GFB EX38 User manual

GFB EX38
External wastegate
instruction manual
Part no. 7003
Ph: +61 (0)2 9534 0099
Fax: +61 (0)2 9534 3999
Email: [email protected]
Web: www.gfb.com.au

INSTAlLation
GFB EX38 Packing list:
Assembled EX38 wastegate
10psi spring (installed)
2 x v-band clamps
2 x 1/8” BSPT hose tails
1 x outlet weld-on flange (part # 7043)
1 x inlet weld-on flange (part # 7053)
1 x valve seat
Exhaust in Smooth flow to
wastegate inlet
Smooth entry of
wastegate gases
Exhaust out
Wastegate exhaust
Install the hose tails onto the wastegate. The thread is 1/8” BSP, which is a commonly available thread should you
wish to use a different type of fitting.
Identify the inlet and outlet weld-on fittings. These are to be welded onto your turbo exhaust manifold and exhaust
system, onto which the EX38 is mounted using the supplied v-band clamps.
Please note the EX38 is compatible with TiAl MVS weld-on fittings, so if you already have an exhaust manifold with
a TiAl fitting, the EX38 will bolt straight up using the GFB-supplied clamps.
The inlet fitting, which is welded to the exhaust manifold and supports the weight of the wastegate, is best suited to
1.75” (44.4mm) O.D. pipe with a wall thickness of at least 0.095” (2.4mm). The outlet fitting is designed to accept
1.5” (38.1mm) O.D. thin-walled tube, which is commonly used for exhaust systems and screamer pipes. Of course,
it is possible to use different size and wall-thickness pipes than those recommended, provided a suitable weld can
be achieved. Replacement weld-on fittings are available separately from GFB if required.
The inlet fitting should be welded to the exhaust manifold after all the exhaust runners have merged, and in a
position that promotes smooth flow to the wastegate – fast-moving exhaust gas is reluctant to make sharp turns,
which significantly reduces the flow potential through the wastegate. The diagram below shows a suggested
installation location.
On any street-driven car, legally the wastegate outlet MUST be connected to the vehicle's exhaust system (before
any catalytic converters and mufflers), and should be done in a way that allows the gases to merge smoothly. On
race cars where regulations allow, the outlet can be routed out of the engine bay to atmosphere.
Ensure the valve seat is inserted into the bottom of the wastegate before final installation.

Base Boost
Pressure (psi)
5psi Inner
(part #7205)
7psi Middle
(part #7207)
10psi Outer
(part #7210)
5
7
10
12
15
17
22
Changing the Spring
Use a metric 3mm hex key to remove four of the cap screws, leaving two opposing screws in place. Care must be
taken during the next step, as the spring force can exceed 40kg, depending on the springs used.
Carefully remove the remaining two screws whilst restraining the cap to prevent it popping off. It is a good idea to
have a helper during this step, or better still, use a press or suitably padded vise to restrain the cap and allow you to
remove it slowly.
Change the spring/s as required, and ensure they sit into the corresponding grooves in the cap. Ensure the bead of
the diaphragm is sitting into the groove, then press the cap down and fully screw in two opposing cap screws,
followed by the remaining four. Ensure the screws are nipped up tight and it is preferable to use a drop of Loctite on
the threads.
The EX38 comes fitted with a 10psi spring, and
also available separately are 5psi and 7psi
springs, which can be used individually or installed
together to achieve different boost levels. Use the
table opposite to determine the combination of
springs required for your desired base boost level.
Note that this table is only a guide to help your
selection – the actual boost level achieved
ultimately depends on a large number of variables,
and may differ from the base boost pressure
shown in the table.
spring selection
Use the following guide to help set up your EX38. You should first determine the minimum and maximum boost
pressure that you want to run, and your control method.
Care should be taken when selecting boost pressures, and it is always best initially to err on the conservative side,
until the engine can be run on a dynamometer to ensure safety. Always consult an expert when making boost
changes, and it is recommended that the car be checked on a dyno, as high boost and/or lean air/fuel mixtures can
cause engine damage or worse, total failure.
If you are planning on having variable boost through the use of a boost controller, the range you can achieve
depends on your turbo setup. The lowest boost your car can run is determined by the spring (this is commonly
known as “gate pressure”), and boost can then be increased through the use of a boost controller.
As a rule of thumb, try to select springs so that your maximum boost is no more than double the “gate pressure”.
Whilst it is possible to increase boost beyond this, you may find that boost becomes less stable and harder to control.
This is because the boost controller must bleed most of the control pressure signal to the actuator, so the wastegate
is less able to self-correct for changes in manifold pressure. Using a stronger spring means the controller bleeds off
less of the pressure signal, giving the wastegate greater ability to regulate boost changes.
boost control methods
There are many different ways to connect the wastegate boost ports; three of the more common methods are
shown on the next page. Whilst it is possible to use any number of different methods that are not shown here, you
should always remember the following:
The lowest boost pressure possible is determined by the spring
The lowest possible boost pressure for a given spring combination is achieved when the
full boost pressure is applied to the lower actuator port, and none to the upper port
Boost pressure increases when you do one or both of the following:
Decrease the pressure at the lower port
Increase the pressure at the upper port

boost control methods
This is the most basic boost control method,
using a pressure hose from a boost source (often
found on the turbo outlet) connected to the lower
actuator port of the wastegate cap.
This configuration results in a boost pressure that
is dictated by the wastegate spring – you must
change the spring to alter the boost level.
The unused upper actuator port should be left
open to atmosphere, but if there is a chance that
water could drip into the upper port, either remove
and rotate the cap, or connect a short length of
hose to the nipple and point it downwards.
The second configuration is a simple adaptation
of the above, with a boost controller (such as the
GFB Atomic) fitted into the pressure hose as
shown to allow the boost to be easily increased
above the base level. The controller does this by
reducing the pressure getting to the wastegate -
the more the controller bleeds off, the higher the
boost.
In the case of the GFB Atomic boost controller, the
arrow on the body must point in the direction
shown, or the controller will have little effect.
If using a different brand controller, you should
consult the instructions for that product.
The third configuration is a typical installation for
electronic boost controllers (such as the GFB G-
Force II).
You should consult your boost controller's
instruction manual for specific information on how
each of the ports of the solenoid valve should be
connected.
This product is intended for racing use only, and it is the owner's responsibility to be aware of the legalities of
fitting this product in his or her state/territory regarding noise, emissions and vehicle modifications.
GFB products are engineered for best performance, however incorrect use or modification of factory systems
may cause damage to or reduce the longevity of the engine/drive-train components.
GFB recommends that only qualified motor engineers fit this product. Warranty is for the period of one year
from the date of purchase and is limited only to the repair or replacement of GFB products provided they are used
as intended and in accordance with all appropriate warnings and limitations. No other warranty is expressed or
implied.
Atomic boost controller
Arrow on controller
body points this way
Solenoid valve T-piece
Boost source
Lower actuator port
Table of contents
Popular Automobile Part manuals by other brands
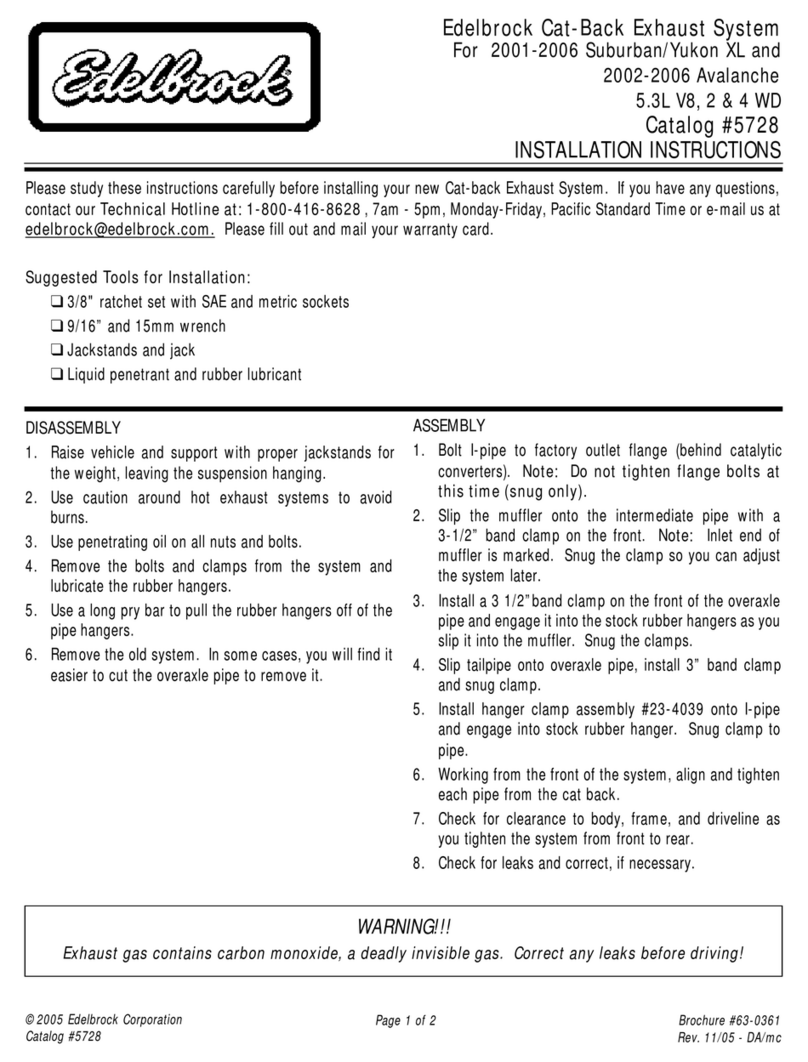
Edelbrock
Edelbrock 5728 installation instructions
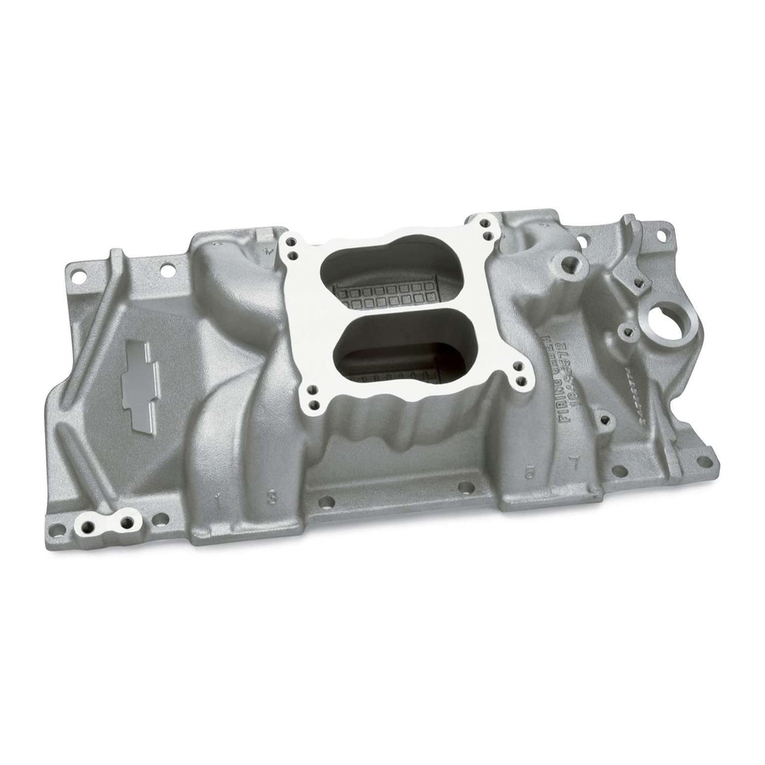
Edelbrock
Edelbrock 24502574 LT4 installation instructions
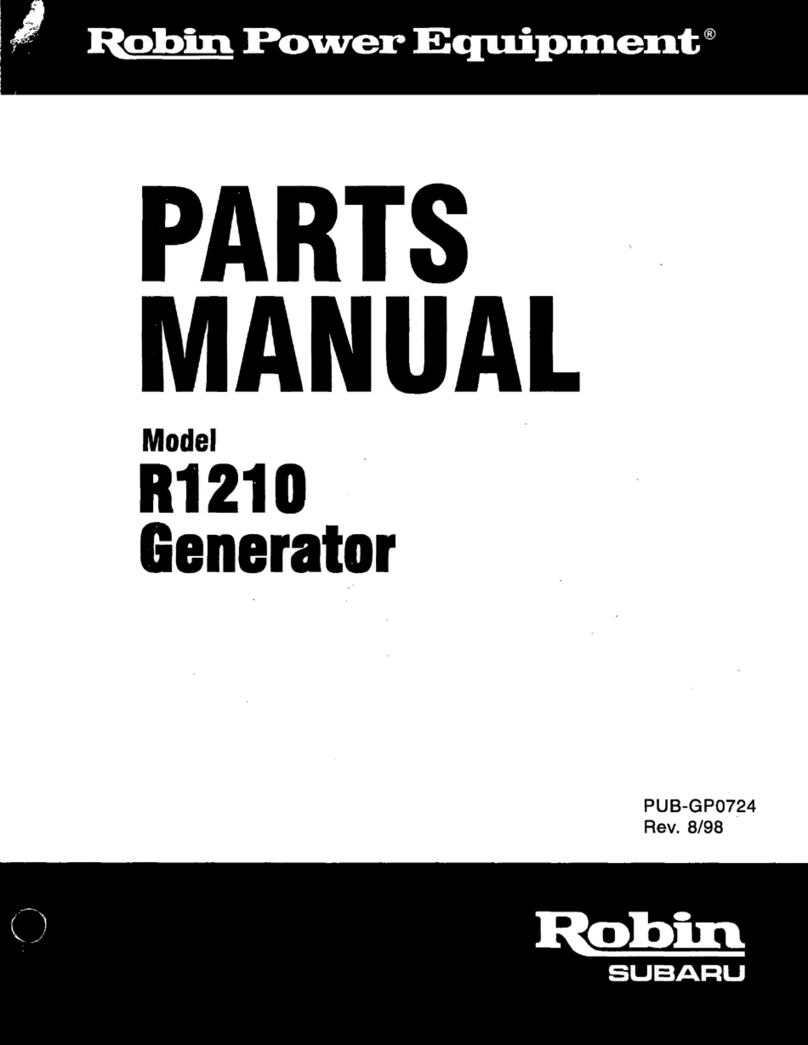
Robin America
Robin America R1210 parts manual
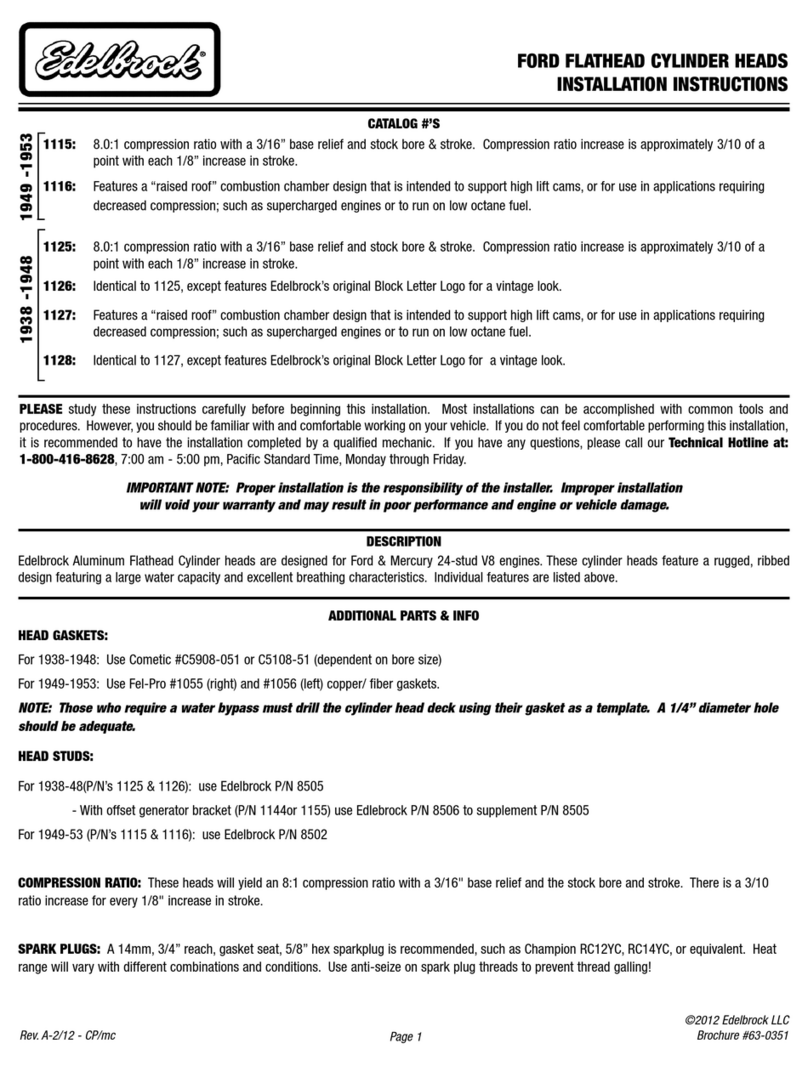
Edelbrock
Edelbrock 1115 installation instructions
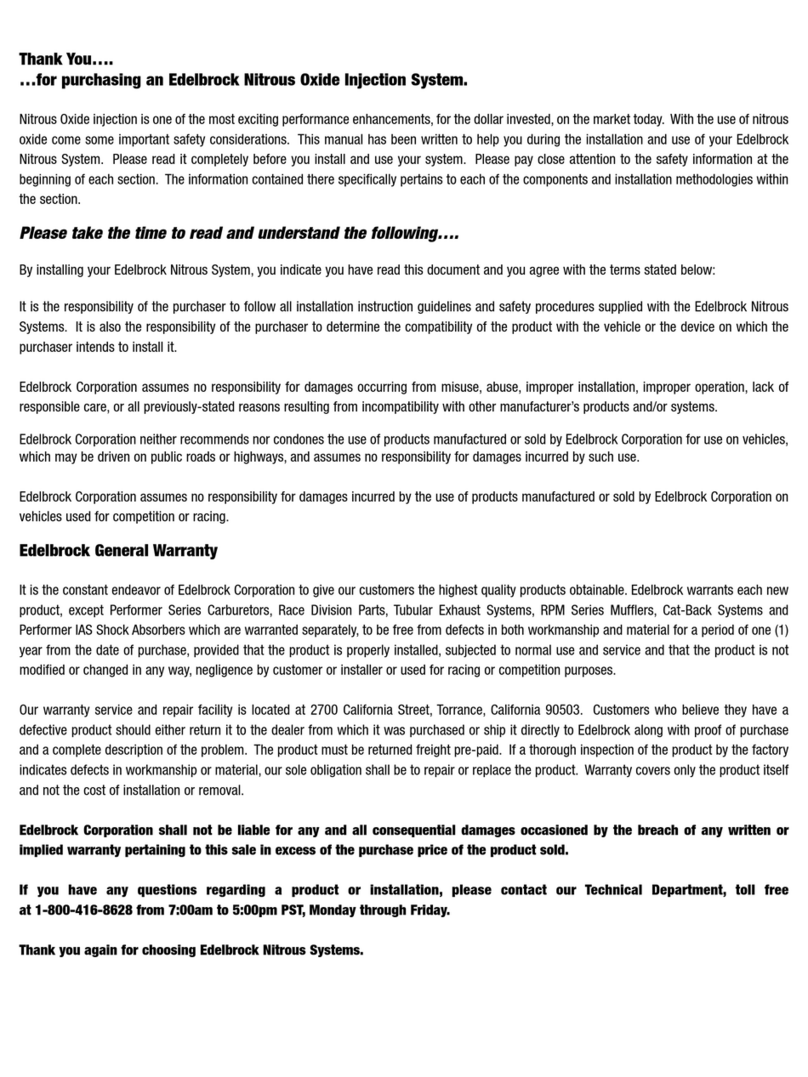
Edelbrock
Edelbrock 71001 installation manual
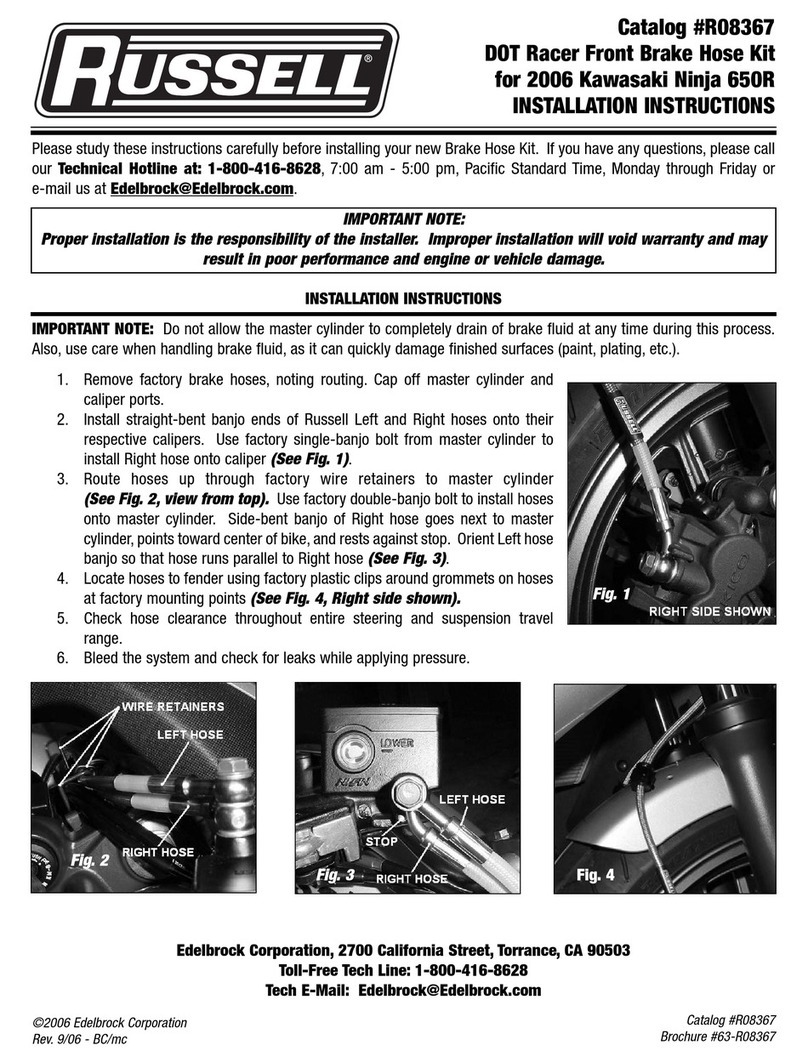
Edelbrock
Edelbrock Russell R08367 installation instructions

AUTOTECH
AUTOTECH 10.425.1125GK-1125K installation instructions
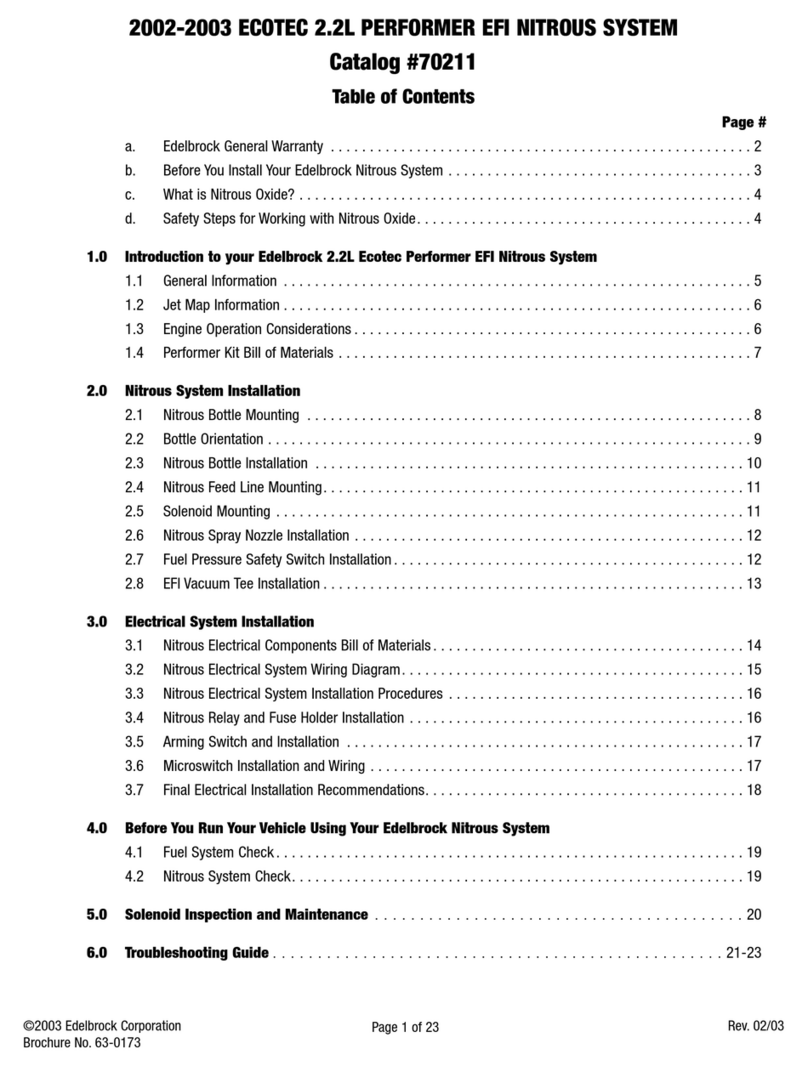
Edelbrock
Edelbrock 70211 installation manual

Toyota
Toyota All Toyota Models Replacement guide
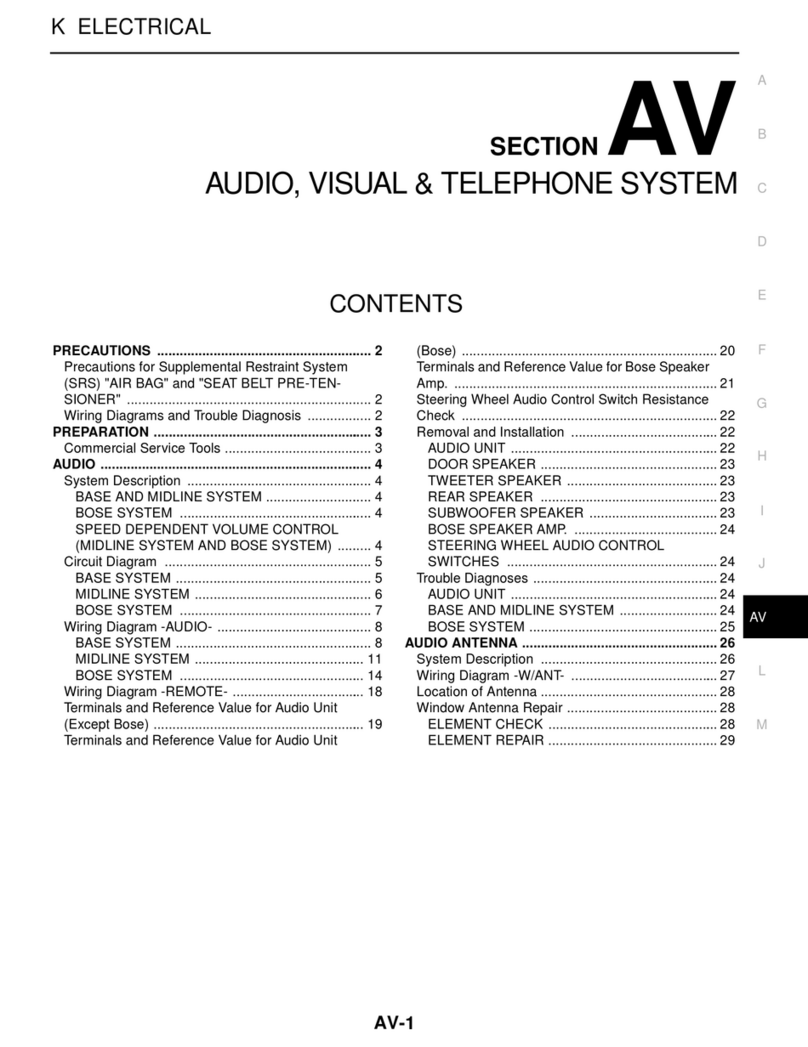
K Electrical
K Electrical AIR BAG Service manual
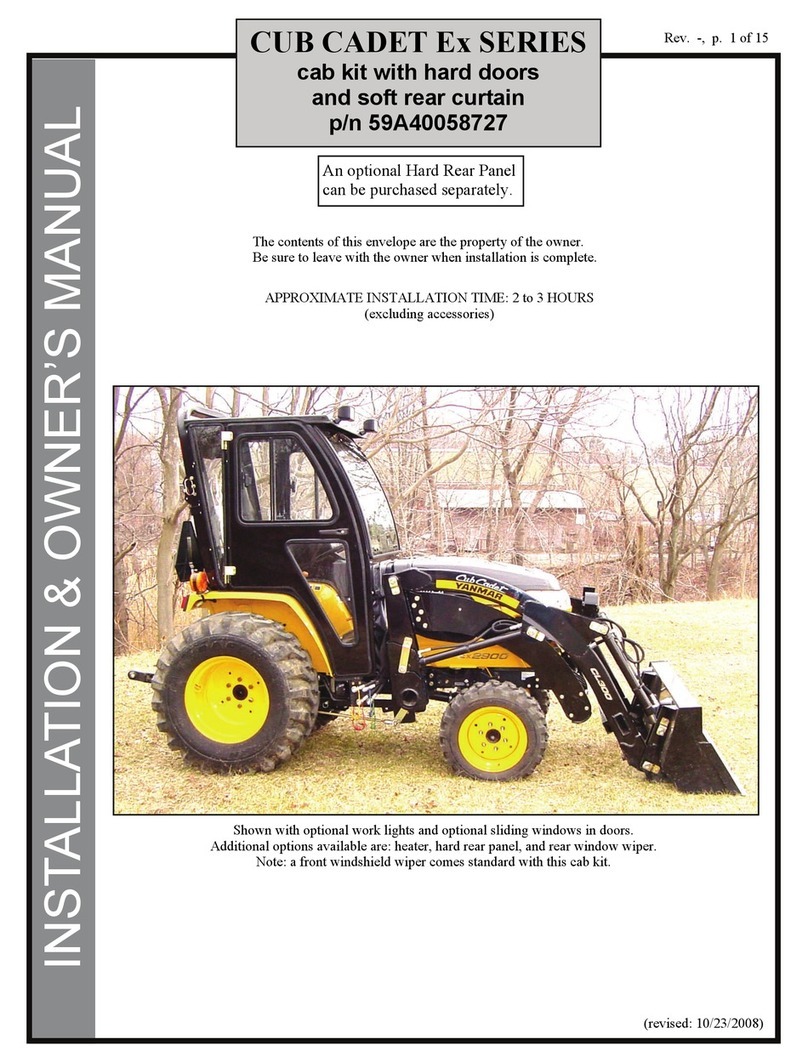
Cub Cadet
Cub Cadet Ex SERIES Installation & owner's manual
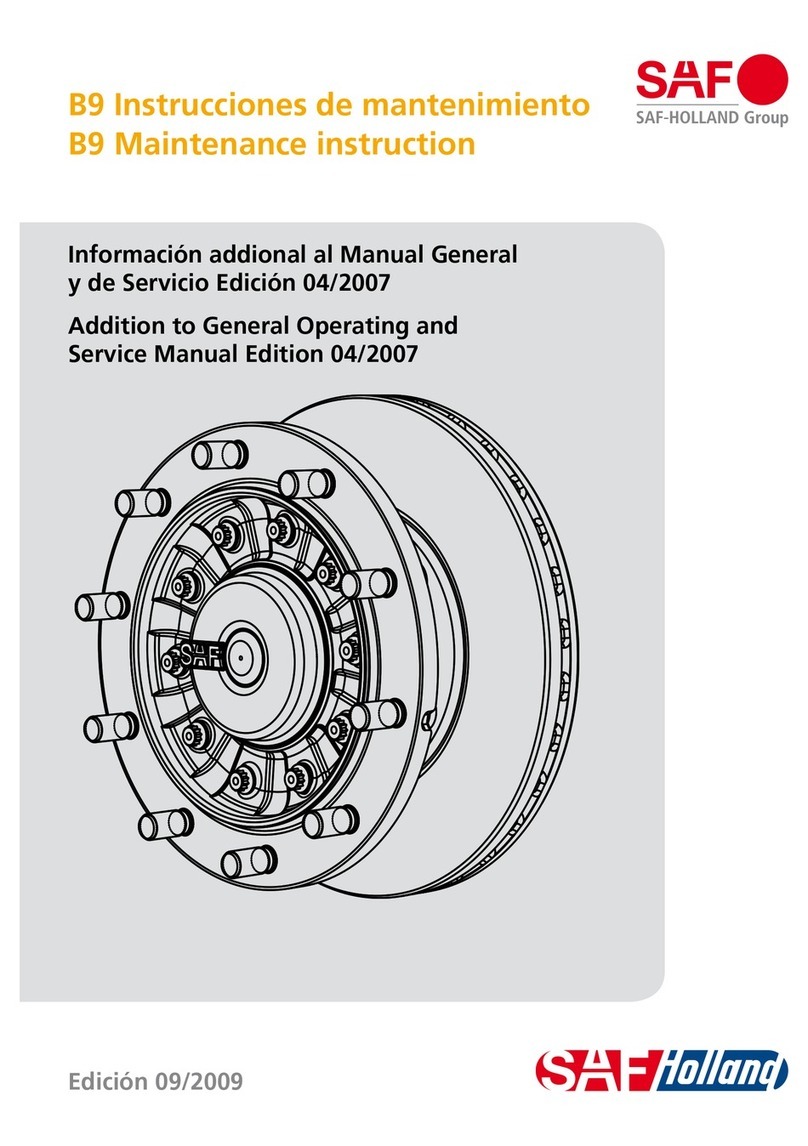
SAF-HOLLAND
SAF-HOLLAND B9 Maintenance Instruction