Honeywell HON 985A User manual

Gas Mixer HON 985A 985.29-2
Serving the Gas Industry
Worldwide
OPERATING AND MAINTENANCE INSTRUCTIONS/
SPARE PARTS EDITION 01/2017

Table of contents Page
1. General information 3
1.1 General information 3
1.2 Safety information 3
1.3 Applications and features 4
4noitarepofoedomdnaerutcurtS4.1
2. Specific operating instructions 5
5erusopxenoitaidarycneuqerfhgiH1.2
5draclortnocrotomreppetS2.2
3. Technical features 5
5reximehtfoserutaeflacinhceT1.3
5rotomreppetsehtfoserutaeflacinhcetdnasnoisnemiD2.3
6)hctiwstimil(rosnesytimixorpehtfoserutaeflacinhceT3.3
7IN-N-WZ-05/001-A589HONgniwardlanoisnemiD4.3
4. Specific maintenance instructions 8
8snoitcurtsniecnanetniamrofslavretnI1.4
4.2 Tightening torques MA 8
4.3 Lubricants 8
4.4 Adhesives 8
5. Maintenance 9
9srosnesytimixorpehtgniltnamsiD1.5
5.2 Dismantling the drive unit 9
01tresniirutneVehtgniltnamsiD3.5
01stlebediugehtgnicalpeR4.5
01tresniirutneVehtgnillatsnI5.5
01woblenoitcudniehtgnitnuoM6.5
5.7 Mounting the drive unit 11
11srosnesytimixorpehtgnitsujdA8.5
6. Spare parts
21IN-N-WZ-05/001-A589HONgniwardstraperapS1.6
31IN-N-WZ-05/001-A589HONtsilstraperapS2.6
51sesoprupecnanetniamrofstraP3.6
985.29-2 p.02

!
!
1. General
1.1 General information
All persons involved with the assembly, operation and/or maintenance of the gas mixer HON 985A -100/50-ZW-N-NI
must attentively read and understand these operating and maintenance instructions in their entirety.
Inspection and maintenance intervals depend mostly on the operating conditions at the respective system.
Amongst other factors, the type of gas used and the corresponding gas composition, and the existing gas
contamination as well as any accumulating condensates must be taken into account. There are no general rules
or recommendations for intervals. Therefore, it is advisable to include the devices in the gas engine maintenance
intervals.
If operational irregularities are discovered during the operation or during a functional test,
unplanned maintenance work on the mixer is required. This must be performed immediately
after the discovery of the deviation in operating behaviour.
During maintenance, components must be cleaned and then checked thoroughly. This is necessary even if there
have not been any unusual observations during operation and/or functional testing. The check must include in
particular seals, all moving parts such as parts with transmission thread and the venturi insert. Any and all defective
parts must be replaced with new ones. The same applies to o-rings removed during dismantling.
Do not use any spare/wear parts and/or oils & lubricants not specifically recommended in the Honeywell operating and
aintenance instructions. In the event spare/wear parts and/or oils & lubricants other than those specifically
recommended are used, Honeywell shall not be held liable for any defects and/or consecutive damages attributable to
such use of illegal parts, lubricants, oils etc.
Some parts in the lists and drawings are marked with a letter “W”. We recommend to always have a reserve of those
parts in stock for maintenance purposes. Those spare parts are put together in a separate table at the end of the
spare parts list.
1.2 Safety information
In this manual, safety information is highlighted by means of the following signal words and eye catchers:
Danger of damage to property and/or the environment
Important additional information
Eye catcher Used for:
Danger to life and limb
985.29-2 p.03
Note
Caution
Danger
Note

985.29-2 p.04
HON 985A-100/50-ZW-N-NI
1.3 Applications and features
•Application
– Variable mixing of air and fuel gas for gas engines (e.g. for λ-control, electronic spark control,
combustion-chamber temperature control)
– Mixing gases for operating gas motors with multiple types of fuel gas (e.g. sewage gas, secondary operation
with natural gas)
– In general, mixing all sorts of gases (e.g. boosting low calorific-value gases e.g. waste dump gas)
– Applicable for natural gas, sewage gas, dump gas, mine gas, propane, butane and neutral gases
•Features
– Simple construction
– Adjustable fuel-gas mixing gap provides for flexible mixing ratios
– Fine adjustment of mixing ratios possible
– Sensitive stepper motors provide for precise adjustment of mixing gap
– Turbulent mixing (homogenization)
Air / fuel gas mixture
not rich enough too rich
increase the mixing gap reduce the mixing gap
1.4 Structure and mode of operation
gas 2 (fuel gas) flowing in through an upstream gas pressure control section to the same pressure as gas 1 (air). With the
reduction of the cross-section, there is an acceleration of gas 1 (air) flowing in. Acceleration means the pressure of the gas
For the mixture of the gases, a torpedo designed for maximum flow rates of the gas mixture is integrated in the device.
The downstream flow edges of the torpedo support the turbulent mixing of the two types of gases (homogenization).
For a more precise adjustment of the mixing ratio (λ-control, for instance), there are sensitive electronic control loops
and motors that can adjust the gap according to operational requirements.
Ratio
Precautions
Gas 2
(Fuel gas)
Gas 1
(Air)
Air/fuel
gas mixture
Constriction
device (torpedo)
Venturi nozzle
Adjustable
mixing gap
Mixing zone
Stepper motor
with control*
*) Stepper motor control, e.g. for
– λ-control
– Control of cylinder temperature
– Electronic spark control
Fig 1: Functional principle

!
Ø 8
13,5
Ø38,1 - 0,025
1,6
M3
19
M6 x 1
2. Specific operating instructions
2.1 High frequency radiation exposure (comment on application at gas engine)
Possible faults due to high frequency radiation exposure (e.g. from the coil and its cable)
must be prevented for the proper response of the proximity sensors and stepper motor,
e.g. by routeing the cables separately.
2.2 Stepper motor control card
A stepper motor control card is not included in the scope of delivery. When choosing a stepper motor control
card, the following data for the stepper motor and the proximity sensors should be taken into account.
3. Technical data
3.1 Technical features of the mixer
Max. permissible pressure load PS 0.5 bar
Mixing ratio Qn air/ Qn fuel gas 3.5 : 1 to 25 : 1
yollamuinimulA:ydoB
leets/yollalA:straplanretnIslairetaM
RBN:slaeS
Max. operating and environmental temperature –10 °C to +80 °C
SEP design in accordance with PED
Table 1: Technical features of the mixer
3.2 Dimensions and technical features of the stepper motor
Fig 2: Dimensional drawing of the stepper motor
Connection plug
Caution
Cable and connection plug must be fastened
properly so that a cable break does not
occur.
Note
max.
rotomreppetsdirbyHngiseD
gnihctiwslellarap,ralopiBepytlioC
²mcg06aitrenifotnemomrotoR
mc
N5.82euqrotgnidloH
Full steps per shaft rotation 200
°8.1)petslluf(elgnapetS
Ω3.1liocrepecnatsiseR
A2esahpreptnerruc.xaM
Hm8.2liocrepytivitcudnI
Length of the electrical supply line approx. 0.3 m
tekcosdnagulpdnuornip-5noitcennoclacirtcelE
Table 2: Technical features of the stepper motor
985.29-2 p.05
Note A socket compatible with the stepper motor is included in the delivery.

+
-
3
24
51
a b c d
e
f
g
h
25
40
M8
LEDInductive sensor Counter nut
Straight socket
Table 3: Technical features of the proximity sensor
Fig 4: Proximity sensor
gulpecived1VnoitcennoC
CDV06–01egatlovgnitarepO
%01≤elppiR
zH005ycneuqerfgnihctiwS
Am001tnerrucgnitarepO
Am51noitpmusnocrewopgnildI
)dehctiwsevitisop(reneponppgnikramtuptuO
)Am001taV3.xam(–egatlovgnitarepOeerfecafrusevitcA
V3.0≤derevocecafrusevitcA
Interference voltage (permissible voltage peaks) max. 1,000 V / 10 ms
Ωk01ecnatsiserlanretnI
eerfsiecafrusevitcanehwthgilwolleyDELsutatsgnihc
tiwS
31WStunretnuocdnagnitsujdA
Note A straight socket compatible with the proximity sensor is included in the delivery.
1 / brown
2 / white
3 / blue
985.29-2 p.06
Fig 5: Proximity sensor connection diagram
Fig 3: Connection diagram of the stepper motor
3.3 Technical features of the proximity sensor (limit switch) for Venturi position
Colours of the wires
a – red
b – red/white
c – black/white
d – black
e – green
f – green/white
g – yellow/white
h – yellow

Ø 65
249
Ø
100
18
20
3)
1)
94
Ø
I
Ø
137
Ø
122
Ø
104.8
4 x
Ø 9
59
83
45°
32
46
36
(13)
56
2)
1)
2)
3)
46
36
A
A
Ø
C
Ø
A
L
X
A-A
(Ø
C)
Ø
B
30°
X
Ø
A
Ø
B
Ø
C
L
44.5 41 39.5 64
48.3 45 43 52
48.3 45 43 59
G1 A
–
34 65
3.4 Dimensional drawing HON 985A-100/50-ZW-N-NI
300 approx.
Gas connection 2
Air connection (hose) Mixture connection
Stepper motor connection
Fuel gas
Gas connection 1
305 approx.
52 to 65
Fastening clamp
Locking screw
Inspection glass
Proximity sensor “lean”
Comments:
985.29-2 p.07
Fig 6: Mixer and gas connection dimensional drawing
Flange type
(second “rich” proximity sensor optional)
Type 1
Type 2
Type 3
Type 4 (Rp 1)
(266 to 279)
Flow direction
I Variable torpedo diameter (see spare parts list)
Induction elbow can be installed at any angle position
in relation to the driving axle
Pressure measurement M14 x 1.5 connection possibility
Variable fuel gas connection (for dimensions and type,
see below)

!
!
27081
27091
27704
4. Specific maintenance instructions
Do not carry out maintenance unless the system is safely de-energised and depressurised.
Danger
4.2 Tightening torques
MA
Screws and nuts without a specification of the tightening torques are tightened according to the commonly available
tables for screw dimensions and qualities using an appropriate tool. Parts with an explicitly specified tightening torque
(see spare parts drawing) are to be tightened to the specified value with a torque wrench (see Table 4).
4.1 Intervals for maintenance purposes
The intervals between maintenance tasks depend largely on the operating conditions of the device. For this purpose,
please observe chapter 1.1. General Information.
If operational irregularities are discovered during the operation or during functional tests, unplanned
maintenance work on the mixer is required. This must be performed immediately after the discovery
of the deviation in operating behaviour.
Note
231321021211.on.soP
Tightening torque in Nm 8 2.8 12 212
Table 4: Tightening torques
MA
4.3. Lubricants
.ontrapHONstnacirbuLstnenopmoC
esaergenociliSsgnir-OllA
etsapylbmessAswercsgninetsafllA
Transmission thread and conical washer
on the threaded rod
Observe the notes regarding lubricants in chapter 1.1 General information.
Caution
Table 5: Lubricants
All O-rings which are replaced (see 1.1 General information) must be lubricated with silicone grease before installation
after the device maintenance.
Slip agent
4.4 Adhesives
The parts to be glued must be completely clean, dry and free of grease. Specifications for adhesive connections
can be found in the spare parts drawing and the following maintenance instructions.
.ontrapHONevisehdAsnoitcennocevisehdA
09662evisehdaciboreanAdoR
09662evisehdaciboreanAdaerhtdoR
Table 6: Adhesives
985.29-2 p.08

!
5. Maintenance
With the description of the individual maintenance steps, the same position numbers are used here for the
identification of the component as can be found in the spare parts drawing (page 12) and the spare parts list
(page 13 and 14).
For simple, easy maintenance work, we recommend following the sequence of the individual steps.
The device must be dismantled from the plant prior to maintenance work.
5.1 Dismantling the proximity sensors
Prior to the dismantling of the drive unit of the mixer and the maintenance work, we strongly
recommend removing the proximity sensors (117) from the device in order to prevent damage.
Prior to their removal, the proximity sensors should be disconnected from the power source.
Unscrew the cable sockets (118) from the proximity sensors.
Loosen the counter nuts and unscrew the proximity sensors from the receptacle (115).
5.2 Dismantling the drive unit
Remove the cap (121), unscrew the hexagon nut (120) and remove the washer (119) from the threaded rod (111).
Unscrew both cylinder screws (116) located behind the conical washer (119) and remove the receptacle (115).
By turning the motor spindle (Figure 7), the venturi insert (101) is first pushed to the mechanical stop on the
mixer body (130) and then unscrewed from the threaded rod with additional rotation of spindle of the stepper
motor (113).
Caution
The next step is the removal of the threaded rod (111) from the device. For this purpose, unscrew the inspection
glass (109) from the induction elbow (133) and loosen the clamp connection between the threaded rod and the
pin (105) by loosening the threaded pin (110).
The threaded rod is an assembly including the following individual parts: Rod thread M6, rod thread M4 and fixing
washer (see Figure 8 and Table 6) are adhered together. Check that all adhesive connections are firmly seated.
Fig 7: Rotation direction of the motor spindle with removal of the drive unit
Rod thread M4
Rod thread M6
Fixing washer
Fig 8: Threaded rod assembly (111)
Then carefully clean and dry all dismantled parts. Check the condition of the transmission thread (motor spindle interior
and threaded rod exterior (111)).
Lightly spray the transmission thread (M6) on the threaded rod and the contact surfaces on the outer diameter of the
washer (119) with slip agent (Table 5). The recommended coating thickness is 5 – 15 μm. Shake slip agent spray can
well before use. We recommend coating the threaded surfaces in a crossing pattern. Allow sprayed surfaces to dry for
5 – 7 minutes at room temperature.
985.29-2 p.09

!
!
5.3 Dismantling the Venturi insert
Loosen the cylinder screw on the profile clip (132) and remove it. Separate the induction elbow (133) from the mixer body (130).
Carefully separate the parts from one another in order to prevent damage to the
pin (105) by bending, etc.
Now the Venturi insert with the pin and torpedo unit (126) (Figure 9) can be pulled out of the mixer body.
)101(tresniirutneV)501(niP
Caution
The torpedo unit (126) is dismantled after unscrewing the pan head screw (125). The venturi insert (101) and the pin
are adhered to one another and may not be separated from one another. If the parts can be easily separated by hand,
the assembly must be repaired (adhered) or replaced.
Fig 9: Unit with venturi insert and pin
Torpedo (126)
Pan head screw (125)
5.4 Replacing the guide belts
The next step is the removal of the guide body (102) from the mixer body (130). Remove and dispose of the used guide
belts (129 and 131). Carefully clean the sliding surfaces on the venturi insert (101) and groove for the guide belts with
adjacent surfaces and allow to dry. Fit new guide belts.
The guide belts (129 and 131) and sliding surfaces may not be lubricated.
The lubrication of the parts can negatively influence the operating behaviour of the device.
Caution
5.5 Installing the venturi insert
Move the mixer body (130) up to the vertical position with the connection side facing the induction elbow (133).
Mount the torpedo unit (126) on the venturi insert (101). In the process, the pan head screw must be secured with
low-strength thread locker (e.g. LOCTITE 221). Slide the guide body (102) into the mixer body up to the mechanical stop.
Insert the venturi insert with the small diameter forward into the guide body and check the ease of movement of the
venturi insert.
however, only to the extent that the venturi insert does not fall through under the force of its own weight. Otherwise,
the play between the venturi insert and the guide belts is too great.
5.6 Mounting the induction elbow
After the adjustment of the guide belts (129 and 131), the induction elbow (133) is mounted on the mixer body (130).
The mixer body remains vertically aligned. Prior to mounting the induction elbow, make sure that the O-ring (104) is greased
and does not twist out of the groove. Carefully place the elbow on the mixer body so that the pin (105) goes in through the
hole in the induction elbow provided for this purpose. Place the profile clip (132) on the angles of the two flanges (on the
housing and the induction elbow) and connect the two parts in the correct spatial arrangement by tightening the cylinder
screw. Observe the tightening torques in Table 4 (page 8).
985.29-2 p.10

5.7 Mounting the drive unit
With moderate pressure on the pin (105), push the venturi insert (101) into the vertically positioned mixer body (130)
up to the mechanical stop. Then place the threaded rod (111) on the end of the pin up to the mechanical stop.
In the process, it must be ensured that the threaded rod is positioned over its hole in the fixing washer of the cylinder
pin (134). By tightening the threaded pin (110), the pin is fixed in the hold. Secure the threaded pin with a low-strength
thread locker (e.g. LOCTITE 221).
Place the stepper motor (113) on the threaded pin and screw it on by rotating the stepper motor spindle up to
the mechanical stop on the flange of the induction elbow (133). Fasten the stepper motor on the induction elbow
with four cylinder screws (112); in the process, observe the tightening torque for the screws (Table 4).
Place the receptacle (115) on the stepper motor spindle and align it to the desired side with the sensor fastening
thread (alignment in the direction of the output flange of the induction elbow is not possible due to the spatial
constraints), and install the cylinder screws (116).
Slide the washer (119) on as shown under 6.1 until the mechanical stop of the threaded rod is reached and fasten
with an M6 hexagon nut (120). Observe the tightening torque (Table 4, page 8).
Then fit the cap (121) and screw in the inspection glass (109) with seal in the induction elbow.
5.8 Adjusting the proximity sensors (limit switches)
Connect the stepper motor (113) of the mixer to the stepper motor control.
Adjust a mixing gap of 0.5 + 0.1 mm by moving the stepper motor. An adjustment of 0.5 mm takes place with
a control frequency of 20 Hz in full step operation in 5 seconds.
With a change to the control frequency by a factor K, the adjusting time changes by the
factor 1/K.
With a change to the step precision by a factor 1/F, the adjusting time changes by the factor F.
With an adjustment of both parameters, factors F and 1/K are multiplied.
Adjust the switching point of the “lean” position by screwing in the proximity sensor (117). Screw in the proximity
sensor until the LED on the sensor goes out. Then lock the proximity sensor in its position by tightening the
counter nut. Observe the tightening torque according to section 6.1 Spare parts drawing.
If the device is equipped with two sensors, the switching point for the “rich” position is adjusted first (max. mixing
gap width). For this purpose, increase the mixing gap an additional 4.5 mm from the “lean” switching point by
moving the stepper motor (total gap width 5 + 0.1 mm). In full step operation the additional adjustment at
a 60 Hz step frequency takes place in 15 seconds. Observe the notice above.
The adjustment of the screw-in position of the proximity sensor, “rich” switching point, takes place analogously to the
adjustment of the “lean” switching point. Then lock the sensor in place here as well by tightening the counter nut.
Note
985.29-2 p.11

125 126 127 128 129 130 131 133 134
WW
*
A
A
101 102
WWW W
103 104 105 106 107 108 109 110 111 112 113 114 115 116 117, 118 119 123 124
120
121
122
132
**
pictured rotated
through 90°
pictured rotated
through 145°
pictured rotated
through 90°
6 Spare parts
985.29-2 p.12
6.1 Spare Parts Drawing HON 985A -100/ 50-ZW-N-NI
MABe sure to comply with torque figures in table 4 on page 8!
W Parts should be held in stock for maintenance purposes
Use adhesive connection in accordance with table 6, page 8
A - A
MA= 10 Nm
MA
MA
MA
MA

.ontraPlairetaMWrebmuNnoitanimoneDmetI
no.
6.2 Spare parts list HON 985A-100/50-ZW-N-NI
36262001ML1tresniirutneV101
26262001ML1ydobediuG201
60702GKW1gniR-O301
75202GKW1gniR-O401
46262001tSN1niP501
69012GKW1gniR-O601
13282KW1gniraebtcatnocgnidilS701
18840001tS1rehsaW801
08272K1ssalgnoitcepsnI901
50421tS1nipdedaerhT011
18262001tSN1etelpmoc,dordedaerhT111
81301tS4wercsrednilyC
211
43542zB/ML1rotautcaraenilrotomreppetS311
70142K1tekcoS411
78262001ML1rosnes,elcatpeceR511
85601tS2wercsrednilyC611
22142tSN1rosnesytimixorP711
32142K1tekcoS811
98262001ML1enoc,rehsaW911
4145tS1tunnogaxeH021
07062K1paC121
65141tS4rehsaW221
02301tS4wercsrednilyC321
124 Flange DN 40, alternatively:
53702001tS11epytegnalF421
43702001tS12epytegnalF421
33702001
tS13epytegnalF421
72802001tS14epytegnalF421
95601tSN1wercsdaehnaP521
W Parts should be held in stock for maintenance purposes
German abbreviations stand for the following materials:
ssarbtsaC...sMGlatemthgiL...MLleetS...tS
cniztsaC...nZGssarB...sMleetssselniatS...tSN
eznorbmuinimulA...zBlAleetstsaC...SGleetsgnirpS...tSF
citsalP...KnoritsacetihpargladiorehpS...GGGleetsgnirpssselniatS...tSFN
slairetamcitehtnyssuommuG...GKezno
rbtsaC...zBGeznorB...zB
slairetamdemaoF...tSSlatemthgiltsaC...MLGreppoC...uC
985.29-2 p.13

Item Denomination Number W Materials Part no.
no.
126 Torpedo, optional:
57262001K181øodeproT621
94513001K152øodeproT621
69403001K103øodeproT621
05513001K133øodeproT621
79403001K163øodeproT621
57162tS1wercsgnikcoL721
24881ML1gnirlaeS821
65262001KW1tlebediuG921
16262001ML1ydobrexiM031
75262001KW1tlebediuG131
72282tSN1pilcelfiorP231
79262001MLG1woblenoitcudnI331
77271tS1nipred
nilyC431
985.29-2 p.14

.ontraPrebmuNnoitanimoneDmetI
no.
607021gniR-O301
752021gniR-O401
690121gniR-O601
132821gniraebtcatnocgnidilS701
652620011tlebediuG921
752620011tlebediuG131
886621rekcoldaerhT
180721esaergenociliS
190721etsapylbmessA
407721tnegapilS
096621evisehdA
6.3 Parts for maintenance purposes
985.29-2 p.15

For More Information
To learn more about Honeywell’s
Advanced Gas Solutions, visit
www.honeywellprocess.com or contact
your Honeywell account manager
GERMANY
Honeywell Process Solutions
Honeywell Gas Technologies GmbH
Osterholzstrasse 45
34123 Kassel, Germany
Tel: +49 (0)561 5007-0
Fax: +49 (0)561 5007-107
HON 985.29_2
2017-01
© 2017 Honeywell International Inc.
Table of contents
Other Honeywell Mixer manuals
Popular Mixer manuals by other brands
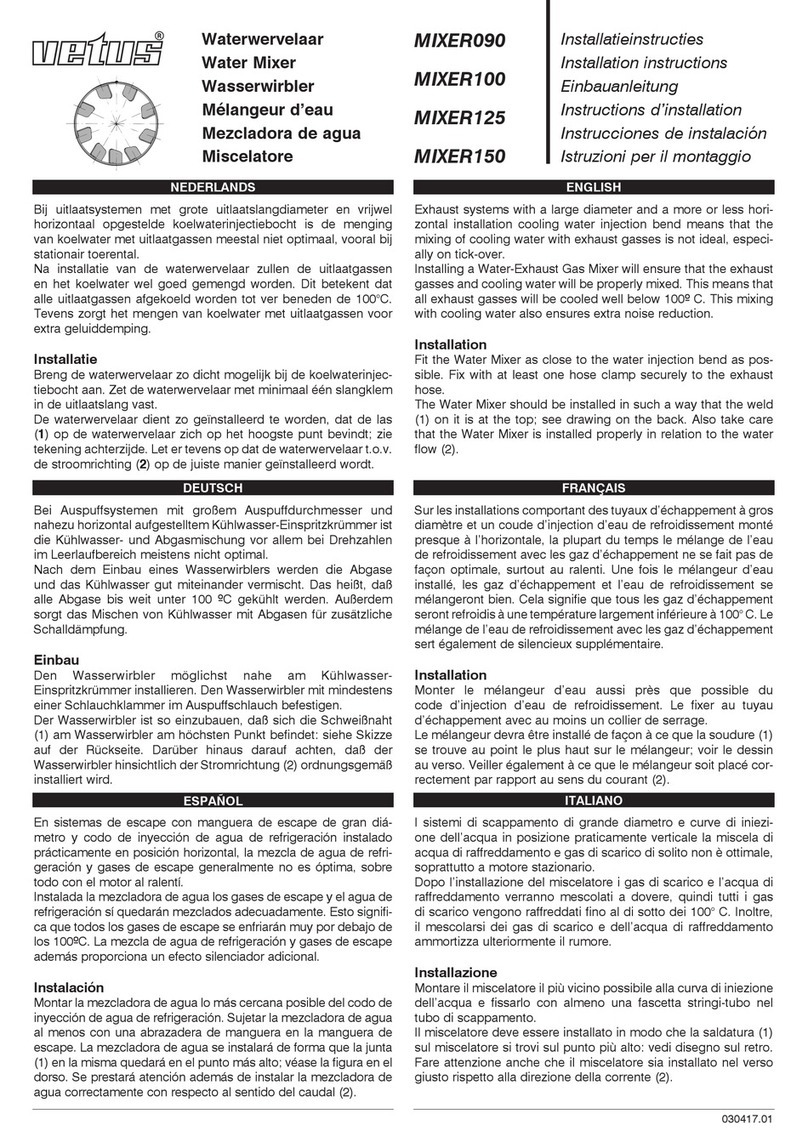
Vetus
Vetus MIXER090 installation instructions
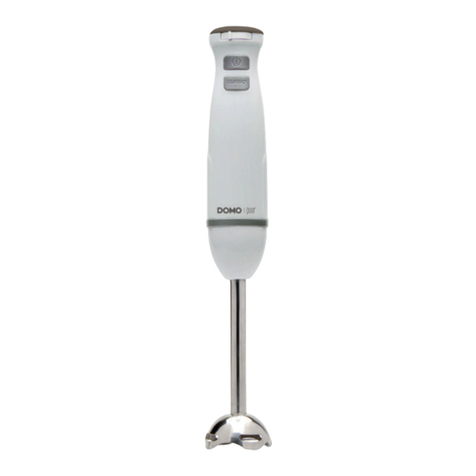
Linea 2000
Linea 2000 DOMO DO9143M Instruction booklet
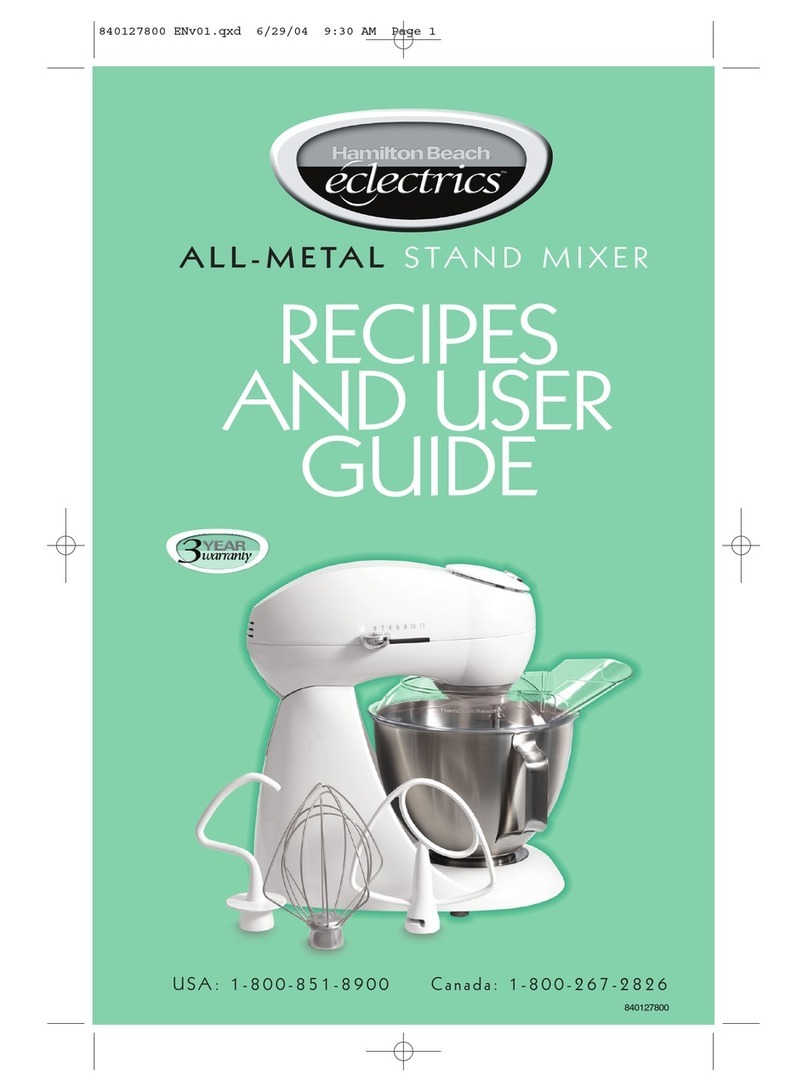
Hamilton Beach
Hamilton Beach Eclectrics 63225 User guide and recipes
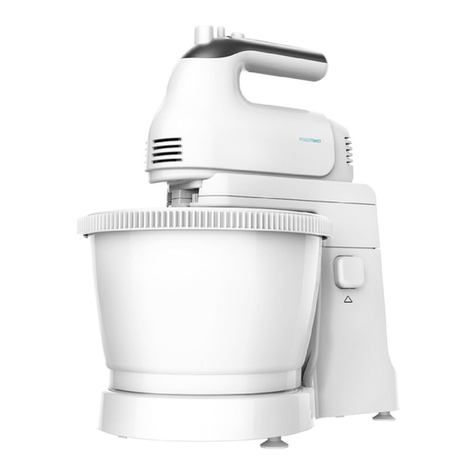
cecotec
cecotec PowerTwist 500 Gyro instruction manual
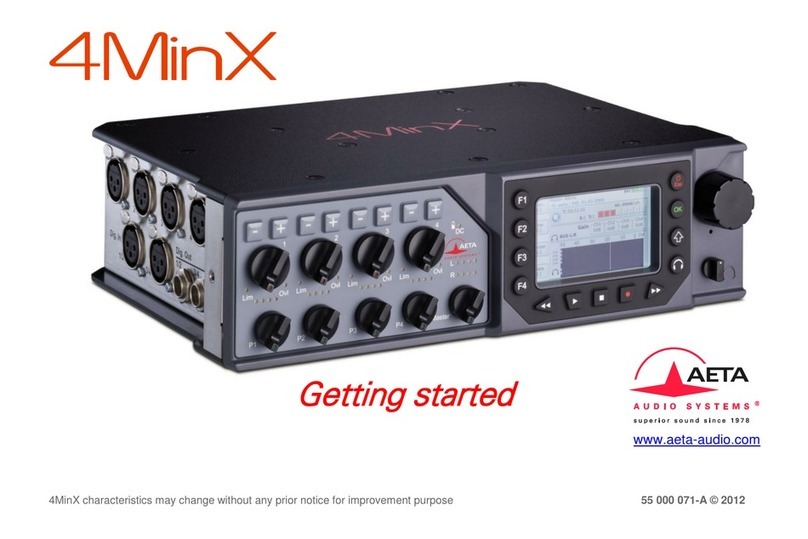
Aeta Audio Systems
Aeta Audio Systems 4MinX Getting started guide
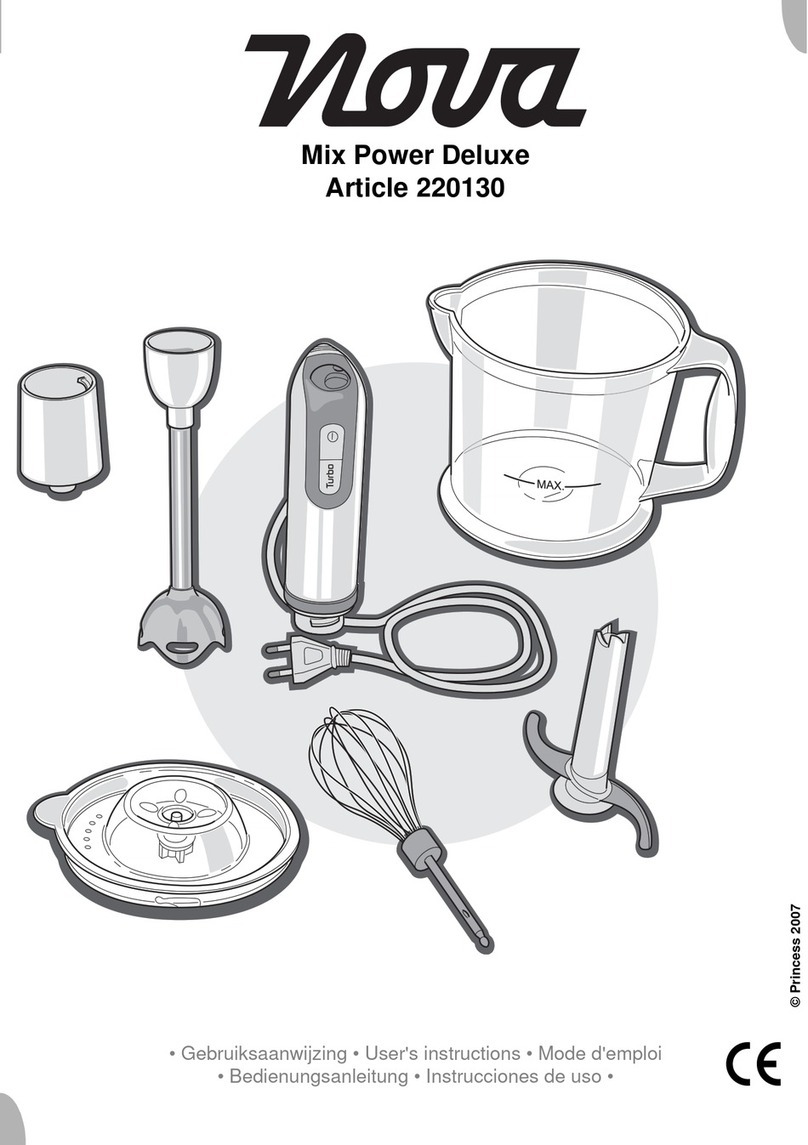
Nova
Nova Mix Power Deluxe 220130 User instructions