Geokon 8032 User manual

Instruction Manual
Model 8032
Terminal Board and
16/32-channel Multiplexer
No part of this instruction manual may be reproduced, by any means, without the written consent of GEOKON®.
The information contained herein is believed to be accurate and reliable. However, GEOKON®assumes no responsibility for
errors, omissions or misinterpretation. The information herein is subject to change without notification.
Copyright © 20015-2020 by GEOKON®
(Doc Rev K, 1/22/20)


Warranty Statement
GEOKON warrants its products to be free of defects in materials and workmanship, under
normal use and service for a period of 13 months from date of purchase. If the unit should
malfunction, it must be returned to the factory for evaluation, freight prepaid. Upon examination
by GEOKON, if the unit is found to be defective, it will be repaired or replaced at no charge.
However, the WARRANTY is VOID if the unit shows evidence of having been tampered with
or shows evidence of being damaged as a result of excessive corrosion or current, heat, moisture
or vibration, improper specification, misapplication, misuse or other operating conditions outside
of GEOKON's control. Components which wear or which are damaged by misuse are not
warranted. This includes fuses and batteries.
GEOKON manufactures scientific instruments whose misuse is potentially dangerous. The
instruments are intended to be installed and used only by qualified personnel. There are no
warranties except as stated herein. There are no other warranties, expressed or implied, including
but not limited to the implied warranties of merchantability and of fitness for a particular
purpose. GEOKON is not responsible for any damages or losses caused to other equipment,
whether direct, indirect, incidental, special or consequential which the purchaser may experience
as a result of the installation or use of the product. The buyer's sole remedy for any breach of this
agreement by GEOKON or any breach of any warranty by GEOKON shall not exceed the
purchase price paid by the purchaser to GEOKON for the unit or units, or equipment directly
affected by such breach. Under no circumstances will GEOKON reimburse the claimant for loss
incurred in removing and/or reinstalling equipment.
Every precaution for accuracy has been taken in the preparation of manuals and/or software,
however, GEOKON neither assumes responsibility for any omissions or errors that may appear
nor assumes liability for any damages or losses that result from the use of the products in
accordance with the information contained in the manual or software.


TABLE of CONTENTS
1. THEORY OF OPERATION ..................................................................................................................................1
1.1 CHANNEL SWITCHING..........................................................................................................................................1
1.2 MODES OF OPERATION ........................................................................................................................................3
1.2.1 Datalogger Mode of Operation...................................................................................................................3
1.2.2 GK-403 Mode of Operation ........................................................................................................................4
2. INSTALLATION AND WIRING ..........................................................................................................................6
2.1 INSTALLATION .....................................................................................................................................................6
2.2 WIRING................................................................................................................................................................6
2.2.1 Model 8032-27 and Load Cell Wiring ........................................................................................................9
2.3 DATALOGGER CONNECTION ..............................................................................................................................10
3. MAINTENANCE AND TROUBLESHOOTING...............................................................................................11
3.1 MAINTENANCE ..................................................................................................................................................11
3.2 TROUBLESHOOTING ...........................................................................................................................................11
APPENDIX A. SPECIFICATIONS.........................................................................................................................12
APPENDIX B. CONNECTOR AND CABLE WIRING........................................................................................14
APPENDIX C. MANUAL SWITCH INSTRUCTIONS ........................................................................................16
APPENDIX D. “DAISY-CHAIN” OPERATION...................................................................................................17
APPENDIX E. MAXIMUM 8032-5 (TAN CABLE) CABLE LENGTHS............................................................18
APPENDIX F. MEMS SENSOR TO MULTIPLEXER WIRING........................................................................19

FIGURES
FIGURE 1-CHANNEL SELECTION SWITCH (POSITION 1ON SW1).................................................................................. 1
FIGURE 2-16-CHANNEL SWITCHING BLOCK DIAGRAM ................................................................................................ 2
FIGURE 3-32-CHANNEL SWITCHING BLOCK DIAGRAM ................................................................................................ 2
FIGURE 4-GK-403/DATALOGGER SELECTION......................................................................................................... 3
FIGURE 5-16-CHANNEL DATALOGGER CHANNEL SELECTION TIMING......................................................................... 3
FIGURE 6-32-CHANNEL DATALOGGER CHANNEL SELECTION TIMING......................................................................... 4
FIGURE 7-16-CHANNEL GK-403 CHANNEL SELECTION TIMING .................................................................................. 4
FIGURE 8-32-CHANNEL GK-403 CHANNEL SELECTION TIMING .................................................................................. 5
FIGURE 9-MULTIPLEXER ENCLOSURE MOUNTING DIMENSIONS .................................................................................. 6
FIGURE 10 -TERMINAL BOARD LAYOUT ....................................................................................................................... 8
FIGURE 11 -MODEL 8032-27 JUMPER WIRE ASSEMBLY ............................................................................................... 9
FIGURE 12 -MANUAL SWITCH PANEL AND ENCLOSURE ..............................................................................................16
FIGURE 13 -“DAISY-CHAIN”CONFIGURATION .............................................................................................................17
FIGURE 14 -RECOMMENDED MAXIMUM CABLE LENGTH.............................................................................................18
TABLES
TABLE 1-16-CHANNEL MULTIPLEXER/TERMINAL BOARD WIRING ............................................................................. 7
TABLE 2-32-CHANNEL MULTIPLEXER/TERMINAL BOARD WIRING ............................................................................. 7
TABLE 3-COMMON CONDUCTOR CHART ..................................................................................................................... 9
TABLE 4-STANDARD VW LOAD CELL WIRING WHEN USING 8032-27........................................................................ 9
TABLE 5-SPECIFICATIONS ...........................................................................................................................................13
TABLE 6-J4 (I/O) CONNECTOR....................................................................................................................................14
TABLE 7-P1 (I/O) CONNECTOR ...................................................................................................................................14
TABLE 8-J1/J2 (TERMINAL BOARD)CONNECTORS .....................................................................................................15
TABLE 9-“DAISY-CHAIN”OPERATION/CHANNELS ACCESSED ...................................................................................17
TABLE 10 -UNIAXIAL MEMS WIRING .........................................................................................................................19
TABLE 11 -BIAXIAL MEMS WIRING ...........................................................................................................................19

1
1. THEORY OF OPERATION
The Model 8032 Terminal Board and Multiplexer expands the number of channels that can be
read by the 8600 Datalogger. Channel switching is accomplished by mechanical relays mounted
on the underside of the circuit board and the transducer connections are accomplished by friction
locking spring-loaded terminals mounted on the top side of the circuit board.
There are two varieties of 8032 board:
8032-E: Terminal Board only – typically used in conjunction with a 4999 Manual Switch Box
8032-C: Terminal Board with Multiplexer – typically used with the 8600 Datalogger.
Two switching configurations are supported, 16-channels of four conductors or 32-channels of
two conductors. For the 8032-C, these configurations are set by a DIP Switch on the top side of
the circuit board. A second DIP Switch selects whether the 8032-C is being used with a
datalogger or GK-403 Readout Box (obsolete model). For the 8032-E, these configurations are
determined by the 4999 Manual Switch Box.
To protect against lightning or EMI/RFI induced transients, each channel is protected by an
integrated lightning protection system, incorporating 230V tripolar plasma surge arrestors, 150V
bipolar plasma surge arrestors, 10uH inductors and 16V transient voltage protection diodes. See
Appendix A for complete specifications on these components.
1.1 Channel Switching
Figure 1 illustrates the DIP switch marked “SW1” on the top side of the multiplexer circuit
board. Switch position 1 is used for switching between 16 and 32-channel operation. If position 1
is set to OFF, the multiplexer is in 16-channel mode. If position 1 is set to ON, the multiplexer
is in 32-channel mode. In Figure 1, 32-channel mode is chosen:
Figure 1 - Channel Selection Switch (Position 1 on SW1)
The 16-channel four-wire switching configuration (Figure 2) is typically used to multiplex four-
wire sensors such as resistance strain gauge load cells. It is also used to switch connections for
instruments which have more than one sensor integral to them, such as vibrating wire pressure
transducers with an integral thermistor for measuring temperature.
ON
OFF
SW1
1
2
3
4

2
Relay
Control
Microcontroller
12V
GROUND
RESET
CLOCK
COM HI 1
COM LO 1
GK-403 or
CR800/CR1000
Sensor #1
12V
GROUND
RESET
CLOCK
Multiplexer/Terminal Board
AG
Sensor
Shield
COM HI 2
COM LO 2
Sensor #16
Sensor
Shield
1H
2H
1L
2L
S1
31H
32H
31L
32L
S16
Figure 2 - 16-Channel Switching Block Diagram
The 32-channel two-wire switching configuration (Figure 3) is typically used to multiplex two-
wire sensors such as a vibrating wire pressure transducers, thermistors or thermocouples.
Relay
Control
Microcontroller
12V
GROUND
RESET
CLOCK
COM HI
COM LO
GK-403 or
CR800/CR1000
Sensor #1
Sensor #32
12V
GROUND
RESET
CLOCK
Multiplexer/Terminal Board
AG
Sensor
Shield
Sensor
Shield
1H
1L
S1
32H
32L
S16
Figure 3 - 32-Channel Switching Block Diagram

3
1.2 Modes of Operation
The multiplexer is powered by a nominal 12 VDC supply. Two control lines (RESET and
CLOCK) determine how channel selection is accomplished. Two schemes are supported - one
when connected when connected to Model 8600 dataloggers, and the other for the GK-403
Vibrating Wire Readout Box (obsolete model). See the following sections explaining how each
mode operates.
Figure 4 illustrates the DIP switch SW2 for switching between a GK-403 or Datalogger
application. “DATALOGGER” is the default SW2 position:
Figure 4 - GK-403/DATALOGGER Selection
1.2.1 Datalogger Mode of Operation
The Datalogger mode of operation uses two control lines to operate the multiplexer. The
RESET line enables the multiplexer and activates the Datalogger mode of clocking.
Pulses received on the CLOCK line sequentially increment the channels while the RESET
line is held high. See the timing diagrams below (Figure 5 and Figure 6)
The CLOCK line sequentially advances the channels beginning with Channel 1. Note the
timing diagrams for 16-channel (shown in Figure 5) and 32-channel (shown in Figure 6)
channel switching arrangements.
Reset
Clock
Channel 1
T1
T2
T3
No Channel
Selected
No Channel
Selected
Channel 16
Pulse 1
Pulse 2
Pulse 31
Timing:
T2 = 2 mSsec(min)
T3 = 4 mSsec(min)
T1 = 50 mSec(min.)
Selected
Selected
Pulse 32
Figure 5 - 16-Channel Datalogger Channel Selection Timing
GK-403
DATALOGGER
SW2

4
Reset
Clock
Channel 1
Channel 2
T1
T2
T3
No Channel
Selected
No Channel
Selected
Channel 32
Pulse 1
Pulse 2
Pulse 32
Selected
Selected
Selected
Timing:
T2 = 2 mSec (min)
T3 = 4 mSec (min)
T1 = 50 mSec (min)
Figure 6 - 32-Channel Datalogger Channel Selection Timing
1.2.2 GK-403 Mode of Operation
(Please note: The GK-403 is an obsolete model. This mode of operation has been
retained for legacy purposes.)
The GK-403 mode of operation uses a single control line to select channels. This scheme
allows individual channels to be selected without having to sequentially advance through
all channels. Multiplexers can also be connected together in a “daisy-chain” fashion using
the GK-403 protocol. In 16-channel mode, the number of clock pulses equals two times
the desired channel number. In 32-channel mode, the number of clock pulses equals the
desired channel number plus one. Note the timing for 16-channel (shown in Figure 7) and
32-channel (shown in Figure 8) switching arrangements.
The GK-403 channel selection scheme is not well suited to long cable lengths. The
maximum recommended distance between the GK-403 and multiplexer is 50 feet (15
meters).
Clock
Channel 2
1
2
Timing:
T2 = min 20 usec
T3 = min 40 µsec (25kHz)
T1 = min 20 usec
Channel Selected
3
Channel 1
1
T4 = 500 µsec
2
T1
T2
T3
T4
4
Figure 7 - 16-Channel GK-403 Channel Selection Timing

5
Clock
T1
T2
T3
Channel 2
1
2
Channel Selected
Channel 1
1
T4
2
3
Timing:
T2 = min 20 usec
T3 = min 40 µsec (25kHz)
T1 = min 20 usec
T4 = 500 µsec
Figure 8 - 32-Channel GK-403 Channel Selection Timing

6
2. INSTALLATION AND WIRING
2.1 Installation
The multiplexer (or terminal board alone) is housed in a Nema 4/4X weatherproof enclosure.
However, it is recommended that additional measures be taken to ensure that water or other
contaminants are prevented from entering and subsequently disrupting operation of the
equipment. For example, in field environments, it could be installed inside an equipment trailer
or shed. The enclosure should be mounted in an upright fashion, i.e. on a wall. The holes located
in the tabs at the top and bottom of the enclosure are used for mounting. Note Figure 9 for
mounting dimensions.
Figure 9 - Multiplexer Enclosure Mounting Dimensions
An earth ground lug is installed on the bottom of the enclosure. Drive a copper stake into the
ground (or use an existing grounded metal structure) and attach a large gauge copper wire (>12
AWG) from earth ground to the earth ground lug of the enclosure.
2.2 Wiring
The enclosure has cable entries for passing the instrument cables to the terminal board. These
entries have seals for specific cable sizes which will minimize the possibility of water or other
contaminants entering the box and causing problems. Plastic dowels are provided for unused
cable entries to prevent moisture and contaminants from entering the enclosure.
If the unit is equipped with manual switching the switch panel must be removed to access the
terminal board. See Appendix C for additional information.

7
Actual gauge connections to the terminal board will vary depending on the instrument type and
cable used. Note the following tables to get the general idea.
Terminal
Board
Vibrating Wire
with Thermistor
Resistance Strain
Gauge Bridge
Linear Potentiometer
(with Remote Sense)
1H
VW Sensor #1
S+ from Bridge #1
Excitation Pot #1
1L
VW Sensor #1
S- from Bridge #1
Wiper Output Pot #1
2H
Thermistor #1
P+ to Bridge #1
Remote Sense Pot #1
2L
Thermistor #1
P- to Bridge #1
Ground Pot #1
S1
Shield Drain Wire
from Sensor #1
Shield Drain Wire
from Bridge #1
Shield Drain Wire
from Pot #1
3H
VW Sensor #2
S+ from Bridge #2
Excitation Pot #2
3L
VW Sensor #2
S- from Bridge #2
Wiper Output Pot #2
4H
Thermistor #2
P+ to Bridge #2
Remote Sense Pot #2
4L
Thermistor #2
P- to Bridge #2
Ground Pot #2
S2
Shield Drain Wire
from Sensor #2
Shield Drain Wire
from Bridge #2
Shield Drain Wire
from Pot #2
•
•
•
•
•
•
•
•
31H
VW Sensor #16
S+ from Bridge #16
Excitation Pot #16
31L
VW Sensor #16
S- from Bridge #16
Wiper Output Pot #16
32H
Thermistor #16
P+ to Bridge #16
Remote Sense Pot #16
32L
Thermistor #16
P- to Bridge #16
Ground Pot #16
S16
Shield Drain Wire
from Sensor #16
Shield Drain Wire
from Bridge #16
Shield Drain Wire
from Pot #16
Table 1 - 16-Channel Multiplexer/Terminal Board Wiring
Terminal
Board
Vibrating Wire
Thermistor
Thermocouple
1H
VW Sensor #1
Thermistor #1
Thermocouple #1
1L
VW Sensor #1
Thermistor #1
Thermocouple #1
2H
VW Sensor #2
Thermistor #2
Thermocouple #2
2L
VW Sensor #2
Thermistor #2
Thermocouple #2
S1
Shield Drain Wires
from Sensors 1&2
Shield Drain Wires
from Thermistors 1&2
3H
VW Sensor #3
Thermistor #3
Thermocouple #3
3L
VW Sensor #3
Thermistor #3
Thermocouple #3
4H
VW Sensor #4
Thermistor #4
Thermocouple #4
4L
VW Sensor #4
Thermistor #4
Thermocouple #4
S2
Shield Drain Wires
from Sensors 3&4
Shield Drain Wires
from Thermistors 3&4
•
•
•
•
•
•
•
•
31H
VW Sensor #31
Thermistor #31
Thermocouple #31
31L
VW Sensor #31
Thermistor #31
Thermocouple #31
32H
VW Sensor #32
Thermistor #32
Thermocouple #32
32L
VW Sensor #32
Thermistor #32
Thermocouple #32
S16
Shield Drain Wires
from Sensors 31&32
Shield Drain Wires
from Thermistors 31&32
Table 2 - 32-Channel Multiplexer/Terminal Board Wiring

8
Figure 10 depicts the terminal board to which gauge connections are made. If the terminal board
is equipped with manual switches, connectors J1 and J2 will have ribbon cables that are
connected to the switch boards.
Terminal Blocks T1/2 to T31/32 are for the gauge connections.
Figure 10 - Terminal Board Layout
J1
J2
1H
1L
2H
2L
S1
3H
3L
4H
4L
S2
5H
5L
6H
6L
S3
7H
7L
8H
8L
S4
9H
9L
10H
10L
S5
11H
11L
12H
12L
S6
13H
13L
14H
14L
S7
15H
15L
16H
16L
S8
17H
17L
18H
18L
S9
19H
19L
20H
20L
S10
21H
21L
22H
22L
S11
23H
23L
24H
24L
S12
25H
25L
26H
26L
S13
27H
27L
28H
28L
S14
29H
29L
30H
30L
S15
31H
31L
32H
32L
S16
EARTH
J4
T1/2
T3/4
T5/6
T7/8
T9/10
T11/12
T13/14
T15/16
T17/18
T19/20
T21/22
T23/24
T25/26
T27/28
T29/30
T31/32
SHLD
SHLD
C1H
C1L
C2H
C2L
SHLD
+12V
GND
RESET
CLOCK
SHLD
P1
GK-403
DATALOGGER
SW2
SW1
ON
OFF

9
2.2.1 Model 8032-27 and Load Cell Wiring
Connect the “common” VW- conductor from the load cell to the 8032-27 by lifting up the
orange tab located on the opposite side of the six black conductors, inserting the common
conductor fully into the 8032-27 (Figure 11), and then pushing down on the orange tab
until it snaps into place. Refer to Table 3 to identify which conductor carries the common
VW- signal.
Figure 11 - Model 8032-27 Jumper Wire Assembly
10 pin Bendix
PT06A-12-10P
Function
3 Gauge VW Load
Cell, Purple Cable
4 Gauge VW Load
Cell, Purple Cable
6 Gauge VW Load
Cell, Orange Cable
H
Common
White's Black*
Green
Blue
Table 3 - Common Conductor Chart
*White's black and Green wires are switched on GEOKON 3-gauge VW load cells prior to serial number 3313.
The following wiring chart details the connections between the load cell and 8032-27
with the terminal board:
Terminal
Board
Vibrating Wire
with Thermistor
1H
VW Sensor #1
1L
8032-27
2H
Thermistor
2L
Thermistor
S1
Shield Drain Wire
3H
VW Sensor #2
3L
8032-27
4H
-
4L
-
S2
-
5H
VW Sensor #3
5L
8032-27
6H
-
6L
-
S3
-
•
•
•
•
11H
VW Sensor #6
11L
8032-7
12H
-
12L
-
S6
-
Table 4 - Standard VW Load Cell Wiring When Using 8032-27

10
2.3 Datalogger Connection
Following sensor and installation, connections between a Datalogger and Multiplexer(s) can be
made using the model 8032-5 interconnect cable. Each Multiplexer employed is connected to the
appropriate weather tight 10-pin Bendix connector mounted on the enclosure. Each connector on
a standard Datalogger is pre-wired to control and read the external Multiplexers.

11
3. MAINTENANCE AND TROUBLESHOOTING
3.1 Maintenance
Maintenance for the Model 8032 Multiplexer/Terminal Board is minimal. The following checks
should be performed periodically though;
Is there water or other contaminants intruding into the enclosure? At times water can wick
through the sensor cables onto the terminal board. This will at some point cause problems with
the system. Water or other contaminants can also enter through improper use of the cable entries.
Additional sealing of the entries can be done with various sealing compounds such as RTV. If
moisture is condensing inside desiccant can be used to keep this to a minimum. Desiccant is
available from the factory.
Are connections corroding? If the unit is installed near salt water for example, salts can form on
the terminals inside the enclosure and cause malfunctions. In this event check that the enclosure
is properly sealed. Use sealing compounds if necessary. Desiccant can also help prevent this
buildup. Sealing sprays such as HumiSeal can also help protect the connections.
Is the earth ground connection acceptable? Check that corrosion has not built up around the
connection to the enclosure (outside or in). Disassemble, sand the connection location to remove
rust or corrosion, and reattach if necessary.
3.2 Troubleshooting
Below are some commonly experienced problems along with possible remedial action. Contact
the factory if any problem remains unresolved or additional help is required.
Symptom: A particular channel on the multiplexer appears to be malfunctioning
Check sensor connections on the terminal board. Clean if corrosion exists.
Try moving the sensor wired to the suspect channel to another channel to verify the
malfunctioning of the channel (as opposed to the sensor).
Symptom: No channels are working
Inspect circuit board for shorts, opens, or other damage.
Is moisture present on circuit board? If so, install desiccant to absorb.
Symptom: Channel selection appears to be random
Has corrosion built up on the circuit board? Clean if necessary.
Is there a source of electrical noise nearby? Move multiplexer or noise source if possible.

12
APPENDIX A. SPECIFICATIONS
GENERAL:
Power Requirements
10-16 VDC (unregulated)
Quiescent Current (Datalogger mode)
80 µA (16CH mode), 130µA (32CH mode)
Quiescent Current (GK-403 mode)
12 mA
Channel Activated Current
30 mA
Control Line Input Impedance
100 kΩ(CLOCK), 100 kΩ(RESET)
Control Line Input Levels
TTL or RS-232 (±9 VDC)
Transient Protection
16 VDC Transzorbs
Operating Temperature
−40 to +60°C
RELAYS:
Type
NAIS TXS2SA-4.5V DPDT non-latching
Power
11.1 mA @ 5VDC (55.5 mW)
Contact Type
Gold clad silver alloy
On Resistance
100 mΩ
Coil Resistance
405 Ω
Maximum Switching Power
30W (resistive)
Maximum Switching Voltage
110 VDC
Maximum Switching Current
1 A
Operate Time
≈5 msec Max.
Release Time
≈5 msec
Switching Life Mechanical: 5 x 10
7
operations
Electrical @ 30W: 2 x 10
5
operations
Ambient Temperature
−40 to +70°C
TRIPOLAR PLASMA SURGE ARRESTOR:
Nominal DC Breakdown Voltage
230V
Surge Life
100 (10/1000 ms pulse @ 200 A)
Maximum Surge Current
5 kA per side (8/20 µs pulse)
Insulation Resistance
109Ω
Operating Temperature
−65 to +125°C
BIPOLAR PLASMA SURGE ARRESTOR:
Nominal DC Breakdown Voltage
150V
Maximum Surge Current
1 kA (8/20 µs pulse)
Insulation Resistance
1010 Ω
Operating Temperature
−65 to +125°C

13
INDUCTOR
Rated Current
4A
Inductance
10µH (±20%)
D.C.R.
25mΩMAX (at 20°C)
TRANSIENT VOLTAGE SUPPRESSOR (TRANSORB):
Rated Power
1500W
Peak forward Surge Current
200A
Reverse Standoff Voltage
16.0V
TRANSDUCER CONNECTION MAXIMUM OPERATING VOLTAGE LEVELS:
Common mode Voltage/Earth Ground
16V(max)
Differential mode Voltage
(Channel # ‘H’ – Channel # ‘L’)
16V(max)
RESET AND CLOCK MAXIMUM OPERATING VOLTAGE LEVELS:
Single ended Control Voltage/System Ground
16V(max)
Table 5 - Specifications

14
APPENDIX B. CONNECTOR AND CABLE WIRING
J4
Inside
Color
10 Pin
Bendix
Description
8032-5 (TAN) Cable
Wire Color
1
Brown
A
COM HI 1
White
2
Red
B
COM LO 1
White's Black
3
Orange
C
COM HI 2 (16-channel)
Red
4
Yellow
D
COM LO 2 (16-channel)
Red's Black
5
Green
K
Analog Ground
Shield Drain Wires – all pairs plus overall
6
Blue
F
+12 Volt Power
Yellow
7
Purple
G
Power Ground
Yellow's Black
8 Grey H
RESET (DATALOGGER)
SENSE (GK-403)
Green
9
White
J
CLOCK
Green's Black
10
E
No Connection
Blue & Blue’s Black (unused)
Table 6 - J4 (I/O) Connector
P1 Terminal
Label Description
8032-5 (TAN) Cable
Wire Color
1,2
SHLD
SHIELD
Shield Drain Wires – all pairs plus overall
3,4
SHLD
SHIELD
Shield Drain Wires – all pairs plus overall
5,6
C1H
COM HI 1
White
7,8
C1L
COM LO 1
White's Black
9,10
C2H
COM HI 2 (16-channel)
Red
11,12
C2L
COM LO 2 (16-channel)
Red's Black
13,14
SHLD
SHIELD
Shield Drain Wires – all pairs plus overall
15,16
+12V
+12 Volt Power
Yellow
17,18
GND
Power Ground
Yellow's Black
19,20
RESET
RESET
Green
21,22
CLOCK
CLOCK
Green's Black
23,24
SHLD
SHIELD
Shield Drain Wires – all pairs plus overall
-
-
No Connection
Blue & Blue’s Black (unused)
Table 7 - P1 (I/O) Connector
Note: P1 is a “stacking” type connector. Odd number terminals are read left to right on the
bottom row. Even numbered terminals are read left to right on the top row.
Other manuals for 8032
1
Table of contents
Other Geokon Multiplexer manuals
Popular Multiplexer manuals by other brands
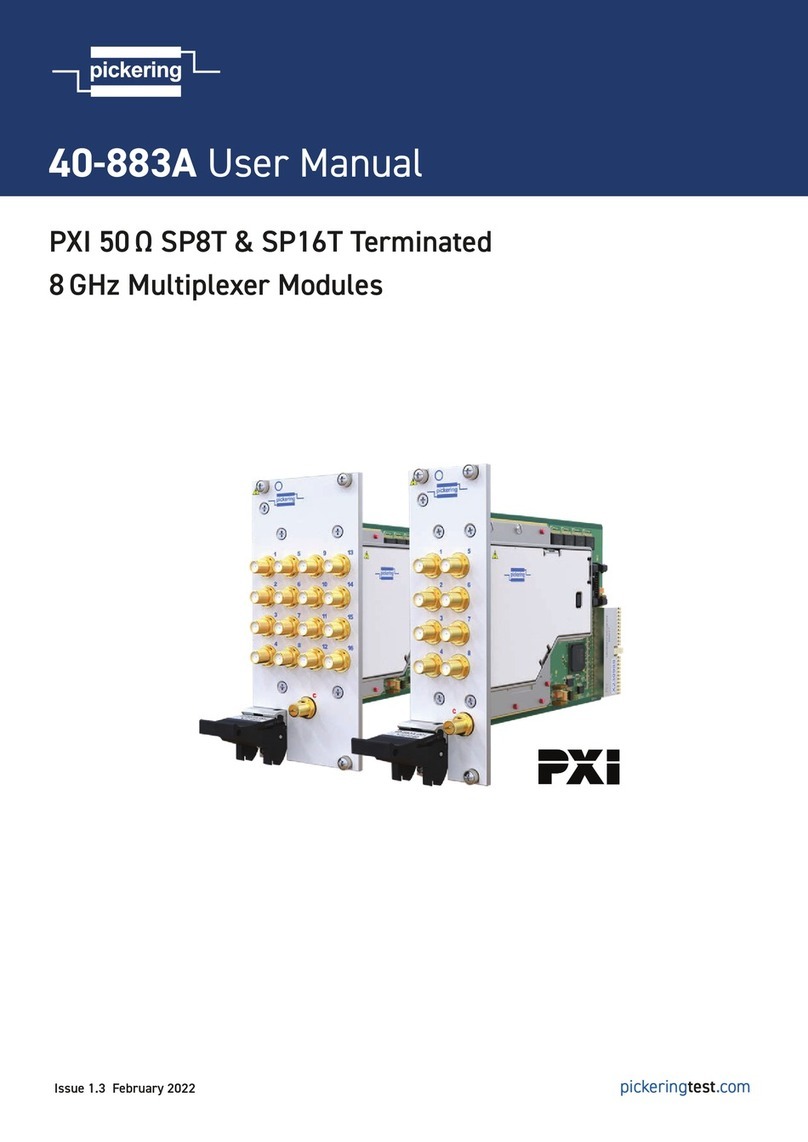
Pickering
Pickering PXI 40-883A user manual
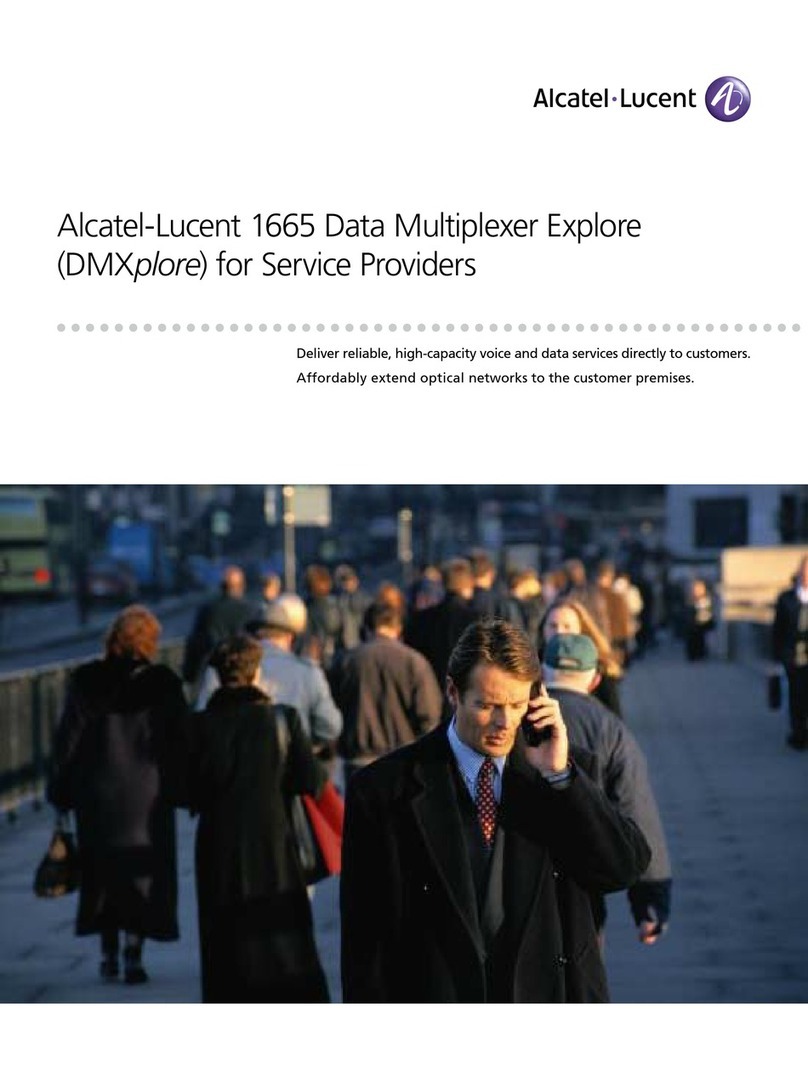
Alcatel-Lucent
Alcatel-Lucent Data Multiplexer Explore 1665 brochure
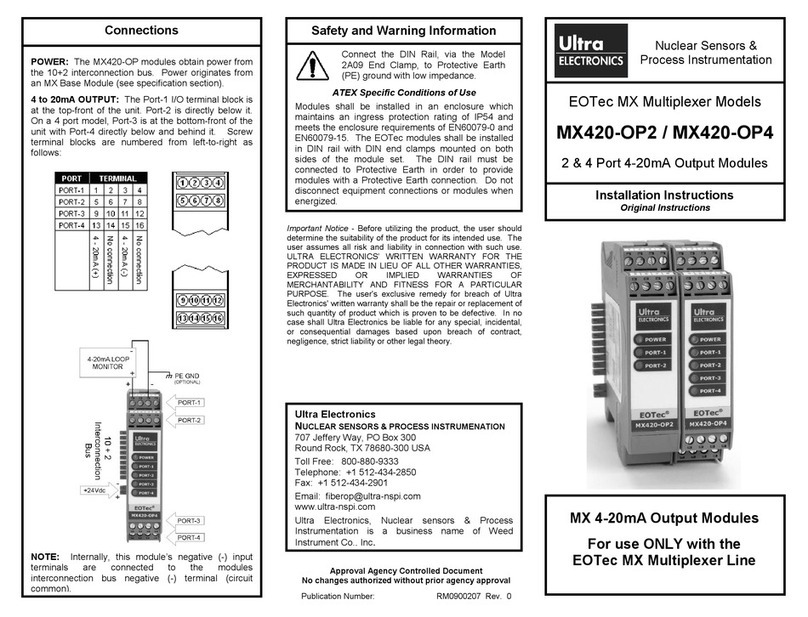
Ultra electronics
Ultra electronics MX420-OP2 installation instructions
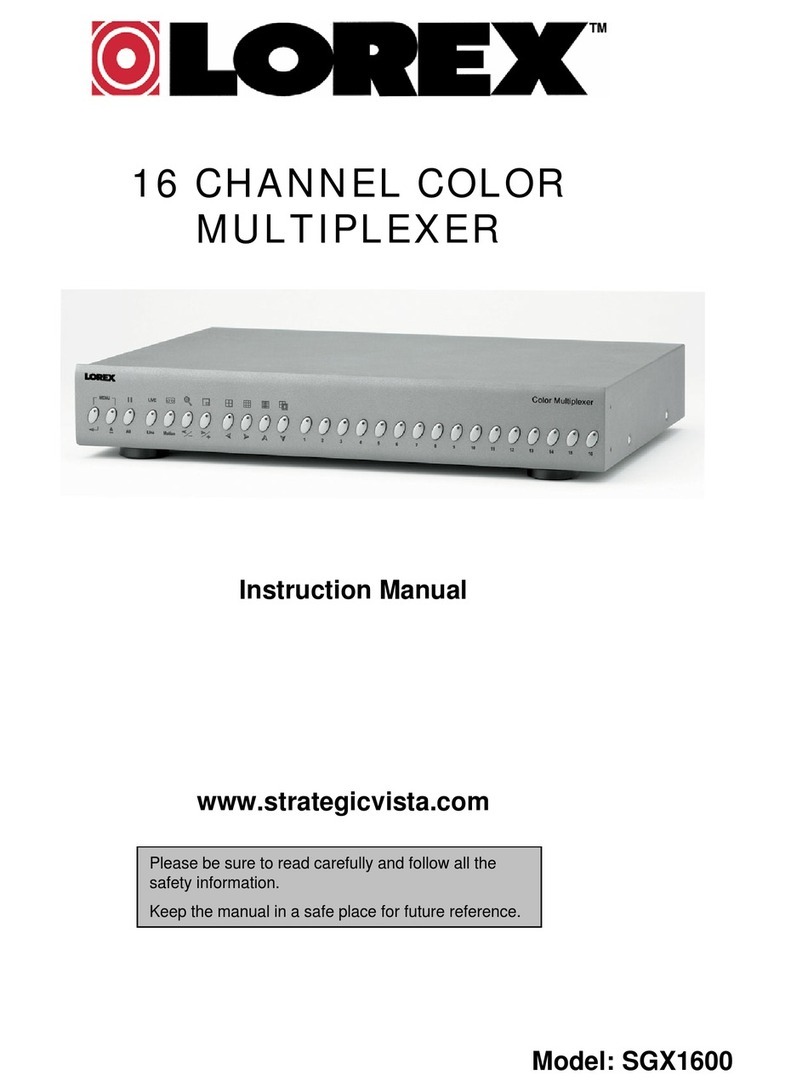
Lorex
Lorex SGX1600 instruction manual
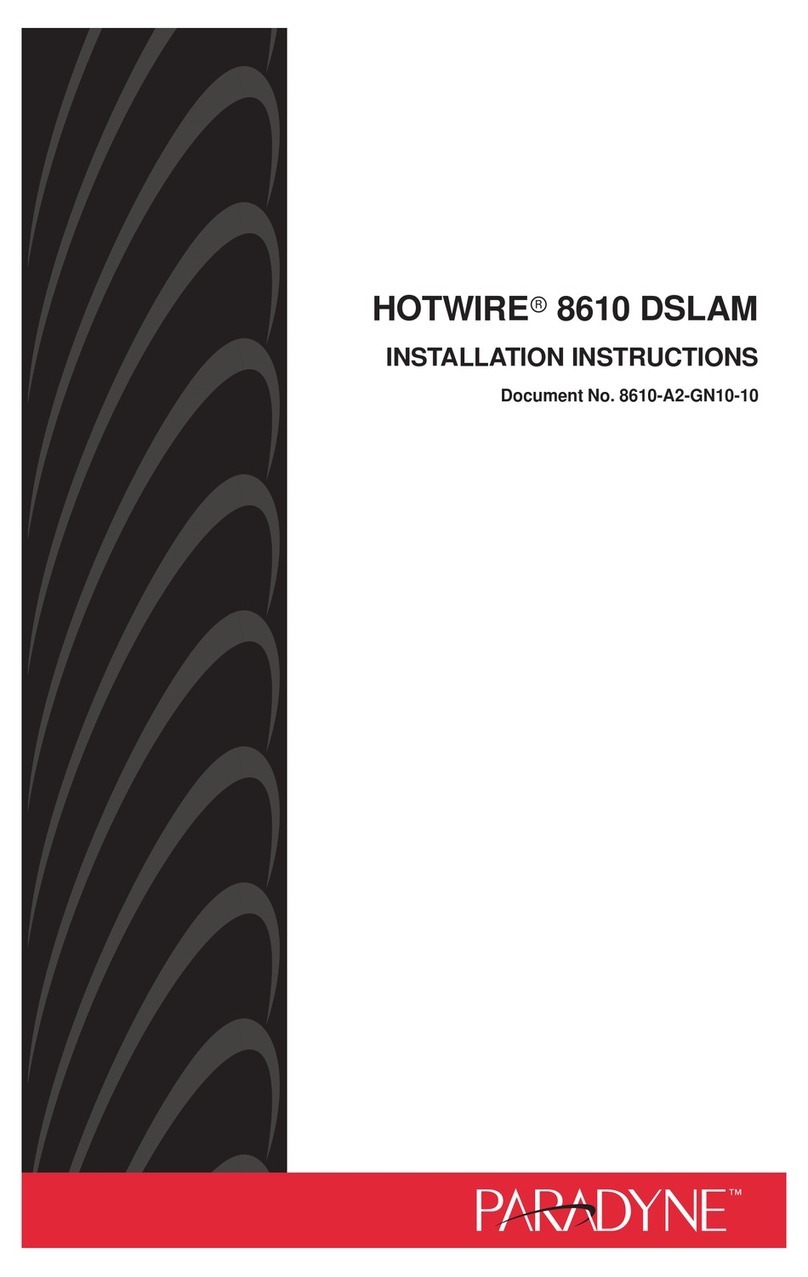
Paradyne
Paradyne HOTWIRE 8610 DSLAM installation instructions

GE
GE StoreSafe Pro Series manual