Giersch GG20-LN Manual

Technical Information • Installation Instructions
Gas
May 2012 edition
In the interests of continuous product
improvement, technical specifications
are subject to change without prior notice!
GG20-LN
GB

2
E.04.99 • G. 09.05.12
Contents
Overview..............................................................................................................3
1. General information/safety instructions.......................................................................................... 3
2. Scope of supply and electrical ratings ........................................................................................... 3
3. Operating instructions .................................................................................................................... 3
4. Instruction ...................................................................................................................................... 3
5. Maintenance and customer service ............................................................................................... 3
6. Key for code designation ............................................................................................................... 4
7. Technical specifications ................................................................................................................. 4
Installation............................................................................................................5
8. Installing flange and burner............................................................................................................ 5
9. Checking the electrode setting........................................................................................................ 5
10. Installing the gas train .................................................................................................................... 5
11. Service position.............................................................................................................................. 6
12. Connecting to power supply.......................................................................................................... 7
Function ...............................................................................................................8
13. Control unit DMG 972 .................................................................................................................... 8
Start-up..............................................................................................................10
14. Air flap actuator STA 13 B0 .......................................................................................................... 10
15. Adjusting the mixing head............................................................................................................ 11
16. Adjusting the ignition electrode .................................................................................................... 11
17. Adjusting the inlet nozzle .............................................................................................................. 11
18. Gas burner with gas train............................................................................................................. 12
19. Adjustment tables ........................................................................................................................ 14
20. Modulating or 2-stage sliding gas burner with gas train................................................................ 17
21. Calculation principle for gas burner adjustment........................................................................... 19
Service instructions/dimensions ........................................................................21
22. Flame control using ionization electrode...................................................................................... 21
23. Measuring the ionization flow....................................................................................................... 21
24. Servicing the air pressure monitor ............................................................................................... 21
25. Circuit diagram GG20-LN ........................................................................................................... 22
26. Possible errors ............................................................................................................................ 25
27. Exploded drawings....................................................................................................................... 26
28. Spare parts list .............................................................................................................................. 27
29. Declaration of conformity for the forced-air gas burner................................................................. 28
30. Burner dimensions / boiler connecting dimensions...................................................................... 30
31. Working ranges............................................................................................................................ 30

3
E.04.99 • G. 09.05.12
1. General information
Installation of a gas-fired heating system must be performed in accordance with the applicable regulations
and guidelines. It is therefore the duty of the installer to be familiar with all applicable regulations and re-
quirements. Installation, start-up and maintenance must be performed with utmost care.
The burner must not be operated in rooms with high levels of air humidity (laundry rooms), dust or corrosive
vapours. The boiler room must be ventilated accordingly with ventilation air. The Giersch GG20-LN gas in
accordance with DIN EN 437 and comply with the European Standard DIN EN 676:2008-11.
2. Scope of delivery and connection data
Before installing the Giersch gas burner, please check that all items included in the scope of delivery are
present.
Scope of delivery:
Burner, sliding flange and gasket, 4 retaining screws, separate operating instructions,
technical information, one 7-pin connector. Gas train and gasket.
Gas installation and commissioning are subject to the applicable national regulations, e.g. in Germany the
Technical Regulations of the DVGW (DVGW-TRGI).
The following must be observed for Switzerland: SVGW Gas Provisions G1, G3: Gas installation EKAS
Form.
1942: Liquefied gas regulation, Part 2 Regulations of cantonal authorities (e. g. fire department regula-
tions).
The gas pipe must be designed to conform to the flow rate and the available gas flow pressure and routed
with the lowest pressure loss over the shortest distance to the burner.
The loss of gas pressure via the gas ramp and the burner and the resistance on the fuel gas side of the
heat generator must be less than the connection flow pressure.
Caution !
Observe the through-flow direction of the gas train.
3. Operating instructions
The operating instructions together with this technical information leaflet must be displayed in a clearly vis-
ible position in the boiler room. It is essential to enter the address of the nearest customer service centre
in the operating instructions.
4. Instruction of operating personnel
Faults are often caused by operator error. The operating personnel must be properly instructed in how the
burner works. In the event of recurring faults, Customer Service should be notified.
5. Maintenance and customer service
The complete system should be checked once a year for correct functioning and leaks by a representative
of the manufacturer or other suitably qualified person.
We accept no liability for consequential damage in cases of incorrect installation or repair, the fitting of non-
genuine parts or where the equipment has been used for purposes for which it was not intended.
Overview

4
E.04.99 • G. 09.05.12
6. Key for code designation
7. Technical specifications
Burner type
Technical data GG20/1-Z-(M)-L-LN GG20/2-Z-(M)-L-LN
Product ID No. CE-0085
Burner output in kW 55 - 170 65 - 235
Gas type Natural gas LL + E = "-N", liquefied gas 3B/P = "-F"
Gas input pressure with MB VEF 407 ¾“ 20
Gas input pressure with MBC 300 VEF 1
“
20
Gas input pressure with MB VEF 412 1“ 20
Mode of operation 2-stage/modulating
Voltage 1 / N PE ~ 50 Hz 220 - 240 V
Current consumption
start max. / operation 1.9 / 1.3 A 3.9 / 2.6 A
Electric motor power (at 2800rpm) in kW 0.18 0.37
Flame control Ionisation
Control box DMG 972
Weight in kg 15.0
18.7
Noise emission in db(A) 72
72
GG20/1-Z-(-M)-L-N(-F)-LN
LowNox
Erdgas LL+E ="-N" oder Flüssiggas ="-F"
Luftabschlussklappe
Zweistufig oder Modulierend
Baugröße
Baureihe
LowNox
Natural gas LL + E = "-N", liquefied gas 3B/P = "-F"
Air damper
2-stage/modulating
Burner type
Burner series
Overview

5
E.04.99 • G. 09.05.12
8. Install flange and burner
Important: Secure the sliding flange so that the
clamping screw 3 is positioned at the top!
When installing the sliding flange, only tighten screws
1 and 2 otherwise it will not be possible to secure the
burner tube with screw 3. Slide in the burner, adjust to
furnace depth and tighten the screws in the following
sequence: 3, 4, 5, raising the housing in the process.
9. Checking electrode setting
• Move the burner into the service position as
described on Page 6.
• Check the setting of the ignition and ionisation elec-
trodes (see Page 11).
10. Installing the gas train
• Remove plastic protective plug.
• Mount the connections and apply the seals
included.
• Observe the installation position.
• Check connecting point of gas ramp with non-corro-
sive foaming agent for leaks and vent the gas pipe.
• When venting, use a hose to discharge the gas
safely to the atmosphere.
For proportional pressure control
GG 20/25(-Z)-M-L-LN with KEV:
Fit the furnace pressure meter tube to the boiler door
with the gradient towards the boiler (if required).
Lay the pressure impulse to the KEV to the corre-
sponding connections p
L
and p
F
.
Use the blue PU hoses supplied.
• Lay the pressure impulse so that no condensate
can flow into the gas ramp.
• Connect hose to furnace pressure meter tube with
connection p
F
(if required).
• Connect hose to connection p
L
with measuring nip-
ple for
air pressure on burner base plate.
If this connection is not made, the magnetic valves
will not open.
Installing the gas train
Installation position for vertical line as desired
Installation position for horizontal line tilted up to max. 90° to left or right, not overhead
Minimum distance to masonry 20 mm
Installation position MBC...
Installation position CG...
Installation position MB...
Installation

6
E.04.99 • G. 09.05.12
11. Service position
Risk of injury by fan impeller on activation in service
position.
• Release quick-release locks (5 x) and detach base
plate,
• Place the keyhole openings in the base plate onto
the socket head cap screws of the housing and lock
them into place.
Installation

7
E.04.99 • G. 09.05.12
12. Connect to power supply
• De-energise the system. Move the master switch into the "OFF" position.
• Check the polarity of all connecting plugs.
• Wire the plug as shown in the terminal diagram. Lay the flexible control line so that the boiler door
remains swivellable.
• Attach cube connector connected to the gas pressure monitor connector A (grey) and to solenoid
valves B1 (black), and secure with screw.
• Connect the 4-pin plug of the power controller (X31) to the black-green socket on the burner (X32).
• If plugs X11 and X31 are wired as shown the terminal diagram, check that the pins are correctly
assigned.
• Connect the 7-pin plug of the boiler controller (X11) to the black-brown socket on the burner (X12).
• The power cord of the 7-pin connecting plug X11 must be fused with a slow-acting fuse rated for min.
6.3 A or a quick-acting fuse rated for max. 10 A.
Connection diagram:
T8
T7
T6
B5
Buchsenteil X32, X12
am Brenner
Steckerteil X31,X11
zum Kessel
X31 X32
zu
auf
Anschluss für GG20-M-L-LN
Y9
T8
T7
T6
B5
Buchsenteil X32, X12
am Brenner
Steckerteil X31,X11
zum Kessel
X32
N
F22
P12
X31
Anschluss für GG 20-Z-L-LN
H12
B4
S3
T2
T1
N
PE
L1
N
PE
L1
N
N
F1 F3
F21
H11
P11
H13
Q1 X11 X12
Buchsenteil X32,X12
am Brenner
Steckerteil X31,X11
zum Kessel
male adapter X31, X11
to boiler
female adapter X32, X12
on burner
male adapter X31, X11
to boiler
female adapter X32, X12
on burner
male adapter X31, X11
to boiler
female adapter X32, X12
on burner
Connection for GG20-Z-L-LN
Connection for GG20-M-L-LN
Legend:
F1 External fuse
F21, F22 Ext. temp. controller, 1st/2nd stages
F3 Ext. safety thermal cutout
F51 Gas pressure monitor
Q1 Main heating switch
H11, H12 Ext. pilot lamp
H13 Ext. fault signal lamp
L1 Phase
PE Protective earth
P11, P12 Time meter
Y1, Y2 Solenoid valve
Y3 Safety solenoid valve
Y9 Ext. controller
N Neutral conductor
Installation

8
E.04.99 • G. 09.05.12
13.Control unit DMG 972
Function testing the control unit
Danger of fatal injury from electric shocks!
Disconnect electrical cable from power supply before car-
rying out any work on live parts!
Troubleshooting may only be carried out by authorised
and trained personnel!
Unlocking may only be carried out by an authorised spe-
cialist.
Check air pressure monitor contact: device goes into fault mode when silicone connecting hose is de-
tached. Reconnect the hose to coupling "+".
Bypass air pressure monitor before start-up: burner motor starts for approx. 2-3 seconds, followed by fault
shut-down. After 10 seconds, an intermittent fault is output and then automatically
reset. A second start-up attempt is made. If the air pressure switch contact is still closed, a true fault shut-
down will occur. If the air pressure switch opens the contact within 10 sec., the burner will go into operation.
Safety and switching functions
In the event of a flame failure during operation, the fuel supply is immediately switched off and the control
box goes into fault mode within 1 sec. Since the faults are not reset after a power failure, the burner motor
switches on for approx. 2-3 sec. when the supply voltage is connected before the device goes into fault
mode again and displays the last fault that occurred.
If a flame signal is given during the pre-ventilation phase, a failure shut-down will occur immediately.
The position of the air pressure controller is continuously checked. There can be no start-up if it is not in its
neutral position. If the NO contact does not close or reopens during the pre-ventilation phase, a failure shut-
down will occur. If there is an insufficient supply of air during operation, the air pressure controller contact
opens and the valves close immediately. The device switches to fault mode within 1 sec.
Fault cause diagnosis
In the event of a fault, the LED remains continuously lit. Every 10 seconds this is interrupted and a flash
code is signalled to provide information about the fault. This results in the following sequence, which re-
peats itself continually until the fault is acknowledged, i.e. the appliance is reset.
Following sequence:
Reader for failure code display:
SatroPen Art. No. 47-10-22542
SatroCom Art. No. 47-10-22563
Luminous phase Dark phase
lasting 10 secs. lasting 0.6 sec.
Dark phase
lasting 1.2 secs.
Flash code
Function

9
E.04.99 • G. 09.05.12
Fault message Flash code Cause of fault
Fault shut-down safety time No flame detection within the safety interval
Extraneous light fault External light during monitored phase, possible sensor
fault
Air controller in working posi-
tion
Air controller contact fused
Air controller time-out Air controller does not close within a defined time span
Air controller opens Air controller contact opens during start-up or operation
Flame failure Flame failure signal in operation
Honeywell: DMG 972 mod. 04
t
v1
= monitored pre-purge time for air pressure monitor 42 sec.
t
vz
= pre-ignition cycle 3 sec.
t
lk
= open air flap command during pre-purging 24 sec.
t
r
= air flap return 18 sec.
t
n
= post-ignition time 1.5 sec.
t
f
= flame simulation supervision 5 sec.
t
s
= safety period 2 sec.
t
v2
=
delay at terminal 6 / C 10 sec.
Function

10
E.04.99 • G. 09.05.12
14. Air flap positioning motor
The positioning drive STA 13 B0 is used to adjust the
air flap on burners with a 2-stage or modulating operat-
ing modes. Make the adjustment using the limit switch
cams on the positioning drive roller.
After each normal shut-down, the positioning drive
moves to fully closed (ST0).
For this purpose, remove the hood from the air flap po-
sitioning motor. Alter the cam positions via the adjust-
ing screws with a standard screwdriver.
The switching cams can be readjusted when calibrat-
ing the burner.
The cam positions for adjusting the burner to the re-
quired min/max output are given in the adjustment ta-
ble.
see adjustment tables on pages 14 - 15.
For this:
Remove the hood from the positioning drive. Alter the cam positions via the adjusting screws with a stand-
ard screwdriver.
The switching cams can be readjusted when calibrating the burner.
Higher number = increase air
Lower number = reduce air
Adjustments to ST1 and ST2 do not become effective until a brief switchover between 1st/2nd stage (or
triggering of Up/Down on output controller) has taken place.
Do not adjust cam ST1/min. to a value that is greater than ST2/max.
After readjusting the burner, refasten the positioning
motor hood and set the switch on the lower part of the
control unit to the position 2nd stage.
ST1
ST0
ST2
Start-up

11
E.04.99 • G. 09.05.12
15.Adjustment of the mixing head
Set the position of the mixing head according to burner
output in accordance with the table on page 14 ff.
16. Adjusting the ignition/ionisation electrode
The electrodes are preset at the factory. The dimensions are specified for checking purposes.
17. Adjusting the inlet nozzle
The position of the inlet nozzle is preset at the factory,
but can be adapted to different system operating condi-
tions, altitude above sea level and outputs.
To adjust, undo the screws (as shown). Set the new
position you have chosen using the scale and the mark
(refer to adjustment table for scale values).
Reattach the inlet nozzle in the new position.
Inlet nozzle position:
- = low blower output (40°)
+ = maximum blower output (16°)
Ignition electrode
Ionisation electrode
11.5 ± 0.5
4-1
11 ± 0.5
12 ± 0.5
5 +2
Ignition electrode
Ionisation electrode
Start-up

12
E.04.99 • G. 09.05.12
18. Gas burner with gas train ....
Version MB:
Exact pneumatic mixture control for optimum energy
utilisation and combustion.
Technical data of gas train MB...
Gas types: Gas type families 1, 2 and 3, acc. to DIN EN 437/EN 2003-09
Inlet pressure: p
E
:
15 to < 360 mbar
Permissible outlet pressure:pG
≥
0..4 to < 100 mbar
Ambient temperature: -15°C to +70°C
Connecting flanges: The connecting flanges are secured with 4 screws. The flanges can be turned
through 90° or 180° in each case. Pressure measuring points in
inlet and in outlet.
Filter: Plastic gauze
Gas pressure monitor
The gas pressure monitor (p
w
) serves to monitor the
gas inlet pressure. The burner is shut down if the gas
inlet pressure drops below the set minimum value
(preset at factory to 12 mbar). The burner starts up au-
tomatically again when the minimum pressure is ex-
ceeded.
Perform the following checks in the course of commissioning or servicing:
Slowly close the ball valve during operation. The gas pressure monitor must switch off the burner
before the max. CO concentration of 10,000 ppm is reached. If the burner does not switch off,
slowly increase the switching point of the gas pressure monitor until it does.
If the burner restarts immediately after shut-down with the ball valves fully open and shuts down
again when the solenoid valves open, the required connection flow pressure is too low. A further
reason for this behaviour could be excessive soiling of the gas filter.
p
W
Start-up

13
E.04.99 • G. 09.05.12
Technical data of gas train CG...
Gas types: :Gas type families 1, 2 and 3, acc. to DIN EN 437/EN 2003-09
Inlet pressure: max. 100 mbar
Permissible outlet pressure:pG
≥
0.4 to < 50 mbar
Max. pressure drop: 50 mbar (P
E
- P
G
)
Ambient temperature: -10°C to +60°C
Connecting flanges: The connecting flanges are secured with 4 screws. The flanges can be turned
through 90° or 180° in each case. Pressure measuring points inlet
and in outlet.
Filter: Plastic gauze
Start-up

14
E.04.99 • G. 09.05.12
19. Adjustment tables
The values specified in the tables are only reference inputs for commissioning. The system set-
tings required in each case must be redefined if values such as boiler output, calorific value and
altitude deviate.
A correction is required in any case.
The maximal burner output can only be achieved in mixing head position 17 mm. Due to the variable mixing
head position, the operating behaviour of the burner can be optimised for different heat generators.
GG20/1-N-LN
Natural gas LL: H
i,n
= 9.3 [kWh/m
3
]
Burner output
[kW]
Boiler output
η= 92% [kW]
Air flap
position
[ ° ]
Mixing head
position
[mm]
Position
inlet nozzle
[ ° ]
Gas nozzle pressure
p
G
[mbar]
Gas flow rate
[m
3
/h]
Stage 2 Stage 1 Stage 2 Stage 1 2nd stage
P9
1st stage
P1
Stage 2 Stage 1 Stage 2 Stage 1
75 55 69 51 23 0 27 0 4.8 2.9 8.3 6.1
85 55 78 51 28 0 27 0 6.8 2.9 9.4 6.1
105 60 97 55 45 10 27 0 9.5 3.2 11.6 6.7
125 70 115 64 100 18 27 0 11.9 4.2 13.9 7.8
100 65 92 60 30 10 17 0 4.1 1.7 11.1 7.2
140 70 129 64 50 13 17 0 8.0 2.0 15.5 7.8
170 85 156 78 100 20 17 0 12 2.7 18.8 9.4
GG20/1-N-LN
Natural gas E: H
i,n
= 10.4 [kWh/m
3
]
Burner output
[kW]
Boiler output
η= 92% [kW]
Air flap
position
[ ° ]
Mixing head
position
[mm]
Position
inlet nozzle
[ ° ]
Gas nozzle pressure
p
G
[mbar]
Gas flow rate
[m
3
/h]
Stage 2 Stage 1 Stage 2 Stage 1 2nd stage
P9
1st stage
P1
Stage 2 Stage 1 Stage 2 Stage 1
75 55 69 51 23 0 27 0 3.8 2.3 7.4 5.5
85 55 78 51 28 0 27 0 5.3 2.3 8.4 5.5
105 60 97 55 45 10 27 0 7.4 2.5 10.4 5.9
125 70 115 64 100 18 27 0 9.3 3.3 12.4 6.9
100 65 92 60 30 10 17 0 3.2 1.3 9.9 6.4
140 70 129 64 50 13 17 0 6.3 1.6 13.9 6.9
170 85 156 78 100 20 17 0 9.4 2.1 16.9 8.4
GG20/1-F-LN
Liquid gas: H
i,n
= 25.89 [kWh/m
3
]
Burner output
[kW]
Boiler output
η= 92% [kW]
Air flap
position
[ ° ]
Mixing head
position
[mm]
Position
inlet nozzle
[ ° ]
Gas nozzle pressure
p
G
[mbar]
Gas flow rate
[m
3
/h]
Stage 2 Stage 1 Stage 2 Stage 1 2nd stage
P9
1st stage
P1
Stage 2 Stage 1 Stage 2 Stage 1
75 55 69 51 23 0 27 0 5.0 2.7 2.9 2.1
85 55 78 51 28 0 27 0 6.4 2.7 3.3 2.1
105 60 97 55 45 10 27 0 9.8 3.2 4.1 2.3
125 70 115 64 100 18 27 0 13.9 4.4 4.8 2.7
100 65 92 60 30 10 17 0 6.3 2.7 3.9 2.5
140 70 129 64 50 13 17 0 12.3 3.1 5.4 2.7
170 85 156 78 100 20 17 0 18.2 4.6 6.6 3.3
Start-up

15
E.04.99 • G. 09.05.12
GG20/2-N-LN
Natural gas LL: H
i,n
= 9.3 [kWh/m
3
]
Burner output
[kW]
Boiler output
η= 92% [kW]
Air flap
position
[ ° ]
Mixing head
position
[mm]
Position
inlet nozzle
[ ° ]
Gas nozzle pressure
p
G
[mbar]
Gas flow rate
[m
3
/h]
Stage 2 Stage 1 Stage 2 Stage 1 2nd stage
P9
1st stage
P1
Stage 2 Stage 1 Stage 2 Stage 1
107 70 98 64 40 0 27 0 8.4 3.6 11.9 7.8
130 70 120 64 58 0 27 0 12.1 3.6 14.4 7.8
140 70 129 64 100 10 27 0 13.0 6.1 15.5 7.8
140 100 129 92 38 20 17 + 16 6.6 3.2 15.5 11.1
200 100 184 92 67 20 17 + 16 11.8 3.2 22.2 11.1
235 120 216 110 100 28 17 + 16 14.1 6.1 26.1 13.3
GG20/2-N-LN
Natural gas E: H
i,n
= 10.4 [kWh/m
3
]
Burner output
[kW]
Boiler output
η= 92% [kW]
Air flap
position
[ ° ]
Mixing head
position
[mm]
Position
inlet nozzle
[ ° ]
Gas nozzle pressure
p
G
[mbar]
Gas flow rate
[m
3
/h]
Stage 2 Stage 1 Stage 2 Stage 1 2nd stage
P9
1st stage
P1
Stage 2 Stage 1 Stage 2 Stage 1
107 70 98 64 40 0 27 0 6.6 2.8 10.6 6.9
130 70 120 64 58 0 27 0 9.5 2.8 12.9 6.9
140 70 129 64 100 10 27 0 10.2 4.8 13.9 6.9
140 100 129 92 38 20 17 + 16 5.2 2.5 13.9 9.9
200 100 184 92 67 20 17 + 16 9.2 2.5 19.8 9.9
235 120 216 110 100 28 17 + 16 11.0 4.8 23.3 11.9
GG20/2 -F-LN
Liquid gas: H
i,n
= 25.89 [kWh/m
3
]
Burner output
[kW]
Boiler output
η= 92% [kW]
Air flap
position
[ ° ]
Mixing head
position [mm]
Position
inlet nozzle
[ ° ]
Gas nozzle pressure
p
G
[mbar]
Gas flow rate
[m
3
/h]
Stage 2 Stage 1 Stage 2 Stage 1 2nd stage
P9
1st stage
P1
Stage 2 Stage 1 Stage 2 Stage 1
107 70 98 64 40 0 27 0 7.2 3.1 4.1 2.7
130 70 120 64 58 0 27 0 10.6 3.1 5.0 2.7
140 70 129 64 100 10 27 0 12.3 3.1 5.4 2.7
140 100 129 92 38 20 17 + 16 6.9 2.9 5.4 3.9
200 100 184 92 67 20 17 + 16 14.1 3.5 7.7 3.9
235 120 216 110 100 28 17 + 16 19.4 5.1 9.1 4.6
Start-up

16
E.04.99 • G. 09.05.12
The burner can be put into operation once the gas and electrical installation and assembly work has been
completed.
• Measure inlet pressure with U-pipe pressure gauge at measuring point "p
E
".
max. 100 mbar (static pressure) for KEV 220, KEV 225
max. 360 mbar (static pressure) for MB407, MB412, MBC300
min. 20 mbar (flow pressure) for -N
min. 35 mbar (flow pressure) for -F
Burner and gas ramp are preset to low output at the factory. This ensures an initial safe start-up of the
burner.
• Use the adjustment tables to set the burner to the desired nominal output.
For this:
• Check the nozzle pressure with U-pipe pressure gauge at measuring point "p
G
".
• Adjust gas pressure and air flow dimension "A" according to adjustment tables.
• Be sure to check the exhaust gas values (CO, CO
2
and/or O
2
).
• Depending on the system, the setting values must be corrected.
• The setting data must be logged once adjustment is complete.
• Check the gas pressure controller after start-up. Close the ball valve slowly, the burner must switch off
without triggering a fault.
The gas supply line and gas assembly must not subject the burner to tensile, compressive
or torsional forces; since these could adversely affect operational safety.
Exhaust gas values Natural gas LL+E Liquefied gas propane 3P
O
2
content 3.5-5.0%
CO
2
content 9-10% 10.5-11.5%
Start-up

17
E.04.99 • G. 09.05.12
20. Modulating or 2-stage sliding gas burner with gas train...
Gas supply measuring point A (p
E
)
nozzle pressure measuring points B (p
G
)
N= Zero point (gas nozzle pressure adjustment for
min. output)
V= Ratio of nozzle pressure to air pressure in the
burner tube (gas nozzle pressure adjustment at
max. output)
p
W
= Pressure at gas pressure monitor
p
F
= Furnace pressure
p
L
= Baffle plate pressure
Preset:
Locate the appropriate line in adjustment table according to boiler
output and adopt setting values.
• Air flow measurement adjustment, air flap position according to adjustment table.
• The settings "V" and "N" are shown on scales on the outside of the device and can be set from both
sides. In the low load range of the burner, the gas-air mix is set with the aid of a parallel shift of the
characteristic curve (adjusting screw "N"). At full load, adjustment screw "V" is used to change the
ratio to achieve the desired gas nozzle pressures p
G
(see adjustment table) and exhaust analysis val-
ues (CO
2
, CO).
Burner start:
• Start the burner at low load; if the burner does not go into operation, turn Nslightly in the "+"
direction and restart.
Precision setting:
Adjust max. output:
• Measure the gas nozzle pressure at B.
• Set burner gradually to high load 2nd stage and correct the exhaust gas analysis at "V".
To do so, set the output controller to max. output (contact from "T6" to "T8" in socket unit X32).
• Move air flap until the max. position is reached (see adjustment table).
• For GG20-Z-L-LN also set 1st/2nd stage switch to 2nd stage.
• Correct exhaust gas values at "V" (see table).
• Set the nozzle pressure by adjusting
the air flap
B
A
p
W
VN
p
L
p
F
Setting "V" Exhaust gas analysis
values
Change in "+"
direction if:
CO
2
too low
O
2
too high
Change in "-"
direction if:
CO
2
too high
O
2
too low
Adapt nozzle pres-
sure
max. output
Max. output
Increase ST2/max.
output if:
Output/nozzle pressure
too low
Reduce ST2/max.
output if:
Output/nozzle pressure
too high
Start-up

18
E.04.99 • G. 09.05.12
Set min. output 1st stage:
• Set burner to low load 1st stage and correct
exhaust gas values at "N".
for GG20-M-L-LN:
To do so, set the output controller to min. output
(contact from "T6" to "T7" in socket unit X32).
for GG20-Z-L-LN:
Set 1st/2nd stage switch to 1st stage.
• Adjust nozzle pressure by adjusting cam
ST1/min. according to the table.
• Correct the exhaust gas values at "N".
• For the positioning drive to approach the newly set
cam position, the output controller must be set to
max. output requirement for a few seconds (contact
from "T6" to "T8").
The positioning drive moves up.
• Reset the output controller to min. output request again (contact from "T6" to "T7").
The positioning drive moves to the newly set min. position.
On the 2-stage sliding version, set the switch 1st/2nd stage briefly to 2nd stage and then reset to 1st
stage.
• Correct the exhaust gas values at "N".
• If necessary, repeat adjustment procedure of cam position ST1/min. output as described above until
desired nozzle pressure is achieved.
• As the adjustments "V“ and "N“ mutually influence each other, the burner must be run up and down
several times between max. and min. heat requirement of the 1st/2nd stage output controller.
• For max. output, correct 2nd stage exhaust gas emission by adjusting "V“ and for min. output correct
1st stage by adjusting "N“.
• Start the burner; if the burner does not start, alter "N“ in direction "+“ and start burner again. Check
exhaust gas emission and, if necessary, alter 1st stage min./start output.
• Close the measuring connection pieces "A“ and "B“ - Do not close the possibly non-used
connection
pF
.
Caution !
Difference between baffle plate pressure p
L
- furnace pressure p
F
must be at least 0.3 mbar.
Adapt nozzle
pressure
min. output
Min. output
Increase ST1/min.
output if:
Output/nozzle pressure
too low
Increase ST1/min.
output if:
Output/nozzle pressure
too high
Setting "N" Exhaust gas analysis
values
Change in "+"
direction if:
CO
2
too low
O
2
too high
Change in "-"
direction if:
CO
2
too high
O
2
too low
Start-up

19
E.04.99 • G. 09.05.12
21. Calculation principle for gas burner adjustment
The values given in the tables are setting values for start-up.
The necessary system adjustment must be newly determined in each case.
General:
the calorific value (H
i,n
) of fuel gases is generally specified
for the normal state (0°C, 1013 mbar).
Natural gas E H
i,n
= 10.4 kWh/m
3
Natural gas LL H
i,n
= 9.3 kWh/m
3
Liquefied gas PB H
i,n
= 25.89 kWh/m
3
Gas meters measure the volume of gas in the operational state.
Gas flow determination:
To allow the heat generator load to be adjusted correctly, the gas flow rate must be determined in advance.
Example:
Height above sea level 230 m
Atmospheric pressure B (according to table) 989 mbar
Gas pressure P
G
at meter 20 mbar
Gas temperature
ϑG
16°C
Boiler rating Q
n
30 kW
Efficiency η
K
(assumed) 92%
Calorific value H
i,n
10.4 kWh/m
3
Gas flow in standard state (V
n
)
1
Gas flow in operating state (V
B
)
Conversion factor (f)
Annual average air pressure
Legend:
Q
n
= boiler output [kW]
η
K
= efficiency [%]
H
i,n
= lower standard calorific value [kWh/m
3
]
f = conversion factor
B = barometric air pressure [mbar]
p
G
= gas pressure at gas meter [mbar]
ϑG
= gas temperature at gas meter [°C]
Average geodetic altitude of the
supply region above sea level [m]
from 1 51 101 151 201 251 301 351 401 451 501 551 601 651 701
to 0 50 100 150 200 250 300 350 400 450 500 550 600 650 700 750
Annual average of air pressure (mbar) 1016 1013 1007 1001 995 989 983 977 971 965 959 953 947 942 936 930
V
nQ
n
η
k
H
×i n,
-------------------- 30kW
0 92 10
×
4kWh
m3
-----------
, ,
----------------------------------------= 3 1m3
h
-------
,= =
V
B
V
n
f
------ 3 1m3
h
-------
,
0 94,
-----------------= 3 3m3
h
-------
,= =
fB P
G
+
1013
-------------- 273
273 ϑ
G
+
--------------------
×=
Start-up

20
E.04.99 • G. 09.05.12
Flow measurement
Determining flow duration at gas meter..
Calculated flow duration in seconds t
spec
for a flow volume of 200 litres (corresponding to 0.2 m
3
)
for the example given above is:
V
B
= 3.3 m
3
/h
Gas flow setting
Measured flow duration in seconds [s] Measures
Greater than calculated flow duration t
soll
Increase gas flow
Less than calculated flow duration t
soll
Reduce gas flow
Equal to calculated flow duration t
soll
Gas flow achieved
t
soll
0 2m
3
3600s
h
---
×,
V
B
m
3
h
------
-------------------------------------- 720m
3
s
h
---
V
B
m
3
h
------
-------------------- 720m
3
s
h
---
3 3m
3
h
------
,
------------------- 218s====
Start-up
Table of contents
Other Giersch Burner manuals
Popular Burner manuals by other brands
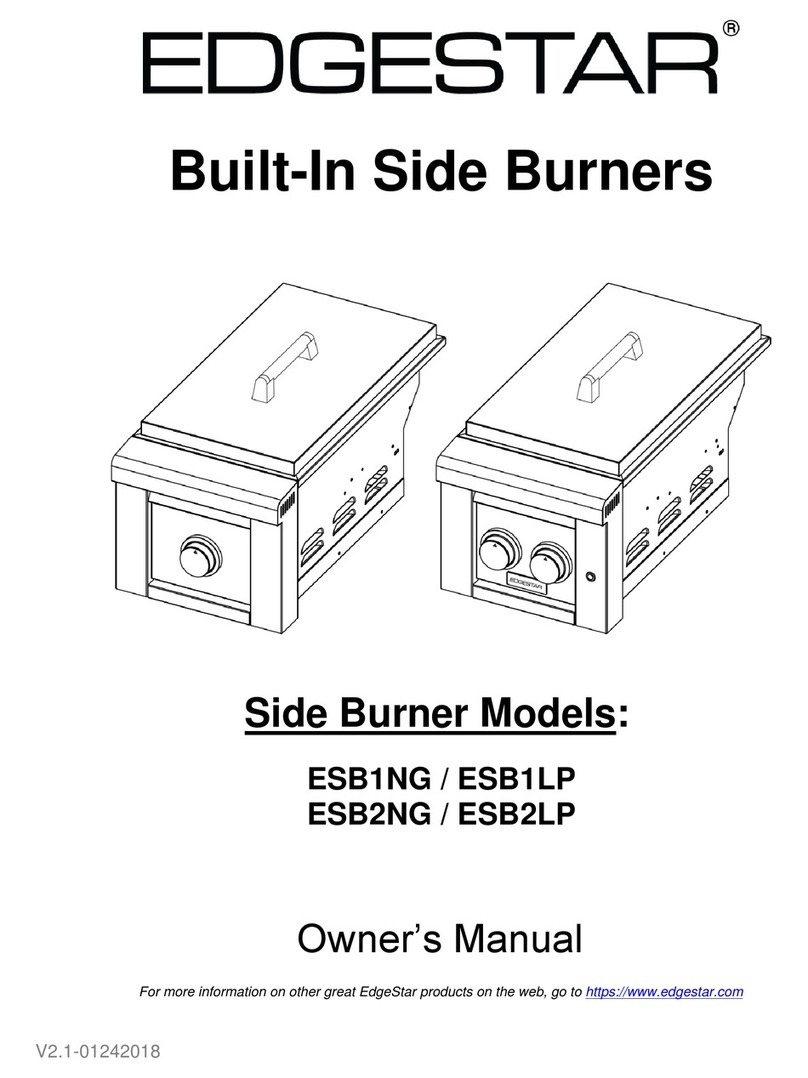
EdgeStar
EdgeStar ESB1NG owner's manual

Beckett
Beckett CG15 manual

Riello Burners
Riello Burners CAMRAY5 150 Installation, use and maintenance instructions
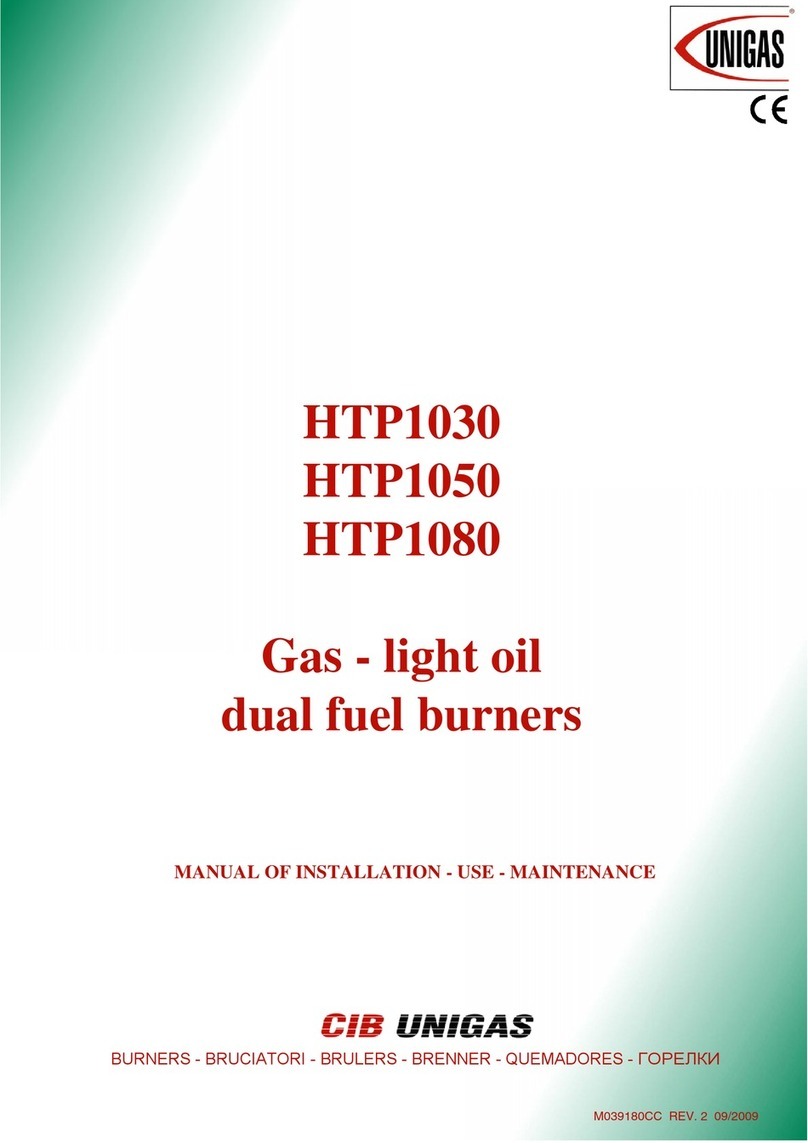
Unigas
Unigas HTP1030 Installation, user's, and maintenance guide
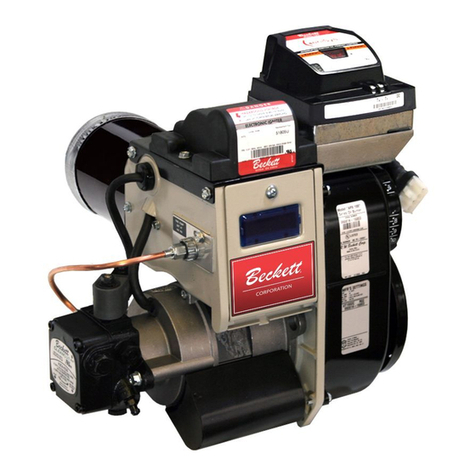
Beckett
Beckett AFII85 installation guide
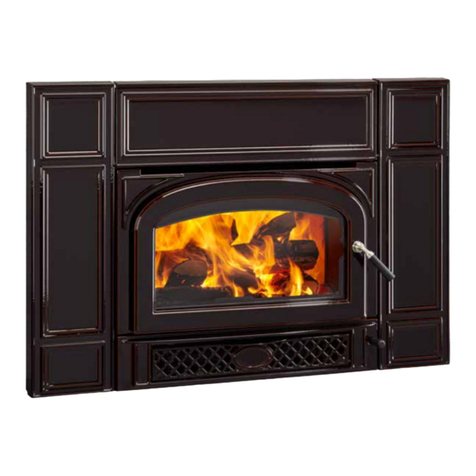
Vermont Castings
Vermont Castings GIFFORD-CB owner's manual

YOKOI KIKAI KOSAKUSHO
YOKOI KIKAI KOSAKUSHO HOPE CJ-1 Handling manual

Lion Premium Grills
Lion Premium Grills L1707 Assembly instruction
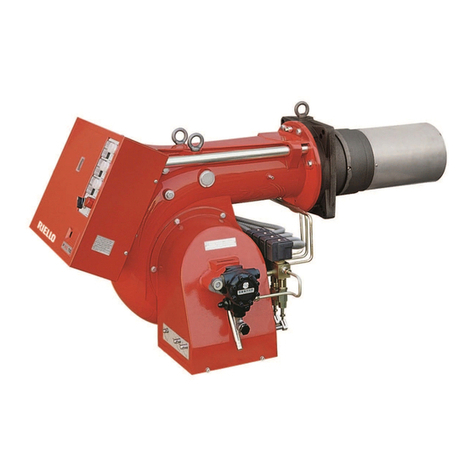
Riello
Riello P 300 T/G Installation, use and maintenance instructions
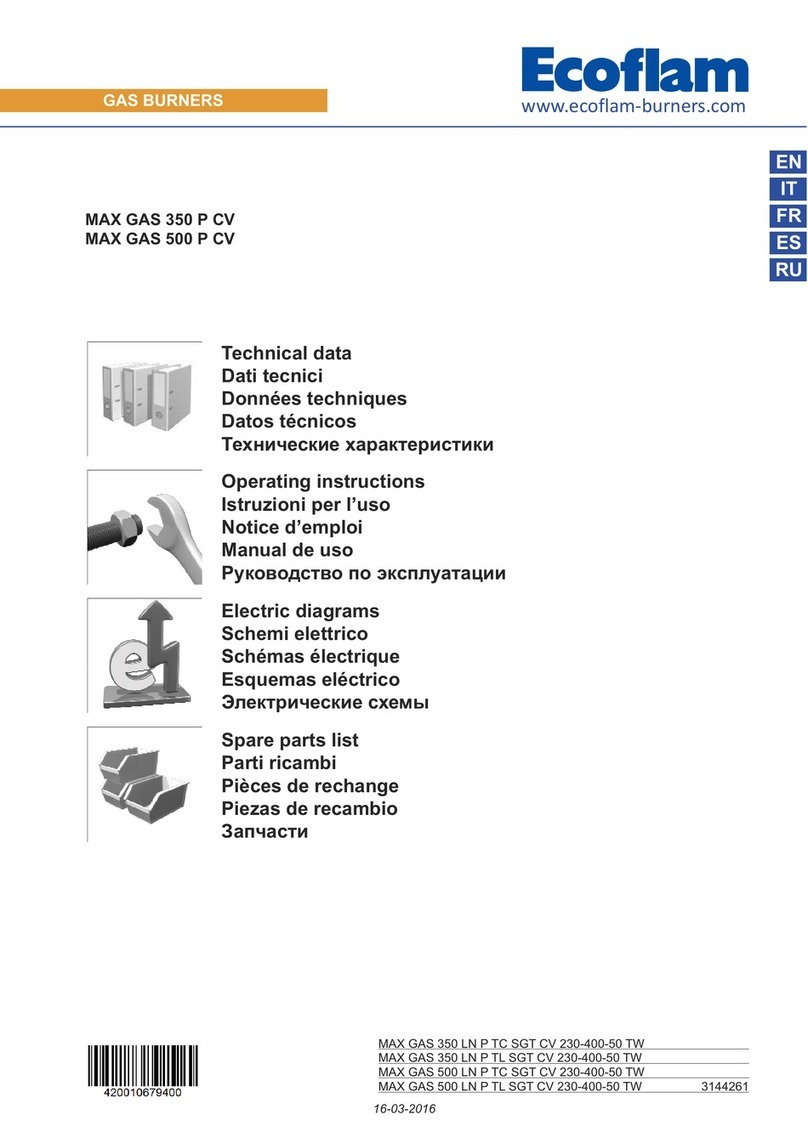
Ecoflam
Ecoflam MAX GAS 350 P CV manual
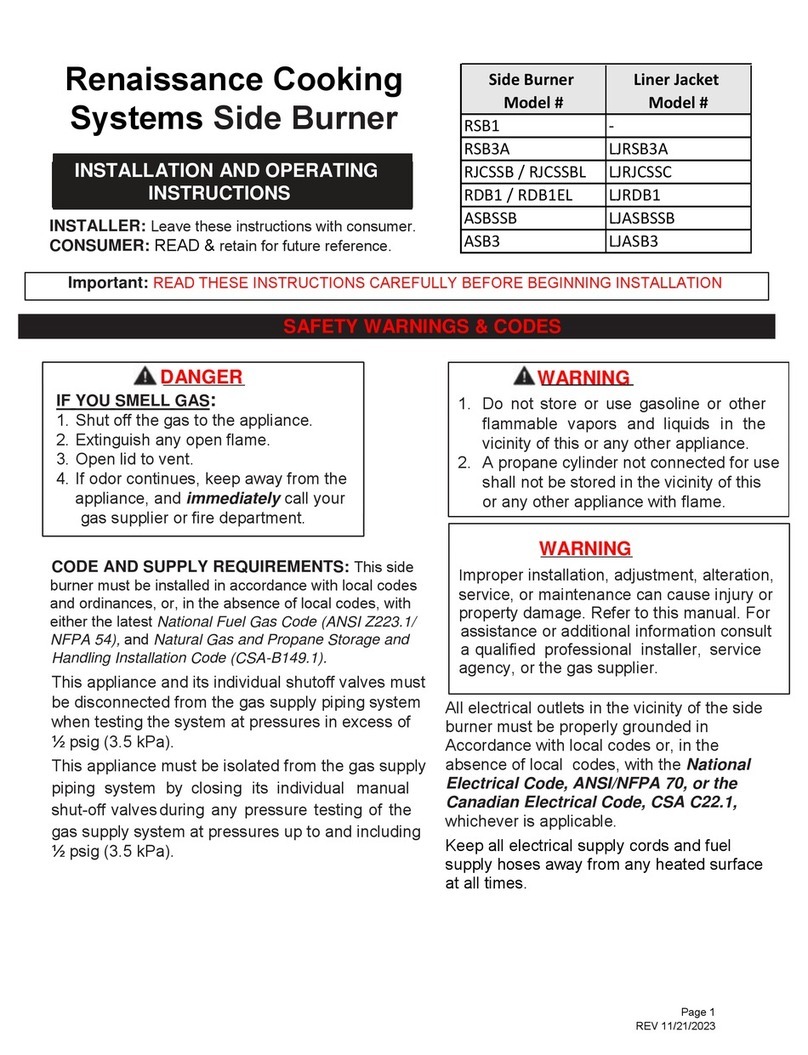
RCS
RCS RSB3A Installation and operating instructions

Weil-McLain
Weil-McLain UltraOil 800057000-Brn-PO Rie F5 Installation and operating manual