halstrup-walcher PSD4 Series User manual

Bus description
PSD4xx positioning system – CANopen

General
7100.006424_Bus description_PSD4xx_CA_J_ENG 22022-08-15
halstrup-walcher GmbH
Stegener Straße 10
79199 Kirchzarten
Germany
Tel. +49 7661 39 63-0
info@halstrup-walcher.com
www.halstrup-walcher.com
© 2022, Be
The manufacturer owns the copyright to this instruction manual. It contains technical data,
instructions and drawings detailing the device’s features and how to use them. It must not be
copied either wholly or in part or made available to third parties.
The instruction manual is part of the product. Please read this manual carefully, follow our
instructions, and pay special attention to the safety information provided. This instruction manual
should be available at all times. Please contact the manufacturer if you do not understand any
part of the instructions.
The manufacturer reserves the right to continue developing this device model without
documenting such development in each individual case. The manufacturer will be happy to
determine whether this manual is up-to-date.

General
7100.006424_Bus description_PSD4xx_CA_J_ENG 3 2022-08-15
Table of contents
1General ......................................................................................................................... 4
2Start-up ......................................................................................................................... 5
2.1 Set the device address ......................................................................................6
2.2 Set the baud rate ...............................................................................................7
2.3 CAN terminating resistor ..................................................................................8
2.4 Switch the device on .........................................................................................9
3Description of CANopen ............................................................................................ 10
3.1 Status LEDs......................................................................................................10
3.2 Table of entries implemented from object dictionary ...................................11
3.3 Table of device-dependent Min., Max. and Default values ...........................21
3.4 Define PDOs.....................................................................................................24
3.5 Detailed description of status bits ..................................................................24
3.6 Detailed description of control bits.................................................................28
4Functions .................................................................................................................... 30
4.1 Starting a positioning run ...............................................................................30
4.2 Types of positioning........................................................................................31
4.2.1 Positioning run
with
loop ..........................................................................31
4.2.2 Positioning run
without
loop.....................................................................32
4.2.3 Manual run.................................................................................................32
4.3 Velocity, acceleration and deceleration..........................................................32
4.4 Maximum start-up and operating current......................................................33
4.5 Behaviour of the drive in case of blocking.....................................................33
4.6 Behaviour of the drive if it is turned manually (readjustment function).......34
4.7 Calculate the absolute physical position........................................................34
4.8 Use of the “Upper mapping end” parameter ................................................38
4.8.1 Delivery state .............................................................................................38
4.8.2 Shifting the positioning range upwards starting from the delivery state
39
4.8.3 Shifting the positioning range downwards starting from the delivery
state 41
4.8.4 Shifting the positioning range depending on the actual position...........42
4.8.5Step-by-step instructions for determining the positioning range...........44
4.9 Set the spindle pitch........................................................................................46
4.10 Abort the run when the master fails ...........................................................46
4.11 Reference runs .............................................................................................47
4.12 Run drive in reverse.....................................................................................48
5Technical data ............................................................................................................ 49
6Notes........................................................................................................................... 50

General
7100.006424_Bus description_PSD4xx_CA_J_ENG 42022-08-15
1 General
This bus description is to be used for the commissioning and integration of the drive into a field
bus system.
Technical data for the electrical connections of your drive can be found in the electrical connector
and pin assignment description on the website:
www.halstrup-walcher.de/technicaldocu
Please search for “PSD” and select your type, click on “Instruction manuals” and download the
“conntector and pin assignment” offered for your bus system.

Start-up
7100.006424_Bus description_PSD4xx_CA_J_ENG 5 2022-08-15
2 Start-up
WARNING Risk of injury if used inappropriately.
The device must be installed by trained technical personnel.
WARNING Risk of burns due to hot drive.
The drive can become very hot during operation.
Allow the drive to cool before touching it.
WARNING Risk of crushing due to rotary movement.
Do not reach into the working area of the drive when it is still
turning.
The user/operator must ensure appropriate protective
measures are taken.
WARNING Incorrect assembly can lead to the destruction of the drive.
WARNING Check that the supply lines are not pinched or crushed.
Lay the supply lines according to the general and specific local
assembly regulations.
If the supply lines have not been delivered together with the
device, please select suitable cables for the application.
Do not operate the direct drive if the supply lines are
noticeably damaged.
WARNING Risk of injury. High contact voltages can occur in the case of
malfunctions.
This can be prevented by grounding.
ATTENTION The drive must be protected against excessive heating.
The user/operator must ensure appropriate protective measures are
taken.
ATTENTION Never apply force to the housing of the drive, e.g. for supporting
weight.

Start-up
7100.006424_Bus description_PSD4xx_CA_J_ENG 62022-08-15
2.1 Set the device address
You can assign a unique device address using the address switch.
Note: If these address switches are set to 00, the address can be set via the CAN bus
with SDO #2026.
The device controls and status elements are located under the sealing plug. You will need a non-
conducting pointed object to adjust the switches (e.g. a screwdriver).
Set the tens and units on the respective address switches.
Turn the device off and on again or use the reset command via the control unit to accept the new
setting. The device address is now set and the setting is active.
Note: The delivery state is 00; the PSD4xx identifies itself using address 1 at the bus.
Note: If you set the address using the switches (i.e. switches set to > 0) you cannot
change this value using the CAN bus.
Note: The yellow LED shows the motor voltage status, the red and green LEDs show the
CANopen status.
Note: Always re-attach the protective cap after setting the address. This will prevent dust
and contaminants from entering the device.

Start-up
7100.006424_Bus description_PSD4xx_CA_J_ENG 7 2022-08-15
2.2 Set the baud rate
You can set the baud rate using the sliding switches S2-S4 (DIP switch 2-4).
The device controls and status elements are located under the sealing plug. You will need a non-
conducting pointed object to adjust the switches.
Please refer to the following table to find the correct baud rate settings and adjust the sliding
switches S2-S4 (DIP switch 2-4) accordingly:
Table: Baud rate:
S2 S3 S4 Description
OFF OFF OFF Set baud rate via bus (default = 500 kBaud)
ON OFF OFF 20 kBaud
OFF ON OFF 50 kBaud
ON ON OFF 125 kBaud
OFF OFF ON 250 kBaud
ON OFF ON 500 kBaud
OFF ON ON 800 kBaud
ON ON ON 1000 kBaud
Turn the device off and on again or use the reset command via the control unit to accept the new
setting.
Note:
Maximum bus length Baud rate
250 m 250 kBaud
100 m 500 kBaud

Start-up
7100.006424_Bus description_PSD4xx_CA_J_ENG 82022-08-15
Note: If the sliding switches S2-S4 are set to OFF, the baud rate is set via the CAN bus
with SDO #2027.
Note: If at least one sliding switch S2-S4 is ON, the baud rate cannot be changed via the
CAN bus.
2.3 CAN terminating resistor
You can use the sliding switch S1 (DIP switch 1) to set the CAN terminating resistor (120 Ω).
Note: For a line topology, the bus termination is at both ends of the network.
The device controls and status elements are located under the sealing plug. You will need a non-
conducting pointed object to adjust the switches (e.g. a screwdriver).
Please refer to the following table for the terminating resistor settings and adjust the sliding switch
S1 (DIP switch 1) accordingly:
S1 Description
OFF Deactivate the terminating resistor
ON Activate the terminating resistor

Start-up
7100.006424_Bus description_PSD4xx_CA_J_ENG 9 2022-08-15
2.4 Switch the device on
To turn on the PSD4xx, install the PSD in the correct position according to the assembly
instructions. You can find information about installing the drive as well as electrical connections
and pin assignments at the following link: www.halstrup-walcher.de/technicaldocu
Please search for “PSD” and select your type, click on “Instruction manuals” and download the
“conntector and pin assignment” offered for your bus system.
The PSD4xx must be grounded before the power supply cable is connected. The grounding cable
must be connected to the correct position on the PSD4xx and to the ground potential (e.g.
machine base).
Note: The positioning system should be connected to the machine base using the
shortest possible cable. The minimum wire cross-section of the grounding cable is
1.5 mm².
Once the PSD has been grounded, it can be connected to the power supply and the
communication interface. The drive is now ready for operation.
Grounding screw

Description of CANopen
7100.006424_Bus description_PSD4xx_CA_J_ENG 10 2022-08-15
3 Description of CANopen
The CAN bus interface uses the CANopen protocol in accordance with CiA DS 301 Version 4.02:
-One transmit and one receive SDO per device
-One asynchronous transmit and receive PDO, active by default
-One heartbeat object every 500 ms
3.1 Status LEDs
The following LEDs are located under the sealing plug:
Green LED (gn) = RUN LED in accordance with CANopen:
Single flashes:
CAN stop
Continuous flashing:
CAN preoperational
Continuously illuminated: CAN operational
Red LED (rd) = ERROR LED in accordance with CANopen:
Single flashes: CAN-transmitter or -receiver has reached its warning limit
Double flashes: Guard event has occurred
Triple flashes:
Sync failure
Continuously illuminated:
CAN bus OFF
Yellow LED (ye) = Display actuator voltage:
Off:
Motor voltage too low or too high
On:
Motor voltage OK
Flashing at 0.5 Hz Motor voltage OK and drive in the delivery state (for parameter values
and axle positions)

Description of CANopen
7100.006424_Bus description_PSD4xx_CA_J_ENG 11 2022-08-15
3.2 Table of entries implemented from object dictionary
Designation
Index
no.
Function
Range of
values
Back
up?
Delivery
state
R/W
Device type
1000
Returns a “0” when read
0
0
R
Error register
1001
Bit 0: General error
Bit 4: Communication error
8 bit
0
R
Error list
1003
Sub index 0: No. of indices
Sub-index 1 and 2: last
emergency errors occurred
8 bit
32 bit
0
0
R
R
Sync ID
1005
COB ID for the sync command
32 bit
No
80h
R/W
Comm cycle
1006
Communication cycle time
32 bit
No
0
R/W
Sync window
1007
Synchronous window time
32 bit
No
0
R/W
Guard time
100C
Guard time in ms
0 = off
16 bit
No
0
R/W
Lifetime
100D
Lifetime factor
8 bit
No
0
R/W
Emcy ID
1014
COB ID for emergency
message
32 bit
80h +
device
address
R
Emcy inhibit
1015
Inhibit time for emergency
message
16 bit
No
0
R/W
Consumer
heartbeat
1016
Sub index 0: No. of indices
(= 2)
Sub index 1 and 2:
Bit 15-0: Heartbeat time in ms
Bit 23-16: Node ID of producer
8 bit
32 bit
No
2
0
R
R/W
Heartbeat
producer
1017
Cycle time for heartbeat via
PSD4xx
0 = off
16 bit
No
500
R/W
Identity
1018
Sub index 0: No. of indices
(= 4)
Sub 1: Vendor-ID
(= 0x000002D8)
Sub 2: Product code
(depends on the device
type)
Sub 3: Revision number (= 0)
Sub 4: Serial number (= 0)
8 bit
32 bit
32 bit
32 bit
32 bit
4
R
R
R
R
R

Description of CANopen
7100.006424_Bus description_PSD4xx_CA_J_ENG 12 2022-08-15
Designation
Index
no.
Function
Range of
values
Back
up?
Delivery
state
R/W
Receive
PDO 1
communi-
cation
parameter
1400
Sub index 0: No. of indices
Sub 1: COB ID of this PDO
8 bit
32 bit
No
0
200h +
device
address
R
R/W
Sub 2: PDO type
8 bit
No
0xFF
R/W
Receive
PDO 1
mapping
1600
Sub index 0: No. of indices
(= 3)
Sub 1: 0x20240010
Sub 2: 0x00000010
Sub 3: 0x20010020
8 bit
32 bit
32 bit
32 bit
3
R
R
R
R
Transmit
PDO 1
communi-
cation
parameter
1800
Sub index 0: No. of indices
Sub 1: COB ID of this PDO
8 bit
32 bit
No
0
180h +
device
address
R
R/W
Sub 2: PDO type
Sub 3: Inhibit time
8 bit
16 bit
No
No
0xFF
1000
(100 ms)
R/W
R/W
Sub 5: Event time
16 bit
No
0
R/W
Transmit
PDO 1
mapping
1A00
Sub index 0: No. of indices
(= 3)
Sub 1: 0x20250010
Sub 2: 0x20300010
Sub 3: 0x20030020
8 bit
32 bit
32 bit
32 bit
3
R
R
R
R
2000:
0...9
10 general purpose registers
32 bit
Yes
0
R/W
Target value
2001
Target position
Value in 1/100 mm (for default
values of numerator,
SDO #2010 and denominator
SDO #2011)
±31 bit
No
0
R/W

Description of CANopen
7100.006424_Bus description_PSD4xx_CA_J_ENG 13 2022-08-15
Designation
Index
no.
Function
Range of
values
Back
up?
Delivery
state
R/W
Actual value
2003
Current actual position;
value in 1/100 mm
(for default values of
numerator, SDO #2010 and
denominator SDO #2011)
Writing to this index number
causes the current position to
be “referenced” to the
transferred value
±31 bit
No
R/W
Referencing
value
2004
Correction factor for the target,
actual and limit switch values
±31 bit
Yes
0
R/W
Positioning
window
2006
Permissible difference between
target and actual values for the
“position reached” bit
The maximum setting value
changes according to the same
factor as the resolution
Value range for standard
settings of numerator
(SDO #2010) and denominator
(SDO #2011): 1…100 steps
0.0025
...0.25
rotations
16 bit
Yes
2
R/W
Actual value
assessment,
numerator
2010
These values can be used to
set a desired user resolution to
the drive.
For a numerator factor of 400,
the spindle pitch/resolution is
stated in the denominator factor
e.g.: Spindle pitch 1.5 mm with
resolution 1/100 mm:
numerator = 400,
denominator = 150
1...
10000
16 bit
Yes
400
R/W
Actual value
assessment,
denominator
2011
1...
10000
16 bit
Yes
400
R/W
Target rpm
Posi
2012
Maximum rpm to be used for
positioning runs;
value in rpm
see
chap. 3.3
16 bit
Yes
see
chap. 3.3
R/W
Target rpm
Manual
2013
Maximum rpm to be used for
manual runs;
value in rpm
see
chap. 3.3
16 bit
Yes
see
chap. 3.3
R/W

Description of CANopen
7100.006424_Bus description_PSD4xx_CA_J_ENG 14 2022-08-15
Designation
Index
no.
Function
Range of
values
Back
up?
Delivery
state
R/W
Maximum
current
2014
Applies after the end of the
start-up phase (during start-up
phase, the value #2018
applies);
value in mA
see
chap. 3.3
16 bit
Yes
see
chap. 3.3
R/W
Upper limit
2016
Maximum permitted target
position
Permissible values:
(Upper mapping end
- 1200 .. 1,611,600 *
denominator/numerator)
For models with an auxiliary
gearbox, the range of values is
reduced in accordance with the
gear ratio.
±31 bit
Yes
see
chap. 3.3
R/W
Lower limit
2017
Minimum permissible target
position
Permissible values:
(Upper mapping end
- 1200 .. 1,611,600 *
denominator/numerator)
For models with an auxiliary
gearbox, the range of values is
reduced in accordance with the
gear ratio.
±31 bit
Yes
See
chap. 3.3
R/W
Max. start-up
current
2018
Value in mA
See
chap. 3.3
16 bit
Yes
See
chap. 3.3
R/W
Time period
for start-up
current
2019
Value in ms
10...
1000
16 bit
Yes
200
R/W
Rpm limit for
aborting run
201A
Value in % of the target rpm
30...90
16 bit
yes
30
R/W
Time elapsed
until speed
falls below
rpm limit for
aborting run
201B
Value in ms
50...500
16 bit
yes
200
R/W
Acceleration
201C
Value in rpm per second
see
chap. 3.3
16 bit
Yes
see
chap. 3.3
R/W

Description of CANopen
7100.006424_Bus description_PSD4xx_CA_J_ENG 15 2022-08-15
Designation
Index
no.
Function
Range of
values
Back
up?
Delivery
state
R/W
Deceleration
201D
Value in rpm per second
see
chap. 3.3
16 bit
Yes
see chap.
3.3
R/W
Loop length
201F
Minimum number of
increments, in which the drive
runs to a target in a specified
direction.
Value in increments
(0 no loop)
The sign determines the
direction of the loop:
Positive loop to larger values
Negative loop to smaller
values
Value range for standard
settings of numerator
(SDO #2010) and denominator
(SDO #2011):
-4000 .. -10 increments and
10 .. 4000 increments and 0
0.025
…10
rotations
or
-0.025
… -10
rotations
or
0
±31 bit
Yes
250
incre-
ments
R/W
Control word
2024
Bit 0: Manual run to larger
values
Bit 1: Manual run to smaller
values
Bit 2: Transfer target value
(During target value
transmission using
PDOs, the target value
is accepted only when
this bit is set.)
Bit 4: Release: The axle will
only run if this bit is set.
Bit 6: Run without loop
Bit 10: Release readjustment
Bit 13: Toggle bit
All other bits are reserved and
must be set to 0
16 bit
No
0
R/W

Description of CANopen
7100.006424_Bus description_PSD4xx_CA_J_ENG 16 2022-08-15
Designation
Index
no.
Function
Range of
values
Back
up?
Delivery
state
R/W
Status
2025
Bit 0: Target position reached
Bit 1: Reserved
Bit 2: Toggle bit
Bit 3: Reserved
Bit 4: Motor power present
Bit 5: Positioning run aborted
Bit 6: Drive is running
Bit 7: Temperature exceeded
Bit 8: Movement opposite loop
direction
Bit 9: Error
Bit 10: Positioning error (block)
Bit 11: Manual displacement
Bit 12: Incorrect target value
Bit 13: Motor power was
missing
Bit 14: Positive range limit
Bit 15: Negative range limit
0..FFFFh
16 bit
R
CAN address
2026
Address of the drive
(if the address is set via the
CAN bus)
If the address switches are
used (i.e. switch position set to
> 0), this value cannot be
changed.
1...127
16 bit
Yes
1
R/W
Baud rate
2027
0: 20 kBaud 4: 500 kBaud
1: 50 kBaud 5: 800 kBaud
2: 125 kBaud 6: 1000 kBaud
3: 250 kBaud
If the baud rate switch is in use
(i.e. switch position not set to
OFF-OFF-OFF), this value
cannot be changed.
0...6
16 bit
Yes
4
R/W

Description of CANopen
7100.006424_Bus description_PSD4xx_CA_J_ENG 17 2022-08-15
Designation
Index
no.
Function
Range of
values
Back
up?
Delivery
state
R/W
Upper
mapping end
2028
Definition of the positioning
range relative to the absolute
value encoder
Permissible values:
(current position + 3 rotations)
… (current position +
4029 rotations)
For models with an auxiliary
gearbox, the range of values is
reduced in accordance with the
gear ratio.
±31 bit
Yes
see
chap. 3.3
R/W
Maximum
holding
current
202B
Holding current at standstill;
in mA
see
chap. 3.3
16 bit
Yes
see
chap. 3.3
R/W
Direction of
rotation
202C
0: Clockwise
(when looking at the output
shaft)
1: Counter clockwise
0 or 1
16 bit
Yes
0
R/W
Actual rpm
2030
Current speed; in rpm
±15 bit
R
Max. actual
current
during last
run
2031
Max. actual current during last
run; in mA
16 bit
R
Actual
current
2033
Actual current; in mA
16 bit
R
U control
203A
Current supply voltage to
control unit, in 0.1 V
16 bit
R
U motor
203B
Current supply voltage to
motor, in 0.1 V
16 bit
R
UMot limit
203C
Voltage limit for bit “Motor
power present” given in
increments of 0.1 V
180...240
16 bit
Yes
185
R/W
UMot filter
203D
Average time for measuring
UMot voltage; given in steps of
1 ms
100...
1000
16 bit
Yes
100
R/W
Temperature
limit
203E
Upper temperature limit in °C
10...80
16 bit
Yes
80
R/W
Device
temperature
203F
Internal device temperature in
°C (accuracy: ± 5 K)
±15 bit
R

Description of CANopen
7100.006424_Bus description_PSD4xx_CA_J_ENG 18 2022-08-15
Designation
Index
no.
Function
Range of
values
Back
up?
Delivery
state
R/W
Production
date
2040
Year and week of manufacture
(given as an integer)
YYWW
16 bit
R
Serial
number
2041
Device serial number
0...65535
16 bit
R
Max. holding
current at
end of run
2042
Max. holding current at end of
run; in mA
see
chap. 3.3
16 bit
Yes
see
chap. 3.3
R/W
Duration of
max. holding
current at
end of run
2043
Duration of max. holding
current at end of run; in ms
0…1000
16 bit
Yes
200
R/W
Device type
204D
One of the following device
types from the PSD series
(the last 2 digits of the 5-digit
numbers refer to the diameter
of the output shaft, e.g. 42208
8 mm shaft):
40105, 40108, 40114, 40308,
40314, 41105, 41108, 41114,
41308, 41314, 42208, 42214,
42414, 42614, 42814, 43208,
43214, 43414, 43614, 43814,
48005, 48008, 48014, 48108,
48114, 49005, 49008, 49014,
49108, 49114
16 bit
R
Version
204E
Software version number
16 bit
R

Description of CANopen
7100.006424_Bus description_PSD4xx_CA_J_ENG 19 2022-08-15
Designation
Index
no.
Function
Range of
values
Back
up?
Delivery
state
R/W
Delivery state
204F
Writing a “-5”:
Resets the drive (corresponds
to switching the control voltage
off and on again)
Writing a “-4”:
Resets all parameters to the
delivery states (CAN address
SDO #2026 to 1, baud rate
SDO #2027 to 500 kBaud),
without saving the parameters
in EEPROM, without a start-up
reference loop and without
positioning in the middle of the
measurement range.
Writing a “-3”:
Resets all parameters to the
delivery states (without
changing the CAN address and
baud rate), without saving the
parameters in EEPROM,
without a start-up reference
loop and without positioning in
the middle of the measurement
range.
Writing a “-2”:
Resets all parameters to the
delivery states (CAN address
SDO #2026 to 1, baud rate
SDO #2027 to 500 kBaud),
without saving the parameters
in EEPROM. The drive then
performs a start-up reference
loop and positions itself in the
middle of the measurement
range.
Continues on next page
-5…-1 or
1
±15 bit
No
R/W

Description of CANopen
7100.006424_Bus description_PSD4xx_CA_J_ENG 20 2022-08-15
Designation
Index
no.
Function
Range of
values
Back
up?
Delivery
state
R/W
Delivery state
Writing a “-1”:
Resets all parameters to the
delivery states (without
changing the CAN address and
baud rate), without saving the
parameters in EEPROM. The
drive then performs a start-up
reference loop and positions
itself in the middle of the
measurement range.
Writing a “1”:
Saves the parameter in
EEPROM
Writing a “0”:
No action
Reading after booting:
0 Memory content correct
≠ 0 Memory content
incorrect
Reading after saving:
0 Saving successfully
completed
≠ 0 Saving is not yet
complete or terminated with
errors (saving can take up to
2000 ms)
-5…-1 or
1
±15 bit
No
R/W
Other manuals for PSD4 Series
8
This manual suits for next models
16
Table of contents
Popular Network Hardware manuals by other brands
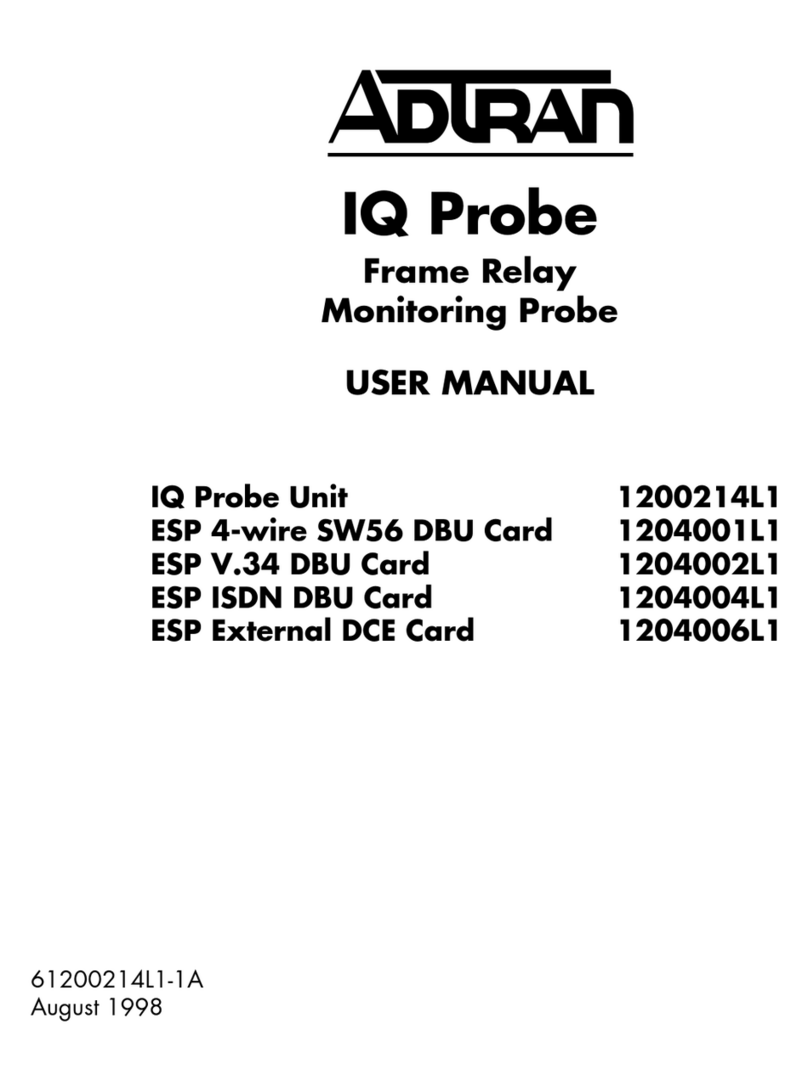
ADTRAN
ADTRAN IQ Probe 1200214L1 user manual
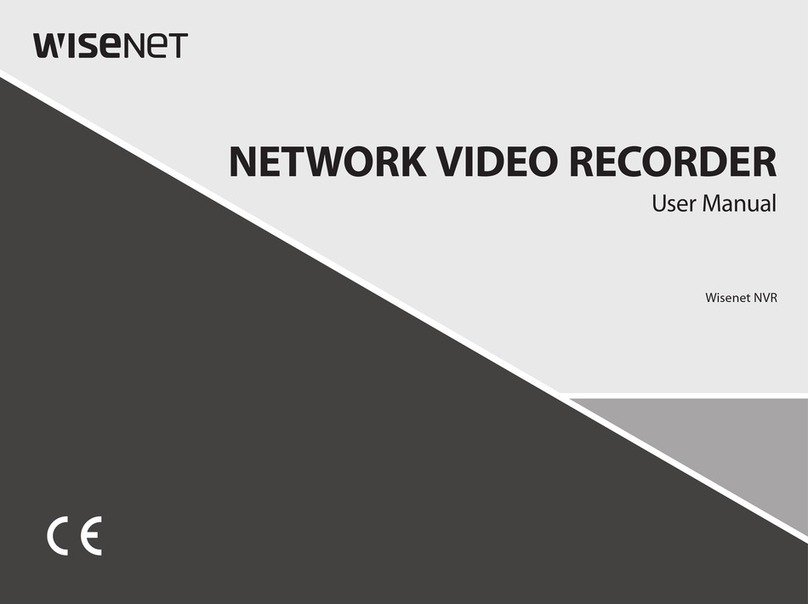
Hanwha Techwin
Hanwha Techwin WISENET XRN-1610 user manual
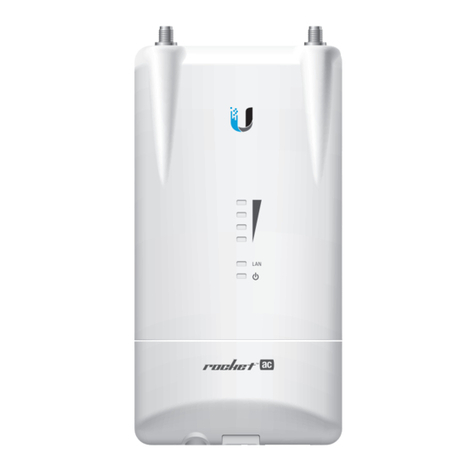
Ubiquiti
Ubiquiti Rocket R5AC-Lite quick start guide

Patton electronics
Patton electronics FORESIGHT 6300 user manual
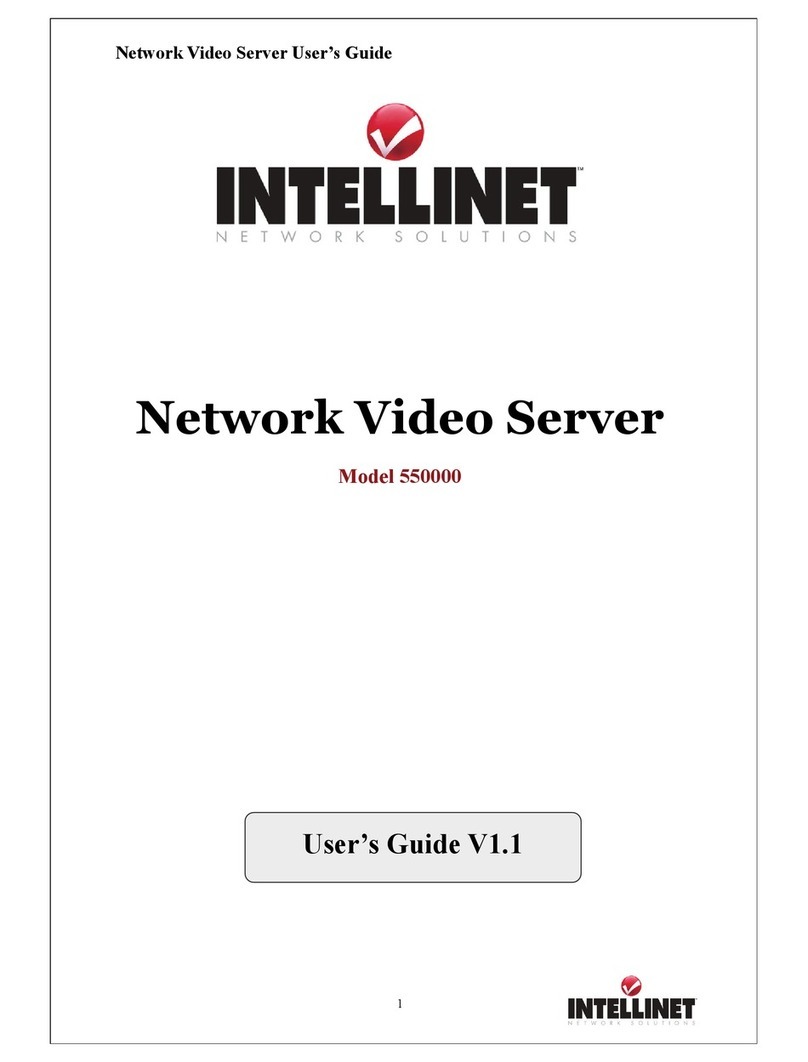
Intellinet
Intellinet 550000 user guide
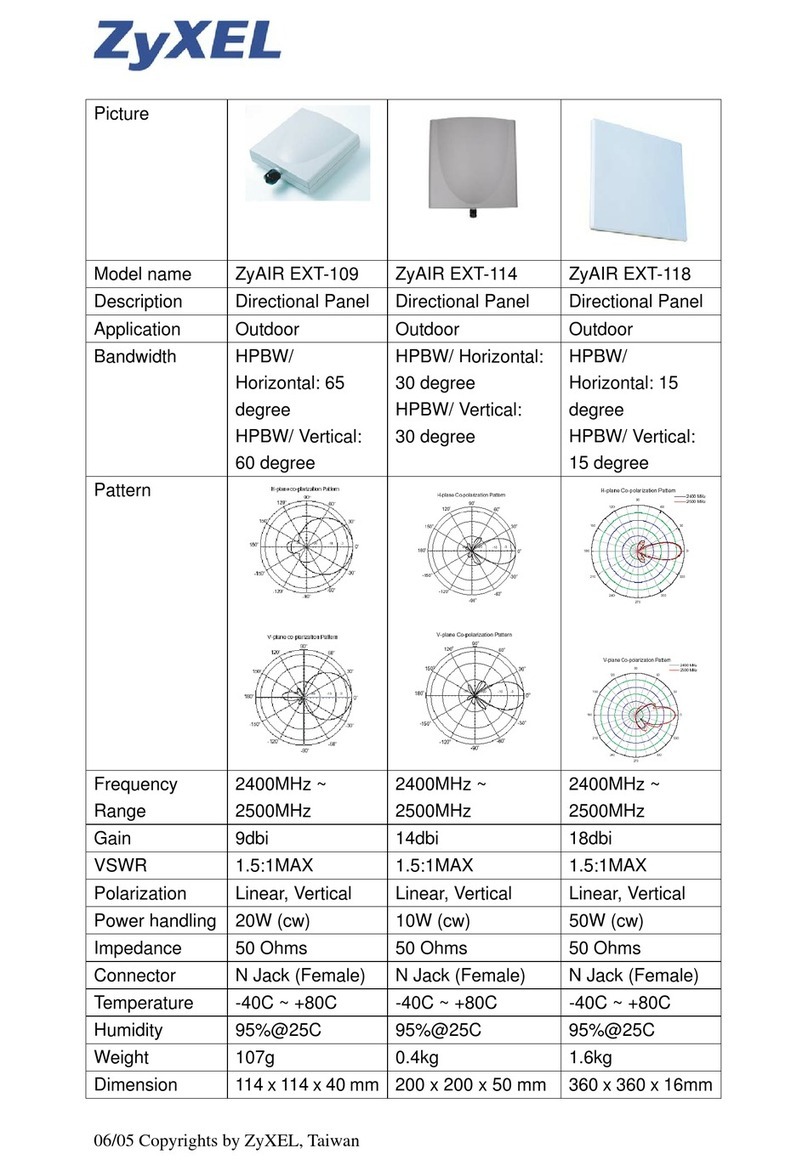
ZyXEL Communications
ZyXEL Communications ZYAIR EXT-109 datasheet
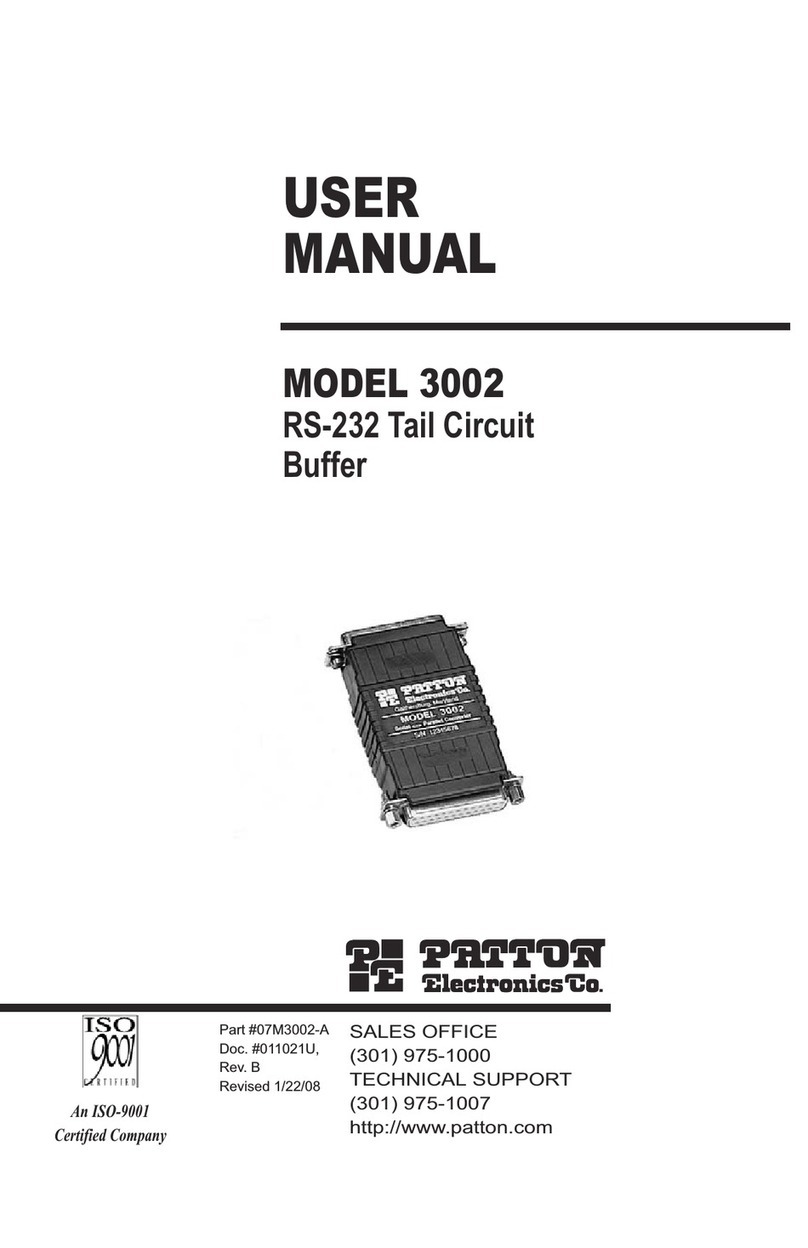
Patton electronics
Patton electronics 3002 user manual
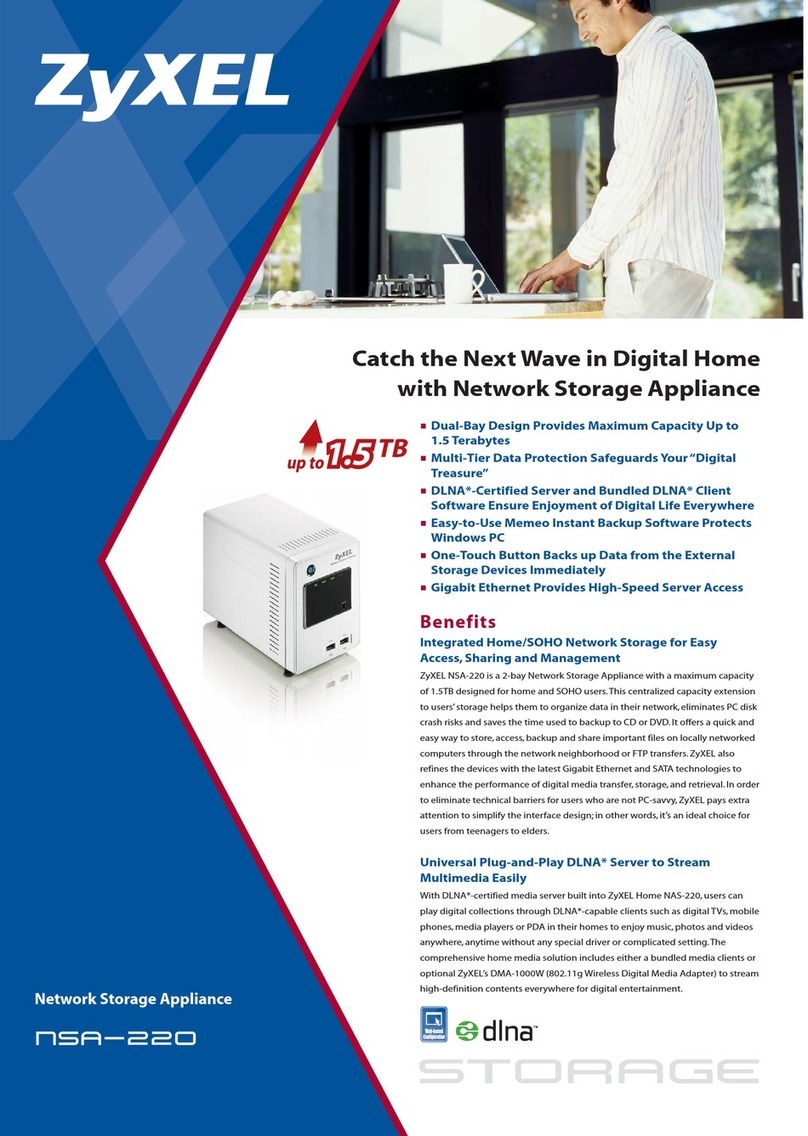
ZyXEL Communications
ZyXEL Communications Network Storage Appliance NSA-220 Specifications
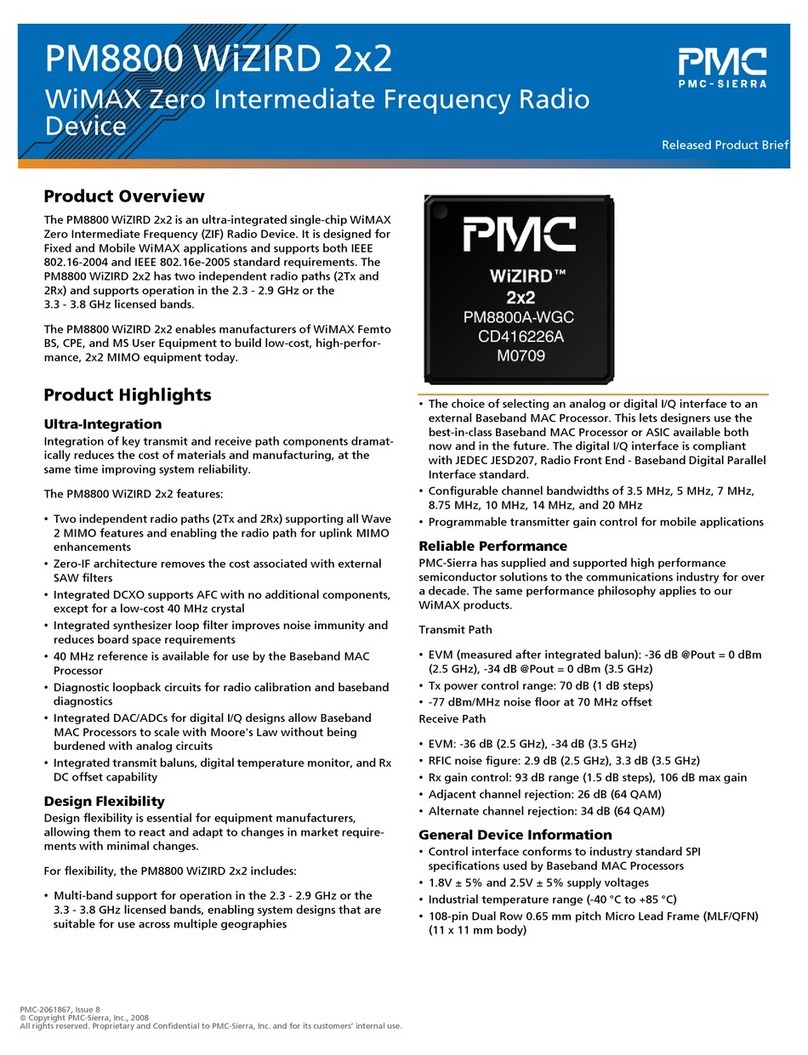
PMC-Sierra
PMC-Sierra M8800 Product overview
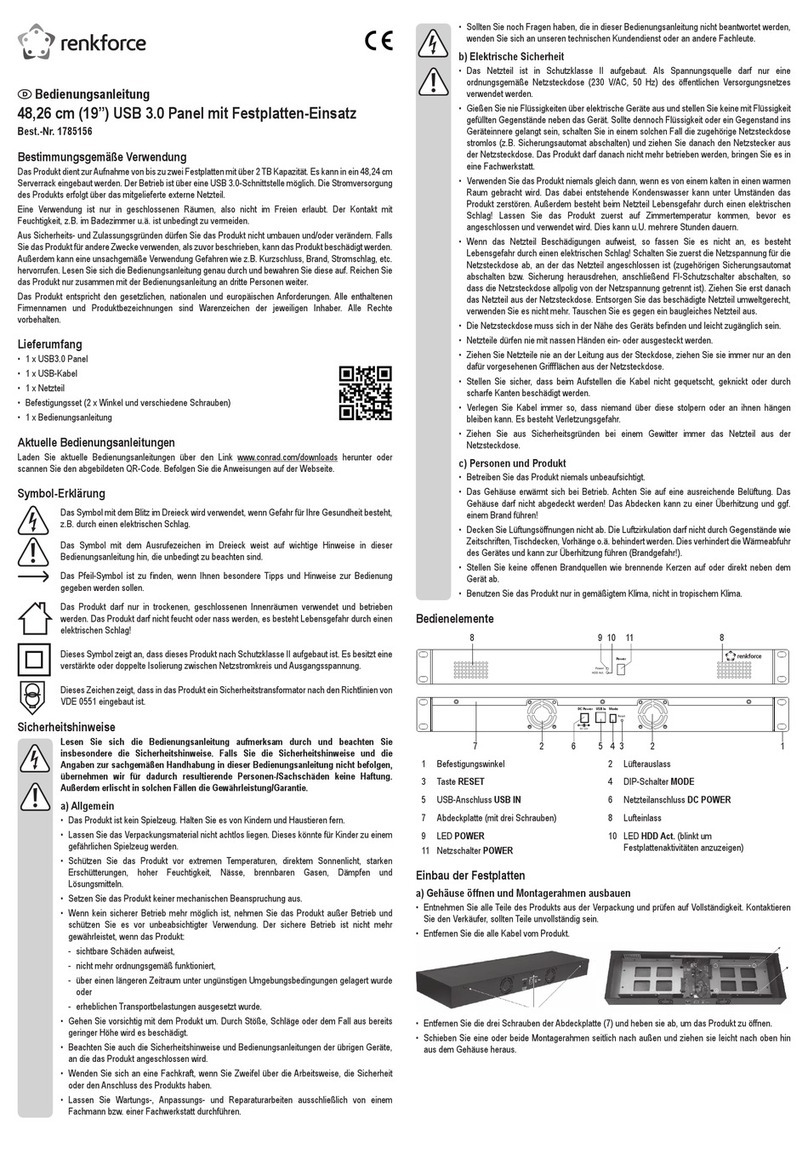
Renkforce
Renkforce 1785156 operating instructions
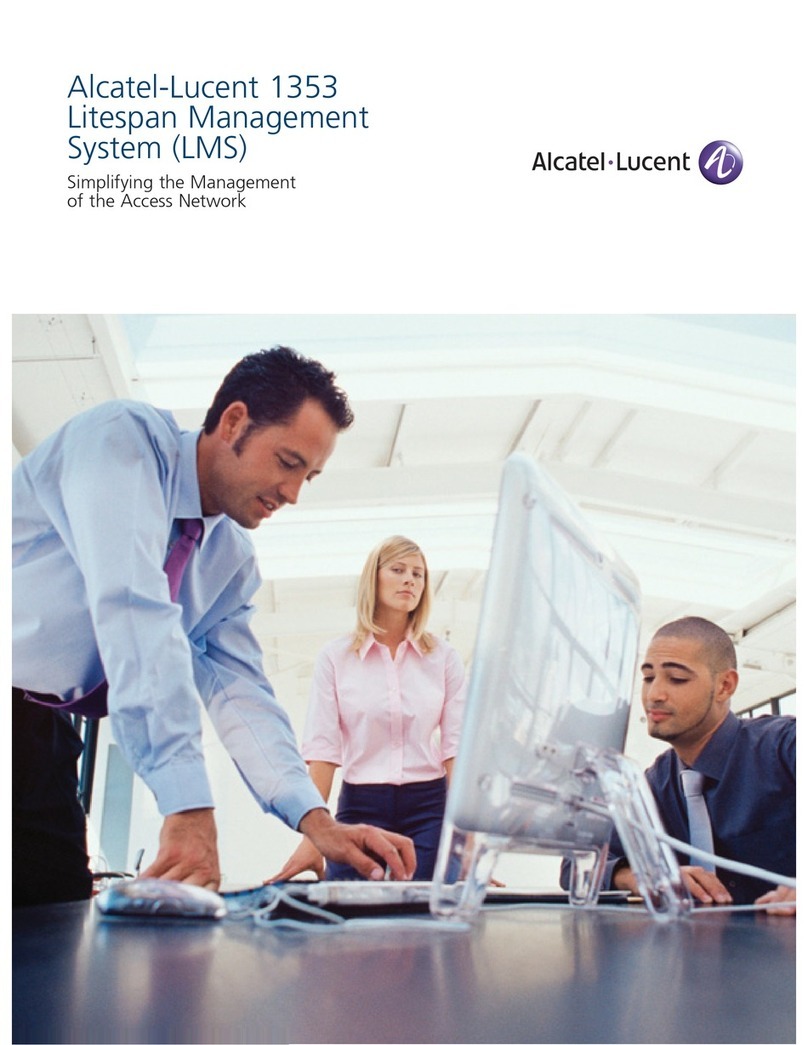
Alcatel-Lucent
Alcatel-Lucent 1353 brochure
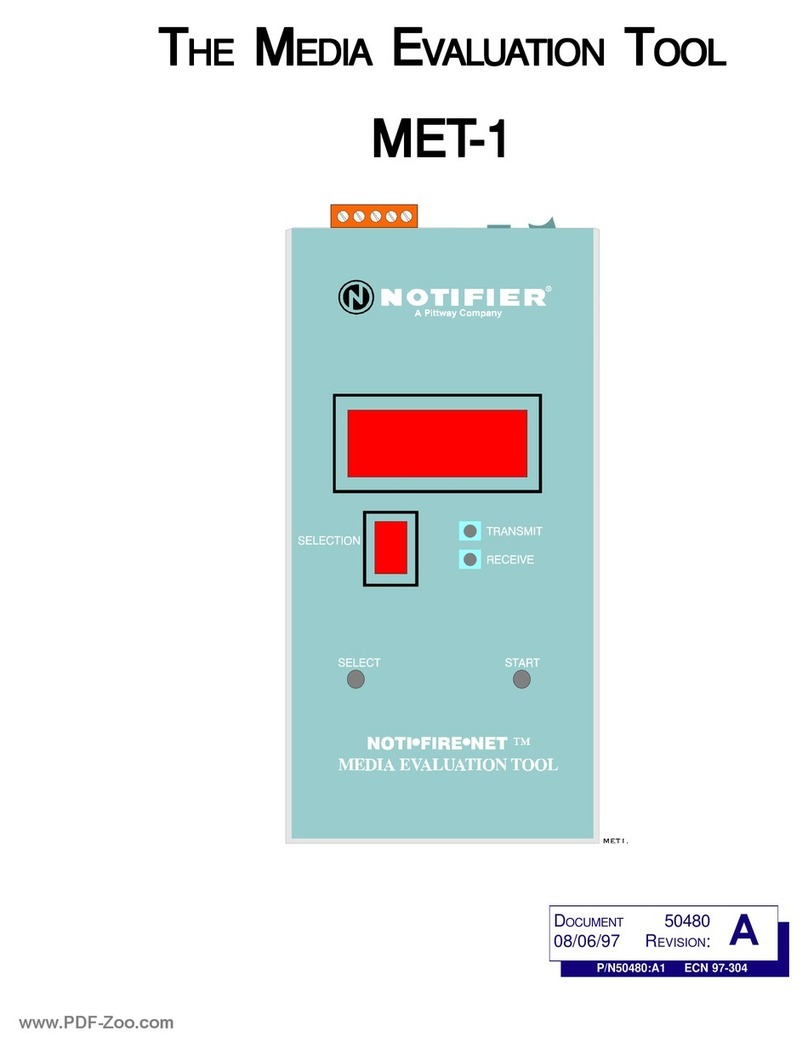
Pittway
Pittway NOTIFIER NET MET-1 manual