Hawker FLEXILEVEL 3 User manual

OPERATING AND INSTALLATION INSTRUCTIONS
FLEXILEVEL 3
Indicator and Controller
Hawker Electronics Limited O&M 96
57 The Avenue, Issue A
Rubery Industrial Estate, Aug 2020
Birmingham, B45 9AL.
Tel: +44(0)121-453-8911
Fax: +44(0)121-453-3777
www.hawker-electronics.co.uk
e-mail: info@hawker-electronics.co.uk

Contents
1. Introduction.................................................................................................................................3
2. Installation...................................................................................................................................3
2.1 Mounting and application environment...................................................................................3
2.2 Cleaning and maintenance.......................................................................................................4
2.3 Electrical connections –Terminal block descriptions ...............................................................4
3. General modes of operation ........................................................................................................7
3.1 Program mode.........................................................................................................................8
3.1.1 Viewing existing programmed values...................................................................................8
3.2 Software programming menu descriptions ..............................................................................8
3.3 Program mode - Programming flow chart..............................................................................10
3.4 Run mode - Description .........................................................................................................13
3.5 Extra functions - Tank simulator and mA monitor..................................................................13
3.5.1 Extra functions flow chart ..................................................................................................14
3.6 Display messages & LED indicators ........................................................................................15
3.7 Display abbreviations with brief description ..........................................................................16
Technical data ...................................................................................................................................17
Declaration of conformity..................................................................................................................18

Page 3of 18
1. Introduction
The FLEXILEVEL 3 (FXL3) when used with a tank sensor1will provide digital indication of a tanks liquid
level or volume. The FXL3 standard model is designed to operate with a linear tank shape i.e. a linear
depth gives linear volume or output. For nonlinear applications see the FXL3NL operating instructions.
The FXL3 has four independent relays that are user programmable over the range being measured. A
fifth relay is available to indicate system power failure. Isolated retransmission current and voltage
signals are available to drive external digital and analogue indicators such as PLC and BMS systems.
The FXL3 is user programmable via four pushbuttons. A user access code can be programmed to
restrict unauthorised access to the program menus.
1The tank sensor is usually a 2 wire loop powered device that operates with 24VDC supplied from the
FXL3. Hawker tank sensors include the MiniSonda, Flexicap and submersible pressure transmitters.
2. Installation
This manual should be read in its entirety before installation.
The crossed-out bin symbol sticker placed on the product reminds you of the need to dispose of the
product correctly at the end of its life.
The product contains NO USER SERVICEABLE PARTS. Repair of this controller shall only be carried out
by the manufacturer or their authorised agent.
The FXL3 Controller must only be installed by suitably competent personnel who have the necessary
experience in installation and commissioning of instrumentation and are familiar with the relevant
codes of practice.
This product has been designed for use in industrial level control applications. It is the user’s
responsibility to ensure the suitability of the equipment for the application, including any external
interface or connected equipment and wiring (risk assessment).
2.1 Mounting and application environment
1. The FXL3 must be installed in the plastic enclosure it is supplied with and should be fixed to a
solid background. The enclosure has provision for 4 mounting screws in its outer corners
which are accessible when the lid is removed. See the data sheet for the mounting-hole
requirements.

Page 4of 18
2. The controller is not intended to be fitted outdoors in direct sunlight or where power washing,
rain or other liquid ingress, or chemical corrosion, may occur. The controller may be further
installed inside a control panel or other protective housing if required.
3. The maximum operating temperatures must be taken into consideration. Adequate spacing
with an air gap should be provided along with ventilation or cooling where necessary. To get
the best performance do not install in environments with large temperature swings.
4. The product should be protected against mechanical impact.
2.2 Cleaning and maintenance
1. Cleaning is not usually required but if necessary the power should be disconnected and the
outer enclosure lid cleaned with a damp cloth and mild detergent. Check any cleaning agents
are suitable for the enclosure material before use. Ensure the product is completely drybefore
reapplying the power.
2. Maintenance is generally not required but visual inspection and calibration check can be
performed in-line with the sites maintenance plan if required.
2.3 Electrical connections –Terminal block descriptions
1. The electrical installation should comply with the relevant regulations for the application,
environment and location it is being installed. Electrical cables should be selected to meet
both the application and product requirements. A 3A max fuse is recommended for the power
supply to the product, and up to 4A max for the relay contacts. See the product datasheet
technical specifications.
2. This product requires a protective earth conductor if it is being powered from ac
mains (hazardous voltage) and/or switching hazardous voltages through the relay contacts.
3. The user connections are only accessible when the products lower trim is removed
(Important: 2 lowest screws only, do not remove the upper trim). Before removing the trim
turn OFF the power to the product and relay contacts, only re-apply power after the trim has
been refitted.
The user connections are all plug in types. All wiring should be terminated and connections checked
before power is applied to the product. It is recommended that cable identifiers are attached to the
cables that reference their function or termination. To reduce noise interference it is important to

Page 5of 18
keep low voltage signal cables away from hazardous voltage and high current cables. The FXL3 comes
with several factory fitted cable glands attached; the user can fit additional glands if required, unused
glands can be sealed to maintain the box integrity. Care should be taken not to damage the PCB if
drilling the box.
Mains Input Connector (TB1)
DC In (TB2)
Notes: For both AC and DC powered products
The electrical supply should be provided via a local fused isolator.
The input power supply should be connected to TB1 (ac) or TB2 (dc) but not both.
When powering the product from DC and the user is switching hazardous voltages through the relay
contacts a protective conductor should be connected to TB1 earth connection.
Vout (TB4)
Use this connector if the product is being powered from mains ac
supply. This is 230V or 110V depending on the product ordered, check
the product label. L=Live, N=Neutral, E=Earth. TB1 has two earth
connections that are internally linked on the PCB, the user is only
required to connect a protective conductor to one of the terminals. All
other terminals are isolated from earth.
Use this connector if the product is being powered
from 24VDC supply. + Positive and - Negative.
Retransmission output signal voltage. This voltage output is linearly
proportional to the value displayed on the LCD e.g. Tank Level and can
be used to drive external equipment. The external load should require
a voltage input and be high impedance. Multiple loads should be
connected in parallel, see retransmission drive specification in data
sheet for load resistance etc.

Page 6of 18
Iout (TB5)
Input (TB3)
mA current input signal to the FXL3, this connects to the tank sensor. The tank sensor output should
be in the range of 0 to 25mA. There are two types of sensor which are detailed below. The 2-wire
loop powered is the most common due to its simplicity and performance.
1. Loop Powered Tank Sensor (2-wire)
If the tank sensor is loop powered (2-wire) the FXL3 can provide its power. In this
case link TB3 pins 1&2, connect TB3 pin3 (+mA) to the tank sensor + connection, connect
TB3 pin4 (-mA) to the tank sensor - connection.
2. Externally Powered Tank Sensor (4-wire)
If the tank sensor is not loop powered i.e. 4-wire it will require external power. In this case
provide external power to the tank sensor as per its instructions, then connect TB3 pin2
(+mA) to the tank sensor +mA connection, connect pin3 (-mA) to the tank sensor -mA
connection. FXL3 TB3 pins 1&4 are left unconnected.
Note: If a screened cable is used the screen is typically connected to the Earth terminal at the FXL3
end only, this is usually for EMI purposes in a noisy environment. If the application requires an isolated
Retransmission output mA current. This current output is linearly
proportional to the value displayed on the LCD e.g. Tank Level. This
current can be used to drive external equipment. The external load
should require a mA current input and be low impedance. Multiple
loads should be connected in series, see retransmission drive
specification in data sheet for load resistance etc.

Page 7of 18
shield (not connected to earth) it can be connected to TB3 pin 4 (-mA). If using an externally powered
device see its specific instructions regarding the screen connection.
Relay Contacts Relay 1, 2, 3, 4 and Fault Relay (TB6, 7, 8, 9 and 10)
Single pole changeover volt free contacts are provided to operate external equipment.
WARNING
Do not switch a mix of hazardous and safe voltage levels through the FXL3 internal relay contacts. If
there is a requirement to do this use interfacing contactors. If switching large or inductive loads use
interfacing contactors, this will preserve the life of the relay contacts. For example, if the application
is switching two external 230VAC pumps and a 5VDC signal to a BMS system. Use 2 x 24VDC
coil/230VAC switching interfacing contactors with overloads for the pumps, and the 5V signal can be
taken direct from a FXL3 relay contact. Connecting like this provides overload protection for the
pumps whilst maintaining safety isolation between voltage levels.
The relay connections have a common type plug so it is important to identify the correct relay being
interfaced. For safety and maintenance purposes it is recommended the relay contact supplies have
a local means of disconnection via a fused isolator.
NOTE: RELAYS 1, 2, 3 & 4 are user programmable; the FAULT RELAY is not user programmable. See
section 5.0 Run Mode –Description.
3. General modes of operation
There are three modes of operation referred to as:
Program mode- Used during commissioning to adjust software parameters.
Run mode- Normal Operation.
Extras mode- Includes a tank cycling mode and mA current meter.
These are available as a sub menu from ‘run’mode.

Page 8of 18
Before the FXL3 can be used some parameters have to be programmed by the user. In all cases this
will be at least the tank empty, tank full, LCD low and LCD high values. Other options are configurable
via the software menus, these are explained below.
3.1 Program mode
To enter program mode hold the M key for 3s. The display will show ‘CodE’, the user must enter the
4 digit access code, the default value is 0000. The user has the option to change this code in the menus
once access has been granted. Generally the UP/DOWN keys are used to alter parameters or values,
the E key used to view or store, the M key to escape. From the Main Menu the UP and DOWN keys
will go forward or back one menu at a time. Keeping the UP or DOWN key pressed while adjusting a
value gives a fast response, press and release the keys for a slow response, i.e. fine adjust.
3.1.1 Viewing existing programmed values
Once in program mode existing settings can be viewed by pressing the E key at the relevant menu.
This is available for all menus except ILo, IHi, dECP and Iact. ILo and IHi values can be checked by
accessing the ILob and IHib menus. Note: There is no need to enter program mode to view the decimal
point and Iact, these can be observed from Run mode by looking at the LCD and Reverse Acting LED
respectively.
It is advisable to make a note of all the user programmed parameters in the event the unit has to be
re-programmed at a later date. This also eliminates the need to empty and fill vessels if it has to be
re-programmed or the data is accidentally erased.
3.2 Software programming menu descriptions
Table 1 outlines the menus and is a logical way to program the unit.
LCD
Description
ILo
Tank empty or low input current. Whilst setting this parameter the FXL3 will display the real time
input current in mA from the tank sensor (XX.XX). Empty the tank to the low point wait for the
value to settle and press E.
ILo must be < IHi. If it isn’t practical to empty the tank this value can be set using the keys, see
ILob menu.
IHi
Tank full or high input current. Whilst setting this parameter the FXL3 will display the real time
input current in mA from the tank sensor (XX.XX). Fill the tank to the high point wait for the value
to settle and press E.
IHi must be > ILo.If it isn’t practical to fill the tank this value can be set using the keys, see IHib
menu.
ILob
Tank empty or low input current. As an alternative to emptying the tank (see ILo) this value can
be set using the FXL3 keys. Enter the mA value into the FXL3 using the UP & DOWN keys.
IHib
Tank full or high input current. If it isn’t possible to fill the tank (see IHi) the high point can be set
in mA using the FXL3 keys. Enter the mA value into the FXL3 using the UP & DOWN keys.
Notes:

Page 9of 18
Where possible it is always best to use the live signal from the tank sensor to set the low and high
points. This will achieve the best accuracy as it takes account of any variables in the installation,
e.g. sensor mounting position and signal tolerance of the tank sensor. The mA value is only a
reference for the LCD low and high points. Provided LcdL and LcdH are set up at the respective
levels of ILo and IHi a very accurate measurement can be achieved.
Always try to use a tank sensor that gives out a reasonable mA output span over the tank liquid
level, this will give best results e.g. 5-18mA would be much better than 5-7mA.
It is acceptable to use combinations of ILo, IHi, ILob, IHib for tank setup.
LcdL
Enter the value you want to display on the LCD at the low input level (ILo). This must be between
0000 and 9999. Use the UP & DOWN keys. LcdL must be < LcdH.
LcdH
Enter the value you want to display on the LCD at the high input level (IHi). This must be between
0000 and 9999. Use the UP & DOWN keys. LcdL must be < LcdH.
Notes:
The decimal point may not be in the correct position when setting LcdL & LcdH this can be ignored
as it is set up in in a later menu.
Examples: If you require - 0 to 100.0%, set LcdL as 0000, and LcdH as 1000
200 to 6000, set LcdL as 0200, and LcdH as 6000
dECP
Use the UP key to set the decimal point position xxxx or xxx.x or xx.xx or x.xxx
r1on
Use the UP & DOWN keys to adjust the relay1 ON point. Must be between LcdL & LcdH, inclusive.
r1oF
Use the UP & DOWN keys to adjust the relay1 OFF point. Must be between LcdL & LcdH, inclusive.
Notes:
The menu also shows on/off points for Relays 2, 3 and 4. Repeat the adjustments as necessary.
If relays are not being used it is recommended to disable the relay, this reduces the power
consumption and stops its LED operating. To disable any relay set the ON&OFF points to the
same value.
OPLo
Use the UP & DOWN keys to adjust (fine tune) the low mA/Volts retransmission value. This value
is precisely calibrated at Hawker Electronics factory but the user can adjust if necessary.
OPHi
Use the UP & DOWN keys to adjust (fine tune) the high mA/Volts retransmission value. This value
is precisely calibrated at Hawker Electronics works but the user can adjust if necessary.
Note:
The retransmission voltage tracks the retransmission current so adjusting one will automatically
alter the other.
IAct
The output retransmission current and voltage may be configured for forward acting (For) or
Reverse Acting (rEv). Forward: 0-100% input gives 0-100% output, Reverse: 0-100% input gives
100-0% output. Reverse is useful if signal monitoring the emptiness of a tank.
CCod
Use the UP & DOWN keys to set a new menu access code between 0000 and 9999. Factory
default code is 0000. A user programmed code will replace the factory default 0000 code. If the
user code is lost contact Hawker Electronics.

Page 10 of 18
3.3 Program mode - Programming flow chart

Page 11 of 18

Page 12 of 18

Page 13 of 18
3.4 Run mode - Description
This is the normal working mode after the unit has been commissioned. When in RUN mode the
power LED will be ON and the LCD will display a tank level or volume. The relays will operate at the
user programmed ON/OFF points. Relay 1, 2, 3 and 4 LEDs will indicate if a relay is energised or de-
energised, LED ON=relay energised. The Fault Relay RY5 is normally energised and will de-energise
with an input fault or power loss, the fault LED will illuminate when a fault occurs provided power is
present. The Rev Acting LED will be OFF unless the user has programmed the unit for a reverse
transmission output.
The LCD colon will flash approximately every 5s to indicate RUN mode.
3.5 Extra functions - Tank simulator and mA monitor
The FXL3 has two extra features that are available from RUN mode, a ‘Tank Simulator’ and ‘Real Time
mA indicator’.These features are useful for commissioning, diagnostics or temporarily taking the unit
out of normal RUN mode.
To access these features from RUN mode press and Hold the UP key for 3s, use the UP key to toggle
between the two features, press E key to select whichever required. To ensure the unit is not left
permanently in these modes there is an automatic timeout of approximately 5 minutes. The menu
will then go back a level and display tCyC or nAIP, press E to re-enter the extra function mode or M to
escape to RUN mode.
LCD
Description
tCyC
Tank Cycle mode. Use the UP and DOWN keys to electronically simulate the liquid level changing
in real time, this simulates cycling through the tank filling and emptying processes.This
simulation will operate all of the relays, LCD, retransmission output current and voltage and LEDs
as though the signal was coming real time from the tank sensor with a changing liquid level. This
is useful for testing the relays and any external equipment operates as expected. It also removes
the need for an external current source or altering any wiring to prove the system. The step
resolution will depend on the LCD values normally 0.1% for 4-20mA 0 to 100.0%, likewise if the
LCD max is 9999 then the steps will be 9.9. The Tank Cycle function will also test for over-range,
under-range, and fault relay operation.
When in this mode the colon will flash approximately every 2s. (Faster while UP/DOWN is
pressed).
It is recommended that the Tank Cycling feature is used post commissioning to check all relays,
LCD and signal outputs operate as expected. Warning: External equipment may operate when
using this function.
nAIP
mA Input mode. The LCD will display the real time mA current input from the tank sensor
connected to TB3. This is useful for diagnostics and checking the mA value from the tank sensor
is correct at various levels in the tank. This feature can also be used for commissioning. For
example if the user monitors the mA values with the tank empty and full when convenient, at a
later time the values can be entered using the ILob and IHib menus for a very accurate setup.
No external multimeter or current source is required. When in this mode the colon will not be
displayed and the decimal point will be permanent e.g. 20.00.

Page 14 of 18
3.5.1 Extra functions flow chart
UPress for 3s
Extra Features Menu
Tank Cycle and mA Meter
access from Run Mode
tCyCTank Cycle EU
D
Pressing M from most menus
escapes
xxxxrun
Flexilevel3 LCD
Flexilevel3 Button
M
2s
M
xxxx
nAIP E
U
xx.xx xxxxrun
2s
M
mA Input
UP key toggles
between each
menu
tCyC: Use the Flexilevel3 UP/DOWN keys to
simulate a changing liquid level. This will
simulate a varying input mA current instead of
using the real tank sensor output.
The LCD, output relays, re-transmit and LEDs
will operate using all the users pre-
programmed values as if the liquid level is
really changing.
This can be performed with or without a real
tank sensor attached.
nAIP: mA Input mode. In this mode the
Flexilevel3 LCD displays the real time current
in mA that it is receiving from the tank sensor
or any device attached to its signal input
connector TB3
Back
to
RUN
mode
These modes are useful for commissioning,
fault finding and creating an artificial tank level
condition.

Page 15 of 18
3.6 Display messages & LED indicators
LCD
FACIA LED
Description
General
PWR
Power LED is ON when AC or DC power is supplied to the product
RLY1-4
Relays 1 to 4, LED is ON when the relay is energised, OFF when de-
energised
REV
ACT
Reverse Acting LED is ON when in Reverse Acting retransmission mode
Errors
----
4 upper LCD dashes. The input is over the programmed range by up to approx.
0.5mA.
----
FAULT
RLY
4 upper LCD dashes & FAULT LED flashing. The input is over the programmed
range by between approx. 0.5mA to 25mA. The fault relay (RY5) will be de-
energised.
Shrt
FAULT
RLY
LCD display ‘Shrt’ & FAULT LED flashing. The input is over the programmed
range by 25mA or more. The fault relay (RY5) will be de-energised.
----
4 lower LCD dashes. The input is under the programmed range
Note: This feature is not available if using zero input current (ILo) as a valid value
OPEN
FAULT
RLY
LCD display ‘OPEN’ & FAULT LED flashing. The input is under the programmed
range or open circuit. The fault relay (RY5) will be de-energised.
Note: This feature is available if using a low or zero input current (ILo) as a valid value
Extra Features mode
tCYC
Tank Cycle, Extras menu. Diagnostic feature. M to escape to Run mode.
nAIP
mA Meter, Extras menu. Diagnostic feature. M to escape to Run mode.
Program mode
run
Temporary flash, the unit is about to start normal running operation
Err
2s flash, a user programmed parameter has been set incorrectly
Note: If this occurs the software will try to take the user back to the incorrectly set menu
done
2s flash, a user programmed parameter change has been acknowledged

Page 16 of 18
3.7 Display abbreviations with brief description
Abbreviation
Full Form
Brief Description
CCod
Change Code
Change the program access code
CodE
Code
Enter the program access code
dECP
Decimal Point
Decimal Point Position for display
Err
Error
Incorrectly programmed value
For
Forward
Retransmission mA is forward acting, i.e. follows input direction
IAct
Current Acting
Retransmission mA direction compared to the input, see ‘For’ or ‘rEu’
IHi
Input High
High level input current from tank sensor in real-time
IHib
Input High Buttons
High level input current entered by user using FXL3 buttons
ILo
Input Low
Low level input current from tank sensor in real-time
ILob
Input Low Buttons
Low level input current, entered by user using FXL3 buttons
LcdH
Liquid Crystal Display High
User displayed value when the tank is at its high input level
LcdL
Liquid Crystal Display Low
User displayed value when the tank is at its low input level
nAIP
mA Input
Extra Menu function, displays the real-time input current in mA
OPEN
Open Circuit
The input mA signal is very low or open circuit
OPHi
Output High
Tank high level output retransmission current in mA
OPLo
Output Low
Tank low level output retransmission current in mA
r1oF
Relay 1 OFF point
Value at which relay 1 will de-energise
r1on
Relay 1 ON point
Value at which relay 1 will energise
r2oF
Relay 2 OFF point
Value at which relay 2 will de-energise
r2on
Relay 2 ON point
Value at which relay 2 will energise
r3oF
Relay 3 OFF point
Value at which relay 3 will de-energise
r3on
Relay 3 ON point
Value at which relay 3 will energise
r4oF
Relay 4 OFF point
Value at which relay 4 will de-energise
r4on
Relay 4 ON point
Value at which relay 4 will energise
rEu
Reverse Acting
Retransmission mA is reverse acting, i.e. reverse of input direction
run
Run Mode
Brief display before the FXL3 starts normal run operation
Shrt
Short Circuit
The input mA signal exceeds the maximum allowed value
tCYC
Tank Cycling Simulator
Extra menu function, use FXL3 keys to simulate the tank level

Page 17 of 18
Technical data
Data taken at 20°C, 230VAC powered unit, loop powered sensor attached, LCD 0-100.0%, 4-20mA I/O. All relays
energised. Due to continuing development specifications are subject to change without notice.
Input Supply: 230VAC, 110VAC ±10% 50/60Hz, 24VDC ±10%
Input Power: VAC 8VA, VDC 4.5W
Inrush Current: 2.7A@24VDC 10ms, 145mA@230VAC 10ms
Installation Category: Over Voltage Cat II
Output Transmitter Supply: 24VDC, ±10% (optional 36VDC), isolated from input, current limiting
at approx. 30mA
Input mA range: 0 to 25mA, any part of
Input Resistance: 10 ohms standard
LCD: 4 Digit, 9mm high characters, scalable between 0000 and 9999 any
part of, user adjustable decimal point
Input Resolution: 00.01mA
Input Response time: <750ms 63% FS
Input Display Accuracy: 0.1%
Input Output Resolution: 0.01mA input - 0.02mA output retransmission
0.03mA input - 0.001V output retransmission
IO Response time: <1.5s 63% FS
LEDs: Relay energised x 4
Power ON x 1
Reverse acting output x 1
Fault x 1
Retransmission: Programmable within 0 to 21mA range, 4-20mA into 1000 ohms, 1-
5V into min 2K, 0-21mA/0-5.25V, isolated from input and supply.
Relays: SPCO contacts. 4A 250VAC, 30VDC resistive load
1x107ops mechanical endurance, 1x105ops electrical endurance
Conformal Coating: Available on request
Password: Program menus access, 4 digit 0000 to 9999 user programmable
Tank Cycling: Simulated tank cycling via keypad 0.1% steps of FS LCD setting
mA meter FXL3 LCD accuracy: mAIP Function, 0.01mA (0.5-24mA 0.05%)
Operating Temp: -10°C to +40°C
Enclosure: 254x180x84mm (HxWxD), IP66, base & cover polycarbonate, sealing
material Polyurethane, cover screw Polyamide - glass-fibre
reinforced - torque 1.2Nm, wall mounting, impact Strength IK08.
Enclosure Mounting holes: (x4)-165mm (hor) 239mm (vert) centres, mounting screw 6-8mm
dia.
Weight: 1.5Kg

Page 18 of 18
Declaration of conformity
EU DECLARATION OF CONFORMITY
Product Model: Flexilevel 3 (FXL3)
Manufacturer: Hawker Electronics Ltd, 57 The Avenue, Rubery Industrial Estate, Rubery,
Birmingham, B45 9AL
This declaration of conformity is issued under the sole responsibility of the manufacturer.
Object of the declaration:
The object of the declaration described above is in conformity with the relevant Union
harmonised legislation:
- Low Voltage Directive (2014/35/EU)
- EMC Directive (2014/30/EU)
- RoHS Directive (2011/65/EU)
Reference to the relevant harmonised standards used in relation to which conformity is
declared:
- LVDEN 61010-1:2010
- EMC Overall Specification EN 61326-1:2006
- RoHS EN 50581:2012
Additional Information:
The product named above complies with the parts of the standards listed. The company
operates an internal production control system that ensures compliance between the
manufactured products and the technical documentation.
Signed for and on behalf of:
Hawker Electronics Ltd on 04th March 2020
J J Slevin (Managing Director)
Table of contents
Other Hawker Controllers manuals
Popular Controllers manuals by other brands
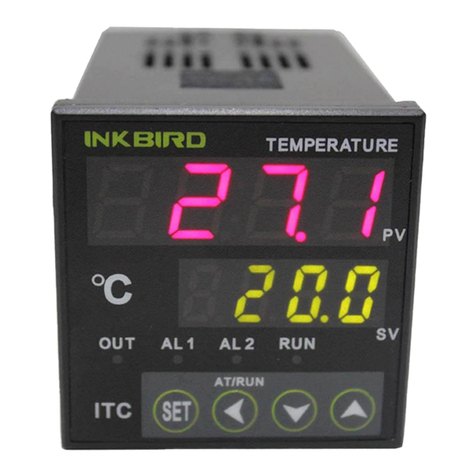
Ink Bird
Ink Bird ITC-100 user manual
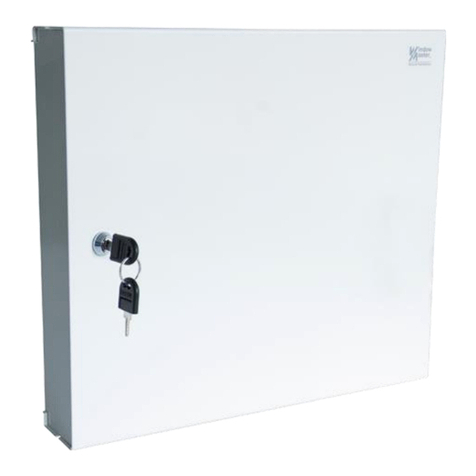
WindowMaster
WindowMaster MotorController WCC 310 Installation instructions manual
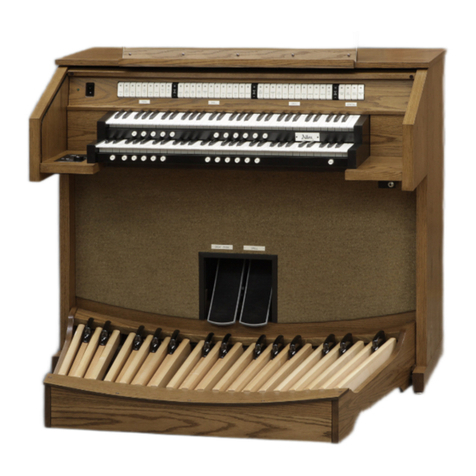
Allen Organ Company LLC
Allen Organ Company LLC Classic R-10 quick start guide
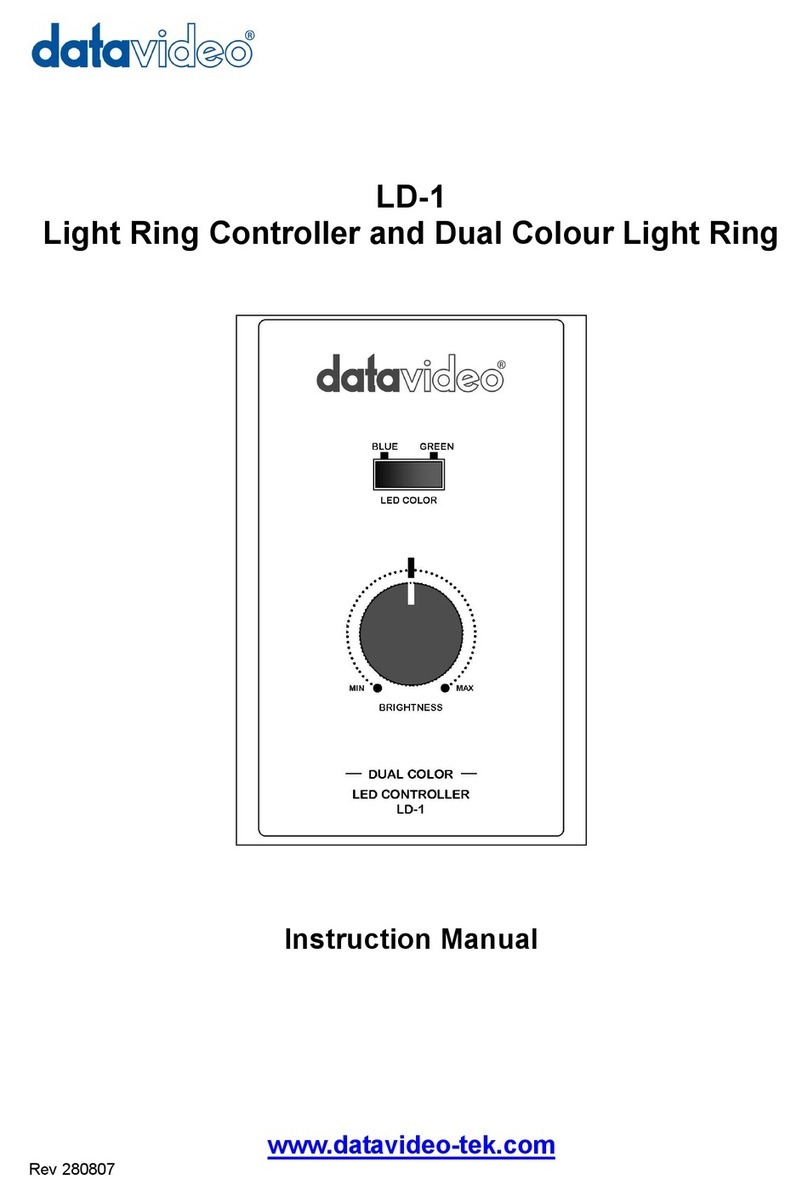
Data Video
Data Video LD-1 instruction manual
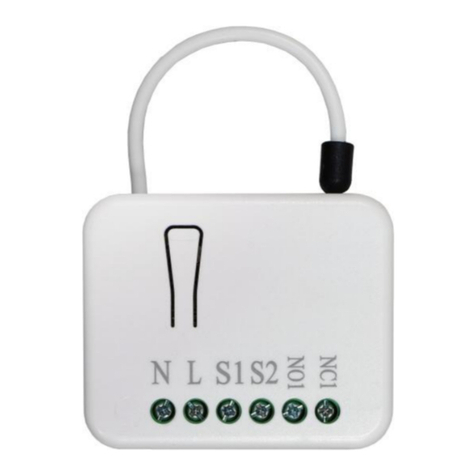
AirLive
AirLive SA-103 user manual
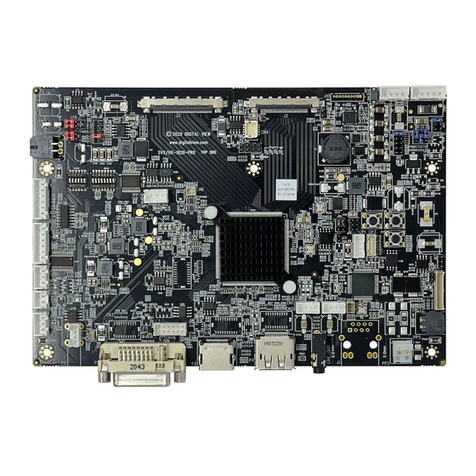
digitalview
digitalview SVX-1920-PRO instructions