Grinnell F470 User manual

PREACTION SYSTEM, DOUBLE INTERLOCK
ELECTRIC/PNEUMATIC RELEASE
MODEL F470 - 4 and 6 INCH (100 and 150 mm)
m /f -7 fxjp
- 2 FEET
II (600mm)
MINIMUM
..
cr”
0
I- Model F470 External Resetting
Multimatic Deluge Valve
2- Model F52O/F5201Swing Check
Valve
3- System Main Control Valve
(supervised in open position)
4- System Shut-Off Valve
(supervised in open position)
5 Solenoid Valve
6- Dry Pilot Actuator
7- Low Air Pressure Alam, Switch
8- Waterflow Pressure Alam Switch
Q- Manual Control Station
lo- Automatic Air/Nitrogen Pressure
Maintenance Device
13- Manual Pull Station (as required)
14- Alarm Bell
15 Heat Detectors (or other fire
detection devices)
16- Automatic Sprinklers
17- Water Supply Pressure Gauge
18- System Air Pressure Gauge
lQ- Diaphragm Chamber Pressure
Gauge
A- Power Supply To Panel
B- Audible Alarm Circuit
C- Fire Detection Initiating Circuit
D- Waterflow Alarm Initiating Circuit
E- Supervisory Alarm Initiating Circuit
F- Releasing Circuit
- .- FIGURE A
MODEL F470 ELECTRIC/PNEUMATIC
DOUBLE INTERLOCK PREACTION SYSTEM
- SCHEMATIC OF TYPICAL ARRANGEMENT-
1l- Water Motor Alarm (optional)
12- Deluge Valve Releasing Panel
with Battery Back-Up
G- Manual Pull Initiating Circuit
The 4 and 6 inch (100 and 150 mm)
Model F470 Electric/Pneumatic Dou-
ble interlock Preaction Systems (Ref.
Figure A) are designed for use in ap-
plications, such as refrigerated areas,
requiring the maximum degree of pro-
tection .against inadvertent flooding of
the sprinkler system piping.
The F470 Electric/Pneumatic Double
Interlock Preaction System utilizes a
Model F470 External Resetting Multi-
mati& Deluge Valve and a Model
F520 or F5201 Swing Check Valve,
with releasing trim consisting of both a
Solenoid Valve and a Dry Pilot Actua-
tor in a series configuration. The Swing
Check Valve isolates the Deluge Valve
from the system air pressure, which
holds the Dry Pilot Actuator closed.
The Solenoid Valve remains closed
until it is electrically energized by a
deluge valve releasing panel (auto-
matic control unit) that is operated by
either a fire detection device or manual
pull station.
In order for the Double Interlock Pre-
action System to automatically actu-
ate, two independent events must
occur. The deluge valve releasing
Printed in U.S.A. 1-96 TD1151
OBSOLETE

Left Side Front
NOTES:
(a.) f$gmncferance, additional 2’ (50 mm) is
(b.) Add Q”(230mm) for optional F470 Double
Interlock Accelerator Trim.
Dim
A’
:
4 INCH SYSTEM
Inches (mm)
23.25 ;:;A;7.00
12.00 (305)
Dim
A’
:
6 INCH SYSTEM
Inches (mm)
26.25
5.25 :Fz;
12.00
FIGURE B E 8.69 g; ED 8.69
14.56 I;::;
15.44
INSTALLATION CONFIGURATION F 13.89 (348) F 14.50
AND CLEARANCE DIMENSIONS l F520 or F5201 l F520 or F5201
panel must operate and open the So-
lenoid Valve upon automatic operation
of the electric fire detection initiating
circuit or manual operation of the elec-
tric-manual pull initiating circuit, and
the sprinkler system piping must lose
air pressure due to operation of one or
more sprinklers.
The Double Interlock Preaction Sys-
tem will automatically actuate only
when both the Dry Pilot Actuator and
the Solenoid Valve are open at the
same time. Accidental opening of just
the Dry Pilot Actuator (for example: a
lift truck accidentally dislodges a
sprinkler), or just energizing the Sole-
noid Valve (for example: an accidental
operation of an electric pull station),
will only cause an alarm, and will not
actuate the system or flood the sprink-
ler system piping.
Both the 4 and 6 inch (100 and 150
mm) F470 Double Interlock Preaction
Systems may be equipped, as an op-
tion, with the Model F311 Accelerator.
In the case of the F470 Double Inter-
lock Preaction System, the F311 oper-
ates as a quick opening device for the
Dry Pilot Actuator and provides a re-
duction in the time to open it, following
the operation of one or more automatic
sprinklers.
The 4 and 6 inch (100 and 150 mm)
Model F470 Electric/Pneumatic Dou-
ble Interlock Preaction Systems are
listed by Underwriters Laboratories
Inc. and Underwriters’ Laboratories of
Canada as Double Interlock Type
Water Control Valves, and they are
approved by Factory Mutual Research
Corporation as Refrigerated Area Sys-
tems for use in refrigerated rooms or
buildings.
WARNZNG
The 4 and 6 inch Model F470 Double
Interlock Preaction Systems with the
-2-
OBSOLETE

associated trim described herein must
be installed and maintained in com-
pliance with this document, as well as
with the applicable standards of the
National Fire Protection Association,
in addition to the standards of any
other Authorities Having Jurisdic-
tion. Failure to do so may impair the
integrity of the associated devices.
The owner is responsible for main-
taining their fire protection system
and devices in proper operating con-
dition. The installing contractor or
manufacturer should be contacted rel-
ative to any questions.
The 4 and 6 inch (100 and 150 mm)
Model F470 Electric/Pneumatic Dou-
ble Interlock Preaction Systems, as
well as their associated trim, are rated
for use at a minimum service pressure
of 20 psi (1,4 bar) and a maximum
service pressure of 175 psi (12,l bar).
The following is a list of the Technical
Data Sheets for the valves and de-
vices which are required as part of the
Double Interlock Preaction System:
Deluge Valve . . . . . . . . TD116
Swing Check Valve . . . . TD320
Dry Pilot Actuator . . . . . TDl17W
Solenoid Valve . . . . . . . TD119
Manual Control Station . . TD121
Water-flow Pressure Alarm
Switch . . . . . . . . . . . TD213
Low Air Pressure Alarm
Switch . . . . . . . . . . . TD232
The following is a list of the Technical
Data Sheets for additional items which
may be considered for use with the
Double Interlock Preaction System:
Accelerator . . . . . . . . . TD109
System Pressure Maintenance De-
vice (select one)
-Air Pressure Reducing Type
. . . . . . . . . . . . . . TDlll
-Air Compressor Control Type
. . . . . . . . . . . . . . TD112
-Nitrogen Press. Reducing Type
. . . . . . . . . . . . . . TD113
Water Motor Alarm . . . . . TD250
System Design Considerations
The .automatic sprinklers, as well as
the deluge valve releasing panel (au-
tomatic control unit), fire detection de-
vices, manual pull stations, and signal-
ing devices, which are utilized with the
Double Interlock Preaction System
must be UL Listed, ULC Listed, C-UL
Listed, or FM Approved, as applicable.
Because a double interlock preaction
system requires time for a drop in sys-
tem air pressure to occur (in addition
to responding to a separate heat de-
tection system), before it will allow
water to enter the system piping, this
system has characteristics similar to a
dry pipe sprinkler system. Therefore,
the system design considerations for a
dry pipe system are normally applied
to a double interlock preaction system
- including a 30% increase in design
area; quick opening devices for sys-
tem capacities of 500 gallons (1890
litres) or more; a maximum 1 minute
water delivery time for system capaci-
ties of 750 gallon (2850 litres) or more;
and, prohibition of gridded system pip-
ing.
The deluge valve, swing check valve,
and all interconnecting piping must be
located in a readily visible and acces-
sible location and in an area which can
be maintained at a minimum tempera-
ture of 4O’F/4’C.
NOTE
Heat tracing is not permitted for the
deluge valve, swing check valve, or
any of the interconnecting piping.
Heat tracing can promote the forma-
tion of hardened mineral deposits
which can prevent system operation.
Heat tracing can also result in dam-
age to the F470 Deluge Valve Dia-
phragm Assembly.
In planning the installation, consider-
ation must also be given to the dis-
posal of the large quantities of water
which may be associated with draining
the system or performing a flow test.
Installation configuration and clear-
ance dimensions are given in Figure B.
The flanged inlet and outlet connec-
tions are faced and drilled per ANSI
Standard 816.1. The grooved outlet
connection of the F5201 Swing Check
Valve is cut in accordance with
Gruvlok standard .groove specifica-
tions for steel pipe, and they are suit-
able for use with grooved end pipe
couplings that are listed or approved
for fire protection service.
In order to readily perform the System
Inspection Procedure described in the
Care and Maintenance section, it is
recommended that a System Shut-Off
Valve be installed above the Model
F52O/F5201 Swing Check Valve, as
shown in Figure A. The System Shut-
Off Valve should be a listed or ap-
proved (as appropriate) indicating
valve with a supervisory switch to mon-
itor the normally open position.
-3-
System Air Pressure Requirements
Graph B shows the minimum Elec-
tric/Pneumatic Double Interlock Pre-
action System air pressure require-
ment as a function of the water supply
pressure. Use of an automatic air or
nitrogen maintenance device is recom-
mended and may be required by the
Authority Having Jurisdiction.
NOTE
The dew point of the air or nitrogen
must be maintained below the lowest
ambient temperature to which the
Double Interlock Preaction System
piping will be exposed, or as required
by the Authority Having Jurisdiction.
Accumulation of water in the connec-
tion to the Dry Pilot Actuator will
lower the air pressure at which the
Dry Pilot Actuator will open and pos-
sibly prevent proper operation. Also,
introduction of moisture into the sys-
tem piping that is exposed to freezing
temperatures can create ice build up
which could prevent proper operation
of the system.
Friction Loss
The nominal pressure losses versus
flow rate for the 4 and 6 inch (100 and
150 mm) combinations of the Model
F470 Multimatic Valve with either the
Model F520 or F5201 Swing Check
Valve are shown in Graphs A-l and
A-2.
The approximate friction losses, based
on the Hazen and Williams formula
and expressed in equivalent length of
Schedule 40 pipe, are given below for
each size deluge and swing check
valve combination. The equivalent
length of pipe has been calculated on
the basis of the flow rates typically
used with each size system.
SIZE OF c = 100 CM20
VALVES FT. OF PIPE FT. OF PIPE
4” 18.2 25.5
6’ 26.4 36.9
Valve Trim
The F470 Electric/Pneumatic Double
Interlock Preaction Trim, illustrated in
Figure C, is designed to be used in
addition to the (Wet Pilot) Actuation
Trim shown in Figure D. The combina-
tion of these two trim arrangements
forms the complete double interlock
preaction trim arrangement. Figure C
also illustrates the optional Double In-
terlock Accelerator Trim complete with
Model F311 Accelerator. All of the trim
arrangements are designed for use
with either the 4 or 6 inch (100 or 150
mm) valve arrangements.
Fire Department Connection
When installing a fire department con-
nection per NFPA 13 for preaction sys-
tems, a tee fitting (to accomodate the
supply from the fire department con-
nection) will be required between the
OBSOLETE

300 400 500 700 1000 2000 3000
FLOW RATE IN U.S. GALLONS PER MINUTE (GPM)
100 2000 3000 5000 7000 10000
FLOW RATE IN LITRES PER MINUTE (LPM)
GRAPH A-l
GRAPHS A-l and A-2
GRAPH A-2
NOMINAL PRESSURE LOSS VERSUS FLOW
FOR THE MODEL F470 DOUBLE INTERLOCK PREACTION SYSTEM
(DELUGE VALVE AND CHECK VALVE COMBINATION)
F470 Deluge Valve and the
F52OIF5201 Swing Check Valve. To
facilitate the increased elevation of the
F52O/F5201 Swing Check Valve, the
nipple below the Solenoid Valve (9-
Fig. C) may be increased in length
accordingly.
NOTE
Do not increase the length of the nip-
ple between the Solenoid Valve and
Dry Pilot Actuator or the nipple above
the Dry Pilot Actuator. Increasing ei-
ther of these two nipple lengths may
impair operation of the system.
As indicated in the General Descrip-
tion section, two independent events
resulting in opening of both the Dry
Pilot Actuator and the Solenoid Valve
must occur to actuate the Model F470
Electric/Pneumatic Double Interlock
Preaction System.
When the Double Interlock Preaction
System is set for service, the dia-
phragm chamber of the Model F470
Deluge Valve is pressurized through
the diaphragm chamber supply con-
nection (Fig. D). The Model F470 Del-
uge Valve is a differential type valve
which depends upon the water pres-
sure in the diaphragm chamber to hold
the clapper closed against the water
supply pressure. The Model F470 Del-
uge Valve has a nominal trip ratio of
2.5 to 1, i.e., the valve operates when
pressure in the diaphragm chamber is
reduced to approximately two-fifths of
the water supply pressure.
The Model F470 External Resetting
Deluge Valve is described in TD116.
Opening of both the Dry Pilot Actuator
and the Solenoid Valve (8 & 9 - Fig. C),
or operating the Manual Control Sta-
tion (3 - Fig. D) will release water from
the Multimatic Valve diaphragm cham-
ber faster than it can be replenished
through the l/8 inch (3,2 mm) diameter
orifice of the Priming Supply Restric-
tion (8 - Fig. D). A rapid pressure drop
then results in the diaphragm chamber
-4-
and the differential between the dia-
phragm chamber and waterway is
eliminated. The water supply pressure
then forces the waterway clapper
open, permitting a flow of water to the
Double Interlock Preaction System
piping. Water flowing into the system
also flows through the normally open
Alarm Control Valve (Fig. D) to the
Waterflow Pressure Alarm Switch (Fig.
C), which actuates the system alarm
signal.
The Double Interlock Preaction Sys-
tem will automatically operate only
when both the Solenoid Valve and the
Dry Pilot Actuator are open at the
same time. Opening of just the Dry
Pilot Actuator (e.g., a lift truck acciden-
tally dislodges a sprinkler) or just ener-
gizing the Solenoid Valve (e.g., an ac-
cidental operation of an electric pull
station) will only cause an alarm, via
the low air pressure alarm switch orthe
deluge valve releasing panel, as appli-
cable, to indicate that the system re-
quires attention. The system will not
actuate or flood the sprinkler system
piping.
As an option, the 4 and 6 inch (100 and
150 mm) Double Interlock Preaction
Systems may be equipped with a
Model F311 Accelerator (Fig. C) forthe
purpose of obtaining a reduction in the
time for the Dry Pilot Actuator to open
following the operation of one or more
automatic sprinklers.
With the optional Double Interlock Ac-
celerator Trim, the communication be-
OBSOLETE

WATER SUPPLY PRESSURE IN PSI
GRAPH B
DOUBLE INTERLOCK PREACTION SYSTEM
AIR PRESSURE REQUIREMENTS
tween the system air pressure and the
Dry Pilot Actuator is made directly
through the Accelerator Trim. The
F311 Accelerator automatically ad-
justs to small as well as slow changes
in system pressure, but trips when
there is a rapid and steady drop in
pressure (such as will occur when a
sprinkler operates). Upon tripping, the
F311 Accelerator will relieve system
air pressure from the Dry Pilot Actuator
faster than it can be replenished
through the 3/32 inch (2,4 mm) diame-
ter orifice in the clapper of the l/2 inch
(15 mm) Swing Check Valve (E - Fig.
C), resulting in quick opening of the
Dry Pilot Actuator following a sprinkler
operation.
The Model F311 Accelerator is de-
scribed in Technical Data Sheet
TD109.
The deluge valve, swing check valve,
and all interconnecting piping must be
installed in a readily visible and acces-
sible location and in an area which can
be maintained at a minimum tempera-
ture of 4O’F/4’C.
NOTE
Heat tracing is not permitted for the
deluge valve, swing check valve, or
any of the interconnecting piping.
Heat tracing will promote the forma-
tion of hardened mineral deposits
which can prevent valve operation.
Heat tracing can also result in dam-
age to the F470 Deluge Valve Dia-
phragm Assembly.
The 4 and 6 inch (100 and 150 mm)
Electric/Pneumatic Double Interlock
Preaction Systems must be installed in
accordance with the following instruc-
tions. Proper operation of the Double
Interlock Preaction System depends
upon it being installed in accordance
with the instructions given below. Fail-
ure to follow these instructions may
prevent the devices from functioning
properly as well as void listings, ap-
provals, and the manufacturer’s war-
ranties.
1. All pipe thread connections must
be free of scale and burrs before
installation. Use pipe thread seal-
ant sparingly on male pipe threads
only.
2. The F470 Deluge Valve must be
installed vertically as shown in Fig-
ure B and C.
3. To attach the lower flange of the
F520 or F5201 Check Valve to the
upper flange of the F470 Deluge
Valve, as shown in Figure B, at
least four out of the eight required
flange fasteners must be stud bolts
and nuts. The stud bolts must be
5/8”-11 UNC x 3-l/4” long for4 inch
(100 mm) valves and 3/4”-10UNC
;a;;3f” long for 6 inch (150 mm)
4. Install the (Wet Pilot) Actuation
Trim as specifie.d by TDl16 and
then the Double Interlock Preac-
tion Trim as shown in Figure C.
Care must be taken to make sure
that check valves, globe valves,
etc. are installed with the flow ar-
rows in the proper direction.
Drain tubing to the Drip Funnel
must be installed with smooth
bends that will not restrict flow.
5. Attach the Model F470 Double In-
terlock Label (11 - Fig. C) to the 2
inch high x 4 inch (50 x 200 mm)
wide nameplate mounting pad on
-5-
the Handhole Cover of the
F52OIF5201 Swing Check Valve.
Place the Label over the man-
ufacturer’s logo nameplate, if one
is located on the pad.
6. The Diaphragm Chamber Supply
Connection (Fig. C) must be con-
nected to the water supply side of
the System Main Control Valve to
facilitate setting of the F470 Del-
uge Valve.
7. Connect the Air Supply Connec-
tion to an air or nitrogen supply.
Use of an automatic air or nitrogen
maintenance device is recom-
mended and may be required by
the Authority Having Jurisdiction.
Refer to Graph B for Double Inter-
lock Preaction System air pressure
requirements.
An air dryer, when specified, is to
be installed as required by the Au-
thority Having Jurisdiction.
8. Install, as applicable, the optional
Double Interlock Accelerator Trim
as shown in Figure C.
The drain tubing must be installed
with smooth bends that will not re-
strict flow.
The connection to the system pip-
ing must be located on the supply
side of the System Shut-off Valve
(Fig. A) and at least two feet above
the F52OIF5201 Check Valve, so
that drain back/condensate will not
flow into the Accelerator piping.
Connections to a feed or cross
main must be made either to the
side or top of the main.
After installing the F311 Accelera-
tor, close the Accelerator Control
Valve.
NOTES
Failure to follow the above in-
structions can result in accidental
tripping of the Accelerator.
The Accelerator Control Valve
must be closed during hydrostatic
testing of the system to prevent
internal damage to the F311 Ac-
celerator.
9. The Low Air Pressure Alarm
Switch (Fig. C) is to be adjusted to
operate on falling pressure at ap-
proximately 6 psi (0,4 bar) below
the minimum Double Interlock Dry
System air pressure requirement
shown on Graph B.
10. The Pressure Relief Valve (5 - Fig.
C) is factory set to relieve at a
pressure of approximately 45 psi
(3,l bar), which can typically be
used for a maximum system pres-
OBSOLETE

ACCELERATOR CONNECTION TO SYSTEM
REFER TO INSTALLATION STEP 8
E
/
ACCELERATOR CONTROL
P VALVE (NORMALLY OPEN)
A- Model F311 Ii- l/4’ Tube, 36’
Accelerator long (2 req’d)
B- 250 lb. Air J- l/2’ Plug
Pressure Gauge K- 112’x l/4’
c- 112’Y-Strainer Reducing Elbow
Q- l/2’ Globe Vatve L- l/2” x l/2’ x l/4’
E- 112’ Swing Check Tee
Valve WI 3l32’ M- I/2’ Tee
Orifice N- l/4’ x I’ Nipple
F- I/4’ Angle Valve P- 112’ x l-1/2’
G- l/4’ Tubing Nipple (5 req’d)
Connector Q- 112’ x 3’ Nipple
(2req’d)
Optional Accelerator Trim
- Bill of Materiaie-
I- 250 lb. Air Pressure
Gauge
2- l/4’ Gauge Test
Valve
3- Model PSIO-2A
Pressure Alarm Switch
4- Model PS40-1A
Pressure Alan Switch
5 l/4’ Pressure Relief
Valve
6- l/2’ Globe Valve
7- l/2” Swing Check Valve
9 Model B-l Dry Pilot
Actuator
9- 24 VDC Solenoid Valve
IO- T Angle Valve
ll- Label
12- l/2” Tubing Connector
13- l/2’ Tube, 36’ long
14- l/2’ Union
15 I/2’ 45’ Elbow
16- l/2’ 90’ Elbow (4 req’d)
17- l/2’ Tee (2 req’d)
19 l/2’ x l/2’ x l/4’ Tee
19- l/4’ Plug
20- l/C X 4’ Nipple
21- l/2” x close Nipple
22- l/2’ x l-1/2’ Nioole
(10 req’d) ”
23- l/2’ x 2’ Nipple
24- l/2’ x 5’ Nipple
for 4’ valves,
l/2’ x 5-l/2’ Nipple
for 6’ valves
25- l/2’ x 4-W’ Niwle
’ ’
26- 2’ x 2-112’
Nipple
Double interlock Preaction Trim
- Bill of Materiaie-
FIGURE C
4 AND 6 INCH DOUBLE INTERLOCK PREACTION TRIM & OPTIONAL ACCELERATOR TRIM
-6
OBSOLETE

I- 300 lb. Water
Pressure Gauge
(2req’d)
2- 114’ Gauge
Test Valve
3- Model Fli30
Manual Control
Station
4- 2’ Angle Vaive
5- l/2’ Ball Valve
(2 req’d)
6- l/2’ Swing Check
Valve
7- l/2’ Spring Loaded
Check Valve
6 Priming Supply
Restriction
9- I/2’ Y-Strainer
lo- Model F793
Automatic Drain
Valve
II- Drip Funnel
supporl Plug
12- Drip Funnel
Support
13- Drip Funnel
14- 3132’ Vent
Fitting
15- I/2’ Angle
Valve
16- I/4’ Tube,
30’ long
17- ll2’Tube
Connector
19 l/2’ Tube,
24’ long
19- l/4’ Plug
20- l/2’ Plug
21- 314” Plug
22- l/2’ Union
(5 w’d)
23- l/2’ 90’ Elbow
(3 req’d)
24- l/2’ Tee (6 req’d)
25- l/2’ x l/4’ x I/2” Tee
(3 req’d)
26- I/2’ x I/2’ x 3l4’ Tee
27- 2’ 90’ Elbow
29 l/2’ x1-112”
Nipple
(17 req’d)
29- l/2’ x 3’
Nipple
30- l/2” x 4” Nipple
31- I/2” x 5’ Nipple
(2req’d)
32- l/2’ x7-112
Nipple
33- II2 x 10-l/2”
Nipple for
4” valve,
l/2’ x 12’
Nipple for
6’ valve
34- l/4’ x 1-l/2
Nipple
35- 2 x 3
Nipple
(2req’d)
13
21
‘CTION \
26
ALARM CONTROL VALVE *
(NORMALLY OPEN) 26
25
ALARM TEST 16
LLY CLOSED)
‘DIAPHRAGM CHAMBER
PRESSURE GAUGE
TO DRIP FUNNE MANUAL CONTROL STATION
TO DRIP FUNNEL
DIAPHRAGM CHAMBER
SUPPLY CONTROL VALVE
(NORMALLY OPEN) 26
23
ul‘DIAPHRAGM CHAMBER
SUPPLY CONNECTION
FIGURE D
(Reference from TD116)
(WET PILOT) ACTUATION TRIM FOR MODEL F470 DELUGE VALVE
NOTES:
1. The nipples utilized in the trim arrangements shown in Figures C and D are Schedule 40 steel per ASTM A53 or Al35
and they are threaded per ANSI B1.20.1 The fittings are either malleable iron per ANSI 816.3 or cast iron per ANSI
816.4.
2. The trim arrangement shown in Figure D is factory assembled as shown in TD116.
3. “Standard order” trim is provided with black nipples and fittings: however, galvanized nipples and fittings are available
on “special order”.
-7-
OBSOLETE

11
12
A. Immediately verify whether or not
a fire situation is present. If a fire
condition does exist, notify the
local fire service and follow the
plan prescribed by the Authority
Having Jurisdiction.
B. If a fire condition does not exist:
1. Close the Diaphragm Chamber
Supply Control Valve (Fig. D).
2. Close the system’s Main Control
Valve (Fig. A).
3. Open the Main Drain Valve (Fig.
D) at the rear of the F470 Deluge
Valve.
4. If the system has been flooded,
open the System Main Drain
Valve at the side of the
F52O/F5201 Check Valve (Fig.
C), Inspector’s Test Connection,
and all auxiliary drains in the sys-
tem piping. Check to see that the
drainage water will not cause
damage or result in dangerous
conditions.
5. Notify the alarm monitoring sta-
tions (if applicable) as well as the
Authority Having Jurisdiction that
there is an impairment to the fire
protection system.
6. Determine if the false alarm was
caused by the electric fire detec-
tion system or a low air pressure
condition and then promptly cor-
rect the impairment and return the
fire protection system to service,
as soon as possible.
sure of 40 psi (2,8 bar). The Pres-
sure Relief Valve may be reset;
however, it must be be reset to
relieve at a pressure which is in
accordance with the requirements
of the Authority Havng Jurisdiction.
To reset the Pressure Relief Valve,
first loosen the jam nut and then
adjust the cap accordingly -
clockwise for a higher pressure
setting or counterclockwise for a
lower pressure setting. After verify-
ing the desired pressure setting,
tighten the jam nut.
Suitable provision must be made
for disposal of drain water. Drain-
age water must be directed such
that it will not cause damage or
result in dangerous conditions.
All conduit and electrical connec-
tions are to be made in accordance
with the requirements of the Au-
thority Having Jurisdiction and/or
the National Electrical Code.
The Double Interlock Preaction Sys-
tem will not automatically reset after an
operation. It must be manually reset
and it should be restored to service as
soon as possible.
NOTES
It is recommended that the individual
responsible for placing the Double Zn-
terlock Preaction System in service de-
velop a working understanding of the
system in general, prior to placing it
in operation. These instructions, as
well as individual instructions for the
deluge valve, swing check valve, dry
pilot actuator, solenoid valve, manual
control station, switches, accelerator
(if applicable), and pressure mainte-
nance device should be reviewed.
After placing a fire protection system
in service, notify the proper authori-
ties and advise those responsible for
monitoring proprietary and /or cen-
tral station alarms.
The procedure is as follows:
1. Close the Diaphragm Chamber
Supply Control Valve (Fig. D).
2. Operate (open) the Manual Control
Station (Fig. D) to assure that the
F470 Deluge Valve Diaphragm
Chamber is vented.
3. Close the Double Interlock System
Main Control Valve (Fig. A), Air
Supply Control Valve (Fig. C), and,
if applicable, the Accelerator Con-
trol Valve (Fig. C).
4. Open the System Main Drain Valve
(Fig. C), Main Drain Valve at the
rear of the F470 (Fig. D),
Inspector’s Test Connection, and
all auxiliary drains in the system
piping. Check to see that the drain-
age water will not cause damage
or result in dangerous conditions.
NOTE
Do not open the Inspector’s Test
Connection and auxiliary drains
if resetting after a system test; oth-
erwise, system airpressure will be
relieved unnecessarily.
Inspect for and clear all ice plugs,
where system piping has been ex-
posed to freezing conditions and
when there has been a flow of
water into the system.
Close the System Main Drain
Valve. Insoector’s Test Connec-
tion, and ail auxiliary drains in the
system piping. Leave the Main
Drain Valve at the rear of the F470
open.
Depress the plunger of the Auto-
-8-
matic Drain Valve (Fig. D), to verify
that it is open and that the F470
Deluge Valve has been completely
drained.
8. Clean out the Strainer (Fig. D) in
the connection to the F470 Deluge
Valve Diaphragm Chamber.
9. Push the F470 Reset Knob inward
to allow the Clapper to reseat.
Under normal circumstances, the
reseating of the Clapper can be
heard. However, after the system
inspection procedure, for example,
due to minimal flow through a par-
tially opened main control valve,
the Clapper may not have latched
fully open. In this case, the reseat-
ing sound of the Clapper will not be
heard.
10. Close the Manual Control Station
(Fig. D) by pushing the operating
lever up. Do not close the hinged
cover at this time.
Il. Open the Alarm Control Valve (Fig.
D), if it was closed to silence local
alarms.
It is recommended that the Alarm
Control Valve be wire sealed in the
open position with a No. 16 twisted
wire, the ends of which are se-
cured by a lead seal. The wire seal
should be looped through the hole
in the handle and tightly twisted
around the pipe nipple adjacent to
the handle.
12. Replace all damaged or operated
sprinklers. Replacement sprinklers
must be of the same type and tem-
;;;;rtre rating as those which op-
NOTE
In order to prevent the possibility
of a subsequent operation of an
overheated solder type sprinkler,
any solder type sprinklers which
were possibly exposed to a temper-
aturegreater than their maximum
rated ambient must also be re-
placed.
13. Service the air dryer, if applicable,
in accordance with the man-
ufacturer’s instructions.
14. Open (energize) the Solenoid
Valve by manually operating the
deluge valve releasing panel.
15. Open the Diaphragm Chamber
Supply Control Valve (Fig. D) and
allow water to discharge from the
Dry Pilot Actuator. Close the Dia-
phragm Chamber Supply Control
Valve when air is no longer present
in the discharge from the Dry Pilot
Actuator.
OBSOLETE

16. If resetting after a test, fully open
the System Shut-Off Valve (Fig. A),
if applicable.
17. Open the Air Supply Control Valve
(Fig. C) and pressurize the sprink-
ler system in accordance with
Graph B.
18. Return the Solenoid Valve to its
normally closed position by reset-
ting the automatic control unit.
19. Fully open the Diaphragm Cham-
ber Supply Valve (Fig. D) and allow
time for full pressure to build up in
the Diaphragm Chamber of the
Multimatic Valve.
20. Operate (open) the Manual Control
Station (Fig. D). SLOWLY close
the operating lever, by pushing it
up, after air is no longer present in
the discharge from the drain tub-
ing. Close the hinged cover and
insert a new break rod (PSN 92-
289-1-008) in the small hole
through the top of the enclosing
box.
21. Inspect the drain connections from
the Dry Pilot Actuator and Manual
Control Station for leaks. Leaks, if
any, must be corrected before the
system is restored to service.
22. Reset the F311 Accelerator (Fig.
C) as follows, if the system is so
equipped; otherwise, proceed to
Step 23.
a. Close the Accelerator Control
Valve.
b. Slowly remove the plug from the
Strainer at the Accelerator inlet to
relieve any inlet pressure. This
procedure will trip the Accelerator
if it is not already tripped.
c. Clean out the Strainer at the Ac-
celerator inlet.
NOTE
A clogged strainer can prevent
the Accelerator from properly
tripping the system.
d. Open the Accelerator Bleed-off
Valve (Fig. C) and blow any resid-
ual water in the connection to the
system piping out through the
tube to the Drip Funnel. Close the
Bleed-off Valve after water
ceases to drain.
e. Open the Accelerator Control
Valve one-quarter turn and blow
any residual water in the connec-
tion to the system piping out
through the Strainer.
f. Close the Accelerator Control
Valve and replace the Strainer
Plug.
g. Slowly remove the Vent Plug lo-
cated in the front of the Accelera-
tor Cover and bleed off any resid-
ual pressure in the Accelerator
Differential Chamber.
h. Unscrew (counter-clockwise rota-
tion) the knurled Reset Knob at
the front of the Accelerator until it
resists further turning. A click,
which is the sound of the Lever
snapping back into the set posi-
tion, should be heard. Screw the
Reset Knob back in until it is finger
tight.
i.
i.
Replace the Vent Plug.
Verify that the system pressure
has returned to normal.
k. Using a watch, note the time for
the pressure in the Differential
Chamber of the Accelerator to in-
crease to 10 psi, after the Accel-
erator Control Valve is opened.
The time should be within the
range of values indicated below,
for optimum performance of the
Accelerator.
System Air
Pressure,
PSI
20
25
30
40
50
60
Time to 10 psi, sec.
Min. Max.
40 160
29 116
23 92
15 60
12 48
9 36
NOTE
Zf the time to pressurize the Dif-
ferential Chamber of the F311
Accelerator is not within the
range of values given in the
above table or any other resetting
problem is encountered, the Ac-
celerator Control Valve should
be closed and corrective action
taken (refer to TD109).
I. When the air pressure in the Dif-
ferential Chamber of the Acceler-
ator is equal to that in the system,
the Accelerator is set and ready
for service.
23. Slowly open the Main Control
Valve (Fig. A). Close the Main
Drain Valve at the rear of the F470
as soon as water discharges from
the drain connection. Observe the
Automatic Drain Valve for leaks. If
there are leaks, either the Clapper
is not properly seated and the Dou-
ble Interlock Preaction System
must be reset, or there is internal
leakage past the Clapper Facing or
Diaphragm. Determine/correct the
cause of the leakage problem. If
there are no leaks, fully open the
Main Control Valve (Fig. A).
24. Verify that the deluge valve releas-
-9-
ing panel is returned to a normal
standby condition.
25. It is recommended that the Main
Control Valve and the System
Shut-Off Valve (if applicable) be
locked in the full open position if
they are not monitored by supervi-
sory switches.
NOTE
After placing a fire protection sys-
tem in service, notify the proper
authorities and advise those re-
sponsible for monitoring propri-
etary and/or central station
alarms.
The Double Interlock Preaction Sys-
tem is now set for service.
The Double Interlock Preaction Sys-
tem requires regularly scheduled care
and maintenance of its principle com-
ponents, as described in their individ-
ual technical data sheets. In addition,
it is recommended that the proper op-
eration and condition of the system be
periodically verified in accordance with
the following described inspection pro-
cedure.
Any impairment to the system must be
promptly corrected in order to maintain
the integrity of the system.
It is recommended that the System
Inspection Procedure be performed at
least semi-annually by a qualified In-
spection Service. The Double Interlock
Preaction System Inspection Proce-
dure may be followed in lieu of per-
forming any of the operational tests
recommended in the Technical Data
Sheets for the Model F470 Deluge
Valve, Model F52OIF5201 Swing
Check Valve, Model B-1 Dry Pilot Ac-
tuator, 24 VDC Solenoid Valve, Mod-
els PSlO-2A and PS40-1A Pressure
Switches, and Model F180 Manual
Control Station.
NOTES
1. It is recommended that individu-
als responsible for care and main-
tenance of the Double Interlock
Preaction System develop a work-
ing understanding of the system,
in general, prior to performing in-
spection andlor maintenance
procedures. These instructions,
as well as individual instructions
for the deluge valve, swing check
valve, dry pilot actuator, solenoid
valve, manual control station,
switches, accelerator (if applica-
ble), and pressure maintenance
device should be reviewed.
2. The following procedures pertain
to the automatic control valve
OBSOLETE

portion of the Double Interlock
Preaction System. Refer to the
manufacturer’s instructions and
NFPA 25 for care and mainte-
nance procedures for all other de-
vices (e.g., electric detection, main
control and system shut-off
valves, supervisory devices,
sprinklers, etc.).
3. Before performing the System Zn-
spection Procedure, which will re-
sult in operation of alarms, notify
theproperauthorities and allper-
sonnel who may be affected.
4. Before closing a fire protection
system main control valve for
maintenance work on the firepro-
tection system which it controls,
permission to shut down the af-
fected fire protection system must
be obtained from the proper au-
thorities and all personnel who
may be affected by this action
must be notified.
System inspection Procedure
1. Close the Main Control Valve (Fig.
A) and then open the Main Drain
Valve at the rear of the F470 (Fig.
W
2. Open (energize) the Solenoid
Valve by manually operating the
automatic control unit. Verify that
there is no leakage out the Dry
Pilot Actuator drain. Also, verify full
operation of the deluge valve re-
leasing panel and its associated
alarms.
NOTES
During this procedure, the Sole-
noid Valve is opened; however, the
Dry Pilot Actuator should remain
closed and the F470 Deluge Valve
Diaphragm Chamber should re-
main pressurized.
This procedure is used to verify
that the F470 Deluge Valve will
remain set if the ele:tric detection
system operates but the sprinkler
system remains in its normally
pressurized condition.
3. Open the Inspector’s Test Connec-
tion but be prepared to close it, as
well as the Accelerator Control
Valve (Fig. C), if applicable, im-
mediately after verifying the follow-
ing:
a. If the system is equipped with an
Accelerator, verify that the time to
Accelerator trip is essentially the
same as in previous tests, and
verify that the Diaphragm Cham-
ber Pressure Gauge (Fig. D) de-
creases to a pressure below 25%
of the water supply pressure.
b. Verify that the Low Pressure
Alarm Switch (Fig. C) and its as-
sociated alarms operate properly.
The Low Pressure Alarm Switch
should operate at the previously
established pressure (refer to In-
stallation section, Step 10).
Close the Inspector’s Test Con-
nection, and, if applicable, close
the Accelerator Control Valve.
4. Close the Diaphragm Chamber
Supply Control Valve (Fig. D).
5. Close the System Shut-off Valve
(Fig. A) after the system air pres-
sure has been restored to normal.
6. Manually restore the electric fire
detection system to a normal con-
dition in accordance with the
manufacturer’s instructions. The
Solenoid Valve will then be de-en-
ergized and returned to its nor-
mally closed position.
7. Open the Diaphragm Chamber
Supply Control Valve.
8. Open the Main Control Valve (Fig.
A) one turn beyond the position at
which water just begins to flow
from the Main Drain Valve at the
rear of the F470.
9. Close the Main Drain Valve at the
rear of the F470 (Fig. D).
10. Close the Air Supply Control Valve
(Fig. C).
11. Open the Dry Pilot Actuator by par-
tially opening the System Main
Drain Valve (Fig. C) to relieve air
pressure at the inlet to the Actua-
tor. Verify that there is no leakage
out the Dry Pilot Actuator.
NOTES
During this procedure, the Dry
Pilot Actuator is opened; however,
the Solenoid Valve should remain
closed and the F470 Deluge Valve
Diaphragm Chamber should re-
main pressurized.
This procedure is used to verify
that the F470 Deluge Valve will
remain set if the Dry Pilot Actua-
tor operates due to loss of system
air pressure and the electric detec-
tion system remains in a normal
condition.
12. Open (energize) the Solenoid
Valve by operating the deluge
valve releasing panel, and verify
the following:
a. Verify that the F470 Deluge Valve
operates, as is indicated by a dis-
charge of water from the System
Main Drain Valve and the Auto-
matic Drain Valve. The Automatic
Drain Valve may or may not close
depending on the amount of flow
past the partially open Main Con-
trol Valve.
b. Verify that the Water-flow Pres-
sure Alarm Switch (Fig. C) and its
associated alarms properly oper-
ate.
c. Verify that the Water Motor Alarm,
if applicable, properly operates.
NOTE
This procedure simulates opening
of both the Dry Pilot Actuator (loss
of system air pressure) and Sole-
noid Valve (operation of the auto-
matic control unit) to verify auto-
matic system operation.
13. Reset the Double Interlock Dry
System in accordance with the Re-
setting Procedure section.
Seller warrants for a period of one year
from the date of shipment (warranty
period) that the products furnished
hereunder will be free from defects in
material and workmanship.
For further details on Warranty, see
Price List.
All orders must include the description
and Product Symbol Number (PSN).
NOTES
Heat detection equipment and signal-
ling devices must be separately or-
dered.
To attach the lower flange of the F520
or F5201 Check Valve to the upper
flange of the F470 Deluge Valve, as
shown in Figure B, at least four out of
the eight required flange fasteners
must be stud bolts and nuts. The stud
bolts, which are to be separately or-
dered, must be 5/8”-1lUNC x 3-l/4”
long for 4 inch (100 mm) valves and
3/4”-IOUNC x 3-314” long for 6 inch
(150 mm) valves.
Use of an automatic pressure mainte-
nance device is recommended. Refer
to Table A.
When ordering the 4 or 6 inch (100 or
150 mm) Double Interlock Preaction
System, ‘the following items selected
-lO-
OBSOLETE

DELUGE
VALVE
Specify: (specify size), Model F470 External Resetting Deluge Valve , PSN (specify).
4Inch (100 mm) . . . . . . . . . . . . PSN 52-470-l-013 77 Ibs. (34,Qkg)
6 Inch (150 mm) . . . . . . . . . . . PSN 52-470-l-015 111 Ibs. (%I,3 kg)
Specify: (specify size), (specify model) Check Valve, PSN (specify).
SWING
CHECK
VALVE
4 Inch (100 mm), Model F520 Flange x Flange PSN 52-520-l-013 62 tbs. (26,l kg)
6 Inch (150 mm), Model F520 Flange x Flange PSN 52-520-l-015 93 Ibs. (42,2 kg)
4 Inch (100 mm), Model F5201 Flange x Groove . . PSN 52-520-l-413 51 Ibs. (23,l kg)
6 Inch (150 mm), Model F5201 Flange x Groove . . PSN 52-520-I-615 76 Ibs. (35,4 kg)
ELECJPNEUMATIC
DOUBLE
INTERLOCK
PREACTION TRIM
Specify: (specify Black or Galvanized) 4 and 6 inch (100 and 150 mm) Electric/Pneumatic
Double Interlock Preaction Trim, PSN (specify).
‘Standard Order’ Black . PSN 52-470-l-100 26 Ibs. (11,6 kg)
“Special Order” Galvanized . . . PSN 52-470-2-l 00 26 Ibs. (ii,6 kg)
ACTUATION
TRIM
Specify: Factory assembled* (specify black or galvanized), Wet Pilot Actuation Trim for use
with the Model F470 External Resetting Deluge Valve, PSN (specify)
“Standard Order” Black . . . . PSN 52-470-l-101 28 Ibs. (12,7 kg)
‘Special Order” Galvanized . . . . PSN 52-470-2-101 28 Ibs. (12,7 kg)
* The actuation trim is factory assembled as shown in TDI 16. Unassembled trim can be
provided on “special order”.
AUTOMATIC
PRESSURE
MAINTENANCE
DEVICE
(recommended)
Select one of the following three options and specify: (product name), PSN (specify).
Model F324 Air Maintenance Device (Pressure Reducing Type) . . PSN 52-324-I-002 6.5 Ibs. (2,Qkg)
Model F326 Air Maintenance Device (Compressor Control Type) . PSN 52-326-l-001 8.5 Ibs. (3,8 kg)
Model F328 Nitrogen Maintenance Device . . . PSN 52-328-l-001 3.7 Ibs. (1,5 kg)
ACCELERATOR
(as applicable)
Specify: Double Interlock Accelerator Trim complete with F311 Accelerator,
PSN 52-470-I -200.
. . . . . . . . . . . . . . . . . . . . . . . . . . . . . . . . . . . . . . . . .
TABLE A
14 Ibs. (6,4 kg)
INDIVIDUAL COMPONENT ORDERING LIST
FOR 4 and 6 INCH (100 and 150 mm) ELECTRIC /PNEUMATIC DOUBLE INTERLOCK PREACTION SYSTEMS
from Table A should be ordered:
l Deluge Valve
l Swing Check Valve
l Electric/Pneumatic Double Interlock
Preaction Trim
l (Wet Pilot) Actuation Trim
l Automatic Pressure Maintenance
Device (recommended)
l Accelerator (as applicable)
Replacement Trim Parts:
Specify: (description) for use with Dou-
ble Interlock Preaction System, PSN
(specify).
Figure C - Double Interlock Preaction Trim
l-250 lb. Air
Pressure Gauge . . . . PSN 92-343-l-012
2-114’ Gauge Test
Valve . . . . . . . . . . PSN 46-005-l-002
3-Model PSlO-PA
Waterflow
Pressure Alarm
Switch . . PSN 54-281-l-002
4-Model PS40-1A
Low Air
Pressure Alarm
Switch PSN 54-281-l -003
5-114’ Pressure
Relief Valve . . . PSN 92-343-l -020
6-l/2’ Globe Valve . PSN 46-047-l -004
7-112’ Swing Type
Check Valve . PSN 46-049-l -004
8-Model B-1 Dry
Pilot Actuator . . PSN 52-280-l -001
9-24 VDC Solenoid
Valve . . . . . . . . PSN 52-287-l -024
10-2’ Angle Valve . . . . . . . . . PSN 46-048-l-009
Figure C - Double Interlock Accelerator Trim
A-Model F311
Accelerator . .PSN 52-31l-l-001
B-250 lb. Air
Pressure Gauge .PSN 92-343-l-012
C-1/2” Y-Strainer. .PSN 52-353-l-005
D-112’ Globe Valve . .PSN 46-047-l-004
E-1/2’ Swing Check
Valve with 3/32”
orifice .PSN 52-403-I-004
F-1/4’ Angle Valve .PSN 46-048-l -002
-ll-
OBSOLETE

@ Reg. trademark of GRINNELL CORPORATION, 3 TYCO PARK, EXETER, NH 03833 A tL/CO INTERNATIONAL LTD. COMPANY
OBSOLETE
Other manuals for F470
1
Other Grinnell Control Unit manuals
Popular Control Unit manuals by other brands

CHERUBINI
CHERUBINI TDS COMPACT instructions

Intermatic
Intermatic Grasslin Talento Smart LAN operating instructions
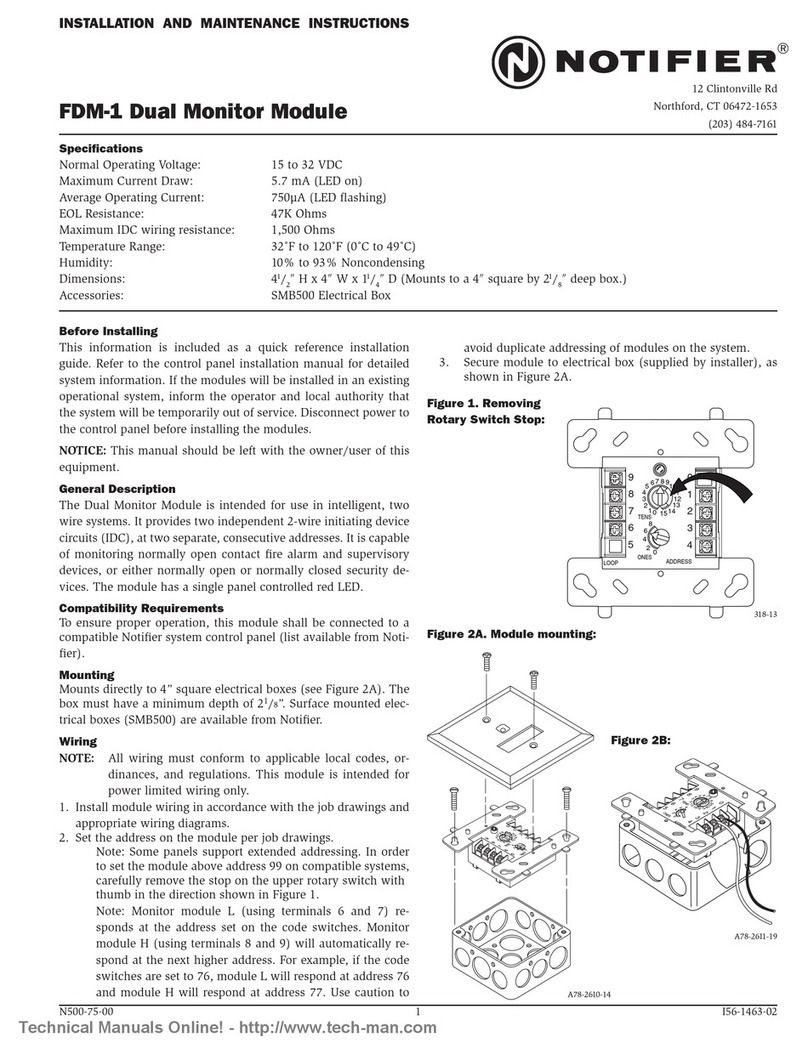
Notifier
Notifier FDM-1 Installation and maintenance instructions
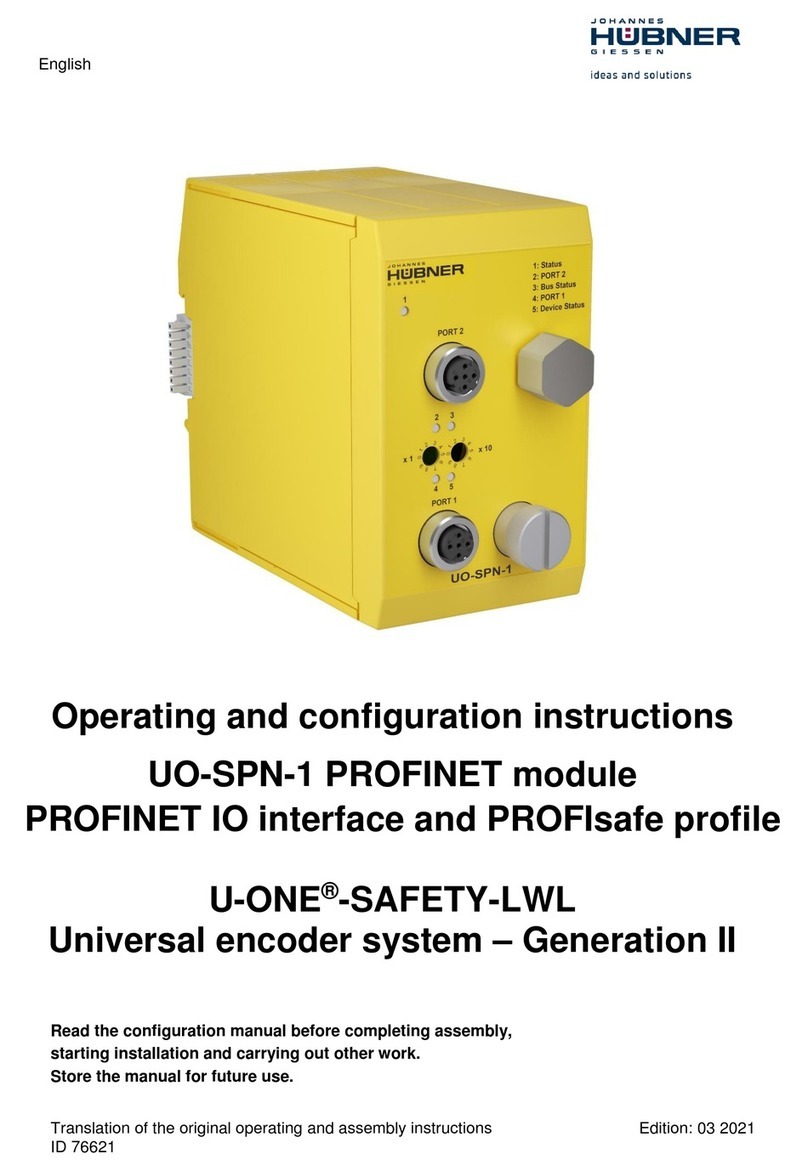
Hubner
Hubner UO-SPN-1 Operating and configuration instructions
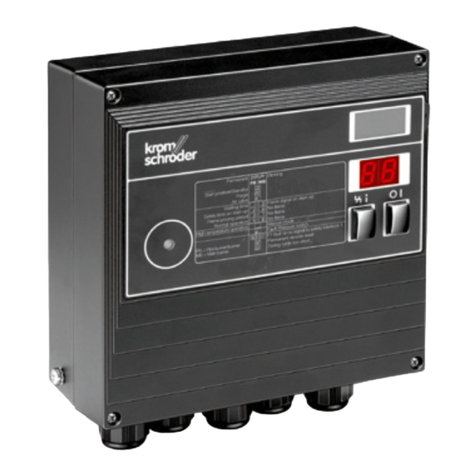
Honeywell
Honeywell BCU 460 technical information
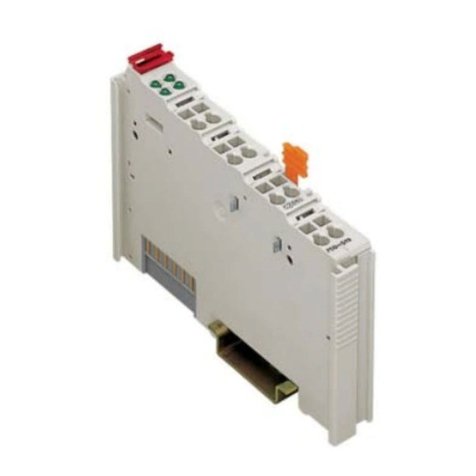
WAGO
WAGO 750-532 manual