Hogfors 31300CS Series User manual

INSTALLATION AND OPERATION
MANUAL 31300CS SERIES
30/04/2014

INSTALLATION AND OPERATION MANUAL 31300CS SERIES
2
CONTENT
General.................................................................................................3
Transport and storage......................................................................4
Hoisting................................................................................................5
Installation position ..........................................................................6
Recommended mounting................................................................11
Welding.................................................................................................12
Flushing ...............................................................................................13
Start up.................................................................................................14
Control use..........................................................................................15
Cavitation.............................................................................................17
Valve operation ..................................................................................19
Troubleshooting.................................................................................21

INSTALLATION AND OPERATION MANUAL 31300CS SERIES
3
General
For complete information regarding the installation, operation, maintenance and
repair of the valve please see the full version of the instructions for installation, ope-
ration and maintenance of Högfors valves.
Valve disc must remain in closed position during transport, storage and installation.
Prohibited to hoist the valve from the
actuator.
Prohibited to remove the actuator during transportation, installation and operation.

INSTALLATION AND OPERATION MANUAL 31300CS SERIES
4
The valve is delivered with an actuator that has been adjusted at the factory.
Transport and storage
•
When receiving the valve, please check that there is no transportation damages.
•
The valve must be stored in a secure location away from rain.
•
The packing is not designed for long-term storage in the open air.
Prohibited to change the factory settings of the actuator

INSTALLATION AND OPERATION MANUAL 31300CS SERIES
5
Hoisting
Please follow the recommended method for hoisting as shown below. Please use soft
cable for hoisting.
Förbjudet att lyfta ventilen i manöverdonet

INSTALLATION AND OPERATION MANUAL 31300CS SERIES
6
Installation postition
Please do not install the valve in the lowest sections of the pipeline or other places
where there is likely to be a concentration of impurities.

INSTALLATION AND OPERATION MANUAL 31300CS SERIES
7
The valve can be mounted in horizontal (A), vertical (V) or diagonal (C) pipeline.

INSTALLATION AND OPERATION MANUAL 31300CS SERIES
8
Please place the valve as far as possible from sources of turbulence: pumps, elbows
and tees.
Minimum Clearances:
After the tee or tapping L1 = DN x 3
Before the pump (suction side) L2 = DN x 3
After the pump (pressure side) L3 = DN x 5
L3
L2
L1

INSTALLATION AND OPERATION MANUAL 31300CS SERIES
9
Do not install the pipeline support under the valve.
If the valve valve is the final item in the pipeline, then a welded plug flange must be
installed.

INSTALLATION AND OPERATION MANUAL 31300CS SERIES
10
Recommended position of the valve in the pipeline:
1) shaft horizontally or
2) shaft inclined, but as close as possible to the horizontal position.
Rekommenderad position Tillåten position
Tillåten position Ej rekommenderad position
Vinkel a <45 deg
Vinkel a <45 deg

INSTALLATION AND OPERATION MANUAL 31300CS SERIES
11
Recommended mounting
When installing with the recommended pipe insertions, which are welded in the
workshop, the insertion length is 0.2 - 1.4 meters depending on the DN of the
pipeline.
0.2—1.4m
Clean the pipes before mounting.
Keep the disc in the closed position
during installation!

INSTALLATION AND OPERATION MANUAL 31300CS SERIES
12
Welding
Welding surface is covered with a layer of anticorrosion protection. Please remove it
prior to welding by using organic solvent, or mechanically.
Connect the pipe and the valve together with 4-8 tack welds, depending on the size
of the valve DN. Single tack weld length maximum 80 mm. Tack welding order is
counterclockwise 1-2-3-4-5-6 as shown below.
Welding root, filling and final pass order 1-2-3-4 counterclockwise as shown below.
Note! Ensure that the valve body is not deformed by welding.

INSTALLATION AND OPERATION MANUAL 31300CS SERIES
13
When the valve is mounted in vertical
pipeline, cover the valve disk with
100-150mm water cushion.
Flushing
After installation, please flush the pipeline to remove impurities.
Fushing is done by adding pressure and flow in
the pipeline.
Set the valve disc to the open position of 25-30
degrees to reach the maximum flow velocity at
valve seat area.
The valve disc must remain in a closed position during the whole welding process.

INSTALLATION AND OPERATION MANUAL 31300CS SERIES
14
Start-up
Use the by-pass valve for filling the pipeline. By-pass valve is required for DN400 and
more.
The by-pass valve size depends on the lenght of the pipeline. If using too small DN
size by-pass valve it will be impossible to fill the pipeline within a reasonable (given)
time. The recommended DN size of the by-pass valve is 10% - 20% of the size of the
main valve DN.
The valve disc must remain in closed position until the pipeline is completely filled.

INSTALLATION AND OPERATION MANUAL 31300CS SERIES
15
Control use
The Högfors valves are suitable for shut-off and for control use.
Operating angle range of the disk for control is 10 ˚ - 80 ˚.
Flow KV values for the valves and the formula for the flow KV
calculation can be found in the product card.
10˚....80˚
In case of difficulty in the selection of control valve, please contact your local
Högfors representative.
Disc opening angles below < 10 degree
are not suitable for control.
α =

INSTALLATION AND OPERATION MANUAL 31300CS SERIES
16
When using the pipeline reduction with the valve position please consider the
increased mechanical stresses affecting the valve. Please use additional supports.
Pipeline reduction leads to an acceleration in the flow:
The acceptable flow rate for water:
- Recommended velocity - 2 m / s,
- Maximum allowable - 5 m / s,
- Short-time maximum allowable - 7.5 m / s.
Pipeline reduction DN size should not be less than 50% of the DN main pipe.
DN> DN (pipe reduction)> (DN / 2)
DN (control)
The flow rate should not exceed the values above.

INSTALLATION AND OPERATION MANUAL 31300CS SERIES
17
In operation, the long term use of valve for control may affect the seat tightness
class. In order to improve the reliability of the network, please use additonal valve for
Shut-off use. 1st valve for control 2nd for shut-off.
Cavitation
Operation valve under continuous nt cavitation conditions can lead to accelerated
wear of valve parts and significantly shorten the life of the valve.
Appearance of the cavitation is usually accompanied by, a sharp increase in acoustic
noise and vibrations occur.
In most cases, the risk of cavitation can be significantly reduced by constructive
measures in the design of the pipeline.
Avoid continous cavitation conditions.

INSTALLATION AND OPERATION MANUAL 31300CS SERIES
18
If the disk is in the open position by a small angle (0-10 ˚), then before closing it is ne-
cessary to open the disk to a larger angle (25 ˚ -30 ˚) for flushing impurities that may
have been collected between the disk and the seat.
1.
Disc open 10 ˚ degree
2.
Flushing Disc 25 ˚ degree
3.
Disc closed
3
1
2

INSTALLATION AND OPERATION MANUAL 31300CS SERIES
19
Valve operation
Do not use excessive force to rotate the wheel gear. Only 1 person is needed to ope-
rate the gear and handwheel. Do not use any tools to operate the valve. Do not try to
adjust the actuator settings.
Disconnecting the actuator will lead to the loss of the factory settings of the actuator.
When reinstalling the actuator it requires reconfiguration.
Prohibited the remove the actuator when there is pressure in the pipeline.

INSTALLATION AND OPERATION MANUAL 31300CS SERIES
20
Each manual gearbox and an electric actuator have a mechanical position indicator.
Position "OPEN" Position "SHUT“
If the valve is already installed in the pipeline, the approximate position of the disk
can be determined by the groove at the end of the shaft.
Groove at the end of
the shaft.
Table of contents
Other Hogfors Control Unit manuals
Popular Control Unit manuals by other brands
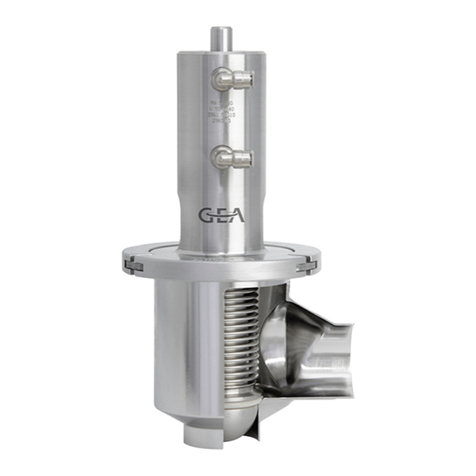
GEA
GEA Aseptomag GD Operating instruction
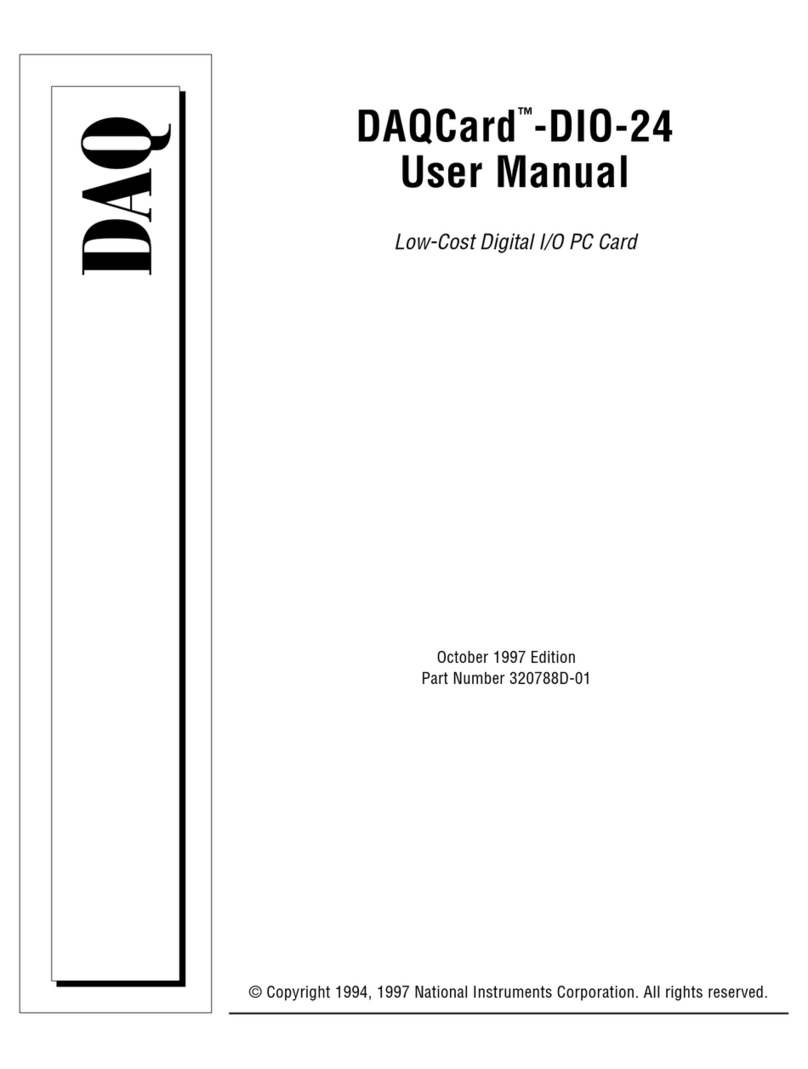
National Instruments
National Instruments DAQCard-DIO-24 user manual
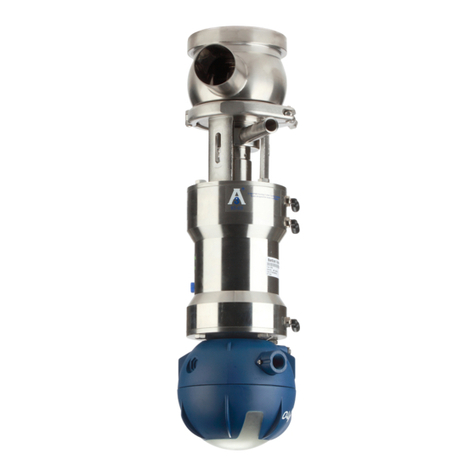
Bardiani
Bardiani B935 Use and maintenance manual
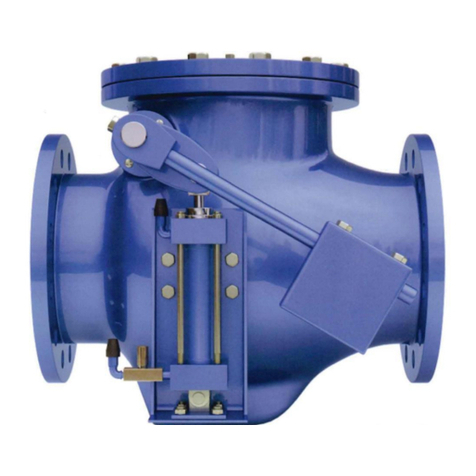
DeZurik
DeZurik APCO CVS-6000 Installation, operation and maintenance manual
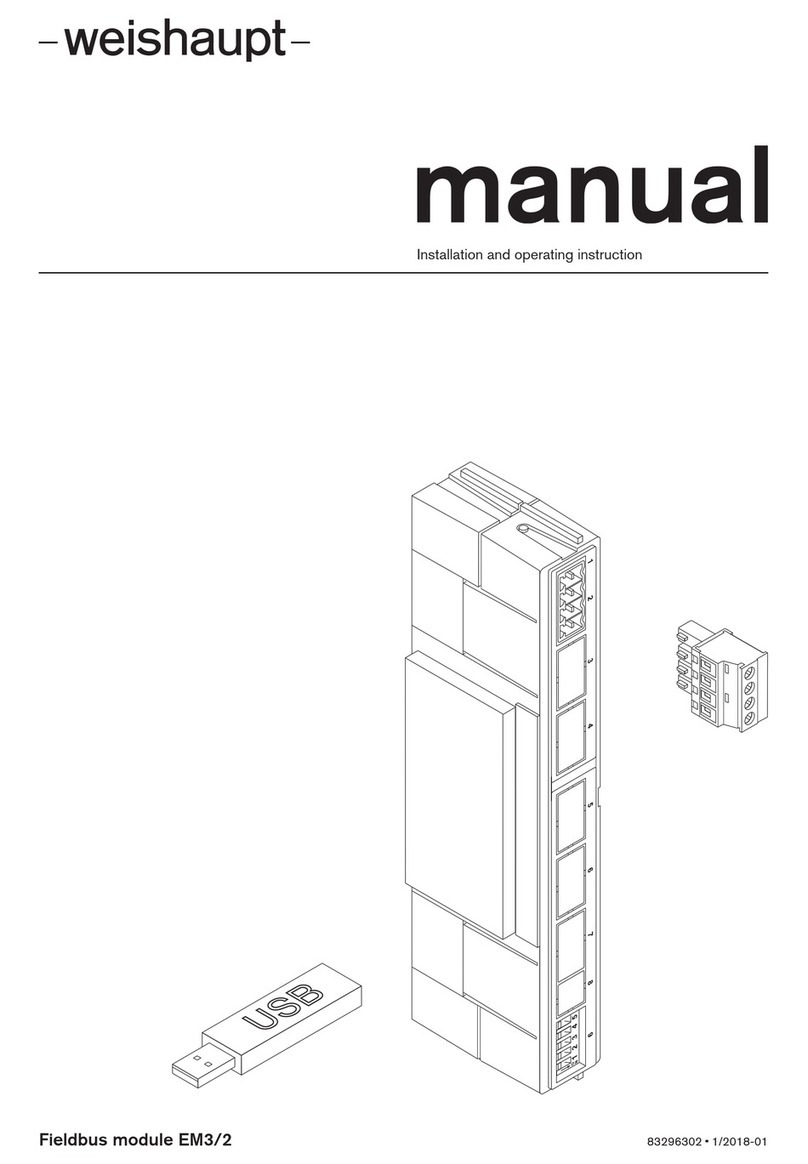
Weishaupt
Weishaupt EM3/2 manual
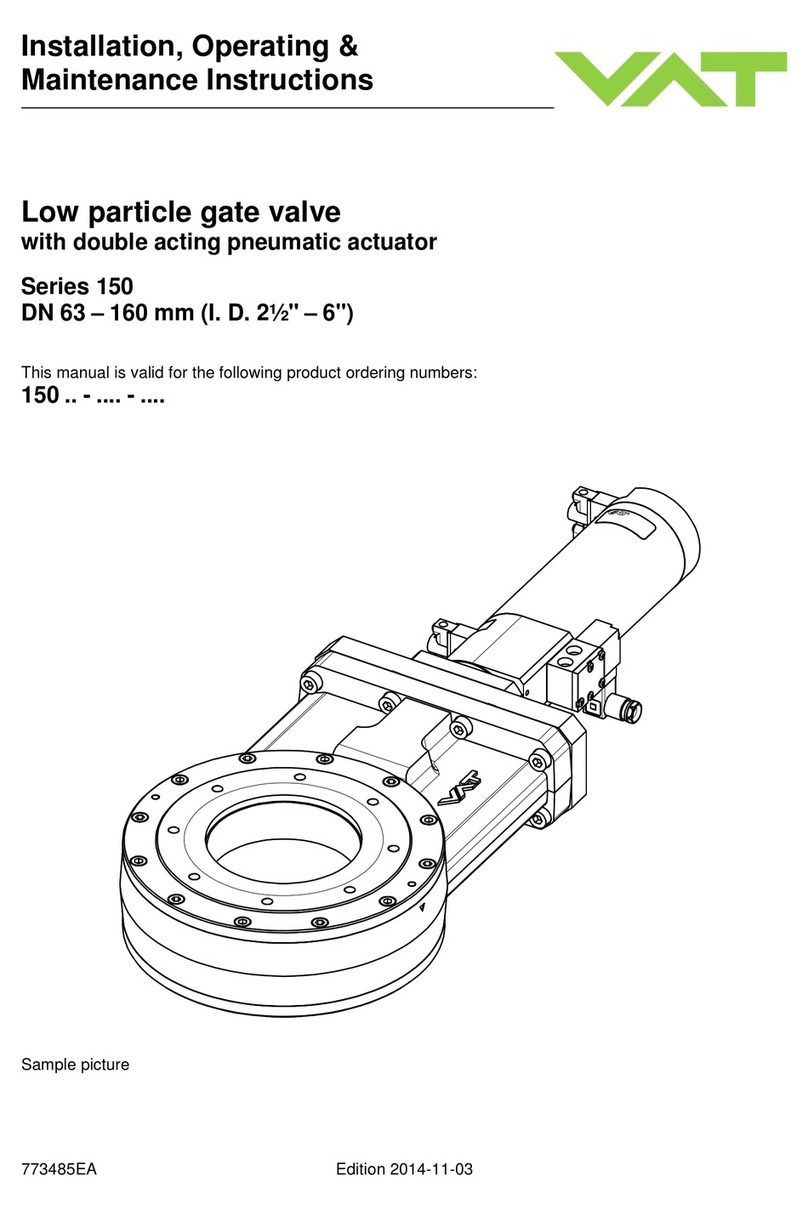
VAT
VAT 150 Series Installation, operating, & maintenance instructions