Harman PF100 Installation instructions

“Ce manuel est disponible en Français sur demande”

2
Combustion
Blower
Combustion
Blower cover
Fan Control
Hopper Lid
Latches
Control Cover
3 Speed Switch
Viewing Glass
Outer Door
Vent Pipe
Heat Exchanger
Shaker Handle
Outer Door Latches
Filter Box
Hopper

3
Please read this entire manual before you install and use your new
furnace. Failure to follow instructions may result in
property damage, bodily injury, or even death.
Hearth & Home Technologies, Inc.
352 Mountain House Road
Halifax, PA 17032
Note: This appliance is also approved for
installation into a shop.
Pellet Furnace - PF100
Omni-Test Laboratories, Inc.
135-S-02-2
Pellet Fueled Central/Supplementary For
Residential Use
CAN/CSA B366.1-M91, UL 391,
ASTM E1509-04 & ULC/ORD C1482- M1990

4
This Edge Toward
Furnace
The cold air return lter box can be assembled with the
lter frame on either side or the back, provided there is
access to the combustion blower and ue area.
It is not recomended that the lter frame be installed
on the same side as the ash door due to the need to
access the combustion blower, lter, and ue pipe for
service.
1. Place the bottom on the oor. The edge closest to
the knockouts will be the edge towards the furnace.
See Fig. 4.
2. Place the desired vertical panel inside the bottom
tray and hold into place with one Tek screw in the
bottom middle hole. (solid panel shown) See Fig 4.
Bottom
Solid Side Panel
Knockouts
Tek screw from outside
Bottom (same as
top)
Top (same as bottom)
Filter Frame Panel
Solid Side Panel
Blower access Panel
Blower access
Panel Cover
Switch

5
3. Place the lter frame panel inside the bottom and
inside the solid panel corner. See Fig. 6 for corner
detail. Make sure that the lter opening is up.See
Fig. 5 Hold the lter panel to the solid panel with
a Tek screw in the middle hole of the solid panel,
and one in the bottom middle hole under the lter
opening.
.
Filter Frame Panel
Filter opening must be up
Open Side Panel
4. Place the remaining panel, (in this case the
blower access panel) in the bottom panel and into
the corner of the solid panel. See Fig. 7. Make sure
that the panel is in the upright position. There are
no cover mounting holes in the bottom edge of this
panel. Hold the panel into place with one Tek screw
in the middle hole of the solid panel and one in the
bottom middle hole of the blower access panel.

6
5. Place the top on the lter box as shown in gure 8. A
t this
time all Tek screws can be inserted around the lter box.
Except for the (6) screws that attach the blower
access panel in place.
There should not be any screws protruding from the
box on the side toward the furnace. Also DO NOT put
a screw into the top center of the lter panel as a screw
in this location will interfere with the lter access cover.
6. Pry out the two knockouts in the top of the box and
install the ex connector and the switch. See Fig. 9.
Don’t forget the HI-MED-LO switch label on the
switch before the locknut.Make sure that the setscrew
on the ex connector is not pointing toward the furnace
end of the box when the locknut is fully tightened.The
lter box is now ready to install onto the furnace.
Follow the Blower mounting instructions on page 7
before continuing to step #7.
The blower should be mounted on the furnace
before the lter box for ease of distribution blower
installation.
It is best to wait until the blower, lter box, and
cold air return duct work is installed before installing
the lter and side panel.
7. After the Filter Box is installed on the furnace the
electrical wiring to the three speed switch needs to be
completed. White or Purple Neutral to White Neutral,
Violet from the Fan Control to the center terminal of the
switch, and the Black, Red, and Blue or Yellow to the
terminals shown.
The 1000 CFM blower is a 3-speed, and will
wire as shown. The 1450 CFM blower is a single speed
blower, therefore the three speed switch will not be
used. The 1638 CFM blower is a 4 speed, only hook
up the three colors shown and tape off the orange wire.
See Fig. 10.
8. Install the access panel cover by hooking the lip at
the bottom of the cover over the edge in the lter box.
Use 6 Tek screws to secure the access panel.
9. To install the lter, insert the lter into the lter slot
and slide completely into the frame. Take note to the air
ow arrow on the lter when installing. Slide the lter
access cover over the opening with the upright angle
toward the lter box. If a Tek was put into the middle
hole by mistake, remove the screw to allow the access
cover to t properly.
Top
Access
Panel Cover
opening
3 Speed Switch
Flex connector
Violet 120VAC
From fan control
Yellow on 1638 CFM motor
BOTTOM VIEW OF 3-SPEED SWITCH
Blue
Med.
Black
High
Red
Low

7
Install the blower mounting brackets on the blower
as shown in Fig. 11.
1. Install ( 4) Tek screws on each side where shown
in Fig. 11. Start with the two center screws.
There are two small holes in the
discharge end of the blower that match the two
center holes on the small angle of the blower
bracket. The two (2) outer holes are drilled by
theTek screws.
2. Mount blower with brackets installed on the
furnace as shown in Fig. 12. Each side will require
6 Tek screws.
The furnace blower opening is made
large enough for the use of any of the 3 offered
blowers. The blower mounting brackets will t either
blower. The inner hole pattern is for the 1000 CFM
blower and the outer pattern is for the 1450 or
1638 CFM blowers.
Regardless of the supply air duct size
installed, the Distribution Blower Motor be
checked for running Amperage. Check the motor
name plate for the full load AMPS. If the amperage
is running higher than that listed, a supply air
restricting damper may be required to increase the
supply plenum positive static pressure.
Mounting Screws
3. Mount the lter box on the furnace with ( 6 )
#10 x 3/4 Tek screws, 3 on each side. Visually
locate these holes so you are familiar with their
location on the lter box and the furnace. Access
to the mounting holes can be gained through the
blower access panel cover and the lter opening.
See Fig. 14.
Two pieces of 2x4 stacked laying at
on the oor 12 inches from the blower opening will
support the lter box during installation

8
The rebrick is shipped in the ash pan. It will need
to be placed on the brick shelf as shown in Fig.
15. It can be installed with either face to the re.
Hold the brick longways and slide it down into the
slot on the shelf. There is a stop at the rear of the
shelf to stop the rearward travel.The brick just sits
on the shelf in the upright position.
The upper heat exchanger bafe comes shipped
along side the ashpan. Remove the ashpan and
the bafe. This upper bafe needs to be installed
before operating the furnace.
The bafe has a long 45 degree bend on the
bottom of the rebox side. See Fig. 17.
On the opposite side there are four hooks that
will support the bafe. On the front and rear of the
rebox walls there are slots that these hooks t
into. See Fig. 16
Slide the upper bafe down to meet the slots, while
you hold the bafe against the heat exchanger. You
will notice that the upper bafe will hold the lower
bafe plate into position. See Fig.17.
Note how the upper and lower bafes are
held into position because they will need to be
removed during heat exchanger cleaning.
Bafe support bracket
45o bend

9
A combustion blower is used to extract the combustion
gases from the rebox. This creates a negative
pressure in the rebox and a positive pressure in
the venting system as shown in g. 2. The longer the
vent pipe and more elbows used in the system, the
greater the ow resistance. Because of these facts,
we recommend using as few elbows as possible and
30 feet or less of vent pipe. The maximum horizontal
run should not exceed 18 feet. Remember, the
horizontal pipe sections will accumulate with y-ash
rst. Keep this area clean.
Be
sure to use a starting collar to attach the venting
system to the furnace.
4” pellet vent pipe (known as PL vent) is constructed
of two layers with air space between the layers.
This air space acts as an insulator and reduces the
outside surface temperature to allow a clearance to
combustibles as low as 2 inches. This clearance is
tested and listed by the pipe manufacturers.
The sections of pipe lock together to form an air tight
seal in most cases; however, in some cases a perfect
seal is not achieved. For this reason and the fact that
the furnace operates with a positive vent pressure,
The rst thing needed is deciding where and how
the furnace will be installed.
Things that need to be taken into consideration
are Venting, Supply and Return Ducting, Electrical,
and Condensation Drainage (if A/C is installed).
Don’t forget access to the furnace for service.
When the return air inlet position is known, the
lter box and distribution blower can be installed.
After the furnace is set into place, the venting can
be completed.
The shaded areas are where the
clearances for the PL vent pipe must be
maintained at . After the venting leaves
the shaded area it may be installed as per
the vent manuafacturer instructions. (Only
listed wall pass-throughs and re stops may
be used.)
See
NOTES: on
page 12
16”
16”

10
The minimum vent conguration is a 90o or Tee on
a starter collar and a 24” length horizontal through an
exterior wall. A cap or other bird screen on the end
should direct the ue gasses down and away from the
structure. See Fig. 18.
The maximum horizontal length is 18 feet. The
minimum termination height above the exterior grade
is 18”. The maximum total length of any conguration
is 30 feet*. * ( see venting graph on page 11)
NOTE: Cleanout Tee’s should always be used on the
transitions to horizontal pipe to allow easy access for
cleaning.
The venting graph allows for (one) 90 deg. or Tee
tting in any conguration.
If more 90’s, T’s, or 45’s are needed the total length
must be adjusted to allow for the added restriction.
Up to four (4) additional 90’s, Tee’s, or equivalent 45’s
can be added as long as the overall length is adjusted
in accordance with the values listed below.
( See the venting graph on page 11.)
Each Vertical ---- 90 deg. or T subtract 2.5 feet
Each Vertical ---- 45 deg. subtract 1.5 feet
Each Horizontal - 90 deg. or T subtract 5.0 feet
Each Horizontal - 45 deg. subtract 2.5 feet
This is especially important in high humidity cold
weather climates, such as maritime areas, lake shores,
and low river valleys.
4” Type “L”
or “PL” Vent
pipe
This is the minimum venting conguration.
NOTE: This would only be allowed with
walls.
Fig. 18
1”

11
•Installing the pellet vent with a minimum vertical
rise of ve feet. Preferably terminating above the
roof line.
•Installing an outside air connection to the
appliance.
•Maintain specied clearances to windows, doors
and air inlets, including air conditioners.
•Vents should not be placed below ventillated
softs.
•Avoid venting into alcove locations.
•Vents should not terminate under overhangs,
decks or onto covered porches.
•Maintain minimum clearance of 12” from the
vent termination to the exterior wall.
Hearth & Home Technologies strongly recommends
the use of outside air for all pellet furnace
applications.
Per national building codes, consideration must be
given to combustion air supply for all appliances
in the vicinity of the pellet boiler. Failure to supply
adequate combustion air for all appliance demands
may lead to backdrafting of those appliances.
Consult with your HVAC Professional to determine
that all combustion air requirements are met.
The air
intake is best located on the same exterior wall as,
and lower than the exhaust vent outlet.
The air
intake is best located on the exterior wall oriented
towards the prevailing wind direction, during the
heating season.

12
WARNING: Venting terminals must not be recessed
into a wall or siding.
NOTE: Only PL vent pipe wall pass-throughs and re
stops should be used when venting through combustible
materials.
NOTE: Always take into consideration the effect the
prevailing wind direction or other wind currents will
cause with yash and /or smoke when placing the
termination.
A. The clearance above grade must be a minimum of
18”.
B. The clearance to a window or door that may be
opened must be a minimum of 48” to the side, 48” below
the window/door, and 12” above the window/door.
C. A 12” clearance to a permanently closed window is
recommended to prevent condensation on the window.
D. The vertical clearance to a ventilated soft located
above the terminal within a horizontal distance of 2 feet
(60 cm) from the center-line of the terminal must be a
minimum of 18”.
E. The clearance to an unventilated soft must be a
minimum of 12”.
F. The clearance to an outside corner is 11” from center
of pipe.
G. The clearance to an inside corner is 12”.
H. A vent must not be installed within 3 feet (90 cm)
above a gas meter/regulator assembly when measured
from the horizontal center-line of the regulator.
I. The clearance to service regulator vent outlet must be
a minimum of 6 feet.
J. The clearance to a non-mechanical air supply inlet
to the building or the combustion air inlet to any other
appliance must be a minimum of 48”.
K. The clearance to a mechanical air supply inlet must
be a minimum of 10 feet.
L. The clearance above a paved sidewalk or a paved
driveway located on public property must be a minimum
of 7 feet.
M. The clearance under a veranda, porch, deck or
balcony must be a minimum of 12 inches.
NOTE: The clearance to vegetation and other
exterior combustibles such as mulch is 36” as measured
from the center of the outlet or cap. This 36” radius
continues to grade or a minimum of 7 feet below the
outlet.
Certain Canadian and or Local codes or regulations
may require different clearances.
A vent shall not terminate directly above a side-
walk or paved driveway which is located between two
single family dwellings and serves both dwellings.
Only permitted if veranda, porch, deck, or balcony
is fully open on a minimum of 2 sides beneath the oor.
V= Vent terminal

13
If installing the furnace in a room separated from the
remaining living spaces, the minimum size of the room must
be no smaller than 8’ x 8’. See Fig. 21. The reason for this
is heat build-up and required space for service and normal
operation.This is the minimum size of the room even if it is
built of non-combustible material.
High and low air vents MUST be installed between the room
and the remaining living space. Each vent should be at least
72 square inches in area. ( The vent size will need to be
increased if there is no return air ducting system.)
The striped areas are the minimum clearances to combustibles
which is 36” from stove body, not the hopper or blower.
The shaded area indicates the required oor protection area.
The furnace requires 48” x 52” of oor protection centered
around the skidplate footprint. Flooring should be a minimum
of 26 gauge sheet metal covering the installation clearance
area and 18” in front of, and 8” to either side of the ash pan
door.
The 18” clearance from the hopper end is a manufacturer’s
recommendation for adding pellets and/or servicing the
feeder mechanism.
The minimum clearance to the top of the plenum is 1”.
Note the minimum height to the bottom of the supply duct if
it crosses the hopper.
The minimum duct conguration to a living space above the
furnace is as shown below. An offset of at least 24” MUST
be installed between the plenum and the oor register. The
register size MUST have an area of at least 240 square
inches.
When installing a oor
register, the temperature of the
discharge air MUST be taken into
consideration (The discharge air
temperature may be high enough to
cause burns if not properly operated
and maintained.)
The Blower Motor full
load AMPS MUST be checked.A
plenum damper may be required to
adjust the motor full load AMPS to the
motor nameplate rating.
18”
Floor Protector
48” wide
36”
52” long
1”

14
16”
181/8” 181/8”
Chimneys taller than 20’ above the connection will
require a draft test to determine if the draft is too high.
Note: The High Burn Draft should not exceed .85
IWC. Some form of a restrictor plate may be required at
the top of high chimneys to reduce the draft. See page
20 for the Draft Test procedure.
See NOTES:
on page 12
The shaded area is where the clearance for the PL
vent pipe must be maintained at . After the venting
leaves the shaded area it may be installed as per the
vent manufacturer instructions. (Only listed 4” pellet
vent wall pass-throughs and re stops may be used.)
See Fig. 23 & 25.
When wood is burned slowly, it produces tar and other organic
vapors, which combine with expelled moisture to form creosote. The creosote vapors condense in the relatively
cool chimney ue of a slow-burning re. As a result, creosote residue accumulates on the ue lining. When ignited,
this creosote makes an extremely hot re. The pellet vent pipe should be inspected at least twice monthly during
the heating season to determine if a creosote buildup has occurred. If creosote has accumulated it should be
removed to reduce the risk of a chimney re.
Guidance on minimizing creosote formation and the need for periodic creosote removal: The chimney should
be inspected during the heating season to determine if a creosote build-up has occurred. If a signicant layer of
creosote has accumulated (3mm or more) it should be removed to reduce the risk of a chimney re.
This furnace may be used and installed into an existing
masonry or Class A metal chimney.
be vented into a chimney ue
serving another appliance.
The chimney should be cleaned and or inspected before
installation.
16

15
The use of outside air is optional. Connecting to
outside air may be required by local codes, and
is strongly recommended. To install outside air,
use 2¾” I.D. metal ex pipe, part # 2-00-08544
(12’6”length) or part #2-00-08545 (25’ length).
There is a break-away hole on the rear panel
which must be removed before connecting the
ex pipe. See Fig. 28. The pipe should be run
outside and terminate 3 feet or more below or 1
foot or more to the side of the vent pipe outlet.
Never terminate the outside air above the vent
pipe outlet. The maximum length of this pipe is
25 feet. Inlet cover, part #1-10-09542 should be
used to keep birds, rodents etc.out of the inlet
pipe. See Fig. 27.
If outside air is installed, the inlet cover
should not be placed in an area where drifting of
snow or ice will build up, blocking the intake air
supply.
Only metal Intake Flex should be used for the
Outside Air Supply connection.
Only a screened or rodent protected Outside Air
Intake cover should be used as an outside weather
cover.
The Outside Air Intake Pipe is inside the Feeder
Cover and to the right of the feeder motor. The 2 ¾”
steel ex pipe is made to slide over the outside of
the Air Intake Pipe. See Fig. 29. It should be held
into place with some silicone, foil tape, or a hose
clamp.(not supplied)
Heat rises in the house and leaks out at upper
levels. This air must be replaced with cold air from
outdoors which ows into lower levels of the house.
Vents and chimneys into basements and lower
levels can become the conduit for air supply and
reverse under these conditions.
The outside air supply will supply most of the
demands of the pellet appliance to resist back-
drafting, but consideration must be given to the
total house demand. It may be necessary to add
additional ventilation to the space in which the
pellet appliance is located. Consult with your HVAC
professional to determine the ventilation demands
for your house.
Inlet Cover part#
1-10-09542
Outside Air Inlet Pipe
Outside Air Pipe Knockout

16
The Wall Control sends and receives information
from the control board through a 4 wire Datacom
cable. There is a 100’ length of this cable supplied
with the furnace. 100’ lengths of this cable can
also be ordered separately, part #3-20-02583.
Alternately, any Datacom cable -CAT3- 2 twisted
pair 24ga solid wire can be acquired at a local
electrical supply house. Also any CAT3-24ga. solid
wire 2, 3, or 4 pair cable can be used because they
all have the same pair color combinations. The
maximum length of wall control wiring is 100 feet.
The furnace connecting point is a 4 pole screw
terminal block on the side of the hopper just
around the corner to the right of the control. Follow
the wiring instructions on the label alongside the
terminal block. See Fig. 31.
With this small gauge of wire, care
must be taken not to overtighten the terminal
screws thus, breaking the wire.
There are tie-wrap holes in the face of the hopper
aprox. every 6” to keep the cable secure and out
of the way.
The Wall Control is made to t on a standard
wall case electrical box. It could also be mounted
directly to a stud using 2 drywall screws. In either
case the screws should be turned in and tested
for a snug t when the Wall Control is slid down
over the screws. The Wall Control only hangs on
the screws so a good t is important.
Remove the Wall Control and make the Datacom
cable connections with the UY auto splicers
provided. . Following
the wiring diagram on the inside of the Wall Control
make each splice. See Fig. 32. Insert the two
matching color wires fully into the two holes of one
of the UY connectors. A pair of standard Channel-
lock pliers works ideally to squeeze the raised
button down into the UY connector body. Extra UY
connectors can be purchased. Part # 3-20-00200
A pair of needle nose pliers may be
helpful to insert the BLUE T-stat wires fully into the
connector. Visually inspect to see that the wires
are fully inserted before squeezing the UY splicer.
Orange - Red (+ LED )
Orange/White - White or Black ( - LED)
Blue - Blue ( Tstat )
Blue/White - Blue ( Tstat )
Datacom Wall Control
Cable

17
The pellet furnace may be connected to a gas or oil-
red central furnace or heat pump duct system. Prior
to installation, determine whether all requirements for
installation including all clearnaces can be met.
The pellet furnace warm air supply and the cold air
return must be installed in a parallel arrangement.
EXAMPLE: The warm air supply duct from the pellet
furnace is to be connected to the warm air supply of the
existing furnace. Also the cold air return duct from the
existing furnace is to be connected to the cold air return
duct of the pellet furnace. Isolation dampers (2) should
be installed in the ductwork. (1) in the warm air supply
duct for the existing furnace and (1) in the warm air
supply duct of the pellet furnace after or “downstream”
of the high limit/fan control. These dampers can be
manually operated or fully automatic. In either case,
the unit that is not being used must be prevented from
being operated. (This also can be done manually or
automatically.) Any control wiring, power wiring
needed should be performed by a qualied installer
and/or electrician.
The warm-air supply outlet of the pellet furnace shall
not be connected to the cold-air return inlet of the
existing furnace because of the possibility of overheating
components of the existing furnace, causing the existing
furnace to operate other than as intended.
We recommend that the warm air supply plenum
be constructed of sheet metal.
Fig. 33
This furnace may be installed in a manufactured /
mobile home. The following specic requirements
must be met;
1. The furnace must be hooked up to an outside
air source.(see page 15)
2. The furnace must be secured or bolted to the
oor of the mobile home. Use lag bolts through the
provided holes (see below).
3. The furnace must be
grounded to the frame of
the mobile home.
4. Floor protection and
clearance specications
must be followed,
including the minimum
room size of 8 feet by
8 feet.
5. As in any installation, the furnace must be vented
to the outside, using only approved 4 inch pellet
venting materials.
6. The furnace can not be installed in a room
specied as a sleeping room.
Lag Bolt
Holes

18
An easy rule of thumb for A/C CFM blower size
is, .75 to 1 CFM for each square foot of conditioned
space. (std. 8’ ceiling height)
This furnace can be tted with an air conditioning
coil mounted in the supply air plenum.
HHT is not responsible for sizing, duct placement,
or interconnections. However we have made adding
A/C to the furnace easier with the information listed
below.
There is a factory installed junction box ready to
accept your A/C relay. The A/C fan control center
with 40 va transformer must have a DPDT relay.
White Rodgers # 90-112, part # 3-20-38056 is
available. Other brands are also acceptable for use.
The wiring should be done as per Fig. 34. The
low voltage wiring to the outside condensing unit
and the cooling thermostat are not shown. See
condensing unit diagrams for that information.
This style of relay is used to lock out the feeder
system of the pellet furnace when the A/C unit is
calling for cooling. This is a fail-safe against both
units operating at the same time. See the
in the lower left corner.
The speed or velocity of air moving through duct
systems increases as the duct decreases in size with
the same CFM blower. The sound of air owing through
the duct increases as the velocity increases. Therefore
the largest duct size practial should be used.
The velocity to sound level must be taken into
consideration when connecting this furnace into an
existing duct system.
As a primary source furnace the duct system can be
installed to t the customers needs.
These are recommended Supply Air duct sizes (in
square inches)for some of the different CFM blowers
that may be used with this furnace.
Static-In. W.C. .3 Minimum to .6 Maximum
1000 cfm. 270 in² 210 in² 160 in²
1450 cfm 360 in² 290 in² 220 in²
1638 cfm 470 in² 360 in² 290 in²
(These duct sizes are only recommendations. )
The Return Air duct system should be sized
aproximately 10 percent larger for heating only systems
and 20 percent larger if air conditioning is installed.
It is highly recomended that
the furnace control be turned
to the “OFF” position whenever
air conditioning is being used,
whether or not it is interconnected.
Regardless of the supply
air duct size installed, the Distribution
Blower Motor be checked for
running Amperage. Check the motor
name plate for the full load AMPS. If
the amperage is running higher than
that listed, a supply air restricting
damper may be required to increase
the supply plenum positive static
pressure.

19
1. The Fan Control must be placed in the discharge
plenum approximately 11 inches above the discharge
opening of the furnace, as close to center as possible.
The best place is on the same side as the ash
door because of ease of access. See Fig. 35.
Care must be taken when installing the Fan
Control when an air conditioning A Coil is used. The
Fan Control always be installed below the A Coil
in low plenum installations.
2. Install the ex and wiring.
3. Make sure that the ue venting will not interfere with
the ex to the Fan Control.
4. Pry out one of the bottom knockouts of the Fan
Control. Install the 90 degree ex connector as shown in
Fig. 36. One of the locknuts stays on the outside of the
box and one goes on the inside to tighten the connector
into place. This allows for maximum room for the wires
around the switches.
5.
Figure 36 shown with copper jumper already removed.
6. Connect the two VIOLET wires to the FAN CONTROL
switch. ( It doesn’t matter which wire is on which screw).
See Fig. 36.
7. Connect the WHITE and SKY BLUE wires to the
LIMIT switch. ( It doesn’t matter which wire is on which
screw). See Fig. 36.
8. Make sure that all of the wires are out of the way
when closing the cover. ( Excess twisting and pinching
of the wires could cause a short circuit.)
9. HIGH LIMIT setup is simple, just rotate the high limit
pointer clockwise until it is against the tamper-proof
screw. (Never adjust this screw)
10. FAN CONTROL setup: Move both fan control
pointers together until they touch, then rotate both
pointers together until the gap between them is directly
over the middle 0 of 100. See Fig 36.
This is the best fan control position we have
found during factory testing. These fan control settings
can be adjusted if desired.
High limit fan control
High Limit
Setpoint
Fan Control
Setpoint
Locknuts outside and inside

20
To install power to the furnace rst remove the cover
on the circuit breaker junction box shown.
Inside you will nd the main terminal block.(See wiring
diagram on page 36 for location of main terminal block
and proper power connections). In the bottom of the box
a knockout hole is provided for the incoming wire.
The recommended circuit is 15 Amp 120
V.A.C. 60 Hz. This furnace should be the only appliance
on the circuit.
The recommended high and low voltages are, 130
V.A.C. 60 Hz maximum high voltage, and 113 V.A.C. 60
Hz minimum low voltage.
The furnace will continue to operate at voltages as low
as 105 V.A.C. , although it can not be guaranteed that
automatic ignition will occur. Also, there is the possibility
of a distribution blower motor overload.
After the venting is completed, the rebox low draft
will need to be checked and possibly adjusted. After
removing the 3/8” bolt from the draft hole shown in Fig.
38, insert the draft meter tube. The inner ash door and
the hopper lid must be latched during this test. ( It is
recommended that the draft meter have a scale of 0 to
1” WC.)
Turn the Feed Adjuster to “Test”. this will start the
combustion blower and allow you to check and record
the High Draft ______ - IWC date _______ (There is
no adjustment for the High Draft)
After the rst 60 seconds, the “Test” mode lowers the
combustion blower voltage to the Low Burn voltage.
During this lowered voltage cycle the
and adjusted if necessary. The
recommended low draft setting should be between -.25 &
-.35 IWC. Depending on the amount of vertical rise, it may
not be possible to get a low draft reading in this range.
In this case, a maximum low draft of -.55 is acceptable.
The adjustment screw is through the small hole to the
right of the Igniter Light. See Fig. 39. Adjusted the Low
Draft to __________ -IWC.
Draft meter bolt
Furnace Control
“Test”
Low Draft Adjustment Pot
Other manuals for PF100
1
Table of contents
Other Harman Furnace manuals
Popular Furnace manuals by other brands
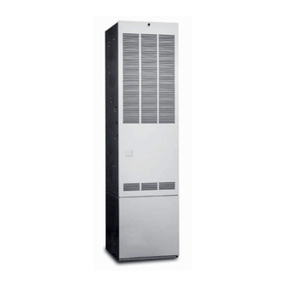
Nordyne
Nordyne M1B Owner's manual and installation instructions
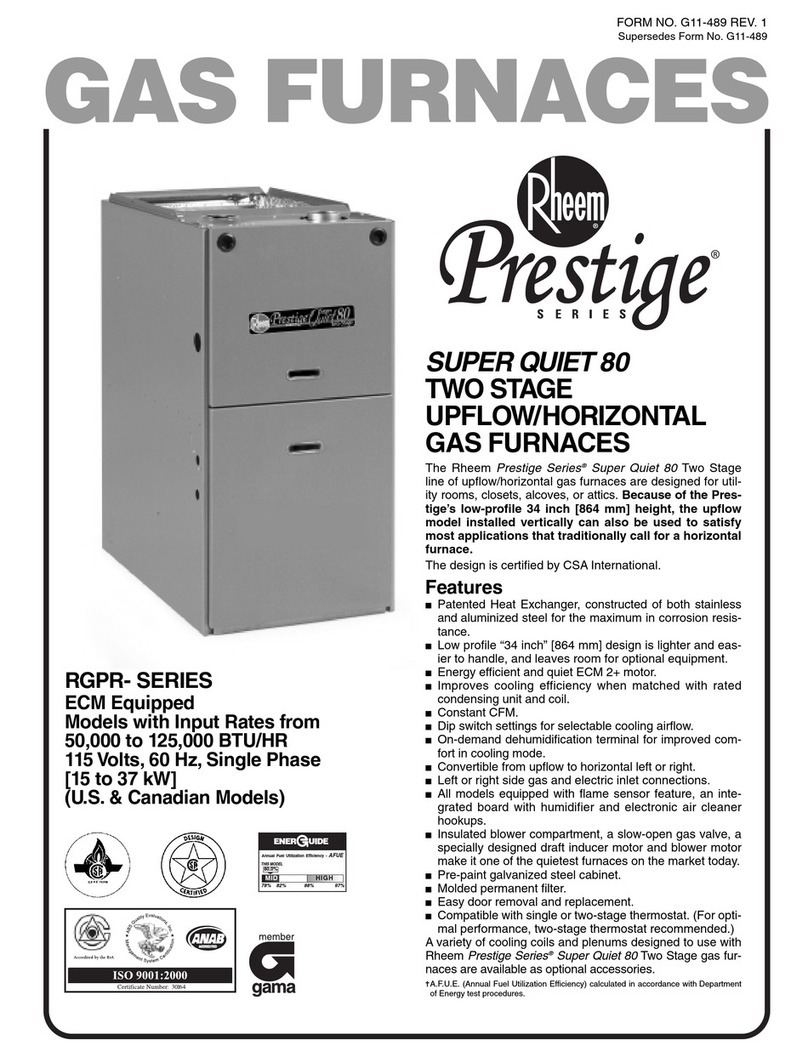
Rheem
Rheem RGPR 05EBMKR manual
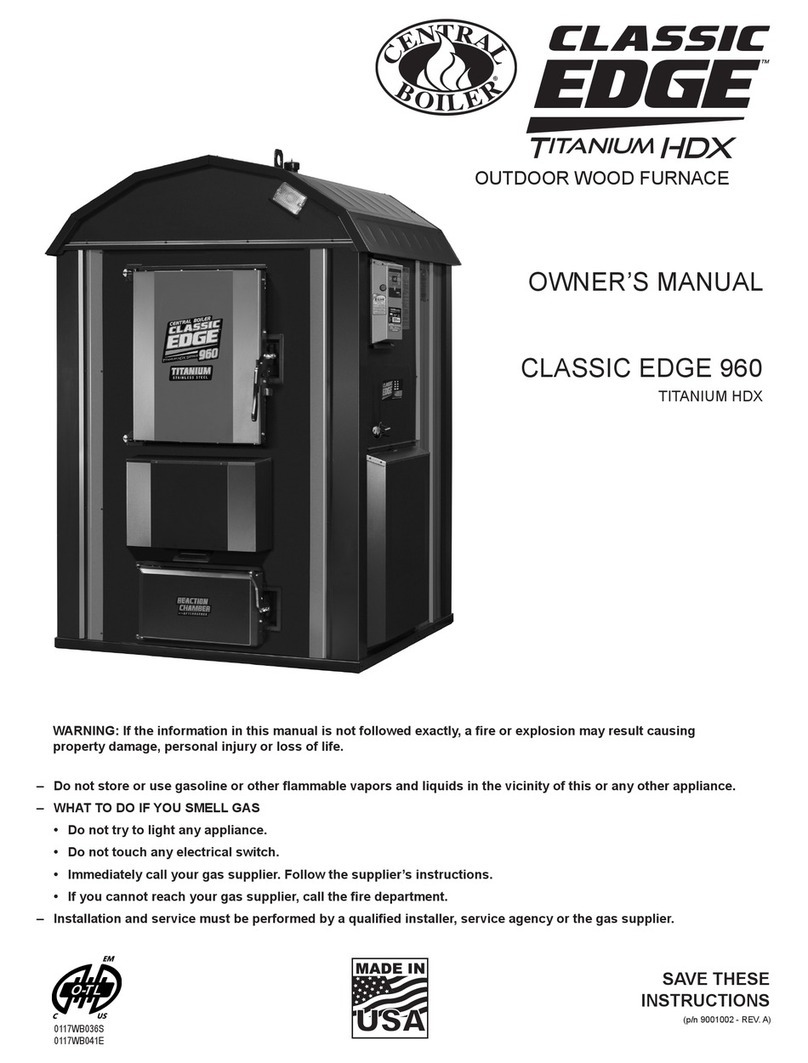
Central Boiler
Central Boiler CLASSIC EDGE 960 TITANIUM HDX owner's manual
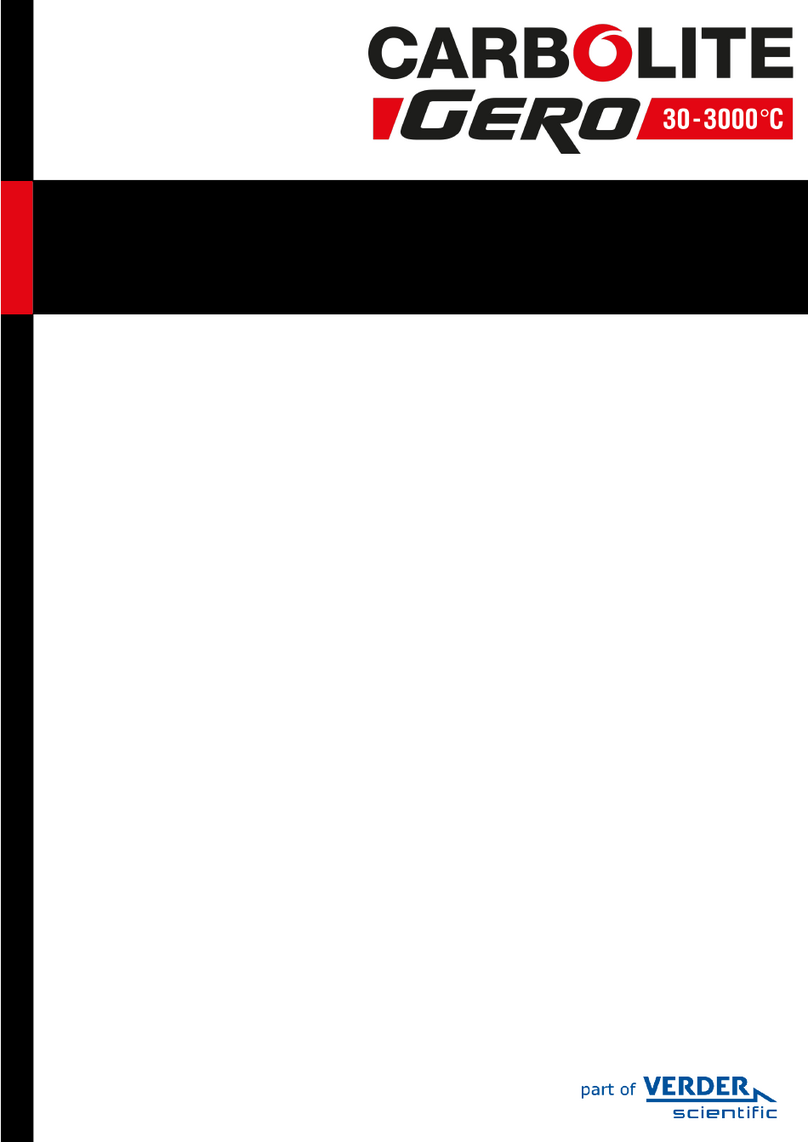
VERDER
VERDER CARBOLITE GERO E Series Installation, operation and maintenance instructions
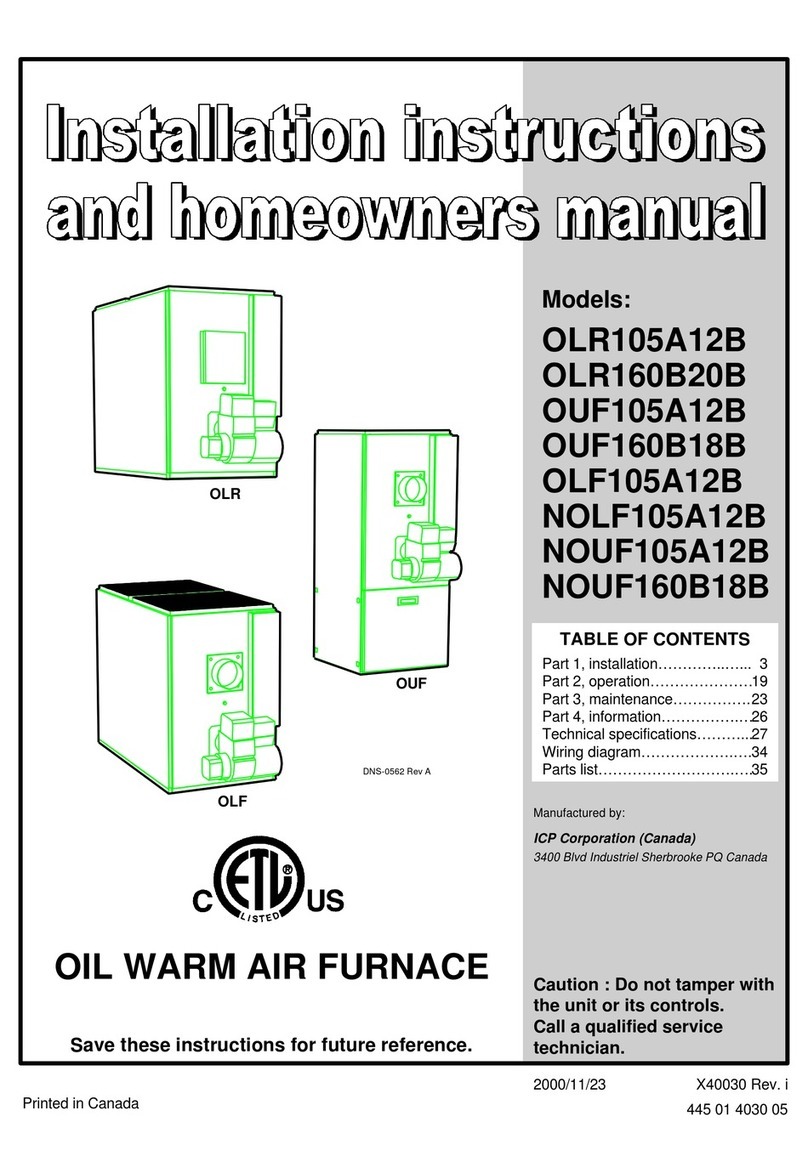
ICP
ICP OLR Series Installation instructions and homeowner's manual
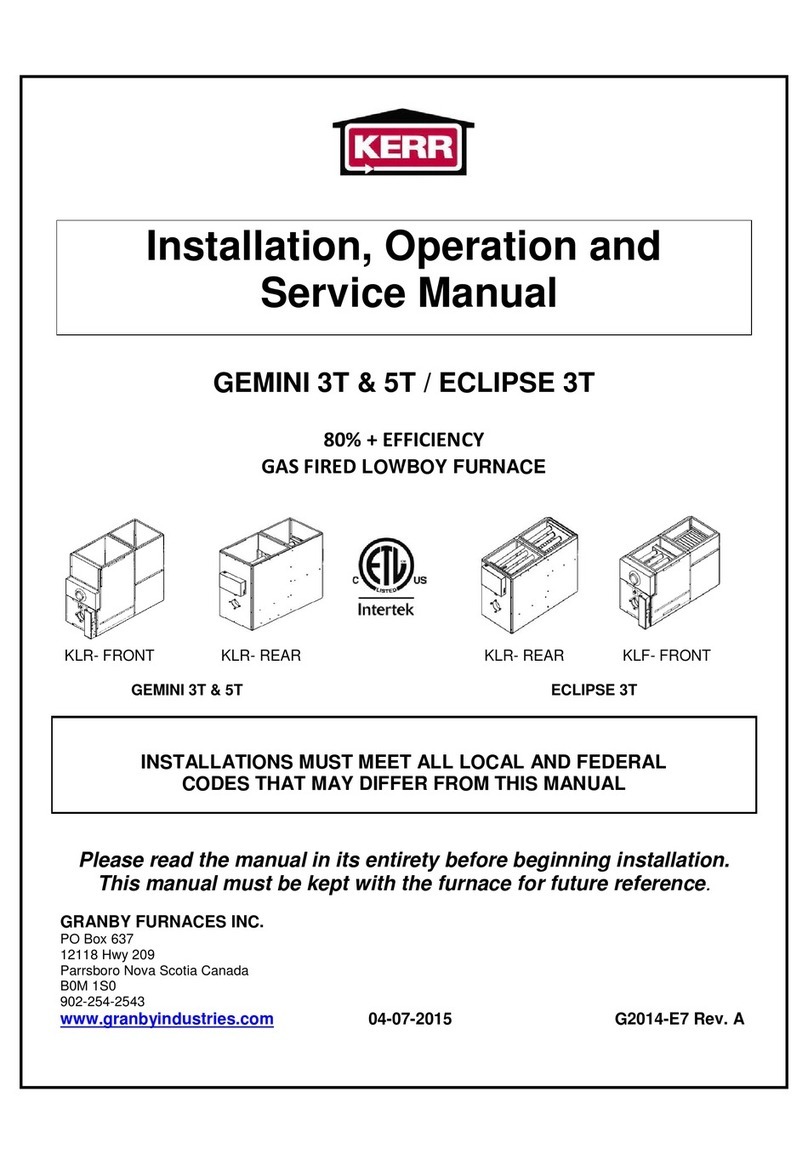
KERR
KERR GEMINI 3T Installation, operation and service manual