GEViCAM GD-155000 User manual

GD
SERIES
Dual-tap Giga-bit Ethernet Cameras
GEViCAM Inc.
A GigE Vision Camera Company
GEViCAM OPERATIONS MANUAL
Rev: Ver. A.0.2
Date: 8-17-07
GD-155000
Preliminary

2
2
Disclaimer and Notice
The material contained in this manual consists of information that is proprietary to GEViCAM Inc. and may
only be used by purchasers of the products. GEViCAM Inc. makes no warranty for the use of its product and
assumes no responsibility for any errors which may appear or for damages resulting from the use of the infor-
mation contained herein. GEViCAM Inc. reserves the right to make changes without notice.
Warranty
All of our solid-state cameras sold in North America have a full three-year warranty. Those sold elsewhere
have a full one year warranty. If any such product proves defective during the warranty period, GEViCAM Inc.
will repair the defective product without charge for parts and labor or will provide replacement in exchange for
the defective product. This warranty shall not apply to any damage, defect or failure caused by improper use
or inadequate maintenance.
Certifications
CE Compliance
The GEViCAM platform including GP-3360, GP-2360, GP-3780 and GP-21400 cameras has been certified to
conform the requirement of Council Directive 89/336/EC for electromagnetic compatibility and to comply with
the following European Standards;
Immunity: EN50082 –2/1997
Emission: CISPR22: 1997/EN55011: 1998 Class B
All GEViCAM products bearing the CE mark have been declared to be in conformance with the applicable
EEC Council Directives. However, certain factory-installed options or customer-requested modifications may
compromise the electromagnetic compatibility and affect CE compliance. Please note that the use of inter-
connect cables that are not properly grounded or shielded may affect CE compliance.
FCC
This equipment has been tested and found to comply with the limit for a class A digital device, pursuant to
Part 15 of the FCC rules. These limits are designed to provide reasonable protection against harmful interfer-
ence when the equipment is operated in a commercial environment. This equipment generates, uses and ra-
diates radio frequency energy and, if not installed and used in accordance with the instruction manual, may
cause harmful interference to radio communications. Operation of this equipment in a residential area may
cause harmful interference, in which case the user will be required to correct the interference at his expense.
Warning
Changes or modifications to this unit not expressly approved by the party responsible for FCC compliance
could void the user’s authority to operate the equipment.
GEViCAM Inc

3
3
Table of Contents
1 Introduction Page
1.1 Product Family Description 6
1.2 Features and Benefits
1.3 GigE Vision Standard Compliant Models
1.4 System Configuration 7
1.4.1 Camera Power Requirement
1.4.1.1 GPIO Connector
1.4.1.2 RJ-45 Connector
1.4.2 PC Requirement
1.4.2.1 PC Basic Requirement
1.4.2.2 Network Adaptor
1.4.2.3 Ethernet Switch
2Installation 8
2.1CameraSetup
2.1.1 Getting started
2.1.2 Connect power
2.1.2.1 GPIO Pin Assignment
2.1.2.2 RJ-45 Connector and Ethernet Cable
2.1.2.3 Cable Assembly and Power Supply
2.1.3 Lens Mount and Lens Selection
2.2 Driver Installation 9
2.2.1PCSoftware
2.2.2 Install High Performance Driver
2.2.2.1 Ver 2.2.1 High Performance Driver
2.2.2.2 Ver 2.3.1 e-Bus Driver (Recommended) 10
2.2.2.3 Connecting Ethernet and Open Coyote Application
3 Operation (Camera Control Section) 11
3.1 GigE Camera Function Blocks
3.2 Coyote Application Software (Ver. 2.3.1.) 12
3.2.1 Launch Coyote Application
3.2.2 Configure Camera Control 13
3.3 Basic Camera Control, Register-base Control 14
3.3.1 Gain and Black Level Control
3.3.1.1 Gain Control
3.3.1.2 Black Level Control
3.3.1.3 Dynamic Range and S/N Ratio
3.3.2 Data Output Modes
3.3.2.1 12-bit, 10-bit, 8-bit Linear Output
3.3.2.2 8-bit LUT (Gamma) Output
3.3.2.3 16-bit Data Conversion
3.3.2.4 Test Pattern Generator 15
3.3.3 Asynchronous Reset and No-delay Reset
3.3.3.1 H and V Async Reset
3.3.3.2 Trigger Mode Selection
3.3.4 Exposure Control
3.3.4.1 Programmed Exposure Control
3.3.4.2 Pulse-width Exposure Control 16
3.3.4.3 Internal Exposure Control Pulse Generator
3.3.5 Full Scan and Partial Scan
3.3.5.1 Full Scan
3.3.5.2 Partial Scan
3.3.5.3 ROI Setting in Frame Grabber Function
GEViCAM Inc

4
4
GEViCAM Inc
Table of contents (continue) Page
3.3.6 Strobe/ Internal Exposure Signal Output 16
3.3.7 Back-to-back Strobing 17
3.3.8 Multiple Frame Capture (ITS Mode) and Bracketing Exposure
3.4 Advanced Camera Functions (Hardware Description)
3.4.1 RS-485 Interface
3.4.1.1 RS-485
3.4.1.2 CAN Device Control 18
3.4.2 Opto-isolated I/O
3.4.3 Audio CODEC I/O
3.4.4 Temperature Sensor
4 Operations (Frame Grabber Section …. GigE Interface) 19
4.1 General Description of GigE Interface
4.2 Related Documents
4.3 Functions and Features
4.4 Camera Configuration and Control 20
4.4.1 Camera Interface (Select Camera)
4.4.2 Pixel Format and Image Size Selection
4.4.3 Port Control (Serial Port Control for Camera Functions) 21
4.4.4ColorCamera 22
4.4.5 Save Configuration Parameters to Flash
4.5 Image Capture and Save 23
4.6 GPIO (Programmable Logic Control) 24
4.6.1 Programmable Logic Controller Functions
4.6.1.1PLCMainBlock
4.6.1.2 Configuring PLC Functions 25
4.6.1.3 Signal Routing Block
4.6.1.4LUT
4.6.1.5 Programming Pulse Generator 26
4.6.1.6 Enhanced Function Block Connections 27
4.6.1.7 Programming PLC Control Bit
4.6.1.8 Other Programmable Logic Controller Function 30
4.6.2 GPIO Connector and Cables
4.6.3 GPIO Input and Output 31
5Camera Control Command and Register Map 32
6SDK 33
6.1 SDK (Software Development Kit)
6.2Upgrade
7 Troubleshooting

5
5
GEViCAM Inc
APPENDIX
Page
8Specifications 34
8.1Electrical
8.2 Power Consumption and Thermal consideration
8.3Mechanical 35
9PleoraDocumentLists 36
9.1 iPort Coyote
9.2 iPort IP Engine Instruction
9.3 e-Bus Instruction Quick Start 37
9.4 iPort Instruction Quick Start
9.5 What’s New in Version 2.3.1
9.6 PLC (Programmable Logic Controller) Reference
9.7 Troubleshooting Guide 38
List of Figures and Tables
Page Page
Fig. 1 MDR-14 Connectors 8 Fig. 2 PSC 12 8
Fig. 3 GPIO, Industrial RJ-45 Cables 8 Fig. 4 Device Manager 9
Fig. 5 Locate File 9 Fig. 6 Pro/1000 Grabber Driver 9
Fig. 7 Driver Selection 10 Fig. 8 Coyote Connection Detect 10
Fig. 9 IP Engine Selection 10 Fig. 10 Set IP Engine IP Address 10
Fig. 11 Coyote Connection 10 Fig. 12 Camera Function Blocks 11
Fig. 13 High Performance IP Address 12 Fig. 14 Camera Selection 12
Fig. 15 Configuration, Image 12 Fig. 16 Configuration, Pixel 12
Fig. 17 Coyote Acquisition 12 Fig. 18 Port Communication 13
Fig. 19 Camera Gain Register Code 12 Fig. 20 Async Trigger Timing 16
Fig. 21 Internal Reset Delay 16 Fig. 22 Back-to-back Strobe Timing 17
Fig. 23 GPIO Board 18 Fig. 24 Select Camera 20
Fig. 25 Acquisition 20 Fig. 26 Pixel Depth 20
Fig. 27 Image Size 20 Fig. 28 Port Communication, Read 21
Fig. 29 Port Communication, Write 21 Fig. 30 RGB Starting Pattern 22
Fig. 31 RGB Filter 22 Fig. 32 Save Configuration to Flash 22
Fig. 33 Save State to Flash 22 Fig. 34 Grab Continuous 23
Fig. 35 Image Saving, File format 23 Fig. 36 PLC Main Block 24
Fig. 37 GEViCAM PLC Block 24 Fig. 38 Configuration, IP Engine 25
Fig. 39 Signal Routing Block, I0 25 Fig. 40 Signal Routing Block, LUT 25
Fig. 41 Enhanced Func. Block, Trigger 26 Fig. 42 Coyote, IP Engine 26
Fig. 43 Pulse Generators 26 Fig. 44 Enhance Function Blocks 27
Fig. 45 PLC Control Bits 27 Fig. 46 Pulse Generator 0, LUT 28
Fig. 47 Pulse Generators 28 Fig. 48 PLC Control Bits 28
Fig. 49 Delayer Block 29 Fig. 50 Delayer LUT 29
Fig. 51 Pulse Gen / Delayer 29 Fig. 52 Pulse Generators 29
Fig. 53 Back Plate 30 Fig. 54 MDR-14 Connectors 30
Fig. 55 GPIO Industrial RJ-45 Cables 30 Fig. 56 Cable Structure 30
Fig. 57 TTL Input / Output 31 Fig. 58 Opto-isolated I/O 31
Fig. 59 Mechanical Drawing 35 Fig. 60 SDK Documentation List 36
Table 1 Pin Assignment 8 Table 2 Auto-iris Connection 18
Table 3 Control Registers Address & Data 32 Table 4 Electronic Specifications 34

6
6
GEViCAM GigE Vision Cameras Operation Manual
1. Introduction
1.1 Product Family Description:
GEViCAM is specialized in the state-of-the-art Giga-bit Ethernet camera design and manufacturing.
The GD-series are the dual-tap models of high performance GigE Vision camera family.
In the small and robust package, it contains two-channel digital video camera functions, frame grab-
ber, programmable logic control, and Giga-bit Ethernet interface all together. In today’s many applica-
tions, which use full advantage of digital data for image capture, process and manipulation for the best
result, the GigE technology excels the most. GEViCAM family is designed to serve for the demanding
and vast applications.
The high speed, high band width data output directly from camera to PC in 100m of distance elimi-
nates the need of a frame grabber, expensive multiple cables, and a simple PLC device or industrial
interfaces.
The applications cover machine vision, high security, ITS, medical and scientific field.
This base model series provide a dual-tap CCD platform for VGA, mega-pixel, and 5 to 10 Mega-pixel
cameras in monochrome and RGB Bayer color.
1.2 Features and Benefit
•1Gigabit/s high speed point-to-point transmission
•No frame grabber required for image capture
•100m with Gigabit Ethernet cable CAT5e or CAT6
•GigE Vision standard compliance
•Field upgradeable firmware via Ethernet
•Excellent S/N (>58dB) for 12-bit, 10-bit or 8-bit output, 12 to 8-bit Gamma conversion and cus-
tom LUT
•Dynamic channel balance
•No-delay asynchronous reset with time stamp and async shutter
•GPIO for local I/O, RS-485 communication for auxiliary devices, Audio I/O
•Color (RGB Bayer) versions
•Miniature, robust package (34 x 34 x 68 mm)
•Industrial Ethernet and GPIO connectors
•Various drivers available for existing machine vision software
•Extensive software developer’s kit (SDK)
•Best cost-performance GigE camera
1.3 GgiE Vision Standard Compliant Cameras
The latest development of GigE Vision standard requires separate protocol from Pleora iPort protocol
and the GigE Vision protocol version is called “GEV” version. There are some minor trade off from the
versatile and flexible iPort protocol but GEV plays key roles to interface with many GigE compliant API
software and devices as “Plug and Play” connectivity. Because of the key protocol differences, the
firmware is not compatible each other and must order as the separate models. However, the SDK and
control software is the same for both models.
Please refer supplemental GEV Manual for the GigE Vision compliant cameras. The GigE Vision
models are marked as “GEV” or “GigE” logo.
GEViCAM Inc

7
7
1.4 System Configuration
The GigE Vision cameras require two parts of system configurations; Camera setup and PC setup.
1.4.1 Camera Power Requirement
1.4.1.1 GPIO Connector
Camera power is 12 V DC ±10% and we recommend to support more than 1A on inrush current at the
start-up.
The typical current consumption of GD-series is 400 mA at standby and 450 mA when it sends
streamed images.
We suggest to use the industrial GPIO cable (Intercon1; GPIO-XX-PS) but the standard MDR-14 pin
plug (3M;10114-3000PE) with a MDR shell can be used.
1.4.1.2 RJ-45 Connector
Data communication uses standard RJ-45. The GigE standard requires CAT-5e or CAT-6 Ethernet
cables.
Either Patch cable or Cross cable works for the camera interface. We suggest using the industrial
GigE cable (Intercon1 GigE cable; GEVPT-XX-P) for the secure and reliable operations.
1.4.2 PC Requirement
1.4.2.1 PC Basic Requirement
To achieve the full bandwidth of the GigE Vision cameras, a PC must have at least
•1.4 GHz or faster CPU (Pentium 4, Athlon)
•Windows 2000, XP Professional, or Red Hat Linux (custom application)
•More than 128M Byte of RAM
•A GP video card supporting DirectX 8.1 and not using shared memory (See Pleora documents;
A normal video card works but with less efficiency of the CPU performance.) Built-in graphic card
in a laptop or general PC may not be able to display full resolution of GD-155000. Reduced image
size for display format may be required.
1.4.2.2 Network Adaptor
A PC must have a GigE NIC (Network Interface Card) to achieve full performance. Each NIC card
contains an Ethernet PHY chip made by various companies. For the best performance, we suggest
using the Intel Pro1000 NIC. With the Pleora e-Bus Driver, other NIC can be also used.
See driver installation section.
We recommend the following network adaptors;
Intel Pro/1000 MT Desktop Adaptor (32-bit PCI),
Intel Pro/1000 MT Server Adaptor (64-bit PCI-X),
Intel Pro/1000 MT Dual and Quad Port Server Adaptors.
1.4.2.3 Ethernet Switch
Since the GigE Vision standards comply with the Internet Protocol, the products should work with
standard switches. However, machine vision industry requires jumbo-packet handling thus limits the
selection of applicable switches.
The following switches have been suggested by Pleora.
3COM 3C1740x (3800 Family)
3C1770x (4900 Family)
DLINK DGS-10xxTx 10/100/1000 Family
DGS-3308-FG, DGS-3308-TG
CISCO WS-C3750G-12S-S
The above list may change from time to time. Please contact GEViCAM or Pleora for the updated
models.
GEViCAM Inc

8
8
2. Installation
2.1 Camera Setup
2.1.1 Getting started
We recommend you to save the original packing cartons for camera and accessories in case you
need to return or exchange an item. It is a good idea to bench-test the products prior to the field
installation. GEViCAM cameras have highly integrated functions and do not need many add-ons.
However, please check the product items and options or accessories if you ordered them.
2.1.2 Connect Power
2.1.2.1 GPIO Pin Assignment
The GPIO connector is MDR-14 and the mating
plug is 3M’s P/N 10114-3000PE or equivalent.
Apply +12VDC (±10%) to pin 8 and return (Power
GND) to pin1. (Table 1) (Fig.1)
Once the polarity is confirmed, power up the cam-
era. The current consumption is around 350mA
without connecting Ethernet cable to PC.
2.1.2.2 RJ-45 Connector and Ethernet Cable
Connect a CAT-5e or CAT-6 Ethernet cable to
camera and PC.
The Ethernet connector has two green LEDs built-in.
They are not power indicators. They light when Ethernet
cable is connected to PC. One LED brinks when the data is
being transferred. Once Ethernet is connected, the power
consumption goes up to 400mA range without data transfer
(standby state).
2.1.2.3 Cable Assembly and Power Supply
We suggest to use an industrial GPIO cable made by
Intercon1. (P/N GPIO-XX-PS)
For the easy application or demonstration, the PSC12
(Power Supply with a MDR connector) is also available as
our accessory item. (Fig.2)
Industrial GigE cables are also available from Intercon1.
(P/N GEVPT-XX-P). These cables are available in various
length (in XX m).
The strain relief of both GigE and GPIO cables are using
thumb screws to secure the contacts. (Fig. 3)
2.1.3 Lens Mount and Lens Selection
Standard lens mount is C-mount and CS-mount is available
as option. Choose proper lens for the field of view and aper-
ture control as optics are always important factors for good
image quality. We call “Garbage in - garbage out princi-
ple”. No matter how good the image process is, if input is
not good, the final data may not be good at all. Keeping the
initial image the best quality with optics and camera perform-
ance prior to the frame grabbing, is very important.
GEViCAM Inc
Pin Description Pin Description
1 GND (Power RTN) 8 +12VDC In
2 GND 9 Trigger In (TTL)
3 Strobe out (TTL) 10 RS-485-
4 RS-485+ 11 Opto D1 in-
5 Opto D1 in+ 12 Opto D2 out-
6 Opto D2 out+ 13 Audio out
7 GND 14 Audio in
Table 1
Fig. 1
PSC12 Fig. 2
GPIO Cable GigE Industrial Cable
Fig. 3

9
9
2.2 Driver Installation
2.2.1 PC Software
Use the Pleora Coyote Software to launch the High-performance Driver and GigE communication. For
detailed installation of the High-performance Driver, please refer the Pleora’s instruction document.
The Standard Ethernet Driver (Windows Stack) has to be replaced with the High-performance Driver.
The current version of driver is ver. 2.2.1 (High Performance Driver) or 2.3.1 (e-Bus Driver).
The ver. 2.2.1 is recommended only for Intel NIC (Pro/1000) and whoever has already been using it.
The ver. 2.3.1 works for various NIC manufacturers. You can choose either High-performance Driver
or E-Bus Driver based on your system.
For the new installation, we suggest to use the ver.
2.3.1.
2.2.2 Install High Performance Driver
At first, a GigE NIC card (Network Interface Card) is
required for your PC. Intel Pro 1000 NIC card is
recommended in the PC. Install from the file or
download the Pleora Coyote SDK software, which
contains the High-performance Driver in Pleora
iPort file. For the ver. 2.3.1 installation, skip 2.2.2.1.
2.2.2.1 Ver. 2.2.1 High Performance Driver
Go to “Control Panel” and open “System”. Go to
“Hardware” and select “Device Manager”. Look for
“Network adapters” and find which cards are listed.
It should show “Pro/1000 network connection” or
similar. Right click and select “update driver” (Fig.
4). Go to Window search for software, then select
“Install from a list (advanced)”. Next, select “Don’t
search. I will choose driver to install”. It may list up
available drivers and highlight “Pro /1000 Grabber
driver”.
If it is not listed, it may ask to find the file. Browse
the file where the Pleora iPort software exists. Find
“Pro 1000” (may be inside of Window NT or 2000
file) and click (Fig. 5). The High Performance Driver
should be installed into the PC.
After the High Performance Driver installation, the
Device Manager shows Pleora icon for the Grabber
Driver. (Fig. 6)
To switch back to the original Pro/1000 network
driver (Window Stack), repeat the same process by
selecting “Pro1000 Grabber Device”, right click and
update the driver with the original version (i.e.
Pro/1000 MT Server).
GEViCAM Inc
Fig. 4
Fig. 5
Fig. 6

10
10
2.2.2.2 Ver. 2.3.1 e-Bus Driver (Recommended)
Install the GEViCAM SDK ver. 2.3.1.
If you have the ver. 2.2.1 or older one installed, uninstall the
driver at first and make sure iPort file of “Pleora Technologies”
in the Program file is empty.
The installation creates two application icons. One is Coyote
and another is Ethernet Bus Driver Tool. To allow e-Bus Driver
Installation Tool to see all NICs, please make sure all the NICs
have their original Window driver installed.
Follow the Ethernet Bus Installation Tool instruction and select the best driver for your system. The
High performance driver is the best choice for Intel NICs. The good alternative is the e-Bus Driver with
“optimal” for Intel NICs and with “universal driver” for other NICs.
(Fig. 7)
Each time you change the driver, you are required to reboot the
computer. Also when you change the non-Window stack
driver, you have to install Window stack (original driver) at
first, then change to the e-Bus or High-performance Driver
through the Windows stack.
The driver installation method described in 2.2.2.1 can be also
applied for the High Performance Driver of ver. 2.3.1. By doing
so, you do not have to reboot your computer.
2.2.2.3 Open Coyote Application
Connect the camera and PC with an Ethernet cable (CAT-5e or
CAT-6) and power up the camera. LEDs of RJ-45 connector will
be steadily ON. If not, make sure an Ethernet
cable is connected to the PC. Open the Coyote
Application. Coyote window appears. (Fig. 8)
Press “Detect” button. It may take for a while (5
to 10 seconds) to show up IP address. (Fig. 9)
Click OK.
Make sure there is no Firewall protection to this application. In order to check, go to
“Control Panel“ and find “Windows Firewall” icon and add the exception for Coyote
application.
If it warns “subnet do not match”, change the IP address of your camera to match the
network address (Left two major blocks must match. Number must be from 1 to 255).
In this (Fig. 10) picture, it indicates address “0” is used and you need to change to
any number except for 0. Type 1 for the example.
Next is to select the camera type and select “standard camera link camera”. GigE
cameras are not camera link but the internal camera structure is
using Camera Link interface signaling. (Fig. 11)
Once all connections and detections are done, you are ready to
see the image by opening the “Acquisition” tab and click “Start”.
For detailed camera configuration, see section 4.4.
For users who do not have GigE NIC cards but have a normal
Fast Ethernet NIC, the same filter driver can be used with limited
bandwidth. Regardless, the Coyote Filter Driver must be used
(cannot use TCP-IP driver).
GEViCAM Inc
Fig. 7
Fig. 8
Fig. 9
Fig. 10
Fig. 11

11
11
GEViCAM Inc
3. Operations
3.1 GigE Camera Function Blocks
• Imager Block
The Imager block is specific to imager type and it contains the imager driver circuit. By simply
changing this block (single PC board), many types of resolution, size, characteristics of CCD and
CMOS sensors are adapted to the same platform while other blocks remain in the same hardware.
• Signal Process Block
The signal process section is critical to the high performance and the image quality. The 12-bit
high speed A/D conversion is standard for all models. On this board, a RJ-45 connector is
mounted with the shortest traces from the PHY chip.
• GigE Block
The GigE Block consists of a FPGA, PHY and memory ICs.
• FPGA
♦ Timing Gen Block
This is a control logic and timing generator block for the camera. The design prince
ple is register base and easy to reprogram various imager types without effecting
other functions.
♦ iPort (Pleora core) Block
The heart of GigE interface and frame grabber function control is in this block.
♦ PLC (Programmable Logic Controller)
The GPIO function interface is called PLC as it generates necessary functions for
PLC interface.
• PHY
A low power, small package PHY chip is used in a very dense layout. The heat dissipation I
s carefully removed to outside with the heat-pipe architecture for the high reliability opera
tion.
• Memory
A fame grabber function requires large memory space. The standard size is 16 MB but can
be extended to 64 MB as the custom option.
• Power and GPIO
This block seems simple but creates the
major differences from other cameras.
Low power consumption, extremely low
noise characteristics and unique GPIO
functions are the result of our expertise
based on many years of design experience.
• Easy Customization
This is the very refined platform design and easy to build
custom-design products out of these blocks. The blocks
of Imager, Signal and GPIO boards are easily customized.
Please contact GEViCAM for the specific requirement.
Imager
Block
(Dual-tap)
Signal Block (Dual circuit)
Power and GPIO
Timing
Gen i-Port PHY
Memory Block
Fig. 12

12
12
3.2 Coyote Application Software (Ver. 2.3.1)
3.2.1 Launch Coyote Application
Connect Ethernet cable between PC and the RJ-45 connector on
the camera, and GPIO cable between the GPIO connector on
the camera and the power supply. Power up the camera. Launch
the Coyote image-capture-and-control software.
• Firstly, select “display this dialog at application start up” and
click “OK” on application option. Coyote dialog box with
“Connection” tab appears.
• Secondly, click “Detect device” and “High Performance IP
Driver with MAC address” appears. (Fig. 13)
Click “address” and “OK”. The IP addresses appear in the
Connection dialog box.
• On “Camera”, click “Select camera”. GEViCAM cameras are
designed to take the standard Pleora “camera link camera”.
Click “OK”. Then click “Apply”. The IP Engine Setting infor-
mation status indicates “Connected to device”. (Fig. 14)
• Select next tab “Acquisition”. Go to “Configure” and mark
“Show advanced configuration pages”.
• Select “Pixel” Tab. The factory default of B/W camera output
is 8-bit with Dual output format “Right Inverted”. So select 8-
bit (default). And click “OK”. (Fig. 16)
• Open “Image” tab, the image size
for GD-155000 is 2456 x 2058 but
can be changed to smaller numbers
for display limitation of PC. When
smaller width is selected, Offset X
must have the difference from 2456
to set number (example: for 2000 x
2000, offset X is 456). Note: The
horizontal number must be increment
of 4. For the quick test purpose, you
can stay with the default value until
you see image capturing and ready
for configuration changes. (Fig. 15)
For the color versions, Coyote takes only 8-bit input and Gamma 0.45 is
more common for color display. So the factory default of color camera is
set to 8-bit with Gamma. Select
RGB color and the starting pixel orientation. For detail of the
color camera setting, please refer to “Port control” described in
camera control to set the output format to 8-bit Gamma LUT and
color selection in section 4.4.4.
• Acquisition
Now go to acquisition and select “Grab-continuous” and
“Start”. You will see the live images. The grabbing infor-
mation should indicate around 12 fps of image capturing
for 5 Meg, 200 fps for VGA.
At this stage, the image displayed may not be perfect
and you may need further camera and grabber configure-
tions. (Fig. 17)
GEViCAM Inc
Fig. 13
Fig. 14
Fig. 17
Fig. 16
Fig. 15

13
13
3.2.2 Configure and Camera Control
Firstly, open “Configuration Advanced” and set up the
correct image size and pixel information from each tab.
Next, select “Port Communication” tab.
The port is “Serial Port 0” for this camera control. Se-
lect two locations of “Hexadecimal” marks in “Send”
and “Receive”. (Fig. 18)
The camera takes the command as virtual RS-232
control. “Write” starts with 57(hex) and “Read” is 52,
which are equivalent to ASCII “W” and “R”.
For each 8 bit, command has to be sent. Click “Send”
or hit “Return” at each 8-bit input. (If you are using the
ver. 2.2.0, this is only the way to send command).
For example, the register address of “Gain Control “ is
0010 and the data of 32-bit follows. The gain value
resolution is 10-bit and only changes from 0 to 1024
(10-bit). So, sending the maximum gain of 42 dB is;
00 00 03 FF.
Therefore, the sequence of the “Write” command is;
57-send, 00-send, 10-send,
00-send, 00-send, 03-send, FF-send.
After the completion, ACK of “06” appears.
With 42 dB of gain, you will see significantly bright but noisy images.
If you want to see the register reading, type “52” <send>, then “00” <send>, “10” <send>. You will see
data of the address and ACK “0D”.
In the improved version of 2.3.0, this Port Communication command can be sent as one string.
Type “52” <space> “00” <space> “10“<return>. You will see the same read out as before. If you
change the last “10” with “11”, you will get another data reading of the black level.
It is the same process for the “Write” command.
Type “57 00 10 00 00 00 50” <send ( or return)>. For each 8 bit, you have to hit space bar.
Make sure you set back the original gain setting, type “57 00 10 00 00 00 50” <return>.
“Configure” window shows various functions besides the “Port Communication”.
The detailed information is described in section 4.4.
GEViCAM Inc
Fig. 18
Fig. 18

14
14
3.3 Basic Camera Control Register-base Camera Control
The GEViCAM platform is register base. The command control is done with the 16-bit of address and
the 32-bit of data in hexadecimal. To send the “Gain”command of 255 (15dB) as an example, start
with the “Write”command “57” followed by the address “00 10” and the data “00 00 00 FF”. It receives
acknowledgement of “06” after the completion of command. The “Read”command is “52”.
3.3.1 Gain and Black Level Control
3.3.1.1 Gain Control (GainRaw):(0010)
The camera gain is controlled in the10-bit resolution from 6 dB to
42 dB (0~3FF). The variable gain amplifier is set by;
VGA Gain (dB) = (VGA code x 0.035 dB) + 5.3 dB
3.3.1.2 Black Level Control (BlackLevelRaw):(0011, 0019)
The video black level control is in the 8-bit resolution from 0 to 16
digital value out of 255 (0~FF). The factory default is set at 4.0
(digital value)
3.3.1.3 Dynamic Range and S/N Ratio
The GEViCAM platform is set the factory default at the best dy-
namic range. Since the platform performs at very low noise floor
providing overall signal to noise ratio of 60 dB, the cameras are set to operate for the widest dynamic
range in the 12-bit resolution. Because of such a low noise floor, the images, which may look too dark
to human eyes, still contain very good signal once it is enhanced. On the contrary, if high gain is used,
the dark image may be visible but other brighter sections will be saturated and lost. Our concept of a
digital imaging camera is to provide the best signal to noise ratio and use full advantage of digiti-
zation for post image processing (can be real time).
However, those who need high gain operation, it has Max. 42 dB of internal gain adjustment, which is
extremely high gain!
The simplest measurement of S/N Ratio is using black level data deviation (standard-deviation) in a
large region of interest (ROI). The specific definition of SNR is 20 log (255/ rms-noise) and rms-noise
can be replaced by standard-deviation; SNR = 20 log (255/standard-deviation). 255 is saturation level
in 8-bit. Temporal noise, which is averaged in frame by frame data for the exact S/N measurement, is
ignored in this simple measurement. However, in the single frame, the large ROI deviation provides
good representation in practical value. In the 8-bit data, the popular software such as Photoshop can
measure the standard deviation.
3.3.2 Data Output Modes (0012)
3.3.2.1 12-bit, 10-bit, 8-bit Linear Output (PixelDepth): (00 00 00 00, - 01, -02)
The GEViCAM platform has a 12-bit high speed A/D converter and the output is selectable of 12, 10
and 8-bit (Factory Default: 8-bit). Both 10 and 8-bit conversions are done by taking the most significant
bits out of the 12 bit. All black and white cameras are set at the linear output. Dual-tap output must
use packed data format for 10 and 12 bit (Pixel Tab).
3.3.2.2 8-bit LUT (Gamma) Output: (00 00 00 03)
The 12-bit to 8-bit conversion LUT (Look Up Table) is built in. The multiple knee Gamma (0.45) LUT is
embedded for the better dynamic range but limiting dark noise. All color cameras are set the factory
default to 8-bit and Gamma 0.45. Custom LUT is unloadable. See field upgrade in section 6.2.
3.3.2.3 16-bit Data Conversion: (00 00 00 20)
Many image process or analysis software uses 8-bit or 16-bit raw data input. This selection allows 12-
bit output to be used in 16-bit image input tool. The most significant 12-bits are used in 16-bit.
(Note: Italic description in parentheses is based on GigE Vision standard naming convention.)
GEViCAM Inc
Fig. 19

15
15
3.3.2.4 Test Pattern Generator: (00 00 00 12)
A test pattern generator is built in. It is a useful tool to diagnose Ethernet communication and camera
functions. The output is 8-bit pattern.
3.3.3 Asynchronous Reset and No-delay Reset:
3.3.3.1 H and V Async Reset
The external trigger is a hardware trigger applied to pin #9 of GPIO connector with TTL level same as
Vinit or edge trigger. The default polarity is negative going edge. Positive going edge is selectable by
selecting the register (00 21 00 00 00 01).
GEViCAM has the no-delay reset capability to reset both horizontal and vertical without internal sync
delay. Only a few fixed pixel-clock delays (4 clocks typical) exist as the internal logic delay. The data
output delay occurs through the signal process but it is not the trigger or reset delay. The image cap-
ture is implemented with the internal no-delay reset timing thus they are always synchronized to the
trigger pulses regardless the number of cameras.
This eliminates a need of phase lock loop circuit for synchronizing multiple cameras.
3.3.3.2 Trigger Mode Selection (TriggerMode): (00 23)
In the trigger modes, there are various useful modes as follows;
(1) Async No-delay Trigger: (00 00 00 01)
It resets both internal H and V sync to pixel clock level.
The exposure time is programmable in each mode. The camera module outputs one FVAL equivalent
pulse per trigger for the image capturing. It finishes the complete frame before resetting with the next
trigger. If the trigger pulse comes in before the completion of frame data, it will be ignored. This fea-
ture avoids malfunction of image capturing caused by trigger noise and chattering.
(2) Pulse-width Control (ExposureWidth): (00 00 00 02)
It resets at both external pulse leading edge and trailing edge with no-delay reset. The exposure time
is exactly the same as the pulse width between the leading edge and the trailing edge.
(3) Hardware or Software Trigger (TriggerSelector)
The trigger type is selectable as a part of PLC (GPIO) functions. The hardware trigger is TTL external
trigger and the software trigger is initiated by the PLC program from the PC via Ethernet.
(4) Trigger Polarity (TriggerActivation): (00 21) (00 00 00 00, 01)
The leading edge polarity of either Falling edge or Rising edge is selectable (Factory Default: Falling
edge).
3.3.4 Exposure Control
3.3.4.1 Programmed Exposure Control: (00 24, 00 27, 00 28)
The programmed exposure control is done by electronic shutter mechanism which discharges the
photodiode electrons at the trigger and starts integrating at the shutter timing by counting number of H
clocks. Then the electronic charges are transferred to CCD shift registers to clocked out as video out-
put. This mechanism is applied to all async / shutter modes in normal scan mode, async mode, and
ITS mode. In essence, the electronic shutter control and exposure control is the same meaning.
Exposure Control (ExposureMode, ExposureTimeRaw): (00 24)
The exposure time is variable from 1n to FFFF (65535)n. “n” is number of counts of horizontal lines.
(n = 1H)
VGA 5 Mega-pixel
1n = 10 µs 1n = 32 µs
(= 1/100,000sec) (= 1/30,000sec)
Example: n = FF in hex = 255x32µs = 8.16 ms of exposure in 5 Meg-pixel.
If you want to set 1ms (1/1000 s) for 5 Meg, n = 1000/32 = 31 = 1F (Hex).
So, enter “00 24 00 00 00 1F”.
GEViCAM Inc

16
16
3.3.4.2 Pulse-width Exposure Control
This is selected as Async Pulse-width Control in trigger mode (00 23, 00 00 00 02). The pulse width
between the falling (leading) edge and the rising (trailing) edge is the exact period of the exposure.
The pulse width is not synchronized with the internal timing such as horizontal clock but only latched
with the high speed pixel clock in 25 ns of latency to reproduce identical timing as the trigger pulse.
This is also useful tool for synchronizing multiple cameras triggered with a variable exposure.
3.3.4.3 Internal Exposure Control Pulse Generator
The Coyote software allows user to trigger GigE cameras from the PC or host. See PLC functions in
section 4.6.1.
Note: Some early models may be required firmware upgrade to implement this function.
3.3.5 Full Scan and Partial Scan (00 23, 00 00 00 10, -11, -12, -14)
3.3.5.1 Full Scan: (00 00 00 00, -01, -02, -03, -04)
The basic platform of GD-series use the progressive scan CCD (or CMOS). The full scan image is by
progressive scan, which does not reduce the resolution by capturing one frame (i.e. field image in
Interlace reduces the resolution). The platform uses 40MHz x2 clocks as standard and the typical full
frame rate is 200 fps for VGA, 12 fps for 5 Mega-pixel. The Coyote grabber function “image
size” is set to cover the camera’s active pixel data. The horizontal number is multiple of 4 and the verti-
cal is the exact vertical pixel numbers.
3.3.5.2 Partial Scan: (Mode A: 00 00 00 10, - 11, -12, -14 and Mode B: - 20, -21, -22, -24)
The GD-series output the full frame images in higher frame rate than most of similar cameras but also
output the partial scan images with even higher frame rate. The VGA full scan is 200 fps but 240 line
partial scan outputs 380 fps. The factory set partial scan lines are 240 for the VGA, and 1380 (A) and
1080 (B) for the 5-Meg. The location of starting lines is programmable (00 26). The vertical area is
variable only in horizontal line counts (Horizontal pixel number does not change). This field of view
adjustment is helpful to align the point of interest without moving the camera position.
The exposure control and other functions of normal scan are also applied to the partial scan modes.
3.3.5.3 ROI Setting in Frame Grabber Function (Coyote Application)
Along with the camera side of partial scan, the frame grabber function of the GigE cameras can select
specific size of ROI (Region of Interest). This does not help increasing the fame rate but the data
transmission and bandwidth can be improved by sending small section only, which, in turn, speeds up
the signal processing. See the image size setting in Coyote Application 4.4.2.
3.3.6 Strobe/ Internal Exposure Signal Output
For all async reset modes, the internal exposure pulse is output from the GPIO pin (Pin #3). This can
be used to trigger strobe or other control devices. The output is TTL - active high.
The signal is same as the internal exposure control pulse so that it can be monitored for the exposure
timing, image grabbing, and internal frame rate in each mode. The internal delay of all resets is 4 pixel
clock. (Fig. 20 and 21)
GEViCAM Inc
PW control Strobe out and
trigger
Fig. 20 Async Trigger and Internal Reset Timings Fig. 21 Internal Reset Delay

17
17
3.3.7 Back-to-back Strobing: (00 23 00 00 00 03), (00 25)
Two consecutive strobes per one trigger are output with a programmable interval before and after the
CCD transfer gate. Thus two frame images of strobe lightings at very short interval can be captured.
Since this method freezes objects in specific interval or almost simultaneously, the application is effec-
tive for high speed object motion analysis, dual lighting imaging (i.e. front-lit/back-lit, two color LED
strobes, visible and IR lighting, etc.). By analyzing the two frames, it can find the particle trajectory, ac-
curate motion speed, different angle views, different material properties, etc.
This mode is only applied to the Full Scan Mode and the programmable interval (00 25) is within the
one frame period. (It can be longer as custom option such as two frames or 100ms apart).
The interval programming is;
= Number of (n - 2) x 1H (horizontal clock)
For 1 ms interval for 5-Meg, the command is;
57 00 25 00 00 00 1B
( n-2 = 1000/32 = 31 , n = 33 = 21 hex).
To be precise, this gives 1.01375 ms of interval.
The minimum interval is 00 00 00 04.
This mode is only effective in the dark environment
and strobe lights are only the light source.
3.3.8 Multiple Frame Capture (ITS Mode), Bracketing Exposure: (00 23, 00 00 00 04)
This is similar to multiple-shot photography with different exposures to bracket the lighting conditions.
This is a good tool for ITS license plate reading, high security identifications of critical object imaging.
The number of frames being captured are programmable as well as each exposure time.
(Example; three shots per trigger with 1/250, 1/500, 1/1000s and use the best image among three)
The number of frames per trigger is programmed with (00 29) register. Currently you can choose one,
two or three frames. (00 00 00 00, -02, -03 respectively). The exposure is (00 24) for the first frame,
(00 27) for the second frame and (00 28) for the third frame.
3.4 Advanced Camera Functions (Hardware Description)
A GigE camera is powerful and it serves as a local server in a network. Besides common I/Os such as
external trigger input and strobe signal output, it provides additional port controls.
The GD-series can handle RS-485 Serial Interface, CAN (optional), Opto-isolated I/Os, Digital Audio
Input and Output, and Temperature Sensor.
3.4.1 RS-485 Interface
3.4.1.1 RS-485
Customers can send own RS-485 serial control protocol via Ethernet. Industrial RS-485, PROFI-bus,
surveillance pan-and-tilt / zoom lens control protocol, lane control signals are a few examples. A CAN
device can be also used for industrial serial control. In camera control (Port control), RS-485 is using
Port #1. (Port 0 is used for camera control). These serial communications are transparent between PC
and camera GPIO outputs. This application is simply using an Ethernet cable to handle user’s serial
communications besides image transfer so that there is no specific protocol provided as part of SDK.
See Port Control section 4.4.3.
GEViCAM Inc
Fig. 22

18
18
3.4.1.2 CAN Device Control
CAN (Controller Area Network) is slightly different serial bus using the same technology as RS-485.
As option, we can mount CAN device instead of RS-485 transceiver. CAN protocol must be provided
by user.
3.4.2 Opto-isolated I/O
There are two sets of optically-isolated inputs and outputs (Fig. 23).
With setting of solder jumpers J1 and J2, the IOs can be one input/one
output, two inputs, or two outputs. These IOs are designed for the appli-
cations which need different voltages, used in high surge/noise environ-
ment, the signal isolation from camera body, etc.
Standard setting is one input (D1=J1 open) and one output (D2=J2
short).
For input selection, J1 and J2 jumpers are open, and they are shorted
(solder jumper) for output.
Factory default is open on J1 and short on J2.
3.4.3 Audio CODEC I/O
It has a built-in audio CODEC to handle digital audio via Ethernet. It uses the high speed serial port
(Bulk port 0) to take audio stream. The input can be also used for analog input monitoring (AC cou-
pled) in audio frequency range (10 Hz - 10 KHz) such as the Doppler speedometer, chopped DC level
detection, etc. The audio input and output have no audio amp or speaker driver. Therefore, auxiliary
device may be required.
The GPIO pin assignment is #13 for output, #14 for input. The full function cable uses shield cable for
these pins. The signal is similar to the computer audio IO (AUX input, earphone output).
3.4.4 Temperature Sensor
A temperature sensor is built-in on the GPIO board to monitor internal thermal condition. It is part of
internal I2C control (90 XX) and the value can be accessed by reading the register address in the
Camera control port (0). Type “52” (Read) then address “90 00” for the I2C temperature sensor. You
will get the data in hexadecimal. The raw data have to be converted to actual °C (binary formatted in
2’s complement). The resolution of data output is 9 bit (0.5°C resolution) with one sign bit. The data
are in hexadecimal and have to be converted to binary in the 9-bit resolution from MSB in 16-bit.
bit 15 bit 14 bit 13 bit 12 bit 11 bit 10 bit 9 bit 8 bit 7 bit 6-0
Sign bit 26 °C/bit 25 °C/bit 24 °C/bit 23 °C/bit 22 °C/bit 21 °C/bit 20 °C/bit 2-1 °C/bit all 0
For example: Hexadecimal Binary Decimal Ta (°C) = 1/2 x (Decimal)
0FA 0111 1101 0 250 +125
032 0001 1001 0 50 +25
001 0000 0000 1 1 0.5
000 0000 0000 0 0 0
001* 1111 1111 1 -1 -0.5
370* 1100 1001 0 -110 -55
(Negative temperature conversion is done by complimenting each binary bit and adding 1 and
Sign bit is 1). * These data indicate negative values due to the sign bit of Binary data.
Example: Type “52 a0 00” <Return>. You will see the data of 52 a0 00 00 00 00 50 0D. On the data,
50 Hex is 80 in Decimal. So the temperature is 40 °C (0D is “Acknowledge”)
(Note: Refer the related document of MCP9800 for more details.)
GEViCAM Inc
GPIO Board
Fig. 23
W1 GND W2 Video
W3 Cont+ W4 Cont-
W5 Drive- W6 Drive+
(5V) Table 2

19
19
4. Operations (Frame Grabber Section …. GigE Interface)
4.1 General Description of GigE Interface
Ethernet is the most popular and widely used for the digital communication method today, of which
technology is proven and robust. Giga-bit Ethernet is an extension of fast Ethernet but has 1 Giga-bit
band width, which has the best advantage for image processing and sending high resolution, high
speed digital video to a host. It eliminates a need of frame grabber in machine vision thus cost per-
formance improves against the conventional [Analog Camera + Frame Grabber] or [Digital Camera
(Camera Link) + Frame Grabber] combination. There are numbers of benefits to go to GigE cameras
in many applications
Pleora Engine: GEViCAM uses Pleora Technologies’ engine, core and SDK.
4.2 Related Documents
When you open up the SDK installation, you will find a document file in Pleora Technologies’ iPort or
e-Bus software files (located in program file). It contains Quick start instruction, C++ SDK reference
guide, iPort user’s manual, Driver manual and other important information. See appendix for the detail.
4.3 Functions and Features
There are numbers of benefits to go to GigE cameras in many applications.
• Pleora engine: GEViCAM uses industry-leading Pleora Technologies’ engine, core and SDK.
Many organizations worldwide support the SDK as well as Pleora’s support group.
• High Performance Driver to off-load CPU task
The most critical parameter to choose the system is if you have enough CPU power for your
image processing, other communications, display, etc. The typical CPU usage of high perform-
ance driver in streamed video transmission is less than 2% (mostly below 1%).
• Deterministic continuous data transfer at 1Gb/s for 100m or more with switches.
The cable length is major advantage of Ethernet. This feature allows the new concept of factory
process control with computers away from each machines.
• Versatile SDK to support wide range of applications
Window OS, Linux, Various NIC card (and PHY), popular application drivers, OEM re-branding,
Training class at Pleora, continuous improvement, etc. are some of the features.
Frame Grabber Functions:
GigE camera-interface acts as a frame grabber function and the brief specification is as follows;
• On board Memory: 16 MB (64MB as custom option)
• Programmable Logic Control:
4 Pulse generator and Timers, 1 Rescaler, 1 Delayer, 1 Counter, Input debouncing,
Timestamp generator, Timestamp trigger, Software controlled I/O, GPIO FIFO
• Serial Ports:
Internal UART 3 ports
(Serial Port 0=Normally used for Camera Control; Port 1= RS-485; and Bulk Port 0= Audio I/O)
• Ethernet Band-width: 1Gb/s
• Unicast and Multicast: Yes
• Static Configuration: Yes, 4.01
• BOOTP: Yes
• DHCP: Yes, 4.06
• Data Format: Gray scale (8, 10, 12, 16-bit) and Color RGB Bayer (8-bit)
• Image Size (capability): Up to 4K (H, multiple of 4) x 4K (V)
• Image capture Continuous, Single, Save images (continuous, fixed number) in various
formats)
• Other Functions:
Windowing, Decimation, Data port mapping, Pixel shifting, Pixel inversion
GEViCAM Inc

20
20
4.4 Camera Configuration and Control
4.4.1 Camera Interface (Select Camera)
A GigE camera interfaces the camera block and the frame grab-
ber block. The basic structure of GigE interface is designed to
keep camera block as a Camera Link signaling (not real Camera
Link but signal and data format follow Camera Link definition).
Therefore, the Coyote application software calls for “Standard
Camera Link” as the GEViCAM connection. (Fig. 24)
In order to operate the frame grabber functions, the camera and
PC must be connected, the proper driver and Coyote Application
soft-ware need to be installed.
Please refer section 2 and 3 for the software and driver installa-
tion, camera setup and application software device detection.
Now you are ready to use the application software and control
various camera functions. The GD-series platform
can perform vast tasks beyond normal camera
functions. Let’s go through the Coyote application
software. After all connections are done, you will
see “Coyote” window. Open “Acquisition” and
“start”. An Image display pops up and the acquisi-
tion rate is displayed. (Fig. 25)
Next, click “Configure” button and mark “show
advanced configuration page” at the bottom left.
4.4.2 Pixel Format and Image Size Selection
Open up “Pixel” tab and select proper data either
“Grayscale” or “RGB color”.
The pixel depth is selectable.
Factory Default: 8-bit. (Fig. 26)
Then go to “Image”
tab and input the
correct pixel num-
bers. It cannot go
more than the cam-
era output pixels
(Active pixel num-
bers. See specifica-
tion). If higher num-
ber than active pixel
is selected, display
may freeze. (Fig.27)
.
GEViCAM Inc
Fig. 25
Fig. 24
Fig. 26 Fig. 27
Table of contents
Popular Digital Camera manuals by other brands
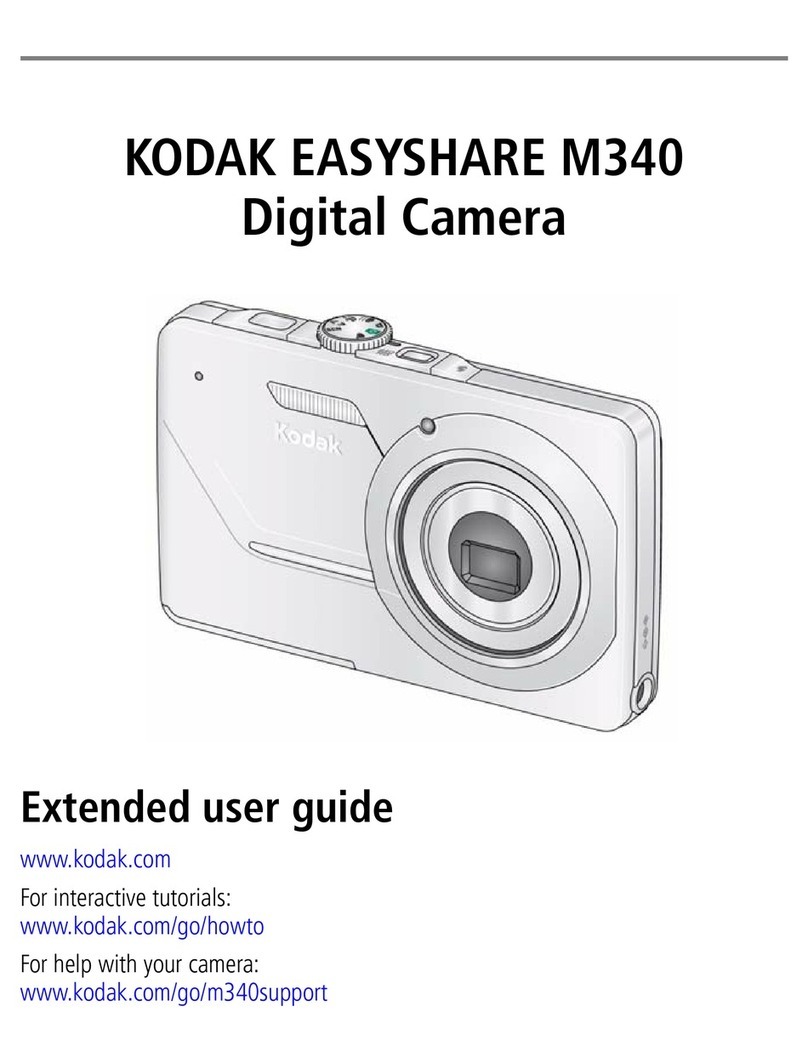
Kodak
Kodak M340 - GUIA COMPLETO DO USUARIO Extended user guide
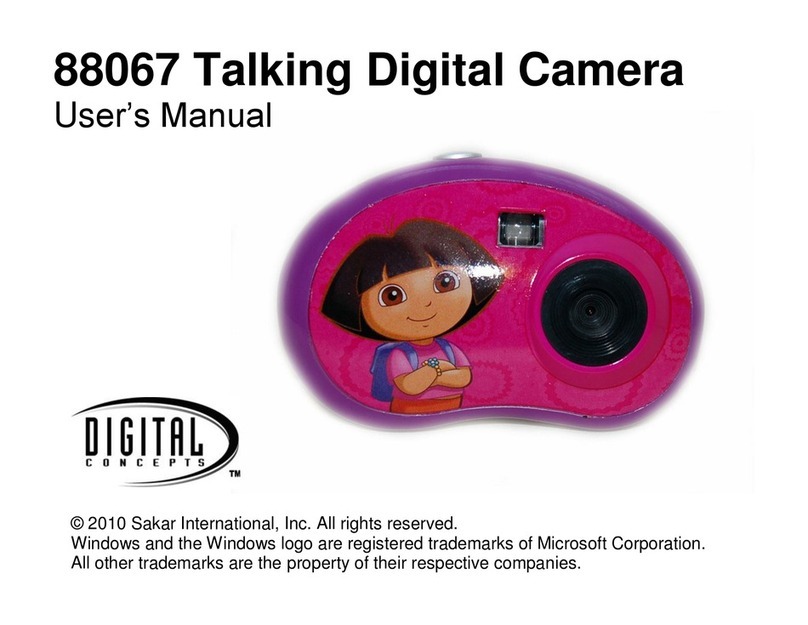
Digital Concepts
Digital Concepts 88067 user manual

Nikon
Nikon Nuvis 300 instruction manual
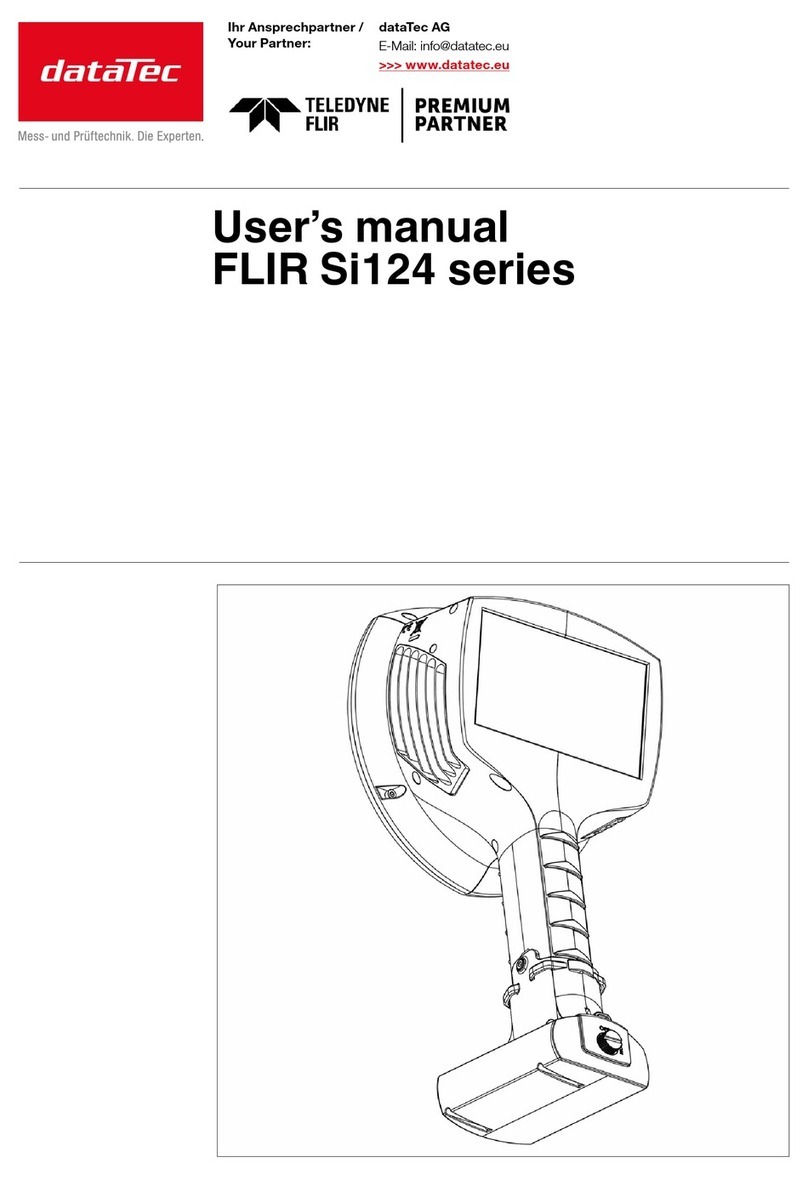
Teledyne
Teledyne FLIR Si124 Series user manual
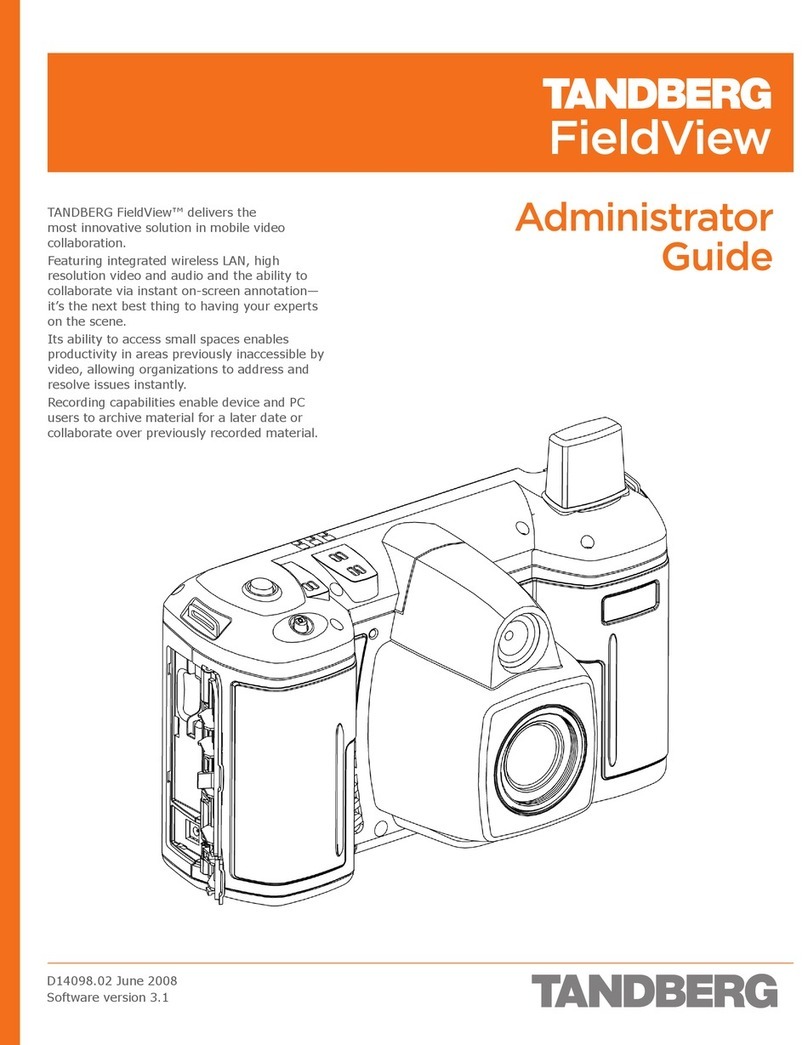
TANDBERG
TANDBERG FieldView Administrator's guide
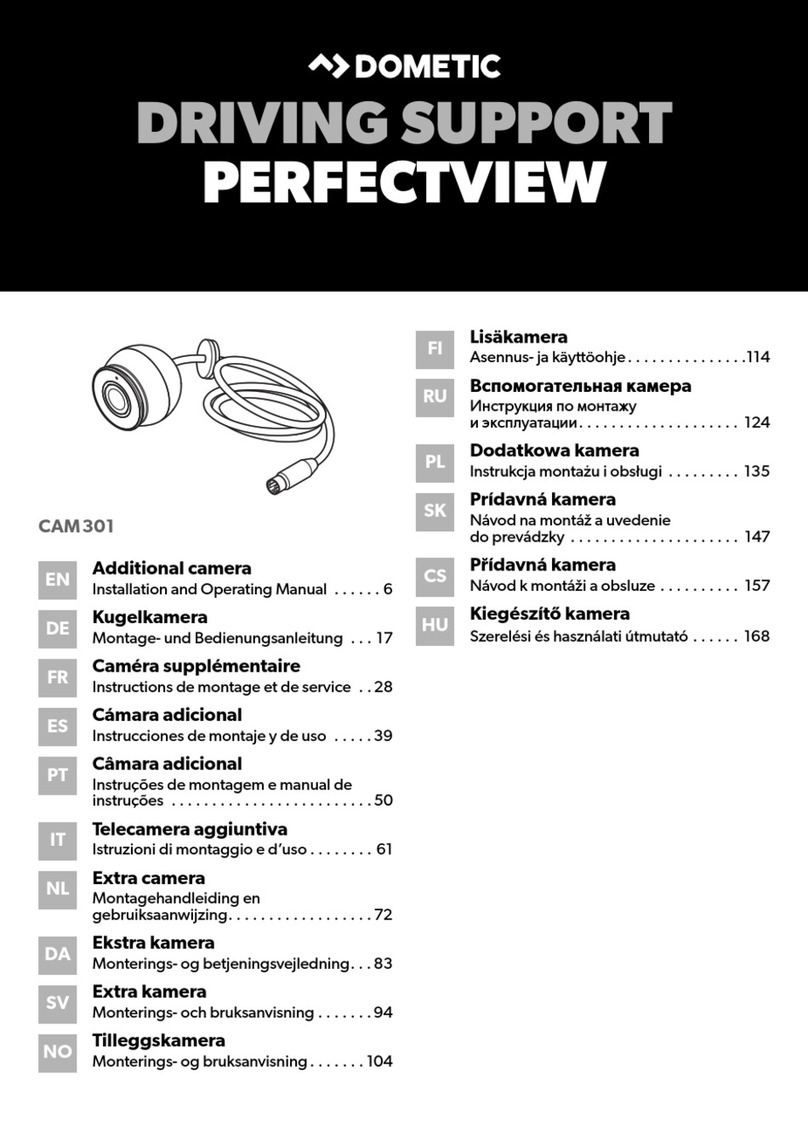
Dometic
Dometic PerfectView CAM301 Installation and operating manual