GSi GCE 45 User manual

CE Compliant GCE Sampler
Model: GCE 45 and GCE 90
Installation and Operation Manual -
Original Instructions
PNEG-2175CE
Version: 1.0
Date: 01-13-22
PNEG-2175CE

2 PNEG-2175CE CE Compliant Sampler - Model GCE 45 and GCE 90
CE Declaration of Compliance
EC MACHINERY DIRECTIVE
2006/42/EC
1004 East Illinois Street, Assumption, IL, 62510, USA
+1 217 226 4429
The GSI Group declares that the machine, parts or equipment
GCE Cross Cut Samplers
Models: 45CE, 90CE
Sizes: All
With Sentinel Controls
Model: STL-400-3-***-GCE
Meet the Essential Requirements of the ATEX Directive 2014/34/EU and Machinery Directive
2006/42/EC
• Combustible material Grain Dust
• Minimum ignition temperature 180°C (maximum design surface temperature 100°C)
• Ex II2/2D Ex h IIIB/- T100°C Db with GSI Sentinel Controls
• Ex II3/3D Ex h IIIB/- T100°C Dc without GSI Sentinel Controls
In accordance with the following standards:
1. All installation shall be in accordance with manual PNEG-2175CE.
2. Sentinel controls shall not be installed inside the potentially explosive environment.
Signed:
IEC 60079-0:2017 Explosive atmospheres - Part 0: Equipment - General requirements
EN ISO 80079-36:2016 Explosive atmospheres. Part 36: Non-electrical equipment for explosive atmospheres -
Basic method and requirements
EN ISO 80079-37:2016
Explosive atmospheres. Part 37: Non-electrical equipment for explosive atmospheres -
non-electrical type of protection constructional safety ‘c’, control of ignition sources ‘b’,
liquid immersion ‘k’
EN ISO 12100:2010 Safety of machinery - General principles for design - Risk assessment and risk reduction
EN60204-1:2018 Safety of machinery - Electrical equipment of machines

Table of Contents
PNEG-2175CE CE Compliant Sampler - Model GCE 45 and GCE 90 3
Contents
Chapter 1 Introduction ..........................................................................................................................................4
General Safety Statements ................................................................................................................... 4
Scope .................................................................................................................................................... 4
Ordering Parts ....................................................................................................................................... 5
Replacement Parts ................................................................................................................................ 5
Repair Kits ............................................................................................................................................. 5
Chapter 2 Safety .....................................................................................................................................................6
Safety Guidelines .................................................................................................................................. 6
Cautionary Symbol Definitions .............................................................................................................. 7
Safety Cautions ..................................................................................................................................... 8
Safety Sign-Off Sheet ......................................................................................................................... 11
Chapter 3 Decals ..................................................................................................................................................12
Chapter 4 General Information ...........................................................................................................................15
System Description ............................................................................................................................. 15
Optional Features ................................................................................................................................ 15
Correct Use of the GCE Sampler ........................................................................................................ 15
Electrical Safety .................................................................................................................................. 16
Safe Access ........................................................................................................................................ 18
ATEX Compliance ............................................................................................................................... 18
ATEX Control Requirements (Zones 22 and 21) ................................................................................ 18
Ignition Hazard Assessment - GCE Samplers .................................................................................... 19
Guarding of Moving Parts ................................................................................................................... 19
Safety in Maintenance and Servicing .................................................................................................. 20
Chapter 5 Installation ..........................................................................................................................................21
Receiving Inspection ........................................................................................................................... 21
Pre-Installation Preparation ................................................................................................................. 21
Location ............................................................................................................................................... 21
General Mounting Guidelines .............................................................................................................. 21
Material Sample Transport Lines ........................................................................................................ 22
Controller Location .............................................................................................................................. 22
Field Wiring ......................................................................................................................................... 22
Chapter 6 Operation ............................................................................................................................................23
Sampler Controls ................................................................................................................................ 23
Configuring the Controls ..................................................................................................................... 26
Chapter 7 Wiring Diagrams .................................................................................................................................28
CE Control Electrical Layout ............................................................................................................... 28
CE Control Motor Connections ........................................................................................................... 30
CE Control Connections ...................................................................................................................... 31
Chapter 8 Maintenance and Repair ....................................................................................................................32
General Maintenance .......................................................................................................................... 32
Testing ATEX Controls ........................................................................................................................ 32
Periodic Inspection .............................................................................................................................. 33
Lubrication ........................................................................................................................................... 33
Mechanical Repair Procedures ........................................................................................................... 34
Chapter 9 Troubleshooting .................................................................................................................................37
General GCE Sampler Troubleshooting ............................................................................................. 37
Chapter 10 Parts List ...........................................................................................................................................38
Sampler Model GCE 45 Parts ........................................................................................................... 38
Sampler Model GCE 90 Parts ........................................................................................................... 41
Chapter 11 Warranty ............................................................................................................................................45

4 PNEG-2175CE CE Compliant Sampler - Model GCE 45 and GCE 90
1. Introduction
This manual covers the installation and operation for the Sampler Model GCE 45 and 90. This manual
provides guidelines for installing the product. You must retain a qualified contractor to provide on-site
expertise. INTERSYSTEMS IS NOT RESPONSIBLE FOR THE INSTALLATION OF THIS PRODUCT.
InterSystems reserves the right to improve its product whenever possible and practical to do so. We
reserve the right to change, improve and modify products at any time without obligation to make changes,
improvements and modifications on equipment sold previously.
General Safety Statements
1. The Sampler system is designed and manufactured with operator safety in mind. However, residual
hazards remain due to the nature of material handling and specific material hazards. Use extreme
caution at all times.
2. Modifications to equipment may cause extremely dangerous situations that could result in damage
to the equipment as well as serious injury or death. Never modify the equipment.
3. InterSystems recommends that you contact the local power company to have a representative survey
the installation to ensure wiring is compatible with their system and adequate power is supplied to
the unit.
4. Consult InterSystems before making any changes to the sampler or its operating environment.
Careless changes could result in death or serious injury to people and reduce the performance and
service life of the equipment.
5. Never perform any service on this equipment or any powered equipment until all power has been
shut off and locked out so that it cannot be restored without the consent and knowledge of the person
who interrupted power. Power includes electrical, fluid, mechanical or pneumatic energy.
6. Never perform any service on this equipment without utilizing the required PPE (Personal Protective
Equipment). Refer to the MSDS (s) (Material Safety Data Sheet (s)), on all products to which this
equipment is in contact to determine what PPE is required.
Scope
The certified drawings list the non-standard components that have been incorporated into the equipment.
InterSystems, Inc. normally stocks non-fabricated parts and non-custom OEM parts. Replacement parts
for any other components, including fabricated parts and custom OEM components can be supplied
upon request.
This equipment is to be operated only on the voltage designated on the certified
electrical drawings. Fire or explosion may result, which can cause death, serious
injury and extensive damage to equipment. Do not connect to voltages other than
designated.

1. Introduction
PNEG-2175CE CE Compliant Sampler - Model GCE 45 and GCE 90 5
Ordering Parts
Direct parts orders or requests for technical assistance to your sales representative or to:
InterSystems
1004 E. Illinois St.
Assumption, IL 62510-0020
Phone: 1-217-226-4421
Fax: 1-217-226-4420
Please have available the MODEL NUMBER, SERIAL NUMBER and CUSTOMER ORDER NUMBER of
the equipment in question as well as the location where the sampler is INSTALLED.
Replacement Parts
The InterSystems, Inc. sampler is a quality built piece of machinery. As with any machine, parts do wear
out and fail. It is InterSystems recommendation that a small supply of spare parts be kept on hand to cover
any minor breakdowns. A separate priced spare parts list will be sent identifying the suggested spare
parts. It is also necessary to check the certified drawings, which will list any special or custom components
utilized on this equipment.
Repair Kits
The following chart lists repair kits and parts that are available from InterSystems. These kits are offered
as a more economical solution by rebuilding the defective part rather than replacing it. However in some
cases the part may be beyond repair and replacement will be necessary.
Product Code Description
34769 Standard SAE 80W-90 EP Gear Lubricant Oil Quart (Pennzoil 4096)
529601 Optional Synthetic Gear Lubricant Oil Quart (Mobil SHC634)
35342 #50 Friction Facing (Ref #16 on Page 36.)
35527 Limit Switch Contact Block 1 N.O. 1 N.C.

6 PNEG-2175CE CE Compliant Sampler - Model GCE 45 and GCE 90
2. Safety
Safety Guidelines
Safety guidelines are general-to-specific safety rules that must be followed at all times. This manual is
written to help you understand safe operating procedures and problems that can be encountered by the
operator and other personnel when using this equipment. Read and save these instructions.
As owner or operator, you are responsible for understanding the requirements, hazards, and precautions
that exist and to inform others as required. Unqualified persons must stay out of the work area at all times.
Alterations must not be made to the equipment. Alterations can produce dangerous situations resulting in
SERIOUS INJURY or DEATH.
This equipment must be installed in accordance with the current installation codes and applicable
regulations, which must be carefully followed in all cases. Authorities having jurisdiction must be consulted
before installations are made.
When necessary, you must consider the installation location relative to electrical, fuel and water utilities.
Personnel operating or working around equipment must read this manual. This manual must be delivered
with equipment to its owner. Failure to read this manual and its safety instructions is a misuse of the
equipment.
ST-0001-4

2. Safety
PNEG-2175CE CE Compliant Sampler - Model GCE 45 and GCE 90 7
Cautionary Symbol Definitions
Cautionary symbols appear in this manual and on product decals. The symbols alert the user of potential
safety hazards, prohibited activities and mandatory actions. To help you recognize this information, we
use the symbols that are defined below.
DANGER
WARNING
CAUTION
NOTICE
This symbol indicates an imminently hazardous situation
which, if not avoided, will result in serious injury or death.
This symbol indicates a potentially hazardous situation
which, if not avoided, can result in serious injury or death.
This symbol indicates a potentially hazardous situation which,
if not avoided, can result in minor or moderate injury.
This symbol is used to address practices not related to
personal injury.
This symbol indicates a general hazard.
This symbol indicates a prohibited activity.
This symbol indicates a mandatory action.
ST-0005-2

2. Safety
8 PNEG-2175CE CE Compliant Sampler - Model GCE 45 and GCE 90
Safety Cautions
Use Personal Protective Equipment
Eye
Protection
Hearing
Protection
Hand
Protection
Head
Protection
Respiratory
Protection
Foot
Protection
Fall
Protection
• Use appropriate personal protective equipment:
• Wear clothing appropriate to the job.
• Remove all jewelry.
• Tie long hair up and back.
ST-0004-1
Follow Safety Instructions
• Carefully read all safety messages in this manual and
safety signs on your machine. Keep signs in good
condition. Replace missing or damaged safety signs.
Be sure new equipment components and repair parts
include the current safety signs. Replacement safety
signs are available from the manufacturer.
• Learn how to operate the machine and how to use
controls properly. Do not let anyone operate without
instruction.
• If you do not understand any part of this manual or
need assistance, contact your dealer.
ST-0002-1

2. Safety
PNEG-2175CE CE Compliant Sampler - Model GCE 45 and GCE 90 9
Maintain Equipment and Work Area
• Understand service procedures before doing work. Keep area
clean and dry.
• Never service equipment while it is operating. Keep hands, feet,
and clothing away from moving parts.
• Keep your equipment in proper working condition. Replace worn
or broken parts immediately.
ST-0003-1
Stay Clear of Hoisted Equipment
• Always use proper lifting or hoisting equipment when assembling
or disassembling equipment.
• Do not walk or stand under hoisted equipment.
• Always use sturdy and stable supports when needed for
installation. Not following these safety precautions creates the
risk of falling equipment, which could crush personnel and cause
serious injury or death.
ST-0047-1
Sharp Edge Hazard
• This product has sharp edges, which can cause serious injury.
• To avoid injury, handle sharp edges with caution and always use
proper protective clothing and equipment.
ST-0036-2
Install and Operate Electrical Equipment Properly
• Electrical controls must be installed by a qualified electrician and
must meet the standards set by applicable local codes (National
Electrical Code for the US, Canadian Electric Code, or EN60204
along with applicable European Directives for Europe).
• Lock-out power source before making adjustments, cleaning, or
maintaining equipment.
• Make sure all equipment and bins are properly grounded.
ST-0075-1

2. Safety
10 PNEG-2175CE CE Compliant Sampler - Model GCE 45 and GCE 90
Stay Clear of Moving Parts
• Stay clear - machine can start without warning.
• Entanglement in gate will cause serious injury.
• Keep all shields and covers in place at all times.
• Lock-out power source before making adjustments, cleaning, or
maintaining equipment.
ST-0070-1
Flying Material and High Pressure Air Hazard
• Flying material and/or high pressure air can cause
severe eye injury or blindness.
• Wear safety glasses around operating equipment.
ST-0071-1
Stay Clear of Rotating Parts
• Do not service equipment while it is in operation.
• Entanglement in rotating parts or exposed belts will cause serious
injury or death.
• Keep all shields and covers in place at all times.
• Lock-out power source before making adjustments, cleaning, or
maintaining equipment.
ST-0072-1

2. Safety
PNEG-2175CE CE Compliant Sampler - Model GCE 45 and GCE 90 11
Safety Sign-Off Sheet
Below is a sign-off sheet that can be used to verify that all personnel have read and understood the safety
instructions. This sign-off sheet is provided for your convenience and personal record keeping.
Date Employee Name Supervisor Name
Toxic Fume and Dust Hazard
• Do all work outside or in a well-ventilated area. Dispose of paint and
solvent properly.
• Remove paint before welding or heating:
— Avoid potentially toxic fumes and dust. Hazardous fumes can be
generated when paint is heated by welding, soldering, or
using a torch.
— If you sand or grind paint, avoid breathing the dust. Wear an
approved respirator.
— If you use solvent or paint-stripper, remove stripper with soap
and water before welding.
— Remove solvent or stripper containers and other flammable
material from area. Allow fumes to disperse at least 15 minutes
before welding or heating.
ST-0043-2
ST-0007

12 PNEG-2175CE CE Compliant Sampler - Model GCE 45 and GCE 90
3. Decals
The safety decals on your equipment are safety indicators which must be carefully read and understood
by all personnel involved in the installation, operation, service and maintenance of the equipment.
To replace a damaged of missing decal, contact us to receive a free replacement.
InterSystems
1004 E. Illinois St.
Assumption, IL 62510-0020
Phone: 1-217-226-4421
Fax: 1-217-226-4420
Figure 3A GCE Sampler Safety Label Locations
NOTE: These signs must never be removed, tampered with, painted over or obscured in anyway. If labels
are damaged or become unreadable, replacement labels are available from InterSystems.

3. Decals
PNEG-2175CE CE Compliant Sampler - Model GCE 45 and GCE 90 13
Ref # Decal # Decals Description
1 EMC 30 34 Moving Part
2 EMC 402 34 Lock Out Machine
3 EMC 403 34 Starts Without Warning
4- Rating Plate
WARNING
Moving parts can
cut and crush.
Lockout energy
source before
inspection or
service.
Reorder No. EMC 30 34
C
Clarion Clarionsafety.com
WARNING
Avoid serious
injury or death.
This machine MUST be
locked out in accordance
with current OSHA
requirements before
any maintenance or
service is performed.
Reorder No. EMC 402 3416089
C
Clarion Clarionsafety.com
WARNING
Stay clear.
Machine
starts without
warning.
CClarion clarionsafety.com
Reorder No. EMC 403 34
400 V AC: 3 ph: 50 hz: 7A FLC
II2/2D; Ex h IIIB T100°C Db
1234567
-10°C/+40°C
SN
InterSystems
13217 IL Highway 133 Paris, IL, 61944-6701
USA
GCE SAMPLER
90
34
MODEL
SIZE
T
Tcrit
tnorm
tcrit
100°C
2.4 s
1.2 s

3. Decals
14 PNEG-2175CE CE Compliant Sampler - Model GCE 45 and GCE 90
5 EMC 428 34 Eye Protection
6 DC-2553 InterSystems Logo
7 EMC 24 34 Exposed Belt
Ref # Decal # Decals Description
WARNING
Flying material can
cause severe eye
injury or blindness.
No. EMC 28 34
Wear safety glasses
around operating
equipment.
15225
CClarion
DC-2553
WARNING
Moving parts can
crush and cut.
No. EMC 24 34
Lockout power before
removing guard
or servicing.
Do NOT operate with
guard removed.
CClarion

PNEG-2175CE CE Compliant Sampler - Model GCE 45 and GCE 90 15
4. General Information
System Description
The GCE Sampler is designed to collect a representative sample of granular, flake, pellet or other
materials in a gravity conveying line.
Sample collection is initiated in response to either an operator’s manual command or a signal
automatically generated by controller logic, usually time-based but which could also be volume or quantity
based. A sample cycle begins when an electric motor drives the slotted sample cutter through the product
flow to collect a sample of the material. The sample flows through the sample cutter and out the discharge
as it travels through the material flow. The sample cutter, when at rest, is situated under one of two dust
seals that seal the sample cutter. The sample from the sample cutter flows into to the sample hopper and
out the 3.00" (76 mm) O.D. discharge tube. The sample, flowing via gravity from the hopper discharge, will
then be routed to a sample divider or directly to the desired sample collection point.
Optional Features
The certified drawings indicate which, if any, optional features are included with a sampling system. Some
of the more frequently specified optional features are briefly described in the following list.
1. Controller arranged to initiate a sampling cycle based on quantity or volume of material passing
through conveying line rather than upon elapsed time periods.
2. ATEX compliant sampler for use in dusty atmospheres and with internal zone designated up to
ATEX zone 21D.
NOTE:
ATEX compliant sampler does not include electrical controllers, which must be installed
outside the ATEX zone.
3. Components of special materials, such as stainless steel or nedox coatings.
4. Programmable controls to sequence the sampler and the sample collection equipment.
5. Abrasion resistant linings of urethane, AR carbon steel plate, 304 stainless steel or ceramic tile.
Correct Use of the GCE Sampler
The sampler is designed to be used for automatic, intermittent sampling of free-flowing, granular, flake or
pelleted materials in a gravity conveying line.
In particular the sampler is not designed to be used as follows:
1. Continuous sampling.
2. Sampling liquids, sludges or slurries.
3. Sampling rock, stone, sand, gravel or other highly abrasive materials.
4. Sampling materials prone to sparking on impact.
5. Sampling corrosive materials.
6. Sampling materials with maximum aggregate size greater than 1-3/8" (35 mm).
Any other form of use is a misuse of the sampler and may result in damage or
serious/fatal injury.

4. General Information
16 PNEG-2175CE CE Compliant Sampler - Model GCE 45 and GCE 90
7. Sampling volatile, explosive or highly flammable materials.
8. Use other than when connected directly to a material handling system.
9. Use with either the inlet or outlet exposed such that moving parts can be reached.
10. Use with manual filling of emptying.
11. Use when modified in any way.
12. Use in environmental conditions contrary to those marked on the rating plate.
13. Use underground or in mining processes.
14. Sampling of clean, dust free material is inherent to reducing the risk of a potentiality explosive dust
air mixture forming inside the sampler.
15. Where high levels of dust are anticipated inside the sampler, ventilation and extraction should be
used to reduce concentrations.
16. Operators should be aware of health risks from dusts, mould and other biological agents from
the materials being sampled. Overall design of the facility in which the sampler operates shall
minimize this exposure and personal protective equipment (PPE) shall be used to further reduce
risks if required.
NOTE:
The sampler may be installed or used in a potentially explosive environment ONLY when specified
as such by GSI and when carrying the relevant ATEX rating. Refer to the ATEX Compliance that
follows.
Electrical Safety
Equipment shall include:
1. Fuse protected main power supply.
a. The electrical supply should include earth leakage protection, ex: residual current device (RCD)
or residual current circuit breaker (RCCB), to provide automatic disconnection in the event of a
fault.
2. Lockable main safety disconnect.
a. Disconnects all electrical power.
3. Lockable motor service disconnect.
a. Adjacent to each motor (or group of motors).
b. Disconnects all power to the motors.

4. General Information
PNEG-2175CE CE Compliant Sampler - Model GCE 45 and GCE 90 17
4. Emergency stops.
a. Stops all equipment immediately when pressed.
b. Must remain engaged until manually disengaged.
c. Equipment shall not immediately restart when the emergency stop is reset.
5. Door safety interlocks - where doors provide access to dangerous machinery.
a. Immediately stops and prevents restart of all
equipment when the door is open.
b. Equipment shall not immediately restart when the door in closed.
c. Design of the safety related parts of the control system (SRPCS) shall be carried out following
risk assessment and in accordance with EN ISO 13849.
6. The electrical supply shall include a properly designed protective earth system (PE),
with connection to all exposed conductive parts.
7. All motors shall be connected to protective earth at the terminal provided.
8. The control system shall include,
a. Short circuit protection.
b. Start/stop controls (labelled 1 and 0 respectively).
9. Equipment shall not immediately restart following re-establishment of power.
10. Motor circuits shall include over current protection set according to the full load current, stated on the
motor rating plate.
11. Motor thermal protection may also be required.
12. All electrical design, installation and testing must be carried out by a qualified electrical engineer, in
accordance with EU Directives and Standards, local laws and codes. Specific reference should be
made to EN 60204 for electrical equipment and controls.

4. General Information
18 PNEG-2175CE CE Compliant Sampler - Model GCE 45 and GCE 90
Safe Access
The GCE sampler may be installed at heights and as part of a larger material handling system. To ensure
correct and safe maintenance, servicing and repair can be carried out, safe access to the sampler is
required.
1. Suitable fixed ladders or stairs in accordance with EN ISO 14122-3 or EN ISO 14122-4.
2. Suitable working platform, in accordance with EN ISO 14122-2, providing access to all parts of
the sampler.
ATEX Compliance
GCE samplers may be specified for use in or containing a potentially explosive environment.
1. Classification of the ATEX zone on site is the end users responsibility, but shall be limited to zones
21 or 22 (dusts). Use in all other zones is prohibited.
2. Samplers must be ordered, specified and marked according to the designated zone.
3. Compliance and use in an ATEX zone requires use of a safety control system (control of ignition
sources). Refer to CE Control Electrical Layout on Page 28 for more details.
ATEX Control Requirements (Zones 22 and 21)
1. To prevent excessive motor temperatures, the motors are provided with internal thermal switches.
These must be installed into the control system in the locations provided or, for non-GSI controls, in
the location identified by the control manufacturer.
2. Where user designed controls are used, the controls shall be designed to provide a minimum level
of ignition protection b1 or be designed to meet the requirements of control of ignition sources to
explosion protection level (EPL) Db, in accordance with EN80079-37.
3. User supplied controls, in addition to the requirements given above, shall include:
a. Motor over temperature control and/or monitoring. Motor temperature shall not exceed 100°C.
b. Sampler over speed detection. Sampler speed shall not exceed 1m/s.
c. Sampler motor maximum run time shut off. The sampler motor shall not run for longer than 20s.
This feature is required to ensure that the clutch fitted to the sampler is not slipping, resulting in
potential high surface temperatures and potential sources of ignition. Maximum surface
temperature shall not exceed 100°C.
4. Where any of the limits stated above are exceeded, the control shall bring the sampler to a stop and
shall not allow restart without direct intervention from the operator. This shall only be permitted once
the cause of the fault has been identified and rectified.
5. These functions shall be testable. (See testing ATEX controls on Page 32.)

4. General Information
PNEG-2175CE CE Compliant Sampler - Model GCE 45 and GCE 90 19
Ignition Hazard Assessment - GCE Samplers
Guarding of Moving Parts
GCE samplers have hazardous moving parts which present a risk of serious injury when unguarded.
The samplers operate under automatic control and may start unexpectedly and without warning.
1. Guards are provided to enclose all moving parts except those involved in the sampling process.
2. Moving parts involved in the sampling process shall be made inaccessible at installation by enclosing
both the inlet and outlet of the sampler such that the moving parts cannot be reached by any part of
the human body.
3. Generally this is achieved by close coupling the sampler inlet and outlet to the upstream and
downstream conveying system.
4. Where this is not suitable (ex: open hopper inlet), the installer must ensure access to the moving parts
is restricted in accordance with EN ISO 13857 or through other methods (ex: interlocking controls).
5. Under certain circumstances it may be necessary to remove guards. Only do this when the sampler
and other associated equipment is isolated and locked out from the power supply.
6. Never operate the sampler with the guards removed.
Possible Ignition
Sources
Equipment
related Yes/No Reason Controls
Hot Surfaces Yes
Sliding friction of moving parts on static parts
Surface temperature of gearbox and motor
Slipping torque tamer clutch
Bearing temperatures
Constructional safety
Control of ignition sources
Surface temperature control
Overrun timers
Mechanical Sparks Yes
Single impact of mal-adjusted moving part.
Chain/sprocket failure
Sampling incorrect materials, prone to impact
sparks
Constructional safety
Operator’s manual instruction on
correct use
Flames, Hot Gases No None present
Electric Sparks Yes
Potential arcs at electrical connections, in motors
and switches.
Static electricity sparks from non-conductive
surfaces.
Constructional safety
Control of ignition sources
Electrical controls design and
installation to EN 60204
Stray Electric
Current and Cathodic
Corrosion Protection
No None present
Static Electricity Yes None present
Lightning No To be addressed on specific installation location To be addressed on site
Electromagnetic
Waves No None present
Ionising Radiation No None present
High Frequency
Radiation No None present
Ultrasonics No None present
Adiabatic
Compression No None present
Chemical Reaction No None present

4. General Information
20 PNEG-2175CE CE Compliant Sampler - Model GCE 45 and GCE 90
Safety in Maintenance and Servicing
Only suitably competent/qualified persons should carry out servicing or maintenance on the GCE sampler.
The following recommendations should be considered:
1. Safe Access: Samplers may be installed in remote locations and at height. Ideally safe, permanent
access should be provided. However in the event that this is not the case, the service technician
should use safe methods, such as a powered work platform or tower scaffold. It is not recommended
to work solely off a ladder.
2. Safe Isolation: Service and maintenance should be carried out only when the sampler has been
disconnected and locked off from all power/energy supplies and the key remains solely in the
possession of the service technician. The sampler operates under automatic control and will start
without warning. Working in or on a sampler that has not been disconnected and locked out can
result in very serious injury. It may also be necessary to isolate other equipment associated with or
attached to the sampler.
3. Safe Troubleshooting: In extreme circumstances, when troubleshooting a malfunctioning sampler it
may become necessary to observe the sampler operating with guards removed. This should only be
carried out in MANUAL mode and, if the sample control is remote from the sampler, with a second
person manning the controls. Refer to Sampler Controls on Page 23 for information on how to
operate the sampler in manual mode.
NOTE:
This only applies where the GSI Sample Sentinel controls are being used. For other control
types, refer to the control manufacturer.
4. NEVER attempt to intervene or work on the sampler when powered up, even when in manual mode.
This manual suits for next models
1
Table of contents
Other GSi Sampler manuals
Popular Sampler manuals by other brands
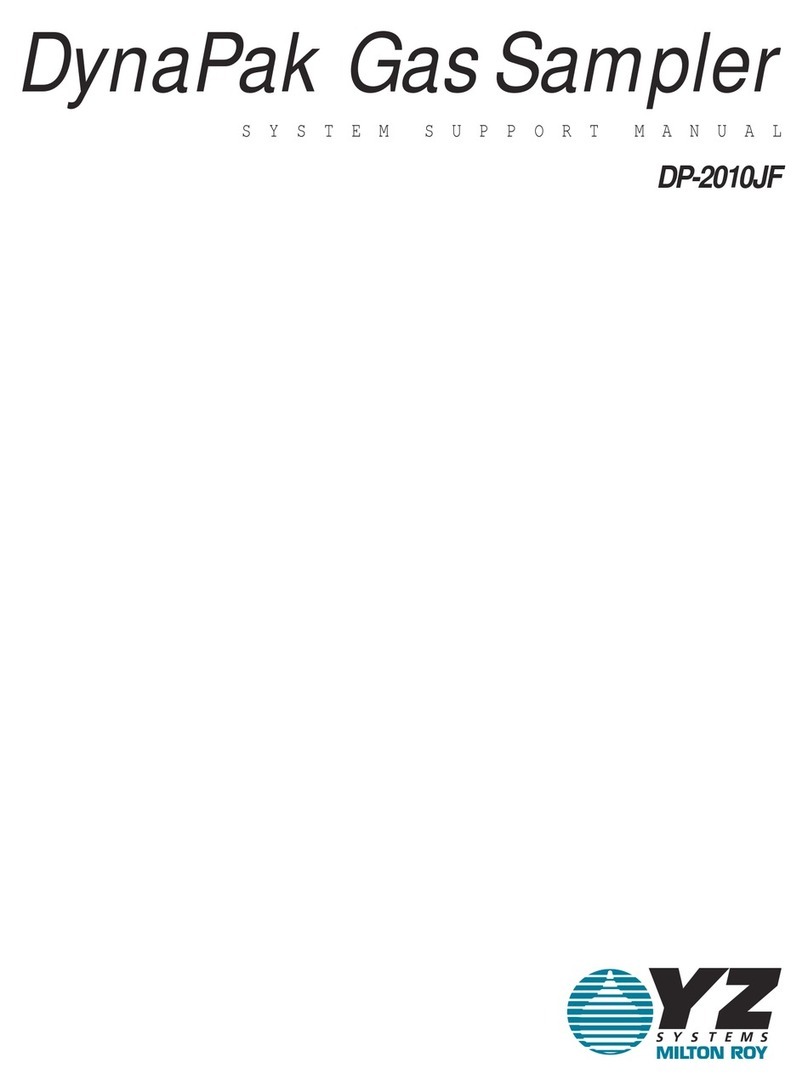
YZ Systems
YZ Systems DynaPak DP-2010JF Instructions & operating manual
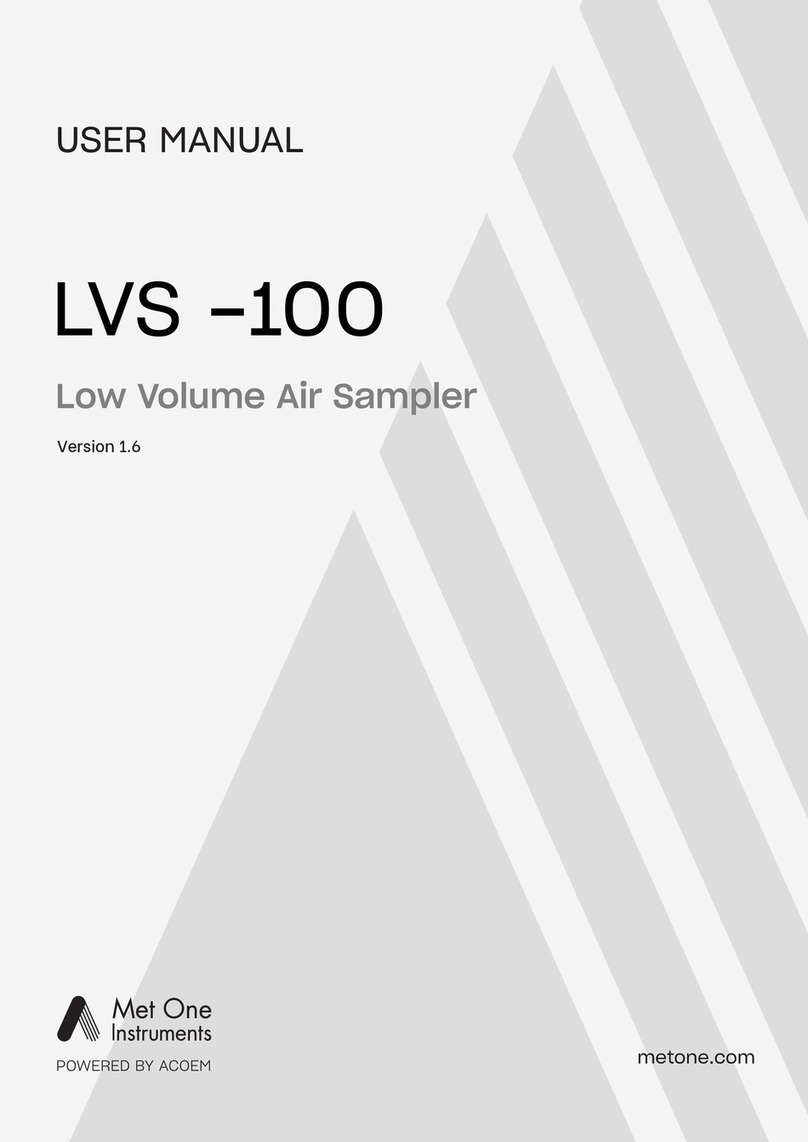
Met One Instruments
Met One Instruments LVS-100 user manual
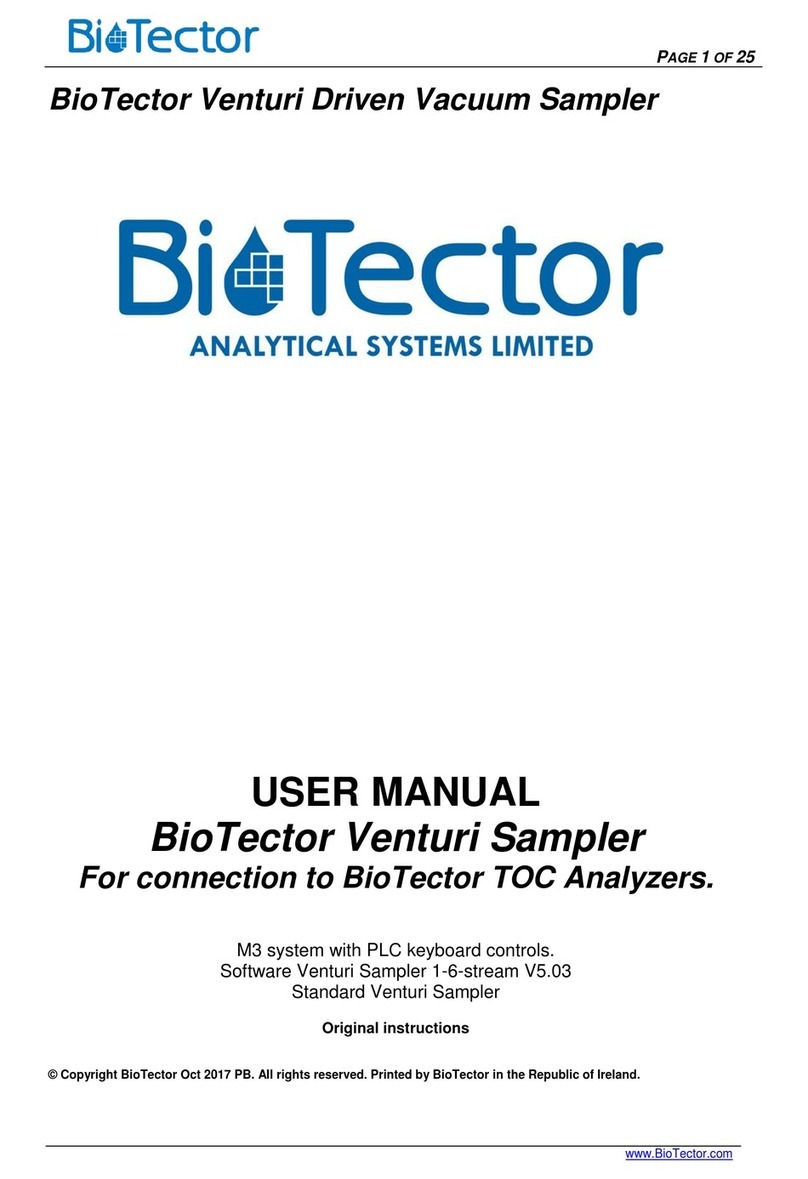
Biotector
Biotector Venturi 19-BAS-001 user manual
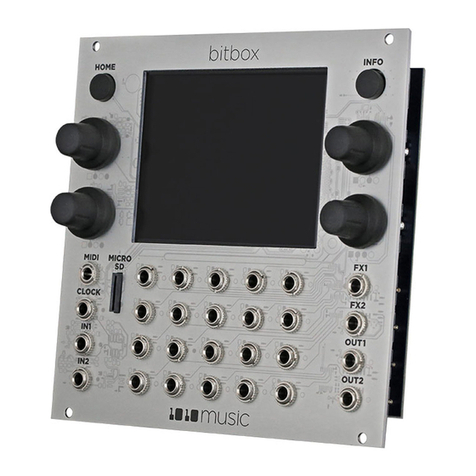
1010music
1010music Bitbox MK2 1.0 quick start guide
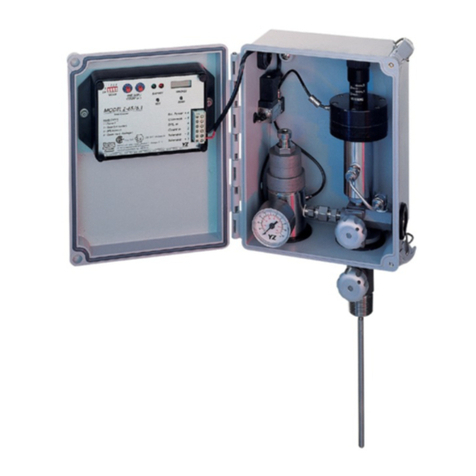
YZ Systems
YZ Systems DynaPak 2010N Series manual
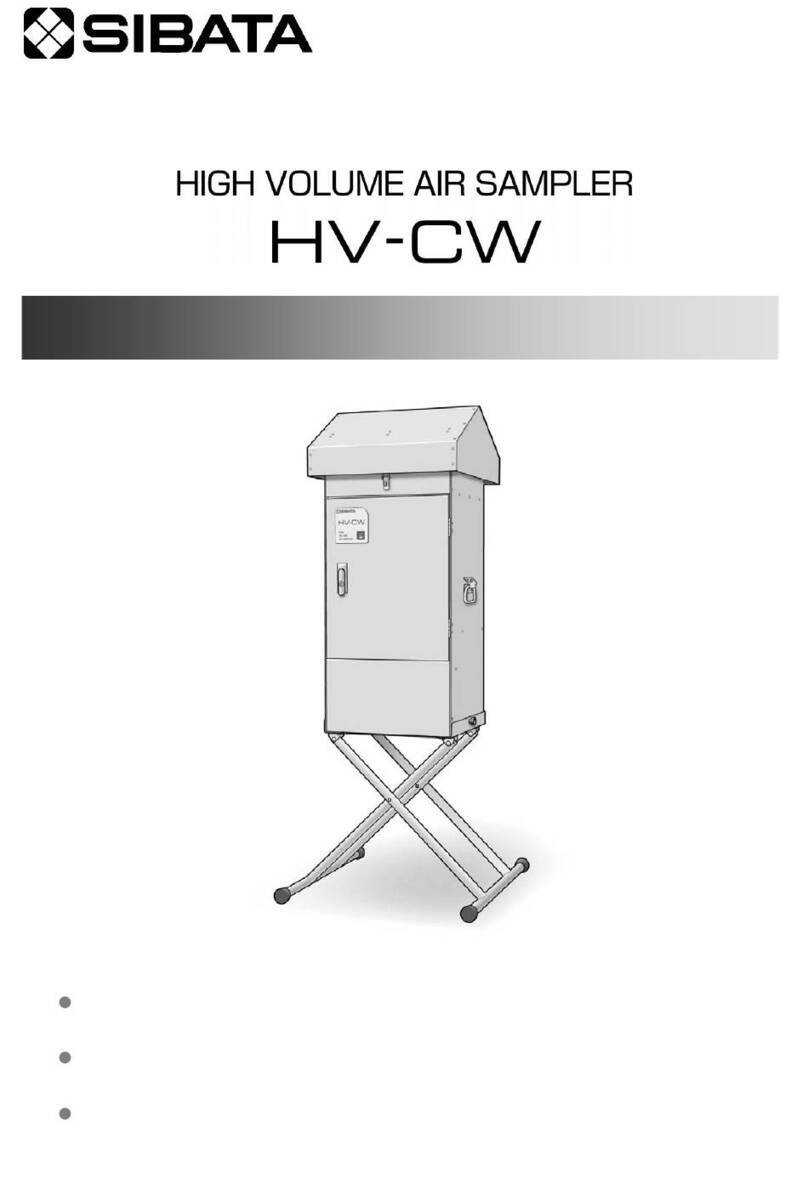
Sibata
Sibata HV-CW Operation manual