr Operator's manual

ASA Electronics
ASA Electronics DA VINCI 40 ST manual