Grinnell F470 User manual

DELUGE VALVE,EXTERNAL RESETTING
MODEL F470 MULTIMATIC®— 4 and 6 INCH (100 and 150 mm)
GENERAL DESCRIPTION
The 4 and 6 inch (100 and 150 mm),
Model F470 External Resetting Multi-
matic Deluge Valves are differential
latch type valves designed for fire pro-
tection system service. They are used
as “automatic water control valves” in
deluge, preaction, and special types of
fire protection systems such as foam-
water and double interlock. The F470
Valves also provide for actuation of fire
alarms upon system operation.
The external resetting feature of the
F470 Valve provides for easy resetting
of a deluge or preaction system, with-
out having to open a valve handhole
cover to manually reposition a clapper
andlatchmechanism.Simplydepress-
ing a plunger at the left side of the
F470 Valve allows the clapper and
latch to reset.
Operation of an F470 Valve is provided
byanactuation(detection)systemthat
is separate from the normally dry sys-
tem piping. Trim configuration options
for automatic operation of the F470
include wet pilot actuation, dry pilot
actuation, and electric actuation. Trim
arrangements also provide for local
emergency (manual) release of the
F470 Valves.
APPROVALS AND STANDARDS
The 4 and 6 inch (100 and 150 mm),
Model F470 External Resetting Multi-
matic Deluge Valves are listed by Un-
derwriters Laboratories Inc. and Un-
derwriters’ Laboratories of Canada.
The F470 Valves are also approved by
Factory Mutual Research Corporation
and the Scientific Services Laborato-
ries (Australia).
The Model F470 Deluge Valves with
either wet or dry pilot actuation and
galvanized trim are approved by the
Loss Prevention Council (United King-
dom).
Inquiries concerning approval by the
Verband der Schadeversicherer
should be directed to Grinnell Sales &
Distribution, Kopersteden 1, NL-7547
TJ Enschede, Netherlands, Tel. 31-
534-283-434 / Fax. 31-534-283-377.
Printed in U.S.A. 9-99 TD116
FIGURE A
MODEL F470 EXTERNAL RESETTING MULTIMATIC DELUGE VALVES
— DIMENSIONS AND PORT LOCATIONS —
4 Inch (100 mm) Valve
6 Inch (150 mm) Valve
Nominal Dimensions in Inches and (mm)
VALVE
SIZE
4
(100)
6
(150)
VALVE
SIZE
4
(100)
6
(150)
A
2"
NPT
2"
NPT
J
8.00
(203,2)
8.87
(225,3)
B
1/2"
NPT
1/2"
NPT
K
10.50
(266,7)
11.50
(292,1)
C
1/2"
NPT
1/2"
NPT
L
8.50
(215,9)
9.18
(233,2)
D
1/2"
NPT
1/2"
NPT
M
3.75
(95,3)
4.54
(115,3)
E
3.44
(87,4)
3.40
(86,4)
N
2.37
(60,2)
3.20
(81,3)
F
2.56
(65,0)
2.45
(62,2)
P
2.56
(65,0)
2.45
(62,2)
G
2.73
(69,3)
3.69
(93,7)
Q
1.72
(43,7)
1.82
(46,2)
H
5.25
(133,4)
6.63
(168,4)
R
13.25
(336,6)
14.25
(362,0)
OBSOLETE

-2-
1 - Body
2 - Clapper
3 - Clapper Facing
4 - Clapper Facing
Retainer
5 - Clapper Bolt
6 - Seat Ring
FIGURE B
MODEL F470 EXTERNAL RESETTING MULTIMATIC DELUGE VALVE
— ASSEMBLY —
7 - Clapper Latch
8 - O-Ring, # 3-908
9-Reset
Bushing
10 - O-Ring, # 2-109*
11 - Reset Plunger
12 - Reset Knob
13 - Diaphragm Cover
Bolt, (5 req’d)
1/2" - 13 UNC x 1"
14 - Diaphragm Retainer
15 - Flange & Push Rod
Assembly
16 - Diaphragm
17 - Diaphragm
Housing
18 - 1/2" Pipe Plug
(4 req’d)
19 - Bearing (4 req’d)
20 - Clapper Hinge Pin
21 - Latch Hinge Pin
22 - Handhole Cover
23 - Handhole Cover Gasket
24 - Handhole Cover Bolt,
(1/2" - 13 UNC x 1-1/2"
4 req’d for 4" valve)
(3/4" - 11 UNC x 1-1/2"
5 req’d for 6" valve)
* Lubricated with Dow Corning FS3452 Flurosilicone Grease.
Nominal Dimensions in Inches and (MM)
AS 2129 (TABLE E)
ISO 2084 (PN10)†
JIS B 2210 (10K)
4" (100 mm) Valve Size 6" (150 mm) Valve Size
ABAB
7.50 (190,5)
7.00 (178,0)
7.09 (180,0)
6.89 (175,0)
0.75 (19,0)
0.71 (18,0)
0.71 (18,0)
0.75 (19,0)
9.50 (241,3) 0.88 (22,2)
9.25 (235,0)
9.45 (240,0)
9.45 (240,0)
0.87 (22,0)
0.87 (22,0)
0.91 (23,0)
†Same drilling as for BS 4504 Section 3.2 (PN10) and DIN 2532 (PN10).
TABLE A
DIMENSIONAL SPECIFICATIONS FOR SELECTION OF FLANGE DRILLING
ANSI B16.1 (CLASS 125)
OBSOLETE

The Model F470 Multimatic Deluge
ValvesareacceptedbytheCityofNew
York under MEA 38-92-M.
WARNING
The Model F470 Multimatic Deluge
Valves described herein must be in-
stalled and maintained in compli-
ance with this document, as well as
with the applicable standards of the
National Fire Protection Association,
in addition to the standards of any
other authorities having jurisdiction.
Failuretodosomayimpairtheinteg-
rity of these devices.
The owner is responsible for main-
taining their fire protection system
and devices in proper operating con-
dition. The installing contractor or
manufacturer should be contacted
relative to any questions.
TECHNICAL DATA
Deluge Valve:
The 4 and 6 inch (100 and 150 mm),
Model F470 External Resetting Multi-
matic Deluge Valves are rated for use
at a maximum service pressure of 175
psi (12,1 bar). The Valve dimensions
are shown in Figure A, and all of the
ports are NPT threaded per ANSI
Standard B1.20.1. Flanged inlet and
outlet connections are available drilled
per ANSI, AS, ISO, and JIS specifica-
tion options indicated in Table A.When
the flange drilling is provided to AS,
ISO, or JIS specifications, the label
located on the Handhole Cover indi-
cates the specification to which the
flange drilling has been provided.
The F470 Valve is to be installed verti-
cally, as shown in Figure A. Exterior
surfaces of the F470 Valve are painted
red, and the year of manufacture is
indicated on the Handhole Cover.
Components of the F470 Valve are
shown in Figure B. The Body, Hand-
hole Cover, and Diaphragm Cover are
ductile iron per ASTM A536 (UNS
F33100). The Handhole Cover Gasket
is neoprene, and the Clapper Facing,
Diaphragm, and O-Rings are EPDM.
The Seat Ring, Clapper, Diaphragm
Retainer, and the Flange of the Flange
& Push Rod Assembly are bronze per
ASTM B62 (UNS C83600).The Clap-
per Latch is aluminum bronze per
ASTM B148 (UNS C956200), the Re-
set Bushing is brass per ASTM B16
(UNS C36000), and the Bearings are
bronze perASTM B438,Grade 1,Type
II. The Clapper Facing Retainer, Clap-
per Bolt, Reset Plunger, Clapper
Hinge Pin, Latch Hinge Pin, and the
Push Rod of the Flange & Push Rod
Assembly are fabricated from austeni-
tic stainless steel. The Reset Knob is
phenolic, and the Handhole Cover
Bolts, Diaphragm Cover Bolts, and
Pipe Plugs are carbon steel.
The nominal pressure losses versus
flow are shown in Graphs A-1 and A-2.
Theapproximate frictionlosses,based
on the Hazen and Williams formula
and expressed in equivalent length of
Schedule 40 pipe with C = 120, is 12
feet for the 4 inch (100 mm) valve size
and 30 feet for the 6 inch (150 mm)
valve size. The equivalent length of
pipe has been calculated on the basis
of the flow rates typically used with
each size valve.
Valve Trim:
The Wet Pilot Actuation Trim, Dry Pilot
Actuation Trim, or Electric Actuation
Trim illustrated in Figure F-1 form a
part of the laboratory listings and ap-
-3
GRAPHS A-1 and A-2
NOMINAL PRESSURE LOSS VERSUS FLOW
GRAPH A-1 GRAPH A-2
OBSOLETE

proval of the F470 Valves and are nec-
essary for their proper operation.Each
package of trim includes the following
items:
•Water Supply Pressure Gauge
•Diaphragm Chamber
Pressure Gauge
•DiaphragmChamber Connections
•Actuation Devices (as applicable)
•Main Drain Valve
•Alarm Test Valve
•Alarm Control Valve
•Automatic Drain Valve
•Dry Pilot Line Pressure Gauge
(as applicable)
To ease field assembly of the trim ar-
rangements, the appropriate compo-
nents required for Wet Pilot Actuation,
Dry Pilot Actuation, or Electric Actua-
tion are factory assembled as shown
in Figure F-2.
Wet Pilot Actuation
(Figure F-1, Items 1 through 35)
The Wet Pilot Actuation Trim provides
for connection of a detection system
consisting of wet pilot sprinklers (heat
detectors) and manual control stations
interconnected with minimum 1/2 inch
(15 mm) Schedule 40 steel pipe. The
pilot line is connected to the “Wet Pilot
Detection”connection shown in Figure
F-1. Nominal installation dimensions
for the Wet Pilot Actuation Trim are
shown in Figure D.
Wet pilot sprinklers are to be minimum
1/2 inch (15 mm) orifice listed or ap-
proved automatic sprinklers. Manual
Control Stations are to be either the
ModelF180orF184describedinTech-
nical Data Sheet TD121.
The maximum height of a wet pilot line
above the F470 Valve must not exceed
the limitations given in Graph B as a
function of the minimum water supply
pressure to the F470 Valve and the
length of the pilot line to the most re-
mote pilot sprinkler.
Provision must be made for installing
a 1/2 inch (15mm) orifice, Inspector’s
Test Connection at the most hydrauli-
cally demanding location of a wet pilot
line (usually adjacent to the highest
and most remote wet pilot sprinkler or
manual control station).
-4-
GRAPH B
WET PILOT LINE DESIGN CRITERIA
GRAPH C
DRY PILOT LINE PRESSURE REQUIREMENTS
OBSOLETE

To determine the most hydraulically
demanding location of a wet pilot line,
when the choice between two or more
locations is not readily apparent, de-
termine for each location the elevation
above the F470 Valve and the equiva-
lent length of fittings plus horizontal
pipe from the F470 Valve to the loca-
tion. Then, using Graph B, determine
the minimum system supply pressure
required for the elevation and equiva-
lent length of pipe at each location.
Interpolate between the equivalent
lengthplotsasnecessary.Thelocation
requiring the highest system supply
pressure is the most hydraulically de-
manding location for the wet pilot line.
(Reference: In no case should the re-
quired system supplypressure exceed
theactualavailableminimumexpected
system supply pressure.)
Operation of a pilot sprinkler or open-
ing of a manual control station results
in a rapid pressure drop in the Dia-
phragm Chamber of the F470 Valve,
and the force differential applied
through the Clapper Latch which holds
the Clapper down in the set position is
reduced to below the valve trip point.
NOTES
WetPilotLinesmustbemaintainedat
a minimum temperatureof 40°F/4°C.
Itis recommendedthatinternallygal-
vanized pipe and cast iron fittings be
used for wet pilot lines.
Dry Pilot Actuation
(Figure F, Items 1 through 35 plus
Items D1 through D14)
The Dry Pilot Actuation Trim provides
for installation of a detection system
consisting of dry pilot sprinklers (heat
detectors) and manual control stations
interconnected with minimum 1/2 inch
(15 mm) steel pipe. The pilot line,
which is to be pressurized with air or
nitrogen, is connected to the “Dry Pilot
Detection”connection shown in Figure
F. Provision must be made for a 1/2
inch (15 mm) orifice, Inspector’s Test
Connection at the most remote loca-
tion from the F470 Valve. Nominal in-
stallation dimensions for Dry Pilot Ac-
tuationTrimareshowninFigureE.
The Dry Pilot Actuation Trim is pro-
videdwitha listed and approvedModel
B-1 Dry Pilot Actuator, which is de-
scribed in Technical Data Sheet
TD117W.The Actuator is rated for use
at a maximum pilot service pressure of
50 psi (3,4 bar) and a maximum water
supply service pressure of 175 psi
(12,1 bar).
Operation of a pilot sprinkler or open-
ing of a manual control station, re-
leases pneumatic pressure from the
pilot line.In turn, the Dry Pilot Actuator
opens resulting in a rapid pressure
drop in the Diaphragm Chamber of the
F470 Valve, and the force differential
applied through the Clapper Latch
which holds the Clapper down in the
set position is reduced to below the
valvetrippoint.
Dry pilot sprinklers are to be minimum
1/2 inch (15 mm) orifice listed or ap-
proved automatic sprinklers. Manual
Control Stations are to be either the
ModelF180orF184describedinTech-
nical Data Sheet TD121.
Graph C shows the “minimum pilot line
service pressure” as a function of the
watersupplypressure.Thepressurein
the dry pilot actuation system must be
automatically maintained using one of
the following maintenance devices, as
appropriate.
•Model F324 Air Maintenance De-
vice (pressure reducing type), re-
fer to Technical Data Sheet
TD111.
•Model F326 Air Maintenance De-
vice(compressorcontroltype),re-
fer to Technical Data Sheet
TD112.
•Model F328 Nitrogen Mainte-
nance Device (high pressure re-
ducing type), refer to Technical
Data Sheet TD113.
NOTES
The dew point of the pilot line air
pressure must be maintained below
the lowest ambient temperature to
which the dry pilot actuation system
will be exposed. Accumulation of
water in the pilot line connection to
the Actuator will lower the air pres-
sure at which the Actuator will open
and possibly prevent proper opera-
tion. Also, introduction of moisture
into the pilot lines exposed to freezing
temperatures can create an ice
buildup which could prevent proper
operation of the Actuator.
Anairdryermustbeinstalledwhere
the moisture content of the air supply
is not properly controlled at less than
the required value. The desiccant
dryer with mounting accessories de-
scribed in Technical Data Sheet
TD135is suitablefor use withamaxi-
mum inlet pressure of 150 psi (10,3
bar) and for drying system air down
to a dew point of less than -20°F/-
29°C at a pressure of 45 psi (3,1 bar).
It is recommended that an F328 Ni-
trogenMaintenanceDevicebeutilized
in dry pilot actuation system applica-
tions where the dew point must be
maintained below -20°F/-29°C. See
Technical Data Sheet TD113.
Itis recommendedthatinternallygal-
vanized pipe and cast iron fittings be
used for dry pilot lines.
Supervision of the pressure in the dry
pilot actuation system and/or alarm
which separately indicates operation
of the detection system is recom-
mended and may be required by the
authority having jurisdiction. A dual
setting low pressure alarm switch,
such as the unit described in Technical
Data Sheet TD210, is suitable for the
service. The recommended pressure
settings are as follows:
• Low pressure alarm setting at
approximately 6 psi (0,4 bar)
below the minimum pilot line
service pressure requirement
shown in Graph C.
• Fire alarm setting at approxi-
mately 15 psi (1,0 bar) below
the minimum pilot line service
pressure requirement shown
in Graph C.
The Pressure Relief Valve (Ref. Item
D5 - Fig. F) is factory set to relieve at
apressureofapproximately45psi(3,1
bar); however, it may be field adjusted
to a lower pressure, if required.
Electric Actuation Trim
(Figure F, Items 1 through 35 plus
Items E1 through E5)
The Electric Actuation Trim is required
for electric operation of the F470 Valve
by a detection system consisting of
electrical devices such as heat sensi-
tive thermostats, smoke detectors,
and/or electric manual pull stations.
Information on the various types of So-
lenoid Valves that may be used with
this trim package is given in Technical
Data Sheet TD119. A listed and ap-
proved, 24VDC Solenoid Valve for
non-hazardous locations is supplied
as standard. Nominal installation di-
mensions for the Electric Actuation
Trim are shown in Figure D.
NOTE
ApprovalbyFactoryMutualiscontin-
gent on the use of an FM Approved
24VDC Solenoid Valve. FM only ap-
proves solenoid valves for use in non-
hazardous locations.
The Electric Actuation Trim is only to
be used in conjunction with an electric
deluge valve releasing panel (auto-
matic control unit) that is listed or ap-
proved (as appropriate) for fire protec-
tion system releasing service. In
addition, the deluge valve releasing
panel is only to be operated by listed
or approved (as appropriate) fire de-
tectors.
Operation of an electrical device such
as a heat sensitive thermostat, smoke
detector, or electrical manual control
stationsignalsthedelugevalvereleas-
ing panel to energize the Solenoid
Valve. In turn, the energized Solenoid
Valve opens resulting in a rapid pres-
sure drop in the Diaphragm Chamber
-5-
OBSOLETE

of the F470 Valve, and the force differ-
ential applied through the Clapper
Latch which holds the Clapper downin
theset position is reducedtobelowthe
valvetrippoint.
NOTE
Consult with the Authority Having
Jurisdiction regarding installation
criteria pertaining to electric actua-
tion circuitry.
OPERATING PRINCIPLES
The Model F470 Multimatic Deluge
Valve is a differential latch type valve
which depends upon water pressure in
the Diaphragm Chamber (Ref. Figure
C-1) to hold the Clapper closed
againstthewatersupply pressure.The
nominal trip ratio is 2.5 to 1, i.e., the
F470 Valve operates (opens) when the
pressurein the DiaphragmChamberis
reduced to approximately 40 percent
of the water supply pressure.
When the F470 Valve is setforservice,
the Diaphragm Chamber is pressur-
ized through the trim connections from
the inlet side of the system’s main con-
trol valve, for example an O.S.&Y.gate
valve or butterfly valve (Ref. Figure G-
1, G-2, or G-3). Opening of an actua-
tion device, for example the solenoid
valve in the Electric Actuation Trim
(Ref.Fig.G-3),releaseswaterfromthe
Diaphragm Chamber faster than it can
be replenished through the 1/8 inch
(3,2mm) Restriction in the Diaphragm
Chamber Supply Connection. This re-
sults in a rapid pressure drop in the
Diaphragm Chamber and the force dif-
ferential applied through the Clapper
Latch to hold the Clapper down in the
set position is reduced to below the
valve trip point.The water supply pres-
sure then forces the Clapper open per-
mitting water to flow into the system
piping, as well as through the Alarm
Porttoactuatethesystemalarms(Ref.
Figure C-2).
When the system main control valve is
closed to stop waterflow into the sys-
tem, the Clapper will be prevented
from resetting by the Clapper Latch
until the Rest Knob is pushed inward
(Ref. Figure C-3). Pushing the Reset
Knobinwardwilltemporarilyreposition
the Clapper Latch away from the wa-
terway and allows the Clapper to drop
into the seated position.
-6-
FIGURE C
MODEL F470 EXTERNAL RESETTING MULTIMATIC DELUGE VALVE
— SET AND OPEN POSITIONS —
— Open Position (Flowing)—
Figure C-2
— Set Position —
Figure C-1
— Open Position (No Flow)—
Figure C-3
OBSOLETE

INSTALLATION
NOTES
Proper operation of the Model F470
Multimatic Deluge Valves depends
upon their trim being installed in ac-
cordance with the instructions given
in this Technical Data Sheet. Failure
to follow the appropriate trim dia-
gram may prevent the F470 Valve
from functioning properly, as well as
void listings, approvals, and the
manufacturer’s warranties.
The F470 Valve must be installed in a
readily visible and accessible loca-
tion.
TheF470Valve,associatedtrim,and
wet pilot lines must be maintained at
a minimum temperatureof 40°F/4°C.
HeattracingoftheF470Valveorits
associated trim is not permitted.Heat
tracing can result in the formation of
hardened mineral deposits which are
capable of preventing proper opera-
tion.
The Model F470 Multimatic Deluge
Valve is to be installed in accordance
with the following criteria:
1a. Flange mounting fasteners are to be
tightened uniformly using a cross-
draw sequence. Fastener specifica-
tions are to be as required by the
authority having jurisdiction. Tight-
eningtorquesaretobeasindicated
below.
Valve Fastener Torque
Size Size Ft. Lbs. (Nm)
4" 5/8" (M16) 40-50 (54-68)
6" 3/4" (M20) 50-65 (68-81)
1b. Allnipples,fittings,anddevicesmust
be clean and free of scale and burrs
before installation. Use pipe thread
sealant sparingly on male pipe
threads only.
NOTE
It is recommended that internally
galvanized pipe and cast iron fit-
tingsbeusedforwetordrypilot
lines.
2. The F470 Valve must be trimmed in
accordance with Figures F-1 & F-2.
3. Care must be taken to make sure
that check valves, strainers, globe
valves,etc.areinstalledwiththeflow
arrows in the proper direction.
4. Drain tubing to the drip funnel must
be installed with smooth bends that
will not restrict flow.
5. The main drain and drip funnel drain
may be interconnected provided a
check valve is located at least 12
-7-
FIGURE D
NOMINAL INSTALLATION DIMENSIONS FOR
WET PILOT ACTUATION TRIM OR ELECTRIC ACTUATION TRIM
Left View Front View
*MINIMUM CLEARANCE, ADDITIONAL 2" (50mm) RECOMMENDED
Nominal Installation Dimensions in Inches and (MM)
VALVE
SIZE
4
(100)
6
(150)
A
12.00
(304,8)
12.00
(304,8)
J
7.75
(196,9)
8.56
(217,4)
B
8.69
(220,7)
8.69
(220,7)
K
6.31
(160,3)
6.31
(160,3)
C
14.25
(362,0)
15.12
(384,0)
L
0.25
(6,4)
0.12
(3,0)
D
13.69
(347,7)
14.50
(368,3)
E
19.00
(482,6)
20.00
(508,0)
F
5.44
(138,2)
5.50
(139,7)
G
6.69
(169,9)
7.62
(193,5)
H
8.75
(222,3)
8.88
(225,6)
OBSOLETE

inches (300 mm) below the drip fun-
nel.
6. Suitable provision must be made for
disposal of drain water. Drainage
water must be directed such that it
will not cause accidental damage to
property or danger to persons.
7. Connect the Diaphragm Chamber
Supply Control Valvetotheinlet side
of the system’s main control valve in
order to facilitate setting of the F470
Valve (Ref.G-1, G-2, or G-3).
8. An Inspector’s Test Connection, as
described in the Technical Data sec-
tion,must beprovidedforWetor Dry
Pilot Actuation systems.
9. An Air Maintenance Device, as de-
scribed in the Technical Data Sec-
tion, must be provided for Dry Pilot
Actuation.
10. Adesiccantdryer,whenspecifiedfor
Dry Pilot Actuation, is to be installed
between a drip leg and the Air Main-
tenance Device.
11. The Low Pressure Alarm Switch for
DryPilotActuationistobeadjusted
as follows:
• Low pressure alarm setting at
approximately 6 psi (0,4 bar)
below the minimum pilot line
service pressure requirement
shown in Graph C.
• Fire alarm setting at approxi-
mately 15 psi (1,0 bar) below
the minimum pilot line service
pressure requirement shown
in Graph C.
-8-
FIGURE E
NOMINAL INSTALLATION DIMENSIONS FOR
DRY PILOT ACTUATION TRIM
Left View Front View
*MINIMUM CLEARANCE, ADDITIONAL 2" (50mm) RECOMMENDED
Nominal Installation Dimensions in Inches and (MM)
VALVE
SIZE
4
(100)
6
(150)
A
12.00
(304,8)
12.00
(304,8)
J
7.75
(196,9)
8.56
(217,4)
B
8.69
(220,7)
8.69
(220,7)
K
6.31
(160,3)
6.31
(160,3)
C
14.56
(369,8)
15.44
(392,2)
L
0.25
(6,4)
0.12
(3,0)
D
13.69
(347,7)
14.50
(368,3)
E
30.12
(765,0)
31.12
(790,4)
F
5.44
(138,2)
5.50
(139,7)
G
6.69
(169,9)
7.62
(193,5)
H
8.75
(222,3)
8.88
(225,6)
OBSOLETE

12. Unused pressure alarm switch con-
nections must be plugged.
13. The Pressure Relief Valve provided
with the Dry Pilot Actuation Trim is
factory set to relieveat a pressure of
approximately 45 psi (3,1 bar),
which can typically be used for a
maximum normal dry pilot actuation
system pressure of 40 psi (2,8 bar).
The Pressure Relief Valve may be
reset;however,it must be be reset to
relieve at a pressure which is in ac-
cordance with the requirements of
the authority having jurisdiction.
To reset the Pressure Relief Valve,
first loosen the jam nut and then
adjust the cap accordingly — clock-
wise for a higher pressure setting or
counterclockwise for a lower pres-
sure setting. After verifying the de-
sired pressure setting, tighten the
jam nut.
14. Conduit and electrical connections
are to be made in accordance with
the requirements of the authority
having jurisdiction and/or the Na-
tional Electric Code.
VALVE SETTING PROCEDURE
Steps 1 through 12 are to be per-
formed when initially setting the Model
F470 Multimatic Deluge Valve;after an
operational test of the fire protection
system;or, after system operation due
to a fire.
1. ClosetheDiaphragmChamberSup-
ply Control Valve.
2. Close the Main Control Valve, and if
thesystemisequippedwithDryPilot
Actuation, close the Air Supply Con-
trol Valve (Ref.Figure F).
3. Open the Main Drain Valve and all
auxiliary drains in the system.Close
the auxiliary drain valves after water
ceases todischarge.Leave the Main
Drain Valve open.
4. Depress the plunger of the Automat-
ic Drain Valve to verify that it is open
and that the F470 Valve is com-
pletely drained.
5. Push the ResetKnobinwardtoallow
the Clapper to reseat.
Under normal circumstances, the
reseating of the Clapper can be
heard; however, during an annual
operation test procedure, for exam-
ple, due to minimal flow through a
partially opened main control valve,
the Clapper may not latch open as
shown in Figure C-3. In which case
the reseating sound of the Clapper
will not be heard.
Also under normal circumstances,
water pressure in the riser will have
exerted sufficient force on the Dia-
phragm so as to have emptied most
of the water from the Diaphragm
Chamber which, in turn, will ease
the pushing of the Reset Knob by
eliminating the resistive force pro-
duced by a water filled Diaphragm
Chamber. Therefore, should water
remain in the Diaphragm Chamber,
the Reset Plunger will need to be
depressed with added force to push
the remaining water out of the Dia-
phragm Chamber and through an
open actuation device (e.g., a Dry
Pilot Actuator or Solenoid Valve).
NOTE
If the Reset Knob can not be de-
pressed sufficiently to allow the
Clapper to reseat, operate (open)
the Manual Control Station and
then once again push the Reset
Knob with sufficient force to push
the water out of the Diaphragm
Chamber through the Manual
Control Station drain.
6. Clean the Strainer in theDiaphragm
Chamber Supply connection by re-
moving the clean-out plug and
strainer basket.The Strainer may be
flushed out by momentarily opening
the Diaphragm Chamber Supply
Control Valve.
7. Open the Alarm Control Valve (Fig.
F), if it was closed to silence local
alarms.
It is recommended that the Alarm
Control Valve be wire sealed in the
open position with a No. 16 twisted
wire, the ends of which are secured
by a lead seal.The wire seal should
be looped through the hole in the
handleandtightlytwistedaroundthe
pipe nipple adjacent to the handle.
8. Reset the actuation system.
Manual Actuation — Push the oper-
ating lever up;however, do not close
the hinged cover at this time.
Wet Pilot Actuation — Replace op-
erated pilot sprinklers and/or reset
the manual control stations.
Dry Pilot Actuation — Replace oper-
ated pilot sprinklers and/or reset the
manual control stations. Re-estab-
lish dry pilot pneumatic pressure.
Electric Actuation — Reset the elec-
tric detection system in accordance
with the manufacturer’s instructions
to de-energize the solenoid valve.
NOTE
In order to prevent the possibility
of a subsequent operation of an
overheated solder type pilot sprin-
kler, any solder type pilot sprin-
klers which were possibly exposed
to a temperature greater than
their maximum rated ambient
must be replaced.
9. Open the DiaphragmChamber Sup-
ply Control Valve and allow time for
full pressure to build up in the Dia-
phragm Chamber.
10. Operate (open) the Manual Control
Station to vent trapped air from the
Diaphragm Chamber. If necessary,
first open the hinged cover, and then
fullypulldownontheoperatinglever.
SLOWLY close the operating lever,
by pushing it up, after aerated water
ceases to discharge from the Man-
ual Control Station drain tubing.
Close the hinged cover and insert a
new break rod in the small hole
through the top of the enclosing
box.
If wet pilot actuation is being used,
crackopen the Inspector’s TestCon-
nection and any other vent valves, to
relieve trapped air. After the dis-
charge of air has stopped, close the
vent valves and the Inspector’s Test
Connection.
11. Inspect drain connections from the
Manual Control Station, Solenoid
Valve, Dry Pilot Actuator, and Alarm
Devices, as applicable. Any leaks
must be corrected before proceed-
ing to the next step.
12. Slowly open the Main Control Valve.
Close the Main Drain Valve as soon
as water discharges from the drain
connection. Observe the Automatic
Drain Valve for leaks. If there are
leaks, determine/correct the cause
of the leakage problem. If there are
no leaks, the F470 Valve is ready to
be placed in service and the Main
Control Ave must then be fully
opened.
NOTE
After setting a fire protection system,
notify the proper authorities and ad-
vise those responsible for monitoring
proprietary and/or central station
alarms.
-9-
OBSOLETE

-10-
FIGURE F-1
EXPLODED VIEW OF VALVE TRIM
NOTE: Refer to Page11 for the corresponding bills of materials.
OBSOLETE

CARE AND MAINTENANCE
The following procedures and inspec-
tions should be perform as indicated,
in addition to any specific require-
ments of the NFPA, and any impair-
ment must be immediately corrected.
It is also recommended that fire pro-
tection systems be inspected by a
qualified Inspection Service.
NOTES
The operational test procedure,water-
flow pressure alarm test procedure,
and low pressure alarm test proce-
dure will result in operation of the
associated alarms. Consequently, no-
tification must first be given to the
owner and the fire department, cen-
tral station, or other signal station to
which the alarms are connected.
Before closing a fire protection system
main control valve for maintenance
work on the fire protection system
which it controls, permission to shut
down the effected fire protection sys-
tems must first be obtained from the
proper authorities and all personnel
who may be affected by this decision
must be notified.
Annual Operation Test Procedure
Proper operation of the F470 Valve
(i.e., opening of the F470 Valve as dur-
-11-
VALVE TRIM
BILLS OF MATERIALS
NOTES:
1. WetPilotActuationTrimconsistsof
Items 1 through 35.
2. Dry PilotActuationTrim consists of
Items 1 through 35 plus Items D1
through D14.
3. Electric Actuation Trim consists of
Items 1 through 35 plus Items E1
through E5.
4. The nipples utilized in the trim ar-
rangements are Schedule 40 steel
per ASTM A53 or A135 and they are
threaded per ANSI B1.20.1 The fit-
tings are either malleable iron per
ANSI B16.3 or cast iron per ANSI
B16.4.
“Standard order” trim is provided
with black nipples and fittings: how-
ever, galvanized nipples and fittings
are available on “special order”.
1 - 300 lb. Water Pres-
sure Gauge
(2 req’d)
2 - 1/4" Gauge
Test Valve
3 - Model F180
Manual Control
Station
4 - 2" Angle Valve
5 - 1/2" Ball Valve
(2 req’d)
6 - 1/2" Swing Check
Valve
7 - 1/2" Spring
Loaded Check
Valve
8 - Priming Supply Re-
striction
9 - 1/2" Y-Strainer
10 - Model F793
Automatic
Drain Valve
11 - Drip Funnel
Support Plug
12 - Drip Funnel
Support
13 - Drip Funnel
14 - 3/32" Vent
Fitting
15 - 1/2" Angle
Valve
16 - 1/4" Tube,
30" long
17 - 1/2" Tube
Connector
18 - 1/2" Tube,
24" long
19 - 1/4" Plug
20 - 1/2" Plug
21 - 3/4" Plug
22 - 1/2" Union
(5 req’d)
23 - 1/2" 90° Elbow (3
req’d)
24 - 1/2" Tee (6 req’d)
25 - 1/2" x 1/4" x 1/2"
Tee (3 req’d)
26 - 1/2" x 1/2" x 3/4"
Tee
27 - 2" 90° Elbow
28 - 1/2" x 1-1/2"
Nipple
(17 req’d)
29 - 1/2" x 3"
Nipple
30 - 1/2" x 4" Nipple
31 - 1/2" x 5" Nipple
(2 req’d)
32 - 1/2" x 7-1/2"
Nipple
33 - 1/2" x 10-1/2"
Nipple for
4" valve,
1/2" x 12"
Nipple for
6" valve
34 - 1/4" x 1-1/2"
Nipple
35 - 2 x 3"
Nipple
(2 req’d)
D1 - Model B-1
Dry Pilot
Actuator
D2 - 250 lb. Air
Pressure
Gauge
D3 - 1/4" Gauge
Test Valve
D4 - 1/2" Globe
Valve
D5 - 1/4" Pressure
Relief Valve
D6 - 1/4" Plug
D7 - 1/2" Tube
Connector
D8 - 1/2" Tube,
24" long
D9 - 1/2" 90° Elbow
(2 req’d)
D10 - 1/2" x 1/2" x 1/4"
Tee (2 req’d)
D11 - 1/2" Tee
(2 req’d)
D12 - 1/4" x 1-1/2"
Nipple
D13 - 1/2" x 1-1/2"
Nipple
(7 req’d)
D14 - 1/2" x 3"
Nipple
E1 - 1/2" 90° Elbow
E2 - 1/2" Tube
Connector
E3 - 1/2" Tube,
24" long
E4 - 1/2" x 1-1/2"
Nipple
(2 req’d)
E5 - 24VDC Solenoid
Valve
FIGURE F-2
“STANDARD ORDER” FACTORY ASSEMBLED VALVE TRIM
OBSOLETE

FIGURE G-1
DELUGE VALVE SYSTEM SCHEMATIC
— WET PILOT ACTUATION—
FIGURE G-2
DELUGE VALVE SYSTEM SCHEMATIC
— DRY PILOT ACTUATION—
-12-
OBSOLETE

ing a fire condition) should be verified
at least once a year as follows:
1. Ifwatermustbepreventedfromflow-
ing beyond the riser, perform the fol-
lowing steps.
a. Close the Main Control Valve.
b. Open the Main Drain Valve.
c. Open the Main Control Valve
oneturn beyondthepositionat
which water just begins to flow
from the Main Drain Valve.
d. Close the Main Drain Valve.
2. Determine the type of actuation/de-
tection system, and operate the
F470 Valve accordingly.
NOTE
Be prepared to quickly perform
Steps3,4,and5,ifwatermustbe
prevented from flowing beyond
the riser.
Wet Pilot Actuation — Open the
Inspector’s Test Connection.
Dry Pilot Actuation — Open the
Inspector’s Test Connection.
Electric Actuation — Test the del-
uge releasing panel (automatic con-
trol unit) in accordance with the
manufacturer’s instructions to ener-
gize the solenoid valve.
3. Verify that the F470 Valve has
tripped, as indicated by the flow of
water into the system.
4. ClosetheDiaphragmChamberSup-
ply Control Valve.
5. Close the system’s Main Control
Valve.
6. Reset the F470 Deluge Valve in ac-
cordance with the Valve Setting Pro-
cedure.
Five Year Internal Valve Inspection
Once every five years during the an-
nual operational test procedure and
prior to the F470 Valve being reset,the
internal parts of the F470 Valve should
be cleaned and then inspected for
wear and damage. Make certain that
the two 1/8 inch (3,2mm) diameter
pressure equalizing vents in the top of
the Clapper are open. Special consid-
eration should be given to the condi-
tion of the Diaphragm and the Clapper
Facing. The Diaphragm and/or Clap-
per Facing should be replaced if there
are any signs of deterioration due to
age or chemicals in the water.
NOTE
If the water supply contains chemi-
cals which tend to attack an EPDM
type rubber or the five year inspection
indicates a build-up of debris within
the valve which could affect its proper
operation, then the frequency of the
internal valve inspection procedure
should be increased as appropriate.
Worn or damaged parts must be re-
placed and the F470 Valve must be
reassembled in accordance with Fig-
ure B. The Cap Screws securing the
Diaphragm and Handhole Covers
should be uniformly tightened using a
cross-draw sequence.
Quarterly Solenoid Valve Test Pro-
cedure For Electric Actuation
Proper operation of the Solenoid Valve
for electric actuation should beverified
at least quarterly as follows:
1. Close the Main Control Valve.
2. Open the Main Drain Valve.
3. Test the automatic control unit (del-
uge releasing panel) in accordance
FIGURE G-3
DELUGE VALVE SYSTEM SCHEMATIC
— ELECTRIC ACTUATION—
-13-
OBSOLETE

with the manufacturer’s instructions
to energize the solenoid valve.
4. Verify that the flow of water from the
Solenoid Valve drain connection in-
creases to a full flow.
5. Verify that the Diaphragm Chamber
pressure has decreased to below
25% of the water supply pressure.
6. Reset the electric detection system
in accordance with the manufac-
turer’s instructions to de-energize
the solenoid valve. Check the Sole-
noid Valve drain for leaks.Any leaks
must be corrected before proceed-
ing to the next step.
7. Slowly open the Main Control Valve.
Close the Main Drain Valve as soon
as water discharges from the drain
connection. Observe the Automatic
Drain Valve for leaks. If there are
leaks, determine/correct the cause
of the leakage problem. If there are
no leaks, the F470 Valve is ready to
be placed in service and the Main
Control Valve must then be fully
opened.
Quarterly Dry Pilot Actuator Test
Procedure For Dry Pilot Actuation
Proper operation of the Dry Pilot Ac-
tuator for dry pilot actuation should be
verified at least quarterly as follows:
1. Close the Main Control Valve.
2. Open the Main Drain Valve.
3. Open the Inspector’s Test Connec-
tion on the Dry Pilot Line.
4. Verify that the flow of water from the
Dry Pilot Actuator drain connection
increases to a full flow.
5. Verify that the Diaphragm Chamber
pressure has decreased to below
25% of the water supply pressure.
6. Close the Inspector’s Test Connec-
tion and allow the dry pilot line pres-
sure to re-establish. Check the Dry
Pilot Actuator drain for leaks. Any
leaks must be corrected before pro-
ceeding to the next step.
7. Slowly open the Main Control Valve.
Close the Main Drain Valve as soon
as water discharges from the drain
connection. Observe the Automatic
Drain Valve for leaks. If there are
leaks, determine/correct the cause
of the leakage problem. If there are
no leaks, the F470 Valve is ready to
be placed in service and the Main
Control Ave must then be fully
opened.
Quarterly Waterflow Alarm Test
Procedure
Testingof the system waterflowalarms
should be performed quarterly.To test
the waterflow alarm, open the Alarm
Test Valve, which will allow a flow of
water to the Pressure Alarm Switch
and/or Water Motor Alarm.Upon satis-
factory completion of the test, close
the Alarm Test Valve.
Quarterly Low Pressure Alarm Test
Procedure And Condensate Drain
Procedure For Dry Pilot Actuation
For Dry Pilot Actuation, testing of the
Low Pressure Alarm Switch and drain-
age of the pilot line condensate should
be performed quarterly as follows.
1. ClosetheDiaphragmChamberSup-
ply Control Valve.
2. Close the Main Control Valve.
3. Open the Main Drain Valve.
4. Drain the dry pilot line condensate
as follows.
a. Close the Gauge Test Valve lo-
cated below the Dry Pilot Line
Pressure Gauge.
b. Remove the 1/4" Plug from the
Gauge Test Valve.
c. Crack Open the Gauge Test
Valve and allow all conden-
sate, if any, to drain out.
d. Close the Gauge Test Valve,
replace the Plug, and then
open the Gauge Test Valve.
5. Open the Inspector’s Test Connec-
tion, and slowly relieve pneumatic
pressure. Verify that the Low pres-
sureAlarmSwitchisoperationaland
that the low pressure set points are
as follows:
• Low pressure alarm setting at
approximately 6 psi (0,4 bar)
below the minimum pilot line
service pressure requirement
shown in Graph C.
• Fire alarm setting at approxi-
mately 15 psi (1,0 bar) below
the minimum pilot line service
pressure requirement shown
in Graph C.
6. Close the Inspector’s Test Connec-
tion, and allow the Dry Pilot Line to
automatically repressurize.
7. Open the DiaphragmChamber Sup-
ply Control Valve.
8. Slowly open the Main Control Valve.
Close the Main Drain Valve as soon
as water discharges from the drain
connection. Observe the Automatic
Drain Valve for leaks. If there are
leaks, determine/correct the cause
of the leakage problem. If there are
no leaks, fully open the Main Control
Valve.
WARRANTY
Seller warrants for aperiod of oneyear
from the date of shipment (warranty
period) that the products furnished
hereunder will be free from defects in
material and workmanship.
For further details on Warranty, see
Price List.
ORDERING PROCEDURE
All orders for Model F470 Multimatic
Deluge Valves, trim, accessories, and
replacement parts must include the
description and Product Symbol
Number (PSN), where applicable.
Valves:
Unless otherwise specified, the F470
Valves will be provided with ANSI
flange drilling.
Specify:(specify size) Model F470 Ex-
ternal Resetting Multimatic Deluge
Valve with (specify abbreviation — re-
fer to Table A, Page 2) flange drilling,
PSN (specify).
ANSI
4" (100 mm). . . . . . . . . . . . . . PSN 52-470-1-013
6" (150 mm). . . . . . . . . . . . . . PSN 52-470-1-015
ISO
4" (100 mm). . . . . . . . . . . . . . PSN 52-470-4-113
6" (150 mm). . . . . . . . . . . . . . PSN 52-470-4-115
AS
4" (100 mm). . . . . . . . . . . . . . PSN 52-470-4-313
6" (150 mm). . . . . . . . . . . . . . PSN 52-470-4-315
JIS
4" (100 mm). . . . . . . . . . . . . . PSN 52-470-4-713
6" (150 mm). . . . . . . . . . . . . . PSN 52-470-4-715
Trim:
Unless otherwise specified, all trim ar-
rangements are provided factory as-
sembled as shown in Figure F-2. Un-
assembled trim packages as shown in
Figure F-1 can be provided on “special
order”. Product Symbol Numbers
(PSN) need not be specified when or-
dering unassembled trim.
-14-
OBSOLETE

“Standard Order”
Factory Assembled Black Trim:
Specify: Factory assembled black
(specify type trim) for use with the
Model F470 Multimatic External Re-
setting Deluge Valve, PSN (specify).
Wet Pilot Actuation
Trim. . . . . . . . . . . . . . . . . . . PSN 52-470-1-101
Dry Pilot Actuation
Trim. . . . . . . . . . . . . . . . . . . PSN 52-470-1-102
Electric Actuation
Trim With 24VDC
Solenoid Valve . . . . . . . . . . PSN 52-470-1-103
“Special Order”
Factory Assembled
Galvanized Trim:
Specify: Factory assembled galva-
nized (specify type trim) for use with
the Model F470 Multimatic External
Resetting Deluge Valve, PSN (spec-
ify).
Wet Pilot Actuation
Trim. . . . . . . . . . . . . . . . . . . PSN 52-470-2-101
Dry Pilot Actuation
Trim. . . . . . . . . . . . . . . . . . . PSN 52-470-2-102
Electric Actuation
Trim With 24VDC
Solenoid Valve . . . . . . . . . . PSN 52-470-2-103
“Special Order” Electric Actuation
Trim With Separately Ordered Sole-
noid Valve:
Specify: (Specify Factory assembled
or Unassembled), (specify black or
galvanized) Electric Actuation Trim
With Separately Ordered Solenoid
Valve for use with the Model F470Mul-
timatic External Resetting Deluge
Valve.
Whenordering“ElectricActuationTrim
With Separately Ordered Solenoid
Valve”, refer to Technical Data Sheet
TD119 for information on separately
ordered, UL Listed Solenoid Valves
that may be suitable for use in hazard-
ous locations or that have voltage rat-
ings other than 24VDC.
NOTE
Factory Mutual Approval for electric
actuation of the F470 Valve is contin-
gent on the use of the FM Approved
24VDC Solenoid Valve provided with
the “Standard Order” Electric Actua-
tion Trim, PSN 52-470-1-103 or PSN
52-470-2-103.
Accessories:
Refer to the following Technical Data
Sheets (TD), as applicable.
PressureAlarmSwitch........ TD213
Low Pressure Alarm Switch . . . . TD210
Model F324 Air Maintenance
Device................... TD111
Model F326 Air Maintenance
Device................... TD112
Model F328 Nitrogen Maintenance
Device................... TD113
DesiccantDryer............. TD135
Model F180 or F184
Manual Control Stations . . . . . TD121
Valve Replacement Parts Kit:
The Valve Replacement Parts Kit con-
tains a Clapper Facing, Diaphragm,
and Handhole Cover Gasket. It is rec-
ommended to have these parts readily
available when servicing the Model
F470 Multimatic Deluge Valve.
Specify: Valve Replacement Parts Kit
for use with (specify size) inch Model
F470 Multimatic External Resetting
Deluge Valve.
4" (100 mm) . . . . . . . . . . . . . . PSN 92-470-1-101
6" (150 mm) . . . . . . . . . . . . . . PSN 92-470-1-102
Replacement Valve Parts (Fig. B):
Specify: (description) for use with
(specify size) Model F470 Multimatic
External Resetting Deluge Valve, PSN
(specify).
4 inch (100 mm) Valve
2 - Clapper. . . . . . . . . . . . . . . PSN 92-470-1-006
3 - Clapper Facing. . . . . . . . . PSN 92-470-1-009
4 - Clapper Facing
Retainer . . . . . . . . . . . . PSN 92-470-1-004
5 - Clapper Bolt . . . . . . . . . . . PSN 62-634-1-112
7 - Clapper Latch. . . . . . . . . . PSN 92-470-1-005
8 - O-Ring . . . . . . . . . . . . . . . PSN 62-578-1-306
9 - Reset Bushing . . . . . . . . . PSN 92-470-1-052
10 - O-Ring . . . . . . . . . . . . . . PSN 62-578-1-307
11 - Reset Plunger. . . . . . . . . PSN 92-470-1-053
12 - Reset Knob. . . . . . . . . . . PSN 62-470-1-001
13 - Diaphragm
Cover Bolt. . . . . . . . . . . PSN 62-039-1-207
14 - Diaphragm
Retainer . . . . . . . . . . . . PSN 92-470-1-049
15 - Flange & Push
Rod Assembly . . . . . . . PSN 92-470-1-040
16 - Diaphragm . . . . . . . . . . . PSN 92-470-1-031
17 - Diaphragm
Cover . . . . . . . . . . . . . . PSN 92-470-1-029
20 - Clapper Hinge
Pin. . . . . . . . . . . . . . . . . PSN 92-470-1-038
21 - Latch Hinge Pin . . . . . . . PSN 92-470-1-023
22 - Handhole Cover. . . . . . . PSN 92-470-1-002
23 - Handhole
Cover Gasket . . . . . . . . PSN 92-470-1-008
24 - Handhole
Cover Bolt. . . . . . . . . . . PSN 62-039-1-208
- Flurosilicone
Grease
1.5 grams . . . . . . . . . . . PSN 92-302-1-641
57 grams . . . . . . . . . . . PSN 92-302-1-642
6 inch (150 mm) Valve
2 - Clapper. . . . . . . . . . . . . . . PSN 92-470-1-025
3 - Clapper Facing. . . . . . . . . PSN 92-470-1-032
4 - Clapper Facing
Retainer . . . . . . . . . . . . PSN 92-470-1-026
5 - Clapper Bolt . . . . . . . . . . . PSN 62-634-1-113
7 - Clapper Latch. . . . . . . . . . PSN 92-470-1-030
8 - O-Ring . . . . . . . . . . . . . . . PSN 62-578-1-306
9 - Reset Bushing . . . . . . . . . PSN 92-470-1-052
10 - O-Ring . . . . . . . . . . . . . . PSN 62-578-1-307
11 - Reset Plunger. . . . . . . . . PSN 92-470-1-053
12-ResetKnob...........PSN62-470-1-001
13 - Diaphragm
CoverBolt ...........PSN62-039-1-207
14 - Diaphragm
Retainer . . . . . . . . . . ...PSN92-470-1-049
15 - Flange & Push
RodAssembly........PSN92-470-1-040
16 - Diaphragm. . . . . . . . . ...PSN92-470-1-031
17 - Diaphragm
Cover...............PSN92-470-1-029
20 - Clapper Hinge
Pin.................PSN92-470-1-039
21-LatchHingePin........PSN92-470-1-023
22 - Handhole Cover . . . . ...PSN92-470-1-021
23 - Handhole
CoverGasket.........PSN92-470-1-033
24 - Handhole
CoverBolt ...........PSN62-634-1-407
- Flurosilicone
Grease
1.5grams............PSN92-302-1-641
57grams............PSN92-302-1-642
Replacement Trim Parts (Fig. F):
Specify: (description) for use with
Model F470 External Resetting Multi-
matic Deluge Valve, PSN (specify).
1 - 300 lb. Water
Pressure
Gauge . . . . . . . . . . . ...PSN92-343-1-005
2 - 1/4" Gauge Test
Valve ...............PSN46-005-1-002
3 - F180 Manual
Control Station. . . . . ...PSN52-289-1-001
4-2"AngleValve..........PSN46-048-1-009
5-1/2"BallValve..........PSN46-050-1-004
6 - 1/2" Swing
CheckValve..........PSN46-049-1-004
7 - 1/2" Spring
Loaded Check
Valve ...............PSN92-322-1-002
8 - Priming Supply
Restriction...........PSN92-020-1-009
9-1/2"Y-Strainer..........PSN52-353-1-005
10 - F793 Automat-
icDrainValve ........PSN52-793-1-004
11 - Drip Funnel
Support Plug . . . . . . ...PSN92-211-1-005
12 - Drip Funnel
Support . . . . . . . . . . ...PSN92-211-1-003
13 - Drip Funnel . . . . . . . . ...PSN92-343-1-007
14 - 3/32" Vent
Fitting...............PSN92-032-1-002
15 - 1/2" Angle
Valve ...............PSN46-048-1-004
D1 - B-1 Dry Pilot
Actuator . . . . . . . . . . ...PSN52-280-1-001
D2 - 250 lb. Air
Pressure
Gauge . . . . . . . . . . . ...PSN92-343-1-012
D3 - 1/4" Gauge
TestValve...........PSN46-005-1-002
D4 - 1/2" Globe
Valve ...............PSN46-047-1-004
D5 - 1/4" Pressure
ReliefValve..........PSN92-343-1-020
E5 - 24VDC Sole-
noidValve ...........PSN52-287-1-024
WEIGHTS
The following are the nominal weights for
the valves and trim:
4" Model F470 Multimatic
DelugeValve.............. 77lbs.(35kg)
6" Model F470 Multimatic
DelugeValve.............. 111lbs.(49kg)
WetPilotActuationTrim ....... 28lbs.(13kg)
DryPilotActuationTrim........ 41lbs.(18kg)
Electric Actuation Trim
With 24VDC Solenoid Valve . . 33 lbs. (15 kg)
-15-
OBSOLETE

® Reg.trademark of GRINNELL CORPORATION, 3 TYCO PARK, EXETER, NH 03833
OBSOLETE
Other manuals for F470
1
Table of contents
Other Grinnell Control Unit manuals
Popular Control Unit manuals by other brands

ADEMCO
ADEMCO TeleSmart Installation and setup guide
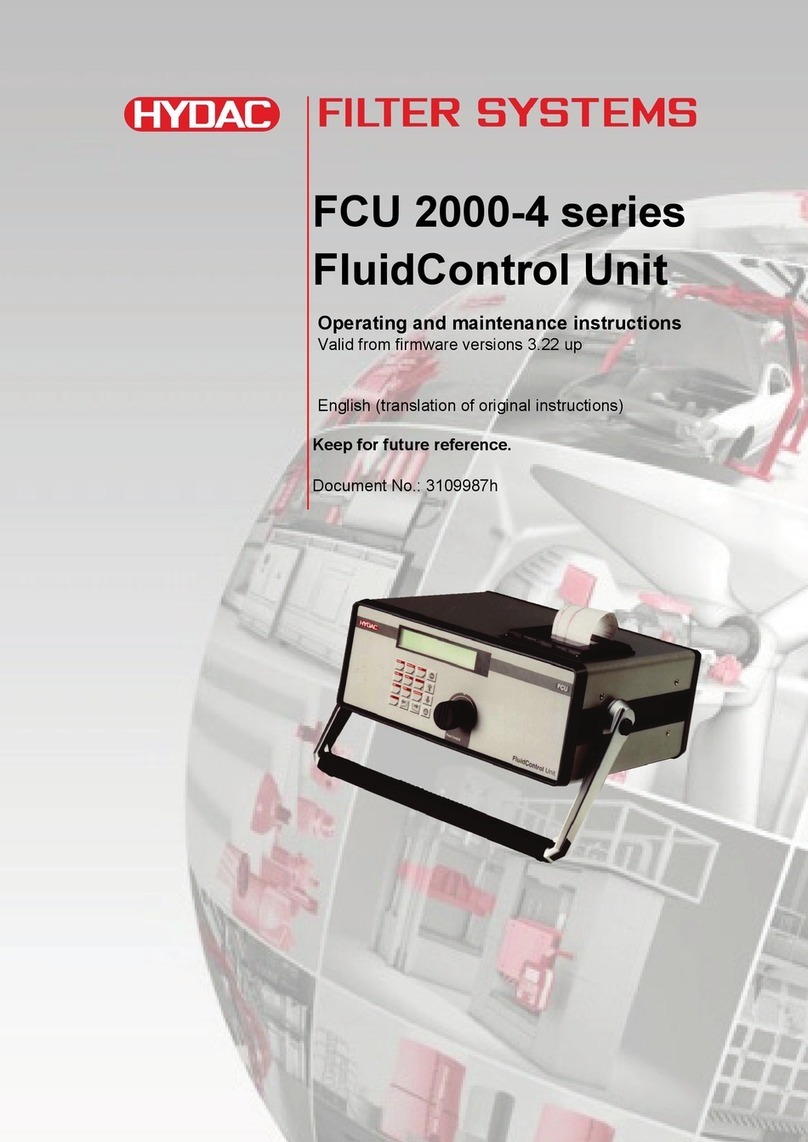
HYDAC FILTER SYSTEMS
HYDAC FILTER SYSTEMS FCU 2000-4 Series Operating and maintenance instructions
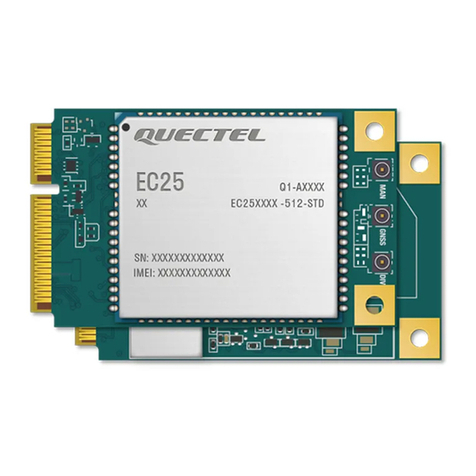
Quectel
Quectel EC25 series Hardware design
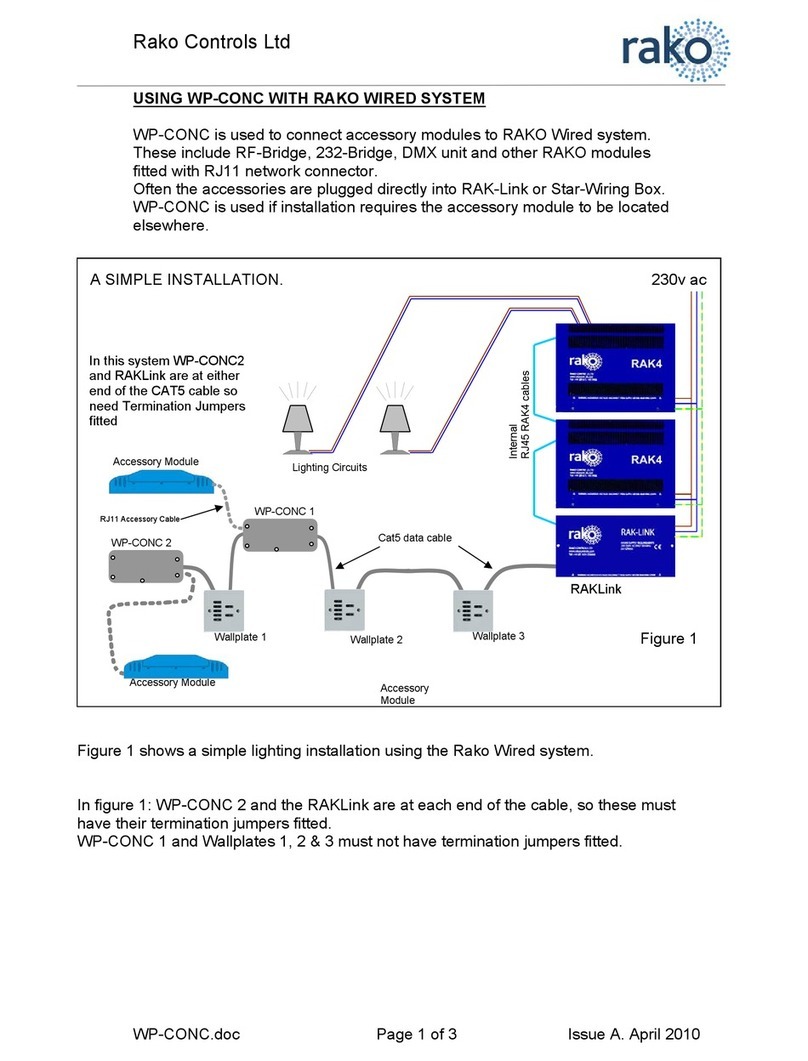
rako
rako WP-CONC manual
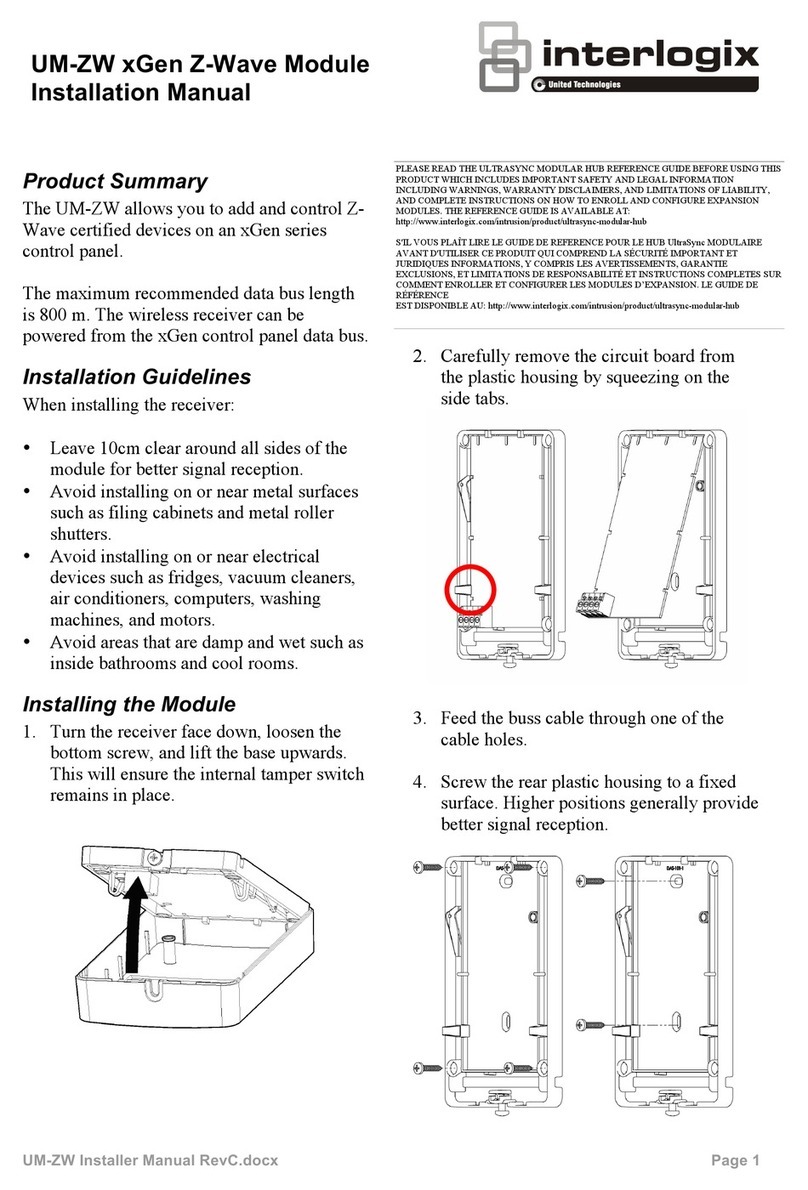
Interlogix
Interlogix UM-ZW installation manual
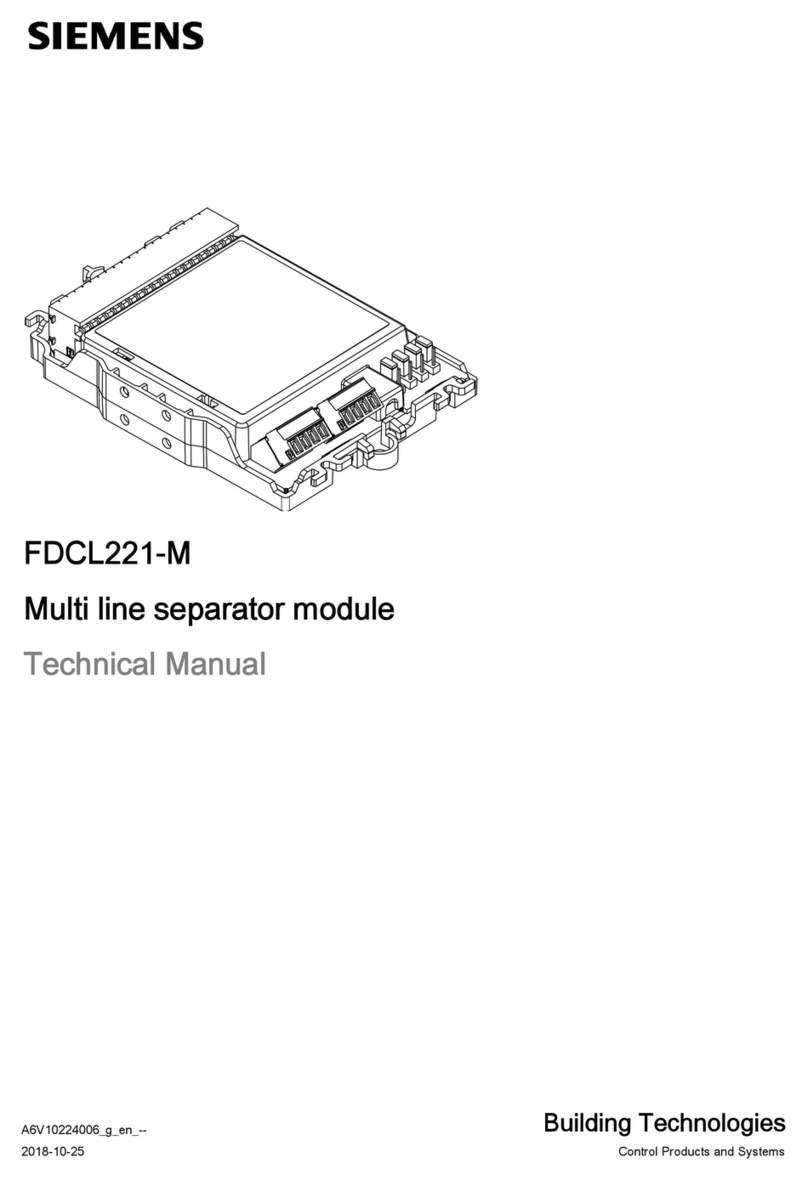
Siemens
Siemens FDCL221-M Technical manual