Humboldt HM-4165 User manual

product manual
03.11
HM-4165
3-Cell Manual Control Panel


INTRODUCTION
The HM-4165 Pressure Control/Distribution Panel is designed to
control cell and back pressure outputs for up to three triaxial cells.
A digital pressure display allows the monitoring of the pressure of each
output individually. The HM-4165 panel includes the air and water
distribution capabilities including tap water, as well as de-aerated water.
The panel also controls the vacuum necessary to remove air from the tap
water in the de-airing tank. The digital pressure gauge is powered by an
AC to DC transformer and a 110/220 VAC power source is required. A
supply of compressed air is necessary as well as vacuum, tap water, and
a drain to allow water to be removed from the test apparatus.
INSTALLATION
The HM-4165 is a simple bench mounted system, which requires no
fixed mounting.
PANEL MOUNTING
A pair of supporting feet is supplied with the panel so that it can be
bench mounted and remain stable. Screws, nuts, and washers for the
support feet are supplied so that the support feet can be attached as
shown in Figure 1.
AIR/WATER CONNECTIONS
All connections will require either 1/4 inch OD or 1/8 inch OD flexible
tubing. However, metric adapters are available to allow connecting the
¼ inch tubing to 6 mm tubing.
PANEL CONNECTIONS
The panel is equipped with push-to-connect-style fittings on the back
side of the panel frame. It is necessary to use 1/4" OD flexible tubing
to make the connections. Figure 2 shows how the connections are to be
made with air and water sources, as well as connections to the triaxial
cell and other equipment. The panel is designed to accommodate 3
triaxial test apparatuses simultaneously. However, only the connections
for one triaxial test apparatus are shown in the figure. The two remaining
test apparatuses connect to their respective connection locations. Insert
the tubing into the fittings. The seal in the fitting will resist the tubing
and a little extra force will be required to get the tubing to pass through
the seal in the fitting. To make sure the fitting is in all the way, lightly
pull on the tubing. If it comes out of the fitting, it was not inserted
completely. While facing the back of the panel, the four connections
starting from the left are for the water drain, tap water input, vacuum
input, and compressed air input respectively. The last three connections
1

2
are for de-aerated water return from the de-airing tank, tap water going
to the de-airing tank, and air/vacuum to the de-airing tank respectively.
On the face of the panel are the connections for air pressure outputs to
the HM-4151A Bladder Air/Water Cylinders for cell pressure and back
pressure, tap water and de-aerated water for the bladder cylinders,
automatic volume change, and the triaxial cell. Also, there is an auxiliary
pressure connection for air pressure up to 10 psi and an auxiliary vacuum
connection. These connections are made using quick disconnect style
fittings. These fittings have a barbed end and a nut which fits over
the tubing to clamp the tubing on to the barbed end of the fitting.
To disconnect the fittings from the panel, push down on the tab at the
top of the socket half of the fitting as shown in Figure 3. The plug half
of the fitting will pop outward. To reconnect it, just push the plug
into the socket until the tab clicks and locks the plug in place. The
connection for the tap water to the base of the sample via the volume
change device requires a 1/4" to 1/8" push-to-connect adapter to allow
the attachment of 1/4" tubing from the panel to the 1/8" OD tubing
which connects to the volume change device. This adapter is supplied
with the panel.
BLADDER CYLINDER CONNECTION
The bladder cylinders have push to connect style fittings at the bottom
of the assembly. These fittings use the ¼ inch OD tubing and attach
the by the same method as the fittings on the back side of the panel.
The center fitting is for air pressure from the right side of the panel. The
other push-to-connect fitting is for water from the connections on the
front of the panel. There are two bladder cylinders required per triaxial
cell. One bladder cylinder is for cell pressure and tap water supply, the
other cylinder is for back pressure and de-aerated sample water supply.
The air pressure line for one of the bladder cylinders will connect to the
Cell air pressure connection on the front of the panel and the water line
for that bladder cylinder will connect to the Bladder A connection on
the front of the panel. The air line for the second bladder cylinder will
connect to the pore water pressure (PWP) connection on the front of the
panel and the water line for the second bladder cylinder will connect to
the Bladder B connection on the front of the panel as shown in Figure 2.
AUTO VOLUME CHANGE CONNECTION
The Automatic Volume Change Device has push-to-connect fittings for
1/8" OD tubing. The volume change device is connected to the panel at
the Base connection on the front of the panel as shown in Figure 2. The
connection for the tap water to the base of the sample via the volume
change device requires a 1/4" to 1/8" push-to-connect adapter to allow
the attachment of 1/4" tubing from the panel to the 1/8" OD tubing

3
which connects to the volume change device. This adapter is supplied
with the panel.
TRIAXIAL CELL CONNECTION
The triaxial cell has compression fittings on the front as shown in
Figure 4. The cell connection on the triaxial cell connects to the water
connection at the Cell connection on the front of the panel. The base
connection on the triaxial cell connects to the volume change device as
shown in Figure 2 and not directly to the panel.
DE-AIRING TANK CONNECTION
The de-airing tank has connections for the tap water in, de-aerated
water out, and air/vacuum lines. These lines connect to the back side
of the panel at the corresponding push-to-connect fittings as shown in
Figure 2.
ELECTRICAL CONNECTION
The only electrical connection required is to connect the AC to DC
transformer into the back of the digital display and then plug the
transformer into a 110/220 VAC electrical socket as in Figure 5.
OPERATION
After making all of the necessary connections, check to make sure all
of the valves on the front of the panel are set to the off position. Also,
loosen the jam nuts on the regulators as shown in Figure 3.
AIR PRESSURE ADJUSTMENT
There are a total of seven regulators on the panel. The main regulator,
located below the gauge labeled SYSTEM AIR PRESSURE, controls the
supply of air for all of the other regulators. There are six regulators on
the front of the panel near the center which control the output pressure
to the bladder cylinders for cell pressure and back pressure control.
There is also a small regulator at the front of the panel in the upper
right corner labeled AUXILIARY AIR PRESSURE. This regulator is used to
control up to 10 psi of pressure to assist in the purging of water either
from the triaxial cell or from the de-airing tank. This regulator has a
locking knob which must be pulled out to adjust the pressure or pushed
in to lock it into position.

4
AIR/WATER CONTROL VALVES
There are several control valves on the panel for on/off operation of the
air and water control.
There are two valves under the De-Airing Tank heading (Figure 6). These
valves control flow of water to and from the de-airing tank and air or
vacuum to the tank. The water flow valve either allows tap water to fill
the tank or allows the tank to be drained for cleaning and maintenance.
The other valve is for the application of vacuum to the de-airing tank to
remove air from the water in the tank and it also allows compressed air
to be pumped into the tank to assist in draining the water from the tank.
The small auxiliary regulator controls the amount of pressure to assist in
draining the water from the de-airing tank. Set the desired pressure by
turning the knob on the auxiliary regulator in the clockwise direction.
NOTE: These valves must be in the off position during a test.
There are three valves under the AIR CONNECTION heading (Figure
7) on the front of the panel (one valve per triaxial cell). These valves
connect the digital display to the corresponding regulators so that the
pressure for any individual air line can be displayed one at a time.
When the valve is in the off position, the pressure is still controlled by
the regulator. NOTE: When the pressure is displayed for one of the cell
air connections, the other cell air valves must be in the OFF position or
else the incorrect pressure will be displayed.
There are six valves under the WATER CONNECTION heading. There
are two valves for each triaxial cell apparatus which are used to control
the flow of tap water to the cell and to the corresponding bladder
cylinder and also de-aerated water to the Auto Volume Change and to
the other bladder cylinder in the apparatus (Figure 8). When the valve
is in the FILL position, water flows to the cell and bladder cylinder at the
same time, or to the second bladder cylinder and to the Auto Volume
Change at the same time. The CELL valve has drain position which
allows water to be drained from the cell. NOTE: These valves should be
in the off position during a test. The valve is in the off position when the
knob is pointed to the left.
PRESSURE GAUGES
There are two pressure gauges on the panel. The gauge at the upper
left side is used to monitor the pressure regulated by the main pressure
input regulator. It is a mechanical gauge and requires no electrical
source. The other gauge has a digital display and is used to monitor the
air pressure in the bladder cylinders which control the pressure in the
cell and the back pressure in the sample. To operate this gauge, it must
first be connected to an AC power source. It has an On/Off button on
the left side of the display.

5
AIR FILTER
There is an in-line air filter which filters the incoming air from the
compressed air source. It also traps water and other fluids in the line.
MAINTENANCE
There is very little maintenance required. The digital gauge operates
with AC power. If the gauge fails to operate, first check the transformer
to determine if it is operational.
The air filter should be checked every day to determine if the white filter
element is dirty or if fluid must be drained from the clear plastic bowl.
To remove water or fluids from the bowl, turn the black knob at the
bottom of the clear plastic bowl. To purge the fluids from the bowl, turn
the knob as if tightening a right handed screw and the fluids will drain
out of the bottom. To close it, turn the knob as if loosening the screw.
Caution: The filter may be under pressure. If so, the fluids will spray out
at high velocity.
If the filter becomes dirty and clogged, open the drain plug as described
above to relieve pressure. Remove the bowl by rotating the bowl
counterclockwise to unscrew it from the filter body. Be careful not to
lose or damage the o-ring that seals the bowl to the body of the filter.
Next, unscrew the filter support by turning it clockwise until it comes off.
Slide the filter element off of the support and replace it with a new filter.
Reassemble the air filter assembly in the reverse order.
FIGURE 1
MOUNTING FEET ASSEMBLY
8-32 UNC NUT WITH WASHER
8-32 UNC MACHINE SCREW
Figure 1: Mounting Feet Assembly

7
HM-2310.20
DISPLACEMENT
TRANSDUCER
HM-4170
PWP
HM-2300.020
LOAD CELL
HM-4199B
TRIAXIAL CELL
HM-3000
DIGITAL MASTER LOADER
HM-4187A.3F
DE-AIRING TANK
HM-2310.10
DISPLACEMENT
TRANSDUCER
HM-2315
VOLUME
CHANGE
DEVICE
HM-4151A
BLADDER
AIR/WATER CYLINDER
HM-4165
DISTRIBUTION
PANEL
COMPRESSED
AIR
VACUUM
TAP
WATER
DRAIN
HUMBOLDT MFG. CO.
MANUALLY CONTROLLED 3 TRIAXIAL CELL SYSTEM
TO CELL VALVE
TO BASE VALVE
FIGURE 2
Figure 2

6
LOOSEN JAM NUT
PRIOR TO ADJUSTING
AIR PRESSURE
PUSH DOWN
TO RELEASE
CONNECTOR
FIGURE 3
Figure 3
Figure 4 Triaxial Cell
PRESSURE
TRANSDUCER
TO CELL
TO BASE
AIR BLEED
VALVE
FIGURE 4
TRIAXIAL CELL

Figure 5B
Figure 5Figure 5

FIGURE 6
DE-AIRING TANK CONTROL VALVES
DE-AIRED WATER
FILL DRAIN
OFF
VACUUM PRESSURE
TURN KNOB LEFT
TO FILL DE-AIRING
TANK WITH TAP WATER
OR
TURN KNOB RIGHT TO
DRAIN DE-AIRING TANK
TURN KNOB LEFT TO
APPLY VACUUM TO
DE-AIRING TANK
OR
TURN KNOB RIGHT TO
APPLY PRESSURE TO
ASSIST DRAINING
OF DE-AIRING TANK
AIR CONNECTION
OFF
PWP
CELL
STEP 1: TURN KNOB
POINTING UP TO "CELL"
STEP 2: ADJUST CELL
PRESSURE BY ADJUSTING
REGULATOR TO THE
PRESSURE SHOWN ON THE
DIGITAL DISPLAY
STEP 3: TURN KNOB
POINTING DOWN TO
"PWP"
STEP 4: ADJUST BACK
PRESSURE TO THE DESIRED
PRESSURE SHOWN ON THE
DIGITAL DISPLAY
FIGURE 7
CELL AND BACK PRESSURE CONTROLS
Figure 6
Figure 7

8
WATER CONNECTION
CELL
BLADDER
A
FILL
DRAIN
BASE
BLADDER
B
FILL
CELL
PWP
FIGURE 8
CELL AND SAMPLE BASE WATER CONTROLS
TURN KNOB UP
TO FILL CELL AND
BLADDER CYLINDER "A"
WITH TAP WATER
TURN KNOB DOWN
TO DRAIN CELL
AND BLADDER
TURN KNOB DOWN
TO FILL CELL AND
BLADDER CYLINDER "B"
WITH DE-AERATED
WATER
Figure 8

9
Introduction
Follow these instructions when installing, operating, or servicing the product.
Application Limits
These products are intended for use in general purpose compressed air
systems only.
Operating Inlet Pressure:
kPa PSIG bar
with Polycarbonate Bowl 1000 150 10.3
with Metal Bowl 1700 250 17.0
NOTE: The maximum recommended pressure drop for a particulate filter is
70 kPa (10 psig, 0.7 bar)
Ambient Temperature Range:
with Polycarbonate Bowl 0°C to 52°C (32°F to 125°F)
with Metal Bowl 0°C to 80°C (32°F to 175°F)
ANSI Symbols
Micro-Mist Lubricators (Figure 1)
Description
These micro-mist lubricators are designed to deliver an atomized oil mist to air
operated tools, motors, and other pneumatic equipment. Units are equipped
with full-view sight glass for visual indication of oil drop rate, needle valve feed
adjustment to regulate oil drop rate, and a venturi bypass disc to compensate
for changes in air flow demands.
Installation of Lubricator
1. Lubricator should be installed with reasonable accessibility for service
whenever possible - repair service kits are available. Keep pipe and tubing
lengths to a minimum with inside clean and free of dirt and chips. Pipe
joint compounds should be used sparingly and applied only to the male
pipe – never into the female port. Do not use PTFE tape to seal pipe joints
- pieces have a tendency to break off and lodge inside the unit, possibly
causing malfunction.
2. Install lubricator so that air flow is in the direction of arrow on body.
3. Installation should be upstream from, and as close as possible, to the
device it is to lubricate (valve, cylinder, tool, etc.). Whenever possible,
avoid locations that require air-borne oil to move in an upward direction to
reach the device to be lubricated.
4. The installation of an individual lubricator for each air consuming device
provides best assurances of proper lubrication.
5. In new installations, it is good practice to “wet down” the inside diameter of
piping and/hose with oil before making final connections. Although your
lubricator delivers oil to the line, pre-coating the inside diameter with oil
helps insure that proper amounts of oil are delivered to the point
of application.
Operation & Service of Lubricator
!
Warning: Before filling, inlet pressure must be eliminated and
then de-pressurize system pressure.
1. FILLING - After de-pressurizing system, remove fill plug or bowl to refill
lubricator. Fill bowl to fill line indicated on the bowl with oil of 150 to 200
SSU at 100°F viscosity - same as SAE No. 10 (petroleum based hydraulic
oils or spindle oils are good examples). DO NOT USE OILS WITH TACKY
ADDITIVES, COMPOUND OILS CONTAINING SOLVENTS, GRAPHITE,
SOAPS OR DETERGENTS. (Automotive oils generally contain detergents
and are not recommended.
2. Replace the fill plug or bowl and seat firmly. Excessive torque is not
necessary. The lubricator is now ready for setting.
3. OIL DELIVERY ADJUSTMENT - To adjust oil delivery, turn the adjusting
needle on top of the lubricator.
Leaner - Clockwise Richer - Counterclockwise
By counting the number of drops per minute in the sight dome, you can adjust
lubricator to your required setting. Approximately 3% of the droplets visible in
the sight dome go downstream; adjust drip rate accordingly. Consult oil delivery
conversion chart (see below).
Generally, one drop per minute downstream for every 10-15 SCFM flow is
satisfactory. 25 drops per minute equals one ounce per hour - volume of oil
passing through the sight dome.
NOTE: This is a constant density type lubricator which delivers a constant
ratio of oil to air flow. Therefore, if air flow increases or decreases, oil
delivery will be effected proportionately. ONLY IF DIFFERENT RATIO
IS DESIRED NEED YOUR NEEDLE VALVE SETTING BE CHANGED
AFTER YOUR INITIAL SETTING.
1
2
3
4
5
6
7
Downstream Delivery DPM
33 67 100 133 167 200 233
Dome Drip Rate DPM
Oil Delivery Conversion
3% of Drip Rate to Downstream
Installation & Service Instructions:
1M103G
Miniature Series
Micro-Mist Lubricators &
Particulate Filters
ISSUED: November, 2003
Supersedes: September, 2000
Doc.# 1M103, ECN# 030539, Rev. 8
WARNING
To avoid unpredictable system behavior that can cause personal injury
and property damage:
• Disconnect electrical supply (when necessary) before installation,
servicing, or conversion.
• Disconnect air supply and depressurize all air lines connected to
this product before installation, servicing, or conversion.
• Operate within the manufacturer’s specified pressure, temperature,
and other conditions listed in these instructions.
• Medium must be moisture-free if ambient temperature is below
freezing.
• Service according to procedures listed in these instructions.
• Installation, service, and conversion of these products must be
performed by knowledgeable personnel who understand how
pneumatic products are to be applied.
• After installation, servicing, or conversion, air and electrical
supplies (when necessary) should be connected and the product
tested for proper function and leakage. If audible leakage is present,
or the product does not operate properly, do not put into use.
• Warnings and specifications on the product should not be covered
by paint, etc. If masking is not possible, contact your local
representative for replacement labels.
WARNING
FAILURE OR IMPROPER SELECTION OR IMPROPER USE OF THE
PRODUCTS AND/OR SYSTEMS DESCRIBED HEREIN OR RELATED
ITEMS CAN CAUSE DEATH, PERSONAL INJURY AND PROPERTY
DAMAGE.
This document and other information from The Company, its subsidiaries
and authorized distributors provide product and/or system options for
further investigation by users having technical expertise. It is important
that you analyze all aspects of your application, including consequences
of any failure and review the information concerning the product or
systems in the current product catalog. Due to the variety of operating
conditions and applications for these products or systems, the user,
through its own analysis and testing, is solely responsible for making
the final selection of the products and systems and assuring that all
performance, safety and warning requirements of the application are
met.
The products described herein, including without limitation, product
features, specifications, designs, availability and pricing, are subject to
change by The Company and its subsidiaries at any time without notice.
EXTRA COPIES OF THESE INSTRUCTIONS ARE AVAILABLE FOR
INCLUSION IN EQUIPMENT / MAINTENANCE MANUALS THAT UTILIZE
THESE PRODUCTS. CONTACT YOUR LOCAL REPRESENTATIVE.
Pneumatic Division
Richland, Michigan 49083
269-629-5000
!
!
Lubricator Particulate Filte
r
Wilkerson Lubricators and Filters



www.humboldtmfg.com
HUMBOLDT
Testing Equipment for Construction Materials
Humboldt Mfg. Co.
3801 North 25th Avenue
Schiller Park, Illinois 60176 U.S.A.
U.S.A. Toll Free: 1.800.544.7220
Voice: 1.708.456.6300
Fax: 1.708.456.0137
Email: [email protected]
Warranty
Humboldt Mfg. Co. warrants its products to be free from defects in material or
workmanship. The exclusive remedy for this warranty is Humboldt Mfg. Co.,
factory replacement of any part or parts of such product, for the warranty of this
product please refer to Humboldt Mfg. Co. catalog on Terms and Conditions
of Sale. The purchaser is responsible for the transportation charges. Humboldt
Mfg. Co. shall not be responsible under this warranty if the goods have been
improperly maintained, installed, operated or the goods have been altered or
modified so as to adversely affect the operation, use performance or durability
or so as to change their intended use. The Humboldt Mfg. Co. liability under
the warranty contained in this clause is limited to the repair or replacement of
defective goods and making good, defective workmanship.
Table of contents
Other Humboldt Control Panel manuals
Popular Control Panel manuals by other brands
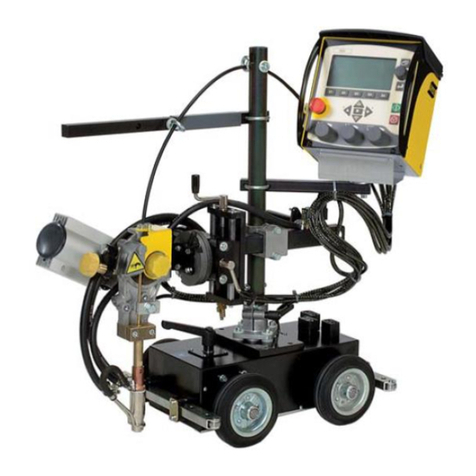
ESAB
ESAB A2 PEK instruction manual
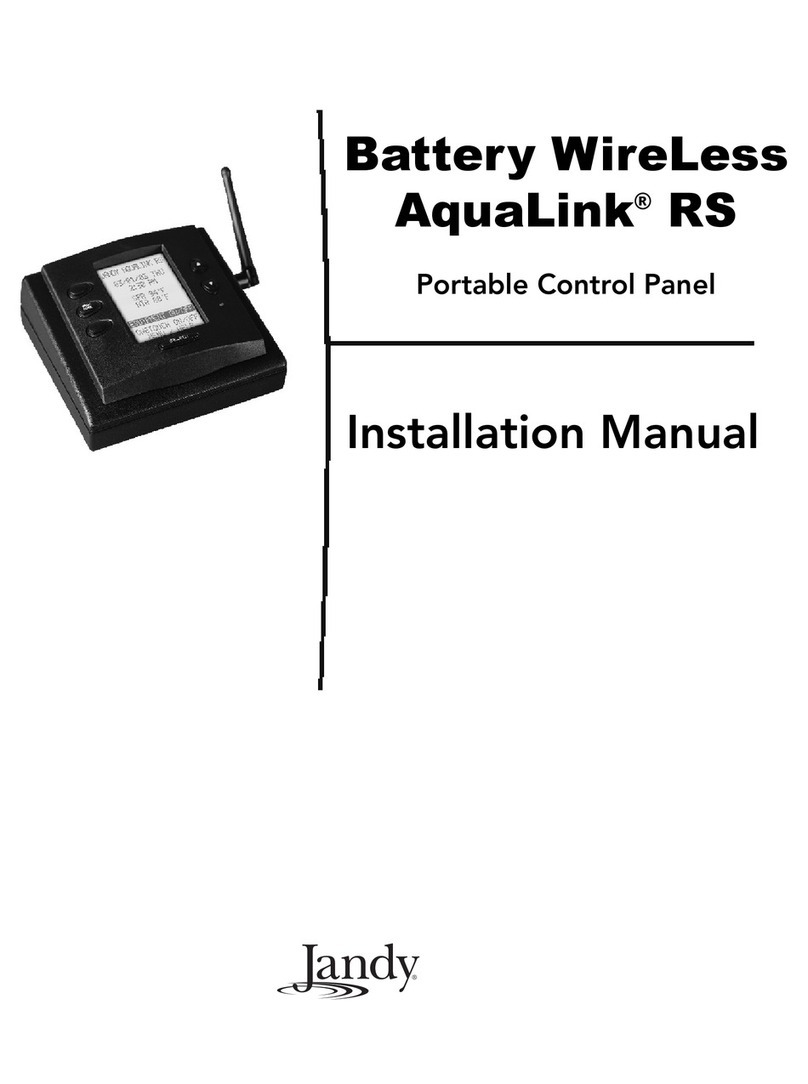
Jandy
Jandy AquaLink RS installation manual

Toshiba
Toshiba TCB-EXS21TLE installation instructions
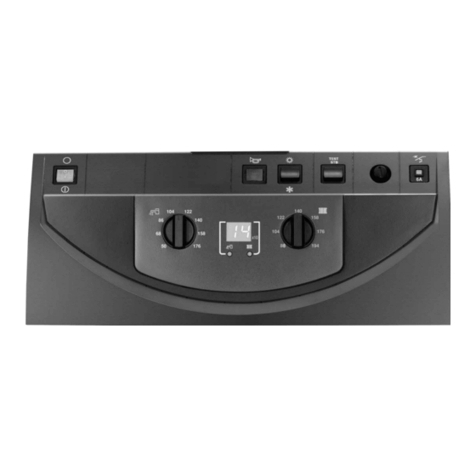
DeDietrich
DeDietrich B control panel Instructions for use, Electrical connection, Start up
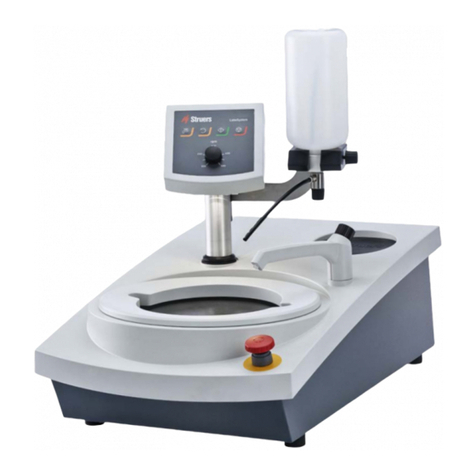
Struers
Struers LaboForce-100 instruction manual

Bosch
Bosch D9412GV4 Program entry guide
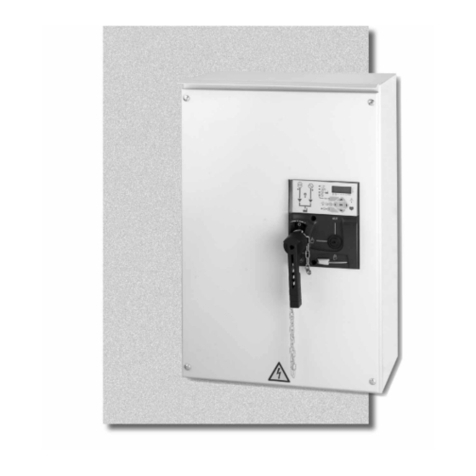
socomec
socomec ATI 250 A Technical instruction manual
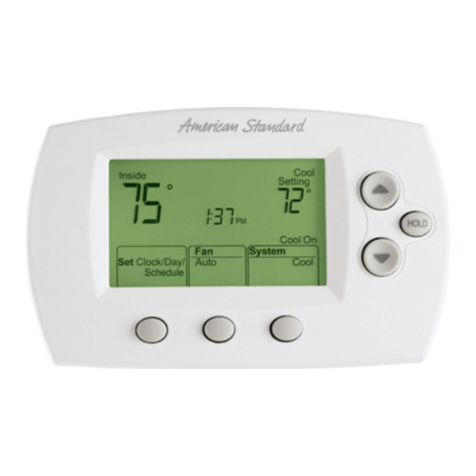
American Standard
American Standard ACONT602AF22MA installation instructions
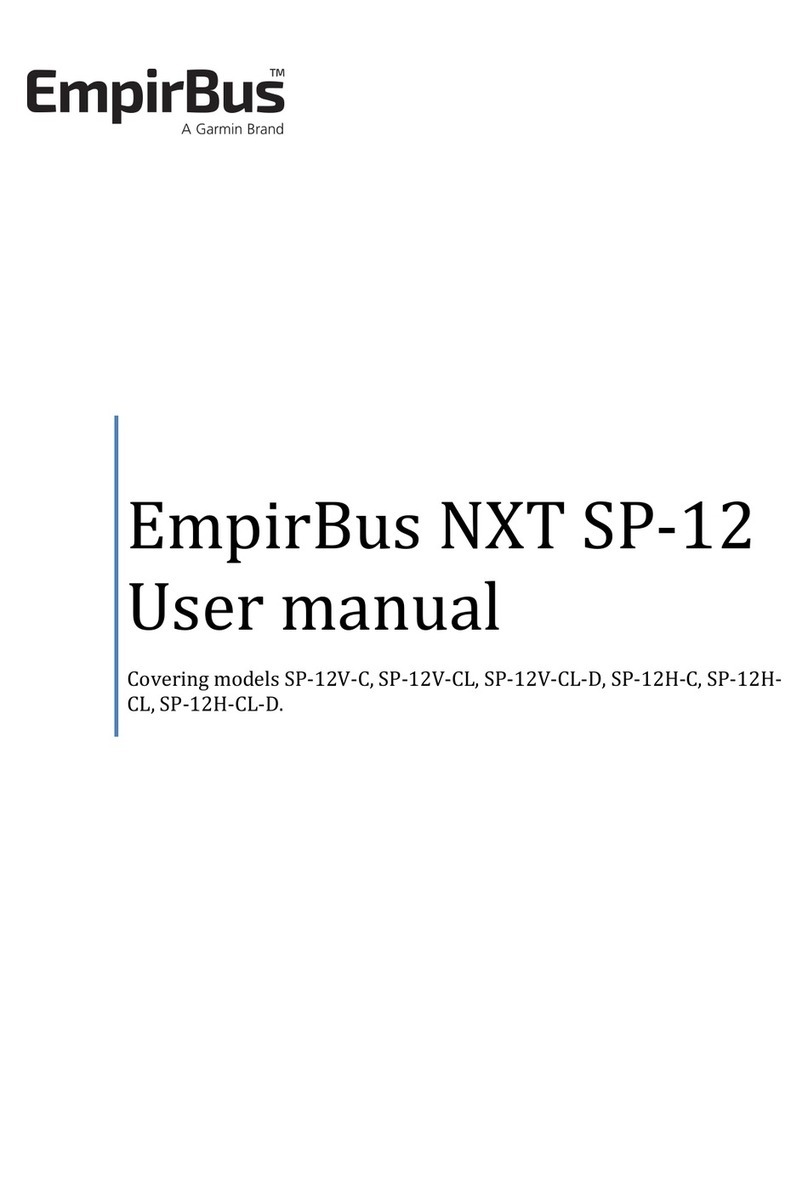
EmpirBus
EmpirBus NXT SP-12V-C user manual
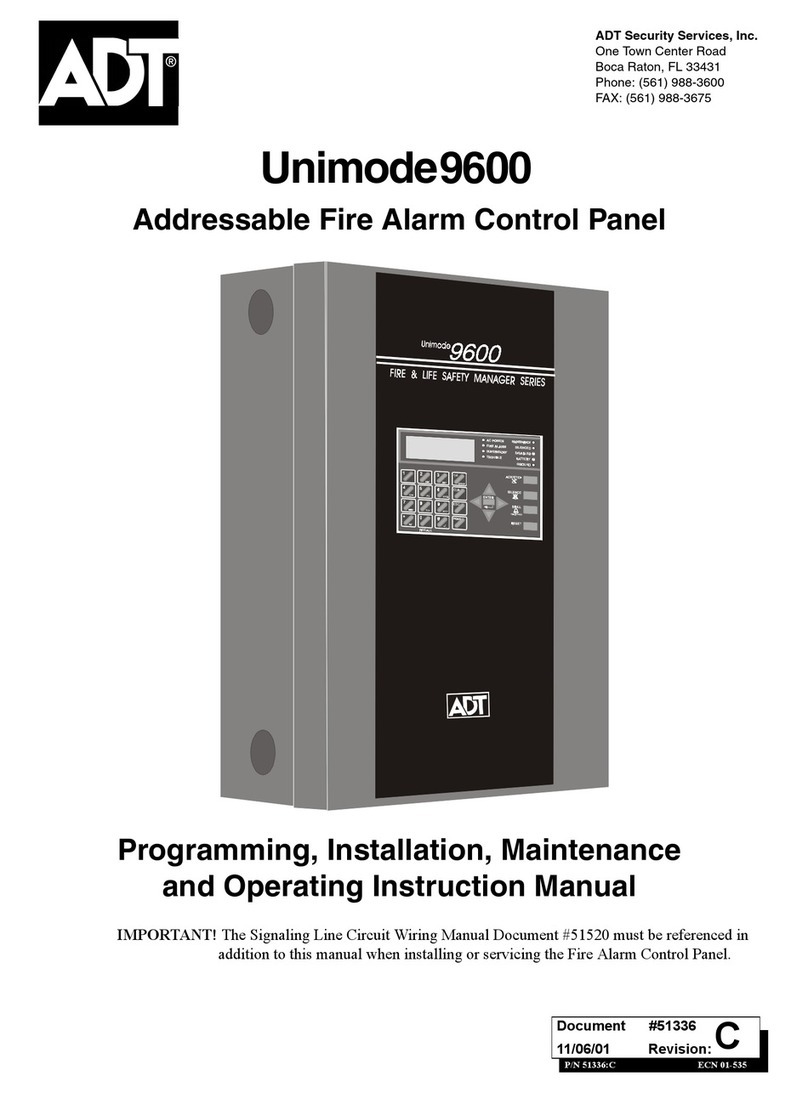
ADT
ADT Unimode 9600 Installation and operating instruction

Bentel Security
Bentel Security Omnia user manual
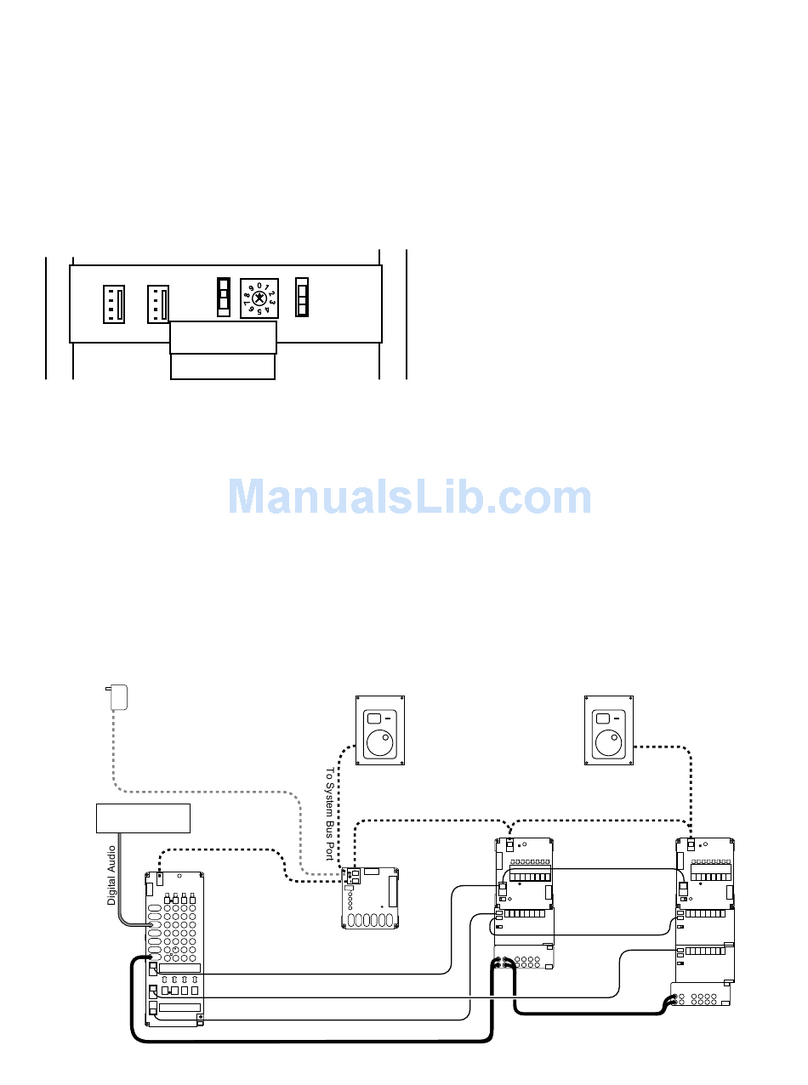
Audio Authority
Audio Authority 906G Installation and operation