G.B.C G300 User manual

2
ELECTRONIC GRINDER G300
Original Insgtructions - Rev. 00 -.2018—In compliance with § 1.7.4 of the Machine Directive 2006/42/CE
G.B.C. Industrial Tools S.p.A.
Via Sandro Pertini 41/46 – 25046 Cazzago S.Martino (BS) – Italia – Tel. + 39 030 7451154 – Info: sales@gbcspa.com
Index Pag. 02
Foreword Pag. 03
Warranty General Clauses Pag. 04
Intended Use Of The Machine Pag. 05
Safety Prescriptions Pag. 06
Specific Safety Prescriptions Pag. 07
Standard Equipment Pag. 08
Technical Data Pag. 09
Measures Pag. 10
Grinding Disc Specifications Pag. 11
Electric Controls ( Power Box) Pag. 12
Electric Controls ( Switchboard ) Pag. 13
Function of the Electirc Controls ( Machine Start Up ) Pag. 14
Machine Setup ( Replacing the Abrasive Disc ) Pag. 15
Machine Setup ( Adjustment of the Angle of Incidence ) Pag. 20
Machine Setup ( Use of the Guiding Wheels ) Pag. 21
Machine Setup ( Replacement of the Guiding Wheels ) Pag. 22
Manual Control Functions ( Positioning of the Abrasive Disc ) Pag. 23
Automatic Control Functions ( Machine Start Procedure ) Pag. 25
Automatic Control Functions ( Machine Stopping Procedure ) Pag. 29
Maintenance ( Fumes Extractor Cleaning “where available”) Pag. 30
Maintenance ( Lubricaton of the Moving Parts ) Pag. 32
Troubleshooting Pag. 33

3
ELECTRONIC GRINDER G300
Original Insgtructions - Rev. 00 -.2018—In compliance with § 1.7.4 of the Machine Directive 2006/42/CE
G.B.C. Industrial Tools S.p.A.
Via Sandro Pertini 41/46 – 25046 Cazzago S.Martino (BS) – Italia – Tel. + 39 030 7451154 – Info: sales@gbcspa.com
This Manual is supplied together with the machine it makes reference to. The customer
may apply for further copies to G.B.C. Industrial Tools S.p.A. Our company owns the
copyright of this document and any partial or complete copy or distribution to natural per-
sons or to corporate bodies is strictly forbid-den unless our prior approval to do so is ob-
tained. G.B.C. Industrial Tools S.p.A.
informs its customers that any operation carried out on the machines which is not pre-
scribed in this manual entails the automatic invalidation of the warranty. G.B.C. Indus-
trial Tools S.p.A.
recommends to contact the Maintenance Service in Torbiato di Adro – Italy prior to pro-
ceed with any modification on the machine.
You are invited to scrupulously adhere to the information written on the identifica-
tion tag.
For any further information you are invited to contact us at these numbers:
Tel. +39 - 030 - 7451154
Fax +39 - 030 - 7356629
FOREWORD

4
ELECTRONIC GRINDER G300
Original Insgtructions - Rev. 00 -.2018—In compliance with § 1.7.4 of the Machine Directive 2006/42/CE
G.B.C. Industrial Tools S.p.A.
Via Sandro Pertini 41/46 – 25046 Cazzago S.Martino (BS) – Italia – Tel. + 39 030 7451154 – Info: sales@gbcspa.com
G.B.C. guarantees the reliability of the machine and its conformity to the specifications
herewith reported. The warranty covers the machine in its whole for a time period of one
year from the shipment date (ref. Delivery Note) for any flaw not imputable to the user.
The parts subject to wear are excluded from the warranty at sole discretion of G.B.C..
In case of any operational malfunction arising during the warranty period, G.B.C And its
Maintenance Service, hereinafter called MSS, will remedy this inconvenient free of
charge , both for handwork and for eventual replaced parts, except when the malfunction
is directly or indirectly imputable to misuse or alteration. In any case the machine must
not be disassembled or altered before the shipment. The warranty is valid only when the
warranty document is duly signed by G.B.C. and by a G.B.C. official distributor connect-
ed with the MSS maintenance service.
The shipment of the defective material must be performed within 8 (eight) days from the
notification of the defect and/or the claim and/or the request of technical assistance. On
the contrary the warranty will be void. G.B.C. and MSS obligations will cover the defect
resolution, the general maintenance and the inspection of the parts subject of the claim
only. The component replacement is at G.B.C. discretion only. The shipmen to costs
from and to the MSS as well as the direct and indirect costs rising from repair of the
product are at user’s charge. Any warranty repair or extraordinary repair must be execut-
ed by G.B.C. and MSS, otherwise the warranty will be void.
Any ordinary maintenance performed by the customer/user or by any service centre non
recognized or approved by G.B.C. will not be refunded and will make the warranty void.
The warranty is not valid for cases not listed in this certificate or for damage caused by a
misuse of materials, power supply, negligence, unauthorized modifications, atmospheric
events, acts of vandalism, incautious handling and/or transport, use of non original
G.B.C. parts and damage for causes not specified by G.B.C. and for which G.B.C. de-
clines any responsibility. G.B.C. reserves the right to modify and to improve its products
without any obligation to modify equipment and components already supplied. Nobody is
authorized to modify the conditions herewith contained or to issue any on behalf of
G.B.C. The claim terms for defects and/or damages in the material or of the ordered
quantities, are those pre-scribed by the Civil Code; the goods acceptance entails the
buyer to automatically accept the above mentioned warranty clauses.
WARRANTY GENERAL CLAUSES

5
ELECTRONIC GRINDER G300
Original Insgtructions - Rev. 00 -.2018—In compliance with § 1.7.4 of the Machine Directive 2006/42/CE
G.B.C. Industrial Tools S.p.A.
Via Sandro Pertini 41/46 – 25046 Cazzago S.Martino (BS) – Italia – Tel. + 39 030 7451154 – Info: sales@gbcspa.com
THE G300 CAN BE USED ONLY BY SPECIALIZED OPERA-
TORS WHO HAVE ATTENDED THE NECESSARY FORMA-
TION
UPON SPECIFIC FORMATION WE DO ARE NOT IN POSI-
TION TO WARN ABOUT ANY EVENTUAL IMPROPER USE
OF THE MACHINE
The grinder G300 represents a crucial evolution of the grinding processes in the field of metal
metalworking and heavy industries as well as an evolution of the general grinding processes
granting the following advantages:
− Significant reduction of the processing times in comparison to the normal grinders em-
ployment;
− Material removal high rate;
− No thermal alteration on the welding area;
− Working homogeneity;
− Elimination of vibrations;
− Improvement of the working conditions and safety;
− Significant reduction of injury risks (flying debris, tendinitis and sprains, stress fractu-
res) related to the extended use of hand grinders.
INTENDED USE OF THE MACHINE

6
ELECTRONIC GRINDER G300
Original Insgtructions - Rev. 00 -.2018—In compliance with § 1.7.4 of the Machine Directive 2006/42/CE
G.B.C. Industrial Tools S.p.A.
Via Sandro Pertini 41/46 – 25046 Cazzago S.Martino (BS) – Italia – Tel. + 39 030 7451154 – Info: sales@gbcspa.com
The authorized operator in any case will not have to disregard the basic safety rules such as:
Using gloves and goggles (safety gear supplied by the company responsible for the site or
for the building)
To properly illuminate the working area
Ensure you are operating in an area which grants free movements (at least 1,5 metres around
the operator)
Do not replace the control system and do not replace parts with non original spare parts, and
do not project violent water squirts on the machine
Keep the hands away from hot and sharpened parts.
G.B.C. Industrial Tools S.p.A. remarks that for any non specified circumstances it is neces-
sary to obtain the authorization of the manufacturer.
G.B.C. Industrial Tools S.p.A. designs and assembles its machines in strict compliance with the
safety regulations provided by the applicable EC directives and by the Italian laws regulat-ing
this matter.
G.B.C. Industrial Tools S.p.A. declines any responsibility for misuse of its machines and their
use when in contrast with the regulation listed hereinafter and with the use and maintenance in-
structions hereto.
• Carefully read ALL the following regulations and the instructions herewith attached before
starting any operation.
• Carefully ensure that the operator and the foreman using the machine are fully aware of all
the regulations and all the instructions and that they are qualified to operate the unit.
• Strictly attain to the indications given by the international symbols applies on the ma-chine
and/or on its case.
• Do not perform any maintenance operation when the machine is plugged to the power sup-
ply.
• Before every use, ensure the power supply connections to be conform to the specs given by
our manual.
SAFETY PRESCRIPTIONS

7
ELECTRONIC GRINDER G300
Original Insgtructions - Rev. 00 -.2018—In compliance with § 1.7.4 of the Machine Directive 2006/42/CE
G.B.C. Industrial Tools S.p.A.
Via Sandro Pertini 41/46 – 25046 Cazzago S.Martino (BS) – Italia – Tel. + 39 030 7451154 – Info: sales@gbcspa.com
SPECIFIC SAFETY PRESTCRIPTIONS FOR
THE G300
- WEAR ULTRAVIOLET PROTECTION GOGGLES
- WEAR EAR PROTECTION
- WEAR DUST MASK
- Apply a tag showing the grinding disc maximum speed (60 m/s). This speed must al-
ways be lower than the maximum speed sustainable by the disc which is declared by
the manufacturer (80 m/s).

8
ELECTRONIC GRINDER G300
Original Insgtructions - Rev. 00 -.2018—In compliance with § 1.7.4 of the Machine Directive 2006/42/CE
G.B.C. Industrial Tools S.p.A.
Via Sandro Pertini 41/46 – 25046 Cazzago S.Martino (BS) – Italia – Tel. + 39 030 7451154 – Info: sales@gbcspa.com
La macchina viene fornita al cliente corredata di:
• N.1 24mm Double Ended Hexagon Wrench
• N.1 80-120mm Hook Wrench
• N.1 24mm Wrench
• N.2 Hook Wrenches 40-42
• N.1 6mm Allen Key
• N.1 Pliers for Elastic Rings
• N.1 Set of shims ( for grinding discs with thickness 10-12-14)
• Set of wheels for grooves from 10 a 42mm
• Instruction manual
G300
SERVICE TOOLS
INSTRUCTION MANUAL
STANDARD EQUIPMENT
SET OF WHEELSSET OF SHIMS

9
ELECTRONIC GRINDER G300
Original Insgtructions - Rev. 00 -.2018—In compliance with § 1.7.4 of the Machine Directive 2006/42/CE
G.B.C. Industrial Tools S.p.A.
Via Sandro Pertini 41/46 – 25046 Cazzago S.Martino (BS) – Italia – Tel. + 39 030 7451154 – Info: sales@gbcspa.com
CARATTERISTICHE TECNICHE
TECHNICAL SPECIFICATIONS
FEATURES
UNIT
MEASU-
RE
VALUE NOTES
Power supply (V) 400 -
Main Motor Power (KW) 5.50 -
Air Extractor Power (KW) 0.85 -
Feeding Motor Power (KW) 0.12 -
Disc Motor Power (KW) 0.03 -
Total Power (KW) 6.5 -
Grinding Disc Speed (RPM) 4000 -
Grinding Disc Maximum Diameter (mm) 300 -
Disc Fixing Hole Diameter (mm) 40 -
Allowed Grinding Discs Thickness (mm) 8÷10÷12÷14 -
Gringing Disc Peripheral Speed (m/s) 60 Con disco mola non
consumato
Cutting Depth (mm) 0÷70 Con disco mola non
consumato
Load Exertion (Kg) 20÷40
Sforzo che dipende
dalla profondità di
taglio
Recommended Feeding Speed (mm/min) 500÷2600 Velocità ideale tra
1000 e 2000
Constant noise at 2mt from the grinding disc
Noise peak at 2mt from the disc
(dB A)
(dB B)
80÷85
110÷120
Vedi nota nella
pagina successiva
Machine weight (Kg) 198
Completa di
corredo

10
ELECTRONIC GRINDER G300
Original Insgtructions - Rev. 00 -.2018—In compliance with § 1.7.4 of the Machine Directive 2006/42/CE
G.B.C. Industrial Tools S.p.A.
Via Sandro Pertini 41/46 – 25046 Cazzago S.Martino (BS) – Italia – Tel. + 39 030 7451154 – Info: sales@gbcspa.com
NOTE:
G.B.C. Industrial Tools S.p.A. declares that every machine is tested on steels commonly used in mechani-
cal and metal work fabrication with 30mm wall thickness. The figures listed in the above chart are de-
tected by a phonometer certified by an acoustic calibrator model DELTA HOM HD 9102 certificato
LAT (former SIT) N. SIT 03229/09 and we confirm the figures recorder are in compliance with the re-
gulation EN 60745.
Therefore following the evaluation of the environmental risks on the workplace, regulated by the law
decree 81/08 and following modifications, in compliance with the directive 2003/10/CE, and of the art.190
of such law decree, the personnel authorized to operate the G300 must be trained and educated in re-
gards to the above directive and must be equipped with the personal protective equipment (PPE) and
acoustic detection system on request of the operator himself or if deemed necessary by the medical staff.
MEASURES

11
ELECTRONIC GRINDER G300
Original Insgtructions - Rev. 00 -.2018—In compliance with § 1.7.4 of the Machine Directive 2006/42/CE
G.B.C. Industrial Tools S.p.A.
Via Sandro Pertini 41/46 – 25046 Cazzago S.Martino (BS) – Italia – Tel. + 39 030 7451154 – Info: sales@gbcspa.com
GRINDING DISC SPECIFICATIONS
EXAMPLE OF MARKING OF THE GRINDING DISC
THE GRINDING DISC WILL HAVE TO HAVE THE FOLLOWING FEATURES:
Max. OD 300 mm
Thickness: 08 ÷12 mm
Mounting hole : Ø40mm
RPM max.5090/min
Max.80m/s
Reference regulations: EN 12413 ÷ ANSI B7.1
Expiry date and binding agent are clearly stamped on the disc.

12
ELECTRONIC GRINDER G300
Original Insgtructions - Rev. 00 -.2018—In compliance with § 1.7.4 of the Machine Directive 2006/42/CE
G.B.C. Industrial Tools S.p.A.
Via Sandro Pertini 41/46 – 25046 Cazzago S.Martino (BS) – Italia – Tel. + 39 030 7451154 – Info: sales@gbcspa.com
ELECTRIC CONTROLS
Electrical panel :
1 - ON/OFF Master Switch
2 - White light (Tension detection)
3 - Red light (Error)
3
1
2

13
ELECTRONIC GRINDER G300
Original Insgtructions - Rev. 00 -.2018—In compliance with § 1.7.4 of the Machine Directive 2006/42/CE
G.B.C. Industrial Tools S.p.A.
Via Sandro Pertini 41/46 – 25046 Cazzago S.Martino (BS) – Italia – Tel. + 39 030 7451154 – Info: sales@gbcspa.com
CONTROL PANEL :
1 - Trolley Speed Regulator
2 - Grinding Disc Push Regulator
3 - Grinding Disc Lowering Speed Regulator (Manual Mode)
4 - Starter Switch
5 - Grinding Disc Start/stop Switch
6 - Grinding Disc lifting/lowering switch (manual / automatic)
7 - Emergency Stop
8 - Manuale / Automatic Mode Switch
9 - Trolley Feeding Switch Manual / Auto
10 –Trolley Feeding Stop Button
123
45678910

14
ELECTRONIC GRINDER G300
Original Insgtructions - Rev. 00 -.2018—In compliance with § 1.7.4 of the Machine Directive 2006/42/CE
G.B.C. Industrial Tools S.p.A.
Via Sandro Pertini 41/46 – 25046 Cazzago S.Martino (BS) – Italia – Tel. + 39 030 7451154 – Info: sales@gbcspa.com
MACHINE STARTING PROCEDURE
ACCENSIONE MACCHINA
1 - Start Lever
1

15
ELECTRONIC GRINDER G300
Original Insgtructions - Rev. 00 -.2018—In compliance with § 1.7.4 of the Machine Directive 2006/42/CE
G.B.C. Industrial Tools S.p.A.
Via Sandro Pertini 41/46 – 25046 Cazzago S.Martino (BS) – Italia – Tel. + 39 030 7451154 – Info: sales@gbcspa.com
GRINDING DISC INSTALLATION AND REMOVAL
The installation or the replacement of the grinding disc are operations to be executed with
the very same procedure as described below:
1) Open the metal latches located on the perimeter of the protection as shown in the photo
n.1
2) Remove the protection using the handle.
1
2

16
ELECTRONIC GRINDER G300
Original Insgtructions - Rev. 00 -.2018—In compliance with § 1.7.4 of the Machine Directive 2006/42/CE
G.B.C. Industrial Tools S.p.A.
Via Sandro Pertini 41/46 – 25046 Cazzago S.Martino (BS) – Italia – Tel. + 39 030 7451154 – Info: sales@gbcspa.com
− 3) Remove the fixing screw using the specific wrench supplied with the machine.
− 4) Pull out the spindle guard.
3
4

17
ELECTRONIC GRINDER G300
Original Insgtructions - Rev. 00 -.2018—In compliance with § 1.7.4 of the Machine Directive 2006/42/CE
G.B.C. Industrial Tools S.p.A.
Via Sandro Pertini 41/46 – 25046 Cazzago S.Martino (BS) – Italia – Tel. + 39 030 7451154 – Info: sales@gbcspa.com
− 5) Take a new grinding disc and the shim stamped with the details of the same disc
thickness among those allowed by the technical specifications of the machine.
− 6) Insert the disc and the shim on the spindle guard as shown in the picture.
− 7) Insert the spindle guard coupled with the abrasive disc in place making sure to
match the internal hexagon pattern of the screws. N.B. To achieve a fast and correct
fixing of the grinding disc engage the other side of the spindle guard with the hook
wrench and leave it laying against the protection so that you can easily fasten the fi-
xing screw with one hand only.
6
7
5

18
ELECTRONIC GRINDER G300
Original Insgtructions - Rev. 00 -.2018—In compliance with § 1.7.4 of the Machine Directive 2006/42/CE
G.B.C. Industrial Tools S.p.A.
Via Sandro Pertini 41/46 – 25046 Cazzago S.Martino (BS) – Italia – Tel. + 39 030 7451154 – Info: sales@gbcspa.com
− 8) Install back the protection removed at the beginning of the procedure.
8
8

19
ELECTRONIC GRINDER G300
Original Insgtructions - Rev. 00 -.2018—In compliance with § 1.7.4 of the Machine Directive 2006/42/CE
G.B.C. Industrial Tools S.p.A.
Via Sandro Pertini 41/46 – 25046 Cazzago S.Martino (BS) – Italia – Tel. + 39 030 7451154 – Info: sales@gbcspa.com
ADJUSTMENT OF THE ANGLE OF INCIDENCE
− 1) Loose the threaded locking nut with the specific tool supplied with the machine.
− 2) Screw the locking nut back on the threaded rod for at least 5mm as shown in the
picture.
− 3) loose the positioning nut with a counter-clockwise rotation using the specific
wrench supplied with the machine service tool kit.
2
1
3

20
ELECTRONIC GRINDER G300
Original Insgtructions - Rev. 00 -.2018—In compliance with § 1.7.4 of the Machine Directive 2006/42/CE
G.B.C. Industrial Tools S.p.A.
Via Sandro Pertini 41/46 – 25046 Cazzago S.Martino (BS) – Italia – Tel. + 39 030 7451154 – Info: sales@gbcspa.com
− 4) Adjust the angle of incidence by rotating the central
screw in one direction or the other with the specific Allen Key
− 5) N.B. The angle of incidence of the machine can be adjusted from 0° to maximum
of 5° as shown in the picture.
− 6) Once the required angle of incidence is reached the operator will have to fasten
the positioning nut while keeping in position the central screw as shown in the pictu-
re.
− 7) Screw back the locking nut making sure it is properly fastened by acting simulta-
neously on the threaded rod as well with two wrenches as shown in the picture.
67
45
Table of contents
Other G.B.C Grinder manuals
Popular Grinder manuals by other brands
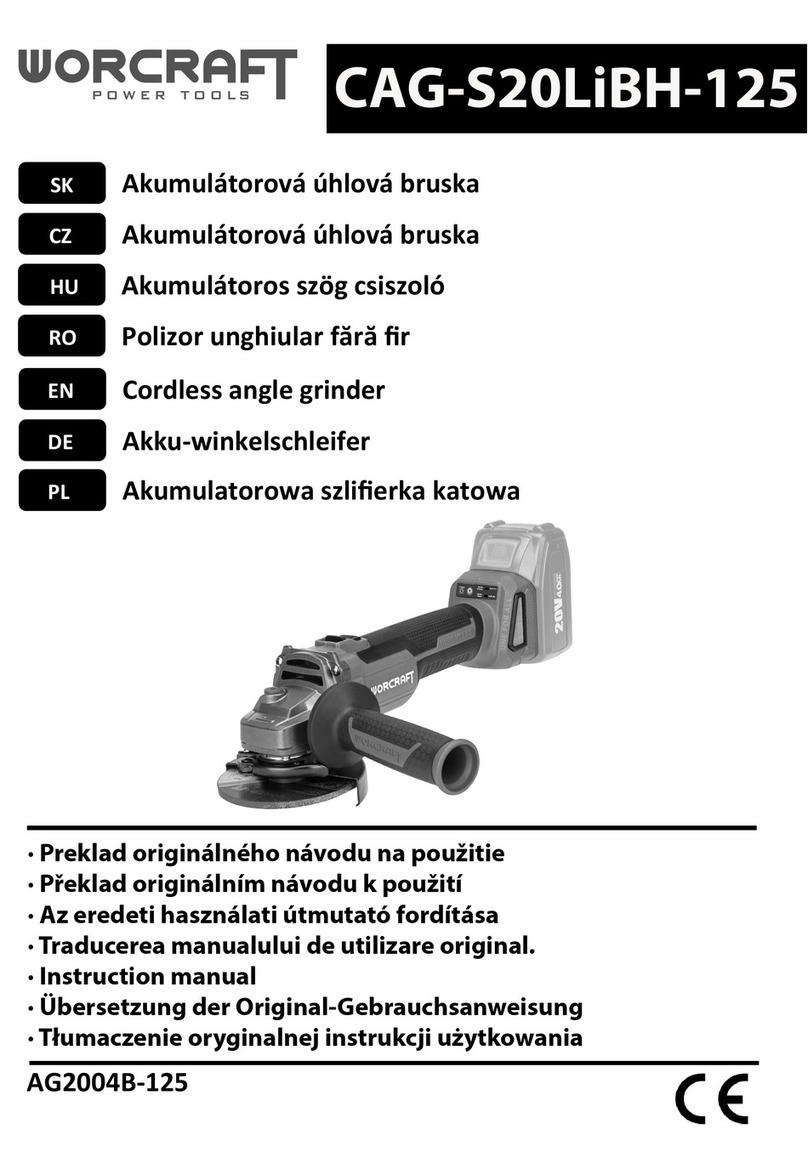
Worcraft
Worcraft CAG-S20LiBH instruction manual

Parkside
Parkside PNTS 250 A1 Translation of the original instructions

Ferm Industrial
Ferm Industrial AGM1117P Original instructions

Milwaukee
Milwaukee AG 8-100 Original instructions

Nakayama
Nakayama ES3010 manual
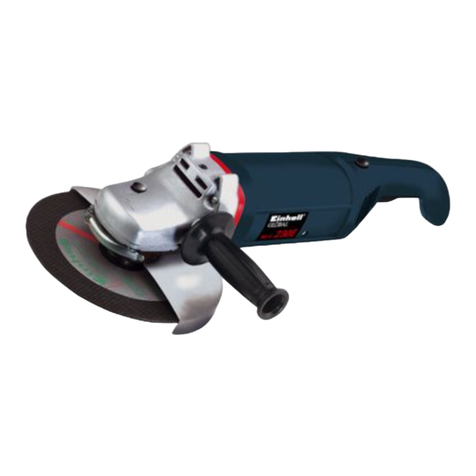
Einhell Global
Einhell Global WS-G 230 E operating instructions