FORST ST6 D42 Manual

12-M-001 Revision 1.1
Operation & Maintenance Manual
English

Page 2
Redwood Global Ltd,
Unit 86, Livingstone Road, Walworth Business Park, Andover,
Hampshire. SP10 5NS. United Kingdom

Page 3
Contents
1.0 Introduction ..........................................................................................................5
1.1 Purpose of Chipper...........................................................................................6
1.2 Exterior Components ........................................................................................7
2.0 Safety...................................................................................................................9
2.1 Safety Working..................................................................................................9
2.2 DO’s and DON’Ts ...........................................................................................10
2.3 Noise Test Information....................................................................................11
3.0 Transportation & Storage...................................................................................12
3.1 Towing the Chipper.........................................................................................12
3.2 Attaching and Detaching the Chipper .............................................................12
3.2 Lifting the Chipper...........................................................................................13
3.3 Storage of the Chipper....................................................................................13
4.0 Chipper Operation..............................................................................................14
4.1 Control Panel & Ignition ..................................................................................15
4.2 Feed Speed Adjustment..................................................................................18
4.3 Emergency Stopping.......................................................................................19
4.4 Feed Jam & Blockages...................................................................................20
5.0 Routine Maintenance .........................................................................................21
5.1 Debris Screen.................................................................................................22
5.2 Engine Maintenance .......................................................................................22
5.3 Fastener tightening torques ............................................................................22
5.4 Service Schedule............................................................................................23
5.5 Chipper Diagrams...........................................................................................24
5.6 Blade Changing ..............................................................................................26
5.7 Blade Sharpening ...........................................................................................27
5.8 Hydraulic Oil Filter...........................................................................................28
5.6.1 Removal and Replacement......................................................................28
5.9 Oils, Fluids and Lubricants..............................................................................29
5.10 Drive belt tension ..........................................................................................30
5.11 Battery...........................................................................................................31
6.0 Parts Lists & Diagrams.......................................................................................34
6.1 Tray & Stop Bar ..............................................................................................34
6.3 Top feed roller assembly.................................................................................36
6.4 Flywheel Assembly .........................................................................................37

Page 4
6.5 Bottom Feed Roller.........................................................................................38
6.6 Anvil................................................................................................................39
6.7 Stone Trap......................................................................................................40
6.8 Belt Tensioner assembly.................................................................................41
6.9 Safety Curtain.................................................................................................42
6.10 Chute Assembly............................................................................................43
6.11 Fuel tank assembly.......................................................................................44
6.12 Light board assembly....................................................................................45
6.13 Running gear –hitch & axle..........................................................................46
6.14 Hydraulics circuit diagram.............................................................................46
6.15 Electrical Circuit Diagrams............................................................................47
6.16 Decals...........................................................................................................48
6.17 Manufacturer’s Statutory Plate......................................................................49
6.18 Vehicle Identification Number (VIN) Plate.....................................................50
7.0 Warranty and Certification..................................................................................51
7.1 Warranty .........................................................................................................51
7.2 Certification.....................................................................................................52

Page 5
1.0 Introduction
Thank you for becoming the owner of this Redwood Global Ltd, Först ST6D wood
chipping machine. By observing the contents of this manual, we hope the chipper
gives safe and productive service. This user manual is intended for the
owner/operator to safely and effectively operate this chipper and carry out routine
maintenance between services. This is not a comprehensive service manual. See
Service Schedule for routine maintenance and when to take the chipper to a service
specialist. For engine maintenance, please refer to the engine manual supplied with
this chipper.
This chipper has been through a pre-delivery inspection before leaving the factory
and is ready to use.
Also, damage to property and this chipper may occur. Please observe and obey all
warning signs (decals) located on the chipper. Their meaning is covered in this
manual under decals.
All personnel working with this chipper must be adequately trained in its use and
most importantly, follow the advice on safe working practices.
Redwood Global Ltd endeavour to continuously develop and improve its products.
They reserve the right to make changes at any time, without notice or incurring any
obligation.
Continuous improvement will affect chipper design and production so there may be
minor discrepancies between the actual product and this manual.
This manual must remain with the chipper for reference by operators and includes
hiring or if the chipper is resold.
Before use and as a minimum, the safety and chipper operation
sections covered in Chapter 2 be read and understood. Failure to
do so could result in serious injury or loss of life to the operator
and others nearby.

Page 6
1.1 Purpose of Chipper
The Först ST6D is designed to reduce wood material up to 150mm diameter to
woodchip. This chipper is capable of processing up to 5 tonnes of wood per hour.
Twin hydraulic motors
150mm
30 litres
17 litres
5 tonnes/hour
EN590 Diesel
Roller Feed
Max. material diameter
Fuel Capacity
Hydraulic Oil Capacity
Material processing
Fuel type
Doosan D18
31kW (42hp)
Water Cooled
1165kg
Electric
Engine
Max. power
Cooling
Kerb weight
Starting

Page 7
1.2 Exterior Components
1. Feed touch sensors
2. Fuel tank
3. Prop stand
4. Control valve speed adjust
5. Control panel
6. Bonnet latch
7. Bonnet
8. Statutory plate & VIN
9. Light socket
10.Breakaway cable
11.Handbrake
12.Tow hitch
13.Jockey wheel handle
14.Lifting point
15.Chute rotation clamp
16.Chute handle clamp
17.Chute hood

Page 8
1. Spare wheel
2. Document box
3. Hopper
4. Battery
5. Number plate
6. Feed touch sensors
7. Stop bar
8. Hopper tray
9. Safety curtain
10.Emergency stop
11.Chute handle
12.Chute

Page 9
2.0 Safety
2.1 Safety Working
Before using this chipper, make sure that you are trained and fluent in its operation.
Know the location of and how to use all the safety features. Know how to control the
feed and stop the chipper in an emergency. Be familiar with the hazards and safe
working practices to prevent injury and damage to property and chipper. Also be
aware of the legal restrictions for personnel and towing with vehicles.
•The minimum age for service personnel is 18
years. Personnel aged 16 can use the
chipper for training under supervision by a
suitably trained person of 18 years or over.
•Operators and personnel working with this
chipper must not be under the influence of
alcohol, drugs or medication that would impair
judgement, concentration or reaction times.
Excessive tiredness is also a risk.
•In use, woodchip and debris are ejected with
considerable force from the chute and can
travel up to 10m. Make sure the chute directs
woodchip to a safe location so that no one can
be harmed or property damaged. Do not allow
discharge to be directed onto roads or public
rights of way.
•Maintain a 10m exclusion zone around the
chipper and clearly mark if in a public area.
Keep this area free of material build up.
•Make sure the chipper is on even, level and
stable ground and cannot move or topple
when in use. Use wheel chocks if necessary.
•Keep children and animals well away from the
working area.
•The chipper operator must wear protective
equipment:
▪Chainsaw safety helmet (EN 397) with
mesh visor (EN 1731)
▪Correctly rated ear defenders (EN 352)
▪Work gloves with elasticated wrist bands.
▪Steel toe cap boots (EN345-1)
▪Close fitting heavy duty non-snag clothing.
Hi-viz clothing (EN 471) if needed.
▪Protect breathing with a face mask if
appropriate. Some plant material can give
off harmful dust and poisonous vapours.
This may cause respiratory problems or
serious poisoning. Check the material to
be processed before starting.
•DO NOT wear rings, bracelets, watches,
jewellery or anything that could be caught on
the material being fed and draw you into the
chipper.
•All personnel operating or feeding material into
the chipper must wear heavy duty non-snag
clothing to help prevent being caught on
material and drawn into the chipper. The feed
mechanism of this chipper uses high powered
hydraulic motors to drive sharp toothed rollers
that feed material into the cutting blades. DO
NOT take risks with it. NEVER ASSIST ANY
MATERIAL INTO THE FEED ROLLERS WITH
HANDS OR FEET. Use the wooden paddle or
further long material if necessary.
•Never climb onto the hopper area while the
chipper is in operation.
•CAUTION! –Keep hands and feet outside the
hopper. Do not attempt to force material into
the chipper by hand –use a piece of wood if
necessary.
•Material can be forcibly ejected from the hopper
towards the operator. Ensure full head and
face protection is worn.
•Very twisted material should be trimmed into
manageable pieces. Failure to do this can
result in material extending outside the hopper,
moving aggressively side-to-side creating a
hazard to the operator.
•Do not try to force material over 150mm in
diameter into the chipper.
•Carefully site the chipper so operators can work
furthest from any local danger. For example,
on a road side, place chipper so operators work
on the verge and not in the road exposed to
traffic

Page 10
2.2 DO’s and DON’Ts
•DO ensure that the starting of the chipper can cause
no hazard before starting. i.e. no persons are in the
hopper or in any other danger aera
•DO stop the chipper before making any adjustments,
refuelling or cleaning
•DO make sure the chipper has stopped rotating and
remove the ignition key before any maintenance or the
chipper is left unattended. The belts and pulley are to
be used to ensure visually that the chipper has
stopped rotating
•DO ensure that the chipper is level, well supported
and cannot move during use
•DO run the chipper at full throttle
•DO conduct regular chipper checks for visual fluid
leaks
•DO take regular breaks. Wearing protective
equipment can be hot and tiring leading to a lack of
concentration, increasing the risk of having an
accident
•DO keep hands, feet and clothing out of feed area,
chute and moving parts
•DO always check the all of controls and safety devices
(emergency stops, stop bar) before feeding any wood
into the chipper
•DO remove any additional debris attached to the wood
before commencing work i.e. nails, wire, rope etc
•DO NOT use chipper in poor visibility or insufficient
light to see clearly
•DO NOT use or attempt to start the chipper without the
discharge chute or guards correctly and securely fitted
•DO NOT stand directly in front of the in-feed hopper
when using the chipper. Stand to one side
•DO NOT allow the following to enter the chipper as
damage is likely:
•DO NOT stand in front of the chute
•DO NOT smoke when refuelling. Petrol fuel is highly
flammable and explosive in certain conditions
•DO NOT let anyone who has not received instruction,
operate the chipper
•DO NOT climb on the chipper at any time except for a
tracked chipper ride-on plate where fitted
•DO NOT handle material partially engaged in the
chipper while in operation
•DO NOT touch any exposed wiring whilst the chipper
is running
•DO NOT restart the chipper immediately if an
emergency stop has caused a shut down. Before
disengaging the emergency stop a thorough
inspection of the chipper should be carried out to
ensure the safety conditions are being met
Bricks
Metal
String
Glass
Cloth
Rubber
Plastic
Roots
Stones
Bedding Plants

Page 11
2.3 Noise Test Information
Chipper
ST6 D 42
Test
50mm x 50mm 4.2m long sawn pine
Noise levels above 85dB (A) will be experienced at the working position and within a
4-metre radius. Operators and personnel within a 4-metre radius must wear
appropriate ear protection at all times while chipper is in operation to prevent the risk
of hearing damage.
A-weighted emission sound pressure (beside operator’s ear) LpA = 105.7dB(A).
Peak C-weighted instantaneous sound pressure (beside operator’s ear) LCpeak =
123.5dB(C). Results at 10 metre radii are calculated.
As required by Forestry machinery - Wood chippers –Safety BS EN 13525 and in
line with Machinery Directive 2006/42/EC.
Guaranteed sound power level: 118dB(A)

Page 12
3.0 Transportation & Storage
3.1 Towing the Chipper
•When towing the chipper, the maximum legal
speed limit on UK roads is 60mph (96km/h).
•On very rough and uneven road surfaces, reduce
speed to protect the chipper from undue vibration.
•When off road, avoid objects that may collide with
the chipper underside.
•Avoid steep gradients when off road.
•Avoid excessively pot holed ground.
Exercise caution when reversing the chipper as the
short wheel base will react quickly to steering.
•Keep tyre pressures inflated to 2.76 Bar or 40 psi.
•Check wheel nuts are tightened to between 90Nm
and 100Nm.
•Tyres fitted to the ST6D must be 205/65R15C
102/100T with a load index of 102 = 850kgs and a
speed rating of “T” which equates to 118mph
(190km/h) which is above the UK permissible
towing speed.
•Clear chipper of loose woodchip material before
departing.
•Ensure the chute is securely fixed at the inboard
position before departing.
•Ensure that the hopper tray is closed in the up
position and the locking latch is fully engaged
before departing.
3.2 Attaching and Detaching the Chipper
Attaching the Chipper
Detaching the Chipper
1. Check that the vehicle ball hitch is well greased.
2. Raise the chipper hitch by turning the jockey
wheel handle anticlockwise until the hitch socket
is above the vehicle hitch ball.
3. Reverse the vehicle until the ball is directly
below the chipper hitch socket.
4. Attach the breakaway cable/secondary coupling
to a suitably strong point on the vehicle, not the
ball hitch.
5. Ensure the barrel lock is retracted from the tow
head.
6. Grasp handle on tow head and push back catch
with thumb.
7. Wind the jockey wheel handle clockwise to
lower the hitch socket onto the ball hitch.
8. Release tow head handle and continue to wind
the jockey wheel handle clockwise. The tow
head should snap into place on the ball hitch. If
it doesn’t, repeat previous two steps.
9. Wind jockey wheel up until fully retracted and
the jockey wheel frame is seated in its notch on
the stem. The chipper’s weight should be fully
on the vehicle.
10. Release the jockey wheel clamp and slide the
jockey wheel assembly fully up then tighten
clamp.
11. Connect the vehicle trailer socket to the chipper
socket with the connection lead. Check all
chipper lights and tow vehicle lights are working
correctly.
12. Insert the barrel lock for security.
13. The chipper is now properly attached to the tow
vehicle.
1. Ensure the machine will not roll away after
being disconnected from the tow vehicle.
2. Disconnect the trailer socket from the tow
vehicle.
3. Release the barrel lock.
4. Release the breakaway cable/secondary
coupling.
5. Release the jockey wheel assembly clamp, fully
lower the wheel and tighten the clamp.
6. Wind the jockey wheel handle anticlockwise
until it starts to take the machine weight.
7. Grasp the tow head handle and release the
catch with your thumb.
8. Wind the jockey wheel handle anticlockwise
until the tow head is clear of the ball hitch.
9. Drive the tow vehicle clear of the machine.
10. Level the machine by winding the jockey wheel
handle.
11. The machine is now fully detached from the tow
vehicle.

Page 13
3.2 Lifting the Chipper
The lifting eye is designed for securely holding the chipper’s weight only. Do not use
hoist hook directly on the lifting eye. Use a correctly rated safety shackle. Inspect
lifting eye before each use and do not use if damaged.
Ensure the chamber lid bolts are secure and tightened to the correct torque (86 Nm).
3.3 Storage of the Chipper
For safe storage of the chipper, ensure the following points are met:
1. Chipper to be stored on a level, even surface
2. Hand brake must be applied
3. Hopper tray to be in the ‘Up’ Position

Page 14
4.0 Chipper Operation
1. Fold down hopper tray
2. Start engine
a. Turn ignition key to pre-heat
b. Wait for display to indicate ‘start engine’
c. Turn key to crank engine and release once firing
3. Allow engine to run for 30 seconds at idle, then increase revs to full
4. To feed material into chipper, tap the green button once
5. To stop, push the E-Stop button or push the red stop bar
6. To reverse the feed:
a. Tap the orange button once for a momentary reverse
b. Tap the orange button twice for continuous reverse
7. Stop the machine:
a. Touch the E-stop or push the stop bar
b. Reduce revs to idle
c. Switch off ignition and remove key
8. Before transporting the machine:
a. Sweep out debris from hopper
b. Close hopper tray using the stop bar and engage the locking pins

Page 15
4.1 Control Panel & Ignition
This chipper is fitted with an engine PLC (Programmable Logic Controller) system
that manages the engine, feed and all safety features. The control panel is located
on the right-side panel. Feed and engine speed are controlled with a “No Stress”
function ensuring that cutting conditions are kept within optimum limits. This
maximises throughput while minimising jams and blockages. There will be times
when material is being cut and the feed will momentarily stop until engine speed
increases. At this point, the feed will start without warning. Service warnings shown
below will be displayed at certain intervals. The engine will not start until OK is
pressed.
•First 20 Hour Warning: "Change Hydraulic Oil Filter"
•Every 20 Hour Warning: "Blade and Machine check required see manual"
•Every 500 Hour Service Warning: "Full Service recommended"
4.1.1 Control Panel
1. Control Panel
2. Feed speed adjust
3. Grease bank
4. Throttle
5. Ignition

Page 16
4.1.2 Ignition Switch
1. Key rotation in switch to start
2. Ignition switch positions & function
3. Off
4. Ignition
5. Pre-Heat
6. Spring biased to pre-heat when released
7. Start
8. Key rotation in switch to stop
Turn ignition key clockwise to first position, then to pre-heat, start display will show,
enables pre-heat automatically showing start display + pre-heat.
4.1.3 Control Panel
OR with Pre-heat
Turn ignition key fully clockwise to crank engine. Display will automatically go to P1
If engine fails to start, turn key to off position and start process again. P1 shows
Working Hours and charging indicator text at the screen bottom centre.

Page 17
P2 shows I/O tests. Tests all functions and safety controls.
Pin screen
P3 shows No-Stress Settings
•Actual RPM
•Upper Band - 1400 RPM
•Mid Band –1125 RPM
•Lower Band –925 RPM
•
Pin screen automatically displays if any setting changes are attempted.
P4 shows Pre-Heat Settings
•Enable Pre-Heat –True
•Pre-Heat Time –10
•Crank Time –3
To stop engine, turn off with ignition key
by turning fully anti-clockwise.

Page 18
4.2 Feed Speed Adjustment
The feed speed can be adjusted to suit the material being chipped. Turn dial to align
number with pip. Set feed speed so that the No-Stress operates as little as possible,
this will give the highest throughput. When feeding Leylandii or leafy material, set
feed roller speed to 4.5.
Control valve speed adjustment
Position indicated by pip
0 = minimum
10 = maximum

Page 19
4.3 Emergency Stopping
1. Red Stop Bar
2. Orange reverse button
3. Green forward button
4. E-Stop
Before using the chipper:
1. Start the machine with the ignition key on the control panel.
2. With the engine running at full speed tap the green button (3) and the rollers
will go into forward (chipping mode).
3. Tap the orange button and the rollers will go into a short reverse, tap it again
and the rollers will continue in reverse.
4. To stop the feed rollers, push the red stop bar (1) and the rollers will stop
instantly and or push the e-stop button and whole machine will shut down.
5. If any of these functions fail, turn off the machine and remove the key from the
ignition switch and contact Redwood Global and ask for service.

Page 20
4.4 Feed Jam & Blockages
Be aware that whatever is fed into the machine has to come out of the chute.
Always monitor the state of chip flow out of the chute. If it stops, STOP FEEDING
MATERIAL IMMEDIATELY. Continuing to feed material will further compact a
blockage and make it more difficult to clear.
If the chipping chamber or chute become blocked:
1. Stop the engine and remove ignition key
2. Remove chute and check that it is clear
3. If the chipping chamber is blocked, open the engine cover, then chipping
chamber cover. DO NOT REACH INTO THE CHIPPING CHAMBER WITH
HANDS. Beware that the flywheel within the chipping chamber has two sharp
blades mounted on it and can move causing a serious injury risk. Wearing
protective gloves and using a piece of wood, carefully clean out the chipping
chamber
If feed becomes jammed:
1. Stop the engine and remove
ignition key
2. Open engine and chipping
chamber covers
3. Release feed roller spring tension
on both sides by slackening off the
eye bolt nuts and remove if
necessary
4. Insert feed lift tool and lift top feed
roller to fully open
5. Insert M12 screw into side of feed
chamber and screw completely in
If possible, lower top feed roller
onto the screw to secure in the
open position. This screw acts
as a safety stop once the
obstruction has been removed.
6. There should now be access to
the feed chamber. Beware that
this is the machines cutting zone. The top and bottom feed rollers have sharp
teeth and the flywheel cutting blades are not far from them. DO NOT PUT
HANDS INTO THIS AREA. Wearing protective gloves and using a piece of
wood, carefully clear jammed material inside feed chamber
7. When clear, lift top feed roller via lifting tool, remove top feed M12 securing
screw, lower top feed roller and remove lifting tool
8. Re-assemble feed tensioner springs and close covers
1. Slacken or remove spring tensioner nuts
both sides before lifting feed roller
2. Insert top feed roller lifting tool into slot
and lift
3. Insert m12 screw to hold feed in open
position
Table of contents
Other FORST Chipper manuals
Popular Chipper manuals by other brands
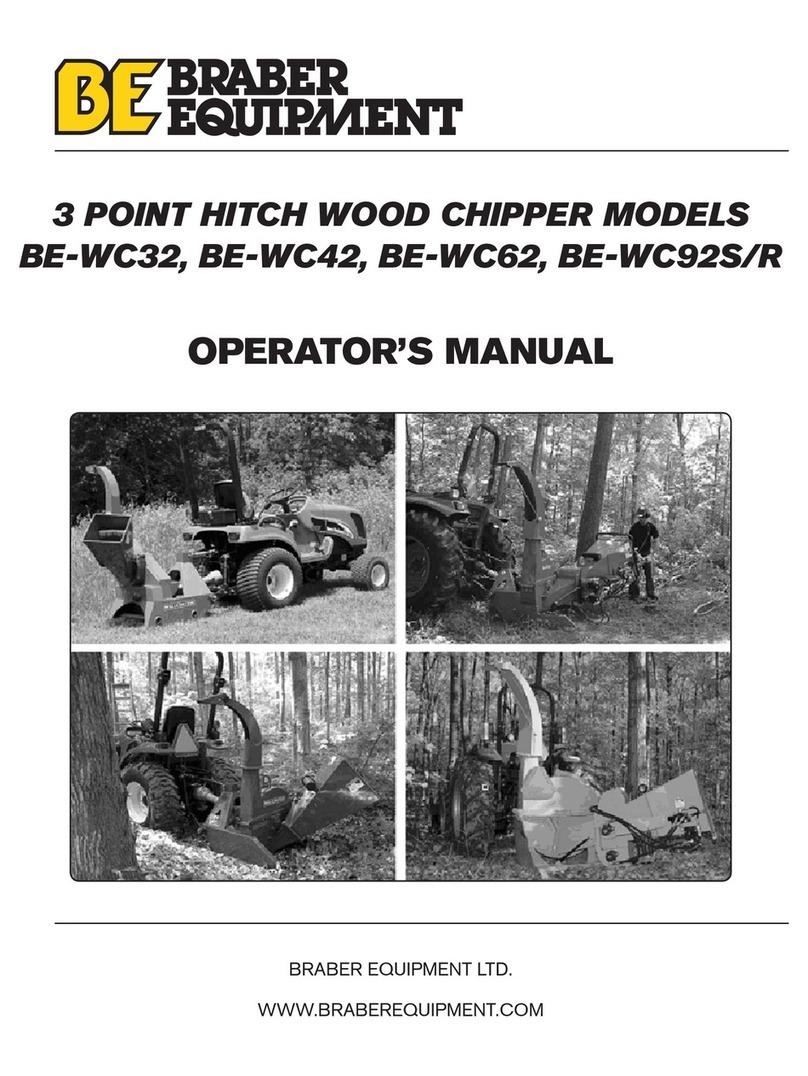
Braber Equipment
Braber Equipment BE-WC32 Operator's manual
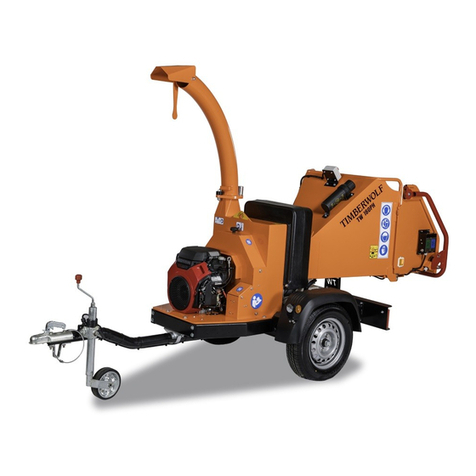
Timberwolf
Timberwolf TW 125PH instruction manual
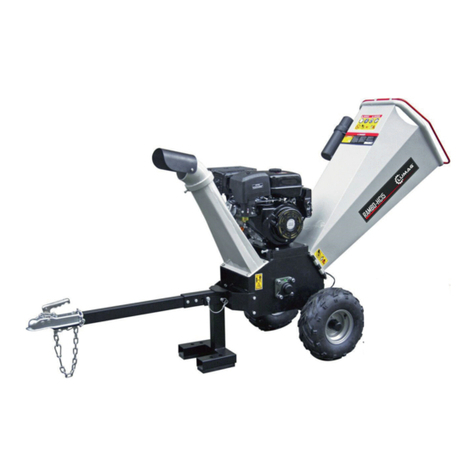
Lumag
Lumag Rambo HC15 Operator's manual
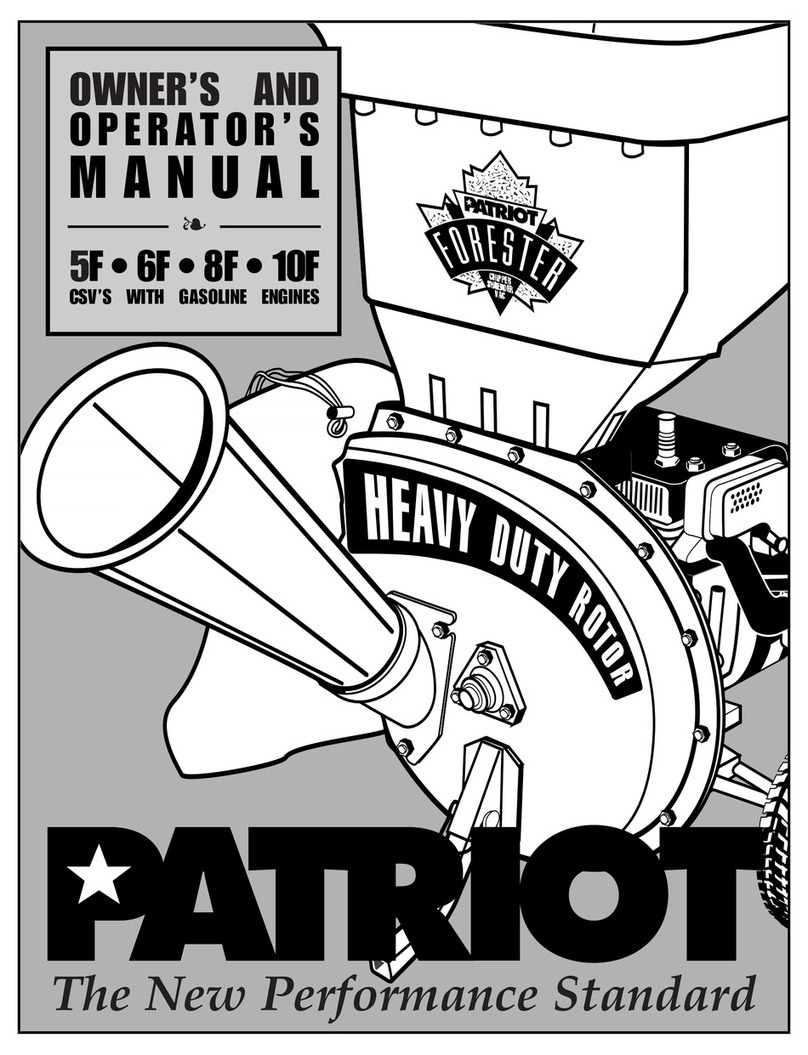
Patriot
Patriot FORESTER Chipper-Shredder-Vac 5F Owner's and operator's manual
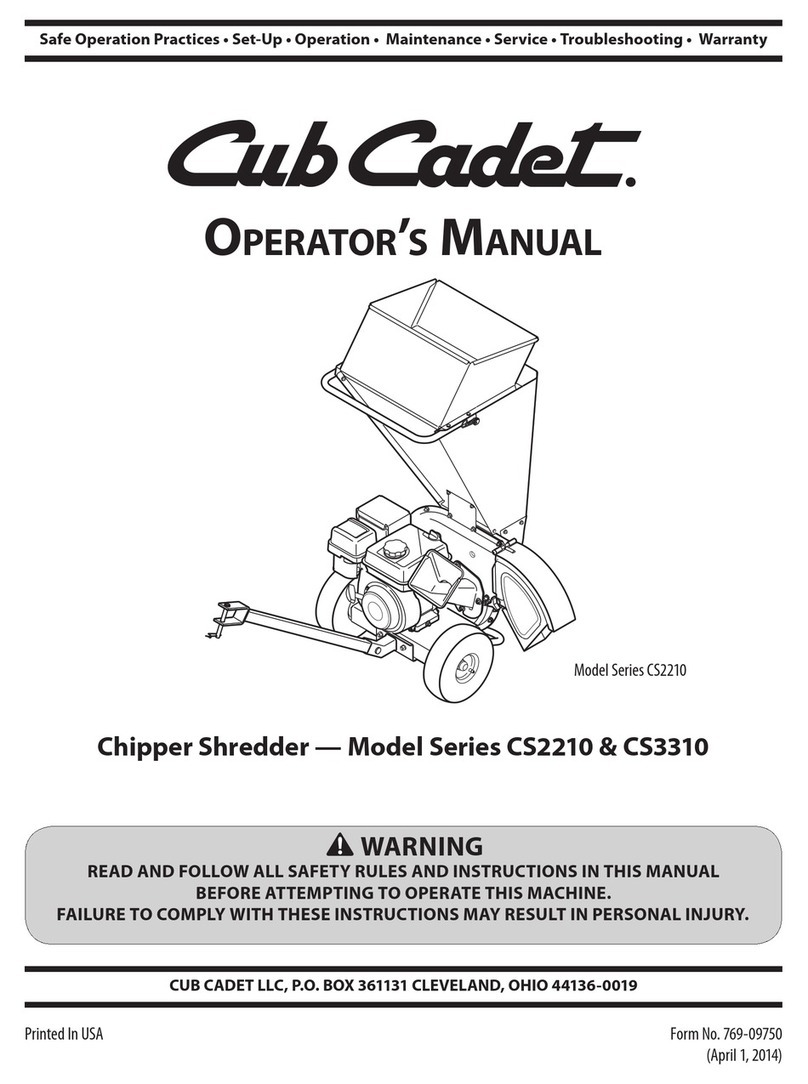
Cub Cadet
Cub Cadet CS 2210 Series Operator's manual
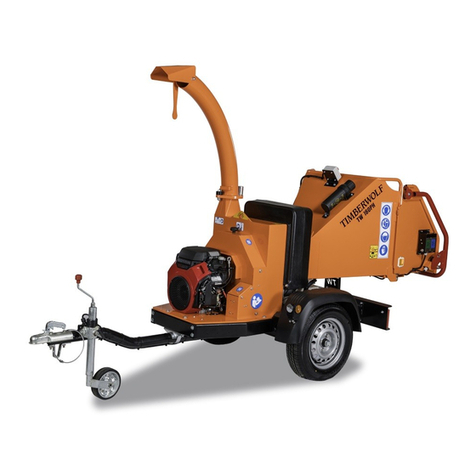
Timberwolf
Timberwolf TW 160PH instruction manual