Gefa HG1 User manual

HG1
ARMATURENTECHNIK
Original instructions
Germaniastraße 28 • D-44379 Dortmund
Tel.: +49 (0)231 / 61 00 9-0 • Fax: +49 (0)231 / 61 00 9-80
Internet: www.gefa.com • E-Mail: [email protected]
Version 0 • Dokument-Nr. 74572811

HG1
Table of contents
1 Imprint .............................................................................................................................................................3
2 Safety instruction ...........................................................................................................................................4
2.1 Used information and warning signs.........................................................................................................4
2.2 Intended Use ............................................................................................................................................5
2.3 User ..........................................................................................................................................................5
2.4 Improper use.............................................................................................................................................5
2.5 Due diligence of the operator....................................................................................................................5
2.6 Product safety...........................................................................................................................................6
2.7 Product-specific dangers ..........................................................................................................................6
2.8 Outflowing media ......................................................................................................................................6
2.9 Failure of actuator operating power ..........................................................................................................6
2.10 Mounting of actuators ...............................................................................................................................6
3 Scope of delivery............................................................................................................................................7
3.1 Exploded view DN50-300 .........................................................................................................................7
3.2 Exploded view DN350-500 .......................................................................................................................8
3.3 Exploded view DN600 ..............................................................................................................................9
3.4 Bearing protection and vacuum seal DN50-600 DN50-600 (optional)......................................................9
3.5 Components high performance butterfly valve series HG ......................................................................10
4 Transport and storage .................................................................................................................................12
5 Mounting and initial operation ....................................................................................................................13
5.1 Installation conditions .............................................................................................................................13
5.2 Installation position .................................................................................................................................14
5.3 Initial operation .......................................................................................................................................15
5.4 Mounting instructions..............................................................................................................................15
5.5 Impermissible operation..........................................................................................................................17
6 Operation.......................................................................................................................................................18
7 Maintenance and repair ...............................................................................................................................19
7.1 Maintenance ...........................................................................................................................................19
7.2 Tighten/Replacing the Gland Packing ....................................................................................................19
7.3 Replacing the Seat .................................................................................................................................19
8 Decommissioning and disposal..................................................................................................................21
8.1 Decommissioning ...................................................................................................................................21
8.2 Removing of the valve ............................................................................................................................21
8.3 Disposal ..................................................................................................................................................22
9 How to proceed in case of malfunctions....................................................................................................23
10 Annex.............................................................................................................................................................25
10.1 Mounting of operating elements .............................................................................................................25
10.1.1 Mounting of the hand lever ......................................................................................................... 26
10.1.2 Mounting of the MULTITOP mounting plate ............................................................................... 26
2 / 26 Version 0 • Dokument-Nr. 74572811

HG1
1 Imprint
Read the operating instructions thoroughly before installing your valve. Failure to follow these instructions or the
warning and safety labels could result in serious injury or property damage. These operating instructions must
be available to all users at all times. GEFA Processtechnik GmbH is not liable for unauthorized changes of the
device or for improper use.
All rights reserved GEFA Processtechnik GmbH
GEFA Processtechnik GmbH
Germaniastraße 28
44379 Dortmund, Germany
Tel: +49(0)231-61009-0
Fax: +49(0)231-61009-80
E-Mail: [email protected]
3 / 26
Version 0 • Dokument-Nr. 74572811
Internet: www.gefa.com • E-Mail: [email protected]

HG1
4 / 26 Version 0 • Dokument-Nr. 74572811
Internet: www.gefa.com • E-Mail: [email protected]
2 Safety instruction
This chapter contains basic instructions for the safe handling of this valve.
Observe all instructions for transport, storage, installation, commissioning, maintenance and decommissioning
as well as disposal. In explosive arenas, the relevant standards, the specifications of the manufacturer and the
risk assessment must be observed
Failure to observe safety instructions may result in personal injury and / or property damage.
The safety instructions in this documentation are uniform and marked with an icon on the left side of the note. A
signal word above the text indicates the hazard level. The color of the hazard word additionally signals the haz-
ard level.
The warning notice also includes:
>Nature and origin of danger.
>Possible consequences of the danger!
>Measures to avoid the danger.
If more than one hazard level occurs, the safety notice for the highest level is used.
Nature and origin of danger.
Possible consequences of the danger!
Measures to avoid the danger.
Signal words for warnings
The signal word identifies the severity of the hazard that occurs if it is not avoided.
DANGER means: Serious personal injury threatens immediately.
WARNING means: Serious personal injury may be imminent.
CAUTION means: Light / medium personal injury threatens immediately.
NOTICE means: property damage threatens directly or possibly.
2.1 Used information and warning signs
The warning sign represents a source of danger. Warning signs are located
>At the device near the source of danger.
>In the operating instructions before the activity is described, which can be a hazard.
The following information and warning signs are used in this operating manual:
Safety Notice General
Wear safety gloves
Wear safety shoes
Observe and obey all local safety regulations, safety precautions and operating instructions. These apply in ad-
dition to or in addition to the safety instructions stated and shown in this manual. If contradictory identifications
occur, speak with the responsible authority. All PPE (personal protective equipment) must be provided by the
user of the valve.

HG1
2.2 Intended Use
The valve is used exclusively for shutting off, throttling and regulating media flows under the Consideration of
the data given on the valve and technical details given in this manual Data, diagrams, applications described
and only in connection with the components, which are recommended by GEFA Processtechnik GmbH, ap-
proved and mentioned in this documentation. The faultless and safe operation of the device requires proper
transport, proper storage and installation as well as careful operation and maintenance. This documentation is
part of the device and must be available at all times. Observe all safety regulations which are listed in this docu-
mentation. The strength according to PED is considered with a simplified calculation on alternating stress. Quasi
static operation has been assumed. The suitability of the product wetted parts used and their chemical resist-
ance must be clarified before commissioning the system. The usual flow rates for this valve must not be ex-
ceeded. Changes or modifications to the device are not permitted. The improper use leads to the exclusion of
any liability claims.
2.3 User
All work on the unit may only be performed by qualified personnel and together with this documentation. Quali-
fied persons within the meaning of this documentation are those who are authorized to assemble, commission
and mark devices, systems and connections in accordance with the standards of safety technology.
2.4 Improper use
Do not mount the valve if:
>Parts are obviously damaged
>There is not enough free space to ensure easy operation of the hand levers, handwheels and manual emer-
gency shifts.
or the fitting as:
>Support member of the pipe guide is used.
>Riser is used.
>This includes the actuators such as hand levers, gear operator, actuator, feedback and control systems.
2.5 Due diligence of the operator
It is the duty of care of the operator to plan and control all actions that ensure safety in the workplace.
In particular, the operator must ensure that:
>the valve is only used as intended.
>the valve is only operated in a perfect, fully functional condition.
>the safety regulations relevant to the installation site and generally applicable technical rules for the installa-
tion location must be observed.
>the permissible materials of the wetted parts are suitable for the media, pressures and temperatures used.
The operator must also ensure that the responsible personnel:
>has the necessary qualifications to work with the valve.
>has read and understood the operation instructions before working with the valve and follows the described
instructions.
>can clearly identify all safety signs required for the work.
>All necessary protective equipment is provided and must be worn.
5 / 26
Version 0 • Dokument-Nr. 74572811
Internet: www.gefa.com • E-Mail: [email protected]

HG1
6 / 26 Version 0 • Dokument-Nr. 74572811
Internet: www.gefa.com • E-Mail: [email protected]
2.6 Product safety
The valves of GEFA Processtechnik GmbH correspond to the state of the art and the prescribed safety rules,
but nervertheless hazards can occur in connection with valves. The valve may only be operated in proper condi-
tion, in the intended area and under consideration of all associated documentation. Any change to the valve
may only be made after approval by the manufacturer. The basic requirement for trouble-free operation is
proper connection of the electrical, hydraulic and pneumatic lines.
WARNING Improper use / excessive stress of the valve
The use of material incompatible media or operating outside the approved specification, exceeding
the manufacturer's approved pressure and temperature limits, the use of the valve as a climbing
aid, including all actuators (hand lever, gearbox, drive, feedback and control systems), and from
the outside acting loads and shear forces due to additional stresses can lead to failure of the pres-
sure-bearing parts and bursting of the valve.
2.7 Product-specific dangers
WARNING Dangers relating to a valve
The flow medium, the control pressure, the temperature and moving parts can potentially pose a
hazard. These potential hazards must be prevented by appropriate activities by the operator.
It is not permissible to reach into the valve at any time. In general, there is a risk of injury to moving
parts.
2.8 Outflowing media
WARNING Outflowing media
If harmful or environmentally hazardous media leak out (e.g. leaks or disassembly of the valve),
they must be collected in such a way that there are no hazards to persons or the environment. Ob-
serve all applicable local regulations that apply to the disposal of the respective medium and the
valve.
2.9 Failure of actuator operating power
WARNING Failure of actuator operating power
In case of failure of actuator operating power, the valve could go into a state of insecurity for its in-
tended use.
Choose your valve in such a way that if the actuator operating power fails, the valve can change
into a safe operating state for its intended use.
2.10 Mounting of actuators
Observe the following notes for mounting of a valve actuator.
CAUTION Ventilation of pneumatic components
a) During venting operations on pneumatic components, increased noise may occur.
ðPrevent this by suitable measures (silencer).
NOTICE Mounting of actuators
Actuators must be installed in alignment with the valve stem. Tensions can lead to increased wear
or leakage of the stem seal.
The weight of a built-up actuator must not load the stem of the valve on one side. Therefore actuat-
ors must be intercepted if necessary - without fixation.
Pneumatic or hydraulic actuators must be operated at the agreed design pressure. Pay attention to
the maximum permissible operating pressure.

HG1
3 Scope of delivery
3.1 Exploded view DN50-300
(The description of the components can be found at the end of the chapter)
7 / 26
Version 0 • Dokument-Nr. 74572811
Internet: www.gefa.com • E-Mail: [email protected]

HG1
8 / 26 Version 0 • Dokument-Nr. 74572811
Internet: www.gefa.com • E-Mail: [email protected]
3.2 Exploded view DN350-500
(The description of the components can be found at the end of the chapter)

HG1
3.3 Exploded view DN600
(The description of the components can be found at the end of the chapter)
9 / 26
Version 0 • Dokument-Nr. 74572811
Internet: www.gefa.com • E-Mail: [email protected]

HG1
10 / 26 Version 0 • Dokument-Nr. 74572811
Internet: www.gefa.com • E-Mail: [email protected]
3.4 Bearing protection and vacuum seal DN50-600 DN50-600 (optional)
Vacuum
seal
Bearing
protection
Bearing
protection
(The description of the components can be found at the end of the chapter)

HG1
3.5 Components high performance butterfly valve series HG
Pos. Description
1.1 Body
1.2 Disc with stem
1.2.1 Disc
1.2.2 Stem
1.2.3 Straight pin
1.2.4 Tapered pin (≤ DN300)
1.3 Seat
1.4 Insert ring
1.5 Set screw / Cylinder screw
1.6 Bearing
1.7 Gland packing
1.7.1 Gland packing
1.7.2 Gland packing
1.8 Stopfbuchse
1.9 Gland
1.10 Hexagon screw
1.11 Hexagon nut
1.12 Limit stop
1.13 Set screw
1.14 Bottom flange
1.15 Axial securing device
1.16 Bottom flange seal
1.17 O-ring
1.18 Hexagon screw
1.19 Sealing tape (optional)
1.20 Sealing tape (optional)
1.30 O-ring (optional)
1.31 O-ring (optional)
1.32 O-ring (optional)
(See illustrations in this chapter)
11 / 26
Version 0 • Dokument-Nr. 74572811
Internet: www.gefa.com • E-Mail: [email protected]

HG1
12 / 26 Version 0 • Dokument-Nr. 74572811
Internet: www.gefa.com • E-Mail: [email protected]
4 Transport and storage
WARNING Transport of the valve
Failure to comply with the transport instructions can result in significant personal injury(even death)
and property damage.
NOTICE Transport
The transport may only be carried out by qualified and authorized personnel with suitable protect-
ive equipment.
In order to guarantee a faultless function, pay attention to the following during transport and storage:
>The valve must be transported and stored dry and clean.
>During transport and intermediate storage the high performance butterfly valve should not be outside a tem-
perature range of -15°C and +30°C.
>In humid rooms, a drying material or heating must be used to avoid condensation
>If the valves are painted (coated) on the outside, this coating must remain without damage, otherwise the
faulty spots must be repaired immediately!
>The factory-adjusted basic setting (position of the disc at delivery) must not be changed.
The transport packaging protects the valve against soiling and damage, therefore it is important:
>do not remove the packaging until the valve is going to be installed.
To prevent damage and life-threatening injuries when transporting the valve:
>Impact and vibrations must be avoided.
>Only use suitable and approved load handling equipment and slings.
>When selecting the load suspension and slinging equipment, take the weight of the valve into account.
>The transportation routes must be blocked and marked, that no unauthorized person can enter the danger
zone.
>Do not suspend large valve on the gearbox or flange! Protect the shut-off element and flange sealing sur-
faces against any damage!
>For valves that are delivered without actuation, the shut-off element is not secured against adjustment. It
must be transported in such a way that it can not be opened from the closed position by external influences
(eg vibration).

HG1
5 Mounting and initial operation
Before installing and initial operation of the valve, the customer is obliged to check the completeness and cor-
rectness of the scope of delivery. In particular, the suitability of the materials and the operating parameters such
as nominal diameter, pressure rating, medium, operating temperatures and, if applicable, control characteristics
should be verified with the intended operating conditions and the ambient conditions (piping system). If you
have ordered additional parts or a customized valve, please check the details carefully.
WARNING damaged / incomplete valve
Damaged or incomplete valves no longer meet the safety requirements and must not be installed.
WARNING Hazardous media
Work on parts in contact with hazardous media may only be carried out with appropriate protective
equipment.
CAUTION Earthing the valve
If the valve is supplied with anti-static device and used in potentially explosive zones, the body of
the valve must be connected effectively at site with the potential compensation cable before the
valve is put into operation.
NOTICE Avoid vibration
Vibrations, water hammer and cavitation as well as abrasive media components lead to damage to
the valve and impair the service life.
NOTICE Installation at high suspended matter concentrations
If the concentration of suspended matter is high (e.g. media which are very viscous), it is recom-
mended to mount the high performance butterfly valve with valve shaft in horizontal position and
stop boss facing upwards.
NOTICE Approach end position „open”!
The end position is always approached from the open position. This is the only way to ensure that
any clearance from the drive (eg gearbox) that is possibly present has no influence on the end pos-
ition. If the exact end position is exceeded, bring the valve back into the open or partly open posi-
tion. Then approach the end position again from the open position.
13 / 26
Version 0 • Dokument-Nr. 74572811
Internet: www.gefa.com • E-Mail: [email protected]

HG1
14 / 26 Version 0 • Dokument-Nr. 74572811
Internet: www.gefa.com • E-Mail: [email protected]
5.1 Installation conditions
In order to ensure trouble-free functioning of the valve, pay attention in the provided range of the fitting:
▪that the piping system must be routed, that damaging shear and bending stresses can not affect the valve
body.
▪that there is enough free space available, that the operation of the hand lever, the hand wheel and the emer-
gency and switching devices is easily possible.
>The valve must be installed between pipeline flanges according to DIN 2501 or ANSI B16.5. It should be
taken into account, that a valve which is designed for a particular flange standard cannot be normally used
for other flanges.
>If pipeline flanges are to be used which are not in accordance with the specifications of the order, the manu-
facturer is to be consulted.
>Pipelines always have to be run in such a way that damaging shear and bending stresses cannot act on the
valve body.
>The surfaces of the pipeline flanges between which the valve is installed have to be parallel to one another,
the sealing surfaces must be clean and without damage. No cross marks may be visible.
>Flanges and pipes must not be completely welded when the valve is installed, as the valve can be dam-
aged.
>The valve is installed with two suitable seals between two pipe flanges.
>Screws, nuts and seals are not included in the manufacturer scope of supply, but must be available during
installation. All flange gaskets intended for the application can be used.
>The "clearance" of the mating flanges - including inner coating - has to be sufficient to allow the disc to be
fully opened without touching (ØDi ≥ ØL + 6 mm). This must be checked before the valve is installed and
compared with the space necessary for the valve according to the table.
DN D ØL X Y
50 43 46 8 2
65 46 59 13 10
80 46 76 21 15
100 52 93 26 24
125 56 118 38 31
150 56 139 48 41
200 60 190 71 62
250 68 238 93 80
300 78 281 110 95
350 78 321 130 115
400 102 363 139 128
500 127 468 180 168
600 154 542 202 199

HG1
5.2 Installation position
The valve can basically be installed in any position.
If the concentration of suspended matter is high (e.g. media which are very viscous), it is recommended to
mount the high performance butterfly valve with valve shaft in horizontal position and stop boss facing upwards.
For nominal sizes >DN300 it is generally recommended to mount the valve with valve shaft in horizontal posi-
tion.
The recommended pressure direction (direction of the arrow on the body) guarantees the highest level of tight-
ness. The valve also provides a reliable seal when it is used against the recommended pressure direction.
Consult the manufacturer if the valve is to be used for applications with a frequent change of pressure direction.
5.3 Initial operation
Factory-provided the valve was tested for leaks with air or water. Remains of the test medium may still be
present at the contact surfaces of the valve. Pay attention to any reactions with the operating medium. Before
installing the valve, flush the pipeline and remove any general impurities, welding residues, etc. Remove the
transport packaging shortly before fitting the valve to avoid damage during transport.
Before putting the valve into operation:
▪check that all necessary connections (e.g. compressed air connections) are connected and secure.
▪flush the pipeline with the valve completly open to remove any impurities (such as welding residues) that may
have occurred during installation.
▪check the function of the valve. If there is any doubt about the function, replace the valve.
During a system pressure test the following pressures must not be exceeded:
>1,5 x PS with shut-off element in open position
>1.1 x ∆PS (max. differential pressure) or 1.1 x PS (max. operating pressure) with the shut-off element
closed, the lower value must be used.
NOTICE Flushing process
The valve must not be switched during the flushing process.
15 / 26
Version 0 • Dokument-Nr. 74572811
Internet: www.gefa.com • E-Mail: [email protected]

HG1
16 / 26 Version 0 • Dokument-Nr. 74572811
Internet: www.gefa.com • E-Mail: [email protected]
5.4 Mounting instructions
>Prior to the mounting of the valve, flush the pipeline to remove all traces of soiling, welding residues, etc.
>Remove the transport packaging and check whether the flange connections are without damage and clean.
>Check whether the flange clearance is in accordance with the face-to-face dimension of the valve.
>Before mounting the valve, the flanges are to be sufficiently spread using a suitable tool.
>The valve must be completely closed.
>In order to intercept the valve between the flanges during the mounting process, we recommend (depending
on the mounting position) to insert the lower flange screws without tightening them. The screw is not to be
initially inserted in the centring aid area (rib).
>Insert the high performance valve and the seals between the flanges.
>Insert the flange screws.
>Remove the spreader and hand-tighten the screws.
>Check whether the valve, the seals and the counter-flanges are in true alignment.
>Carefully open and close the valve in order to ensure that the valve disc is not getting in touch with the
pipeline. Check that the disc has adequate clearance.
>With thevalve disc completely closed, tighten the flange screws crosswise using the stipulated torque.
The tightening torque depends on the seals chosen.
>If no specifications are given, the following standard values can be used:
Flange screw M16 M20 M24 M27 M30 M33
Torque in Nm 85 165 285 425 570 780

HG1
5.5 Impermissible operation
In order to operate the valve as efficiently as possible and to avoid malfunctions:
>Valves must not be used to support the pipeline nor as a step-up. This includes the different kinds of opera-
tion like hand levers, gear operators, actuators, feedback and control systems.
>Never operate the valve without actuating devices and/or locking of the shut-off-element.
>Do not exceed the pressure and temperature range specified on the valve or specified in the technical data
(PS / TS, the corresponding pressure-temperature range diagram can be found in chapter technical data un-
der pressure-temperature range diagram).
>Avoid all foreign particles on the sealing surfaces.
>Do not operate the valve in the cavitation area.
>The throttling and control range in an intermediate position with an opening of 0 to 20% is not permissible in
the long run, as the flow rate will be excessive high and the valve will be damaged.
17 / 26
Version 0 • Dokument-Nr. 74572811
Internet: www.gefa.com • E-Mail: [email protected]

HG1
18 / 26 Version 0 • Dokument-Nr. 74572811
Internet: www.gefa.com • E-Mail: [email protected]
6 Operation
CAUTION Pipelines are under pressure
a) Before removing the valve make sure that the pipe section is depressurised and evacuated.
ðIn case of toxic, caustic and other outgasing media the pipe section must also be ventilated.
DANGER There is an acute danger to life when opening a pressurized valve!
Opening of screw connenctions, limit switches, manual overrides or auxiliary equipment when the
valve is under pressure may result in eruption of the fluid and damage to the valve.
NOTICE Opening a (pressurized) valve
Since the operator of the valve is responsible for a safety rating, it is important to observe and
comply with all local and company safety regulations. In addition, in order to ensure safe working
on a valve, at least all safety precautions listed below must be taken:
a) Make sure that the pipe section into which the valve has been integrated is depressurised and
drained
b) Let the valve and the flow medium cool down. If dangerous substances have flowed through
the relevant pipe section, it must be additionally rinsed and aerated.
c) Remove attached actuators before removing the valve or secure them against unauthorized
use and accidental operation.
WARNING Hazardous media
Work on parts in contact with hazardous media may only be carried out with appropriate protective
equipment.
NOTICE Inspection
In the case of dangerous fluids, the tightness must be checked regularly, especially against the at-
mosphere. If there are signs of leakage, these must be remedied immediately by resealing.
NOTICE Usability of the valve
Valves that regularly remain in one position must be operated at regular intervals to ensure their
mobility.
The valve may only be operated by trained persons who know the operating instructions, understand them and
can work in accordance with.

HG1
7 Maintenance and repair
WARNING Hazardous media
Work on parts in contact with hazardous media may only be carried out with appropriate protective
equipment.
CAUTION Pipelines are under pressure
a) Before removing the valve make sure that the pipe section is depressurised and evacuated.
ðIn case of toxic, caustic and other outgasing media the pipe section must also be ventilated.
NOTICE Qualified persons
Work on the valve may only be carried out by qualified and authorised persons.
7.1 Maintenance
DANGER There is an acute danger to life when opening a pressurized valve!
Opening of screw connenctions, limit switches, manual overrides or auxiliary equipment when the
valve is under pressure may result in eruption of the fluid and damage to the valve.
The valves of GEFA Processtechnik GmbH are as far as possible maintenance-free. However, for operational
safety reasons, all valves should nevertheless be checked regularly, for example by assessing the external con-
dition and their accessories. Valves should generally be operated regularly in order not to impair the proper op-
eration of all moving parts due to excessive downtimes. Maintenance intervals are to be determined by the op-
erator according to the conditions of use.
A routine maintenance or lubrication of the valve is not necessary.
7.2 Tighten/Replacing the Gland Packing
Should a leakage occur at the gland packing, retighten the gland nut(1.11)*. Take care that the gland nut is not.
Normally the leakage can be stopped by simply turning the nut by a quarter.
If the leakage cannot be stopped using the above method, the gland packing must be replaced. For replacing
the gland packing the valve needs not to be removed from the pipeline. Follow the steps below to safely change
the stuffing box packing.
>Check whether the pipeline has been rendered depressurized and is empty.
>Remove the operating element. See chapter Mounting the hand lever and chapter Installing the MULTITOP
mounting plate-
>Loosen the fixing devices(1.13)* of the limit stop and lift off the limit stop.
>Loosen the fixing devices(1.10, 1.11)* of the gland flange and lift off the gland flange (1.9)*.
>Remove the gland(1.8)*. A groove in the upper part of the gland makes the removal easier.
>Remove the packing rings (1.7)* and thoroughly clean the packing area.
>Insert a new packing set, whereby it is to be ensured that the correct packing material is used.
>Insert the gland, place the gland flange on top and fix it using the screws and nuts.
>Tighten the nuts reciprocally so that the gland flange is not tilted. Only slightly tighten the nuts until the leak-
age is stopped.
>Reinstall the operating element.
*(See chapter 3 "Scope of delivery")
19 / 26
Version 0 • Dokument-Nr. 74572811
Internet: www.gefa.com • E-Mail: [email protected]

HG1
20 / 26 Version 0 • Dokument-Nr. 74572811
Internet: www.gefa.com • E-Mail: [email protected]
7.3 Replacing the Seat
The valve must be taken out of the pipeline for replacing the seat.
>Ensure that the pipeline is rendered depressurized and is empty.
>Completely close the valve, loosen the flange screws and remove them so far that the valve can be taken
out.
>Lay the valve down with the insert ring(1.4)* facing upwards.
>Loosen the set screws or cylinder screws (1.5)* and remove the insert ring.
>Remove the old seat (1.3)* as well as seal (1.19 / 1.20 Optional)*.Clean the body and insert ring in the area
of the seat-engaging surface.
>If necessary, glue a new sealing tape (1.19 / 1.20) * onto the insert ring.
>Lateral screw connection (1.5)*: Open the valve. For metallic seat, place the seat in the body and then place
the insert ring on the seat. For non-metallic seat rings, insert the seat into the insert ring and then place the
insert ring with the seat on the body. For double-seated rings (e.g. firesafe version), place the metallic ring
on the body, place the non-metallic seat in the insert ring and then place the insert ring with the non - metal-
lic seat on the metallic. Screw in setscrews (1.5) * only until the insert ring can be moved but can not be
pushed out. Close the valve disc to center the insert ring and the seat, alternately tighten the setscrews
hand-tight in order to fix the insert ring.
>Axial screw connection (1.5)*: Close the valve completely. For metallic seat, place the seat in the body and
then place the insert ring on the seat. For non-metallic seat rings, insert the seat into the insert ring and then
place the insert ring with the seat on the body. For double-seated rings (e.g. firesafe version), place the
metallic ring on the body, place the non-metallic seat in the insert ring and then place the insert ring with the
non-metallic seat on the metallic ring and alternately tighten the cylinder screws (1.5) *.
>*(See chapter 3 "Scope of delivery")
Table of contents
Other Gefa Control Unit manuals
Popular Control Unit manuals by other brands
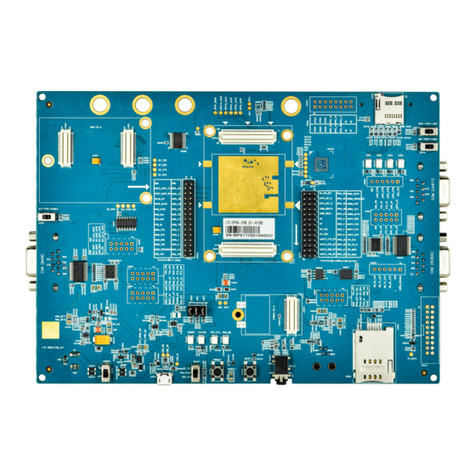
Quectel
Quectel LTE OPEN EVB user guide
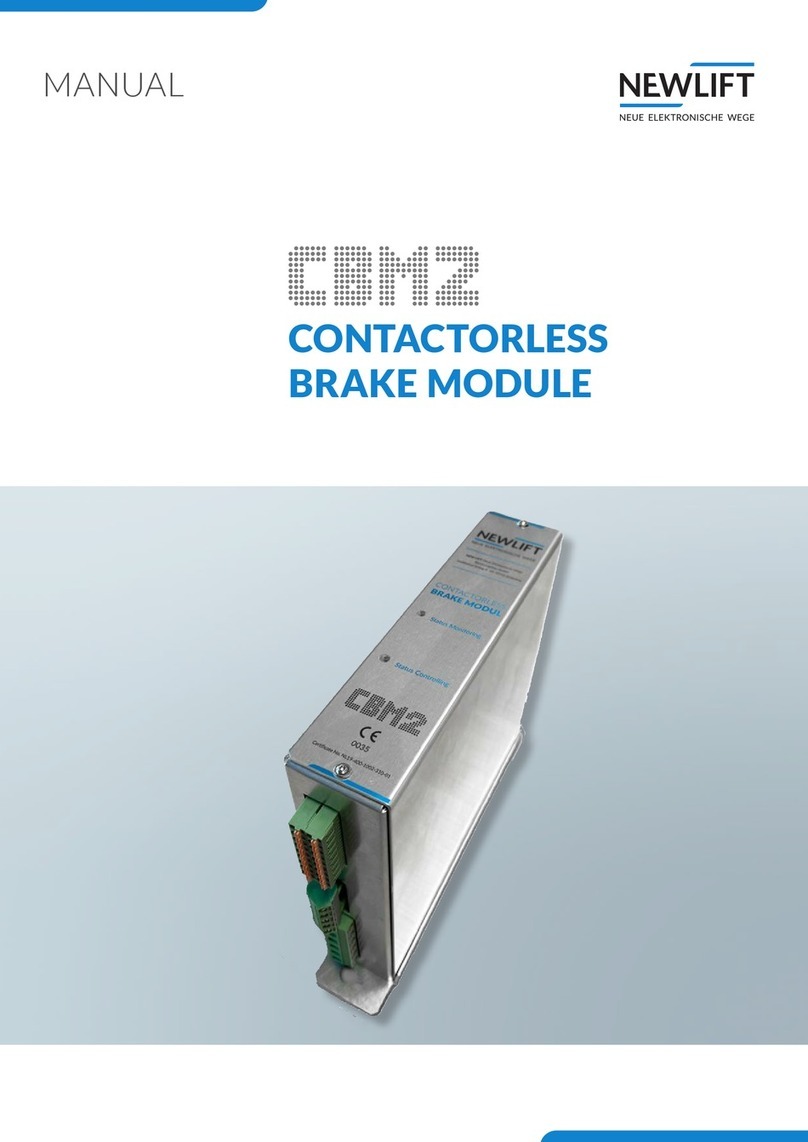
New lift
New lift CBM2 manual

Crane
Crane Dominator PRO Z4000 Series Installation, operating and maintenance instructions
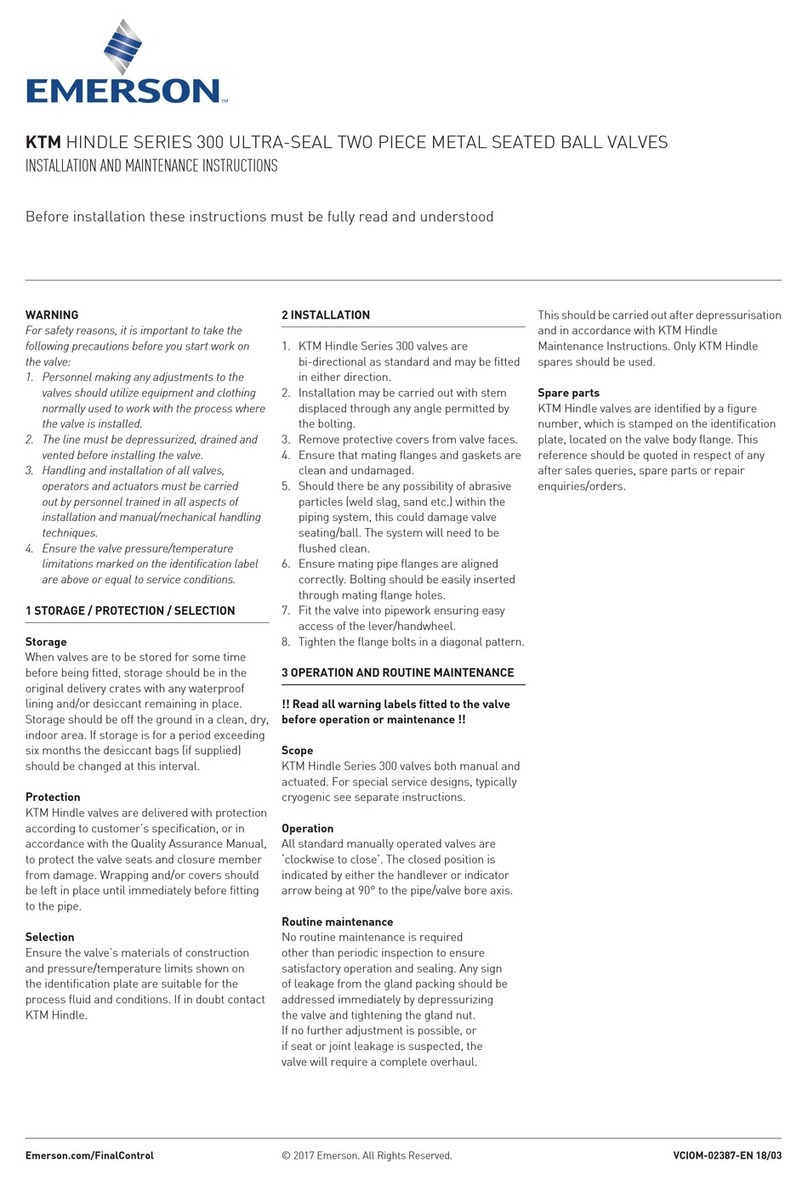
Emerson
Emerson KTM Hindle 300 Series Installation and maintenance instructions
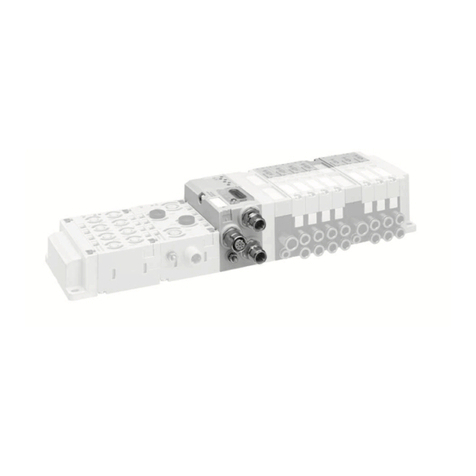
Emerson
Emerson AVENTICS System description

Xiamen Four-Faith Communication
Xiamen Four-Faith Communication F8913D user manual
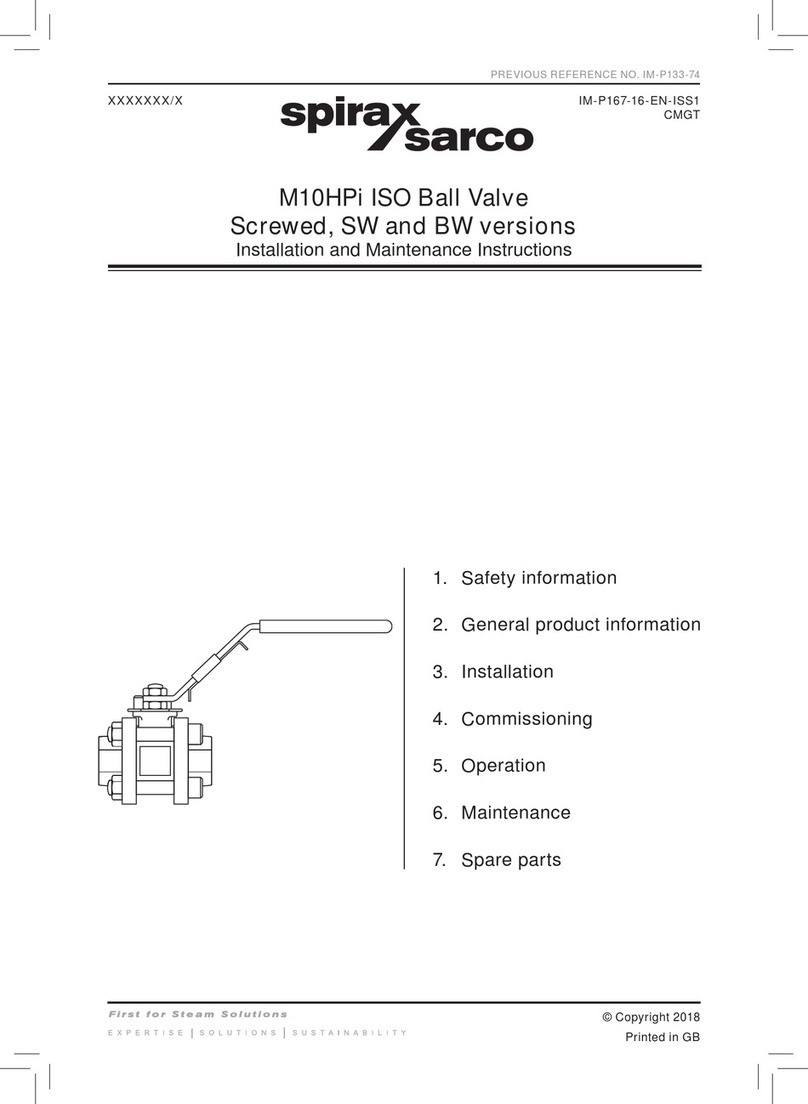
Spirax Sarco
Spirax Sarco M10HPi ISO Series Installation and maintenance instructions
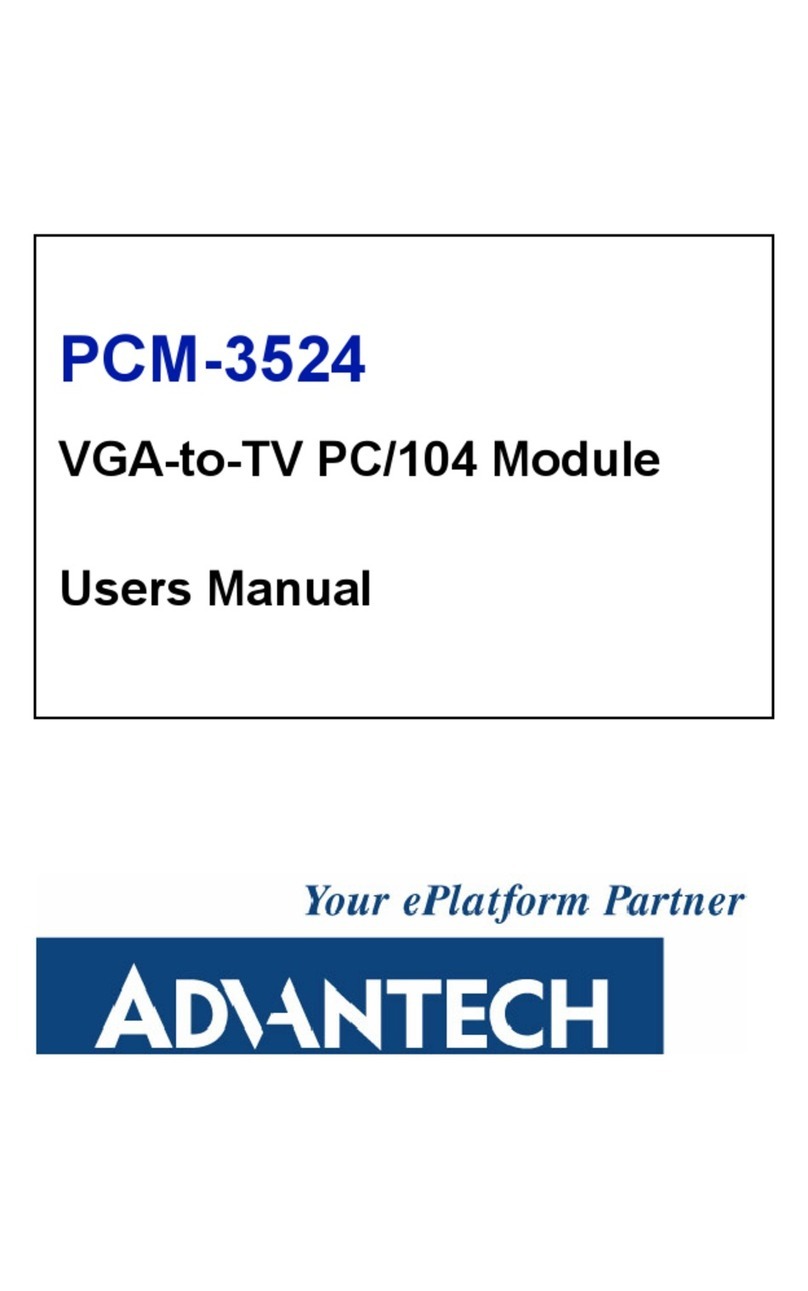
Advantech
Advantech PCM-3524 user manual
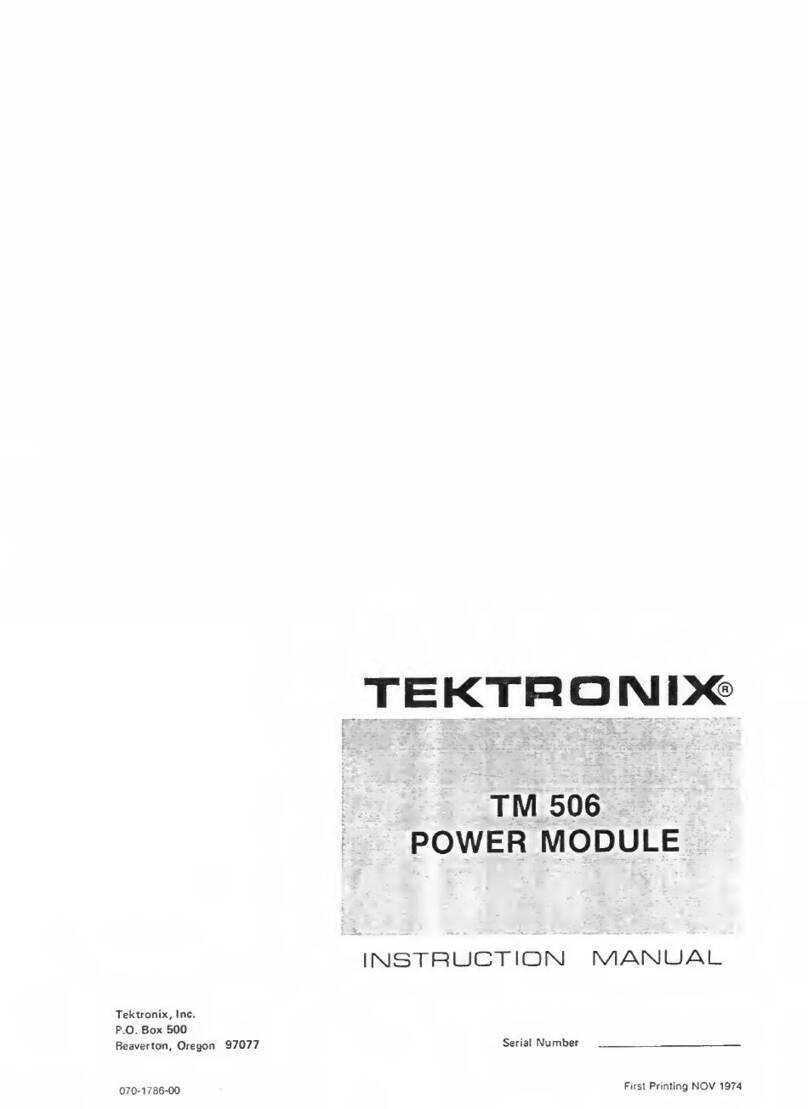
Tektronix
Tektronix TM 506 instruction manual
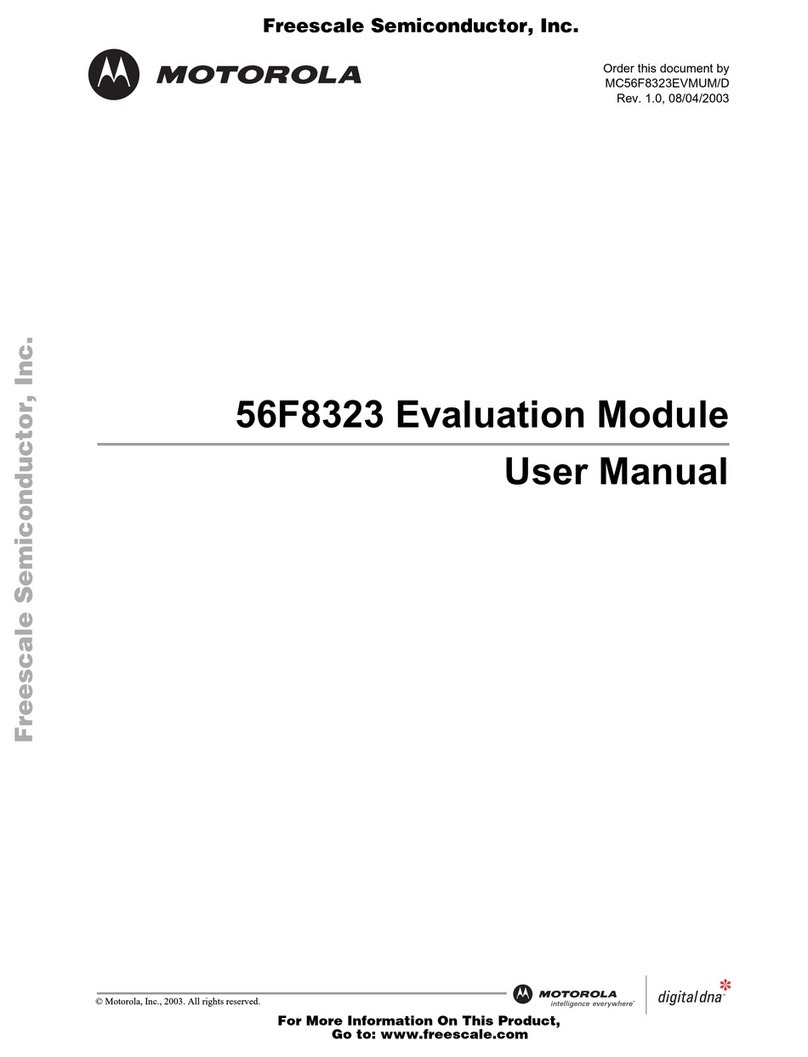
Motorola
Motorola 56F8323 user manual
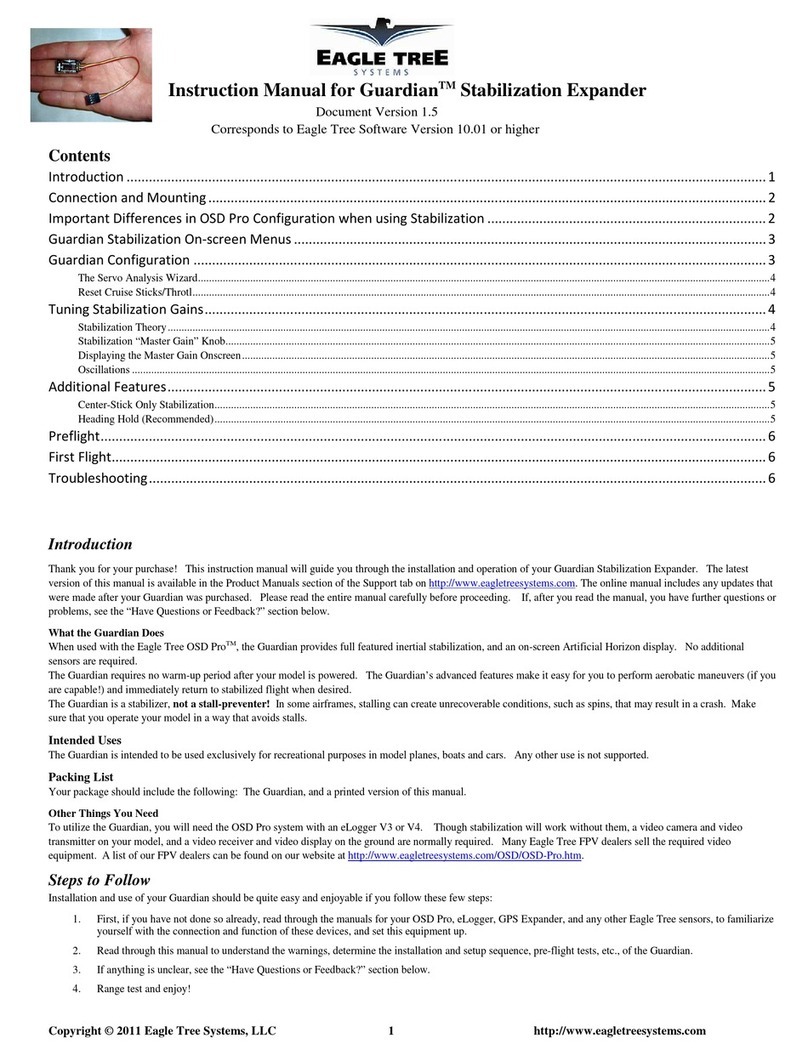
Eagle Tree Systems
Eagle Tree Systems Guardian ET-GUARD instruction manual
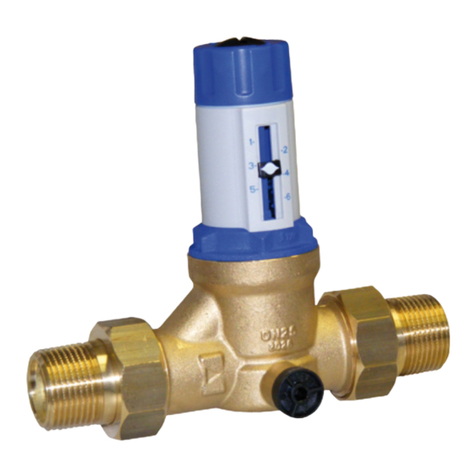
SYR
SYR 315.2 Instructions for use