GSi IS TD User manual

9575 N. 109th Ave.
Omaha, Nebraska 68142
(402) 330-1500
www.intersystems.net
SAFETY
INSTALLATION
OPERATION
MAINTENANCE
MANUAL
SAMPLER
Model TD
No. PC 522818A
Revised 2006-10-26

1
Table of Contents
I. GENERAL SAFETY INFORMATION .....................................................................................................................3
II. GENERAL INFORMATION ...................................................................................................................................5
2.1 System Description .................................................................................................................................5
2.2 Optional Features ...................................................................................................................................6
2.3 Material Sampled....................................................................................................................................6
2.4 Sampler Construction .............................................................................................................................6
III. GENERAL INSTALLATION REQUIREMENTS ....................................................................................................7
3.1 Receiving Inspection...............................................................................................................................7
3.2 Pre-Installation Preparation ....................................................................................................................7
3.3 Location ..................................................................................................................................................7
3.4 General Mounting Guidelines .................................................................................................................7
3.5 Material Sample Transport Lines............................................................................................................8
3.6 Controller Location..................................................................................................................................8
3.7 System Wiring.........................................................................................................................................8
3.7.1 Electrical Power Requirements, System..............................................................................................8
3.7.1.1 Controller ..........................................................................................................................................8
3.7.1.2 Drive Motor .......................................................................................................................................8
IV. OPERATIONS AND ADJUSTMENTS..................................................................................................................9
4.1 Control Components And Their Functions..............................................................................................9
4.1.1 POWER OFF/ON Switch S-1 ............................................................................................................10
4.1.2 POWER Pilot Light.............................................................................................................................10
4.1.3 TRAVERSE LEFT Pilot Light.............................................................................................................10
4.1.4 TRAVERSE RIGHT Pilot Light...........................................................................................................10
4.1.5 Digital Display Timer T-1 (Standard)..................................................................................................10
4.1.6 Main Fuse ..........................................................................................................................................11
4.1.7 Index Relay IR-1 ................................................................................................................................11
4.1.8 Reverse Delay Timer Relays .............................................................................................................12
4.1.9 Terminal Strip.....................................................................................................................................12
4.2 Sampler Mounted Electrical Components.............................................................................................12
4.2.1 Limit Switches, LS-1 & LS-2 ..............................................................................................................12
4.2.2 Drive Motor ........................................................................................................................................12
V. MAINTENANCE AND REPAIR ...........................................................................................................................13
5.1 General Maintenance............................................................................................................................13
5.2 Periodic Inspection................................................................................................................................13
5.3 Lubrication .............................................................................................................................................14
5.3.1 Drive Chain, Sprockets & Idler Shaft .................................................................................................14
5.3.2 Gear Reducer ....................................................................................................................................14
5.4 Mechanical Repair Procedures.............................................................................................................14
5.4.1 Drive Chain Adjustment .....................................................................................................................14
5.4.2 Limit Switch Adjustment.....................................................................................................................14
5.4.3 Sample Cutter Blade Replacement....................................................................................................14
5.4.4 Sample Cutter Seals Replacement....................................................................................................15
5.4.5 Drive Clutch Adjustment ....................................................................................................................15
5.4.6 Drive Clutch, Facings, Bushing & Sprocket Replacement .................................................................15
VI. TROUBLESHOOTING .......................................................................................................................................17
6.1 General TD Sampler Troubleshooting ..................................................................................................17
VII. REPLACEMENT PARTS...................................................................................................................................18
7.1 Scope....................................................................................................................................................18
7.2 Ordering Parts ......................................................................................................................................18
7.3 Replacement Parts ...............................................................................................................................18
7.4 Repair Kits ............................................................................................................................................18

2
7.4.1 Sampler Parts Listing TD (see Figure 7-1) ........................................................................................19
7.4.1 Sampler Parts Listing TD (see Figure 7-1) ........................................................................................20
VIII. WARRANTY.....................................................................................................................................................22
List Of Illustrations & Drawings
FIGURE 1-1, TD SAMPLER SAFETY LABEL LOCATIONS ......................................................................................4
FIGURE 2-1, TYPICAL INSTALLATION, MODEL TD SAMPLING SYSTEM ............................................................5
FIGURE 4-1, STANDARD NEMA 12 CONTROL PANEL DETAIL.............................................................................9
FIGURE 4-2, LIMIT SWITCH CONNECTIONS ........................................................................................................12
FIGURE 5-1, DRIVE CLUTCH DETAIL....................................................................................................................16
FIGURE 7-1, TD SAMPLER PARTS DRAWING......................................................................................................21

3
I. GENERAL SAFETY INFORMATION
SAFETY FIRST! The symbols shown identify
examples of the safety labels and signs to
be found on InterSystems equipment. They
are affixed to the equipment to warn of
danger to persons and of possible
equipment damage. These signs must
never be removed, tampered with, painted
over or obscured in any way. (See Page 4
for label locations.) If labels are damaged or
become unreadable, replacement labels are
available from InterSystems. The user must
institute a continuing program to instruct all personnel in safe operating and maintenance procedures, and to
insure that all safety devices, guards, and covers are intact and operable, and that all safety signs are legible.
Consult InterSystems, Inc. before making any changes to the sampler or its operating environment. Careless
changes could result in death or serious injury to people, and reduce the performance and service life of the
equipment.
Never perform any service on this equipment or any other powered equipment until all power has been shut off
and locked out so that it cannot be restored without the consent and knowledge of the person who interrupted
power. Power includes electrical, fluid, mechanical, or pneumatic energy.
Never perform any service on this equipment without utilizing the required PPE (personal protective equipment).
Refer to the MSDS(s), material safety data sheet(s), on all the products to which this equipment is in contact with
to determine what PPE is required.
DANGER
THIS EQUIPMENT IS TO BE OPERATED ONLY ON THE VOLTAGE DESIGNATED ON THE
CERTIFIED ELECTRICAL DRAWING(S)! FIRE OR EXPLOSION MAY RESULT, WHICH CAN
CAUSE DEATH, SERIOUS INJURY, AND EXTENSIVE DAMAGE TO EQUIPMENT. DO NOT
CONNECT TO VOLTAGES OTHER THAN DESIGNATED.

4
FIGURE 1-1, TD SAMPLER SAFETY LABEL LOCATIONS

5
II. GENERAL INFORMATION
2.1 System Description
The TD Sampler is designed to collect a representative sample of granular, pellet, or other materials from the end
of a belt conveyor. Figure 2-1 illustrates a typical TD Sampler application.
Sample collection is initiated in response to either an operator's manual command or a signal automatically
generated by controller logic, usually time-based but which could also be volume or quantity based. A sample
cycle begins when an electric motor drives the slotted sample cutter through the product flow to collect a sample of
the material. The sample is pnuematically withdrawn from the sample pelican via a SD sample delivery system.
The sample cutter, when at rest, is situated under one of two dust seals that seal the sample cutter. The sample,
flowing via gravity from the SD system, will then be routed to a sample divider or directly to the desired sample
collection point.
FIGURE 2-1, TYPICAL INSTALLATION, MODEL TD SAMPLING SYSTEM

6
2.2 Optional Features
The certified drawings indicate which, if any, optional features are included with a sampling system. Some of the
more frequently specified optional features are briefly described in the following list.
A. Controller arranged to initiate a sampling cycle based on quantity or volume of material passing through
conveying line rather than upon elapsed time periods.
B. An explosion proof sampler control is available in two enclosure classifications.
1. The NEMA 9 control with the rating of:
Class 2, Groups E, F & G, Division 1 & 2
2. The NEMA 7 control with the rating of:
Class 1, Groups C & D, Division 1 & 2
Class 2, Groups E, F & G, Division 1 & 2
C. Components of special materials, such as stainless steel or nedox coatings.
D. Programmable Controls to sequence the sampler and the sample collection equipment.
E. Abrasion resistant linings of urethane, AR carbon steel plate, 304 stainless steel or ceramic tile.
2.3 Material Sampled
Most materials from light to heavy density granules, pellets.
2.4 Sampler Construction
Standard sampler construction is of painted carbon steel.
Explosion-proof limit switches with the rating of:
Class 1, Groups C & D, Division 1 & 2
Class 2, Groups E, F & G, Division 1 & 2
An explosion-proof motor with the rating of:
Class 1, Groups D, Division 1 & 2
Class 2, Groups E, F & G, Division 1 & 2
Other materials and/or finishes appropriate to the operating environment and the material or product being
sampled may be used. Refer to the certified drawing(s) for any optional or special components installed on the
sampler.

7
III. GENERAL INSTALLATION REQUIREMENTS
3.1 Receiving Inspection
Carefully inspect the sampling system for damage as soon as it is received. Also, verify that the quantity of parts
or packages actually received corresponds to the quantity shown on the packing slip. Report any damage or
shortage to the delivering carrier as soon as possible. InterSystems' responsibility for the equipment ended with
acceptance by the delivering carrier. Refer to the bill of lading.
3.2 Pre-Installation Preparation
Note, before starting sampling system installation, study this manual, the certified drawing(s) furnished with the
system, and other applicable documents (including, but not limited to OSHA Regulations; the National Electrical
Code; and all other applicable federal, state, and local codes and regulations).
3.3 Location
The TD sampler is typically mounted on the end of a belt conveyor carrying the product to be sampled as in Figure
2-1. Install the sampler as it is shown and noted on the certified drawings. The sampler may or may not be
supplied with a partial or a whole conveyor discharge hood. Provide necessary access and maintenance
platforms for ease of maintenance.
The sampler is to be installed only as shown on the certified drawing(s). If an alternate mounting arrangement is
desired contact InterSystems prior to installation for proper guidance. The sampler is of a general design with
modifications specifically for your application. It may be necessary to rework the sampler in order for it to function
properly if you alter the application.
3.4 General Mounting Guidelines
DANGER
SAMPLER CANNOT SUPPORT ANY OTHER EQUIPMENT OR CONVEYING LINE!
COLLAPSE OF THE WHOLE SYSTEM CAN CAUSE DEATH, SERIOUS INJURY, AND
EXTENSIVE DAMAGE TO EQUIPMENT. PROPERLY SUPPORT ALL SPOUTS,
CONTAINERS, AND CONVEYING LINES.
The sampler needs to be installed, as shown and noted on the certified drawings.
A. Locate and mark the desired mounting location of the sampler.
B. Position the sampler. Weld and/or fasten in place.

8
3.5 Material Sample Transport Lines
The tubing used to transport material samples must be compatible with the operating environment and the
material sampled. Typically a 3.00 OD rigid tubing is directly connected to the sample outlet using a compression
type coupling. The tubing is then routed to the SD sample delivery system using the most direct route with the
fewest number of bends.
Make all connections airtight and make sure all interior surfaces of joints are smooth and flush. Any ragged or
raised tube ends will collect dust and debris as well as retard material flow. Air leaks can interfere with the
vacuum conveying system. Escaping sample material can contaminate surrounding atmosphere and equipment.
3.6 Controller Location
A. Use vibration isolation pads when mounting the control enclosure or mount the controller in a vibration-
free location.
B. Unless ordered for severe duty, locate controller so it is protected from water and dust.
C. Unless an explosion-proof rated controller was specifically ordered, DO NOT locate the controller in a
hazardous area.
D. Most applications require that the sampler be in easy view of the controller.
3.7 System Wiring
Refer to the certified electrical drawing(s) for specific wiring requirements.
The controller was completely assembled and tested with the sampler before it left the factory. The electrical
installation must comply with OSHA Regulations; the National Electrical Code; and all other applicable federal,
state, and local codes and regulations.
If wiring between the controller and the sampler unit is run through rigid conduit, use a short length of flexible
conduit to connect wiring to the sampler. This will isolate the rigid conduit from any vibration originating in the
product conveying line and sampler.
3.7.1 Electrical Power Requirements, System
Refer to the certified electrical drawing(s) to determine if other voltages or a larger service is required.
3.7.1.1 Controller
110/120 VAC, 50/60 Hz, Single Phase, 10 Amp Max. (does not include motor power requirements).
Optional - 220/240 VAC, 50/60 Hz, Single Phase, 5 Amp Max. (does not include motor power requirements).
3.7.1.2 Drive Motor
Refer to the certified drawing(s) of the TD sampler for motor size, horsepower, voltage, and current rating.

9
IV. OPERATIONS AND ADJUSTMENTS
DANGER
FAILURE TO OBSERVE ALL SAFETY RULES, WRITTEN AND IMPLIED, AND THOSE
SUGGESTED BY COMMON SENSE, CAN RESULT IN DEATH, SERIOUS INJURY, AND /OR
EQUIPMENT DAMAGE. LOCKOUT POWER BEFORE PERFORMING ANY MAINTENANCE.
4.1 Control Components And Their Functions
FIGURE 4-1, STANDARD NEMA 12 CONTROL PANEL DETAIL
Refer to the certified electrical drawing(s) for dimensions on control panels with optional features.

10
4.1.1 POWER OFF/ON Switch S-1
This toggle switch controls all electrical power to the controller and the sampler unit.
WARNING
THIS MACHINE STARTS WITHOUT WARNING. MOVING PARTS CAN CAUSE SEVERE
INJURY. CLEAR AREA PRIOR TO CONTROLLER START-UP.
4.1.2 POWER Pilot Light
This light is illuminated as long as power is available to the controller and the POWER switch (S-1) is set to ON.
4.1.3 TRAVERSE LEFT Pilot Light
This light will illuminate when the sample pelican is traversing left thru the product flow and will stay lit until the
sample pelican trips the limit switch on the left side.
4.1.4 TRAVERSE RIGHT Pilot Light
This light will illuminate when the sample pelican is traversing right thru the product flow and will stay lit until the
sample pelican trips the limit switch on the right side.
4.1.5 Digital Display Timer T-1 (Standard)
As arranged for use in this system, the timer operates in the DOWN & STOP mode. When the power is turned on
the illuminated display resets to the value dialed in to the Three Digit Preset and immediately the timer begins
timing down. When the illuminated display reads all zeroes (000), the timer has "timed out" and initiates a
sampling cycle. The sample pelican traverses through the product flow to collect a sample. The timer display
resets to the preset value and another timing interval is initiated. If the controller is shut off or the power is
interrupted, the timing cycle is terminated. When power is restored, the display is reset to the preset value and
another cycle begins. NOTE: The timer resets immediately upon timing out and initiating a sample cycle thus
providing a true time interval between samples.
A. External Settings
1. THE DISPLAY:
The high intensity blue fluorescent display consists of three digits and decimal point (if decimal is set
in tenths or hundredths position). Also, there is a blinking Timing Bar and a special Time-Out symbol.
The Timing Bar appears to the right of the digits and blinks once every second during timing. The
Timing Bar shows quickly that the timer is actively timing especially when the digits do not change
rapidly as in the "hours" ranges. When the delay relay is energized at time-out, a triangular Time-Out
symbol appears to the left of the digits. The Timing Bar blinks noticeably faster at time-out.

11
2. SETTING SWITCHES:
The three digits are set with the rotary switch knobs located beneath each digit. These knobs can be
rotated in either direction (CW or CCW), and they are "pull" removable if digit set security is desired.
Changing one or more digits, during timing, will instantly be reflected by an equivalent change in the
timer's display. Setting all three digits to zero will cause instant time-out of the timer.
B. Internal Settings
THE 365 DIGITAL DISPLAY TIMER MUST BE REMOVED FROM ITS HOUSING TO ALTER ANY OF
THE FOLLOWING SETTINGS.
1. TIME RANGE:
Decimal Point Location can be changed with the white plastic lever mounted behind the front face of
the timer. This lever moves into three positions. With finger force you can change its position and at
the same time observe the front of the timer. NOTE - this procedure sets the decimal point
electronically as well as visually.
Time Units (Sec/Min/Hr) are set by moving a small width metal arm in a slotted arc on the side plate
nearest to the units (Sec/Min/Hr) window. By depressing this arm slightly with a pencil or pen point, it
can be moved to a new position. The time units physically change in the timer's face and the timer is
electronically switched to the new units as well.
2. LINE FREQUENCY:
To set the proper line frequency, connect the jumper wire to either the 50 HZ or 60 HZ pin. These
pins are clearly marked on the side of the timer.
NOTE: THE TIMER CHASSIS AND THE HOUSING ARE POLARIZED SO THAT THE CHASSIS CANNOT
BE INSERTED INTO ITS HOUSING UPSIDE-DOWN. IF THE TIMER IS FORCED INTO THE HOUSING
UPSIDE-DOWN DAMAGE WILL RESULT.
4.1.6 Main Fuse
This fuse, located in a fuse block within the controller enclosure, protects the controller and sampler components
against overloads and short circuits.
For 110/120 VAC, 1PH operation use ONLY a Buss Type FNM, 4 Amp, 250 Volt Slo-Blo fuse or equal.
For 220/240 VAC, 1PH operation use ONLY a Buss Type FNM, 2 Amp, 250 Volt Slo-Blo fuse or equal.
Optional - For standard sampling systems with excess sample leg or auger.
For 110/120 VAC, 1PH operation use ONLY a Buss Type FNM, 10 Amp, 250 Volt Slo-Blo fuse or equal.
For 220/240 VAC, 1PH operation use ONLY a Buss Type FNM, 5 Amp, 250 Volt Slo-Blo fuse or equal.
4.1.7 Index Relay IR-1
This mechanical latching relay signals the sampler motor starter coils. When the relay coil receives a momentary
signal from the timer T-1 the maintained switch contacts change to the alternate position. Upon changing position
the opposite motor starter coil receives power, the motor starts and a sample is taken.

12
4.1.8 Reverse Delay Timer Relays
These timers monitor the amount of time the sample
pelican takes to traverse from one side to the other and will
force the starter to reverse if the sample cutter takes too
long to complete its traverse. If the sample cutter fails to
traverse fully accross the material flow and trip the limit
switch prior to timing out the starter will reverse the motor
direction an return the cutter to the position it was at prior
to starting. The sample cutter is designed to travel at fixed
speed of 20 inches per second. Use the following chart
when setting the timer settings. Note an additional half
second was added to the theoretical traverse time to allow
for acceleration.
4.1.9 Terminal Strip
This 20-position barrier terminal strip serves as the controller's interface and connection point for all external
circuits and for the components mounted on the enclosure's front panel. Refer to the certified electrical
drawing(s).
4.2 Sampler Mounted Electrical Components
4.2.1 Limit Switches, LS-1 & LS-2
One of these switches is actuated when the
sample cutter is in a rest position. Upon initiation
of a sample cycle the power is routed through the
normally closed contacts of the opposite limit
sample to the drive motor starter. The drive
motor starts and the sample cutter traverses
through the material flow towards the other side.
Upon reaching the opposite side the limit switch is
tripped. The opening of the normally closed
contacts removes power to the drive motor starter
thus stopping the sample cutter rotation. The
sample cutter remains on this side until another
signal to sample is given by the controller.
Correct wiring termination is essential to proper
sampler operation. Refer to figure 4-2, it shows
the limit switch utilized on the Exporter sampler
and the physical orientation of the proper wiring connections.
4.2.2 Drive Motor
This motor drives the sample cutter through a right angle gear reducer and a set of sprockets and chain. Verify
that the motor is turning the proper direction of rotation when wiring the system. On initial setup, jog the motor to
insure proper rotation.
MODEL
SIZE
STROKE RECOMMENDED
DELAY TIMER SETTING
18 15 1.3 sec
24 21 1.6 sec
30 27 1.9 sec
36 33 2.2 sec
42 39 2.5 sec
48 49 3.0 sec
54 55 3.3 sec
60 61 3.6 sec
66 67 3.9 sec
72 73 4.2 sec
FIGURE 4-2, LIMIT SWITCH CONNECTIONS

13
V. MAINTENANCE AND REPAIR
DANGER
FAILURE TO OBSERVE ALL SAFETY RULES, WRITTEN AND IMPLIED, AND THOSE
SUGGESTED BY COMMON SENSE, CAN RESULT IN DEATH, SERIOUS INJURY, AND /OR
EQUIPMENT DAMAGE. LOCKOUT POWER BEFORE PERFORMING ANY MAINTENANCE.
5.1 General Maintenance
A good maintenance program involves thorough general housekeeping, adequate periodic re-lubrication, and
replacement of worn or damaged components.
5.2 Periodic Inspection
At regularly scheduled intervals, while observing all safety precautions, observe the sampler as it operates.
Inspect for:
A. Loose or missing hardware
B. Noisy motor or motor/reducer bearings
C. Overheated motor or reducer
D. Adequate lubricant in gear reducer
E. Loose drive chain
F. Structural damage
G. Rust or corrosion
H. Damaged wiring, including exposed conductors and connections
I. Make sure that all guards are in place and that all warning labels are in place and legible. Section
I, GENERAL SAFETY INFORMATION, explains the purpose and intended location of the warning
signs. Warning signs are an important part of any safety program; replace any missing signs
IMMEDIATELY!

14
5.3 Lubrication
5.3.1 Drive Chain, Sprockets & Idler Shaft
The drive chain, sprockets & idler shaft have been greased at the factory. The chain should be thoroughly
cleaned and re-greased once a year using a multi-purpose grease. The idler shaft should also be greased at the
same time.
5.3.2 Gear Reducer
The gear reducer is shipped filled with oil. Check the oil level every six months and add oil if required. Under
normal sampler operating conditions the oil should be changed once every two years.
Use a gear lubricant with an AGMA #8 rating for normal operating conditions. Use a synthetic gear lubricant such
as "Mobil SHC 634" for extreme operating conditions.
5.4 Mechanical Repair Procedures
5.4.1 Drive Chain Adjustment
The drive chain will need adjustment periodically to maintain proper tension. The chain is attached to the sample
pelican drive nose by means of two eye bolts. Loosen, adjust and re-tighten the eye bolt nuts to increase or
decrease chain tension. The chain only needs to be tight enough to prevent any sag or slack. As the chain wears
it will stretch to a point where the adjustment of the eye bolts will no longer permit further tightening. Shorten the
chain by removing a link if necessary.
5.4.2 Limit Switch Adjustment
Loosen and adjust the limit switch arm if required. The limit switches trip on the drive nose of the sampler and
signal the control to remove power from the motor. They should trip before the sample pelican completes its
traverse. When a limit switch trips the sample pelican should gently coast to a stop under the dust seal and up
against the bumper.
5.4.3 Sample Cutter Blade Replacement
When following the instructions below, refer to the applicable drawing of the sampler. Reference the drawing of
the sampler on page 21 and the certified drawing(s).
A. Shutoff and lockout all power (electrical, pneumatic and hydraulic).
B. Shut down conveying line.
C. Open the seal door near the sample cutter.
D. Remove the 1/4-20UNC hex head bolts fastening the sample cutter to the sample pelican.
E. Using a utility knife, cut the caulking seal around the bottom of the cutter blade and remove.
F. Install the new cutter blade on the sample pelican.
G. Re-install the 1/4-20UNC hex head bolts fastening the sample cutter to the sample pelican.
H. Re-caulk the joint between the cutter blade and the sample pelican to ensure a tight seal.

15
I. Close Re-install the inspection cover on the housing.
J. Restore power to the sampler and operate it through several collection cycles.
5.4.4 Sample Cutter Seals Replacement
When following the instructions below, refer to the applicable drawing of the sampler. Reference the drawing of
the sampler on page 21 and the certified drawing(s).
A. Shutoff and lockout all power (electrical, pneumatic and hydraulic).
B. Shut down conveying line.
C. Open the seal doors on the side of the housing.
D. Remove the 5/16-18UNC wing nuts fastening the sample cutter seal brackets to the baffle. Avoid
dropping the assemblies inside the sampler.
E. Wrap the new seals around the seal brackets and re-install.
F. Check to see that the cutter fits snugly under the pelican seals.
G. Restore power to the sampler and operate it through several collection cycles.
5.4.5 Drive Clutch Adjustment
The drive clutch may need adjustment if it starts to slip. When following the instructions below, refer to the clutch
drawing page 16.
A. Shutoff and lockout all power (electrical, pneumatic and hydraulic).
B. Shut down conveying line.
C. Open the drive cover access panel.
D. Fully loosen the three (3) tension screws (items 10F).
E. Loosen the adjusting nut set screw (item 10E) at least nine turns.
F. Turn the adjusting nut (item 10D) clockwise to finger tightness. Tighten an additional 1/2 to 3/4 turn.
G. Turn the adjusting nut to position the adjusting nut set screw (item 10E) in the nearest spline on the
clutch hub (item 10A) and tighten the set screw. Do not tighten the set screw on the threads of the
hub.
H. Tighten the three (3) tension screws (items 10F) and close the drive cover access panel.
I. Restore power to the sampler and operate it through several collection cycles.
5.4.6 Drive Clutch, Facings, Bushing & Sprocket Replacement
The drive clutch may need to be replaced if adjustment fails to prevent slippage. When following the instructions
below, refer to the clutch detail figure 5-1 on page 16.

16
A. Shutoff and lockout all power (electrical, pneumatic and hydraulic).
B. Shut down conveying line.
C. Open the drive cover access panel.
D. Fully loosen the three (3) tension screws (items 10F).
E. Loosen the adjusting nut set screw (item 10E) at least nine turns.
F. Remove the adjusting nut (item 10D), splined plate (item 10B), friction facing (item 10C), sprocket
(item 12) & bushing (item 11).
G. Re-assemble the clutch using the new facings (items 10C), sprocket (item 12) & bushing (item 11).
H. Turn the adjusting nut (item 10D) clockwise to finger tightness. Tighten an additional 1/2 to 3/4 turn.
I. Turn the adjusting nut to position the adjusting nut set screw (item 10E) in the nearest spline on the
clutch hub (item 10A) and tighten the set screw. Do not tighten the set screw on the threads of the
hub.
J. Tighten the three (3) tension screws (items 10F) and close the drive cover access panel.
K. Restore power to the sampler and operate it through several collection cycles.
FIGURE 5-1, DRIVE CLUTCH DETAIL FIGURE 5-1, DRIVE CLUTCH DETAIL

17
VI. TROUBLESHOOTING
6.1 General TD Sampler Troubleshooting
DANGER
CARELESS OR ACCIDENTAL RESTORATION OF POWER CAN RESULT IN DEATH OR
SERIOUS INJURY. MAKE CERTAIN AREA IS CLEAR BEFORE REMOVING LOCKOUTS.
SYMPTOM POSSIBLE CAUSE CORRECTIVE ACTION
Sampler does not cycle Power switch OFF. Turn power switch ON.
(Power light Off). Circuit breaker is open. Reset breaker.
Main fuse is blown. Replace.
Faulty supply wiring. Correct. Refer to certified electrical
schematic.
Defective power switch.
Replace switch.
Sampler does not cycle
(Power light On).
Faulty system wiring. Correct. Refer to certified electrical
schematic.
Motor power off. Turn on.
Motor starter heaters tripped. Reset.
Motor burnt out. Replace.
Motor thermal overload tripped. Allow motor to cool & reset.
Defective timer T-1.
Replace timer if line voltage is
present across #1 & #2 on timer T-1.
Sampler leaks air or material
continuously out the sample
Sample cutter not stopping under
the seals.
Adjust limit switch. Refer to Section
5.4.2.
discharge. Sampler installed in a pressurized
conveying line.
Eliminate pressure or relocate
sampler.
Sample cutter worn. Inspect & replace. Refer to Section
5.4.3.
Sample cutter seals deteriorated.
Inspect & replace. Refer to Section
5.4.4.
Sampler makes loud banging
noises.
Limit switches not set properly.
Adjust limit switch. Refer to Section
5.4.2.

18
VII. REPLACEMENT PARTS
7.1 Scope
The certified drawings list the non-standard components that have been incorporated into the equipment.
InterSystems, Inc. normally stocks non-fabricated parts and non-custom OEM parts. Replacement parts for any
other components, including fabricated parts and custom OEM components can be supplied upon request.
7.2 Ordering Parts
Direct parts orders or requests for technical assistance to your sales representative or to:
InterSystems, Inc.
13330 "I" St.
Omaha, NE. 68137
Phone: (402) 330-1500
FAX: (402) 330-3350
Please have available the MODEL NUMBER, SERIAL NUMBER and CUSTOMER ORDER NUMBER of the
equipment in question as well as the location where the sampler is INSTALLED.
7.3 Replacement Parts
The InterSystems, Inc. sampler is a quality built piece of machinery. As with any machine, parts do wear out and
fail. It is InterSystems' recommendation that a small supply of spare parts be kept on hand to cover any minor
breakdowns. A separate priced Spare Parts List will be sent identifying the suggested spare parts. It is also
necessary to check the certified drawings, which will list any special or custom components utilized on this
equipment.
7.4 Repair Kits
The Following chart lists repair kits and parts that are available from InterSystems. These kits are offered as a
more economical solution by rebuilding the defective part rather than replacing it. However in some cases the part
may be beyond repair and replacement will be necessary.
Product Code Description
34769 Standard SAE 80W-90 EP Gear Lubricant Oil Quart (Pennzoil 4096)
529601 Optional Synthetic Gear Lubricant Oil Quart (Mobil SHC634)
35342 #50 Friction Facing (item #10C on figure 5-1)
35527 Limit Switch Contact Block 1 N.O. 1 N.C.

19
7.4.1 Sampler Parts Listing TD (see Figure 7-1)
ITEM NO. PART NO. DESCRIPTION QTY
1 34672 IDLER MOUNT BASE 1
2 34007 IDLER SPROCKET 1
3 34008 IDLER SHAFT 1
4 34376 GEAR REDUCER 1
5 34379 3 HP NEMA 9 MOTOR 1
6 34661 GEAR BOX SPACER 4
7 514487 RUBBER BUMPER 2
8 522580 SPACER (RUBBER BUMPER) 2
9 34760 CLUTCH SPRING 1
10 34370 CLUTCH 1
11 34371 CLUTCH BUSHING 1
12 34374 CLUTCH SPROCKET 1
13 34505 WORM CLAMP 2
14 34033 #60H OFFSET LINK 2
15 34758 #60H CONNECTOR LINK A/R
16 510811 EYE BOLT W/ OFFSET LINK 2
17 35355 ADJ LS LEVER ARM 2
18 35352 LIMIT SWITCH BRKT 2
19 35354 LIMIT SWITCH 2
20 35073 3 ID GUM RUBBER TUBE A/R
21 SEE CERT. DWG. PELICAN DUST SEAL BRACKET 2
22 SEE CERT. DWG. SAMPLE PELICAN 1
23 SEE CERT. DWG. CUTTER BLADE 1
24 SEE CERT. DWG. SAMPLE WITHDRAWL TUBE 1
25 SEE CERT. DWG. BAFFLE SET (2 PIECES) 1
26 SEE CERT. DWG. EXPANDED METAL RAIL GUARD 2
ITEM
NO.
PART
NO.
DESCRIPTION MACHINE SIZE
(CONVEYOR BELT WIDTH)
18 24 30 36 42
QTY (IN FEET)
27 34029 #60H ROLLER CHAIN 7.0 8.0 9.0 10.0 11.0
28 34499 3 ID PLASTIFLEX HOSE 2.5 3.0 3.5 4.0 5.0
ITEM
NO.
PART
NO.
DESCRIPTION MACHINE SIZE
(CONVEYOR BELT WIDTH)
48 54 60 66 72
QTY (IN FEET)
27 34029 #60H ROLLER CHAIN 13.0 14.0 15.0 16.0 17.0
28 34499 3 ID PLASTIFLEX HOSE 6.0 6.5 7.0 7.5 8.0
Table of contents
Other GSi Sampler manuals
Popular Sampler manuals by other brands

MBV
MBV Millipore Atmos MAS-100 quick start guide
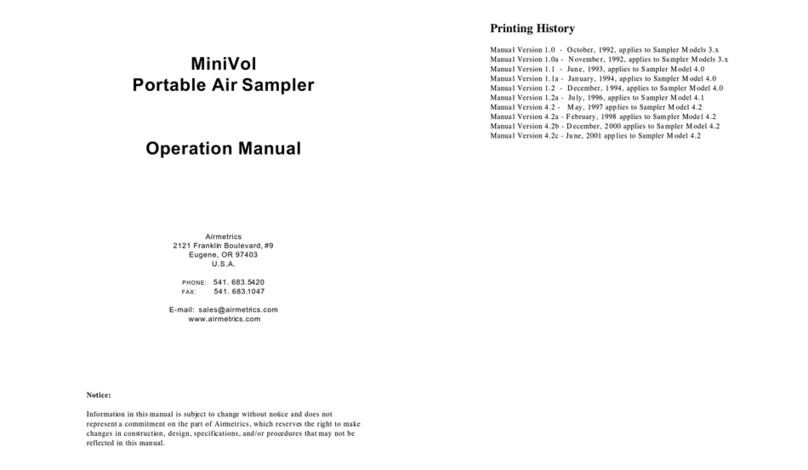
Airmetrics
Airmetrics MiniVol Operation manual
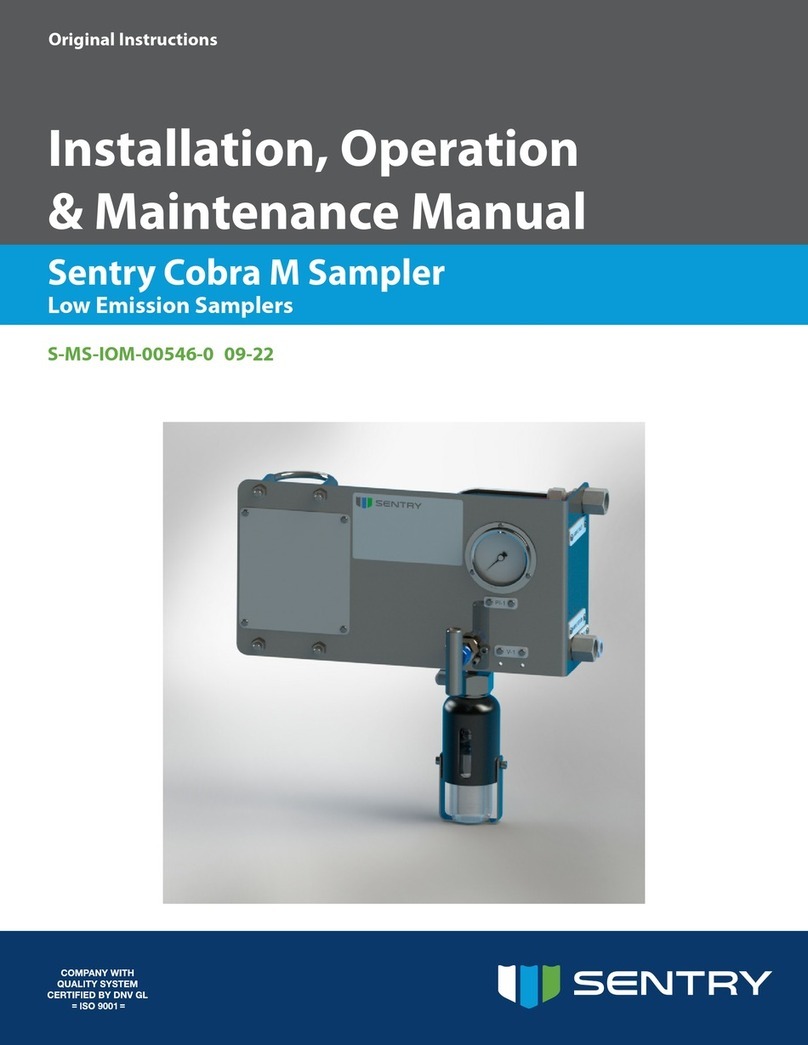
Sentry
Sentry Cobra M Installation, operation & maintenance manual
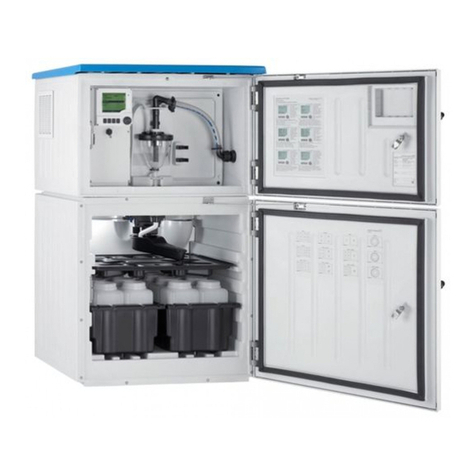
Endress+Hauser
Endress+Hauser Liquistation CSF34 Brief operating instructions
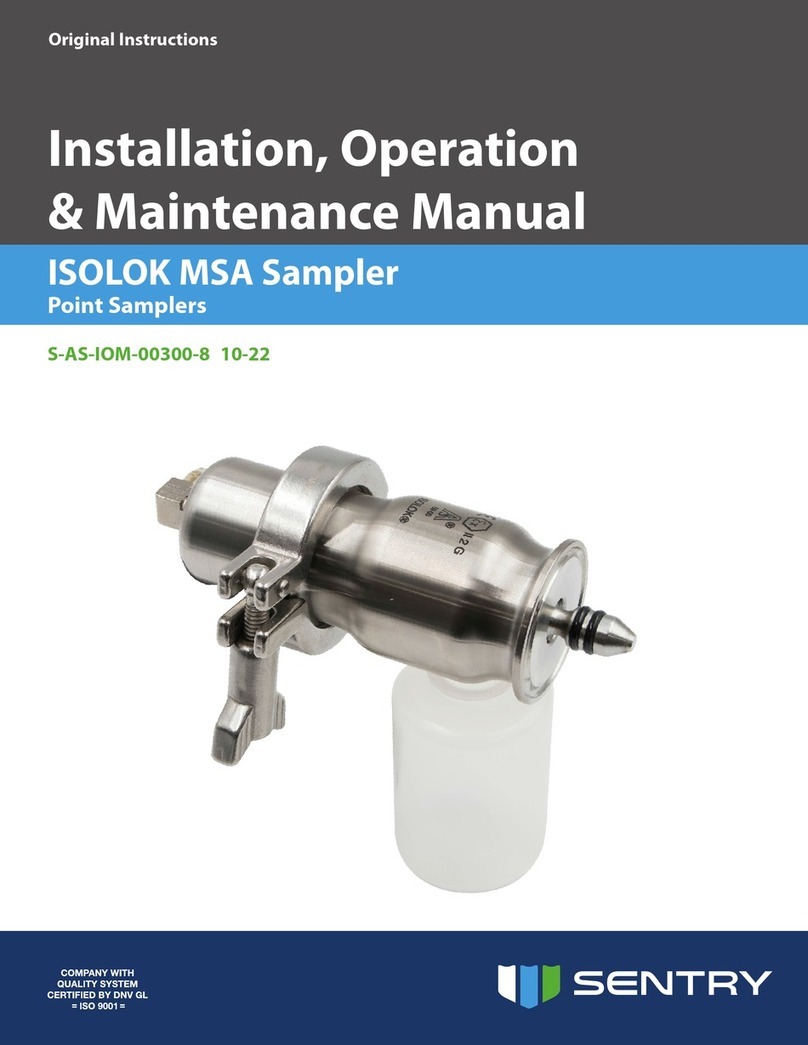
Sentry
Sentry ISOLOK MSA Installation, operation & maintenance manual
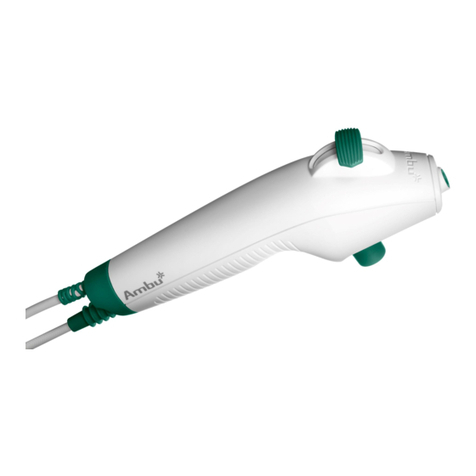
Ambu
Ambu aScope 4 Broncho Regular Instructions for use