Humboldt h-4169 User manual

product manual
H-4169_man_0315
H-4169
Automatic Mechanical Compactor

SAFETY WARNING
Please read these instructions thoroughly to become familiar
with the operation of the machine before attempting to run it.
This machine is NOT designed to operate with the doors open.
It has an electrical door interlock.
Keep hands, clothing and other objects away from moving parts when
the machine is in operation.
Introduction
It is very important that these instructions be read to become thoroughly familiar with
the operation of the Machine before attempting to run it. The mechanical compactor
more closely duplicates hand-compaction methods. It is suitable for standard or modified
Proctor compaction tests with adjustment for 12" or 18" drop and accommodating 4" or
6" inside diameter molds. Test results show that the H-4169 Compactor can give results
within 1% when compared with hand compaction and a 4" mold.
It is recommended for this compaction machine to be bolted to a concrete floor or
mounted on a concrete base. We recommend a base approximately 15" wide x 24"
deep x 12 to 18" high. The machine should be firmly bolted in place. The bolt holes
are 10.625" centers in width, 14.5" centers in depth. The machine should be set level,
checking that the turntable is level in both directions.
A 20 amp receptacle with an on-off switch is required
and must also be provided by user.
Machine must be turned off when not in use. This machine will not operate with
the doors open.
Machine Set up
Take one of the hammers, which are packed separately for shipping, and insert into the
hammer cage, the round-type hammer is used with a 4" mold, while the pie-shaped foot
is used with a 6" mold. In order to perform this operation proceed as follows:
1. Place a mold on the turntable. A 0.25" diameter pin extends from the center of
the turntable and is used to center the mold. After locating the mold in position
bolt the mold down to the table. Two sets of holes are located on the turntable for
mounting the 4" and 6" molds.
2. Remove the front cage bar by pulling down the spring-loaded retaining pin on
top of same and lift out. Insert the hammer with foot down into the hammer
cage from the front of the machine. Slowly slide the hammer down. DO NOT
DROP, taking care not to trap fingers. Replace front cage bar. Close hinged cover
and secure latch.

3. The hammer can now be lifted by manipulating the jog switch, until it is high
enough to swing the hammer safety device under the hammer opening, that soil
can be added to mold.
4. Whenever a mold is being changed or inspected, run the hammer up in the
machine by means of the jog switch. Then swing the hammer safety arm, painted
yellow, under the hammer opening. If the hammer should float down from its own
weight, it will come to rest on the safety device. When ready to proceed with the
testing, just jog the hammer up and swing the safety arm out of the way to the
right.
Operation
For compaction with a standard mold, 6" inside diameter.
Place the first layer of soil in the mold and place the mold in position on the turntable
and clamp tightly. The height change cam should be in the top position for 18" drop.
(See height change cam instructions). Set the pre-determining counter to 54. (See
instructions for pre-determining counter). This will insure that 55 blows are struck, at the
end of said number, the machine will automatically stop.
Press the green start button on the right hand side of the machine. Immediately,
the carriage will rise lifting the hammer until such time as the hammer lifting catch is
withdrawn by the uppermost cam on the cam bar. The hammer will fall, and as the
carriage completes its cycle, it will be picked up again. As the carriage rises, lifting the
hammer with it, the table rotating switch is actuated, which actuates the timing circuit,
which actuates the turntable. (See Table mechanism).
The machine will continue to run until such time as 55 blows have been struck. When the
machine stops, the hammer should be lifted by means of the jog switch and an additional
layer of soil placed in position in the mold and roughly leveled. Reset the counter and
repeat as above. Continue until all layers have been compacted. The collar should be
on the mold at least for the last two layers. When using a 6" mold, the pie-foot hammer
must be used. (See hammer instructions and table adjustment).
For compaction with 4" mold
Remove the pie-shape hammer from machine and replace with 5.5 lbs round hammer.
(See hammer instruction and table adjustment).
Place first layer of soil in the mold and place mold in the turntable and secure. The height
change cam must be set for 12" drop. (See height change instructions). Set the counter
to 24 and press the start button. Machine will run until 25 blows have been struck. Raise
hammer by using jog switch, add a layer of soil and repeat.

Table Mechanism
The table mechanism assembly is fitted to and contained within the base of the machine.
The table is rotated by a stepping motor. As the table rotating switch, #701, is depressed,
the table begins to rotate. The amount of rotation of the turntable can be controlled
by the time-delay circuit located in the switch box on the right side of the machine.
Turn the knob clockwise for more rotation or counter clockwise for less. Before starting
the machine the first time, turn the knob all the way to the left. Start machine without
hammer, turn knob slowly to the right until the desired amount of index is accomplished.
The knob setting can be left set, except for only minor adjustments.
Table Adjustment. Change mold sizes.
When changing molds from 4" to 6" or vice versa the whole base must be moved.
Loosen the 4 hex bolts on the table base. The whole assembly now can be moved in
or out for adjusting the clearance between hammer and inside diameter of mold. This
adjustment must be made when changing from one mold size to another. The clearance
should be about 0.1" or 2.5 mm.
Predetermining Counter
To start machine up:
Switch the power on, (your wall switch) the counter will light up showing "00". At this
point the jog button is operative. Set the counter by pressing "X 10" for tens. "X 1" for
single digits, then press "Reset". Now the counter is set up.
Push the start button, the machine will start up, when counter shows "00", the machine
will stop. To repeat the same number of blows only the "Reset" needs to be pressed.
If the hammer is picked up by the jog button, or being held up to add more soil the
counter should be set one count less than the desired count. When machine is not in use
the power should be turned off (Your wall switch).
Height Change Mechanism
The top cam, #413, is located on the cam bar, #1410, at the rear of the carriage. The
cam disengages the catch #304, and causes the hammer to fall. There are two positions
in which this cam can be placed. The lower position will release the hammer from a 12"
drop and the upper position will release the hammer for an 18" drop. To change the
cam from one position to an other, it is only necessary to remove the socket cap screw,
#418. The cam is inserted in a slot and can be pulled out by hand. Insert cam in the
desired position and replace the screw. The slot in the upper cam is meant for calibration
adjustment.
Hammer Lifting Mechanism
A 1/2 HP electric motor is fitted with a gear box, which drives an endless chain. A link on
this chain carries a spindle, which fits into a bronze block. The bronze block slides in a
horizontal groove in the carriage, #2301. The carriage slides in a vertical direction on two
steel guide bars. The cam bar, #1410, has a slot at the upper end in which the top cam,
#413, is located. In a slot at the lower end, the pick-up cam, #414, is located. It is spring
loaded. With the carriage in the low position, the spring loaded cam will push the catch

#304, into the hammer grooves. The carriage will carry the hammer up where the top
cam pulls the catch back and drops the hammer.
Chain Adjustment
With the carriage in the down position, one should be able to move the chain about
0.25" sideways. If it gets to be a lot more, it can break the micro switch. To adjust the
chain, loosen the 4 bolts holding the idler. Push the idler up with the 0.25" bolt under
the idler shaft. Then tighten bolts again.
Hammer Note
The hammer is guided in its free fall by three vertical rods. The removable rod, #403, acts
as a guide to keep the pie hammer from rotating. The hammer with the 2" diameter foot
or the hammer with the pie foot weight is 5.5 lbs. To change either hammer to 10 lbs.,
a weighted plug is used. It is inserted into the top of the hammer and held in place with
a socket capscrew. NEVER DROP HAMMER ON TURNTABLE OR IN EMPTY MOLD. The
hammer must free-fall. The front cage bar is adjustable. This can be done by moving the
adjusting plates #419 top and #420 bottom in or out. Loosen the 0.25" bolts somewhat
and tap the plates in or out, re-tighten screws.
Molds
The molds are made special for the H-4169 Compactor.
Standard Proctor Compaction Mold, 4": H-4141
Standard Proctor Compaction Mold, Split Design, 4": H-4225
Modified Proctor Compaction Mold, 6": H-4162
Modified Proctor Compaction Mold, Split Design, 6": H-4161A
CBR Mold with Perforated Base, 6": H-4151
CBR Mold with Solid Base, 6": H-4149
Compaction Mold, 6": H-4159
LBR Mold, 6": H-4163
Calibration Kit for H-4169 Compactor: H-4169CK
Mechanical Compactor Safety Cage: H-4169.100-B

Instructions for Replacing Micro Switch
Before doing anything, remove the hammer and unplug the machine. To
replace switch proceed as follows: Remove defective switch from bracket, install
new switch and switch cover on bracket. Check the new switch by pressing the
lever down by hand to where you hear or feel a click, (see Fig. I). Release the
lever slowly, you should hear or feel another click. At this point the lever should
be about 1/16" away from the stop pin. The lever may need to be re-bend a
little to get close to 1/16" (see Fig.2).
Proper Adjustment of Switch Bracket
Loosen screws "A and B" slightly, move switch bracket all the way to right. By
means of Jog-Button, manipulate the carrier pin to the highest point of the
switch lever, as shown in "Fig.3".
Now move the switch bracket to the left, until you hear a click in the switch.
Move it about 1/16" to 3/32". Beyond this point, further to the left, (see Fig.4).
Then tighten screws "A and B". After this is done the machine is ready to run.
NOTE: There must be a nylon bushing (part #207) on the carrier pin. Also the
chain should not be too loose and flapping.

Lubrication and Maintenance
The only lubrication that is needed is some light oil on the Catch. A spray lubri-
cant works best on the Drive Chain. The oil level in the gear reducer should be
checked. Mobilegear 634 is recommended. Use a Grease Gun to lubricate the
two fittings on the Carriage and Chain. The Guide Bars must be kept clean and
dry, do not lubricate. See Chain adjustment in this manual.
Problem Cause Cure
Counter does not light up,
Push buttons do not work No power to machine Check power supply and
proper voltage
Jog-button works, counter
shows "00", Run button does
not work
Counter not set up properly Read counter predetermining
instructions
Counter does not count
down, Turntable indexes
properly
Defective counter Replace counting unit
Counter does not count
down, Turntable does not turn
1) 701 switch out of adjustment,
defective.
2) nylon roller #207 missing
3) Timing Module defective
1) check adjustment, replace
2) replace
3) replace
Counter does not count
down, Turntable turns con-
tinuously
1) Index knob turned too far to
right,
2) 701 switch stuck closed
3) Timing Module defective
1) turn knob to left for indexing
2) check 701 switch
3) replace Timing Module
Turntable motor is very noisy
at start, sometimes runs CW/
CCW or just growls
Timing Module
Turntable Motor
1) replace
2) send turntable motor in for
inspection, special motor
Machine runs fine, but misses
count and index occasionally 701 Switch out of adjustment See Switch instruction in this
manual
701 Switch keeps breaking Chain too loose See Chain Adjustment in this
manual
Hammer does not get
picked up
1) lower cam spring
2) Cam not moving free
3) Hammer cage too loose
4) Cam bar out of adjustment
1) Remove lower cam and
spring, stretch or replace
2) remove any burrs
3) adjust front cage bar
4) Cam bar needs to be
adjusted high enough so the
catch snaps into the hammer
groove all the way
Hammer drops on the way up
1) Hammer cage too loose
2) Steel ball under Catch not
effective
1) adjust front cage bar
2) Replace
3) Be sure the steel Ball and
Spring are under the Catch
Hammer hits mold after mold
size change
Turntable was not changed after
Mold change
See table adjustment in this
manual

www.humboldtmfg.com
HUMBOLDT
Testing Equipment for Construction Materials
Humboldt Mfg. Co.
875 Tollgate Road
Elgin Illinois 60123 U.S.A.
U.S.A. Toll Free: 1.800.544.7220
Voice: 1.708.456.6300
Fax: 1.708.456.0137
Email: [email protected]
Supplied By:
Warranty
Humboldt Mfg. Co. warrants its products to be free from defects in material or
workmanship. The exclusive remedy for this warranty is Humboldt Mfg. Co.,
factory replacement of any part or parts of such product, for the warranty of this
product please refer to Humboldt Mfg. Co. catalog on Terms and Conditions
of Sale. The purchaser is responsible for the transportation charges. Humboldt
Mfg. Co. shall not be responsible under this warranty if the goods have been
improperly maintained, installed, operated or the goods have been altered or
modified so as to adversely affect the operation, use performance or durability
or so as to change their intended use. The Humboldt Mfg. Co. liability under
the warranty contained in this clause is limited to the repair or replacement of
defective goods and making good, defective workmanship.
Table of contents
Popular Garbage Disposal manuals by other brands
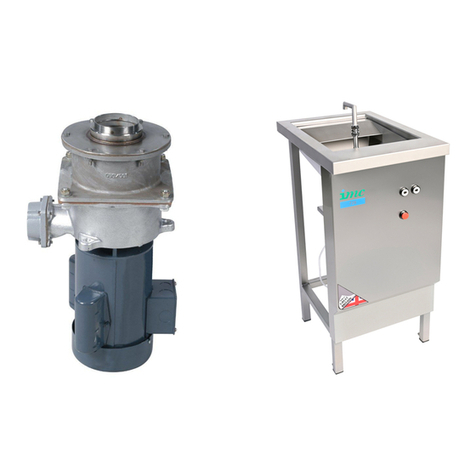
IMC
IMC 700 Series Installation, operating and servicing instructions
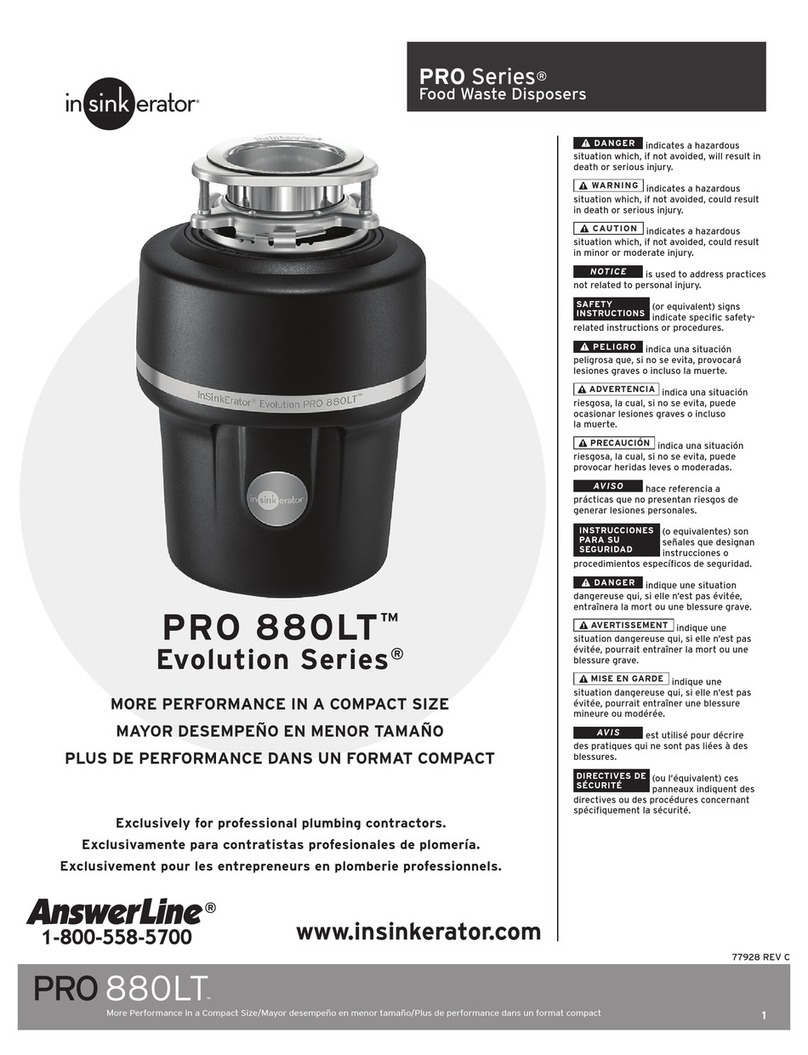
InSinkErator
InSinkErator Evolution PRO 880LT manual
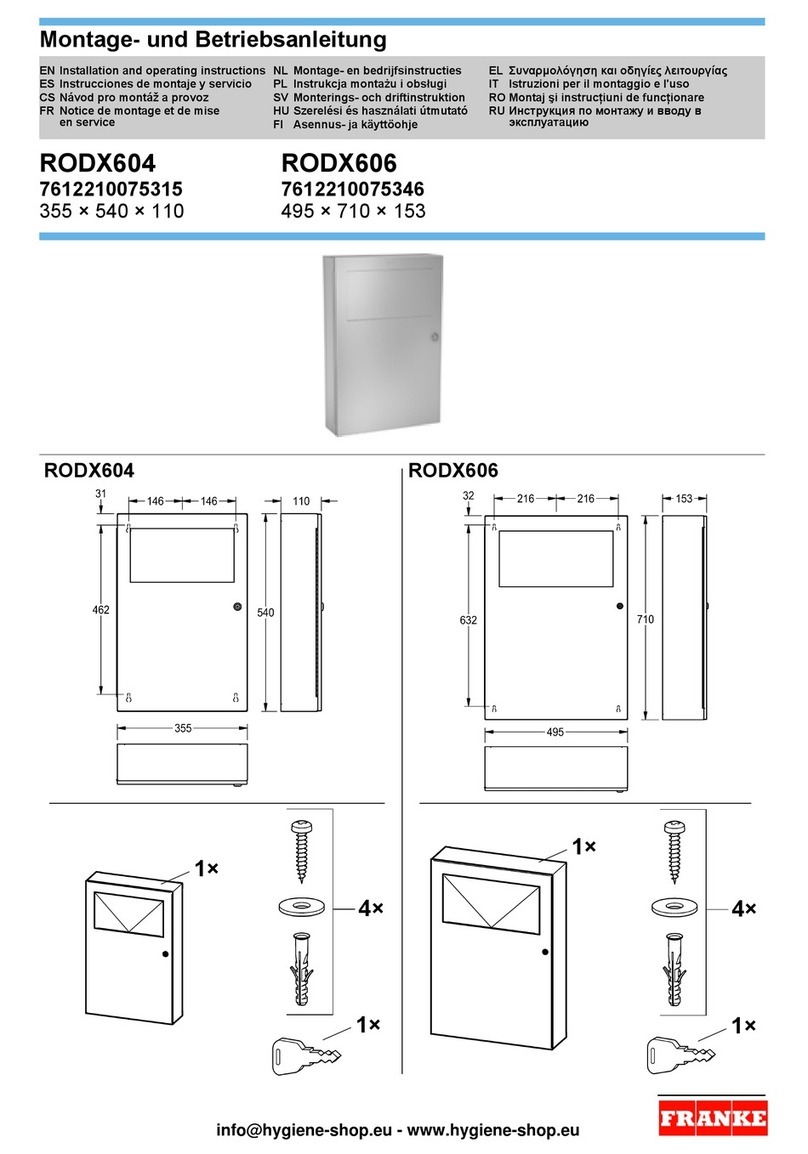
Franke
Franke RODX604 Installation and operating instructions
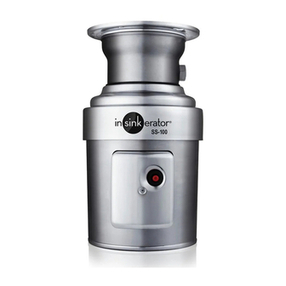
InSinkErator
InSinkErator 13954 Installation & use manual

KitchenAid
KitchenAid INTEGRATED COMPACTOR Use and care guide
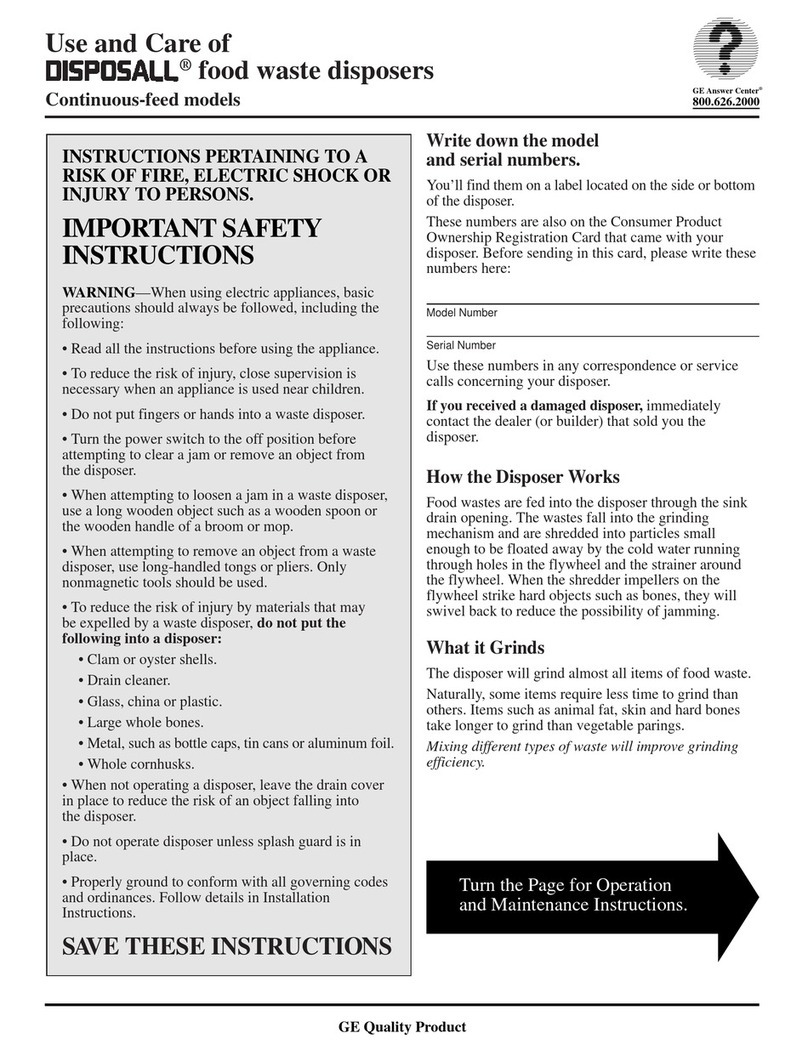
GE
GE GFC100 Use and care
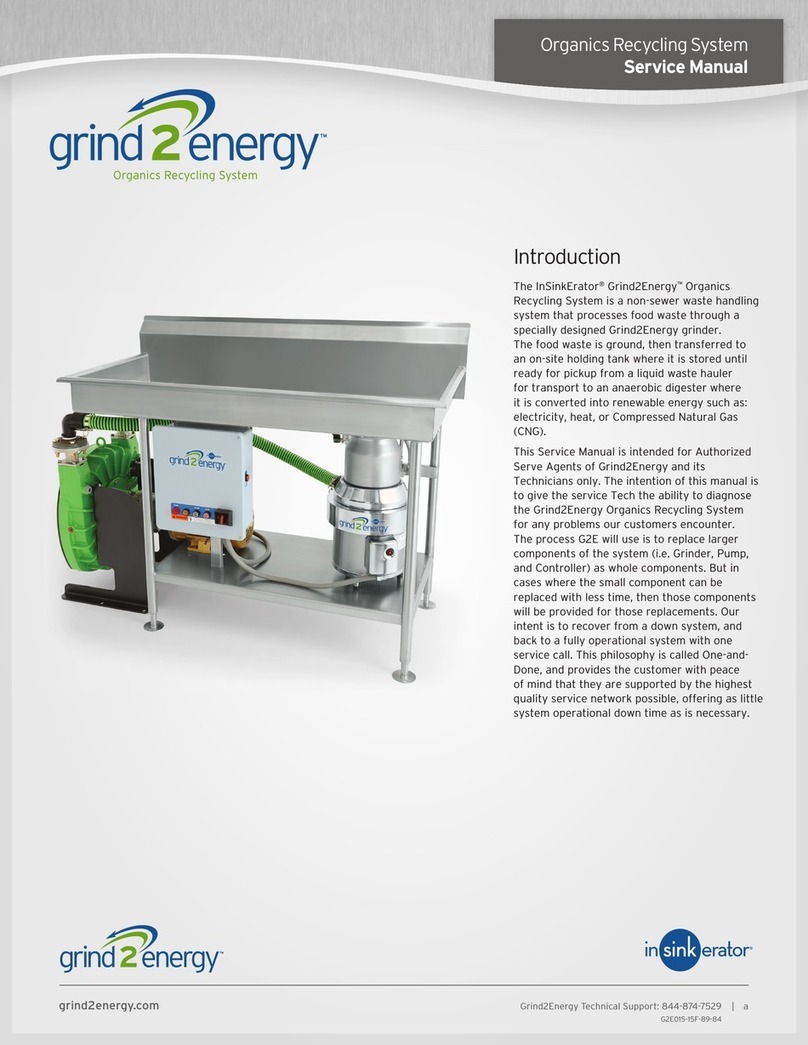
Emerson
Emerson InSinkErator Grind2Energy Service manual

KWC
KWC RODAN RODX605TT Installation and operating instructions
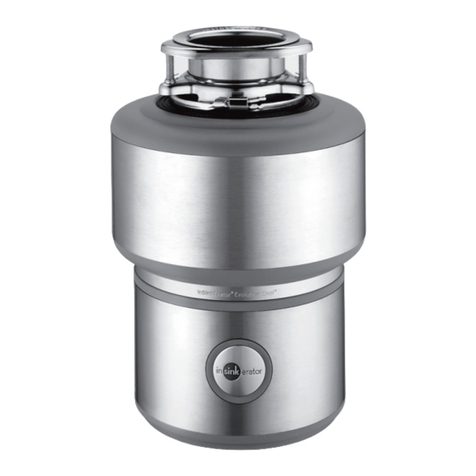
InSinkErator
InSinkErator Evolution Excel Manual reset
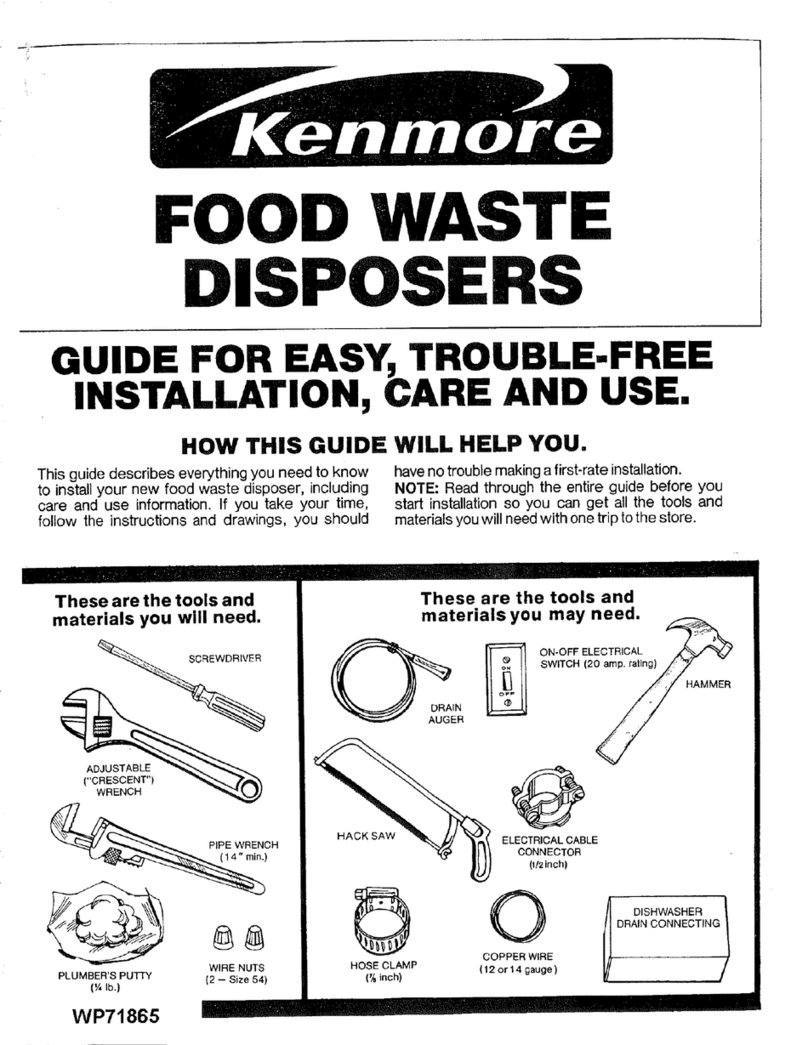
Kenmore
Kenmore WP71865 Use & care guide
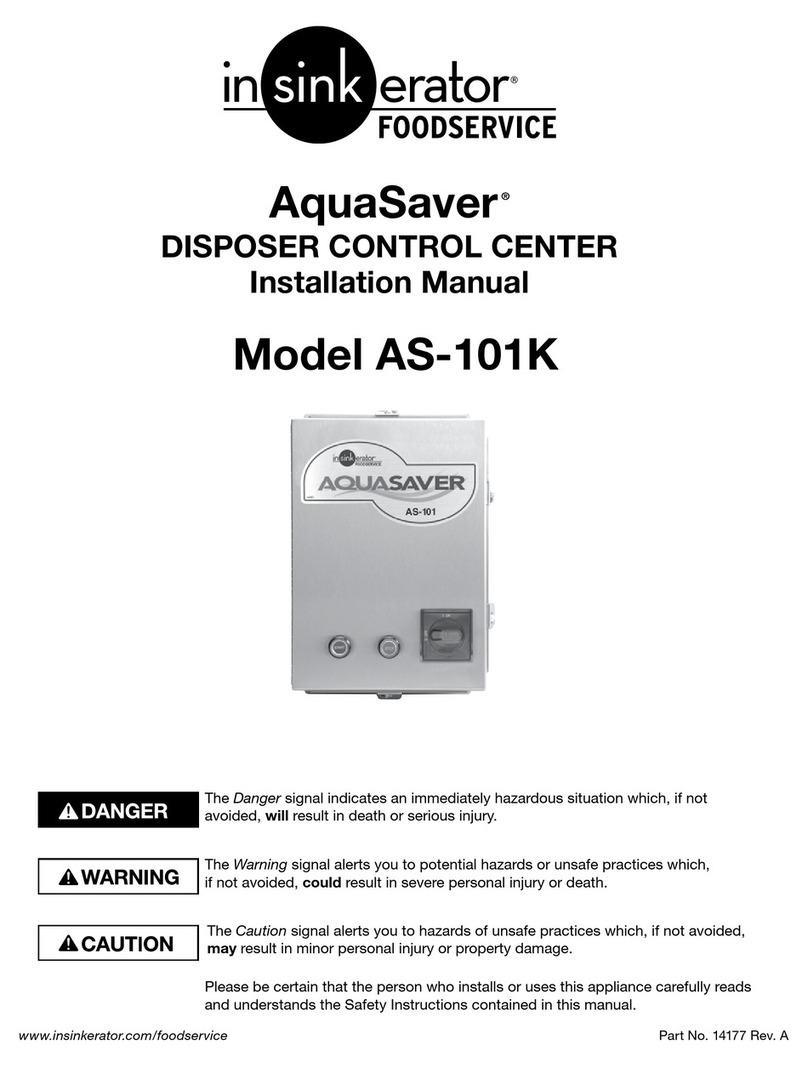
InSinkErator
InSinkErator AQUASAVER AS-101K installation manual

Bort
Bort MASTER ECO installation instructions