Hiniker DB-7929-1 User manual

HINIKER SNOW PLOW
HYDRAULIC UNIT
POWER UNITS
DB-7929-1, DB-7929-2 & DB-7929-3
SERVICE MANUAL
DO NOT USE OR OPERATE THIS EQUIPMENT UNTIL THIS MANUAL
HAS BEEN READ AND THOROUGHLY UNDERSTOOD
PART NUMBER 25012811


Introduction
POWER UNIT OPERATION
GENERAL
The hydraulic power unit DB-7929-1 consists of
a 12 VDC motor, a hydraulic pump rated at 1.3
GPM @ 1600 PSI, and a valve body contain-
ing three electric solenoids, two hydraulic valves
and three adjustable pressure relief valves. The
uid supply line for the pump is submerged in a
1.5 quart capacity reservoir and is ltered by a
149 micron screen.
The hydraulic power unit DB-7929-2 consists of
a 12 VDC motor, a hydraulic pump rated at 1.75
GPM @ 1600 PSI, and a valve body contain-
ing three electric solenoids, two hydraulic valves
and three adjustable pressure relieve valves.
The uid supply line for the pump is submerged
in a 1.5 quart capacity reservoir and is ltered by
a 149 micron screen.
The hydraulic power unit DB-7929-3 consists of
a 12 VDC motor, a hydraulic pump rated at 1.75
GPM @ 1600 PSI, and a valve body contain-
ing three electric solenoids, two hydraulic valves
and three adjustable pressure relieve valves.
The uid supply line for the pump is submerged
in a 1.5 quart capacity reservoir and is ltered by
a 149 micron screen.
The valve body directs hydraulic uid to oper-
ate four hydraulic circuits, raise, lower, angle left
and angle right.The angle and lift circuits receive
uid under pressure, and the lower circuit does
not, however, pressure is generated in the lower
circuit as uid returns to the reservoir.
Raise Mode Of Operation
Operating the Raise switch energizes the 12
VDC Motor and de-energizes the raise/lower so-
lenoid. Hydraulic uid under pressure is then di-
rected through the Neutral position of the angle
left/right spool valve, and a one way check valve
to the lift cylinder.
Releasing the Raise switch de-energizes the 12
VDC motor. The raise circuit is protected by a
pressure relief valve set to relieve system pres-
sure at approximately 2400 PSI Trip and Scoop
Plows, 2000 PSI Home and Steel Straight Plows.
Typically, pressure is relieved when the hydrau-
lic lift cylinder reaches the full up position.
Lower Mode Of Operation
Operating the Lower switch energizes the raise/
lower solenoid, lowers the blade and establishes
a oat circuit. The oat circuit allows uid to en-
ter or exit the raise cylinder allowing the blade to
follow the contours of the ground.
Angle Left or Right Mode Of Operation
Operating the Angle switch energizes the 12
VDC motor and either the angle left solenoid
or angle right solenoid. The angle circuit is pro-
tected by two pressure relief valves (crossover
valves) set to relieve system pressure at ap-
proximately 2100 PSI, Home and Steel Straight
Plow, 2500 PSI, Trip and Scoop Plow and 1600
PSI, 10’ Straight Plow. Typically, pressure is
relieved when the hydraulic angle cylinder (s)
reaches the full left or full right position.

Power Unit - Hydraulic
POWER UNIT - STRAIGHT AND SCOOP PLOW
DWG. NO. 6586

Power Unit - Hydraulic Circuit Diagram
POWER UNIT - HYDRAULIC CIRCUIT DIAGRAM
DWG. NO. 4180A

REF.
NO. PART
NUMBER DESCRIPTION QTY. REF.
NO. PART
NUMBER DESCRIPTION QTY.
1
2
3
4
5
6
7
8
9
10
11
12
13
14
15
16
17
18
25010734
25011706
25010239
033-12007
950-001-327
25010332
25010244
25010221
25010334
25010214
25010236
25010220
950-004-071
25010436
25010240
25010217
25010330
25010518
25010230
25010337
PumpAssembly DB7929-3
PumpAssembly DB7929-2
PumpAssembly DB7929-1
SAE Flat Washer 5/16 Inch
Hex Head Cap Screw 5/16-24 x 3 Gr. 8
Inlet Plumbing Kit
Plumbing Elbow
Filter
Pump O-Ring Kit
Coupling
O-Ring
Plumbing Magnet
Machine Screw #12-24 x 1/2 - Hex Washer Head
Decal - Fill Line
Plastic Tank
Plastic Breather
Adjustable Relief Valve Kit
Adjustable Relief Valve 0-Ring
Motor 12V DC
Motor Brush Kit
1
1
1
2
2
1
1
1
1
1
1
1
4
1
1
1
1
1
1
1
19
20
21
22
23
24
25
26
27
28
29
30
31
32
33
34
35
36
37
25012673
952-001-001
951-001-003
25011654
25011667
25010544
25010992
25012674
25012677
25010746
25010762
25012686
25012685
25012684
25012683
25012688
25012687
950-004-115
952-004-080
Ground Stud
Lock Washer 1/4 Inch
Hex Nut 1/4-20
Release Valve Kit, Double Spade Coil
Solenoid Coil 10V DC
Cartridge Release Valve
O-Ring Kit
Spring
Return Orifice
Check Valve
Manifold O-Ring Kit
ORB Plug
Set Screw 3/8-24 x .38 Selflock
Spring
Ball .25 Dia. Steel
Directional Valve
Solenoid Coil 10V DC
SocketHeadCapScrewW/ThreadLock1/4-20x13/4
Lock Washer 1/4 x .363 O.D.
1
1
1
1
1
1
1
1
1
1
1
2
2
2
2
1
2
4
4
DWG. NO. 6528
Power Unit - Component Location
POWER UNIT - COMPONENT LOCATION

TABLE OF CONTENTS
2502811 6/10 Manual/25012811
Table of Contents 1
Troubleshooting Procedures...............................................................................................2
Plow Will Not Raise............................................................................................................3
Plow Will Not Angle Or Angles In One Direction Only .........................................................4
No Plow Functions Except Down........................................................................................5
Plow Angles Slowly ............................................................................................................6
Plow Lifts Slowly.................................................................................................................7
Plow Will Not Hold Angle....................................................................................................8
Plow Will Not Stay Up.........................................................................................................9
Plow Will Not Lower..........................................................................................................10
DC Motor Removal And Replacement...............................................................................11
DC Motor Brush Removal And Replacement.....................................................................12
Check Valve Removal, Cleaning And Replacement ..........................................................13
Adjustable Relief Valve Removal, Cleaning And Replacement..........................................14
Normally Closed (NC) Release Valve Removal, Cleaning And Replacement.....................15
Valve Removal And Replacement.....................................................................................16
Directional Solenoid Valve Removal, Cleaning And Replacement................................17-18
Directional Relief Valve Removal, Cleaning And Replacement..........................................19
Hydraulic Pump Removal, Cleaning And Replacement ................................................20-22
Electrical/Hydraulic Troubleshooting.................................................................................23
Hydraulic Pump Test ........................................................................................................24
DC Motor Current Draw (Full Load) ..................................................................................25
DC Motor Current Draw (No Load)....................................................................................26
Normally Closed (NC) Release Valve Test........................................................................27
Directional Solenoid Valve Test........................................................................................28
Directional Relief Valve Testing And Adjustment..........................................................29-31
Adjustable Relief Valve Testing And Adjustment..........................................................31-32

TROUBLESHOOTING PROCEDURES
INTRODUCTION
This section is designed to help you troubleshoot
the hydraulic system on the Hiniker Snow Plow.
Each procedure consists of a detailed problem
description followed by a step-by-step ow chart
that will direct you to do certain service or test
procedures. If each service or test procedure is
done step-by-step in the order given, the prob-
lem can usually be corrected.
INITIAL INSPECTION
1. Make sure vehicle is in park and parking
brake is set.
2. Lower plow to the ground before servicing
any part of the hydraulic or electrical sys-
tems.
3. Inspect all wiring harness connectors for:
A. Corrosion or dirt in and/or on Pins and
Sockets.
B. Damaged or missing Pins and/or
Sockets.
C. Full engagement of Pins into respective
Sockets.
4. Check Ground.
A.Makesurebatterygroundtovehicleframe
is clean, corrosion free and tight.
B. Make sure that ground connections from
the Snow Plow harness to vehicle frame
or battery are clean, corrosion free and
tight.
5. Verify the correct hydraulic uid is being
used in unit and make sure oil level is to “Fill
Line” when the plow is on the ground and
angle cylinders are full.
6. Check all hoses and cylinders for proper
condition and leaks.
7. Make sure battery is charged and charging
system is in good condition.
8. Check 10 AMP fuse in relay/junction box
located on the Underhood Wiring Harness.
Replace if bad.
9. Make sure joystick controller is connected in
the cab and turned on.
2 Troubleshooting

Plow Will Not Raise 3
PLOW WILL NOT RAISE
Perform all initial inspections and checks listed on page 2 before beginning test procedure.
WARNING: Never disconnect any hydraulic line or tting with the unit in the raised posi-
tion. Always lower the unit and relieve pressure before removing any lines or caps.Allow
the system to cool down before draining oil or handling system components. Serious
burns can result from contact with hot oil.
PLOW WILL NOT RAISE
ALL OTHER FUNCTIONS ARE NORMAL.
DOES PUMP MOTOR RUN?
Turn ignition switch on and move joystick to
the Up position. Check NC Release Valve
for magnetism by loosely holding metal end
of screwdriver within 1/8” of the nut end of
NC Release Valve Coil.
Is screwdriver attracted to nut end of coil?
Refer to electrical troubleshooting.
Does pump motor run?
Remove, inspect and clean Adjustable Re-
lief Valve. Repair or replace as necessary.
See page 14.
Reinstall and adjust. See page 31-32.
Does plow raise?
Call Hiniker Service Does Plow Raise?
Call Hiniker Service
Yes No
No Yes
No Yes End
Remove, inspect and clean NC Release
Valve. See page 15. Repair or replace as
necessary. Does plow raise?
No Yes End
YesNo
End
YesNo
Refer to electrical troubleshooting.
Check ttings and lift cylinder hose for ob-
structions. Remove lift cylinder and drain
oil. Check for a frozen/binding cylinder by
manually compressing and extending the
cylinder. Repair or replace as necessary.
Does plow raise?
No Yes End

PLOW WILL NOT ANGLE OR
ANGLES IN ONE DIRECTION ONLY
Perform all initial inspections and checks listed on page 2 before beginning test procedure.
PLOW WILL NOT ANGLE OR ANGLES IN ONE DIRECTION ONLY.
UP AND DOWN FUNCTIONS ARE NORMAL.
DOES PUMP MOTOR RUN?
Test the Directional Solenoid Valve (s). See
“Directional Solenoid Valve Test” page 28.
Repair or replace as necessary.
See page 17-18.
Does plow angle both ways?
Remove, clean and inspect RV1 & RV2 Re-
lief Valves. See page 19. Repair or replace
as necessary. Reinstall. Adjust pressure.
See page 29-30.
Does plow angle both ways?
NoYes
YesNo End
Call Hiniker Service
Refer to electrical troubleshooting.
Does pump motor run?
YesNo End
YesNo
WARNING: Never disconnect any hydraulic line or tting with the unit in the raised posi-
tion. Always lower the unit and relieve pressure before removing any lines or caps.Allow
the system to cool down before draining oil or handling system components. Serious
burns can result from contact with hot oil.
Note: If the plow angles only one way when the joystick is moved in any direction (except Down),
The directional solenoid valves is stuck and holding the valve in that position (see “Directional
Solenoid Valve Removal, Cleaning and Replacement “ page 17-18).
Note: If the plow raises when joystick is moved left or right, the valve is stuck in the NEUTRAL posi-
tion (see “Valve Removal and Cleaning” page 17-18).
4 Plow Will Not Angle/Angles One Direction Only
Call Hiniker Service
Does plow angle
both ways?
YesNo End
Check angle cylinder hoses and ttings for
obstructions. Remove angle cylinders from
plow and drain oil. Check for a frozen/bind-
ing cylinder by manually compressing and
extending the cylinder. Repair or replace as
necessary.
Does plow angle both ways?
YesNo End

No Plow Functions Except Down 5
NO PLOW FUNCTIONS EXCEPT DOWN
Perform all initial inspections and checks listed on page 2 before beginning test procedure.
NO PLOW FUNCTIONS EXCEPT DOWN
DOES PUMP MOTOR RUN?
Does Starter Solenoid click
when plow is functioned? YesNo Remove Motor from Power Unit (see “DC Motor
Removal” on page 11). Remove Coupler and in-
spect for damage. Is Coupler good?
YesNo
Note: When performing the following test procedures, make sure that you test to the vehicle battery
terminals, not to the vehicle ground or DC motor ground.
YesNo
Is there 12 VDC on
the small terminal of
the Starter Solenoid
with joystick in angle
or up position?
Is there 12 VDC on
both large terminals
of the Starter Sole-
noid with joystick in
angle or up position?
Replace Coupler and inspect Input Shaft on
Hydraulic Pump. Replace parts as required.
Does plow operate correctly?
Install Coupler onto Hydraulic
PumpShaftandrotatebyhand.
Does Pump turn by hand?
NoYes
YesNo
Check all wiring and plug connectors from
Starter Solenoid back to joystick control-
ler. Replace or repair as required.
Does plow operate correctly?
YesNo
End
End
Check Starter Solenoid Mount Plate for
ground. Is ground good?
YesNo
Check 24” black wire.
Ensure Starter Sole-
noid is connected to
goodvehiclegroundei-
ther directly or through
24” black wire.
Replace Starter
Solenoid.
Does plow operate
correctly?
YesNo
End
Remove, inspect
and clean Pump.
See page 20-22. YesNo
Pull Reservoir. Inspect and clean pump intake screen and
tube for damage and/or breakage or plugged condition.
See page 20-22. Repair and/or replace parts as required.
Does plow operate correctly?
YesNo End
Replace Starter Solenoid.
Does plow operate correctly?
YesNo Is there 12 VDC
atredstripedwire
on Motor Power
Terminal?
YesNo
End YesNo
Checkredstripedwirefrom
Motor to Starter Solenoid.
Repair or replace parts as
required.
Installjumpercable
fromvehiclebattery
NEG (-) terminal to
case of motor.
Does motor run?
Repair (page 12).
Replace motor (page 11).
Check black wire from motor to vehicle battery NEG
(-) terminal. Repair and/or replace parts as required.
Does plow operate correctly?
YesNo
YesNo
Refer to electrical troubleshooting.
Refer to electrical troubleshooting.
Refer to electrical troubleshooting.

PLOW ANGLES SLOWLY
Perform all initial inspections and checks listed on page 2 before beginning test procedure.
PLOW ANGLES SLOWLY
ALL OTHER FUNCTIONS ARE NORMAL.
REMOVE, INSPECT AND CLEAN DIRECTIONAL VALVE.
SEE PAGE 17-18.
ADJUST PRESSURE. SEE PAGE 29-30.
DOES PLOW ANGLE FULLY LEFT AND
RIGHT FROM CENTER IN APPROXIMATELY 2 SECONDS?
Remove, inspect and clean Directional
Valve. See page 17-18.
Does plow angle fully left and right from en-
ter in approximately 2 seconds?
Check ttings and lift cylinder hose for ob-
structions. Remove and drain oil from angle
cylinders. Check for a binding cylinder by
manually compressing and extending cyl-
inders by hand. Repair or replace as nec-
essary. Does plow angle fully left and right
from center in approximately 2 seconds?
YesNo
YesNo End
Yes
No
Note: Until pump system warms, slow functioning of the V-Plow will occur in extremely cold tempera-
tures unless a high quality oil that is appropriate for the temperatures in which you will be plow-
ing snow is used. See chart below.
Note: Ensure vehicle battery is fully charged and alternator output is 13.6 Volts minimum with engine
running and no accessories on.
End
Call Hiniker Service DWG NO. 3066
6 Plow Angles Slowly
WARNING: Never disconnect any hydraulic line or tting with the unit in the raised posi-
tion. Always lower the unit and relieve pressure before removing any lines or caps.Allow
the system to cool down before draining oil or handling system components. Serious
burns can result from contact with hot oil.

Plow Lifts Slowly 7
PLOW LIFTS SLOWLY
Perform all initial inspections and checks listed on page 2 before beginning test procedure.
PLOW LIFTS SLOWLY
ALL OTHER FUNCTIONS ARE NORMAL.
DOES PLOW LIFT FULLY UP IN APPROXIMATELY 2 SECONDS?
Remove, inspect and clean Adjustable
Relief Valve. See page 14.
Adjust pressure. See page 31-32.
Does plow lift fully up in approximately 2
seconds?
Check ttings and lift cylinder hose for ob-
structions. Remove lift cylinder and drain
oil. Check for a binding cylinder by manu-
ally compressing and extending the cylinder.
Repair or replace as necessary.
Does plow lift fully up in approximately 2
seconds?
YesNo
YesNo End
Yes
No
Note: Until pump system warms, slow functioning of the V-Plow will occur in extremely cold tempera-
tures unless a high quality oil that is appropriate for the temperatures in which you will be plow-
ing snow is used. See chart below.
Note: Ensure vehicle battery is fully charged and alternator output is 13.6 Volts minimum with engine
running and no accessories on.
End
Call Hiniker Service DWG NO. 3066
WARNING: Never disconnect any hydraulic line or tting with the unit in the raised posi-
tion. Always lower the unit and relieve pressure before removing any lines or caps.Allow
the system to cool down before draining oil or handling system components. Serious
burns can result from contact with hot oil.

8 Plow Will Not Hold Angle
PLOW WILL NOT HOLD ANGLE
Perform all initial inspections and checks listed on page 2 before beginning test procedure.
PLOW WILL NOT HOLD ANGLE.
ALL OTHER FUNCTIONS ARE NORMAL.
REMOVE, INSPECT AND CLEAN RELIEF VALVES.
SEE PAGE 19.
ADJUST PRESSURE. SEE PAGE 29-30.
DOES PLOW HOLD ANGLE?
Remove, inspect and clean Directional
Valve. See page 17-18.
Does plow hold angle?
YesNo
YesNo
End
End
Call Hiniker Service
WARNING: Never disconnect any hydraulic line or tting with the unit in the raised posi-
tion. Always lower the unit and relieve pressure before removing any lines or caps.Allow
the system to cool down before draining oil or handling system components. Serious
burns can result from contact with hot oil.

Plow Will Not Stay Up 9
PLOW WILL NOT STAY UP.
ALL OTHER FUNCTIONS ARE NORMAL.
REMOVE, INSPECT AND CLEAN CHECK VALVE.
SEE PAGE 13.
DOES PLOW STAY UP?
Remove, inspect and clean NC
Release Valve.
See page 15.
Does plow stay up?
Momentarily move joystick to the Up po-
sition to ensure that the oat mode is Off.
Verify that there is no voltage at the NC Re-
lease Valve, using a voltmeter or test light.
Is voltage present?
YesNo
YesNo End
Refer to electrical troubleshooting.
Does Plow Stay Up?
YesNo
End
YesNo
Call Hiniker Service
End
PLOW WILL NOT STAY UP
Perform all initial inspections and checks listed on page 2 before beginning test procedure.
WARNING: Never disconnect any hydraulic line or tting with the unit in the raised posi-
tion. Always lower the unit and relieve pressure before removing any lines or caps.Allow
the system to cool down before draining oil or handling system components. Serious
burns can result from contact with hot oil.
Call Hiniker Service

10 Plow Will Not Lower
PLOW WILL NOT LOWER
ALL OTHER FUNCTIONS ARE NORMAL.
PERFORM STEPS 1 THRU 5 OF THE
“NORMALLY CLOSED RELEASE VALVE TEST.”
SEE PAGE 27.
DO NOT REPLACE CARTRIDGE VALVE AT THIS TIME.
DOES PLOW LOWER?
Support plow blade with a oor jack or
other suitable means. Relieve hydrau-
lic pressure by loosening hose tting on
lift cylinder. Remove, inspect and clean
NC Release Valve. See page 15.
Ensure plunger pushes in approximate-
ly 1/16” and springs back. If it does not,
replace cartridge valve. Reinstall.
Does plow lower?
Support plow blade same as above.
Check for plugged ttings, hydraulic hose
and external ow control valve. Remove
and drain oil from lift cylinder. Check for
frozen/binding cylinder by manually com-
pressing and extending the cylinders.
Repair or replace as necessary.
Does plow lower?
YesNo
YesNo End
YesNo
End
End
PLOW WILL NOT LOWER
Perform all initial inspections and checks listed on page 2 before beginning test procedure.
WARNING: Never disconnect any hydraulic line or tting with the unit in the raised posi-
tion. Always lower the unit and relieve pressure before removing any lines or caps.Allow
the system to cool down before draining oil or handling system components. Serious
burns can result from contact with hot oil.
Call Hiniker Service

DC Motor Removal and Replacement 11
DC MOTOR REMOVAL AND REPLACEMENT
WARNING: Disconnect Vehicle Battery
prior to performing this procedure to
avoid electrical shock or burns.
1
2
PHOTO NO. 1000322A
Disconnect the vehicle negative battery termi-
nal wire (solid black). Remove motor terminal
nut and remove power lead (solid red or red-
striped).
MOUNT BOLTS
PHILLIPS HEAD SCREWS
MOTOR CAP
MOTOR
DWG NO. 3512
Remove the two Phillips head screws from the
motor cap. Using a 3/8” wrench loosen the two
motor mounting bolts. Do not remove bolts.
NOTE: Use care when removing the motor from
the endhead, the motor can separate into three
pieces and will require additional time to reas-
semble.
Hold motor together while removing it from the
end head.
NOTE: If oil is found in the cavity of the valve
passage where the coupling is located, replace-
ment of the oil pump shaft seal is necessary be-
fore the unit can be put back into service.
See page 20.
PHILLIPS HEAD SCREWS
MOTOR CAP MOTOR
MOTOR TERMINAL
(POS)
GROUND SCREW
(NEG) COUPLING
PUMP SHAFT
VALVE PASSAGE
SHIPPING NUTS
(REMOVE)
DWG NO. 3513
Remove shipping nuts from new motor, align
splined shaft of motor with coupler and position
motor onto the location pins on the end head.
Torque the two motor mounting bolts to 5-8 ft.
lbs. with a 3/8” wrench. Reattach motor cap.
Reconnect the vehicle negative battery terminal
wire (solid black) and the power lead (solid red
or red striped). See photo 1000322A.

12 DC Motor Brush Removal and Replacement
DC MOTOR BRUSH REMOVAL AND REPLACEMENT
WARNING: Disconnect Vehicle Battery
prior to performing this procedure to
avoid electrical shock or burns.
1
2
PHOTO NO. 1000322A
Disconnect the vehicle negative battery terminal
wire (solid black). Remove motor terminal nut and
remove power lead (solid red or red-striped).
PHILLIPS HEAD SCREWS
MOTOR CAP
MOTOR
DWG NO. 3514
Remove the two Phillips head screws from the mo-
tor cap. Remove motor cap.
PHOTO NO. 3747
NOTE: If your motor is equipped with two (2)
brushes with bare wires (Ground brushes) and
two (2) brushes with insulated wires (POS brush-
es), make sure that you note location of the two
types and replace them with like type brushes.
WARNING: Failure to replace Brushes
correctly will severely damage Motor
and may cause electrical res. FAIL-
URE TO HEED CAN RESULT IN SERIOUS IN-
JURY OR DEATH.
PHOTO NO. 1000326
Remove screws from brush leads. Carefully pry
back the tension spring with a tool and remove
brush. Replace brush if it is 1/4” or less in length.
(P/N 25010337)
IMPORTANT: Brushes should be replaced as
a set. DO NOT replace one Brush only.
Clean the motor commutator with a spray elec-
trical contact cleaner before installing brushes.
To install new brushes reverse the procedure.

Check Valve Removal, Cleaning and Replacement 13
CHECK VALVE REMOVAL, CLEANING &
REPLACEMENT
WARNING: Never disconnect any hy-
draulic line or tting with the unit in
the raised position. Always lower the
unit and relieve pressure before removing
any lines or caps. Allow the system to cool
down before draining oil or handling system
components. Serious burns can result from
contact with hot oil.
PHOTO NO. 1000298A
Remove the check valve body with a 7/8” hex
socket.
PHOTO NO. 10002317
Inspect the check valve O-rings for wear and
contamination. Replace if necessary. (P/N
25010992).
Inspect the ball and ball seat for wear, gouges
or pitting. Replace the assembly as necessary.
Clean with solvent and inspect the end head
carefully with a pencil magnet for contamination.
Flush out end head with clean hydraulic oil.
Install check valve body and tighten to 10-15 ft.
lbs.

14 Relief Valve Removal, Cleaning & Replacement
RELIEF VALVE REMOVAL,
CLEANING AND REPLACEMENT
WARNING: Never disconnect any hy-
draulic line or fitting with the unit in
the raised position. Always lower the
unit and relieve pressure before removing
any lines or caps. Allow the system to cool
down before draining oil or handling system
components. Serious burns can result from
contact with hot oil.
PHOTO NO. 1000294A
Remove the cap with a 1” wrench.
Remove the valve adjustment screw with a
straight slot screwdriver. Remove spring.
Remove the ball with a pencil magnet. Inspect
the spring, ball, and seat in the end head for
contamination, distortion, or wear.
Flush out end head with clean hydraulic oil.
BALL
O-RING
SPRING
ADJ. SCREW VALVE CAP
DWG NO. 3516
Re-install the ball, spring and adjustment screw.
The adjustment screw should be turned in ap-
proximately 5-6 full turns.
Check O-ring in cap for cuts and replace as nec-
essary. (P/N 25010518).
Install cap, ensuring that the O-ring is in cap
groove. Tighten cap with 1” wrench.
Adjust relief pressure. See “Adjustable Relief
Valve, Testing and Adjustment.” Page 31-32.
This manual suits for next models
2
Table of contents
Popular Portable Generator manuals by other brands
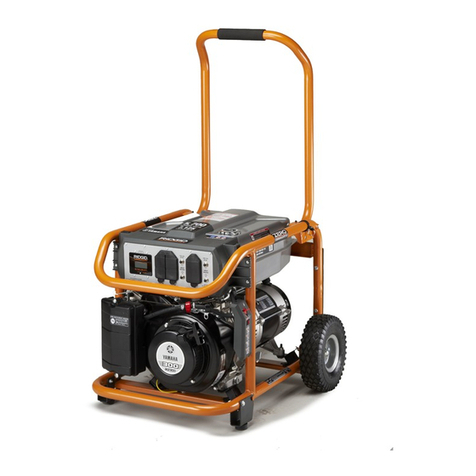
RIDGID
RIDGID RD905712 Series Operator's manual
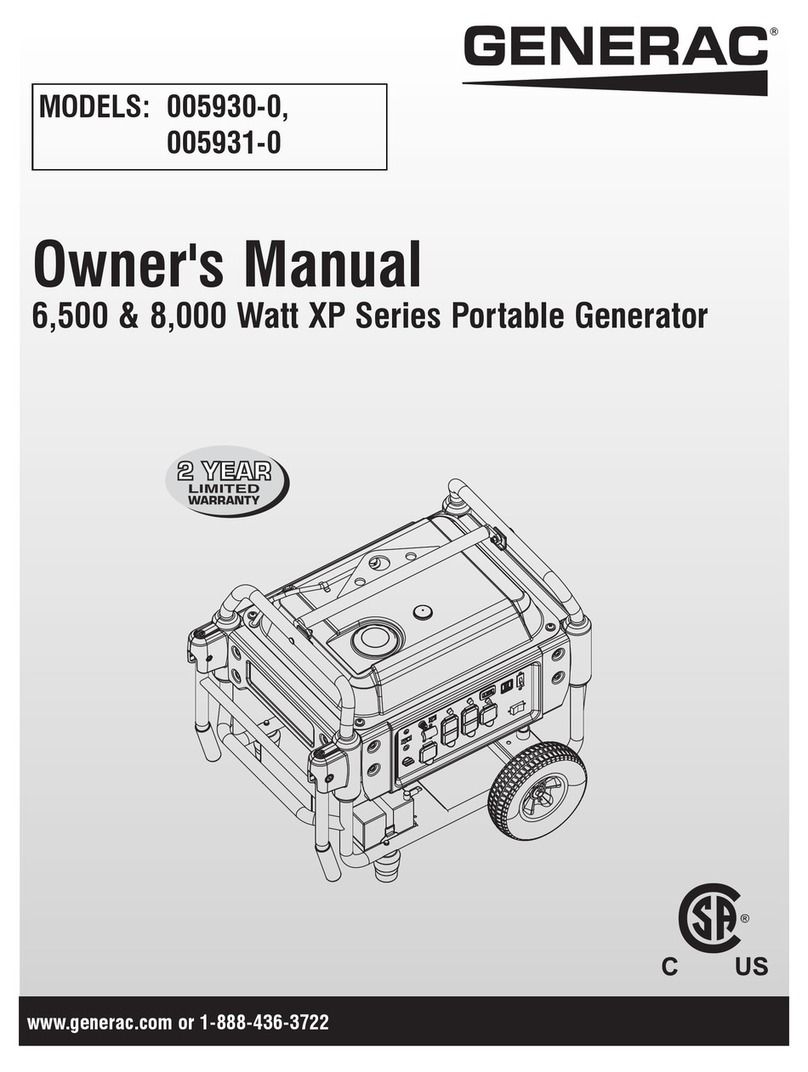
Generac Power Systems
Generac Power Systems 005930-0 owner's manual

Energizer
Energizer eZV4800 user guide
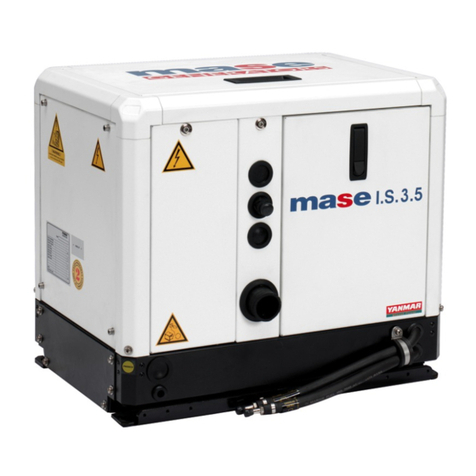
Mase
Mase IS 3.5 Use and maintenance manual
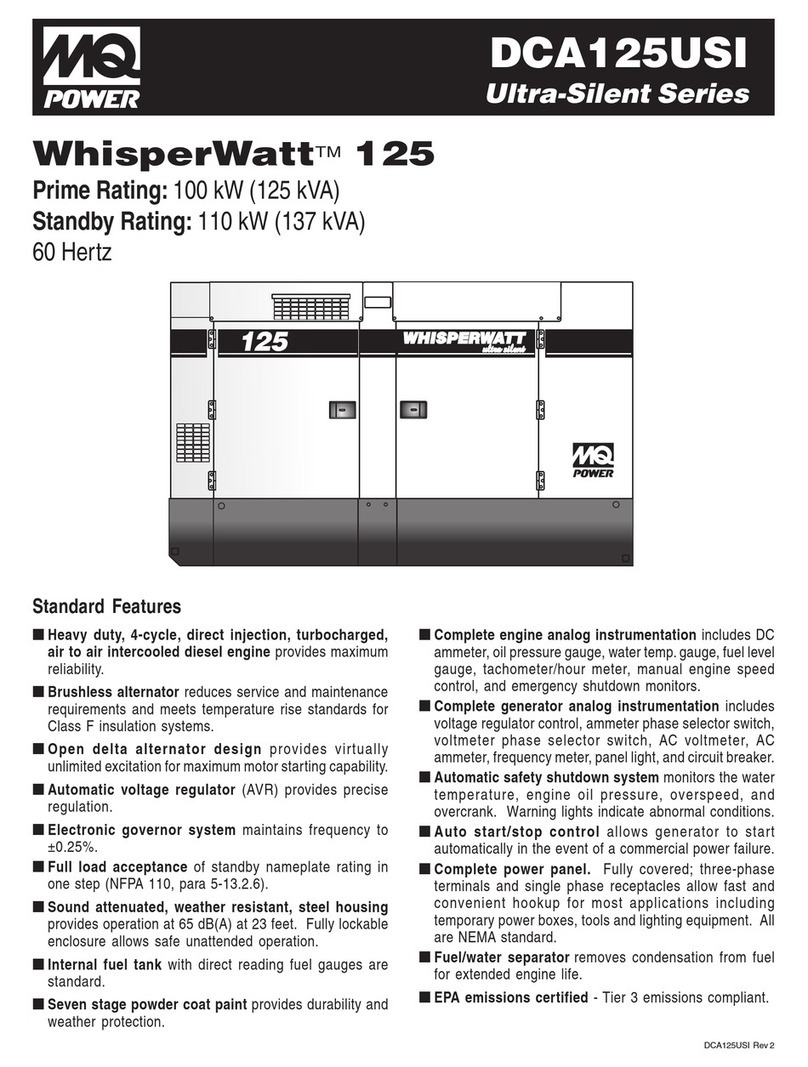
MULTIQUIP
MULTIQUIP WhisperWatt 125 DCA125USI Features and specifications
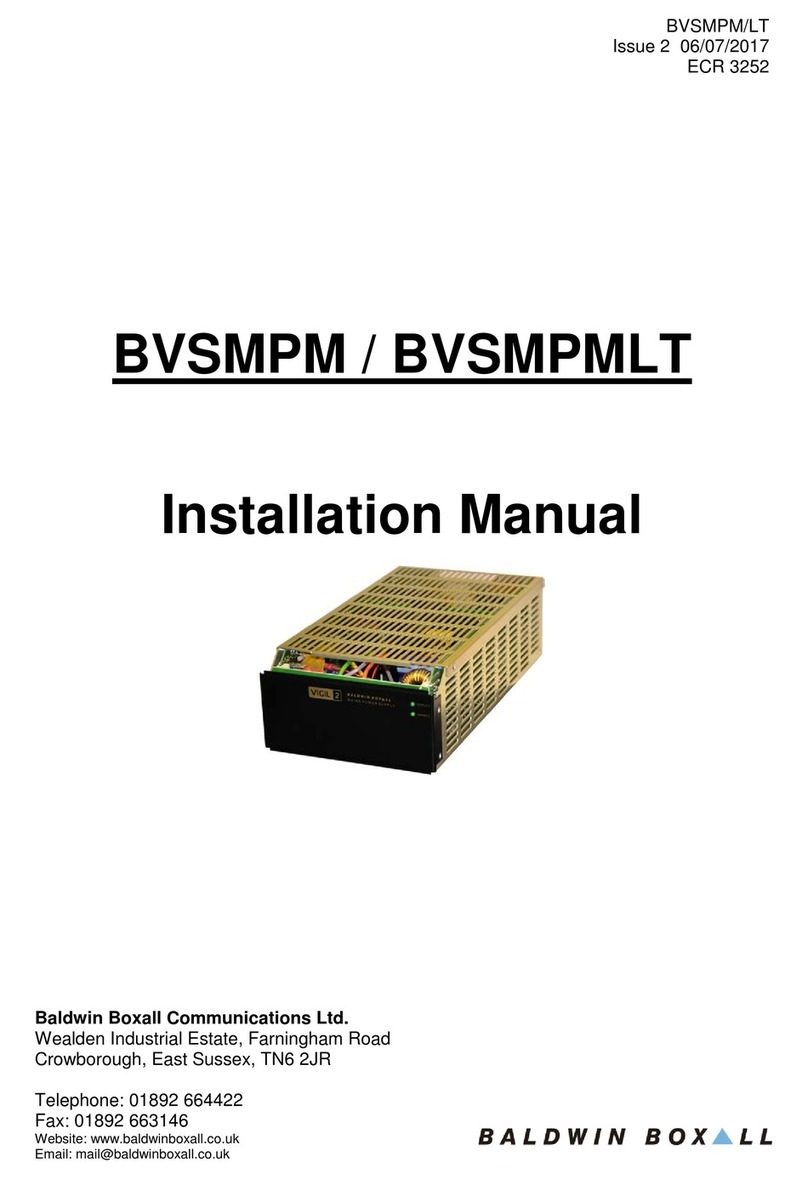
Baldwin Boxall
Baldwin Boxall BVSMPM installation manual