Holley 551-102 User manual

Sniper Standalone Transmission Controller
Full User Manual
551-102
Contents
Overview ....................................................................................................................................................................................................1
Kit Contents/Additional Parts Required ......................................................................................................................................................1
General Operation......................................................................................................................................................................................2
Initial Use....................................................................................................................................................................................................4
Perform Wizard ..........................................................................................................................................................................................4
Tuning and Setup Parameters....................................................................................................................................................................6
Setup Icon..............................................................................................................................................................................................7
Shifts Icon..............................................................................................................................................................................................9
WOT Shifts Icon...................................................................................................................................................................................10
TCC Icons............................................................................................................................................................................................10
Line Pressure Icon...............................................................................................................................................................................12
Outputs Icon.........................................................................................................................................................................................13
Monitors/Gauges......................................................................................................................................................................................14
OVERVIEW
The Sniper Transmission Controller (STC) allows the use of common GM and Ford electronic four speed transmissions. Part Number
551-102 is a stand-alone controller and is intended to work with carbureted or EFI applications that don’t support electronic
transmission control. You will need a throttle position sensor if one is not already installed. The included 3.5” touch screen is used to
perform all the allowable adjustments (shift speed, torque converter lockup, etc.) No programming is available with PC computer
software, however the transmission functions can be data-logged and reviewed with Sniper EFI PC software.
KIT CONTENTS/ADDITIONAL PARTS REQUIRED
This kit contains the Sniper Transmission Control Module, 3.5” Touchscreen handheld tuner, and power/sensor harness.
The user must purchase a transmission harness separately that fits their specific transmission. These harnesses are as follows
(note that these are the same harnesses used for Holley Dominator and Terminator X Max ECUs):
558-405 –GM 4L60/70/80E
558-455 –2009+ GM 4L60E*
558-470 –1998+ Ford 4R70W/4R75W
558-471 –1992-1997 Ford AODE/4R70W

* The “2009+” 4L60E specifically applies to OEM/factory original applications. When dealing with a GM Performance Parts, reman, or
unknown year transmission the transmission connector should be checked per the image below. If pin “F” (Circled in Figure 1 below)
IS PRESENT, you need the 558-455 harness. If it is NOT present you need the 558-405 harness. Go by THIS PIN ONLY as the other
pins may vary transmission to transmission. Be sure you compare your connector to the image below by “clocking” the pins based on
the connector slot.
Figure 1
A throttle position sensor (TPS) is required. If one is not available Holley offers the following:
534-202 –For Holley carbs with electric chokes
534-214 –For Holley Gen 3 Dominator carbs
1951 –For Street Demon carbs
120002 –Can be retrofitted to most carbs
GENERAL OPERATION
GM and Ford four Speed electronic overdrive transmissions are simple in operation. They have four speeds with the top gear being an
overdrive and all have a lockup torque converter that eliminates any slippage when the lockup is applied. With a stock torque converter
the lockup should only be applied under light throttle conditions or excessive wear will occur.
Upshifts, downshifts, and torque converter lockup are based on vehicle speed and throttle position (or optionally the MAP sensor) and
are adjustable with the 3.5” touch screen.
WIRING
Transmission Harness
Install the (purchased separately) transmission harness. Connected it into the 26 pin (smaller) connector on the STC unit. Instructions
for the specific transmission harness can be found at Holley.com under the transmission harness part number. They typically have a
power connection to the battery and are plug-and-play to the transmission.
Loose Wires:
The included harness with the 34 Pin connector has the following loose wire connections:
Red (16 Gauge) –Connect to battery power
Black (16 Gauge) –Connect to battery ground
Red/White (20 Gauge) –Connect to +12v switched ignition power
RPM Signal Input –ONE of the following two wires (Purple or White) wires need to be connected to an RPM signal input as follows:

Purple (20 Gauge) –RPM Signal Input –This should be used when a “12 volt square wave” signal is available to connect to. This
would be the “tach out” signal on a MSD/CD box, some MSD Ready-to-Run distributors, or possibly a signal out of an EFI ECU.
NEVER, NEVER connect this directly to ANY ignition coil. This should never be connected to an HEI distributor or HEI coil.
White (20 Gauge) –RPM Signal Input –If a “12 volt square wave signal” is not available and a MSD/CD ignition box is NOT used.
Connect this to the negative side of the coil. This would typically be used on a stock factory vehicle.
Grey/Red (20 gauge) –Fan Output 1- Optional –Turns on/off based on transmission temperature. This is a GROUND output and
should ALWAYS be used to trigger a relay.
Grey/Yellow (20 gauge) –Fan Output 2- Optional –Turns on/off based on transmission temperature. This is a GROUND output and
should ALWAYS be used to trigger a relay.
Blue/White (20 gauge) –Speedometer Output –Optional –Used to send signal to an electronic speedometer. (configure PPM setting
in the 3.5 handheld).
3.5” Touch Screen LCD Connection:
Connect the 3.5 Touch Screen into the 4 pin CAN bus connector.
Terminated Connectors:
There are two terminated connectors in the harness, the TPS (Throttle Position Sensor) and MAP (Manifold Air Pressure) sensor. One
or both are required depending on the calibration. All base calibrations are intended for use with a TPS input (TPS is REQUIRED for
proper operation), and no MAP sensor input. A MAP sensor is typically used with boosted applications for the Line Pressure table
(OPTIONAL).
TPS –The TPS connector is a common style used for a variety of Throttle Position Sensors. If your TPS uses a different connector,
replace the one on the harness. The pinout is as follows:
Orange Wire –5 Volt Reference
Black Wire –Sensor Ground
Green –TPS Signal
MAP –The MAP sensor connector is for the common GM 1 Bar MAP. (Holley PN 538-24). The pinout is as follows:
Orange Wire –5 Volt Reference
Black Wire –Sensor Ground
Red/Black –MAP Signal
STC 34 Pin Connector Pinout (pins not shown are not used):
Description
Color
Pin
Coil –Input
White
A1
Battery Power (A2/3/4 tied together)
Red
A2
Battery Power (A2/3/4 tied together)
Red
A3
Battery Power (A2/3/4 tied together)
Red
A4
TPS Input
Green
A5
Ground (A6/7/8 tied together)
Black
A6
Ground (A6/7/8 tied together)
Black
A7
Ground (A6/7/8 tied together)
Black
A8
Fan Output
Grey/Red
A9
Switched +12V Input
Red/White
A10
Fan Output 2
Grey/Yellow
A17
Sensor Ground
Black
A18
MAP Sensor Input
Red/Black
A23
CAN Low
Orange
A24
CAN Power
White
A25
Sensor +5V
Orange
A26
Speedometer Out
Blue/White
A28
Crank/RPM Input
Purple
A30
CAN Hi
Tan
A32
CAN Ground
Black
A33

INITIAL USE
Turn on the vehicle’s ignition power. When powered up you’ll see the main screen (Figure 2). The Sniper EFI as well as the
Transmission controller functions (tuning, gauges, wizards, logging) will all be performed through the same icons in Figure 2.
Figure 2
PERFORM WIZARD
The STC wizard must be performed. This will prompt the user to select the proper transmission, tire size, etc. This is required for the
transmission controller to function.
Numeric entries can be entered using the “slider bar” or clicking on the numeric value and using the keypad. Select “Next” after making
a selection or “Back” to a previous entry.
Select the “Wizards” icon.
Select the “STC Wizard” icon (Figure 3).
Figure 3
1) Select Transmission Type (Figure 4) –more detailed information on these selections are a few pages down in the manual if
needed. Note: The 1.63 ratio is by far the most common 4L60E version.
Figure 4
2) Select Ignition Type –See the WIRING section above. If you connected the WHITE wire, select “Coil (-)”, if you connected the
purple wire, select “CD Box”.

3) Number of Cylinders
4) Select MAP Sensor –If your application is naturally aspirated (no turbo or supercharger), you’ll almost always not need/use a
MAP sensor. Select “None Used” if none is used.
5) Enter Tire Diameter (Figure 5) –Enter Height/Diameter for rear tire in inches.
Figure 5
6) Enter Rear Gear Ratio (Figure 6).
Figure 6
7) The next entry is “Automatically Scale Shift Tables” (Figure 7). It is advised to select “Yes” to this. This will rescale all of the
up/down shift tables for the user’s specific tire diameter and rear gear ratio (compared to the base calibration values of a 4.10
gear and 27.7” tire). If this is not done, up/downshifts may occur early or late and a lot of manual adjustment may be required.
Figure 7

8) At this point a base calibration will be created and you’ll see a file name of “AT” or “FAT” (Figure 8). Select “Start” and you
will be prompted to cycle the ignition power. Select “Finish” (Figure 9).
Figure 8 Figure 9
9) Next, return to the “Wizards” menu and select “TPS Autoset”. Select this icon and follow the instructions. Press the pedal
fully, twice, when requested. If the TPS Autoset is not successful it means the TPS wiring is not correct or there is a sensor
issue.
At this point, the transmission controller programmed with a base calibration and is in a drivable condition. Use the Tuning Parameters
to adjust transmission shifting, torque converter, and other operations. Information is provided below. It is highly advised to read all of
these instructions and perform any adjustments before driving the car.
TUNING AND SETUP PARAMETERS
All Sniper Transmission Control tuning and setup parameters are accessed from the home screen via the “Tuning” and “Transmission”
icons. The following goes through all these which includes how to tune transmission operation. Figure 10 are the choices shown
under the “Tuning” icon from the home screen.
Figure 10
Select the “Transmission” icon. The icons in Figure 11 are displayed.
Figure 11

Setup Icon
Select the Setup icon, and the choices in Figure 12 are displayed. Most (not all) of these were configured during the wizard process.
Figure 12
General Icon
Select the general icon. The transmission types are displayed (previously selected in the wizard).
Transmission Type –Select the proper type from the following:
- GM 4L60/5E with 1.75 second gear, Pre-2009 (this is an uncommon transmission found in some 305 engine applications)
- GM 4L60/5E with 1.63 second gear Pre-2009 (most common application, select this if you are unsure)
- GM 4L70E (2009+)
- GM4L80/5E
- Ford AODE
- Ford 4R70W (92-97)
- Ford 4R70W (98-03)
- Ford 4R70W (2003+)
Engine/Ignition Icon
These were selected in the wizard process.

Sensors Icon
This area can be used to change/add a MAP sensor. The “MAP Sensor Offset” shouldn’t need to be changed from 0, but can be use if
the sensor value is off by a few percent.
Gear Ratios Icon
Gear Ratios –This was entered when the “STC Wizard” was used. Allows the choice of “Stock” or “Custom” ratios. Unless the
transmission was custom built with different gear sets, “Stock” will always be chosen. When Custom is selected it will allow editing of
the gear ratios.
Figure 13
Speed Calculation Icon
Tire Diameter –This should already be entered if the “STC Wizard” was used. Enter the tire diameter (height) in inches
Rear Gear Ratio –This was entered when the “STC Wizard” was used. Enter the rear axle gear ratio.
Speedometer Output –The speedometer is a 12v pulsed output typically used to drive an electronic speedometer. It is pre-
programmed to be enabled. There’s no harm in leaving it enabled even if it isn’t being used, make sure the loose speedometer output
wire isn’t shorted however.
Speedometer PPM –This is how many “Pulses per Mile” are output on the speedometer output. 4000PPM is a commonly used value.
Figure 14

Table Config Icon
Line Pressure Scale –Chooses whether the MAP (Manifold Air Pressure) sensor or TPS (Throttle Position Sensor) is used for the line
pressure table. Naturally aspirated engines should use TPS and boosted engines typically use MAP, as engines can generate boost
under non-WOT TPS conditions which require higher line pressure. The base Wizard calibrations are set to use TPS. If you’re engine
is boosted you should highly consider changing this and tuning so that you have maximum line pressure (0% duty cycle) at by at least
100 kPa/0 PSI of boost as a base recommendation.
Torque Converter Lockup Scale - Chooses whether the MAP (Manifold Air Pressure) sensor or TPS (Throttle Position Sensor) is used
for the torque converter lockup table. Naturally aspirated engines should use TPS and boosted engines can use either depending on
the preference of the tuner. The base Wizard calibrations are set to use TPS.
Figure 15
Shifts Icon
Up/Down Shift Tables
These tables are used to command the up and down shifts between each gear. Figure 16 gives the low/high range of each gear.
Select each one separately to edit the up and downshifts for each gear. Figure 17 is the graphical editing screen. The Y axis (up and
down) is based on vehicle speed. The X axis (right to left) is based on TPS (throttle position). One gear change at a time is graphed
and can be edited. The red line is the up-shift line. The blue line is the down-shift line. The down-shift line should ALWAYS be below
the up-shift line. The touch screen display is programmed to not allow for a downshift to be above an upshift in each gear (it always
forces a 2 MPH spread, minimum and will give the user a warning if this occurs). Only one item (upshift or downshift per gear) is
editable on each selection.
There should be enough “space” horizontally (left to right) between the up-shift and down-shift lines such that the transmission does not
shift back and forth between gears when the TPS or MAP values change at the same speed. This occurs when you depress the pedal
and the car isn’t accelerating at a fast rate.
Figure 16 Figure 17 Figure 18
Figure 18 is opened by selecting the “Options” tab on Figure 17. The “Increase” and “Decrease” allows a single upshift or downshift
line to be moved up or down by a percentage. This is the easiest way to change a curve. The “Entire Curve” and “Point-by-point”
changes whether the curve is changed by an individual point or the entire curve moved. The Digitally and Graphically selection are
choices on how the graph is edited. Digitally is usually easiest.
Using a stylus/pointer, is the easiest way to edit.
Tuning the up/down shift tables dramatically affects the “feel” of how the transmission operates. Many times this is up to the preference
of the user. Raise or lower the shift points until they suit individual tastes.
You also never want a lower gear up shift or down shift point to occur at a higher vehicle speed than a higher gear shift point. So, scroll
through every table to make sure this is the case at each TPS/MAP point.
Up/Down Shift Calibration DON’TS:
Never allow for a downshift point to be at a higher vehicle speed than the up shift point (the user will be prompted with a
warning and this will not be allowed if this is attempted)

Never allow for an up-shift point on a lower gear, to occur at a higher vehicle speed than a higher gear shift point. This can be
checked by looking at the “Shifts” screen and viewing the lowest and highest shift MPH for each upshift and making sure the
“Shift Up 1st-2nd” values are lower than the “Shift Up 2nd-3rd” values for example.
WOT Shifts Icon
The WOT shift tables (Figure 19) are purely based on RPM. Enter the engine speed at which you want them to occur when at wide
open throttle.
Figure 19
TCC Icons
The TCC icons (Figure 20) allow complete tuning of all torque converter lockup operations.
Figure 20
Activation Icon
The TCC Activation parameters (Figure 21) allow for various parameters to adjust when the converter is locked.
Figure 21
Minimum Gear to Enable - Selects the minimum gear that the TCC will be applied. The TCC is typically only applied in an overdrive
gear.
Minimum RPM to Enable - Minimum engine speed at which the TCC will apply. This value can be adjusted so that engines with large
camshafts, etc., do not hesitate if the TCC is applied at too low of an engine speed, causing the engine to lug.
RPM to Disable - The RPM to Disable TCC is applied to unlock the TCC once it is locked. The Lock and Unlock values should not be
too close together, or they will continuously lock and unlock. Applications with high stall torque converters will typically need 400-700
RPM or more between these values.

Time in Gear Before Lockup –This is a delay that occurs before the converter locks when it shifts into a gear where lockup occurs. 2
seconds is a good starting point for good drivability.
De-activation Icon
The De-activation parameters (Figure 22) are various parameters to adjust when the converter unlocks.
Figure 22
Max TPS TCC - Throttle position value when the TCC will unlock. Most lockup torque converters do not have a clutch designed to lock
up when higher power is being applied. If that is the case, it is best to unlock the converter when more power is being applied which
can simply be performed by inputting a TPS value typically between 25-50%.
TCC Disable –This is used to turn all TCC functionality On and Off. It would always be on unless there was a problem or reason to
completely disable it.
Unlock During Upshift –This parameter only comes into play if the converter is locked in multiple gears (for example both 3rd and 4th).
If enabled the converter will unlock when an upshift is commanded then relock after the “Time in Gear Before Lockup” occurs.
Unlock During Downshift –This parameter only comes into play if the converter is locked in multiple gears (for example both 3rd and
4th). If enabled the converter will unlock when a downshift is commanded then relock after the “Time in Gear Before Lockup” occurs.
Lock/Unlock Icon
Figure 23 Figure 24
Lock and Unlock –These parameters (Figures 23 & 24) work in addition to the TCC Parameters by offering additional tuning based on
vehicle speed. This keeps the TCC from locking up during ‘around-town’ driving if it is not desired. The Lock values should always be
higher than the Unlock values. Adjustments to these can be done by using the graph.
Slew Rate Icon
Figure 25
These parameters (Figure 25) are used to adjust “how hard the lockup hits”. The can be adjusted so that the lockup clutches slip some
at apply.

Lockup Beginning Duty Cycle - This is typically set at 50%
Lockup Ending Duty Cycle –This needs to be set at 100%
Lockup Time –This is how long it takes to go from the beginning to ending duty cycle. .5 seconds makes for a quick, hard apply,
increasing this value to 1-3 seconds will smooth the lockup apply.
Unlock Beginning Duty Cycle –This should be set to 100%
Unlock Ending Duty Cycle –This is typically set to 50%
Unlock Time –This is typically set to .5 seconds.
Line Pressure Icon
Figure 26 Figure 27
The line pressure table (Figures 26 & 27) determines how much line pressure is applied in each gear based on TPS or MAP. Each
gear is separately editable. The following reviews what “Gear to Edit” affects what area:
1st Gear –Pressure in 1st gear
2nd Gear –Pressure on 1-2 shift and 2nd gear
3rd Gear –Pressure on 2-3 shift and 3rd gear
4th Gear –Pressure on 3-4 shift and 4th gear
The higher the Duty Cycle Percentage, the LESS line pressure there will be. The Duty Cycle should increase as the TPS or MAP
sensor increases (load increases).
If a shift is too harsh, lower the line pressure for that shift, at the specific MAP or TPS position the shift occurred. When online, the
graph will be highlighted to show the present TPS/MAP location. The feel may be dependent on the torque converter used. A stock
torque converter may require less line pressure so the shifts aren’t overly harsh. A “high stall” converter may use more line pressure to
give a better feel on a shift.
At idle and cruise, values above 40-50% typically are not suitable, resulting in low line pressure which will damage the transmission
quickly. Idle values are typically 35-40 and will decrease to 0 at 80-100% throttle.
At WOT, the line pressure should be at or close to the maximum pressure (0% duty cycle).
Figure 28 is opened when “Options” is selected. It is easiest to us the “Softer” and “Firmer” buttons on it to soften and firmware
shifts/line pressure.
Figure 28

Temperature Modifier
The Temp vs. Line Pressure table (Figure 29) is used to alter the line pressure base on transmission fluid temperature. When the fluid
is cold, it is thicker. The line pressure can be increased to maintain the same end “feel” when the fluid is cold as when warm. To
“increase” line pressure, enter a negative value in the Temp vs. Line Pressure chart. Values of -5 to -7% are typically used at temps
below 100°F.
Figure 29
Outputs Icon
Enable Line Temp Fan #1 (Figure 30) –This is pre-programmed in a disabled state. To use, it must be enabled with the handheld.
When enabled, an output (Pin A9, Grey wire with red stripe) is triggered that is intended to turn on a fan based on the transmission line
temperature. The “On” temperature is when the output is activated and the “Off” temperature is when the output will be deactivated.
The Off temp must be lower than the on temp.
Enable Line Temp Fan #2 (Figure 30) - This is pre-programmed in a disabled state. To use, it must be enabled with the
handheld.When enabled, an output (Pin A17, Grey wire with yellow stripe) is triggered that is intended to turn on a fan based on the
transmission line temperature. The “On” temperature is when the output is activated and the “Off” temperature is when the output will
be deactivated. The Off temp must be lower than the on temp. Note that the gauge screens do not show Fan #2 status.
Figure 30

MONITORS/GAUGES
You can view the transmission parameters by selecting the “Monitor” icon and then either the “Monitors” or “Mulit-Gauge” icons.
Monitors has two transmission specific screens (Trans #1 and #2) (Figures 31-33) and Multi-gauge has a “Trans/Engine” screen
(Figures 34-35). You can set up a custom screen using the “Dash #1/2/3” screens.
Figure 31 Figure 32 Figure 33
Figure 34 Figure 35
LED Definition
The unit has 8 LEDs. Three of them are used as follows:
LED #1 –Blinks green to indicate the unit is powered and basic operation is being properly performed.
LED #2 –This LED will light up blue when an ECU (such as a Sniper EFI unit) is connected and the STC is properly receiving CANbus
information. If an ECU is connected and powered and this LED is not lit up, there is a CANbus issue (wiring connection, etc.). Note:
Having the 3.5” handheld display connected by itself will not cause this LED to light up as is the cae in standalone mode.
LED #3 –This will light up red when the unit does not have a proper calibration loaded. When it is operating properly it should not be
lit.
LEDs #4-8 –None of these will be active.
FIRMWARE UPDATES
Firmware Updates –Updating the STC
To update the STC firmware (there shouldn’t be a need to do this typically, so unless you are aware of a specific need don’t do it), copy
the new firmware to the SD card. Copy it to the “STC” directory on the SD card. Insert the SD card into the 3.5 handheld. Select the
“File” icon, the “STC HW/FW” icon. Next select the “Upgrade STC Firmware” button. Select the desired firmware to update to.
Holley Performance Products
Toll Free Technical Service: 1-866-464-6553
Technical Service: 1-270-781-9741
For online help, please refer to the Technical Information section of our website: www.holley.com
© 2023 Holley Performance Products, Inc. All rights reserved. Tous Droits Réservés.
199R12494
Revision Date: 9-26-23
Other manuals for 551-102
1
Table of contents
Other Holley Controllers manuals
Popular Controllers manuals by other brands
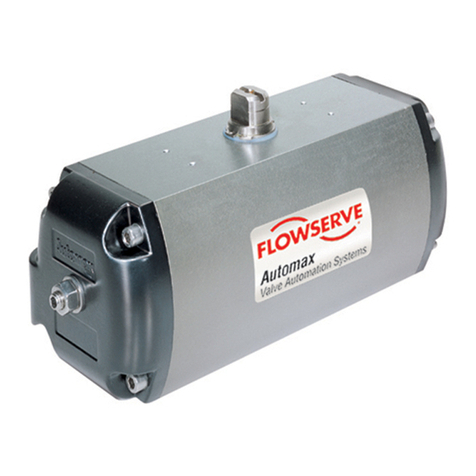
Flowserve
Flowserve Automax SuperNova S050 Installation, operating, & maintenance instructions
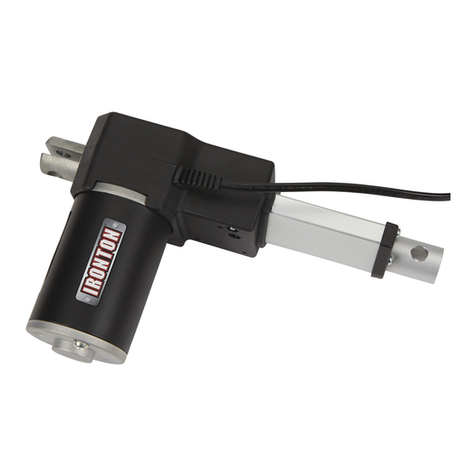
Ironton
Ironton 74365 owner's manual
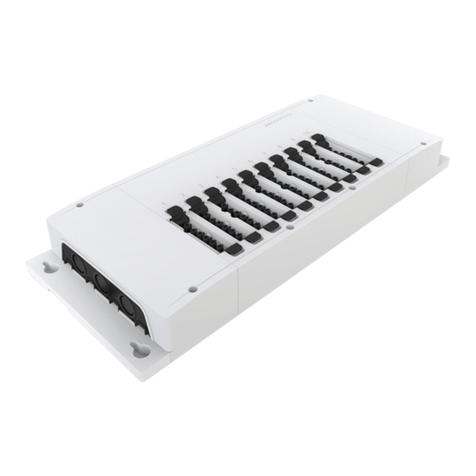
Zencontrol
Zencontrol zc-blind manual
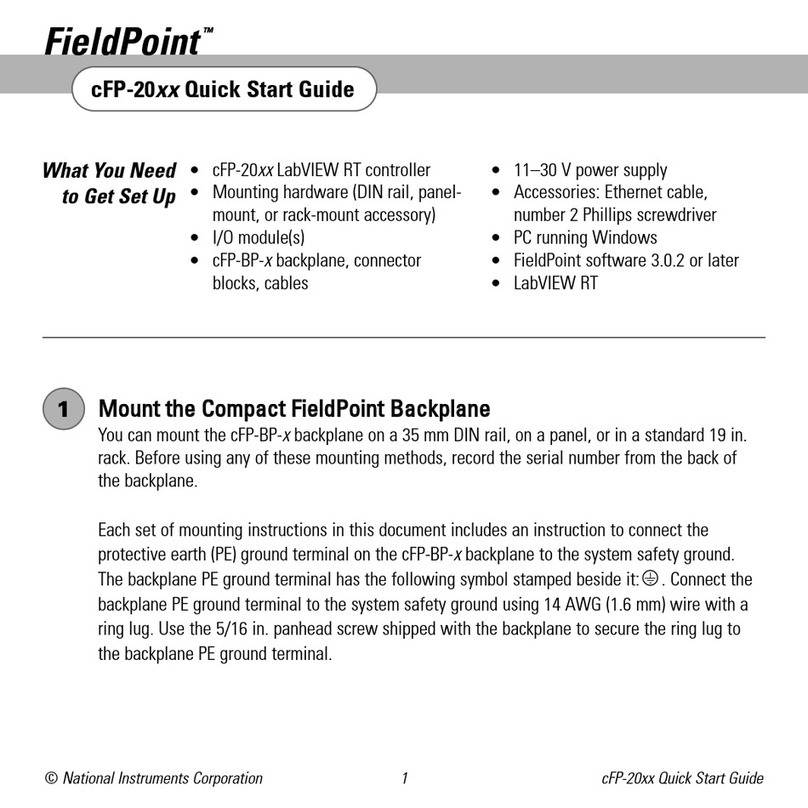
National Instruments Corporation
National Instruments Corporation FieldPoint cFP-20 Series quick start guide

Steca
Steca Tarom 4545 Installation and operating instructions
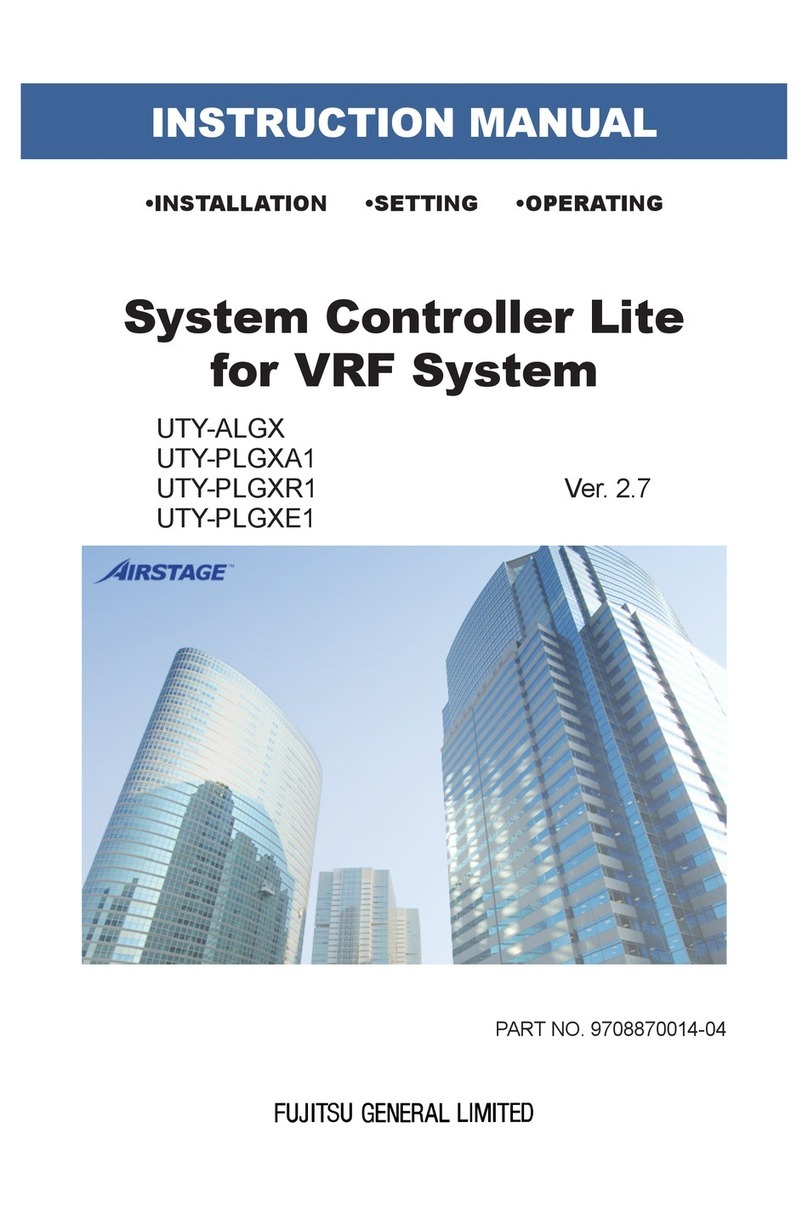
Fujitsu
Fujitsu AIRSTAGE UTY-ALGX instruction manual